机械制造技术课程设计拨叉的加工工艺规程及其钻铰27孔的夹具设计【全套图纸】
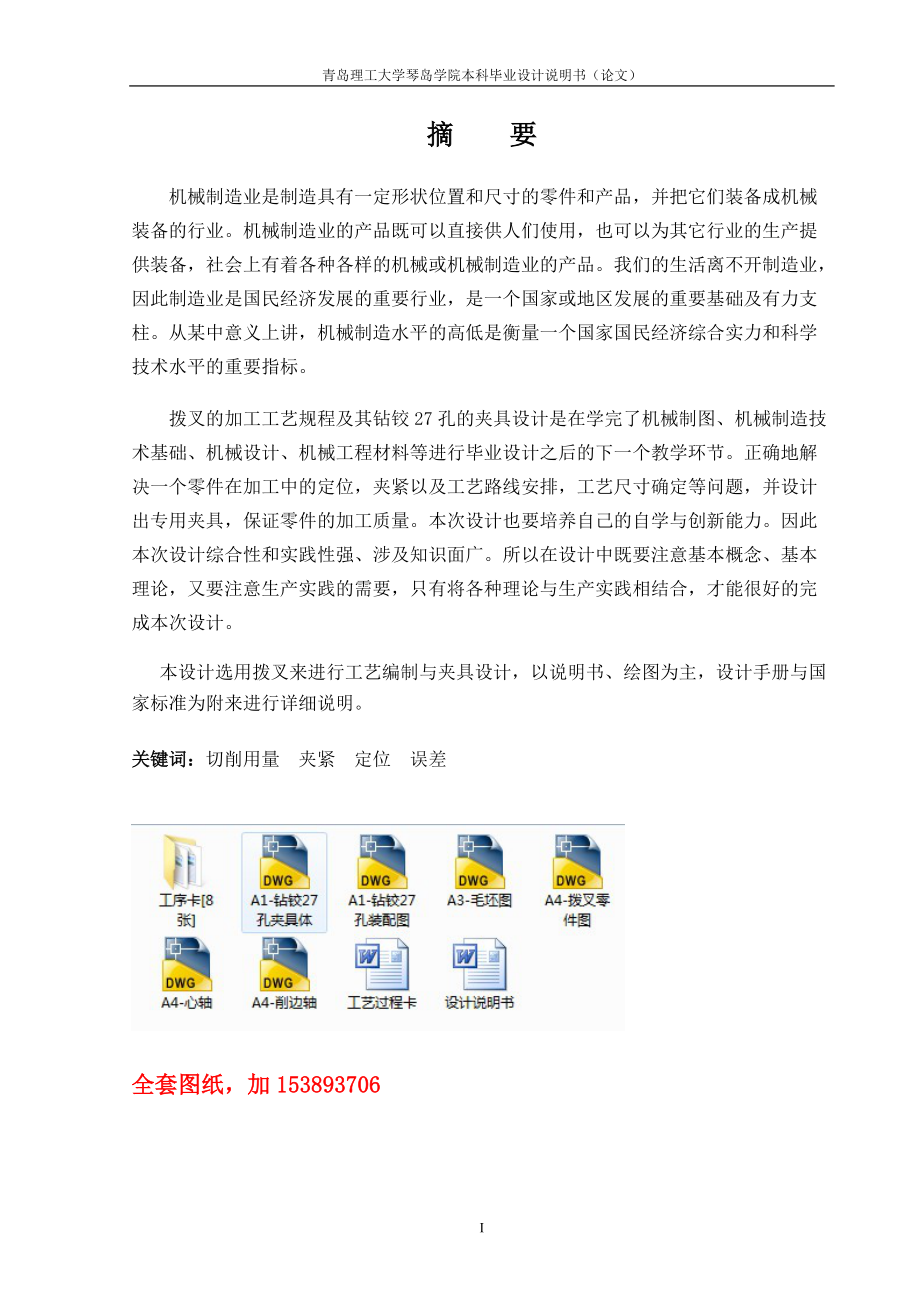


《机械制造技术课程设计拨叉的加工工艺规程及其钻铰27孔的夹具设计【全套图纸】》由会员分享,可在线阅读,更多相关《机械制造技术课程设计拨叉的加工工艺规程及其钻铰27孔的夹具设计【全套图纸】(39页珍藏版)》请在装配图网上搜索。
1、青岛理工大学琴岛学院本科毕业设计说明书(论文)摘 要机械制造业是制造具有一定形状位置和尺寸的零件和产品,并把它们装备成机械装备的行业。机械制造业的产品既可以直接供人们使用,也可以为其它行业的生产提供装备,社会上有着各种各样的机械或机械制造业的产品。我们的生活离不开制造业,因此制造业是国民经济发展的重要行业,是一个国家或地区发展的重要基础及有力支柱。从某中意义上讲,机械制造水平的高低是衡量一个国家国民经济综合实力和科学技术水平的重要指标。拨叉的加工工艺规程及其钻铰27孔的夹具设计是在学完了机械制图、机械制造技术基础、机械设计、机械工程材料等进行毕业设计之后的下一个教学环节。正确地解决一个零件在加
2、工中的定位,夹紧以及工艺路线安排,工艺尺寸确定等问题,并设计出专用夹具,保证零件的加工质量。本次设计也要培养自己的自学与创新能力。因此本次设计综合性和实践性强、涉及知识面广。所以在设计中既要注意基本概念、基本理论,又要注意生产实践的需要,只有将各种理论与生产实践相结合,才能很好的完成本次设计。本设计选用拨叉来进行工艺编制与夹具设计,以说明书、绘图为主,设计手册与国家标准为附来进行详细说明。关键词:切削用量 夹紧 定位 误差全套图纸,加153893706AbstractMachinery manufacturing industry is making a certain shape posit
3、ion and size of parts and products, equipment and put them into machinery and equipment industry. Machinery manufacturing products can be directly for the use, can also provide equipment for other sectors of social production, has a mechanical or mechanical manufacturing a variety of products. Our l
4、ife is inseparable from the manufacturing industry, the manufacturing industry is an important industry of national economic development, is the important base and backbone of the development of a country or region. In some sense, the level of manufacturing level is an important indicator to measure
5、 a countrys comprehensive economic strength and the level of science and technology.Fixture design process planning for fork and milling 2- 30 end, drilling, expansion, hinge 27H8 hole is teaching a link of graduation design in the studied mechanical drawing, mechanical manufacturing technology, mec
6、hanical design, mechanical engineering materials. A correct solution of a components in processing localization, clamping and the craft route arrangement, process dimensions are determined, and design a special fixture, spare parts processing quality assurance. This design is to develop self-study a
7、nd innovation ability of their own. Therefore, the design of integrated and practical, wide range of knowledge. So in the design should not only pay attention to the basic theory, basic concepts, but also pay attention to the production needs of the practice, only by combining the theory and product
8、ion practice, the completion of the design can be very gooThis design uses the fork to process planning and fixture design, mainly to the specification, drawing, design manual and the national standard for attachment to a detailed description of.Keywords: cutting clamping and positioning errorIII目 录
9、摘 要I1 概述发展11.1 机床夹具的主要功能11.2 机床夹具的组成11.3 夹具设计的步骤和基本要求12 零件的工艺设计132.1 零件的工艺设计132.2 工艺规程的设计133 加工设备与工艺装备的选择263.1 选择机床263.2 选择夹具264 零件钻床的夹具设计334.1 问题的提出334.2 定位基准的选择334.3 切削力与夹紧力的计算334.4 定位误差分析334.5 钻套的设计344.6 钻床夹具截图36结 论38致 谢39参考文献401概述发展1.1机床夹具的主要功能 机床夹具已成为机械加工时的重要装备,同时是机械加工不可缺少的部件,在机床技术向高速、高效、精密、复合、
10、智能、环保方向发展的带动下,夹具技术也正朝着高精、高效、模块、组合、通用 、经济方向发展。机床夹具的主要功能是使工件定位夹紧,使工件相对于刀具及机床占有正确的加工位置,保证其被加工表面达到工序所规定的技术要求,工件定位后,经夹紧装置施力于工件,将其固定夹牢,使其在加工过程中不致因切削力、重力、离心力等外力作用而发生位置改变。为了适应不同行业的需求和经济性,夹具有不同的型号,以及不同档次的精度标准供选择。安装方法有找正法和用专用夹具,找正法用于单件、小批生产中,而专用夹具用于生产批量较大或特殊需要时。1.2机床夹具的组成1、定位支承元件 确定工件在夹具中的正确位置并支承工件。2、夹紧装置 将工件
11、夹紧不发生移动。3、对刀或导向元件 保证刀具与工件加工表面的正确位置。4、夹具体 将夹具的所有组成部分组成一体,并保证它们之间的相对位置关系。1.3 夹具设计的步骤和基本要求1.3.1、夹具设计的基本要求夹具在机械加工中起着重要的作用,它直接影响机械加工的质量、工人的劳动强度、生产率和加工成本。因此对设计的夹具,提出以下几点基本要求。1、能稳定可靠地保证工件的加工技术要求。若工件达不到加工技术要求,成为废品,则夹具设计是失败的,该夹具不能用与生产。2、操作简单,便于工件安装,减轻工人的劳动强度,节省工件安装时间,降低辅助工时,保证高的生产效率。3、具有良好的工艺性,便于制造,降低夹具制造成本,
12、从而降低分摊在工件上的加工成本。为保证上述基本要求,夹具的生产过程应按下面程序进行:夹具生产任务书夹具的结构设计使用、制造部门会签夹具制造夹具验收生产使用。夹具生产任务书是由工艺人员在编制工艺规程时,根据生产需要而提出的。任务书中包含内容有设计理由、使用车间、使用设备,该夹具所使用工件工序的工序图并在工序图上要标明工序要求、加工表面、尺寸精度要求及定位定位基准、夹紧点。这是设计夹具的依据,也是验收制造夹具的依据。夹具结构设计是设计人根据夹具设计任务书的加工要求,提出几种可行方案、分析比较、进行误差计算,以确定出合理方案,进行设计。夹具结构设计完成后,要会同使用部门、制造部门就夹具的结构合理性、
13、结构工艺性和经济性进行审核、会签、交付制造。制成的夹具要同设计人员。工艺人员、使用部门、制造部门共同进行验证。当确认夹具可保证工件该工序加工要求,能保证生产率、操作方便、安全,就可交付生产车间使用。1.3.2夹具的设计步骤当接到夹具设计任务书后,按下面6个步骤,逐步设计。1、明确设计任务,收集研究设计的原始资料。原始资料包括如下内容。 A:加工零件的零件图、毛坯图及加工工艺过程,所设计夹具应有的工序图,并了解该工序所使用的设备、刀具、量具、其他辅具以及该工序的加工余量、切削用量、加工要求、生产节拍等参数。 B:了解零件的生产类型,就是决定夹具采用简单结构或复杂结构的依据。若属大批量生产,则力求
14、夹具结构完善、生产率高 或是单件小批量生产或急于应付生产,则夹具结构应简单,以便迅速制造交付使用。C:收集该夹具所用机床的资料,主要指与夹具连接部分的安装尺寸。如铣床夹具要安装在工作台上,要收集工作如大小,工作如T形槽及槽距,以及机床的技术参数。D:收集所使用刀具的资料如刀具的精度、安装方式、使用要求及技术条件等。E:收集国内外同类型夹具资料,吸收其中先进而又能结合本厂情况的合理部分。F:了解本厂制造夹具的能力和使用的条件,如夹具制造的条件及精度水平,有无压缩空气压值等。G:收集有关夹具部件的标准(包括国标、部标、企标、厂标),典型夹具结构图册等。2、确定夹具结构方案,绘制结构草图,其主要内容
15、如下。A:根据工件加工尺寸、要求和开关,确定工件的定位方式,选择或设计定位元件,计算定位误差。B:确定刀具的引导方式及引导元件(指钻夹具、镗夹具)。C:确定工件夹紧方式 ,选择或设计夹紧机构,计算夹紧力。D:确定其他装置(如分度装置、顶出装置)的结构型式。E:确定和设计其他结构,如铣床夹具与机床的连接装置、对刀装置。在确定夹具结构的各组成部分时,可提出几种不同方案,分别画出草图,进行分析比较,从中选择出合理方案。3、绘制夹具总图。应注意以下几点。A:绘制夹具总图,尽量按1:1绘制,以保证直观性。B:主视图尽量符合操作者的正面位置。C:工件轮廓用双点画线绘制,并视为假想透明体,不影响其他元件的绘
16、制。 D:绘图顺序为:工件定位元件引导元件夹紧装置其他装置夹具体。4、标注总图上的尺寸、公差与配合和技术条件。夹具总图结构绘制完成后,需标注五类尺寸和四类技术条件。5、编写零件明细表。明细表应包括零件序号、名称、代号(指标准件代号或通用件代号 )、数量、材料、热处理、质量等。6、绘制总图中非标准件的零件图。1.3.3夹具总图上尺寸、公差与配合和技术条件的标注在夹具设计中,对于初设计者,在夹具总图上如何标注尺寸及技术条件,往往是难点之一,以下对此作简要阐述。1、夹具总图上应标注的五类尺寸A:夹具外形轮廓尺寸指夹具在长、宽、高三个方向上的最大极限尺寸。若有可动部分,则指运动部件在空间达到的极限位置
17、的尺寸。标注夹具外形尺寸的目的是避免夹具与机床或刀具在空间发生干涉。B:工件与定位元件间的联系尺寸主要指工件定位面与定位元件工作面的配合尺寸或各定位元件的位置尺寸,它们直接影响工件加工精度,是计算工件定位误差的依据。C:夹具与刀具的联系尺寸主要指对刀元件或引导元件与夹具定位元件之间的位置尺寸、引导元件之间的位置尺寸或引导与导向部分的配合尺寸。D:夹具与机床的连接部分尺寸这类尺寸主要指夹具与机床主轴或工作如必须固定连接的平俱。如车床夹具要安装在车床主轴上,要标注与车床主轴的连接尺寸,铣床夹具要安装在工作台上,要标注与工作如T形槽相配的定位键尺寸。E:夹具内容的配合尺寸中心轴与夹具体孔的配合尺寸,
18、钻套与衬套、衬套与夹具体的配合尺寸,此类尺寸必须标注尺寸、配合性质及配合精度,否则夹具精度无法保证。2、 夹具总图上应标注的四类技术条件夹具中的技术条件主要指夹具装配好后,各表面之间的位置精度要求。A:定位元件之间的相互位置要求这是指组合定位时多个定位元件之间的相互位置要求或多件装夹时相同定位元件之间的相互位置要求。如两端顶尖顶轴两端中心孔,要求两顶尖轴线同轴度,两V形块对称线的同轴度。B:定位元件与连接元件或夹具体底面的相位置要求夹具的连接元件或夹具体底面是夹具与机床的连接部分,它决定了夹具与机床的相对位置,也就是决定了定位元件相对机床,或刀具的位置,即决定了工件相对机床或刀具的位置。C:引
19、导元件与连接元件或夹具体底面的位置要求D:引导元件与定位元件之间的相互位置要求3、五类尺寸、四类技术条件的分类五类尺寸、四类技术条件根据是否与工序加工要求相关而分为两类,其精度值大小和取法不同。A:与工件加工要求无直接关系的 尺寸公差与配合 这类尺寸公差与配合应按照元件在夹具中的功用和装配要求,根据公差与配合国家标准或参阅有关资料来制定。 技术条件 与工件加工要求无直接关系的夹具上技术条件。B: 与加工要求直接相关的 这类尺寸和技术条件与工件上相应尺寸和技术条件直接对应,直接根据工件相应尺寸公差和相互位置允差的(1/51/2)的值选取。一般工件允差小,取大系数,工件允差大,则取小系数。制定这类
20、夹具尺寸公差时,要注意下列问题。 应经工件的平均尺寸作为夹具相应尺寸的基本尺寸,极限偏差按对称双向标注。 应以工序尺寸(不一定是工件最终尺寸)作为夹具基本尺寸的设计依据。4、夹具调刀尺寸的标注当夹具设计完成,按要求标注尺寸后,对有些夹具如铣夹具,往往还要标注调刀尺寸(调刀尺寸一般是指夹具的调刀基准到对刀元件工作表面的位置尺寸),即刀具相对基准的尺寸,它与工件加工尺寸直接相关,也是夹具总图上关键尺寸要求。1.3.4夹具体设计夹具总体设计中最后完成的主要元件是夹具体。夹具体是夹具基础件、组成夹具的各种元件、机构、装置都要安装在夹具体上。在加工过程中,它还要承受切削力、夹紧、惯性力及由此而产生的振动
21、和冲击。所以,夹具体是夹具中一个设计、制造劳动量大,耗费材料多,加工要求高的零部件。在夹具成本中所占比重较大,制造周期也长,设计时,应给以足够的重视。1、 夹具体和毛坯结构实际生产中所用夹具体常用的有三种结构。A:铸造结构铸造结构夹具体的优点如下: 可铸出复杂的结构形状。 铸件抗压强度大、抗振性好,特别适用于加工时振动大、切削负荷大的场合。 铸件易于加工,价格低廉,成本低。但铸件生产周期长,因存在铸内应力,易引起变形,影响夹具精度的保持性,因此,夹具体必须进行时效处理。B:焊接结构其优点如下: 容易制造,周期短。 采用钢板、型材,如结构合理,布置得当,可减小质量。由于上述两优点,特别适用于新产
22、品试制或临时急用的场合,以缩短生产周期。此外,一些结构简单的小型夹具,如翻转式钻模、盖板式钻模、可缷式钻模,采用焊接式结构十分有利,因为这些夹具要频繁拆缷翻转,力求结构轻巧耐磨。但焊接结构夹具体在焊接过程中的热变形和残余应力对夹具精度会有不得影响,因此,焊完后要进行退火处理;另外,为提高刚性需加加强筋。C:装配结构装配夹具体是选用夹具专用标准毛坯或标准零件,根据使用要求组装而成,可得到精确的外形和空间位置尺寸。标准毛坯和标准零件可组织专业化生产,这样不但可以大大缩短夹具体的生产周期,还可降低生产成本。要使装配夹具体在生产中得到广泛使用,必须实行夹具零部件的标准化、系列化。2、对夹具体的基本要求
23、A:一定的形状和尺寸夹具的外形,取决于安装在夹具上的各种元件、机构、装置的形状及它们之间的布置位置。设计时,只要将组成该夹具的所有元件、机构和装置的结构尺寸都设计好并布置好它们在图纸上的位置,就可以由此勾画出夹具体的大致外形轮廓尺寸。因为是单件生产,一般不作复杂计算设计。通常参照类似的夹具结构,按经验类比法估计确定。确定夹具体尺寸时,可参考下面数据。 铸造结构的夹具体,壁厚取825mm,过厚处挖空。 焊接结构用钢板取610mm,刚度不够时加筋板。 夹具体上不加工表面与工件表面之间应有一定间隙,以保证工件与夹具体之间不发生干涉。间隙大小按以下规定选取:a:夹具体、工件都是毛面,间隙取815mm.
24、b:夹具体是毛面,工件是光面,间隙取410mm.B:足够的强度和刚度目的是减小在加工过程中因受切削力、夹紧力等而发生变形或振动。当刚度不够时,可增设加强筋或用框形结构。若用加强筋,其壁厚取0.70.9倍壁厚,高度不大于壁厚5倍。C:良好的结构工艺性以便于制造、装配、并减少加工工时。如夹具体上大平面上要局部加工,可铸出35mm凸台;各加工表面,最好在同一平面内或在同一回转表面上,以便于加工;尽量减少加工表面面积。另外,对于切削量大的工件所使用夹具,要注意应能方便排屑,以免影响安装精度;对于大而重的夹具体,要考虑起吊装置,如吊环螺钉或起重螺栓。1.1.4铣床夹具简介铣床夹具主要用于加工零件上的平面
25、、凹槽、花键及各种成型面,是最常用的夹具之一,铣削时切削用量较大,且为断续切削,故切削力较大,冲击和振动也较严重,因此设计铣床夹具时,应注意工件的装夹具在工作台上的安装平稳性。按铣削时的进给方式,可将铣床夹具分为直线进给式、圆周进给式和靠模进给式三种。1、直线进给铣床夹具这类夹具安装在铣床工作台上,加工中随工作台按直线进给方式运动。直线进给式铣床夹具的结构特点如下:、 定位键为了确定夹具与机床工作台的相对位置,在夹具体的底面上应设置定位键,两定位键,用沉头螺钉固定在夹具体底面纵向槽的两端,通过定位键与铣床工作台上的T形槽配合,确定了夹具在机床上的正确位置。两定位键间的距离越大,定位精度越高。除
26、定位之外,定位键还能承受部分切削扭矩,减轻夹具固定螺栓的负荷,增加夹具的稳定性。、 对刀元件对刀元件是用来确定刀具与夹具的相对位置的元件,常见的标准对刀块有:圆形对刀块,用于加工单一平面时对刀;方形对刀块,用于调整组合铣刀位置是对刀;直角对刀块,用于加工两互相垂直面或铣槽时对刀;侧装对刀块,它安装在夹具体侧面,用于加工两相互垂直面或铣槽时对刀。具体结构尺寸可参阅“夹具手册”。对刀时,铣刀不能与对刀块的工作表面直接接触,以免损坏切削刃或造成对刀块过早磨损,则应通过塞尺来校准它们之间的相对位置,即将塞尺放在刀具与结刀块工作表面之间,凭借抽动塞尺的松紧感觉来判断铣刀的位置。、 夹具体的设计由于铣削时
27、的切削力和振动较大,因此,铣床夹具的夹具体不仅要有足够的刚度和强度,其高度与宽度之比也应恰当,一般为H/B小于或等你1.25,以降低夹具的重心,使工件的加工表面尽量靠近工作台面,提高加工时夹具的稳定性。为了提高生产率,减轻工人的劳动强度,铣床夹具经常采用联动夹紧机构和铰链夹紧机构。2、 圆周进给铣床夹具圆周时给铣床夹具多用在有回转工作台或回转鼓轮的铣床上,依靠回转台或鼓轮的旋转将工件顺序送入铣床的加工区域,以实现连续切削。在切削的同时,可在装缷区域装缷工件,使辅助时间与机动时间重合,因此它是一种高效率的铣床夹具。设计圆周铣床夹具时应注意下列问题: 、沿圆周排列的工件应尽量紧凑,以减少铣刀的空行
28、程和转台(或鼓轮)的尺寸。 、尺寸较大的夹具不宜制成整体式,可将定位、夹紧元件或装置直接安装在转台上。 、夹紧用手柄、螺母等元件,最好沿转台外沿分布,以便操作。 、应设计合适的工作拍,以减轻工件的劳动强度,并注意安全。3、 靠模铣床夹具带有靠模的铣床夹具称为靠模铣床夹具,用于专用或通用铣床上加工各种非圆曲面。靠模的作用是使工件获得辅助运动。按照主进给运动的运动方式,靠模铣床夹具可分为直线进给和圆周进给两种。靠模板轮廓曲线的设计方法:、 画出工件的准确外形。、 从工件的加工轮廓面或回转中心作均匀的平行线或辐射线。、 在每条平行线或辐射线上,以铣刀半径r作与工件外形轮廓相切的圆,连接各圆心,即得到
29、铣刀中心的运动轨迹。、 从铣刀中心沿各平行线或辐射线截取长度等于线段,得到滚轮中心的运动轨迹。、 从滚轮中心为圆心,滚轮半径R为半径画圆,再作这些圆的内包络线,即得到靠模板的轮廓曲线。铣刀的半径应等于或小于工件轮廓的最小曲率半径,滚柱直径应等于或略大于铣刀直径。为防止滚柱和靠模板磨损后或铣刀刃磨后影响工件的轮廓尺寸,通常将靠模和滚柱作成1015的斜角,以便调整。1.1.5钻床夹具简介钻床夹具,一般习惯上称为钻模。它是在钻床上进行孔的钻、扩、铰、锪、攻螺纹的机床夹具。使用钻模加工时,是借助于钻套确定刀具的位置和引导刀具的进给方向。被加工孔的尺寸精度主要是由刀具本身的精度来保证。而孔的坐标位置精度
30、,则由钻套在夹具上的位置精度来确定,并能防止刀具在加工过程中发生倾斜。因此,在结构上都设置安装钻套的钻模板。一:钻模钻模的结构形式很多,有固定式、分度式、盖板式、翻转式和滑柱式等主要类型地。(1) 固定式钻模:工件在钻床上进行加工的整个过程中位置都不移动的夹具称为固定式钻模。这类钻模在加工孔系工件时一般用在摇臂钻床及多轴钻床上。若用在立式钻床上时,则只能进行单个孔的加工。使用此类夹具时,必须借助于刀具(或心轴),使它准确地置于套筒中,以校正夹具的位置,然后将其坚固。这类加工方式的钻孔精度较高。但装卸麻烦,效率很低。(2) 分度式钻模:分度式钻模主要用来加工围绕一定的回转轴线(立轴、卧轴、倾斜轴
31、)分布的轴向或径向孔系,或分布在工件几个不同表面上的孔。工件在一次装夹中,靠钻模回转依次加工各孔。因此,这类钻模必须有分度装置。广泛用于各类机床夹具上的分度装置分为两类,一类为直线分度装置;另一类为回转分度装置。回转分度装置又根据回转轴相对于夹具体安装基面的位置分为立式分度、卧式分度及斜式分度三种。1、 分度装置的组成分度装置一般由以下几个部分组成。A:转动(或移动)部分 它实现工件的转位(或移位)。B:固定部分 它是分度装置的基体,常与夹具体连接成一体。C:对定机构 它将转动(或移动)部分与固定部分紧固在一起,起减小加工时的振动和保护对定机构的作用。2、 分度对定机构分度对定机构的结构型式很
32、多,常见的有钢球对定机构,结构简单,操作方便,常用于精度不高的场合,或作预定位;手拉式菱形销(或圆柱销)对定机构。具有操纵简便,制造较容易,不需要严格防尘措施等优点。这两种结构在中等精度的分度装置中应用较广;齿轮齿条操纵的圆锥销对定机构,其分度对定精度较高,但要求有防尘措施;杠杆操纵单斜面对定机构,对防尘要求不高,而分度精度较高,故使用较多。(3) 盖板式钻模:盖板式钻模是最简单的一种钻模。它没有夹具体,只有一块钻模板。在一般情况下,钻模板除了装钻套外,还装有定位元件和夹紧装置,加工时,只要将它盖在工件上定位,夹紧即可。盖板式钻模结构简单轻巧,一般多用于加工大型工件上的小孔。但生产效率低,故不
33、适宜于大批量生产。因使用时需经常搬动,故其质量一般不超过10Kg.(4) 翻转式钻模:在使用过程中,需要用手进行翻转。因此,夹具连同工件的质量不能太大(一般限于810Kg以内)。所以,它适合在几个方向钻孔的小型工件加工。(5) 滑柱式钻模:滑柱式钻模的结构已标准化和规格化的夹具。这种钻模应属于通用夹具范畴。它可以是固定式的、移动式的或转动式的。滑柱钻模通常是由夹具体、滑柱、升降模板和锁紧机构等同部分组成。当要设计或选用此类夹具时可直接采用标准预制造好的各部件进行组装。滑柱钻模具有动作快、工作方便、各大附件互换性强、设计夹具及生产准备周期短等特点,非常适用于批量大的生产过程,目前变推广到小批的生
34、产中。 二:钻套钻套(又称钻模套筒)的作用,主要用来确定钻头、扩孔钻、铰刀等定尺寸刀具的轴线位置。当加工一组平行的孔系,而这些孔间的距离又有一定的要求时,则利用位置按加工要求的钻套来保证上述孔心距离的数度,简便可靠。当工件批量很小、孔间距离很小、孔径很小或者钻模板上位置受限制而无法采用钻套时,也允许在钻模板上直接加工出导引道具的导孔。(1) 钻套类型 钻套的结构和尺寸已标准化。根据使用特点,钻套有下列四种型式。 固定钻套(JB/T8045.1-1999)主要用于小批生产条件下单纯用钻头钻孔的工序。固定钻套是直接装在钻模板的相应孔中,因此固定钻套磨损后不能更换。固定钻套有两种结构:无肩的和带肩的
35、。带肩的主要用于钻模板较薄时,用以保持钻套必须得导引长度。有了肩部,还可以防止钻模板上的切屑和冷却液落入钻套孔中。固定钻套的下端应超出钻模板,以防止带状切屑卷入钻套中而加剧钻套的磨损。可换钻套(JB/T8045.2-1999)为了克服固定钻套磨损后无法更换的缺点,因此便有可换钻套结构,标准可换钻套结构的凸缘上铣有台肩,钻套螺钉的台阶形头部压紧在此台肩上而防止可换钻套转动。拧去螺钉,便可取出可换钻套。采用可换钻套的钻模板,在安装可换钻套处应专门配装一个衬套,可换钻套就装在衬套中。这样便可避免更换钻套时损坏钻模板。钻套用衬套的结构和尺寸也已标准化,可换钻套的实际功用仍和固定钻套一样,仅供单纯钻孔的
36、工序用。可换钻套是用在批量较大时,便于钻套磨损后,可以迅速更换。快速钻套(JB/T8045.3-1999)快速钻套是供同一个孔须经多种加工工步(如钻、扩、铰、)所用的。由于在加工过程中须一次更换或取出钻套以适应不同加工刀具的需要,所以需用这种快换钻套。标准块换钻套的结构除在其凸缘铣有台肩以供钻套螺钉压紧外,同时还铣出一削边平面。当此削边平面转至钻套螺钉时,便可向上快速取出钻套。为了防止直接磨损钻模板,在采用快换钻套时,钻模板上必须配有钻套用衬套。布置快换钻套时,必须注意快换钻套的台肩位置应与刀具在加工时的旋转方向相适应,防止钻套因受刀具或切削的摩擦作用而转动时,使钻套台肩面转出钻套螺钉而被向上
37、抬起。特殊钻套:因工件的形状或被加工孔的位置需要而不能使用标准钻套时,需自行设计的钻套称特殊钻套。加长钻套,在加工凹面上的孔时使用,为减少刀具与钻套的摩擦,可将钻套引导高度H以上的孔径放大。斜面或圆弧面上钻孔,排屑空间的高度h0.5mm,可增加钻头刚度,避免钻头引偏或折断。小孔距钻套,用定位销确定钻套位置,兼有定位与夹紧功能的钻套,钻套与衬套之间一段为圆柱间隙配合,一段为螺纹连接,钻套下端为圆锥面,具有对工件定位、夹紧和引导刀具三种功能。(2)钻套的尺寸、公差及材料在选用标准结构的钻套时,钻套导引孔的尺寸与公差须有设计者决定,其余结构尺寸则在标准中都已规定。这时,可按下述原则来确定导引孔的尺寸
38、与公差带。A:钻套导引孔直径的基本尺寸,应等于所导引刀具的最大极限尺寸。B:因为由钻套导引的刀具,都是钻头、扩孔钻、铰刀等定尺寸的刀具,其结构和尺寸都已标准化和规格化,所以钻套导引孔与刀具的配合,应按基轴制来选定。C:钻套导引孔与刀具之间,应保证有一定的配合间隙,以防止两者发生卡住或咬死。一般根据所导引的刀具和加工精度要求来选取导引孔的公差带:钻孔和扩大时选用F7,粗铰时选用G7,精铰时选用G6.D:当采用标准铰刀铰H7或H9孔时,则可不必按刀具最大尺寸来计算。直接按孔的基本尺寸,分别选用F7或E7,作为导引孔的基本尺寸与公差带。E:由于标准钻头的最大尺寸都是所加工孔的基本尺寸,故钻头的导引就
39、只须按孔的基本尺寸取公差带为F7即可。F:如果钻套导引的不是刀具的切削部分,而是刀具的导柱部分,这时也可以按基孔制的相应配合选取为:H7/f7、H7/g6、H6/g5。三:钻模板钻模板用于安装钻套,并确保钻套在钻模上的正确位置。常见的钻模板有以下几种。(1) 固定式钻模板 固定在夹具体上的钻模板称为固定式钻模板。钻模板与夹具体铸成一体或用螺钉和销钉连接的钻模板,这种钻模板可在装配时调整位置,因而使用广泛。固定式钻模板结构简单、钻孔精度高。(2) 铰链式钻模板 当钻模板妨碍工件装缷或钻孔后需要攻螺纹时,可采用铰链式钻模板。铰链销与钻模板的销孔采用G7/h6配合,与铰链座的销孔采用N7/h6配合。
40、钻模板与铰链座之间采用H8/g7配合。钻套导向孔与夹具安装面的垂直度可通过调整两个支承钉的高度加以保证。加工时,钻模板由菱形螺母锁紧,由于铰链销孔之间存在配合间隙,用此类钻模板加工的工件精度比固定式钻模板低。(3) 可缷式钻模板 气动可调式钻模上,采用了可缷钻模反,工件先在可更换预定元件上预定位,可缷钻模板与工件止口配合实现五点定位,夹紧气缸的活塞杆通过开口垫圈将可缷钻模板与工件一起压紧。这类钻模板的定位精度高,可与工件一起装缷。352零件的工艺设计2.1 零件的工艺设计2.1.1 零件的功用题目所给的零件是拨叉,机械中的拨叉,一般分为拨叉爪子,拨叉轴和拨叉手柄座。主要是拨动滑移齿轮,改变其在
41、齿轮轴上的位置,可以上下移动或左右移动,从而实现不同的速度。或则是机械产品中离合器的控制,比如端面结合齿的结构,内外齿的结构,都需要用拨叉控制其一部分来实现结合与分离。还有一种是机械产品中电器的控制也是需要拨叉来实现开关的闭合与断开,一般是电器盒中两边各一个碰卡开关,拨叉左右或上下拨动,从而实现机床不同方向的运转。2.1.2 工艺分析从拨叉零件图可以看出,它有七组加工表面,现分述如下:、工件底面(即2-30下端面与54下端面)、工件顶面(即2-30上端面)、15H7孔、54顶面、宽44两侧面、27H8孔、5孔、拨叉叉口面2.2 工艺规程的设计2.2.1 确定毛坯的制造形式零件材料为HT200,
42、零件成批生产,而且零件的轮廓尺寸不大,选用砂型铸造,采用机械翻砂造型,铸造精度为7级,加工余量等级MA-D,能保证铸件的尺寸要求,这从提高生产率和保证加工精度上考虑也是符合要求的。2.2.2 基准的选择1、精基准的选择选择精基准时要考虑的主要问题是如何保证设计技术要求的实现以及装夹准确、可靠、方便。 用设计基准作为定位基准,实现“基准重合”,以免产生基准不重合误差。 当工件以某一组精基准定位可以较方便地加工很多表面时,应尽可能采用此组精基准定位,实现“基准统一”,以免生产基准转换误差。 当精加工或光整加工工序要求加工余量尽量小而均匀时,应选择加工表面本身作为精基准,即遵循“自为基准”原则。该加
43、工表面与其他表面间的位置精度要求由先行工序保证。 为获得均匀的加工余量或较高 的位置精度,可遵循“互为基准”、反复加工的原则。 有多种方案可供选择时应选择定位准确、稳定、夹紧可靠,可使夹具结构简单的表面作为精基准。根据拨叉零件的技术要求和装配要求,选择拨叉的2-15H7mm孔及其下端面作为定位精基准,零件上有许多表面都可以采用它作为基准进行加工,即遵循“基准统一”原则。2、粗基准的选择 如果必须首先保证工件上加工表面与不加工表面 之间的位置要求,应以不加工表面作为粗基准。如果在工件上有很多不需加工的表面,则应以其中与加工面位置精度要求较高的表面作粗基准。 如果必须首先保证工件某重要表面的加工余
44、量均匀,应选择该表面作精基准。 如需保证各加工表面都有足够的加工余量,应选加工余量较小的表面作粗基准。 选作粗基准的表面应平整,没有浇口、冒口、飞边等缺陷,以便定位可靠。 粗基准一般只能使用一次,特别是主要定位基准,以免产生较大的位置误差。此设计选择30外圆面及其上端面作为定位粗基准准。2.2.3 制定工艺路线制订工艺路线的出发点,应当是使零件的几何形状、尺寸精度及位置精度等技术要求能得到合理的保证。在生产纲领已确定为成批生产的条件下,可以考虑采用万能型机床配以专用夹具,并尽量使工序集中在提高生产率。除此以外,还应当考虑经济效果,以便使生产成本尽量降下来。工艺路线一:工序01:铸造工序02:人
45、工时效工序03:粗铣、精铣工件底面(即2-30下端面与54下端面)工序04:铣工件顶面(即2-30上端面)工序05:钻孔至14;扩14孔至14.8;铰14.8孔至15H7工序06:粗铣、精铣54顶面工序07:铣宽44两侧面工序08:钻孔至24;扩24孔至26.8;铰26.8孔至27H8工序09:配钻孔至4.8;铰4.8孔至5工序10:铣断工序11:清洗去毛刺工序12:检验至图纸要求工序13:入库工艺路线二:工序01:铸造工序02:人工时效工序03:粗铣、精铣工件底面(即30下端面与54下端面)工序04:铣工件顶面(即30上端面)工序05:钻孔至14;扩14孔至14.8;铰14.8孔至15H7工
46、序06:粗铣、精铣54顶面工序07:铣宽44两侧面工序08:钻孔至24;扩24孔至26.8;铰26.8孔至27H8工序09:配钻孔至4.8;铰4.8孔至5工序10:清洗去毛刺工序11:检验至图纸要求工序12:入库工艺路线比较,方案一与方案二的区别在于,方案一,一次加工同时生产两件,而方案二则是生产一件,精度都可以保证,零件的生产纲领为30000件,属于大批量生产,故我们采用方案一。2.2.4 机械加工余量、工序尺寸及毛坯尺寸的确定 1. 工件底面(即2-30下端面与54下端面)的加工余量已知铸件尺寸公差为CT7级,加工余量为MA-D级,查机械制造工艺设计简明手册表2.2-4得,铸件的单边加工余
47、量Z=1.0mm,粗糙度Ra=3.2,查机械制造工艺设计简明手册表1.4-8知,需经过粗铣精铣方可满足其精度要求。粗铣 单边余量Z=0.8mm精铣 单边余量Z=0.2mm2. 工件顶面(即2-30上端面)的加工余量已知铸件尺寸公差为CT7级,加工余量为MA-D级,查机械制造工艺设计简明手册表2.2-4得,铸件的单边加工余量Z=1.0mm,粗糙度Ra=12.5,查机械制造工艺设计简明手册表1.4-8知,一步铣削即可满足其精度要求。3. 15H7孔的加工余量因孔的尺寸小于30,故采用实心铸造,而孔精度等级为7级,查机械制造工艺设计简明手册表2.3-8知,首先钻14孔,再扩14孔至14.8,最后铰1
48、4.8孔至15H7即可满足其精度要求。4. 54顶面的加工余量已知铸件尺寸公差为CT7级,加工余量为MA-D级,查机械制造工艺设计简明手册表2.2-4得,铸件的单边加工余量Z=1.0mm,粗糙度Ra=3.2,查机械制造工艺设计简明手册表1.4-8知,需经过粗铣精铣方可满足其精度要求。粗铣 单边余量Z=0.8mm精铣 单边余量Z=0.2mm5. 宽44两侧面的加工余量已知铸件尺寸公差为CT7级,加工余量为MA-D级,直接铸造成圆形,粗糙度Ra=12.5,查机械制造工艺设计简明手册表1.4-8知,一步铣削即可满足其精度要求。 6. 27H8孔的加工余量因孔的尺寸小于30,故采用实心铸造,而孔精度等
49、级为8级,查机械制造工艺设计简明手册表2.3-8知,首先钻24孔,再扩24孔至26.8,最后铰26.8孔至27H8即可满足其精度要求。 7. 5孔的加工余量因孔的尺寸小于30,故采用实心铸造,孔的粗糙度Ra=0.8,查机械制造工艺设计简明手册表1.4-7知,需经过钻铰方可满足其精度要求,即首先钻孔至4、再铰4孔至5。8. 拨叉叉口面的加工余量因是两件同时加工,拨叉叉口面不留余量。 9. 其它不加工表面,铸造即可满足其精度要求。2.2.5 确定切削用量及基准工时工序01:铸造工序02:人工时效工序03:粗铣、精铣工件底面(即2-30下端面与54下端面)工步一:粗铣工件底面(即2-30下端面与54
50、下端面)1. 选择刀具刀具选取端面铣刀,。2. 决定铣削用量1)决定铣削深度2) 决定每次进给量及切削速度 根据X52K型立式铣床说明书,其功率为为7.5kw,中等系统刚度。根据表查出 ,则按机床标准选取500当500r/min时按机床标准选取3)计算工时切削工时: ,则机动工时为工步二:精铣工件底面(即2-30下端面与54下端面)1. 选择刀具刀具选取端面铣刀,。2. 决定铣削用量1)决定铣削深度2) 决定每次进给量及切削速度 根据X52K型立式铣床说明书,其功率为为7.5kw,中等系统刚度。根据表查出 ,则按机床标准选取800当800r/min时按机床标准选取3)计算工时切削工时: ,则机
51、动工时为工序04:铣工件顶面(即2-30上端面)1. 选择刀具刀具选取端面铣刀,。2. 决定铣削用量1)决定铣削深度2) 决定每次进给量及切削速度 根据X52K型立式铣床说明书,其功率为为7.5kw,中等系统刚度。根据表查出 ,则按机床标准选取500当500r/min时按机床标准选取3)计算工时切削工时: ,则机动工时为工序05:钻孔至14;扩14孔至14.8;铰14.8孔至15H7工步一:钻孔至14确定进给量:根据参考文献表2-7,当钢的,时,。由于本零件在加工14孔时属于低刚度零件,故进给量应乘以系数0.75,则根据Z525机床说明书,现取切削速度:根据参考文献表2-13及表2-14,查得
52、切削速度所以 根据机床说明书,取,故实际切削速度为切削工时:,则机动工时为工步二:扩14孔至14.8利用钻头将孔扩大至,根据有关手册规定,扩钻的切削用量可根据钻孔的切削用量选取根据机床说明书,选取则主轴转速为,并按车床说明书取,实际切削速度为切削工时:,则机动工时为工步三:铰14.8孔至15H7根据参考文献表2-25,得查参考文献表4.2-2,按机床实际进给量和实际转速,取,实际切削速度。切削工时:,则机动工时为工序06:粗铣、精铣54顶面工步一:粗铣54顶面1. 选择刀具刀具选取端面铣刀,。2. 决定铣削用量1)决定铣削深度2) 决定每次进给量及切削速度 根据X52K型立式铣床说明书,其功率
53、为为7.5kw,中等系统刚度。根据表查出 ,则按机床标准选取500当500r/min时按机床标准选取3)计算工时切削工时: ,则机动工时为工步二:精铣54顶面1. 选择刀具刀具选取端面铣刀,。2. 决定铣削用量1)决定铣削深度2) 决定每次进给量及切削速度 根据X52K型立式铣床说明书,其功率为为7.5kw,中等系统刚度。根据表查出 ,则按机床标准选取800当800r/min时按机床标准选取3)计算工时切削工时: ,则机动工时为工序07:铣宽44两侧面1.选择刀具刀具选取立铣刀,刀片采用YG8,,。2. 决定铣削用量1) 决定铣削深度2) 决定每次进给量及切削速度 根据X52K型立铣床说明书,
54、其功率为为7.5kw,中等系统刚度。根据表查出 ,则按机床标准选取800当800r/min时按机床标准选取3) 计算工时切削工时: ,则机动工时为工序08:钻孔至24;扩24孔至26.8;铰26.8孔至27H8工步一:钻孔至24确定进给量:根据参考文献表2-7,当钢的,时,。由于本零件在加工24孔时属于低刚度零件,故进给量应乘以系数0.75,则根据Z525机床说明书,现取切削速度:根据参考文献表2-13及表2-14,查得切削速度所以 根据机床说明书,取,故实际切削速度为切削工时:,则机动工时为工步二:扩24孔至26.8利用钻头将孔扩大至,根据有关手册规定,扩钻的切削用量可根据钻孔的切削用量选取
55、根据机床说明书,选取则主轴转速为,并按车床说明书取,实际切削速度为切削工时:,则机动工时为工步三:铰26.8孔至27H8根据参考文献表2-25,得查参考文献表4.2-2,按机床实际进给量和实际转速,取,实际切削速度。切削工时:,则机动工时为工序09:配钻孔至4.8;铰4.8孔至5工步一:配钻孔至4.8确定进给量:根据参考文献表2-7,当钢的,时,。由于本零件在加工4.8孔时属于低刚度零件,故进给量应乘以系数0.75,则根据Z525机床说明书,现取切削速度:根据参考文献表2-13及表2-14,查得切削速度所以 根据机床说明书,取,故实际切削速度为切削工时:,则机动工时为工步二:铰4.8孔至5根据
56、参考文献表2-25,得查参考文献表4.2-2,按机床实际进给量和实际转速,取,实际切削速度。切削工时:,则机动工时为工序10:铣断1. 选择刀具刀具选取锯片铣刀,刀片采用YG8,,。2. 决定铣削用量1)决定铣削深度2)决定每次进给量及切削速度 根据X62W型卧式铣床说明书,其功率为为7.5kw,中等系统刚度。根据表查出 ,则按机床标准选取600当600r/min时按机床标准选取3)计算工时切削工时: ,则机动工时为工序11:清洗去毛刺工序12:检验至图纸要求工序13:入库3加工设备与工艺装备的选择3.1 选择机床1、粗铣、精铣工件底面(即2-30下端面与54下端面),机床选择X52K立式铣床
57、,刀具选择60端铣刀,量具:选择游标卡尺,辅具有塞尺、对刀块。2、铣工件顶面(即2-30上端面),机床选择X52K立式铣床,刀具选择60端铣刀,量具:选择游标卡尺,辅具有塞尺、对刀块。3、钻孔至14;扩14孔至14.8;铰14.8孔至15H7,机床选择Z525立式钻床,刀具选择14麻花钻、14.8扩孔钻,15铰刀,量具:选择游标卡尺。4、粗铣、精铣54顶面,机床选择X52K立式铣床,刀具选择60端铣刀,量具:选择游标卡尺,辅具有塞尺、对刀块。5、铣宽44两侧面,机床选择X52K立式铣床,刀具选择立铣刀,量具:选择游标卡尺,辅具:有塞尺、对刀块。6、钻孔至24;扩24孔至26.8;铰26.8孔至
58、27H8,机床选择Z525立式钻床,刀具选择24麻花钻、26.8扩孔钻,27铰刀,量具:选择游标卡尺。7、配钻孔至4.8;铰4.8孔至5,机床选择Z525立式钻床,刀具选择4.8麻花钻,5铰刀,量具:选择游标卡尺。8、铣断,机床选择X62W卧式铣床,刀具选择铣刀,量具:选择游标卡尺,辅具:有塞尺、对刀块。3.2 选择夹具对于成批生产的零件,大多采用专用机床夹具。在保证加工质量、操作方便、满足高效的前提下,亦可部分采用通用夹具。本加工工艺规程中,所用夹具均为专用夹具,需专门设计、制造。4零件的钻床夹具设计4.1 问题的提出本夹具主要用于钻孔至24;扩24孔至26.8;铰26.8孔至27H8,精度
59、等级为8级,与15H7孔中心线距离为120,表面粗糙度Ra=3.2,设计夹具时这些都要考虑在内。4.2 定位基准的选择选择15H7孔及其下端面作为定位基准1.夹具体的凸台面与工件底面(即15H7孔下端面)配合限制三个自由度。2.心轴与工件左端15H7孔配合限制两个自由度。3.削边轴与右端15H7孔配合限制一个自由度。4.工件的导向则是由钻模来实现,钻模由支座,钻模板、螺钉、圆柱销、快换钻套、衬套和钻套螺钉等组成。4.3 切削力和夹紧力的计算查表4得切削力计算公式:式中,f=1mm/r,查表得=736MPa, 即=1547N所需夹紧力,查表5得,安全系数K=式中为各种因素的安全系数,查表得:K=1.872,当计算K2.5时,取K=2.5孔轴部分由M8螺母锁紧,查表得夹紧力为12360N=30900N由上计算得,因此采用该夹紧机构工作是可靠的。4.4 定位误差分析(1)移动时基准位移误差 (式5-5)式中: 心轴孔的最大偏差 心轴孔的最小偏差 心轴定位孔与心轴最小配合间隙代入(式5-5)得: =0.011+0+0=0.011 (2) 转角误差 (式5-6)式中: 心轴孔的最大偏差 心轴孔的最小偏差 心轴定位孔与心轴最小配合间隙 削边销孔的最大偏差
- 温馨提示:
1: 本站所有资源如无特殊说明,都需要本地电脑安装OFFICE2007和PDF阅读器。图纸软件为CAD,CAXA,PROE,UG,SolidWorks等.压缩文件请下载最新的WinRAR软件解压。
2: 本站的文档不包含任何第三方提供的附件图纸等,如果需要附件,请联系上传者。文件的所有权益归上传用户所有。
3.本站RAR压缩包中若带图纸,网页内容里面会有图纸预览,若没有图纸预览就没有图纸。
4. 未经权益所有人同意不得将文件中的内容挪作商业或盈利用途。
5. 装配图网仅提供信息存储空间,仅对用户上传内容的表现方式做保护处理,对用户上传分享的文档内容本身不做任何修改或编辑,并不能对任何下载内容负责。
6. 下载文件中如有侵权或不适当内容,请与我们联系,我们立即纠正。
7. 本站不保证下载资源的准确性、安全性和完整性, 同时也不承担用户因使用这些下载资源对自己和他人造成任何形式的伤害或损失。