典型螺母冷镦工艺设计
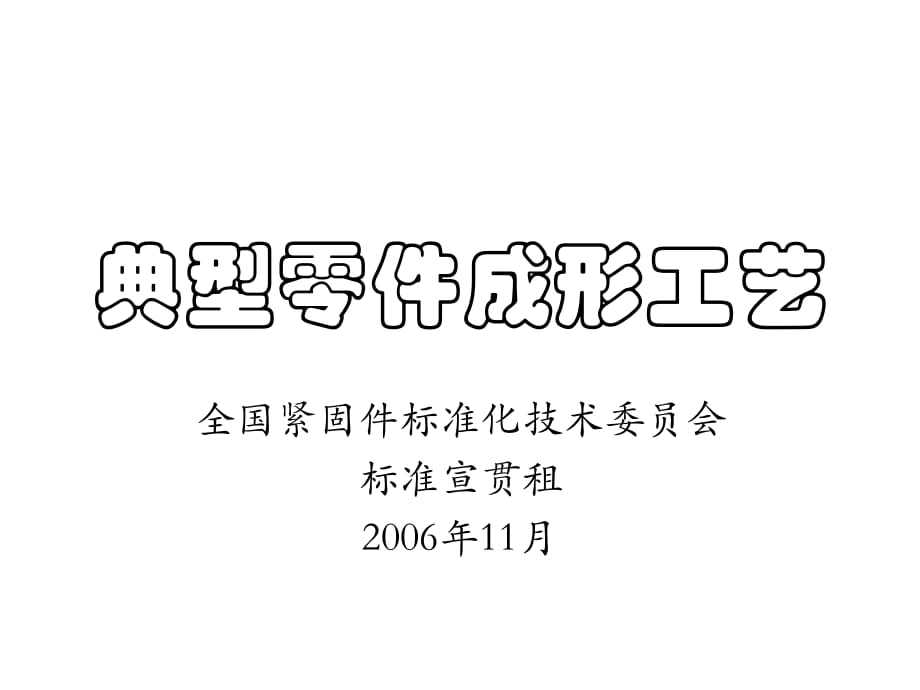


《典型螺母冷镦工艺设计》由会员分享,可在线阅读,更多相关《典型螺母冷镦工艺设计(33页珍藏版)》请在装配图网上搜索。
1、典 型 零 件 成 形 工 艺全 国 紧 固 件 标 准 化 技 术 委 员 会标 准 宣 贯 租2006年 11月 一、汽车后轮内螺母多工位加工工艺介绍 1、工艺分析此零件为典型的挤压杯形件,其分三部分组成:球面凸缘、空心圆柱及四方尾部。 2、变形工步的设计此零件采用五工位成形,其工艺流程为:切料整形镦平镦头精镦头及倒角正反复合挤压。(见下图) 正反复合挤压 镦头及倒角 镦头 镦平 整形 切料 3、变形特点分析 3.1、正反复合挤压变形程度 3.1.1、正挤压断面收缩率F=(1)10026 3.1.2、反挤压断面收缩率F=10010042 3.2、球面凸缘镦粗 3.2.1、镦粗变形特点 镦粗
2、变形一般分为三个区域(见上图)区域称为难变形区,这是和上下压头接触的区域。由于表层受到很大的摩擦阻力,这个区域的单元体都处于三向压应力状态,愈接近中心,三向压缩程度愈强烈,所以这区域的变形很小。区域为大变形区,它是处于上、下两个难变形锥体之间的部分(外围层除外)。这部分受到的接触摩擦力的影响已较小,因而水平方向上受到的压应力较小单元体主要在轴向力作用下产生很大的压缩变形,径向有较大的扩展,由于难变形锥体的挤压作用,还有向上、下弯曲的现象,这些变形的综合,外形出现了鼓形。区域是外侧的筒形部分,称小变形区。它的外侧是自由表面,端面摩擦影响又小,因而应力状态可看成近似单向压缩,其变形不大。 3.2.
3、2、镦粗变形的端面变化球面凸缘镦粗工艺方案如下图所示 球面凸缘镦粗工艺方案如下图所示 针对以上分析,在二序的成形中上端面需预制出一定的球面,使其在三序成形时,金属在向径向扩展时始终保持一弧面,最终与三序上模球面相吻合。在二序毛坯设计中应注意上端面直径的大小,过大,会造成端面尺寸增长过快,使金属还未来得及充满球面顶部就被镦粗压缩,致使球面充不满;过小,会造成在二序成形中,由于球面变形程度较大,致使外圆镦粗,球面端面悬空,无法得到再一次镦平,端面留有切断裂纹,此裂纹会在下序变形中滑移到球面上。 3.3、中间工位毛坯设计中间工位毛坯是挤压前半成品,主要进行材料体积和变形量的分配,为成品挤压形状及尺寸
4、等方面的准备工作。 3.3.1、中间毛坯设计应注意以下问题 1)最大限度满足挤压件的质量要求; 2)应保证充满难以挤压到位的局部形状; 3)避免毛坯呈悬空状态,增设中间变形; 4)中间毛坯锥形的锥度应大于挤压件相应处的锥角,这样便于锥角毛坯放入凹模,确保挤压过程不致出现多余金属。 3.3.2、各毛坯间的尺寸配合 a、径向尺寸的配合关系确定径向尺寸配合关系的原则是:要使毛坯能够自由放入下道的模腔内。在确定各道毛坯尺寸时,应从成品开始反过来进行推算。 b、轴向尺寸的配合关系考虑到成形时,将有部分金属进入模腔内,使轴向尺寸增加一高度H。 c、其它尺寸的配合关系为防止金属滞流,中间毛坯的过渡部位应设计
5、为锥形。 3.4、原材料要求原材料选用冷拉圆钢,由于采用多工位成形,无法进行中间处理,为便于成形,因此需要严格规定原材料的技术要求。其要求为: a. 材料表面应光滑,洁净,不允许有任何的裂纹、气泡、折叠、皱皮、夹杂和发纹存在; b. 磷化膜均匀、致密,结合牢固,厚度在814m,表面不得有拉毛、锈蚀等缺陷; c. 硬度不大于HB160,珠光体级别不小于5级; 3.5、材料体积计算运用制图软件Autocad进行精确的1:1绘制第五工位毛坯立体图,通过工具栏查询可知体积,当然也可分为几个简单的立体形状进行组合计算,得到体积,但运用制图软件可以更快捷、准确,同时可对各部分体积进行调整、编辑,合理设计毛
6、坯尺寸。 4、 成形力计算 4.1、剪切力的计算根据以上设计的毛坯预留间隙,选用ML20Cr,28.1材料。剪切力P280KN ML20Cr,硬度160HB,由图6-31(注:冲压设计手册)查得 材料抗拉强度b550N/mm2 4.2、整形(一序)、镦平(二序)力的计算:整形力P830 KN镦平力P1055KN 镦粗时的系数C值H1d1 C2.4H10.8d1 C35注:冲压设计资料图6-32 镦粗时的系数C值注:冷锻手册图2.47 4.3、三、四序成形力的计算三序成形力 PFC均0.78535.3621.8595/10001075KN四序成形力 PFC均0.78535.821.8595/10
7、001082KN 4.4、正反复合挤压力计算:挤压力PpF凸模23800.78518.682/1000660KN总镦锻力P4980 KN,10FF 5、主要模具设计 5.1、切料工位模具设计为保证切料质量及提高模具使用寿命,切料方式采用套筒切料,割料模及切刀模均采用硬质合金YG20C材料制造,为避免料弯而进料不畅,将割料模入口处制出一定的斜度 5.2、一、二、三、四工位模具设计一、二、三、四工位单位成形力分别为1320 Mpa、1650 Mpa、1071 Mpa、1071 Mpa,必须采用多层次组合凹模结构,为方便模具设计的标准化,统一采用三层组合凹模,三层组合凹模的最佳设计方案是凹模与第一预
8、应力环及第二预应力环同时屈服,而且要根据给定的凹模内外径尺寸来决定能使容许内压达到最大的预应力环直径及过盈量。 6、润滑为了降低成形时的单位成形力,提高零件表面质量,延长模具使用寿命,必须对成形毛坯进行合理的润滑处理。对原材料表面采用磷酸盐处理,经过这样处理的表面形成一层多孔状的薄膜,具有良好塑性,可容纳一定量的润滑剂,同时采用高压润滑油,在进行穿孔挤压时,由于四序毛坯的凹穴存在,形成润滑剂的储存窝,提供充分的润滑。 1、螺母热镦机的优点及缺点 1.1、螺母热镦机的优点、原材料采用热轧棒料,省去改拔、退火、磷化等材料改制工序;、因采用热镦加工,材料的变形量范围大,对于不同规格的产品可以选用同种
9、规格的材料,大大降低原材料的使用规格;采用热镦加工变形抗力较小,中间连皮可制得较冷成形薄,冲孔废料节省20左右;较自动车加工原材料利用率提高1.6倍;、热镦机连续加工,减少冷挤中间退火、磷化等多次往返工序,相对于冷挤分序及自动车加工生产效率提高58倍;、可加工冷成形不能加工的形状复杂的产品;、同类产品热镦加工比冷镦加工所需吨位要少1/3。 1.2、螺母热镦机的缺点、与冷镦工艺相比,对模具的机械性能要求较高,且寿命低;、由于材料通过中频加热,对电能的消耗较大,加工环境较差;、设备投资成本较大,外围辅助设施复杂。 热镦机分为主机及感应加热两大部分组成,棒料由棒料冷端上料台架的冷料存储架自动进入送料
10、机构,通过棒料传送装置经中频感应加热炉加热到设定温度进入热镦机成型,产品经过切料、镦扁、成形、冲孔等工序完成,设备采用双滑块装置,将镦扁与成形、冲孔工序模面分开成90角,镦扁后毛坯经由具有一定落差的环行滑道进入储料区,然后采用夹钳传送到成形、冲孔工序,这样的设计结构,可以最大限度的去处加热所产生的氧化皮,并防止其进入成形模中,避免影响产品质量及降低模具寿命。 3.1、成形毛坯热锻件图的设计热锻件图以冷锻件图为依据,但又有区别,考虑到金属冷缩现象,热锻件图上的尺寸应比冷锻件图的相应尺寸有所增大。理论上加放收缩率后的尺寸按下式计算: Nn(1+Z%)式中 N热锻件尺寸; n冷锻件尺寸; Z终锻温度
11、下锻金属收缩率,钢一般为1.21.6加放收缩率时还应主要下列几点:、无坐标中心的圆角半径不放收缩率;、薄而宽、细而长的尺寸部位,因在热镦时冷却快,收缩率应适当减小。 3.2、体积计算根据热锻件图可知,V总V1+V2-V3 3.4、中间毛坯尺寸的设计中间毛坯尺寸的计算,依据塑性变形材料体积不变原则,。在设计毛坯尺寸时需要特别注意以下几点: C应比B大512,经镦扁后以消除切料造成的外径变形,否则会影响产品质量;必须C/Dd1,防止镦扁坯料经滑道时翻转,造成卡料。如以上条件不满足时,须调整材料直径规格。 4、热锻温度的选择钢在加热的过程终须防止过热及过烧现象的发生,通过长期的生产实践和大量的试验研
12、究,现有钢种的锻造范围均已确定,可从有关手册查得。 5、模具设计相对于冷镦而言,热镦模具的使用环境要恶劣的多,其需承受反复冲击载荷和冷热交变作用,因热应力而容易导致疲劳破裂;模腔表面受到高温金属流动的作用而产生摩擦效应,尤其是坯料表面的氧化皮未清除干净的情况,摩擦作用更加强烈,加速模腔表面的磨损,出现剥落现象。热镦时,成形模受热毛坯的影响,如果模腔表面温度上升至400以上,将发生高温回火现象,容易被压塌和磨损。所以,在热镦时必须作适当的冷却。除设备上已具有的冷却管道外,在设计模具时,也必须考虑冷却水孔的设计。 成形尺寸先从理论上依据计算出的热锻件图,然后再经过生产实践重新确定、修复模具的成形尺
13、寸,以保证产品精度。上模采用组合方式,在生产过程中,上冲头的由于受力及与坯料接触等影响,其损坏较上冲模快,采用此种设计方式,即可简化模具加工难易程度,消除过度处的应力集中,同时方便上冲头的更换,降低模具综合成本。成形凹模结构同冷镦模类似,其设计原则也大致相同,为防止应力集中而产生开裂,成形模采用纵向剖分结构。成形模采用单层套预紧,其过盈量较冷镦模小,因在成形时,成形模与模套存在温度梯度,其线性膨胀量会使实际过盈加大,同时在接触表面产生热胶着,当成形模退出后,两者表面拉伤严重,造成模套报废。为防止成形时,模腔内空气无法排除,在成形模的六方与圆柱结合处设计气孔,此气孔不可太大,避免材料流入而堵住,一般设计为0.6MM。模腔内的冷却主要依靠成形下冲来完成,在成形下冲设计冷却孔,此冷却孔的位置要使冷却水最大限度地均匀喷射到模腔表面。
- 温馨提示:
1: 本站所有资源如无特殊说明,都需要本地电脑安装OFFICE2007和PDF阅读器。图纸软件为CAD,CAXA,PROE,UG,SolidWorks等.压缩文件请下载最新的WinRAR软件解压。
2: 本站的文档不包含任何第三方提供的附件图纸等,如果需要附件,请联系上传者。文件的所有权益归上传用户所有。
3.本站RAR压缩包中若带图纸,网页内容里面会有图纸预览,若没有图纸预览就没有图纸。
4. 未经权益所有人同意不得将文件中的内容挪作商业或盈利用途。
5. 装配图网仅提供信息存储空间,仅对用户上传内容的表现方式做保护处理,对用户上传分享的文档内容本身不做任何修改或编辑,并不能对任何下载内容负责。
6. 下载文件中如有侵权或不适当内容,请与我们联系,我们立即纠正。
7. 本站不保证下载资源的准确性、安全性和完整性, 同时也不承担用户因使用这些下载资源对自己和他人造成任何形式的伤害或损失。