45万吨年丙烷脱氢制丙烯装置工艺操作规程
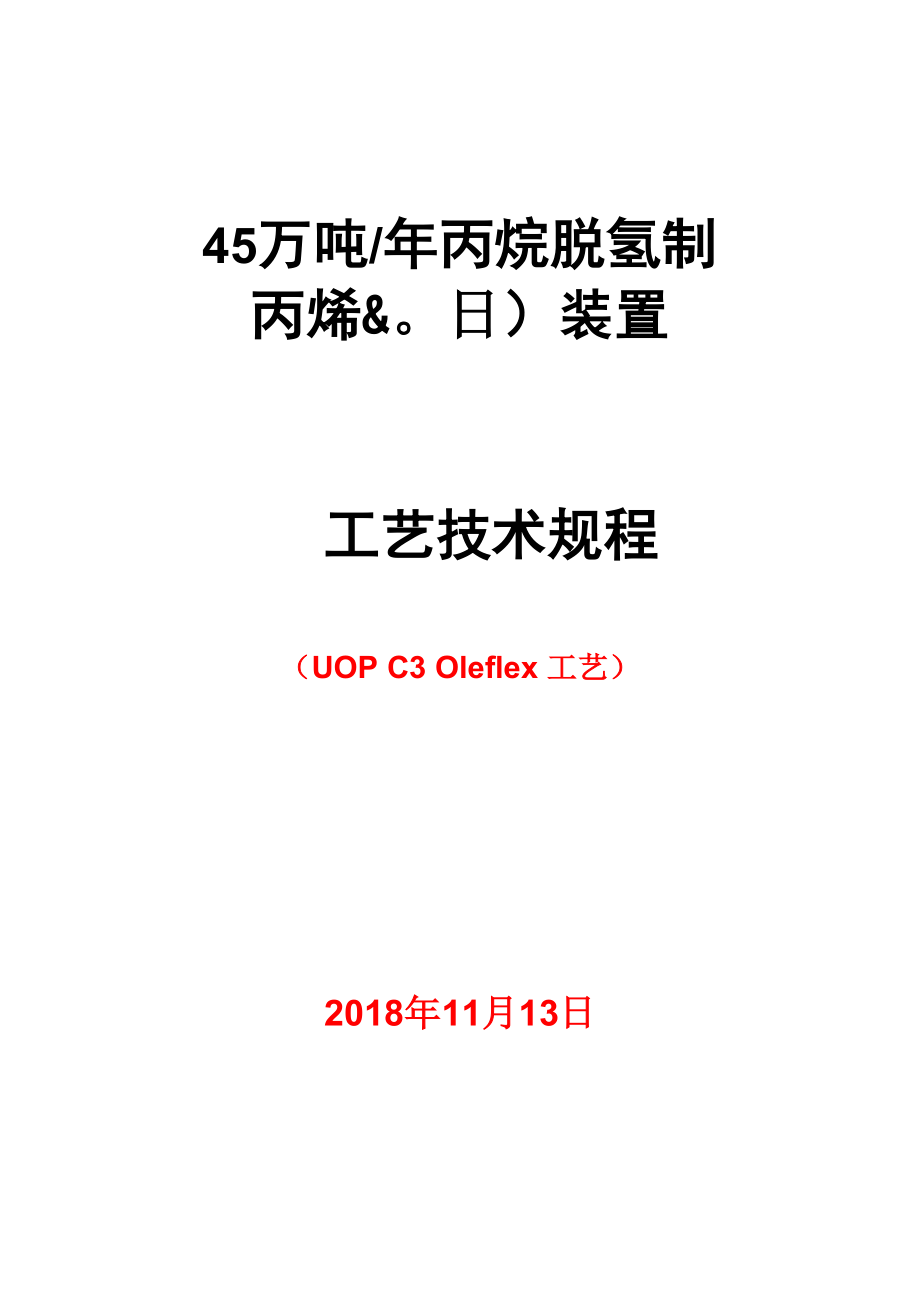


《45万吨年丙烷脱氢制丙烯装置工艺操作规程》由会员分享,可在线阅读,更多相关《45万吨年丙烷脱氢制丙烯装置工艺操作规程(21页珍藏版)》请在装配图网上搜索。
1、45万吨/年丙烷脱氢制丙烯&。日)装置工艺技术规程(UOP C3 Oleflex 工艺)2018年11月13日目录1预处理工段12丙烷脱氢反应工段13催化剂再生工段44冷箱分离工段85 SHP工段96精馏工段97 PSA 工段10 8全厂系统(蒸汽凝液系统) 9丙烷低温储罐及其辅助系统,1310中间罐区11火炬1412空压站及氮气辅助系统1 13本项目涉及的主要化学反应,1预处理工段来自新鲜丙烷进料加热器(21E0601)新鲜丙烷原料先进入进料保护床 (21D0101-1/2),在此用树脂吸附剂除去氮化物和有机金属化合物。这两台保护 床可以通过调整进出料管道来改变两台保护床的前后。接着丙烷原料
2、流过汞脱除 器(21D0102)除汞,然后进入进料干燥器(21D0103-1/2)以脱除原料中水分(原 料中如果含水将在分离系统结冰,就可能堵塞系统。这两台干燥器一般在系统开 车时用来干燥进料,正常运行时可不用。进料干燥器装填分子筛以从丙烷中脱除 水分。进料干燥器设计为每周再生一次,再生用干燥的丙烷气来完成,丙烷在进料 干燥再生蒸发器(21E0120)中用蒸汽先加热到60C,然后用原料干燥再生过热器 (21E0122)加热到232C左右,以与丙烷进料相反的方向进入进料干燥器去再 生干燥床层,然后进入进料干燥再生冷凝器(21E0102),被冷凝后送到进料干燥 再生收集器(21D0104),在此水
3、与再生丙烷分离,丙烷用进料干燥再生泵 (21P0101)输送到在线操作的干燥器入口,废水送至反应工段与含硫废液混合 后一并送至含硫/盐污水处理装置处理。2丙烷脱氢反应工段(1)原料预热及反应自冷箱分离工段回收冷量后的原料丙烷送至热联合进料换热器 (21E0201-1/2/3/4 )内与出反应器的粗产品气进行换热进一步提高进料温度同 时降低粗产品的温度。预热后的原料气中注入少量的二甲基二硫。经预热的物料 经过进料加热炉(21F0201),加热至615C后自反应器底部进入第一反应器 (21R0201),原料气穿过反应器内件与反应器顶部流下的催化剂接触后发生脱氢 反应。从第一反应器出来的物料进入第一
4、中间加热炉(21F0202)。由于脱氢反应 是吸热反应,因此需要在过程中补充物料放出的热量。物料再次被加热至622C 后进入第二反应器(21R0202)继续进行脱氢反应,之后物料依次进入第二中间 加热炉(21F0203)、第三反应器(21R0203)、第三中间加热炉(21F0204)、第四 反应器(21R0204),从第四反应器出来的反应粗产品再次经过热联合进料换热器 中与混合原料换热回收热量后,送至反应产物压缩部分。在反应物料依次进入反应器的同时,来自催化剂连续再生工段的净化气(从 PSA来的经加热后的高纯氢)也从反应器的上部进入到反应器的中心“锥形塞管” 内部进行连续吹扫,以尽量减少工艺气
5、在中心“锥形塞管”内部的停留时间,防 止其在此结焦或其它副反应的发生。硫化物加注罐(21J0201)里的二甲基二硫化物用硫化物注入泵 (21P0207-1/2/3)分别在混合进料进入热联合进料换热器前后注入其中。目的 是为了保持加热炉及反应器内的不锈钢表面上形成格的硫化层,以免不锈钢渗碳 以及减少丙烷原料热裂解成乙烷和甲烷。同时,在本设计仍保留向反应器注水的 管线作为备用,可以把少量水注入到反应器的入口中帮助扩展催化剂的稳定性和 减少催化剂上的焦的形成。注入水采用蒸汽凝液,使用洗涤水补充泵 (21P0209-1/2)注入。(2) 反应产物压缩经回收热量的反应产物首先进入反应流出物冷却器(21E
6、0202-1/2)中进一 步冷却至42C,随后进入反应流出物压缩机进口分离器(21D0201),罐顶的气 相进入反应流出物压缩机第一段(21K0201),经压缩机绝热压缩后的气体温度升 高,被送入反应流出物压缩机第一级间冷却器(21E0203)进行冷却,然后再进 入反应流出物压缩机第一级间分离器(21D0202),罐顶的气相随后依次进入反应 流出物压缩机第二 段进行压缩,进入反应流出物压缩机第二级间冷 却器 (21E0204)冷却,再进入反应流出物压缩机第二级间分离器(21D0203),最后罐 顶的气相进入反应流出物压缩机第三段压缩。经压缩升压的粗产品压力 36MPaG,温度110C自第三段压
7、缩出口物料送去精馏工段脱丙烷塔进料预热器 (21E0603)与脱丙烷塔进料换热以回收热量后温度65 C,然后再进入反应流出 物压缩机出口冷却器(21E0205)进一步冷却至42C,经反应流出物压缩机出 口分离器(21D0204)后,罐顶的气相送去反应产品后处理部分进行除氯、除硫及 干燥处理。反应产物压缩部分还配有溶剂注入罐,在操作过程中需要间断批量的将重芳 烃溶剂(对二乙基苯)分别送入物料冷却器的进口,将附着在换热器管内的结焦 溶解带出,以保证换热器的换热性能,并在各段压缩机进口前的气液分离器内对 溶剂进行收集。收集后的溶剂分批送回溶剂注入罐循环使用。定期检测溶剂中的 杂质含量,当杂质含量高于
8、允许值时则需要更换新的溶剂。(3) 反应产物后处理由于用于在催化剂再生工段需要注氯,催化剂上的氯离子会随反应产物带入 下游。同时在原料气进入在反应器前加注的硫化物和丙烷原料中含有的硫化物均 转化为硫化氢的形式随反应产物带出。催化剂还原过程中还会产生少量的水,其 会在冷箱中会结冰造成堵塞,而H S能使后面SHP单元的催化剂中毒并污染丙烯 2产品和净气。故这些杂质均需要在进入冷箱分离前进行处理以保护后续设备的正 常运行。自反应流出物压缩机压缩后的粗产品气由氯化物处理器(21D0205)的顶部 进入,底部送出。氯化物处理器内装填有活性氧化铝特制的非再生型吸附剂。反 应产物经脱氯后,自上向下流过反应流
9、出物干燥器(21D0206-1/2)。以脱除反应 产物中的HS和水。反应流出物干燥器为两台并联设备,其中一台正常工作,另 2一台进行再生操作。大约48小时进行一次切换。正常操作时,(以21D0206-1为例)产品气自顶部进入干燥器杂质在填料中 被吸附,处理后的产品气自干燥器底部流出送至冷相分离工段进行分离。再生加热时,自冷箱分离工段送来一股净气(主要为氢气)经过再生加热器 (21E0206)加热后将净气预热至232C送入再生中的干燥器(21D0206-2),气 体自下而上经过干燥器,气体将吸附剂上的硫化氢及水带走由顶部排出后进入再 生空冷器(21E0208)冷却后送入再生分离罐(21D0207
10、)气相送入再生洗涤塔, 液相重组分由再生分离罐底泵(21P0208)送入精馏工段脱丙烷塔塔釜液气提塔 (21C0603)汽提回收气相组分,液相作为燃料油使用。再生干燥器完成再生加热后继续进行再生冷却。每个再生周期大约需要再生 加热7.6小时,冷却7.1小时。再生冷却时,仍使用自冷箱分离工段送来的净气 温度34C,此时再生加热器(21E0206)不在工作,净气自下向上进入干燥器 (21D0206-2)将再生后的床层进行冷却,冷却后的气体由干燥器顶部排出再经 过再生空冷器及再生分离器后送入再生洗涤塔。自再生分离器来的气体由再生洗涤器(21C0201)底部进入塔内,再生洗涤 塔为填料塔,下部使用10
11、wt%的氢氧化钠溶液进行循环洗涤除去气体中的硫化 氢,上部使用蒸汽凝液作为洗涤水循环使用洗涤气体中夹带的微量碱液。经洗涤 后的气相主要为含氢气,送往PSAX段进行提纯,一部分会用剩余部分作为产品 送出。洗涤塔中循环的碱液定期进行成分分析,当氢氧化钠含量小于新鲜碱液量 的30%时需进行更换,废碱液由洗涤塔底部排出送至废碱液脱气罐(21D0208) 以除去气体中进入的氢或烃,然后由废碱液输送泵(21P0205)送至含硫/盐污水 处理装置进行处理。同时将配置好的新鲜碱液由加碱装置泵送至碱液循环泵(21P0204-1/2)进口循环至洗涤塔内。上部循环的洗涤水也定期将部分含碱废 水排放至碱液脱气罐(21
12、D0208)中,同时将消耗的新鲜凝液经洗涤液补充罐 (21D0209)及洗涤水补充泵(21P0209-1/2)补充至洗涤塔内。(4)燃料气系统本装置生产过程中可副产以氢气及轻烃类气体为主的可燃气体。此气体可作 为装置加热炉及锅炉的加热的燃料气使用。燃料气主要由来自PSA工段的富氢尾 气,脱乙烷塔塔顶放空气以及脱丙烷塔底部汽提气组成。混合气体进入燃料气分 离罐(21D0211)初步分离后送入燃料气聚结器(21D0212)中将燃料气中夹带的 液相进一步分离,然后送入燃料气加热器(21E0210)将燃料气预热至120C后 送入燃料气管网供加热炉及锅炉使用。燃料气系统还设置一套原料丙烷气化系统,用于装
13、置开车向燃料气管网提供 开车用燃料。并且在装置正常操作时后系统副产燃料气不足以供装置使用时气化 部分丙烷气作补充用。(5)装置副产蒸汽燃料气送至加热炉燃烧后将热量提供给反应进料以维持反应温度,燃料气在 加热炉辐射段燃烧后的烟气经过集合管排放至加热炉的对流段,在对流段内设置 了多组盘管以回收废热烟气的热量副产蒸汽供装置使用。锅炉水自界外锅炉水泵分别送至进料加热炉(21F0201),第一中间加热炉 (21F0202),第二中间加热炉(21F0203),第三中间加热炉(21F0204)对流段 部分的预热管内预热,然后与循环段出口的饱和蒸汽(汽液两相)混合后进入汽 包(21D0210)中。液相锅炉水经
14、锅炉水循环泵(21P0206-1/2 )加压后分别送至 四台加热炉的蒸汽发生段,锅炉水依次经过下部蒸汽发生段及上部蒸汽加热段后 吸收热量副产蒸汽压力4.4MPaG,温度256C,汽水混合物再回到汽包内进行 分离,自汽包顶部排出的蒸汽分别进入进料加热炉(21F0201)和第一中间加热 炉(21F0202)的蒸汽过热段过热,过热蒸汽经过调温后压力4.2MPaG,温度 420C送至中压蒸汽管网供各用户使用。3催化剂再生工段此工段的主要目的是在装置正常操作的情况下,将反应器部分来的因结焦而 降低活性的催化剂进行再生,恢复其活性,然后再送回反应器,从而使反应得以 性能良好的连续进行。(1)反应器段催化剂
15、自第四反应器(21R0204)底部(22根3” /4”均布管)自流至4号 催化剂收集器(21D0317)中。自吹扫气总管来的吹扫气经过除硫加热器(21E0314) 加热至525C送入4号催化剂收集器上部,吹扫催化剂以脱除固体颗粒上的硫化 物(此电加热器为连续工作,然而在其出现故障时,系统可以容许在没有加热的 情况下运行34天),吹扫气自4号催化剂收集器顶部排出,随反应产物送入REC 压缩机。来自第一反应器顶部的排放还原气进入4号催化剂收集器下部去冷却催 化剂颗粒的温度至150C。与此同时用氮气对1号闭锁料斗(21D0318)进行冲压, 至1号闭锁料斗与4号催化剂收集器压力一致时,开启VBB阀组
16、(一个V型球阀 +两个B型球阀),需要催化剂进入1号闭锁料斗(21D0318)。VBB阀组开启初始 设定的时间后关闭,再用氮气对1号闭锁料斗进行吹扫,吹去氢气和碳氢化合物, 将反应区的碳氢环境在此置换为氮气环境,置换气排放至进料加热炉(21F0201) 作为燃料使用。下一步再开启1号闭锁料斗(21D0318)与4号提升料斗(21D0319) 之间的VBB阀组,使催化剂流入4号提升料斗(21D0319)中。由提升气风机 (21B0305)送来的提升气(主要为氮气)先将催化剂从4号提升料斗先提升至 中间分离料斗(21D0322),中间分离料斗顶部分出的含有催化剂粉尘的气体去粉 尘收集器(21D03
17、02),中间分离料斗底部的催化剂再由提升气风机(21B0305) 送来的提升气提升至催化剂再生段的分离料斗(21D0301)。反应器段还包含两台换热器:净气预热器(21E0308 )和CCR气预热器 (21E0309)。净气预热器(21E0308)是将来自PSA的纯氢加热至145C,升温 后的纯氢一股去2号闭锁料斗(21D0305)去做置换气;一股去5号提升料斗 (21D0306)做提升气;一股去反应装置的第一至第四反应器和4号催化剂收集器 (21D0317)。去反应器的的纯氢一部分直接进入到反应器的中心管内,以尽量减 少丙烷气在中心管内的停留时间,防止其在此结焦;一部分需要再经过电加热器 加
18、热到更高的温度去第一、第二、第三和第四反应器的上段。去第一反应器的纯 氢由还原气加热器(21E0310)加热至520550C后进去第一反应器的还原区, 将氧化态催化剂还原使其恢复活性后继续使用。去第二、第三和第四反应器上段 的纯氢分别经过2号反应器净气加热器(21E0311)、3号反应器净气加热器 (21E0312 )和4号反应器净气加热器(21E0313)加热到600C以上再进入反应 器上段,但不做还原用途。去4号催化剂收集器(21D0317)的纯氢经过除硫加 热器(21E0314)加热到600C后去4号催化剂收集器吹扫除硫。CCR气预热器(21E0309)是将来自分离系统的纯度不是很高的氢
19、气加热至 145C后,一股去1、2、3号提升料斗做提升气用,一股与反应装置的热联合进 料换热器(21E0201-14)的壳程出料混合后循环进入进料加热炉(21F0201)。(2)催化剂再生段来自中间分离料斗(21D0322)需要再生的催化剂进入再生段的分离料斗 (21D0301),进一步分离催化剂粉尘。分离料斗(21D0301)顶部循环气进入粉 尘收集器(21D0302),粉尘收集器将粉尘及催化剂过滤收集至催化剂粉尘罐内(约 7天换粉尘罐一次)。由粉尘收集器上部排出的淘析气一部分由除尘风机(21B0304)送回分离料斗(21D0301),另一部分(约循环风量的1/10)送至提 升气风机(21B
20、0305),加压后送至4号提升料斗(21D0319)作为提升气使用。 在提升气风机(21B0305 )的出口引一股提升气至提升气风机调温冷却器(21E0307),冷至44C左右再返回提升气风机的入口,使得提升气温度不至于 过高。分离料斗(21D0301 )与再生塔(21R0301)之间的要保证一定的压差使得再 生塔内的气体不能倒流至分离料斗。催化剂由分离料斗进入再生塔(21R0301) 中进行再生,再生塔内的气体自下而上逆流与催化剂接触,催化剂首先进入上部 烧焦区,接着进入下部烧焦区,在此区域通过和含氧气体接触燃烧去除催化剂表 面的结焦,经过冷却区冷却后再去氯化干燥区,最下段是脱氯区。再生完毕
21、的催 化剂由再生塔底部排出至流量控制料斗(21D0303)及缓冲料斗(21D0304)中。上部再生气自再生塔顶部排出(520C )经过上部再生冷却器(21E0305) 冷却后温度降为478C,与经过空气干燥器(21L0302)干燥后的补充空气混合 由上部再生风机(21B0302 )送回再生塔内进行烧焦循环。上部再生加热器 (21E0303)仅开车时使用。下部再生气自再生塔内中部的收集管内收集后自塔 顶排出,经过下部再生冷却器(21E0306)冷却后温度降为550C,与经过空气 干燥器(21L0302)干燥后的补充空气混合后由下部再生风机(21B0303)送回再 生塔内进行烧焦循环。下部再生加热
22、器(21E0304)仅开车时使用。自下部再生风机(21B0303 )出口引出一股 再生气送至冷却区 冷却器 (21E0301)冷至477C送入再生塔烧焦区下部的冷却区,将经过烧焦后的催化 剂颗粒进行冷却。再生塔(21R0301)的冷却区下段为氯化干燥区,一股经过空气干燥器 (21L0302)干燥后的空气做抽吸气将氯气抽吸混合后送至空气加热器(21E0302) 的出口(白烧工况用仪表空气抽吸氯气,黑烧工况用氮气抽吸氯气);另一股空 气经过空气加热器(21E0302)加热至610C后与含有氯气的空气混合后送入再 生塔的氯化干燥区。在氯化干燥区通过干燥的热空气除去催化剂中的水分,注氯 则是让催化剂中
23、的伯金属在载体颗粒上的进行重新排列,达到更好的分布效果, 提高催化剂活性。再生塔的最下段是脱氯区,在此区通过连续通入氮气来脱除催化剂中的残留 氯,以防止氯进入下游设备。在再生塔(21R0301 )内完成再生过程的催化剂自再生塔底部流出,首先进 入流量控制锁斗(21D0303),流量控制锁斗中的容量约为1分钟的催化剂流量, 之后流至缓冲料斗(21D0304)。缓冲料斗的上部设有新鲜催化剂的加料口,新鲜 催化剂通过催化剂加料漏斗(21D0307)和催化剂加料闭锁料斗(21D0308)加入 缓冲料斗中。催化剂在缓冲料斗(21D0304)中进行收集,到设定的时间后开启的下部的 VBB (一个V型球阀+
24、两个B型球阀),催化剂就流入2号闭锁料斗中(21D0305), 在开启2号闭锁料斗下的VBB阀组前采用H2先对闭锁料斗进行冲压,待锁斗压 力与5号提升料斗(21D0306)压力平衡后开阀,催化剂就流至5号提升料斗中。 关闭VBB阀组开启放空阀泄压。催化剂从5号提升料斗(21D0306)中用来自净 化气预热器(21E0308)的纯氢提升至第一反应器(21R0201 )的上部。催化剂在1号催化剂收集器(21D0311 )中的收集以及在1号提升料斗 (21D0312)中的提升、在2号催化剂收集器(21D0313)中的收集以及在2号提 升料斗(21D0314)中的提升和在3号催化剂收集器(21D031
25、5)中的收集以及在 3号提升料斗(21D0316)中的提升流程除无需脱硫和氮气吹扫外与4号催化剂 收集器(21D0317)的收集以及在4号提升料斗(21D0319)的提升流程相同。(3)放空气处理系统(21L0301)再生塔内除了各个区域要进行必要的气体循环外,还有废气排放,烧焦区及 氯化干燥区的废气均由再生塔中下部的排放口排放出塔外,排放的废气中含有氯 化氢、氯气、二氧化硫等有毒有害气体,需要经过处理达到环保要求后才能排放。 废气首先进入放空气处理系统(21L0301)的洗涤塔用用氢氧化钠溶液及亚硫酸 氢钠溶液吸收处理排放气中的酸性及有毒气体,在经过分液除去废气夹带的液滴 后经烟囱放空至大气
26、。(4)加氯系统(21L0303)催化剂再生工段需要给催化剂进行注氯,注氯的目的是让催化剂伯金属在载 体颗粒上的进行重新排列,达到更好的分布效果,提高催化剂活性。在此专门设 置加氯系统,加氯系统设置在室内,由氯瓶存储间,加氯间和漏氯吸收间组成。 氯气采用钢瓶储存,设计上采用一组钢瓶顺序加注,加注量由钢瓶底部的称量设 备称重计量。4冷箱分离工段本套冷箱分离系统将来自Oleflex工艺单元的反应器流出物流分离为富氢 的净气产品物流和富烃的液体产品物流。该冷箱系统还将一部分富氢气与丙烷进 料混合,作为反应器的混合进料送出。充分利用富氢物流在系统内的膨胀和优化 进出冷箱物流的换热。该系统的主要冷量来源
27、为新鲜丙烷进料和循环氢气的混合 物在冷联合进料换热器中的蒸发,还有另一部分冷量是由反应器流出物气相通过 高、低压膨胀机膨胀制冷而提供。反应器流出物以42C,184MPa(G)进入分离系统(21L0401),在冷联合进料 换热器与联合进料、部分净气换热而被部分冷凝。冷凝后的反应器流出物气相与 液相在高压分离器中分离,分离后的气体经过高压透平膨胀机膨胀节流,膨胀功 驱动膨胀发电机回收能量,气体部分冷凝。之后进入中压分离器进行气、液分离。 出中压分离器的气体被分为净气和循环气等2股物流。循环气进入低压透平膨胀机进一步膨胀降压。低压透平膨胀的能量驱动发电 机,气体部分冷凝。然后进入低压分离器进行气液分
28、离。出低压分离器的循环气 与来自中压分离器的干气在干气冷却器内换热器而被复温。换热后的干气进入干 气分离器进行气液分离。各分离器内的液相进入闪蒸罐内闪蒸,所有的分离器采用液位控制。出闪蒸 罐的气体返回到反应器流出物压缩机进口分离器。闪蒸罐的液体即液体产品,经 过闪蒸罐出料泵加压后在进料冷却器内与去反应器单元的新鲜原料换热,被加热 到约43C,以3.896 MPa(G)出分离系统,至SHP进料加热器。冷新鲜原料与来自干气冷却器的循环气在进入冷联合进料换热器前混合,形 成反应器的混合进料。混合进料与反应器流出物在冷联合进料换热器换热,然后 以约36C,0.368 MPa(G)离开分离系统,至丙烷脱
29、氢反应的混合进料换热器。来自干气分离器的干气被分成2股,其中一股在冷联合进料换热器中与反应 器流出物换热被加热到约38C,另一股在进料冷却器E-0103内被加热到约43C。来自上述2个换热器的干气再次混合后以约0.59 MPa(G)离开分离系统。5 SHPT段来自PSA装置的产品氢气40C, 2.1MPa(G)进入SHP氢气压缩机(21K0502-1/S),压缩至 3.46M Pa(G),然后进入 SHP 混合喷嘴(21M0501),多 余氢气送至界外。来自冷箱分离系统的液体产品(43C, 3.896 MPa(G),与来自产品精馏工 段的工艺液体(17C, 3.92MPa(G)混合,然后进入S
30、HP进料换热器(21E0511), 与0.3M Pa(G)的饱和低压蒸汽换热,被加热至60C,然后进入SHP混合喷嘴 (21M0501),与氢气在此混合,之后经过SHP静态混合器(21M0502)再次混合, 然后进入SHP反应器(21R0501),进行选择性加氢反应,反应后的液体(43C, 3.04MPa(G)被送至脱乙烷塔。6精馅工段经原料预处理工段脱除有机氮、汞及水后的的新鲜丙烷与自丙烯丙烷分离塔 塔底的循环丙烷混合,送往脱丙烷塔进料预热器(21E0603)经反应流出物压缩机 出口物料加热后送至1号脱丙烷塔(21C0601),约90%的丙烷自塔顶采出。塔釜 液经1号脱丙烷塔塔釜泵(21P0
31、603-1/2)加压后送至2号脱丙烷塔(21C0602)作为 进料,1号脱丙烷塔热回收再沸器(21E0604)使用热泵压缩机(21K0601)二级出口 的丙烯作为热源为1号脱丙烷塔塔釜液再沸提供热量,塔釜液再沸用热量不足部 分经蒸汽再沸器(21E0605 )使用低压蒸汽作为热源补充。剩余的10%丙烷自2号脱丙烷塔(21C0602)塔顶采出,两台脱丙烷塔塔顶的 丙烷采出气混合后经脱丙烷塔塔顶冷凝器(21E0608-1/2)冷凝由脱丙烷塔回流罐 (21D0605)收集,收集后的丙烷由脱丙烷塔塔顶凝液泵(21P0602-1/2)加压后,部 分用作1号和2号脱丙烷塔的回流,剩余的丙烷经新鲜丙烷进料加热
32、器(21E0601) 回收热量后送至反应工段。自2号脱丙烷塔(21C0602)塔底采出的C4+烃类经液位调节阀减压后送至脱 丙烷塔塔釜液气提塔(21C0603),自?、人来的尾气作为气提气,气提后的塔釜液 经气提塔出料泵(21P0610)加压,气提器塔底出料冷却器(21E0610)冷却后送至燃 料油储罐。塔顶采出的轻烃送往燃料气系统。自SHP单元来的丙烯丙烷混合物送往脱乙烷气提塔(21C0604),塔釜液送往 丙烯丙烷分离塔(21C0606),塔顶采出的轻烃一部分直接送至脱乙烷精馏塔 (21C0605), 一部分经脱乙烷气提塔冷凝器(21E0612)冷凝后送往脱乙烷精馏塔 (21C0605),
33、脱乙烷精馏塔塔釜液经脱乙烷气提塔回流泵(21P0605-1/2)加压后作 为脱乙烷气提塔(21C0604)的回流液,塔顶采出的轻烃经脱乙烷精馏塔塔顶预冷 器(21E0621)与丙烷低温储罐来的新鲜丙烷换热,再经脱乙烷精馏塔塔顶深冷器 (21E0614)冷凝后送往脱乙烷精馏塔塔顶凝液罐(21D0606)。罐顶气相经脱乙烷精 馏塔塔釜换热器(21E0615)与脱乙烷精馏塔塔釜液换热后送往燃料气系统,罐底 的液相经脱乙烷精馏塔回流泵(21P0604-1/2)加压后作为脱乙烷精馏塔的回流 液。脱乙烷气提塔(21C0604)塔釜液经丙烯丙烷分离塔进料冷却器(21E0616)与 循环丙烷换热后再经丙烯产品
34、加热器(21E0619)与丙烯产品换热,通过调节阀减 压后进入丙烯丙烷分离塔(21C0606)。塔釜液经丙烷循环泵(21P0607-1/2)加压后 与新鲜丙烷混合送往1号脱丙烷塔(21C0601)。塔内累计的二烯烃经二烯烃循环 泵(21P0608)泵加压后送往SHP单元进行选择性加氢。塔顶采出质量分数为 99.6wt%的丙烯送往热泵压缩机入口分离罐(21D0607),分离其中少许液相后的气 相送往热泵压缩机(21K0601)一级入口,经一级压缩后的气相,一部分送往丙烯 丙烷分离塔再沸/冷凝器(21E0617-1/2/3/4)作为丙烯丙烷分离塔塔釜液再沸的 热源,换热后冷凝下来的液相与丙烯丙烷分
35、离塔回流泵(21P0606-1/2)出口的丙 烯混合后作为丙烯丙烷分离塔(21C0606)的回流液,一部分继续送至压缩机二级 入口。经两级压缩后的气相,一部分经丙烯调温冷凝器(21E0618)冷却为液相后 送往热泵压缩机入口分离罐,一部分送到1号脱丙烷塔热回收再沸器(21E0604) 作为1号脱丙烷塔塔釜液再沸的热源,之后经丙烯调温冷却器(21E0607)冷却并 减压后送至热泵压缩机入口分离罐。热泵压缩机入口分离罐内的液态丙烯,一部 分经丙烯丙烷分离塔回流泵(21P0606-1/2)加压与出丙烯丙烷分离塔再沸/冷凝 器(21E0617-1/2/3/4)管程的丙烯混合后作为丙烯丙烷分离塔的回流液
36、,一部分 经丙烯产品泵(21P0609-1/2)加压及丙烯产品加热器(21E0619)加热后送至丙烯 储罐。7 PSAT段来自再生气体洗涤塔的气体以38.15C,0.32MPa(G)进PSA装置后先经过原 料气压缩机(21K0701-1/2)加压至2.2MPa(G)、40C,然后进变压吸附系统,系 统采用10塔PSA工艺流程,即:装置的十个吸附塔的吸附和再生工艺过程由吸 附、连续多次均压降压、顺放、逆放、冲洗、连续多次均压升压和产品气升压等 步骤组成。具体过程简述如下:a. 吸附过程原料气经过原料气水分罐后,自塔底进入正处于吸附状态吸附塔内。在多种 吸附剂依次选择吸附下,其中的各种杂质组份被吸
37、附下来,未被吸附氢气作为产 品从塔顶流出,经压力调节系统稳压后送出界区。其中H2纯度大于99.99%,压 力大于2.1MPa.G。当被吸附杂质的传质区前沿(称为吸附前沿)到达床层出口预留段时,关掉该 吸附塔的原料气进料阀和产品气出口阀,停止吸附。吸附床开始转入再生过程。b. 均压降压过程这是在吸附过程结束后,顺着吸附方向将塔内的较高压力的氢气放入其它已 完成再生的较低压力吸附塔的过程,该过程不仅是降压过程,更是回收床层死空 间氢气的过程,本流程共包括了多次连续的均压降压过程,因而可保证氢气的充 分回收。c. 顺放过程这是在均压降压结束后,首先顺着吸附方向将吸附塔顶部的气体回收进顺放 气缓冲罐的
38、过程,这部分氢气将用作吸附剂的再生气源。d. 逆放过程在顺放过程结束后,吸附前沿已达到床层出口。这时,逆着吸附方向将吸附 塔压力降至0.05Mpa左右,此时被吸附的杂质开始从吸附剂中大量解吸出来,逆 放解吸气进逆放解吸气缓冲罐。e. 冲洗过程在逆放过程全部结束后,为使吸附剂得到彻底的再生,用顺放气缓冲罐中的 氢气逆着吸附方向对吸附床层进行冲洗,进一步降低杂质组分的分压,使吸附剂 得以彻底再生,该过程应尽量缓慢匀速以保证再生的效果。f. 均压升压过程在冲洗再生过程完成后,用来自其它吸附塔的较高压力氢气依次对该吸附塔 进行升压,这一过程与均压降压过程相对应,不仅是升压过程,而且更是回收其 它塔的床
39、层死空间氢气的过程,本流程共包括了连续多次均压升压过程。g. 产品气升压过程在多次均压升压过程完成后,为了使吸附塔可以平稳地切换至下一次吸附并 保证产品纯度在这一过程中不发生波动,需要通过升压调节阀缓慢而平稳地用产 品氢气将吸附塔压力升至吸附压力。经这一过程后吸附塔便完成了一个完整的“吸附-再生”循环,又为下一次 吸附做好了准备。十个吸附塔交替进行以上的吸附、再生操作即可实现气体的连续分离与提 纯。(10个吸附塔在故障时,装置可自动切换至9塔、8塔、7塔、6塔、5塔 操作,以便不停车在线检修故障。)氢气(40C,2.1MPa(G)作为产品气体出PSA装置,一部分去CCR工段吹 扫气加热器,很少
40、一部分去SHP反应工段,其余氢气外售。解吸气(40C,0.03MPa(G)进入PSA尾气压缩机(21K0702)进行升压, 小部分升压至0.66MPa(G),去精馏工段的气提氢气加热器(21E0609);其余部 分只压缩至0.34 MPa(G),作为燃料气送至燃料气系统。8全厂系统(蒸汽凝液系统)PDH装置蒸汽用户分为中压蒸汽(3.65MPaG,260C )用户及低压蒸汽 (0.3MPaG,143.6C )用户。故装置分别设置中压和低压蒸汽凝液回收管网对蒸 汽凝液进行回收。中压蒸汽凝液各用户经管网收集后送至中压凝液闪蒸罐 (21D1001),罐内操作压力0.38MPaG,凝液在罐内闪蒸出低压蒸
41、汽自罐顶排出 并入低压蒸汽管网。闪蒸后的凝液自罐底排出送至低压凝液闪蒸罐(21D01002) 内。自各低压蒸汽用户收集来的低压蒸汽凝液与中压凝液闪蒸罐底部排出的凝 液一并送至低压凝液闪蒸罐(21D01002),罐内操作压力0.02MPaG,凝液在罐内 进一步闪蒸,乏汽自罐顶排出进入闪蒸罐冷凝器(21E1001)内与循环水逆流换 热并冷凝,凝液返回至低压凝液闪蒸罐(21D01002)收集。低压凝液闪蒸罐内的 凝液由罐底凝液返回泵(21P1001-1/2)送至凝液冷却器(21E1002)与冷却水逆 流换热后温度由常压饱和温度冷却至45C送至锅炉水精制系统处理后循环使 用。当界外精制系统无需冷却时,
42、手动关闭至凝液冷却器(21E1002)的阀门, 切换至换热器旁路直接将凝液送至界外锅炉水精制系统。9丙烷低温储罐及其辅助系统丙烷运输船到达业主张家港库区的码头后,液体丙烷由运输船上的输送泵加 压,经过两台液体卸料臂汇聚到卸船总管,经卸船总管输送到丙烷低温储罐 (19T0101-1/2)中。设计的卸船流量为2000m3/h,单台丙烷低温储罐的有效容积 为80000m3,丙烷低温储罐为双金属壁全防罐。为了维持卸船总管的温度,节省卸船准备时间,设置了两台丙烷预冷泵 (19P0102-1/2),一开一备,间断操作,对卸船总管进行预冷。因冷量损失及卸船操作时液体丙烷的闪蒸及体积置换,丙烷低温储罐会产生
43、蒸发气体(BOG),设置三台丙烷BOG压缩机,将产生的蒸发气体压缩至87MPa(G), 之后在丙烷冷凝器(19E0101)与循环水换热,进行冷凝,凝液进入丙烷缓冲槽 (19D0101),通过BOG冷凝液输送泵(19P0103-1/2)将凝液送至丙烷脱氢装置,为 了保持操作灵活性,凝液也可以通过相应管线回到丙烷低温储罐或业主张家港库 区的LPG球罐。丙烷低温储罐设置了四台丙烷输送泵(每个丙烷低温储罐两台丙烷输送泵, 并预留一个丙烷输送泵的泵井),给丙烷脱氢装置供料,四台丙烷输送泵(2开2 备)满足两套66万吨/年丙烷脱氢装置的供料要求。非卸船操作时,丙烷低温储罐的压力在512kPa(G)范围内,
44、卸船时丙烷低温 储罐的压力控制在13kPa(G);当储罐压力超过17kPa(G),应打开储罐压力控制 阀,将BOG气体导入全厂低温低压火炬,避免丙烷低温储罐的压力继续上升。丙烷低温储罐设置有两组液位计、一个高液位和一个低液位开关,监控丙烷 低温储罐的液位。丙烷低温储罐不同液层高度处、吊顶上部气相空间及吊顶下部气相空间设置 有温度检测点,用于丙烷低温储罐正常运行时温度监测;内罐侧壁内表面及内罐 底板内表面设置有多个温度检测点,用于监测丙烷低温储罐初次预冷时温度;外 罐与内罐环隙的底部设有多点的温度检测点,用于监测内罐可能出现的泄露。10中间罐区自精馏工段送来的产品丙烯通过管道送入丙烯储罐(19T
45、0201-16)储存, 单个储罐装填满后,取样分析,合格后可以送往下游聚丙烯装置或装车外运,如 果产品指标不达标,则可以通过不合格丙烯泵19P0202循环回丙烷脱氢装置处 理。丙烷脱氢装置停工时,系统中的液态C3等可以排至空的丙烯储罐或标记好的不合格丙烯储罐。通过丙烯输送泵(19P0201-1/2)为聚丙烯装置供料或通过丙烯装车泵 (19P0204)将丙烯送至装车站进行装车,用倒罐泵Q9P0203)进行储罐之间的 倒罐。丙烯储罐(19T0201-16)排放的不合格丙烯送入脱水罐(19T0202)脱水 后,通过不合格丙烯泵(19P0202)送至2105装置的SHP反应器。来自PDH装置的燃料油经
46、管道送入燃料油罐(19T0203)储存,通过燃料油 输送泵(19P0205)送至锅炉或装车站进行装车。11火炬本项目设置一套地面火炬系统,用于处理低温罐区、丙烷脱氢装置、聚丙烯 装置等事故或火灾工况时排放的放空气。地面火炬系统可保证各装置产生的放空 气能够及时、安全、可靠地燃烧,并满足相关的环保要求。本套火炬系统为封闭式地面火炬,由低温低压冷火炬、低温高压火炬、常温 高压火炬组成,热辐射强度小于5kW/m2,噪音小于75dBA,排放气均满足环保要 求。(1)工艺排放系统管线低温罐区低温低压冷火炬管线低温罐区低温低压冷火炬气经管道(FGLT-01001)输送至分液罐(27D0101), 由分液罐
47、(27D0101)分液后火炬气进入燃烧器,燃烧后放空;分液罐(27D0101) 内分离出的凝缩液由凝液泵(27P0101)送出界区进行处理。常温高压火炬管线丙烷脱氢装置精馏工段、反应工段等工段的热火炬气经管道(WF-01002、DF -01002等)输送至分液罐(27D0102),由分液罐(27D0102)分液后火炬气进 入燃烧器,燃烧后放空;分液罐(27D0102)内分离出凝缩液由凝液泵(27P0102) 送出界区进行处理。低温高压火炬管线丙烷脱氢装置精馏工段、冷箱工段等工段冷火炬气经管道(DF-01002、WF -01002等)及阻火器后进入燃烧器,燃烧后放空。(2)燃料气管线燃料气自界区
48、外经管道接入火炬界区后,分成各路支管分别接至各个长明灯,用作长明灯燃烧的燃料。(3)蒸汽管线蒸汽的主要作用是为火炬气消烟助燃。对于分级燃烧系统中的每一级蒸汽消 烟系统,均对应设置独立的蒸汽管线,而且每一级消烟蒸汽管线上均设自动调节 阀。当防风墙内可燃气体浓度超高报警时,这时自动启动蒸汽吹扫系统,对防风 墙内可燃气体进行稀释、吹扫。(4)氮气管线氮气为各级燃烧器提供吹扫置换用气,防止空气倒灌,确保安全。氮气吹扫管线分成若干支管接入各级燃烧系统。氮气管线上设有自动切断 阀。当某一级火炬气排放结束时,在火炬气管道内会出现真空现象,这时迅速打 开对应的氮气开关阀,对该级火炬气管道和燃烧器进行氮气吹扫,
49、防止空气侧灌。 氮气吹扫时间约10分钟。(5)新鲜水管线新鲜水为各水封罐提供补水来源。补水管线上均设气动调节阀,根据水封罐 的水封要求进行自动挖制。(6)仪表风管线仪表风作为各气动阀门的仪表风气源。(7)凝缩油管线凝缩油管线用于排除分液罐内的凝缩液。分液罐设有凝缩液泵,根据液位变 送器控制凝缩液泵的开启。凝缩液管将火炬气凝结液送出界区进行处理。(8)污水管污水管用于排除水封罐内的含油污水。水封罐溢流水排至污水池。溢流水管线采用U形弯设计。U形弯的高度大于7.5m,在U形弯内可以形成 二次水封,避免火炬气通过U形弯泄放到大气中。火炬系统控制设有长明灯火焰位测和电视监视系统、电点火装置控制、分级
50、燃烧控制系统、蒸汽消烟系统、可燃气体监测和蒸汽吹扫系统、分液罐液位控制 及水封高度控制。封闭式地面火炬采用圆柱形封闭式结构,由地面火炬炉膛、炉膛支往、地面 燃烧器、防风墙、分级燃烧系统以及长明灯自动点火装置组成。地面火炬炉膛排放气的燃烧是完全在圆柱形炉膛内完成的。燃烧过程完全封闭,外界看不 见火光,没有光污染,热辐射较低。炉膛外壳用Q345R制成,内衬有轻质耐火耐 高温陶瓷纤维。陶瓷纤维的耐火度大于1790C,可持续使用在1200C的环境中, 其不受下雨或炉膛温度急速变化的影响,同时还具有良好的吸音降噪特性。整座炉膛均使用陶瓷纤维折叠块,不需要利用钢丝网进行固定,没有任何金 属部件暴露在火焰中
51、。由于钢丝网长期暴露在火焰中的寿命有限,因此采用陶瓷 纤维折叠块,其锚固件是暗藏在折叠块内的。地面燃烧器地面火炬炉膛内设有特殊结构的地面燃烧器。地面燃烧器采用梅花形多孔结 构,可将大股的火炬排放气分成许多小股,以利于空气混合,增加与空气接触面 积,达到无烟燃烧。空气与排放气的混合主要是依靠排放气自身的压力和特殊设 计的燃烧器来完成。梅花形多孔燃烧器在炉膛内呈几何均匀布置,以充分利用空气。燃烧器由耐 热不锈钢材料制成,以保证其长寿命。防风墙地面火炬炉膛外围设有防风墙,可防止炉膛底部侧风对地面燃烧过程的影 响。防风墙用钢筋混凝土制成,可最大限度地降噪和防止热辐射外漏,同时又可 有效阻止操作人员进入
52、炉膛高温区域。防风墙内铺设有小卵石,以增加地面抗热辐射的能力并可有效抵消噪音。防 风墙上设有火焰观察孔。长明灯及点火装置地面火炬炉膛内设有长明灯,长明灯保持常燃,以便任何时刻有排放气排放 都能及时点燃,以确保系统的绝对安全。长明灯的配置和燃烧器的布置息息相关, 通过特殊的燃烧器布置,不仅保证地面火炬安全可靠运行,而且可以减少长明灯 数量、节约燃料气消耗。长明灯采用了引射技术,为高效节能型长明灯,不仅燃料气耗量低,而且可 靠性高,能够在风、雨、雪等各种恶劣环境下保持燃烧。每台长明灯设一套电点火装置。电点火装置由高能发生器、控制面板、高压 导线及发孤装置组成。直接电点火方式与传统的内传焰点火方式相
53、比,具有能量 大、设备体积小、操作简单方便、使用安全可靠等特点。电点火装置可实现自动操作、现场手动操作和中控室遥操。自动点火系统利 用紫外线信号对长明灯燃烧状态进行判断,当长明灯熄灭,控制系统自动启动电 点火装置,重新点燃长明灯。地面火炬的燃烧过程排放气进入地面火炬集气总管后首先通过第一级燃烧器喷出并被长明灯的 火焰引燃。如果排放气量较大,第二级燃烧系统及以后各级燃烧系统上的压力控 制阀会分别开启并参与燃烧。燃烧后的热烟气在炉膛拔力作用下,从炉膛顶部排出,从而在燃烧区域形成 了一定负压,这样外界的空气就能够自动地通过防风墙从炉膛底部源源不断地进 入炉膛内,以保证排放气燃烧所需要的足够的空气量。
54、进入炉膛的空气一方面与 均匀分布的特殊结构的地面燃烧器相配合,使排放气与空气达到最佳混合,从而 实现无烟燃烧;另一方面多余的空气进一步与烟气混合从而有效地降低烟气排出 温度,极大减少烟气对周围环境的热辐射能力。同时由于排放气燃烧火焰及燃烧高温区域均封闭在炉膛内,从而避免了排放 气燃烧时火焰热辐射的外泄,因此外界看不见火光,热辐射较低。除此之外,由于炉膛内壁和防风墙内均衬有轻质耐火耐高温陶瓷纤维,该材 料本身具有良好的吸音降噪特性,可把排放气的燃烧看成是在一个性能良好的消 音器内完成的,因此地面火炬还具有低噪音运行特点。12空压站及氮气辅助系统空压站本空压站为扬子江丙烷脱氢项目全厂(包括一期丙烷
55、脱氢主装置、聚丙烯装 置、低温罐区及中间罐区、火炬等辅助设施及辅助系统)提供开车及正常运行时 所需的工厂空气和仪表空气,保证全厂工厂空气和仪表空气的正常用量及最大用 量。考虑二期丙烷脱氢装置增加的空气用量,预留了新增空压机组的位置。本装置仪表空气及工厂空气均采用相同处理方法制得,规格品质相同。故本 项目拟选择三台公称能力为50Nm3/min的螺杆压缩机(两开一备)将空气压缩到 2MPaA后经高效除油器除油、微热再生干燥器除水和粉尘精滤器除尘,将空气净 化到工艺规定要求进入仪表空气缓冲罐,再分别减压送入工厂空气、仪表空气管 网。在本空压站设有一台有效容积约300m3的仪表空气储罐,保证全厂仪表空
56、气 大约1530分钟的用量;同时设有一台有效容积约300m3的工厂空气储罐,保证 全厂工厂空气大约1530分钟的用量。仪表空气储罐和工厂空气储罐可以互为备 用,也可以同时作为工厂空气或仪表空气储罐使用。本项目用气情况见表2.5.1表2.5.1空气用量统计表PA用量IA用量正常(Nm3/h)最大(Nm3/h)正常(Nm3/h)最大(Nm3/h)丙烷脱氢主装置0200011401300聚丙烯装置31538525003085含硫/盐废水处理5405403050罐区及其它辅助系统540700合计855200042105135其中:(1)PA为各装置间断使用,不考虑间断用量与正常用量的叠加,故选择 20
57、00Nm3/h作为全厂最大PA用量。(2)原料罐区、中间罐区、冷箱、PSA、火炬等装置及其他公用工程量合并 统计,数据见上表“罐区及其它辅助系统”。(3)空压站正常供气量考虑为正常PA用量+正常IA用量,即按5065Nm3/h 设置。(4)空压站最大供气量为最大PA用量+最大IA用量,即按7135Nm3/h设置。(5)空压机的配置选择按:正常供气时,两开一备、单台流量约为 50.65Nm3/min ;最大供气量时,三台全开,单台流量为47.56Nm3/min ;故选择三 台公称处理量50Nm3/min的螺杆机组为本项目提供仪表空气及工厂空气;氮气辅助系统本氮气辅助系统为扬子江丙烷脱氢项目全厂(
58、包括一期丙烷脱氢主装置、聚 丙烯装置、低温罐区及中间罐区、火炬等辅助设施及辅助系统)提供开车及正常 运行时所需的氮气,保证全厂氮气的正常用量及最大用量。本项目所需氮气由气体公司外供,采用管道输送的方式将氮气送至界区交接 点,界区点氮气规格为5MPaG、常温;在本项目厂区内设置一个有效容积约200m3 的氮气缓冲罐,5MPaG、常温的氮气经缓冲、减压后进入全厂氮气管网,氮气缓 冲罐保证全厂大约20分钟的氮气用量;为保证催化剂连续再生工段的独立连续操作,采用单独的管线为一期和二期催化剂连续再生工段提供氮气。本项目用氮气情况见表2.5.2表2.5.2氮气用量统计表氮气用量正常(Nm3/h)最大(Nm
59、3/h)间断(Nm3/h)丙烷脱氢主装置325215010000聚丙烯装置260051294448罐区及其它辅助系统91032362750合计38356258.510000其中:(1)本装置正常氮气用量3835Nm3/h,为各装置正常用气量之和,其中在 非正常工况及聚丙烯装置最大用量下峰值氮气用量约为6258.5Nm3/h;(2)本装置氮气最大消耗量不考虑各装置最大消耗量同时叠加,氮气最大 用量考虑丙烷脱氢主装置正常用量与聚丙烯装置正常用量、罐区及其他辅助系统 最大用量及少量余量之和;(3)间断用气流量为各工段在开停车时吹扫及置换瞬时使用,间断用气流 量按最大用户确定,故按丙烷脱氢主装置间断流量考虑,不考虑各用户开、停车 流量的叠加。13本项目涉及的主要化学反应主反应:C3H8 一 C3H6 + H2副反应:CH 一 CH + CH3 82 44副反应:2CH CH + CH + H3 64 62 22选择性加氢:CH + H CH34236洗气塔碱液喷淋涉及反应:O.7H2S+NaOH一 0.3Na2S + 0.4NaHS + H2O
- 温馨提示:
1: 本站所有资源如无特殊说明,都需要本地电脑安装OFFICE2007和PDF阅读器。图纸软件为CAD,CAXA,PROE,UG,SolidWorks等.压缩文件请下载最新的WinRAR软件解压。
2: 本站的文档不包含任何第三方提供的附件图纸等,如果需要附件,请联系上传者。文件的所有权益归上传用户所有。
3.本站RAR压缩包中若带图纸,网页内容里面会有图纸预览,若没有图纸预览就没有图纸。
4. 未经权益所有人同意不得将文件中的内容挪作商业或盈利用途。
5. 装配图网仅提供信息存储空间,仅对用户上传内容的表现方式做保护处理,对用户上传分享的文档内容本身不做任何修改或编辑,并不能对任何下载内容负责。
6. 下载文件中如有侵权或不适当内容,请与我们联系,我们立即纠正。
7. 本站不保证下载资源的准确性、安全性和完整性, 同时也不承担用户因使用这些下载资源对自己和他人造成任何形式的伤害或损失。