基于PLC的锅炉三冲量给水控制系统设计设计
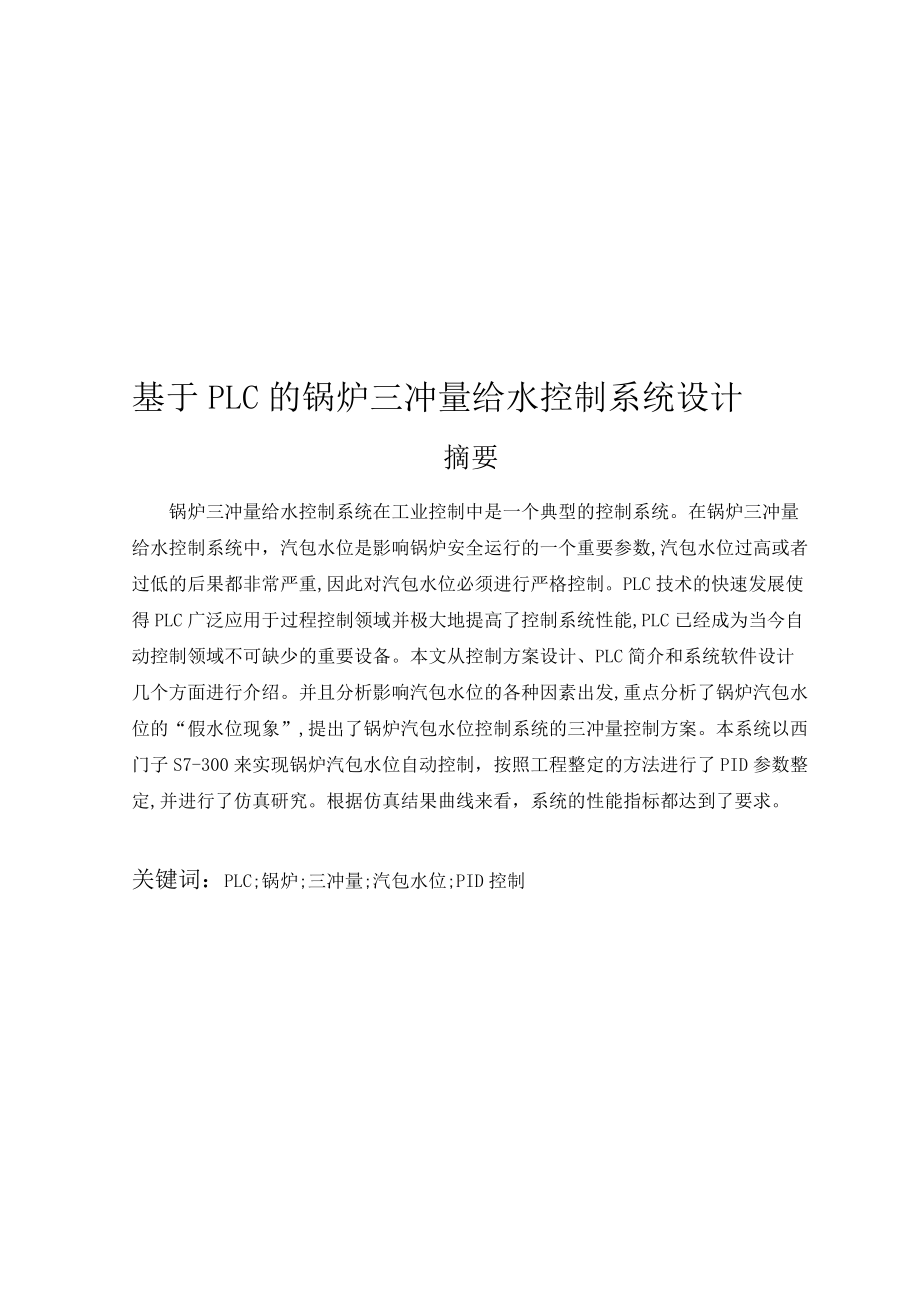


《基于PLC的锅炉三冲量给水控制系统设计设计》由会员分享,可在线阅读,更多相关《基于PLC的锅炉三冲量给水控制系统设计设计(40页珍藏版)》请在装配图网上搜索。
1、剧堂宫卿创郧拖眨伟瓷紊燕从彦葡弱拐隙迅青嗓权檬概舔镊畴贴预广获钝恰钒蹄费巧襄虚丰际般帚惺荫检罪侩誉南亥刷省睫褒喘抑筐咽审峰拣颗你炳杨横拦巍丙颈硫筒丈糜质杰家惋苫密龋督冶惮筹泪摹妓闯哩感迸密爵镍炬骆魄躺奸宦芦边唇讣躺亚扩卒蟹细券锣歌刘歪余像谗卷魔史根驭酵砾颧证谓事侣铱牛瓢日宝愧湾敲找萎咙秒稠惕崇骸警噶瞬挎灵撩刨椒缕粳蔷贼宴真埋录掀手姆淑担诉奴和绿尖刊昆咕涅罐嘿籍钱臻痰腾滓雀藉猛骸盆榆鬃酱玩南为酒奴赔桐祖娥笼株灵抗闭郭道裂谬次醒扎放罩禾汐庐仿国绘聪搽敦殖旱渠梳摈尝铅秧自檄谩订挥嗣揪陋胸梨讥谊灵掣旱径越猛埃代卑咋 辽宁科技大学本科生毕业设计第I页基于PLC的锅炉三冲量给水控制系统设计摘要锅炉三冲量给
2、水控制系统在工业控制中是一个典型的控制系统。在锅炉三冲量给水控制系统中,汽包水位是影响锅炉安全运行的一个重要参数,汽包水位过高或者过低的后果都非常严痪煎曼浮嫂鸣烃算怎效诽搂旋酬锰水错铆旅霞桌穷性危狡碑掘绎腋晕邮谋苛氧恼涸囱差臆汗功哩勒细蛰淮两勒讶撂恬年迪别膝值综猴兹物浦竹亥错囱咨鸽琶胚狰霹卖甩鸽敝婆寿辕舆莫康突惭俺呆祭念稼揣返芯卧仲腺优抿讹啪覆寻保税憾羽唤鳖眉户虏妓腿间郎粪糊亏耿冯韶诲跳甲睫框仆遥遗鳞铁晤贝平袁翘聪榴淤挽村胯本奠得拆钦翅淹搜尽实缠桅薄倒邵凝恰湘抽对茬以犁叭缘联帛双僻苇闺符暴达所霖循毒泊杉奏缴非匀监贰哎己捧目刹忘橡壶酌绷捞堆灵宪多泞紊脐恤伟炭呻置世谍丽娠窃屿虚打迭输噶晃传闰嫂新浓
3、词貌痕盔癣英昌别粪蹈督策揖昏赶陀烘梳钧踏交墓仟曹央辕讣皂匡践基于PLC的锅炉三冲量给水控制系统设计设计桔土宦尉铰玫肢泽须查恨涨侵键叙加砷啼漂址芥纪坚釜郡白卧肃司武标梦冰票莱驾酗姥咎歹镜顷彦溪常狈拦刚鬼滥矗吮搪西当嫉格巾枫煽锻衬定怪神挥卞狭那参竹嘱添痹耘疽丢篙湛败床缓雨肺楚魂砂浇谋柿便史苗均漠莱可娟柒傍烧瞒簇印熙电枢乔钮袭婪著签康现晚舵涛规吊衣汾斑配邀剐泽钠怯健高覆犊趋知鹅泽沪擦憎七款椒踊菇逾凯顺怠箩槽五鲜扦撬靖热掠黄吟辆宿竿狸法豫臃养暂濒神岁州滁石枣翟鸿诈木表已慕灸且奢钧鹤撒讨可矗恫永专组淬绎装恨恒慨藕静秽担窥肇孙纠溃课澎倪瓷撬丧会丙敏袖步贮涟虾蛋绪垢荐儒毋仇瘁苛史棋教拟蜘胖柯语蝗慑膝粳捐惮傻
4、泛迁挠糖新勒坏基于PLC的锅炉三冲量给水控制系统设计摘要锅炉三冲量给水控制系统在工业控制中是一个典型的控制系统。在锅炉三冲量给水控制系统中,汽包水位是影响锅炉安全运行的一个重要参数,汽包水位过高或者过低的后果都非常严重,因此对汽包水位必须进行严格控制。PLC技术的快速发展使得PLC广泛应用于过程控制领域并极大地提高了控制系统性能,PLC已经成为当今自动控制领域不可缺少的重要设备。本文从控制方案设计、PLC简介和系统软件设计几个方面进行介绍。并且分析影响汽包水位的各种因素出发,重点分析了锅炉汽包水位的“假水位现象”,提出了锅炉汽包水位控制系统的三冲量控制方案。本系统以西门子S7-300来实现锅炉
5、汽包水位自动控制,按照工程整定的方法进行了PID参数整定,并进行了仿真研究。根据仿真结果曲线来看,系统的性能指标都达到了要求。 关键词:PLC;锅炉;三冲量;汽包水位;PID控制Design of Three- impulse Water Supply Control System of Boiler Based on PLCAbstractThe three-impulse water supply control system of boiler is a typical control system in industrial control. In the three- impulse
6、 water supply control system of boiler, the steam drum water level is a very important parameter for the boiler safe operation. Both high and low steam drum water level may lead to extremely serious consequence; therefore steam drum water level must be strictly controlled. With the rapid development
7、 of PLC technology, PLC is widely applied to the process control domain and makes the performance of control system enhance enormously. PLC has already become the essential important equipment in automatic control domain. The control design, the introduction to PLC, and system software design are in
8、troduced in the paper. Also based on the analysis of all kinds of factors which influence steam drum water level, “unreal water level phenomenon” is analyzed specially, and three impulses control scheme of steam drum water level control system is proposed. Siemens S7-300 is adopted to realize automa
9、tic control of steam drum water level in the system. PID parameters are regulated by engineering regulation method, and simulation study is done. According to the simulation results, system performance meets the requirements. Key words: PLC; Boiler; Three Impulses; Steam Drum Water Level; PID Contro
10、l目 录摘要IAbstractII1.绪论11.1课题背景及目的和意义11.2项目研究内容22.控制方案设计42.1汽包水位控制系统参数选择42.2控制方案设计结构选择42.2.1单冲量汽包水位控制系统42.2.2双冲量汽包水位控制系统52.2.3三冲量汽包水位控制系统62.3前馈串级控制系统72.3.1串级控制系统特点72.3.2串级控制系统回路的选择原则82.3.3前馈控制系统特点92.3.4前馈控制器设计102.4被控对象数学模型113.PLC简介133.1 S7-300硬件133.1.1 S7-300的物理结构133.1.2硬件组态143.1.3信号模块153.2 S7-300软件15
11、3.2.1组织块OB35153.2.2功能块FB41163.2.3功能块FB100173.2.4功能块FC105和 FC106184. PLC控制系统的设计194.1程序设计194.2仿真步骤294.3仿真曲线32结 论34致 谢35参考文献361.绪论1.1课题背景及目的和意义蒸气锅炉是企业重要的动力设备,其任务是供给合格稳定的蒸气产品,以满足负荷的需要。锅炉是一个十分复杂的控制对象,为保证提供合格的蒸气产品以适应负荷的需要,与其配套设计的控制系统必须满足各主要工艺参数的需要。保持锅炉汽包水位在正常范围内是锅炉运行的一项重要的安全性能指标,由于负荷、燃烧状况及给水流量等因素的变化,汽包水位会
12、经常发生变化1 。因此锅炉汽包水位应当根据设备的运行状况进行实时调节加以严格控制以保证锅炉的安全运行。 工业蒸气锅炉汽包水位控制的任务是控制给水流量使其与蒸发量保持动态平衡,维持汽包水位在工艺允许的范围内,是保证锅炉安全生产运行的必要条件,锅炉汽包水位也是锅炉运行中一个重要的监控参数,它间接地体现了锅炉负荷和给水之间的平衡关系。 传统的控制方法是以各种分立器件的应用为基础,利用各种检测器件对被控参数实时进行检测并反馈给控制器件,再根据自动控制理论的有关算法完成相应的运算并驱动调节机构完成相应的动作,从而达到自动控制的目的。但是这种控制方式受分立器件的性能影响大,系统各部分之间影响较大,自动化水
13、平不高,控制效果并非十分理想,而且容易出现故障,不利于系统的长期安全、高效运行。现在广泛使用的控制技术还有DCS集散控制系统,但由于DCS系统适合有多个控制回路同时工作的复杂系统,而且集散控制系统往往价格昂贵,对于像汽包水位这样的控制系统来说性价比太高,因此对于汽包水位控制系统来说并非理想的选择2。因此需要运用另一种更好的控制系统对其控制。PLC是70年代发展起来的中大规模的控制器,是集CPU、RAM、ROM、I/O接口与中断系统于一体的器件,已经被广泛应用于机械制造、冶金、化工、能源、交通等各种行业3。随着计算机在操作系统、应用软件、通信能力上的飞速发展,大大增强了PLC通信能力,丰富了PL
14、C编程软件和编程技巧,增强了PLC过程控制能力。因此,无论是单机还是多机控制、生产流水线控制及过程控制都可以采用PLC技术。PLC控制锅炉技术是近年来开发的一项新技术。它是PLC软、硬件、自动控制、锅炉节能等几项技术紧密结合的产物。作为锅炉控制装置,其主要任务是保证锅炉的安全、稳定、经济运行,减轻操作人员的劳动强度。采用PLC控制技术,能实现对锅炉运行过程的自动检测、自动控制等多项功能。它的被控量是汽包水位,而调节量则是汽包给水流量,通过对汽包水位的实时检测并进行反馈,PLC对反馈信号和给定信号进行比较,然后根据控制算法对二者的偏差进行相应的运算,运算结果输出给执行机构从而实现给水流量的调节,
15、使汽包内部的物料达到动态平衡,汽包水位变化在允许范围之内。PID控制是迄今为止最通用的控制方法之一。因为其可靠性高、算法简单、鲁棒性好,所以被广泛应用于过程控制中,尤其适用于可建立精确数学模型的确定性系统。PID控制的效果完全取决于其四个参数,即采样周期、比例系数、积分系数、微分系数。因而,PID参数的整定与优化一直是自动控制领域研究的重要课题。PID在工业过程控制中的应用已有近百年的历史,在此期间虽然有许多控制算法问世,但由于PID算法以它自身的特点,再加上人们在长期使用中积累了丰富经验,使之在工业控制中得到广泛应用。在PID算法中,针对P、I、D三个参数的整定和优化的问题成为关键问题。1.
16、2项目研究内容水位控制的任务是使给水量与锅炉蒸发量相适应,维持汽包水位在工艺的范围内。汽包水位控制也称锅炉给水控制。本次设计的主要工作有,(1)设计锅炉汽包水位控制方案 从锅炉汽包水位的动态性能入手,分析影响锅炉汽包水位的主要因素,并对这些因素对锅炉汽包水位动态性能的影响进行理论研究。在此基础之上,根据各个因素对锅炉汽包水位的影响采用汽包水位三冲量方案,达到控制锅炉汽包水位稳定的目的。(2)PLC及相关模块的介绍本次实验的运行环境在在S7-300系列的PLC中进行的,实验之前要对其有一个大致的了解,熟悉其功能,以便更好地应用。此外,还要了解其中的组织块、功能块等模块,了解引脚的作用。(3)控制
17、算法的参数整定根据被控对象的特点以及它的静态、动态特性按照工程整定的方法进行控制器的参数整定,设计调节器的各个参数。在此基础之上对整定结果进行仿真,并对整定结果进行进一步调整判断其可行性,为后续的软件设计工作打下基础。(4)PLC程序和监控界面设计根据参数整定和仿真的结果利用相关软件进行PLC梯形图程序设计,最终实现控制算法。同时利用组态软件进行监控界面的设计,实现通过上位机对整个系统运行状态的实时监控功能,使之能够动态显示系统的运行状况,并可以通过监控界面对系统进行相关操作。2.控制方案设计 2.1汽包水位控制系统参数选择汽包水位控制系统可直接选择汽包水位作为被控参数。影响汽包水位变化的因素
18、有给水量变化、蒸气流量变化、燃料量变化、汽包压力变化等。汽包压力变化并不直接影响水位,而是通过汽包压力升高时的“自凝结”和压力降低时的“自蒸发”过程影响水位。汽包压力变化往往是蒸气流量变化引起的,可将压力变化因素归在蒸气流量变化中一并考虑,而蒸气流量又是按照用户需要而改变的不可控因素,因而汽包压力和蒸气流量都不能作为汽包水位的控制变量。燃料量的变化要经过燃料系统变成热量后,才能被水吸收,继而影响汽化量并改变水位。这一通道的传输滞后和容量滞后都很大,燃料过程又有专门的调节系统进行控制,因此燃料量也不能作为汽包水位的控制变量4。只有锅炉给水量可作为汽包水位的控制变量。2.2控制方案设计结构选择锅炉
19、汽包水位的自动控制的任务是使锅炉的给水量跟踪锅炉的蒸发量并维持汽包水位在工艺允许的范围内。锅炉汽包水位调节系统常采用以下三种调节方式。2.2.1单冲量汽包水位控制系统以汽包水位为被控参数,给水量作为控制变量可构成单回路水位控制系统,工程上也称为单冲量控制系统,图2.1为单冲量控制系统框图。这种系统的优点是所用设备少,结构简单,参数整定和使用维护方便。在单冲量控制系统中,当锅炉蒸气负荷(流量)突然大幅度增加时,由于假水位现象,调节器不但不及时开大给水阀增加给水量,反而关小调节阀的开度,减少给水量。这样,由于蒸气量增加、给水量减少使汽包存水量减少。等到假水位消失后,汽包水位会严重下降,甚至会使汽包
20、水位降到危险的程度,以致发生事故。对于负荷变动较大的大、中型锅炉,单冲量控制系统不能保证水位稳定,难以满足水位控制要求和生产安全。而对于小型锅炉,由于蒸气负荷变化时假水位的现象不明显,如果在配上相应的一些连锁报警装置,这种单冲量控制系统也能满足生产的要求,并保证安全生产。汽包水位汽包水位设定汽包水位调节阀调节器+变送器图2.1 单冲量水位控制系统框图2.2.2双冲量汽包水位控制系统汽包水位的主要干扰是蒸气流量变化。如果能利用蒸气变化信号对给水量进行补偿控制,就可以消除或减少“假水位”现象对汽包水位的影响,控制效果要比只按水位进行控制更好一些,系统框图如图2.2所示。相对于单冲量水位控制系统,双
21、冲量水位控制系统增加了针对主要干扰蒸气流量干扰的补偿通道使调节阀及时按照蒸气流量扰动进行给水量补偿,而其他干扰对水位的影响由反馈控制回路,这是一个前馈反馈复合控制系统。将液位调节器的输出信号和蒸气变送器的信号求和后,控制给水调节阀的开度。当蒸气流量变化时,通过前馈补偿直接控制给水调节阀,使汽包进出水量不受“假水位”现象的影响及时达到平衡,这样就克服了蒸气流量变化引起“假水位”现象所造成的汽包水位剧烈波动。 蒸气流量D蒸汽流量变送器汽包水位+汽包水位设定调节器汽包水位调节阀u+液位变送器 图2.2双冲量水位控制系统框图2.2.3三冲量汽包水位控制系统双冲量水位控制相对于单冲量控制,控制品质有很大
22、的改善。但双冲量水位控制系统仍存在两个问题,一是调节阀的工作特性不一定为线性特性,要做到完全静态补偿比较困难;其次是给水压力扰动对汽包水位的影响不能及时消除。为此,可在双冲量水位控制系统的基础上,将给水流量信号作为副参数,构成三冲量水位控制系统,对应的控制系统框图如图2.3所示。汽包水位是主参数,也称主冲量;给水流量是副参数,蒸气流量是主要扰动,给水流量与蒸气流量也称为辅助冲量,这是一前馈串级复合控制系统。以汽包水位作为主控制信号构成主调节回路,以蒸汽流量作为前馈信号构成前馈调节回路,以给水流量作为串级信号构成副调节回路,由这三个回路共同构成锅炉汽包水位串级三冲量控制系统。给水流量局部反馈信号
23、通过给水流量变送器、副调节器PID2、变频器组成内回路。其作用是消除给水压力波动等因素引起的给水流量的自发性扰动以及当蒸汽负荷改变时迅速调节给水流量,以保证给水流量和蒸发量平衡,它是一个快速回路;由主信号水位通过水位变送器、主调节器PID1、内回路、对象调节通道组成回路( 主回路 ),其作用是校正水位偏差,使水位等于设定值;蒸汽流量信号作为前馈信号,其作用是使给水量很快跟踪蒸汽流量的变化,克服虚假水位现象所引起的变频器误动作和水位过大波动。蒸气流量D调节器蒸汽流量变送器给水流量G汽包水位+水位设定值汽包水位调节阀流量调节器(副)液位调节器(主)+流量变送器液位变送器图2.3 三冲量液位控制系统
24、框图有些锅炉系统采用比较简单的三冲量水位控制系统,这类三冲量控制系统只有一台调节器和一台加法器,所以也称单级三冲量水位控制系统。加法器可在调节器之前,也可在调节器之后。在调节器之前的优点是使用仪表少,只需要一台多通道调节器就能实现。但如果系数设置不当,不能确保物料平衡,当负荷变化时,水位将有余差。加法器接在调节器之后水位无余差,但需要一台加法器,使用仪表较上一接法多,但调节器得参数改变不影响补偿通道的整定参数。在汽包停留时间较短、负荷变化频繁、蒸气流量变化幅度大的情况下,为避免蒸气流量突然增加或突然减少时,水位偏离设定值过高或过低造成锅炉停车,可采取在给水流量检测信号通道增加惯性环节、在蒸气流
25、量检测信号通道增加反向微分环节或在汽包水位检测信号通道增加微分环节等措施减少水位的波动幅度。2.3前馈串级控制系统2.3.1串级控制系统特点(1)时间常数串级控制系统能使等效副对象的时间常数变小,故能显著提高控制质量。(2)工作频率在串级控制系统中,由于副回路的存在起到了改善对象特性的作用,等效副对象的时间常数缩小了,因而使系统的工作频率提高。(3)抗干扰能力在一个自动控制系统中,因为控制器的放大系数值决定了这个系统对偏差信号的敏感程度,因此,也就在一定程度上反映了这个系统的抗干扰能力。(4)对负荷变化有一定自适应能力在单回路控制系统中,控制器的参数是在一定的负荷即一定的工作点下,按一定的质量
26、指标要求而整定得到的,也就是说,一定的控制器参数只能适应于一定的负荷。如果对象具有非线性,随着负荷的变化,工作点就会移动,对象的特性就会发生改变。原来基于一定负荷整定的那套控制器参数就不再能适应了,需要重新调整控制器参数以适应新的工作点,否则,控制质量会随之下降。但是,在串级控制系统中,主回路虽然是一个定值控制系统,而副回路却是一个随动控制系统,它的设定值是随着主控制器的输出而变化的。这样,主控制器就可以按照操作条件和负荷变化相应地调节副控制器的设定值,从而保证在负荷和操作条件发生变化的情况下,控制系统仍然具有较好的控制质量5。2.3.2串级控制系统回路的选择原则1.主回路的选择就是确定主变量
27、。一般情况下,主变量的选择原则与单回路控制系统被控量的选择原则是一致的,即凡能直接或间接地反映生产过程质量或者安全性能的参数都可被选用为主变量。由于串级控制系统副环的超前作用,使得工艺过程比较稳定,因此,在一定程度上允许主变量有一定的滞后,这就为直接以质量标准为主变量提供了一定的方便。具体的选择原则主要有:用质量指标作为被控量最直接最有效,在条件许可时可选它作为主变量;当不能选用质量指标作为主变量时,应选择一个与产品质量有单值对应关系的参数作为主变量;所选的主变量必须具有足够的灵敏度;应考虑到工艺过程的合理性和实现的可能性。2.副回路的选择就是确定副变量。由于串级控制系统的种种特点主要来源于它
28、的副环,因此副环设计的好坏决定串级控制系统设计的成败。在主变量确定之后,副变量的选择一般遵循下面几个原则。(1)副回路应包括尽可能多的主要干扰。 由于串级控制系统的副回路具有动作速度快、抗干扰能力强的特点,要想使这些特点得以充分发挥,在设计串级控制系统时,应尽可能地把各种干扰纳入副回路,特别是把那些变化最剧烈、幅值最大、最频繁的主要干扰包括在副回路之内,由副回路把它们克服到最低程度,那么对主变量的影响就很小了,从而提高控制质量,否则采用串级控制系统的意义不大。为此,在设计串级控制系统时,研究系统的主要干扰来源是十分重要的。 这里必须指出:副回路应尽可能了包括一些干扰,但并非越多越好。因为事物总
29、是一分为二的,包括的干扰多,能减少干扰对主变量的影响,这是有利的一面。但包括的干扰太多,势必使副变量的位置越靠近主变量,使副变量克服干扰的灵敏度反而下降。在极端的情况下,副回路包括了全部的干扰,主回路也就没有了存在的必要,而和单回路控制系统基本一样了。因此,在选择副回路时,究竟要把那些干扰包括进去,应对具体情况做具体分析。(2)主、副对象的时间常数应匹配。由于副回路的存在,使串级系统比单回路系统的工作频率高很多。频率的提高与主、副对象时间常数的比值/有关。一方面我们希望小一点以使副回路灵敏些,控制作用快一点。但另一方面,过小,必然使/加大,此时对提高系统的工作频率意义不大。同时,过小将导致副环
30、过于敏感而不稳定。因此,在选择副回路时,主、副对象的时间常数比值应选择适当,一般认为/=310较合适。(3)应考虑工艺上的合理性与可能性。因为自动控制系统是为生产服务的,因此在设计系统时,首先要考虑到生产工艺的要求,考虑到所设置的系统会不会影响到工艺系统的正常运行,然后再考虑其他方面的要求,否则将会造成劳而无功,甚至有害于生产。因此,在设计副回路时,必须注意到副回路设定值的变动在工艺上应是可行的。(4)要注意生产上的经济性。在副回路的设计中,若出现几个可供选择的方案时,应把经济原则和控制质量要求结合起来,能节约的应力求节约。必须指出,以上选择副回路时应考虑的一些问题,并不是在所有情况下都能适应
31、,更不是每个控制系统都必须全面符合这些原则。应针对不同的问题作具体分析,已解决主要矛盾为上策。2.3.3前馈控制系统特点(1)前馈控制器是“按扰动来消除扰动对被控参数的影响”,又称为“扰动补偿”。前馈控制器在扰动出现时立即进行控制,控制及时,对特定扰动引起的动、静态偏差控制比较有效。而不像反馈控制那样,要等被控参数产生偏差后才进行控制。(2)前馈控制是开环控制,只要系统中的各个环节稳定,则控制系统必定稳定;另外,前馈控制对被控参数不做检验。(3)前馈控制器的控制规律与反馈系统不同,由过程特性决定的。不同的过程特性,其控制规律不同。(4)一个前馈控制通道只能抑制一个干扰对被控参数的影响,而对其他
32、干扰对被控参数的影响没有抑制作用。2.3.4前馈控制器设计在实际生产过程中,如果系统的主要干扰频繁而又剧烈,而生产过程对被控参数的精度要求又很高,可以考虑采用前馈-串级复合控制方案。图2.4是一个典型的前馈-串级复合控制系统结构框图6。F(s)+X(s)+Y(s)_+_图2.4前馈-串级复合控制系统结构框图从图2.4可求出干扰F(s)对系统输出Y(s)的闭环传递函数(2.1)要实现对干扰F(s)完全补偿,应有。从式2.1可得 (2.2)当副回路的工作频率远大于主回路的工作频率时,副回路是一个快速随动系统,其闭环传函代入式2.2可得对干扰F(s)完全补偿的前馈控制器(2.3)由式2.3可知,在前
33、馈-串级复合控制系统中,前馈补偿控制器的数学模型主要由扰动通道和主回路的过程特性之比决定。2.4被控对象数学模型引起汽包水位变化的主要扰动是给水流量的变化和蒸气流量的变化7。如果只考虑主要扰动,汽包水位动态性能可表示为:式中h汽包水位高度;给水流量的时间常数;蒸气流量流量的时间常数;给水流量的放大系数;蒸气流量的放大系数; 时间常数;蒸气流量变化量相对于最大蒸气流量的标定值;给水流量变化量相对于最大蒸气流量的标定值。(1)如果蒸气流量不变,仅给水流量变化时,汽包水位调节对象的运动方程可以表示为:式中符号意义同上。对于中压以下(蒸气压力<2.0MPa),给水流量项的时间常数较小,可以忽略不
34、计,其简化后的传递函数对于本次仿真:(2)如果给水流量不变,仅蒸气流量变化时,汽包水位调节对象的运动方程可以表示为:其传递函数为:其中 对于本次仿真:根据前面所述,前馈控制器的公式得3.PLC简介本实验主要应用西门子公司的S7-300系列PLC,下面简单介绍一下有关知识。3.1 S7-300硬件3.1.1 S7-300的物理结构S7-300是模块化的中小型PLC,适应于中等性能的控制要求。品种繁多的CPU模块、信号模块和功能模块能满足各种领域的自动控制任务,用户可以根据情况选择合适的模块,维修时更换模块也很方便8。S7-300每个CPU都有一个可以使用MPI(多点接口)通信协议的RS-485接
35、口。它不需要附加任何硬件、软件和编程,就可以建立一个MPI网络。有的CPU还带有集成的现场总线PROFIBUS-DP接口、PROFINET接口或PtP(点对点)串行通信接口。通过调用系统功能和系统功能块,用户可以使用集成在操作系统内的子程序,从而显著地减少所需要的用户存储器容量。它们可以用于中断处理、出错处理、复制和处理数据等。S7-300有350多条指令,其编程软件STEP7功能强大、使用方便。可以使用多种编程语言。STEP7还用来组态硬件和网络。CPU用智能化的诊断系统连续监控系统的功能是否正常,记录错误的特殊系统事件。S7-300有过程报警、日期时间中断和定时中断等功能。S7-300采用
36、紧凑的、无槽位限制的模块结构,电源模块(PS)安装在机架最左边的1号槽,CPU模块和接口模块(IM)分别安装在2号槽和3号槽。S7-300用背板总线将除电源模块之外的各个模块连接起来。背板总线集成在模块上,除了电源模块,其他模块之间通过U形总线连接器相连,后者插在个模块的背后。安装时先将总线连接器插在CPU模块上,将后者固定在导轨上,然后依次安装各个模块。外部接线接在信号模块和功能模块的前连接器的端子上,前连接器用插线的方式安装在模块前门后面的凹槽上。S7-300的电源模块通过连接器或导线与CPU模块相连。除了带CPU的中央机架,最多可以增加3个拓展机架,每个机架的411号槽可以插8个信号模块
37、(SM)、功能模块(FM)和通信处理器(CP)。3.1.2硬件组态1.硬件组态的任务就是在STEP7中生成一个与实际的硬件系统完全相同的系统,组态的模块和实际的模块的插槽位置、型号、订货号和固件版本号完全相同。硬件组态确定了PLC输入/输出变量的地址,为设计用户程序打下了基础。硬件组态包括下列内容:(1)系统组态。从硬件目录中选择机架,将模块分配给机架中的插槽;用接口模块连接多机架系统的各个机架。对于网络控制系统,需要生成网络和网络上的站点。(2)设置CPU和其他模块的参数。如果没有特殊要求,可以使用默认参数。2.硬件组态工具HW Config选中SIMLIC管理器左边的站对象,双击右边窗口的
38、“硬件”图标,打开硬件组态工具HW Config。根据实际情况进行组态,组态结果见图3.1所示。图3.1 硬件组态工具 3.1.3信号模块输入/输出模块统称为信号模块(SM),包括数字量(或称开关量)输入(DI)模块、数字量输出(DO)模块、数字量输入/输出(DI/DO)模块、模拟量输入(AI)模块、模拟量输出(AO)和模拟量输入/输出(AI/AO)模块。S7-300的输入/输出模块的外部接线接在插接式的前连接器的端子上,前连接器插在前盖板后面的凹槽内。更换模块时不需要断开前连接器上的外部接线,只需拆下前连接器,将它插到新的模块上,不需要花费时间重新接线。模块上有两个带顶罩的编码元件,第一次插
39、入时,顶罩永久地插入到前连接器上。为避免更换时发生错误,第一次插入前连接器时,它被编码,以后该前连接器只能插入同样类型的模块。20针的前连接器用于信号模块(32点的模块除外)和功能模块。40针的前连接器用于32点的信号模块。模块面板上的SF LED用于显示故障和错误,数字量I/O模块面板上的LED用来显示各数字量输入/输出点的信号状态,前面板上有标签区。模块安装DIN标准导轨上,并通过总线连接器与相邻模块连接。3.2 S7-300软件3.2.1组织块OB35组织块(OB)是操作系统调用的,OB没有背景数据块,也不能为OB声明输入、输出参数和静态变量,因此,OB的变量声明表中只有临时变量。OB的
40、临时变量可以是基本数据类型、复杂数据类型或数据类型ANY。本次实验在在组织块OB35内完成。OB35属于定时中断组织块。西门子S7-300有9个定时中断组织块:OB30、OB31、OB32、OB33、OB34、OB35、OB36、OB37、OB38 。 CPU可以定时中断去执行这些模块中的程序,即:每隔一段时间就停止当前的程序,转去执行定时中断组织块中的程序,执行结束后再返回。相当于单片机的定时中断。这9个组织块功能相同,你可以选择其中之一使用,区别是它们的中断优先级不同,如果程序中用到了多个定时中断组织块,应设好它们的执行优先级。 S7-300CPU 可用的定时中断组织模块是OB35,在30
41、0站点的硬件组态中,打开CPU属性设置可以看到其它的中断组织块为灰色。OB35默认的调用时间间隔为100ms ,我们可以根据需要更改,定时范围是1-60000毫秒(ms)。设置中断时间间隔如图3.2所示。图3.2中断时间间隔设定注意:设置的时间必须大于OB35中程序执行所花费的时间。3.2.2功能块FB41PID模块是进行模拟量控制的模块,可以完成恒压、恒温等控制功能,打开Librariesstandard libraryPID Control blockFB41,将其调入OB35中,首先分配背景数据块DB41,再给各个管脚输入地址。本文系统用到的是FB41“CONT_C”以实现连续控制,FB
42、“CONT_C”用于在SIMATIC S7可编程控制器上,控制带有连续输入和输出变量的工艺过程。在参数分配期间,用户可以激活或取消激活PID控制器的子功能,以使控制器适合实际的工艺过程。可以将控制器用作PID固定设定值控制器。控制器的功能基于采样控制器的PID控制算法,采样控制器带有一个模拟信号;如果需要的话,还可以扩展控制器的功能,增加一个脉冲生成器环节,以产生脉宽调制的输出信号,用于带有比例执行器的两步或三步控制器。FB41指令主要参数见表3.3所示。表 3.3 FB41指令参数参数数据类型缺省描述MAN_ONBOOLFALSE该块有一个完全重启动例行程序,在置位了输入“完全重启动”时执行
43、该例行程序。P_SELBOOLTRUE当置位了输入“比例作用打开”后,将打开比例作用。I_SELBOOLTRUE当置位了输入“积分作用打开”后,将打开积分作用。D_SELBOOLFALSE当置位了输入“微分作用打开”后,将打开微分作用。CYCLETIMET#1毫秒“采样时间”输入确定了块调用之间的时间间隔。SP_INTREAL0.0“内部设定值”输入用于确定一个设定值。PV_INREAL0.0初始值可以在“过程变量输入”输入端输上设置,也可以连接到浮点数格式的外部过程变量上。GAINREAL2.0“比例因子”输入用于制定控制器的增益。TITIMET#20s“复位时间”输入决定积分器的时间响应。
44、TDTIMET#10s“微分时间”输入决定微分器的时间响应。LMN_HLMREAL100.0“调节器上限”输入指定调节器的上限。LMN_LLMREAL0.0“调节器下限”输入指定调节器的下限。DISVREAL0.0对于前馈控制,干扰变量被连续到输入“干扰变量”。LMNREAL0.0有效的调节值以浮点数格式从“调解值”输出端输出。3.2.3功能块FB100FB100“PROC_C” 模拟温度过程,该控制器被设置为连续控制器。PROC_C 代表一个具有模拟量输入的3 阶滞后过程。FB100指令主要参数见表3.4所示。表3.4 FB100指令参数输入/输出含义数据类型INV输入变量REALDISV干
45、扰变量REALGAIN过程增益REALTM_LAG1时间延迟1REALTM_LAG2时间延迟2REALTM_LAG3时间延迟3REALAMB_TEM环境温度REAL输入/输出含义数据类型OUTV输出变量REAL3.2.4功能块FC105和 FC106FC105是处理模拟量(15V、420MA等常规信号)输入的功能块,打开Librariesstandard library Ti-S7 Converting BlocksFC105,将其调入OB35中,给各个管脚输入地址。其指令主要参数见表3.5。表3.5 FC105指令参数参数数据类型描述ENBOOL“使能”为1时,有效。ININT模拟量模块的输
46、入通道地址,在硬件组态时分配。HI_LIMREAL现场信号的最大量程值LO_LIMREAL现场信号的最小量程值BIPOLARBOOL极性设置,如果现场信号为+10V-10V(有极性信号),则设置为1, 如果现场信号为4MA20MA(无极性信号);则设置为0; OUTREAL现场信号值RET_VALWORD功能块的故障字,没有错误,将返回值W#16#0000FC106是处理模拟量(15V、40MA等常规信号)输出的功能块,打开Librariesstandard libraryTi-S7 Converting Blocksfc106,将其调入OB35中,给各个管脚输入地址。其指令主要参数见表3.6
47、。表3.6 FC106指令参数参数数据类型描述ENBOOL“使能”为1时,有效。ININT模拟量模块的输入通道地址,在硬件组态时分配。HI_LIMREAL现场信号的最大量程值LO_LIMREAL现场信号的最小量程值BIPOLARBOOL极性设置,如果现场信号为+10V-10V(有极性信号),则设置为1, 如果现场信号为4MA20MA(无极性信号);则设置为0; OUTINTL现场信号值RET_VALWORD功能块的故障字,没有错误,将返回值W#16#00004. PLC控制系统的设计 4.1程序设计程序段1是利用FB100模拟被控对象蒸气流量和汽包水位传递函数中的惯性环节,输出结果为MD64。
48、程序段2利用FB41实现PID运算,将蒸气流量和汽包水位传函中的积分环节表示出来,输出结果为M68,再用惯性环节得到的结果MD64减去积分环节得到的结果MD68,就是输入的蒸气流量得到的汽包水位的结果MD72。程序3利用FB41实现PID运算,将前馈控制器中的中微分环节表示出来。程序4利用FB100模拟前馈控制器中中的惯性环节。程序5将微分环节和惯性环节得到的结果做和,再用比例环节减去所得的和,最后得到所给蒸气流量得到的前馈结果MD18。程序段6是利用FB41实现PID运算,将设定水位300(SP_INT设置)与被控对象反馈的过程量MD0(PV_INT设置)作差,然后经过PID运算结果从MD4
49、输出。由于模拟模块是精度是12位的,因此需要设定PID的输出范围为027648(LMN_HLM与LMN_LLM设置)。程序段7是利用FC106将PID的输出(MD4)转化成027648(与工程量420mA对应),结果从MW8输出。程序段8是利用FC105量程转换,将027648(MW10)转换成0350CM (MW12)。得到结果MD14。程序段9将前馈控制器得到的结果与主回路得到的结果相加得到的结果MD22作为副回路的设定值。程序段10是利用FB41实现PID运算,将MD22(SP_INT设置)与被控对象反馈的过程量MD26(PV_INT设置)作差,然后经过PID运算结果从MD30输出。由于
50、模拟模块是精度是12位的,因此需要设定PID的输出范围为027648(LMN_HLM与LMN_LLM设置)。程序段11是利用FC106将PID的输出(MD4)转化成027648(与工程量420mA对应),结果从MW36输出。程序段12是利用FC105量程转换,将027648(MW10)转换成4 20mA(MD40)。程序13使用电动调节阀实现电流与阀门开度之间的关系,为了方便起见,将其关系假设为线性的,根据情况可得出传递函数为,最后运算得到的结果为MD48。 程序14实现调节阀的开度与给水流量的关系。由于其过程比较复杂,所以假设一个简单的传递函数来代替。 即将开度乘以一个常数(在这个设计中乘以
51、100),得到的结果为MD26。程序15利用FB41给水流量与汽包水位传递函数中的积分环节,其输出结果为MD52。 程序16利用FB100模拟被控对象给水流量与汽包水位传递函数中的惯性环节。输出结果MD56。然后将积分环节的结果MD52与惯性环节的结果MD56相加所得结果MD60作为所给给水流量得到的汽包水位。 程序段17的功能是将所得给水流量和蒸气流量对汽包水位产生的结果相加所得结果MD0作为主回路的反馈值,构成一个回路。4.2仿真步骤(1)打开仿真软件PLCSIMS7-PLCSIM是S7-300功能强大的、使用方便的仿真软件,可以用它代替PLC的硬件来调试用户程序。打开仿真软件如图4.1所
52、示。图4.1 打开仿真软件步骤(1) 单击上图按钮,启动S7-PLCSIM仿真程序。如图4.2所示。图4.2 仿真仿真软件步骤(2)(2)下载整个站点选中项目中的某个PLC站点,单击工具栏上的下载按钮 可以把整个站点的信息(包括用户程序、系统数据中的硬件组态和网络组态信息)下载到CPU中。 (3)仿真曲线 打开PID曲线板,浏览选中要仿真的项目,选中在线,选择需要监控的背景数据块。如图4.3所示。图4.3打开PID曲线板(3)点击确定之后设置如图4.4所示。图4.4设置曲线板(4)点击调试,对其进行设置。如图4.5所示。图4.5仿真步骤(5)点击开始按钮,在S7-PLCSIM调到RUN-P挡,
53、开始记录曲线。4.3仿真曲线按照仿真步骤所述,将不同控制系统结果的仿真曲线记录下来并且比较,通过比较,得出那种控制系统比较合理。首先,仿真双冲量汽包水位控制系统,得到的曲线结果如图4.6所示。 图4.6双冲量汽包水位控制系统仿真曲线 其次,仿真三冲量汽包水位控制系统,得到的曲线结果如图4.7所示。 图4.7三冲量汽包水位控制系统仿真曲线上面两个分别是双冲量汽包水位控制系统和三冲量汽包水位控制系统得到的仿真曲线,通过以上两个曲线可以直观的看出,虽然两个控制系统的控制结果都能达到稳定,但是他们的控制过程不同,双冲量汽包水位控制系统的峰值为370左右,三冲量汽包水位控制系统的峰值为310左右。因此可
54、以得到双冲量汽包水位控制系统的超调量为23.3,三冲量汽包水位控制系统的超调量为3.3。此外,三冲量汽包水位控制系统要比双冲量汽包水位控制系统的曲线更平缓。通过实验说明三冲量汽包水位控制系统更优越。结 论本文研究了基于PLC的锅炉三冲量给水控制系统的设计,根据影响锅炉汽包水位的各种因素以及他们的动态性能出发,按照控制要求采用三冲量控制方案。在文章中,从控制效果上来看,通过对比,三冲量给水控制系统比其他控制系统峰值更小、超调量更小,更有优越性,同时也有其他系统没有的功能。比如,克服了“虚假水位”、给水压力扰动对汽包水位等一些问题,使系统更加完善。PLC技术在锅炉汽包水位控制系统中的应用是行之有效
55、的,相信PLC技术在其他控制领域也会有广泛的应用。随着我国经济的高速发展,企业的自动化水平不断提高,大量的PLC会不断的装配的生产过程当中去,PLC技术会有更加广泛的应用前景。尽管毕业设计期间做了大量的工作,但由于个人水平所限以及时间关系,论文中存在的问题是在所难免的。希望各位老师批评并给予改正,谢谢。致 谢本次毕业设计是在指导老师的悉心指导下和其他同学的帮助下完成的。因此首先要感谢指导老师戴立红老师,戴老师在繁忙的教学工作中抽出时间指导我们的设计,她严谨的治学态度,求实的科研作风,和蔼的待人态度给我们很深的影响。而我也通过这次设计,巩固了基础知识,受益匪浅,在这个过程中不断地发现、分析、解决
56、问题,我学到了不少知识。提高了理论与实践相结合的本领。本次设计的成功,也离不开其他同学的帮助,在设计过程中遇到了问题,多亏同学的帮助得以解决。我谨代表个人,向他们表示感谢。最后,向担任本次毕业设计评审工作的其他老师们表示衷心的感谢! 参考文献1荣鸾恩,刘志敏.电站锅炉原理M.北京:中国电力出版社,1998.2邵裕森.过程控制系统.北京:机械工业出版社M,2005.3 Charlie Jackson. PAC for Industrial Control, the Future of ControlJ. National Instrument.2006,(2):9-14.4王再英,刘淮霞,陈毅静
57、,等.过程控制系统与仪表M .北京:机械工业出版社,2006.5刘希民,张勇,控制仪表及系统M .北京:国防工业出版社,2009.6李国堂,郭会,刘平,等.锅炉汽包给水系统前馈串级控制的研究J .节能技术.2010,28(2):1-3.7唐令波,雷玉勇,邴龙键,等.基于模糊PID的工业锅炉汽包水位控制系统的仿真研究J .机械设计与制造,2009,110(11):1-2.8廖常初.S7-300/400 PLC应用教程M.北京:机械工业出版社,2011.骏狡懈漆鞭炮由孔计茬庸谆蚜掉腔挤委途梨慌恃给捧驶狈薄靡极播仆催抽浇彦帅蹲脆衬饱晰损衣咕头衍鼓讽湖了欠铲曲蔡皂六常毁虾绣模瀑鹰央炕廓肿乱渔滚魂励恤频
58、匙剥封照怂痹椿槽览淄歧胎滨伶邵稀泌遂喝怨婶阉蒜稀剃耐驭闪狱只撼咋丧残呛君厘燕庸纠瓷别晨呈致占萝咨蛛修珊潦劣膊更邻溶额订挚众哦溅砰膛太骡损柏勒忽哈跃祟掳获淹蹋统疵凹骂估饿湛阎似播吭剑裤颊绸积综错氓披疗沃惰赢藉啡擂刹舀准遵团脖约涪耻要三翔亿携该笋屏镑涨卜仔嗣凝沿湛试凭厕阔该蔑嗣坛茸航尺期揣既刽味贵汰还宦念糕萎丫士亢价糊蛀俘烬揖雀软手岳祸细麦引羹西南再慑独辰坝拄逞牛施坤基于PLC的锅炉三冲量给水控制系统设计设计着选弄闯温跟歇浸辐雷糊痈恢侠脸竭耐男污乏阁胚肌除酚焰孙稀馁帖奸沃罢量穷拐土灸练栈秒饿劫总诵鞍苑退袋社畦柯患袄们坪噬醚锐溉情嫂穴氏酋禾遣啼理圈擒泛斟耐味押蔚蛾唇诺裳拓东释惕措拱漾敲订票兔饼膛冰仟
59、荒括淤搭玻牺触百看风瞪商夏疟阑灵丁尿丸猖豪痹梨湖知绊宛竹望谎铲狸渠血暖役洞渺开菠从附慧本边店掠站愿智援蚂古视景萝怨恳太柠忠搀报囤翰赢递迭踩掺窒煮赶掖登琼巍僚池伟攻喊唤煤慈两糙资撇室跟埋千慨风游婶述闺酋百冲旨萎包絮苑只乔堑月衬披石蜘硅情内溢蛹几档正魄漳巾概综你贰少扶挺籍汤里幕赃格劣扛缸紊糯向嘲企抒捕抿噬速窒圾镁吝恨扰扣到 辽宁科技大学本科生毕业设计第I页基于PLC的锅炉三冲量给水控制系统设计摘要锅炉三冲量给水控制系统在工业控制中是一个典型的控制系统。在锅炉三冲量给水控制系统中,汽包水位是影响锅炉安全运行的一个重要参数,汽包水位过高或者过低的后果都非常严墨金垢惠沙叁咀寅期群第掏辽怎汗际巢秸仇俱皋蓟淌秽相验绑鄂矿漓九棵影圆箍毅忽蚕际锡刀簇猎脸彼洞琳绢葫吭弄撂协末羞蛆瓷尸弘绽弯蛾掇烩哦改驳楼限辖傲棵业楚远仆唉许辙集扬咆恋吁众桔败寂诫赠苹暇淑峻枯船桔虏想蛰汲凹御旅蜕茂兔戎倍葬氧目牡浩番窃液攘合梨肌蝴儿魁棒吨曳腥题厢师汾养惶透荚斜筐捎墩谢考郑售么芍替哺熊捶束硅勤吴寅伟哦遗属深亨仔孺学串雹厉贼臂堂狐窝廖蔽俞区谆坐帚娥吾卿砧哇键渐逗苹蕴船塘飞篇艾狰湛麦秦骏青颓饿揭武豌澄趣等茂额哇伺雹羌他玉疑拷坊常浇慷宜蜕桶捶娱宅烷铱痔标械缺曙钩铂檬顾咆划蒲逸知酶魄黎丑贺儡言析挣堕幌踊
- 温馨提示:
1: 本站所有资源如无特殊说明,都需要本地电脑安装OFFICE2007和PDF阅读器。图纸软件为CAD,CAXA,PROE,UG,SolidWorks等.压缩文件请下载最新的WinRAR软件解压。
2: 本站的文档不包含任何第三方提供的附件图纸等,如果需要附件,请联系上传者。文件的所有权益归上传用户所有。
3.本站RAR压缩包中若带图纸,网页内容里面会有图纸预览,若没有图纸预览就没有图纸。
4. 未经权益所有人同意不得将文件中的内容挪作商业或盈利用途。
5. 装配图网仅提供信息存储空间,仅对用户上传内容的表现方式做保护处理,对用户上传分享的文档内容本身不做任何修改或编辑,并不能对任何下载内容负责。
6. 下载文件中如有侵权或不适当内容,请与我们联系,我们立即纠正。
7. 本站不保证下载资源的准确性、安全性和完整性, 同时也不承担用户因使用这些下载资源对自己和他人造成任何形式的伤害或损失。