09 装置大型化运行总结
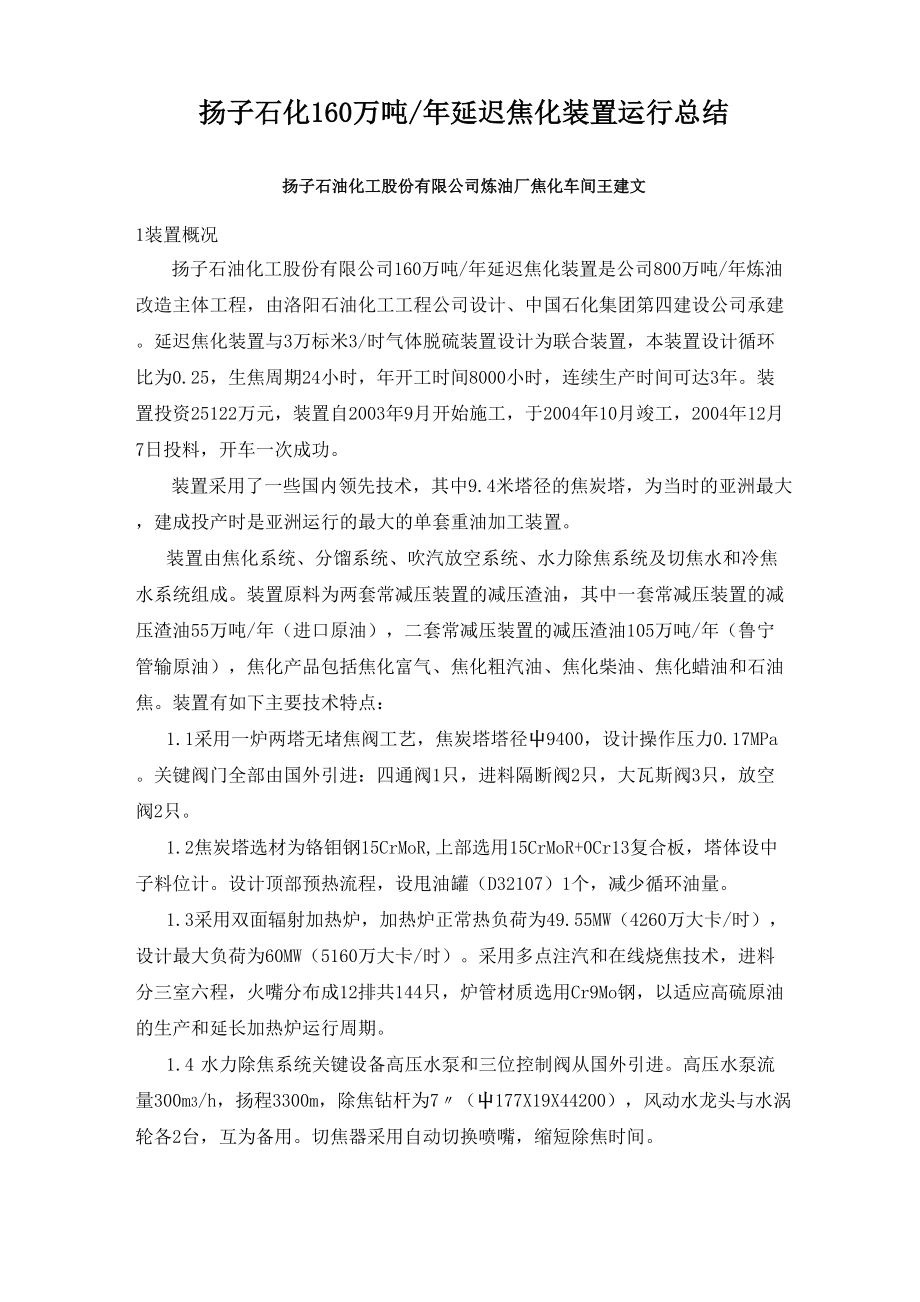


《09 装置大型化运行总结》由会员分享,可在线阅读,更多相关《09 装置大型化运行总结(11页珍藏版)》请在装配图网上搜索。
1、扬子石化160万吨/年延迟焦化装置运行总结扬子石油化工股份有限公司炼油厂焦化车间王建文1装置概况扬子石油化工股份有限公司160万吨/年延迟焦化装置是公司800万吨/年炼油改造主体工程,由洛阳石油化工工程公司设计、中国石化集团第四建设公司承建。延迟焦化装置与3万标米3/时气体脱硫装置设计为联合装置,本装置设计循环比为0.25,生焦周期24小时,年开工时间8000小时,连续生产时间可达3年。装置投资25122万元,装置自2003年9月开始施工,于2004年10月竣工,2004年12月7日投料,开车一次成功。装置采用了一些国内领先技术,其中9.4米塔径的焦炭塔,为当时的亚洲最大,建成投产时是亚洲运行
2、的最大的单套重油加工装置。装置由焦化系统、分馏系统、吹汽放空系统、水力除焦系统及切焦水和冷焦水系统组成。装置原料为两套常减压装置的减压渣油,其中一套常减压装置的减压渣油55万吨/年(进口原油),二套常减压装置的减压渣油105万吨/年(鲁宁管输原油),焦化产品包括焦化富气、焦化粗汽油、焦化柴油、焦化蜡油和石油焦。装置有如下主要技术特点:1.1采用一炉两塔无堵焦阀工艺,焦炭塔塔径屮9400,设计操作压力0.17MPa。关键阀门全部由国外引进:四通阀1只,进料隔断阀2只,大瓦斯阀3只,放空阀2只。1.2焦炭塔选材为铬钼钢15CrMoR,上部选用15CrMoR+0Cr13复合板,塔体设中子料位计。设计
3、顶部预热流程,设甩油罐(D32107)1个,减少循环油量。1.3采用双面辐射加热炉,加热炉正常热负荷为49.55MW(4260万大卡/时),设计最大负荷为60MW(5160万大卡/时)。采用多点注汽和在线烧焦技术,进料分三室六程,火嘴分布成12排共144只,炉管材质选用Cr9Mo钢,以适应高硫原油的生产和延长加热炉运行周期。1.4 水力除焦系统关键设备高压水泵和三位控制阀从国外引进。高压水泵流量300m3/h,扬程3300m,除焦钻杆为7(屮177X19X44200),风动水龙头与水涡轮各2台,互为备用。切焦器采用自动切换喷嘴,缩短除焦时间。1.5分馏塔塔径05400,内件采用38层T型浮阀塔
4、盘,底部设7层人字挡板。1.6 采用“可灵活调节循环比”技术,原料不直接进分馏塔与含有焦粉的高温油气接触,减少加热炉进料的焦粉含量。1.7 采用旋流除油技术和全密闭放空生产工艺,消除放空区恶臭气味,改善工作环境。管道、阀门选材针对装置加工高硫油的实际情况,为防止管道的露点腐蚀和高温硫腐蚀,管道设计在以下部位采取防腐措施,选用铬钼钢无缝钢管:加热炉进料泵的出入口管道;加热炉出入口管道、以及与四通阀相连接的管道;焦炭塔进料线、出口油气线及部分甩油线;分馏塔底循环线,温度大于250C的中段回流和蜡油管线。1.8 节能措施1.9.1 为了回收分馏塔余热,设置四个中间回流,即:顶循环回流、柴油回流、中段
5、回流及重蜡油回流,原料经过中段换热(E32102)、轻蜡油换热(E32103)、重蜡油换热(E32104)和塔底循环油换热(E32105)后,温度可达300C,降低了加热炉热负荷。设柴油蒸汽发生器(E32108)、轻蜡油蒸汽发生器(E32109)和重蜡油蒸汽发生器(E32110),发生0.35MPa蒸汽。使用高效新型火嘴,降低燃料消耗,加热炉设计热效率90.5。2.1 2装置运行状况主要经济指标和运行参数160万吨/年延迟焦化联合装置于2004年12月7日投料,开车一次成功,生产出合格产品,由于设备原因(平衡管隔断阀大量泄漏)和设计上存在缺陷(平衡管隔断阀为单阀,泄漏后无补救措施),运行一个生
6、焦周期(24小时)后,12月8日装置改循环进行消缺,装置消缺完成后,于12月17日重新升温投料。装置于2005年6月2124日进行了标定,标定期间焦化原料,主要以一套常减压渣油为主(约3600t/d,主要为鲁宁管输原油的渣油),不足部分由二套常减压装置(主要为伊朗轻油的渣油)和油品车间提供的部分冷渣,冷渣约占总进料的1015),焦化系统标定期间系统运行基本正常,标定期间,减压渣油处理量为203638kg/h,即年加工能力为162.91万吨/年,是设计值160万吨/年的101.82%,超过设计负荷。循环油量在标定期间最小值为37000kg/h,循环比为0.182;最大值为50000kg/h,循环
7、比为0.246;循环比实现了灵活调节。装置主要经济技术指标见表1,其它情况见附表27。表1技术经济指标执行情况序号技术经济指标设计值标定值05年上半年1加工量(t/d)4800488741832液体收率()62.865.364.943能耗(Kg标油/吨)19.4021.7222.344加工损失0.700.570.615循环比0.250.20.226生焦周期(h)2424242.2.1.1 各系统运行状况焦化系统加热炉装置首次开工时只投用1、3#炉室,2#炉室给蒸汽保护,注汽按上限控制,2#炉室于2005年元月28日并炉,在开工50余天后并炉,获得成功,未发现异常情况。并炉的成功,是设计提出在线
8、烧焦的意图能否实现、确保装置长周期运行的前提。后来,因生产的需要,两次切出2#炉室维持低负荷生产,停炉和并炉,均可在2小时内完成,操作方便,为装置较大幅度的调整负荷创造了灵活的手段;由于加热炉二室因装置负荷调整,多次切出,包括2005年4月10日,高压水泵故障停2室,2005年4月29日,常减压装置停运,焦化改循环,2005年6月3日,四通阀故障,自动切换,停进料一次。导致加热炉第四路的对流入口压力也缓慢上升至1.63MPa左右,较其他分支高出0.3MPa,二室膛温也比一室和三室高3040C,管壁温度最高较其他分支高接近100C。炉管局部有暗斑,出现明显结焦。为保证焦化加热炉的长周期运行,于7
9、月12日至7月16日加热炉二室在线烧焦一次,烧焦后二炉室入口压力、膛温、管壁温度都明显下降至初次投用时的状况。开工初期,加热炉存在如下问题:瓦斯控制阀流量通量低不能满足工艺需要、燃烧状况不好(膛温偏高,火焰飘,燃烧不稳定、烟气排放温度高)、注汽量指示不准等。通过更换大通径瓦斯控制阀,调整优化加热炉操作,目前加热炉运行状况大为改善,热效率达到90以上;注汽流量采用阿纽巴流量计,指示不准只有通过比较和参考控制阀开度以及炉管压降操作,为防止高负荷蒸汽流量大而导致焦炭塔气体线速太高夹带焦粉,根据负荷及时调整注汽量。目前加热炉还存在各炉膛相互影响、不平衡以及管壁测温热偶易脱落的问题。装置标定后对加热炉进
10、行计算,其标定结果如下:表2加热炉主要设计值与标定结果项目设计值标定值备注氧含量3.7%过剩空气系数a1.20加热炉热负荷kw4955049900热效率%90.590.82.2.1.2 焦炭塔9.4 米直径焦炭塔在国内是第一次使用,主要尺寸见图1,设有中子料位计,每台3只,可以清楚显示焦炭塔内生焦、轻重泡沫、给水和放水水位情况,效果很好。急冷油自油气出口处分三点注入,为防止焦粉夹带和油气线结焦,急冷油量较大,目前控制油气出口温度在400C。正常泡沫层高度57米,消泡剂自塔顶注入,可以降低泡沫层12米。塔顶设有柴油注入系统,装置在低负荷运行焦炭塔预热时可补充分馏塔气相负荷,由于低负荷时分馏塔仍能
11、保持较好的分离效果,故系统只试用一次。焦炭塔目前已发现的问题主要有:1、冷焦不透,冷焦时间78小时(自给水开始到放水),由于自生焦孔到塔壁焦层太厚,泡焦不透,放水后期焦炭塔塔顶压力会回升,除焦时切焦水遇到外层热焦产生大量蒸汽,不仅使溜槽口能见度变低影响除焦效果的观察,而且大量蒸汽上升夹带焦粉随风飘散影响装置环境卫生。2、焦炭塔附塔管线晃动带动塔体晃动,引起高温油气管线法兰口泄漏,通过强化管托固定,改进操作(操作内容细化,如引瓦斯、预热、吹汽、给水实行阶梯操作),提高放空塔系统压力来降低气体线速,目前管线和塔体晃动问题已有所缓解。3、焦炭塔塔体保温脱落。焦炭塔保温采用披挂式保温,焦炭塔椭圆顶和裙
12、座部位部位铁皮大片脱落,部分外背带扁钢断裂,可能会影响焦炭塔长周期安全运行,于2005年6月份进行了整改,状况有所改善。焦炭塔标定数据如下:表3焦炭塔分析数据项目单位设计值标定值平均值最大值最小值焦炭塔直径mm9400焦炭塔切线高m26焦炭塔顶温度C420400404.5395.5焦炭塔顶压力MPa(G)0.170.160.160.14焦层咼m20*油气线速m/s0.1370.144注:*标定期间检尺焦炭塔筒体高度依次为:16.4m、16.5m、18m。甩油系统。甩油三台过滤器(甩油罐入口一台、出口两台)设计均为管道过滤器,极易堵塞,已多次清焦,甩油罐出口后来更换一利旧立式过滤器,效果较好。分
13、馏系统分馏塔设计采用导向条阀塔盘,标定结果显示塔的操作指标达到设计要求,能够满足所要求的分离精度。塔盘水力学计算结果显示塔性能良好,在标定处理量下阀孔动能因子最大为8.6(m/s)(kg/m3)1/2,液体超负荷安全系数均大于3.0,具有良好的操作弹性,运行平稳。05年4月份因高压除焦水泵故障,加热炉渣油进料降低到设计负荷的40,生焦周期延长至48小时,分馏塔负荷在50以下的情况下,仍可正常操作,各馏出口质量合格。随着原料性质和循环比的变化,蜡油残炭偶尔会上升。分馏系统存在或出现过如下问题:一是塔底热偶指示温度过高,开工初期达390C以上(设计温度360C),经过调整,正常值仍超过380C,可
14、能与热偶安装位置偏高有关,金陵石化炼油厂160万吨延迟焦化装置出现相同情况,后在塔底抽出口管线增加一热偶,指示温度较塔底测温点低1530C;二是分馏塔塔底循环过滤器结焦现象,开工前两个月塔底循环过滤器带焦堵塞严重,需定期清除(最短4天清一次),为降低分馏塔塔底结焦,目前采用降低焦炭塔油气出口温度,控制在400,加大塔底循环量,目前塔底温度控制在390C以下,塔底循环过滤器芯开孔由屮4扩大到屮8,带焦堵塞情况已得到缓解,正常运行了2个月清一次焦。三是塔顶循环空冷两台风机,冬季开两台回流温度在30C以下,小吹汽时回流带水,泵抽空,停一台回流温度90C以上,满足不了工艺要求,调节余地小,需增设变频控
15、制;四是分馏塔塔顶切水(酸性水)乳化严重,含油高达24%,正在实施改造,增加油水分离过滤器将该部分酸性水进一步处理后含油低于400ppm送出装置。2.2.1 吹汽放空系统放空塔塔顶空冷由于空冷最大冷却负荷的限制(冷却50t/h蒸汽),初始给水由于蒸汽量大,蒸汽不能全部冷凝下来,大量带入火炬系统,威胁火炬系统安全运行。通过改进冷焦给水操作、增加喷淋强化冷却效果等措施,基本解决该问题。放空塔塔顶油水分离罐隔板下方有一屮20的小孔,油水无法分开,现增加一跨线将放空塔顶油和水引起送入沉降罐进行撇油,待停工后再处理隔板屮20的小孔。2.2.2 冷焦水系统冷焦水采用旋流除油技术和全密闭放空生产工艺,采用吸
16、附剂(JXTC)对放空气体脱臭和放空,效果较好,基本消除放空区恶臭气味,改善了工作环境,但需定期更换吸附剂,使用有效期612个月,同时吸附剂吸附浓度达到一定程度与空气接触会自燃,存在安全隐患,目前加氮气进行保护。冷焦水系统运行后发现问题有:一是冷焦水泵P32204入口管线堵,通量不够,已安装临时线,准备更换罐壁抽出阀门,并将安装明管代替原来地管;二是原设计冷焦放水需经一混合器进冷焦水罐,每次放水混合器都发生堵塞,不得不开付线,这样将可能大量焦块带至冷焦水罐,影响冷焦水系统长周期运行,已将混合器更换为过滤器,每天清理;三是旋流除油器运行不稳定,冷焦水储罐未设撇油口,油将会越积越多,最终影响焦炭质
17、量和装置安全,已增加一撇油线,定期撇油。目前系统运行良好。2.2.3 水力除焦系统设备大型化后带来一些新问题:高压水泵扬程高达3300m,焦炭粉焦含量明显较其它焦化装置比例高;水力除焦系统故障率较高,高压水泵和三位控制阀是从国外引进(Flowserve)的设备,高压水泵出现过轴套断裂,三位阀直存在满流到旁路切换不灵活的问题,已更换电机;行车及20吨抓斗吊问题较多,如装车操作难度大、检修频繁等。计划将抓斗更换成16吨,并增加一台备用行车,同时需加强设备维护,充分备好易损件和常规零部件,尽可能缩短检修时间。2.2.4 换热网络标定结果显示,换热网络终温标定值(306C)与设计值(305C)较为吻合
18、,由于分馏塔取热比设计值与标定值不尽相同,说明换热网络具有良好的适应性。换热器传热计算结果显示传热系数与设计值较为接近,设计中采用的波纹管换热器管程膜传热系数均在1200w/(m2.k)以上,同时壳程膜传热系数也得到一定强化,高于普通换热器。3.1 3、在装置长周期运行以及优化方面所作尝试通过技术措施,推行本质安全化设计,从源头确保不留安全隐患。对设计存在的缺陷,对运行中发现的问题,有条件的已整改或正在安排整改,不具备整改条件的问题,积极创造条件整改;参数优化。在吃透设计意图的基础上,进一步核算关键部位的技术参数如加热炉出口温度、吹汽量、给水量、焦炭塔塔顶温度和压力、分馏塔各点操作参数,将系统
19、结焦量和焦粉的夹带量降到最低,并根据原料性质变化及时调整操作;规范反应岗位操作。制定反应岗位确认表,详细列出操作步骤70项,根据现场实际操作情况、参考兄弟厂同类装置操作,已进行多次改进和优化。起到操作前提示、完成后确认签字的作用,从而防止误操作的发生。对于运行装置长周期运行的操作内容细化,如加热炉根据换塔时间采用变温操作,换塔前后炉温提1C,引瓦斯、预热、吹汽、给水实行阶梯操作,充分考虑减少系统结焦和夹带、延迟设备寿命的问题,从而延长装置运行周期;降低循环比,提高处理负荷。装置设计循环比为0.25,实际操作中最低达到过0.12。如果过多的降低循环油回炼量,降低循环油上回流和重蜡油下回流量,导致
20、重蜡油中残炭偏高,影响下游加氢精制催化剂使用寿命,同时提高处理量后生焦量同比例增加,设备大型化后缩短生焦周期更加困难,提量必将降低焦炭塔安全高度,影响装置长周期运行,加工低残炭渣油可以采用降低循环比来适当提高处理量。3.2 缩短生焦周期。缩短生焦周期的潜力不大,设备大型化后,处理塔给水冷焦、除焦、预热等操作等时间压缩比较困难,压缩时间后会带来如冷焦不透、预热不充分影响焦炭塔使用寿命等新问题。3.3 低负荷运行延长换塔时间,避免延迟焦化装置停车利用160万吨/年延迟焦化装置加热炉三室六程的条件,在生产过程中焦炭塔处理环节出现问题,不能正常进行换塔操作的情况下,如05年4月份高压设备轴套断裂,生焦
21、周期必需延长到48小时以上,方可避免停工。通过采取一系列措施,将生产负荷调整到40以下,在保证装置安全和产品质量合格的前提下,有效延长换塔时间(或生焦周期),最长可达到50小时以上,为问题的处理赢得充分时间,避免停车事故的发生,并能在短时间内快速恢复高负荷生产。3.4 加工高硫油本装置于2005年3月1124日掺炼沙轻油渣油,其渣油硫含量最大达到3.38%,由于掺炼的比例较小,占总渣油量的2030%,低于设计原料的硫含量,对装置影响不大,比较明显的是石油焦和酸性水中硫含量的变化,焦炭中硫含量均值由1.83%上升到2.82%,酸性水中硫化物浓度由6700mg/l上升到9800mg/l。4结束语扬
22、子160万吨/年延迟焦化装置作为国内最大单套重油加工装置,建成开车一次成功,运行平稳,标定结果表明装置在处理量、产品质量和收率、公用工程消耗和能耗等方面都达到或好于设计预期值。装置在流程设计方面进行了改进,使装置在开工过程的升温和脱水更加快速、方便、安全;“三室六程”的加热炉和较宽操作弹性分馏塔的,扩大了装置调整负荷范围。由于装置开工时间较短,有些影响装置长周期运行的问题还没有充分暴露;装置在优化运行、深挖潜力以及长周期运行等方面尚有大量工作需要进一步去做。装置大型化能够节省投资、降低能耗、减少操作人员,但设备大型化后会带来一些新的问题,需要今后去完善和解决。26,8.2515.4放水位监测3
23、.6米.泡沫层最高限位焦炭最高限位图1焦碳塔主要尺寸表4焦化装置物料平衡名称收率wt%流率X104t/at/dkg/h设计标定设计标定设计标定设计标定原原油100.00100.00160.00162.94800.04887.3200000203638油合计100.00100.00160.00162.94800.04887.3200000203638焦化富气&8&614.0814.01422.4420.21760017507粗汽油14.814.323.6823.29710.46982960029083产柴油23.024.836.8040.401104.01212.54600050522轻蜡油15
24、.021.42434.867201043.43000043474重蜡油10.04.8167.82480236.3200009847品焦炭28.125.644.9641.701348.81249.25620052048损失0.30.60.480.8114.427.86001157合计100.00100.00160.00162.94800.04887.3200000203638表5装置能耗(标定数据)序号项目消耗量燃料低热值或能耗指标单位能耗单位耗量小时耗量MJ/t原料千克标油/t原料单位数量单位数量单位数量标定值设计值标定值设计值1燃料气t/t0.023t/h4.69MJ/t41868964.2
25、6925.8623.0322.112电KW.h/t11.290kWh/h2299.15MJ/kW.h11.84133.68148.413.193.5433.5MPa蒸汽t/t0.014t/h2.94MJ/t368453.1936.841.270.884l.OMPa蒸汽t/t0.024t/h4.86MJ/t318275.9457.281.811.3750.3MPa蒸汽t/t-0.051t/h-10.35MJ/t2763-140.43-113.28-3.35-2.716工业水t/t0.041t/h&44MJ/t7.120.300.250.010.017循环水t/t2.601t/h529.68MJ/
26、t4.1910.908.610.260.218除氧水t/t0.065t/h13.28MJ/t152.89.966.880.240.169软化水t/t0.036t/h7.43MJ/t10.470.380.250.010.0110热输出-198.9-219.8-4.75-5.25-38.9-0.93合计909.28812.421.7219.40注:原料量按标定处理量203.638t/h。表6原料、中间物料数据(标定数据.部分)项目单位控制值实际最咼最低平均原料渣油渣油粘度mms600950741.2595.2676渣油硫含量wt%1.581.061.35中间物料粗汽油干点C220205200203
27、柴油干点C360342322326蜡油干点C500432421426蜡油残碳wt%0.30.0430.0240.035重蜡油干点C496481490重蜡油残碳wt%0.710.580.66焦炭挥发份wt%2010.456.668.84焦炭灰份wt%1.21.020.220.57焦炭硫含量wt%3.02.842.312.50表7装置主要工艺参数(05年6月)序号名称单位指标最大值最小值平均值1加执炉出口温度C5005504.45498.59499.7021#室北炉膛温度CW80080787538607551531#室南炉膛温度80329534327530842#室北炉膛温度817.09552.2
28、5764.7552#室南炉膛温度81595578157778963#室北炉膛温度82441552547449473#室南炉膛温度7846255011750428管壁温度W650525.11417.05499.29534.59444.75518.41565374505054602561634566554035611974877259221631.67524.00606.289加热炉进料t/h分支254242384110对流入口注汽kg/h分支5012091955095832411辐射入口注汽kg/h.分支200300300.00202.55287.7012辐射管注汽kg/h.分支50120103
29、.7566.7389.0713辐射管注汽94245300711914焦炭塔顶压力MPa02501701401615焦炭塔油气温度CV4204103994003916分馏塔顶压力MPa0.120.110.090.1017分馏塔顶温度C1201012645110011151518循环油返冋温度c60564835898621019柴油隼油箱温度C2301023975221792303720轻蜡油隼油箱温度C33010336.75320.12334.2521重蜡油隼油箱温度C3601037725359033676722蒸发段温度C40039452359003881223分馏塔塔底温度C38038737
30、02538424分馏塔顶分液罐入口温度C4540.7228.8135.8225分馏塔底液面%307069853571596626重蜡油隼油箱液面%507070005000677827轻蜡油隼油箱液面%608080006435705328柴油隼油箱液面%608079.7862.9576.7829放空塔顶压力MPa02501000000330焦化富气(汽油)出装置温度C4544722881358231焦蜡出装置温度C608079825535701032放空塔底液位%306059.0040.0050.0033放空塔顶温度C1601580053061097034瓦苴斤分液罐罐压力MPa03500503903303535封油压力MPa二0.800.940.880.8936空气预执器排烟温度C160180194.30167.70178.7337加执炉烟气氧含量%V547324638焦柴出装置温度C60583244325027
- 温馨提示:
1: 本站所有资源如无特殊说明,都需要本地电脑安装OFFICE2007和PDF阅读器。图纸软件为CAD,CAXA,PROE,UG,SolidWorks等.压缩文件请下载最新的WinRAR软件解压。
2: 本站的文档不包含任何第三方提供的附件图纸等,如果需要附件,请联系上传者。文件的所有权益归上传用户所有。
3.本站RAR压缩包中若带图纸,网页内容里面会有图纸预览,若没有图纸预览就没有图纸。
4. 未经权益所有人同意不得将文件中的内容挪作商业或盈利用途。
5. 装配图网仅提供信息存储空间,仅对用户上传内容的表现方式做保护处理,对用户上传分享的文档内容本身不做任何修改或编辑,并不能对任何下载内容负责。
6. 下载文件中如有侵权或不适当内容,请与我们联系,我们立即纠正。
7. 本站不保证下载资源的准确性、安全性和完整性, 同时也不承担用户因使用这些下载资源对自己和他人造成任何形式的伤害或损失。