实习报告生产实习炼油厂暑期报告
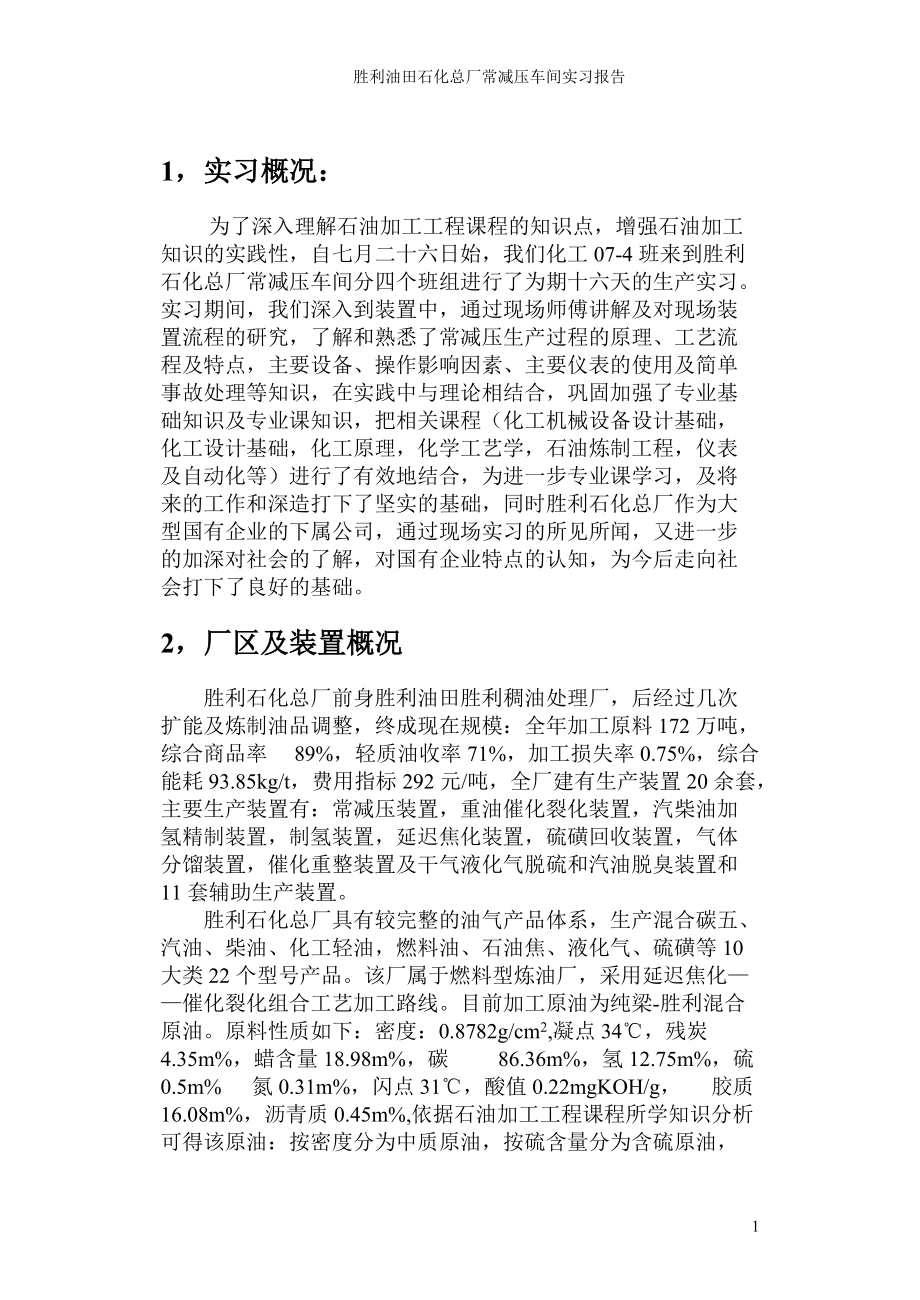


《实习报告生产实习炼油厂暑期报告》由会员分享,可在线阅读,更多相关《实习报告生产实习炼油厂暑期报告(13页珍藏版)》请在装配图网上搜索。
1、 胜利油田石化总厂常减压车间实习报告1,实习概况: 为了深入理解石油加工工程课程的知识点,增强石油加工知识的实践性,自七月二十六日始,我们化工07-4班来到胜利石化总厂常减压车间分四个班组进行了为期十六天的生产实习。实习期间,我们深入到装置中,通过现场师傅讲解及对现场装置流程的研究,了解和熟悉了常减压生产过程的原理、工艺流程及特点,主要设备、操作影响因素、主要仪表的使用及简单事故处理等知识,在实践中与理论相结合,巩固加强了专业基础知识及专业课知识,把相关课程(化工机械设备设计基础,化工设计基础,化工原理,化学工艺学,石油炼制工程,仪表及自动化等)进行了有效地结合,为进一步专业课学习,及将来的工
2、作和深造打下了坚实的基础,同时胜利石化总厂作为大型国有企业的下属公司,通过现场实习的所见所闻,又进一步的加深对社会的了解,对国有企业特点的认知,为今后走向社会打下了良好的基础。2,厂区及装置概况胜利石化总厂前身胜利油田胜利稠油处理厂,后经过几次扩能及炼制油品调整,终成现在规模:全年加工原料172万吨,综合商品率 89%,轻质油收率71%,加工损失率0.75%,综合能耗93.85kg/t,费用指标292元/吨,全厂建有生产装置20余套,主要生产装置有:常减压装置,重油催化裂化装置,汽柴油加氢精制装置,制氢装置,延迟焦化装置,硫磺回收装置,气体分馏装置,催化重整装置及干气液化气脱硫和汽油脱臭装置和
3、11套辅助生产装置。胜利石化总厂具有较完整的油气产品体系,生产混合碳五、汽油、柴油、化工轻油,燃料油、石油焦、液化气、硫磺等10大类22个型号产品。该厂属于燃料型炼油厂,采用延迟焦化催化裂化组合工艺加工路线。目前加工原油为纯梁-胜利混合原油。原料性质如下:密度:0.8782g/cm2,凝点34,残炭4.35m%,蜡含量18.98m%,碳 86.36m%,氢12.75m%,硫0.5m% 氮0.31m%,闪点31,酸值0.22mgKOH/g, 胶质16.08m%,沥青质0.45m%,依据石油加工工程课程所学知识分析可得该原油:按密度分为中质原油,按硫含量分为含硫原油,按酸值分为低酸值原油。根据原油
4、性质及现有装置特点目前该装置加工方案如图一所示。 图一 胜利石化总厂全厂工艺流程图 由图一可知,原料混合后先进入常减压蒸馏装置进行一次加工,生产出汽油。柴油半成品及蜡油、渣油二次加工原料,二次加工原料再由催化裂化装置或延迟焦化装置加工成液化气、汽油、柴油半成品及石油焦。半成品经过双脱或加氢、重整装置进一步精制成为合格产品销售出厂。为提高附加值产品收率,液化气由气体分离装置深加工成丙烯产品作为化工原料,为保护环境,还配套了硫磺回收装置。 常减压装置在炼油厂中具有重要的地位,是炼油厂的“龙头”。胜利石化总厂常减压装置1990年投产,经数次改造后,目前装置处理能力为200万吨/年,年开工时间8400
5、小时。加工原料为纯梁胜利混合原油,原料油实沸点蒸馏数据见表一。由表一可知200以前的馏分占原油的9.3%(w),煤柴油馏分(200350),收率为21.7%(w)减压蜡油馏分(350500),收率为26.51%(w),500的减压渣油(VR),收率为41.92%(w),由油品性质及实沸点蒸馏数据可得该原料适合生产燃料。本套装置由电脱盐、初馏、常压、减压、碱洗五部分组成,主要产品为石脑油,柴油,蜡油(重催原料),减压渣油(焦化原料)详见表二物料平衡表。表一 纯梁胜利混合原油实沸点蒸馏数据沸点范围收率 M 收率 V每馏分总收率每馏分总收率初馏750.80.811751001.061.861.292
6、.291001251.383.241.643.931251501.875.112.166.091501702.167.272.468.551702002.039.32.2310.782002252.9412.243.1913.972252503.6815.923.9617.932502753.4719.393.7221.652753002.8622.253.0624.713003254.126.354.3729.083253504.65314.8933.973503753.8934.894.0638.033753953.3738.263.541.533954255.8144.075.9747.
7、54254503.9748.043.9751.474504754.6252.664.5856.054755004.8557.514.7860.8350041.9299.4338.6499.47损失0.570.53表二 常减压设计物料平衡表名称收率流率 万t/a用途切割范围 原油m%200初顶气0.180.35燃料气初顶油3.687.36石脑油常顶气+损失0.070.14燃料气常顶油0.671.34石脑油HK-150常一线18.0236.05柴油馏分150-300常二线7.6115.22柴油馏分300-360常三线8.7417.48重催原料350-430减顶气0.030.06燃料气减顶油0.04
8、0.08重催原料减一线1.222.44重催原料360-380减二线13.4426.88重催原料370-470减三线13.9427.89重催原料470-545减渣32.3667.71重催原料 焦化原料545总拔67.643,生产装置特点及工艺流程:3.1工艺流程:约55的原油经地下管线,由原油泵(P-01/1、2)吸入装置,经泵增压后进入原油换热系统,原油换热分两路三段进行,出泵的原油依次进入原油-常顶换热器(E-01/1、2,温度由55上升到72),原油-减二、三油换热器(E-103温度上升到84),原油-常一中换热器(E-03/1,2温度上升到100)与热油换热,然后分两路进入第二段换热,一
9、路依次经过原油-常一线换热器(E-02/2温度升至112)和原油-减二线换热器(E-09/3温度升至138)与热油换热,第二路依次经由原油-减一线换热器(E-07温度升至107),原油-常二线换热器(E-04/2温度升至122)和原油-减压渣油换热器(E-101 温度升至138)与热油换热。换热后的原油,进入电脱盐区。138的原油经注水,注缓蚀剂后,在电脱盐混合器中混合,依次进入电脱盐罐(D-01/1、2、3)进行脱盐,脱水。脱盐后的原油原先是经原油接力泵(P-02)升压进入下一步换热。但在加初馏塔后,压力已能够满足工艺需求,所以实际工艺不经接力泵,直接进入第三段换热即脱后换热,原油分两路一路
10、依次经过原油-常一线换热器(E-02/1加热到145),原油-碱渣换热器(E-11/12、13)加热到155,原油-常三线换热器(E-06/1、2加热到188),原油-减一中换热器(E-08/1、2加热到210),原油-常二中换热器(E-05/2、3加热到234) 与热油换热。另一路依次经过原油-减三线换热器(E-10/4 升温至164) 原油-碱渣换热器(E-11/10.11升温到183)原油-常二线换热器E-04/1升温到200)原油-碱渣换热器( E-11/6.9 升温到224)原油-减二线换热器(E-09/2升温到230)与热原油换热两路脱盐原油合并混合后约为232进入初馏塔(c-10
11、1)。初馏塔为板式塔,全塔共16块塔板,经换热后的原油自第三块塔板进入,初顶汽油从初馏塔塔顶出来,经初顶空冷器(EC-101/1、2温度由出塔的100左右降至70)初顶冷却器(E-102 温度降至45),同时为抑制塔顶腐蚀在塔顶注入水,氨和缓蚀剂。经冷凝冷却后的塔顶油进入初顶回流罐(D-101)进行气液分离,灌顶不凝气送加热炉作燃料气,初顶油经初顶泵(P-103/1、2)增压后一路作为冷回流打回初馏塔顶部回流量为14.492t/h,另一路作为产品(石脑油)送出装置,初侧油自第七块塔板经出侧泵(P-102/1、2)抽出,与常一中油混合油进入常压塔,目前该侧线未使用。初底油经初底油泵(P-101/
12、1、2)抽出,经拔头油-减二中换热器(E-10/3、6温度由225上升到238)拔头油-减渣换热器(E-11/4、5升温到250)拔头油-减二中换热器(E-10/1、6升温到278),拔头油-减渣换热器(E-11/2,3升温到285),拔头油-减渣换热器(E-11/1,14升温到295)与热源换热,然后进入常压炉(F-01)加热到365分东西两路进料进入常压塔(c-01)进行分馏。常压塔为复合塔,全塔共有46块塔板,有一个塔顶循环回流,两路中段回流量,三个侧线抽出,为降低油气分压,提高原油拔出率,常压塔底通入一定量的400的气提蒸汽。365的原油自第4块塔板进入,经常压塔分馏后,常顶油气从塔顶
13、出来温度为114,经常顶空冷器(EC-01/1,2,3,4,5,6)冷去到60后进入常顶回流罐(D-02)常压塔所需回流由此经常顶回流泵(P-03/1,2)打回常压塔顶。未冷凝部分由常顶回流罐顶部进入常顶后冷器(L-08/1,2)继续冷凝冷却到40后进入常顶产品罐(D-03),再由常顶产品泵(P-04)将其送出装置,不凝气引入常压炉燃烧。塔顶冷凝水由常顶回流罐(D-02),常顶产品罐(D-03),减顶油水分离器(D-04)后进入含硫污水处理系统。常一线自34块塔板馏出,温度为180,进入常压汽提塔(c-02)气提后,由常一线泵(p-05/1,2)抽出,温度为186,然后经原油-常一线换热器(E
14、-02/1,E-02/2,温度分别降为150,116),常一线空冷器(EC-05/1,2温度将为65)及常一线冷却器(L-09/1)冷却到50后送出装置。常二线 自22块塔板馏出,温度为292进入汽提塔气提后,由常二线泵(p-06/1,2)抽出,然后经原油常二线换热器(E-04/1,E-04/2换热后,温度分别降为197,124),空气预热器,常二线空冷器(EC-06温度降为65),常二线冷却器(l-09/2)温度降为60出装置。常三线油自第6,第10块塔板馏出,温度为349,进入汽提塔后,由常三线泵(p-07/1,2)抽出,然后经原油-常三线换热器(E-06/1,2温度降为183),燃料油换
15、热器(E-12温度降为174),常三油-热水换热器(E-105温度降为117)和常三线冷却器(L-10)冷却到60后送出装置,常顶循环油由常顶循环油泵(P-08/1,2)抽出与原油换热后,温度由131降为71,返回常压塔;常一中油由常一中油泵(P-09)抽出与原油换完热后返回常压塔,温度由273降为203,常二中油由常二中油泵(P-10/1,2)抽出与脱盐原油换完热后返回常压塔,温度由321降为241。356的常底油经常底泵(P-11/1,2)抽进,增压后分两路进入减压炉(F-02)加热到385后送入减压塔(C-03)。减压塔为干式抽真空塔,内有5段填料,5段回流,本装置目前仅采用四段回流,采
16、用减顶三级抽真空。385的常渣油进入减压塔底进行分馏,70的减顶油气从减压塔(c-03)塔顶温度为70,由减顶一级抽真空(EJ-01)抽出,经减顶一级空冷器(EC-02/1,2,3,4)冷却到40,未凝油气和水蒸气由减顶二级抽真空(EJ-02)抽出,经减顶二级空冷器(EC-03/1,2)冷却到40,未凝油气和水蒸气再由减顶三级抽空器(EJ-03)抽出,经减顶三级空冷器(EC-04/1,2)冷却到40,不凝气送到常压炉作为燃料气,自三级空冷器冷却下来的油和水流到减顶油水分离器(D-04),经油、水分离后,减顶油经减顶油泵(P-24/1,2)送出装置,罐内含油污水流到污水回收系统。减一线油由第一段
17、填料出,温度为151,经减一及减顶循环回流泵(P-13/1,2)从减压塔抽出,经原油-减一线换热器(E-07温度降为107),减顶回流及减一空冷器(EC-07)冷却到70后分为两路,一路作为产品送出装置,另一路再经减顶回流冷却器(L-11/1,2)冷却到50,作为回流打入减压塔顶。256的减二线油由减二线及减一中油泵(P-14/1,2)从减压塔抽出后分两路,一路经原油-减一中换热器(E-08/1,2冷却到212),减一中蒸汽发生器(E-104)冷却到187,作为中段回流打回减压塔,另一路经原油-减二线换热器(E-09/2,降到242, E-09/3 降到150),减二线蒸汽发生器(E-09/4
18、)冷却到150。315的减三线油由减三线及减二中油泵(P-15/1,2)从减压塔抽出,经拔头油-减二中换热器(E-10/1,2换热冷却至281后分两路,一路经拔头油-减二中换热器(E-10/3,6)冷却到244,作为中段回流打回减压塔,另一路经原油-减三线换热器(E-10/4)减三线蒸汽发生器(E-10/5)冷却到150后与减二线油混合,混合油经原油-减二三线换热器(E-103)和减二,三线水冷却器(L-13)冷却到80后送出装置。减压渣油经减底泵(P-16/1,2)抽出,依次经拔头油-减渣换热器(E-11/1,14, E-11/2,3, E-11/4,5,温度冷却至238)原油-减渣换热器(
19、 E-11/6,7,8,9 ,E-11/10,11,12,13, E-101温度冷却至150)与拔头油,原油换完热后分三路,第一路经减渣水箱冷却器(L-14)冷却到130,进入灌区。第二路直接送去催化装置,第三路直接送去焦化装置。汽油碱水洗:自常顶产品泵(P-04)和初顶油出油泵(P-103/1,2)送出的常顶,初顶产品与泵P-25/1,2送出的碱液充分混合,进入沉降罐(D-17/1),沉降分离后,碱洗后的汽油送至油品灌区,碱液由罐底切入键槽循环使用。柴油碱水洗:自泵常一线泵P-05/1,2,常二线泵P-06/1,2送来的混合柴油与泵P-26送出的碱液充分混合后进入碱洗罐(D-20/1),沉降
20、后碱渣排入碱渣池,碱洗柴油自碱洗罐(D-20/1),出来后与新鲜水充分混合后进入沉降罐(D-20/2),沉降分离后水洗后的碱性水切入水井,水洗后的柴油进沉降罐(D-17/2)进一步沉降后送入油品罐。3.2工艺特点及原理:结合装置设计说明及石油加工工程课堂知识所学,总结胜利石化总厂常减压装置特点如下:3.2.1防腐蚀:依据课本知识所学常减压装置腐蚀分为两种:一是高温重油部位对金属的腐蚀 常见于加热炉管、转油线、蒸馏塔底及热油泵叶轮等部位,主要原因是由活性硫和环烷酸引起,二是低温轻油部位对金属的腐蚀,常见于冷凝水出现的相变区,主要原因是原油中的盐水解生成盐酸,若原油中既含盐又含硫,则腐蚀更为严重。
21、为此本装置采用了如下防腐蚀措施:1)采用了“一脱四注”措施,即深度电脱盐,原油注碱,塔顶馏出管线注氨,塔顶馏出管线注水,塔顶馏出管线注缓蚀剂,同时为了增加脱盐效果,又加装了超声波破乳剂。电脱盐是利用高压电场的作用,从原油中除去盐、水和其他杂质,通常,原油中所含的盐大部分都溶于水中,所以脱盐脱水的过程同时进行。原油中所含的水是以微小的水滴广泛的分布在原油中,形成相界面较稳定的乳化液,以致于很难用通常的重力沉降的方法来脱除。电脱盐的过程是在原油进脱盐罐前注入3%-5%软化水稀释,并将悬浮在原油中的盐分溶解,经混合法静态混合器充分混合,进入电脱盐罐在高压电场作用下,打破油水的相界面,促进水滴的聚结,
22、形成较大的水滴颗粒,根据原油和水的密度差,通过油层沉降于电脱盐罐底部,随着水的积聚和沉降盐和固体物也沉降于罐底,随着罐底切水自动排除。本厂目前加工的油稠度较大,乳化状态不易打破,操作条件较为苛刻,尽管设置了电脱盐的串并联,但一直采用串联电脱盐模式。脱后原油注碱液即把原油中残留的易水解的氯化镁和氯化钙转化为不易水解的氯化钠,中和在脱盐罐中水解生成的HCL,与原油中的环烷酸和含硫物质反应。不过,为了减少装置设备腐蚀及二次加工的不利影响,目前本厂已不再注碱液,改为“三注”。塔顶馏出线注氨即:氨与塔顶酸性物质中和反应(HCL H2S)进一步降低塔顶及冷却设备的腐蚀。注缓蚀剂是在金属表面形成一层致密的金
23、属保护膜,以减轻氯化铵的垢下腐蚀。在塔顶馏出线上注入软化水目的是为了洗掉注氨所生成的铵盐,以减轻垢下腐蚀,同时把最初冷凝出来的酸性水稀释,中和部分酸性物质,减轻腐蚀,减少氨用量 。并将馏出线内的气体急冷,把最初的冷凝区从塔顶向前移至馏出线内,以减轻冷凝器入口腐蚀,这里师傅告诉我们塔顶注水量不可过大以冷凝水不带油,不乳化为限度,以免造成空冷器负荷太大。2)在流程上加入了初馏塔,减轻常压塔顶、馏出管线和冷凝冷却设备的腐蚀。3.2.2增产能:石化总厂原设计加工能力为150万吨/年,改造后为扩大产能,添加了初馏塔,既有效地降低加热炉和常压塔的负荷,提高了装置的处理量 又降低原油换热系统的操作压力,从而
24、节约装置能耗和操作费用同时保证常压塔的操作平稳,有利于提高产品质量。3.2.3提高原油拔出率和分馏精确度:分馏精确度主要由物系中组分之间分离难易程度即原料性质,回流比和塔板数决定,本装置中常压塔采用了46层处理能力大,分离效果高的新型高效ADV塔盘,以提高常压塔的精馏效果。同时减压塔使用了干式减压蒸馏工艺,即不依赖注入水蒸气以降低油汽分压的减压蒸馏方式,为此全部采用高效规整填料,同时上方设液体分配器,保证填料表面的有效利用率,使用了增压喷射器,采用三级抽真空系统提高减压塔真空度,真空度控制在98KPa左右,采用大直径低速转油线,降低减压炉出口温度及到塔入口之间的压降,为减少气相携带杂质,塔内增
25、设了洗涤段。以上措施有效地解决了湿式减压塔消耗蒸汽量大,塔内汽相负荷大,塔顶冷凝冷却器的负荷大,含油污水量大的问题。并提高了拔出率和处理量,降低了减压炉的负荷,节省了燃料,降低了能耗,减少冷凝冷却器的负荷,减少含油污水量而且操作更加灵活。3.2.4采用多种回流方式:常压塔采用了塔顶回流,塔顶循环回来,常一线中段回流,常二线中段回流,减压塔采用了四段回流,这些回流保证了精馏塔的精馏的作用,取走塔内剩余热量,更方便的控制和调节塔内各点温度,保证塔内汽液相负荷分布均匀,提高产能,同时保证各产品质量。3.2.5节能措施:常减压蒸馏装置的能耗在炼厂全厂能耗中占有重要比重,其能耗约相当于加工原油量的2%
26、,胜利石化总厂常减压采用了多种节约能耗措施,能耗控制在12.5kg/t,具体措施有:1) 常,减压塔顶瓦斯引入常压炉低压瓦斯罐燃烧器燃烧,以消除污染并节约能量。2) 为了充分回收加热炉余热,常压炉,减压炉均采用了空气预热器。常压炉利用引风机和鼓风机分别将常压炉的烟气和空气引入到空气预热器中进行换热,从而降低排出烟气温度,提高空气入炉温度,降低了燃料用量。3) 减压炉采用了水热煤空气预热器,来自动力的除氧水经减压炉水热煤系统与高温烟气换热后到190,换热后的水蒸气至原油罐区给原油加热,提高原油入装置温度,冷却后的脱氧水重新返回水热煤系统构成循环,有效利用了高温烟气的能量。4) 常压炉、减压炉均采
27、用了高效燃烧器,提高辐射室的传热能力,同时常压炉在辐射室上部增加了一排横向的炉管,增加传热面积,降低烟气出辐射室温度,提高操作弹性。5) 常压塔顶油气采用了二级冷凝冷却。先将塔顶油气基本冷凝,将回流部分用泵送回塔顶,把剩下的产品部分送到下一个冷却器,冷却到所需的安全温度。第一级油气和水蒸气基本上被冷凝冷却,这里集中了绝大部分的热负荷,由于传热温差大,即热源比冷源的温度高得多,因此单位传热负荷的传热面积可以减少; 在第二级冷凝冷却中,仅冷却产品部分,虽然传热温差小,但其热负荷占总热负荷的比例小。故而,二级冷凝冷却所需的总传热面积要比一级冷凝冷却小,节省了设备费用。3.2.6优异的换热方案:胜利石
28、化总厂常减压装置采用了优异的换热方案,入装置原油先与温度低的油品换热,每次温升在20,再与温度较高的油品换热。为了降低原油通过换热器的压降,采用了两路换热,同时对于高温位热源的油品进行了多次换热,以充分回收其热量。3.2.7油品精制原理:碱水洗:碱洗是用氢氧化钠和油品中的酸性非烃化合物反应,生成相应的钠盐,这类钠盐大都溶于水,随同碱渣排掉,氢氧化钠不与烃类反应,因此碱洗能出去硫化氢,低分子硫醇,环烷酸,酚类。水洗:主要是溶解油品中经碱洗的盐,从而达到使油品净化的作用4,装置控制方案:常压塔控制原则:1) 温度控制:塔顶温度通过改变塔顶回流量来控制,顶循环回流作为辅助调节手段。一线温度用侧线流出
29、量或顶循环回流来控制,二三线温度一般用侧线流出量来调节。2)液面控制:初馏塔塔底液面通过常压炉进料量来调节,必要时可以调节原油量来辅助控制,常压塔底液面一般由炉-02两路进料量来进行均匀调节,侧线气提塔液面由侧线抽出量来调节。 3)压力控制:对塔顶压力要求保持在正常操作压力,压力波动要小,以确保常压塔的正常操作。减压塔控制原则:减压塔操作是否平稳,馏分油的质量和收率如何,在减压炉出口温度不变的情况下,取决于真空度的高低。任何油品的沸点均随外界的压力和温度的改变而改变,在减压塔内当温度不变,提高真空度时,烃分压降低,油品沸点降低,使常压重油在较低的温度下分馏出较多的馏分油,真正决定油品沸点高低的
30、是塔内进料段的真空度,提高此处的真空度,能降低油品沸点,增大油品的挥发度,提高油品拔出率在塔顶真空度不变时,降低全塔压力降,也可以提高塔内进料段的真空度。1) 温度控制:塔顶温度用顶回流量调节,侧线温度用侧线量或中段回流量调节,各填料段分别用各段回流量调节。2) 液面控制:由减一、二、三线出装置量来控制,减底液控阀来调节 。影响减压塔真空度因素主要有抽真空蒸汽压力不足,天气变化,气温升高等,对此,当抽真空蒸汽压力不足时需要提高蒸汽压力,当温度升高时可以采用加大空冷风量来调节。 加热炉控制原则:两路进料量控制要均匀,其温差不大于5度,常压炉温度控制在365度左右,减压炉温度控制在385度左右。空
31、气预热管不可长时间干烧。5, 实习心得: 实习第一天就是安全教育,炼油装置的任务是将原油加工,分别得到产品及副产品气体,这些产品易爆,易燃,往往有毒,稍有疏忽就会酿成恶果。三级安全教育用活生生的案例告诉了我们什么叫事故源于大意;走在石化总厂的厂区内,处处可见各种标语,无不强调安全的重要性。安全永远是第一要务,尤其是像炼化这样的高危企业。尽管这么严格的管理,但在现场实习中还是发现了不安全因素,也明白了安全教育天天讲,月月讲,年年讲绝不是老生常谈。实习的过程是提高自主学习能力的过程,是锻炼与人交际的过程,是培养发现问题解决问题能力的过程,是从象牙塔走向社会的过程。实习与课堂教学最大的不同在于理论学
32、习有固定的知识架构,由老师毫无保留的提供给你,实习却是一个自己发现问题并想办法解决,这里就不得不提到这次实习的老师现场的师傅们,尽管他们的文化水平不是很高,但是车间里的每一位师傅都有他们独特的技能,他们多年的工作经验,拿出很少的一部分都够我们学很长时间。记得课堂教学时对装置的开停工并没有做系统的讲述,本次实习通过与师傅的交流就很好的补充了这块的知识。装置开工时首先要进行蒸汽贯通吹扫,目的就是用蒸汽检查各条管线进行贯通,检查流程是否畅通同时用蒸汽吹扫管总的铁锈,焊渣及其他杂物,试验设备管线的密封点,焊口是否泄漏,接着就是塔试压,师傅在这里特别强调:给气初期蒸汽量不可过大,要防止冲坏塔内塔盘,试压
33、完后泄压速度同样不可太快,试验期间要多参考几处仪表防止仪表失灵。当上述环节无误时就可以进行常减压开工。常减压开工首先要引柴油试运,用柴油置换设备及系统中残存的水,利用柴油的渗透性考验设备和管线的泄露情况,考验仪表在热状态下的使用情况,一切正常时就可以引原油正式开工。而装置停工时首先要把“四注”及电脱盐注水提前停工8小时。然后降量,降温,切断进料停侧线,退油扫线,扫线蒸塔,蒸塔洗塔,炉子烧焦。印象最为深刻的是带我们班的那个班长,他是司泵出身。去的第一个班,师傅冒着天气的炎热带我们进入热泵房,给我们讲泵的原理,虽然化工原理课堂上也学过泵的知识,但真到了现场就连泵的进出口都找不到,经过师傅的细心教导
34、,逐渐就明白了泵的原理。整理如下: 如图所示1)蒸汽扫线:关闭3,4,5,9处阀门,蒸汽从1,0,2进行泵的扫线,打开放空阀9排除空气。 图二 泵的原理图2)热泵备用原理:备用时,关闭出口阀,热原油经7,8,3,0,4,6返回进料口,从而起到热泵预热的目的。3)走副线:当泵出现故障需要甩掉泵时或,关闭阀3,5,原油经6,5,8直接经单向阀10出去。 除此还有很多工作和生活细节的问题在和师傅的交流中得到解决。作为大型国有企业的下属单位,师傅们给我们讲述了这里的福利和待遇,发展和机遇,人际关系和工作心态。给还没走出校门却即将走向社会的我们上了一堂堂生动的社会课。临别前师傅还叮嘱我们不管以后干啥工作
35、第一印象非常重要,要谦虚灵活,不怕苦。 除了车间的师傅,带队老师更是为人师表的典范,从住宿安排到饮食调度,从科学化的管理到人性化的关怀。无处不体现了老师的细心与关注。实习过程中表扬过,挨批过,欢乐过,沮丧过,最终理解了老师教给我们的绝不仅仅是那些僵硬的知识点,更是一种做事的态度,更是一种做人的准则,与人为善,顺其自然;志存高远,脚踏实地。如果说这次实习知识的学习是基础,那么精神的学习就是升华。曾在一个军队战斗过的的叫战友,曾在一个学校学习过的叫校友,而我们,在烈日下一起去数管线,去跑流程,在黑夜里一起煎熬支撑,围绕在师傅身旁一起听师傅讲课,下班后在宿舍里一起欢乐,我们就是实习队队友。在这荒芜的炼油厂,在这偏僻的旅馆里,不能忘记的就是我们的友谊,或许正如老师说的,有可能这辈子就倒这么一次班,若干年后当我们再相聚相信我们都曾记得在2010年我们有过这么一段记忆,在东营,在胜利石化总厂. 6,感谢 感谢现场师傅们的辛勤指导;感谢带队老师的无私关怀和谆谆教诲;感谢学校给我们提供如此宝贵的实习机会;感谢与我一起奋斗的实习队队友,希望我们未来都能走得更好。13
- 温馨提示:
1: 本站所有资源如无特殊说明,都需要本地电脑安装OFFICE2007和PDF阅读器。图纸软件为CAD,CAXA,PROE,UG,SolidWorks等.压缩文件请下载最新的WinRAR软件解压。
2: 本站的文档不包含任何第三方提供的附件图纸等,如果需要附件,请联系上传者。文件的所有权益归上传用户所有。
3.本站RAR压缩包中若带图纸,网页内容里面会有图纸预览,若没有图纸预览就没有图纸。
4. 未经权益所有人同意不得将文件中的内容挪作商业或盈利用途。
5. 装配图网仅提供信息存储空间,仅对用户上传内容的表现方式做保护处理,对用户上传分享的文档内容本身不做任何修改或编辑,并不能对任何下载内容负责。
6. 下载文件中如有侵权或不适当内容,请与我们联系,我们立即纠正。
7. 本站不保证下载资源的准确性、安全性和完整性, 同时也不承担用户因使用这些下载资源对自己和他人造成任何形式的伤害或损失。