重型货车制动系说明书
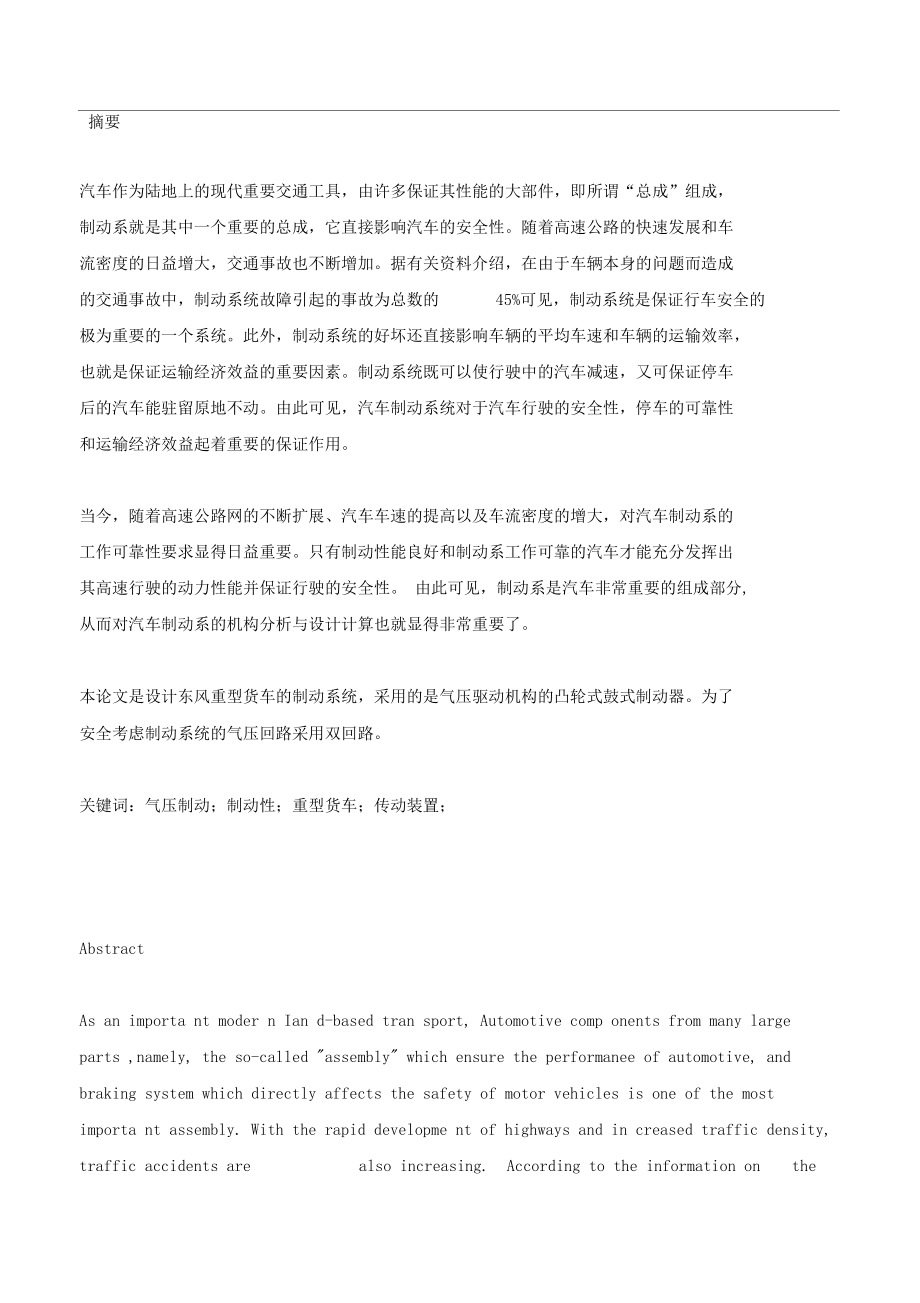


《重型货车制动系说明书》由会员分享,可在线阅读,更多相关《重型货车制动系说明书(42页珍藏版)》请在装配图网上搜索。
1、摘要汽车作为陆地上的现代重要交通工具,由许多保证其性能的大部件,即所谓“总成”组成, 制动系就是其中一个重要的总成,它直接影响汽车的安全性。随着高速公路的快速发展和车 流密度的日益增大,交通事故也不断增加。据有关资料介绍,在由于车辆本身的问题而造成 的交通事故中,制动系统故障引起的事故为总数的45%可见,制动系统是保证行车安全的极为重要的一个系统。此外,制动系统的好坏还直接影响车辆的平均车速和车辆的运输效率, 也就是保证运输经济效益的重要因素。制动系统既可以使行驶中的汽车减速,又可保证停车 后的汽车能驻留原地不动。由此可见,汽车制动系统对于汽车行驶的安全性,停车的可靠性 和运输经济效益起着重要
2、的保证作用。当今,随着高速公路网的不断扩展、汽车车速的提高以及车流密度的增大,对汽车制动系的 工作可靠性要求显得日益重要。只有制动性能良好和制动系工作可靠的汽车才能充分发挥出 其高速行驶的动力性能并保证行驶的安全性。 由此可见,制动系是汽车非常重要的组成部分, 从而对汽车制动系的机构分析与设计计算也就显得非常重要了。本论文是设计东风重型货车的制动系统,采用的是气压驱动机构的凸轮式鼓式制动器。为了 安全考虑制动系统的气压回路采用双回路。关键词:气压制动;制动性;重型货车;传动装置;AbstractAs an importa nt moder n Ian d-based tran sport, A
3、utomotive comp onents from many large parts ,namely, the so-called assembly which ensure the performanee of automotive, and braking system which directly affects the safety of motor vehicles is one of the most importa nt assembly. With the rapid developme nt of highways and in creased traffic densit
4、y, traffic accidents arealso increasing.According to the information onthevehicle itself as a result of problems caused by traffic accidents, the brake system failurecaused the accident accounting for the total number of 45%. So braking systemis an extremely importa nt system to en sure traffic safe
5、ty .In additi on, the brak ing system has a direct impact on the quality of the average vehicle speed and vehicle tran sportati on efficie ncy, that is, an importa nt factor en suri ng cost-effective tran sport. It not only can slow dow n a moving vehicle, but also to en sure that the car can be fix
6、ed in situ after parking. This shows that the vehicle braking system plays an important role in traffic safety, the reliability of parking, and transport econo mic efficie ncy.Today, with ever-exp anding highway n etwork, the improveme nt of vehicle speed and traffic density, on the work ofautomotiv
7、e braking system relia become increasinglyimporta nt. Only vehicles which have good brak ing performa nee and reliable brak ing system can give full play to their high-speed dynamic performance and to ensure the safety of traveling. This shows that the braking system is a very important component of
8、 the vehicle, thus it s very important to the analysis and design of brake system bodies.bility requireme ntsKeywords: air brake; Brake; Heavy trucks; Tran smissi on device;1绪论1.1研究制动系统的意义近百年来,汽车工业之所以常胜不衰主要得益于汽车作为商品在世界各处都有广阔的市场, 生产批量大而给企业带来丰厚的利润。最主要的是科学技术的不断进步,使汽车能逐渐完善 并满足使用者的需求。随着我国汽车产业的不断发展和新交通法规的
9、实施,我国的汽车及其 运输管理开始走向正轨,农用运输车将逐渐退出市场,而重型运输自卸车逐渐呈现出广阔的 发展前景。然而车辆交通安全历来是人们最为关心的问题之一,它直接关系到人民生命和财 产的损失,因此汽车制动系统的可靠性研究至关重要。汽车制动系是用于使行驶中的汽车减 速或停车,使下坡行驶的汽车的车速保持稳定以及使以停驶的汽车在原地(包括在斜坡上) 驻留不动的机构。汽车制动系直接影响着汽车行驶的安全性和停车的可靠性。随着高速公路 的迅速发展和车速的提高以及车流密度的日益增大,为了保证行车安全、停车可靠,汽车制 动系的工作可靠性显得日 益重要。也只有制动性良好、制动系工作可靠的汽车,才能充分发 挥
10、其动力性能。汽车制动系统至少有两套独立的制动装置,即行车制动装置和驻车制动装置:重型汽车或经 常在山区行驶的汽车要增设应急制动装置及辅助制动装置;牵引车还应有自动制动装置。行 车制动装置用于使行驶中的汽车强制减速或停车, 并使汽车在下短坡时保持适当的稳定车速。 其驱动机构常采用双回路或多回路结构,以保证其工作可靠。驻车制动装置用于使汽车可靠 而无时间限制地停驻在一定位置甚至在斜坡上,它也有助于汽车在坡路上起步。驻车制动装 置应采用机械式驱动机构而不用液压或气压驱动,以免其产生故障。应急制动装置用于当行车制动装置意外发生故障而失效时,这时则可利用应急制动装置的机 械力源(如强力压缩弹簧)实现汽车
11、制动。应急制动装置不必是独立的制动系统,它可利用行 车制动装置或驻车制动装置的某些制动器件。应急制动装置也不是每车必备,因为普通的手 力驻车制动器也可以起应急制动的作用。辅助制动装置用于山区行驶的汽车上,利用发动机排气制动或电涡流制动等辅助制动装置, 则可使汽车下长坡时长时间而持续地减低或保持稳定车速并减轻或解除行车制动器的负荷。通常,在总质量为5t以上的客车上和12t以上的载货汽车上装备这种辅助制动一减速装置。 任何一套制动装置均由制动器和制动驱动机构两部分组成。制动器有鼓式与盘式之分。行车 制动是用脚踩下制动踏板操纵车轮制动器来制动全部车轮,而驻车制动则多采用手制动杆操 纵,且具有专门的中
12、央制动器或利用车轮制动器进行制动。中央制动器位于变速器之后的传动系中,用于制动变速器第二轴或传动轴。行车制动和驻车制动这两套 制动装置必须具有独立的制动驱动机构,而且每车必备。行车制动装置的驱动机构,分液压 和气压两种型式。用液压传递操纵力时还应有制动主缸和制动轮缸以及管路;用气压操纵时 还应有空气压缩机、气路管道、贮气简、控制阀和制动气室等。过去,大多数汽车的驻车制动和应急制动都使用中央制动器,其优点是制动位于主减速器之前的变速器第二轴或传动轴的制动力矩较小,容易满足操纵手力小的要求。但在用作应急制 动时,往往使传动轴超载。现代汽车由于车速提高,对应急制动的可靠性要求更严,因此,在中、高级轿
13、车和部分总质量在1.5t以下的载货汽车上,多在后轮制动器上附加手操纵的机 械式驱动机构,使之兼起驻车制动和应急制动的作用,从而取消了中央制动器。重型载货汽 车由于采用气压制动,故多对后轮制动器另设独立的由气压控制而以强力弹簧作为制动力源 的应急兼驻车制动驱动机构,也不再设置中央制动器。但也有一些重型汽车除了采用了上述 措施外,还保留了由气压驱动的中央制动器,以便提高制动系的可靠性。1.2制动系统的发展状况目前国内外汽车制动系统的发展大致相似,国内研究现状:目前制动系统的供能装置主要是,人力制动、伺服制动、动力制动三种形式。目前,人力仅是来控制操纵机构,助力系统分为 伺服制动、气定液压制动、液压
14、制动。液压制动是目前得到广泛应用的一种制动系统。传动 装置上,普遍都是采用气或液压通过管路传递到制动器上,进行压力制动。目前,也有通过 电机进行制动的,通过电机产生的制动力直接作用在制动器上进行制动。制动器主要有鼓式 制动器、盘式制动器两种。鼓式制动器分为很多种、双领蹄式制动器、领从蹄式制动器等。 盘式制动器有固定钳式制动器、浮动钳式制动器等。盘式制动器的摩擦材料在逐渐的发展, 目前国内多以半金属纤维增强复合摩擦材料应用最为普遍。但一些企业和地方根据本身的特 点,也在研究新型摩擦材料。大约从20世纪60年代开始,电子技术的进步成为汽车工业发展的最大动力。现代汽车的控 制系统几乎全由电子控制装置
15、实现,在提高经济性、动力性、可靠性、舒适性和排放控制系 统方面起到明显的作用。因此,电子产品在汽车上的应用比例,已成为评价其品质、性能指 标的重要依据。今天,ABS/ASR已经成为欧美和日本等发达国家汽车的标准设备。目前, ABS/ASR已在欧洲新 载货车中普遍使用,并且欧共体法规 EEC/71/320已强制性规定在总质量大于3.5t的某些载 货车上使用,重型车是首先装用的。然而 ABS/ASF只是解决了紧急制动时附着系数的利用,并可获得较短的制动距离及制动方向稳定性,但是它不能解决制动系统中的所有缺陷。因此ABS/ASF功能,同时可进行制动强度的控制。车辆制动控 制系统的发展主要是控 制技术
16、的发展。一方面是扩大控制范围、增加控制功能;另一方面是采用优化控制理论,实 施伺服控制和高精度控制。在第一方面,ABS功能的扩充除ASR外,同时把悬架和转向控制扩展进来,使ABS不仅仅是防抱死系统,而成为更综合的车辆控制系统。1.3对汽车制动系统的展望今天,ABS/ASR经成为欧美和日本等发达国家汽车的标准设备。车辆制动控制系统的发展主要是控制技术的发展。一方面是扩大控制范围、增加控制功能;另一方面是采用优化控制理论,实施伺服控制和高精度控制。在第一方面,ABS功能的扩充除ASR外,同时把悬架和转向控制扩展进来,使 ABS不仅仅是 防抱死系统,而成为更综合的车辆控制系统。制动器开发厂商还提出了
17、未来将 ABS/TCS和 VDC 与智能化运输系统一体化运用的构想。随着电子控制传动、悬架系统及转向装置的发展,将 产生电子控制系统之间的联系网络,从而产生一些新的功能,如:采用电子控制的离合器可 大大提高汽车静止启动的效率;在制动过程中,通过输入一个驱动命令给电子悬架系统,能 防止车辆的俯仰。在第二个方面,一些智能控制技术如神经网络控制技术是现在比较新的控制技术,已经有人 将其应用在汽车的制动控制系统中。ABS/ASR并不能解决汽车制动中的所有问题。因此由ABS/ASRS一步发展演变成电子控制制动系统(EBS),这将是控制系统发展的一个重要的方向。 但是EBS要想在实际中应用开来,并不是一个
18、简单的问题。除技术外,系统的成本和相关的 法规是其投入应用的关键。经过了一百多年的发展,汽车制动系统的形式已经基本固定下来。随着电子,特别是大规模、 超大规模集成电路的发展,汽车制动系统的形式也将发生变化。如凯西-海斯(K-H)公司在一辆实验车上安装了一种电一液(EH)制动系统,该系统彻底改变了制动器的操作机理。通过采 用4个比例阀和电力电子控制装置,K-H公司的EBM就能考虑到基本制动、ABS牵引力控制、 巡航控制制动干预等情况,而不需另外增加任何一种附加装置。EBM系统潜在的优点是比标准制动器能更加有效地分配基本制动力,从而使制动距离缩短5% 一种完全无油液、完全的电路制动BBW(Brak
19、e-By-Wire)的开发使传统的液压制动装置成为历史。BBW是未来制动控制系统的L发展方向。全电制动不同于传统的制动系统,因为其传递的是 电,而不是液压油或压缩空气,可以省略许多管路和传感器,缩短制动反应时间。其主要包含以下部分:(1)电制动器。其结构和液压制动器基本类似,有盘式和鼓式两种,作动器是电动机;(2)电制动控制单元(ECU)。接收制动踏板发出的信号,控制制动器制动;接收驻车制动信 号,控制驻车制动;接收车轮传感器信号,识别车轮是否抱死、打滑等,控制车轮制动力,实现防抱死和驱动防滑。由于各种控制系统如卫星定位、导航系统,自动变速系统,无级转 向系统,悬架系统等的控制系统与制动控制系
20、统高度集成,所以ECU还得兼顾这些系统的控制;(3)轮速传感器。准确、可靠、及时地获得车轮的速度;(4)线束。给系统传递能源和电控制信号;(5)电源。为整个电制动系统提供能源。与其他系统共用。可以是各种电源,也包括再生能 源。从结构上可以看出这种全电路制动系统具有其他传统制动控制系统无法比拟的优点:(1)整个制动系统结构简单,省去了传统制动系统中的制动油箱、制动主缸、助力装置。液 压阀、复杂的管路系统等部件,使整车质量降低;(2)制动响应时间短,提高制动性能;(3) 无制动液,维护简单;(4) 系统总成制造、装配、测试简单快捷,制动分总成为模块化结构;(5) 采用电线连接,系统耐久性能良好;(
21、6) 易于改进,稍加改进就可以增加各种电控制功能。全电制动控制系统是一个全新的系统,给制动控制系统带来了巨大的变革,为将来的车辆智能控制提供条件。但是,要想全面推广,还有不少问题需要解决:首先是驱动能源问题。采用全电路制动控制系统,需要较多的能源,一个盘式制动器大约需 要1kW的驱动能量。目前车辆12V电力系统提供不了这么大的能量,因此将来车辆动力系统 采用高压电,加大能源供应,可以满足制动能量要求,同时需要解决高电压带来的安全问题。其次是控制系统失效处理。全电制动控制系统面临的一个难题是制动失效的处理。因为不存 在独立的主动备用制动系统,因此需要一个备用系统保证制动安全,不论是ECU元件失效
22、,传感器失效还是制动器本身、线束失效,都能保证制动的基本性能。实现全电制动控制的一 个关键技术是系统失效时的信息交流协议,如 TTP/G系统一旦出现故障,立即发出信息,确保信息传递符合法规最适合的方法是多重通道分时区(TDMA)它可以保证不出现不可预测的信息滞后。 TTP/C协议是根据TDMA制定的。第 三是抗干扰处理。车辆在运行过程中会有各种干扰信号, 如何消除这些干扰信号造成的影响, 目前存在多种抗干扰控制系统,基本上分为两种:即对称式和非对称式抗干扰控制系统。对称式抗干扰控制系统是用两个相同的 CPU和同样的计算程序处理制动信号。非对称式抗干 扰控制系统是用两个不同的 CPU和不一样的计
23、算程序处理制动信号。两种方法各有优缺点。另外,电制动控制系统的软件和硬件如何实现模块化,以适应不同种类的车型需要;如何实 现底盘的模块化,是一个重要的难题。只有将制动、转向、悬架、导航等系统综合考虑进来,从算法上模块化,建立数据总线系统,才能以最低的成本获得最好的控制系统电制动控制系统首先用在混合动力制动系统车辆上,采用液压制动和电制动两种制动系统。这种混合制动系统是全电制动系统的过渡方案。由于两套制动系统共存,使结构复杂,成本 偏咼。随着技术的进步,上述的各种问题会逐步得到解决,全电制动控制系统会真正代替传统的以 液压为主的制动控制系统。综上所述,现代汽车制动控制技术正朝着电子制动控制方向发
24、展。全电制动控制因其巨大的 优越性,将取代传统的以液压为主的传统制动控制系统。同时,随着其他汽车电子技术特别 是超大规模集成电路的发展,电子元件的成本及尺寸不断下降。汽车电子制动控制系统将与其他汽车电子系统如汽车电子悬架系统、汽车主动式方向摆动稳 定系统、电子导航系统、无人驾驶系统等 融合在一起成为综合的汽车电子控制系统,未来的 汽车中就不存在孤立的制动控制系统,各种控制单元集中在一个ECU中,并将逐渐代替常规的控制系统,实现车辆控制的智能化。但是,汽车制动控制技术的发展受整个汽车工业发展的制约。有一个巨大的汽车现有及潜在 的市场的吸引,各种先进的电子技术、生物技术、信息技术以及各种智能技术才
25、不断应用到 汽车制动控制系统中来。同时需要各种国际及国内的相关法规的健全,这样装备新的制动技 术的汽车就会真正应用到汽车的批量生产中。2制动系的总体设计2.1制动系的设计要求1)能适应有关标准和法规的规定。各项性能指标除满足设计任务书的规定和国家标准的有关要求外,也应考虑销售对象国家和地区的法规和用户要求2)具有足够的制动效能。包括行车制动效能和驻坡制动效能3)工作可靠。汽车至少应有行车制动和驻车制动两套制动装置且它们的制动驱动机构应是各 自独立的。行车制动装置的制动驱动机构至少应有两套独立的管路,当其中一套失效时,另 一套应保证汽车制动效能不低于正常值的 30%驻车制动装置应采用工作可靠的机
26、械式制动 驱动机构。4)制动效能的水稳定性好。制动器摩擦表面浸水后,会因水的润滑作用使摩擦系数急剧减小 而发生所谓的“水衰退”现象。一般规定在出水后反复制动 515次,即应恢复其制动效能。 良好的摩擦材料吸水率低,其摩擦性能恢复迅速。也应防止泥沙、污物等进入制动器工作表面,否则会使制动效能降低并加速磨损。某些越野汽车为了防止水相泥沙侵入而采用封闭的 制动器。5)制动时的操纵稳定性好。即以任何速度制动,汽车都不应当失去操纵性和方向稳定性。为此,汽车前、后轮制动器的制动力矩应有适当的比例,最好能随各轴间载荷转移情况而变化; 同一轴上左、右车轮制动器的制动力矩应相同。否则当前轮抱死而侧滑时,将失去操
27、纵性; 后轮抱死而侧滑甩尾,会失去方向稳定性;当左、右轮的制动力矩差值超过15%时,会发生制动时汽车跑偏。对于汽车列车,除了应保证列车各轴有适当的制动力分配外,也应注意主、挂车之间各轴制动开始起作用的时间,特别是主、挂车之间制动开始时间的协调。6)制动效能的热稳定性好。7)制动踏板和手柄的位置和行程符合人-机工程学的要求,即操作方便性好,操纵轻便、舒 适,能减少疲劳。8)作用滞后的时间要尽可能地短。9)制动时不应产生振动和噪声。10)与悬架、转向装置不产生运动干涉,在车轮跳动、汽车转向时不会引起自行制动11) 制动系中应有音响或光信号等警报装置,以便能及时发现制动驱动件的故障和功能失效。12)
28、制动系的机件应使用寿命长、制造成本低,对摩擦材料的选择也应考虑到环保要求2.2汽车参数的选择货车的主要参数长?宽?高(mm 8995?2470?2800轴 距(mm 5100质心距前轴(mm 3480质心距后轴(mm 1620前轮距(mr)2010后轮距(mr)1840最小离地间隙(mm 206整车整备质量(kg) 6900额定载重量(kg)10100 最高车速(km/h)90质心高度(mm)空载1200mm满载850mm吨位级别重卡2.3制动器方案的选择鼓式制动器一般可按其制动蹄受力情况进行分类,它们的制动效能、制动鼓的受力平衡状态以及车轮旋转方向对制动效能的影响均不同,制动器主要由图示进行
29、分类:图2-1制动器的分类Figure 2-1 brake classificati on盘式制动器摩擦副中的旋转元件是以端面工作的金属圆盘,被称为制动盘。其固定元件则有 着多种结构型式,大体上可分为两类。一类是工作面积不大的摩擦块与其金属背板组成的制 动块,每个制动器中有24个。这些制动块及其促动装置都装在横跨制动盘两侧的夹钳形支 架中,总称为制动钳。这种由制动盘和制动钳组成的制动器称为钳盘式制动器。另一类固定 元件的金属背板和摩擦片也呈圆盘形,制动盘的全部工作面可同时与摩擦片接触,这种制动 器称为全盘式制动器。钳盘式制动器过去只用作中央制动器,但目前则愈来愈多地被各级轿 车和货车用作车轮制
30、动器。全盘式制动器只有少数汽车(主要是重型汽车)采用为车轮制动器。鼓式刹车有良好的自刹作用,由于刹车来令片外张,车轮旋转连带着外张的刹车鼓扭曲一个 角度(当然不会大到让你很容易看得出来)刹车来令片外张力(刹车制动力)越大,则情形就越 明显,因此,一般大型车辆还是使用鼓式刹车,除了成本较低外,大型车与小型车的鼓刹, 差别可能只有大型采气动辅助,而小型车采真空辅助来帮助刹车。成本较低:鼓式刹车制造技术层次较低,也是最先用于刹车系统,因此制造成本要比碟式刹车低凸轮式制动器 目前,所有国产汽车及部分外国汽车的气压制动系统中,都采用凸轮促动的车轮制动器,而且大多设计成领从蹄式大货车因为吨位的原因制动力的
31、力量也必须要大,所以用气压(就是鼓式刹车)的方式制动, 如果使用碟式制动,需要把碟做成相当大的直径,而使用鼓式制动,只需要加深鼓的深度就 可以了,直径可以不太大,所以安装起来比较方便。所以在本设计中选用的是鼓式凸轮制动2.4制动驱动机构方案选择制动驱动机构将来自驾驶员或其他力源的力传给制动器,使之产生制动力矩。根据制动力源 的不同,制动驱动机构一般可分为简单制动、动力制动和伺服制动三大类。而力的传递方式 又有机械式,液压式,气压式和气压-液压式的区别,如下表。表2-1制动驱动机构的结构形式制动力源型式制动力源工作介质简单制动系(人力制动系)司机体力 力的传递方式 型式 工作介质 用途 机械式
32、杆系或钢丝绳 液压式制动液仅用于驻车制动部分微型汽车的行车制动动力制动系 空气 气压式 气压-液压式 空气 空气,制动液 制动液 中,重型汽车的行车制 动气压动力制动系发动机动力液压动力制动系制动液液压式私服制动系 真空伺服制动系 气压伺服制动系 司机体力与液压伺服制动系 发动机动力 空气 空气 制动液 液压式 制动液 轿车,微,轻,中型汽车的行车制动人力制动系统是简单制动单靠驾驶员施加的踏板力或手柄力作为制动力源,人力制动。其又分为机械式和液压式两种机构形式。机械式完全靠杆系传力,由于机械效率低,传 动比小,润滑点多,且难以保证前、后轴制动力的正确比例和左、右轮制动力的均衡,所以 在汽车的行
33、车制动装置中已被淘汰。但因其结构简单,成本低,工作可靠,主要用在驻车制 动。液压式简单制动系(通常简称为液压制动系)用于行车制动装置。液压制动的优点是:作用 滞i后时间短(0.10.3s),工作压力高(可达1012MPa,轮缸尺寸小,可布置在制动器内 部作为制动蹄张开机构或制动块压紧机构,使之结构简单、紧凑、质量小、造价低;机械效 率高。液压制动的主要缺点是:过度受热后,部分制动液汽化,在管路中形成气泡而影响传 输,即产生所谓“气阻”,使制动效能减低甚至失效,而当气温过低时(-25?C和更低时), 由于制动液的粘度增大,使工作的可靠性降低,以及当有局部损坏时,使整个系统都不能继 续工作。液压制
34、动曾被广泛应用于乘用车和总质量不大的商用车。伺服制动的制动能源是人力和发动机并用。在正常情况下,其输出工作压力主要由动力伺服 系统产生,而在动力伺服系统失效时,仍可全由人力驱动液压系统产生一定程度的制动力(即由伺服制动转变为人力制动)。因此,在中级以上的轿车及轻,中型客,货汽车上得到了广泛 的应用。按伺服系统能源的不同,可分为真空伺服制动系、气压伺服制动系和液压伺服制动系。其伺 服能源分别为真空能(负气压能),气压能和液压能。真空伺服制动系是利用发动机进气管中节气门后的真空度(负压,一般可达0.050 .07 MPa)作动力源,一般的柴油车若采用真空伺服制动系时,则需有专门的真空源一由发动机驱
35、动的 真空泵或喷吸器构成。气压伺服制动系是由发动机驱动的空气压缩机提供压缩空气作为动力 源,伺服气压一般可达0.60.7 MPa。故在输出力相等时,气压伺服气室直径比真空伺服气 室直径小得多。且在双回路制动系中,如果伺服系统也是分立式的,贝U气压伺服比真空伺服 更适宜,因此后者难于使各回路真空度均衡。但气压伺服系统的其他组成部分却较真空伺服 系统复杂得多。真空私服制动系多用于总质量在1.1t-1.35t以上的轿车及装载质量在6t以下的轻,中型载货汽车上,气压伺服制动系则广泛用于装载质量为612t的商用车,以及少数几种排量在4.0L以上的乘用车。全液压动力制动系是用发动机驱动油泵产生的液压作为制
36、动力源。其制动系的液压系统与动 力转向的液压系统相同,也有开式(常流式)和闭式(常压式)两种。开式(常流式)系统 在不制动时,制动液在无负荷状况下由油泵经制动阀到储液罐不断地循环流动,制动时则借助于阀的节流而产生所需的液压进入轮缸。闭式(常压式)回路因平时保持着高 液压,故又称常压式。它对制动操纵的反应比开式的快,但对回路的密封要求较高。当油泵 出故障时,开式的将立即补气之动作用,而闭式的还有可能利用回路中的蓄能器的液压继续 进行若干次制动。故目前汽车用的全液压动力制动系多用闭式(常压式)的。全液压动力制动系除具有一般液压制动系统的有点外,还具有操纵轻便,制动反应快,制动 能力强,受气阻影响较
37、小,易于采用制动力调节装置和防滑移装置,及可与动力转向,液压悬架,举升机构及其他辅助设备共用液压泵和储油罐等优点。但其机构复杂,精密件多,对系统的封闭性要求也较高,故并未得到广泛应用。各种形式的动力制动在动力系统失效时,制动作用即全部丧失。气压制动系统是发展最早的一种动力制动系统。其供能装置和传动装置全部是气压式的。其 控制装置大多数是由制动踏板机构和制动阀等气压控制原件组成,也有的在踏板机构和制动 阀之间还串联有液压式操纵传动装置。气压制动由于可获得较大的制动驱动力且主车与被拖 的挂车以及汽车列车之间制动驱动系统的连接装置结构简单联接和断开都很方便,因此广泛用于总质量为8t以上尤其是15t以
38、上的载货汽车,越野汽车和客车上但气压制动系必须采用 空气压缩机,贮气罐,制动阀等装置,使结构复杂,笨重,轮廓尺寸大,造价高;管路中气压的产 生和撤除均较慢,作用滞后时间较长(0.30.9s),因此在制动阀到制动气室和贮气罐的距离 较远时有必要加设气动的第二级控制元件一一继动阀(即加速阀)以及快放阀;管路工作压力较低(一般为0.50.7MPa),因而制动气室的直径大,只能置于制动器之外,再通过杆件及凸轮 或楔块驱动制动蹄,使非簧载质量增大;另外,制动气室排气时也有较大噪声。汽车在行驶过程 中驾驶员要经常使用制动器,为了减轻驾驶员的工作强度,目前汽车基本上都采用了伺服制 动系统或动力制动系统。载重
39、汽车一般均采用动力制动系统。在本设计中选用的是气压制动系统。3制动过程的动力学参数计算3.1制动过程车轮所受的制动力汽车受到与行驶方向相反的外力时,才能从一定的速度制动到较小的车速或直至停车。这个 外力只能由地面和空气提供。但由于空气阻力相对较小,所以实际外力主要是由地面提供的, 称之为地面制动力。地面制动力越大,制动距离也越短,所以地面制动力对汽车制动性具有 决定性影响。F面分析一个车轮在制动时的受力情况(1)地面制动力假设滚动阻力偶矩、车轮惯性力和惯性力偶矩均可忽略图,则车轮在平直良好路面上制动时 的受力情况如图4-1所示。图3-1车轮制动时受力简图FIG. 3-1 wheel brak
40、ing force diagramT?是车轮制动器中摩擦片与制动鼓或盘相对滑动时的摩擦力矩,单位为N?m Fxb是地面制动力,单位为N; W为车轮垂直载荷、Fp为车轴对车轮的推力、Fz为地面对车轮的法向反作用力,它们的单位均为 N显然,从力矩平衡得到式中,re为车轮的有效半径(n)o地面制动力是使汽车制动而减速行驶的外力,但地面制动力取决于两个摩擦副的摩擦力:一 个是制动器内制动摩擦片与制动鼓或制动盘间的摩擦力,一个是轮胎与地面间的摩擦力一附 着力。(2)制动器制动力在轮胎周缘为了克服制动器摩擦力矩所需的力称为制动器制动力,以符号F?表示,显然F?Ture(3-2)式中:T?是车轮制动器摩擦副
41、的摩擦力矩。制动器制动力F?是由制动器结构参数所决定的。它与制动器的型式、结构尺寸、摩擦副的而摩擦系数和车轮半径以及踏板力有关。图3-2给出了地面制动力、车轮制动力及附着力三者之间的关系。当踩下制动踏板时,首先 消除制动系间隙后,制动器制动力开始增加。开始时踏板力较小,制动器制动力F?也较小,地面制动力Fxb足以克服制动器制动力F?,而使得车轮滚动。此时,Fxb=F?,在此处键入公 式。且随踏板力增加成线性增加。图3-2地面制动力、车轮制动力及附着力之间的关系FIG. 3-2 ground brak ing force, wheels brak ing force and the relati
42、 on shipbetwee n theadhesion但是地面制动力是地面摩擦阻力的约束反力,其值不能大于地面附着力F?或最大地面制动力Fxbmax即:(3-3)(3-4)当制动踏板力上升到一定值时,地面制动力Fxb达到最大地面制动力Fxb=F?,车轮开始抱死不转而出现拖滑现象。随着制动踏板力以及制动管路压力的继续升高,制动器制动 力F?继续增加,直至踏板最大行程,但是地面制动力Fxb不再增加。上述分析表明,汽车地面制动力 Fxb取决于制动器制动力F?,同时又受到地面附着力F?的闲置。只有当制动器制动力F?足够大,而且地面又能够提供足够大的附着力F?,才能获得足够大的地面制动力。(3) 地面
43、对前、后车轮的法向反作用力图3-3所示为,忽略汽车的滚动阻力偶和旋转质量减速时的惯性阻力偶矩,汽车在水平路面 上制动时的受力情况。图3-3制动时的汽车受力图FIG. 3-3 braking by trying to the car因为制动时车速较低,空气阻力 Fw可忽略不计,则分别对汽车前后轮接地点取矩,整理得前、后轮的地面法向反作用力 Fz1 、 Fz2 为G?Fz1?(b?hg)?L?G?F?(a?hg)z2?L?(3-5)式中:du dt?zg,z为制动强度,G-汽车所受重力;L汽车轴距;L1汽车质心离前轴距离;L2汽车质心离后轴距离;hg为汽车质心高度(满载时hg=850mi)g重力加
44、速度;若在附着系数为?的路面上制动,前、后轮都抱死(无论是同时抱死或分别先后抱死),此时Fxb?F?G或 dudt?g 。 地面作用于前、后轮的法向反作用力为G?Fz1?(b?hg)?L?G?F?(a?hg)z2?L?(3-7)式(3-6 )、(3-7)均为直线方程,由上式可见,当制动强度或附着系数改变时,前后轴车轮的地面法向反作用力的变化是很大的,前轮增大,后轮减小。(4)理想的前、后制动器制动力分配曲线汽车总的地面制动力为:FB式中:z制动强度;(3-8)前轴车轮的地面制动力;后轴车轮的地面制动力FB2由式 (3-5)式 (3-6) 求得前、后轴车轮附着力 :?L2F?1?(G?FB?L?
45、L?F?2?(G1?FB?LhgLhgL)?GLGL(L2?qhg)?(3-9) (L1?qhg)?)?前已指出,制动时前、后车轮同时抱死,对附着条件的利用,制动时汽车的方向稳定性均较为有利。此时的前、后轮制动器制动力 F?1和F?2的关系曲线,常称为理想的前、后轮制动器制动力分配曲线。在任何附着系数 ?的路面上,前、后轮制动器制动力分别等于各自的附着力,即:?Fu1?Fu2?G?Fu1?Fz1?Fu2?Fz2?将(3-7)式代入上式,得 ?Fu1?Fu2?G?Fu1b?hg?Fu2a?hg?( 3-10)式中:Fu1前轴车轮的制动器制动力,Fu1?Fxb1?Fz1;Fu2后轴车轮的制动器制动
46、力,Fu2?Fxb2?Fz2Fxbl前轴车轮的地面制动力;Fxb2后轴车轮的地面制动力;Z1;,Z2地面对前、后轴车轮的法向反力;汽车的重力;Ga , b汽车质心离前、后轴距离;汽车质心高度。hg消去变量?,得Fu21?2?(Gbhg?2Fu1)?( 3-11)如已知汽车轴距L、质心高度hg、总质量ma质心的位置b (质心至后轴的距离),就可用式(3-11 )绘制前、后制动器制动力的理想分配关系曲线,简称I曲线。图3-4就是根据式(3-11) 绘制的汽车在空载和满载两种工况的I曲线。图3-4 I曲线示意图FIG. 3-4 I curve schemes根据方程组(3-30)的两个方程也可直接绘
47、制I曲线。假设一组?值(? = 0.1,0.2,0.3,?,1.0),每个?值代入方程组(3-30 ),就具有一个交点的两条直线,变化?值,取得一组交点,连接这些交点就制成I曲线,见图3-5 o图3-5 理想的前、后制动器制动力分配曲线FIG. 3-5 ideal before and after the fricti onal brak ing power distribute n curveI曲线时踏板力增长到使前、后车轮制动器同时抱死时前、后制动器制动力的理想分配曲线。前、后车轮同时抱死时,Fu1?Fxb1?F?1, Fu1?Fxb1?F?2所以I曲线也是前、后车轮同时抱死时,F?1和F
48、?2的关系曲线。在本设计中,重型货车在满载时的基本数据如下:汽车的重力 G=17000kg轴距L=5100mm质心距前轴 a=3480mm质心距后轴b=1620mm地面附着系数?0.7。将以上数据代入(3-7)( 3-10 ),得Fu1?Fxb1?F?1?50116.7N,Fu2?Fxb2?F?2?68833.3NFz仁75705.9N, Fz2=104294.1N。(5) 具有固定比值的前、后制动器制动力两轴汽车的前、后制动器制动力的比值一般为固定的常数。通常用前制动器制动力对汽车总制动器制动力之比来表明分配比例,即制动器制动力分配系数?,它可表示为?FF?1?(3-12)?Fu1?Fu2式
49、中,Fu1为前制动器制动力;Fu为汽车总制动器制动力,F?制动器制动力。故F?1,Fu2 为后轮?F?,F?2? (1?) F?且F?1F?2若用Fu2?B(Fu1)?1?(3-13)表示,则其为一条直线,此直线通过坐标原点,且其斜率为tan ?1?它是实际前、后制动器制动力实际分配线,简称为?线。如图3-6所示。图3-6载货汽车的I曲线和?曲线FIG. 3-6 mani fest car I curve and? curve3.2制动距离与制动减速度计算(1) 制动距离与制动减速度制动距离与汽车的行驶安全有直接关系,它指的是汽车速度为 uO时,从驾驶员开始操控制动控制装置到汽车完全停住为止所
50、驶过的距离。制动距离与制动踏板力、路面附着条件、 车辆载荷、发动机是否结合等许多因素有关。由于各种汽车的动力性不同,对制动效能也提 出了不同的要求:一般轿车、轻型货车行驶车速高,所以要求制动效能也高;重型货车行驶速度低,要求就稍微低一点。制动减速度是制动时车速对时间的导数,即与制动器制动力及附着力有关。在不同的路面上,由于地面制动力为Fxb?bGdudt。它反映了地面制动力的大小,因此故汽车能达到的减速度(m/s2 )为abmax?bg若允许汽车的前、后轮同时抱死,则abmax?sg式中:G-汽车所受重力,N;(?s=0.7)?s 滑动附着系数;gv重力加速度,g?9.8 m/s2 ;制动初速
51、度,m/s;代入数据得到(2m)制动距离的分析 bnmax?0.7?9.8?6.86m/1?S?3.6?.2?ua022?u?a02?25.92abmax?.2单位s; (0.2s0.45s,计算时取0.3s )(3-14)式中:?2制动机构滞后时间,v2 制动器制动力增长过程所需的时间,单位s;(一般为0.2s)制动器的作用时间,般在 0.2s0.9s之间;2 制动初速度,m/s;计算时总质量10t以上的汽车取v=65km/h=18.1m/s;代入数据得:S?136(0.3?0.22)?19.4?19.4225.92?6.86?4.34s综合国外有关标准和法规:进行制动效能试验时的制动减速度
52、a,载货汽车应为3.46.5m/s2;相应的最大制动距离ST:货车为ST?0.15v?v2/115,式中第一项为反应距离;第二项为制动距离,ST单位为m v单位为m/s。代入数据得:ST?0.15v?v/115?0.15?18.1?18.1/115?226.62m显然,Sv ST,故本设计符合要求。3.3同步附着系数与附着系数利用率计算由式(3-13)可表达为Fu1Fu2?1?(3-15)上式在图3-3中是一条通过坐标原点且斜率为(1-?)/?的直线,是汽车实际前、后制动器制 动力分配线,简称?线。图4-6中?线与I曲线交于B点,B点处的附着系数?=?0,则称?0为 同步附着系数。同 步 附
53、着 系 数 的 计 算 公 式 是:( 3)对于前、后制动器制动力为固定比值的汽车,只有在附着系数?等于同步附着系数?0的路面上,前、后车轮制动器才会同时抱死。当汽车在不同?值的路面上制动时,可能有以下情况:(1) 当?但丧失转向能力。(2) 当?0, ?线位于I曲线上方,制动时总是后轮先抱死,这时容易发生后轴侧滑使汽车失去方向稳定性。(3) 当?0,制动时汽车前、后轮同时抱死,是一种稳定工况,但也失去转向能力。将以下数据汽车的重力 G=170000kg轴距L=5100mr,质心距前轴a=3480mml质心距后轴b=1620mm地面附着系数?0.7。代入式(3-16),得?Fu1Fu?5011
54、6118950.7?0.46把?值代入式(4-15)得:tan =Fu1Fu2?1?=1.168; =49.43 为了防止汽车的前轮失去转向能力和后轮产生侧滑,希望在制动过程中,在即将出现车轮抱死但尚无任何车轮抱死时的制动减速度,为该车可能产生的最高减速度。分析表明,汽车在同步附着系数?0的路面上制动(前、后车轮同时抱死)时,其制动减速度为dudt?qg?0g,即z=?0, z为制动强度。而在其他附着系数?的路面上制动时,达到前轮或后轮即将抱死时的制动强度 z到充分利用。附着条件的利用情况用附着系数利用率(附着力利用率)?表示:??FxbG?z?(3-17)式中:Fxb汽车总的地面制动力;G汽
55、车所受重力;z制动强度。当?=?0 时,z=?0, ?=1,利用率最高。取?=1,则 z=?=?0=0.7:在 0.2?z?0.8 的范围内,必须满足 z?0.1 0.85(?-0.2)。本设计中,z?0.7?0.2275 (满足要求)根据所定的同步附着系数?0 ,由式(3-10 ) 及式(3-13 )得?b?0hgLa?0hg(3-19)(3-18) 1?L(b?Ohg)qGL 进而求得Fxb1?Fxb?Gq?( 3-20 )(3-21 ) Fxb2?Fxb(1?)?Gq(1?)?(a?0hg)q当?=?0 时:Fxb1?F?1, Fxb2?F?2,故 Fxb?G? z二?; ?=1?F?当
56、?Fu?F?G?1 由式和?q/?和式(3-9), (3-14)得Fxb?Gb?b?(?0?)hgb?b?(?0?)hgbb?(?0?)hg( 3-22 ) q?(3-23) ?(3-24)。当?0时:可能得到的最大总制动力取决于后轮刚刚首先抱死的条件,即Fxb2由式(3-6 )、式(3-7 )、式(3-13)和式(3-15)得?F?2GL2?L2?(?0?)hg L2?L2?(?0?)hgL2( 3-25 )(3-26 ) ?0.92(3-27)本设计中汽车的?值恒定,其?0值小于可能遇到的最大附着系数,使其在常遇附着系数范围内?不致过低。在??0的良好路面上紧急制动时,总是后轮先抱死。3.
57、4制动器的最大制动力矩为保证汽车有良好的制动效能和稳定性,应合理地确定前,后轮制动器的制动力矩。最大制动力是在汽车附着质量被完全利用的条件下获得的,这时制动力与地面作用于车轮的法向力Fz1,Fz2成正比。由式(4-10)可知,双轴汽车前、后车轮附着力同时被充分利用或前、后轮同时抱死时的制动力之比为Fu1Fu2?Fz1Fz2?b?0hga?0hg( 3-28)式中:a,b 汽车质心离前、后轴距离;?0同步附着系数;hg汽车质心高度。制动器所能产生的制动力矩,受车轮的计算力矩所制约,即Tu1?Fu1re( 3-29)Tu2?Fu2re式中:Fu1前轴制动器的制动力,Fu1?Fz1?;;Fu2 后轴
58、制动器的制动力,Fu2?Fz2?Fz1作用于前轴车轮上的地面法向反力;Fz2re 作用于后轴车轮上的地面法向反力;一车轮有效半径。对于常遇的道路条件较差,车速较低因而选取了较小的同步附着系数?0值的汽车,为:r了保证在?0的良好的路面上(例如?=0.7 )能够制动到后轴和前轴先后抱死滑移(此),前、后轴的车轮制动器所能产生的最大制动力力矩为Tu1max?Fz1?re?GL(b?hg)?re 时制动强度 z?( 3-30)Tu2max?1?Tu1max( 3-31)对于选取较大?0值的汽车,从保证汽车制动时的稳定性出发,来确定各轴的最大制动力矩。当??0时,相应的极限制动强度zTu2max?GL
59、,故所需的后轴和前轴的最大制动力矩为 (a?zhg)?re(3-30 )Tu1max?1?Tu2max(3-31)式中:?一该车所能遇到的最大附着系数;z制动强度,由式du车轮有效半径。?zgdt确定;re本设计中,同步附着系数?0的值为0.85,所以应用式(3-24)、(3-25)进行计算。将以下数据汽车的重力 G=170000N轴距L=5100mm质心距前轴 a=3480mm质心距后轴b=1620mm地面附着系数?代入式(3-30 )、(3-31 )中,得汽车车轮的有效半径 re?0.49m一个车轮制动器的最大制动力矩为上列计算结果的半值。4制动器的结构及主要零部件设计4.1制动器的结构参
60、数制动鼓内径D输入力F0 一定时,制动鼓内径越大,则制动力矩越大,且散热能力也越强。但D的增大(图4-1 )受轮辋内径限制,制动鼓与轮辋之间应保持足够的间隙,通常要求该间隙不小于2030mm否则不仅制动鼓散热条件太差,而且轮辋受热后可能粘住内胎或烤坏气门嘴。制动鼓 应有足够的壁厚,用来保证有较大的刚度和热容量,以减少制动时的温度。制动鼓的直径小, 刚度就大,并有利于保证制动鼓的加工精度。图4-1鼓式制动器主要几何参数FIG. 4-1 drum brake main ly geometric parameters制动鼓直径与轮辋直径之比D轿车D货车 D/Dr/Dr/Dr 的范围如下:=0.64-
61、0.74 =0.70-0.83制动鼓内径尺寸应参考专业标准QC/T309-199制动鼓工作直径及制动蹄片宽度尺寸系列轿车制动鼓内径一般比轮辋外径小125mm-150gm载货汽车和客车的制动鼓内径一般比轮辋外径小80mm-100m,设计时亦可按轮辋直径初步确定制动鼓内径(见表 5-1)表4-1制动鼓最大内径Table 4-1 brake drum maximum diameter轮辋直径/in制动鼓最大内径/mm 轿车 货车、客车 12 180 220 13 200 240 14 240 260 15 260 300 16 - 320 20 -420制动鼓内径尺寸应符合QC/T 309-1999
62、制动鼓工作直径及制动蹄片宽度尺寸系列的规定。由上述表格和轮胎标准初选制动鼓内径 420mm摩擦衬片宽度b包角?径R既定后。摩擦衬片宽b和包角 便决定了衬片的摩擦面积 A ,而A =Rb,制动蹄各蹄总 的摩擦面积越大则单位压力愈小从而磨损特性愈好。根据国外统计资料分析,单个车轮蹄式 制动器总的衬片摩擦面积随汽车总重而增加具体数如表 4-2 摩擦衬片面积表4-2制动器衬片摩擦面积Table 4-2 brake facing frictio n area汽车类型轿车汽车总质量ma/t 0.9-1.51.5-2.5 单个制动器总的衬片摩擦面积 ?A/mm2 100-200 200-300120-200150-250(多为 150-200)250-400300-650550-1000600-1500(多 600-1200)客车与货车 1.0-1.51.5-2.5 2.5-3.5 3.5-7.0 7.0-12.0 12.0-17.0由根据表2-2选取对于车总质量 m =12t-17t时,A =600-1500cm则 b= A /R =200.6mm,根据 ZBT24005- 89 选取 b=210mrr制动鼓半
- 温馨提示:
1: 本站所有资源如无特殊说明,都需要本地电脑安装OFFICE2007和PDF阅读器。图纸软件为CAD,CAXA,PROE,UG,SolidWorks等.压缩文件请下载最新的WinRAR软件解压。
2: 本站的文档不包含任何第三方提供的附件图纸等,如果需要附件,请联系上传者。文件的所有权益归上传用户所有。
3.本站RAR压缩包中若带图纸,网页内容里面会有图纸预览,若没有图纸预览就没有图纸。
4. 未经权益所有人同意不得将文件中的内容挪作商业或盈利用途。
5. 装配图网仅提供信息存储空间,仅对用户上传内容的表现方式做保护处理,对用户上传分享的文档内容本身不做任何修改或编辑,并不能对任何下载内容负责。
6. 下载文件中如有侵权或不适当内容,请与我们联系,我们立即纠正。
7. 本站不保证下载资源的准确性、安全性和完整性, 同时也不承担用户因使用这些下载资源对自己和他人造成任何形式的伤害或损失。