25万吨年双峰工艺(BORSTAR)聚乙烯装置操作工培训教材1
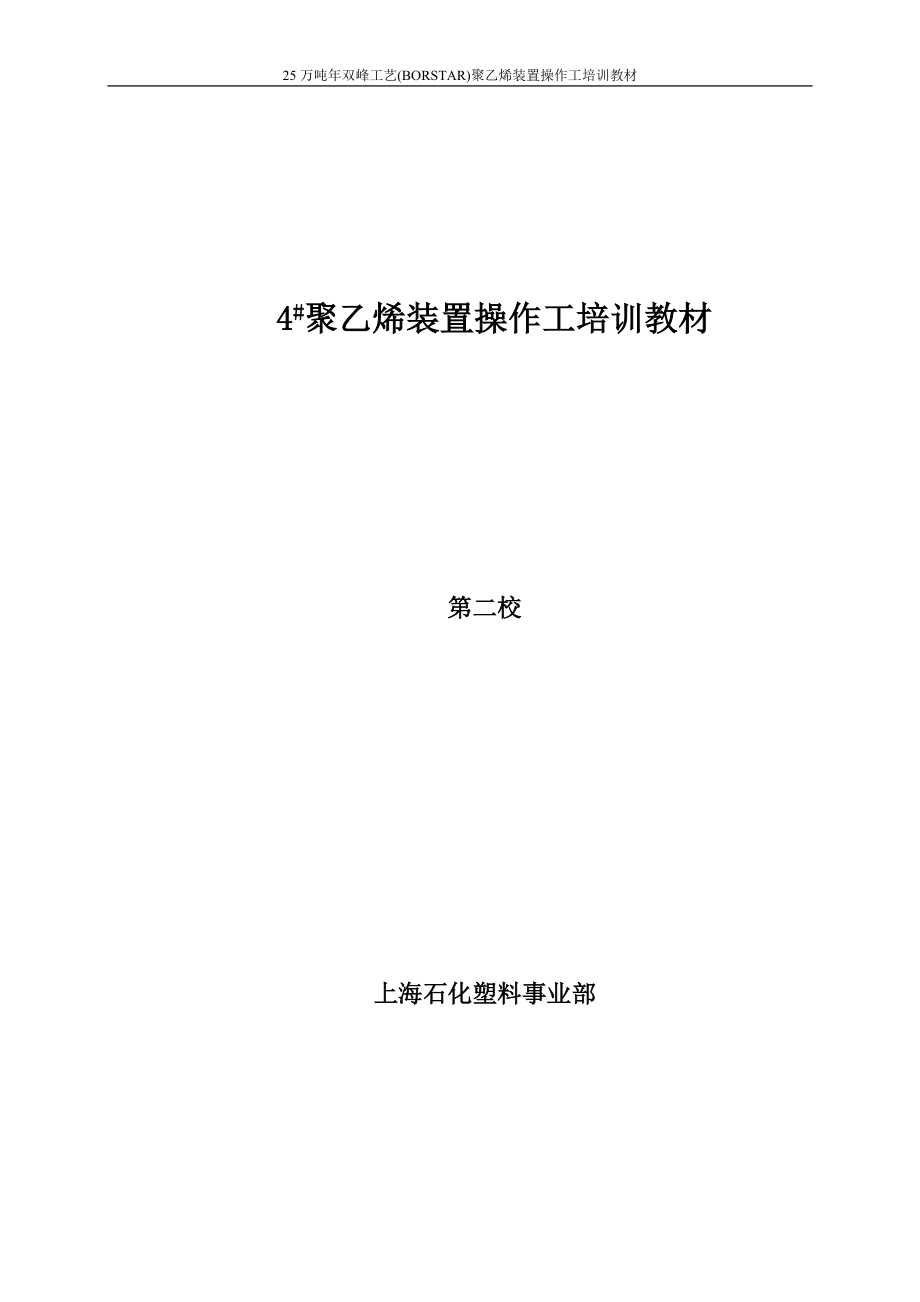


《25万吨年双峰工艺(BORSTAR)聚乙烯装置操作工培训教材1》由会员分享,可在线阅读,更多相关《25万吨年双峰工艺(BORSTAR)聚乙烯装置操作工培训教材1(107页珍藏版)》请在装配图网上搜索。
1、25万吨年双峰工艺(BORSTAR)聚乙烯装置操作工培训教材4#聚乙烯装置操作工培训教材第二校上海石化塑料事业部目 录第一章 25万吨/年双峰工艺(BORSTAR)聚乙烯装置第一节 概 述第二节 工艺原理第三节 工艺流程第四节 技术特点第二章 工艺操作第一节 质量控制第二节 基本操作第三节 产品的切换第四节 正常开、停车第五节 异常情况判断处理第三章 设备第一节 4PE装置设备概述第二节 专用机、泵介绍第四章 电器、仪表第一节 自动控制水平第二节 主要仪表系统第三节 仪表选型第四节 安全技术措施第五节 动力供应第五章 操作案例第一章 25万吨/年双峰工艺(BORSTAR)聚乙烯装置第一节 概
2、述上海石油化工股份有限公司塑料事业部4PE装置是上海石化四期工程70万吨乙烯改造项目的主体装置,系引进北欧化工公司“BORSTAR”双峰聚乙烯专利技术,可生产双峰LLDPE至HDPE的全密度聚乙烯产品,且具有生产自然色和黑色产品的能力。本装置设计生产能力为25万吨/年,运转时数为8000小时/年,操作弹性为70%110%。产品密度范围为(918970)kg/m3;熔体流动速率范围为2(MFR21)100(MFR2);分子量分布范围为530。共可生产六大类型、21个牌号的产品,其中:薄膜料6个、吹塑料3个、挤出涂层料1个、管材料5个、电(光)缆护套料2个、注塑料4个,其中管材料和电(光)缆护套料
3、为黑色产品。表1-1 设计品种年产量分类比例品种比例薄膜料30吹塑料25管材料20电(光)缆护套料15注塑料5挤出涂层料5北星双峰聚乙烯工艺技术基于串联的淤浆环管反应器和流化床气相反应器,由一个预聚合反应器、一个环管反应器及一个气相反应器组成的多个反应器串联,各反应器的反应条件完全独立,采用北欧化工公司自行开发的齐格勒-纳塔(Ziegler-Natter)型催化剂(BCM40G、BCM25E)生产所有产品。该工艺核心是在环管反应器中以超临界丙烷为稀释剂进行乙烯聚合反应,所生成的产物连续送入串联的气相反应器中进一步反应,生成低密度、高分子量的聚乙烯产品基料,整个工艺过程高度灵活,易于控制聚乙烯分
4、子量和共聚单体分布宽度。通过优化聚乙烯主、支链的结构及分子量的分布,使所生产的聚乙烯聚合物成为双峰型聚乙烯聚合物。通过调节共聚单体的含量可以控制密度,可生产HDPE、MDPE和LLDPE等聚合物,本工艺除了可控制共聚单体含量外,还可控制共聚单体的分布。本装置聚乙烯牌号覆盖面较广,产品在不同的应用中显示出优良的性能。选用廉价的丁烯-1作为共聚单体,能达到比任何单峰产品更优异的性能。例如:产品可用于要求较高的、更高压力级别的管子(如PE100管道)或增大管道管径、减薄管道壁厚,由于双峰聚乙烯的强度较高,因而相比可节省30%50%以上的材料。在生产线性低密度聚乙烯薄膜中,菱形袋和层压膜要比典型的LD
5、/HD或LD/LLD混合物节省31-47%的材料。在一般的和家用化学品(HIC)中空吹塑制品应用中,要比典型的单峰牌号节省20-30%的材料。另一个性能是由于机械性能的提高,使得塑料制品循环利用率的程度提高。根据工艺生产特点,该装置可分成7个区域。即:表1-2 装置区域分布0区公用工程2区原料精制系统3区预聚环管反应器/环管反应器4区气相反应器5区稀释剂回收系统6区助催化剂系统7区造粒、掺混和粒料贮存系统第二节 工艺原理1.2.1 高效催化剂双峰聚乙烯技术采用齐格勒-纳塔型催化剂。一般而言,齐格勒-纳塔催化剂是一种络合物,它是通过IV-V 族过渡金属化合物(卤化物、醇盐、烷烃或是芳基衍生物)和
6、I-III族金属卤化物或芳基醇盐反应得到。前者被称为催化剂,后者为助催化剂。虽然对金属的选择范围很大,但并不是所有的组合都具有活性,在实际生产中,使用钛化合物和烷基铝的组合体系。该催化剂对氧气和水特别敏感,因此它们必须严格地在惰性条件下进行制备。最普通齐格勒-纳塔催化剂是钛(Ti)、钒(V)、锆(Zr)、铪(Hf)、钴(Co)和镍(Ni)。这些金属中Ti几乎是在PE生产中唯一应用于工业中的。这些金属一般以卤化盐的形式使用。优先选用的化合物为氯化钛(TiCl4)、三氯化钛(TiCl3)、三氯化钒(VCl3)和三氯氧化钒(VOCl3)。齐格勒-纳塔催化剂有内部载体或无内部载体。内部载体通常是改善催
7、化剂的结构,一般使用硅或氯化镁。助催化剂为有机金属化合物,碳原子与金属原子键合在一起。优先选用的助催化剂为烷基铝。所有这些烷基金属都是可自燃的,必须储存于惰性状态下。当被碳氢化合物高度稀释,它们的活性会有所降低。1.2.2 聚合原理聚合反应被认为具有以下步骤:l 活性点的形成(AB):助催化剂与氯化钛反应。一个氯原子由助催化剂的烷基基团所取代,从而形成碳-金属键。这样就产生了一个空的配位点;l 单体在空位进行配位(C);l 单体插入到Ti-R键之间(D);l 链增长:下一个单体配位到空位,以一个正在增长的聚合链为尾端(EF);l 链转移反应。图1-1 聚合反应机理由于存在配位步骤,齐格勒-纳塔
8、和铬系催化剂也被称为配位聚合催化剂。高分子链的持续增长和链增长的控制都是很重要的。当高分子链终止或从活性点上转移的时候,链增长就结束了。用齐格勒-纳塔催化剂,氢气(链转移剂)起链终止作用。氢气与乙烯的比值越高,聚合物的分子量越低,即MFR上升。链转移反应要消耗氢气。氢气/乙烯比值的升高会在一定程度上引起催化剂活性的下降,链向氢气转移后产生具有饱和键的聚合物。链转移反应过程如下:齐格勒-纳塔催化剂的特点是在反应过程中链转移到氢气的步骤为控制步骤,反应器中形成的聚合物的分子量与反应器中氢气和乙烯的摩尔比成反比。聚合反应的温度升高会引起分子量下降,然而,与氢气的影响相比,温度只是一个很小的因素。为了
9、生产一定分子量的聚合物,不同的催化剂需要不同的氢气/乙烯比。需要用来控制聚合物分子量的氢气越少(低氢气/乙烯比),所用的催化剂对氢气越敏感。共聚单体(丁烯-1)用来控制聚合物的密度。聚合物中共聚单体的含量越高,密度就越低。为生产一定密度的聚合物需共聚单体/乙烯比越低,所用催化剂对共聚单体的反应灵敏度越高。一般情况下,共聚单体的存在会提高齐格勒-纳塔催化剂的活性。在共聚反应中,有多种链增长反应发生。第三节 工艺流程1.3.1 原料精制界区外来的乙烯经计量后先在脱氯、脱硫处理器(V-210)中脱除氯化物和硫化物,而后在乙烯脱CO处理器(V-203)脱除CO,再送至乙烯脱O2处理器(V-204)脱除
10、氧气,经乙烯冷却器(E-202)冷却后,最后进入乙烯干燥器(V-205A/B)脱除水份。干燥后的乙烯经过滤器(F-201A/B)过滤后,部分乙烯直接加入到气相反应器(R-401),其余乙烯经乙烯压缩机组(PK-201A/B)压缩后分别加入预聚反应器(R-301)和环管反应器(R-302)中。简要流程见下图:预聚反应器6.5 MPag保护过滤器界区乙烯脱CO塔脱氧塔干燥塔A/B气相反应器环管反应器6.4MPag操作温度304360-90乙烯冷却器脱硫脱氯塔精制催化剂ZnO乙烯加热器CuO/ZnO60-903 分子筛活性氧化铝Cu/ZnO吸入缓冲罐乙烯压缩机PK201A/B3.0 MPag30C图
11、1-2 乙烯精制流程图表1-3 乙烯精制床设计负荷和周期(设计精制流量 35.5 吨/小时)毒 物入口条件出口条件精制床精制催化剂再生周期(入口条件下)氯(HCl)硫(H2S)CO氧水醇类羰基化合物CO2111116660.110-6 mol0.110-6 mol0.110-6 wt0.110-6 wt0.110-6 mol0.110-6 mol0.110-6 mol 110-6 mol脱硫脱氯塔脱硫脱氯塔脱CO 塔脱氧塔干燥塔干燥塔干燥塔干燥塔ZnOZnOCuO/ZnOCuO (Cu)/ZnO3A 分子筛活性氧化铝Selexsorp CD活性氧化铝Selexsorp CD活性氧化铝Selex
12、sorp COS333 天166 天166 天7 天界区外来的丙烷经稀释剂干燥器(V-223A/B)进行脱水,脱水后进入硫处理器(V-221)脱除COS和其它硫化物,在脱砷处理器(V-228)脱除砷,然后送至加氢处理器(V-222)以脱除烯烃,最后进入稀释剂脱气塔(V-224)脱除氢气之类的轻组份,分别由泵送至催化剂加料系统、预聚反应器、环管反应器、气相反应器和回收丙烷循环中。简要流程见下图:氢气丙烷输送泵A/B原料丙烷进料罐操作条件60 常温 从循环丙烷缓冲罐来干燥塔脱硫塔精制催化剂4 分子筛 活性氧化铝脱砷塔 常温活性氧化铝60 加氢塔丙烷冷却器丙烷预热器界区丙烷CuO/ZnO钯催化剂返回
13、气丙烷贮存罐催化剂配制罐高压丙烷输送泵精制丙烷泵低压丙烷输送泵从循环丙烷罐来丙烷蒸汽去粉料输送系统再沸器脱气槽催化剂计量罐催化剂加料管线过滤器脱气塔冷却器脱丁烯塔顶冷却器气相反应器过滤器循环丙烷罐回收丙烷循环循环丙烷干燥塔循环丙烷罐循环丙烷罐界区丙烷球罐图1-3 丙烷精制流程图表1-4 丙烷精制床设计负荷和周期(设计精制流量 3.0 吨/小时)毒物入口条件出口条件精制床精制催化剂再生周期(入口条件下)醇类硫醇水羰基硫二氧化碳硫化氢砷烯烃1011500.251.510.055000.110-6 wt0.110-6 wt0.110-6 wt0.0510-6 wt110-6 wt0.110-6 wt
14、0.00510-6 wt1010-6 wt干燥塔干燥塔干燥塔丙烷脱硫塔丙烷脱硫塔丙烷脱硫塔丙烷脱胂塔丙烷脱氢塔活性氧化铝活性氧化铝4A 分子筛活性氧化铝活性氧化铝活性氧化铝CuO/ZnOPd 7 天180天2年3-5 年界区外来的丁烯-1(共聚单体)经共聚单体干燥器(V-242A/B)脱除水份后送至预聚反应器(R-301)和环管反应器(R-302)、气相反应器(R-401)。简要流程见下图:丁烯-1进料泵丁烯-1干燥器A/B丁烯-1储罐气相反应器环管反应器预聚反应器操作温度43丁烯-1丁烯-1蒸发器丁烯-1冷却器过滤器精制床催化剂13X分子筛丁烯-1 进料蒸发器图1-4 丁烯-1精制流程图表1
15、-5 丁烯-1精制床设计负荷和周期(设计精制流量 3.4 吨/小时)毒物入口条件出口条件精制床精制催化剂再生周期(入口条件下)水醇类二氧化碳10550.110-6 wt0.110-6 wt110-6 wt干燥塔干燥塔干燥塔13x 分子筛13x 分子筛13x 分子筛30 天界区外来的氢气经计量后进入脱CO/CO2处理器以脱除CO/CO2,然后在干燥器中脱除水份,氢气小部分用于丙烷加氢精制,大部分经氢气压缩机(C-281A/B)压缩至7.0MPag送至预聚反应器、环管反应器、气相反应器。简要流程见下图:界区氢气去乙烯脱氧塔去氮气脱氧塔氢气压缩机PK281A/B过滤器氢气干燥塔A/B去预聚反应器去环
16、管反应器去丙烷加氢精制塔去气相反应器氢气甲烷化脱除CO/CO2氢气冷却器过滤器氢气加热器氢气加热器图1-5 氢气精制流程图界区外来的氮气经氮气加热器(E-261)加热后,进入氮气脱氧处理器(V-261A/B)进行脱氧,使氮气中氧含量小于0.110-6mol。而后经氮气冷却器(E-262)冷却后,进入氮气干燥器(V-262A/B)脱除水份,使氮气中含水量小于1110-6mol。干燥后的氮气经氮气过滤器(F-261)过滤后成为精制氮气。一部分精制氮气经氮气压缩机(C-001A/B)压缩至7.2MPag,然后分成三种压力等级:7.2MPag、3.6MPag、2.3MPag,分别用于试压、吹扫和冲洗。
17、另一部分精制氮气用于第一、二再生系统的再生气体以及各工艺点的吹扫和冲洗。简要流程见下图:氮气脱氧塔A/B氮气干燥器A/B氮气过滤器氮气压缩机A/B0.3 MPag7.2 MPag去环管区域去气相反应器区域降压至3.6MPag /2.3 MPag精制用催化剂CuO/ZnO13X分子筛1.6 MPag0.3 MPag界区氮气0.8 MPag0.8MPag MPag MPag MPag bar(g)氮气加热器氮气冷却器操作温度60-80C43C图1-6 氮气精制流程图第一再生系统由再生气体压缩机(C-262)、第一再生系统加热器(H-201)、再生气体冷却器(E-263)、再生气体冷凝器(E-266
18、A/B)、再生气体分离罐(V-263)组成。该再生气体主要用于乙烯干燥器(V-205A/B)、共聚单体干燥器(V-242A/B)、回收稀释剂干燥器(V-226)、稀释剂干燥器(V-223A/B)等精制床层充填物的再生。简要流程见下图:再生加热器1再生气体缓冲罐再生气体冷凝器A/B氮气乙烯干燥塔丁烯-1干燥塔原料丙烷干燥塔循环丙烷干燥塔火炬再生气体压缩机再生气冷却器乙烯再生系统2AA图1-7 第一再生系统流程图第二再生系统由第二再生系统气体加热器(H-203)、再生气体放空冷却器(E-263)组成。主要用于氮气干燥器(V-262A/B)、乙烯脱CO处理器(V-203)、乙烯脱O2处理器(V-20
19、4)、氮气脱O2处理器(V-261A/B)等精制床层充填物的再生。第一再生系统与第二再生系统相连,作为第二再生系统的备用系统。简要流程见下图:乙烯氢气空气丁烯-1干燥塔再生系统1乙烯脱氧塔氮气脱氧塔乙烯脱CO塔乙烯脱氧塔乙烯脱 CO塔乙烯脱氧塔氮气脱氧塔氮气干燥塔再生系统1氮气再生气加热器2火炬再生气放空冷却系统A氮气脱氧塔图1-8 第二再生系统流程图1.3.2 主、助催化剂和添加剂的配制和进料界区外罐装催化剂由气送经催化剂装填槽过滤器(F-301)加入到催化剂装填槽(V-301),经精制稀释剂浸润13小时后送到催化剂进料槽(V-302A/B),在催化剂进料槽中进一步浸泡34小时,并升压至7.
20、0MPag。然后用精制稀释剂经催化剂进料阀(XV-3004和/或XV-3005)定量地将催化剂加入预聚反应器(R-301)中。催化剂进料阀(XV-3004和XV-3005)是一种特殊的四通旋塞阀。阀芯是由两个不相通的、有斜势的孔组成。该阀的水平方向的孔始终通着,以使稀释剂注入到反应器,而竖直方向的孔用于装填催化剂。通过90/次的旋转,使装填的催化剂注入反应器的过程循环进行。催化剂进料阀阀芯容积共有三组:65 ml、130 ml、200ml,以满足不同牌号、不同产量的需求。当催化剂用完,并在接受新一批催化剂时,应将槽内的稀释剂闪蒸至废催化剂槽(V-303),并将所有的管道和设备中残留的催化剂清洗
21、至V-303,所有软管和连接件用精制氮气吹扫干净,V-301、V-302A/B的残余物可倒空至V-303中。当废催化剂槽(V-303)充满废催化剂和稀释剂时,启动废催化剂槽搅拌器(A-301),同时夹套通入蒸汽进行加热以蒸发稀释剂。经放空过滤器(F-302)过滤后排至火炬或经稀释剂闪蒸汽体袋式过滤器(BF-301A/B)加以回收利用。废催化剂则用精制氮气出空至废催化剂输送罐运出界外处理。简要流程和催化剂加料阀结构示意见下图: 图1-9 催化剂系统示意图助催化剂是一种极易自燃的三乙基铝(TEAL),生产上使用100的TEAL。由于助催化剂的危险特性,所有设备都放置在与其它工艺区隔离的混凝土建筑物
22、内,所有助催化剂储存容器和泵都用混凝土墙相隔离。为了观察助催化剂的溢出或泄漏,助催化剂区配有火焰监测器。在处理助催化剂时,操作人员必需使用特殊的防护衣。界区外来的助催化剂用储罐运至装置,然后用专用卸料管与系统相连,用精氮将贮槽内的助催化剂全部压送到助催化剂贮槽(T-602)中。当储罐倒空后,对所有使用过的软管和接头用油彻底清洗,并用氮气吹扫,以清除所有残余的助催化剂。用精氮将助催化剂从助催化剂贮槽(T-602)压送到助催化剂日用槽(T-603), T-602、T-603有液位指示,当液位高高时联锁关闭精氮压送阀和进料阀。T-602、T-603与助催化剂密封罐(T-606)相连,密封罐部分充油以
23、保持助催化剂系统正压(0.005MPag)。来自日用槽的助催化剂经助催化剂过滤器(F-602)过滤后由助催化剂泵(P-601/P-602/ P-603)送至预聚反应器(R-301)、环管反应器(R-302)。其中,P-601送至环管反应器,P-603送到预聚反应器,P-602作为备泵。在助催化剂设备和管道向大气敞开前,必需用矿物油进行清洗,以彻底除净助催化剂残留物,否则会引起火灾。冲洗油系统由冲洗油贮槽(T-605)、废油槽(T-604)、冲洗油过滤器(F-603)和冲洗油泵(P-604)组成。从冲洗油贮槽(T-605)来的新鲜矿物油经冲洗油过滤器(F-603)用冲洗油泵(P-604)抽到指定
24、的管道和设备。用过的油收集在废油槽(T-604)中。所耗的油量大约是所冲洗容积的10倍。在废油槽(T-604)中,当废油中助催化剂含量达到饱和时,就用冲洗油泵(P-604)将其抽到TEAL处理槽(T-609)中,由助催化剂失活剂泵(P-612)将TEAL失活剂从桶中送入T-609,使T-609中的TEAL失活,失活的废油排空到废油桶中。废油中的助催化剂含量不能超过10%(wt)。助催化剂含量由定期取样检测。为防止因静电所引起的反应器壁积垢和减少成品粉末静电,须在预聚和/或环管反应器中加入抗静电剂。抗静电剂由泵(P-605)将其注入到反应器抗静电剂贮槽(T-607)。抗静电剂靠重力落入1个5升的
25、计量料斗,计量后的抗静电剂加到环管反应器抗静电剂槽(V-601)。将矿物油用P-605送至V-601中,以稀释抗静电剂。通过抗静电剂搅拌器(A-601)搅拌使其均匀,随后送到抗静电剂缓冲槽(T-608),经抗静电剂泵(P-606A/B)计量后送入预聚反应器和环管反应器。P-606A用于预聚反应器,P-606B用于环管反应器。抗静电剂可加到预聚反应器/环管反应器中之一或两者均可。加到预聚/环管反应器的流量可用流量比率调节器调节抗静电剂泵(P-606A/B)的速度加以控制。根据抗静电剂与稀释剂加入反应器的比率,可间接设定流量调节器,该比率范围一般在1010-6wt1510-6wt。比率的设定值和抗
26、静电剂的配制浓度由操作员设定。1.3.3 环管聚合反应来自精制区域的乙烯、共聚单体、氢气与来自稀释剂回收区域循环稀释剂冷却器(E-518)的循环稀释剂一起,通过流量比例控制加入到预聚反应器(R-301),同时助催化剂、催化剂、抗静电剂等定量加入到R-301中。预聚反应器(R-301)为一带夹套水冷却的、二条12英寸腿的环管反应器,预聚合反应是在丙烷中聚合物和原料进行反应。反应压力6.5MPag、反应温度70,与环管反应器的压差为(0.10.15)MPa。根据产率、停留时间和反应器与冷却水之间的温差进行反应控制。聚合产率由乙烯与催化剂的比例控制,聚合物密度由乙烯与丁烯-1的比例控制,聚合物分子量
27、由氢气控制,固体浓度由稀释剂加入量控制,反应温度由夹套冷却水控制,反应压力由环管反应器的压力所决定。预聚反应器循环泵(P-301)以9m/s的线速度循环预聚反应器内的物料,以达到良好的反应物混合和提高传热效率。该泵是置于环管上的轴流泵,用内置滚柱轴承和具有机械安全性密封的双端增压密封,轴端用稀释剂冲洗以防止密封系统被聚合物堵塞。预聚反应器(R-301)有一个专用的循环冷却水系统,该系统由预聚反应器冷却水泵(P-303)、预聚反应器冷却水冷却器(E-307)和预聚反应器加热器(E-301)组成。冷却水为蒸汽冷凝水或脱离子水。冷却水在R-301夹套中以3m/s的流速与反应物逆向流动强化传热,冷却水
28、温度通常由冷却器和旁路调节。反应器与夹套水之间的温差限制了反应器能力,当生产线性低密度聚乙烯(LLDPE)时,该温度差应小于25。温差太大,将导致反应器内低分子量聚合物粘结在管壁上。预聚反应器有一套专用的自动(手动)一氧化碳(CO)中止(微中止)系统,用于防止爆聚、中止反应、减缓反应。该系统由四个一氧化碳(CO)钢瓶和一组切断阀组成。预聚反应器(R-301)中的物料可以排放到排料槽(V-305),如果环管反应器(R-302)和气相反应器(R-401)同时排料,则预聚反应器不能直接向V-305排放,此时,预聚反应器须经环管反应器排放。简要流程见下图:图1-10 预聚系统流程图来自精制区域的乙烯、
29、共聚单体、氢气与来自稀释剂回收区域循环稀释剂冷却器(E-518)的循环稀释剂、C-502的轻组份循环气、P-507A/B的循环共聚单体一起,通过流量比例控制加到环管反应器(R-302),同时已预聚的催化剂、助催化剂、抗静电剂等也加入到R-302中。环管反应器(R-302)亦为一带夹套水冷却的、六条24英寸腿的环管反应器,聚合反应是在超临界丙烷状态下,聚合物和原料发生反应,生成双峰聚乙烯的低分子量部分。反应条件如下:表1-6 环管反应器反应条件聚乙烯产量12.514t/h乙烯浓度6.5mol%共聚单体与乙烯摩尔比0630mol/kmol氢气与乙烯摩尔比120470mol/kmol固体浓度2540
30、wt%温度8595压力6.4MPag环管反应器的控制方式与预聚反应器类似,即根据产率、停留时间和反应器与冷却水之间的温差进行反应控制。聚合率由乙烯与催化剂的比例控制,聚合物密度由乙烯与丁烯-1的比例控制,聚合物分子量由氢气控制,固体浓度由稀释剂加入量控制,反应温度由夹套冷却水控制,反应压力由六根沉降腿的出料阀循环开闭控制。环管反应器循环泵(P-302)以7m/s的线速度使物料在环管反应器内循环,以达到良好的反应物混合和提高传热效率。该泵是置于环管上的轴流泵,用内置滚柱轴承和具有机械安全性密封的双端增压密封,轴端用稀释剂冲洗以防止密封系统被聚合物堵塞。环管反应器内的物料排至沉降腿(SP-302A
31、F),聚合物在沉降腿中沉降后,由程序控制将聚合物送入闪蒸槽(V-304)中。在正常生产情况下,用34条沉降腿出料。每一条沉降腿的底部装有特殊的产品出料阀,在顶部装有一个手动阀和一个自动切断阀。当沉降腿运行时,顶部阀常开,物料在沉降腿中沉降,使固体浓度增至50wt% (典型的沉降时间为3050秒),底部阀由环管反应器(R-302)压力控制系统按180的关-开-关循环程序进行操作。若聚合物淤浆在沉降腿中沉降时间太短,则淤浆不能足够地浓缩;但停留时间太长,则有结块的危险。由于聚合物淤浆在沉降腿中还在反应,故沉降腿装有冷却/加热夹套和稀释剂冲洗点。当某一条沉降腿堵塞时,必须将沉降腿与环管反应器(R-3
32、02)隔断,即关闭切断阀和产品出料阀,这些阀的开闭仅能从现场控制盘上进行操作,关闭相应的稀释剂冲洗阀。待反应器停车时进行清堵。环管反应器(R-302)配有专用的循环冷却水系统,该系统由环管反应器冷却水冷却器(E-302)、环管反应器冷却水泵(P-304)、环管反应器开车加热器(E-303)、冷却水缓蚀剂补充罐(T-305)和冷却水缓冲槽(V-307)组成。冷却水为蒸汽冷凝水或脱离子水。冷却水在R-302夹套中以2m/s的流速与反应物逆向流动强化传热。冷却水温度通常由冷却器、加热器和旁路共同调节,在进入环管反应器夹套前分成三路:第一、二条腿;第三、四条腿和第五、六条腿,每一对腿之间的顶部弯头也有
33、夹套。环管反应器有一套专用的自动(手动)一氧化碳(CO)中止(微中止)系统,用于防止爆聚、中止反应、减缓反应。该系统由四个一氧化碳(CO)钢瓶和一组切断阀组成。一氧化碳注入时在6个点与稀释剂冲洗一起进入环管反应器,以确保一氧化碳快速而又均匀地分散于反应器内。在紧急情况下,环管反应器(R-302)通过三只排料阀和三根1.5英寸管线迅速倒空至排料槽(V-305)。开车料或出空环管反应器和预聚反应器时,可用专用的倒空阀排放到排料槽。排料槽容积大小能容纳预聚反应器和环管反应器的整个容量,另外,其容量也能承受一小时开车料。来自V-305的聚合物再排放到排料收集槽(V-306),用氮气和蒸汽注入V-306
34、,使粉末中的催化剂失活,随后将V-306中的料出空至大袋中。聚合的第一部分在环管反应器中进行。所有原料与来自预聚反应器部分聚合的催化剂一起送入环管反应器。简要流程见下图:图1-11 环管系统流程图沉降腿中的物料经夹套产品出料管线排至闪蒸槽(V-304),物料在该槽中减压并闪蒸,聚合物粉料与烃类气分离,分离出的烃类气经闪蒸气体袋式过滤器(BF-301A/B)和保护过滤器(F-305)过滤粉尘后送到稀释剂回收区域的稀释剂气体分离罐(V-501)。分离的粉尘则经袋式过滤器回转阀(RF-302A/B)回收至V-304中。来自闪蒸槽(V-304)的聚合物粉料和闪蒸气体袋式过滤器(BF-301A/B)的聚
35、合物粉料经产品筛(S-301)过滤大块料后进入粉末料斗(V-308),然后靠重力进入回转进料器(RF-301),再进入粉料输送系统(PK-301),并由回转进料器(RF-301)的转速控制聚合物进入输送系统的量。输送系统(PK-301)是循环气体稀相输送系统,输送气体可以是丙烷或氮气。用丙烷输送聚合物时,经聚合物粉末转向阀(DV-301)输送到气相反应器进料输送槽(V-401);用氮气时,经聚合物粉末转向阀(DV-301)直接输送到产品出料过滤器(BF-402)。输送系统(PK-301)的能力是18000kg/h。输送气体在V-401或BF-402中与粉末分离后经气体过滤器(F-306A/B)
36、和气体入口冷却器(E-305)返回到输送风机(C-301A/B),再由C-301A/B增压并经气体出口冷却器(E-306)冷却后用作输送气体去RF-301。简要流程见下图:图1-12 环管粉料输送系统流程图1.3.4 气相反应器气相反应器是双反应器工艺中的第二反应器,它是一个带搅拌器的流化床反应器。在气相反应器中,无需添加新催化剂,从环管反应器区域来的聚合物就可在气相反应器中继续进行聚合反应。在该反应器中生成聚合物的高分子量部分,从而扩大了最终聚合物产品分子量的分布。反应器之间的产率比可按照目标产品的特性加以调节。反应条件如下: 操作压力:1.9MPag操作温度:(7585)乙烯分压:(0.2
37、0.6)MPag气体流速:0.6m/s停留时间:2.5小时由气力输送系统将环管反应器区域产生的聚合物连续地送到气相反应器区域的进料输送槽(V-401),在该槽中,聚合物粉末与气体分离,气体则通过进料输送过滤器(BF-401)回到输送系统。夹带至过滤器(BF-401)的聚合物则回到进料输送槽(V-401)。从进料输送槽(V-401)来的聚合物间歇地进入聚合物进料槽(V-402),而后按进料程序进入气相反应器(R-401)。气相反应器是流化床反应器,进入反应器的聚乙烯粉末还极具活性,在足够高的流化气速作用下,与循环气体中的反应物继续进行聚合反应,并产生双峰聚乙烯的高分子量部分。来自精制区域的乙烯、
38、共聚单体、氢气、稀释剂通过流量比例控制加到气相反应器循环气体中,其中,大部分乙烯与氢气汇合后从循环气体冷却器下游加入,小部分乙烯经冲洗系统加至气相反应器;共聚单体与稀释剂汇合后从循环气体冷却器上游加入。而循环气体则分成三路从底部进入气相反应器,在与进入反应器的聚合物粉料反应后从顶部离开,反应后的聚合物则由出料口间歇 (或连续)排出,气相反应器共有三组出料系统:一组连续出料;二组间歇(批量)出料。正常运行时用间歇出料系统,当发生反应器出现块料堵塞间歇出料系统时,则投用连续出料系统维持反应器液位。由反应器料位调节器和调节阀控制间歇出料的频率或连续出料的量,并经输送管线送到产品出料过滤器(BF-40
39、2)。在BF-402中,气体与聚合物粉末分离。分离出的气体以切向进入气体回收缓冲槽(V-405),经压缩机增压后回送到气相反应器循环气体中。反应器温度由循环气体入口温度来控制。循环气体入口温度由循环气体冷却器(E-401)冷却水入口温度控制。而冷却水温度则是在控制一定循环冷却水流量下,将热冷却水与冷冷却水汇合控制循环冷却水进入循环气体冷却器(E-401)的温度。循环气体出口温度和冷却水入口温度之间的温差必须监控。当达到最小温差10时,则在系统中需加入更多的丙烷。冷却器出口气体温度必须高于其露点温度3,以避免产生凝液。反应器压力是由氮气和丙烷的加入量来控制总的操作压力。这样就可足以把反应器的热量
40、带走。乙烯分压是通过调节乙烯进料量控制。在紧急情况下,反应器泄压至火炬气系统。在反应器底部,气体入口管线被均匀分成三路管线从反应器底部进入,使床层流化并将反应热带走。进入反应器的聚乙烯粉末还极有活性,必须用足够高的流化速度使固体粒子在反应器内连续活动,以防止因反应太快形成局部热点。故循环气体从反应器底部进入,通过底部气体分布板(SP-402)使循环气体均匀地通过反应器(在分布板上无死角、通过板时有足够的压降),循环气体经反应器顶部扩大段(较大直径)离开反应器。在扩大段中,流化气体线速度降低,使聚合物在扩大段中沉降,随气体夹带的聚合物降至最少。来自V-402的泄压气体与BF-402分离气体以切向
41、进入气体回收缓冲槽(V-405)中以分离夹带的粉尘,再经气体回收过滤器(BF-403)和气体回收保护过滤器(F-401)过滤后在气体回收压缩机入口冷却器(E-403)进行冷却,随后进入气体回收压缩机缓冲槽(V-407),若有冷凝液时,则在气体回收压缩机缓冲槽(V-407)中分离,气体则经气体回收压缩机(C-402)压缩后送至反应器顶部循环气体出口管线中。收集在气体回收缓冲槽(V-405)的聚合物间歇地进入聚合物排料罐(V-416)。在聚合物排料罐(V-416)中,用氮气吹扫聚合物并排到大袋中。排料作业在现场间歇操作。气体回收压缩机(C-402)是三级活塞式压缩机。从段间分离罐V-409中抽出二
42、股气体,用于冲洗和反应器压力控制,当C-402入口压力低时,则补充循环气体和精制氮气。简要流程见下图:图1-13 气相反应器系统流程图气相反应器共有两个独立的一氧化碳中止系统,一氧化碳通过冲洗系统注入气相反应器,以保证一氧化碳均匀分散在整个反应器内。聚合物在料位控制下连续从反应器中排出,并经过滤器送至产品净化槽。在净化槽中,用热氮和蒸汽进行净化,以减少聚合物中的烃含量,并使残余催化剂失活。净化后的聚合物经气力输送系统送至粉料仓。1.3.5 稀释剂回收稀释剂回收区域主要用于脱除催化剂毒物(一氧化碳)、惰性物、齐聚物、重组份等杂质,以防这些物料在系统中积累,另一目的是回收稀释剂、单体、共聚单体等,
43、并将这些回收物循环送回到环管反应器中。来自环管反应器区域的闪蒸气体进入稀释剂气体分离罐(V-501),经入口过滤器(F-501)过滤后由稀释剂气体压缩机(C-501)压缩至2.0MPag。C-501(PK-501机组)是二级四缸迷宫密封型活塞式压缩机,根据入口压力和流量,自动控制100%、75%、50%的负载。压缩后的气体进入重组份塔(V-503) 底部。重组份塔由低压蒸汽加热的再沸器(E-502)、循环冷却水冷却的冷凝器(E-503)组成。通过再沸器加热,使塔内形成一股向上气流;通过冷凝器的冷凝,形成一股向下的液流。气液两相接触进行传热传质,使重组份在塔底部聚集,而轻组份则汇集于塔顶。塔底馏
44、份进入重组份塔底泵(P-508A/B),除大部分经再沸器循环回到塔底外,其余小部分则间歇地排至重组份收集槽(V-504),在V-504中,进行部分闪蒸,闪蒸气返回至V-501中。V-504中浓缩的物料在液位控制下进入重组份贮槽(T-501)。T-501存积到一定液位后,用氮气进行鼓泡吹扫,除去残存轻组份并排放至火炬。将失活剂加入T-501中,使重组份中的三乙基铝失活,随后送入槽车运至界外处理。V-503塔顶轻组份气体经冷凝后,未凝气送至轻组份压缩机组(PK-502)。凝液则流入重组份塔回流罐(V-505)中,经重组份回流泵(P-505A/B)分成二路:一路到重组份塔作为回流,而另一路则去轻组份
45、塔(V-508)进行分离。轻组份塔(V-508)由低压蒸汽加热的再沸器(E-505)、冷凝器(E-514)组成,其分离原理同V-503。塔顶轻组份气体经冷凝器(E-514)冷却后,一部分回流至塔内,一部分未凝气体则送至轻组份压缩机组(PK-502)。塔底组份在液位控制下输送至共聚单体塔(V-509)进行分离。当生产HDPE时,塔底组份可直接去共聚单体塔冷凝器(E-509)。来自V-508底部馏份进入共聚单体塔(V-509)的第十块板。共聚单体塔(V-509)由低压蒸汽加热的再沸器(E-508)、冷凝器(E-509)组成,其分离原理同V-503。塔底馏出物为共聚单体(丁烯-1),并经共聚单体塔底
46、冷却器(E-512)冷却后进入循环共聚单体槽(V-513)。随后在流量控制下经循环共聚单体泵(P-507A/B)送入环管反应器(R-302)或共聚单体干燥器(V-241)或气相反应器。而塔顶气体(主要是循环稀释剂)则在冷凝器(E-509)中冷凝,冷凝液在液位控制下进入循环稀释剂缓冲罐(V-512),而后用共聚单体塔回流泵(P-505A/B)将循环稀释剂打回到V-509顶部或送至原料丙烷进料槽(T-221)。在流量控制下用进料泵(P-506A/B)将循环稀释剂经冷却器(E-518)冷却后送入预聚反应器(R-301)和环管反应器(R-302)中。通过排放调节阀(HIC-5011)间歇地将不凝气排入
47、火炬,以防不凝物在共聚单体塔塔顶冷凝器内积累。来自重组份塔顶冷凝器(E-503)和轻组份塔顶冷凝器(E-514)的不凝气一起进入轻组份分离罐(V-515)进行气液分离。液体间歇地手动排放至T-501。而气体进入轻组份压缩机(C-502)。轻组份压缩机(C-502)是二级活塞式压缩机,入口压力为1.92MPag,一级压缩后的压力为3.5MPag,二级压缩后的出口压力为7.0MPag。气体经一级压缩后在中间冷却器(E-524)冷却,而后进入第二级轻组份分离罐(V-518)进行气液分离,分离液由液位控制排放至V-505。而气体则分成二路:一路去C-502的第二级,进一步压缩至7.0MPag后返回到环
48、管反应器。另一路气体则送到轻气体冷凝器(E-519)进行冷凝,冷凝液送至轻组份分离器(V-514)。轻组份分离器(V-514)由低压蒸汽加热的再沸器(E-521)、冷凝器(E-520)和冷凝器(E-522)组成,其分离原理同V-503。来自E-519的凝液从中部进入V-514,塔底富含丙烷的馏份返回到轻组份塔(V-508)中。而塔顶气体则经E-520冷凝冷却后,凝液回流到塔内,不凝气体则排放至返回气或火炬系统。E-520的冷却剂则来自重组份塔(V-503)塔顶来的液体在E-522冷却后进入E-520减压汽化,冷却E-520中的塔顶气体,减压后的冷却剂气体则在E-522冷却V-503的液体后返回
49、至V-501中。简要流程见下二图:回收稀释剂去循环稀释剂储槽重组份塔回流泵脱重组份塔塔顶冷却器稀释剂气体压缩机吸入缓冲罐轻组份塔塔顶冷却器回流储罐重组份收集罐返回环管反应器从环管反应器来闪蒸气重组份塔再沸器返回气去火炬或去上游乙烯装置回收稀释剂去共聚单体塔 (在生产LLD产品时)吸入过滤网轻组份气体压缩机轻气体分离塔返回气去上游乙烯装置轻气体冷凝器重组份贮存罐轻组份塔再沸器轻组份塔图1-14 稀释剂回收流程图循环共聚单体去环管反应器,气相反应器和共聚单体干燥塔从轻组份塔来循环稀释剂(LLD产品生产时)火炬循环共聚单体泵共聚单体塔塔顶冷凝器回流泵循环共聚单体储罐循环稀释剂储槽共聚单体塔再沸器共聚
50、单体塔预聚反应器循环稀释剂进料泵冷却器从循环稀释剂干燥器来从丙烷精制脱气塔来稀释剂蒸发器环管反应器原料丙烷进料罐循环稀释剂干燥塔气相反应器稀释剂储存罐共聚单体塔塔底出料冷却器从丙烷球罐来丙烷球罐HD产品生产时图1-15 稀释剂回收流程图1.3.6 造粒从气相反应器区域来的粉料送到粉料仓(T-702A/B/C),来自粉料仓的粉料经粉料进料流量计送入挤出机进料输送器(M-705A/B/C)。固体添加剂可通过真空输送系统从包装袋或桶中送入固体添加剂料仓(T-703A/B/C),固体添加剂经失重进料器送到挤出机进料输送器。若生产有色产品,则碳黑母料亦送到挤出机进料输送器。来自挤出机进料输送器的粉料、添
51、加剂、碳黑母料等一并送入挤出机,这些物料在挤出机中熔化、均化、造粒,以形成一定形状的颗粒。而后通过切粒水进行冷却并送到水力输送系统。简要流程见下三图:粉料仓顶部袋式过滤器 BF-703A/B/C粉料仓 T-702 A/B/CN2排大气粉料输送螺杆压缩机C701A/B保护过滤器F-717A/B吸入冷却器E-701输送气冷却器 E-702粉料净化槽V-406 粉料输送回转阀RF-401,RF-402块料收集器SP-401粉料进料计量器 M-704A/B/C粉料进料回转阀 RF-702A/B/C挤出进料输送器 M-705 A/C挤出进料输送器 M-705 B去挤出机 L-701PK-702 粉料氮气
52、输送系统粉料仓的粉料经计量加入挤出机进料斗碳黑母料计量加入料仓 T-723灰色料计量加入料仓T-725固体添加剂、碳黑母料和灰色料输送加入系统挤出机进料输送器 M-705B固体添加剂料仓 T-703 A/B/C固体添加剂抽吸加入料斗碳黑母料输送系统PK-705添加剂计量加入器M-706A/B/C黑色料切粒水系统灰色料输送系统 PK-711挤出机系统PK701(挤出机L701)水下切粒系统和切粒机L702X熔体齿轮泵P-703开车阀M-714熔体过滤网组件 换网器M-715X模板主马达和变速箱非互啮合相向旋转双螺杆挤出机进料斗T-710XSlot 阀启动辅助马达聚合物粉料和添加剂及母料由进料输送
53、器M705B混合均匀后输送加入聚合物颗粒去筛分器和干燥器图1-16 造粒系统流程图由于挤出机(L-701)至掺混料仓的距离较远,故采用水力输送方法。水力输送系统主要由粒子浆料罐、浆料泵、筛分器、干燥器、循环输送水泵、循环输送水罐组成。自然色和黑色粒子有各自的水力输送系统。造粒后的粒子送入浆料罐,通过加入水量控制浆料罐中浆料浓度。浆料经浆料泵送至提浓器中提浓,脱除部分水后回到浆料罐。提浓后的浆料送到干燥器进行脱水,使粒子干燥并筛去细屑。干燥后的粒子经气力输送系统送至掺混区域。来自掺混料仓的聚合物粒料经气力输送系统送到成品料仓。本装置设计能够生产自然色和黑色两种粒料,所以筛分、水力输送、掺混输送的
54、流程分为自然色料和黑色料两套独立的系统。上述流程简明示意图见下二图:黑色粒料生产流程示意图聚合物粉料从聚合系统来(V406)包装添加剂系统聚合物粉料仓挤出机碳黑母料进料仓灰色颗粒进料仓黑色颗粒切粒水系统黑色料掺混料仓筛分器干燥器干燥器颗粒水力输送系统挤出机进料输送器黑色料成品料仓包装自然色颗粒料生产流程示意图聚合物粉料从聚合系统来(V406)添加剂系统聚合物粉料仓挤出机自然色颗粒掺混料仓自然色颗粒切粒水系统干燥器颗粒水力输送系统挤出机进料输送器本色颗粒成品料仓图1-17 粒料生产流程示意图图1-18 聚合系统简明流程图图1-19 挤出造粒和掺混流程图第四节 技术特点1.4.1 工艺流程的特点催
55、化剂进人环管反应器后,完成第一步聚合反应,聚合物和未反应的单体在闪蒸罐分离,回收的单体返回环管反应器,环管反应生成的低分子量聚合物输送到气相流化床反应器,进行第二步聚合反应,在此反应器中,主要生成高分子量的聚合物。由于没有新催化剂进人到气相流化床反应器,所以两个反应器均通过同一催化剂进行催化聚合,使分子量差异巨大的不同类型聚合物达到分子级混合,这是机械混合不可能达到的。同时,灵活的流程设计,使得生产工艺流程的组合和分离较为方便,实现即能生产双峰型产品,又能生产单峰型产品的功能。环管反应器中采用超临界丙烷作为稀释剂进行低分子量部分聚乙烯的生产。一方面,是因为丙烷易得、价廉,另一方面,因为其临界温
56、度低于聚乙烯的熔点。所谓超临界丙烷,是指丙烷的温度和压力都处于临界状态(97,4.3MPag)。其它工艺常用的稀释剂异丁烷的临界温度超过聚乙烯的熔融温度,所以该工艺不能采用超临界异丁烷。一般地说,超临界流体既不是气体,也非液体,具有粘度低、可压缩性高(同气体相似)、密度高、热容高(又像液体)的性质。所以,当烃类混合物的温度和压力超过其临界值时,气体组份并不从流体中分离出来,在环管反应器中无气泡生成,不会导致环管泵气蚀。在闪蒸罐中,聚合物与丙烷很容易分离,进入到气相反应器的粉料流动性较好。同时,经过试验证明,在超临界的丙烷流体中,低分子量的聚乙烯的溶解度也较低,这有利于防止反应器结垢。采用环管和
57、气相流化床反应器组合,使得本工艺存在其它的明显优势如下:(1)第一反应器中停留时间较短,使开车和牌号切换简单容易(2)环管反应器生成的聚合物通过充分闪燕后进入气相反应器,从而易于控制气相反应器中的气相组成,实现在两个主反应器中对熔融指数和密度的分别单独控制,并可根据产品特性要求优化两个反应器的产率配比(3)气相反应器中产品密度较低,在LLDPE产品密度范围内。其共聚单体分布设计也极其灵活,可以实现最佳的共聚单体分布,产品的熔体流动速率范围极广。(4)用丙烷部分替代氮气作为反应器的循环气,可使气相反应器的产能大大增加。 本工艺对催化剂的要求较高,因为所用催化剂必须能够在不同反应器的各种极端操作条
58、件下,即无论是浆液反应条件,还是气相流化反应条件,均能确保生产所要求的聚合物结构,且其活性稳定高效。催化剂是PE生产工艺的重要组成部分,Borstar专利的BCG25E、BCM40E催化剂连同所选择的反应器组合是生产双峰聚乙烯的基础。综合催化剂性能优点有以下几点:1. 均匀性所谓均匀性,是催化剂的化学物质均匀分布在载体上。由于化学物质的均匀分布,使单体在催化剂表面上的聚合反应较均匀,因而可得到比较均匀的聚合物粉未。2. 良好的总产率在聚合工艺中,催化剂的生产能力可表述为每公斤催化剂可生产多少聚合物的量。由于催化剂的寿命较长,即催化剂自加入预聚反应器开始,直至气相反应器,催化剂始终具有活性(在反
59、应器中的停留时间共约44.5小时),即在整个生产工艺条件下都具有较高的活性,因而使催化剂的生产能力提高,并使最终产品中的催化剂残余物较少。3. 3. 活性与熔融指数和密度的平衡性由于该催化剂对氢气的敏感性高,因此能够生产低分子量到高分子量的系列产品;又由于该催化剂对共聚单体具有良好的灵敏性,因而在聚合中可控制聚合物的支链,使产品的密度变宽,即从LLD到HD范围。也就是说,用单一的催化剂,可生产分子量分布(用熔体流动速率比来表示,FRR21/5MFR21/MFR5)为530、密度范围为918970kg/m3的聚乙烯产品。4. 4. 理想的表面形态聚合物的粒子形状和大小在聚合反应中是非常重要的,它
60、们直接决定着反应中最大的聚合物浓度及产量。齐格勒-纳塔型催化剂是一种配位型聚合催化剂,因而在配位聚合工艺中,催化剂的形状决定了聚合物粒子形状。由于该催化剂具有优良的形状及粒径分布,使聚合物拥有很好的粉末形态。u5. 催化剂典型特征值 钛含量 2 wt% 镁含量 2 wt% 铝含量 2.5 wt% 堆密度 450 kg/m3 干燥后烃含量 48 wt% 粒径分布 10 10% 20 50% 40 90% 平均粒径 20 1.4.2 产品技术的特点在本工艺中,在环管反应器中生成高熔融指数、低分子量的聚合物,既改善了加工性,又窄化分子量分布,减少了易产生烟雾和味道的分子量很低的部分;在气相反应器中生成低熔融指数、高分子量、密度较低的聚合物,通过增加
- 温馨提示:
1: 本站所有资源如无特殊说明,都需要本地电脑安装OFFICE2007和PDF阅读器。图纸软件为CAD,CAXA,PROE,UG,SolidWorks等.压缩文件请下载最新的WinRAR软件解压。
2: 本站的文档不包含任何第三方提供的附件图纸等,如果需要附件,请联系上传者。文件的所有权益归上传用户所有。
3.本站RAR压缩包中若带图纸,网页内容里面会有图纸预览,若没有图纸预览就没有图纸。
4. 未经权益所有人同意不得将文件中的内容挪作商业或盈利用途。
5. 装配图网仅提供信息存储空间,仅对用户上传内容的表现方式做保护处理,对用户上传分享的文档内容本身不做任何修改或编辑,并不能对任何下载内容负责。
6. 下载文件中如有侵权或不适当内容,请与我们联系,我们立即纠正。
7. 本站不保证下载资源的准确性、安全性和完整性, 同时也不承担用户因使用这些下载资源对自己和他人造成任何形式的伤害或损失。