基于AT89S51单片机的余热锅炉蒸汽温度控制系统设计
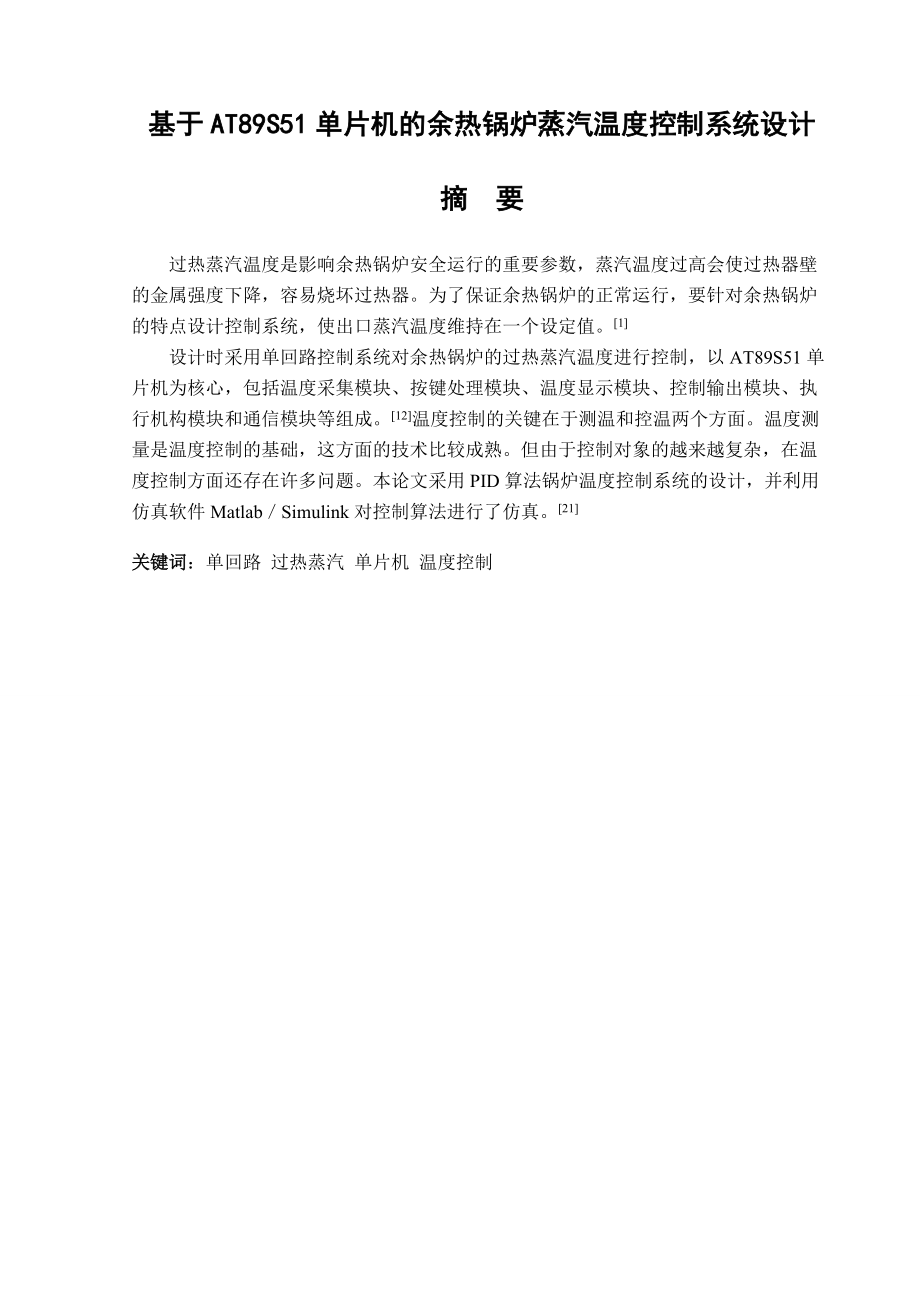


《基于AT89S51单片机的余热锅炉蒸汽温度控制系统设计》由会员分享,可在线阅读,更多相关《基于AT89S51单片机的余热锅炉蒸汽温度控制系统设计(51页珍藏版)》请在装配图网上搜索。
1、基于AT89S51单片机的余热锅炉蒸汽温度控制系统设计摘 要过热蒸汽温度是影响余热锅炉安全运行的重要参数,蒸汽温度过高会使过热器壁的金属强度下降,容易烧坏过热器。为了保证余热锅炉的正常运行,要针对余热锅炉的特点设计控制系统,使出口蒸汽温度维持在一个设定值。1设计时采用单回路控制系统对余热锅炉的过热蒸汽温度进行控制,以AT89S51单片机为核心,包括温度采集模块、按键处理模块、温度显示模块、控制输出模块、执行机构模块和通信模块等组成。12温度控制的关键在于测温和控温两个方面。温度测量是温度控制的基础,这方面的技术比较成熟。但由于控制对象的越来越复杂,在温度控制方面还存在许多问题。本论文采用PID
2、算法锅炉温度控制系统的设计,并利用仿真软件MatlabSimulink对控制算法进行了仿真。21关键词:单回路 过热蒸汽 单片机 温度控制IABSTRACTThe superheated steam temperature is an important parameter that affects the safe operation of the waste heat boiler, the steam temperature is too high will make the metal strength superheater wall down, easy to burn out.
3、In order to ensure the normal operation of waste heat boiler, to design characteristic of the control system for waste heat boiler, the outlet steam temperature maintained at a set value. Designed with a single loop control system for waste heat boiler superheated steam temperature is controlled to
4、AT89S51 microcontroller as the core, including temperature acquisition module, the key processing module, temperature display module, the control output module, actuator modules and communication modules and other components. Temperature control is the key to both temperature and temperature. Temper
5、ature measurements are the basis for temperature control, this technology is more mature. However, due to more complex control object, the temperature control many problems still exist. This paper uses the PID algorithm boiler temperature control system design, and the use of simulation software MAT
6、LAB / SIMULINK simulation of the control algorithm.Keywords: single loop superheated steam microcontroller temperature control II目 录摘 要IABSTRACTII第1章 绪论1 1.1 设计的背景及意义1 1.2 国内外研究现状2 1.3 设计的目的4第2章 余热锅炉蒸汽温度控制系统设计6 2.1 控制方案选择62.1.1 影响过热蒸汽温度的因素62.1.2 单回路控制方案92.1.3串级控制方案102.1.4 前馈控制方案12 2.2 控制方案的比较和方案确定14
7、2.2.1 控制方案的比较142.2.2 方案的确定15第3章 系统硬件设计17 3.1 系统结构框图17 3.2 单片机与8155的接口电路17 3.3 信号输入部分183.3.1 温度信号采集与处理183.3.2 A/D转换19 3.4 显示电路设计19 3.5 信号输出部分213.5.1 D/A转换213.5.2 4-20mA标准信号输出22 3.6 串口与上位机通信电路22 3.7 报警电路设计23 3.8 键盘电路设计24 3.9 稳压电源电路设计25 3.10 单片机最小系统263.10.1时钟电路263.10.2复位电路27第4章 系统软件设计28 4.1 软件设计思路28 4.
8、2 系统软件流程图284.2.1 主程序流程图284.2.2 采样子程序304.2.3 数字滤波304.2.4 中断服务314.2.5 显示环节软件设计334.2.6 上位机控制软件设计344.2.7 PID子程序35第5章 系统的仿真38 5.1 仿真工具38 5.2 MATLAB及其模糊逻辑工具箱和仿真环境385.2.1 MATLAB概况385.2.2模糊逻辑工具箱39 5.3 PID算法的设计及分析405.3.1控制算法的确定405.3.2数学模型的建立41 5.4 基于Matlab仿真44结 论47致 谢48参考文献49附录1 设计系统部分源代码.51附录2 系统硬件图.54CONTE
9、NTSABSTRACTIABSTRACTIIChapter 1 Introduction1 1.1 Design background and significance of a1 1.2 Research status2 1.3 Design Objective4Chapter 2 HRSG steam temperature control system design6 2.1 Control scheme selection6 2.1.1 Factors affecting the superheated steam temperature6 2.1.2 Single-loop cont
10、rol scheme9 2.1.3 Cascade Control Programme10 2.1.4 Feedforward control program12 2.2 Comparison of control schemes and programs identified14 2.2.1 Comparison of 11 control scheme14 2.2.2 The program identified15Chapter 3 Hardware Design17 3.1 System Block Diagram17 3.2 With 8155 microcontroller int
11、erface circuit17 3.3 Signal input section17 3.3.1 The temperature signal acquisition and processing18 3.3.2 A / D converter19 3.4 Shows the circuit design19 3.5 Signal output section21 3.5.1 D / A converter21 3.5.2 4-20mA standard signal output22 3.6 Serial Communication between PC Circuit22 3.7 Ala
12、rm Circuit Design23 3.8 Keyboard Circuit Design24 3.9 Regulated Power Supply Circuit Design25 3.10 Minimum System Microcontroller26 3.10.1 Clock Circuit26 3.10.2 Reset Circuit27Chapter 4 System Software Design28 4.1 Software design ideas28 4.2 System software flow chart28 4.2.1 The main program flow
13、 chart28 4.2.2 The sampling subroutine30 4.2.3 Software Design Display link30 4.2.4 Interrupt Service31 4.2.5 Digital Filter33 4.2.6 PC control software design34 4.2.7 PID subroutine35Chapter 5 System Simulation38 5.1 Simulation Tools38 5.2 MATLAB and fuzzy logic toolbox and simulation environment38
14、 5.2.1 MATLAB Overview38 5.2.2 Fuzzy Logic Toolbox39 5.3 PID algorithm design and analysis40 5.3.1 Determination of the control algorithm40 5.3.2 Mathematical Model 41 5.4 Based on Matlab simulation 44Conclusion47Acknowledgements48References49Appendix 1 design system part of the source code.51Append
15、ix 2 System hardware chart.54VI第1章 绪论1.1 设计的背景及意义余热锅炉是专门用于与转炉配套的热能利用转换设备,包括热交换、锅筒、除氧水箱等三部分。它利用转炉吹炼过程中产生的高温烟气对锅筒中的水循环加热,并在锅筒中进行汽水分离,把产生的蒸汽送往厂区热力网。其中,锅筒的给水来自除氧器,通过给水调节阀门来调整给水流量。11同时,锅筒内的水通过循环泵循环流经热交换器,吸取热交换器中烟气的热量,以获得能量。锅筒内的水温远高于水的沸点,由此产生蒸汽,经过蒸汽流量调节阀门送入厂区热力网,产生经济效益。9从转炉来的烟气通过热交换器后,温度达到旋风收尘和化工厂所能接受的数值,
16、参与后续生产过程。尽管锅炉系统种类繁多,各种类型锅炉的工艺流程和操作控制各有特点,但对过程检测、控制的要求是基本相同的。这既包括对锅炉产汽量和产汽压力的要求,也包括对锅炉自身安全、稳定运行的要求。锅炉生产过程检测控制应达到下述基本目的:锅炉汽包水位必须保持在一定范围内;锅炉产汽量必须适应用汽设备用汽量变化的要求;锅炉产汽压力必须满足用汽设备的要求;过热蒸汽温度必须根据用汽设备的要求保持在一定的范围内;燃烧系统必须维持安全、经济的运行。过热蒸汽温度是火力发电厂锅炉设备的重要参数,在热电厂生产过程中,整个汽水通道中温度最高的是过热蒸汽温度。过热器正常工作的温度,一般要接近于材料允许的最高温度。如果
17、过热蒸汽温度过高,则过热器易损坏,还会使汽轮机内部引起过度的热膨胀,严重影响生产运行的安全;如果过热蒸汽温度偏低,则设备的效率将会降低,同时使通过汽轮机最后几级的蒸汽湿度增加,引起叶片的磨损。因此,在锅炉运行中,保证过热蒸汽的温度在正常范围内是非常重要的。另外,在现代化的工业生产中,电流、电压、温度、压力、流量、流速和开关量都是常用的主要被控参数,人们都需要对各类加热炉、热处理炉、反应炉和锅炉中的温度进行检测和控制。可以说几乎80%的工业部门都不得不考虑着温度的因素。因此,这就需要在现有锅炉控制技术的基础上进行一定的改进,设计一种性价比合理的、使用和维护方便的锅炉过热蒸汽温度控制系统。此外,如
18、果过热蒸汽温度变化过大,还会引起汽轮机转子和汽缸的涨差变化,甚至会产生剧烈振动,危及到机组的运行安全。因此,必须相当严格地将过热汽温控制在给定值附近。一般中、高压锅炉过热蒸汽温度的暂时偏差不允许超过10,长期偏差不允许超过5,这个要求对过热蒸汽温度控制系统来说是非常高的。所以对锅炉蒸汽温度的控制非常必要。1.2 国内外研究现状目前,国外利用余热发电的新趋势,是单机功率小,载热体温度低(即利用中低温余热发电)。或内也有一些利用余热发电,如炭黑工业中的低热值尾气余热和硫酸工业中的硫酸余热发电等,所发的电能主要工厂自用。目前,已把如何利用中低温的低品位余热发电,作为开发节能新技术的重要课题。余热锅炉
19、是一种理想的节能设备,它不但能节约能源,而且对提高主流程的质量,减轻公害和满足某些工艺流程要求,都起着十分重要的作用。现有的余热锅炉按进锅炉的介质特性,有以下几种主要型式:1)废烟气不需要进一步处理的余热锅炉;2)废烟气需要进一步处理的余热锅炉;3)废烟气要进一步处理,且其冷却在给定时间内完成的余热锅炉;4)固体显热的余热锅炉。近十几年,余热锅炉技术发展十分迅猛。七十年代初我国着手并开始实施发展余热锅炉的规划。从1974年到1980年,先后投资扩建余热锅炉研究和制造基地,现已形成具有一定的余热锅炉研制能力以及科研基地。至今已开发并制造了涉及15个类别、74个品种、101个规格的余热锅炉2000
20、余台。我国余热锅炉产品技术水品,除少数接近或到达国际上同类产品的先进水平外,大多数相当于国外五、六十年代的水平,其主要差距反应在以下几个方面:1)热利用率低;2)自控水平落后;3)积灰率高和清除效果差(特别是有色冶炼工艺中的余热锅炉)。实践证明,余热锅炉在各企业的节能中发挥了相当有效的作用,获得了较好的经济效益,其投资一般可在34年内回收。余热锅炉的作用现已超越了单纯的余热利用,事实上它的作用与工艺流程现代化和防止环境污染方面已无法截然分开,所以各种类型的余热锅炉相继问世。我国近几年产量每年约在400500蒸吨之间,尚不能满足市场的需要。据预测,1990年,全国余热锅炉需要量在1000蒸吨/年
21、以上。随着技术的进步,今后工业部门将普遍采用高能效的先进工艺流程,这样能源的有效利用率提高,高温余热资源总量相应减少,而中、低温余热资源相应增长。因此,余热利用技术将由高温余热回收技术转向中,低温和固体显热的余热回收利用技术,但在近期仍以发展高温余热回收的锅炉产品为主。如干法熄焦余热锅炉,化铁炉余热锅炉,转炉余热锅炉等。当然也必须为今后发展中、低温和固体显热回收的余热利用技术以及城市垃圾焚烧余热锅炉开展一些科研工作,以加快设计,制造各种类型、容量和参数的余热锅炉,来满足是长的需求。余热锅炉是机械产品及余热发电设备的一个重要组成部分,因此发展余热锅炉,振兴余热锅炉行业,也是振兴机械工业和电力工业
22、,促进产品质量、上品种和上水平不可缺少的环节。为实现上述目的,建议采取以下措施:1)改进老式产品,开发新产品,赶上世界先进水平;2)在产品发展中,科研设计要与推广应用相结合;3)加强与国外的技术交流,借鉴国外的先进经验;4)制定必要的技术和经济政策,发挥科研人员的工作积极性。1.3 设计的目的余热锅炉是燃气蒸汽联合循环发电的主设备之一。和常规锅炉不同,余热锅炉中不发生燃烧过程,也没有燃烧相关的设备,从本质上讲,它只是一个燃气水蒸汽的换热器。其与燃气轮机配合,燃气轮机的排气(温度约在500600)进入余热锅炉,加热受热面中的水,水吸热变为高温高压的蒸汽再进入汽轮机,完成联合循环。锅炉是火力发电厂
23、单元机组中的主要设备之一,它是一种系统复杂、体积庞大和昂贵上的能量转换设备,其内部发生的物理化学过程非常复杂,而且各种过程机密耦合,他们相互制约、相互影响。对于余热锅炉动态的研究,往往借助于为它建立的某种简化模型。然而,对于锅炉内部的某些工作机理,人们至今尚未充分掌握。因此,如何建立比较符合实际而又相当简单的锅炉数学模型,尚待研究和值得研究。本文的设计目的,就是针对过热蒸汽温度的特点,在深入分析过热蒸汽温度调节的过程,过热蒸汽温度调节对象的静态特性、动态特性以及过热蒸汽温度控制的设计难的基础上,确定在过热蒸汽温度控制系统中应用单回路控制的可行性,并考虑根据蒸汽温度偏差和偏差的变化情况调整控制器
24、的参数,以实现最优控制。并且由控制系统输出信号来控制执行器,通过调节执行器去控制减温水阀门的开度,从而实现控制过热蒸汽温度。并且通过仿真验证来控制效果。采用AT89C51单片机来对温度进行控制,可以大幅度提高被控温度的技术指标,从而能够大大提高产品的质量和数量。因此,单片机对温度的控制问题是一个工业生产中经常会遇到的问题。第2章 余热锅炉蒸汽温度控制系统设计2.1 控制方案选择随着控制理论的发展,越来越多的智能控制技术,如自适应控制、模型预测控制、模糊控制、神经网络等,被引入到锅炉过热蒸汽温度控制中。但这些控制技术主要是为了改善和提高控制系统的控制品质,并没有从引起过热蒸汽温度波动的源头入手。
25、通常,烟气温度过高是引起过热蒸汽温度过高的主要原因。一般,过热蒸汽温度在烟气扰动下延迟较小,而在减温水量扰动下延迟较大,这种特性将使过热蒸汽温度的控制滞后。蒸汽温度系统则是余热锅炉系统安全正常运行,确保蒸汽品质的重要部分。本设计主要考虑的部分是余热锅炉蒸汽温度系统的控制。蒸汽温度系统包括一级过热器、减温器、二级过热器。控制任务是使过热器出口温度维持在允许范围内,并保护过热器时管壁温度不超过允许的工作温度。2.1.1 影响过热蒸汽温度的因素影响过热蒸汽温度的因素很多,其中主要的有:过热器是一个多容且延迟较大的惯性环节,设备结构设计与控制要求存在若矛盾,各种扰动因素之间相互影响,如蒸汽量、锅炉给水
26、温度、流经过热器的烟气温度及流速的变化等。而对各种不同的扰动,过热蒸汽温度的动态特性也各不相同。1、蒸汽流量扰动下的蒸汽温度对象的动态特性引起蒸汽流量扰动的原因有两个:一是蒸汽母管的压力变化,二是汽轮机调节阀的开度变化。结构形式不同的过热器,在相同蒸汽流量的扰动下,汽温变化的特性是不一样的。当锅炉负荷扰动时,蒸汽流量的变化使沿整个过热器管路长度上各点的蒸汽流速几乎同时改变,从而改变过热器的对流放热系数,使沿整个过热器各点的蒸汽温度几乎同时改变,因而汽温反应较快。其传递函数可以表示为: (2-1)式中: 锅炉负荷扰动时被控对象的放大系数; 一负荷扰动后对象的滞后时间; 对象的时间常数。从阶跃响应
27、曲线可知,其特点是:有延迟、有惯性、有自平衡能力,但其延迟和惯性都比较小,即时间常数和滞后时间都比较小,且较小。动态特性曲线如图2-1所示。2、烟气侧热量扰动下蒸汽温度对象的动态特性当燃料量、送风量或煤种等发生变化时,都会引起烟气流速和烟气温度的变化,从而改变了传热情况,导致过热器出口温度的变化。由于烟气传热量的改变是沿着整个过热器长度方向上同时发生的,因此汽温变化的迟延很小,一般在15-25s之间。烟气侧扰动的汽温响应曲线如图2-1所示,它与蒸汽量扰动下的情况类似。4烟气热量的扰动也几乎同时影响过热器管道长度方向各处的蒸汽温度,故它是一个具有自平衡能力、滞后和惯性都不大的对象,其传递函数可表
28、示为一个二阶系统,即: (2-2)式中: 为烟气温度但对象特征总的特点是:有迟延,有惯性,有自平衡能力。图2-1 蒸汽量D和烟气传热量Q扰动3、蒸汽温度在减温水量扰动下的动态特性当减温水量发生扰动时,虽然减温器出口处汽温已发生变化,但要经过较长的过热器管道才能使出口汽温发生变化,其扰动地点(过热器入口)与测量蒸汽温度的地点(过热器出口)之间有着较大的距离,此时过热器是一个有纯滞后的多容对象。动态曲线图如图2-2所示。当扰动发生后,要隔较长时间才能是蒸汽温度发生变化,滞后时间比较大,滞后时间约为30-60s。图2-2 蒸汽温度在减温水Ws扰动综上所述,可归纳出以下几点:(1)过热器出口蒸汽温度对
29、象不管在哪一种扰动下都有延迟和惯性,有自平衡能力。而且改变任何一个输入参数(扰动),其他的输入参数都可能直接或间接的影响出口蒸汽温度,这使得控制对象的动态过程十分复杂。(2)在减温水流量扰动下,过热器出口蒸汽温度对象具有较大的传递滞后和容量滞后,缩减减温器与蒸汽温度控制点之间的距离,可以改善其动态特性。(3)在烟气侧热量和蒸汽流量扰动下,蒸汽温度控制对象的动态特性比较好。由图可见,在减温水流量扰动下,减温器出口过热汽温的响应比过热器出口汽温快得多,可以肯定,在喷水减温过热蒸汽温度调节系统中,以减温器出口过热汽温作为导前信号构成调节系统,可大大改善控制系统的性能。总的来说,根据对过热蒸汽温度调节
30、对象做阶跃扰动试验得出的动态特性曲线可知,它们均为有延迟的惯性环节,但各自的动态特性参数值有较大的差别。因此,过热蒸汽温度控制的主要任务就是:(1)克服各种干扰因素,将过热器出口蒸汽温度维持在规定允许的范围内,从而保持蒸汽品质合格;(2)保护过热器管壁温度不超过允许的工作温度。本设计主要以控制减温水流量的变化来阐述对蒸汽温度的自动调节。2.1.2 单回路控制方案单回路控制系统是最基本的控制系统。由于其结构简单,投资少,易于调整,操作维护比较方便,又能满足多数工业生产的控制要求,应用十分广泛。在运行过程中,改变减温水流量,实际上是改变过热器出口蒸汽的热度,亦改变进口蒸汽温度。25减温器有表面式和
31、喷水式两种。减温器尽可能德安装在靠近蒸汽出口处,但一定要考虑过热器材料的安全问题,这样能够获得较好的动态特性。调节器和控制对象是单回路控制系统的两个主要组成部分。它们的特性将决定控制系统的控制质量,因此讨论控制对象的特征参数和调节器的调节参数对控制质量的影响是非常必要的。对象动态特性是确定系统结构、调节器的控制规律、设置调节器参数的依据,那么根据对象动态特性和生产过程对控制质量的要求,确定调节参数的数值是控制系统投入前要做的一项重要工作。如图2-3单回路方式原理图所示,系统引入过热蒸汽温度作为反馈量,是典型的简单控制系统。当过热蒸汽温度的测量值等于设定值时,喷水阀门不动,系统处在动态平衡状态,
32、此时,若炉膛燃烧工况发变化使蒸汽温度上升,造成给定值和测量值产生偏差,则偏差信号经过控制器的方向判断及数学运算后,产生控制信号使喷水阀门以适当形式打开喷水流量。测量值最终回到设定值,系统重新回到平衡状态。图2-3 单回路方式原理图2.1.3串级控制方案过热器出口蒸汽温度串级控制系统采用两级调节器,这两级调节器串在一起,各有其特殊任务,形成了特有的双闭环系统,由副调节器和减温器出口温度形成的闭环称为副环。由主调节器和主信号-出口蒸汽温度,形成的闭环称为主环,可见副环是环在主环之中。如图2-4所示为串级调节系统原理图。过热蒸汽温度调节的主要困难在于引起蒸汽温度变化的扰动因素很多,不容易控制。如蒸汽
33、流量、火焰中心位置、燃烧工况、烟汽温度和流速、炉温变化。其中起主要作用的是蒸汽流量和减温水流量两个方面。由于被控对象(过热器通道)具有较大的延迟和惯性以及运行中要求有较小的温度控制偏差。针对过热蒸汽汽温调节对象调节通道惯性延迟大、被调量信号反馈慢的特点,应该从对象的调节通道中选择一个比被调量反应快的中间点信号作为调节的补充反馈信号,以改善调节通道的动态特性,提高调节系统的控制品质。图2-4 蒸汽温串级调节系统原理图将图2-4所示过热蒸汽温调节原理图转化为方框图,即为图2-5所示,由图2-5所示可以看出,此串级控制回路是用两个串联的PID控制器和一个执行器来控制主汽温度的。其基本原理就是系统根据
34、过热汽温度设定值和反馈值y1的偏差e,作为主调节器的输入,主调节器经过PID运算后的输出u1作为副调节器的输入设定值,此设定值与二级喷水减温器的出口温度反馈y2的偏差e2作为二级过热器出口温度调节器的输入,其输出u2作为执行器的输入动作指令。图2-5 串级PID控制图一般在过热蒸汽温度调节系统中,副调节回路的动态特性的迟延和惯性比较小,在这种情况下,副回路的调节过程快得多,当副回路消除喷水扰动时,过热汽温度基本上不受影响。因此,当副回路动作时主回路可以看作是开路,主回路动作时,副回路可以看作是迅速动作的随动系统,即二级减温器出口温度基本上与校正信号e2成比例变化。2.1.4 前馈控制方案为改善
35、调节品质,引入导前气温微分信号,组成气温调节系统的有一种策略。由气温被调对象的动态特性可知,导前气温可以提前反应扰动,取其微分信号引入调节器后,由于微分信号动态时不为零稳态时为零,所以动态时可使调节器的调节作用超前,稳态时可使过热器出口温度等于给定值,从而改善调节品质。在过热蒸汽温度的控制中,扰动有很多如蒸汽流量扰动、烟气侧传热量的扰动、喷水量扰动等等。如果我们引入一个量来校正就构成了前馈控制系统。如图2-6为前馈控制的原理图及方框图。图2-6 前馈控制原理图及方框图将减温器出口温度的微分信号作为前馈信号,与过热器出口温度相加后作为过热器温度控制器测量,当减温器出口温度有变化时,才引入前馈信号
36、。稳定情况下,该微分信号为零,与单回路控制系统相同。其中是原调节算法,是执行元件和可能的其他环节。现希望用完全抵消扰动的影响。把图2-6等效为图2-7,显然,只有当=才能完全抵消扰动的影响。图2-7 等效的原理框图2.2 控制方案的比较和方案确定2.2.1 控制方案的比较 闭环控制系统是指控制器与被控对象之间既有顺向控制又有反向联系的控制系统。闭环控制系统的优点是不管任何扰动引起被控变量偏离设定值,都会产生控制作用去克服被控变量与设定值的偏差。因此闭环控制系统有较高的控制精度和较好的适应能力,其应用范围非常广泛。缺点是闭环控制系统的控制作用只有在偏差出现后才产生,当系统的惯性滞后和纯滞后较大时
37、,控制作用对扰动的克服不及时,从而使其控制质量大大降低。17在闭环控制系统中,根据设定值的不同形式,又可分为定值控制系统,随动控制系统和程序控制系统。串级控制系统由于副环的存在,改善了对象的特性,使等效副对象的时间常数减小,系统的工作频率提高。同时,由于串级系统有主、副两只控制器,使控制器的总放大倍数增大,系统的抗干扰能力增强。主调节器为PID,副调节器为PI,在串级系统中,由于副回路可以很快的消除减温水流量的自发性扰动和其他进入副回路的各种扰动,对过热蒸汽温度的稳定起粗调作用,主调节器的作用是保证过热蒸汽温度趋于给定值。然而当工况变化时,对象特性发生变化,这将使得控制质量变坏,一般控制效果不
38、好。单回路控制系统的特点是将被控量的状态测量出来并和给定值进行比较,有偏差就可以修正,因此必须知道被控量的准确状态,如果不能正确的检测出被控量的状态,就不能进行控制,所以要求检测环节的精度和灵敏度更高。另外,作为被控量的过程变量,如果不先改变其状态而把它直接作为控制系统的信号,在大多数情况下是不适宜的。所以除了特别简单的自动控制外,一般不采用对被控量直接控制的方式。在多数的过程控制中,一般都将通过检测环节的信号变换成便于控制的信号。前馈控制系统是依据干扰的大小;其调节作用发生在过程输出变量出现偏差之前,比单回路控制及时。前馈控制必须使用针对具体过程的干扰和受控输出变量特性的专用控制器。不可能有
39、专用的前馈控制器。这也给实际应用增加了麻烦和困难。一种前馈控制作用只能消除一种干扰的影响。前馈和反馈完全不同,前馈控制不是闭环而是开环系统。控制变量被调节后并不反过来影响干扰变量;调节作用对受控输出变量影响的结果也没有反馈机制。相形之下,一个反馈回路有可能克服多种干扰的影响。由此可以看出,尽管前馈控制具有在理论上可以实现完美控制的吸引力,实际应用还仍然受到许多限制。2.2.2 方案的确定不同的控制方法都有自己的优点与缺点,由于此系统干扰很小可以忽略不计,以上三种方案都能实现对过热蒸汽温度的控制,但是从成本上来看单回路控制更经济些,因此经过分析采用单回路控制能满足本设计的需要,而且单回路控制形式
40、简单,容易实现。根据控制要求,温度单回路控制系统的控制参数是蒸汽温度,测量便采用温度传感器,控制器是单片机,执行器是调节阀,所以温度单回路控制系统的结构框图如图2-8所示。图2-8 单回路控制系统方框图第3章 系统硬件设计3.1 系统结构框图余热锅炉蒸汽温度控制系统的主控部分由单片机构成。通过按键电路进行温度报警值的设定,并对锅炉的过热蒸汽温进行采集及处理,然后与报警值比较,当过热蒸汽温度的测量值等于设定值时,喷水阀门不动,系统处在动态平衡状态。8此时,若炉膛燃烧工况发变化使蒸汽温度上升,造成给定值和测量值产生偏差,则偏差信号经过控制器的方向判断及数学运算后,产生控制信号使喷水阀门以适当形式打
41、开喷水流量。测量值最终回到设定值,系统重新回到平衡状态。下图3-1为系统结构框图。图3-1 系统方案框图3.2 单片机与8155的接口电路MCS-51单片机可直接和8155连接,不需要任何外加逻辑电路,可以直接为系统增加256B外部RAM、22根I/O线及一个14位定时器。其基本硬件连接方法如图3-2所示。由于8155片内有锁存器,所以单片机P0口输出的低8位地址不需要另加锁存器,直接与8155的AD7AD0相连,既作为低8位地址总线,又作为数据总线,利用8051的ALE信号的下降沿锁存P0送出的地址信息。片选信号CE和IO/M选择信号分别接P2.7和P2.0。图3-2 51单片机与8155的
42、连接方式3.3 信号输入部分3.3.1 温度信号采集与处理采用构建桥式电路,电桥的四个电阻中三个是恒定的,另一个用Pt100热电阻,当Pt100电阻值变化时,测试端产生一个电势差,由此电势差换算出温度。电路中使用的是1k(0)的铂电阻,因为铂电阻阻值高达1k所以不受布线温度的影响。R0、R1、Rt构成桥式电路桥式电路的输出电压经由差动放大器放大。可以表示为: (3-1)在图中所示参数的条件下,的灵敏度为1.395mA/;为了将他放大为10mA/的灵敏度,差动放大器的增益G必须为10/1.395=7.17倍。具体电路如图3-3所示。该电路中为了使桥式电路的电阻不受影响,将输入电阻选取了高达1M的
43、数值,由此决定了运算放大器必须是低输入偏置电流的场效应管晶体管输入型。经过仪器放大器放大后的电压输出送给A/D转换芯片的INO口,从而把热电阻的阻值转换成数字量。18图3-3 信号采集与处理3.3.2 A/D转换利用热电阻PT100温度传感器具有抗振动、稳定性好、准确度高、耐高压、线性较好的特点作为温度传感器,然后通过运算放大器构建差分放大将温度信号转换成ADC0809模拟通道的输入的0-5V标准信号,再将模拟信号转换为数字信号,送入单片机。AD转换器选ADC0809,ADC0809是一种逐次比较式的8路模拟输入,内部具有所存功能,故不需加地址锁存器。ALE脚为地址所存信号,高电平有效,三根地
44、址线固定接地,由于地址信号已经固定,固将ALE接高电平。系统只需要一路信号,选择IN-0作为输入。START脚为AD转换启动信号,高电平有效,程序控制。AD采样值为系统的偏差信号,固选择ADC0809的VREF接+5V和-5V。由图可以看出,ALE信号和START信号联系在一起,这样连接可以在信号的前沿写入地址信号,在其后沿启动A/D转换。START和ALE互连可以使ADC0809在接收模拟量路数地址时启动工作。START启动信号由89S51的WR和P2.5经或非门产生。AD转换结果由8155的PA0PA7口读入,故将AD转换器的输出与8155的PA0PA7口相连,高地位依次相连。AD转换器与
45、单片机的接口电路如下图3-4所示。图3-4 ADC0809与单片机的接口设计3.4 显示电路设计数码管动态显示实际是将所有数码管的8个笔画段ah的各同名段分别并接在一起,并把他们接在单片机的字段输出口上。为了防止各个数码管同时显示相同的数字,各个数码管的公共端COM还要收到另一组信号的控制,即把他们连到位输出口上。这样,一组数码管显示器需要由两组信号来控制:一组字段输出口输出的字形代码,用来控制显示的字形,称为段码;另一组是位输出口的控制信号,用来选择第几个显示器工作,称为位码。所谓动态显示就是利用循环扫描的方式,分时轮流宣统各个数码管的公共端,使各个数码管轮流导通,在导通的同时送上不同的段码
46、。当扫描速度达到一定程度时,人眼就分辨不出来了,即认为各个数码管在同时显示。12如图3-5所示,8155的PB口作为段控制,PC口通过4个PNP型三极管8550控制数码管的4个COM公共端。如果要第一个数码管显示数据,PC0需要输出低电平0,则此时第一个PNP三极管导通,通过第一位数码管的COM公共端向第一个数码管供电。以此类推,可以分时点亮4个LED数码管。但是,需要注意的是不能让PC0PC3中的2个或2个以上同时输出低电平0,否则就会造成显示混乱,除非2个数码管上要显示的内容相同。本例中数码管选择的是SM410364共阳极四位一体的LED显示器。三极管采用PNP型8550,PB口接的限流电
47、阻是8个470的;PC口上接的电阻是4个4.7K的;PB口接的8个上拉电阻都是4.7K的。图3-5 数码管动态显示驱动电路3.5 信号输出部分3.5.1 D/A转换DAC0832的基本原理是把数字量的每一位转换成相应的模拟量,然后根据叠加定理将每一位对应的模拟分量相加,输出相应的电流或者电压。DAC0832是具有两个输入数据寄存器的8位DAC,可以直接与51单片机相连,参考电压+5V,直接与供电电源相连。DAC0832是电流型输出,在应用时外接运放使之成为电压型输出。CSDA:片选信号输入线(选通数据锁存器),低电平有效;WR:数据锁存器写选通输入线,负脉冲(脉宽应大于500ns)有效。由IL
48、E、CS、WR1的逻辑组合产生LE1,当LE1为高电平时,数据锁存器状态随输入数据线变换,LE1的负跳变时将输入数据锁存;DAC0832的数据口和单片机的P1口相连,片选信号CS为P2.6。如图3-6为DAC0832与单片机的连接电路。图3-6 DAC0832与单片机的接口设计3.5.2 4-20mA标准信号输出 LM324的5管脚与DAC0832的(IOUT2)12管脚相连,LM324的6管脚与DAC0832的(IOUT1)11管脚相连,LM324的7管脚与DAC0832的REF(9)管脚相连。第一级运算放大器的作用是将DAC0832输出的电流信号转化为电压信号V1,第二级运算放大器的作用是
49、将输出的0-5V电压转换为4-20mA标准信号。从而控制输出调节蒸汽温度减温阀,达到减温的目的。4-20mA标准信号输出如下图3-7所示。图3-7 4-20mA标准信号输出3.6 串口与上位机通信电路单片机与外部设备或单片机与单片机之间的数据传输称为通信,其传输介质称为通信接口。按信号传输方式,通信可分为并行通信与串行通信两种基本方式。14上位机的RS232串口标准为:正电平在+3V+15V,负电平在-3V-15V。也就是说对于RS232信号而言,当传输点评的绝对值大于3V时,电路可以有效地检查出来,介于-3V+3V之间的电压无意义,低于-15V或高于+15V的电压也认为无意义。因此,实际工作
50、时,应保证电平在(315)V之间。而单片机使用的是TTL/COMS电平,与RS232串行借口标准是不兼容的,因此要实现上位机和单片机之间的通信,必须进行电平的转换。这里采用电平转换收发芯片MAX232进行RS232与TTL/CMOS电平的转换,实现单片机与计算机通信,51单片机与该芯片接口电路如图3-8所示,T1IN、T2IN为TTL/CMOS电平输入端,T1IN、T2IN可连接单片机的TXD(发送)引脚。R1OUT、R2OUT为TTL/COMS电平输出端,R1OUT、R2OUT可连接单片机的RXD(接收)引脚。R1IN、R2IN为RS232电平输入端,R1IN、R2IN连接DB9借口的3脚,
51、接收上位机发来的数据。T1OUT、T2OUT为RS232电平输出端,T1OUT、T2OUT连接到DB9的2脚,向上位机发送数据。1、3和4、5引脚之间分别接电容,Vcc和V+之间接电容,GND和V-之间接电容。DB9接口的5脚必须接地。图3-8 单片机与MAX232的接口电路3.7 报警电路设计报警电路与8155的PC4口相连接,由于单片机的I/O口输出的电流无法直接驱动蜂鸣器,所以设计了报警电路如图3-9所示:当蒸汽温度高于上限温度、低于下限温度或者在输入错误时,单片机给8155的PC4口输出一个低电平信号来导通三极管8550以驱动蜂鸣器和LED灯,进行系统报警,当温度恢复到设置范围内后,声
52、光报警自动撤销。图3-9 报警电路3.8 键盘电路设计键盘是由一组规则排列的按键组成,一个按键实际上是一个开关元件,也就是说键盘是一组规则排列的开关。本次设计中,按键较少,故而选择独立式按键。进入系统之前首先对温度报警值的设置。本系统有四个按键分别K1,K2,K3,K4。(1)K1功能键:选择修改温度设定值、上限值、下限值、显示温度。(2) K2确认键:对结果确认并保存。(3) K3加1键:设置余热锅炉锅炉温度报警值的温度值增加按键;K3每按下一次,位选标志所指的当前位的值加比上一次值增加一。(4) K4减1键:设置余热锅炉锅炉温度报警值的温度值减少按键;K4每按下一次,位选标志所指的当前位的
53、值比上一次值减少一。如图3-10所示四个按键分别与单片机的P2.1、P2.2、P2.3、P2.4相连,各个按键的开关处均采用了4*10K的上拉电阻,这是为了保证按键开关断开时,各I/O口线有确定的高电平。图3-10 键盘电路3.9 稳压电源电路设计如下图3-11所示是由变压器、整流电路、滤波电路、稳压电源等几部分电路组成。变压器的输出端是三抽头的,经过两组整流二极管整流,在通过电容C1、C6和C2、C7滤波后分别输入到稳压片子7812和7912的输入端,从7812 和7912的输出端就可以得到比较稳定的12V电压和-12V电压。12V电压在通过两个电容滤波后输入到7805稳压芯片的输入端,在7
54、805的输出端就可以得到5V的稳定电压。图3-11中两个发光二极管起到电源指示作用。图3-11 稳压电源电路图3.10 单片机最小系统3.10.1时钟电路单片机虽然有内部振荡电路,但要形成时钟,必须外部附加电路。利用芯片内部的振荡电路,在第18脚XTAL1、第19脚XTAL2上外接定时元件,内部的振荡电路便产生自激振荡,用示波器可以观察到XTAL2输出的时钟信号。振荡晶体可在1.2MHz12MHz之间选择,电容值无严格要求,但在电容值取值对振荡频率输出的稳定性、大小、振荡电路起振速度有少许影响,CX1、CX2可在20pF100pF之间取值。在外部晶体上选用晶体振荡器,频率为12MHz,为提高频
55、率稳定性,CX1、CX2都为30pF。时钟电路如图3-12所示。图3-12 时钟电路3.10.2复位电路复位是单片机的初始化操作,在其上电后第9脚RESET出现24个振荡周期以上的高电平后,单片机内部初始复位。如图3-13所示是一个简单的手动复位与上电复位综合的复位电路。R1、R2构成手动复位电路,R2一般取15K.当R1=200时,R2=1K时,若按键按下,实现可靠复位其复位电压为4.17V。当k闭合、Urst3V时,是可靠的复位电平,则该电路的复位时间约为11ms。为保证可靠复位,一般选取复位时间为10ms即可。2图3-13 复位电路第4章 系统软件设计4.1 软件设计思路本章详细的介绍了
56、基于AT89S51单片机的余热锅炉过热蒸汽温度控制系统的软件设计。根据系统功能,可以将系统设计为若干个子程序进行设计,如温度采集子程序、PID控制子程序、显示子程序等。本章从设计思路、软件系统框图出发,先介绍整体思路,在逐一分析各模块程序算法的实现,最终编写满足任务需要的程序。本系统要完成温度信号的采集与控制,需要实现温度信号的采集与A/D转换、数据处理、数据显示、数据传输等基本功能。从功能上可以将其分为信号输入、控制单元、信号输出三大部分进行设计。4.2 系统软件流程图4.2.1 主程序流程图在系统软件中,主程序依次完成系统初始化、温度信号采集与处理、PID控制算法、温度显示、上位机等.系统
57、的初始化包括通信的初始化(串口的初始化,ADC0809的初始化,通信缓冲区的初始化),LED显示的初始化,输出端口的初始化,采集、累计数据的初始化。A/D转换包括数据转换(主要实现将测量电路监测到的电压信号转换成LED显示所需的数据类型)。显示数据包括显示温度的上限值、下限值以及温度数值显示。其程序主流程图如下图4-1所示。设计时采用单回路控制系统对余热锅炉的过热蒸汽温度进行控制,以AT89S51单片机为核心,包括温度采集模块、按键处理模块、温度显示模块、控制输出模块、执行机构模块和通信模块等组成。图4-1 主程序流程图4.2.2 采样子程序首先由热电阻温度传感器检测外部输入的模拟量信号,通过
58、运算放大器构建差分放大后,温度信号转换成ADC模拟通道输入的标准信号,将模拟信号转换为数字信号后进行显示温度测量结果,图4-2所示为温度信号采集流程图。图4-2 采样子程序流程图4.2.3 数字滤波由于干扰的存在,可能导致AD转换的结果与锅炉蒸汽温度出现差异,为了提高系统的可靠性和信号的真实性,采用程序计算的方法对采样信号进行平滑加工,从而克服虚假信号,这种算法称为数字滤波。数字滤波的方法有以下几种:1.限幅滤波,其基本方法是通过比较相邻(n和n-1时刻)的两个采样值和,如果它们的差值过大超出了参数可能的最大变化范围,则认为发生了随机干扰,并视后一次采样值为非法值,应予剔除。2.中值滤波,就是
59、连续采样三次,取中间值作为本次采样值。3.算术平均滤波,就是连续取几个采样值进行算术平均。因算术平均滤波方法简单、数据采集更加精确,滤波结果就是对单点温度多次采样的平均值,更加准确的反应了被测温度的大小,因此,本系统采用了算术平均滤波法。设计时,外部输入的模拟量信号首先由温度传感器送入放大器,然后进行模拟量采集,在一次采样间隔时间T内,依次将各输入量轮流接到A/D转换器进行一次转换。为了准确地反映被测信号,防止干扰,对每一路信号在20 ms内采集4次,即采样间隔时间T=5ms,4次采集完成后再将4次采集的值求平均得出此次采集的结果。在20ms的采集完成后,要将数据按照量程或计算公式转换为有实际
60、意义的数据,并根据报警界限判断数据是否有低于下限或超出上限的报警。134.2.4 中断服务T0中断服务程序是温度控制系统的主题程序,用于启动数/模转换器、读入采样数据、数字滤波等。AT89S51利用T1中断的时间完成本次采样值转换成显示值而放入显示单元缓冲区和调用温度显示程序。89S51从T1中断服务程序返回后即可恢复现场和返回主程序,以等待下次T0中断。主要服务子程序包括温度检测采样及数字滤波子程序、带符号双字节乘法子程序和标度转换子程序,目的是把实际采样取得的二进制值转换BCD码形式的温度值,然后存放在显示缓冲区中,供显示子程序调用。22其中断服务程序如图4-3所示。图4-3 中断服务程序
61、框图对于一般线性仪表来说,标准转换公式: (4-1)其中,为一次测量仪表的下限;Am为一次测量仪表的上限;Vx为实际测量值(工程量);Vm为仪表上限对应的数字量;为仪表下限对应的数字量。4.2.5 显示环节软件设计在本环节由于选用的数码显示是动态数码显示,可以对数码管进行十分位、个位、十位、百位不同位置的提取并进行修改其位值,通过与按键和上位机的结合更简单的进行温度数值修改如图4-4所示。图4-4 显示环节流程图4.2.6 上位机控制软件设计由单片机采集的测试点实时温度,通过MAX232传输到上位机,实现与单片机串行通信。在上位机中,完成温度传感器64位激光ROM读取并显示、实时温度数据显示、蒸汽温度控制点、蒸汽温度低报警点、蒸汽温度高报警点、数据存储、历史数据查询。如图4-5所示为上位机控制流程图。图4-5 上位机控制流程图4.2.7 PID子程序根据蒸汽温度对给定温度的偏差,用PID算法对两者之差做变换,然后输出信号控制调节阀。调节阀由给定信号开始动作,控制高温烟气的流量,从而控制出口蒸汽的温度。按照偏差的比例、积分和微分产生控制作用(PID控制),是过程控制中应用最广泛的一种控制形式。24PID控制程序PID是对系统进行线性控制的一种控制器。所谓PID控制,就是按设定值与测量值之问偏差的比例、偏差的
- 温馨提示:
1: 本站所有资源如无特殊说明,都需要本地电脑安装OFFICE2007和PDF阅读器。图纸软件为CAD,CAXA,PROE,UG,SolidWorks等.压缩文件请下载最新的WinRAR软件解压。
2: 本站的文档不包含任何第三方提供的附件图纸等,如果需要附件,请联系上传者。文件的所有权益归上传用户所有。
3.本站RAR压缩包中若带图纸,网页内容里面会有图纸预览,若没有图纸预览就没有图纸。
4. 未经权益所有人同意不得将文件中的内容挪作商业或盈利用途。
5. 装配图网仅提供信息存储空间,仅对用户上传内容的表现方式做保护处理,对用户上传分享的文档内容本身不做任何修改或编辑,并不能对任何下载内容负责。
6. 下载文件中如有侵权或不适当内容,请与我们联系,我们立即纠正。
7. 本站不保证下载资源的准确性、安全性和完整性, 同时也不承担用户因使用这些下载资源对自己和他人造成任何形式的伤害或损失。