浅析20CrMnTi热轧棒材表面裂纹特点及产生原因.doc
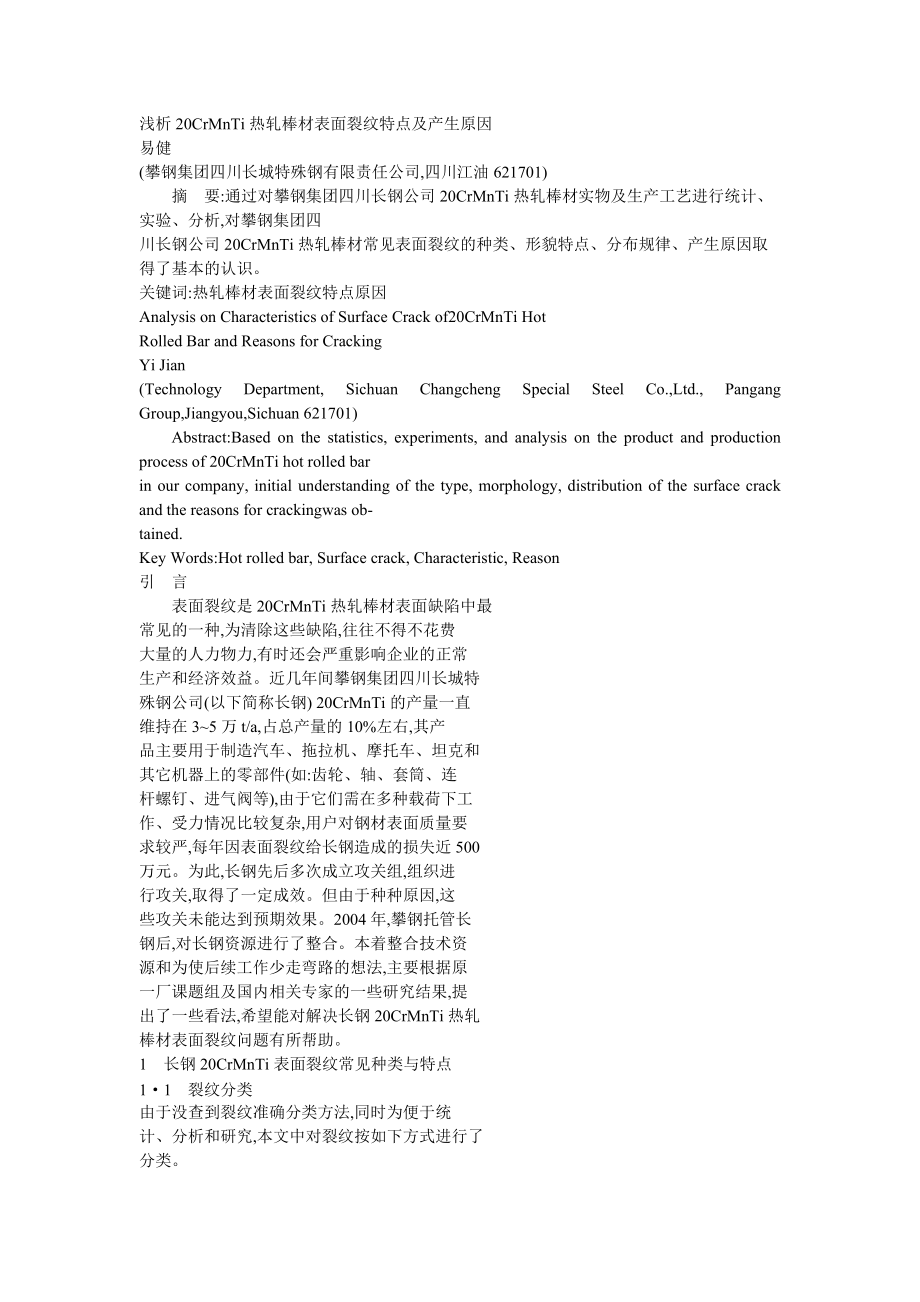


《浅析20CrMnTi热轧棒材表面裂纹特点及产生原因.doc》由会员分享,可在线阅读,更多相关《浅析20CrMnTi热轧棒材表面裂纹特点及产生原因.doc(14页珍藏版)》请在装配图网上搜索。
1、浅析20CrMnTi热轧棒材表面裂纹特点及产生原因易健(攀钢集团四川长城特殊钢有限责任公司,四川江油621701)摘要:通过对攀钢集团四川长钢公司20CrMnTi热轧棒材实物及生产工艺进行统计、实验、分析,对攀钢集团四川长钢公司20CrMnTi热轧棒材常见表面裂纹的种类、形貌特点、分布规律、产生原因取得了基本的认识。关键词:热轧棒材表面裂纹特点原因Analysis on Characteristics of Surface Crack of20CrMnTi HotRolled Bar and Reasons for CrackingYi Jian(Technology Department,
2、Sichuan Changcheng Special Steel Co.,Ltd., Pangang Group,Jiangyou,Sichuan 621701)Abstract:Based on the statistics, experiments, and analysis on the product and production process of 20CrMnTi hot rolled barin our company, initial understanding of the type, morphology, distribution of the surface crac
3、k and the reasons for crackingwas ob-tained.Key Words:Hot rolled bar, Surface crack, Characteristic, Reason引言表面裂纹是20CrMnTi热轧棒材表面缺陷中最常见的一种,为清除这些缺陷,往往不得不花费大量的人力物力,有时还会严重影响企业的正常生产和经济效益。近几年间攀钢集团四川长城特殊钢公司(以下简称长钢) 20CrMnTi的产量一直维持在35万t/a,占总产量的10%左右,其产品主要用于制造汽车、拖拉机、摩托车、坦克和其它机器上的零部件(如:齿轮、轴、套筒、连杆螺钉、进气阀等),由于它们
4、需在多种载荷下工作、受力情况比较复杂,用户对钢材表面质量要求较严,每年因表面裂纹给长钢造成的损失近500万元。为此,长钢先后多次成立攻关组,组织进行攻关,取得了一定成效。但由于种种原因,这些攻关未能达到预期效果。2004年,攀钢托管长钢后,对长钢资源进行了整合。本着整合技术资源和为使后续工作少走弯路的想法,主要根据原一厂课题组及国内相关专家的一些研究结果,提出了一些看法,希望能对解决长钢20CrMnTi热轧棒材表面裂纹问题有所帮助。1长钢20CrMnTi表面裂纹常见种类与特点11裂纹分类由于没查到裂纹准确分类方法,同时为便于统计、分析和研究,本文中对裂纹按如下方式进行了分类。直型裂纹:指裂纹总
5、长60%以上基本呈直线且偏角小于30度的裂纹。曲型裂纹(不规则裂纹):除直型裂纹以外的裂纹。长型裂纹:指裂纹长度大于等于300mm的表面裂纹。短型裂纹:指裂纹长度小于300mm的表面裂纹。宽型裂纹:指裂纹最大宽度大于等于1mm的表面裂纹。窄型裂纹:指裂纹最大宽度小于1mm的表面裂纹。深型裂纹:指裂纹深度大于0.4表面裂纹。浅型裂纹:指裂纹深度小于0.4表面裂纹。密型裂纹:指在圆周角小于等于30度所对应的圆周面上裂纹条数小于等于3条的裂纹疏型裂纹:指在圆周角小于等于30度所对应的圆周面上裂纹条数大于3条的裂纹1.2大批量进行统计、分析和研究、检测,采用以 下非常规检测手段裂纹长度测度方法:如裂纹
6、呈直线,直接用游标卡尺测量,如有偏角,则用线沿裂纹走向记下裂纹长度再用游标卡尺测量线长。裂纹宽度测度方法:肉眼观测最宽处再用游标卡尺测量其宽度。裂纹深度测量方法:在砂轮上在试样裂纹处打磨至肉眼不见,再用千分尺测量外径与打磨前外径的差值计为其裂纹的深度。裂纹面圆周角度测量方法:在裂纹处将试样切断,再测裂纹断面所对应的角度。1.3统计对象与方法及结果1.3.1统计对象攀钢集团长钢公司20CrMnTi热轧棒材生产工艺路线较为复杂,基本包括了国内大部分工艺路线,为了便于研究和叙述,这里只选取较有代表性的一生产区60mm圆热轧棒材的生产工艺路线作简单介绍。其工艺路线如下:工艺路线1:电炉模铸锻造开坯轧制
7、工艺路线2:电炉精炼连铸轧制1.3.2统计方法在成品机架分别按不同工艺路线各随机抽取5000个裂纹样,按上述规定将其归入不同表面裂纹类。然后进行组合。1.3.3统计结果经对10000个试样进行检测和统计,并进行组合,各种裂纹所占比例见表1。表1热轧棒材表面裂纹种类比例表Table1Statistical information on the types of surface cracks裂纹名称比例/%直宽短型34.27直长型27.58不规则型8.75其它29.9合计100由表1可知,长钢生产的20CrMnTi表面裂纹主要是直宽短型、直长型、及不规则型。侧。该类裂纹大多较深,有的经打磨后,可能
8、超差。1.4.3不规则型这类裂纹以短而细为其主要特征,裂口比发丝宽;一般可见圆底,呈断续分布。可以检测出,大部分为常见的发纹。2钢锭质量与表面裂纹关系由于研究中对钢锭表面质量均有严格要求,所有试验用钢锭表面质量均经课题组人员验收才取用,因此可假定钢锭表面质量未对试验结论造成重大影响,这里只考虑钢锭内部质量与表面裂纹关系。根据上述思路设计进行了500kg、800kg及150mm150mm连铸坯、200mm200mm方连铸坯锭型对比实验、气体含量对比实验、夹杂物对比实验三个试验项。实验中,于轧制加热装炉前,模铸每炉分清头、尾各选2支坯,进炉排在前面,然后作好标记,记录,以便轧后热锯取样时取到钢锭真
9、正的头、尾;为了使两种方坯在轧制同规格材时的加热制度、轧制参数等条件尽量相近,以利找出锭型对轧材表面质量的影响关系,轧制加热装炉时采用两种规格方坯(以炉为单位)交替进炉加热;记录好加热、轧制工艺参数,对应抽查表面情况,做四次实验。2.1第一试验情况选20CrMnTi模铸轧材10炉,550kg 5炉,800kg5炉,成品机架随机取样40支,经低倍酸洗后,其表面检验结果如表2所示。Examination results on surface crackof rolled bar produced by mould casting blank锭型裂纹率/%大锭尾60.00小锭尾75大锭头50小锭头1
10、00从表2中的数据可以看出:本次实验的10炉大锭轧材表面裂纹产生机率比小锭轧材产生机率低。头部轧材表面裂纹产生机率较尾部大。2.2第二次试验的轧材表面质量检查情况第二次试验的10炉20CrMnT连铸坯轧材(150方mm150mm 5炉,200mm200mm方5炉),每炉分别抽取了20支钢材对应检查,结果见表3。表3第二次试验20CrMnTi表面裂纹情况Table3Examination results on surface cracks of therolled bar produced by continuous casting blank坯型表面情况每支裂纹条数裂纹严重者裂纹较轻者条数裂纹
11、率最少最多平均材支数占总裂纹/%材支数占总裂纹/%200 6 30 0 2 0.40 2 33.33 4 66.67150 6 30 0 4 0.60 0 0 6 100200 3 1.5 0 4 0.30 0 0 3 100150 5 25 0多条0.20 1 20 4 80200 19 95 0多条2.50 17 89.47 2 10.53150 16 80 0多条3.60 12 75 4 25200 4 20 0多条0.15 3 75 1 25150 16 80 0 10 1.5 5 31.25 11 68.75200 6 30 0多条0.45 4 66.67 2 33.33150 9
12、45 0 5 0.85 1 11.11 8 88.89200 38 38 0 0.76 2.6 68 12 31.59150 52 52 0 1.35 19 36.56 33 63.460 45 0 1.055 45 59.77 45 50表3内数据表明:这10炉连铸坯轧材中,200方连铸坯轧材表面裂纹发生机率小于150mm150mm方连铸坯轧材表面裂纹发生机率,但200mm200mm方连铸坯轧材裂纹较严重的材发生机率高于150mm150mm方连铸坯轧材。2.3第三次试验的轧材表面质量检查情况第三次试验20炉钢,其中550kg锭5炉、800kg锭5炉、150mm150mm方连铸坯5炉、200m
13、m200mm方连铸坯5炉。每炉随机抽样20支,空冷后表检。检验结果见表4表4第三次试验20CrMnTi表面裂纹情况表Table4Statistical information on the surfacecracks in the third test锭型坯型表面情况每支裂纹条数裂纹严重者裂纹较轻者发生裂纹支数裂纹率/%最少最多平均材支数占总裂纹/%材支数占总裂纹/%150方150方6 30 0 2 0.35 1 16.67 5 83.33200方200方4 20 0 6 0.85 4 44.44 5 55.56550kg 130方锻坯9 45 0 10 1.00 1 11.11 8 88.8
14、9800kg 130方锻坯8 40 0 12 1.70 3 37.50 62.50由表4不难看出:本次试验中连铸坯轧材表面裂纹发生机率小于模铸轧材。2.4第四次试验的轧材表面质量检查情况第四次试验6炉钢,其中550kg锭3炉、分别开成130mmmm130mm方坯、140mm140mm方坯、150mm150mm方坯, 800kg锭3炉、分别开成130mm130mm方坯、140mm140mm方坯、150mm150mm方坯150。基于前三次的试验、检测内容及统计分析之情况,本次试验只进行轧材表面质量的检验和分析。方法是每炉随机抽样20支,结果见表5。表5第四次试验20CrMnTi表面裂纹情况表Tab
15、le5Statistical information on the surfacecracks in the fourth test锭型/kg坯料/mm2发生裂纹支数裂纹率/%最少最多平均材支数550 130130 8 40 0 12 0.3 3140130 8 40 0 10 0.35 1150130 9 45 0 10 0.4 1800 130130 6 30 0 8 0.3 1140130 6 30 0 7 0.32 0150130 7 35 0 6 0.35 0由表5不难看出:在轧机孔型不变情况下,坯料尺寸也会对轧材表面质量产生影响。同时可以推断孔型系统和坯料尺寸有个最佳配合。3四次试
16、验表面裂纹的类型通过分别对四次试验所取试样的表面裂纹按类型统计,可知模铸轧材的表面裂纹主要是发纹为主,直、短、宽、浅型裂纹次之。连铸坯轧材表面裂纹以直短宽型裂纹居多,其中150mm150mm方连铸坯轧材的表面裂纹主要是细、直长深型和直短宽型裂纹为主,其次是发纹;200mm200mm方连铸坯轧材的表面裂纹则以发纹和直短宽型为主。4加热参数与表面裂纹关系通过对第一次、第二次试验的轧制加热参数(加热温度、时间、阴阳面温差)的现场考查可以看出这样一个趋势:在轧制加热时,若加热段(腰炉)的温度高于(或近于)均热段(头炉)温度,则轧材表面裂纹率较低,且每支材上的平均裂纹条数也明显较少:反之,则裂纹率和每支
17、材的平均裂纹条数均偏高。此外,还可以看出加热时钢坯阴阳面温差的大小与表面裂纹也存在一定联系,这将在后面加以分析。5表面裂纹在轧材表面的分布情形为便于寻找表面裂纹在轧材上的分布规律及表面裂纹形成原因与分布情形的关系:将裂纹在轧材表面的分布分为四种情形:即:(1)单侧裂纹;(2)双侧裂纹;(3)三面裂纹;(4)周身裂纹。并按各次试验进行分析通过对四次试验结果的统计分析可知:模铸轧材的表面裂纹以单侧裂纹为主,其次是周身裂纹。连铸坯轧材表面裂纹常以双侧裂纹形式出现,但有时周身裂纹的轧材数比重有可能占主导地位。6表面裂纹产生的机理探讨6.1直、短、宽型裂纹的致因在对直、短、宽型裂纹的金相观察时发现,这类
18、裂纹与表面垂直,裂纹处有呈黑色蜂窝状气孔通道、周边基体明显的脱碳现象,周围或尾部有氧化物夹杂的聚集,氧化物位于与下常驻组织交界处的脱碳层中。由此可以推断,该类裂纹主要是由皮下汽泡造成。其产生过程是钢液凝固过程中,氢、氮、氧等呈现气态析出,在钢锭中留下气孔或显成的微气体、破坏了钢的致密性,钢锭(坯)加热时造成缺陷暴露后与炉气接触被氧化,轧制过程不能焊合而形成表面裂纹。脱碳是在高温下钢料所含的碳分别与炉气中的H2O、CO2、O2、H2等进行化学反应,造成钢料表面层含碳量减少。为防止这类裂纹的产生或有效地减少轧材的直、短、宽型裂纹,必须保证冶炼和浇铸的质量,减少皮下汽泡的产生。6.2直长裂纹的形成原
19、因在对宏观为直长裂纹进行金相高倍观察时发现,周边基体组织正常,部分裂纹处有脱碳现象,但脱碳层不深。裂纹槽底平直,裂纹源与裂纹末端形状差别不大,裂纹中或裂纹源处往往含有氧化铁(皮)夹杂。由此可见,20CrMnTi轧材中的细、直、长深型裂纹实质上就是折迭裂纹。其形成机理是由于在加工过程中,坯料中的折迭未能及时清除,则在以后的加工工序中便会导致应力集中而开裂。防止折迭产生方法有:(1)加强轧机调整,避免在间道次出耳子;(2)孔型某部位磨出尖棱时,应及时修磨或更换;(3)加强导板的检查、调整,保持工件表面光滑、平整,以免划伤轧件;(4)钢坯清理的沟槽要严格按标准规定的长、宽、深比例进行。特别值得一提的
20、是:20CrMnTi轧材表面的部分折迭有形似“鬼线”的缺陷相伴随。这种“鬼线”其实是包裹着夹杂物的白色铁素体带。其表面裂纹的特征是大、长、直、深裂纹为折迭裂纹。所取样金相高倍观察发现:裂纹尖端较粗,尖端及裂纹两侧有较深的氧化铁层。经4%硝酸、酒精溶液腐蚀后观察高倍组织的结果为:(1)裂纹的两侧出现较厚的脱碳层;(2)在裂纹尖端的延长线上出现一条似铁素体为主的条带(暂定名为“鬼线”)。“鬼线”的铁素体圈正常组织细小且连续,可见铁素体晶界。6.3密集不规则型裂纹的形成原因对密集不规则型裂纹的分析结果表明此种裂纹横截面上的形貌极不规则。它们有的形态为折迭,但是裂纹处或末端折入的并非氧化铁皮,而是非金
21、属夹杂。裂纹处或附近常伴有大块夹杂物。其形成机理是20CrMnTi是多晶体金属,在外力作用下产生变形时,主要以滑移方式进行变形,其重要物点是各晶粒填充形状的相互制约性和相互协调性。若因某种原因使晶粒的充形不能相互协调或协调不好金属的变形抗力就大,有时塑性也变差。晶界、晶粒取向、杂质、第2相、晶粒的粗细等都影响晶粒充形的协调性。在多晶体中,当晶界的滑移面与作用力可能成45。时,这些晶粒成为软取向的晶粒。滑移面不与作用力呈45。的称为硬取向晶粒。在外力作用下软取向的晶粒可优先产生滑移变形。多晶体中不仅晶粒与晶粒间的变形程度不同,而且每个晶粒内部的变形也不相同。软三角取向晶粒的变形在晶界外便受压抑使
22、用使变形减小,硬取向晶粒受牵挂使变形增加。两者在晶界处变形必须保持一致。这样,在受压的软取向晶粒上受拉伸应力。与此对应,在压缩内力区产生压应力,拉伸应力区产生拉应力。这些应力和原来由外力引起的应力合起来便会在某区域集中更大的应力,变形越不协调应力集中越大。尤其是金属内含有杂质和第二相时,一方面杂质和第二相可阻碍滑移的进行;另一方面杂质偏聚的地方和硬的第二相会起到硬取向晶粒那样的作用,引起应力集中。夹杂物和第二相常集中在钢锭柱状晶彼此相遇(方形、矩形断面锭的等分角线外)以及柱状晶和等轴晶的交界处,这些地方最薄弱。带圆角的锭或圆锭柱状晶垂直周边排列,这时薄弱部位移到锭的中心部。由上述可知:由于20
23、CrMnTi轧材表面密集型裂纹处存在大块状夹杂物,故在晶界处产生微量元素和夹杂物的偏聚,使得某些元素(如S、P)在晶界的含量应高于钢中的平均含量。在高温轧制变形过程中晶体的滑移在晶界与夹杂物界面处受阻而产生应力集中及因多滑移时,滑移受相互穿插,造成晶界脆化和晶界的初始熔化。晶界的熔化温度低于晶内的熔化温度,且晶界强度低于晶内强度,所以在晶界处首先出现显微裂纹。这些显微裂纹因处于应力集中的晶界,如果它处的区域为拉应力区(如:加热产生的温度应力为拉应力的区域),则显微裂纹就会不断扩展,以致把无数小裂纹连接成宏观的表面裂纹。这类裂纹由于晶界的多方向性及夹杂物分布的多方向性,使得晶界显微裂纹方向不定,
24、从而致使这类轧材表面裂纺的宠观形貌无规律性。由此可见要降低该类表面裂纹,提高钢液沌洁度,降低夹杂物含量是有效手段之一。6.4发纹产生的机理探讨6.4.1钢坯加热时阴、阳面温差与发纹的关系钢坯在加热过程中(轧制前)产生的内应力,根据其形成的原因不同,有温度应力和组织应力。(1)温度应力:在钢坯加热过程中,当钢坯温度介于0至500550范围时,钢坯处于弹性状态,此时若钢坯出现温度梯度,则势必产生温度应力,如温度应力超过强度极限,便会造成钢坯破坏。当温度升高到500550以上时,由于进入塑性状态,而变形抗力又较低,通过塑性变形,温度应力也就消失。钢坯在轧制加热0至500550时,始终存在不同程度的阴
25、阳面温差,从而使得钢坯在加热时产生温度应力。其阳面温度高膨胀大,它的膨胀将受到阴面的约束,则引起的温度应力压应力(阳面);而阴面温度低,膨胀小,相反会受到阳面作用促做它膨胀,则产生的温度应力为拉应力(阴面),同理,钢坯加热时心部将产生拉就力。现以圆柱坯料为例说明其应力状况。(应力单位为N/mm2)圆柱坯表面的温度应力为:双向压应力状态。r=0,z=q=-EI-Y12(负号表示“压应力”)圆柱坯心部的温度应力为:三向拉应力状态。r=q=EI-Y14,z=EI-Y12=2r=2q其中:t坯料断面的最大温差/;线膨胀第数/mm/mm;E弹性模数/N/mm2;泊桑系数。钢坯加热时阳面轴向、切向受压应力
26、作用,阴面轴向、切向受拉应力作用。故阴面易产生裂纹,且裂纹暴露在空气中,裂口易氧化,在以后的加工中不能得以焊合而作为表面裂纹(发纹)保留在轧材上,这是造成轧材表单侧发纹的原因之一。组织应力:且有相变的钢在加工过程中,由于相变前后组织的比容发生变化,以及钢料的表层与心部不同时发生相变,这样引起的内应力为组织应力,总的规律是:增大比容的转变区受压应力,减少比容的转变区受拉应力。组织应力也是三项应力,但切向应力最大。20CrMnTi的室温组织是铁素体和珠光体。随着钢坯加热温度的升高,表层首先发生奥氏体转变。由于奥氏体的比容小于铁素体的比容,于是此时的组织应力为:表层为拉应力,心部是压应力。这正好与温
27、度应力方向相反,而使总的内应力降低。这时又因钢料处于较高温度下,使组织应力得以迅速松驰。随着温度继续升高,心部也进行奥氏体转变,此刻所引起的组织应力心部为拉应力,表层是压应力。虽与温度应力同向,使总的内应力增大,但这时温度很高,一般不会产生裂纹。总之,在钢坯加热过程中,组织应力没有危险性,温度应力(0至500 550范围内)才是加热时钢坯表面裂纹的致因。6.4.2轧材在冷却过程中的内应力与发纹的关系钢坯在加热过程中会产生内应力,同样,轧材在冷却过程中也会引起内应力。由于轧材冷却后期处于温度较低的弹性状态,因此冷却内应力危险性比加热内应力更大。按照冷却时内应力产生的原因不同,分为温度应力,组织应
28、力和残余应力。(1)温度应力:在轧材冷却初期,表层冷却快,体积收缩大;心部冷却慢,体积收缩小,由于表层的收缩受到心部阻碍。表层产生拉应力,心部引起压应力。这时可能产生表面裂纹,表面裂纹的特征是分布轧材的周身。随着继续冷却到后期,表层温很低,体积收缩停止,而心部体积收缩却受表层制约,结果使温度应力变为表层压应力,心部为拉应力,此刻易生产内裂。冷却的温度应力和加热温度应力一样,也是三向应力状态,最大是轴向应力。(2)组织应力:20CrMnTi轧材在冷却过程中因有相变发生,所以同样会产生组织应力。随着轧材温度的降低,表层先发生组织转变,由比容较小的奥氏体转变为比容较大的铁素体,这时所引起的组织应力是
29、:表层压应力、心部拉应力。但心部温度比较高,处于塑性良好的奥氏体状态,通过局部塑性变形,上述应力得到松驰。随着轧材继续冷却,心部也发生相变,这时生产的组织应力,心部是压应力,表层为拉应力。应力不断增大,直到相变结束为止。冷却组织应力也和加热组织应力一样是三向应力状态,且其中切向应力最大,这是引起表面纵向裂纹(沿轧制方向的发纹)的重要原因。(3)残余应力:轧材在轧制成形过程中,由于变形不均加工硬化所引起的内应力,如未能及时得到再结晶软化将其消除,轧后便成为残余应力保留下来。轧材在轧后冷却过程中,存在上述三种内应力,总的内应力为三都叠加,当叠加的应力值超过极限,便会在轧材相应部位引起裂纹。(若叠加
30、的应力在表面为拉应力,并应力值超过强度极限,则产生表面裂纹)。如果叠加的内应力没造成破坏,冷却终了便保留下来,作为轧材的残余应力。6.4.3钢坯截面尺寸与发纹的关系由实验4的结果,我们已经知道130mm130mm方坯、140mm140mm方坯、150mm150mm方坯轧材的表面裂纹发生机率是不同的,三者发生严重裂纹的机率也是不一样的。这是由于三种方坯在轧制时所能过的孔型是同一套孔型系统,但三者的变形情况不同。以130mm130mm方坯和150mm150mm方坯为例,说明变化。分析如下:500mm轧机前四道次孔型图(略)轧制时的咬入角:cos= 1-h/D轧制时的咬入角:cos= 1-h/Dg则
31、=arccos(1-h/Dg)宽展系数:=(0.575Dg(/2)/H(1-2(/2)(当用钢轧辊时)其中:咬入角(度);h压下量/mmDg轧辊工作直径/mmH轧件轧前高度/mm(1)轧制130坯前四道次的变形情况第一道次:空过,无变形第二道次:压下量h =30(mm),轧辊工作直径Dg= 400mm则咬入角为:= 22.33。,H= 130mm宽展系数:= 0.2099宽展量:b =h= 0.209930 = 6.297(mm)即经过第二道次轧制后,130mm130mm坯截面尺寸变为:136.297100/mm2)第三道次:从孔型图上尺寸和第二道次轧制后坯料的截面尺寸可知,本道次也是空过,无
32、变形。第四道次:轧件轧前高度H=136.297mm,压下量h= 136.297-108 = 28.297(mm)轧辊工作直径Dg= 392mm那么咬入角是:= 21.90。宽展系数:= 0.1948宽展量:b=h= 5.5123(mm)此时坯料宽度应是105.5123(mm) 104(mm)所以坯料的宽展要受到一定的限制,不会象前面道次那样自由宽展。150mm150mm坯和130mm130mm坯在该道次轧制后的截面尺寸应基本相同,轧后的变形情况也相近。轧制150mm150mm坯前四道次的变形情况第一道次,轧件轧前高度H=150mm,压下量h =150-130=20(mm)轧辊工作直径Dg= 5
33、00-130 = 370(mm)则咬入角为:=18.92(度)宽展系数:=0.1565宽展量:b=h= 3.13(mm)即:第一道次轧制后坯料截面尺寸是153.13mm2第二道次:H=130.00mm压下量h= 30mm轧辊工作直径Dg= 500-100 = 400(mm)则咬入角为:=22.33。宽展系数:=0.2099宽展量:b=6.297与130mm130mm坯同此时,坯料截面尺寸是:宽度B = 159.427mm高度= 130mm第三道次(翻钢)H=159.427mmh=159.427-137 = 22.427mmDg= 500-137 = 363(mm)则咬入角为:= 20.24。宽
34、展系数:= 0.1492宽展量:b= 3.346mm在第三道次轧制后,坯料的宽度应是103.346mm100mm,但由于要受到孔型的限制,坯料不能自由宽展。第四道次:H= 137mm压下量h= 29mm轧辊工作直径Dg= 500-108 = 392(mm)则咬入角为:= 22.18。宽展系数:=0.1947宽展量:b=5.649 此时,如第三道次宽展不限制的话,坯料宽度是B=108.9929mm从以上的计算可以看出:150mm150 mm方坯的情况与130mm130mm方坯的不同,主要是在第一道次和第三道次。130mm130mm坯在这两道次是空过无变形,而150mm150mm坯在这两道次的压下
35、量都比较大。特别是第三道次150mm150mm方坯是限制宽展。方坯在箱型孔型中轧制时,由于受到侧壁一定量的限制宽展,轧件在上下被压,向前延伸的变形过程中,表面将收缩而产生皱纹,再经以后各道次的变形成材,从而造成轧材表面有发纹,这种情形产生的发纹,在轧材上就是两面对称型发纹。如果压下量越大,限制宽展的程度越大,则发纹越严重。这是是150mm150 mm坯轧材发纹比130mm130mm坯轧材发纹多的一个主要原因。加外由于150mm150 mm坯截面尺寸大于130mm130 mm坯,在加热时,150mm150 mm坯的温度梯度也就比130mm130 mm坯大,温度应力所造成的应力发纹也多一些。这是1
36、50mm150 mm坯轧材表面质量次于130mm130 mm坯轧材的原因之二。实际生产中,考虑到部份发纹通过后部精整工序轻微清理可以消除,而严重的裂纹只有报废,为追求经济效益,因此往往需在质量和成本中寻找一个平衡点,经测算和实践证明本孔型系统用145mm145 mm方坯在保证质量的前提下是最经济的。计算和实验方法与上述相同,这里不再述。6.4.4钢坯加热时表面氧化铁皮与发纹的关系钢坯在加热到高温时,表层中的铁和炉气中的氧化性气体(如O2、CO2、H2O、SO2等)发生化学反应,结果使钢坯表层变成氧化铁(即氧化皮)。轧制时,由于第一、二道次(未翻钢)钢坯上表面的氧化铁皮脱落后仍留在坯上表面而被压
37、入,第三道次翻钢轧制后氧化铁皮掉下造成表面凹坑或麻点,在成品道次被拉长面形成发纹,此情况下,所产生的发纹应是分布于轧材的单侧。7结论(1) 20CrMnTi表面裂纹按宏观形貌分,主要是:直短宽型裂纹、直长型裂纹及不规则型裂纹和发纹。(2)直短宽型裂纹大部分实质上皮下汽泡裂纹;直长型裂纹大部分是轧制裂纹,其中直长深型裂纹实质折迭裂纹、直长浅型大部分为拉丝裂纹,不规则裂纹多为夹杂裂纹。(3)夹杂裂纹的内因是皮下夹杂。一般来源于残留在钢液中的内在夹杂和凝固富集反应形成的大颗粒夹杂以及炉渣、耐火材料等。(4)发纹的形成原因主要有:钢坯加热时因温度应力(阴、阳面温差带来)形成的发纹、轧材冷却时时温度应力
38、和组织应力所产生的发纹、钢坯轧制时压量和限制宽展所形成的发纹以及钢坯氧化铁皮所造成的发纹。(5)合理的孔型或选择合适的坯料尺寸,也能减少表面裂纹发生机率。(6)要有效地减少20CrMnTi表面裂纹、除必须保证冶炼和浇注、坯料的质量外,还必须保持加热、轧制的质量。致谢:在撰写及试验研究过程中得到了西安建筑科技大学、济南大学、重庆大学、钢铁研究总院、重庆钢专、二汽、长钢技术中心、长钢技术部、长钢质计部领导、校友、同事、朋友的大力帮助,特此表示感谢!参考方献1李代钟.钢中的非金属平杂物M.北京:科学出版社,19832 曲英.炼钢学原理M.北京:冶金工业出版社,19803张志文.锻造工艺学M.北京:机械工业出版社,19834王延溥.轧钢工艺学M.北京:冶金工业出版社,19815北京钢铁学院.金属塑性变形与轧制原理M.北京:北京钢铁学院出版社,198118
- 温馨提示:
1: 本站所有资源如无特殊说明,都需要本地电脑安装OFFICE2007和PDF阅读器。图纸软件为CAD,CAXA,PROE,UG,SolidWorks等.压缩文件请下载最新的WinRAR软件解压。
2: 本站的文档不包含任何第三方提供的附件图纸等,如果需要附件,请联系上传者。文件的所有权益归上传用户所有。
3.本站RAR压缩包中若带图纸,网页内容里面会有图纸预览,若没有图纸预览就没有图纸。
4. 未经权益所有人同意不得将文件中的内容挪作商业或盈利用途。
5. 装配图网仅提供信息存储空间,仅对用户上传内容的表现方式做保护处理,对用户上传分享的文档内容本身不做任何修改或编辑,并不能对任何下载内容负责。
6. 下载文件中如有侵权或不适当内容,请与我们联系,我们立即纠正。
7. 本站不保证下载资源的准确性、安全性和完整性, 同时也不承担用户因使用这些下载资源对自己和他人造成任何形式的伤害或损失。
最新文档
- 人教版初中生物第1章第1节生物的特征课件
- 人教版初中生物中考复习第三单元第三章绿色植物与课件_002
- 信道编码10-15上课课件
- 缺血性脑卒中--从急性期到二级预防课件
- 信道定义及数学模型课件
- 线虫概论蛔虫鞭虫课件
- 组织学与胚胎学-07神经组织课件
- 人教版初中物理新旧教材对比资料课件
- 组织学与胚胎学-09Th 皮肤课件
- 人教版初中生物七年级上册-开花和结果课件
- 人教版初中生物七上第一单元第一章第1节《生物的特征》-课件
- 人教版初中生物七上第一单元第二章第1节《生物与环境的关系》-课件
- 癌痛的护理(专科护士培训)图文课件
- 组织学与胚胎学-08神经系统课件
- 人教版初中生物中考复习第三单元第三章绿色植物与1课件