陶瓷微裂纹检测方法
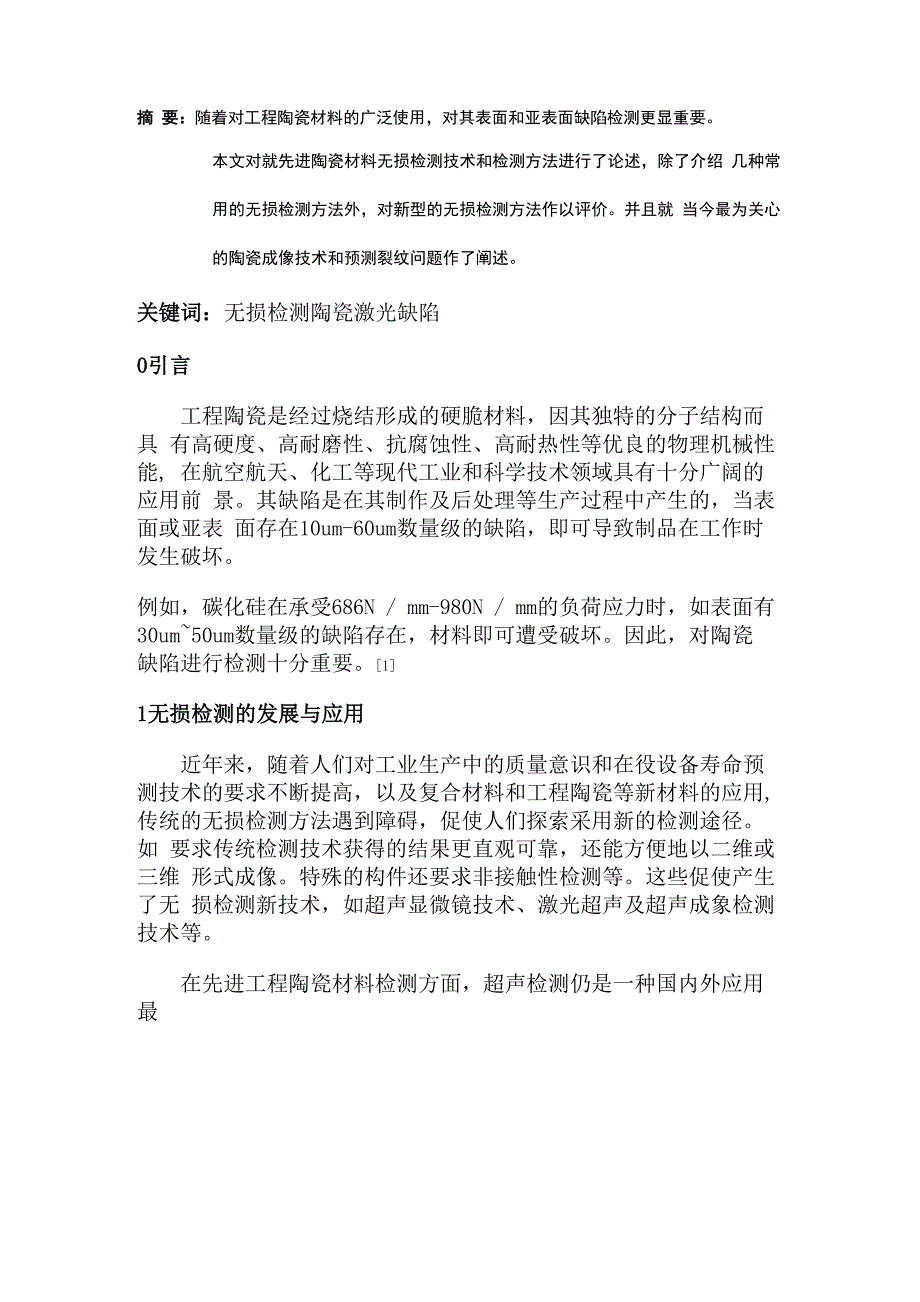


《陶瓷微裂纹检测方法》由会员分享,可在线阅读,更多相关《陶瓷微裂纹检测方法(14页珍藏版)》请在装配图网上搜索。
1、摘 要:随着对工程陶瓷材料的广泛使用,对其表面和亚表面缺陷检测更显重要。本文对就先进陶瓷材料无损检测技术和检测方法进行了论述,除了介绍 几种常用的无损检测方法外,对新型的无损检测方法作以评价。并且就 当今最为关心的陶瓷成像技术和预测裂纹问题作了阐述。关键词:无损检测陶瓷激光缺陷0引言工程陶瓷是经过烧结形成的硬脆材料,因其独特的分子结构而具 有高硬度、高耐磨性、抗腐蚀性、高耐热性等优良的物理机械性能, 在航空航天、化工等现代工业和科学技术领域具有十分广阔的应用前 景。其缺陷是在其制作及后处理等生产过程中产生的,当表面或亚表 面存在10um-60um数量级的缺陷,即可导致制品在工作时发生破坏。例如
2、,碳化硅在承受686N / mm-980N / mm的负荷应力时,如表面有 30um50um数量级的缺陷存在,材料即可遭受破坏。因此,对陶瓷 缺陷进行检测十分重要。11无损检测的发展与应用近年来,随着人们对工业生产中的质量意识和在役设备寿命预 测技术的要求不断提高,以及复合材料和工程陶瓷等新材料的应用, 传统的无损检测方法遇到障碍,促使人们探索采用新的检测途径。如 要求传统检测技术获得的结果更直观可靠,还能方便地以二维或三维 形式成像。特殊的构件还要求非接触性检测等。这些促使产生了无 损检测新技术,如超声显微镜技术、激光超声及超声成象检测技术等。在先进工程陶瓷材料检测方面,超声检测仍是一种国内
3、外应用最广泛、发展较快的无损检测技术。其发展经历了超声波无损探伤 (NDI)、超声波无损检测(NDT)、和超声无损评价(NDE)三个阶段。在 国外,工业发达国家的无损检测技术已逐步从NDI和NDT向NDE过渡。 现在无损检测的发展是从一般无损评价向自动无损评价和定量无损 评价发展(即从NDE向ANDE和QNDE发展)。采用计算机进行检测 和分析数据,这将减少人为因素的影响,提高检测的可靠性。目前,国外采用人工智能、激光等技术与无损检测技术有机结合 以实现复杂形面复合构件的超声扫描成像检测,将现代数字信号处理 与人工神经网络技术用于超声检测。超声与断裂力学知识相结合,对 材料构件的强度与剩余寿命
4、进行评估等方面很有发展前景。 2先进工程陶瓷材料的无损检测技术21陶瓷材料无损检测的具体目标陶瓷材料无损检测的具体目标是检出对性能不利的裂纹、气孔、 结块、夹杂等缺陷。它的难度在于需要检测的缺陷极其微小,一般比 金属或复合材料小l 一2个数量级。典型的结构陶瓷,为防止材料快 速破坏,需检出6o 600um的缺陷;对于缓慢裂纹生长需预测寿命的, 要检出20200um的缺陷;为提高韧性而控制材料组织,必须检出10 一50um的缺陷;为对精密部件控制制造工艺,则需检出1 一30um的 缺陷。有些学者认为细晶陶瓷(如热压氮化硅)的临界尺寸小至25um 以下;而粗晶陶瓷(如反应烧结氮化硅)要高一些,可以
5、是501O0um。基金项目:国家自然科学基金资助项目(50475114);天津市科技发展计划项目支持作者简介:程应科(1974-),男,硕士,研究方向为机械制造及自 动化。近年来,用于陶瓷无损检测的方法有:表面浸透检测(荧光法、 着色法),x射线层析成像、红外热成像、超声A扫描及c扫描、声 发射、微焦点x射线、超声显微镜等。其中最常用的方法是超声检测。23超声检测原理和应用超声检测原理是当超声波进入物体遇到缺陷时,一部分声波会产 生反射,发射和接收器可对反射波进行分析,就能异常精确地测出缺 陷来。使用它可以显示内部缺陷的位置和大小,测定材料厚度等,可 判别密度差异、弹性模量、厚度等特性和几何形
6、状的变化方面。超声检测主要是应用超声波的声速和衰减这2个参量来获得有关 材料微观组织和力学性能的信息。声速可用于测定厚度、裂纹位置和 体积、残留应力(应变)。超声波衰减测量则可极其灵敏地指示出因材 料微观组织的变化而引起内部损耗。为了检出现代陶瓷中的微小缺 陷,常用水浸探伤法和聚焦型探头。缺陷的检出能力与所用超声波频 率有关。频率越高,波束越细,缺陷检出能力就越强。但频率越高, 超声波的衰减也越严重。根据散射理论,超声波有可能检出尺寸为波长1. 8%的缺陷。 Reynolds等证明25MHz聚焦探头能发现碳化硅陶瓷中直径为100um的 空穴,而此时超声波的波长约400um。这些暗示了较低频率超
7、声渡检 测陶瓷的可行性。黎润民等用对氮化硅陶瓷进行了检测,检出了距表 面7mm的D0. 05mm的钨丝。在陶瓷气孔率的检测中,Kuner th等使用了直探头和聚焦探头(超 声波频率为100MHz,波长约为120um),研究了碳化硅陶瓷中微米数量 级直径的气孔对常规纵波的背散射。结论是单个气孔的散射通常极 小,并不能检测到.但可检测到群气孔的散射。高频超声因有的大的 衰碱和设备的昂贵,所以低频超声检测陶瓷倍受关注.Nagara和Panakkal等发现氧化锆陶瓷中声速和气孔率(或密度) 是线性关系。Klima发现在氮化硅和碳化硅陶瓷中,声速和密度呈线 性关系,微观组织如晶粒尺寸、晶粒形状、空穴尺寸
8、及分布对声速影 响很小.然而对高频超声波衰减的影响却很大.因此测量衰减更能有 效地评价材料的微观组织和力学性能。Roth等用半经验模型解释了 多晶材料中声速和气孔率的经验线性关系,推测材料的晶粒尺寸、密 度、气孔率等组织特征和力学性能。在陶瓷及陶瓷基复合材料微缺陷的超声检测中,通过人工缺陷试 样的试验得出,泄漏瑞利波法比纵波垂直入射法,对孔型及槽型人工 缺陷均具有更好的检测灵敏度,在层状结构陶瓷基复合材料中可检出 直径115um的人工孔;在陶瓷材料中,可检出直径为53um的人工孔 和宽度为43um的人工槽。目前,采用智能、激光等技术与无损检 测技术有机结合以实现复杂形面复合构件的超声扫描成像检
9、测,是近 年来国外复合材料构件无损检测领域研究的前沿课题。183几种新型的无损检测技术在陶瓷材料的无损检测中,激光超声、扫描声显微镜、扫描激光声显微镜(SLAM)及相关成像等新技术得到了长足的发展。31激光超声检测技术及其应用激光激发超声波原理和提高激发的超声信号强度参见文献。加 与传统的压电换能器技术相比,激光超声最主要的优点是非接触检 测,它消除了压电换能器技术中的耦合剂的影响,可用于各种较复杂 形貌试样的特性检测。它能以光波波长为测量标准而精确测量超声位 移.如激光扫描式超声显微镜法,对内部缺陷也有很强的检出能力, 一般可检出尺寸在10um以上的气孔缺陷。由于极短的激光脉冲可以激发出极短
10、的超声脉冲,通过对衍射超 声波渡越时间差的分析,可以准确地确定各种缺陷、包括各种体缺陷 和表面缺陷的位置,其精度可优于0.1mm。如美国斯坦福大学、加 拿大的QeenS大学等将LGAP与光探针相结合,很容易地探测到亚表 面的缺陷,实现高精度无损检测。在洛克希德马丁公司的激光超 声检验技术中心的检验系统中,激光束可以从与轴线成45度角入射而 在形状复杂构件中产生超声,而传统的水浸系统,入射角必须保持在 3度内才能产生超声。激光超声微裂纹检测技术的发展,该技术不仅适用于对铝、陶瓷 和钢在高温下的材料特性测定和快速运动等需非接触检测的工件,而 且为微结构和微小零件的理论分析提供有力的手段,特别是对于
11、物质 表面和亚表面的物理化学特性的研究起到了推动作用。国内同济大学 的钱梦騄等首先将激光超声技术应用到对纳米材料的分析上,得出了声速与制备纳米材料时的压力、温度的关系;可对纳米陶瓷的声速 及相应的杨氏模量进行测定;可以方便地评估弯曲表面试件的应力状 态等。但是,激光超声的不足是检测系统庞大以及检测环境要求较高 (要隔振等)。32超声波显微成像技术在陶瓷材料检测中的应用在现代无损检测技术中,超声成象技术是一种令人瞩目的新技 术。它具有检测一致性,可靠性、复现性高,检测结果自动比较,对 缺陷做动态检测等优点。目前已经使用和正在开发的成像技术包括B,C,D扫描成像、超声显微术、P扫描成像、ALOK超
12、声成像技术、合 成孔径聚焦技术SAFI、超声全息成像、超声CT成像等技术。成像分 析中采用了数字信号处理的最新技术,包括时间渡越衍射技术、倒谱 分析与相关分析等。几种常见的扫描超声成像系统包括用户除使用信 号处理算法或图像显示外,有时须借助于专家系统等技术的支持。3321超声成像无损检测系统以电器开关检测的专用设备为例。超声成像无损检测系统超声成 像无损检测系统如下图。采用水浸超声C扫描成像原理是以水为耦合 剂,应用水浸点聚焦探头,使发射的超声波束垂直于试样的被测面, 并聚焦于被测面,对试样进行逐点逐行扫描,同时将每一点反射回波 的模拟信号转换成数字信号,并保存及进行信号处理,最后将信号对 应
13、地显示在计算机屏幕上,显示成二维伪彩色的图像。其原理如图1 所示,其中图1(a)表示C扫描路径,图1(b)表示C扫描时试样探头和 精密扫查器的相对位置。(a)C扫描路径(b)C扫描时探头和扫查器的位置图1水浸超声C扫描成像无损检测系统示意图图2计算机辅助的超声波显微镜对陶瓷垫片的检查通过对大量开关电器电触头的检测,将后处理的试样用扫描仪扫 描成像,与本系统超声C扫描图像对比,结果表明,本系统缺陷检测 结果与实际缺陷界面基本一致。图2是利用计算机辅助的超声波显微镜对3个碳化硅垫片的检查 情况。扫描形成的图象具有高放大率和高分辨率。可以由法向入射的 声波束或者从不同的角度或者相对表面不同的方向的声
14、波束成象。这 样便于分析加载或机械加工对材料的影响。可以明显看出,图中左边 和中间两图反映无磨损垫片的情况。右图表示垫片具有磨损,因而有 一定量的反向散射回声,可以看出,图象明显不同于无磨损垫片的。12322陶瓷的超声c扫描由计算机辅助的超声波显微镜(C型扫描)适用于表面的检测、或 者因机械加工或处理损坏的陶瓷材料表面的检查、薄的试件和较厚试 件限定区的容量检查。在对工程陶瓷材料的内部缺陷的检测中,传统的工程陶瓷的内部 缺陷大多采用水浸探伤法,以水浸纵波垂直探伤法检测缺陷时,波束 路程可以直接读出。为检出微小缺陷而采用高频率探头时,因超声波 衰减大,往往检不出缺陷,这时改用较低频率的探头反而可
15、以检出缺 陷,最低频率的范围为20kHz2o0kHz。当采用水浸斜角探头而使用 横波时,其声速比纵波声速小,以此提高探伤的分辨能力。多晶片散 射波法是检测工程陶瓷内部缺陷的有效方法。如图5所示,在探头内 的透声楔周边排列多个晶片,使纵波垂直地射到被检工件上,以斜角 接收反射波时,由散射波的图像,利用反波恩(InveresBorn)近似, 可推定缺陷尺寸。以椭圆体缺陷为例,如果使接收晶片的数目N=25 左右,可以较高的精度推定X、Y、z轴方向的缺陷尺寸。如表1所示。16现在使用C扫描法能方便地检测工程陶瓷内部缺陷的位置、大小 和分布状态。用25MHz的探头对常压烧结的氮化硅进行C扫描,可发 现表
16、面下2mm深处10um75um的线状缺陷。以15MHz的探头对氮化硅 进行C扫描,可以检出30um的气孔。以30MHz的聚焦型超声波对氧 化锆进行C扫描,可清晰地检出尺寸在20um以上的所有气孔。实验参数半轴占(um)NeO%25394010150172627119549262812353619012256真值479747图5多晶片散射波法表1椭圆缺陷尺寸的推定精度相比常规的超声波检测方法,超声波显微照相术可以提供较高的 横向和深度方向的分辨度,可实现非常小的不连续点的检测,精确地 定位,对细小裂纹可形成逼真的图象,提高了实验数据的可靠性。但 这受到讯号衰减、被检零件的深度、穿透度等因素影响。
17、目前,c扫 描的发展方向是提高检测范围、能力和分辨率。超声C扫描成像可分为常规和显微成像c扫描两种。1、C扫描能够检测试样中的气孔、裂纹、夹杂和孔隙率等,特 别是可以清晰地显示出所有的夹杂物,包括对x射线不敏感的非铁夹 杂物,可根据成像图形测定缺陷的大小。C扫描成像的分辨率较高, 用10MHz对氮化硅陶瓷进行检测,可以检出直径30mm的气孔。常规c扫描:常规c扫描工作频率较低,一般在10MHz以下, 也有用到50MHz的高频。Frlant等用常规c扫描进行了碳化硅纤维强 化的玻璃陶瓷复合材料的检测,发现c扫描中透过的超声波能量和材 料的动态弹性模量有定量关系。常规扫描受到陶瓷材料气孔率的限 制
18、。陶瓷检测中一般使用高频来检测小缺陷,但同时也使来自气孔的 散射大大增强。Borwer研究了气孔率对c扫描成像的影响,同时对 比了 x射线、c扫描、SLAM技术在陶瓷检测中各自的优势。2、显微成像c扫描(如SAM)比常规c扫描应用更为广泛,它的 工作频率可达20200MHZ,此时对表面及亚表面的检测分辨率可达l 一2um。Nonaka等用100MHz的探头检测出了预埋在碳化硅陶瓷中的直 径为10200um的钨丝,钨丝距上表面1. 5mm。此时,由于高频导致 的大衰减,仪器的增益需要很大,但需要图像处理技术来增强图象。 Stelwagen等用使用的是10100MHz的低频SAM技术,检出了氧化铝
19、 陶瓷中500um深处直径为130um的体积型缺陷和10 15um宽的表面 裂纹以及400um的氧化锆涂层的分层缺陷。SAM的主要特点有:横向分辨率高,纵向分辨率低,适于测量 与声束垂直的面状缺陷;可测曲面样品;对表面耦合状况很是敏感, 对表面光洁程度要求较高;水中声速和陶瓷中声速的差异使焦点变形 大。323激光扫描显微成像技术目前,在上述用于先进陶瓷的检测方法中,激光扫描显微成像(SLAM)法在缺陷检出能力、现场实用性及容易实现自动化等方面都有着明显的优势。在先进陶瓷材料表面缺陷的检测中,同一形状和尺寸的表面缺陷比 内部缺陷更容易引起破坏,因此表面缺陷的检测特别重要。传统的水 浸表面波法检测
20、表面缺陷实验证明,采用水浸表面波法用15MHz水浸 探头对表面有激光加工伤痕的氮化硅进行探伤时,最低可以检测到缺 陷直径是65um。用此法对含有人工缺陷的氧化铝试块进行水浸表面波 法探伤时,可以全检出直径40um、深50um以上的人工缺陷。另外, 根据表面波的分辨率高于横波和纵波的关系,使用12MHz的表面波, 采用液浸法,检出了位于表面以下1 2mm处、大小为40um的缺陷。 Reynolds用25MHz和50MHz表面波探测表面开口裂纹,发现表面波探 动时,表面光洁度对探伤影响很大,似乎和最佳频率有关。但没有找 到光洁度和最佳探伤频率的关系。梳形电极探头法是一种直接接触表面波法,用贴有梳形
21、电极的铌 酸锂探头和100Hz的高频对氮化硅制造的涡轮叶片探伤,可检查出深 度为50um2o0um的裂纹。而超声显微镜法采用的是100MHz,1GHz的 高频超声波,其分辨能力高,可正确把握缺陷的形状。当采用00MHz 时,可检出氮化硅表面深度为20um的凹痕。激光扫描式超声显微镜 法是透过试样的超声波在试样表面形成动态脉动图样时,以激光将其 检出的方法,对表面线状缺陷的检出能力很强,宽20um、深10um的 微裂纹亦能检出。15目前,关于找到限制会造成裂纹的缺陷和在断裂试验前预测裂纹 的报道很少。Sun, J.G.等人使用激光扫描技术检测装置对氮化硅表 面和亚表面的缺陷和机加工损伤的检测提供
22、了二维的数字图象。提出 了高的去除率和粗的研磨会形成激光散射下粗糙的表面,并且机械损 伤更加严重。在对试件进行不同深度的研磨和测量后,表明在激光所 描述的缺陷特征和显微镜下观察的表面/亚表面的固有缺陷有关。这 为描叙裂纹作了基础。gJ.M.Zhang等使用基于激光扫描的NDZ装置, 在断裂实验前分析了 8个长拄状氮化硅试件表面。如图3为激光扫描系 统图。TransrbEn anJF 忤汹 MulljplitfTLje-图3激光扫描系统图图4表明了试件在显微相片和激光扫描图象下,试件2裂纹形成之间的区别。使用激光扫描图象检验了断裂实验前裂纹起因。结合激光 扫射技术和断裂实验可得到以下实验结果:裂
23、纹的产生通常是固有缺 陷,但有时机加工也是形成的原因之一。裂纹产生于最大尺寸的缺陷 和激光扫描图象中缺陷密度最大的地方。这项研究表明激光扫描技术 可以在断裂实验前预测裂纹的起因,具有十分广阔的前景。14图4 (a)显微镜下断裂区域 图4 (b)激光扫描下断裂图像图4 (c) 激光扫描下断裂起因SLAM (扫描激光声显微镜)技术主要应用于航空、航天构件重要部位 陶瓷材料检测。它不仅对面型、体积缺陷有很好的检测能力,而且对 内部裂纹及表面空穴的检测也有较好的效果。但是构件的表面状况对 检测可靠性有的影响很大。5总结与展望。综上可知,有效分析陶瓷材料表面/亚表面结构的缺陷的方法中, AE声发射检测其
24、不足是须解决由于裂纹小信号也变小,环境和检测 器的噪音问题,在一定试验条件下材料与构件可能由于的损伤产生声 发射5。常规的低频超声波系统(510MHz)或具有1. 5mm焦点的常规 x射线系统,虽都能对材料表面及其表面下的结构进行检测,但是一 般分辨率不高。微焦点X射线法,它可检测小至10um的裂纹,但裂 纹的方位应与x射线束方向一致。超声波显微照成像可提供表面或表 面以下两处裂纹的图象。当频率为50MHz时,其空间分辨率可达25um。 其分辨能力介于常规的和微聚焦x射线法之间。但是它可以准确地确 定诸如薄层裂纹或龟裂。这是x射线法难以实现的。但是激光超声由于技术发展存在不足之处。如对同一缺陷
25、,用超 声波水浸C扫描成像图和激光超声检测技术给出的CT成像图进行比 较,超声波显微照相术对裂纹检测的可靠性较高。在一个或两个缺陷 的成像中,在相应的衰减度阈值选择比较合适的情况下,它们重合的 相当好,但CT成像缺陷部位的边沿轮廓不是很圆。另外,怎样更有 效地提高激发的超声信号强度,解决检测系统隔振等是需要亟待解决 的问题。19 20目前,以激光超声表面波为代表的用于微小缺陷检测的光技术的 研究,成为超声工程和无损检测领域的一个重要内容。国内外在积极 研究增强陶瓷材料韧性的方法的同时,已把开发陶瓷材料寿命预估方 法和新构检测方法列为首要课题。通过研究和预测微裂纹的扩展规 律,可以极大地推动机械疲劳设计理论和安全系数法设计理论的发 展,其发展和应用前景十分乐观。
- 温馨提示:
1: 本站所有资源如无特殊说明,都需要本地电脑安装OFFICE2007和PDF阅读器。图纸软件为CAD,CAXA,PROE,UG,SolidWorks等.压缩文件请下载最新的WinRAR软件解压。
2: 本站的文档不包含任何第三方提供的附件图纸等,如果需要附件,请联系上传者。文件的所有权益归上传用户所有。
3.本站RAR压缩包中若带图纸,网页内容里面会有图纸预览,若没有图纸预览就没有图纸。
4. 未经权益所有人同意不得将文件中的内容挪作商业或盈利用途。
5. 装配图网仅提供信息存储空间,仅对用户上传内容的表现方式做保护处理,对用户上传分享的文档内容本身不做任何修改或编辑,并不能对任何下载内容负责。
6. 下载文件中如有侵权或不适当内容,请与我们联系,我们立即纠正。
7. 本站不保证下载资源的准确性、安全性和完整性, 同时也不承担用户因使用这些下载资源对自己和他人造成任何形式的伤害或损失。