(精品)炼油工艺流程
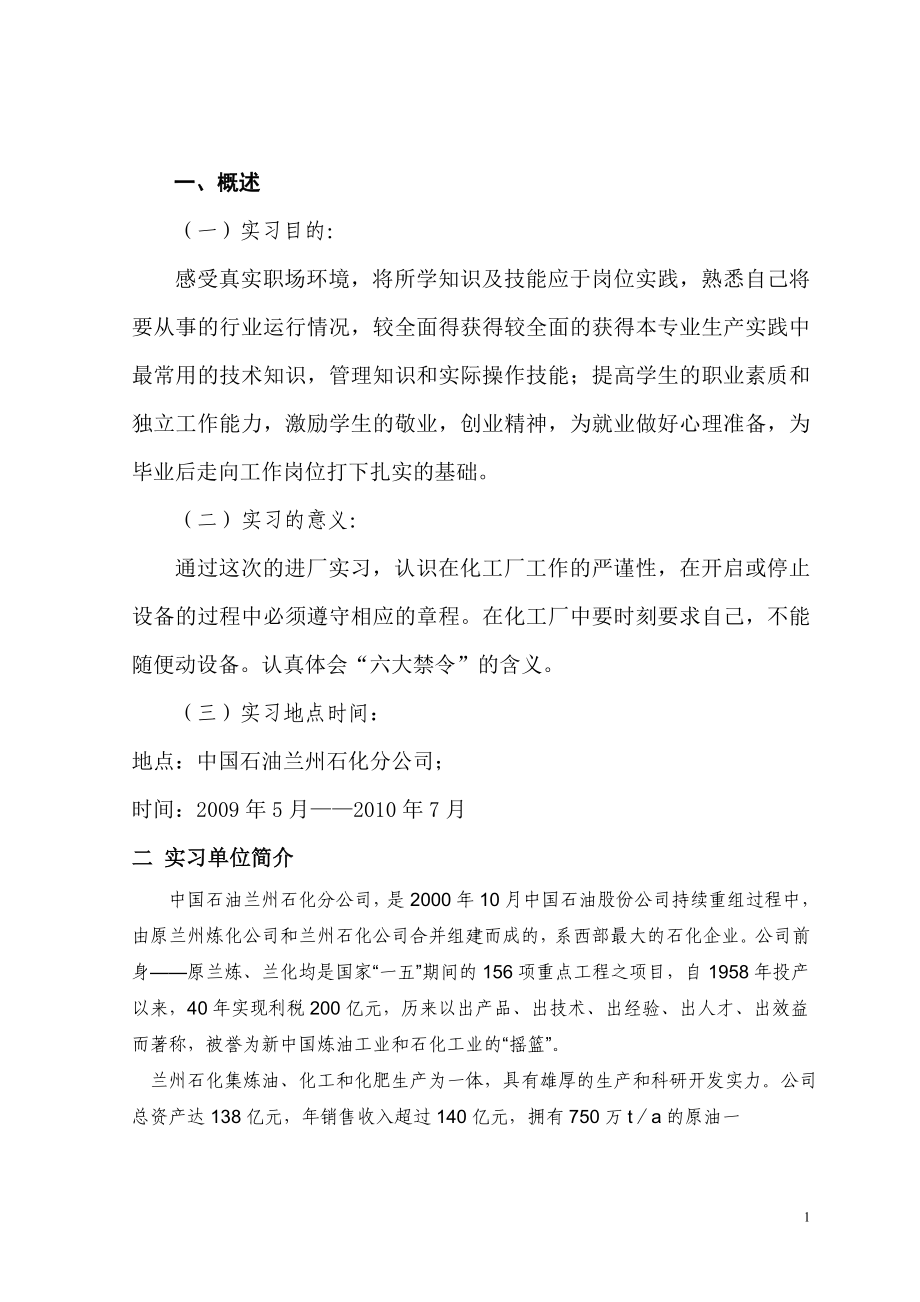


《(精品)炼油工艺流程》由会员分享,可在线阅读,更多相关《(精品)炼油工艺流程(39页珍藏版)》请在装配图网上搜索。
1、一、概述(一)实习目的:感受真实职场环境,将所学知识及技能应于岗位实践,熟悉自己将要从事的行业运行情况,较全面得获得较全面的获得本专业生产实践中最常用的技术知识,管理知识和实际操作技能;提高学生的职业素质和独立工作能力,激励学生的敬业,创业精神,为就业做好心理准备,为毕业后走向工作岗位打下扎实的基础。(二) 实习的意义:通过这次的进厂实习,认识在化工厂工作的严谨性,在开启或停止设备的过程中必须遵守相应的章程。在化工厂中要时刻要求自己,不能随便动设备。认真体会“六大禁令”的含义。(三)实习地点时间:地点:中国石油兰州石化分公司;时间:2009年5月2010年7月二 实习单位简介中国石油兰州石化分
2、公司,是2000年10月中国石油股份公司持续重组过程中,由原兰州炼化公司和兰州石化公司合并组建而成的,系西部最大的石化企业。公司前身原兰炼、兰化均是国家“一五”期间的156项重点工程之项目,自1958年投产以来,40年实现利税200亿元,历来以出产品、出技术、出经验、出人才、出效益而著称,被誉为新中国炼油工业和石化工业的“摇篮”。 兰州石化集炼油、化工和化肥生产为一体,具有雄厚的生产和科研开发实力。公司总资产达138亿元,年销售收入超过140亿元,拥有750万ta的原油一 次加工能力,并具备相配套的二次加工能力,能生产汽煤柴润等多种类油品、合成树脂、合成橡胶、合成纤维、化肥以及催化裂化催化剂、
3、石油添加剂等400余种石化产品,有多种产品荣获国家金银质奖,在国内外市场享有良好的声誉。 国家西部大开发战略的实施,给兰州石化带来了新的发展机遇。由于兰州独特的地理位置,公司成为上游新疆等大型油田原油出路畅通的重要保障,又是西北地区成品油和化工产品的最大生产商,也是成品油进入川渝、拓展西南地区市场的重要基地。因此,中国石油股份公司确定在兰州建设世界级石化基地的战略构想,把兰州石化作为四大炼油和四大化工生产基地之一进行规划建设。 未来发展中,兰州石化炼油能力将达到1200万ta,乙烯生产能力达到100万ta,同时配套建设大型芳烃及其后加工等化工生产装置,炼油和化工主体工艺技术、装备和控制手段、产
4、品质量、环保和主要经济技术指标将达到国内外先进水平。公司正在全力实施业务发展规划,加快建成千万吨级炼油和化工生产基地,推动西部地区的经济建设,决心为中国石油的价值提升和国家的经济建设作出更大的贡献。 中国石油兰州石化分公司,是2000年10月中国石油股份公司持续重组过程中,由原兰州炼化公司和兰州石化公司合并组建而成的,系西部最大的石化企业。公司前身原兰炼、兰化均是国家“一五”期间的156项重点工程之项目,自1958年投产以来,40年实现利税200亿元,历来以出产品、出技术、出经验、出人才、出效益而著称,被誉为新中国炼油工业和石化工业的“摇篮”。 兰州石化集炼油、化工和化肥生产为一体,具有雄厚的
5、生产和科研开发实力。公司总资产达138亿元,年销售收入超过140亿元,拥有750万ta的原油一次加工能力,并具备相配套的二次加工能力,能生产汽煤柴润等多种类油品、合成树脂、合成橡胶、合成纤维、化肥以及催化裂化催化剂、石油添加剂等400余种石化产品,有多种产品荣获国家金银质奖,在国内外市场享有良好的声誉。 国家西部大开发战略的实施,给兰州石化带来了新的发展机遇。由于兰州独特的地理位置,公司成为上游新疆等大型油田原油出路畅通的重要保障,又是西北地区成品油和化工产品的最大生产商,也是成品油进入川渝、拓展西南地区市场的重要基地。因此,中国石油股份公司确定在兰州建设世界级石化基地的战略构想,把兰州石化作
6、为四大炼油和四大化工生产基地之一进行规划建设。 未来发展中,兰州石化炼油能力将达到1200万ta,乙烯生产能力达到100万ta,同时配套建设大型芳烃及其后加工等化工生产装置,炼油和化工主体工艺技术、装备和控制手段、产品质量、环保和主要经济技术指标将达到国内外先进水平。公司正在全力实施业务发展规划,加快建成千万吨级炼油和化工生产基地,推动西部地区的经济建设,决心为中国石油的价值提升和国家的经济建设作出更大的贡献。三 具体实习单位(炼油厂)简介 兰州石化公司炼油厂是个有着40多年历史的老企业,拥有常减压、重油催化、连续重整芳烃抽提、润滑油加氢处理、柴油加氢、溶剂脱蜡、润滑油补充精制等多种加工手段,
7、近年来,炼油厂相继新建投产了年500万吨常减压蒸馏、年300万吨重油催化裂化、年120万吨延迟焦化等6套新装置,完成了扩建丙酸、烷基化等装置的扩建改造,使炼厂装置构成、经济效益、各项指标均发生了显著变化,原油加工能力也由年550万吨扩建至年1050万吨四 报告内容介绍(一)原料与产品装置一期工况所加工原料为自常减压蒸馏装置来的加工苏丹混合原油的减压蜡油,二期工况所加工原料为自常减压蒸馏装置来的加工沙轻、沙中混合原油的减压蜡油。主要产品有石脑油、航煤和柴油等。(二) 生产原理以减压蜡油为原料,UF-210STAR为精制催化剂,HC-115为裂化催化剂,用高纯氢在350多摄氏度下进行加氢精制和裂化
8、反应,以最大量生成中间馏分柴油。(三)生产控制的主要指标表-1反应器操作条件项 目操作条件精制段裂化段后精制段催化剂UF-210STARSHC-115UF-310STARS体积空速,h-1(对新鲜进料)2.161.22(一期)0.80(二期)15工艺流程单段全循环工艺条件混合进料比1.70反应器入口氢油比7131反应温度,一期二期初期末期初期末期第一床层入口温度,358422358406出口温度,366429387435第二床层入口温度,366429364407出口温度,373436393436第三床层入口温度,368413392412出口温度,381423407426第四床层入口温度,381
9、423393412出口温度,392434407426表-2高、低压分离器及塔操作条件项 目单 位数值一期二期热高压分离器温度316316压力MPa(g)15.5115.51热低压分离器温度290292压力MPa(g)2.912.91冷高压分离器温度5555压力MPa(g)15.1715.17冷低压分离器温度5454压力MPa(g)2.832.83循环氢脱硫塔进料温度循环氢4040贫胺液50塔顶温度4048塔底温度4050塔顶压力MPa15.0615.06低分气脱硫塔进料温度低分气4040贫胺液4646塔顶温度4444塔底温度4353塔顶压力MPa(g)2.532.53汽提塔进料温度冷低分液22
10、1216热低分液289292汽提蒸汽410410塔顶温度128138塔底温度251264塔顶压力MPa(g)1.011.01项 目单 位数值一期二期分馏塔进料温度闪蒸气275298汽提塔底液379379汽提蒸汽371371塔顶温度129125塔底温度348347塔顶压力MPa(g)0.080.08航煤汽提塔进料温度184178塔顶温度201192塔底温度217207塔顶压力MPa(g)0.100.10柴油汽提塔进料温度264273塔顶温度260269塔底温度248256塔顶压力MPa(g)0.110.11(四)车间工艺流程叙述1反应系统工艺流程自罐区来的冷原料油经原料油预过滤器预过滤,再进入聚
11、结脱水器(M101)脱水,并与自常减压装置来的热减压蜡油混合,然后经过原料油/循环柴油换热器(E101AB)的管程与来自分馏部分的循环柴油换热,通过原料油自动反冲洗过滤器(S101)除去大于25m的固体颗粒,最后进入原料油缓冲罐(D101)。原料油缓冲罐中的原料经原料油泵(P101AB)升压后,先经热高分气/原料油换热器(E107AD)管程、反应产物/冷原料油换热器(E105AB)管程、反应产物/热原料油换热器(E103AC)管程换热,再与来自循环氢加热炉(F101)的循环氢混合后,进入加氢裂化反应器(R101)进行加氢精制、加氢裂化反应。自加氢裂化反应器(R101)来的反应产物经反应产物/热
12、原料油换热器(E103AC)壳程、反应产物/汽提塔底油换热器(E104)管程、反应产物/冷原料油换热器(E105AB)壳程换热至316后,进入热高压分离器(D103),反应产物在热高压分离器中进行气、液分离。热高分气经过热高分气/热循环氢换热器(E106AB)壳程、热高分气/原料油换热器(E107AD)壳程、热高分气/冷循环氢换热器(E108)壳程与循环氢和原料油换热、再经过高压空冷(A101 AP)冷却后进入冷高压分离器(D102)进行油、水、气三相分离。为了防止反应产物中的铵盐在低温部分结晶,通过注水泵(P220AB)将水注入到热高分气空冷器(A101AP)上游的管道中。在热高分液管道上设
13、置热高分液能量回收透平(P102)驱动一台原料油泵(P101A)。热高分液经能量回收透平后进入热高分液/汽提塔底油换热器(E113)管程与汽提塔底油换热后送至热低压分离器(D104)进一步闪蒸,热低压分离器气相经热低分气空冷器(A102)冷却后送至冷低压分离器(D105)。冷高分气经冷高气冷却器(E109)冷却后赶往循环氢脱硫塔(C101)脱硫,然后进入循环氢压缩机(K102)。循环氢升压后分两路:一路作为急冷氢进入加氢裂化反应器(R101),另一路与来自新氢压缩机(K101AC)三级出口的新氢混合,经热高分气/冷循环氢换热器(E108)管程、热高分气/热循环氢换热器(E106AB)管程换热后
14、进入循环氢加热炉(F101),然后与原料油混合作为反应进料。冷高分油至冷低压分离器(D105)进一步闪蒸,冷低分气经过冷低分气冷却器E112冷却后与柴油加氢精制装置来的低分气一起经干气脱硫塔脱硫后送至PSA装置回收氢气。冷高分水进入冷低压分离器进一步闪蒸,冷低分水送至硫磺回收装置。冷低分油经汽提塔进料/循环航煤换热器(E206AB)和汽提塔进料/分馏塔底油换热器(E202AC)分别与循环航煤和分馏塔底油换热后送至汽提塔。热低压分离器(D105)液体直接送至汽提塔。2分馏系统工艺流程来自反应部分的冷、热低分油分别从不同位置进入汽提塔(C201)10、16层塔板,塔底通入3.5MPa中压蒸汽汽提。
15、塔顶气相经汽提塔顶空冷器(A201AH)冷却至48后进入汽提塔顶回流罐(D201)进行油、气、水三相分离。含硫气体至轻烃回收装置进一步回收液化气;含硫污水送至硫磺回收装置;塔顶油相经塔顶回流泵(P201)后一部分送回塔顶作为回流,另一部分送至轻烃回收装置。汽提塔底油作为分馏塔进料。汽提塔底油经热高分液/汽提塔底油换热器(E113)壳程、反应产物/汽提塔底油换热器(E104)壳程换热后进入预闪蒸罐(D202),闪蒸后的气相直接进入分馏塔(C202)37层塔板,液相部分经分馏塔进料泵(P202AB)升压、分馏塔进料加热炉(F201)加热后进入分馏塔46层塔板下部。分馏塔塔顶气相经分馏塔顶空冷器(A
16、202AP)冷凝冷却至88后进入分馏塔顶回流罐(D203),液相经分馏塔顶回流泵(P205AB)升压后一部分作为塔顶回流,另一部分石脑油在一期工况经分馏塔顶石脑油空冷器(A-208)和石脑油冷却器(E210AB)至40后送至石脑油加氢装置,在二期工况经分馏塔顶石脑油空冷器(A-208)和石脑油冷却器(E210AB)付线直接送至轻烃回收装置;含油污水经分馏塔顶污水泵(P204AB)升压后,一部分送至注水罐(D205),然后经注水泵(P220AB)升压后作为反应部分注水,剩余部分送至柴油加氢精制装置。塔底油经分馏塔底油泵(P203AB)升压,一部分循环至挂壁塔,经蒸汽汽提后约0.5%(对原料)的未
17、转化油经未转化油蒸汽发生器(E209)发生0.4MPa低低压蒸汽后送至重油催化裂化装置原料油罐;另一部分经航煤汽提塔重沸器(E204)提供热源、分馏塔底油蒸汽发生器(E214)发生1.0MPa低压蒸汽、汽提塔进料/分馏塔底油换热器(E202AC)管程与冷低分油换热后,再经未转化油空冷器(A203AF)冷却至168循环至反应部分原料油缓冲罐(D101)。分馏塔中部设侧线航煤汽提塔(C204),塔底热源由航煤汽提塔重沸器(E204)提供,热源为分馏塔底油;塔底航煤产品经航煤产品泵(P208AB)升压、航煤产品/热水换热器(E213)回收低温热、航煤空冷器(A206AB)、航煤产品冷却器(E205)
18、冷却后,一部分送去与产品柴油调合,剩余部分送出装置。分馏塔下部设侧线柴油汽提塔(C203),塔底采用3.5MPa中压蒸汽汽提;塔底柴油产品经柴油产品泵(P208AB)升压、柴油及循环柴油蒸汽发生器(E215)发生1.0MPa低压蒸汽、柴油产品/锅炉给水换热器(E203)、柴油产品/热水换热器(E216AB)回收低温热、柴油产品空冷器(A204AD)冷却、柴油聚结脱水器(M201)、柴油盐干燥器(D204)脱水后出装置。分馏塔设航煤中段回流和柴油中段回流,柴油中段回流经循环柴油泵(P206AB)升压、柴油及循环柴油蒸汽发生器(E215)发生1.0MPa低压蒸汽、循环柴油/原料油热器(E101)壳
19、程、循环柴油/热水换热器(E212)回收低温热后返回分馏塔。航煤中段回流经循环航煤泵(P209AB)升压、经汽提塔进料/循环航煤换热器(E206AB)换热、循环航煤/热水换热器(E211AB)回收低温热后返回分馏塔。3脱硫系统工艺流程装置设置冷低分气(富氢气体)脱硫塔(C102),自冷低压分离器(D105)来的富氢气体与柴油加氢精制装置来的低分气一起经脱硫后,送至PSA装置进行氢提浓,提浓氢送入全厂氢气管网。(五)本岗位操作规程1 反应系统操作原则严格按照装置工艺设计条件、设备操作指标,保证原料油系统、循环氢系统、新氢系统、反应器、高低压分离系统、脱硫系统的正常生产和平稳运行。根据公司的整体物
20、料平衡,以及产品质量控制指标要求,控制装置的原料处理量及加氢反应深度。岗位负责生产操作调节,工艺参数记录,日常巡检,设备运行维护,异常事故处理,装置开、停工,严格执行交接班制度,确保装置“安、稳、长、满、优”运行。加氢裂化装置属于高温、高压、临氢装置,同时,加氢反应过程为放热反应,反应温度的变化对装置的安全生产极为重要。因此必须严格控制反应温度、压力,避免出现超温、超压的现象,确保装置人员和设备的安全。装置首次开工中,正常升温速度为10/h,最大为30/h;正常升压速度为1.5MPa/h,最大为2.8MPa/h。反应器器壁最低温度(由表面热电偶测出)在达到最小升压温度93以前,其操作压力不能超
21、过冷高分正常操作压力的30%(4.56MPa)。当器壁最低温度在达到最小升压温度93以后,其操作压力才允许逐渐升高到正常操作压力,升压速率不宜大于2.8MPa/h。经历操作一个周期后再开工,升压过程中,反应器器壁最低温度(由表面热电偶测出)在达到93以前,其操作压力必须降至冷高分正常操作压力的30%(4.56MPa)以下。在正常生产时升降温速度:精制床层入口温度新催化剂为2/h,旧催化剂4/h;裂化各床层入口温度新催化剂为0.5/h,旧催化剂2/h。特别是新催化剂,温度控制更要小心。当温度接近于工艺指标510,可不必急于调整加热炉燃料,应根据转化率、分馏系统的产品分布缓慢调节反应温度,且待反应
22、器温度平稳后再调整加热炉出口温度,使温度控制在工艺指标范围内。正常加、减原料油时,提降量速度为10吨/时,并根据原料油的性质及当时的操作温度来调整加热炉的出口温度,使操作温度达到控制指标。若连续加、减原料油,应等前一次的反应温度平稳后再进行。在加原料油时,若发现反应床层温度上升过快或过高,应立即减少燃料气或用冷氢量来调节,待反应床层温度平稳后,再继续恢复操作。正常生产中,应保持各床层冷氢阀在65%开度状态,坚决不允许100%开度进行操作,以备急用。调节各床层冷氢量时,应尽量保持各床层温升10及尽量相等的出口温度,为了整个系统的相对平稳,每次调节应在0.5左右。在升高或降低反应压力时应严格按照升
23、压或降压速度进行。当压力接近操作压力0.51.0MPa时,应缓慢升压、降压,待系统压力平稳后再调整到工艺指标内。当反应系统压力下降,如果无法恢复到正常操作压力,且最小氢分压低12.8MPa时,应立即降低炉出口温度,降低反应进料量,维持系统最低氢分压为12.8MPa以上(氢分压为高分压力与循环氢纯度的乘积)。无论如何,循环氢量都不能低于设计流量的75%。在降温、降量过程中,严防降量过快,导致反器床层温度超温。停工降温时,当反应器冷却至205以下,应确保循环气中CO含量不得超过30ppm。目的是避免产生有毒的碳酸镍Ni(CO)4。反应器停工后,应以氮气充压至0.1MPa0.22MPa密封,以防空气
24、进入。A 原料油缓冲罐D101液位控制(1)控制范围D101原料缓冲罐液位LIC1003:40%60%。(2)控制目标LIC1003设定值为50%。(3)相关参数D101原料缓冲罐液位控制LIC1003、冷原料油流量控制FIC1002A/B、液位控制选择开关LY1003A/B。(4)控制方式原料油缓冲罐的液位与装置进料流量构成液位流量串级控制回路。通常,不控制热VGO进料量(FIC-1003),通过调节罐区来的冷VGO进料量控制缓冲罐液位;当装置进料全部为热VGO时,关闭冷VGO进料,通过调节热VGO进料量控制缓冲罐液位。在冷、热VGO进料量控制回路之间设置切换开关,根据装置具体的进料方式,在
25、冷VGO和热VGO进料流量间切换控制,与缓冲罐液位组成对应的串级控制回路。D101原料缓冲罐液位控制LIC1003共有三种工况,由选择开关LY1003A/B进行选择。一是开工初始进冲洗油建液位时由LY1003B选择,LIC1003与冲洗油流量控制阀FV3002实现单回路控制。二是开工过程中由LY1003A选择,LIC1003与热进料流量控制FIC1003串级,LIC1003为主调节器,FIC1003为副调节器。三是正常生产时由LY1003A选择,LIC1003与冷原料油流量控制FIC1002A/B进行串级,LIC1003为主调节器,FIC1002A/B为副调节器。B 反应器入口温度调节(1)控
26、制范围反应器入口温度TIC1023:358。(2)控制目标设定反应温度波动不超过1。(3)相关参数反应炉出口温度TIC1021、原料油换热温度TIC1012、原料含硫量、含氮量、循环氢纯度。(4)控制方式aR101入口温度TIC1023与F101总出口温度TIC1021进行串级控制。TIC1023为主调节器,bTIC1021为副调节器。调节原料油换热后温度TIC1012时,会影响反应器入口温度,当原料油换热后温度升高,则反应器入口温度升高,此时需降低循环氢加热炉总出口温度;当原料油换热后温度降低,则反应器入口温度降低,此时需升高循环氢加热炉总出口温度。C 裂化床层温度调节(1)控制范围裂化反应
27、器床层温度TIC1205、TIC1206、TIC1207:366/368/381(2)控制目标设定反应温度波动不超过1。反应器裂化段任一床层温升15。(3)相关参数裂化床层入口温度(TIC1205、TIC1206、TIC1207)、裂化床层入口及床层冷氢量、循环氢纯度、循环氢流量。(4)控制方式裂化床层各床层入口温度由冷氢的流量控制。循环氢流量由循环氢压缩机转速控制。循环氢纯度由C-101顶氢气排放至PSA提纯FIC1026控制。D循环氢加热炉支路阀位控制(1)控制范围循环氢加热炉支路最大阀位控制ZIC1100:090%。(2)控制目标最高阀位不超过90%。设定最大阀位波动不超过2%。(3)相
28、关参数循环氢加热炉F101支路流量控制FIC1010AJ。(4)控制方式ZIC1100正作用,与支路流控FIC1010AJ进行复杂控制,其设定值为各支路流量控制阀的最小阀位,输出为支路流量控制器的设定值。加热炉的10个支路流控FIC1010AJ为反作用,对应四个流控阀的阀位进行低选,其最小阀位作为ZIC1100的实际值。E 循环氢加热炉F101出口温度控制(1)控制范围循环氢加热炉出口温度控制TIC1021:444513。(2)控制目标操作初期操作温度为444左右,末期513左右。设定温度波动不超过1。(3)相关参数F101出口温度指示TI1440。F101燃料气流量控制FIC1091,供风流
29、量控制FIC1098,空/燃比控制HIC1053,高信号选择开关TY7008B,低信号选择开关TY7008A。(4)控制方式F101出口温度控制TIC1021,反作用,与燃料气流量控制FIC1091、供风流量控制FIC1098进行复杂控制。TIC1021的输出分两路,一是与实际的燃料气量进行高选,二是与由供风量计算出来的所需燃料气量进行低选。F101提温时TIC1021输出增加,输出信号经高选开关FY1098B后,与空燃比HIC1053相乘,得出所需的风量作为FIC1098的设定值,增加供风量。增加后的供风量再除以空燃料比,计算出所需的燃料气量,经低选开关FY1098A后作为燃料气流量控制FI
30、C1091的设定值,从而增加燃料气量。增加后的燃料气量再与TIC1021的输出进行高选比较,直到两者相等为止,完成提温过程。F101I降温时TIC1021输出减少,输出信号先经低选开关FY1098A后,直接降低燃料气量FIC1091,当燃料气量降低后,再经高选开关FY1098B与空燃料比HIC1053相乘得到相应的供风量,作为FIC1098的设定值来降低风量。此时的风量再除以空燃比计算所需的燃料气量,并与TIC1021的输出信号进行低选比较,直到两者相等为止,完成降温过程。F循环氢纯度控制(1)控制范围循环氢纯度:85%。(2)控制目标循环氢纯度90%以上。(3)相关参数R101反应温度、新氢
31、纯度、原料含氮、含硫量、热高分D103温度变化、空冷器A101注水量的变化。(4)控制方式循环氢纯度降低,通过FV1026废氢的排放调整。G装置操作压力控制(1)控制范围装置操作压力(冷高分压力)控制PIC1015:1415.2MPa。(2)控制目标操作压力PIC1015:15.0MPa。设定压力波动不超过0.5MPa。(3)相关参数冷高压分离器顶部压力指示PI1067;循环氢排放流量控制FIC1026;选择开关PY1027A;高信号选择开关FY1026。(4)控制方式装置操作压力控制PIC10151,正作用,采用分程控制,与新氢压力低保护控制PV1015、循环氢排放流量控制FIC1026组成
32、复杂控制回路。PIC7021输出050%,新氢逐级返回控制阀阀位0100%;PIC7021输出50100,循环氢排放阀阀位0100%。正常操作时,PIC1015输出在050%,对新氢逐级返回控制阀进行调节,改变进入装置的新氢量。当PIC1015输出达到50100%,此时打开循环氢排放阀以降低压力。 H新氢压缩机的压力控制(1)控制范围新氢压缩机各级缓冲罐压力控制PIC1027A/1028/1029:2.08、4.22、8.58MPa(2)控制目标设定压力波动不超过0.5MPa。(3)相关参数新氢压缩机各级入压力控制PIC1027A/1028/1029,冷高分顶压力控制PIC1015。(4)控制
33、方式新氢压缩机压力采取逐级递推控制。新氢压缩机出口压力逐级递推控制,就是新氢压缩机各级入口分液罐压力分程控制本级新氢返回到前一级的量(第一级为放空量)和本级出口返回到入口的量,每级返回量在本级和下一级入口压力信号中低选。当压缩机入口压力低时,根据每一级入口压力调节相应返回量使入口压力上升。当出口压力升高到一定范围后,则根据每级出口压力控制返回量,逐级返回,保证了压缩机出口新氢压力的稳定。在一级入口分液罐D106,一般通过调节压缩机一级出口至入口的返回量来保证压力稳定;当压力过高时,开启放空(PV1027)。由于有三台新氢压缩机,二开一备,设置切换开关PY1027A,根据机组运行情况,选择控制信
34、号的流向。J 高、低分液位控制(1)控制范围热高分液位LIC1006:40%60%。(2)控制目标液位控制设定值50%。设定液位波动不超过2。(3)相关参数热高压分离器液位控制LIC1006A、LIC1006B;低信号选择开关LY1006A,控制阀选择开关L17006B。(4)控制方式热高分D103液位为分程控制,调节器LIC1006的输出分0%33%、33%67%和67%100%三部分,分别作用调节阀LV1006A、LV1006B和LV1006C。高压液体经A阀驱动液力透平P102后进入热低压分离器,而B阀和C阀是旁路液力透平,直接去热低压分离器。K贫胺液缓冲罐D114压力控制(1)控制范围
35、D114贫胺液缓冲罐压力PIC1020控制范围:0.200.25MPa。(2)控制目标设定压力为0.21MPa,压力波动不超过0.05MPa。最高压力不超过1.2MPa。(3)相关参数D114原料缓冲罐压力控制PIC1020。(4)控制方式D114贫胺液缓冲罐压力控制PIC1020采用分程控制,PIC1020输出050%,PV1020A阀阀位1000%;输出50100%,PV1020B阀阀位0100%。L 循环氢脱硫塔液位控制(1)控制范围循环氢脱硫塔入口分液罐液位控制LIC1018A/B:020%。循环氢脱硫塔液位控制LIC1017A/B:4060%。(2)控制目标LIC1017A/B液位设
36、定值为50之间。设定LIC1018A/B为0%。(3)相关参数入口分液罐液位控制LIC1018,控制阀选择开关LY1018 A/B;脱硫塔液位控制LIC1017 A/B,控制阀选择开关LY1017A/B。(4)控制方式入口分液罐液位LIC1018 A/B,单回路控制,正作用。两个液位控制阀LV1018A、LV1018B设置串级状态,经选择开关LY7018 A/B后选择一个参与自动控制,另一个备用。脱硫塔液位控制LIC1017 A/B,单回路控制,正作用。两个液位控制阀LV1017A、LV1017B设置串级状态,经选择开关LY1017 A/B后选择一个参与自动控制,另一个2分馏系统操作原则严格执
37、行分馏岗位的工艺操作指南,保证脱气塔、分馏塔、航煤及柴油塔汽提塔的正常生产。负责本岗位的开、停车及事故处理,根据产品质量要求,生产合格的石脑油、航煤、柴油等产品;同时负责分馏系统所有的换热器、水冷器、空冷器及机泵的正常运转,确保分馏进料加热炉F201的安全平稳运行,做好设备和工艺管线的日常维护工作。加强巡回检查力度,并做好本岗位的交接班和原始数据记录,保证整个装置的安全平稳运行。分馏系统的目的是获得符合规范的产品,利用脱气塔、分馏塔、航煤及柴油塔把反应流出物分割成干气、石脑油、航煤、柴油等合格产品。分馏岗位操作主要把握三条原则:物料平衡、气液平衡和热量平衡的原则;定性参数轻易不要改变,利用定量
38、参数来调节的原则。分馏操作对全装置的平稳操作起着重要的作用,并掌握着主要产品的质量控制。分馏系统稳定操作的原则:在稳定物料平衡的基础上,调节塔的热量供给和热量分布,确保产品的合格,在操作重要区别什么是定性参数(P、T),什么是定量参数(F),尽量保持定性参数不变,通过调节定量参数来调节产品质量。即在正常操作中应稳定塔顶压力、塔顶温度、塔底液面及各中段回流量,以侧线抽出量来调整产品质量。温度:温度是系统热平衡和物料平衡的关键因素,要想保持系统的平稳操作,就要严格控制好各点的温度。分馏各点温度的高低主要视进料性质而定,温度是随着进料裂化程度增加而降低的,所以在正常操作中,应随进料性质变化及时调整各
39、点温度。压力:压力控制的平稳与否直接影响产品质量、系统的热平衡和物料平衡,甚至威胁到装置的安全生产。在对塔压力进行调节时要进行全面分析,尽力找出影响塔压的主要因素(一般情况下主要有:进料、回流带水、轻组分量变化),进行准确而合理的调整使操作平稳下来。在进行压力调节时要缓慢,不要过猛,不要随便改变给定值,防止大幅度波动造成冲塔事故。液面:液面是系统物料平衡的集中体现,塔底液面的高低将不同程度的影响产品质量,收率及平稳操作,液面过高将会造成携带甚至冲塔现象,液面过低易造成塔底泵抽空,以致损坏设备。所以平衡好各塔液位尤其重要,它是系统稳定操作的基础,一般液位控制在40-60%。分馏操作是一种连续的动
40、态操作,针对不同的处理量和不同的转化率,有着不同的稳定的操作参数组,当进料和转化率发生改变时,分馏就要做及时调整,以保证产品的质量和收率,这是因为在固有塔设备的条件下,压力、进料量和进料组成一定时,要使目的产品通过汽化、冷凝,得以分离需要的最少热量值是一定的,而在实际生产中,所提供的热量要大于这一热量值,才能使在每层塔盘上的传质传热过程进行的充分,保证塔盘效率和产品分离精度,而多余的那部分热量即是塔顶回流和中段回流取走的热量。这部分过剩热量的大小决定了操作能耗的大小,在正常操作过程中,应时刻注意顶回流量(中段回流量)及相应温度。不能只为了控制顶温一味地增大回流量,可以通过调节炉出口温度稳定顶温
41、,对于C-202来说,在调节过程中,如果产品能保证质量,能用中段回流取热的,尽量用中段回流,因为塔顶取热不能回收利用。当然这部分过剩能量也不能太小,否则分馏塔将没有内回流无法操作,产品分离将不会得到保证。选择适当的回流量对塔的操作很重要,在进料和转化率有小的波动时,只需将过剩热量做一下调整,就可保证操作仍在原操作参数下进行。在正常操作时应尽量稳定塔顶回流量、一、二中回流量和回流温度,同时在分馏塔进料量增加时相应比例提高一、二中回流量。(1)汽提塔C201操作因素分析汽提塔的主要目的是脱除反应生成油中的硫化氢含量,保证石脑油、航煤等产品腐蚀合格,也可减少硫化氢对分馏系统设备的腐蚀。上述也是该塔操
42、作调整的最根本的出发点和依据。在分馏时,汽提硫化氢近似于汽提丙烷,所以用水蒸汽汽提掉硫化氢也近似于汽提掉丙烷或比丙烷更重些的烃类。当塔的操作压力恒定时,塔的操作温度是一个重要参数。若塔顶温度太低时,部分水蒸汽会在塔顶冷凝,回流至塔内,被热油再次汽化,这样引起水汽水的内部循环,最终造成液泛;若塔顶温度过高,就会有大量C5汽化,增加塔顶冷凝负荷。因此,操作温度应按照设计条件来操作。1)压力压力是产品的定性值,它决定于油品的沸点,在相同温度、相同组成下,决定油品的汽化率,对整塔的操作有直接影响。塔压力升高,油品的沸点升高,汽化率下降,塔内气相减少,组分分离难度增加,要保证分离效果,所需热量增加,能耗
43、高,此时应注意塔的温度和产品分割;塔压力降低,油品的沸点降低,相同温度下汽化率增加,塔温下降,把流体送入下游装置的液压推动力将降低,气体流率将增加,塔内气相负荷增加,塔盘负荷增加,干气排放量增加,加工损失大,且易产生雾沫夹带,分离效果差。为了避免混乱或事故,不要迅速改变PIC2004的压力给定值。通常此压力是恒定不变的,而用调节回流量来调节塔温。脱气塔的塔顶压力是通过设在脱气塔回流罐D201的干气上的压控PIC2004来调节,利用干气的排放至轻烃回收来调节汽提塔C201的塔顶压力。正常操作期间,脱气塔C201的设计操作压力为0.97MPa。2)温度温度在一定的压力和油品组成下,反映油品的汽化率
44、。为了生产合格产品,在汽提塔操作中,温度调节是重要的。汽提塔C201共有四个温度可供调节,即进料温度、塔顶温度、回流温度、塔底温度。可以控制来自热低压分离器的热油温度和来自E202的冷低分油温度及塔底吹入的过热蒸汽量,来控制塔的各点温度。这些温度都反映了产品的质量和蒸馏程度。a:进料温度汽提塔进料温度有一个最佳值,如果温度太高,进料会大量地蒸发,而塔的效率也会因精馏段(进料以上塔盘)各组分分离不适当而降低。也会增加塔顶冷凝热负荷引起过多的能量损失。对汽提塔进料物流温度影响最大的是热高分温度。这个温度是由TIC1225控制的。最佳温度要以设计数据为依据,并在操作中不断总结修改。汽提塔的设计进料温
45、度为:221(冷低分油)、289(热低分油)。b:塔顶温度塔顶气相温度是塔顶液相的泡点温度,是塔顶产品中重关键组分浓度的主要标志,如果塔顶温度高必须加大回流量,或调整进料温度和塔底汽提蒸汽量。汽提塔的塔顶温度设计操作值为138。c:回流温度回流温度受空冷器A201的控制,回流温度的高低直接影响塔的分离效果和操作费用。通过控制空冷器的叶片转角,把空冷出口温度TI2004的温度控制到最佳温度,设计温度为48。温度高(饱和回流),取热方式为汽化潜热,所需的换热塔盘数少,能保证其它塔盘的效率;回流温度低(冷回流),取热方式为潜热和显热,所需换热塔盘多,且塔顶轻组分易被携带到下层塔盘,影响塔盘的分离效果
46、。空冷A201出口温度即为汽提塔顶回流温度,回流温度设计值为48,要稳定操作,避免温度超高。d:塔底温度塔底液体温度是它的泡点温度,体现塔底液体中轻关键组分的浓度,如果塔底温度太高,就必须加大回流量,反之应减少回流量。正常塔底设计温度为251。3)流量a:进料量当装置的处理量改变时,汽提塔C201的进料也要相应改变,这就打破了原有的物料平衡和热量平衡,因此塔的操作也相应的调整。当脱气塔的进料率增加(减少)时,为维持物料平衡和热量平衡,保持C201、D201的液位稳定,必须按比例增加(减少)回流量和塔底吹汽量,以维持塔顶和塔底产物质量稳定。b:抽出量该塔塔顶抽出产品去轻烃回收装置,抽出量FIC2
47、005与塔顶回流罐D201液位控制LIC2003组成串级控制来控制抽出轻烃量。抽出量是以稳定回流罐D201液位为依据。c:回流量回流量是调节塔内热量平衡的重要手段之一,也是调整产品分馏精度的主要手段,还是衡量操作好坏的方法之一。塔顶回流是调节塔顶温度及H2S脱除效率的最敏感的手段。回流量增加,塔顶取热量增加,塔顶温度、塔底温度降低,同时增加了塔顶冷凝负荷,生产能耗和操作费用增加。在保证硫化氢脱除效果的前提下,回流量控制不是很大,防止意外事故(如液泛)的发生。注意,如果外回流流率不变,而回流温度降低,塔中内回流将会增加。汽提塔回流量的控制是通过塔顶温控TIC2002串级来调节,以保持塔顶温度的恒
48、定。如果进料中液化气体和轻组分相对减少时应增大回流量,同时增大塔内的汽提蒸汽量,以保证汽提塔精馏段塔盘上的液层,提供足够的汽液相,防止因轻组分不足而产生漏液和干板现象。d:塔底汽提蒸汽量汽提塔C201的汽提蒸汽是3.6MPa中压蒸汽。塔底吹汽量是汽提塔操作重要而又敏感的操作参数,提高汽提蒸汽量有利于硫化氢的脱除。但塔内过多的汽提蒸汽会导致水蒸汽在塔内冷凝,而且高的汽提蒸汽也会带来塔的液泛。因此,应调节脱气塔的汽提蒸汽量,达到既有足够的蒸汽量脱除生成油中的硫化氢,又能避免水蒸汽的冷凝,以便节能和减少污水量。(2)分馏塔C202操作因素分析分馏塔的主要目的是把反应生成油分离出所需要的产品,影响产品
49、质量的操作参数有:塔操作压力、温度、流量、汽提蒸汽量、侧线塔的操作。1)压力分馏塔顶压力为分程控制,它是通过控制阀PV2013B调节塔顶回流罐D203的气体去低压放空总管,以及通过控制阀PV2013A调节燃料气入回流罐的流量实现。在塔的馏出物产量和汽化量一定时,改变塔的压力,就改变了分馏加热炉的热负荷。反之,加热炉负荷一定(炉出口温度一定)时,降低塔压力,可增加过汽化量,从而提高了分馏塔馏出物的产率。降低塔压力,塔顶系统需在较低温度下操作。分馏塔的设计操作压力为0.083MPa。分馏塔顶压力由装在分馏塔顶系统的PIC2013控制,压力信号取自C203顶气相馏出线上,回流罐气体出口线上装两组调节
50、阀。燃料气来气线上的为A阀,排放气线上的为B阀,两阀组为分程控制。因为该塔顶气体没有多少气体,必须引燃料气协助控制。排放气去低压放空总管。2)温度分馏塔C202共有进料温度、塔顶温度、塔底温度、侧线抽出温度、中段回流温度、回流温度可用于调整分馏塔产品分离精度、拔出率、热量平衡和操作能耗。a:进料温度进料温度指示着带入塔内热量的大小和汽化率,进料温度主要取决于分馏加热炉F201供给的热量,分馏进料温度设计值为379。b:塔顶温度分馏塔的塔顶温度是通过对塔顶回流线流控FIC2018和塔顶温控TIC2016串级进行调节而实现的,通过调节塔顶回流率控制塔顶温度。塔顶温度决定石脑油的干点,此温度随产品切
51、割点而变化,但应在110130的范围内。如果要提高石脑油的上限切割温度,则TIC2016的给定值也要增加,并要调节到新的位置上。分馏塔顶温度设计值为129。c:塔底温度分馏塔底温度是通过对加热炉出口温度调节来控制的,它是塔底油品的泡点温度,塔底温度高,蒸发量大,塔底油轻组分少,侧线产品的干点偏高,组分变重。航煤的初馏点高,闪点高。塔底温度低时,合理组分蒸发不了,产品质量轻,也加重了下游设备的负荷。一期塔底温度的设计值为348。d:侧线抽出温度侧线抽出温度就是抽出塔盘的温度。该塔盘温度是由塔盘上的液体组成确定的(液体的泡点),所以塔盘的温度应控制在与所需产品组成相符的温度上。侧线抽出温度高,产品
52、组分重,干点高,正常情况靠抽出量调节,抽出量大,温度升高,随生产方案的不同而改变。分馏塔的抽出侧线装有盘装仪表TI2018(航煤)、TI2019(柴油)。初期航煤侧线的抽出温度为191,柴油侧线的抽出温度为270;末期航煤侧线的抽出温度为188,柴油侧线的抽出温度为267。e:回流温度回流温度的作用与C201相同,它是靠塔顶空冷器A202来调节,设计值为89。f:中段回流温度一中回流温度是分程控制,靠装在返塔线上的温控阀TIC2036调节换热器E211的付线流量阀TV2036和主线流量阀TV2036A来控制温度。二中回流温度是分程控制,靠装在返塔线上的温控阀TIC2034调节换热器E212的付
53、线流量阀2034B和主线流量阀2034A来控制温度。中段回流温度的高低直接影响塔内的热量平衡,温度高,返塔后的换热塔盘数少,取热少,塔盘温度上升,使塔上部热量增加,塔顶温度和侧线抽出温度都要上升,影响产品分离效果。正常操作温度不应有大的波动,取热量靠中段回流量来调节。3)流量a:进料量汽提塔底油通过自压送往分馏塔。该物料经换热后进入预闪蒸罐D202,罐底液休分8路去F201加热,每路上上有流量指示控制(FI2012AH)并与预闪蒸罐液位指示控制(LIC2005)构成串级控制。经分馏炉F201加热后合为一根转油线,去分馏塔进料段;罐顶气体直接进入分馏塔进料段。分馏塔的进料量将随装置进料量而变化。
54、b:侧线抽出量分馏塔有两条侧线产品:航煤、柴油。侧线产品的抽出量可以根据需要来调整。例如,当为获得最大量重石脑油产率时,可以减少航煤的抽出量,以使本应属于重石脑油馏分的组成尽可能多地上升到塔顶进入石脑油馏分中;当为了获得尽可能高的尾油产率时,就可以减少柴油的抽出量,降低柴油的干点,使更多的组分进入尾油馏分中去,等等。所以侧线产品抽出率是调节产品构成,最大量生产所需的产品的重要调节手段之一。此外,侧线抽出量的大小直接影响产品的质量,在进料量和性质不变的情况下,增加侧线抽出量,侧线产品的干点增加,拔出率增大,下游产品的初馏点、闪点、凝点增加。当侧线抽出量改变时,塔的内回流改变。抽出量增加,内回流减
55、少,汽相负荷相对增加,使塔下部温度升高,操作上为了保证塔顶产品和侧线产品的质量,就需要增加回流量和中段回流量或降低F201炉出口温度。侧线抽出量的大小是由进料量和转化率决定的,也是由不同生产方案决定的,一般情况不宜大幅度波动。c:中段回流量中段回流量的控制是靠装在返塔线上流控来调节(一中靠流控FIC2025调节,二中靠流控FIC2020调节),而循环量的大小要根据塔内过剩热量来决定,当塔顶取热量大时,侧线抽出温度高,塔顶降温困难,都要增大中段回流的方法来调节,以减少塔顶负荷。d:塔顶回流量塔顶回流量的作用与C201相同,它是靠塔顶挥发线上温控TIC2016与塔顶回流线上流控FIC2018串级控
56、制的。4)汽提蒸汽量分馏塔的汽提蒸汽是3.6MPak中压蒸汽。当蒸汽吹入塔内后,就降低了油气的分压,吹入的蒸汽越多油气分压降低的就越多。在较低的油气分压下,液相油中的较轻组分就更易于挥发出来,形成气相回流。增加汽提蒸汽量可提高塔顶及侧线产品馏出物的回收量,同时降低塔底油中轻质油品含量,但高的水蒸汽流率将增加塔内气相负荷。增加塔顶冷凝器的热负荷,也增加了含硫污水量。最佳的汽提蒸汽量应根据产品回收率和分离精确度以及塔顶冷凝器负荷等操作经验来确定。根据产品分析的结果,人为的调节汽提蒸汽量。5)侧线汽提塔的操作分馏塔共有两条侧线,第一条侧线是从分馏塔的第17层塔盘抽出的航煤,进入航煤汽提塔(C204)
57、的第1层塔盘。第二条侧线是从分馏塔的第31层塔盘抽出的柴油,进入柴油汽提塔(C203)的第1层塔盘。侧线汽提塔的作用是用产品的重沸或汽提蒸汽汽提掉油品中的轻组分(返回分馏塔),以使产品闪点合格。航煤和柴油侧线的抽出是按汽提塔液位调节。航煤汽提塔塔底重沸器E204是以循环尾油为热源。6反应系统工艺流程图五 实习心得体会 2010年5月10日,我开始了我的顶岗实习任务。本次实习主旨在于:实践性的了解实际生产中的化学工艺流程、提高实际动手能力和操作能力,在有限的时间里掌握整套装置的工艺流程和操作方法。以便自己能够尽快适应岗位,开始自己的职业生涯。在这接近一个月的时间内,我收获了很多的东西,这些都是我
58、在学校里和课本上找不到的,现在我们已经是毕业了,马上就要踏入社会,这些实践性的东西对我们来说是至关重要的,它让我们脱离了书生的稚气,增加了对社会的感性认识、首先我们进行了三级安全教育。为期一周的厂级安全教育,我们学习了有关集团公司出台的反违章六大禁令,看了一些安全警示录视屏。这让我感受很深刻,化工行业安全生产很重要,稍微的小错误都会造成不可估量的损失。我们一定要认真的学习操作规程,切不可违反操作规程操作。下车间之后由车间领导带我们参观了生产线、工人师傅给我们进行了入厂安全讲座。并进行了车间级的安全教育培训和考核。然后和班组的工人师傅学习,采取一对一的辅导和教导。现在的化工厂自动化程度比较高,工
59、人劳动相对比较轻松。工厂采取五班三到的工作作息时间,一班的时间是8个小时,也就是说,工人师傅要一个人在一个岗位上一呆就是八个小时。一开始我们都觉得不可思议,对于我们来说,在学校里有丰富多彩的娱乐活动和同学朋友,这八个小时单调的工作难以想象,但是随着与工人师傅共同工作的时间久了才知道自己的想法是多么的幼稚,我们现在吃穿不愁,但是真正到了社会上,首先我们的自己养活自己!然后的为家庭担起相应的责任!我们必须靠自己的劳动来实现这些!这时我们就不会觉得这八个小时是多么的漫长了,因为这八个小时的背后是我们劳动换来的收获。 实习是为了尽早的适应岗位,尽早的适应岗位才能发挥自己的价值。要想使自己成为一个优秀的员工,就必须学习好岗位知识。吃苦在前才能有以后的好生活。通过这段时间的实习,我最大的收获就是,我认识到了自己的不足,尤其是在真正动手方面。也许我们有良好的理论基础,但只有实习才能让所学知识应用到实际当中,为了以后的生活,为了适应社会,我一定好好实习,完成学校的实习任务,给学校一个满意的答复,也给自己圆满的大学生活画上句号。 最后,此报告在完成期间得到厂里指导教师朱颖和学校指导教师郭哑铃老师的支持和帮助,在此表示感谢! 成绩评定表指导教师评语: 指导教师 日期班主任意见: 班主任 日期系意见: 日期39
- 温馨提示:
1: 本站所有资源如无特殊说明,都需要本地电脑安装OFFICE2007和PDF阅读器。图纸软件为CAD,CAXA,PROE,UG,SolidWorks等.压缩文件请下载最新的WinRAR软件解压。
2: 本站的文档不包含任何第三方提供的附件图纸等,如果需要附件,请联系上传者。文件的所有权益归上传用户所有。
3.本站RAR压缩包中若带图纸,网页内容里面会有图纸预览,若没有图纸预览就没有图纸。
4. 未经权益所有人同意不得将文件中的内容挪作商业或盈利用途。
5. 装配图网仅提供信息存储空间,仅对用户上传内容的表现方式做保护处理,对用户上传分享的文档内容本身不做任何修改或编辑,并不能对任何下载内容负责。
6. 下载文件中如有侵权或不适当内容,请与我们联系,我们立即纠正。
7. 本站不保证下载资源的准确性、安全性和完整性, 同时也不承担用户因使用这些下载资源对自己和他人造成任何形式的伤害或损失。