尿素设备装置、原料
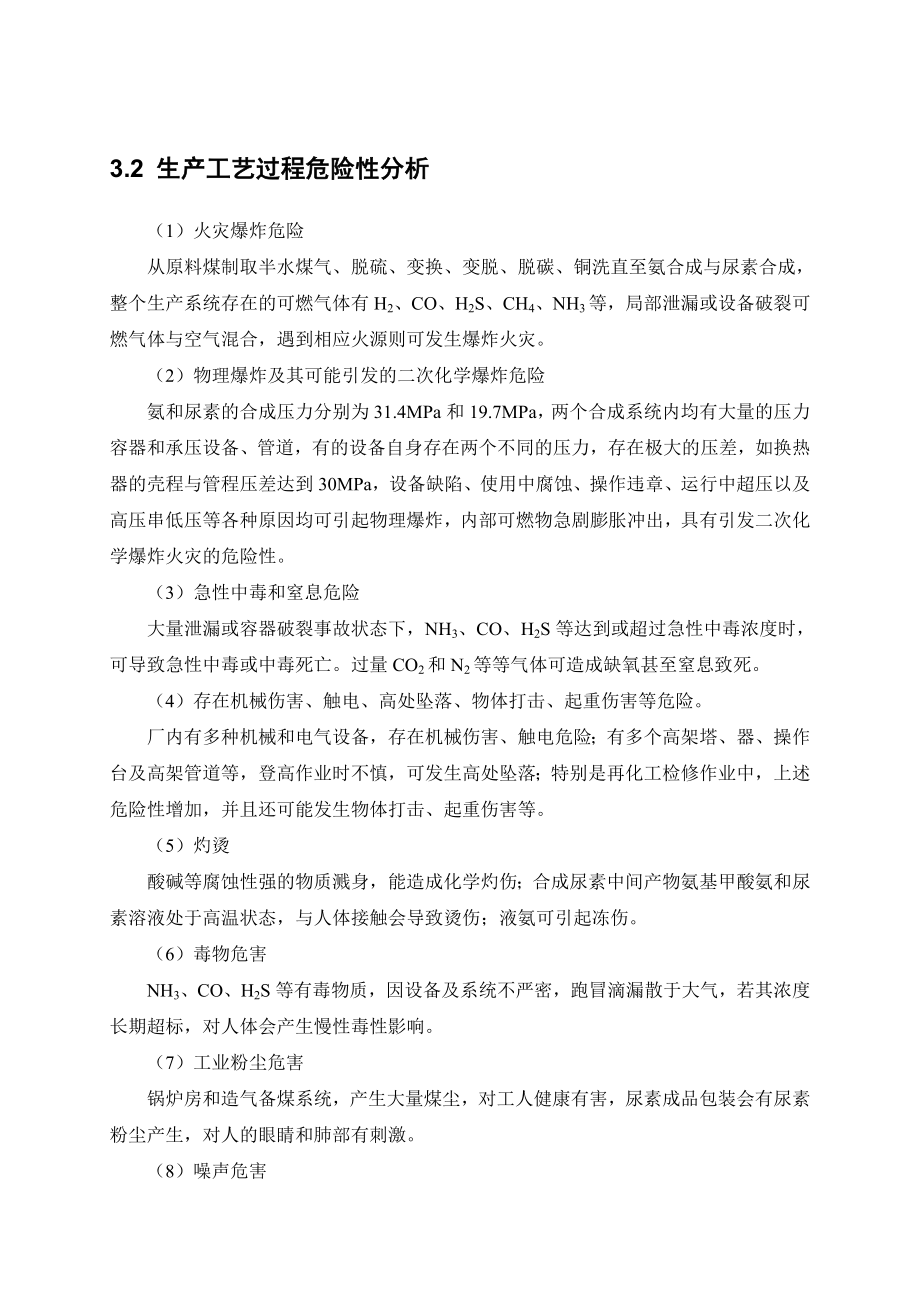


《尿素设备装置、原料》由会员分享,可在线阅读,更多相关《尿素设备装置、原料(21页珍藏版)》请在装配图网上搜索。
1、 3.2 生产工艺过程危险性分析(1)火灾爆炸危险从原料煤制取半水煤气、脱硫、变换、变脱、脱碳、铜洗直至氨合成与尿素合成,整个生产系统存在的可燃气体有H2、CO、H2S、CH4、NH3等,局部泄漏或设备破裂可燃气体与空气混合,遇到相应火源则可发生爆炸火灾。(2)物理爆炸及其可能引发的二次化学爆炸危险氨和尿素的合成压力分别为31.4MPa和19.7MPa,两个合成系统内均有大量的压力容器和承压设备、管道,有的设备自身存在两个不同的压力,存在极大的压差,如换热器的壳程与管程压差达到30MPa,设备缺陷、使用中腐蚀、操作违章、运行中超压以及高压串低压等各种原因均可引起物理爆炸,内部可燃物急剧膨胀冲出
2、,具有引发二次化学爆炸火灾的危险性。(3)急性中毒和窒息危险大量泄漏或容器破裂事故状态下,NH3、CO、H2S等达到或超过急性中毒浓度时,可导致急性中毒或中毒死亡。过量CO2和N2等等气体可造成缺氧甚至窒息致死。(4)存在机械伤害、触电、高处坠落、物体打击、起重伤害等危险。厂内有多种机械和电气设备,存在机械伤害、触电危险;有多个高架塔、器、操作台及高架管道等,登高作业时不慎,可发生高处坠落;特别是再化工检修作业中,上述危险性增加,并且还可能发生物体打击、起重伤害等。(5)灼烫酸碱等腐蚀性强的物质溅身,能造成化学灼伤;合成尿素中间产物氨基甲酸氨和尿素溶液处于高温状态,与人体接触会导致烫伤;液氨可
3、引起冻伤。(6)毒物危害NH3、CO、H2S等有毒物质,因设备及系统不严密,跑冒滴漏散于大气,若其浓度长期超标,对人体会产生慢性毒性影响。(7)工业粉尘危害锅炉房和造气备煤系统,产生大量煤尘,对工人健康有害,尿素成品包装会有尿素粉尘产生,对人的眼睛和肺部有刺激。(8)噪声危害空气鼓风机、罗茨鼓风机、压缩机、循环机、空压机、机泵等会产生较高强度噪声,长期接触可影响人体健康。(9)锅炉房、造气炉、氮氢压缩机房等再夏季可存在高温危害。根据危险因素分析,该项目工程的主要危险危害因素为火灾爆炸危险、物理爆炸危险及其可能引发的二次化学爆炸危险、急性中毒和窒息危险、机械伤害、触电、高处坠落、物体打击、起重伤
4、害、灼烫危险等。该项目工程的有害因素为毒物危害、工业粉尘危害、噪声危害、高温危害。2.3.1合成氨工艺简介合成氨工艺以山西白煤和京西煤为原料,经煤气发生炉固定层煤气化造气、PDS法脱硫、低硫低温变换、PDS法及活性碳法变换气脱硫、NHD法脱碳、铜洗法净化、中亚下合成氨。2.3.2 尿素生产工艺简介尿素生产采用水溶液全循环法流程。脱碳来的二氧化碳经压缩、净化后和液氨及循环回收的一甲液一期送入尿素合成塔在19.7MPa压力和188温度下进行合成,尿素以熔融状态自塔顶流出后经分离、闪蒸、回收、蒸发、蒸馏、造粒得尿素产品,包装入库。2.4 主要原料、辅料、消耗及产品产量该公司合成氨生产能力为4万吨/年
5、,尿素生产能力6万吨/年。主要原、辅材料情况表2.2和表2.3。表2.2合成氨主要原、辅料情况序号原辅料名称单位年用量来源运输条件备注1原料煤吨7.2万山西、京西由汽车或火车运输2各种催化剂吨52外购汽车运输3NHD溶剂吨40外购汽车运输一次投料量200L4其它化学品吨9.0外购汽车运输表2.3合成尿素主要原辅料情况序号原辅料材料名称规格单位年用量来源运输条件1液氨NH399.5吨36000来自液氨库管道运输2CO2气体CO298.5吨47100脱碳工段管道输送3活性碳吨16.6外购汽车运输4润滑油吨24.0外购汽车运输2.5.1合成氨工艺装置情况合成氨工艺共涉及设备181台套。主要设备有:2
6、400煤气发生炉6台,4M8-36/320氮氢气压缩机4台,4000中变炉1台,4000低变炉1台,3600半水煤气脱硫塔1台,5000m3气柜1座,1000铜洗塔1台,1000系列合成塔1套,3000变换气脱硫塔1台,8AS-17冰机1台,4AV-17冰机2台,沸腾锅炉SHF20-25型3台。2.5.2 尿素装置尿素装置静止设备40台,其中反应容器1台,塔器5台,换热器16台,贮槽8台,其它设备10台。本装置主要特点为高温、高压、强腐蚀,因此,对含有尿素、甲胺液及湿的CO气体等介质腐蚀的设备,选用不锈钢型,其余根据设计压力的要求采用碳钢。尿素装置主要设备有尿素合成塔、预蒸馏塔、一段吸收塔,二
7、分塔和一段蒸发器。5.1 周边环境该厂位于天津市以北119公里,蓟县城西5公里,在京蓟公路的北侧,离北京市84公里。铁路线有津蓟铁路,天津、蓟县全程113公里。另有京坨线,北京坨子头89公里处经过蓟县。全厂占地面积116880.7平方米。(见厂土地使用证)该厂位于蓟县城西,处于城关和官庄两镇辖区的结合地带。以生产区为中心,1公里半径范围内周边的单位或村庄为:东邻蓟县师范学校相聚800米;东北邻小刀剪营村相距500米;天津石矿相距800米;西邻廊坊市水泥电杆厂相距400米;蓟县物资公司木材库相距600米;蓟县石油公司油库相距950米;西南邻贾各庄村相距800米;背面为五名山;南面为蓟官、邦喜公路
8、。6.1 造气该单元包括原料准备、半水煤气制备、除尘洗涤和吹风气回收系统。煤、空气、水蒸气为原料在煤气发生炉内采用吹风、上吹、下吹、二次上吹、空气吹净五段循环生产半水煤气。造气的五个阶段阀门的换向,是由计算机控制的,油压为动力完成换成控制操作。出炉水煤气经除尘、洗涤后进入气柜。其中吹风气则进入吹风气回收系统,在燃烧炉内燃烧,铜洗再生气及合成放空气和氨罐驰放气也引入此燃烧炉烧掉,燃烧后高温气经水管锅炉、第二空气预热器、蒸汽过热器、余热回收器、软水加热器、第一空气预热器后通过引风机由烟囱排出主要工艺设备煤气发生炉、空气鼓风机、除尘器、洗汽塔、水管锅炉和余热回收器。物质危险性火灾爆炸危险性造气单元所
9、产水煤气中含有易燃易爆气体,如H2、CO、H2S、CH4等,它们与空气混合达燃爆极限,遇到火源则发生火灾爆炸。中毒危险CO、H2S是毒性物质,当煤气泄漏,在空气中CO、H2S浓度达到30mg/m3、10mg/m3时。则产生急性中毒,严重者导致死亡。腐蚀危害煤气中H2S和CO2是腐蚀性气体,作用于设备、容器、管件、阀门会达成腐蚀。轻则造成内漏外漏,重则使设备强度大大降低,压力波动时可能造成物理爆炸。漏出的可燃气体和有毒气体又增加了火灾爆炸和中毒的危险性。生产工艺及设备引发的危险性造气中的吹风、上吹、下吹、二次上吹、空气吹净五段循环是由油压缩机自动控制进行均连续工艺过程。造气工段易发生中毒和爆炸,
10、主要由于人员的违章检修。发生事故的部位主要在鼓风机及空气总管、煤气发生炉水夹套及炉口、洗气箱和洗气塔。鼓风机鼓风机是将空气送入煤气发生炉的设备,正常情况下工作介质为空气,无爆炸危险。但当因停电、跳闸等原因停车后,煤气发生炉处于造气状态,且阀门大多内漏,特别是当洗气箱、 局部堵塞阻力增大煤气憋压时,更易内漏进入空气总管和鼓风机中。开车时鼓风机产生火花或检修作业违章动火引起爆炸。鼓风机噪声也危害健康。空气总管危险性同鼓风机。煤气发生炉水夹套制造水夹套材质缺陷或焊接不合格,加上使用中的腐蚀使加讨强度降低、当违章操作如蒸汽出口阀关闭后忘记打开,安全阀存在故障时,易发生超压爆炸事故。特别是夹套严重缺水,
11、内壁高温情况下,突然加入大量冷水、急剧气化、蒸汽憋压引起爆炸;同时高温内壁突然加水急冷产生冷缩应力也极易使内壁破裂,造成水流入炉内,又将引发炉膛爆炸事故。洗汽塔煤气夹带杂物使洗汽塔局部堵塞,系统阻力增大、煤气憋压,易从内漏的阀门回流至空气总管和鼓风机,引起总管及风机爆炸。洗汽塔检修时,若不隔绝、不置换或置换不彻底,也不进行气体分析,入内检修则易中毒,若动火或机械火花可引起爆炸。此外,本单元机械电气设备在排除故障及检修作业时还存在机械伤害、触电等危险;在高处作业中,当缺少安全防护措施或措施不当或由于违章等原因还可发生高处坠落事故。6.2 煤气气柜单元气柜储存半水煤气,具有均衡负荷的缓冲、煤气均因
12、混合及分离灰尘等作用。单元危险、有害因素辨识:(1)本单元危险物质是煤气,其易燃、易爆、易中毒的危险危害同造气单元的分析。(2)生产工艺及设备引发的危险性:气柜能发生爆炸事故原因主要有:正常生产中煤气阀杆脱落,致使吹风时空气直接通过下行阀进入气柜,导致气柜中氧气含量过高,达到爆炸极限范围,当水封严重缺水情况下,炉内热煤气进入柜内引起爆炸;或者在气柜检修时因为未置换或置换不彻底或直接用空气进行置换,均使气柜中可燃气在爆炸范围内,不做气体分析情况下违章动火引起爆炸。本单元中中毒事故,多发生在气柜水封井,为调正或开、关溢流阀而下到水封井内,不带防毒面具或佩带不合格的面具,而导致煤气中毒。气柜是厂内危
13、险源之一,应强化安全管理,制定并严格执行安全检查制度、安全检修制度、动火票制度并认真做好煤气化验,杜绝不合格煤气入柜,以保证安全生产。6.3 压缩单元(1)氮氢压缩是为变换、变脱、铜洗、合成氨提供相应工艺压力的工段。(2)主要设备:氮氢气压缩机(3)单元危险、有害因素辨识物质危险危害性与造气、脱硫相同工艺危险性增加。高压情况下,易燃易爆物质爆炸范围变宽;高压增大泄漏的可能性,一旦泄漏可形成爆炸混合气;高压泄漏流速大,磨擦强烈易产生静电火花能自己引爆。设备危险性压缩机如果出现压缩机一段进口负压,则易形成煤气系统吸入空气,易引发爆炸事故;利用空气试压试漏,开机太久冷却不好,管道积碳遇高温易发生爆炸
14、;试压时若连接阀门未脱开,没插盲板易造成煤气与空气混合发生爆炸;违章带压拆卸零件易使高压气窜入低压部位,造成爆炸事故及中毒与火灾。压缩机泄漏,机房通风不好,可燃气及有毒气体喷出,易形成混合爆炸气体,遇火源会发生爆炸事故或人员中毒事故。此外,压缩机长期高压告诉运行,若润滑不好或水冷却不够和长期疲劳应力作用下,可能发生机械零部件损坏事故。此外压缩机噪声危害较大。天车天车机械电气失灵或故障,或操作不熟练,上下配合不好,或者违章驾驶等原因,易发生起重伤害;天车故障,人员检修时常登高,不小心或者安全措施不当,易发生高处坠落事故。6.4 脱硫(1)工艺简介脱硫包括变换前脱硫和变换后脱硫两部分。变换前脱硫是
15、用PDS法脱除半水煤气中的硫化氢,其工艺流程为:从气柜来的半水煤气经静电除焦器除去焦油等杂质,由罗茨鼓风机加压送至冷却塔,将气体温度降至35左右,再进入脱硫塔底部与自塔顶喷淋而下的脱硫液逆流接触,以脱除其中的硫化氢,净化气自塔顶引出经电捕焦油器除焦油后送入氮氢压缩机。脱硫塔底部出来的含硫富液,经再生泵打到喷射再生槽进行再生,再生贫液回脱硫塔顶部循环使用。由再生槽溢流的硫泡沫,经硫泡沫槽送至熔硫釜由蒸汽加热熔融,送入硫磺锭模冷却成型得副产品硫磺。(2)主要设备罗茨鼓风机、电捕焦油器、再生槽冷却塔、脱硫塔、变脱塔、活性碳脱硫槽、熔硫釜。(3)单元危险、有害因素辨识物质危险性主要是半水煤气中的H2、
16、CO、CH4、H2S等易燃、易爆、易中毒并具有腐蚀性的气体,其危险危害同造气单元。设备及工艺危险性A、罗茨鼓风机当造气因故障产生气量减少,工作人员未发现,前后联系不够,未及时减量,则罗茨鼓风机将煤气系统抽成负压,可能会从多个部位吸入空气,使煤气成为爆炸气体混合物,遇火源则发生爆炸。检修罗茨风机时若不隔绝、不置换、不做气体分析,冒然进入则易发生煤气中毒,违章动火则发生爆炸。此外罗茨鼓风机还存在噪声危害。B、熔硫釜该设备属压力容器,若材质缺陷,夹套焊接质量差或严重腐蚀,则超压易发生爆炸事故。C、脱硫塔检修时不隔绝,不置换或置换不彻底,也不做气体分析,入塔检修可发生煤气中毒或动火爆炸事故。直接使用空
17、气置换易发生爆炸。D、检修脱变塔、焦碳过滤器、其水分离器、电捕焦油器、冷却塔等设备中的中毒和爆炸危险性与脱硫塔相似。6.5 变换与脱碳(1)工艺简介变换是将煤气中的CO转化成CO2的过程,脱碳是将CO2从煤气中分离出来。变换工艺流程为:压缩机二段来的半水煤气进入焦碳过滤器,除杂质后进入热水塔饱和段,后经主热交换器换热升温至310330,进入中温变换炉,CO与水蒸气进行变换反应放出大量热。出中变炉气体,经注热交换器及一段冷却器冷却至200左右进入低变炉上段,变换反应后气体由上段出,经二段冷却后进低变炉下段进一步变换,出下段的变换气经换热、冷却、分离后送变换气脱硫。 脱碳工艺为:变脱后原料气由氮氢
18、压缩三段送至气气换热器,降温达12,经分离器分离液滴后送入吸收塔底部,由下而上与顶部喷淋NHD溶液逆流接触,变换气中大部分CO2被吸收,塔顶出气经净化器分离器除沫后,送气气换热器换热升温达30返回氮氢压缩四段,加压后送铜洗。吸收了CO2的富液,由塔底出,减压后依次经氨冷器、高压闪蒸、低压闪蒸后经富液泵来提压送至气提塔顶部由上而下与塔底部送入空气逆流接触进行传热传质,其CO2被气提出来,气提后贫液经贫液泵加压达2.2MPa,经氨冷器冷却后返回吸收塔顶部循环使用。高压闪蒸气返回压缩机一段,低压闪蒸气经气气换热器达到30后送CO2压缩一段(2)主要设备饱和热水器、中温变换炉、低温变换炉、吸收塔、气提
19、塔、脱水塔、泵、鼓风机等。(3)单元危险有害因素辨识A、物质危险性同前所述。B、工艺危险性本单元中变换温度一般为400500左右。有些设备工作压力也较高。如吸收塔及塔前换热器等为1.6MPa;高压闪蒸槽为0.6MPa。带压增加了危险性,使易燃易爆和腐蚀危险性增强。C、设备危险性饱和热水器该设备为压力容器,因材质或制造质量问题特别是焊接质量问题,使用中冲刷腐蚀严重,一旦承受不了工作压力时,则发生物理爆炸,也可能引发化学爆炸。检修作业时,不隔绝、不置换、不做气体分析而违章动火,可能引发爆炸。中(低)变换炉该设备为压力容器,因材质或制造缺陷及使用中开停车的温度骤变,常引起管道、人孔等部位泄漏,引发着
20、火爆炸。煤气中氧气含量过高,可发生过氧爆炸。人员检修作业不置换清洗进入炉内,则引起中毒或爆炸。吸收塔吸收塔为压力容器,工作压力1.6MPa。若因材质或制造缺陷,或长期超压运行导致疲劳应力,或长期腐蚀作用使塔体强度降低,不能承受其工作压力波动时,易发生物理爆炸并可引发化学爆炸事故。吸收塔检修时,若不隔离、不置换,或虽置换了,但未彻底隔离煤气以及置换不彻底等,违章动火或检修中出现的各种火花,可引发爆炸事故。如果在不卸压或有余压情况下,人员就拆卸零部件,可能导致零件冲出,造成物体打击伤害。气气换热器、净化器分离器、高压闪蒸槽等,亦均为压力容器,其危险性和事故模式和吸收塔相似。6.6 铜洗(1)工艺简
21、介铜洗是合成氨原料气的最后精致,其工艺流程为:压缩五段来原料气经油分离器分出油污后进锅洗塔底部,与塔顶喷淋的铜氨液逆流接触,脱去气体中CO、CO2、H2S、O2、CH4、Ar等,精炼气自塔顶引出经分离器分离夹带的雾滴后送压缩六段加压送合成氨。铜洗塔底部出来的铜洗液经减压后送往再生塔,铜氨液依次经回流塔下加热器、还原器、上加热器、再生器,再生后的铜氨液经化铜桶补铜后,进入下加热器与回流来的铜氨液换热后去铜洗水冷器、氨冷器、过滤器,经高压铜泵打至铜洗塔顶部喷淋。铜洗再生气含CO较多,送吹风气回收工段燃烧炉。(2)主要设备铜洗塔、铜液分离器、氨冷器、氨回收塔、再生塔、再生器等。(3)单元危险有害因素
22、辨识A、物质危险性脱碳后合成氨原料气中H2达74左右,易燃易爆,爆炸下限低,上限高,危险性大。铜氨液及起重所含游离氨对人体有毒害作用,不但对眼睛产生强烈刺激,过量吸入或入口会中毒死亡。B、工艺危险性该单元中高低压交错,如铜洗塔、铜液分离器、铜液泵及其输出部分均为高压(达12MPa)系统,而铜液再生系统为低压,压力只有0.15MPa左右。在铜洗塔液位计冲洗、铜液分离器的排放、铜液泵开停车等关键操作中,一旦操作失误易造成高压串低压,导致着火爆炸事故的发生。C设备危险性铜洗塔该塔为高压设备,工作压力达12MPa,若塔体本身质量缺陷及使用中冲刷腐蚀,长期高压运行,材料疲劳应力等,使强度下降,若不能承受
23、工作压力波动时,则发生塔体爆炸并引发化学爆炸火灾事故。铜洗塔的附件如玻璃液位计或联结用垫片等,因质量缺陷或安装不当以及操作中超压或其他操作失误,会引起液位计破裂或铜氨液泄漏及H2、N2大量喷出,遇火源或静电火花可引发爆炸事故。铜洗塔检修中易出现以下事故:未隔绝、未置换、未做气体分析冒然入塔引起中毒,产生火花及违章动火发生爆炸;在塔未清洗干净的情况下,用空气试压试漏发生爆炸;系统检修后,塔内充满空气,未进行置换就用原料气试压试漏发生爆炸。检修作业带余压情况下拆卸零部件,零部件冲出击人导致伤害。铜液分离器为高压设备,其危险性同铜洗塔。高压铜泵该设备为高压运转机械,它所连接的阀门、法兰、垫片及高压螺
24、栓等,因质量问题、长期腐蚀、疲劳应力等强度下降,不能承受相应压力时断裂或爆破,铜洗液及N2、H2大量喷出,告诉气流导致静电火花或其它火源引发化学爆炸,也易导致中毒。再生塔、回流塔、再生器、还原器、氨回收塔等,检修中毒或火灾爆炸事故,原理同前。6.7 合成氨(1)工艺简介合成氨是合格的N2、H2原料在高温高压催化剂作用下于合成塔内合成的。(2)主要设备合成塔、循环气加热器、废热回收器、软化水加热器、冷交换器壳程、NH3冷凝器、NH3分离器、循环机、氨水泵等。(3)单元危险、有害因素辨识物质危险性本单元危险性物质为H2和NH3,NH3具有火灾爆炸危险性和毒性危害。工艺危险性A、存在高温高压危险系统
25、压力达31.4MPa,温度为450500。高温高压使危险性增加,如:腐蚀加剧,特别是氮氢腐蚀、金属脱碳,易产生裂纹使强度降低;高温高压下,材料持续塑性变形,使设备易破裂;易产生泄漏,且泄漏速度增大,高速喷出磨擦产生静电火花,极易自身引爆。B、系统内高压低压并存,危险性增大合成NH3压力为30MPa左右,NH3分离系统压力为1.6MPa,违章或操作失误,易造成高压串低压,引起爆炸事故。C、设备内高低压并存同一个设备内不同部位存在不同压力,如合成塔、氨冷器等。均可高压串低压,造成设备损坏人身伤亡事故。设备危险性A、氨合成塔合成塔内套因制造质量差、试压时升压过快或超过所承受的最大压力时,可发生那套爆
26、炸事故。合成塔因制造质量上的缺陷,长期运行腐蚀严重,他别是违章超温超压条件下的氢腐蚀,使金属材料强度降低,当不能承受其工作压力波动时,则会发生合成塔塔体爆炸事故。合成塔顶部因可燃气体泄漏,引发着火事故。在不泄压、不隔绝、不置换情况下,打开塔顶盖检修时,因可燃气喷出(带有触媒)触媒氧化着火引发爆炸事故。B、氨分离器氨分离器因液位计质量差或安装不当,包括垫片质量差,或者因升压过快等原因可发生超压爆炸或泄漏,大量NH3等可燃气体喷出,因静电火花等火源可引发爆炸事故。还可导致中毒伤害。操作违章还可能使氨分离器高压气串低压,输氨管道发生超压爆炸,NH3及易燃大量喷出导致火花爆炸或中毒。C、循环机高压运转
27、设备,因材质差或质量缺陷以及长期重负荷超压运行的疲劳应力,螺栓松脱等,主要部件(如活塞杆、压盖)遭到破坏或断裂,导致高压可燃气喷出,遇机械火花或静电火花等引发爆炸事故。操作不当也可引发爆炸事故。D、NH3冷凝器、冷交换器、循环器加热器等,均为压力容器,若因材质或制造质量上的问题或长期在冷、热应力作用下以及腐蚀等因素,使其强度减低,可能因超压产生物理爆炸并引发二次化学爆炸,大量NH3在空气重可能使人中毒。设备若带压拆卸,零部件可导致物体打击伤害;不隔绝、不置换情况下动火施焊,可能发生火灾爆炸;在高处检修,有高处坠落危险等。6.8 液氨储罐在厂东边偏南位置,设置有6台卧式储罐,起重3台储罐单罐容积
28、为100m3,3台储罐单罐容积为48m3。罐区最大储量约为260t,根据国家标准重大危险源辨识(GB18218-2000),该罐区储存的液氨量超过规定的临界量(100t),因此该罐区为重大危险源。储罐北面和东西为厂外空地,南邻冷冻站。最高储存压力为2.2MPa。贮罐贮存的是过热液氨,当温度和压力增大时,超过罐体强度极限,有可能发生物理爆炸。罐体破裂泄漏出的液氨,闪蒸成氨气体,若遇火源会发生火灾爆炸,也可发生氨气中毒。贮罐和液氨输送管道及管件因腐蚀或制造质量差等原因,有可能发生泄漏,会发生氨中毒;当液氨喷射到人的皮肤上,会发生灼烫伤害。6.9 粗醇合成(1)工艺简介粗醇合成是利用氨合成原料气中的
29、CO和H2在1213MPa、催化剂作用下的醇合成塔内合成CH3OH。同时进行的有换热、分离过程,甲醇(粗)进入粗醇贮槽。(2)主要工艺设备甲醇合成塔、甲醇水冷器、甲醇分离器、油水分离器、水洗塔、中间粗醇贮槽和点机。(3)单元危险有害因素辨识物质危险性甲醇生产过程所设计到的易燃气体和液体有CO、CH3OH等,它们与空气混合达爆炸极限时,遇相应激发能或点火能则发生火灾、爆炸。亦可导致人员中毒或死亡。设备引发的危险性本单元设备设施中压力容器较多,如甲醇合成塔、甲醇水冷器等,若因材质或制造缺陷,或长期超压运行疲劳应力,或长期腐蚀作用使塔体轻度降低,不能承受其工作压力波动时,发生物理爆炸并可引发化学爆炸
30、事故。合成塔检修时,若不隔离、不置换、或虽置换了,但未彻底隔离煤气以及置换不彻底等,违章动火或检修中出现的各种火花,可引发爆炸事故。如果在不卸压或有余压情况下,人员就拆卸零部件,可能导致零件冲出,造成物体打击伤害。此外,本单元机械电气设备在排除故障及检修作业时还存在机械伤害、触电等危险;在高处作业中,当缺少安全防护措施或措施不当或由于违章等原因还可发生高处坠落事故;本单元设备产生的噪声较大,对健康有害。7.0 尿素装置概况及危险有害因素辨识为便于进行评价,根据工艺特点和实际情况,可将该尿素项目划分为二氧化碳压缩与净化、尿素合成、造粒及包装等单元。7.1 二氧化碳压缩与净化单元(1)工艺简介来自
31、脱碳工段的二氧化碳(温度低于35,压力为0.1004MPa,纯度98.5干基体积,含硫化氢110mg/Nm3),与罗茨鼓风机送来的空气混合后,经压缩、净化使气体中的硫化氢降低至10mg/Nm3以下,并将压力提高到20.7MPa温度,约125送往尿素合成塔。(2)主要设备二氧化碳压缩机组,气水分离器、过滤器、脱硫槽、废油澄清槽、罗茨鼓风机、桥式起重机。(3)单元危险、有害因素辨识二氧化碳压缩机1压缩机的旋转和往复直线运动或摆动的零部件,如防护不当具有机械伤害的危险。压缩机运行过程中,如压缩介质组份发生重大变化,润滑或冷却信通出现故障,可使设备局部过热、超压;若连锁控制、安全阀出现故障,可能造成设
32、备损坏(如烧瓦、传动零件断裂和缸体破坏等)及人员伤亡事故。2输气管线及净化设备由于安装不合格或因腐蚀、超压而破裂,发生二氧化碳,硫化氢泄漏,可引起人员窒息或中毒伤害。3在设备安装、运行和维修时,使用起重设备过程中,因设备缺陷或操作失误等,均可能发生挤压、碰撞及砸伤工作人员的起重伤害事故。4压缩机、鼓风机运转过程中,会产生较大的噪声。7.2 尿素合成、造粒及包装单元(1)工艺简介本单元以二氧化碳(加入0.5的氧)和氨为原料,采用改进型水溶液全循环法生产尿素,熔融的尿素送往造粒塔造粒,而后送至包装贮存。(2)主要设备尿素合成塔、预蒸馏塔、二分塔、尾吸塔、尿素造粒塔、中立自流式单称包装机、胶带输送机
33、、手动单梁起重机。(3)单元危险有害因素辨识工艺危险性尿素合成是压力为19.7MPa,温度为188条件下实现合成的。高温下的高压介质增加了危险性。设备装置的危险危害A、尿素合成塔、预蒸馏塔、一吸塔尿素合成塔压力达20MPa,预蒸馏塔及一吸塔承压约1.8MPa。因制造缺陷、使用中腐蚀、超压等,一旦压力超过材料承受极限则存在爆炸可能性。爆炸时将有尿素、NH3、CO2、甲胺等泄漏,造成氨装独或引发二次爆炸火灾事故,而高温尿素等介质还可引起灼烫。B、尾吸塔、氨水泵液氨泵出口压力达22MPa,属高压机泵、泵体及其部件、出口管线、管件、阀门等,若损坏或破裂,则NH3喷出导致NH3中毒或引发二次爆炸火灾。C
34、、尾吸塔、氨冷器在尾吸塔内,为其主成份一般为NH3、H2、O2,若遇到气流冲击静电火花或放空气流遇雷电激发而回火等,可引起爆炸事故。氨冷器等如果操作条件控制的不合适,也可形成爆炸性气体,发生爆炸事故。D、手动单梁起重机、电动葫芦因电气、机械故障、操作失误或指挥联络不当,可发生起重伤害。此外还有高处坠落和触电伤害、机械伤害等,尿素粉尘进入眼及肺部对人有害。8.0 生产工艺及其变更情况8.1 合成氨工艺合成氨经技术改造后,仍以山西白煤和京西煤为原料,经煤气发生炉固定层煤气化造气、PDS法脱硫、低硫低温变换、PDS法及活性碳法变换气脱硫、NHD法脱碳、铜洗法净化、中压下合成氨。(1)粗醇合成利用氨合
35、成原料气中的CO和H2在1213MPa,催化剂作用下的醇合成塔内合成CH3OH。同时进行的有换热、分离过程,甲醇(粗)进入粗醇贮槽。(2)造气进厂白煤经破碎过筛合格,称重后送入吊煤斗、再用电动葫芦提升至煤气发生炉顶上的加料斗,均匀的加入炉内,以供制气。制气分吹风、上吹、下吹、二次上吹、空气吹净五个阶段进行。(3)半水煤气脱硫气柜来的半水煤气先经焦碳过滤器,除去焦油等杂质,由罗茨鼓风机加压送至冷却塔将气体温度降至35左右再进入脱硫塔底部,与自塔顶喷拼而下的脱硫液逆流接触,以脱除其中的硫化氢,净化气自塔顶引出经电捕焦油除去其中的焦油后送入氮氢气压缩机。(4)氮氢气压缩由电捕焦油器来的半水煤气,经气
36、水分离器分离水分后进入压缩机一段气缸,经一、二段压缩至0.8MPa左右送往变换工段,变换后的气体再经变换气脱硫脱除硫化氢后进入压缩机三段,三段出口气体压力达到1.8MPa左右经冷却分油水后进入二氧化碳脱除装置,脱除二氧化碳的气体进入压缩机四、五段压缩,压力升至12MPa冷却分离油水后进入氨合成工段。(5)交换由氮氢气压缩机二段出来的半水煤气经冷却器降温口进入焦碳过滤器,分离油水并过滤油尘,然后经饱和塔增湿,预腐蚀器分离带水并提温,后经热交换器和电加热器提温后进入1低变炉,经一段催化剂层变换后引出,在1喷水罐增湿,降温并补加一定量的蒸汽后返回1低变炉二段催化剂层,继续进行交换反应,然后出1低变炉
37、,依次经过热交换器,预腐蚀器,在2喷水罐内调温,增湿后经电加热器送入2低变炉,再进行交换反应,出2低变炉的气体经第一加热器、热水塔、第二水加热器、冷却塔后,作为合格的变换气送至下一工段。(6)变化气脱硫从变换来的低变气,压力0.7MPa温度40左右进变换气脱硫塔底部与自上而下的脱硫液喷淋接触,进行逆流吸收反应,将低变气中的硫化氢脱至20mg/Nm3以下脱硫后的气体由塔顶出来经气液分离器分离出来的液滴后在经活性碳槽将气体中硫化氢脱至10mg/Nm3去压缩工段。脱硫后的富液由塔底出来减压后送至半水煤气喷射再生系统回收硫磺。再省溶液由泵加压后送入变换气脱硫塔循环使用。(7)脱碳由氮氢气压缩机来的1.
38、7MPa(绝压)的变换气,经气水分离器后由吸收塔底部进入,与塔顶喷淋而下的碳丙液逆流接触,变换气中绝大部分二氧化碳被碳丙液吸收,含CO20.5的净化气经丝网除沫后由吸收塔顶部引出,经净化气分离器后进入闪蒸洗涤塔的净化气洗涤段,在此用含碳丙10的稀溶液将气相夹带的碳丙洗涤回收,出净化气洗涤段的净化气送至氮氢压缩机工段。(8)铜洗工段由氮氢压缩机来的原料气经油分离器分离油污后进入铜洗塔底部,与喷顶喷淋而下的铜氨液逆流接触,脱去气体中的微量一氧化碳、二氧化碳、硫化氢、氧气等,精炼气自铜洗塔顶部引出,经分离器分离夹带的雾滴后送回氮氢压缩机。(9)氨合成从氮氢气压缩机六段出来的精致气经冷却水分离水油后补
39、入到氨冷器进口,与循环器一期进入氨冷器,在氨冷器中,循环器所含的氨及新鲜气中所含的油水被冷凝下来,然后进入冷交换器二次进口,在冷交换器中冷凝下来的液氨,油水等被分离下来,分离后的气体进入循环机补充压力后经油分离器分离气相中所含的油污后进合成塔依次入口,沿合成塔一次入口,沿合成塔外壳与内筒的环隙自上而下温度约升至6080从合成塔下部出来进入循环预热器与软水加热器来的热气换热,换热后的气体再进入合成塔,经塔内换热器与合成后的气体换热后进入触媒层进行N23H22NH3的反应,热软水去废热回收器。从软水加热器出来的气体再经循环预热器水冷却到36左右进入氨分离器分离出冷凝下来的液氮后进冷交换器与氨蒸发来
40、的循环气进行换热后与新鲜空气混合重复上述循环。氨分离器及冷交换器分离的液氮节流后送往氨贮罐。该生产工艺成熟,无工艺变更。8.2 尿素生产工艺尿素生产采用水溶液全循环法流程。脱碳来的二氧化碳经压缩、净化后和液氨及循环回收的甲液一期送入尿素合成塔再19.7MPa压力和188温度下进行合成,尿素以熔融状态自塔顶流出后经分离、闪蒸、回收、蒸发、蒸馏、造粒的尿素产品,包装入库。(1)二氧化碳压缩来自脱碳工段温度小于35,压力为0.10049MPa(绝压),纯度98.5(干基体积)的二氧化碳气体与罗茨鼓风机送入的空气混合后,气体(二氧化碳95.7干基体积),经水气分离器分离出水滴,然后进入二氧化碳压缩机、
41、经一、二段压缩0.901.050MPa(绝压)冷却、除油、除水后,送往二氧化碳净化脱硫塔、经活性碳脱硫后,净化气返回二氧化碳压缩机,经三、四、五段压缩到20.7MPa(绝压)约125送往尿素合成塔。(2)二氧化碳净化来自二氧化碳压缩机二段出口含硫化物约110mg/Nm3粗二氧化碳气体,进入两个串联的活性碳脱硫槽;将气体中的硫化物脱至10mg/Nm3以下,硫化物转变成元素硫,附着在活性碳上,净化后气体去二氧化碳压缩机三段入口,净化气中硫化物含量大于10mg/Nm3时,切换脱硫槽,更换新活性碳脱硫剂,含硫的活性碳掺入燃烧煤中作燃料或外售。(3)氨的输送及尿素合成来自液氨贮罐的32,2.05MPa(
42、绝压)的原料液氨经液氨过滤器过滤,流量计记录流量后进入液氨缓冲槽的原料室,来自氨冷凝器的循环液氨进入液氨缓冲槽的回流室,其中一部分越过当班与原料氨混合后,经液氨泵加压至约20.69MPa(绝压)送往氨预热器,被蒸汽冷凝液加热至70进入尿素合成塔。缓冲槽回流室的液氨作为一吸塔的回流氨。原料二氧化碳气体、液氨,循环回收工序来的一甲液同时送入尿素合成塔,再约19.7MPa(绝压),188的合成条件下,经足够的停留时间,约有63的二氧化碳转化为尿素,反应熔融物自塔顶排出,尿素合成塔压力由出口压力调节阀控制。(4)循环回收尿素合成塔的反应融融物经出口压力调节阀减压至1.77MPa(绝压),进入预蒸馏塔上
43、部,在此分离出闪蒸气体后,溶液自流至中部蒸馏段,与一段加热器来的热气体逆流接触,进行换热蒸馏,使液相中的部分甲胺与过剩氨分解,气化进入气相,同时,气相中的水蒸气部分冷凝,尿液自蒸馏段下部流往一分加热器,在蒸汽的加热作用下,约88的甲胺在此分解,约155160气液混合物自一分加热器上升至预蒸馏塔底部分离为两相,液相自塔底排出,经减压送往二分塔,气相自下而上地通过蒸馏段自塔顶排往蒸发器热能回收段。一段分解系统所需的防腐空气自空压机提供,空气自一份加热器尿液入口管道上补入。来自预蒸馏塔的气体预二甲液在一段蒸发器热能回收段混合,发生部分冷凝,放出的热量用于加热尿素溶液。热能回收排出的气液混合物进入一吸
44、冷却器底部,在循环冷却软水的冷却作用下,气体进一步发生冷凝。出一吸冷却器的气液混合物进入一吸塔底,气相经鼓泡吸收后,未吸收的气体进入精洗段被来自惰洗器的浓氨水与来自液氨缓冲槽的回流氨进一步精洗吸收,塔顶排出的约50,含二氧化碳100ppm的氨气进入氨冷凝器(B),部分氨气在此被冷凝下来流往液氮缓冲槽。出氨冷凝器(B)的气体经惰洗器防爆空间后,进入氨冷凝器(C),在此冷凝下来的液氮也流往氨缓冲槽,未冷凝气体送至惰洗器,被来自二循二冷凝器的氨水吸收,为其减压送至尾吸塔。惰洗器排出的45氨水送往一吸塔顶部,一吸塔底部将得到约9095的一甲液经一甲泵加压送往尿素合成塔。预蒸馏塔底部排出的尿液减压至0.
45、290.30MPa(绝压)后,送入二分塔上部的填料段,与来自二分塔加热段的气体逆流接触后进入加热段,被蒸汽加热到135140,尿液中残留过剩氨与甲胺基本在此气化分解进入气相。出加热段的气液混合物经分离后,尿液减压送往闪蒸槽,气体经填料段后自二分塔顶排出,与来自解吸系统的解吸气混合后进入二循一冷凝器,被蒸发冷凝液吸收,生成的二甲液由二甲泵送往一段蒸发冷凝液吸收,生成额氨水由氨水泵送往惰洗器,尾气去尾吸塔。惰洗器尾气与二循二冷凝器尾气混合后由尾吸塔底部进入,被来自尾吸泵的蒸发冷凝液吸收,生成的碳铵液送至碳铵液槽贮存。尾气通过放空总管放空。(5)尿液加工二分塔排出的尿液减压至约0.044MPa(绝压
46、)后进入闪蒸槽,在此分离为气液两相,约90,71(重量)的尿液排往一段蒸发加热器,尿液经热能回收段和蒸汽加热段被加热到130,浓度约为96(重量)。在一段蒸发器分离段分离出的尿液去二段蒸发器,在0.0033MPa(绝压),140下被浓缩到约99.7(重量)的熔融尿素,经分离段分离后,熔融尿素由熔融泵送往位于造粒塔顶部分旋转喷头进行造粒。造粒塔底部得到的成品颗粒尿素由胶带输送机送至包装楼称量包装。当蒸发系统操作不正常时,从闪蒸槽出来的尿液可暂贮存在尿液槽,等蒸发造粒系统正常后,由尿液泵送入一段蒸发器。闪蒸气与一段蒸发气均送至一段蒸发冷凝器冷凝,未凝气由一段蒸发喷射器抽至放空总管放空。二段蒸发气先
47、进入二段蒸发水冷凝器冷凝,未凝气体进入二段蒸发冷凝器进一步冷凝,未凝气由二段蒸发喷射器(A)抽至中间冷凝器冷凝,未凝气自二段蒸发喷射器(B)抽至放空总管放空。二段蒸发冷凝器以从冷冻工段来的液氨作为冷冻介质,液氨吸热气化后,气氨返回冷冻工段。(6)工艺冷凝被分配及解吸碳铵液槽分为一段蒸发冷凝液室、碳铵液室。二段蒸发冷凝液贮存于二表槽,由蒸发冷凝液泵送往二循一冷凝器与二循二冷凝器,其不足部分引碳铵液槽之一段蒸发冷凝液以补充。一段蒸发冷凝液与中间冷凝器冷凝液贮存于一段蒸发冷凝液室,除部分补入二表槽外,其余全部由尾吸泵送至尾吸塔顶作为吸收液,尾吸塔底部得到的碳铵液室贮存,系统各处的排放液也送入碳铵液室
48、。碳铵液由解吸泵送至解吸换热器,与来自解吸塔底部的废液进行换热后进入解吸塔上部,经塔盘蒸馏后,塔顶将得到的NH3CO2H2O混合气体进入解吸冷凝器,在此部分冷凝,冷凝液返回解吸塔顶作为回流液,气相去二循一冷凝器,解吸塔底部约145,含氨0.12(重量),含尿素0.7(重量)的废液经解吸换热器回收热量后排在污水处理装置。解吸冷凝器的操作是根据解吸负荷及工艺生产系统的水平衡情况,通过改变进入解吸冷凝器的软水流量来调节解析气的温度,控制解析气的冷凝程度,湿的随解吸气返回生成系统的水量得到适宜的控制。(7)蒸汽及蒸汽冷凝液1.275MPa(绝压)的饱和蒸汽来自锅炉房,经调节阀稳压并分离出来分后进入各加
49、热设备及各蒸发喷射器。来各自加热设备的1.275MPa(绝压)的蒸汽冷凝液,进入冷凝液膨胀槽,产生约0.39MPa(绝压)的饱和蒸汽,作为中低压工艺系统的保温蒸汽。保温蒸汽不足部分通过压力调节阀向冷凝液膨胀槽引入1.275MPa(绝压)蒸汽。冷凝液膨胀槽排出的蒸汽冷凝液送往氨预热器作为加热热源,然后排至蒸汽冷凝液槽。各楼层的保温蒸汽冷凝液也收集于蒸汽冷凝液槽。蒸汽冷凝液槽的蒸汽冷凝液由蒸汽冷凝液泵加压,部分送至生产系统使用,其余经导电仪自动分析后送锅炉房。(8)冷却水来自尿素循环水装置的冷却水,温度32,压力0.593MPa(绝压),经上水总管分配去各冷却设备,各冷却设备的回水排入下水总管。离开尿素界区的温升约6,压力约0.294MPa(绝压)的冷却水返回尿素循环水冷却塔。(9)成品包装贮运从尿素造粒塔底部漏斗下来的颗粒尿素,通过溜管到皮带输送机送至包装楼的尿素贮斗贮存。再通过溜管至自动包装机,自动称量,机器缝袋后,运至成品库码垛贮存待运。该生产工艺成熟,无工艺变更。
- 温馨提示:
1: 本站所有资源如无特殊说明,都需要本地电脑安装OFFICE2007和PDF阅读器。图纸软件为CAD,CAXA,PROE,UG,SolidWorks等.压缩文件请下载最新的WinRAR软件解压。
2: 本站的文档不包含任何第三方提供的附件图纸等,如果需要附件,请联系上传者。文件的所有权益归上传用户所有。
3.本站RAR压缩包中若带图纸,网页内容里面会有图纸预览,若没有图纸预览就没有图纸。
4. 未经权益所有人同意不得将文件中的内容挪作商业或盈利用途。
5. 装配图网仅提供信息存储空间,仅对用户上传内容的表现方式做保护处理,对用户上传分享的文档内容本身不做任何修改或编辑,并不能对任何下载内容负责。
6. 下载文件中如有侵权或不适当内容,请与我们联系,我们立即纠正。
7. 本站不保证下载资源的准确性、安全性和完整性, 同时也不承担用户因使用这些下载资源对自己和他人造成任何形式的伤害或损失。