《铸锭缺陷》PPT课件
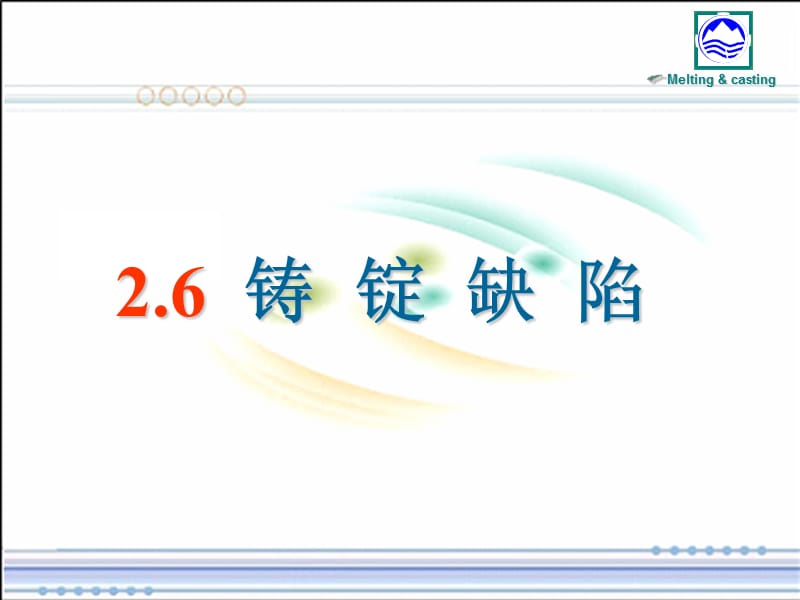


《《铸锭缺陷》PPT课件》由会员分享,可在线阅读,更多相关《《铸锭缺陷》PPT课件(21页珍藏版)》请在装配图网上搜索。
1、2.6 铸 锭 缺 陷,本章内容要点,铸锭偏析组织; 铸锭缩孔与疏松缺陷; 铸锭裂纹缺陷; 铸锭冷隔; 铸锭夹杂。,本章目录,2.6.1 铸锭偏析 (1) 晶内偏析 (2) 晶界偏析 (3) 正偏析与反偏析 (4) 偏析瘤 (5) 防止偏析的方法 2.6.2 铸锭的缩孔与疏松 (1) 金属的凝固收缩 (2) 缩孔与疏松的形成 (3) 影响缩孔与疏松的因素 (4) 防止缩孔与疏松的措施,2.6.3 铸锭裂纹 (1) 铸造裂纹的形成过程 (2) 热裂纹 (3) 冷裂纹 (4) 防止裂纹的途径 2.6.4 铸锭冷隔 (1) 冷隔的特征 (2) 冷隔的形成 (3) 冷隔的危害 (4) 防止冷隔的途径,
2、2.6.1 铸锭偏析 偏析是合金凝固过程中,溶质的再分配及晶体长大速度大于溶质扩散速度,使先析出的固相与液相的浓度不同所致。偏析,微观偏析,宏观偏析,晶内偏析,晶界偏析,比重偏析,正偏析,反偏析,(1) 晶内偏析 晶内偏析的影响因素: (a)冷却速度; (b)偏析元素的扩散能力; (c)液固相线间隔。,A,B,液相线,固相线,C0,a1,a2,a3,L1,L2,L3,固溶体不平衡结晶示意图,a1,a3,a2,(2) 晶界偏析 是溶质元素在晶界堆积的结果,主要原因是: (a)液固相溶质分配系数的不同; (b)形成化合物。,晶界偏析形成过程示意图,(3) 比重偏析 其形成原因是: (a)液相分层;
3、 (b)固相与液相比重不同。,(4) 正偏析与反偏析 其形成原因是: (a)溶质分配系数K的不同, K1时,后结晶的固相溶质含量低,出现正偏析; (c)同时,与粗大的枝状晶有关。,(5 )偏析瘤 是一种严重的反偏析现象,通常在铸锭的表面出现偏析瘤。,锡青铜中偏析瘤的形成 过程,(a)形成枝晶,(b)出现间隙,(c)富锡熔体外溢,锡偏析瘤,枝晶,出现间隙,铸模,铸模,铸模,(6 )防止偏析的方法 偏析是凝固过程中溶质再分布的结果。因此,一切能使成分均匀化和晶粒 细化的方法,均有利于防止或减少偏析。 基本措施有: 增大冷却强度, 搅拌,变质处理,采用短结晶器,降低浇注温度,加强二次水冷,使液穴浅平
4、等。,2.6.2缩孔与疏松 (a)概念:在铸锭中部、头部、晶界及枝晶间等地方,常常有一些宏观和显徽的收缩孔洞,通称为缩孔。 细小而分散的缩孔称为分散缩孔或缩松。 (b)危害:缩孔或缩松都会减小铸锭受力的有效面积,并在缩孔和缩松处产生应力集中,因而显著 降低铸锭的力学性能。 (c) 原因:产生缩孔和缩松的最直接原因,是金属凝固时发生的凝固体收缩。,(1) 金属的凝固收缩 收缩的分类:包括凝固前的液态收缩、由液态变为固态的凝固收缩及凝固后的固态收缩。 液态收缩率为12%、凝固收缩率为27%、固态收缩率为59%。,凝固收缩的开始温度,当温度下降至液相线下的点划线时枝晶数量增多彼此相连构成连续的骨架,
5、此时铸锭中已有55一70的固相,使开始凝固收缩,(2) 缩孔与疏松的形成,缩孔形成示意图,疏松形成示意图,形成原因: 在顺序凝固条件下,因金属液态和凝固 收缩造成的孔洞得不到金属液的补缩而产生 的。,(3) 影响缩孔与疏松的因素(a)金属性质的影响 当温度梯度一定时,合金的结晶温度范围越小,则凝固区越窄,铸锭形成缩孔的倾向越大;反之,结晶温度范围大,则凝固区宽,等轴晶发达,补缩困难,形成缩松的倾向大。,缩孔区,疏松区,液相线,成分,温度,液相线,疏松和缩孔形成示意图,(b)金属浇铸工艺条件的影响,凡是提高铸锭断面温度梯度的措施,如铁模铸锭时,提高浇注温度和浇注速度,均有利于集中缩孔的形成;反之
6、,降低浇注温度和浇注速度,提高模温,则有利于分散缩孔或缩松的形成。,(4) 防止缩孔与疏松的途径,基本途径:是根据合金的体收缩特性、结晶温度范围大小及铸锭尺寸等,制定正确的铸锭工艺,在保证铸锭自下而上顺序凝固条件下,尽可能使分散缩孔或缩松转化为铸锭头部的集中缩孔,然后通过人工补缩来消除。,2.6.3 铸锭裂纹 裂纹分类:根据裂纹的形成阶段分为冷裂纹(凝固后)和热裂纹(凝固过程)。 根据裂纹形状和在铸锭中的位置,裂纹又可分为许多种,热裂纹可分 为表面裂纹、皮下裂纹、晶间裂纹、中心裂纹、环状裂纹、放射状型纹 等;冷裂纹可分为顶裂纹、底裂纹、侧裂纹、纵向表面裂纹等。 (1) 铸造应力的形成,形成的原
7、因,可分为热应力、相变应力和机械应力。,(a)热应力是铸锭凝固过程中因温度变化引起的附加应力。,连续铸锭过程中热应力分布情况,(b)机械应力是铸锭凝固过程中,因受结晶器机械作用而产生的附加应力; (c)相变应力是铸锭凝固过程中,因体变化所产生的附加应力。,(2) 热裂纹的形成机理和影响因素,热裂是在凝固收缩开始温度至非平衡固相线温度范围内形成的。热裂形成机理 主要有液膜理论、强度理论及裂纹形成功理论。,(a)液膜理论,液膜理论示意图,凝固末期晶间残留的液膜 受铸锭收缩影响,液膜在拉应 力作用下被拉伸,当拉应力或 拉伸量足够大时,液膜就会破 裂,形成晶间热裂纹。,(b)强度理论,强度理论认为,合
8、金在线收缩开始温度至非平衡固相点间的有效结晶温度范围,强度和塑性极低,故在铸造应力作用下易于热裂。,(c)形成功理论,裂纹形成功理论认为,热裂通常要经历裂纹的形核和扩展两个阶段。裂纹形核多发生在晶界上液相汇集处。若偏聚于晶界的低熔点元素和化合物对基体金属润湿性好,则裂纹形成功小,裂纹易形核,铸锭热烈倾向大。,(d)影响热裂纹的因素,主要的有金属性质、绕注工艺及铸锭结构等。 其中: 合金的有效结晶温度范围宽,线收缩大,则合金的热裂倾向也大; 浇注温度高,往往提高脆性区上限温度; 提高冷却速度,由于非平衡凝固会改变共晶成分降低共晶温度,因而降低脆 性区下限温度。,可以根据合金的平衡凝固 温度范围大
9、小,粗略估计合金 的热裂倾向大小。成分越靠近 共晶点合金,热裂倾向越小。,当浇注速度及宽厚比n一定时,随着锭厚增 大,热裂倾向增大。 当锭厚一定时,热裂随着浇注速度增大而增 大。,裂纹倾向与冷却速度和铸锭壁厚的关系,裂纹倾向与平衡凝固温度范围的关系,(3) 冷裂纹的形成机理和影响因素,(a) 冷裂的形成机理:是铸锭冷却到温度较低的弹性状态时,因铸锭内外温差大、铸造应力超过合金的强度极限而产生的,并且往往是由热裂扩展而成的。 (b) 影响因素:,合金的导热性和塑性直接影响冷裂纹倾向(合金成分),此外,非金属夹杂物、 晶粒粗大也会促进冷裂。热裂纹的尖端是应力集中处,在铸锭凝固后的冷却过程 中,热应
10、力足够大时,会使热裂纹扩展成冷裂纹。,一切能提高合金在凝固区或脆性区的塑性和强度,减少非平衡共晶或改善其 分布状况,细化晶粒,降低温度梯度等因素,皆利于防止铸锭热裂和冷裂。工 艺上主要是通过控制合金成分,限制杂质含量以及选择合适工艺相配合等方法, 来防止铸锭产生裂纹。,(4 ) 防止裂纹的途径,2.6.4铸造冷隔,(1) 冷隔:是铸锭的表面缺陷,呈弧线形向铸锭中心延伸的裂纹。 (2) 冷隔成因:金属熔体不能均匀地浇注在铸锭上表面时,使新 的熔体在已经凝固的金属表面上,由于氧化层等 影响润湿的因素以及热烈的因素,使后来的金属 不能与下面的金属熔为一体,故出现裂纹。,铸锭,熔池,冷隔,冷隔形态及形
11、成过程,(3) 冷隔的危害:严重破坏铸锭组织的连续性,同时, 在冷隔内存在大量的低熔点化合物,易引起应力集中, 形成裂纹源,使整个铸锭开裂。,(4) 防止冷隔的措施: a-提高浇注温度,增加金属流动性; b-增大结晶器的锥度,使熔体的导热性降低,相对提高熔体温度; c-在浇注过程中,对结晶器内的熔体进行搅拌; d-采用热顶铸造方式。,总结:,1偏析 (1) 晶内偏析 (2) 晶界偏析 (3) 比重偏析 (4)正偏析与反偏析 (5) 偏析瘤 (6) 防止偏析的方法 2缩孔与疏松 (1) 金属的凝固收缩 (2) 缩孔与疏松的形成 (3) 影响缩孔与疏松的因素 (4) 防止缩孔与疏松的途径 3裂纹 (1) 铸造造应力的形成 (2) 热裂纹 (3) 冷裂纹 (4) 防止裂纹的途径,4冷隔 (1) 冷隔的特征 (2) 冷隔的危害 (3) 冷隔的成因 (4) 防止冷隔的途径,铸锭成形方法及设备,有色金属铸锭方法,连续铸锭,不连续铸锭,铁模铸锭,水冷模铸锭,沉浸铸锭,对开模铸锭,平模铸锭,整体模铸锭,立模铸锭,水冷对开模铸锭,水冷整体模铸锭,倾斜模铸锭,无流铸锭,静模铸锭,无模铸锭,动模铸锭,立式铸锭,卧式铸锭(水平铸锭和横向铸锭),辊间铸锭(倾斜式,下注式等),辊模铸锭(CASTEX,Properzi等),链模铸锭,普通滑动结晶器铸锭,特殊铸锭:热顶铸锭等,
- 温馨提示:
1: 本站所有资源如无特殊说明,都需要本地电脑安装OFFICE2007和PDF阅读器。图纸软件为CAD,CAXA,PROE,UG,SolidWorks等.压缩文件请下载最新的WinRAR软件解压。
2: 本站的文档不包含任何第三方提供的附件图纸等,如果需要附件,请联系上传者。文件的所有权益归上传用户所有。
3.本站RAR压缩包中若带图纸,网页内容里面会有图纸预览,若没有图纸预览就没有图纸。
4. 未经权益所有人同意不得将文件中的内容挪作商业或盈利用途。
5. 装配图网仅提供信息存储空间,仅对用户上传内容的表现方式做保护处理,对用户上传分享的文档内容本身不做任何修改或编辑,并不能对任何下载内容负责。
6. 下载文件中如有侵权或不适当内容,请与我们联系,我们立即纠正。
7. 本站不保证下载资源的准确性、安全性和完整性, 同时也不承担用户因使用这些下载资源对自己和他人造成任何形式的伤害或损失。