毕业设计(论文)-主轴制造工艺编制
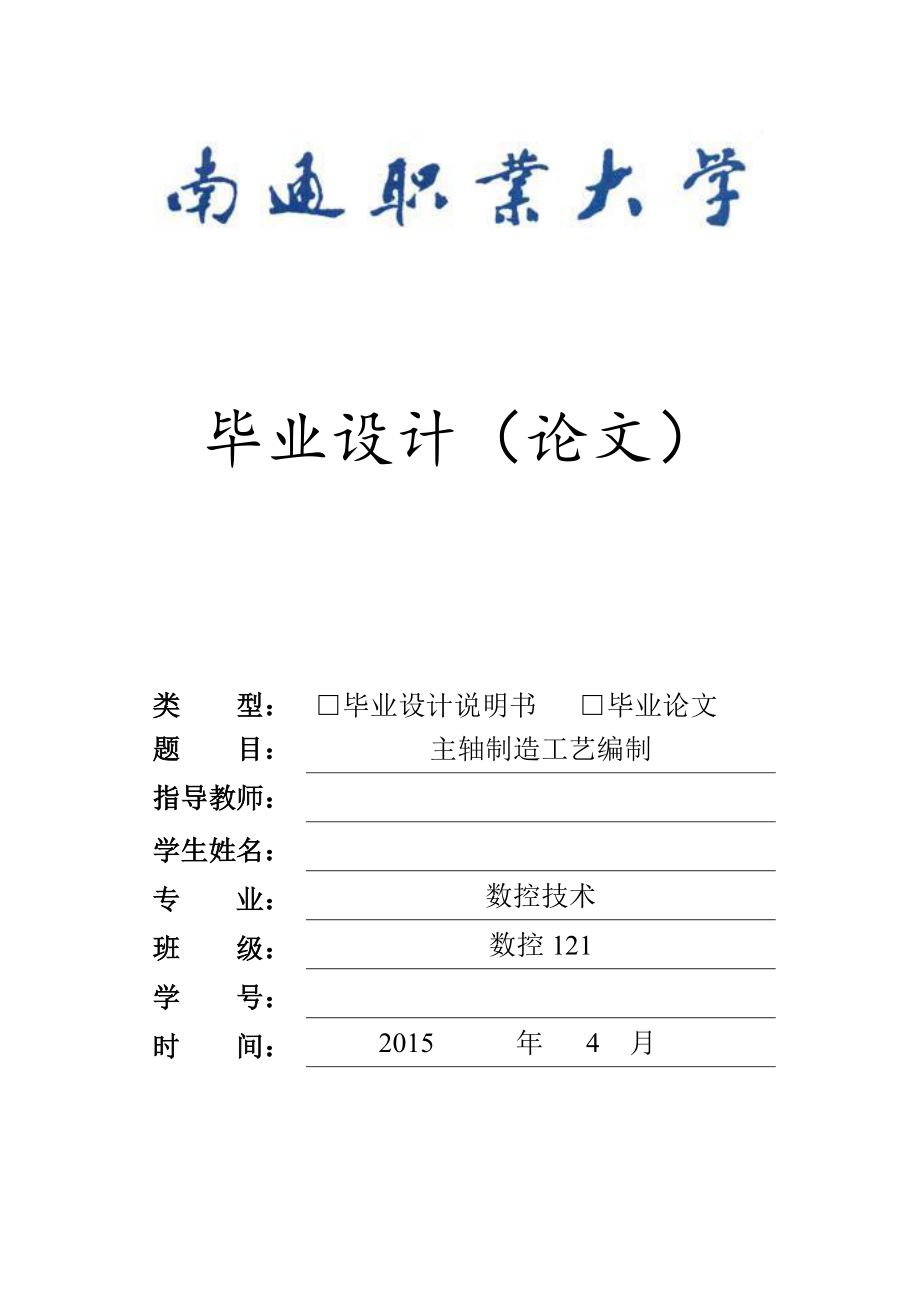


《毕业设计(论文)-主轴制造工艺编制》由会员分享,可在线阅读,更多相关《毕业设计(论文)-主轴制造工艺编制(58页珍藏版)》请在装配图网上搜索。
1、毕业设计(论文)类 型:毕业设计说明书 毕业论文题 目:主轴制造工艺编制指导教师:学生姓名:专 业:数控技术班 级:数控121学 号:时 间:2015年4月 摘要轴类零件是一种常用的典型零件,主要用于支承齿轮、带轮等传动零件及运动和扭矩,故其结构组成中具有许多外圆、轴肩、螺纹、螺尾退刀槽、砂轮越程槽和键槽。外圆用于安装轴承、齿轮、带轮等;轴肩用于轴上零件和轴本身的轴向定位;螺纹用于安装各种锁紧螺母和高速螺母;螺尾退刀槽供加工螺纹时退刀用;砂轮越程则是为了能完整地磨削出外圆和端面等;键槽用来安装键,以传递扭矩。轴类零件按其结构特点可分为简单轴、阶梯轴、空心轴和异型轴4大类。轴通常是其轴颈支承在机
2、器的支架或箱体上,实现运动和动力的传递。根据其功用及工作条件,轴类零件的技术要求通常包括以下几个方面。(1) 尺寸精度和形状精度。轴类零件的尺寸精度主要指轴的直径尺寸精度。轴上直径支承轴径和配合轴径(装配传动件的轴径)的尺寸精度和形状精度是轴的主要之一,它讲影响轴的回转精度和配合精度。(2) 位置精度。为保证轴上转动件的传动精度,必须规定支承轴颈与配合轴径的位置精度。通常以配合轴颈的径向圆跳动或同轴度来保证。(3)表面粗糙度。轴上的表面以支承轴颈的表面质量要求最高,其次是配合轴颈或工作表面。这是保证轴与轴承以上轴与轴上传动件正确可靠配合的重要影响。在生产实际中,轴颈的尺寸精度通常为IT6IT9
3、,精密的轴颈可达IT5;一般轴的形状精度应控制在直径公差范围之内;精密轴颈的形状精度应控制在直径公差的1/51/2之内。表面粗槽度Ra值,支持颈,支撑轴颈一般为0.630.16,配合轴颈一般为2.50.63;配合轴颈对支承轴颈径向圆跳动一般为0.010.03,高精度轴0.0010.005。AbstractShaft partsis a typical partsin common use,mainly used to support thegear,pulleyand othertransmission partsand motionand torque,so thestructurehasm
4、anyouter circle,shoulder,screw,screw tailslot,grinding wheel grooveand keyways.The outer circlefor the installation ofbearings,gears,pulleys;shoulderforparts on the shaftandshaftaxial positioningitself;the threadfor the installation of variouslock nut andhigh speednuts;screw tailslotforprocessing th
5、readcutter;grinding wheelis in order tocompletethe outer circle andend facegrinding;keyused to install thekeyto transfer torque.Shaft partsaccording to its structurecharacteristics can be divided into thesimpleshaft,shaft,hollow shaft andshaftshaped4 categories.The shaftis usuallytheshaftis supporte
6、d on the bracketor boxmachine,realize the transmission of motion and power.According toits functionand working conditions,requirementsof shaft partsgenerallyinclude the following.(1)the dimensional accuracyandshape accuracy.The dimensional accuracyof shaft partsmainly refers to thediameter sizepreci
7、sion of shaft.The shaftdiameter ofsupportingshaftand shaft(assemblydriveshaft diameter)of thedimensional accuracy and shape accuracyisone of the mainshaft,theeffect ofshaftrotating accuracy andfitting accuracy.(2)the position precision.As thetransmissionprecisionshaftrotating parts,must specify theb
8、earing neckshaftsizeandposition precision.Circular runoutorcoaxialto ensure thatusually inradial fitshaft neck.(3)surface roughness.Surface of the shafton thesurface quality ofcrankshaft bearingrequirementsthe highest,followed by theshaftneck orworking surface.Thisis to ensure thatthe shaft and the
9、bearingshaft and shaftdriveamorecorrect and reliablewithimportant influence.In the actual production,the sizeprecision of the shaft neckis usually IT6IT9,the precision of theshaft neckup to IT5;shapeprecisionshaftshould be controlledwithinthe diameter tolerance;shapeprecisionshaftshould becontrolled
10、 withinthe diameter tolerance of1/51/2.Surface roughdegree Ra valueof carotidgroove,support,support shaftneckis generally 0.630.16,with theshaftis 2.50.63;with theshaft neckofcrankshaft bearingradial runoutis generally 0.010.03,high precisionshaft 0.0010.005.前言本设计是根据机械制造工艺学课程所有教材和参考书及数控车床及编程加工技术来进行主
11、轴制造工艺设计的。本次设计的主轴的制造工艺包括外圆的加工、孔的加工、锥孔的加工、内螺纹的加工、外螺纹的加工以及键槽的加工。主轴的制造工艺的制定要综合考虑各方面的因素,其中最主要的是以下两个方面:一:工艺路线的制定要确保(形状精度、位置精度、尺寸精度以及表面粗糙度);二:工艺路线的制定要保证零件的生产率。在确保主轴精度的前提下为了保证零件的生产率,本次设计采用先进制造方法方法与传统制造方法先相结合来制定工艺路线。以下是本次设计主轴的大概内容:1. 主轴的外圆的加工包括外圆表面的加工、槽的加工以及螺纹的加工,根据要求和结合主轴外圆的结构特点,采用数控机床即可满足对主轴外圆的加工。采用数控编程加工即
12、可以确保主轴的精度要求,又可以保证生产率。2. 主轴的孔、锥孔、键槽以及内螺纹的加工较为复杂,故根据要求及主轴的特点采用传统的制造方法。通过分析论证及必要的计算,以此来选择合适的制造工艺路线。本次设计由陈振玉老师以及其他多为老师的指导。由于本次设计的编者水平有限,故在主轴设计中难免有不足之处,还望各位老师提出宝贵的意见。PrefaceThis design is all according to the mechanical manufacturing technology curriculum textbooks and reference books and the CNC lathe p
13、rocessing technology and programming design for spindle manufacturing process. The design of spindle manufacturing process including cylindrical hole processing, the processing, the taper hole processing, the internal thread processing, the external thread machining as well as the key way. Spindle m
14、anufacturing technology formulation to consider various factors, one of the most important are the following two aspects: one: the craft route formulation to ensure (shape accuracy, position accuracy, dimensional accuracy and surface roughness); Two: the craft route formulation to ensure that the co
15、mponents of the productivity.On the premise of to ensure the accuracy of spindle parts to ensure productivity, and the design method of the use of advanced manufacturing methods and the traditional manufacturing method first to make the combination of process route. The following is the design of sp
16、indle probably content:1. The main shaft of the cylindrical processing including machining, groove on the surface of the cylindrical and thread processing, according to the requirements and with the structure characteristics of a cylindrical shaft, using nc machine tool can meet the machining of cyl
17、indrical shaft. Using the numerical control programming can ensure the precision of the spindle, and can ensure productivity.2. The spindle hole and cone hole, slotting, and internal thread processing is relatively complex, so according to the requirements and the characteristics of the spindle with
18、 traditional manufacturing methods. Through analysis and necessary calculation, in order to choose appropriate manufacturing process route.The design for the teachers guidance by Chen Zhenyu teacher and other more.Due to the design editor level is limited, so the hard to avoid in the design of spind
19、le has shortcomings, still hope teachers put forward valuable opinion.目录一零件的工艺分析及生产类型的确定11.零件的作用12.零件的工艺分析1二选择毛坯,确定毛坯尺寸,设计毛坯图11.选择毛坯12.确定机械加工余量,毛坯尺寸和公差1三选择加工方法,制定工艺路线21.定位基准的选择22.零件加工方法的选择23.制定加工工艺路线3四工序设计41.选择加工设备与工艺设备4:选择机床4:选择夹具4:选择刀具5:选择量具52.确定工序尺寸6五确定切削用量及基本时间71.工序一切削用量及基本时间的确定72.工序二切削用量及基本时间的确
20、定73.工序三切削用量及基本时间的确定84.工序四切削用量及基本时间的确定95.工序五切削用量及基本时间的确定196.工序六切削用量及基本时间的确定257.工序七切削用量及基本时间的确定288.工序八切削用量及基本时间的确定319.工序九切削用量及基本时间的确定3310.工序十切削用量及基本时间的确定34六数控加工程序35七.总结41八附录42九参考文献43I一零件的工艺分析及生产类型的确定1.零件的作用机床主轴的作用是从发动机或电动机接受动力并将动力传给其它机件,从而实现机械加工。轴类零件是一种常用的典型零件,主要用于支承齿轮、带轮等传动零件及运动和扭矩,故其结构组成中具有许多外圆、轴肩、螺
21、纹、螺尾退刀槽、砂轮越程槽和键槽。外圆用于安装轴承、齿轮、带轮等;轴肩用于轴上零件和轴本身的轴向定位;螺纹用于安装各种锁紧螺母和高速螺母;螺尾退刀槽供加工螺纹时退刀用;砂轮越程则是为了能完整地磨削出外圆和端面等;键槽用来安装键,以传递扭矩。2.零件的工艺分析通过对该零件图的重新绘制,知原图样的试图正确,完整,尺寸,公差及技术要求齐全。通过对零件图纸的分析,零件的精度要求较高。端面部分用来安装刀具,为了保证加工零件的精度,故位置精度、尺寸精度与表面粗糙度要求较高。主轴的外圆部分主要与传动机构相连,用来接收动力。故位置精度与表面粗糙度较高。其中主轴端面上有内螺纹,用来与其他结构相连来固定主轴,故位
22、置精度较高。主轴外圆上有外螺纹,尺寸精度较高。主轴上的键槽主要用来安装键,以传递扭矩,故键槽侧面的表面粗糙度要求较高。二选择毛坯,确定毛坯尺寸,设计毛坯图1.选择毛坯该零件为机床主轴,用于机床传动,力学性能要求高,要求有较高的强度,该零件材料为20Cr,毛坯采用锻造加工方法,毛坯在机械加工之前,均需进行正火或退火处理,以此来使钢材的晶粒细化,以消除残余应力,降低毛坯硬度,改善切削加工性能。2.确定机械加工余量,毛坯尺寸和公差注:表1.46表示机械制造工艺设计简明手册上表1.46; 表2.7*表示切削用量简明手册上表2.7根据零件图计算轮廓尺寸,最大轴径D1=97mm,最小轴径D2=65mm,轴
23、长L=475mm。确定加工余量,取最大轴径加工余量为RMA1=5mm;中间轴径70mm加工余量为RMA2=3mm;两端面加工余量为RMA3=5mm。毛坯基本尺寸最大轴径d1=107mm,最小轴径d2=76mm,,轴长L=485mm,故毛坯尺寸为107mm485mm。根据毛坯锻件的形状,锻件形状复杂系数: 锻件重量 锻件外轮廓包裹体重量 查得20Cr的密度:经行计算的=18.48 =7.2 查表2.210得,锻件形状为简单级 20Cr含碳量C:0.180.24%0.65%查表2.211得,锻件材质系数级别为M1查表2.225得,锻件单边余量:厚度(直径)方向:2.02.5mm,水平方向为:2.3
24、3.0mm 根据锻件公差与加工余量的主要因素:当加工表面粗糙度Ra1.6时,其余量要适当加大,故上面毛坯的尺寸选择合适三选择加工方法,制定工艺路线1.定位基准的选择.粗基准的选择原则:按照有关粗基准选择原则,当零件有不加工表面的时候,应选取这些不加工的表面为粗基准。现取外圆表面及端面为粗基准。.精基准的选择原则:精基准的选择主要应该考虑基准重合的问题,故选择加工后的外圆表面与端面作为精基准。2.零件加工方法的选择该零件为机床主轴,按照零件图纸技术要求,其加工方法选择如下。.主轴两端面的表面粗糙度为Ra0.8,查表1.46得,采用粗车、半精车和精车加工。.主轴外圆尺寸精度要求较高,且根据要求,采
25、用数控编程加工。.主轴左端有孔27.5mm,表面粗糙度为Ra0.8,查表1.47得,采用钻孔、粗镗、半精镗和精镗加工。.主轴左端有7:24锥孔,表面粗糙度为Ra0.4,查表1.47得,采用粗镗、班精镗、精镗和浮动镗刀块精镗加工。.主轴左端有30mm内槽,无表面粗糙度为Ra3.2,查表1.47得,采用粗镗加工即可。.主轴右端有41mm孔,表面粗糙度为Ra3.2 ,查表1.47得,故采粗镗和半精镗加工。.主轴右端有47H7孔,表面粗糙度为Ra0.8,查表1.47得,采用钻孔、粗镗、半精镗和精镗加工。.主轴左端面有键槽深9mm,表面粗糙度为Ra0.8,查表1.48得,采用粗铣和精铣加工。.主轴右端外
26、圆表面上有键槽60.5mm16mm,深6mm,表面粗糙度为Ra1.6,查表1.48得,查表1.48得,采用粗铣和精铣加工。.主轴左端面上有内螺纹2M66H 深12、6M86H 深23,查表1.414得,故采用钻孔及攻丝加工。.主轴右端面上有内螺纹4M56H,查表1.414得,故采用钻孔及攻丝加工。.主轴右端外圆表面上有内螺纹M86H,查表1.414得,故采用钻孔及攻丝加工。3.制定加工工艺路线工序一:锻造主轴毛坯,并进行热处理工序二:车主轴两端面并钻中心孔工序三:用数控车床加工主轴外圆工序四:在主轴左端面上钻孔26mm,并进行粗镗、半精镗和精镗孔加工达到尺寸要求;粗镗、半精镗、精镗和浮动镗刀块
27、精镗加工7:24锥孔达到尺寸要求;粗镗30内槽。工序五:在主轴右端面进行粗镗和半精镗孔加工达到尺寸要 求;粗镗、半精镗和精镗孔41mm达到尺寸要求,倒内角。工序六:粗铣、精铣左端面键槽深9mm。工序七:粗铣、精铣右端外圆表面上键槽深6mm达到尺寸要求。工序八:在主轴左端面上钻2个孔5.2mm,攻丝M6;钻6个孔6.8,攻丝M8。工序九:在主轴右端面钻4个孔4.2mm,攻丝M5。工序十:在主轴右端面外圆表面上钻孔6.8mm,攻丝M8。工序十一:终检入库。四工序设计1.选择加工设备与工艺设备:选择机床工序二:本工序为车端面和钻中心孔,为了车加工时的顶尖和孔加工时的预制精确定位故选用CA6140卧式
28、车床即可。工序三:本工序为车削主轴外圆,根据要求要用数控编程加工,故选择CK6140数控车床即可满足加工要求。工序四:本工序为钻孔、粗镗、半精镗和精镗孔27.5,以及粗镗、半精镗、精镗和浮动镗刀块精镗7:24锥孔和镗30内槽,故选用T616卧式铣镗床即可。工序五:本工序为粗镗和半精镗孔41,以及粗镗、半精镗和精镗孔47,故选用T616卧式铣镗床即可。工序六:本工序为粗铣和精铣左端面上键槽,故选用X62卧式万能铣床即可。工序七:本工序为粗铣和精铣右端外圆表面上键槽,故选用X62卧式万能铣床即可。工序八:在主轴左端面上钻孔并进行攻丝,故选用Z32K万向摇臂钻床即可。工序九:在主轴右端面上钻孔并进行
29、攻丝,故选用Z32K万向摇臂钻床即可。工序十:在主轴右端外圆表面上钻孔并进行攻丝,故选用Z32K万向摇臂钻床即可。:选择夹具根据零件的加工要求,车削加工时用三爪卡盘和大顶针即可,其他各工序使用通用即可。:选择刀具查表3.14得钻中心孔选用中心钻A5(GB607885),车削端面时用选用90外圆车刀。车削外圆时,由于采用数控车床加工,故选用一般数控车刀即可:选用90外圆车刀、1.5mm宽切槽刀、3mm宽切槽刀和60外螺纹车刀。查表3.16得,钻头选用锥柄麻花钻d=4.2、d=5.2、d=6.8(GB143885)、锥柄超长麻花钻d=26、d=39(GB613785)。查表3.11、3.12得,镗
30、刀选用硬质合金单刃镗刀(主偏角r=60),内切槽刀(主偏角r=90)。查表3.130得,铣刀选用莫氏锥柄立铣刀d=12(GB110685)。查表3.147得,丝锥选用粗柄机用丝锥M5、M6、M8(GB346483)。:选择量具由于本批零件为中批量生产,故选用通用量具工序一:车削端面时选用游标卡尺,测量范围为300500mm,游标读数值为0.02mm;游标卡尺,测量范围为0125mm,游标读数值为0.02mm;工序三:车削外圆时选用游标卡尺,测量范围为300500mm,游标读数值为0.02mm;游标卡尺,测量范围为0125mm,游标读数值为0.02mm;外径千分尺,测量范围为5075mm,分度值
31、为0.01mm;外径千分尺,测量范围为75100mm,分度值为0.01mm。工序四:钻镗左端面孔时选用内径百分表,测量范围为1835mm,示值误差为0.015mm;内径百分表,测量范围为3550mm,示值误差为0.015mm。工序五:钻镗右端面孔时选用内径百分表,测量范围为3550mm,示值误差为0.015mm;游标深度卡尺,测量范围为0500mm,游标读数值为0.02mm。工序六、七:铣键槽时选用游标高度尺,测量范围为0200mm,游标读数值0.02mm;游标卡尺,测量范围为0125mm,游标读数值为0.02mm。工序八、九、十:钻孔时选用游标深度卡尺,测量范围为0200mm,游标读数值为0
32、.02mm。2. 确定工序尺寸工序一:在主轴两端面上钻中心孔d=6.3mm,孔深10mm;车主轴两端面,查表2.35得 端面加工余量 (mm) 加工方法 粗车 半精车 精车 加工余量 5 0.8 0.2工序四:由表2.38得 27.5孔加工工序尺寸 (mm) 加工方法零件尺寸毛坯尺寸加工余量公差 钻孔 26 0 粗镗 26.8 26 半精镗 27.3 26.8 0.40 精镗 27.5 27.3 0.25 0.004 镗内槽 30 27.5 0.10.1 7:24锥孔加工工序余量 (mm) 加工方法粗镗半精镗精镗浮动镗刀块精镗 加工余量 1.7 0.65 0.10 0工序五:由表2.38得 4
33、1孔加工工序尺寸 (mm)加工方法零件尺寸毛坯尺寸加工余量公差 粗镗 40.5 39 0.5 半精镗 41 40.5 00.1 47H7孔加工工序尺寸 (mm)加工方法零件尺寸毛坯尺寸加工余量公差 粗镗 46 41 1.0 半精镗 46.8 46 0.2 精镗 47 46.8 0+0.025工序六:左端面上键槽加工工序尺寸 由表2.322得键槽深9,粗铣宽度余量3.0,粗铣宽度偏差+0.18+0.27工序七:右端外圆表面上键槽加工工序尺寸由表2.322得键槽深6,粗铣宽度余量3.0,粗铣宽度偏差+0.18+0.27工序八:左端面上内螺纹加工工序尺寸由表2.320得2M66H第一次钻孔为d=5.
34、2,攻丝得M6由表2.320得6M86H第一次钻孔为d=6.8,攻丝得M8工序九:右端面上内螺纹加工工序尺寸 由表2.320得4M56H第一次钻孔为d=4.2,攻丝得M5工序十:右端外圆表面上内螺纹加工工序尺寸 由表2.320得M86H第一次钻孔为d=6.8,攻丝得M8五确定切削用量及基本时间1.工序一切削用量及基本时间的确定由于本工序为锻造主轴毛坯,并进行毛坯的热处理,故以实际锻造时间为准。2.工序二切削用量及基本时间的确定 切削用量本工序为车端面和钻中心孔,查表1.1*、1.2*、1.3*得,选刀杆尺寸刀具为硬质合金车刀,材料为YT15,前角、后角、主偏角、由表3.14查得,选择d=6.3
35、mm、d1=16mm、中心钻A5(GB607885),钻两个中心孔。 粗车切削用量及基本时间的确定确定进给量查表1.4*得,粗车时进给量:,根据表4.29得,取选择钻头磨钝标准及耐用度查表1.9*得,后刀面最大磨损限度为0.81.0mm,取1.0mm,耐用度确定切削速度查表1.27*得,切削速度计算公式: 为切削速度修正系数 查表1.28*得,、 代入求得查表1.27*得,、代入求得粗车主轴左端时主轴转速 ,根据CA6140机床转速表4.28选取粗车主轴左端时主轴转速 ,根据CA6140机床转速表4.28选取故粗车时根据实际情况主轴转速取中间值,查表4.28选取验证机床功率查表1.29*得,主
36、切削力: 切削时消耗的功率: 查表1.29*得,、查表1.28*得,切削力修正系数 代入求得: 查表4.27得,CA6140机床的主电动机功率为7.5,所以所选切削速度与转速合格基本时间 公式中,查表1.26*得,入切量及超切量(2)半精车切削用量及基本时间的确定刀具不变确定进给量查表1.6*得,半精车时进给量:,根据表4.29得,取选择钻头磨钝标准及耐用度查表1.9*得,后刀面最大磨损限度为0.81.0mm,取1.0mm,耐用度确定切削速度查表1.27*得,切削速度计算公式: 为切削速度修正系数 查表1.28*得,、 代入求得查表1.27*得,、代入求得粗车主轴左端时主轴转速 ,根据CA61
37、40机床转速表4.28选取粗车主轴左端时主轴转速 ,根据CA6140机床转速表4.28选取故粗车时根据实际情况主轴转速取中间值,查表4.28选取验证机床功率查表1.29*得,主切削力: 切削时消耗的功率: 查表1.29*得,、查表1.28*得,切削力修正系数 代入求得: 查表4.27得,CA6140机床的主电动机功率为7.5,所以所选切削速度与转速合格基本时间 公式中,查表1.26*得,入切量及超切量(3)精车切削用量及基本时间的确定刀具不变确定进给量查表1.6*得,精车时进给量:,根据表4.29得,取选择钻头磨钝标准及耐用度查表1.9*得,后刀面最大磨损限度为0.81.0mm,取1.0mm,
38、耐用度确定切削速度查表1.27*得,切削速度计算公式: 为切削速度修正系数 查表1.28*得,、 代入求得查表1.27*得,、代入求得粗车主轴左端时主轴转速 ,根据CA6140机床转速表4.28选取粗车主轴左端时主轴转速 ,根据CA6140机床转速表4.28选取故粗车时根据实际情况主轴转速取中间值,查表4.28选取验证机床功率查表1.29*得,主切削力: 切削时消耗的功率: 查表1.29*得,、查表1.28*得,切削力修正系数 代入求得: 查表4.27得,CA6140机床的主电动机功率为7.5,所以所选切削速度与转速合格基本时间 公式中,查表1.26*得,入切量及超切量(4)钻中心孔切削用量及
39、基本时间的确定确定进给量由于本工序为钻中心孔,较为简单,故宜采用手动进给。选择钻头磨钝标准及耐用度由表2.12*查得,钻头后到面最大磨损限度为0.40.8mm,选取0.6mm;耐用度。确定切削速度由表2.14*查得,抗拉强度b835MPa的20Cr加工性7类;根据表2.7*暂定,由表2.13*查得、,根据Z32K机床转速表4.212取n=432r/min(钻孔时采用较低转速)实际切削速度基本时间有表6.25查得公式 代入得 (5) 总工时3.工序三切削用量及基本时间的确定本工序为采用数控车床车削主轴外圆查表得机床选用CK6140数控车床,该机床转速范围为251600r/min,纵向进给范围为0
40、.042.16mm,机床功率e=4.5kw,使用切削液。由于本工序采用数控编程加工,故切削用量、进给量及基本时间j以实际数控加工时为主要参数:粗车时选择转速600r/min,进给量0.2mm/r,每次切削深度p=1.5mm;精车时选择转速800r/min,进给量0.1mm/r;仿形车时选择转速1000r/min,进给量0.1mm/r;切槽时选择转速300r/min,进给量0.05mm/r;车螺纹时选择转速300r/min,进给量1.5mm/r4.工序四切削用量及基本时间的确定 钻孔切削用量及基本时间的确定本工序为钻镗27.5mm孔,镗7:24锥孔和镗30mm内槽 为孔深,为孔径5故采用深孔钻,
41、加用切削液,机床为T616卧式铣镗床确定进给量查表2.7*得,进给量=0.320.40mm/r,根据钻头强度与机床所允许的最大轴向力,查表2.9*得,取=0.20mm/r,钻头的刃磨形式为标准确定钻头磨钝标准和耐用度查表2.12*得,当钻头直径d0=26mm时,后刀面最大磨损量为0.81.0mm,取1.0mm;耐用度=50min确定切削速度和工作台每分钟进给量查表2.14*得,根据材料b835MPa和硬度HBS179,20Cr加工性属7类;查表2.13*得,当=0.20mm/r、d0=26mm时,取=15m/min,查表2.31*得切削速度的修正系数 查表1.28*得,、 代入求得0.74=6
42、.525m/min ,根据机床T616转速表4.220取验证机床功率根据=0.20mm/r、布氏硬度(HBS)179,查表2.22*得取,故所选机床及加工参数合格主轴转速为、进给量、基本时间 查表2.29*得,入切量及超切量=10mm代入求得 粗镗7:24锥孔切削用量及基本时间的确定粗镗时选用刀具为硬质合金单刃镗刀,材料为YG6,前角=8、后角、主偏角、kr=15、,机床不变确定进给量由查表1.5*,进给量,取,确定机床转速及切削速度查表1.9*得,刀具寿命:查表1.27*得,切削速度计算公式: 为切削速度修正系数 查表1.28*得,、 代入求得查表1.27*得,、代入求得:主轴转速 ,根据机
43、床T616转速表4.220取校验机床功率查表1.29*得,主切削力: 切削时消耗的功率: 查表1.29*得,、查表1.28*得,切削力修正系数 代入求得: 查表4.219得,T616机床的主电动机功率为4,所以所选切削速度与转速合格基本时间查表6.21得公式: 代入求得 半精镗7:24锥孔切削用量及基本时间的确定镗刀与机床不变确定进给量查表1.5*得,进给量,取确定机床转速及切削速度查表1.9*得,刀具寿命:查表1.27*得,切削速度计算公式: 为切削速度修正系数 查表1.28*得,、 代入求得查表1.27*得,、代入求得:主轴转速 ,根据机床T616转速表4.220取校验机床功率查表1.29
44、*得,主切削力: 切削时消耗的功率: 查表1.29*得,、查表1.28*得,切削力修正系数代入求得: 查表4.219得,T616机床的主电动机功率为4,所以所选切削速度与转速合格基本时间查表6.21得公式: 代入求得 精镗7:24锥孔切削用量及基本时间的确定镗刀与机床不变确定进给量查表1.5*得,进给量,取确定机床转速及切削速度查表1.9*得,刀具寿命:查表1.27*得,切削速度计算公式: 为切削速度修正系数 查表1.28*得,、 代入求得查表1.27*得,、代入求得:主轴转速 ,根据机床T616转速表4.220取校验机床功率查表1.29*得,主切削力: 切削时消耗的功率: 查表1.29*得,
45、、 查表1.28*得,切削力修正系数代入求得: 查表4.219得,T616机床的主电动机功率为4,所以所选切削速度与转速合格基本时间查表6.21得公式: 代入求得 浮动镗刀块精镗7:24锥孔切削用量及基本时间的确定镗刀与机床不变确定进给量查表1.5*得,进给量,取确定机床转速及切削速度查表1.9*得,刀具寿命:查表1.27*得,切削速度计算公式: 为切削速度修正系数 查表1.28*得,、 代入求得查表1.27*得,、代入求得:主轴转速 ,根据机床T616转速表4.220取校验机床功率查表1.29*得,主切削力: 切削时消耗的功率: 查表1.29*得,、查表1.28*得,切削力修正系数 代入求得
46、: 查表4.219得,T616机床的主电动机功率为4,所以所选切削速度与转速合格基本时间查表6.21得公式: 代入求得 粗镗26mm孔切削用量及基本时间的确定镗刀与机床不变确定进给量查表1.5*得,进给量,取确定机床转速及切削速度查表1.9*得,刀具寿命:查表1.27*得,切削速度计算公式: 为切削速度修正系数 查表1.28*得,、 代入求得查表1.27*得,、代入求得:主轴转速 ,根据机床T616转速表4.220取校验机床功率查表1.29*得,主切削力: 切削时消耗的功率: 查表1.29*得,、查表1.28*得,切削力修正系数 代入求得: 查表4.219得,T616机床的主电动机功率为4,所
47、以所选切削速度与转速合格基本时间查表6.21得公式: 代入求得 半精镗26.8mm孔切削用量及基本时间的确定镗刀与机床不变确定进给量查表1.5*得,进给量,取确定机床转速及切削速度查表1.9*得,刀具寿命:查表1.27*得,切削速度计算公式: 为切削速度修正系数 查表1.28*得,、 代入求得查表1.27*得,、代入求得:主轴转速 ,根据机床T616转速表4.220取校验机床功率查表1.29*得,主切削力: 切削时消耗的功率: 查表1.29*得,、查表1.28*得,切削力修正系数 代入求得: 查表4.219得,T616机床的主电动机功率为4,所以所选切削速度与转速合格基本时间查表6.21得公式
48、: 代入求得 精镗26.8mm孔切削用量及基本时间的确定镗刀与机床不变确定进给量查表1.5*得,进给量,取确定机床转速及切削速度查表1.9*得,刀具寿命:查表1.27*得,切削速度计算公式: 为切削速度修正系数 查表1.28*得,、 代入求得查表1.27*得,、代入求得:主轴转速 ,根据机床T616转速表4.220取校验机床功率查表1.29*得,主切削力: 切削时消耗的功率: 查表1.29*得,、查表1.28*得,切削力修正系数 代入求得: 查表4.219得,T616机床的主电动机功率为4,所以所选切削速度与转速合格基本时间查表6.21得公式: 代入求得 镗30mm内槽切削用量及基本时间的确定
49、镗刀选用内切槽刀主偏角 机床不变确定进给量查表17*得,进给量,取;查表1.18*得切削速度确定机床转速及切削速度查表1.9*得,刀具寿命:查表1.27*得,切削速度计算公式: 为切削速度修正系数 查表1.28*得,、 代入求得查表1.27*得,、代入求得:主轴转速 ,根据机床T616转速表4.220取校验机床功率查表1.29*得,主切削力: 切削时消耗的功率: 查表1.29*得,、查表1.28*得,切削力修正系数 代入求得: 查表4.219得,T616机床的主电动机功率为4,所以所选切削速度与转速合格基本时间查表6.21得公式: 当主偏角 总工时5. 工序五切削用量及基本时间的确定 粗镗39
50、mm孔切削用量及基本时间的确定镗刀与机床不变确定进给量查表1.5*得,进给量,取确定机床转速及切削速度查表1.9*得,刀具寿命:查表1.27*得,切削速度计算公式: 为切削速度修正系数 查表1.28*得,、 代入求得查表1.27*得,、代入求得:主轴转速 ,根据机床T616转速表4.220取校验机床功率查表1.29*得,主切削力: 切削时消耗的功率: 查表1.29*得,、查表1.28*得,切削力修正系数 代入求得: 查表4.219得,T616机床的主电动机功率为4,所以所选切削速度与转速合格基本时间查表6.21得公式: 代入求得 半精镗40.5mm孔切削用量及基本时间的确定镗刀与机床不变确定进
51、给量查表1.5*得,进给量,取确定机床转速及切削速度查表1.9*得,刀具寿命:查表1.27*得,切削速度计算公式: 为切削速度修正系数 查表1.28*得,、 代入求得查表1.27*得,、代入求得:主轴转速 ,根据机床T616转速表4.220取校验机床功率查表1.29*得,主切削力: 切削时消耗的功率: 查表1.29*得,、查表1.28*得,切削力修正系数 代入求得: 查表4.219得,T616机床的主电动机功率为4,所以所选切削速度与转速合格基本时间查表6.21得公式: 代入求得 粗镗41mm孔切削用量及基本时间的确定镗刀与机床不变确定进给量查表1.5*得,进给量,取确定机床转速及切削速度查表
52、1.9*得,刀具寿命:查表1.27*得,切削速度计算公式: 为切削速度修正系数 查表1.28*得,、 代入求得查表1.27*得,、代入求得:主轴转速 ,根据机床T616转速表4.220取校验机床功率查表1.29*得,主切削力: 切削时消耗的功率: 查表1.29*得,、查表1.28*得,切削力修正系数 代入求得: 查表4.219得,T616机床的主电动机功率为4,所以所选切削速度与转速合格基本时间查表6.21得公式: 代入求得 半精镗46mm孔切削用量及基本时间的确定镗刀与机床不变确定进给量查表1.5*得,进给量,取确定机床转速及切削速度查表1.9*得,刀具寿命:查表1.27*得,切削速度计算公
53、式: 为切削速度修正系数 查表1.28*得,、 代入求得查表1.27*得,、代入求得:主轴转速 ,根据机床T616转速表4.220取校验机床功率查表1.29*得,主切削力: 切削时消耗的功率: 查表1.29*得,、查表1.28*得,切削力修正系数 代入求得: 查表4.219得,T616机床的主电动机功率为4,所以所选切削速度与转速合格基本时间查表6.21得公式: 代入求得 精镗46.8mm孔切削用量及基本时间的确定镗刀与机床不变确定进给量查表1.5*得,进给量,取确定机床转速及切削速度查表1.9*得,刀具寿命:查表1.27*得,切削速度计算公式: 为切削速度修正系数 查表1.28*得,、 代入
54、求得查表1.27*得,、代入求得:主轴转速 ,根据机床T616转速表4.220取校验机床功率查表1.29*得,主切削力: 切削时消耗的功率: 查表1.29*得,、查表1.28*得,切削力修正系数代入求得: 查表4.219得,T616机床的主电动机功率为4,所以所选切削速度与转速合格基本时间查表6.21得公式: 代入求得 总工时6.工序六切削用量及基本时间的确定本工序为铣左端面上键槽,机床采用X62卧式万能铣床即可,根据图纸要求:铣削宽度、铣削深度,故选用高速钢莫氏锥柄立铣刀(GB110685) 粗铣切削用量及基本时间的确定切削用量查表3.2*得,加工材料,铣刀前角、周齿后角、端齿后角、刀齿螺旋
55、角;查表3.130得,、齿数确定进给量铣刀直径、铣削宽度,查表3.4*得,每齿进给量 取选择铣刀磨钝标准及耐用度查表3.7*、3.8*得,粗加工时铣刀后刀面最大磨损限度为0.150.20mm,取0.20mm,耐用度确定切削速度和工作台每分钟进给量查表3.27*得公式 (切削速度修正系数吗,由表1.28*查得)、代入求得主轴转速 根据X62机床转速表4.239得,选择实际切削速度工作台每分钟进给量:根据X62机床工作台进给量表4.240选择实际每齿进给量校验机床功率查表3.28*得,铣削时功率公式:圆周力公式: (切削力修正修正系数由表1.28*查得)代入求得 查表4.238得X62铣床主轴电动机的功率为7.5kW,故所选切削用量可以采用。所确定的切削用量为:基本时间查表6.27得公式:
- 温馨提示:
1: 本站所有资源如无特殊说明,都需要本地电脑安装OFFICE2007和PDF阅读器。图纸软件为CAD,CAXA,PROE,UG,SolidWorks等.压缩文件请下载最新的WinRAR软件解压。
2: 本站的文档不包含任何第三方提供的附件图纸等,如果需要附件,请联系上传者。文件的所有权益归上传用户所有。
3.本站RAR压缩包中若带图纸,网页内容里面会有图纸预览,若没有图纸预览就没有图纸。
4. 未经权益所有人同意不得将文件中的内容挪作商业或盈利用途。
5. 装配图网仅提供信息存储空间,仅对用户上传内容的表现方式做保护处理,对用户上传分享的文档内容本身不做任何修改或编辑,并不能对任何下载内容负责。
6. 下载文件中如有侵权或不适当内容,请与我们联系,我们立即纠正。
7. 本站不保证下载资源的准确性、安全性和完整性, 同时也不承担用户因使用这些下载资源对自己和他人造成任何形式的伤害或损失。