数控机床传动与进给机构设计
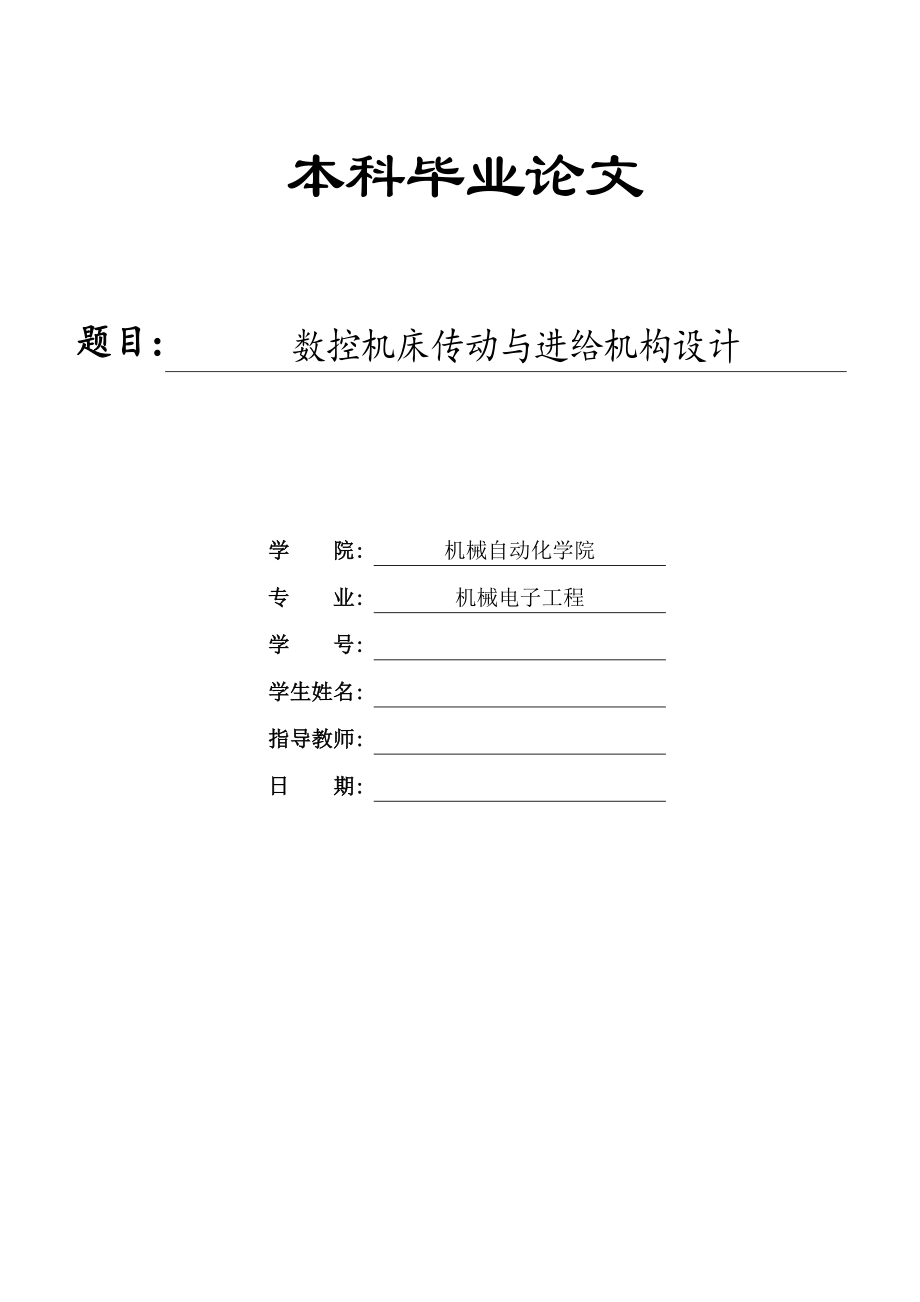


《数控机床传动与进给机构设计》由会员分享,可在线阅读,更多相关《数控机床传动与进给机构设计(31页珍藏版)》请在装配图网上搜索。
1、本科毕业论文题目:数控机床传动与进给机构设计学 院:机械自动化学院专 业:机械电子工程学 号:学生姓名:指导教师:日 期:摘 要本次设计主要包括两部分内容,第一部分是主传动系统的设计,第二部分是进给传动系统的设计,主传动系统的设计目标是使机床主轴能在一定转速范围内实现无级调速,在设计这一部分时,主要进行了一下几项工作:分级变速箱的设计,主轴尺寸设计,支承方式的选择,为了满足主轴的刚度要求,还要对主轴进行校核计算。进给传动系统设计的主要目标是使机床工作台能在xy方向上自由移动,机床xyz三方向上的传动构件相同,故只需设计x方向传动系统,主要涉及到:导轨的选型,滚珠丝杠与支承轴承,驱动电机的选型与
2、计算,主要零部件的精度验算,装配图设计,确定各部分零件的主要尺寸后,零件的细节尺寸设计在装配图中完成。在对零件进行校核时,主要根据零件的刚度和寿命进行校核,本次设计主要的设计方法是理论设计和经验设计。关键词: 数控铣床; 主传动; 进给传动; 伺服电机Abstract This design mainly includes two parts, the first part is the design of the main drive system, the second part is the design of the feed drive system, the main drive
3、system design goal is to make the machine spindle in a certain speed range to achieve stepless speed , In the design of this part, the main work carried out a few: classification gearbox design, spindle size design, support the choice of way, in order to meet the stiffness requirements of the spindl
4、e, but also the spindle to check the calculation. Feeding drive system design of the main goal is to make the machine table in the xy direction of free movement, the machine xyz three directions of the same transmission components, so only the design of x-direction drive system, mainly related to: g
5、uide selection, Ball screw and bearing bearing, drive motor selection and calculation, the accuracy of the main parts of the calculation, assembly diagram design to determine the main parts of the various parts of the size of the details of the design of parts in the assembly diagram to complete. In
6、 the parts to check, mainly based on the stiffness and life of parts to check, the design of the main design method is the theoretical design and experience design.Key words: CNC milling machine; Main drive; Feed drive; Servo motor 29目 录1 绪论51.1 选题的背景及意义51.2 数控机床的发展情况51.3 设计任务62 主传动系统设计72.1 概述72.2 分
7、级变速箱的设计72.2.1 分级变速箱的变速级数72.2.2 传动公比的确定72.2.3 传动齿轮齿数的确定72.3 主轴组件的基本要求82.4 采用滚动轴承的主轴组件92.4.1 支承方式的选择92.4.2 轴承间隙的调整与预紧92.5 主轴尺寸设计92.6 主轴组件的刚度计算102.7 轴承润滑和主轴密封112.8 本章小结113 进给传动系统设计133.1 导轨轴向负载力计算133.2 导轨的选型133.3 滚珠丝杠与支承轴承143.3.1 滚珠丝杠的计算143.3.2 支承用轴承的选用163.3.3 承载能力校验163.4 驱动电机的选型与计算173.5 主要零部件的精度验算183.5
8、.1 伺服刚度KR183.5.2 丝杠的轴向拉压刚度183.5.3 轴承的轴向刚度183.5.4 滚珠与滚道的接触刚度Kc193.5.5 进给传动系统的综合拉压刚度K193.6 进给传动系统的动态特性分析193.7 驱动电动机与滚珠丝杠的连接193.8 本章小结204 数控机床控制系统设计214.1 控制系统硬件的基本组成214.1.1 概述214.1.2 数控系统的主要性能与规格214.1.3 主轴和进给轴控制的硬件系统22 4.2 数控机床主要的电气控制回路235 总结24参考文献24致谢251 绪论1.1 选题的背景及意义以数控机床作为本次设计的主要内容,非常贴近于国家目前的经济发展大势
9、。前不久国家提出了中国工业4.0,中国制造2025等发展目标,这不仅仅是一句口号,还会转化为切切实实的行动,如何实现工业4.0?参照德国的标准,实现工业4.0必须要实现生产的智能化和数据化,依靠传统的机床根本无法实现这一点,必须借助于新一代的数控机床才有可能实现这一目标,数控机床能实现自动化的加工,加工精度和经济效益远高于工人手工操作,人们只需将预先写好的程序传入数控机床,机床便能读取这些命令并加工出满足工艺要求的各种零件,大大提高了生产效率,降低了工人的工作负担。数控机床的加工能力远大于普通机床,这是因为与普通机床相比,它多了一个重要的组成部分,即数控系统,经过多年的发展,数控系统已经成为一
10、个比较成熟的分支,它主要包括输入输出,数控装置,伺服装置和相关的辅助装置。加工零件时,工人必须先根据零件的加工工艺编写程序,然后将程序输入数控系统中去,完成这一过程的就是数控系统的输入输出设备,主要有手动输入和通信接口两种输入方式。数控装置是数控系统的核心,相当于机床的cpu,它能识别输入的程序,并将这些程序转化为机床的控制命令,通常使用微型计算机完成这一功能。数控机床的伺服系统包括主要的传动结构和动力部分,是完成机床机械运动的主要装置,本篇论文也主要围绕这一部分展开,包括主传动系统和进给系统,主传动系统控制刀具的运动,刀具轨迹的具体实现方法则是在微型计算机中通过插补运算得到,进给传动系统则实
11、现工件的各种运动,主要通过三轴的丝杠来实现。机床是一个复杂的系统,它由许多小装置组合到一起,在数控装置的控制下,完成各种复杂的运动。本次主要设计伺服系统,设计时也不能脱离这个系统,要考虑到与其他装置的相互配合,例如,数控机床一般都能实现自动换刀的功能,刀具又与主轴配合到一起,因此在设计主传动系统主轴时,要考虑到自动换刀装置,在比如机床的温度控制系统,在设计机床的各个运动部件时,都应该考虑到这一系统。1.2 数控机床的发展情况经过从最初的购买引进,到现在的自主创新,中国的机床行业从无到有,有了巨大的发展,现在,在国家的大力扶持下,我国的机床行业迎来了又一个发展机遇期,在相关的技术领域不断取得突破
12、,大连机床厂是一家运营比较成功的机床企业,该厂的许多机床代表着中国机床市场上最高端的一批产品,例如VDWA50、B50五轴立式加工中心,这一型号机床能实现刀具的三轴运动,工作台采用两轴联动加工技术,实现了机床的五轴联动加工,该机床利用重心驱动,复合设计等相关原理,使得机床具有良好的工作性能,结构紧凑,性价比高。在第十五届中国国际机床展览会上,中国的机床企业展示了大量的先进机床,例如沈阳机床展示的i5智能机床,宝鸡西力精密机械展示的FTN50自动化加工单元,数控系统方面则有华中数控展示的华中8型数控系统。本次机床展览会显示了中国机床行业令人惊讶的创新能力与产品设计能力,在多年的发展过程中,中国的
13、机床行业并没有在外国的技术封锁与残酷的市场竞争中消亡,反而依靠自身能力,一步一个脚印,走出了自己的康庄大道,出现了一批具有极强研发能力的企业,例如沈阳机床,大连机床,华中数控,广州数控等等。现如今,中国的机床行业仍有大量的问题没有解决,经过2008年经融危机后,西方的许多工业强国都意识到了制造业在国民经济中的重要地位,纷纷加大了对制造业的研发投入,中国面临的竞争也越来越激烈,与国际上的机床制造强国相比,中国的机床制造业主要存在以下几项缺点:(1)在技术水平上,经过多年的发展,外国企业积累了雄厚的研发能力,目前,他们已将目光投向与新一代数控机床设计,技术方面呈现“高,精,尖”的特点,在这些高水平
14、数控机床设计上,中国仍有一定的差距。(2)从机床市场上的产品组成上看,机床市场上产品的整体水平还处于中下游,技术水平与西方发达国家相比有一定的差距,一些高水平的数控机床还处于试验阶段,并没有投放市场。(3)从数控机床的研发设计能力上看,中国的机床行业研发能力还有不足,机床是一个系统,且比一般产品更加复杂,它有许多零件组成,每一个都对整个系统的性能产生一定的影响,没有雄厚的科研能力与相关的技术积累,很难设计出性能优异的机床,而中国的机床行业就是缺少相关的技术积累,一直处于摸索过程中。(4)从市场化程度上看,中国机床行业在国际市场上并没有占据很大的市场份额,甚至在国内市场上所占份额都不算太大,主要
15、因为中国机床水平落后于西方的工业强国,虽然中国一直在奋起直追,但中国面临的竞争压力只会越来越大。目前,这些问题已经引起了相关部门的重视,产业扶持力度也在不断加大,相信将来,中国的机床行业也能赶上世界先进水平。1.3 设计任务 本次设计主要包括两大部分内容,第一部分是主传动系统的设计,已知参数有主电机功率5.5kw,最高转速为6000r/min,额定功率为1500r/min,主轴转速范围为306000r/min,具体设计内容有:分级变速箱的设计,主轴的设计,主轴支承轴承的设计。第二部分是进给传动系统的设计,已知参数有工作台重量210kg,最大承重300kg,面积1000320mm,切削速度104
16、000mm/min,最大速度5000mm/min,工作台x向行程600mm,定位精度0.05mm,具体设计零件有滚珠丝杠的设计,支承轴承的设计,导轨的选型,伺服电机的设计,伺服电机与滚珠丝杠的连接,滚珠丝杠的刚度校核与寿命校核。2 主传动系统设计2.1 概述主轴电机启动后,经过主轴箱的变速机构,来调节刀具的切削速度,进而加工加工各种不同的零件。主轴电机的转速可以调节,属于无级调速,但是调速范围不大,在本次设计中,主电动机参数已知,其额定转速为1500r/min,经过变频器变速后最大转速可以达到6000r/min,为了使数控铣床的主轴能够无级调速,并且扭矩能够实现加工要求,可以在调速电机后串联有
17、级调速机构,即齿轮调速,进过无极变速和有级变速的共同调节,可以使主轴转速范围满足设计要求,在加工零件时,主轴转速应在其计算转速以上,此时可以充分发挥主电动机的功率。2.2分级变速箱的设计2.2.1分级变速箱的变速级数 在设计机床的主传动系统时,已知的设计参数有:主轴的调速范围为306000r/min,计算转速为500r/min,采用5.5kw的主轴专用变频电机作为主电动机使用,电动机的基本转速为1500r/min,最高转速可达6000r/min。主轴要求的恒功率调速范围: Rnp=6000/500=12电动机的恒功率调速范围为: Rp=6000/1500=4机床在加工零件时,电动机会工作在恒功
18、率范围,这是电动机的主要工作状态,但由计算可以,在恒功率范围内,电动机的调速范围达不到主轴的要求,因此要设计分级变速箱,以满足主轴的调速范围。故可以使用两对齿轮变速。2.2.2传动公比的确定 分级变速箱各级转速之比,即为传动公比,前面已经求得,变速箱为两级变速机构,一般情况下,可以使各级转速之间满足等比数列关系,这样可以使转速损失均匀分布到各级,也能使设计过程变得更加简单,传动公比的大小是有规定的,其取值大小只能为一下几种:1.06、1.12、1.26、1.41、1.58、1.78、2.因为电动机电额定转速为1500r/min,主轴的额定转速为500r/min,Z=2,故可求得传动公比为:,=
19、1.73,取=1.78.2.2.3传动齿轮齿数的确定 在确定齿轮齿数时,应该使齿轮齿轮的结构更加紧凑,使机床主传动系统的误差更小,具体要求如下:1) 齿轮的齿数和Sz不应过大两个齿轮相互啮合时,齿数越多,两齿轮的中心矩也就会更大,这会加大主传动系统的质量,也会使其尺寸加大,一般推荐齿轮的齿数和小于100.2) 小齿轮的齿数尽量取较小值,但也不能过小,过小会产生根切,也可能使两轴靠地过近,使其他结构发生碰撞,一般情况下,小齿轮的齿数应该不小于18个。3) 齿轮齿数应该满足传动公比在设计只初,就确定了传动公比为1.78,故在选择齿轮齿数时,也要满足该要求,两者之间允许存在误差,但误差应在合理范围之
20、内。 使用查表法可求得齿轮齿数查阅机械制造技术装备及设计表4.2-3,当=1.78时取Z1=27,则Z2=75-27=48,取Z2=45,Z3=30时,Z4=84-30=54,Z5=32时,Z6=52,r/min由上述可得,主传动系统图和转速图如下:600027:4552:3230:542000150050090306000 1500Z5 Z4 Z690Z3Z2 Z11 图2.1 主传动系统图 图2.2 转速图 2.3 主轴组件的基本要求 (1) 回转精度 在机床运转状态下,测量主轴前轴颈的径向圆跳动,轴向窜动,即可得到主轴的回转精度,主轴加工零件时,主要就是做旋转运动,因此,如果主轴存在回转
21、精度误差,这种误差将会传递到零件的各个尺寸中去,对机床的整个精度造成极大影响。 (2) 刚度 主轴抵抗变形的能力称为主轴的刚度,主轴刚度与其结构和材料有关,作为机床主传动系统的一部分,当其变形量过大时,会直接影响到与其装配的轴承、齿轮等等其他零件,会使这些零件的工作性能发生变化,进而使整个系统的性能降低。(3) 抗震性主轴在运转的过程中,存在震动现象,主轴抵抗这种震动的能力被称为抗震性,当主轴的抗震性过低时,不仅不能加工出满意的零件,还会大幅缩短刀具的使用寿命,也会使主轴与轴承,齿轮之间发生碰撞,磨损,加大配合间隙,一般采取的措施是安装阻尼器,来增加主轴的抗震性。(4)温升 主轴旋转速度最高可
22、达6000r/min,高速运转时会产生剧烈摩擦,使温度升高,机床性能受到很大影响,常见的有,主轴温度升高产生热变形,进而使回转精度降低,也会使主轴零件之间产生相对位移,使它们之间的配合准确性下降,轴承温度过高时会发生膨胀,使内径减小,极端情况下会发生抱轴现象。为了解决这一问题,一般机床都会增加冷却系统。使机床温度保持在20以内。(5)耐磨性 主轴上安装刀具的地方,是最容易发生磨损的地方,磨损量过大时,会影响到刀具的安装精度,进而使加工零件的精度达不到要求,主轴的耐磨性主要与主轴的材料和热处理有关 ,对于一般的精密机床,常用的主轴材料为40Cr或者20Cr,16MnCr5,12CrNi2A,并将
23、主轴渗碳淬硬处理,使其HRC硬度不低于60.(6) 主轴主要的精度指标根据一般的设计经验,主轴前支承轴承的同轴度约为5微米,轴承与轴组成过盈配合,过盈量在5微米以内,主轴前端为7:24的锥孔,该孔与前支承轴承的同轴度为3至5微米,采用7:24锥孔的原因是在安装刀具是易定位且不自锁。2.4 采用滚动轴承的主轴组件2.4.1 支承方式的选择在设计主轴支承方式时,主要根据经验设计,如今大部分数控铣床主轴支承均采用角接触球轴承,具有很好的固定作用,但滚子与滚道的接触方式为点接触式,其刚度较低,承载能力太小,为了克服这些缺点,可以使用双列背对背安装并预紧,本次设计中,机床主轴轴承选用7212AC/P4,
24、其尺寸大小为:60mm110mm22mm,本次设计时,角接触球轴承采用4级精度,能够满足要求的工作精和运转平稳性,查阅参考文献1表4-1-16得,轴承与轴的配合采用h4(预紧),查表4-1-17得:轴承与外壳孔的配合公差带型号为H5.2.4.2 轴承间隙的调整与预紧 轴承预紧能有效地提升轴承的工作性能,在轴承上添加一个适当的预紧力,可以使滚子与滚道之间的接触面积增加,增加了结构的刚度,预紧力也不能过大,过大时使两者之间的接触压力过大,运动过程中发热量增大,使寿命降低,采用下图所示方法预紧时,适当大小的预紧力应为轴向负荷的四分之一。 图2.3 轴承的预紧2.5 主轴尺寸设计主轴的主要参数包括以下
25、几个部分:(1) 主轴直径主轴直径会对主轴刚度和主传动系统的整体大小产生一定影响,加大主轴直径会使公差值增大,主轴的精度就会降低,故在设计主轴的尺寸大小时,只能根据经验和相关资料来确定主轴直径,一般而言,前轴颈直径大于后轴颈直径,且为其(0.70.8)倍。查阅参考文献2表4.3-8,选取前轴颈直径D1=65mm,后轴颈直径D2=50mm。(2) 主轴内孔直径的确定在保证主轴刚度的前提下,应使主轴内孔直径尽量取大,根据经验设计,孔径应为直径的二分之一,故孔径大小为25mm。(3) 主轴悬伸量a的确定主轴的前悬伸量不能过大,也不能过小,过大时,会使主轴刚度和稳定性降低,容易发生挠动,而为了保证主轴
26、前端到工作台的距离,前悬伸量也不能太小,主轴悬伸量可按下表选取。 表2.1 主轴悬伸量与前端轴颈之比 机床和主轴的类型 a/ D1 通用机床和精密机床 0.51.5中等长度铣床 1.252.5加工孔等结构的机床,需要较长的加工刀杆 2.5 取取悬伸量与主轴前轴颈直径之比为1.25,则主轴悬伸量为a=1.2560=70mm.(4) 主轴支承跨距L的确定主轴支承跨距可按如下经验公式计算: 式中 D主轴外径(mm) d主轴内径(mm) K500N/m。通常而言,L=(23)a,故L可取210mm。2.6主轴组件的刚度计算 主轴前轴颈直径为65mm,后轴颈直径为50mm,在计算主轴的刚度时,可将其近似
27、认为为一个等直径长轴,轴径为前后轴颈直径的平均值。 d=(65+50)/2=57.5mm切削工件时,主轴前端会受到工件的反作用力,如图,则挠度为: 式中 F外载荷(N); a前悬伸(mm); L跨距(mm); E弹性模量,钢的E=2(MPa); I截面惯性矩,I=0.05()(); d主轴外径(mm); di主轴孔径(mm)。将E、I代入式中可得: 孔的直径相对与轴的直径而言较小,在计算时为了简化计算过程,孔的影响可以忽略: 弯曲刚度 : 同理可简化为 : 2.7 轴承润滑和主轴密封对轴承进行润滑可有效地提升轴承的工作性能,减小发热量,使磨损量降低,延长轴承的使用寿命,在现代的数控机床系统中,
28、常用的润滑方式有油润滑和脂润滑,这两种润滑方式各有优缺点,油润滑通常应用于告诉旋转主轴中,使用方便,更换简单,与其相比,采用脂润滑时,润滑脂更换更加困难,但更换一次后即可以使用很长时间,维护费用低,温度上升也较慢,因此在本次设计中,采用脂润滑方式。在机床工作时,会产生很多的切削和粉尘,这些杂质很容易进入到润滑脂中,使润滑效果降低,同时也会对零件表面造成磨损,故必须对主轴进行密封,脂润滑的主轴组件多用不接触的曲路密封,如图: 图2.4 主轴的密封2.8本章小结设计主传动系统的整体思路就是设计无级变速机构和有级变速机构,无级变速机构主要是主轴电机自带的调速性能,有级变速机构主要是变速齿轮箱,交流主
29、轴变频电机主电机的参数已知,故本章更加侧重于主传动系统的有级调速设计,在此过程中,先确定了调速级数,然后根据等比原则确定了传动公比,根据设计经验,确定了传动齿轮齿数。机床主传动系统的主要零件是机床主轴和支承轴承,主轴对机床的工作性能有极大的影响,机床主轴前轴颈直径只能根据经验查阅相关资料确定,确定原则就是机床主轴要求的回转精度,刚度,稳定性等要求,确定前轴颈直径后,便根据结构要求,使主轴尺寸递减,得到其他各部分主轴直径,主轴刚度验算则采用了简化方法,将主轴视为一根等直径长轴,采用理论计算方法验算其刚度满足要求。背对背安装的角接触球轴承大量用于现代数控机床主轴支承,是比较成功的设计先列,本次设计
30、中,借鉴该种方法,同样采用角接触球轴承支承主轴,求得主轴直径后,可以确定轴承的具体型号。3 进给传动系统设计3.1导轨轴向负载力计算(1) 主轴的计算转速属于已知参数,其大小为500r/min,采用125mm铣刀强力铣削可得主切削力Fz,铣刀的切削速度为: 机床的机械效率为0.8时,Fz计算如下:(2) 切削分力的计算查阅参考文献3表2-1可得: 式中:F1纵向切削分力; Fv垂向切削分力; Fc横向切削分力。切削时,工件固定在工作台上,工作台会受到一定的作用力,工作台尤在导轨上移动,此时导轨摩擦力大小为:式中:摩擦系数,=0.06; W工作台自重和负载,W=(210+300)9.8=4998
31、N; fg镶条紧固力(N),查3表2-3得:fg=1500N.不切削时,摩擦力F0计算如下:(3)查阅参考文献3式(2-10a)得,进给牵引力为:3.2导轨的选型 矩形导轨结构简单,使用维护方便,能承受较大载荷,能较好地满足工艺要求,本次设计中,导轨选用矩形导轨,工作台运动过程中,会与导轨产生摩擦,这对工作台的平稳运行十分不利,为此,在导轨和工作台之间加上一层用特殊材料制成的软带可以显著提高工作台的工作性能,防止出现爬行现象,贴塑导轨具有良好的工作性能,但它与矩形导轨相互配合时,在磨损后不能自动补偿间隙,当磨损量过大,使间隙过大时,会使工作太的运动失去准确性,难以定位,故需要对导轨间隙进行调整
32、,如下图所示,才用修复刮研式方法调整间隙,当间隙过大时,可以刮研左边平面,当间隙过小时,可以刮研右边平面。 图3.1 导轨3.3 滚珠丝杠与支承轴承3.3.1滚珠丝杠的计算伺服电机的最高转速是1500r/min,工作台的最高移动速度为5000mm/min,故丝杠基本导程为: 丝杠的最低转速为:则丝杠的平均转速为:丝杠的平均载荷为:丝杠的额定动载荷为:滚珠丝杠的最大轴向变形量可按如下方法计算:最大轴向变形量取最小值max=6.67m丝杠螺母到支承的最大距离计算如下:估算最小螺纹底径:式中:E弹性模量(Mpa),一般滚珠丝杠去E=2.1105Mpa; max轴向变形量; F0导轨的静摩擦力。上述计
33、算可得如下结论:丝杠导程为3.33mm,丝杠的额定动载荷为10.41KN,丝杠底径不小于18.28mm,故查阅参考文献2附录表A-3可选丝杠型号为FFZD3206-3,其基本参数如下: 图3.2 滚珠丝杠滚珠丝杠螺母副的预加负荷为: 取Fp=13000/9=1444N滚珠丝杠预拉伸力Ft的计算:3.3.2 支承轴承的选用(1)轴承的轴向负载力:(2)轴承的预紧力Fp计算如下:(3) 轴承的当量轴向载荷计算如下(4) 基本额定动载荷C计算如下:查参考文献3表2-25得,径向系数X=1.9,轴向系数Y=0.54,故在安装时,要对滚珠丝杠螺母副进行预拉伸,在支承形式的选择上,选用两端固定的支承形式,
34、60角接触球轴承背对背安装时有许多优点,可以承受两个方向的轴向力,由计算可知,丝杠的螺纹底径为27.9mm,采取过盈配合,故可选取内径为25mm的轴承,角接触球轴承7205B的主要参数为内径25mm,外径52mm,厚度15mm,基本额定动负荷14600N,动负荷大于预紧力,最高转速也能够满足要求。3.3.3 承载能力校验(1)滚珠丝杠临界转速校核(2)滚珠丝杠螺母副额定寿命的校验 由上述计算结果知,丝杠的额定动载荷大小为13000N,在机床一般工作情况下,运转条件系数大小为1.3,滚珠丝杠轴向载荷的计算结果为1048.71N,计算转速为500r/min,故滚珠丝杠螺母副的额定寿命为:该滚珠丝杠
35、满足要求。3.4 驱动电机的选型与计算(1)已知最大的进给力Fmax=1048.71N,丝杠导程Ph=6mm,预紧力Fp=1444N,机械效率=0.9,由参考文献3式(2-54)可得外部载荷所产生的摩擦力矩为: 由式(2-56)可得预紧力所产生的摩擦力矩为:由式(2-55)可得摩擦负载力矩为:则最大切削负载力矩为:(2)负载惯量计算伺服电动机的转子惯量JM应与负载惯量JL相匹配,移动部件总的质量为510kg,查阅参考文献2式(4.4-5)可得电动机轴上的转动惯量为:丝杠公称直径为D0=32mm=0.032m,长度l=1.2m,丝杠材料钢的密度=7.8103kg/m3.由参考文献2式(4.4-6
36、)可知丝杠加载电动机轴上的惯量:联轴节加上锁紧螺母等的惯量J3可直接查阅手册得;J3=0.0001kgm2。故负载的总惯量为:按中小型数控机床惯量匹配条件,1JM/JL4,所选伺服电机的转子惯量JM应在1.5296.11610kgm2范围之内。根据上述计算可初步选择交流伺服电动机GK6061-6AC31-FE,其额定转速为2000r/min,静转矩M0=6Nm,相电流I0=6.2A,转矩常数KT=1.09Nm/A,转动惯量J=8.710-4kgm2,重量为10.6kg。(3)空载加速转矩计算在工作台加速到最大移动速度的过程中,所需的空载加速转矩Ta按参考文献2式(4.4-8)求得:空载加速时,
37、主要克服的是惯性。如选用GK6061-6AC31-FE电动机,总惯量为: 一般情况下,数控铣床伺服系统的开环增益为20Hz,工作台加速到最大速度所需的时间为ta=3/ks=0.15s则空载加速转矩为:由上式可知,该伺服电机能够满足要求。3.5 主要零部件的精度验算 本次设计中要求滚珠丝杠的定位精度要达到0.05mm,滚珠丝杠的定位主要是数控装置来控制,而具体实现则是由丝杠的机械结构完成,由此可见,进给传动系统的精度主要受到数控装置的精度和丝杠的机械精度影响,这一部分主要完成丝杠的机械精度验算。3.5.1伺服刚度KR KM是伺服电机的增益,可近似认为KM=1/Ke。GK606伺服电机的转矩系数K
38、t=1.09Nm/A,由前述计算可知,伺服系统增益Ks值为20,开环增益Kv0=40/s,反电动势系数Ke=0.764sV/rad,电枢直流电阻RM=0.3,故工作台的直线刚度计算如下:3.5.2滚珠丝杠的拉压刚度 滚珠丝杠的固定方式不同,其拉压刚度也会不同,本次设计中,丝杠为一端轴向定位结构,工作台的纵向行程为已知参数600mm,当工作台移动到离固定支承最远时,滚珠丝杠有最小拉压刚度,当工作台移动到离固定支承最近时,它们不可直接接触,中间还应该有一段距离,假设为150mm,故可得丝杆 的最大距离为750mm,即lmax=0.75m,代入参考文献2式(4.4-18)可得丝杠的拉压刚度为:式中,
39、di为丝杠的最小螺纹底径,E是钢的弹性模量,E=200Gpa,则:3.5.3丝杠轴承的轴向刚度 滚珠丝杠的固定端所选用的轴承位7205B角接触球轴承,其基本参数为:钢球数Z=12,钢球直径大小db=7.5mm,由前述计算可知,其预加载荷F0大小为1444N,导轨的摩擦力F0为389.88N,故轴向载荷Fa=F0+F0=1444+389.88=1833.88N,轴承的载荷刚度Kb计算如下:3.5.4滚珠与滚道的接触刚度Kc 滚珠丝杠的刚度K=839N/m,额定动载荷Ca=13000N,由前面的计算结论,丝杠的最大轴向载荷Famax=1833.88N,则接触刚度Kc为:3.5.5进给传动系统的综合
40、拉压刚度K(2) 弹性模量在进行定位精度验算时,要计算其弹性变形,为了避免其他因素影响到机床的定位,故只能在空载状态下验算,此时弹性变形只由空载摩擦力引起。3.6 进给传动系统的动态特性分析 在前述的计算中,已经求得滚珠丝杠的综合拉压刚度为K为94.86N/m,查阅参考文献3表A-3可得滚珠丝杠的滚珠丝杠螺母副的质量为:机床工作台和工件夹具的质量m为510kg,所以上述两者的等效质量md为:分析计算结果,nc数值较大,在设计机械传动系统的刚度时,nc一般取为300rad/s,故nc=430.8rad/s能够满足要求。3.7 驱动电动机与滚珠丝杠的连接 联轴器的型号有很多种,很多都能满足此次设计
41、要求,目前市场上的数控机床应用最多的是膜片联轴器,本次设计也采用膜片联轴器,滚珠丝杠的最小螺纹底径为27.9mm,故丝杠末端直径会小于28mm,取为24mm,刚好能与联轴器相互配合。查阅参考文献3附表A-6得,联轴器型号为02,联轴器简图如下: 图3.3 弹性联轴器3.8本章小结本章是本次设计的第二个主要部分,从驱动环节到执行环节,每一部分都有具体的设计要求与设计任务。采用交流伺服电机作为系统的动力源,其转速要能满足机床的最大移动速度(5000r/min),同时要能提供足够的扭矩,交流伺服电机不仅能满足这些要求,同时其转速与电源频率成比例关系,易于调节,采用膜片联轴器将电机与丝杠连接,丝杠则选
42、用FFZD3206-3,其循环方式为内循环,并对丝杠的转速和寿命进行了验算。机床导轨选用矩形导轨,为了降低导轨面的摩擦力,使工作台运动更加平稳,在导轨间隙贴塑,机床工作台的重量为210kg,最大承重为300kg,带有三个T行槽,其具体结构设计在装配图中完成。在设计完系统的主要零件后,计算了整个系统的刚度,由此对系统的动态特性进行了分析,其最低固有频率满足要求。4数控机床控制系统设计4.1 控制系统硬件的基本组成4.1.1 概述 数控机床与普通机床的最大不同便是多了一个数控系统,数控系统主要有输入输出装置,控制装置,伺服装置,辅助装置组成,其结构大致如下图所示:驱动系统控制对象(设备)控制微机键
43、盘显示辅助控制检测 图4.1 控制系统目前市场上能生产数控系统的大型公司主要有华中数控,广州数控,北京凯恩帝数控,本次设计中,采用华中数控公司的HNC-21MD数控系统和HSV-160型全数字交流伺服驱动单元及GK6交流永磁同步伺服电机和变频主轴。4.1.2 数控系统的主要性能及规格 HNC-21MD是一款比较成熟的产品,目前已大量运用于数控机床上,采用这款数控系统完全能满足此设计要求。主要由以下几个部分组成:l 工业PC机l 中央处理单元(CPU)高性能32位微处理器l 存储器(DRAM RAM)SMB RAMl 程序断电存储区Flash ROM 16MBl 显示器:8.4寸彩色LCD分辨率
44、为640480l NC键盘l RS232 接口RS232 波特率为19200l 网络接口 以太网接口l 控制轴数3轴HNC-21MD主要参数如下: 表4.1 HNC-21MD参数CNC功能最大控制轴:36进给轴+1主轴 联动轴数:3轴最小分辨率:1微米坐标系设定 加工过程图形仿真显示和实时跟踪MDI功能 n M、S、T功能固定铣削循环CNC编程最小编程尺寸:0.001毫米、度 最大编程尺寸:99999.999最大编程行数:50万行 公/英制编程绝对/相对指令编程 宏指令编程子程序调用 工件坐标系设定直径/半径编程 自动控制倒角(圆角、直角)插补功能直线插补,最大6个轴圆弧插补 攻丝切削刀具补偿
45、功能刀具长度补偿 刀尖半径补偿操作功能8.4/TFT彩色液晶显示屏 防静电薄膜编程面板与机床操作面板PC标准键盘接口 手持单元(选件)图形显示功能与动态实时仿真 网络通讯功能(选件)进给轴功能无限旋转轴功能 最高设定速度43000mm/min进给修调0%-150% 快移修调0%-100%多种回参考点功能:单向、双向主轴功能主轴转速:最大32000rpm主轴修调:从0%-150% 主轴速度和修调显示辅助功能主轴正反转 n 自动换刀 n 冷却开/停PCL功能内嵌式PLC 提供标准PLC例程 PLC状态显示HNC-21MD外观图和尺寸图如下: 图4.2 HNC-21MD外观图 图4.3 HNC-21
46、MD尺寸图4.1.3主轴和进给轴控制的硬件系统本次设计中,机床主轴的调速范围为306000r/min,可以采用HSV-160交流伺服驱动单元,HSV-160的产品参数如下: 表4.2 HSV-160参数输入电源三相AC220V电源,-15%+10%,50/60Hz环境条件温 度环境温度 055(无结露)保存温度 -2065海 拔海拔 1000 以下振 动5.88s2以下,1060Hz(共振频率下不可连续使用)控制方式IGBT PWM方式 正弦波驱动全数字串行绝对式编码器EnDat2.1/2.2协议、HiperFACE协议、TAMAGAWA协议A/B相通用复合增量式编码器,A/B/Z/、U/V/
47、W信号差动输入(RS422电平)控制信号输 入使能、复位、触发信号、用户指定输 出报警、用户指定正面面板按键 5个、八段数码管 6个(组合显示)、LED 2个再生制动内置再生制动电阻,可选配外部制动电阻控制模式位置控制、速度控制、转矩控制、位置/速度控制监视功能转速、当前位置、位置偏差、电机转矩、运行状态等4.2数控机床主要的电气控制回路(1) plc连接电路图如下 图4.5 plc连接电路图5总结 经过为期三个月的设计,本次数控机床的进给传动机构设计总算是完成了,在整个设计过程中,不仅运用到了以前学过的基础知识,也接触到了许多以前不了解的新的领域,对设计者的整体水平都有巨大的提升。可以说,我
48、也是站在巨人的肩膀上才完成了这项工作,设计中,借鉴了大量前人的经验,同时加入了自己的一些创新想法,一些结构参数与市场上的XK713并不完全相同,在具体工作中,先根据主轴电机设计了分级变速机构,分级变速机构是按照等比原则设计,这样在满足设计要求的前提下简化了设计过程,设计主轴时在满足主轴的性能要求下,根据设计经验初步设计了主轴的参数,主轴的具体设计参数是在装配图的设计过程中完成的,这样的设计方法不仅能使主轴的参数满足设计要求,同时也能使主传动系统中各部分的结构尺寸更加协调,使整个系统成为一个有机的整体。本次设计中完成的第二项主要工作就是进给机构的设计,这个过程主要包含四个部分,第一部分是滚珠丝杠
49、的设计,滚珠丝杠属于标准件,只需计算出几个主要参数就可以根据国标选择出具体的型号,选用丝杠后,对其进行了刚度校核,以验算其是否满足设计要求,第二部分是工作台的设计,工作台的尺寸是以知的,其结构设计只能根据前人的设计经验,在装配图的设计中完成了这一项工作,第三部分是导轨的选用,目前市场上通用的导轨形式只有几种,本次设计选用了矩形贴塑导轨,这种导轨结构形式简单,且有着良好的工作性能,第四部分是伺服驱动电机的选择,主要是根据系统的转动惯量与转速来确定,本次设计主要完成了数控系统中伺服装置的设计,在控制部分只是选择了主要的控制核心,在电气控制回路和plc控制程序方面仍有大量工作有待完成。 参考文献1
50、现代使用机床设计手册编委会.现代使用机床设计手册M.北京:机械工业出 版社,20062 杜君文.机械制造技术装备及设计M.天津:天津大学出版社,19983 范超毅.数控技术课程设计M.武汉:华中科技大学出版社,20074 王爱玲.现代数控机床M.北京:国防工业出版社,20035 濮良贵.机械设计M.北京:高等教育出版社,20136 宋玉阶.电工与电子技术M.武汉:华中科技大学出版社,20127 机床设计手册编写组.机床设计手册M.北京:机械工业出版社,19988 李福生.实用数控机床技术手册M.北京:北京出版社,19939 吴振彪.机电综合设计基础M.北京:中国人民大学出版社,200010 何
51、雪明.数控技术M.武汉:华中科技大学出版社,200611 戴曙.金属切削机床M.北京:机械工业出版社,199512 毕承恩.现代数控机床M.北京:机械工业出版社,199113 王先逵.机械制造工艺学M.北京:机械工业出版社,199514 周开勤.机械零件手册M.北京:高等教育出版社,199415 徐瀚.机械设计手册.北京:机械工业出版社,200116 汝元功.机械设计手册M.北京:高等教育出版社,199517 成大先.机械设计图册.M.北京:化学工业出版社,200018 刘朝儒.机械制图M.北京:高等教育出版社,200119 黄靖远.机械设计学M.北京:机械工业出版社,199920 W. Bo
52、lton, “Mechatronics, Electronic Control Systems in Mechanical and Electrical Engineering”, ISBN 0582-35705-5, Addison Wesley Longman, (1999). 21 S. Devdas, A.K. Richard “Mechatronics System Design PWS Publishing Company, (1997). 22 S.Karunakaran, N.S.Dasharathy, “Mechatronics and Machine Tools, Mc G
53、raw Hill Book Company,(1999). 23 Grbz, R., “Retrofitting of the Conventional lathe to CNC Lathe” Conference Proceedings, 7. International Machine and Manufacturing Congress, (1996), p. 145. 24 Gurbuz, R., “Mechatronics and Mechatronics Application, Selection of Motor and Motor Drivers for Converting a General Purpose Lathe to CNC Lathe”, Gazi University Technical Education Faculty, Journal of Polytechnics, Number: 471,(2001), p. 39.致谢
- 温馨提示:
1: 本站所有资源如无特殊说明,都需要本地电脑安装OFFICE2007和PDF阅读器。图纸软件为CAD,CAXA,PROE,UG,SolidWorks等.压缩文件请下载最新的WinRAR软件解压。
2: 本站的文档不包含任何第三方提供的附件图纸等,如果需要附件,请联系上传者。文件的所有权益归上传用户所有。
3.本站RAR压缩包中若带图纸,网页内容里面会有图纸预览,若没有图纸预览就没有图纸。
4. 未经权益所有人同意不得将文件中的内容挪作商业或盈利用途。
5. 装配图网仅提供信息存储空间,仅对用户上传内容的表现方式做保护处理,对用户上传分享的文档内容本身不做任何修改或编辑,并不能对任何下载内容负责。
6. 下载文件中如有侵权或不适当内容,请与我们联系,我们立即纠正。
7. 本站不保证下载资源的准确性、安全性和完整性, 同时也不承担用户因使用这些下载资源对自己和他人造成任何形式的伤害或损失。