毕业设计(论文)螺旋榨油机设计
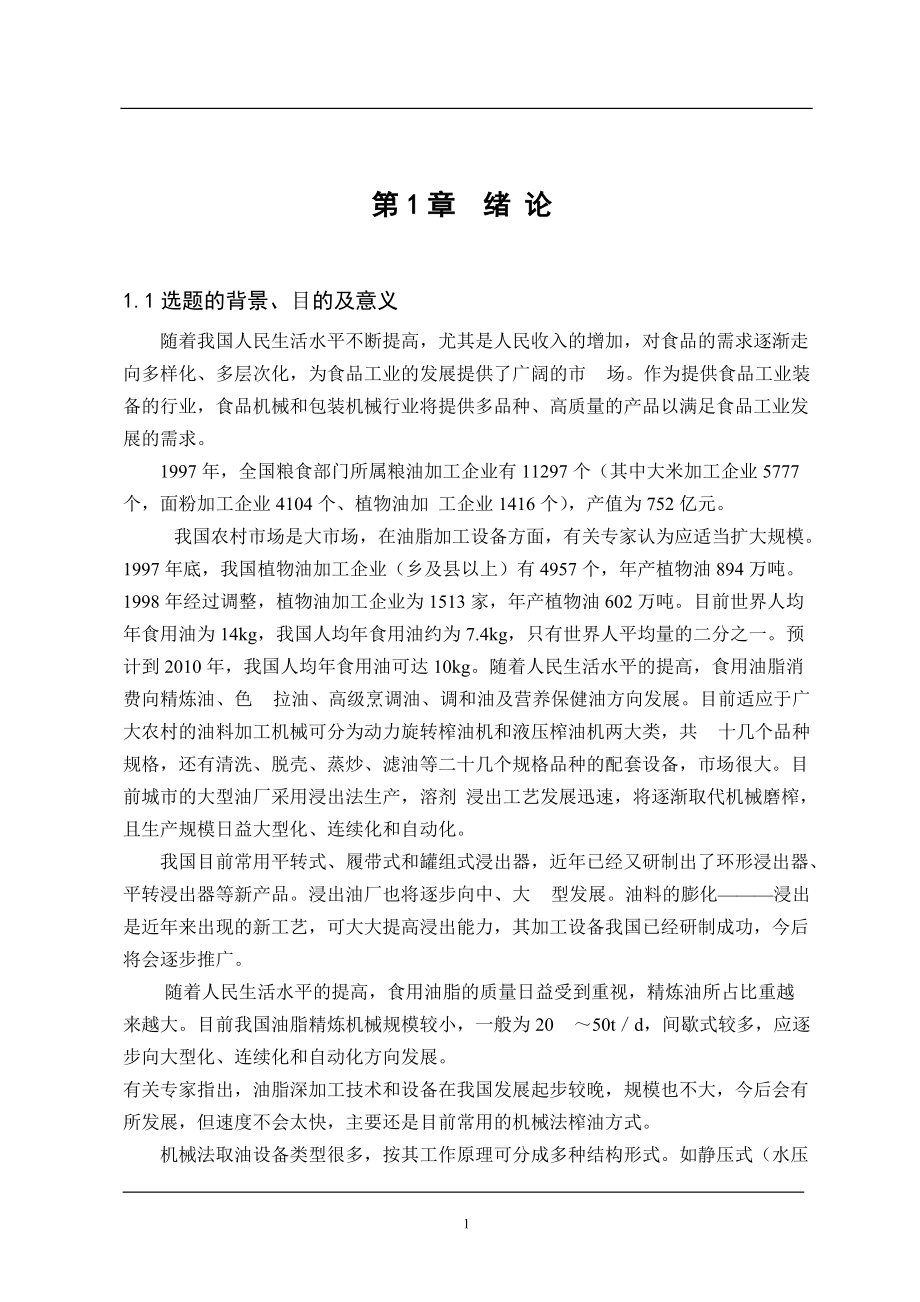


《毕业设计(论文)螺旋榨油机设计》由会员分享,可在线阅读,更多相关《毕业设计(论文)螺旋榨油机设计(32页珍藏版)》请在装配图网上搜索。
1、第1章 绪 论1.1选题的背景、目的及意义随着我国人民生活水平不断提高,尤其是人民收入的增加,对食品的需求逐渐走向多样化、多层次化,为食品工业的发展提供了广阔的市 场。作为提供食品工业装备的行业,食品机械和包装机械行业将提供多品种、高质量的产品以满足食品工业发展的需求。1997年,全国粮食部门所属粮油加工企业有11297个(其中大米加工企业5777个,面粉加工企业4104个、植物油加 工企业1416个),产值为752亿元。 我国农村市场是大市场,在油脂加工设备方面,有关专家认为应适当扩大规模。1997年底,我国植物油加工企业(乡及县以上)有4957个,年产植物油894万吨。1998年经过调整,
2、植物油加工企业为1513家,年产植物油602万吨。目前世界人均年食用油为14kg,我国人均年食用油约为7.4kg,只有世界人平均量的二分之一。预计到2010年,我国人均年食用油可达10kg。随着人民生活水平的提高,食用油脂消费向精炼油、色 拉油、高级烹调油、调和油及营养保健油方向发展。目前适应于广大农村的油料加工机械可分为动力旋转榨油机和液压榨油机两大类,共 十几个品种规格,还有清洗、脱壳、蒸炒、滤油等二十几个规格品种的配套设备,市场很大。目前城市的大型油厂采用浸出法生产,溶剂 浸出工艺发展迅速,将逐渐取代机械磨榨,且生产规模日益大型化、连续化和自动化。我国目前常用平转式、履带式和罐组式浸出器
3、,近年已经又研制出了环形浸出器、平转浸出器等新产品。浸出油厂也将逐步向中、大 型发展。油料的膨化浸出是近年来出现的新工艺,可大大提高浸出能力,其加工设备我国已经研制成功,今后将会逐步推广。随着人民生活水平的提高,食用油脂的质量日益受到重视,精炼油所占比重越来越大。目前我国油脂精炼机械规模较小,一般为20 50td,间歇式较多,应逐步向大型化、连续化和自动化方向发展。有关专家指出,油脂深加工技术和设备在我国发展起步较晚,规模也不大,今后会有所发展,但速度不会太快,主要还是目前常用的机械法榨油方式。机械法取油设备类型很多,按其工作原理可分成多种结构形式。如静压式(水压式)、搅拌挤压式、螺旋挤压式(
4、螺旋榨油机)、偏心回转挤压式(回转偏心轮榨油机)以及离心力挤压分离(水浸法分离油渣)等。其中常用的有液压榨油机和螺旋榨油机两大类。而液压榨油机除特殊用途外,也将逐渐由高效螺旋榨油机所取代。液压榨油机有手动、机动以及立式、卧式等类型。立式手动液压榨油机由榨油部分和手动压力泵组成,可压榨多种油料,经预处理后的料坯经轧坯、蒸炒并制成饼坯后放入榨膛内压榨。通常液压榨油机配备制饼机(手动或液压式)。手动或电动液压榨油机的压力泵有单柱塞泵、套式柱塞泵等多种类型,其中套式泵结构简单、压力变换方便,有能满足榨油过程先快后慢,压力由小到大的工艺要求,该液压榨油机结构简单,但操作劳动强度大,不能连续作业。制浆成型
5、半连续式液压榨油机,该榨油机压力高,压榨时间短(825min),能自动控制,是一种适用压榨可可、芝麻、花生仁等高油分软脂油料的专用榨油机。但对设备材质、压力泵、制造要求较高,成本高,一般应用范围不广。螺旋榨油机是利用旋转的榨螺轴将料坯在榨膛内连续推进,由于榨螺上螺旋导程逐渐缩短或螺纹深度逐渐变浅,榨膛内的空间容积(榨膛容积或空余体积)逐渐减小,从而产生压榨作用,将油从榨笼缝隙中挤出,残渣压榨成饼,从出口端排出。螺旋压榨在食品生产中,由于液压榨油机取油生产的间歇性,压榨周期长,装卸料饼麻烦,而且设备笨重,占地面积大等缺点,限制了它的发展,因此,有被螺旋榨油机取代的趋势。1.2 国内外研究状况和相
6、关领域中已有的研究成果利用高新技术进行米、面、油的精深加工,可使粮油资源成倍增值。以下是目前世界上较为先进的几种粮油加工高新技术。 机电一体化技术、光电控制技术、智能技术。这三项技术是世界发达国家现代米、面、油精深加工必用的高新技术,运用于粮油加工的原料储运、保鲜,产品加工、质量控制,成品储存和发放的全过程,是粮油加工达到高效、优质、低耗的重要技术手段。 挤压膨化技术。挤压膨化技术是世界发达国家用于粮油加工、食品制作、纤维和淀粉降解、谷物和大豆蛋白组织化、谷物细胞壁破壁等生化反应器。在早餐食品、休闲食品制作和粮油深加工中有着广泛的应用前景。如米糠挤压稳定化技术,可使米糠品质稳定,延缓劣变,提高
7、米糠的储藏性;油料挤压膨化可提高出油率;米、面等原料经挤压膨化,可以生产丰富多彩的谷物早餐食品和休闲食品;大豆经挤压膨化可生产大豆组织化食品等。 生物技术。生物技术是世纪高新技术中的核心技术之一。在粮油加工中有着广泛的应用前景,其中各种生物酶制剂是深加工必不可少的,谷物转化淀粉糖、超纯度米淀粉、多孔淀粉、高蛋白米粉、高纯度米蛋白、米糠蛋白、米糠营养素、肌醇,酶法制油、脂交换等深加工产品的生产都需要生物技术和淀粉酶、糖化的酶、蛋白酶、脂肪酶、纤维素的酶、植酸酶等多种酶制剂和酶工程技术。 膜分离、离子交换、色谱分离技术。这三项技术是粮油深加工和副产品综合利用必不可少的高新技术,油料和谷物蛋白及其功
8、能肽的制备,谷物细胞壁多糖及粮油资源中各种功能性活性物质的分离、纯化、制备等高附加值产品的生产都必需利用超滤、钠米滤等膜分离高新技术。 超细粉碎技术超细粉碎技术超细粉碎技术超细粉碎技术是粮油深加工中的常用技术。高压气流超细粉碎是国际世纪年代发展起来的高新技术,广泛应用于粮油资源转化成食品、医药、化妆品等工业,可将淀粉颗粒粉碎至微米,也可将纤维素粉碎至几个微米,在粮油深加工和副产品综合利用方面有着重要的应用价值。 超临界二氧化碳萃取和分子蒸馏技术。超临界二氧化碳萃取和分子蒸馏技术,是粮油深加工中一些高附加值精细产品制备的必备技术手段,超临界二氧化碳萃取技术利用粮油及副产品中的某些功能成份。如维生
9、素、天然功能色素可溶解于超临界二氧化碳中,得到分离;如甾醇、碳醇可通过分子蒸馏把它们从混合物中蒸馏出来,获得高纯度产品。 微胶囊化技术。这是一种制造各功能性粉沫油脂,粮油及副产品中的功能成份的微胶囊化包埋保护的必备的高新技术,易氧化、变质的的高附加值产品经微胶囊化后,可延长这些物质的储存期,并还有缓释功能和满足某些物质特殊的功能要求。 快速检测技术。为确保粮油加工产品的营养、安全、卫生,对粮油加工的原料、在制品、成品的快速检测技术已是高新技术在粮油加工中的重要组成内容。1.3 螺旋榨油机的工作原理螺旋榨油机的工作原理概括为:榨油机运转时,预处理好的料胚从料斗进入榨膛,榨膛由榨条和榨圈组成。料胚
10、由榨螺的螺旋逐渐推进受到二次压榨,压榨力的来源是:料胚由1-2节榨螺向前推进到3节榨螺,由于3节榨螺根径逐渐增大(即牙形高度逐渐减小)螺纹逐渐加宽,从而榨螺与榨圈间的容积逐渐减小,进而将料胚推进到4节榨螺与5节榨螺处,榨膛容积增大,料胚被松散后继续向前推进。通过调节调饼头与出饼圈之间的间隙,控制出饼厚度,由于榨膛的特殊结构,料胚在榨膛产生复杂的相对运动和很大的摩擦力,致使油料的纤维的胶体遭受破坏,在巨大的压力下,油就从榨条缝隙和榨圈的出油槽中挤出来。1.4 榨油的工艺流程油料在进入油机前,需要过一系列的预处理,一般有清选,棉籽脱绒或带壳油料的剥壳和破碎、软化、轧胚、蒸炒等工序。大豆工序:大豆清
11、选破碎(分离)(粗轧)软化轧胚蒸炒压榨毛油(豆饼)1.5 设计榨油机的一般程序一部机器的质量基本上决定于设计质量。制造过程对机器质量所起的作用,本质上就在于实现设计时所规定的质量。因此,机器的设计阶段是决定机器好坏的关键。1.5.1计划阶段在根据生产或生活的需要提出所要设计的新机器后,计划阶段只是一个预备阶段。此时,对所要设计的机器仅有一个模糊的概念。在计划阶段中,对所设计的机器的需求情况作充分的调查研究和分析。通过分析,进一步明确机器所应有的功能,并为以后的决策提出由环境、经济、加工以及时限等各个方面所确定的约束条件。在此基础上,明确地写出设计任务的全面要求及细节,最后形成设计任务书,作为本
12、阶段的总结。设计任务书大体上应包括:机器的功能,经济性及环保性的估计制造方面的大致估计,基本使用要求,以及完成设计任务的预计期限等。此时,对这些要求及条件一般也只能给出一个合理的范围,而不是准确的数字。例如可以用必须达到的要求、最低要求、希望达到的要求等方式予以确定。1.5.2 方案设计阶段本阶段对设计的成败起关键作用。在这一阶段中也充分地表现出设计工作有多个解(方案)的特点。机器功能得分析,就是要对设计任务书提出的机器功能中必须达到的要求、最低要求及希望达到的要求进行综合分析,即这些功能能否实现,多项功能间有无矛盾,相互间能否替代等。最后确定出功能参数,作为进一步设计的依据。在这一步骤中,要
13、恰当处理需要与可能、理想与现实、发展目标与当前目标等之间可能产生的矛盾问题。确定功能参数后,即可提出可能的解决办法,亦即提出可能采用的方案。寻找方案时,可按原动部分、传动部分及执行部分分别进行讨论。较为常用的办法是先从执行部分开始讨论。进行机器评价时,还必须对机器的可靠性进行分析,把可靠性作为一项评价的指标。从可靠性的观点来看,盲目的追求复杂的结构往往是不明智的。一般地讲,系统越复杂,则系统的可靠性就越低。为了提高复杂系统的可靠性,就必须增加并联设备系统,而这不可避免地提高机器的成本。通过方案评价,最后进行决策,确定一个根据进行下步技术设计的原理图或机构运动简图。在方案设计阶段,要正确地处理好
14、借鉴与创新的关系。同类机器成功的先例应当借鉴,原先薄弱环节及不符合现有任务要求的部分应当加以改进或者根本改变。既要积极创新,反对保守和照办原有设计,也要反对一味求新而把合理的原由经验弃置不用这两种错误倾向。1.5.3 技术设计阶段技术设计阶段的目标是产生总装配图及部件装配草图。通过草图设计确定出各部件及其零件的外形及基本尺寸,包括各部件之间的连接零、部件的外形及基本尺寸。最后绘制零件的工作图、部件装配图和总装图。为了确定主要零件的基本尺寸,必须做以下工作: 机器的运动学设计根据确定的结构方案,确定原动机的参数(功率、转速、线速度等)。然后,做运动学的计算,从而确定各运动构件的运动参数(转速、速
15、度、加速度)。 机器的动力学计算结合个部件的结构及运动参数,计算各主要零件所受载荷的大小及特性。此时求出的载荷,由于零件尚未设计出来,因而知识作用于零件上的公称或名义载荷。 零件的工作能力设计已知主要零件所受的公称载荷的大小和特性,即可做零部件的初步设计。设计所依据的工作能力准则,需参照零部件的一般失效情况、工作特性、环境条件等合理地拟定,一般有强度、刚度、振动稳定性、寿命等准则。通过计算或类比,即可决定零部件的基本尺寸。 部件装配草图及总装配草图的设计根据已定出的主要零部件的基本尺寸,设计出部件装配图及总装配草图。草图上需对所有零件的外形及尺寸进行结构化设计。在此步骤中,需要很好的协调各零部
16、件的结构及尺寸,全面地考虑所设计的零部件的结构工艺性,使全部零件有最好的构形。 主要零件的校核有一些零件,在上述第三部中由于具体的结构未定,难于进行详细的工作能力计算,所以,只能作初步计算及设计。在绘制部件装配草图及总装配草图以后,所有零件的结构及尺寸均为已知,相互邻接的零件之间的关系也为已知。只有在这时,才可以较为精确的定出作用在零件上的载荷,决定影响零件工作能力的各个细节因素。只有在此条件下,才有可能并且必须对一些重要的或者外形及受力情况复杂的零件进行精确的校核计算。根据校核的结果,反复地修改零件的结构及尺寸,直到满意为止。草图设计完成以后,即可根据草图业已确定的零件基本尺寸,设计零件的工
17、作图。此时,仍有大量的零件结构细节要加以推敲和确定。设计工作图时,要充分考虑到零件的加工和装配工艺性、零件在加工过程中和加工完成后的检验要求和实施方法等。有些细节安排如果对零件的工作能力有值得考虑的影响时,还需返回去重新校核工作能力。最后绘制除标准以外的全部零件的工作图。按最后定型的零件工作图上的结构及尺寸,重新绘制部件装配图及总装配图。通过这一工作,可以检查出零件工作图中可能隐藏的尺寸和结构的错误。人们把这一工作通俗地称为“纸上装配”。1.6 本章小结本章节通过查阅图书及网上资料,了解了国内和国外市场上榨油机的现状和未来的发展方向,同时了解了螺旋榨油机的工作原理与工艺流程,并提出螺旋榨油机的
18、初步设计方案和工艺设计计划。第2章螺旋榨油机的设计计算2.1 电动机的选取本次设计适于大豆、菜籽等多种油料作物,对象是中、小型油厂,因此选取的电机功率不高。电机型号 YL-112M-7 额定功率 7.5KW ;额定电流=8.8A ; 效率 =84 % ;功率因数 cos=0.82 ;Tmax/TN =(最大转矩)/(额定转矩) = 2.3 ; Tmin/TN =1.5 ; 总传动比 =6.98 2.2 螺旋榨油机主要参数的确定2.2.1 榨膛容积比 ch (2.1)查表15. 5-1坯实际压缩比P=2.39 ; 实际压缩比n=3.25本次设计的螺旋榨油机对象是大豆,其总压缩比7.514 ,取7
19、.52.2.2 进料端榨膛容积Vj的计算根据设计能力等参数,可按下式计算:Vj=QBm/60KfKnrmn (2.2)将数据代入公式3.2得: Vj=(300kg/h0.91000)/(600.60.70.760r/min)=255.102 cm因此VJ=255.102 ;出坯率m=0.9 ; 料坯充满系数Kf=0.6 ;系 数Ke=0.7; 入榨料坯容重rm=0.7/ ;出口端榨膛容积Vch ,由公式3.1 VJ/Vch 推出 Vch= VJ/=18.22 cm2.2.3 功率消耗理论公式Nr=(qnRp)/6000 (kw) (2.3)对于中小型机器r=57 kw ;取 r=6kw 2.2
20、.4榨膛压力P=(2471n5.5)/e0.022w (kPa) (2.4)将数据代入公式3.4得:P=(24710.000853.255.5)/e0. 0223.5=1372.94 kPa2.2.5榨膛压缩比曲线本设计的螺旋榨油机,是二级压榨型,其曲线图2.1 :图2.1 榨膛压缩比曲线2.3 榨螺轴的设计计算榨螺轴是螺旋榨油机的主要工作部件之一,榨螺轴的结构参数、转速、材质的选择对形成榨膛压力、油与饼的质量,生产率和生产成本有很大关系。在设计中,采用套装式变导程二级压榨型榨螺轴,如图2.2,它将榨螺分成若干段,套装在芯轴上用螺母压紧,连续型榨螺轴的相邻榨螺紧接,没有距圈,结构较简单,榨膛压
21、力较大,回料少,但齿型复杂,加工须配置专用机床,适用于较小型榨油机。图 2.2 榨螺轴2.3.1 连续型榨螺轴尺寸如下表所示:表2.3.1 榨螺轴尺寸表榨螺号1234567节长1201108030454545导程42423631.531.5螺旋外径70707070707070螺旋内径505050/6769.2/6759/64.364.3/69.669.6/76.6齿顶宽/齿根宽6/166/166/168/9.911.7/13.6 2.3.2 榨螺齿形锥形根圆榨螺榨螺齿形尺寸30;=1545,最大为90;10;榨螺最小壁厚=(D0-d)/2=620 mm,取6 mm . 图2.3 3号榨螺2.3
22、.3 榨螺材料榨螺用15或20号低碳钢经气体渗碳(渗碳层厚度为1.52mm),淬火、回火处理后,表面硬度为HRC5862 。2.4 轴和轴啮合齿轮的计算2.4.1 齿轮的选用选用直齿圆柱齿轮传动,级精度。已知输入功率P1=7 kw ; 小齿轮转速n1=418.6 r/min ; 齿数比u=i1=2.25 条件:带式输送机,工作平稳,转向不变。1、材料选择轴上的小齿轮材料为45#,硬度为217255HBS,取硬度为240HBS,啮合的中齿轮材料为QT500-5(调质),硬度(147241)HBS,硬度取为200HBS 。2、齿轮齿数的选择小齿轮的齿数Z1=13,中齿轮的齿数为Z2=iZ1=29.
23、25,取Z=30芯轴转速n=60r/min3、按齿面接触强度设计. 确定公式 d1t2.32 (2.5)公式3.5内的各计算数值. 试选载荷系数:K1=1.3. 计算小齿轮传递的转距:T1 =95.5105P1/n1 =95.51057/418.6=6.126104 Nmm. 齿宽系数d=1. 由表查得材料的弹性影响系数ZE=181.4 Mpa1/2. 由图册按齿面硬度查得:小齿轮的接触疲劳强度极限:Hlim1= 650 MPa大齿轮的接触疲劳强度极限:Hlim2= 550 Mpa. 由公式计算应力循环次数N1 = 60 n1jLh = 60418.61( 2830010) = 1.2109N
24、2 =0.53109. 接触疲劳系数 KHN1=0.9 ,KHN2=0.87. 计算接触疲劳许用应力取失效概率为 1%,安全系数为 S=1,H1 =KHN1Hlim1/s =0.9650 = 585 MpaH2 =0.87550 = 478.5 Mpa. 计算. 试算小齿轮分度圆直径 d1t , 代入H中较小的值d1t2.32 (2.6)经计算得 d1t=67.499 mm . 计算圆周速度V =d1tn1/(601000) = 3.1467.499418.6/(601000) =1.479 m/s.计算尺宽b = dd1t = 167.499 = 67.499 mm. 齿宽与齿高之比 b/h
25、模数: mt= d1t/z1 = 67.499/13 = 5.192 mm齿高: h=2.25 mt =2.255.192 =11.683 mmb/h = 5.778. 载荷系数根据v=1.479 m/s , 7级精度,由图册查得动载系数 KV =1.08.直齿轮,假设 KAFt / b 100 N/mm ,由表查得:KH=KF=1.2 ;由表查得:使用系数KA=1 ; 由表查得:7级精度,小齿轮相对支承,非对称布置时KH =1.12+0.18(1+0.6d2) d2 + 0.2310-3b =1.12+0.18(1+0.612)12+0.2310-367.499=1.424由b/h=5.77
26、8, KH=1.424 查得 KF=1.52 ; 故载荷系数为:K=KAKVKHKH =11.081.21.424 =1.845按实际的载荷系数校正所算得的分度圆直径,由公式3.7d1 = d1t = 67.499 (2.7)得 d1 = 75.85 mm. 计算模数 m= d1/z1 =75.85/13 =5.835 mm4、按齿根弯曲强度设计m (2.8). 确定公式内的各计算数值. 由图册查小齿轮的弯曲疲劳强度极限FE1=560 Mpa ;大齿轮的弯曲疲劳强度极限FE2=440 Mpa. 由图册查得弯曲疲劳寿命系数:KFN1=0.85 , KFN2 =0.88. 计算弯曲疲劳许用应力取弯
27、曲疲劳安全系数 S=1.4F1= MpaF2= Mpa. 计算载荷系数K=KAKVKFKF=11.081.21.52=1.97. 查取齿形系数YFa1=3.13 YFa2=2.52. 应力校正系数:YSa1=1.48 YSa2=1.625. 计算大小齿轮的并加以比较:1=0.013622=0.01480 大齿轮的数值大。. 设计计算由公式3.8得:m=3.09 mm对比计算结果,取按齿根弯曲强度设计的,m=3.09 mm,就近圆整为标准值 m=3 , 按接触疲劳强度计算分度圆直径 d1=75.85 mm ,从而计算出小齿轮齿数 z1=d1/m=75.85/3=25.28=26大齿轮齿数 z2=
28、uz1=2.2526=58.5 ,取 z2=595、几何尺寸计算. 计算分度圆直径d1=z1m=263=78 mmd2=z2m=593=177 mm. 计算中心距a=(d1+d2)/2=127.5 mm. 齿轮宽度b=dd1=178=78 mm取 B2=80 mm , B1=85 mm6、验算Ft=2T1/d1=29.126104/78=2340.77 NKAFt/b=12340.77/78=30 N/mm 100 N/mm.所以,该齿轮设计符合要求。2.4.2 确定小齿轮的齿形参数 标准直齿圆柱齿轮几何尺寸: 分度圆直径d :d1=mz1=326=78 mmd2=mz2=359=177 mm
29、 齿顶高haha=ha*m=13=3 mm 齿根高 hf=(ha*+c*)m=(1+0.25)3=3.75 mm 齿全高 h=ha+hf =(2ha*+c*)m=3+3.75=6.75 mm 齿顶圆直径 da1=d1+2ha=(z1+2ha*)m=78+23=84 mmda2=d22ha=(z22ha*)m=17723=183 mm 齿根圆直径 df1 =d12hf=(z12ha*2c*)m=(262120.25)3=70.5 mmdf2=d22hf=(z22ha*c*)m=169.5 mm 基圆直径 db1=d1Cos=78Cos20o=73.296 mmdb2=d2Cos=177Cos20
30、o=166.326mm 齿距p=m=3=9.42 mm 齿厚s=m/2=3/2=4.7 mm 齿槽宽e=m/2=4.7 mm 中心距a=(d2d1)/2=m(z2z1)/2=127.5 mm 顶隙 c=c*m=30.25=0.752.5 轴的计算校核2.5.1 选材及表面预处理1.材料: 轴主要用碳钢,本设计从经济实用角度选用45#钢.2.热处理: 高频淬火,表面强化处理喷丸,提高轴的抗疲劳强度,45#钢热处理调质 .轴表面淬火处理: 淬硬层深度耐磨.3.工作条件: 载荷不大,深度 0.51.5 mm.2.5.2 轴的结构设计1.轴肩高度 a=(0.070.1)d (d为轴的直径,轴环宽度b=
31、1.4a)按扭矩强度条件计算T=T/wT=9.55106p/( 0.2nd3 )T (2.9)其中 T 为扭转切应力,单位是 Mpa.轴45#钢 T=2545 Mpa A0=126103 mm32.轴的直径 d= (2.10) 式中取A0=105 mm3轴传递的功率 p=4 kw,轴的转速 n=418.6 r/mind=22.28 mm对于直径d100 mm的轴,有一个键槽时,轴径增大5%7%,为将轴径圆整为标准直径, d= mm, L=60 mm,( L长系列60 mm,短系列42 mm) 。 此处为轴的校核图形,图2.4 轴的受力图总弯矩 M=474 Nm校核轴的强度,按第三强度理论计算应
32、力 (2.11)对于直径为d的圆轴,弯曲应力=M/w,扭转切应力 =T/wT=T/2w (2.12)其中,w (mm3) 为轴的抗弯截面系数,W=式中 b=6,t=4,d=28 mm则轴的弯矩合成强度条件为:/1842.89=50 Mpa-1对称循环应变力时,轴的许用弯曲应力经查表得-1=60 Mpaca-1 符合强度要求. 轴所受的载荷是从轴上零件传来的。计算时,常将轴上的分布载荷简化为集中力,其作用点取为载荷分布段的中点,作用在轴上的扭矩,一般从传动件轮毂宽度的中点算起。通常把轴当作置于铰链支座上的梁,支反力的作用点与轴承的类型和布置方式有关。2.6 皮带轮的设计计算小带轮的基准直径 d1
33、=71 mm ; 大带轮的基准直径 d2=315 mm平带传动在传动中心距较大的情况下平带的材质选用帆布芯平带。带轮带宽b=50 mm ,带轮宽 B=63 mm 求带速 d1=(601000v)/(n1) 其中n1=418.6r/min ,d1=71mm ; i=n1/n2 imax ,查表13-1-42 取i=3 ,则n2=139.53r/min ;带厚=1.2n ,查表13-1-45 n=3 ,则=3.6mm .初定中心距 a0 1.5(d1+d2) a05(d1+d2) ,则579 a01502.7 键的选择设计 2.7.1 键的选择键的截面尺寸bh由轴的直径d由标准中选定。键的长度L一
34、般可按轮毂的长度而定,即键长等于或略短于轮毂的长度。I轴 :d=22 mm 处选用普通平键键宽b键高h bh =66 . 键L , L1=25mm,L2=56mm,轴深度 t=4.0 mm2.7.2 键的校核计算假定载荷在键的工作面上均匀分布,普通平键连接的强度条件为p=2T103/(kld) p (2.13)T传递的转矩为 T=9.126104 N mmK键与轮毂键槽的接触高度,k=0.5h=0.56=3 mml键的工作长度,圆头平键l=L-b=56-6=50mmd轴的直径 d=22 mmp 许用挤压应力 p =100120 Mpa, 查表取 p=110 Mpa将数值代入公式 p=29.12
35、610103/(35622)=55.309Mpap=110 Mpa 符合标准。故,键的标记为: 键656 .2.8 轴承的设计2.8.1 轴承寿命 Lh=106/(60n)(c/p) (2.14)对于滚子轴承,=10/3,我们计算I轴的滚动轴承为圆锥滚子轴承32905。已知: n=418.6 r/min ,预期计算寿命Lh=5000h. 由公式得出,C求比值 Fa/Fr=1284.3/2966=0.43Lh (2.17)故所选轴承为圆锥滚子轴承32905 ,满足寿命要求 。2.9 本章小结本章主要为螺旋榨油机的强度计算和校核,并在校核中对零件结构的合理性进行了分析。为榨油机的结构设计做了基础性
36、铺垫。第3章 螺旋榨油机的结构设计3.1 榨螺轴的设计榨螺轴是由芯轴,榨轴,出渣梢头,销紧螺母,调整螺栓,轴承等构成。装配榨轴时,榨螺与榨螺之间必须压紧,防止榨螺之间出现塞饼现象,必须拧紧销紧螺母,饼的厚度用旋转的调整螺栓来控制。6个榨螺型号不同,材料为20# .3.2 榨笼的构造榨笼是由上下榨笼内装有条排圈,条排,元排所构成。条排24件,元排17件,还有压紧螺母内装有出饼圈,榨膛的两端分别于齿轮箱和机架相连接。3.3 齿轮箱的构造及入料器的构造齿轮箱是由齿箱盖,齿箱体,圆柱齿轮,传动轴,轴承,皮带轮等构成,可从顶部油塞孔加机油,从油标处看加油高度。入料器的组成主要有立轴,锥齿轮,轴承支座,固
37、定板,锥斗等,使用自动进料器可以节省劳动力,提高生产效率。3.4 带轮的结构设计大三角带轮的结构尺寸基准直径 dd=330mm ,带轮宽B=(Z-1)e+2f=30.3 mm,槽间距e=120.3 ,取e=12.3 mm .第一对称面至端面的距离 f=81 ,取f=9.15 mm ,基准线上槽深 ha=2.0 mm ,外径 da=dd+2ha=334 mm ,最小轮缘厚 =5.5 mm ,取=10 mm .基准下槽深 hf=9.0 mm , 轮槽角=38 .基准宽度 bd=8.5 mm .d1=(1.82)d=44 mm ,d2=da-2(ha+hf+)=292 mm ,h1=290=38.7
38、7 mm ,h2=0.8h1=31.01 mm ,b1=0.4h1=15.508 mm ,b2=0.8b1=12.4064 mm ,f1=0.2h1=7.754 mm ,f2=0.2h2=6.202 mm ,L=(1.52)d=30.3 mm .3.5 调节装置的设计调节装置的主要目的是调节出渣的粗细,相应的改变榨膛的压力机构,为抵饼圈整轴移动或出饼圈同芯轴一起做轴向移动。其结构简单,操作方便,机架的受力能在运转中调节,但芯轴的轴2头易损坏。由于采用整轴移动或夹饼圈,因此螺栓连接松脱现象比较严重,此装置平稳,低速重载的静载荷,因此采用对顶螺母,两螺母对顶拧紧后,使旋合螺纹间始终受到附加的压力和
39、摩擦力的作用,工作载荷有变动时该摩擦力仍然存在。3.6 键的选择键是一种标准零件,通常用来实现轴与轮毂之间的周向固定,以传递转矩,有的还能实现轴上零件的轴向固定或轴向滑动的导向。3.6.1 轴上的键 轴径 d=22 mm , bh=87 ,L=180 mm ,轴径 d=28mm处的为普通平键,公称尺寸 bh=87 ,键长 L=70 mm ;3.6.2 轴上的键 轴径 d=28 mm , bh=87 , 键长 L=140 mm ;3.6.3 芯轴上的键, 轴径 d=35 mm , bh=108 , 键长 L=180 mm ;轴的深度 t=5.0 mm .3.6.4 芯轴上的键, 轴径 d=35
40、mm , bh=108 , 键长 L=450 mm .3.7 滚动轴承的选择3.7.1 轴上的轴承的选择轴上的大齿轮 B=95 mm ,B200 , d=35 mm ,内径 D=35 mm ,D1=1.8D=63 , 轮毂厚t ,t=14 mm ,L=(1.21.5)D=52.5 mm , =(2.54)mn=108 , H1=0.8D=28 ,H2=0.8H1=22.4 ,C=H1/5=5.8 ,但要求 C10 ,取 C=10 ,S=H1/6 ,取 S=10 ;选用芯轴上的轴承时,依据D1来选,D1=63 mm ,选调心滚子轴承,型号为22212 ,尺寸如下:d=60 mm ,D=110 m
41、m ,B=28 mm ,Cr=81.8 KN ,COr=122 ,脂润滑 n=3200 r/min ,重量 W=1.22 kg .d2=75.7 mm ,D2=93.5 mm ,rmin=1.5 ,安装尺寸 damin=69 mm ,Damax=101 mm ,ramax=1.5 ;计算系数 e=0.28 ,Y1=2.4 ,Y2=3.6 ,YO=2.4 .3.7.2 轴和轴的轴承选用相同型号的轴承,圆锥滚子轴承,型号为32905 ;轴径 d=25 mm ,基本尺寸 d=25 mm ,D=42 mm ,T=12 mm ,B=12 mm ,C=9 ,COr=21 ,Cr=16 ,W=0.064 k
42、g ;计算系数 e=0.32 ,Y=1.9 ,YO=1 ,其他尺寸 a=8.7 ,rmin=0.3 ,r1min=0.3 ,ramax=rbmax=0.3 ,=1018,取=153.8 榨螺轴与齿轮轴的联接设计为了拆装方便,本设计齿轮箱与榨笼采用法兰盘连接。而榨螺轴与齿轮轴采用凸缘连轴器联接,它是一种刚性联轴器,其所要求联接的两轴必须严格对中,因此对机器安装精度要求较高,否则会在轴中引起很大的附加应力。如图3.1是利用绞制孔用螺栓联接来实现两轴的队中,靠螺栓杆部承受剪切和挤压来传递转距。安装时不用移动轴,但绞孔加工较麻烦。3.9 本章小结本章主要为螺旋榨油机的总体设计,和标准件的选择。标准件的
43、选用使得榨油机的易损零件更换起来更加容易和方便。第4章 螺旋榨油机的安装使用4.1 螺旋榨油机的润滑与保养1、所有油杯、油眼至少每天加油一次。2、减速齿轮箱内所用齿轮油,除在试车时加入外,以后在每次定期大检修时,必须加以过滤或更换。如发现变质则应随时更换。加油量不宜超过大齿箱下部油标油面线,以免过量油从主轴漏出,污染干饼块。3、校饼和螺旋轴部分定一个月检修一次。检修时必须除去油粕,彻底清洗检查,如榨螺、衬圈发现裂缝或其它损坏时,需进行修理或调换(如停车一段时期后在下次开车前必须先进行检修一次)。4、整台榨油机一般可定6个月大检修一次。检修时必须全部拆开清洗检查,如有损坏,需进行修理或调换。润滑
44、部位: (1)齿轮减速箱内齿轮用机油;双曲线齿轮油或3040号机油。(2)调节螺栓内套机油。(3)滚动轴承 润滑脂。(4)料斗部分轴承座机油 ,齿轮植物油。齿轮减速箱内的润滑油从箱盖的油孔加入。减速器下部设放油螺塞,油位的高低以油标中心高为准,由于榨油机在使用中温度高,因此应用粘度较大的机油作润滑油,在使用中难免有少量的植物油渗入润滑油中,所以在榨有氧气性油料如桐籽,大豆,亚麻籽等时所用润滑油应采用有抗氧化性的机油。调节螺栓上没有注油螺塞,拆下螺塞即可加油润滑其内套。4.2 榨油机的安装榨油机购回后,应选择光线充足,空气流通,有足够作业面积的室内安装,应根据机器的说明书进行检查。着重检查机器安
45、装是否正确,各连接管、件是否牢固和安全。然后调试,使机器处于正常的工作状态。正式开机前,一面检查零部件有无松动和损坏。各轴承润滑油是否充满。转动皮带轮,倾听传动件间有无撞击或其他杂音,若无方可开机。调整螺旋轴与出饼圈的间隙,方法是先使螺旋轴向前抵死饼口,然后倒退23转,使间隙控制在0.51毫米。安装需要注意的几点: 现场安装具体结构、混凝土成分配合,依当地土壤情况决定。 水泥底高度可按实际需要施工。 电动机安装于轨座上。电动机的水泥底座,必须根据所配电动机及其轨座尺寸施工。 榨油机安装时应校正水平。4.3 螺旋榨油机的使用同一台榨油机,不同的人操作,会有不同的出油率,生产率。这就是说明,操作者
46、技术及熟练程度是紧密相关的,因此,无论谁使用榨油机,在使用之前都要做好如下准备工作。榨油之前必须要对油料进行预处理。4.3.1 油料的预处理油料压榨前必须进行预处理,因为它直接影响榨油机的性能、寿命、安全、油品质量及出油率,预处理过程如下: 油料的清选:无论什么种类的油料,都要进行清选,清出其中的泥沙、石子、金属等杂物,如果清选不好会加快零件磨损,或导致油机损坏,也影响出油率。 剥壳和分离为了充分发挥榨油机的生产能力,必须事先把带壳的油料剥挣或分离开来。如花生、桐籽、棉籽等。 破碎与扎坯对颗粒较大的油料,如花生仁、大豆、棉籽等,最好要经过破碎和扎坯,破坏油料仁的组织,扩大受热面积,便于软化,提
47、高出油率。 蒸炒蒸炒是提高出油率的关键,是热榨的必备工序,蒸炒温度因油料不同而各异。料坯蒸炒应均匀,保温要好,适当控制含水量。4.3.2 试车前的调整: 齿轮箱,调节螺栓内的轴套,都要先注机油;新榨油机安装完成后,试车前各润滑部分应加注润滑油脂后才可开车。 紧固底座螺栓及其它各部位螺栓; 搬动调节螺栓手柄,看转动是否灵活,搬动大三角带轮,看齿轮传动是否有阻力 松开紧定螺母,搬动调节螺栓手柄使导饼环与出饼圈接触,然后按顺时针方向转45圈,再把紧定螺母销紧;榨笼榨条间的缝隙,必须根据所榨油料先进行调整,可以调换榨条间的垫片来调节。调整榨条间隙时,各长、短压板相互之间应基本平直,切忌异峰突起,以免跑
48、渣。压榨过程中出现跑渣,不宜单纯过分旋紧大螺栓,以免造成螺栓塑性变形而强度减弱。大量跑渣时应打开榨笼壳,检查各部,调整各长、短压板之间平直度,以保证榨笼壳上、下压紧免于跑渣。 点电动机,检查榨轴旋转方向是否正确。正确后,让榨油机空车运转半小时,观察各部分有否不正常现象,注意各部分轴承有否过热现象,齿轮运转有否不规则噪音,机身是否振动反常,以及各运转部分有否与杂物碰击声响,证明一切正常后即可开始试车。4.3.3 压榨前的试车 榨油机运转正常后,便可小量投入试车,必须慢慢地投料,投料后,观察出饼情况,此时投料不能急。料多榨膛压力突增,负荷加大,易引起堵塞。严重时会使榨笼爆裂。 此时榨螺与榨笼温度很
49、低,尚不能进行榨油,要想使本机达到良好效果,按经验机体温度须达到烫手的程度(约80o以上)。因此试车过程也是升温过程。需使料坯通过榨笼来提高温度,缓缓投料十余分钟后,看出饼圈是否有饼片推出,为此必须将出饼端的缝隙尽量开大,使校饼指针接近“-2”,让熟坯顺利通过榨笼,同时将下料门逐步开大,约半小时左右,待榨笼温度升高后,再逐步缩小出饼端的缝隙至3mm左右(即指针指示在“0”的位置),饼即成瓦状排出,榨笼出油量逐步增加,出油位置亦渐渐自出饼端向前移至第一、第二档榨条交接处,此时电动机负荷亦稳定在1216A左右,此后出饼在12毫米厚度片状时(此时会出现一瞬间的粗糙磨合声响,克服过后,就会正常出饼)机
50、膛要磨合2040分钟,目的是使机膛升温,达到烫手的程度,这是出油也最旺,属于正常状态,则说明榨油操作过程已臻于正常,即可长期保持这种情况,此时紧定螺母锁紧就不要动了,为连续压榨做好准备。4.3.4 投产压榨以上准备工作都正常后,就可以正式投产了, 压榨时,应严格控制出饼厚度,油料品种不同,压榨次数不同,出饼厚度的控制要求也不同,一般0.32.5毫米。具体数据可参照各榨油机的说明书要求,视情况而定。压榨芝麻等出油率较高的油料时,可分批投料(每批5公斤为宜),每批连榨23次。因首批压榨,油流较大,带走的热量较多,可将首批压榨后的油饼立即装机进行第二三次压榨。再压榨时出油相对减少,油流带走的热量较少
51、,可使机器温度马上回升到7080,以保证正常工作机温。每批投料,均应按上述顺序进行。工作中,应用木棒勤捣进料斗以防油料口堵塞或搭桥,力求喂料均匀,交应及时清理漏渣,回收到油渣可放回料斗继续压榨。此时需要要观察注意以下三种情况: 就是正常投产,投料时也要均匀,必须是等量的徐徐送料。操作者细心掌握投料量是十分重要的环节。 观察电流表,如果超过1620安培,说明榨膛阻力增大,此时应松动调节螺栓,使饼增厚迅速排饼。(此时还会有一个现象,就是第十六和十七号圆排的油道会出现条饼现象)这是因为投料过猛所至。如果电流表读数急于下降,排饼速度显著减慢,那是进料器棚料,可用木棒捅一捅。经过次处理后,仍然不见效果,
52、那就说明在第4号榨螺处形成坚固饼圈,搪塞进料,此时应立刻停车,退出榨轴,清理榨膛,原因清楚后再继续压榨。 如果运转,压榨,排饼,出油都正常时,那就要稳定投料量和速度来保证。此时就要注意倾听整机运转声音有无不正常声响,如果没有可连续压榨。4.3.5 停车 正常停车,应将料胚全部榨完。再将生坯加入榨笼挤出硬饼和剩余熟坯,当在出饼端发现排出生坯时, 松动紧定螺母将榨轴反复进退数次,使膛内余料走完,抽出榨轴。清理干净,再捅进膛内。 紧急停车,因故障而停车,必须先停止上料。然后迅速松动紧定螺母,退出调节螺栓。如果扭不动,可用手搬动大三角皮带轮反转。由排料处排除膛料。再抽出榨轴,同作法。停机后清理停止工作
53、后,应抽出榨油机螺旋轴,及时清理榨膛及各间隙内残渣,以免硬结而影响下次工作。折榨螺时,应北将其托平,防止碰伤,卸下后应立放,以防变形。4.4 注意事项 正常运转时也不能粗心大意,应注意各部位工作情况。润滑是否良好,如果有不正常现象应停车及时处理。 油料作物应清选干净,严防混入金属物质。 严禁用金属捅料坯。 出饼圈和导饼环严禁无间隙开车。 使用自动进料器是件好事,但对于没有操作经验的人来说,开始就是用是不合适的。4.5 操作过程中出现的故障及排除4.5.1熟坯过分干燥时发生的现象 油机的榨笼内发出格!格!响声,并使整台榨油机振动。 出饼端瓦形饼不能成块而碎散,饼呈黑褐色而有焦斑。 榨油机的电动机
54、负荷高于正常(30A以上)。 出油位置移向出饼方向,出饼口冒青烟,出油减少,油色深褐。这些现象若持续时间较长,会造成榨油机重大损失事故,所以遇有以上情况时,关小下料门,减少向榨笼送料,放大出饼端间隙,以减小榨笼内压力,在进料口处加入生坯,使榨油机负荷逐步下降后,再加以调节使之恢复正常工作。4.5.2 熟坯温度太低、含水量较大时发生的现象 有时会不进料或进料少,料与轴一起转动。 饼块发松、发软,水汽很浓,饼带油,饼块由出饼口出来时跟着主轴一起转动。 榨油机的电动机负荷降低(12A以下)。 出油减少,油色发白起沫,出油位置移向进料方向。出现上述现象时,可在进料口处加入干的渣饼,这样可使榨油机逐步恢
55、复正常工作。4.5.3 一般常见故障及排除 榨油机榨油过程中,出现一般卡死现象时,可采用反搬三角带方法排除。如果反搬三角带轮也无济于事,那就扭下机架底角螺栓、松动下榨笼,拆下上榨笼,再送动压紧螺栓,依次松动圆排。并能清出饼结块,一直到能拉出榨轴为止,这一过程必须趁榨膛没有降温的情况下完成。 突然停车,螺旋轴卡死现象。压榨初期,榨膛未磨热即大量投料引起,可用热的油料籽(也可用加热水的干饼)缓缓进料,反复磨机,使温度升高。 压榨过程中,榨膛断料,然后又大量投料,造成排料不畅,榨膛被油料堵塞引起。因此,加料时应连续均匀,饼不能太薄。一旦发生故障,应立即关闭电源,将进料调节板插死,停止进料,并将排料板
56、打开,倒开螺旋轴,使之退出。然后清除膛内油料,重新压榨。油料未清选,有石子、金属等硬异物进入榨膛引起。 新榨油机或者是新换榨轴时,往往有不走料现象,有时不出饼或者是少量出饼,此时只要投入少量的残饼渣,慢慢投料,并调整出饼厚度即可。 不出油或出油率过低原料不湿或太干,受潮发霉,籽料不饱,杂质过多引起。须重新清选油料,并高速好油料水分。排油缝被油渣堵塞或榨条装配得太紧引起。应根据含油量高低,调整榨条的松紧度。开榨初期,榨膛温度低,出饼太薄或太厚、零件磨损等都会引起不出油或出油率过低。压榨过程中,有时会出现油析不出来的现象,有时不出饼或者是少量出饼,此时只要投入少量的残饼渣,情况就会好转。挺了一班后
57、再榨油,机膛内油排不出来。此时可能是圆排的油槽被枯饼堵死,应拆开上榨笼,取出圆排,在热水中浸泡十余分钟,用钢丝刷将油槽洗净。 当压榨含油量高或是粘度较大的油料时,应拆出排骨圈,重新装配条排。增大其间隙来解决排油问题。 易损件,如榨轴、出饼圈、导饼环、圆排等,当作业一个时期后,磨损过于严重就不能再用了,应及时更换。 跑渣过多榨油过程中,榨条间少量跑渣是正常现象。若跑渣过多,可能有如下原因:个别榨条弯曲或间隙过大。此时,可卸下榨条,用纱布或油石将甲型榨条三凸方打磨,调直榨条重装,必要时垫些薄铁皮,使间隙保持在0.050.08毫米范围内。油料塑性不好,出饼困难,使机膛压力增加。此时,应将油料适量拌水,并进行磨机,提高机温以提高油料塑性。如果出饼太薄。应按说明书要求适当加大出饼厚度。 出饼不顺原因之一是饼的厚薄不适宜,应调整出饼厚度;之二是由于有干饼或石子、铁块等硬异物进入机膛,应立即停机,抽出榨螺,检查并清除饼圈和机膛内的干饼、杂物。并根据出饼圈磨损情况,修理或更换新配件。 回油可能是因油缝堵塞或油缝太小表面不光引起。前者应拆除榨条进行清洗,后者应调整榨条间隙,用油石磨光油缝。 不进料油料的水分过多,应进行日晒或炒干。榨螺表面不光,应用砂布打磨榨螺轴或用干渣磨光。榨条磨损,榨条多边形被破坏,可翻转使用或损榨条。 烧膛原因为油料水分偏低,榨螺转速偏高,机温过高等引起,应提高油料水分含量,
- 温馨提示:
1: 本站所有资源如无特殊说明,都需要本地电脑安装OFFICE2007和PDF阅读器。图纸软件为CAD,CAXA,PROE,UG,SolidWorks等.压缩文件请下载最新的WinRAR软件解压。
2: 本站的文档不包含任何第三方提供的附件图纸等,如果需要附件,请联系上传者。文件的所有权益归上传用户所有。
3.本站RAR压缩包中若带图纸,网页内容里面会有图纸预览,若没有图纸预览就没有图纸。
4. 未经权益所有人同意不得将文件中的内容挪作商业或盈利用途。
5. 装配图网仅提供信息存储空间,仅对用户上传内容的表现方式做保护处理,对用户上传分享的文档内容本身不做任何修改或编辑,并不能对任何下载内容负责。
6. 下载文件中如有侵权或不适当内容,请与我们联系,我们立即纠正。
7. 本站不保证下载资源的准确性、安全性和完整性, 同时也不承担用户因使用这些下载资源对自己和他人造成任何形式的伤害或损失。