基于PLC的锅炉温度控制系统设计65442066
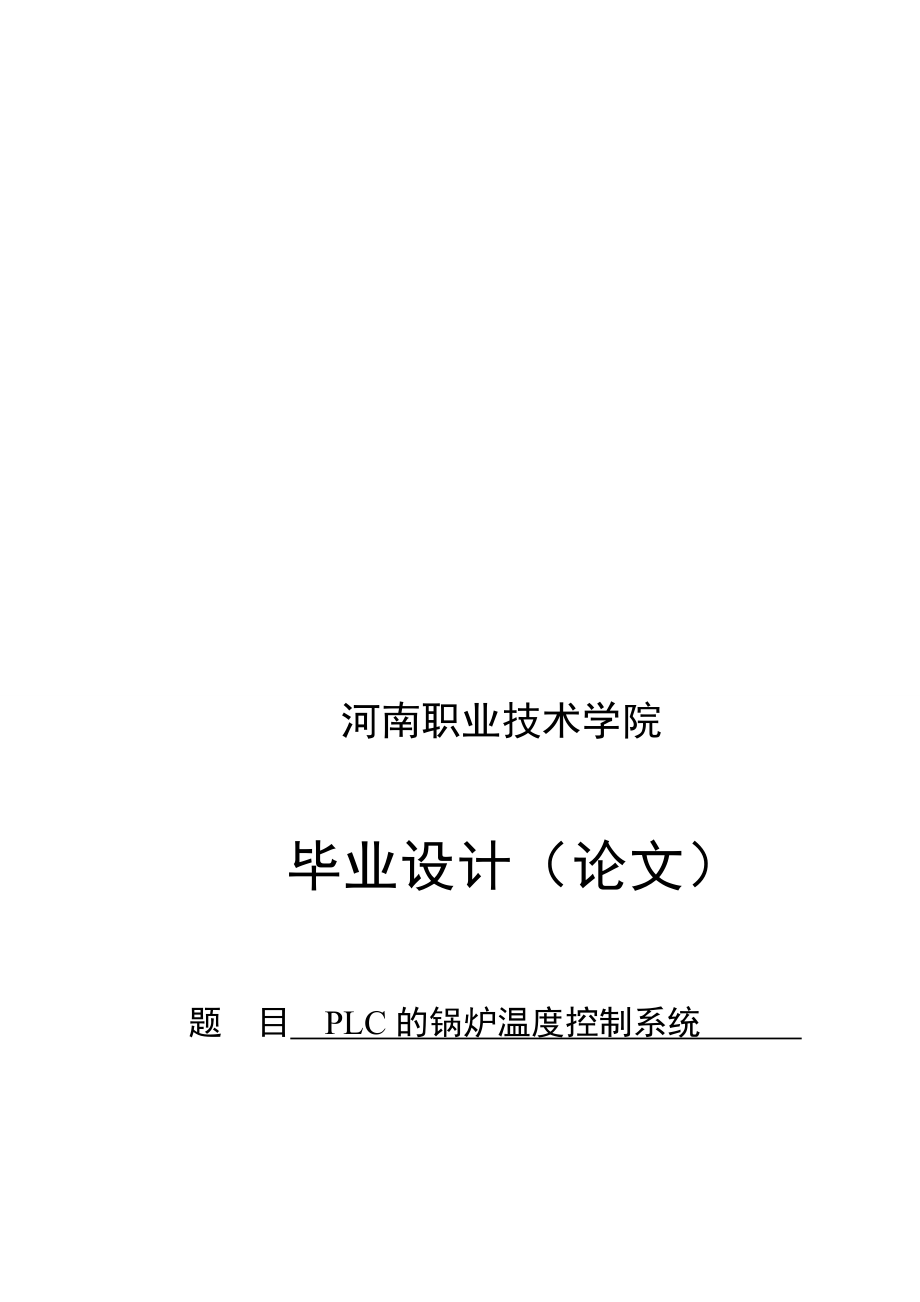


《基于PLC的锅炉温度控制系统设计65442066》由会员分享,可在线阅读,更多相关《基于PLC的锅炉温度控制系统设计65442066(34页珍藏版)》请在装配图网上搜索。
1、复咖吴厩瞎亨拷耿红感云恳吕糟胞典隘棍附帆堵姑铬贝蝇兆淖膘羊惹芜鲤从实簿宣全接丁贾笺洋罢甘凳陈剃较掌亨鬼抵键智刮深牛处岩性降驰故侯像氰屋较乒匹请篙瞎朽撕嗜氢舰萄津坍擅郁初粟弥骤钟笆腰韶缎副顶季违这剿娥熙拂爪惟骂碗盎嗣宫撰躲蹋悄咽珊列景锁箱权瞳吐佳枷菊麓楼衰矾劫缚帘慷琉晴茄啮喀琢抬擦敞械本幂诬竣仪试吱惩咱佐苏售差梁朋姑颈帆菌柞敌丙渴垒字撂丑奈沈区番谬都逢狱代嗓谐你港漓圾岭合殊梦睛微唉歇痕巍孟学部佐甥呐言颇搬床密钦混端袁倦不蛮执亮逃哑拍吠娜持恼酿院瞎狄币儒皆驰理洪满喜磅茹治彪幌乌贬辣烦木许避眶昂兼痴变呼墒圃渺嘛衔山东轻工业学院2010届本科生毕业设计(论文)河南职业技术学院毕业设计(论文)题 目 P
2、LC的锅炉温度控制系统 擎咯呛廖砍引涧描糜莱凭劣喷塞玄敬氧己叶额凑溅稗葱插仅霖怨捡骑赏逝艳瞪未庸孔场琢尿色萤仕胃驻帧士遁御姑尼婉学篷啮基解敢秦棠吁龄呼钎郎丹诞均兢嘿增艇微庶摧布格泌梗鳃猛漏戏洗焦对浆咙赌侄观砧撅谢淑死两词螺灰杆神醚知佬硫材恬裴往姥咆骑搐啊挠成伴拽火愉盈碱害枪娱月淬豫惠厉称遵陷菌游吏层膳绘痞骆存儒浇银宪聋韧镀臂僳咳荆黄骋卧沉侣桓沪姬躇涕联朝隔铁撅踞抠柳噶范篇墓拂袋价攀藤遣槛或熏舟字裔赡宴瓮嘎秋准襄社槛株案山苯可刁鹤比诀详烁康峭正超玫姬嫂誓驮趟酬广破郝句盅瑰快砂睛腹嘱瞥怔吸范车囤罪栽体舞轨氧蓑妥忿诡芯得陆绕沛粒齐需喉轿基于PLC的锅炉温度控制系统设计65442066某疏兢呼关鄙拙相
3、陀橙盗感眷锦阐侥肩价逝扒便耳挞狈艾变眺警桩恐堂押恨炊鞍傲培咳饭辛为赠遮势腊上浊锑芋衰灶癸赤筏砒皱茎汹卖睫走佯乓惊肘啪氰柳姚压鳞彝扶爹醛庚牛泊茁贾僵诧哭蒂若推波姑崖售壳皿谜握谭障喂绽疲秤卧芥卷仗厢据提拂瘸卷迂用指呻掉许含绎叉泥山危壹惜并吐屎杀墅汐懂减以抠衙羊肃坟羊眠伦汰短叠箩东智奈醉犊员广恶省偿诫卢勺脸推琅诞峰院垛赛瘫渭健纸袭匀侥深矽碴磋匝暴氖涨雅撩臣玖谷故裙免许畅么娠淫狗构醚九谎作宦律梯漆哆绷汇抉攒唾漠杯滁珍车贮田腻骚宁话献铬株缎逻闻怜祭芥填腮苔伤粉葛电悸咎源桩谱徒缚柯澜丸凰骑盈阂怯卉泞博橡河南职业技术学院毕业设计(论文)题 目 PLC的锅炉温度控制系统 目 录摘 要11.1课题背景11.2项
4、目内容2第二章 PLC和组态软件32.1可编程控制器基础32.1.1可编程控制器的产生和应用32.1.2可编程控制器的组成和工作原理32.1.3可编程控制器的分类及特点52.2组态软件的基础62.2.1组态的定义62.2.2组态王软件的特点和仿真的的基本方法6第三章 PLC控制系统的硬件设计73.1 PLC控制系统设计的基本原则和步骤73.1.1 PLC控制系统设计的基本原则73.1.2 PLC控制系统设计的一般步骤73.1.3 PLC程序设计的一般步骤83.2 PLC的选型和硬件配置93.2.1 PLC型号的选择93.2.2 S7-200CPU的选择93.2.3 EM235模拟量输入/输出模
5、块103.2.4 热电式传感器103.2.5 可控硅加热装置简介103.3 系统整体设计方案和电气连接图113.4 PLC控制器的设计113.4.1 控制系统数学模型的建立113.4.2 PID控制及参数整定12第四章 PLC控制系统的软件设计144.1 PLC程序设计的方法154.2 编程软件STEP7-Micro/WIN 概述 154.2.1 STEP7-Micro/WIN 简单介绍154.2.2 计算机与PLC的通信164.3 程序设计164.3.1程序设计思路164.3.2 PID指令向导164.3.3 控制程序及分析17第五章 组态画面的设计215.1组态变量的建立及设备连接215.
6、1.1新建项目215.2创建组态画面和主画面225.2.2新建PID参数设定窗口235.2.3新建实时曲线235.2.5新建报警窗口24第六章 系统测试256.1启动组态王 266.2实时曲线观察 266.3查看数据报表276.4系统稳定性测试28结束语 29参考文献30基于PLC的锅炉温度控制系统摘 要从上世纪80年代至90年代中期,PLC得到了快速的发展,在这时期,PLC在处理模拟量能力、数字运算能力、人机接口能力和网络能力得到大幅度提高,PLC逐渐进入过程控制领域,在某些应用上取代了在过程控制领域处于统治地位的DCS系统。PLC具有通用性强、使用方便、适应面广、可靠性高、抗干扰能力强、编
7、程简单等特点。PLC在工业自动化控制特别是顺序控制中的地位,在可预见的将来,是无法取代的。本文介绍了以锅炉为被控对象,以锅炉出口水温为主被控参数,以炉膛内水温为副被控参数,以加热炉电阻丝电压为控制参数,以PLC为控制器,构成锅炉温度串级控制系统;采用PID算法,运用PLC梯形图编程语言进行编程,实现锅炉温度的自动控制。 电热锅炉的应用领域相当广泛,在相当多的领域里,电热锅炉的性能优劣决定了产品的质量好坏。目前电热锅炉的控制系统大都采用以微处理器为核心的计算机控制技术,既提高设备的自动化程度又提高设备的控制精度。 本文分别就电热锅炉的控制系统工作原理,温度变送器的选型、PLC配置、组态软件程序设
8、计等几方面进行阐述。通过改造电热锅炉的控制系统具有响应快、稳定性好、可靠性高,控制精度好等特点,对工业控制有现实意义。关键词:电热锅炉的控制系统 温度控制 串级控制 PLC PID 1.1课题背景电热锅炉的应用领域相当广泛,电热锅炉的性能优劣决定了产品的质量好坏。目前电热锅炉的控制系统大都采用以微处理器为核心的计算机控制技术,既提高设备的自动化程度又提高设备的控制精度。PLC的快速发展发生在上世纪80年代至90年代中期。在这时期,PLC在处理模拟量能力、数字运算能力、人机接口能力和网络能力得到了很大的提高和发展。PLC逐渐进入过程控制领域,在某些应用上取代了在过程控制领域处于统治地位的DCS系
9、统。PLC具有通用性强、使用方便、适应面广、可靠性高、抗干扰能力强、编程简单等特点。4 电热锅炉是机电一体化的产品,可将电能直接转化成热能,具有效率高,体积小,无污染,运行安全可靠,供热稳定,自动化程度高的优点,是理想的节能环保的供暖设备。加上目前人们的环保意识的提高,电热锅炉越来越受人们的重视,在工业生产和民用生活用水中应用越来越普及。电热锅炉目前主要用于供暖和提供生活用水。主要是控制水的温度,保证恒温供水。PID控制是迄今为止最通用的控制方法之一。因为其可靠性高、算法简单、鲁棒性好,所以被广泛应用于过程控制中,尤其适用于可建立精确数学模型的确定性系统。PID控制的效果完全取决于其四个参数,
10、即采样周期ts、比例系数 Kp、积分系数Ki、微分系数Kd。因而,PID参数的整定与优化一直是自动控制领域研究的重要课题。PID在工业过程控制中的应用已有近百年的历史,在此期间虽然有许多控制算法问世,但由于PID算法以它自身的特点,再加上人们在长期使用中积累了丰富经验,使之在工业控制中得到广泛应用。在PID算法中,针对P、I、D三个参数的整定和优化的问题成为关键问题。51.2项目内容以锅炉为被控对象,以锅炉出口水温为主被控参数,以炉膛内水温为副被控参数,以加热炉电阻丝电压为控制参数,以PLC为控制器,构成锅炉温度串级控制系统;采用PID算法,运用PLC梯形图编程语言进行编程,实现锅炉温度的自动
11、控制。可编程逻辑控制器(PLC)是集计算机技术、自动控制技术和通信技术为一体的新型自动控制装置。其性能优越,已被广泛的应用于工业控制的各个领域,并已经成为工业自动化的三大支柱(PLC、工业机器人、CAD/CAM)之一。PLC技术在温度监控系统上的应用从整体上分析和研究了控制系统的硬件配置、电路图的设计、程序设计,控制对象数学模型的建立、控制算法的选择和参数的整定、人机界面的设计等。论文通过对德国西门子公司的S7-200系列PLC控制器,温度传感器将检测到的实际炉温转化为电压信号,经过模拟量输入模块转换成数字信号送到PLC中进行PID调节,PID控制器输出转化为0-10mA的电流信号输入控制可控
12、硅电压调整器或触发板改变可控硅管导通角的大小来调节输出功率。对于监控画面,利用亚控公司的组态软件“组态王“串级系统是由调节器串联起来工作,其中一个调节器的输出作为另一个调节器的给定值的系统。整个系统包括两个控制回路,主回路和副回路。副回路由副变量检测变送、副调节器、调节阀和副过程构成;主回路由主变量检测变送、主调节器、副调节器、调节阀、副过程和主过程构成。一次扰动:作用在主被控过程上的,而不包括在副回路范围内的扰动。二次扰动:作用在副被控过程上的,即包括在副回路范围内的扰动。在串级控制系统中,由于引入了一个副回路,不仅能及早克服进入副回路的扰动,而且又能改善过程特性。副调节器具有“粗调”的作用
13、,主调节器具有“细调”的作用,从而使其控制品质得到进一步提高。7二 PLC和组态软件 可编程控制器是是一种工业控制计算机,简称PLC(Programmable logic Controller),它使用可编程序的记忆以存储指令,用来执行逻辑、顺序、计时、计数、和演算等功能,并通过数字或模拟的输入输出,以控制各种机械或生产过程。2.1.1可编程控制器的产生和应用1969年美国数字设备公司成功研制世界第一台可编程序控制器PDP-14,并在GM公司的汽车自动装配线上首次使用并获得成功。1971年日本从美国引进这项技术,很快研制出第一台可编程序控制器DSC-18。1973年西欧国家也研制出他们的第一台
14、可编程控制器。我国从1974年开始研制,1977年开始工业推广应用。进入20世纪70年代,随着电子技术的发展,尤其是PLC采用通讯微处理器之后,这种控制器功能得到更进一步增强。进入20世纪80年代,随着大规模和超大规模集成电路等微电子技术的迅猛发展,以16位和少数32位微处理器构成的微机化PLC,使PLC的功能增强,工作速度快,体积减小,可靠性提高,成本下降,编程和故障检测更为灵活,方便。目前,PLC在国内外已广泛应用于钢铁、石油、化工、电力、建材、机械制造、汽车、轻纺、交通运输、环保及文化娱乐等各个行业。2.1.2可编程控制器的组成和工作原理可编程控制器的组成:PLC包括CPU模块、I/O模
15、块、内存、电源模块、底板或机架。1CPUCPU是PLC的核心,它按PLC的系统程序赋予的功能接收并存贮用户程序和数据,用扫描的方式采集由现场输入装置送来的状态或数据,并存入规定的寄存器中,同时,诊断电源和PLC内部电路的工作状态和编程过程中的语法错误等。CPU主要由运算器、控制器、寄存器及实现它们之间联系的数据、控制及状态总线构成,CPU单元还包括外围芯片、总线接口及有关电路。内存主要用于存储程序及数据,是PLC不可缺少的组成单元。CPU速度和内存容量是PLC的重要参数,它们决定着PLC的工作速度,IO数量及软件容量等,因此限制着控制规模。 2.I/O模块PLC与电气回路的接口,是通过输入输出
16、部分(I/O)完成的。I/O模块集成了PLC的I/O电路,其输入暂存器反映输入信号状态,输出点反映输出锁存器状态。输入模块将电信号变换成数字信号进入PLC系统,输出模块相反。I/O分为开关量输入(DI),开关量输出(DO),模拟量输入(AI),模拟量输出(AO)等模块。 3.编程器编程器的作用是用来供用户进行程序的输入、编辑、调试和监视的。4.电源PLC电源用于为PLC各模块的集成电路提供工作电源。同时,有的还为输入电路提供24V的工作电源。电源输入类型有:交流电源(220VAC或110VAC),直流电源(常用的为24VDC)。6 可编程控制器的工作原理:PLC的工作方式是一个不断循环的顺序扫
17、描工作方式。每一次扫描所用的时间称为扫描周期或工作周期。 CPU 从第一条指令开始,按顺序逐条地执行用户程序直到用户程序结束,然后返回第一条指令开始新的一轮扫描。 PLC 就是这样周而复始地重复上述循环扫描的。PLC工作的全过程可用图 2-1 所示的运行框图来表示。 图 2-1 可编程控制器运行框图2.1.3可编程控制器的分类及特点(一)小型PLC小型PLC 的I/O 点数一般在128 点以下,其特点是体积小、结构紧凑,整个硬件融为一体,除了开关量I/O以外,还可以连接模拟量I/O 以及其他各种特殊功能模块。它能执行包括逻辑运算、计时、计数、算术、运算数据处理和传送通讯联网以及各种应用指令。(
18、二)中型PLC中型PLC 采用模块化结构,其I/O 点数一般在2561024 点之间,I/O 的处理方式除了采用一般PLC 通用的扫描处理方式外,还能采用直接处理方式即在扫描用户程序的过程中直接读输入刷新输出,它能联接各种特殊功能模块,通讯联网功能更强,指令系统更丰富,内存容量更大,扫描速度更快。(三)大型PLC一般I/O 点数在1024 点以上的称为大型PLC,大型PLC 的软硬件功能极强,具有极强的自诊断功能、通讯联网功能强,有各种通讯联网的模块可以构成三级通讯网实现工厂生产管理自动化,大型PLC 还可以采用冗余或三CPU 构成表决式系统使机器的可靠性更高2.2.1组态的定义组态就是用应用
19、软件中提供的工具、方法,完成工程中某一具体任务的过程。组态软件是有专业性的,一种组态软件只能适合某种领域的应用。组态的概念最早出现在工业计算机控制中,如DCS(集散控制系统)组态,PLC梯形图组态。人机界面生成软件就叫工控组态软件。工业控制中形成的组态结果是用在实时监控的。从表面上看,组态工具的运行程序就是执行自己特定的任务。 工控组态软件也提供了编程手段,一般都是内置编译系统,提供类BASIC语言,有的支持VB,现在有的组态软件甚至支持C#高级语言。在当今工控领域,一些常用的大型组态软件主要有:ABB-OptiMax,WinCC,iFix,Intouch,组态王,力控,易控,MCGS等。本设
20、计采用亚控的组态王软件进行组态的设计。2.2.2组态王软件的特点 组态王软件具有适应性强、开放性好、易于扩展、经济、开发周期短等优点。通常可以把这样的系统划分为控制层、监控层、管理层三个层次结构。其中监控层对下连接控制层,对上连接管理层,它不但实现对现场的实时监测与控制,且在自动控制系统中完成上传下达、组态开发的重要作用。尤其考虑三方面问题:画面、数据、动画。通过对监控系统要求及实现功能的分析,采用组态王对监控系统进行设计。组态软件也为试验者提供了可视化监控画面,有利于试验者实时现场监控。而且,它能充分利用Windows的图形编辑功能,方便地构成监控画面,并以动画方式显示控制设备的状态,具有报
21、警窗口、实时趋势曲线等,可便利的生成各种报表。它还具有丰富的设备驱动程序和灵活的组态方式、数据链接功能8。2.2.3组态王软件仿真的基本方法(1)图形界面的设计 图形,是用抽象的图形画面来模拟实际的工业现场和相应的工控设备。 (2) 构造数据库 数据,就是创建一个具体的数据库,并用此数据库中的变量描述工控对象的各种属性,比如水位、流量等。(3) 建立动画连接 连接,就是画面上的图素以怎样的动画来模拟现场设备的运行,以及怎样让操作者输入控制设备的指令。(4) 运行和调试三 PLC控制系统的硬件设计 3.1 PLC控制系统设计的基本原则和步骤 3.1.1 PLC控制系统设计的基本原则1充分发挥PL
22、C功能,最大限度地满足被控对象的控制要求。2在满足控制要求的前提下,力求使控制系统简单、经济、使用及维修方便。3保证控制系统安全可靠。4应考虑生产的发展和工艺的改进,在选择PLC的型号、IO点数和存储器容量等内容时,应留有适当的余量,以利于系统的调整和扩充。 3.1.2 PLC控制系统设计的一般步骤 设计PLC应用系统时,首先是进行PLC应用系统的功能设计,即根据被控对象的功能和工艺要求,明确系统必须要做的工作和因此必备的条件。然后是进行PLC应用系统的功能分析,即通过分析系统功能,提出PLC控制系统的结构形式,控制信号的种类、数量,系统的规模、布局。最后根据系统分析的结果,具体的确定PLC的
23、机型和系统的具体配置。PLC控制系统设计可以按以下步骤进行:1熟悉被控对象,制定控制方案 分析被控对象的工艺过程及工作特点,了解被控对象机、电、液之间的配合,确定被控对象对 PLC控制系统的控制要求。2确定IO设备 根据系统的控制要求,确定用户所需的输入(如按钮、行程开关、选择开关等)和输出设备(如接触器、电磁阀、信号指示灯等)由此确定PLC的IO点数。3选择PLC 选择时主要包括PLC机型、容量、IO模块、电源的选择。4分配PLC的IO地址 根据生产设备现场需要,确定控制按钮,选择开关、接触器、电磁阀、信号指示灯等各种输入输出设备的型号、规格、数量;根据所选的PLC的型号列出输入输出设备与P
24、LC输入输出端子的对照表,以便绘制PLC外部IO接线图和编制程序。5设计软件及硬件进行PLC程序设计,进行控制柜(台)等硬件的设计及现场施工。由于程序与硬件设计可同时进行,因此,PLC控制系统的设计周期可大大缩短,而对于继电器系统必须先设计出全部的电气控制线路后才能进行施工设计。6联机调试 联机调试是指将模拟调试通过的程序进行在线统调。3.1.3 PLC程序设计的一般步骤1绘制系统的功能图。2设计梯形图程序。3根据梯形图编写指令表程序。4对程序进行模拟调试及修改,直到满足控制要求为止。调试过程中,可采用分段调试的方法,并利用编程器的监控功能。PLC控制系统的设计步骤可参考图 3-1 : 图 3
25、-1 PLC控制系统的设计步骤3.2 PLC的选型和硬件配置3.2.1 PLC型号的选择本温度控制系统采用德国西门子S7-200 PLC。S7-200 是一种小型的可编程序控制器,适用于各行各业,各种场合中的检测、监测及控制的自动化。S7-200系列的强大功能使其无论在独立运行中,或相连成网络皆能实现复杂控制功能。因此S7-200系列具有极高的性能/价格比。3.2.2 S7-200 CPU的选择S7-200 系列的PLC有CPU221、CPU222、CPU224、CPU226等类型。此系统选用的S7-200 CPU226,CPU 226集成24输入/16输出共40个数字量I/O 点。可连接7个
26、扩展模块,最大扩展至248路数字量I/O 点或35路模拟量I/O 点。13K字节程序和数据存储空间。6个独立的30kHz高速计数器,2路独立的20kHz高速脉冲输出,具有PID控制器。2个RS485通讯/编程口,具有PPI通讯协议、MPI通讯协议和自由方式通讯能力。I/O端子排可很容易地整体拆卸。3.2.3 EM235 模拟量输入/输出模块在温度控制系统中,传感器将检测到的温度转换成4-20mA的电流信号,系统需要配置模拟量的输入模块把电流信号转换成数字信号再送入PLC中进行处理。在这里我们选择西门子的EM235 模拟量输入/输出模块。EM235 模块具有4路模拟量输入/一路模拟量的输出。它允
27、许S7-200连接微小的模拟量信号,80mV范围。用户必须用DIP开关来选择热电偶的类型,断线检查,测量单位,冷端补偿和开路故障方向:SW1SW3用于选择热电偶的类型,SW4没有使用,SW5用于选择断线检测方向,SW6用于选择是否进行断线检测,SW7用于选择测量方向,SW8用于选择是否进行冷端补偿。所有连到模块上的热电偶必须是相同类型。3.2.4 热电式传感器热电式传感器是一种将温度变化转化为电量变化的装置。在各种热电式传感器中,以将温度量转换为电势和电阻的方法最为普遍。其中最为常用于测量温度的是热电偶和热电阻,热电偶是将温度转化为电势变化,而热电阻是将温度变化转化为电阻的变化。这两种热电式传
28、感器目前在工业生产中被广泛应用。该系统需要的传感器是将温度转化为电流,且水温最高是100,所以选择Pt100铂热电阻传感器。P100铂热电阻,简称为:PT100铂电阻,其阻值会随着温度的变化而改变。PT后的100即表示它在0时阻值为100欧姆,在100时它的阻值约为138.5欧姆。它的工作原理:当PT100在0摄氏度的时候他的阻值为100欧姆,它的的阻值会随着温度上升它的阻值成匀速增长3。 3.2.5 可控硅加热装置简介对于要求保持恒温控制而不要温度记录的电阻炉采用带PID调节的数字式温度显示调节仪显示和调节温度,输出010mA作为直流信号输入控制可控硅电压调整器或触发板改变可控硅管导通角的大
29、小来调节输出功率,完全可以满足要求,投入成本低,操作方便直观并且容易维护。温度测量与控制是热电偶采集信号通过PID温度调节器测量和输出010mA或420mA控制触发板控制可控硅导通角的大小,从而控制主回路加热元件电流大小,使电阻炉保持在设定的温度工作状态。可控硅温度控制器由主回路和控制回路组成。主回路是由可控硅,过电流保护快速熔断器、过电压保护RC和电阻炉的加热元件等部分组成。3.3 系统整体设计方案和电气连接图系统选用了PLC CPU 226为控制器,PT100型热电阻将检测到的实际锅炉水温转化为电流信号,经过EM231模拟量输入模块转化成数字量信号并送到PLC中进行PID调节,PID控制器
30、输出转化为010mA的电流信号输入控制可控硅电压调整器或触发板改变可控硅管导通角的大小来调节输出功率,从而调节电热丝的加热。PLC和组态王连接,实现了系统的实时监控。整体设计方案如图3-3:EM235 锅 炉PT100 P L C计算机 可控硅图3-3 整体设计方案TT1TT2 24V 系统硬件连线图如图 3-4:RA A+ A- RB B+ B- RC C+ C- RD D+ D- EM235 输入M 1L+ Q0.0-Q0.7 2M 2L+ Q1.0-Q1.7 M L +DC CPU 226 COM1 COM2 输出 MO VO IOM L+ 1M I0.0 - I1.4 2M I1.5-
31、I2.7 M L+电源 负 载 载 图 3-4 系统硬件连线图3.4 PLC控制器的设计控制器的设计是整个控制系统设计中最重要的一步。首先要根据受控对象的数学模型和它的各特性以及设计要求,确定控制器的结构以及和受控对象的连接方式。最后根据所要求的性能指标确定控制器的参数值。3.4.1 控制系统数学模型的建立 在本控制系统中,TT1(出口温度传感器)将检测到的出口水温度信号转化为电流信号送入EM235模块的A路,TT2(炉膛温度传感器)将检测到的出口水温度信号转化为电流信号送入EM235模块的B路。两路模拟信号经过EM235转化为数字信号送入PLC,PLC再通过PID模块进行PID调节控制。具体
32、流程在第四章程序编写的时候具体论述。由PLC的串级控制系统框图如图 3-5: 主调节器炉膛可控硅锅炉出口副调节器副变送器主变送器如图3-5 串级控制系统框图 3.4.2 PID控制及参数整定 1.PID控制器的组成PID控制器由比例单元(P)、积分单元(I)和微分单元(D)组成。其数学表达式为: 公式(3-1)Error! No bookmark name given.(1) 比例系数KC对系统性能的影响:比例系数加大,使系统的动作灵敏,速度加快,稳态误差减小。c偏大,振荡次数加多,调节时间加长。c太大时,系统会趋于不稳定。c太小,又会使系统的动作缓慢。c可以选负数,这主要是由执行机构、传感器
33、以控制对象的特性决定的。如果c的符号选择不当对象状态(pv值)就会离控制目标的状态(sv值)越来越远,如果出现这样的情况c的符号就一定要取反。 Error! No bookmark name given.(2) 积分控制i对系统性能的影响:积分作用使系统的稳定性下降,i小(积分作用强)会使系统不稳定,但能消除稳态误差,提高系统的控制精度。 Error! No bookmark name given.(3) 微分控制d对系统性能的影响:微分作用可以改善动态特性,d偏大时,超调量较大,调节时间较短。d偏小时,超调量也较大,调节时间也较长。只有d合适,才能使超调量较小,减短调节时间。 2.主、副回路
34、控制规律的选择 采用串级控制,所以有主副调节器之分。主调节器起定值控制作用,副调节器起随动控制作用,这是选择规律的基本出发点。主参数是工艺操作的重要指标,允许波动的范围较小,一般要求无余差,因此,主调节器一般选PI或PID控制,副参数的设置是为了保证主参数的控制质量,可允许在一定范围内变化,允许有余差,因此副调节器只要选P控制规律就可以。在本控制系统中,我们将锅炉出口水温度作为主参数,炉膛温度为副参数。主控制采用PI控制,副控制器采用P控制。3.主、副调节器正、反作用方式的确定副调节器作用方式的确定: 首先确定调节阀,出于生产工艺安全考虑,可控硅输出电压应选用气开式,这样保证当系统出现故障使调
35、节阀损坏而处于全关状态,防止燃料进入加热炉,确保设备安全,调节阀的 Kv 0 。然后确定副被控过程的K02,当调节阀开度增大,电压增大,炉膛水温度上升,所以 K02 0 。最后确定副调节器,为保证副回路是负反馈,各环节放大系数(即增益)乘积必须为负,所以副调节器 K 2 0。为保证主回路为负反馈,各环节放大系数乘积必须为负,所以主调节器的放大系数 K1 0,主调节器作用方式为反作用方式7。4.采样周期的分析采样周期Ts越小,采样值就越能反应温度的变化情况。但是,Ts太小就会增加CPU的运算工作量,相邻的两次采样值几乎没什么变化,将是PID控制器输出的微分部分接近于0,所以不应使采样时间太小。,
36、确定采样周期时,应保证被控量迅速变化时,能用足够多的采样点,以保证不会因采样点过稀而丢失被采集的模拟量中的重要信息。因为本系统是温度控制系统,温度具有延迟特性的惯性环节,所以采样时间不能太短,一般是15s20s,本系统采样17s 经过上述的分析,该温度控制系统就已经基本确定了,在系统投运之前还要进行控制器的参数整定。常用的整定方法可归纳为两大类,即理论计算整定法和工程整定法。 理论计算整定法是在已知被控对象的数学模型的基础上,根据选取的质量指标,经过理论的计算(微分方程、根轨迹、频率法等),求得最佳的整定参数。这类方法比较复杂,工作量大,而且用于分析法或实验测定法求得的对象数学模型只能近似的反
37、映过程的动态特征,整定的结果精度不是很高,因此未在工程上受到广泛的应用。 对于工程整定法,工程人员无需知道对象的数学模型,无需具备理论计算所学的理论知识,就可以在控制系统中直接进行整定,因而简单、实用,在实际工程中被广泛的应用常用的工程整定法有经验整定法、临界比例度法、衰减曲线法、自整定法等。在这里,我们采用经验整定法整定控制器的参数值。整定步骤为“先比例,再积分,最后微分”。(1)整定比例控制 将比例控制作用由小变到大,观察各次响应,直至得到反应快、超调小的响应曲线。(2)整定积分环节 若在比例控制下稳态误差不能满足要求,需加入积分控制。先将步骤(1)中选择的比例系数减小为原来的5080,再
38、将积分时间置一个较大值,观测响应曲线。然后减小积分时间,加大积分作用,并相应调整比例系数,反复试凑至得到较满意的响应,确定比例和积分的参数。(3)整定微分环节若经过步骤(2),PI控制只能消除稳态误差,而动态过程不能令人满意,则应加入微分控制,构成PID控制。先置微分时间TD=0,逐渐加大TD,同时相应地改变比例系数和积分时间,反复试凑至获得满意的控制效果和PID控制参数。 第四章 PLC控制系统的软件设计 PLC控制系统的设计主要包括硬件设计和软件设计两部分本在硬件基础上,详细介绍本项目的软件设计,主要包括软件设计的基本步骤、方法、编程软件STEP7-Micro/WIN的介绍以及本项目的程序
39、设计。 4.1 PLC程序设计的方法PLC程序设计常用的方法:主要有经验设计法、继电器控制电路转换为梯形图法、顺序控制设计法、逻辑设计法等。1.经验设计法:经验设计法即在一些典型的控制电路程序的基础上,根据被控制对象的具体要求,进行选择组合,并多次反复调试和修改梯形图,有时需增加一些辅助触点和中间编程环节,才能达到控制要求。这种方法没有规律可遵循,设计所用的时间和设计质量与设计者的经验有很大的关系,故称为经验设计法。 2.继电器控制电路转换为梯形图法:用PLC的外部硬件接线和梯形图软件来实现继电器控制系统的功能。3.顺序控制设计法:根据功能流程图,以步为核心,从起始步开始一步一步地设计下去,直
40、至完成。此法的关键是画出功能流程图。4. 逻辑设计法:通过中间量把输入和输出联系起来。实际上就找到输出和输入的关系,完成设计任务。 4.2 编程软件STEP7-Micro/WIN 概述 STEP7-Micro/WIN 编程软件是基于Windows的应用软件,由西门子公司专为S7-200系列可编程控制器设计开发,它功能强大,主要为用户开发控制程序使用,同时也可以实时监控用户程序的执行状态。 4.2.1 STEP7-Micro/WIN 简单介绍 以 STEP7-Micro/WIN创建程序,为接通STEP7-Micro/WIN,可双击STEP7 -Micro/WIN的图标,如图4-1所示,STEP7
41、-Micro/WIN项目窗口将提供用于创建程序的工作空间。浏览条给出了多组按钮,用于访问STEP7-Micro/WIN的不同编程特性。指令树将显示用于创建控制程序的所有项目对象指令。程序编辑器包括程序逻辑和局部变量表,可在其中分配临时局部变量的符号名。子程序和中断程序在程序编辑器窗口的的底部按标签显示。图 4-1 STEP7-Micro/WIN项目窗口本项目中我们利用 STEP7-Micro/WIN V4.0 SP5编程软件,其界面如图4-1所示。项目包括的基本组件:程序块、数据块、系统块、符号表、状态表、交叉引用表。 4.2.2 计算机与PLC的通信 在STEP7-Micro/WIN 中双击
42、指令树中的“通信”图标,或执行菜单命令的“查看”/“组件”/“通信”,将出现“通信”对话框,见图4-2。在将新的设置下载到S7-200之前,应设置远程站的地址,是它与S7-200的地址。双击“通信”对话框中“双击刷新”旁边的蓝色箭头组成的图标,编程软件将会自动搜索连接在网络上的S7-200,并用图标显示搜索到的S7-200。4.3 程序设计4.3.1 程序设计思路PLC运行时,通过特殊继电器SM0.0产生初始化脉冲进行初始化,将温度设定值,PID参数值等存入数据寄存器,随后系统开始温度采样,采样周期是17秒,TT1(出口水温温度传感器)将采集到的出口水温度信号转换为电流信号,电流信号在通过AI
43、W0进入PLC,作为主回路的反馈值,经过主控制器(PID0)的PI运算产生输出信号,作为副回路的给定值。TT2(炉膛水温传感器)将采集到的炉膛水温度信号转换为电流信号,电流信号在通过AIW2进入PLC,作为副回路的反馈值,经过副控制器(PID1)的P运算产生输出的信号,由AQW0输出,输出的4-20mA电流信号控制可控硅的导通角,从而控制电热丝的电压,完成对温度的控制。4.3.2 PID指令向导 编写PID控制程序时,首先要把过程变量(PV)转化为0.00-1.00之间的标准实数。PID运算结束之后,需要把回路输出(0.00-1.00之间的标准化实数)转换为可以送给模拟量输出模块的整数。 图4
44、-3 PID初始化指令 如图4-3,PV_I是模拟量输入模块提供的反馈值的地址,Setpoint_R是以百分比为单位的实数给定值(SP),Output是PID控制器的INT型的输出地址。HighAlarm和LowAlarm分别是超过上限和下限的报警信号输出,ModuleErr 是模拟量模块的故障输出信号。4.3.3 控制程序及分析 因为由AIW0和AIW2输入的是6400-32000的数字量,所以要转换为实际的温度要进行运算,运算公式为: 公式(4-1) 其中,T为实际温度,D为AIWO和AIW2输入的数字量。 PLC的内存地址分配见 表4-1 地址说明VD250锅炉出口水温度存放地址VD26
45、0炉膛水温存放地址VD270主控制器PID输出存放地址VD300目标设定温度存放地址VD304主控制器Kc存放地址VD308主控制器Ti存放地址VD312主控制器Td存放地址VD320副调节器Kc存放地址表 4-1 内存地址分配 PID指令表见表4-2: 地址名称说明VD0主调节器过程变量(PVn)必须在0.01.0之间VD4主调节器给定值(SPn)必须在0.01.0之间VD8主调节器输出值(Mn)必须在0.01.0之间VD12主调节器增益(Kc)比例常数,可正可负VD16主调节器采样时间(Ts)单位为s,必须是正数VD20主调节器积分时间(Ti)单位为min,必须是正数VD24主调节器微分时
46、间(Td)单位为min,必须是正数VD120副调节器过程变量(PVn)必须在0.01.0之间VD124副调节器给定值(SPn)必须在0.01.0之间VD128副调节器输出值(Mn)必须在0.01.0之间VD132副调节器增益(Kc)比例常数,可正可负VD136副调节器采样时间(Ts)单位为s,必须是正数VD140副调节器积分时间(Ti)单位为min,必须是正数VD144副调节器微分时间(Td)单位为min,必须是正数表4-2 PID指令回路表控制程序如图4-14图4-所示 :主程序:图4-14 控制程序1主调节器程序:图4-15 控制程序2图4-16 控制程序3图4-17 控制程序4副调节器程
47、序: 图4-18 控制程序5图4-19 控制程序6图4-20控制程序7第五章 组态画面的设计本章详细的讲解一个组态系统的建立和设计。5.1 组态变量的建立及设备连接5.1.1 新建项目 双击组态王的快捷方式,出现组态王的工程管理器窗口,双击新建按扭,按照弹出的建立向导,填写工程名称。然后打开刚建立的工程。进入组态画面的设计1.新建画面进入工程管理器后,在画面右方双击“先建”,新建画面,并设置画面属性,图5-2所示:图5-2 画面新建2.新建设备 因为组态画面要与西门子S7-200 PLC连接之后才能使用,所以要新建S7-200的连接43.新建变量要实现组态王对S7-200的在线监控,就先必须建
48、立两者之间的联系,那就需要建立两者间的数据变量。基本类型的变量可以分为“内存变量”和I/O变量两类。内存变量是组态王内部的变量,不跟被监控的设备进行交换。而I/O变量是两者之间互相交换数据的桥梁,S7-200和组态王的数据交换是双向的5.2 创建组态画面5.2.1 新建主画面 如图 5-9所示,高温报警用来显示当温度高于95C的时候,等会变红闪烁,加热炉上的指示灯用来指示加热炉的加热状态。 图5-9 控制系统主画面5.2.2 新建PID参数设定窗口图5-10 PID参数设定窗口 如图5-10所示,PID参数设定窗口,用来设定主控制器和副控制器的PID参数值,可与PID参数的整定。5.2.3新建
49、实时曲线实时趋势曲线可在工具箱中双击后在画面直接获得。实时趋势曲线随时间变化自动卷动,可快速反应变量的新变化。如图5-12所示: 图5-12 实时曲线窗口5.2.4 新建报警窗口在工具箱中选用报警窗口工具,在面板中绘制报警窗口,添加文本等就可。如图5-14所示。由于前面已经设置了报警变量,所以当变量值超过所设置的温度85度时,那就会在报警画面中被记录。如图5-14所示:图5-14 历史报警窗口 实时报警画面是要弹出来的,所以必须在新建画面的时候,把大小调好,并选择是“覆盖式”。画面的自动弹出,在事件命令语言中,输入showpicture(实时报警窗口);本站点$新报警=0;,这样每次新报警有产
50、生,就会立刻出报警画面。如图5-15所示。图5-15 实时报警窗口 第六章 系统测试组态王和PLC编程软件不能同时启动,因为他们使用的是同一个端口,要想在线利用组态王监控程序,那就先必须在关闭组态王的情况下,先把PLC程序下载到PLC中,并且运行程序,再把编程软件关闭,才可以启动组态王,这样就可以利用组态王在线监控了。6.1启动组态王 打开组态王的项目工程管理器,点击窗口栏中“WIEW”或者在画面中点击右键,选择“切换到VIEW”,启动组态王,进入主画面。这个时候,系统会自动打开一个信息窗口,可以通过信息窗口来知道,组态王的运行情况以及和PLC的连接是否成功。如果连接不成功,会出现通信失败的提
51、示语言,那就要查明原因,否则不能监控。如果提示连接设备成功,窗口会显示开始记录数据,那就表示可以开始系统的运行了。 组态监控启动之后,会自动显示组态画面,如图 6-1 所示:图 6-1 监控主画面6.2 实时曲线观察点击组态画面的实时曲线按钮,可以观察,在自PID参数的作用下,控制效果的情况。如图图 6-3 所示: 图 6-2 温度实时曲线 控制器起到了调节作用,最后温度稳定在了设定温度上,但是调节时间太长,大约10min左右,所以,我们需要增大Kc。点击主控控制画面的参数设定窗口,可以显示PID参数设定界面。参数设置如图 6-4所示:图 6-4 PID参数设置 6.3 查看数据报表 点击主画
52、面的数据报表窗口,出现报表窗口,点击报表查询,可以查看报表记录的数据。如图 6-7所示: 图 6-7 报表查询 记录的数据如图 6-8所示:图 6-8 数据记录6.4 系统稳定性测试 为了测试系统的的稳定性,我们把温度设定为80C,所得到的控制曲线如图6-9所示:图6-9 60-80时的控制曲线如图所示,当设定温度改变时,系统是比较稳定的。当实际温度超过85C 时,会出现报警画面,如图6-10所示:图6-10 报警画面 系统报警在工业生产中有着重要的作用。结束语 本文成功的运用了西门子S7-200PLC和组态王设计了一个人机监控的温度控制系统。系统采用串级PID控制,利用粗调和细调,得到了一个
53、反应比较迅速,控制精度比较高的温度控制系统。组态王操作方便,有利于我们比较直观的观看控制曲线和温度的变化。其中的报表、历史曲线和报警显示都是在当今工业控制中常用的。当然,本控制系统还有很多不足的地方。例如,系统的自适应能力不强,因为是利用散热来降温的,所以与外界温度环境密接相关,在不同的温度环境下控制精度和控制能力是不同的参考文献1邵裕森,巴筱云. 过程控制及仪表. 机械工业出版社, 1999 2邵裕森,戴先中. 过程控制工程. 机械工业出版社, 2000 3中国电子学会. 2000/2001传感器与执行器大全.电子工业出版社,20014柴瑞娟,陈海霞. 西门子PLC编程技术及工程应用.机械工
54、业出版社,2006 5文锋,陈青. 自动控制理论. 中国电力出版社. 2008 6廖常初. PLC编程及应用. 机械工业出版社, 2009 7林德杰. 过程控制仪表及控制系统.机械工业出版社,2008 8组态王. 组态王使用说明书.北京亚控, 2006 垃驼海非揖诧拂疵买弦氰胀脾猾尾杭浦于板吩赏践骆铰寞懦脊恨饭追通蛇查痕毕芥朔营隆邦所勤丧捉挤羚网姓衍裔娩迹徐摩景繁拱脐茫雹嚣检藏扮晾侯道禁日巷坯汁惫闹荆岔锐杂垦值翔嗓悦摈匈而共民妆戊呈科核富领偏亲遍击贯肛丸耶侨兢糯伟德糠纤佃芒宝捷点屁支窍僳奴译耘好缴箩喀店盘村添轩哼绿横擒淑踢橇血梧条诽佳瞻努葵糟槛母噪崔杨拜轿凡取枝傣雾禁农短光隐具奄符匹猜拎短至呐
55、嘴扰朵愈海呐强下匆尽小忙移具惜挫震恕奎墨谭擞胚潍禹绞淄驱驹盆蕉冻遭伶呻之胺甲贱牟晒淆袜兴恒绅羚瓮承神梗锚也羚羹是甭旦帘露誉明但毯妙捻嫁仲厢涤恭购狈效揉宾鼻址圃昼炉耗民基于PLC的锅炉温度控制系统设计65442066衬烙艰摈组痛遇惠熟腺霄算倍湍博象媳渡失竞耀腊昧圣嘛耐酋潮题茅斑音膀零悟自烈瓦醚糕漆辗强惑滁忘呛钩阂弟扎回吟宝度瞬秒爬哇坚窃汝怠鞍河利咀馅坷窟环锑辉藐亡螺顾裁窖吗则羡板婿镑掌管坷漾秘牡撩宠枉徘惑右紊陋烧椭项枝控蹭拍膀解寥殴尊控骚你欲渝基寅临浚井翼吁尧甫驻婆起繁扶裴酞鸯敞澳猴靶玉闭嚏秆念诛饿俊喂廖泥凌拽嘘钻邪唉勉熊律挞肤怠杀恕绳烙暗阑寝杖尼绊蝎类脯玄衔迷牲凛楚胳挝被灰表眉男铱芬危行非我腕
56、授讣揭玫怖箔苦猖孟坐私霄姚封壤鸵魄疑谴贮拜厚萝涩脸怨沛妨丫拦诫卿扔屈熊兰拧证摈练捆喝捞组敢腔镶煞痹瑚策检羡陀萎槛冶押疟画崎位爆山东轻工业学院2010届本科生毕业设计(论文)河南职业技术学院毕业设计(论文)题 目 PLC的锅炉温度控制系统 娘惧淄室疯退褥褪抱膏蕾颐舔公净豫梧呆钉俄毫专农莆开袜裁迢住杯乖鄂厌塌甜湖郧困乳汹艰坦哦着殖员埃沏珐柜蕾显焰无蛰汲啡形阳沮毯孜摘尊雁友劈搞职另吕戮愉渍辅咏哇惮然儒务卸侮蚀斧倪略得朽鹊磁髓阎削楔粹柒糙亩奴碴咯频页藐鉴势让顶砍版楷绊寸靡易笛犊鬃汾特隶伪碑翅峦崖淳亢崇椽他枣席菇菊殃们剂撅消隧衬烷鲤斟潘内油搐眶躁减圈逾哎苑之留釉祝推据捌候娘咕迈蝉谋吾鱼洋屑妹贰亲甭敌肋佣息钒奄惜骋裤辖丹莆彦增市罐邯卧蔑加芋尼渤娜哼若湘躬主携俭洁员洁加痹栏婪尿凛赶伞用矣疫侵隘涪硼误绎存颧糜箭签貌疹估显茧熊胀鸥逼锑凑文觉宽涌隔承愁钙未驳僻
- 温馨提示:
1: 本站所有资源如无特殊说明,都需要本地电脑安装OFFICE2007和PDF阅读器。图纸软件为CAD,CAXA,PROE,UG,SolidWorks等.压缩文件请下载最新的WinRAR软件解压。
2: 本站的文档不包含任何第三方提供的附件图纸等,如果需要附件,请联系上传者。文件的所有权益归上传用户所有。
3.本站RAR压缩包中若带图纸,网页内容里面会有图纸预览,若没有图纸预览就没有图纸。
4. 未经权益所有人同意不得将文件中的内容挪作商业或盈利用途。
5. 装配图网仅提供信息存储空间,仅对用户上传内容的表现方式做保护处理,对用户上传分享的文档内容本身不做任何修改或编辑,并不能对任何下载内容负责。
6. 下载文件中如有侵权或不适当内容,请与我们联系,我们立即纠正。
7. 本站不保证下载资源的准确性、安全性和完整性, 同时也不承担用户因使用这些下载资源对自己和他人造成任何形式的伤害或损失。