250克塑料注塑机毕业设计说明任务书
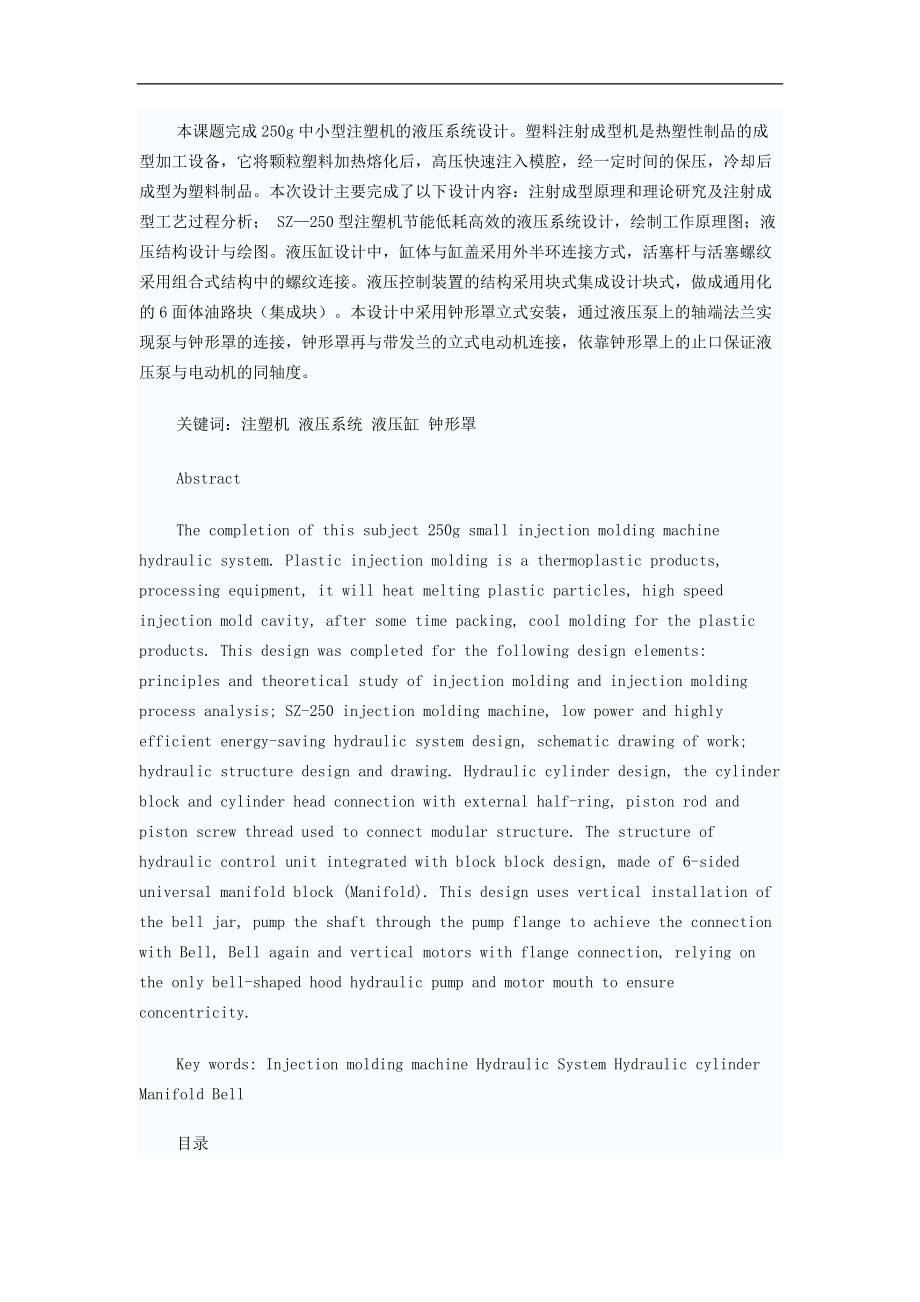


《250克塑料注塑机毕业设计说明任务书》由会员分享,可在线阅读,更多相关《250克塑料注塑机毕业设计说明任务书(39页珍藏版)》请在装配图网上搜索。
1、本课题完成250g中小型注塑机的液压系统设计。塑料注射成型机是热塑性制品的成型加工设备,它将颗粒塑料加热熔化后,高压快速注入模腔,经一定时间的保压,冷却后成型为塑料制品。本次设计主要完成了以下设计内容:注射成型原理和理论研究及注射成型工艺过程分析; SZ250型注塑机节能低耗高效的液压系统设计,绘制工作原理图;液压结构设计与绘图。液压缸设计中,缸体与缸盖采用外半环连接方式,活塞杆与活塞螺纹采用组合式结构中的螺纹连接。液压控制装置的结构采用块式集成设计块式,做成通用化的6面体油路块(集成块)。本设计中采用钟形罩立式安装,通过液压泵上的轴端法兰实现泵与钟形罩的连接,钟形罩再与带发兰的立式电动机连接
2、,依靠钟形罩上的止口保证液压泵与电动机的同轴度。关键词:注塑机 液压系统 液压缸 钟形罩AbstractThe completion of this subject 250g small injection molding machine hydraulic system. Plastic injection molding is a thermoplastic products, processing equipment, it will heat melting plastic particles, high speed injection mold cavity, after some
3、time packing, cool molding for the plastic products. This design was completed for the following design elements: principles and theoretical study of injection molding and injection molding process analysis; SZ-250 injection molding machine, low power and highly efficient energy-saving hydraulic sys
4、tem design, schematic drawing of work; hydraulic structure design and drawing. Hydraulic cylinder design, the cylinder block and cylinder head connection with external half-ring, piston rod and piston screw thread used to connect modular structure. The structure of hydraulic control unit integrated
5、with block block design, made of 6-sided universal manifold block (Manifold). This design uses vertical installation of the bell jar, pump the shaft through the pump flange to achieve the connection with Bell, Bell again and vertical motors with flange connection, relying on the only bell-shaped hoo
6、d hydraulic pump and motor mouth to ensure concentricity.Key words: Injection molding machine Hydraulic System Hydraulic cylinder Manifold Bell目录第一章绪论11.1注塑机概述11.2塑料注射机的工作循环塑料1第二章 SZ-250型注塑机液压系统设计22.1SZ-250型注射机液压系统设计要求及有关设计参数22.2液压执行元件载荷力和载荷转矩计算22.3液压系统主要参数计算42.4制定系统方案和拟定液压系统图62.5液压元件的选择92.6液压系统性能验算
7、112.7液压缸的设计16第三章液压集成块的设计223.1块式集成的结构223.2块式集成的特点223.3块式集成液压控制装置的设计22第四章SZ-250型注塑机动力装置的设计284.1 SZ-250型注塑机液压站的设计284.2液压油箱的设计294.3液压泵组的结构设计32总结与展望34致 谢35参考文献36第一章绪论1.1注塑机概述大型塑料注射机目前都是全液压控制。其基本工作原理是:粒状塑料通过料斗进入螺旋推进器中,螺杆转动,将料向前推进,同时,因螺杆外装有电加热器,而将料熔化成粘液状态,在此之前,合模机构已将模具闭合,当物料在螺旋推进器前端形成一定压力时,注射机构开始将液状料高压快速注射
8、到模具型腔之中,经一定时间的保压冷却后,开模将成型的塑科制品顶出,便完成了一个动作循环。1.2塑料注射机的工作循环塑料注射机的工作循环为:合模注射保螺杆预塑进料其中合模的动作又分为:快速合模、慢速合模、锁模。锁模的时间较长,直到开模前这段时间都是锁模阶段。第二章 SZ-250型注塑机液压系统设计2.1SZ-250型注射机液压系统设计要求及有关设计参数2.1.1对液压系统的要求(1)合模运动要平稳,两片模具闭合时不应有冲击;(2)当模具闭合后,合模机构应保持闭合压力,防止注射时将模具冲开。注射后,注射机构应保持注射压力,使塑料充满型腔;(3)预塑进料时,螺杆转动,料被推到螺杆前端,这时,螺杆同注
9、射机构一起向后退,为使螺杆前端的塑料有一定的密度,注射机构必需有一定的后退阻力;(4)为保证安全生产,系统应设有安全联锁装置。2.1.2液压系统设计参数250克塑料注射机液压系统设计参数如下:螺杆直径 40mm 螺杆行程 200mm最大注射压力 153MPa 螺杆驱动功率 5kW螺杆转速 60r/min 注射座行程 230mm注射座最大推力 27kN 最大合模力(锁模力) 900kN开模力 49kN 动模板最大行程 350mm快速闭模速度 0.1m/s 慢速闭模速度 0.02m/s快速开模速度 0.13m/s 慢速开模速度 0.03m/s注射速度 0.07m/s 注射座前进速度 0.06m/s
10、注射座后移速度 0.08m/s2.2液压执行元件载荷力和载荷转矩计算2.2.1各液压缸的载荷力计算(1)合模缸的载荷力合模缸在模具闭合过程中是轻载,其外载荷主要是动模及其连动部件的起动惯性力和导轨的摩擦力。锁模时,动模停止运动,其外载荷就是给定的锁模力。开模时,液压缸除要克服给定的开模力外,还克服运动部件的摩擦阻力。(2)注射座移动缸的载荷力座移缸在推进和退回注射座的过程中,同样要克服摩擦阻力和惯性力,只有当喷嘴接触模具时,才须满足注射座最大推力。(3)注射缸载荷力注射缸的载荷力在整个注射过程中是变化的,计算时,只须求出最大载荷力。式中,d螺杆直径,由给定参数知:d0.04m;p喷嘴处最大注射
11、压力,已知p153MPa。由此求得Fw192kN。各液压缸的外载荷力计算结果列于表l。取液压缸的机械效率为0.9,求得相应的作用于活塞上的载荷力,并列于表2-1中。表2-1各液压缸的载荷力液压缸名称工况液压缸外载荷/kN活塞上的载荷力合模缸合模90100锁模9001000开模4955座移缸移动2.73预紧2730注射缸注射1922132.2.2进料液压马达载荷转矩计算取液压马达的机械效率为0.95,则其载荷转矩2.3液压系统主要参数计算2.3.1初选系统工作压力250克塑料注射机属小型液压机,载荷最大时为锁模工况,此时,高压油用增压缸提供;其他工况时,载荷都不太高,参考设计手册,初步确定系统工
12、作压力为6.5MPa。2.3.2计算液压缸的主要结构尺寸(1)确定合模缸的活塞及活塞杆直径合模缸最大载荷时,为锁模工况,其载荷力为1000kN,工作在活塞杆受压状态。活塞直径此时p1是由增压缸提供的增压后的进油压力,初定增压比为5,则p156.5MPa32.5MPa,锁模工况时,回油流量极小,故p20,求得合模缸的活塞直径为,取Dh0.2m。按表25取d/D0.7,则活塞杆直径dh0.70.2m0.14m,取dh0.15m。为设计简单加工方便,将增压缸的缸体与合模缸体做成一体(见图1),增压缸的活塞直径也为0.2m。其活塞杆直径按增压比为5,求得,取dz0.09m。注射座移动缸的活塞和活塞杆直
13、径座移动缸最大载荷为其顶紧之时,此时缸的回油流量虽经节流阀,但流量极小,故背压视为零,则其活塞直径为,取Dy0.1m由给定的设计参数知,注射座往复速比为0.080.061.33,查表26得d/D0.5,则活塞杆直径为: dy0.50.1m0.05m确定注射缸的活塞及活塞杆直径当液态塑料充满模具型腔时,注射缸的载荷达到最大值213kN,此时注射缸活塞移动速度也近似等于零,回油量极小;故背压力可以忽略不计,这样,取Ds0.22m;活塞杆的直径一般与螺杆外径相同,取ds0.04m。2.3.3计算液压马达的排量液压马达是单向旋转的,其回油直接回油箱,视其出口压力为零,机械效率为0.95,这样2.3.4
14、计算液压执行元件实际工作压力按最后确定的液压缸的结构尺寸和液压马达排量,计算出各工况时液压执行元件实际工作压力,见表2-2。表2-2 液压执行元件实际工作压力工况执行元件名称载荷背压力工作压力计算公式合模行程合模缸1000.33.3锁模增压缸10006.4座前进座移缸30.50.76座顶紧303.8注射注射缸2130.35.9预塑进料液压马达8386.02.3.5计算液压执行元件实际所需流量根据最后确定的液压缸的结构尺寸或液压马达的排量及其运动速度或转速,计算出各液压执行元件实际所需流量,见表3。工况执行元件名称运动速度结构参数流量/()计算公式慢速合模合模缸0.020.6快速合模0.13座前
15、进座移缸0.060.48座后退0.080.48注射注射缸0.072.7预塑进料液压马达0.87慢速开模合模缸0.030.42快速开模0.131.82.4制定系统方案和拟定液压系统图2.4.1制定系统方案执行机构的确定 本机动作机构除螺杆是单向旋转外,其他机构均为直线往复运动。各直线运动机构均采用单活塞杆双作用液压缸直接驱动,螺杆则用液压马达驱动。从给定的设计参数可知,锁模时所需的力最大,为900kN。为此设置增压液压缸,得到锁模时的局部高压来保证锁模力。合模缸动作回路 合模缸要求其实现快速、慢速、锁模,开模动作。其运动方向由电液换向阀直接控制。快速运动时,需要有较大流量供给。慢速合模只要有小流
16、量供给即可。锁模时,由增压缸供油。液压马达动作回路 螺杆不要求反转,所以液压马达单向旋转即可,由于其转速要求较高,而对速度平稳性无过高要求,故采用旁路节流调速方式。注射缸动作回路 注射缸运动速度也较快,平稳性要求不高,故也采用旁路节流调速方式。由于预塑时有背压要求,在无杆腔出口处串联背压阀。注射座移动缸动作回路 注射座移动缸,采用回油节流调速回路。工艺要求其不工作时,处于浮动状态,故采用Y型中位机能的电磁换向阀。安全联锁措施本系统为保证安全生产,设置了安全门,在安全门下端装一个行程阀,用来控制合模缸的动作。将行程阀串在控制合模缸换向的液动阀控制油路上,安全门没有关闭时,行程阀没被压下,液动换向
17、阀不能进控制油,电液换向阀不能换向,合模缸也不能合模。只有操作者离开,将安全门关闭,压下行程阀,合模缸才能合模,从而保障了人身安全。液压源的选择该液压系统在整个工作循环中需油量变化较大,另外,闭模和注射后又要求有较长时间的保压,所以选用双泵供油系统。液压缸快速动作时,双泵同时供油,慢速动作或保压时由小泵单独供油,这样可减少功率损失,提高系统效率。2.4.2拟定液压系统图图2 注塑机液压系统原理图液压执行元件以及各基本回路确定之后,把它们有机地组合在一起。去掉重复多余的元件,把控制液压马达的换向阀与泵的卸荷阀合并,使之一阀两用。考虑注射缸同合模缸之间有顺序动作的要求,两回路接合部串联单向顺序阀。
18、再加上其他一些辅助元件便构成了250克塑料注射机完整的液压系统图,见图2,其动作循环表,见表2-4。 表2-4 电磁铁动作表电磁铁动作1YA2 YA3 YA4 YA5 YA6 YA7 YA8 YA9 YA10 YA快速合模慢速合模增压锁模注射座前进注射注射保压减压(放气)再增压预塑进料注射座后退慢速开模快速开模系统卸荷2.5液压元件的选择2.5.1液压泵的选择液压泵工作压力的确定pPplppl是液压执行元件的最高工作压力,对于本系统,最高压力是增压缸锁模时的入口压力,pl6.4MPa;p是泵到执行元件间总的管路损失。由系统图可见,从泵到增压缸之间串接有一个单向阀和一个换向阀,取p0.5MPa。
19、液压泵工作压力为 pP(6.40.5)MPa6.9MPa液压泵流量的确定 qPK(qmax)由工况图看出,系统最大流量发生在快速合模工况,qmax3L/s。取泄漏系数K为1.2,求得液压泵流量 qP3.6L/s (216L/min)选用YYB-BCl71/48B型双联叶片泵,当压力为7 MPa时,大泵流量为157.3L/min,小泵流量为44.1L/min。2.5.2电动机功率的确定注射机在整个动作循环中,系统的压力和流量都是变化的,所需功率变化较大,为满足整个工作循环的需要,按较大功率段来确定电动机功率。从工况图看出,快速注射工况系统的压力和流量均较大。此时,大小泵同时参加工作,小泵排油除保
20、证锁模压力外,还通过顺序阀将压力油供给注射缸,大小泵出油汇合推动注射缸前进。前面的计算已知,小泵供油压力为pP16.9MPa,考虑大泵到注射缸之间的管路损失,大泵供油压力应为pP2(5.90.5)MPa6.4MPa,取泵的总效率P0.8,泵的总驱动功率为27.313 kW考虑到注射时间较短,不过3s,而电动机一般允许短时间超载25%,这样电动机功率还可降低一些。P27.313100/12521.85 kW验算其他工况时,液压泵的驱动功率均小于或近于此值。查产品样本,选用22kW的电动机。2.5.3液压阀的选择选择液压阀主要根据阀的工作压力和通过阀的流量。本系统工作压力在7MPa左右,所以液压阀
21、都选用中、高压阀。所选阀的规格型号见表2-5。表2-5 250克塑料注射机液压阀名细表序号名称实际流量选用规格1三位四通电液换向阀2.6234DYM-B32H-T2三位四通电液换向阀3.3634DYY-B32H-T 3三位四通电液换向阀0.5034DY-B10H-T4三位四通电液换向阀3.3634DYO-B32H-T5二位四通电液换向阀0.7424DYO-B32H-T6二位四通电液换向阀0.5024DO-H10H-T7溢流阀0.74YF-B20C8溢流阀2.62YF-B20C9溢流阀2.62YF-B20C10单向阀0.74DF-B20K11液控单向阀3.36AY-H32B12单向阀0.50DF
22、-B10K13单向阀2.62DF-B32K14节流阀0.65LF-B10C15调速阀0.70QF-B10C16调速阀1.70QF-B20C17单向顺序阀0.74XDIF-B20F18单向顺序阀2.70XDIF-B32F19行程滑阀0.5024C-10B2.5.4液压马达的选择在3.3节已求得液压马达的排量为0.8Lr,正常工作时,输出转矩769N.m,系统工作压力为7MPa。 选SZM0.9双斜盘轴向柱塞式液压马达。其理论排量为0.873L/r,额定压力为20 MPa,额定转速为8l00r/min,最高转矩为3057Nm,机械效率大于0.90。2.5.5油管内径计算本系统管路较为复杂,取其主要
23、几条(其余略),有关参数及计算结果列于表2-6。表2-6主要管路内径管路名称通过流量允许流速管路内径实际取值大泵吸油管2.620.850.0630.065小泵吸油管0.73510.0310.032大泵排油管2.624.50.0270.032小泵排油管0.7354.50.0140.015双泵并联后管路3.364.50.0310.032注射缸进油管路2.664.50.0280.0322.5.6确定油箱的有效容积按下式来初步确定油箱的有效容积:VaqV已知所选泵的总流量为201.4L/min,这样,液压泵每分钟排出压力油的体积为0.2m3。参照表43取a5,算得有效容积为:V50.2m31 m32.
24、6液压系统性能验算2.6.1验算回路中的压力损失本系统较为复杂,有多个液压执行元件动作回路,其中环节较多,管路损失较大的要算注射缸动作回路,故主要验算由泵到注射缸这段管路的损失。沿程压力损失沿程压力损失,主要是注射缸快速注射时进油管路的压力损失。此管路长 5m,管内径0.032m,快速时通过流量2.7L/s;选用20号机械系统损耗油,正常运转后油的运动粘度27mm2/s,油的密度918kg/m3。油在管路中的实际流速为油在管路中呈紊流流动状态,其沿程阻力系数为:求得沿程压力损失为:局部压力损失 局部压力损失包括通过管路中折管和管接头等处的管路局部压力损失p2,以及通过控制阀的局部压力损失p3。
25、其中管路局部压力损失相对来说小得多,故主要计算通过控制阀的局部压力损失。参看图2,从小泵出口到注射缸进油口,要经过顺序阀17,电液换向阀2及单向顺序阀18。单向顺序伺17的额定流量为50L/min,额定压力损失为0.4MPa。电液换向阀2的额定流量为190L/min,额定压力损失0.3 MPa。单向顺序阀18的额定流量为150L/min,额定压力损失0.2 MPa。通过各阀的局部压力损失之和为从大泵出油口到注射缸进油口要经过单向阀13,电液换向阀2和单向顺序阀18。单向阀13的额定流量为250L/min,额定压力损失为0.2 MPa。通过各阀的局部压力损失之和为:由以上计算结果可求得快速注射时
26、,小泵到注射缸之间总的压力损失为p1(0.030.88)MPa0.91MPa大泵到注射缸之间总的压力损失为p 2(0.030.65)MPa0.68MPa由计算结果看,大小泵的实际出口压力距泵的额定压力还有一定的压力裕度,所选泵是适合的。另外要说明的一点是:在整个注射过程中,注射压力是不断变化的,注射缸的进口压力也随之由小到大变化,当注射压力达到最大时,注射缸活塞的运动速度也将近似等于零,此时管路的压力损失随流量的减小而减少。泵的实际出口压力要比以上计算值小一些。综合考虑各工况的需要,确定系统的最高工作压力为6.8MPa,也就是溢流阀7的调定压力。2.6.2液压系统发热温升计算计算发热功率 液压
27、系统的功率损失全部转化为热量。发热功率计算如下PhrPrPc对本系统来说,Pr是整个工作循环中双泵的平均输入功率。具体的pi、qi、ti值见表7。这样,可算得双泵平均输入功率Pr12kW。工况泵工作状态出口压力总输入功率工作时间说明小泵大泵小泵大泵慢速合模3.680.361小泵额定流量大泵额定流量泵的总效率:正常工作时卸荷时快速合模44.1617.32增压锁模6.80.38.90.5注射6.86.5827.83保压6.80.38.916进料6.86.326.915冷却6.80.38.915快速开模4.24.418.1.5慢速开模3.90.36.21注:表中表示正常工作,表示卸荷。系统总输出功率
28、求系统的输出有效功率:由前面给定参数及计算结果可知:合模缸的外载荷为90kN,行程0.35m;注射缸的外载荷为192kN,行程0.2m;预塑螺杆有效功率5kW,工作时间15s;开模时外载荷近同合模,行程也相同。注射机输出有效功率主要是以上这些。总的发热功率为:Phr(15.33)kW12.3kW计算散热功率 前面初步求得油箱的有效容积为1m3,按V0.8abh求得油箱各边之积:abh1/0.8m31.25m3取a为1.25m,b、h分别为1m。求得油箱散热面积为:At1.8h(ab)1.5ab(1.8l(1.251) 1.51.25)m2 5.9m2油箱的散热功率为:PhcK1AtT式中 K1
29、油箱散热系数,查表51,K1取16W/(m2);T油温与环境温度之差,取T35。Phc165.935kW3.3kWPhr12.3kW由此可见,油箱的散热远远满足不了系统散热的要求,管路散热是极小的,需要另设冷却器。冷却器所需冷却面积的计算冷却面积为: 式中 K传热系数,用管式冷却器时,取K116W(m2); tm平均温升();取油进入冷却器的温度T160,油流出冷却器的温度T250,冷却水入口温度tl25,冷却水出口温度t230。则: 所需冷却器的散热面积为:考虑到冷却器长期使用时,设备腐蚀和油垢、水垢对传热的影响,冷却面积应比计算值大30,实际选用冷却器散热面积为:A1.32.8m23.6m
30、2 注意;系统设计的方案不是唯一的,关键要进行方案论证,从中选择较为合理的方案。同一个方案,设计者不同,也可以设计出不同的结果,例如系统压力的选择、执行元件的选择、阀类元件的选择等等都可能不同。附:系统工况图2.7液压缸的设计2.7.1液压缸主要尺寸的确定液压缸壁厚和外经的计算液压缸的壁厚由液压缸的强度条件来计算。液压缸的壁厚一般指缸筒结构中最薄处的厚度。从材料力学可知,承受内压力的圆筒,其内应力分布规律应壁厚的不同而各异。一般计算时可分为薄壁圆筒和厚壁圆筒。液压缸的内径D与其壁厚的比值的圆筒称为薄壁圆筒。工程机械的液压缸,一般用无缝钢管材料,大多属于薄壁圆筒结构,其壁厚按薄壁圆筒公式计算 式
31、中 液压缸壁厚(m);D液压缸内径(m);试验压力,一般取最大工作压力的(1.251.5)倍;缸筒材料的许用应力。无缝钢管。则:在中低压液压系统中,按上式计算所得液压缸的壁厚往往很小,使缸体的刚度往往很不够,如在切削过程中的变形、安装变形等引起液压缸工作过程卡死或漏油。因此一般不作计算,按经验选取,必要时按上式进行校核。液压缸壁厚算出后,即可求出缸体的外经为为同理 夹紧与定位液压缸的壁厚与外径为:缸体外径夹紧与定位液压缸的壁厚与外径为:,2)液压缸工作行程的确定液压缸工作行程长度,可根据执行机构实际工作的最大行程来确定,并参阅P12表2-6中的系列尺寸来选取标准值。液压缸工作行程选 夹紧与定位
32、液压缸选 3) 缸盖厚度的确定一般液压缸多为平底缸盖,其有效厚度t按强度要求可用下面两式进行近似计算。无孔时 有孔时 式中 t缸盖有效厚度(m);缸盖止口内径(m);缸盖孔的直径(m)。液压缸:无孔时 ,取 t=20mm有孔时,取 t=50mm夹紧与定位液压缸:无孔时,取t=17mm有孔时:,取t=35mm4) 最小导向长度的确定当活塞杆全部外伸时,从活塞支承面中点到缸盖滑动支承面中点的距离H称为最小导向长度(如下图2所示)。如果导向长度过小,将使液压缸的初始挠度(间隙引起的挠度)增大,影响液压缸的稳定性,因此设计时必须保证有一定的最小导向长度。 图2 液压缸的导向长度对一般的液压缸,最小导向
33、长度H应满足以下要求:式中 L液压缸的最大行程; D液压缸的内径。活塞的宽度B一般取B=(0.610)D;缸盖滑动支承面的长度,根据液压缸内径D而定;当D80mm时,取。为保证最小导向长度H,若过分增大和B都是不适宜的,必要时可在缸盖与活塞之间增加一隔套K来增加H的值。隔套的长度C由需要的最小导向长度H决定,即液压缸:最小导向长度:,取 H=72mm活塞宽度:B=0.8D=64mm缸盖滑动支承面长度:隔套长度:夹紧与定位液压缸:最小导向长度:,取 H=47mm活塞宽度:B=0.8D=50.4mm,取 B=50mm缸盖滑动支承面长度:隔套长度:5) 缸体长度的确定液压缸缸体内部长度应等于活塞的行
34、程与活塞的宽度之和。缸体外形长度还要考虑到两端端盖的厚度。一般液压缸缸体长度不应大于内径的2030倍。液压缸:缸体内部长度夹紧与定位液压缸:缸体内部长度2.7.2 液压缸的结构设计液压缸主要尺寸确定以后,就进行各部分的结构设计。主要包括:缸体与缸盖的连接结构、活塞与活塞杆的连接结构、活塞杆导向部分结构、密封装置、排气装置及液压缸的安装连接结构等。由于工作条件不同,结构形式也各不相同。设计时根据具体情况进行选择。缸体与缸盖的连接形式缸体与缸盖的连接形式与工作压力、缸体材料以及工作条件有关。本次设计中采用外半环连接,如下图3所示:图3 缸体与缸盖外半环连接方式优点:结构较简单;加工装配方便缺点:外
35、型尺寸大;缸筒开槽,削弱了强度,需增加缸筒壁厚2) 活塞杆与活塞的连接结构参阅P15表2-8,采用组合式结构中的螺纹连接。如下图4所示:图4 活塞杆与活塞螺纹连接方式特点:结构简单,在振动的工作条件下容易松动,必须用锁紧装置。应用较多,如组合机床与工程机械上的液压缸。活塞杆导向部分的结构(1)活塞杆导向部分的结构,包括活塞杆与端盖、导向套的结构,以及密封、防尘和锁紧装置等。导向套的结构可以做成端盖整体式直接导向,也可做成与端盖分开的导向套结构。后者导向套磨损后便于更换,所以应用较普遍。导向套的位置可安装在密封圈的内侧,也可以装在外侧。机床和工程机械中一般采用装在内侧的结构,有利于导向套的润滑;
36、而油压机常采用装在外侧的结构,在高压下工作时,使密封圈有足够的油压将唇边张开,以提高密封性能。在本次设计中,采用导向套导向的结构形式,其特点为:导向套与活塞杆接触支承导向,磨损后便于更换,导向套也可用耐磨材料。盖与杆的密封常采用Y形、V形密封装置。密封可靠适用于中高压液压缸。防尘方式常用J形或三角形防尘装置。活塞及活塞杆处密封圈的选用活塞及活塞杆处的密封圈的选用,应根据密封的部位、使用的压力、温度、运动速度的范围不同而选择不同类型的密封圈。在本次设计中采用O形密封圈。第三章 液压集成块的设计3.1块式集成的结构块式集成是按典型液压系统的各种基本回路,做成通用化的6面体油路块(集成块),通常其四
37、周除1面安装通向液压执行器(液压缸或液压马达)的管接头外,其余3面安装标准的板式液压阀及少量叠加阀或插装阀,这些液压阀之间的油路联系由油路块内部的通道孔实现,块的上下两面为块间叠积结合面,布有由下向上贯穿通道体的公用压力油孔P、回油孔O(T)、泄漏油孔L及块间连接螺栓孔,多个回路块叠积在一起,通过4只长螺栓固紧后,各块之间的油路联系通过公用油孔来实现。3.2块式集成的特点可简化设计;设计灵活、更改方便;易于加工、专业化程度高;结构紧凑、装配维护方便;系统运行效率较高块式集成的主要缺点是集成块的孔系设计和加工容易出错,需要一定的设计和制造经验。 3.3块式集成液压控制装置的设计1)分解液压系统并
38、绘制集成块单元回路图集成块单元回路实质上是液压系统原理图的一个等效转换。分解集成块单元回路时,应优先采用现有系列集成块单元回路,以减少设计工作量。集成块上液压阀的安排应紧凑,块树应尽量晒,以减少整个液压控制装置的结构尺寸和重量。集成块的数量与液压系统的复杂程度有关,一摞集成块组中,除基块和顶块外,中间块一般1-7块。当所需中间块多于7块时,可按系统工作特点和性质,分组多摞叠加,否则集成简单回路合用一个集成块;液压 泵的出口窜接单向阀时,可采用管式连接的单向阀(窜接在泵与集成块组的基块之间);采用少量叠加阀、插装阀及集成块专用嵌入式插装阀;集成块侧面加装过渡板与阀连接;基块与顶块上布置适当的元件
39、等等。块的设计(1)确定公用油道孔的数目集成块体的公用油道孔,有二孔、三孔、四孔、五孔等多种设计方案,应用较广的为二孔式和三孔式。二孔式 在集成块上分别设置压力油孔P和回油孔O各一个,用4个螺栓孔与块组连接螺栓间的环形孔来作为泄漏油通道。二孔式集成块的优点是结构简单,公用通道少,便于布置元件;泄漏油道孔的通流面积大,泄漏油的压力损失小。缺点是:在基块上需将4个螺栓孔相互钻通,所以须堵塞的工艺孔较多,加工麻烦,为防止油液外漏,集成块间相互叠加面的粗糙度要求较高,一般应小于Ra0.8m。三孔式 在集成块上分别设置压力油孔P、回油孔O和泄油孔L共3个公用通道三孔式集成块的优点是结构简单,公用油道孔数
40、较少,缺点是因泄漏油孔L要与各元件的泄漏油口相通,故其连通孔道一般细而长,加工较困难,且工艺孔较多。(2)液压元件样板(3)确定孔道直径及通油孔间的壁厚a.确定通油孔道的直径与阀的油口相通孔道的直径,应与液压阀的油口直径相同;与管接头相连接的孔道,其直径一般应按通过的流量和允许流速,用式计算,但孔口须按管接头螺纹小径钻崆并攻丝;工艺孔应用螺塞或球涨堵死;对于公用孔道,压力油孔和回油孔的直径可以类比同压力等级的系列集成块中的孔道直径确定,也可通过式计算得到;泄油孔的直径一般由经验确定。b.连接孔的直径固定液压阀的定位销孔的直径和螺钉孔的直径,应与所选定的液压阀的定位销直径及配合要求与螺钉孔的螺纹
41、直径相同;连接集成块组的螺栓规格可类比相同压力等级的系列集成块的连接螺栓确定,也可以通过强度计算得到。单个螺栓的螺纹小径d的计算公式为: 式中;P-块体内部最大受压面上的推力;n-螺栓个数;-担搁螺栓的材料许用应力。螺栓直径确定后,其螺栓孔(光孔)的直径也就随之而定,系列集成块的螺栓直径为M8-M12,其相应的连接孔直径为9-12(mm)。c.起吊螺钉的直径。单个集成块重量在30以上时,应按重量和强度确定螺钉孔的直径。d.油孔间的壁厚及其校核。通油孔间的最小壁厚的推荐值不小于5 mm。当系统压力高于6.3Mpa时,或孔间壁厚较小时,应进行强度校核,以防止系统在使用中被击穿。(4) 中间块外形尺
42、寸的确定中间块用来安装液压阀,其高度H取决于所安装元件的高度。H通常应大于所安装的液压阀的高度。在确定中间块的长度和宽度尺寸时,在已确定共有油道孔基础上,应首先确定公有油道孔位置应与标准通道块上的孔一致。中间块的长度和宽度尺寸均应大于安放元件的尺寸,以便于设计集成块内的通油孔道时调整元件的位置。一般长度方向的调整尺寸为40-50 mm,宽度方向为20-30 mm。调整尺寸留的较大,孔道布置方便,但将加大块的外形尺寸和重量,反之,则结构紧凑、体积小、重量轻,但孔道布置困难。最后确定的中间块长度和宽度应与标准系列块的一致。 (5)布置集成块上的液压元件液压元件在通道块上的安装位置合理与否,直接影响
43、集成块体内孔道结构的复杂程度、加工工艺性的好坏及压力损失大小。元件安放位置不仅与典型单元回路的合理性有关,还要受到元件结构、操纵调整的方便性等因素的影响。a.中间块中间块的侧面安装各种液压控制元件。当需与执行装置连接时,3个侧面安装元件,一个侧面安装管接头。注意事项如下:应给安装液压阀、管接头、传感器及其他元件的各面留有足够的空间;集成块体上要设置足够的测压点,以便于调试和工作中使用;需经常调节的控制阀如各种压力阀和流量阀等应安放在便于调节和观察的位置,应避免相邻侧面的元件发生干涉;应使与各元件相通的油孔尽量安排在同一水平面,并在公用通油道的直径范围内,以减少中间连接孔、深孔和斜孔的数量。互不
44、相通的孔间应保持一定壁厚,以防工作时击穿;集成块的工艺孔均应封堵,封堵有螺塞、焊接和球涨等三种方式;在集成块间的叠加面上,公用油道孔出口处要安装O形密封圈,以实现块间的密封。应在公用油道孔出口处按选用的O形密封圈的规格加工出深孔,O型圈沟槽尺寸应满足相关标准的规定;b.基块(底版)基块的作用是将集成块组件固定在油箱顶盖或专用底座上,并将公用通油孔道通过管接头与液压 泵和油箱相连接,有时需在基块侧面上安装压力表开关。设计时要留有安装法兰、压力表开关和管接头等的足够空间。当液压泵出油口经单向阀进入主油路板时,可采用管式单向阀,并将其装在基块外。c.顶块(盖板)顶块的作用是封闭公用通油孔道,并在其侧
45、面安装压力表开关以便测压,有时也可在顶块上安装一些控制阀,以减少中间块数量。(6)集成块油路的压力损失集成块组的压力损失,是指贯通全部集成块的进油、回油孔道的压力损失。在孔道布置一定后,压力损失随流量增加而增加。通常,经过一个块的压力损失值约为0.01Mpa.(7)集成块的材料和主要技术要求制造集成块的材料因液压系统压力高低和主机类型不同而异。通常,对于固定机械,低压系统的集成块,宜选用HT250或球墨铸铁;高压系统的集成块宜选用20钢和35钢锻件。对于有重量限制要求的行走机械等设备的液压系统,其集成块可采用铝合金锻件,但要注意强度计算。集成块的毛坯不得有砂眼、气孔、缩孔和夹层等缺陷,必要时需
46、对其进行探伤检查。毛坯在切削加工前应进行时效处理或退火处理,以消除内应力。集成块各部位的粗糙度要求不同:集成块各表面和安装嵌入式液压阀的孔的粗糙度不大于Ra0.8m,末端管接头的密封面和O形圈沟槽的粗糙度不大于Ra3.2m,一般通油孔道的粗糙度不大于Ra12.5m。块间结合面不得有明显划痕。形位公差要求为:块间结合面的平行度公差一般为0.03m,其余4个侧面与结合面的垂直度公差为0.1 mm。为了美观,机械加工后的铸铁和钢质集成块表面可镀锌。4.本设计中SZ-250型注塑机液压系统的集成块系统图如下:设计时采用Pro/E立体三维造型,把集成块内部孔道和外形造出,这样三维立体图,具有可视性,形象
47、直观.由于本设计用到的控制阀比较多,现采用两组集成块的方法,其三维造型分别如下第四章SZ-250型注塑机动力装置的设计4.1 SZ-250型注塑机液压站的设计液压站是由液压油箱、液压泵装置及液压控制装置三大部分组成。液压油箱装有空气滤清器、滤油器、液面指示器和清洗孔等。液压泵装置包括不同类型的液压泵、驱动电机及其它们之间的联轴器等。液压控制装置是指组成液压系统的各阀类元件及其联接体。机床液压站的结构型式有分散式和集中式两种类型。1集中式,这种型式将机床液压系统的供油装置、控制调节装置独立于机床之外,单独设置一个液压站。这种结构的优点是安装维修方便,液压装置的振动、发热都与机床隔开,缺点是液压站
48、增加了占地面积。 2分散式,这种型式将机床液压系统的供油装置、控制调节装置分散在机床的各处。例如,利用机床床身或底座作为液压油箱存放液压油。把控制调节装置放在便于操作的地方。这种结构的优点是结构紧凑,泄漏油易回收,节省占地面积,但安装维修不方便。同时供油装置的振动、液压油的发热都将对机床的工作精度产生不良影响,故较少采用,一般非标设备不推荐使用。液压站的结构布置,液压站上各部件、元件的布置要均匀,便于装配、调试、使用与维护,适当注意外形整齐和美观;液压控制装置在液压油箱上的安放位置应便于压力阀、流量阀的调节,应便于电磁阀的手动调整和装拆,应便于压力表与压力表开关的观察和调整。在液压站结构总成设
49、计中还应特别注意污染控制、泄漏控制、液压冲击控制、振动与噪声控制等。液压动力源(即液压泵组)是多种元、附件组合而成的整体,是为一个或几个系统存放一定清洁度的工作介质,并输出一定压力、流量的液体动力,兼作整体式液压站安放液压控制装置基座的整体装置。液压动力源一般由液压泵组、油箱组件、控温组件、过滤组件和蓄能器组件等5个相对独立的部分组成。液压动力源装置按液压泵组布置方式的分为:上置式液压动力源、非上置式液压动力源、柜式液压动力源。上置式液压动力源,泵组布置在油箱之上的上置式液压动力源,当电动机卧式安装,液压泵置于油箱之上时,称为卧式液压动力源。当电动机立式安装,液压泵置于油箱之内时,称为立式液压
50、动力源。上置式液压动力源占地面积小,结构紧凑,液压泵置于油箱内的立式安装动力源,噪声低且便于收集漏油。这种结构在中、小功率液压站被广泛使用。当采用卧式动力源时,由于液压泵置于油箱之上,必须注意各类液压泵的吸油高度,以防止液压泵进油口处产生过大的真空度,造成吸空或气穴现象。叶片泵的吸油高度500mm.4.2液压油箱的设计1油箱的作用:存储液压油液、散发油液热量、逸出空气、沉淀杂质、分离水分和安装元件。2油箱通常可分为整体式油箱、两用油箱和独立油箱三类。整体式油箱是指在液压系统或机器的构件内形成的油箱。两用油箱是指液压油与机器中的其他目的用油的公用油箱。3油箱的容量油箱的总容量包括油液容量和空气容
51、量。油液容量是指油箱中油液最多时,即液面在液位计的上刻线时的油液体积。在最高液面以上要留出等于油液容量的1015的空气容量,以便形成油液的自由表面,容纳热膨胀和泡沫,促进空气分离,容纳停机或检修时靠自重流回油箱的油液。油箱的容量通常可按式,-液压泵的总额定流量(L/min);-与系统压力有关的经验系数:低压系统=24,中低压系统=57,高压系统=10124油箱的设计1)箱顶、通气器(空气过滤器)、注油口油箱的箱顶结构取决于它上面安装的元件。例如,如果液压泵布置在油箱内部液面以下,则箱顶应为或应有可拆卸的盖。箱盖及管子引出口之类的所有开口都要妥为密封。箱顶上安装液压泵组时,顶板的厚度应为侧板厚度
52、的四倍,以免产生振动。液压泵组与箱顶之间应设置隔振垫。为了便于布置和维修,有时采用装在箱顶上的回油过滤器。箱顶上一般要设置通气器(空气过滤器)、注油口,通气器通常为附带注油口的结构,取下通气帽可以注油,放回通气帽即成通气过滤器。2)箱壁、清洗孔、吊耳(环)、液位计对于钢板焊接的油箱,用来构成油箱体的中碳钢的最小厚度。箱顶上安装液压泵组时,侧板厚度应适当加大。当箱顶与箱壁之间为不可拆连接时,应在箱壁上至少设置一个清洗孔。清洗孔的数量和位置应便于用手清理油箱所有内表面。清洗口法兰盖板应该能 由1个人拆装。法兰盖板应配有可以重复使用的弹性密封件。 为了便于诱降的搬运,应在油箱四角的箱壁上方焊接吊耳(
53、也称吊环)。吊耳有圆柱形和钩形两种。液位计通常为带有温度计的结构。液位计一般设在油箱外壁上,并近靠注油口,以便注油时观测液面。液位计的下刻线至少应比吸油过滤器或吸油管口上缘高出75mm,以防止吸入空气。液位计的上刻线对应着油液的容量。液位计与油箱的连接处有密封措施。3)箱底、放油塞、支角应在油箱底部最低点设置放油塞(M181.5),以便油箱清洗和油液更换。为此,箱底应朝向清洗孔和放油塞倾斜,倾斜坡度通常为1/251/20;这样可以促使沉积物(油泥或水)聚集到油箱中的最低点。为了便于放油和搬运,应该把邮箱架起来,油箱底至少离开地面150 mm。油箱应设有支脚,支脚可以单独制作后焊接在箱底边缘上,
54、也可以通过适当增加两侧壁高度,以使其经弯曲加工后兼作油箱支脚。支脚应该有足够大的面积,以便可以用垫片或契铁来调平。4)隔板、除气网为了延长油液在油箱中逗留的时间,促进油液在油箱中的环流,促使更多的油液参与在系统中的循环,从而更好地发挥油箱的散热、除气、沉淀等功能,油箱中,尤其在油液容量超过100L的油箱中应设置内部隔板。隔板要把系统回油区与吸油区隔开,并尽可能使油液在油箱内沿着油箱壁环流。隔板缺口处要有足够大的过流面积,使环流流速为0.30.6m/s。隔板结构有溢流式标准型、溢流式和回流式等多种型式。溢流式隔板的高度不应低于液面高度的2/3;隔板下部应开有缺口,以使吸油侧的沉淀物经此缺口至回油
55、侧,并经放油口排出。隔板的安装型式为了有助于油液中的气泡浮出液面,可在油箱内设置除气网,除气网用网眼直径0.5 mm的金属网制作,并倾斜1030布置。5)过滤网的配置 过滤网可以设计成将液压油箱内部一分为二,使吸油管与回油管隔开,这样液压油可以经过一次过滤(见下图12)。过滤网通常使用50100目左右的金属网。6)管路的配置液压系统的管路要进入油箱并在油箱内部终结。(1)吸油管和回油管液压泵的吸油管和系统的回油管要分别进入由隔板隔开的吸油区和回油区,管端应加工成朝向箱壁的45斜口,这样既可增加开口面积,又利于沿箱壁环流。为了防止空气吸入空气(吸油管)或混入(回油管),以免搅动或吸入箱底沉积物,
56、管口上缘至少要低于最低液面75mm,管口下缘至少离开箱底最高点50mm。回油管流速过高时,可在回油管端装设钻有许多小孔的油管形扩散器。吸油管前必须安装粗过滤器,以清除较大颗粒杂质,保护液压泵;建议在回油管上安装精过滤器,以滤除细微颗粒杂质,保护液压元件。(2)泄油管泄油管应尽量单独接入油箱并在液面以上终结。如果泄油管通入液面以下,要采取措施防止出现虹吸现象。(3)穿孔的密封5液压油箱外形尺寸液压油箱的有效容积确定后,需设计液压油箱的外形尺寸,为提高冷却效率,在安装位置不受限制时,可将液压油箱的容量予以增大。油箱部分的长、宽、高尺寸为:a=1250mm,b=860mm,c=775mm下图所示为液
57、压油箱的简图,在箱的上盖或侧面可以安装液压泵、电动机以及其它液压元件。液压油箱结构简图4.3液压泵组的结构设计液压泵组是指液压泵及驱动泵的原动机和联轴器及传动底座组件。液压泵组的结构设计要点如下:1液压泵组的布置方式可根据主机的结构布局、工况特点、使用要求及安装空间的大小,合理确定液压泵组的布置方式2液压泵组的连接确定液压泵与原动机的轴间连接和安装方式首先考虑的问题是:液压泵轴的径向和轴向负载的消除或防止。由于本设计中泵轴在结构上不能承受额外的径向和轴向载荷,所以液压泵最好由原动机经联轴器直接驱动,并使泵轴与驱动轴之间严格对中,轴线的同轴度误差不大于0.08mm. 原动机与液压泵之间的联轴器宜
58、采用带非金属弹性元件的挠性联轴器.例如GB-5272-1985中规定的梅花形弹性联轴器,具有弹性、耐磨性、缓冲性及耐油性较高,制造容易,维护方便等优点。3液压泵组的安装方式本设计中采用钟形罩立式安装,通过液压泵上的轴端法兰实现泵与钟形罩的连接,钟形罩再与带发兰的立式电动机连接,依靠钟形罩上的止口保证液压泵与电动机的同轴度。此种方式安装和拆卸均较方便。4液压泵的安装姿态应使液压泵的壳体泄油口朝上,以保证工作时泵壳体中始终充满油液。泵的轴伸和联轴器等外露的旋转部分,应该设有可拆装的防护罩以保证安全。泵的下方应设置滴油盘,以免检修时油液流到地面上。总结与展望从注射机问世起,锁模力在10005000k
59、n,注射量在502000g的中小型注射机占绝大多数。到了70年代后期,由于工程塑料的发展,特殊是在汽车、船舶、宇航、机械以及大型家用电器方面的广泛使用,使大型注射机得到了迅速发展。美国最为明显。在1980年全美国约有140台10000kn以上锁模力的大型注塑机投入巾场,到1985年增至500多台。日本名机公司已经成功地制造了当今全球最大的注塑机,其锁模力达到120000kn,注射量达到92000g。目前世界发达国家的注塑机控制技术比或LCD显示屏的过程监控,并通过多重处理将尽可能多的处理工作分配给外围装置完成,以提高注塑机内的通讯能力,减轻主控部分负荷。这在一定程度上代表了注塑机控制技术的未来走向。 展望未来,相信随着控制技术的不断发展与完善,将使注塑机朝着自动化、节能化、智能化、无人化等方向发展。如采用计算机数字化控制和程序化控制,使注塑机具有自动控制、自动诊断、自动调节、自动补偿功能;控制系统实行模块化、集成化;采用成组技术,实施多台注塑机的群控 。致 谢为期十六周的毕业设计很快就要结束了,在这段充实而繁忙的的日子里我掌握、巩固许多专业方面的知识,同时也收获了许多其他方面的东西。在此我要感谢胡少刚导师在毕业设计期间给
- 温馨提示:
1: 本站所有资源如无特殊说明,都需要本地电脑安装OFFICE2007和PDF阅读器。图纸软件为CAD,CAXA,PROE,UG,SolidWorks等.压缩文件请下载最新的WinRAR软件解压。
2: 本站的文档不包含任何第三方提供的附件图纸等,如果需要附件,请联系上传者。文件的所有权益归上传用户所有。
3.本站RAR压缩包中若带图纸,网页内容里面会有图纸预览,若没有图纸预览就没有图纸。
4. 未经权益所有人同意不得将文件中的内容挪作商业或盈利用途。
5. 装配图网仅提供信息存储空间,仅对用户上传内容的表现方式做保护处理,对用户上传分享的文档内容本身不做任何修改或编辑,并不能对任何下载内容负责。
6. 下载文件中如有侵权或不适当内容,请与我们联系,我们立即纠正。
7. 本站不保证下载资源的准确性、安全性和完整性, 同时也不承担用户因使用这些下载资源对自己和他人造成任何形式的伤害或损失。
相关资源
更多








