毕业设计(论文)三缸单作用乳化液泵的设计(全套图纸)
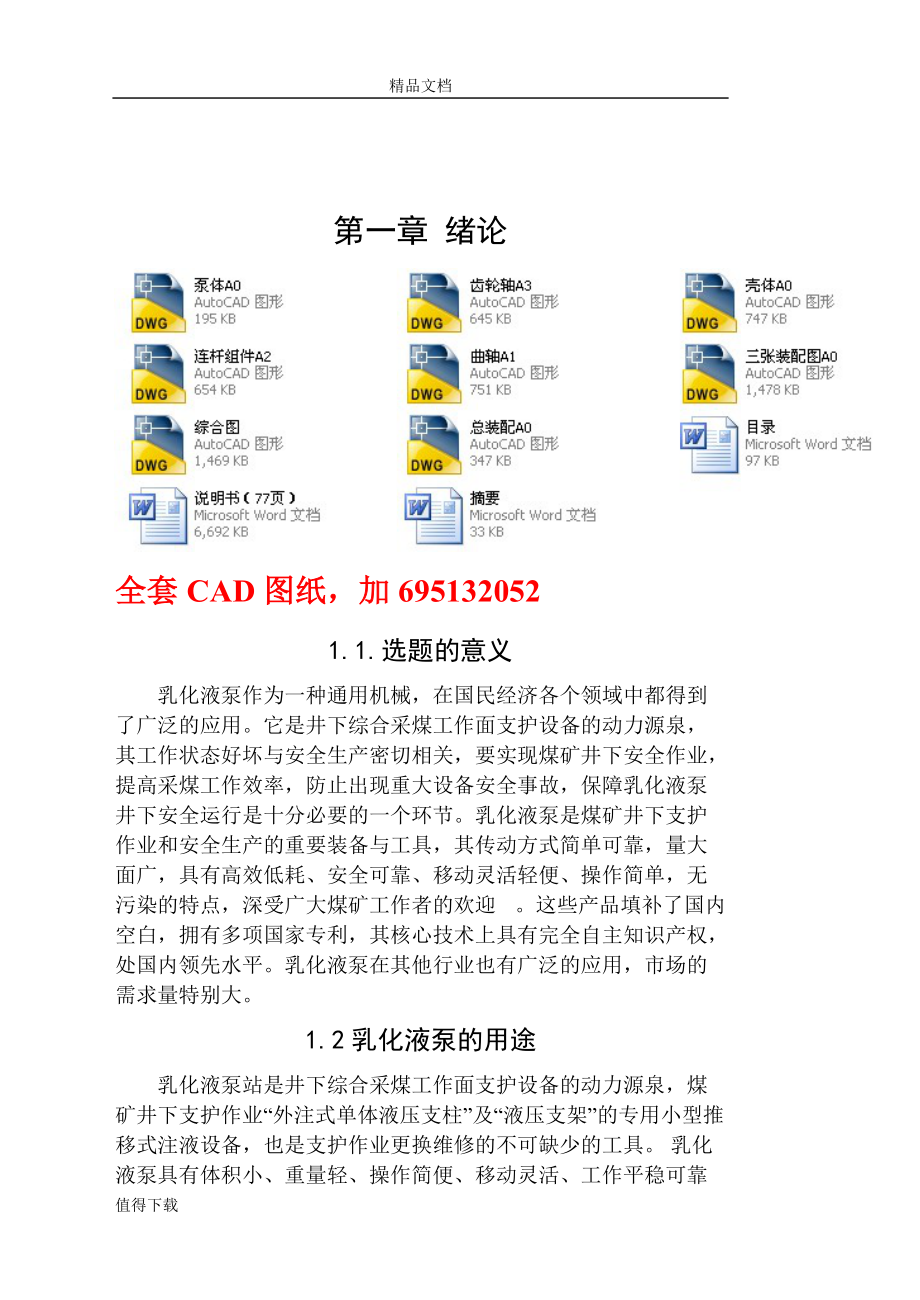


《毕业设计(论文)三缸单作用乳化液泵的设计(全套图纸)》由会员分享,可在线阅读,更多相关《毕业设计(论文)三缸单作用乳化液泵的设计(全套图纸)(79页珍藏版)》请在装配图网上搜索。
1、精品文档第一章 绪论全套CAD图纸,加6951320521.1.选题的意义乳化液泵作为一种通用机械,在国民经济各个领域中都得到了广泛的应用。它是井下综合采煤工作面支护设备的动力源泉,其工作状态好坏与安全生产密切相关,要实现煤矿井下安全作业,提高采煤工作效率,防止出现重大设备安全事故,保障乳化液泵井下安全运行是十分必要的一个环节。乳化液泵是煤矿井下支护作业和安全生产的重要装备与工具,其传动方式简单可靠,量大面广,具有高效低耗、安全可靠、移动灵活轻便、操作简单,无污染的特点,深受广大煤矿工作者的欢迎 。这些产品填补了国内空白,拥有多项国家专利,其核心技术上具有完全自主知识产权,处国内领先水平。乳化
2、液泵在其他行业也有广泛的应用,市场的需求量特别大。1.2乳化液泵的用途乳化液泵站是井下综合采煤工作面支护设备的动力源泉,煤矿井下支护作业“外注式单体液压支柱”及“液压支架”的专用小型推移式注液设备,也是支护作业更换维修的不可缺少的工具。乳化液泵具有体积小、重量轻、操作简便、移动灵活、工作平稳可靠和高效、节能、安全的特点,尤其是在空间狭小的坑道口、掘进头、低煤层和回采面等地段,更是一般大型注液泵站无法替代的产品,深受广大煤矿工作者的欢迎。乳化液泵是要实现煤矿井下安全运行的十分必要的一个环节。由于乳化液泵具有流量均匀、压力稳定、运转平稳、强度高、脉冲小、油温低、噪声小、使用维护方便等特点,所以还广
3、泛适用于管道清洗、工件清洗、玻璃清洗、工程掘进等。1.3设计的理论基础研究的内容及方法乳化液泵在许多行业中都有广泛的应用,通过对流体力学、液压传动、机械制图和流体机械等的学习对设计有了一定的理论基础,在实习过程中到车间的参观和对泵的一些零部件及工作原理的认识使我对乳化液泵的设计有了基本的思路,利用理论课学过的知识进行理论分析热力学分析和对比计算,再通过查阅资料与分析计算相结合进行方案的设计,根据计算校核进行及时的修改和设计修订,实现优化设计,并能很直观的反映出乳化液泵的内部结构和工作原理。随着经济的发展在很多生产技术领域内,广泛使用着以曲柄连杆机构为传动方式的柱塞泵。此种传动方式,简单可靠,量
4、大面广。从小型的实验室计量泵到超过1 MW的大功率石油钻井泵,以及油田注水、压裂、固井、输油、输液等工况往复泵,几乎均被此种传动方式所覆盖,可谓独领风骚、经久不衰,。应该肯定,以往对传统往复泵的理论研究和实验研究,系统完整,揭示其运动规律与动力特性,对发展生产技术将继续发挥重要作用。但与任何其它事物的发展过程一样,恰恰在对传统往复泵工作机理研究逐步深入并取得积极成果的同时,也开始认识到传统的曲柄连杆机构所决定的运动与动力特性局限了其自身的应用范畴及发展。通过以上分析可以领悟出一个道理,即在曲柄连杆机构传动的往复泵中,其所以要发展三缸泵、四缸泵、五缸泵、六缸泵甚至七缸泵等多缸泵,从动力学特性的本
5、质上来判断,都仅仅是为了尽可能减少叠加加速度,以减小液流惯性损失,以及减小叠加排量波动度,以改善吸入性能和排液工艺质量,即采用增加结构复杂性的手段来改善曲柄连杆传动方式的动力特性与运动特性,这在机械设计中是常见的事情,但其所付出的代价是巨大的。在传统的曲柄连杆机构传动的往复泵发展过程中,排量、压力的波动以及吸入系统惯性损失对自吸性能的严重影响,始终制约着泵速的提高。虽然排出预压空气包、吸入缓冲器及吸入灌注泵的配套使用能在一定程度上缓解这些矛盾,但不是从根本上解决问题,所以,20世纪80年代初期出现的“适当增长冲程长度、合理降低额定泵速、发展中速往复泵”的技术路线。这种对策的实质,实际上就是对曲
6、柄连杆机构往复泵适用范围的标定,也就是说,在综合考虑运行工况、使用条件、制造水平、基础工业水准的条件下,曲柄连杆机构的往复泵只适应在中速或较低的泵速下才能确保其运动的可靠性。如果提高泵速,则必须附加排出端减振装置和吸入端灌注设备。在这种情况下,由于提高泵速所导致的减小往复泵体积及质量的优点,将被附属设备复杂程度的提高、质量的增加以及维修成本的增加抵销得一干二净。也就是说,企图在单纯的参数设计上提高泵速、缩短冲程来减小往复泵的体积与质量,主观愿望在情理之中,客观效果在意料之外,因而限制了它的进一步发展。但任何事物的发展都存在矛盾,并且任何新生事物也只能在一定的领域内具有适应性,归纳起来,有以下几
7、点认识作为引玉之砖:(1)传统的往复泵,仍将继续在生产技术领域内发挥巨大作用,一般地说,在中速和较低的泵速下,可靠性程度较高,“适当增长冲程长度、合理降低泵速”的技术路线仍是切合实际和具有现实意义的。(2)恒排量往复泵,以发展三缸单作用型式为宜,如果盲目增加缸数,其效果将与发展恒排量泵的宗旨背道而驰,如果毫无顾忌地提高泵速,也将引起单缸内的汽化并使工况恶化,因此,凸轮传动的恒排量往复泵的参数设计,似宜为“适当缩短冲程长度、合理提高额定泵速”。(3)恒排量往复泵对油田注水泵、增压注水泵、注聚合物泵特别适应,具有现实的技术开发价值,并将对驱油泵(特别是稠油泵)等有特殊工艺要求的泵的发展起促进作用。
8、(4)传统往复泵与恒排量往复泵,在相当长的历史阶段内必将长期共存,并按技术特征、工况条件、工艺要求、经济效益来划分其各自占领的领域、各扬其长、各得其所、互相补充、共同发展。第二章 总体方案的确定.泵型的选择及特点根据给定的设计参数和压力高等应用特点,选用的泵型为往复泵,往复泵可以分为机动泵、手动泵、柱塞泵、隔膜泵、计量泵、立式泵、卧式泵、对置式泵、轴向平行式泵等,这些泵之间有着密切联系22。2.1.1机动泵及其共同特点用独立的旋转原动机(如电动机、柴油机、汽油机等)驱动的泵,称为机动泵。用电动机驱动的泵又叫电动泵。机动泵通常由液力端、传动端、减速机,原动机及其附属设备(润滑、冷却系统等)所组成
9、。机动泵的共同特点:.瞬时流量脉动而平均流量(泵的流量)只取决于泵的主要结构参数(每分钟往复次数)、 (柱塞的行程)、(柱塞直径)而与泵的排出压力几乎无关,当、为确定值时,泵的流量是基本恒定的。.泵的排出压力是一个独立参数,不是泵的固有特性,它只取决于排出管路的特性而与泵的结构参数和原动机的功率无关。.机动泵都需要有一个把原动旋转运动转化为柱塞往复运动或隔膜周期性弹性变形的传动端,故一般讲,结构较复杂,运动零部件数量较多,造价也较昂贵。表2-1 常见的几种机动柱塞泵的参数范围22用途(介质)化工用泵(化工介质)液压机(乳化液)泵型卧式三联(缸)单作用柱塞泵卧式三联(缸)单作用柱塞泵(m/h)(
10、10N/m)(spm)(10m)(10m)(m/s)(kw)2.1.2直接作用泵及其特点液力端柱塞与动力端直接连接的泵,通称为直接作用泵。动力端的工作介质可以是蒸汽,压缩气体(通常是空气)或有压液体(一般是油)。其中最常用的是蒸汽,也叫蒸汽直接作用泵。直接作用泵通常由液力端、动力缸,配汽(气或液)机构及其它附属设备所组成。直接作用泵的共同特点:.瞬时流量脉动较小,平均流量(泵的流量)也只取决于、.但在蒸汽泵中,由于蒸汽源的压力是恒定的,因此当在蒸汽进口截流时,进入汽缸(动力缸)的蒸汽量和蒸汽压力将同时发生变化,相应的柱塞速度和或将发生变化,从而泵的流量就不能恒定;另一方面,如果泵的排出压力增高
11、时,由于汽缸内蒸汽压力不变,所以柱塞速度(或)就会自行降低,泵的流量也随之减小。故蒸汽直接作用不会过载。.泵的排出压力取决于管路特性,因此,对于直接作用泵来讲,泵的最大排出压力取决于它和动力端工作介质的压差。这样一来,安全阀就可设置工作介质一侧,既可以保护动力源设备又使操作上比较安全。.直接作用泵无须具备由旋转运动转化为柱塞往复运动的传动端,因此,就泵本身来讲,结构较简单,易损件少,造价也较低廉。但对于需要自备动力源的直接作用泵,泵机组还是较为复杂的。.直接作用实现流量调节则较为方便,只要改变工作介质的流量就可以达到泵的流量调节的目的。.直接作用泵,特点是蒸汽直接作用泵,因无产生火花的动力装置
12、,因此适用于要求防火的场合。.直接作用的型式较少,只有双联(缸)双作用,双联(缸)单作用,单联(缸)双作用或单联(缸)单作用几种有限的型式。由于上述特点,直接作用泵使用范围没有机动泵那样广泛。目前,蒸汽直接作用泵主要用于输送石油及其副产品,如石蜡、沥青等;以气或液体为工作介质的直接作用泵则主要用作产生高压或超高压的增压泵22。2.1.3手动泵及其特点用人力通过杠杆机构驱动柱塞做往复运动的泵,称为手动泵。手动泵的特点:.泵的流量和均匀度均无定植,它取决于人力在单位时间内的操作次数和操作均匀程度。.泵的排出压力取决于排出管路特性和排出端压力。泵的额定排出压力则与泵的结构强度,液力端密封质量及人力大
13、小有关。手动泵主要用于缺少动力或无须其他动力的场合。例如:简易水压试验,简易农药喷雾、农村简易深井提水,食品工业提升液状物以及简易消防用泵等。2.1.4柱塞泵及其特点在液力端往复运动副上,运动件上无密封元件的叫柱塞。相应的泵称为柱塞泵.柱塞泵的特点:.柱塞泵的柱塞形状简单,柱塞直径可制得很小,但不宜过大目前所见到的柱塞直径范围大多在=3 150(10m),个别的达0.2m。直径过小,会遇到加工工艺上的困难,直径过大,特别是卧式泵,因柱塞自重过大造成对密封的偏磨,影响密封的使用寿命。.由于结构的原因,柱塞泵大多制成单作用的,几乎不制成双作用泵。.因柱塞密封(填料箱)在结构上易于变形,在材料选择上
14、也比较灵活,故柱塞泵适用的排出压力范围较广泛,且宜制成高压泵。2.1.5 隔膜泵及其特点泵的液力端借助于隔膜(膜片、波纹管等)来组成工作腔,以隔膜周期弹性变形来代替柱塞的往复运动的泵,称为隔膜泵。隔膜泵的特点:.在泵的液力端以隔膜的静密封代替了柱塞的动密封,因此可作到输送介质绝对不外漏。因此,隔膜泵适于输送易燃、易爆、剧毒、恶臭以及具有放射性等对人体有害的介质,也用于输送纯度高、价格昂贵的物料。对于强腐蚀、易挥发、易结晶以及磨砺性很强的悬浮液,有时也采用隔膜泵,以改善柱塞密封的工作条件,延长其使用寿命。.为了保证隔膜的强度和使用寿命,隔膜的弹性变形挠度通常很小,故对隔膜泵来讲,隔膜工作腔的行程
15、容积不可能很大,否则其径向尺寸就会很大。另外,隔膜泵的每分钟的往复次数也较低。.由于结构上的原因,隔膜泵的余隙容积较大,而且在泵的吸入过程中需要额外克服隔膜变形的阻力,故隔膜泵吸入性能较差,容积效率也较低。.隔膜泵,特别是液力隔膜泵在结构上要比柱塞泵复杂,使用、维护的技术要求也较高。2.1.6卧式泵及其共同特点液缸或柱塞中心线为水平布置的泵,均称为卧式泵。往复泵多为卧式泵,其共同特点如下:.便于操作者观察泵的运转情况,拆、装、使用、维修较为方便。.机组在高度方向尺寸时,不需要很高的厂房;但在长、宽方向尺寸较大时,占地面积则较大。.因为柱塞做水平往复运动,密封件在工作时须承受柱塞自重,容易产生偏
16、磨,尤其当柱塞较重、悬臂很长时,这种现象更为明显。.卧式泵的机械惯性力水平分力较大,而泵的基础承受水平分力的能力又较差,故卧式泵对基础的强度和刚度要求较高。2.1.7 立式泵及其共同特点液缸或柱塞中心线是垂直布置的泵,称为立式泵。立式泵的共同特点:.高度方向尺寸较大,厂房高,但长、宽方向尺寸小,、占地面积少。.运转时,柱塞密封不承受柱塞自重,不易产生偏磨。.机械惯性力水平分力小,垂直分力大,而泵基础有较强的承受垂直分力的能力,故对基础要求不高。.一般讲,立式泵的吸排阀、吸排管布置上较困难,拆装、维护也不太方便,特别是当液力端置于下侧时更明显。但当把液力端置于上侧时,则有所改善。通过对以上几种型
17、式泵的特点的对比,再结合乳化液泵本身的结构特点及其用途,此次设计选用三联单作用机动卧式柱塞泵。2.2液力端结构型式选择在往复泵上把柱塞从滑块处脱开一直到泵的进出口处的部件,称为液力端,液力端是介质过流部分,通常由液缸体,活塞和缸套或柱塞及其密封(填料箱)、吸入阀和排出阀组件、缸盖和阀箱盖以及吸入和排出集合管(或集液器)等所组成,液力端结构型式的选择应与泵型及总体结构型式时,应遵循下述基本原则:.过流性好,水力阻力损失小,为此,液流通道应力求短而直,尽管避免拐弯和急剧的断面变化。.液流通道应利于气体排出,不允许有死区,造成气体滞留,通常,吸入阀应置于液缸体下部,排出阀应置于液缸体顶部。.吸入阀和
18、排出阀应垂直布置,以利于阀板正常启闭和密封,特殊情况下也可以倾斜和水平布置。.余隙容积应尽可能小,尤其是对高压短行程泵或当泵输送含气量大,易挥发性介质时,更应力求减小余隙容积。.易损件寿命长,更换方便。.制造工艺性好不同的泵有不同的液力端,甚至相同的泵型也有不同的液力端,因此液力端结构型式很难统一划分,按泵的吸入阀、排出阀的布置型式、液流通道特性和结构特性可分为:直通式、直角式、阶梯式。对于卧式三联单作用柱塞泵的液力端选用直通式。2.3传动端结构型式选择往复泵上传递动力的部件叫传动端,对于机动泵,传动端是指从滑块起一直到主轴(曲轴)伸出端(动力输入端)为止的部件,如果是泵内减速的,则传动端包括
19、减速机构,如果是泵外减速的,则传动端不包括减速机构,减速机独立,如果是直联泵则传动端没有减速机构,也无减速机。对直接作用泵,传动端即指动力缸(汽缸、气缸)等部件。机动泵的传动端主要由机体、曲轴连杆、曲柄、滑块及润滑冷却等辅助设备所组成11。传动端结构型式选择也应和泵型及总体结构型式选择同时进行,在选择和设计传动端时应遵循以下基本原则:.传动端所属主要零部件必须满足泵最大柱塞力下是强度和刚度的要求。.传动端内各运动副,必须是润滑可靠,满足比压和Pv允许值,润滑油温升也限制在设计要求以内,必要时应有冷却设备。 .在结构和尺寸要求允许的范围内,应力求减小连杆比这样不仅可减小滑块处的比压,而且可减少惯
20、性水头的影响,从而可改善泵阀工作条件和泵的吸入性能。 .要合理的选择液缸中心线的夹角,曲柄间错角,力求使机械的惯性力和惯性力矩得到平衡,减轻对基础的挠力载荷。.传动端,尤其是立式泵传动端,应考虑重心的稳定性。传动端顶部应设有运转时排气,停车时封闭的排气装置,底部应设有排放润滑油的油脂。.拆、装、检修方便,大型泵的传动端还应考虑到传动端各零部件的起吊方式和措施。.易损件及运动副应工作可靠,寿命长,更换较方便。.加工、制造工艺性好。图2-1 乳化液泵总体结构图1 机体 2 连杆 3 滑块 4 曲轴 5 减速机构 6 缸套组件 7 柱塞 第三章 泵的主要结构参数的选择与确定3.1泵的主要尺寸参数的确
21、定3.1.1给定设计参数工作介质:乳化液油(含3-5乳油的中性溶液)排出压力:P=35MP 排量:Q=80Lmin往复泵柱塞个数:Z=3个泵的排出压力额定值仅取决于结构强度、液力端密封对对质量及原动机的额定功率而与流量无关。由公式2210m/s式中 泵的实际流量,10m/s 泵的理论流量,10m/s 泵的容积效率 柱塞截面积,m 柱塞直径,m 柱塞行程长度,m 曲轴转数(rpm)或柱塞的每分钟往复次数spm 泵的联数(柱塞数) 系数 (柱塞杆截面积,m) =(柱塞杆直径,m) 柱塞的平均速度,ms 程径比由上式可知,流量与、等结构参数有关,如果在总体设计时预先选定了泵型和总体结构型式,那么、即
22、为已知,因此,决定Q的主要结构参数就是、和,对于柱塞泵则只有、三个主要结构参数22。3.1.2柱塞直径和行程的确定1.柱塞平均速度的选择的大小直接影响泵各运动副零、部件的摩擦和磨损,特别是对柱塞及其密封这一对运动副的影响尤为显著。不应选择过大,过大摩擦和磨损严重,特别是当柱塞及其密封一旦严重磨损,泄露就将增加,流量下降,排出压力也不能达到额定值。也不能选择过小,要获得一定的值,当一经确定,即为确定值如果选择过小,值就必须较大,这样一来。不仅使液力端径向尺寸增加,而且因柱塞力是和成正比的,传动端受力也随之聚增,从而会使泵的总体尺寸和重量增大。.选取值的一般原则和方法可参考泵的有效功率来选取,一般
23、讲,越大,也越大,反之则宜取较小值,因为大,柱塞力趋于增大,为了减小活塞力,或加大,或提高,其结果都使增大。.活塞平均速度的确定22的大小主要与折合成单联单作用泵的有效功率有关=m/s式中 柱塞平均速度,ms 统计系数 (0.180.8) 折合成单联但作用泵的有效功率,kw (3-1) 式中 Q泵的流量,Lmin当选取时 泵的排出压力,10N/m 泵的吸入压力,10N/m,当或为常压事,全压力- 泵的联数 系数 ,对于单作用泵 K=0 对双作用泵, ,(取0.3)由公式(3-1)kw所以:ms2.曲轴转数和柱塞行程长度的选择当选定后,柱塞的直径可算出由公式查表2-6常见泵型的值范围及建议值22
24、,对一般的卧式三联单作用机动泵值范围现有产品(180720spm)取通过圆整取行程m对于机动泵16)S m3.柱塞直径的确定由经验公式22: (3-2)式中 曲轴的转数rmin 柱塞的行程长度m 柱塞的面积m 联数 容积效率 泵的流量Lmin对于容积效率的选择:当输送常温清水时=0.800.98,当输送石油产品、热水、液化胫等介质时,=0.600.80。对乳化液泵取=0.9由公式(3-2) 解出柱塞直径m4.程径比5.吸入和排出管内径的选择这两个值的选取主要取决于吸入、排出管内介质的流速和。、过大;水力阻力损失过大,消耗能量多,泵的吸入性能差,而且容易产生液缸内空化和汽蚀以及泵的过流量现象;、
25、过小,管路和液力端尺寸较大。在往复泵中,通常要限制、值,尤其值限制更重要,一般取值范围是:2ms,2.5 ms为了制造方便常常采用相同的、值,即取,令 ms式中 吸入管内径 m 排出管内径 m 泵的流量ms 吸入管内介质的平均流速ms 排出管介质的平均流速ms3.2电动机的选择3.2.1原动机功率的选择与确定1.原动机的选择kw =PS式中 泵的全压力 泵的实际流量Lmin也可以按下列公式计算kw式中 泵的全压力 10N/m 泵的实际流量Lmin 2.泵的轴功率(输入功率) (3-3)式中 泵的效率,电动泵的效率范围0.9 取 由公式(3-3)kw3.原动机的功率 kw (3-4) 式中 泵的
26、传动装置效率 原动机的效率 取=0.99由于泵的效率已包括了泵的传动机构的摩擦损失,所以,泵的传动装置效率只与泵的减速机构的机械损失有关。当采用齿轮传动时,0.99(闭式);采用平皮带传动时=0.920.98,三角皮带传动时=0.900.94由公式(3-4)kwkw3.2.2电动机的选择图3-1 Y250M4型电动表3-120原动机功率储备系数泵的型号电动机的功率机动泵2储备系数21.51.251.151.10kw通过圆整后取kw查表3-2 Y系列电动机技术数据可知20,选取Y250M4型电动机=55kw A rmin 功率因数0.88第四章 主要零部件的设计4.1液力端主要零部件的设计柱塞泵
27、液力端通常由液缸体和缸盖,吸入和排出阀箱、阀盖、缸套柱塞和填料箱以及进出口法兰等。液缸体是柱塞泵中主要承受液压的零件之一,由于它的形状复杂、壁后不均,内有十字或T型交孔、应力集中大,而且是与输送介质接触,并承受内压交变载荷,因此,它的设计合理性,对其寿命有较大的影响。特别是当输送高温、高压、强腐蚀性介质时,应注意以下几点:.要选取合适的材料和热处理方式,既要有较高的强度指标和抗腐能力,又要特别注意到材料对应力集中的敏感性。.在结构设计上要求形状简单,壁厚均匀,内部流道孔相交也应尽可能减少,实践证明;在同等条件下,T型交孔要比十字型交孔的液缸体寿命长一些。.如果加工工艺允许,在内部流道交孔应予导
28、圆,并对加工表面做强化处理,以减弱应力集中的影响。.如果在总体和液力端部件设计时就能注意到把液缸体内的高度应力集中部位和高度变载荷区分开来,将会有效地提高液缸的使用寿命。图4-1a直通式布置的液缸体 图4-1b 垂直布置的液缸体液缸体的结构型式主要是服从本泵的总体结构型式和液力端结构选型,液缸体的结构特点可按泵的数分为单作用液缸体和双作用液缸体。对于单作用柱塞泵适合于整体式液缸体,此形式的泵的多个工作腔在同一个块体上,这种液缸体钢性好,工作间距小,机加工量少,但工件较大。整体式柱塞泵液缸体除特殊型外,大多是由若干个垂直相交圆柱面流道孔所组成的一个多工作腔体。下图是典型的液缸体剖视图。图(a)是
29、吸入阀和排出阀组直通式布置的液缸体;图(b)是吸入阀和排出阀互相垂直布置的液缸体.4.1.1液缸体壁厚的确定及强度校核1.液缸体壁厚的确定假定液缸体为一外圆半径为,内圆半径为的等厚壁圆筒且壁厚相对轮薄()时,则可由薄壁筒公式确定壁厚: 10m (4-1) 一般取C=0.30.8(10m)对于球墨铸铁=600800 10N/m式中 壁厚,10m 焊接系数,无焊接=1 缸内最大工作压力,10Pa 液缸体内径,10m 考虑铸造偏心及腐蚀所留的裕量由公式(4-1)m2.强度校核对于薄壁筒() 10N/m (4-2)因为液缸体一般不焊接支管,所以=1由公式(4-2)符合要求。图4-2缸套组件4.2传动端
30、主要零部件的设计4.2.1机体的组成及设计机动往复泵传动端主要由机体、曲轴、连杆、滑块等主要零部件所组成。机体是传动端主要零部件之一,通常由机身、机盖、轴承盖等主要零部件所构成。 1.机体的主要作用.作为传动机构和曲柄连杆机构的支承、定位及运动导向用;.承受或传递泵的作用力和力矩;.作为液力端的支承作用并用天安装某些辅助设备。泵的机体,按其毛坯的形式可分为铸造机体和焊接机体两种。一般讲,铸造机体具体有较高的刚度和抗震能力,稳定性好,易于获得所需的强度,生产周期短,成本也较低,因而在柱塞泵中广为应用。但铸造机体壁厚较厚,整个机体很笨重,通常只适用于固定基础安装。焊接机体多采用低碳钢组焊而成,重要
31、较轻,便于移动。但此种机体刚性较差,制造周期长,成本高。通常只用于要求往常移动的泵。2.机体的结构设计机体结构设计的一般原则.应有足够的强度和刚度,在此前提下,力求重量轻 .结构上力求简单,外形力求美观。铸造和机加工工艺性能应良好。在结构设计上要有便于制造、加工的基准面,以期能较好的保证各加工表面的几何形状、尺寸精度和形状位置分差。不必要的加工表面应力求减小,简化工表,缩短生产周期,降低成本 .便于曲柄机构和传动机构的拆装,调整和检修,便于机体内部的清洗和润滑油的排放和更新.机体底部应有足够的承重面积,尽可能的降低重心,保证其承载能力和泵运转时的稳定性。3.减速机构的设计由于从电动机轴输出的转
32、速过高,采用泵内减速,即一级齿轮减速。1. 传动比的计算查表2-2 Y系列电动机技术数据可知20,选取Y250M4型电动机kw Lmin 功率因数0.88A式中 电动机转数,rmin 电机效率曲轴的转数,rmin 图4-3 减速机构.选定精度等级、材料及齿数.此机器为一般工作机器,速度不高,故选用7级精度.选小齿轮材料为40Cr (调质)硬度为HBS,大齿轮材料为45钢(调质)硬度为HBS.选小齿轮齿数,大齿轮齿数,取.按齿面接触强度设计 (4-3) .试选载荷系数 .计算小齿轮传递的转矩N.m.查表10-7选取齿宽系数21.查表2110-6查得材料的弹性影响系数.查图10-21d按齿面的硬度
33、查得小齿轮的接触疲劳极限 MPa,大齿轮的接触疲劳强度极限 MPa21.计算应力循环次数查由表10-13得21式中 齿轮转速 齿轮每转一圈时,同一齿面啮合的次数 齿轮的工作寿命(单位为h).查图10-19查得接触疲劳强度寿命系数21 .计算接触疲劳许用应力取失效概率为1%。安全系数S=1 MPa MPa. 按齿面接触强度设计计算. 试算小齿轮分度圆直径,代入中极小值由公式(4-3) =0.078m.计算圆周速度ms.计算齿宽查表10-7,取齿宽系数21m.计算齿宽和齿高之比模数 mm齿高 m.计算动载荷系数根据ms,7级精度,查由图10-8查得动载荷系数21,对于直齿轮,假设100Nmm,查由
34、表2110-3查得,查表10-2查得使用安全系数21查表10-4查得7级精度,小齿轮相对支撑非对称布置时21代入数据后由 查图2110-13得故载荷系数 .按实际载荷系数校正所算得的分度圆直径m.计算模数mm.按齿根弯曲强度设计由弯曲强度的设计公式为 (4-4)确定系数. 查图10-20C查得小齿轮的弯曲疲劳强度极限 MPa,大齿轮的弯曲疲劳强度极限 MPa21. 查图10-18查得弯曲疲劳寿命系数、21.计算弯曲疲劳许用应力取弯曲疲劳系数MPa MPa.计算载荷系数 =.查取齿形系数由表2110-5查得 . 查取齿形系数由表2110-5查得 .计算大小齿轮的并加以比较. 按齿根弯曲强度设计计
35、算由公式(4-4)mm对比计算结果,由齿面接触疲劳强度计算的模数大于由齿根弯曲疲劳强度计算的模数,由于齿轮模数的大小主要取决于弯曲强度所决定的承载能力,而齿面接触疲劳强度所决定的承载能力,反与齿轮直径(即模数和齿数的乘积)有关,可取弯曲强度算得的模数3.33mm进行圆整为标准的值mm,按接触强度算得的分度圆直径算出小齿轮齿数通过圆整后取大齿轮齿数 ,取这样设计出的齿轮传动既满足了齿面接触疲劳强度,又满足了齿根弯曲疲劳强度,并做到结构紧凑,避免浪费。.几何尺寸计算. 计算分度圆直径mm. 计算中心距m计算齿轮宽度m取m m.验算N Nm100000 Nm由验算可知符合要求。4.2.2曲轴设计 曲
36、轴是把原动机的旋转运动转化为柱塞往复运动的重要部件之一。工作时,它为承受周期性的交变载荷,产生交变的扭转应力和弯曲应力。1.曲轴的结构特点和选择对于乳化液泵采用两支承三曲拐曲轴型式,这种型式的曲轴因具支承少,使曲轴和机体的加式量减少,传动端装配也简单。相反的,因曲柄错角为120o的三拐二支承曲轴不能简化成平面曲轴,故受力状况复杂,刚度和强度较差,在同等条件下就显得粗笨。曲轴典型结构及各个部位.轴端轴心线与曲轴旋转中心同心的轴向端部叫轴端。曲轴通常有两端,轴的外伸端叫前端。因前端一般均与原动机或机泵外减速机相连接,并作为总扭矩的输入端,故前端也叫输入端。相对的另一端叫后端,也叫尾端。.轴颈轴颈包
37、括主轴颈,支承轴颈和曲柄销。主轴颈系指轴端上安装主轴承或曲轴支承中间轴承上的部位。显然支承轴颈须与主轴颈同轴心。曲柄销是指曲轴上与连杆大头连接的部位(也叫连杆轴颈),它与主轴颈不同心。.曲拐,曲柄,曲柄半径曲轴上连接主轴和曲柄销或连接两相邻曲柄销的部位叫做曲柄,前者又称为短臂,后者又称为长臂。曲柄与曲柄销的组合体称为曲拐,靠近主轴颈的曲拐较短又叫短拐。连接两曲柄销的拐较长,又叫长拐。由主轴颈中心(亦即旋轴中心)到任意曲柄销中心的距离称为曲柄半径。曲拐布置或曲柄错角选定曲轴的拐数和曲轴柄错角主要取决于泵的型式,联数和作用数的选择。曲柄错角的选择还应考虑有利于减小流量不均匀度,惯性力和惯性力矩的平
38、衡并有利于两主轴颈处挠曲交形相接近,对于三联单作用泵取曲柄错角为120o(各错角均等),而且若以靠近曲轴输入端为第一曲柄,并以它为基准,顺旋转方向计算时,第二曲柄与第一曲柄间的错角取为240o,第三曲柄与第一曲柄的错角则取为120o。这样才有利于主轴颈处的交形(倾角)接近。特别轴前端主轴颈外伸部位有附加力矩时,更是如此。曲轴支承和轴承选择对于二支承三拐曲轴的刚度较差,主轴承处的主轴颈变形倾角较大,故主轴承多采用允许倾角较大的向心球轴承而很少采用滑动轴承。.轴颈铸造曲轴则因铸造工艺能够获得较为复杂的形状,故轴颈可采用空心结构。内孔径约为外圆直径的2/51/5,空心结构可以减轻曲轴重量,降低材料应
39、力集中,使应力分布均匀,有利于提高曲轴的疲劳强度(一般空心比实心轴可提高疲劳强度约50%)。.曲柄采用椭圆形的曲柄,材料利用最合理,疲劳强度高。但对自由锻造曲轴,曲柄外形需靠模加工成型。.过渡圆角泵工作时,轴颈与曲柄连接处最容易形成应力集中,而导致曲轴早期破坏,因此在此处应取圆滑过渡的圆角以提高曲轴的疲劳强度。.油孔曲轴轴颈一般采用有压润滑油强迫润滑和冷却,为此曲轴内应有油孔作为润滑油的通道。曲轴主油孔(轴向)直径一般取(0.070.08)(其中为曲柄销直径)。但最小不应小于0.004m。曲柄销上的径向油孔直径比主轴孔直径略小,一般取0.05。其出口与轴颈表面相贯处,应倒圆、抛光,以避免此处应
40、力集中和降低曲轴疲劳强度。倒圆的圆角半径约为油孔直径的一半。.轴端轴端常见的形状是:前端多为圆柱体或圆锥体。后端多为圆柱体。圆柱轴端加工方便,但拆装较困难。圆锥轴端便于拆装,但加工较麻烦,锥面锥度一般取1:10也可取1:15或1:20。因前端为总扭矩输入端,故前端多有键槽以备安装键来传递扭矩。.轴封轴前端为外伸端,为防止润滑油由外伸处泄漏,在相应的机体处应设轴封,最常用的轴封是橡胶轴封和毛毡轴封。2.曲轴结构设计 图4-4 曲轴1. 曲轴销直径确定图4-5 曲柄销直径的尺寸曲拐轴的曲柄销直径D(图4-5)22可按经验公式初步确定 10m (4-5)式中 P最大柱塞力,t (柱塞力)对于二支承三
41、拐曲轴系数应取偏大值由公式(4-5)m通过圆整后取m.主轴颈m一般曲拐主轴颈变形倾角最大,故考虑到主轴承倾角允许值且应根据主轴承内径进行圆整,此外,当确定主轴颈尺寸时,还应顾及到轴颈重叠度,应尽可能避免等于零或接近于零甚至于小于零的情况(见图4-6)22图4-6 曲拐主轴颈尺寸 1. 轴颈长度轴颈长度还应满足曲柄销问题(即液缸中间距)a的要求 (4-6)式中 曲柄厚度,10m 曲柄两侧台肩厚度, 10m曲柄厚度m式中 曲柄销直径, 10m.曲柄宽度m式中 曲柄销直径, 10m.曲柄半径m.核算轴颈重叠度相邻两曲柄销处 式中 曲柄销直径, 10m主轴颈与曲柄销处 .连杆大头轴瓦宽度m式中 曲柄销
42、直径, 10m.曲柄长度m.曲柄厚度长臂 m 取m短臂取m.曲柄宽 m式中 曲柄销直径, 10m.校核液缸中心距由公式(4-6)m式中 曲柄长度,10m 曲柄厚度, 10m长臂曲柄厚度,10m3.曲轴受力分析作用在两支点三拐曲轴上的力有:作用在曲柄销中点的集中力切向力和径向力的作用在主轴颈上的支反力;作用在输入端主轴颈上的总扭矩。4.曲轴外力计算图4-7 作用在曲轴销上的外力切向力,径向力,支反力及轴前端载荷均是作用在曲轴上的外力,总的输入扭矩则是作用在曲轴上的外力矩。这些力和力矩都是曲柄转角的函数。对于三联单作用泵在统一瞬间,作用在各曲轴销上的力方向不同,若设第一曲柄转角,则第二曲柄转角为第
43、三转角。当三联泵任一柱塞处于吸程阶段0180时,其活塞力,当任一柱塞处于排程阶段180360其柱塞力且是一常量,当任意柱塞处于前、后死点或,不考虑运动副的间隙)柱塞力将有一突变或由突增到或相反。 图4-8 作用在主轴颈上的外力,和力矩表4-1两支点三拐曲轴外力(力矩) 22 作用 力名称符号作用点计算公式往复惯性力十字头销中点旋转惯性力曲柄销活塞力活塞端当当综合活塞力十字头销中点连杆力沿连杆中心线径向力曲柄销中点切向力曲柄销中点输入扭矩输入销主轴颈(阻力矩)轴前端A点的支反力轴前端主轴颈中点轴尾端B点的支反力轴尾端主轴颈中点支反力在垂直于轴曲柄中线方向的投影轴前端主轴颈中点轴尾端主轴颈中点1.
44、 往复惯性力式中 每联往复运动部分质量,10Nsm 曲柄半径 m 曲柄角速度rads 曲柄半径与连杆长之比 曲柄转角 rad 在泵的初步计算时最大往复运动部分的质量可按最大活塞力估计: (4-7)式中 最大柱塞力,10N 柱塞直径, 10m 泵的最大排出压力,10N/m由公式(4-7)当 =321.428 =-160.714 =-160.7142. 旋转惯性力式中 转化到曲柄销中心的曲拐不平衡质量, 10Nsm连杆质量, 10Nsm 转化成往复运动质量的系数,一般为K=0.30.4.对高速泵取小值对低速或中速泵取大值。式中 材料重度 , 10N/m 取 (10Nsm)在液缸内液体压力的作用下,
45、对活塞端和缸盖则产生大小相等,方向相反的力P。称为柱塞力P: (4-8)式中 柱塞的截面积 10m 液缸内液体的压力,在实际计算时可用泵的最大排出压力代替由公式(4-8) =1905.753. 活塞受拉为正 4. 综合柱塞力式中 活塞力,10N 往复惯性力,10N 摩擦力, 10N一般情况下因与活塞比较,摩擦力很小可以略去。 5. 连杆活塞力查表(4-4)可知22 =-2098.167 =163.17966. 径向力通过查表4-622 =-105.322 =2847.634 =1372.567. 切向力通过查表4-522 8. 输入扭矩通过查表5-6两支点三拐曲轴可知22 4931 6379
46、-1096 -3721.8 4818.4 601.26 5223.86 -5825.125.曲轴强度校核由于曲轴承受交变载荷,其破坏形式多半是由疲劳引起的,因此,在通常情况下,应按疲劳强度校核,但在实际计算过程中为了简化计算过程,往往把曲柄所受载荷看成是内应力幅等于最大内应力的对称循环载荷。略去应力集中和尺寸系数对计算结果的影响而代之以选用较大的安全系数,这样一来,就可使复杂的疲劳强度校核具有静强度校核的简单形式,即用静强度校核代替疲劳强度校核。1. 静强度校核静强度校核时,首先要判定曲轴可能产生最大内应力的截面(危险截面)及其相应的曲柄转角相位(危险相位),对于三联单作用泵,因为有三个曲柄转
47、角相错120的柱塞在工作,上述位置并不包括一切可能产生最大内力的相位,一般讲应该至少每隔,求出一系列的曲柄外力和需要截面的内力,从中寻找最大值,从而来确定危险相位,显然,这一计算过程是相当烦琐的。此外,由查表5-7计算22所求得的、,的单向最大值,还不能全面反映对应截面的合成效果,而且按某一强度理论进行合成时,截面的实际应力还应与截面形状尺寸有关,也就是说,内力最大的截面,未必是内应力最大的截面。对两支点三拐曲轴,按表5-6,5-722顺序进行详细计算并且假定表5-722那23个截面都具有直径相同的圆形截面的断面模数下,求出三个的矢量,和分别求出了对应的、以及矢量和的相位角这一计算结果表明:.
48、所有轴颈两端主轴颈和各曲柄销各截面的矢量和最大值() 均在,时产生,这正是各轴颈产生最大内力的危险相位。.在假定各轴颈截面尺寸相同情况下,在第曲柄销中点(截面12)截面最大,其次是截面13处,再次是截面6和19,截面6和9最大内力数值上大体相同实际上只校核6和12两个截面就可以了。短臂曲柄截面2虽然内力和较小,但截面尺寸也小,因此也不能忽略。实际计算表明,对应内力矢量和最大的危险相位角是:对截面9为对截面16为对截面2为总上所述,对于两支点三拐曲轴静强度校核截面通常可在下述几个截面中选取,即危险截面: 图4-9 两支点三拐曲轴的计算截面的选取.第二曲柄销中点,相应查表5-7中的截面1222,对
49、应的危险相位是、。.长拐的两个长臂中点,相应查表5-7中截面9和1622,但因两截面应力值相近,只校核一个就够了。.输入端主轴颈的根部(与曲柄1相接处),此处内力比第曲柄销中心小,但因直径尺寸也小,因此要校核,如果此处直径与曲柄直径相接近,可不必校核。.接近输入端主轴颈的第一曲轴的轴颈重叠处,此处内力小于长臂中点截面的内力,但因此处曲柄较薄,也应校核,如果此处曲柄厚度与长臂曲柄厚度接近且重叠度较大时可略去。不论轴颈或曲柄截面,静强度校核的公式: (4-9)式中 曲轴材料的对称弯曲疲劳强度,10N/m。当曲轴材料为40或45号钢时,10N/m 危险截面上危险点的正应力,10N/m 危险截面上危险
50、点的切应力,10N/m 计算的安全系数 许用安全系数,通常取=4.06.52. 危险截面应力计算危险截面危险点应力、的计算,可分为轴颈(圆形)截面和曲柄(非圆形)截面几种形式:. 轴颈截面应力计算两支点三拐曲轴颈上各截面应力计算有如下特点:没有轴向力(,查表5-7)22绕Z轴和绕y轴的抗弯断面模数相等且与绕X轴的抗扭断面模数存在这样的关系:查表(5-8)22表4-2 曲轴常用断面几何特性计算公式截面形状公式面积A(10m)抗弯断面惯性距(m)抗弯断面模数(10m)抗扭断面惯性矩( 10m)抗扭断面模数(10 m)形心至断面边缘距离(10m) 10N/m (4-10)式中 、分别是校核截面绕轴绕
51、轴的弯矩和绕轴的扭矩,10N/m、分别是校核截面绕轴的抗弯断面模数和绕 轴的抗扭断面模数。图4-10 曲轴强度校核截面的选取 轴颈截面的静强度校核 校核截面1-1,截面的位置垂直于输入端主轴颈主轴颈与曲柄相接处,危险相位角。材料的弯曲疲劳极限=25003400(45号钢)10N/m,许用安全系数,绕轴的扭矩,10N/m =46348.7绕轴弯矩,10N/m =10838.5绕轴弯矩,10N/m =10245.6抗弯断面模数,10m =2649.375计算安全系数 =60.54 校核截面1-1,截面的位置垂直于曲柄销中线,在曲柄销中点,危险相位角,材料的弯曲疲劳强度=25003400(45号钢)
52、10N/m,许用安全系数,绕轴的扭矩,10N.m =56427.8绕轴的弯矩,10N.m=381659.4绕轴弯矩,10N.m=298546.5抗弯断面模数,10m=2649.375计算安全系数=16.293由计算结果可知,均大于许用安全系数,符号条件。4.2.3连杆设计1.连杆结构型式特点连杆是传动端曲柄连杆机构中连接曲轴和滑块的部件,连杆的运动是一平面运动。可以把连杆运动看成是沿液缸中心线移动和绕滑块摆动的两种简单的运动的合成。连杆与曲轴相连的一头称为大头,与滑块相连的一头称为小头。通常连杆由连杆体、连杆盖、大头轴瓦、小头衬套以及连杆螺栓、连杆螺母等所组成1. 连杆体杆体截面形状有圆形,工
53、字形,矩形和十字形几种形式。圆形截面杆体最容易机加工,但在获得同样强度和刚度的条件下,其金属利用率低,该型式主要用于低速,大型和小批生产的连杆。工字形截面的杆体和其他形状截面杆体相比较,在同样强度和刚度的条件下具有最小的运动量,但毛坯一般是铸成和模锻成的,该型适合于高速轻型和大批生产的连杆。矩形和十字形截面杆体的材料利用率大体上介于前述两者之间,毛坯一般为铸件,采用也十分广泛,所以通过比较选用工字形截面的杆体。1 大头轴瓦 2 连杆螺母 3 连杆盖 4 连杆螺栓 5 连杆体 6 小头衬套图十一 连杆结构.连杆大头因为往复泵多采用曲拐,为了便于拆装和对大头轴瓦间隙进行调整,连杆大头制成剖分式结构
54、,即连杆大头由连杆盖和连杆体所组成并用两只螺栓连结成一体。连杆螺栓承受交变载荷,螺母处应备有防松装置。常用的最佳防松方式:冠形螺母加开口销,也有的在螺母下加止动弹簧垫圈。大多数连杆的剖分式大头均采用连杆螺栓连接,一旦螺栓拉断,可保护杆体不致报废,但也有少数连杆采用螺钉连接,即把螺钉直接旋入杆体大头处的螺孔内,连接连杆盖。这种连接可使杆体不必像螺栓连接那样在杆体大头背部划一平窝,从而减小杆体工作时的应力集中。为了保证连杆盖与杆体的装配位置不变,在两者间设有定位销钉,定位套筒或具有定位凸颈的连杆螺栓。.连杆小头连杆小头均制成整体式,小头形状有圆形,偏心圆和球形等不同形式,对于此次设计采用圆形,小头
55、与滑块连接方式为球面整体式连接。2.连杆的结构设计.一般设计要求.连杆应具有足够的刚度和强度,工作时不致破坏或弯曲变形。.大、小头结构合理,适合装配有足够承载能力的轴瓦或轴承。.在满足上述条件下,应尽可能选取合理的外形、截面尺寸、减轻重量,即可减少运动质量也有利于加工制造和拆装。.连杆定位连杆定位是用来限制连杆在工作时垂直于连杆体中心线方向的窜动的,定位方式可分为大头定位和小头定位两种。大头采用厚壁轴瓦或小头采用球面连接时,适合于大头定位,大头采用薄壁瓦时,因没有翻边,故不适合大头定位,特别是大头为闭式结构,内装滚动轴承时,不便于大头定位,多采用小头定位。这里采用小头定位,用小头定位时,以小头衬套端面作为定位面,通过该端面与小头体两侧配合端面之间的间隙来
- 温馨提示:
1: 本站所有资源如无特殊说明,都需要本地电脑安装OFFICE2007和PDF阅读器。图纸软件为CAD,CAXA,PROE,UG,SolidWorks等.压缩文件请下载最新的WinRAR软件解压。
2: 本站的文档不包含任何第三方提供的附件图纸等,如果需要附件,请联系上传者。文件的所有权益归上传用户所有。
3.本站RAR压缩包中若带图纸,网页内容里面会有图纸预览,若没有图纸预览就没有图纸。
4. 未经权益所有人同意不得将文件中的内容挪作商业或盈利用途。
5. 装配图网仅提供信息存储空间,仅对用户上传内容的表现方式做保护处理,对用户上传分享的文档内容本身不做任何修改或编辑,并不能对任何下载内容负责。
6. 下载文件中如有侵权或不适当内容,请与我们联系,我们立即纠正。
7. 本站不保证下载资源的准确性、安全性和完整性, 同时也不承担用户因使用这些下载资源对自己和他人造成任何形式的伤害或损失。
最新文档
- 人教版初中生物第1章第1节生物的特征课件
- 人教版初中生物中考复习第三单元第三章绿色植物与课件_002
- 信道编码10-15上课课件
- 缺血性脑卒中--从急性期到二级预防课件
- 信道定义及数学模型课件
- 线虫概论蛔虫鞭虫课件
- 组织学与胚胎学-07神经组织课件
- 人教版初中物理新旧教材对比资料课件
- 组织学与胚胎学-09Th 皮肤课件
- 人教版初中生物七年级上册-开花和结果课件
- 人教版初中生物七上第一单元第一章第1节《生物的特征》-课件
- 人教版初中生物七上第一单元第二章第1节《生物与环境的关系》-课件
- 癌痛的护理(专科护士培训)图文课件
- 组织学与胚胎学-08神经系统课件
- 人教版初中生物中考复习第三单元第三章绿色植物与1课件