引线片冲压工艺及级进模具设计说明书
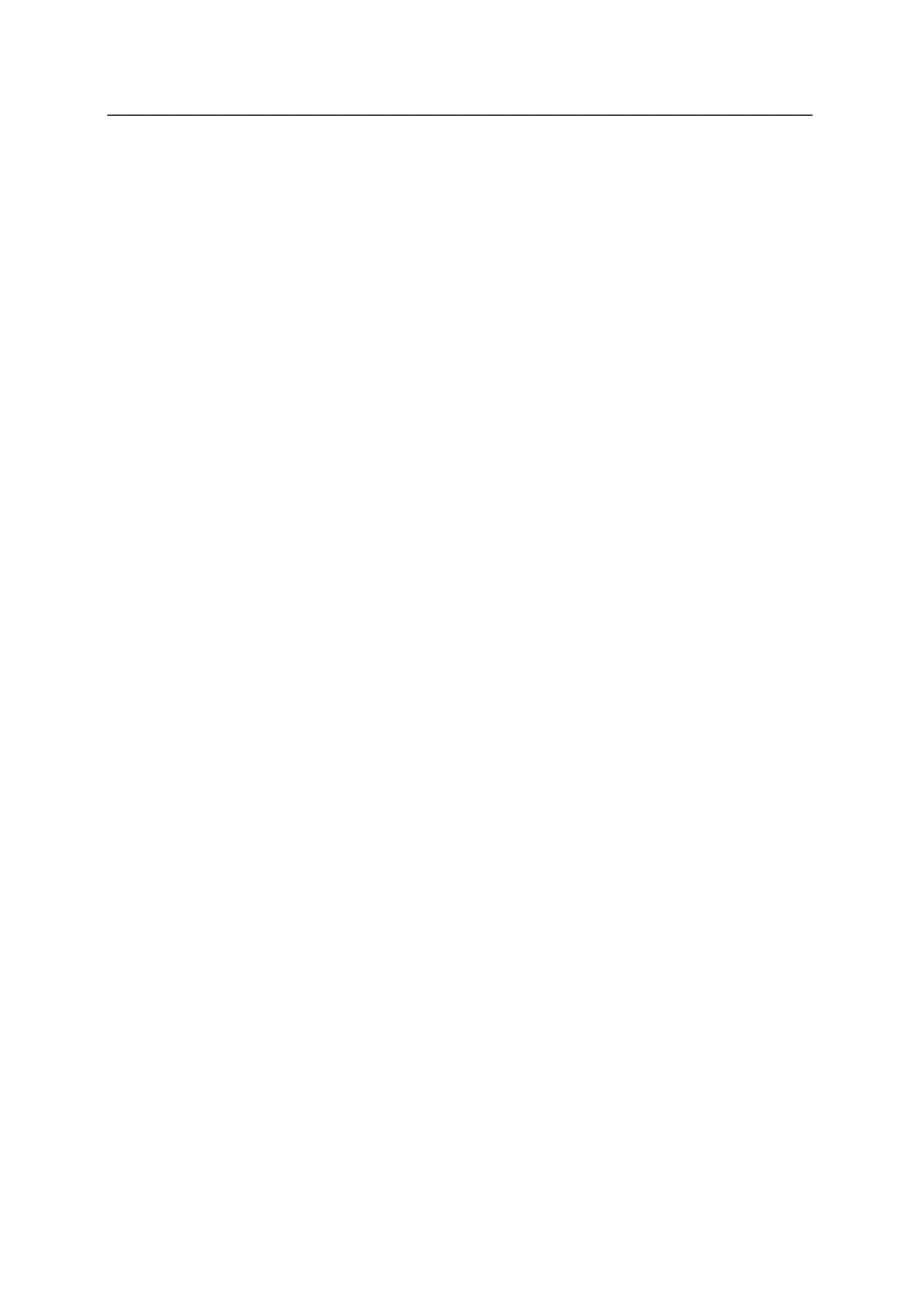


《引线片冲压工艺及级进模具设计说明书》由会员分享,可在线阅读,更多相关《引线片冲压工艺及级进模具设计说明书(45页珍藏版)》请在装配图网上搜索。
1、摘要本课题作为本次的毕业设计,属于在校期间最后的一次针对模具进行设计,本课题的主要工作是完成压圈垫片的设计,结合分析能够得知,要求降低材料损耗节约成本,就要求采用2道单独工序完成成产,引线片是汽车中十分关键的零件,通过和滑轨配合,从而得到垫片零件。本课题主要是针对该零件进一步进行优化设计,从而达到新的生产要求。最初制定的是通过2副单工序模具来实现产品加工,不过因为大部分模具因为存在精度偏低的问题,导致最后产品品质不佳,并且生产效率不高。本课题针对此问题决定对生产优化,改善产品品质同时提升产率。在设计开始之前,本人调研大量资料文献以及书籍,在理论作为基础的背景下以严谨态度来对相设计进行计算,同时
2、和专业工程师交流,最后设计得到本课题中的连续模结构。目前这种结构市场占有少,同时加工难度大,其中同时集成多道加工工序过程成为一个整体的模具,因此在设计的时候要求充分考虑不同工序的顺序关系,以此为基础来保障最后产品尺寸达到精度要求。为加快工件生产速率,因此采用了自动送料机构,取代传统人工送料方式,让其具备很高生产速率。除此以外,对于制件而言,外观同样很关键,因此设计中要求平面要求光滑平整,同时对模具设计,尽可能选取标准零件,让获取也更加容易 。本本课题的设计中,借助于完善的CAD/CAM技术实现辅助设计,可以确保模具最后能够得到足够精度的前提下,极大程度缩减典型计算模式中繁琐求解流程,让设计工作
3、更容易实现。不难得知对于高、精、尖的模具展开设计,未来借助于CAD/CAE/CAM技术来完成辅助工作也是未来的趋势。关键词:模具;CAD/CAE/CAM技术;引线片AbstractThis topic as the graduation design, belong to the school during the last for mould design, this topics main job is to complete the design of the clamping ring gasket, combining with the analysis can know, cost
4、 savings to reduce material loss and will require the use of two separate procedures to complete, compression ring gasket are critical parts of the car, through and slippery course, clamping ring gasket parts is obtained. This topic is to further optimize the design of this part, so as to meet the n
5、ew production requirements. Initially, two sets of single working procedure molds were developed to realize product processing. However, due to the low accuracy of most molds, the final product quality was not good and the production efficiency was not high. Aiming at this problem, this subject deci
6、des to optimize the production, improve the product quality and improve the production rate at the same time.Before the design began, I investigated a large number of materials, literature and books, calculated the phase design with a rigorous attitude under the background of theory as the basis, an
7、d communicated with professional engineers. Finally, I designed the composite mold structure in this project. At present, this structure has a small market share and is difficult to process at the same time. Among them, multiple processing processes are integrated into a whole mold at the same time.
8、 Therefore, it is required to fully consider the sequence relationship of different processes in the design, so as to guarantee the final product size to meet the accuracy requirements based on this.In order to speed up the workpiece production rate, the automatic feeding mechanism is adopted to rep
9、lace the traditional manual feeding method, so that it has a high production rate. In addition, for the parts, the appearance is also very important, so the design requires the plane to be smooth and flat, at the same time for the mold design, as far as possible to select standard parts, so that it
10、is easier to obtain. thisIn the design of this topic, with the help of the perfect CAD/CAM technology to realize the auxiliary design, it can ensure that the mold can finally get enough accuracy under the premise, greatly reduce the tedious solution process in the typical calculation mode, so that t
11、he design work is easier to achieve. It is not difficult to know that the CAD/CAE/CAM technology is also the future trend to complete the auxiliary work for the design of high, fine and pointed molds.Key words: mold; CAD/CAE/CAM technology; ring gasketIII目录摘要IAbstractII前言2绪论3第一章 零件的工艺性分析6第二章 零件工艺方案的
12、拟定7第三章 排样设计及材料利用率计算9第四章 冲压力计算及初步确定压力机13第五章 模具压力中心的计算15第六章 模具刃口尺寸及其公差的确定17第七章 模具工作零件的结构设计22第八章 模具标准件的选取27第九章 模具其他非标零件的设计与选取30第十章 模具冲压设备的校核31设计总结33参考文献34致谢35前言在当前的发展浪潮中,模具设计制造早就已经是正在盛行的一个产业。未来的模具技术发展趋势也是集中于高、精、尖的方向不断推进,从而在模具产品技术含量日益提升的同时,还能够减少加工周期,并且不断往无人值守、智能信息化、全面化、电子设计化以及自动化的方向推进,在将来这一领域内,技术将进一步集成、
13、设备也会变得更加先进、产品也要逐步开始品牌化、对于管理也要推行信息化管理,并且经营范围也要往国家化方向拓展。对于整个模具制造内,其中超过50%的产值是通过冷冲模设计制造所贡献的。冲压技术在当前属于先进性高,并且切削量少甚至没有的一种加工工艺,优势在于加工速率快、成本低廉、对于材料也有较高的利用率,并且得到产品的精度也很稳定。能够很方便的就实现对工件轻量化处理,并且操作容易实现,也能够很方便的完成自动化与机械设备融合,目前在实际生产内的应用十分多。对于冲压模具内,升级于普通模的复合模在精度上更高,并且生产效率十分好,是当前应用最多模具之一,对于零件复杂,且要求大批量生产而言比较实用。对于复合模的
14、设计,其中关键之处在于毛坯排样,采用方案不同会得到不同材料利用率,同时还会影响到冲压加工过程的工艺性、模具自身的结构形式以及使用寿命等。结合相关数据证实,对于冲压件而言,其材料费用占总成本超过3/5。由此可知,排样的合理性,能够有效增强材料利用效率,同时缩减生产成本。作为制造的起源的设计工作,咋进行时必须全面分析模具结构,对如何提升产率要进行考虑,还有就是后期怎么维修方便。不过也不可以把责任都推到设计中,实际生产过程中,要求结合具体的问题来开展分析,结合实际状态针对模具采取一定调节也是被要求的。设计过程中,对于工艺分析而言,就是要求对设计的关键位置正确的进行引导。除此以外,对于生产而言,针对模
15、具开展的保养、维护也很关键。对于模具开展维修,要求关注很多细节点,从而排查原因所在,接着就是针对性维修。对于模具进行拆卸时,一定要认真细致,避免导致模具出现损伤,采取保养举措也能够在最大程度上提升模具的使用年限。绪论选题背景及意义本课题的来源是通过实习公司提供,然后由指导导师审核得以通过。在本课题中主要的工作是针对冲压模开展设计,意义在于以原有公司现有模具为基础,对其进行优化改进,从而增强产品品质,提高经济效益。上个世纪的中期,在国外对于模具以及相应工业就曾给予过十分高的评价,并美国将其比喻成美国工业的基石;日本则称之为推动社会走向繁荣昌盛的根本动力;德国则认为是金属加工中的王者;东欧则认为是
16、黄金一样重要。到了上世纪后期,我国才逐步意识模具在机械加工领域中的重要程度,并提出了模具工业为当代工业之母的理念。在本设计,制造业正在摆脱传统技术的机械,开始采用以信息化技术为基础的机械设备发展,也就是对传统工业采用信息化的相关技术进行升级和改造。随着经济体系走向全球一体化,市场也从原有国内走向全世界,导致生产商之间的竞争力度进一步扩大,这也要求厂商对于市场的需求做出快速的响应。如今柔性自动化技术以及相应设备也被急需。除此以外,在信息技术以及微电子技术日新月异、蓬勃发展的当下,给柔性自动化技术的发展奠定了坚实的基础,在这种背景下,工业装备逐步走向数控化、柔性化以及智能化。据统计,当前全球模具工
17、业做出的产值贡献就高达661亿美元,其中一半是由亚洲贡献的,而日本则是亚洲贡献最大的一个,年产值基本维持在了200亿美元。据统计美国的全年产值仅50亿美元,中国虽然是后来才发展起来,不过产值也超过了69亿美元。不过光看产值并不能够代表该国技术水准。我国虽然在模具领域中,无论是品种、数量或是在技术以及品质上都得到一定程度提升,不过和先进技术国家依旧存在较大的距离。因此在国内,对于一些品质要求高、使用年限要求久、结构相对复杂、大规模的一类高档次模具还是都依赖于从国外进口,比较突出的就是针对中高档轿车生产中所采用的覆盖件模具,基本都是通过从国外进口。除此以外技术含量不高的一些模具生产已经超过了市场的
18、需求,所以利润已经被压缩到极限。在最近的五年时间内,国内从国外进口的模具平均每年都要消耗11.2亿美元,这个价格还并没有将相关的附属设备计算在内。由此可见中国在模具市场还是存在较大发展空间,也由此可知本设计的意义重大。研究现状全球范围内,模具以及相应产业早已构建为1个行业,因此对其发展也有对应行政机构进行管理与指导。在日本就有“型技术协会”,在我国台湾也成立了“台湾模具工业同业公会”,国内更是成立了规模最大的“中国模具工业协会”,不用省市都有该协会的分会存在。现如今模具行业规模庞大,国内的相应公司就有几万家。近些年中,国内在冲压模具水平上有比较显著的提升。借助于大型冲压模具,已经能够完成单件设
19、备质量超过50t的模具的设计以及生产,同时具备了在中档轿车中相关配件所采用的覆盖件的生产模具还有多工级进模的加工。在精度上已经能够到达1到2m,使用寿命更是高达2亿次。表面粗糙度可以不超过1.5m、对于直径超过0.3m这种大尺寸厚板精虫模具在拥有的技术水平上已经十分高。国内在对于模具中应用CAD/CAM技术并持续发展超过20年。最早在1984年,由华科(早起为华中工学院)以及733厂合作,一起开发了精冲模的CAD/CAM系统的开发。在同期,上交针对该系统也成功研制。从本世纪开始,CAD/CAM技术已经逐步推广,如今,有一定生产能力的厂商,都具备该项技术,还有一些比较优秀的企业还掌握了CAE的技
20、能。国内目前针对汽车覆模件的模具生产商,基本都已经借助于CAD/CAM技术还有DL图相关技术完成对模具设计,并且已经逐步从二维开始向三位设计拓展,零件图已经逐步被总图取代。对于冲压成型CAE的软件,国内不仅仅只有国外的软件,在国内华科、湖大以及吉林大学相继开发出了具有相对高性能,并具备自主姿势产权的相关设计软件,而且已经在实际应用中得到了相应的印证,能过获取相对多高的效益。RP(即快速原型)典型经济模具的应用,进一步提升了对大型汽车中覆盖件加工采用模具的生产,能够有效消除对于低熔点合金模具内只能够借助于样件浇铸的模式来生产模具,导致最终模具精度不高、零件加工精度偏低并且制造业麻烦的缺陷,达到了
21、借助于三维建模软件完成模具快速的加工生产。这也意味着在汽车大型覆盖件模具的加工中应用RPM应用实现。本课题对全球针对模具的研究现状从多个角度分析,从而明确本课题研究的意义所在,从而开着本课题工作。5第一章 零件的工艺性分析图1.1 产品图产品的名称:引线片工件图:如图1.1;产品的材料:A3;产品的材料厚度:1.5mm;精度等级:未注零件尺寸公差按照IT14级选取。工件表面质量:工件表面无毛刺、压痕、拉裂、油污等不良现象1.1 产品材料分析材料名称:普通碳素钢;材料牌号:A3;材料状态:未退火;抗剪强度:304-373Mpa;抗拉强度:432-461Mpa;屈服点:235Mpa;伸长率:21-
22、25%1.2 工件结构形状分析工件外形通过冲压这种工艺手段所满足的工艺性主要有:本课题针对工件采用的冲压成型制备,最后可以得到一个满足尺寸要求的零件,借助于直线以及圆弧结构一起组成垫片结构外形,因此在整体结构上繁琐性不强,程度适中,因此借助于普通的冲压工艺,就可以十分方便的实现对该零件的加工。参照图1.1,可以发现工件中的孔都相对大,结合相关文献资料可以确定:不存在保护装置时,冲裁件冲圆孔的最小直径时,最小孔尺寸为1t,因为原材料在厚度上仅1.5mm。可以确定冲裁件中圆孔的最小直径大小是1.5mm。通过分析可以确定,对于工件采取冲孔可以达到最终需求。对于孔边距也提出要求,必须不能够底与1.5t
23、;由此可确定,工件能够满足最终需求。针对模具进行设计,必须全面分析工件需要满足的精度,精度不同,工件采取的加工设备的模具也不一样。比如在线切割内走丝有快中慢三种模式。因为本课题设计对象在精度上没有太高要求,并且也没有将公差标注,这种情况通常采用公差等级属于IT14。如果表面粗糙度也没有标注,通常采用等级为Ra6.3。第二章 零件工艺方案的拟定2.1 冲裁工艺方法的选择冲裁工序分为单工序冲裁、复合冲裁和级进冲裁三种工序的性能。(1)根据生产批量来确定,一般来说和试样生产采用单工序模具,中、大批量生产采用复合模具或级进模具。(2)根据冲裁件的尺寸精度等级来确定,复合模具冲裁裁件尺寸精度等级较高,避
24、免了多次单工序的定位误差,并且在冲裁过程中可以进行压料,冲裁件比较平整。(3)根据工件的结构的复杂程度,生产批量,模具的性能,级进模具可以将复杂多工艺的工件在一副模具上分步完成,避免了多单工序定位和模具设计的周转,且模具运行速度快、生产效率高,但模具结构比较复杂设计和制造周期长。对于安装垫片采取冲压成型工艺时,结合其零件图进行研究与分析,对于其加工,需要加工手段主要是冲孔、落料2种冲压方式。在本课题内制定了3套工序方案,分别是:第一套方案:单工序生产,也就是三个成型案都是独立。所采用冲压模具在结构上也是相对简单,对其加工生产所需时间周期也不长,在制造难度上也不高,但是在本设计内针对加强支架工件
25、生产,要求配置2套冲压模具,这就带来了模具成本的提升,无法满足本课题中针对零件采用大批量生产方式的相关要求。第二套方案:落料冲孔复合模,这套方案优势在于具备较高加工效率,并且可获取相对高精度,成本也不是很高。第三套方案:落料冲孔级进生产方案这套方案中是借助连续生产模式完成加工,一般针对的为大批量零件生产,因此仅用1副模具就够,在加工效率上相对快,不过产品在精度上就相对一般,并且对其设计、加工以及后期的维护都相对困难,尤其是架起模具的时候,通常耗费很多时间来对其实现调整,一般使用都是和送料机配套使用。对比上述三种方案,如果选用第一套方案以实际生产作为参考依据,第三套方案最合适,能够达到大批量生产
26、需求。如果从成本以及要求大批量生产角度考虑,采用级进模完成前期的设计以及加工,在后续维护的时候,成本就会相对高。如果采用的为第二套方案,在设计以及制造上难度不是很大,并且降低人工成本投入。对于第二套方案,相比前两种精度是最好的。而第一套方案一般适合小批量生产,精度也相对较低。为了满足客户大批量生产的要求,在本课题内最终选用的还是级进模模完成生产,即采用方案3。本课题设计的产品有最开始的平板原料到成品,其中采用工序有好几道,对这几道工序要求按一定次序排序才能够加工得到满足质量需求的产品,接下来针对性计算。第三章 排样设计及材料利用率计算3.1 排样方式的选择与设计冲裁件在板料、带料或条料上的布置
27、方法称为排样。排样的意义在于减小材料消耗、提高生产率和延长模具寿命,排样是否合理将影响到材料的合理利用、冲件质量、生产率、模具结构与寿命。排样的方法有:直排、斜排、对直排、混合排 ,根据设计模具制件的形状、厚度、材料等方面全面考虑。因此考虑以下三种方案:方案一:有废料排样 沿冲件外形冲裁,在冲件周边都留有搭边。冲件尺寸完全由冲模来保证,因此冲件精度高,模具寿命高,但材料利用率低。方案二:少废料排样 因受剪切条料和定位误差的影响,冲件质量差,模具寿命较方案一低,但材料利用率稍高,冲模结构简单。方案三:无废料排样 冲件的质量、尺寸精度、模具寿命更低一些,但材料利用率最高。综合工件形状结构,考虑排样
28、条料的强度,模具寿命和尺寸精度,决定采用有废料的排样方案。图3.1 排样图3.2 搭边值的确定如表3-1所示:根据工件外形,结合工件材料厚度为1.5mm,a的最小值取1mm,a1最小值取1.8mm。参照本课题内对于安装垫片所采用的冲压成型工艺的真实状况而言,在考虑多种因素以后,最后确定条料彼此所存在的搭边值a的大小是1mm,因此可以选用侧搭边结构的方式完成设计任务,因为需要结合经济型的先关要求,在达到使用要求的条件下,要求尽量缩减在采取冲压成型工艺进行加工时,消耗的成本,最终就可以确定,搭边值a1的取值是1.8mm,通过这个设计可确保冲压模具的凹模在强度上达到要求,还可以确保在加工过程能够顺利
29、实现,表3-1 搭边a和a1数值 (mm) 材料厚度圆件及r2t的圆角矩形件边长L50mm矩形件边长L50mm或圆角r2taa1aa1aa10.250.250.50.50.80.81.21.21.61.62.02.02.52.53.03.03.51.81.21.00.81.01.21.51.82.22.01.51.21.01.21.51.82.22.52.21.81.51.21.51.82.02.22.52.52.01.81.51.82.52.22.52.82.82.21.81.51.82.02.22.52.83.02.52.01.82.02.22.52.83.23.3 材料利用率的计算根据模
30、具的结构不同,可分为有侧压装置的模具和无侧压装置的模具,侧压装置的作用是用于压紧送进模具的条料(从料带侧面压紧),使条料不至于侧向窜动,以利于稳定地加工生产。侧压装置适用于工件材料厚度较小,精度较高的自动模具。在这次的模具设计中,采用的是无侧压的导向装置。故按公式3-1计算: B=(Dmax+2a1+C) (3-1) 式中:B-条料宽度; Dmax-条料宽度方向冲裁件的最大尺寸; a1-侧搭边值,可参考表3-1; -条料宽度的单向(负向)偏差,见表3-2; C-导料板与最宽条料之间的间隙,其最小值见表3-3。 表3-2 剪料公差及条料与导料板之间隙 (mm)条料宽度B/mm材料厚度t/mm01
31、12233550501001001501502202203000.40.50.70.80.50.60.70.80.90.70.80.91.01.10.91.01.11.21.3表3-3 有侧压装置和无侧压装置对照表 (mm)材料厚度t(mm)无侧压装置有侧压装置条料宽度B(mm)10010020020030010010000.50.511223340.50.50.50.50.50.50.5111111115555588888所以根据以上理论数据由公式3-1得出条料宽度为: B=(Dmax+2a1+C)=(18+21.8+0.8)-00.5mm=22.4-00.5mm3.1.2 材料利用率的计算
32、关于材料利用率,可用公式3-2表示: =A/BS100% (3-2)式中, A-一个步距内冲裁件的实际面;B-条料宽度; S-步距。由图3-1和公式3-2得: A=54.6mm2 =A/BS100% =54.6x2(22.4x14.9)100%32.6% 32 第四章 冲压力计算及初步确定压力机4.1 冲压力的计算 计算冲裁力是为了选择合适的压力机,设计模具和检验模具的强度,压力机的吨位必须大于所计算的冲裁力,以适宜冲裁的要求,普通平刃冲裁模,其冲裁力F一般可以按公式4-1计算:F=KtL (4-1) 式中, -材料抗剪强度(MPa); L-冲裁周边总长(mm); t-材料厚度(mm)。系数K
33、是考虑到冲裁模刃口的磨损,凸模与凹模间隙之波动(数值的变化或分布不均)润滑情况,材料力学性能与厚度公差的变化等因数而设置的安全系数K,一般取13。当查不到抗剪强度时,可以用抗拉强度b代替,而取K取1.3的近似计算法计算。 冲裁力由公式5-1得: F冲=KtL =1.31.578.8350 =53.8KN4.1.2 卸料力计算当上模完成一次冲裁后,冲入凹模内的制件或废料因弹性扩张而梗塞在凹模内,或因弹性收缩而会紧箍在凸模上。为了使冲裁工作连续,操作方便,必须将套在凸模上的材料卸下,从凸模上刮下材料所需的力,称为卸料力;在上模中,将冲裁完成的冲裁件从凹模中推出的力称为推件力,卸料力、推件力计算公式
34、如下: F卸= K卸 F冲 (4-2)F卸= K卸 F冲 (4-3)式中, F卸-卸料力;F推-推件力;F冲-冲裁力;K卸、K推-卸料力、推件力系数,通过查文献1,表3-8即下表4-1获得;表4-1 卸料力、推件力和顶件力系数 (mm)料厚/mmK卸K推K顶钢0.10.10.50.52.52.56.56.50.0650.0750.0450.0550.040.050.030.040.020.020.10.0630.0550.0450.0250.140.080.060.050.03 卸料力系数、推件力系数通过查表5-1确定,由公式4-2、4-3得: F卸= K卸 F冲 =0.0553.8 2.7K
35、NF推= K推 F冲 =0.05553.8 3.0KN4.3 压力机的初选压力机可分为机械式和液压式,机械式分为摩擦压力机、曲柄压力机、高速冲床,液压式分为油压机、水压机,而在生产中一般常选用曲柄压力机,曲柄压力机分有开式和闭式两种,开式机身形状似英文字母C,其操作可见大,但机身刚度差,压力机在工作负荷作用下会产生变形,一般压力机吨位不超过2000KW。闭式机左右两侧封闭,操作不方便,但机身刚度好,压力机精度高。考虑到经济性能、加工要求和操作方便在此选开式压力机。由于冲裁模具采用弹压卸料装置,故总的冲压力包括: F= F冲+F卸+F推 =53.8+2.7+3.0 =59.4KN根据总冲压力数据
36、,这里初选压力机,初选压力机为J23-6.3型压力机。第五章 模具压力中心的计算5.1 压力中心的计算 对零件采取冲裁来成型时,在冲压模的凹凸模中的刃口出,承载的力相对复杂,力的类型比较多,将其汇总成合力,所处位置就是冲压模具的压力中心。为确保冲压模具使用状态下,能够具备较好力平衡状体,因此就要求参照模具自身的结构以及工件结构来开展分析,从而确定压力中心的合适点,这样才能够最大程度保证和模柄的中心位置是重叠,这样才能够确保模具使用中能够正常顺利,防止因为受力不均带来的相关机构以及部件出现了磨损,进而缩短模具的使用年限。对于压力中心确定原则主要如下:1、 当采用冲压成型加工时,其中采用冲裁件在结
37、构上呈现对称分布,则压力中心是取得为冲裁件几何中心。2、 当采用冲压成型加工时,其中采用冲裁件在结构上呈现对称分布,则压力中心是要求和冲裁件几何中心重叠。 (5-1 ) (5-2)上:X0:对应的为; Y0:对应的为; F:对应的为; X:对应的为;Y:对应的为。3、CAD确定冲模压力中心。AUTOcad是一种通用绘图软件,不是专门的模具设计软件,因此不能直接用于确定模具压力中心,但是这款软件具有查询封闭区域质心的功能,可通过分析和图形转换,扩展计算机的这一功能,就可间接确定冲模的压力中心。根据料带的排布建立以下坐标示意图,具体如下图5.1所示:由于工件形状相同且分布位置不对称,这里我们选择用
38、第四种办法来快速计算模具的压力中心,具体结果如下图所示。第六章 模具刃口尺寸及其公差的确定冲裁件的尺寸精度主要决定于模具的刃口尺寸精度,模具的合理间隙值也要靠模具刃口尺寸及制造精度来保证。正确确定模具刃口尺寸及其制造公差,是设计冲裁模主要任务之一。6.1 冲裁部分间隙的确定设计模具时一定要选择合理的间隙,以保证冲裁件的断面质量、尺寸精度满足产品的要求,所需冲裁力小、模具寿命高,但分别从质量,冲裁力、模具寿命等方面的要求确定的合理间隙并不是同一个数值,只是彼此接近。考虑到制造中的偏差及使用中的磨损、生产中通常只选择一个适当的范围作为合理间隙,只要间隙在这个范围内,就可以冲出良好的制件,这个范围的
39、最小值称为最小合理间隙Zmin,最大值称为最大合理间隙Zmax。考虑到模具在使用过程中的磨损使间隙增大,故设计与制造新模具时要采用最小合理间隙值Zmin。冲裁间隙的大小对冲裁件的断面质量有极其重要的影响,此外,冲裁间隙还影响模具寿命、卸料力、推件力、冲裁力和冲裁件的尺寸精度。较大的间隙可使凸模侧面及材料间的摩擦减小,并延缓间隙由于受到制造和装配精度的限制,虽然提高了模具寿命而,但出现间隙不均匀。因此,冲裁间隙是冲裁工艺与模具设计中的一个非常重要的工艺参数。 冲裁间隙是冲裁工艺与冲裁模具设计的一个重要工艺参数,对冲裁件质量、冲裁力和模具寿命均有很大的影响。冲裁间隙还影响着冲裁件的尺寸精度。冲裁件
40、的尺寸精度是指冲裁件的实际尺寸与基本尺寸的差值,差值越小,精度越高。间隙过大,会使落料件尺寸小于凸凹模尺寸,冲孔件尺寸大于凸模尺寸,冲裁力也会慢慢下降,卸料力、推件力或顶件力都将随之下降。间隙过小,会使落料件尺寸大于凸凹模尺寸,冲孔件尺寸小于凸模尺寸,冲裁力也会增大,会使模具刃口磨损加剧,还会产生凸凹模胀裂,小凸模折断,凸模和凸凹模相互啃刃等异常损坏。由此可见,我们在确定冲裁间隙时,一定要有一个合理的范围作为间隙值,当然我们在设计时要采用最小合理间隙。查教材冷冲压模具课程设计与毕业设计指导表3-7可知,Zmin=0.132mm Zmax=0.24mm。6.2 冲裁刃口尺寸的计算及依据与法则设计
41、模具时一定要选择合理的间隙,以保证冲裁件的断面质量、尺寸精度满足产品的要求,所需冲裁力小、模具寿命高,但分别从质量,冲裁力、模具寿命等方面的要求确定的合理间隙并不是同一个数值,只是彼此接近。考虑到制造中的偏差及使用中的磨损、生产中通常只选择一个适当的范围作为合理间隙,只要间隙在这个范围内,就可以冲出良好的制件,这个范围的最小值称为最小合理间隙Zmin,最大值称为最大合理间隙Zmax。考虑到模具在使用过程中的磨损使间隙增大,故设计与制造新模具时要采用最小合理间隙值Zmin。冲裁间隙的大小对冲裁件的断面质量有极其重要的影响,此外,冲裁间隙还影响模具寿命、卸料力、推件力、冲裁力和冲裁件的尺寸精度。较
42、大的间隙可使凸模侧面及材料间的摩擦减小,并延缓间隙由于受到制造和装配精度的限制,虽然提高了模具寿命而,但出现间隙不均匀。因此,冲裁间隙是冲裁工艺与模具设计中的一个非常重要的工艺参数。 冲裁间隙是冲裁工艺与冲裁模具设计的一个重要工艺参数,对冲裁件质量、冲裁力和模具寿命均有很大的影响。冲裁间隙还影响着冲裁件的尺寸精度。冲裁件的尺寸精度是指冲裁件的实际尺寸与基本尺寸的差值,差值越小,精度越高。间隙过大,会使落料件尺寸小于凸凹模尺寸,冲孔件尺寸大于凸模尺寸,冲裁力也会慢慢下降,卸料力、推件力或顶件力都将随之下降。间隙过小,会使落料件尺寸大于凸凹模尺寸,冲孔件尺寸小于凸模尺寸,冲裁力也会增大,会使模具刃
43、口磨损加剧,还会产生凸凹模胀裂,小凸模折断,凸模和凸凹模相互啃刃等异常损坏。由此可见,我们在确定冲裁间隙时,一定要有一个合理的范围作为间隙值,当然我们在设计时要采用最小合理间隙。文献资料查得,Zmin=0.132mm Zmax=0.24mm。 6.2 刃口尺寸的计算及依据与法则冲裁件的尺寸精度主要决定于凸、凹模刃口尺寸及公差,模具的合理间隙也是靠凸、凹模刃口尺寸及其公差来保证。凸、凹模的设计原则 冲孔时,设计计算以凸模为准,间隙放大在凹模刃口上。 落料时,设计计算以凹模为准,间隙缩小在凸模刃口上。由于本次设计刀口尺寸较复杂,本套模具采用配合加工法进行加工。配合加工时计算公式如下:对于刃口磨损后
44、尺寸产品越来越小的尺寸: (6.1) 凹模的刃口尺寸根据凸模刀口实际尺寸按照间隙要求配做。 对于刃口磨损后尺寸产品越来越大的尺寸: (6.2) 凸模的刃口尺寸根据凹模刀口实际尺寸按照间隙要求配做。 其中:Bd、Ad-为相应基准体的基本尺寸;Bmin-为工件的下极限尺寸;Amax-为工件的上极限尺寸; ,-分别为凸、凹模制造公差,通过下表6-1获得;-为工件公差;x-为磨损系数,其值在0.51之间,通过查下表6-2获得。根据未注零件尺寸公差按照IT14级选取,通过查找对应国标的表格数据查得:刃口磨损后产品尺寸越来越小的尺寸:mm,mm,mm,;刃口磨损后产品尺寸越来越大的尺寸:mm,mm,mm,
45、mm,mm,mm。对于刃口磨损后产品尺寸越来越小的尺寸根据公式6.1:Bd1=(1.85+0.750.12)0-0.020 = 1.940-0.020mmBd2=(1.65+10.12)0-0.020 = 1.770-0.020mmBd3=(6.5+0.750.1)0-0.020 = 6.580-0.020mm对于刃口磨损后产品尺寸越来越大的尺寸根据公式6.2有: Ad1=(1.850.50.25)0+0.02=1.730+0.02mmAd2=(9.40.750.1)0+0.020=9.330+0.020mmAd3=(1.510.12)0+0.020=1.380+0.020mmAd4=(3.7
46、10.16)0+0.020=3.540+0.020mmAd5=(2.20.50.25)0+0.020=2.080+0.020mmAd6=(13.410.2)0+0.020=13.20+0.020mm配合件的基本尺寸与上述基准件尺寸相同,不需要标注公差,但是需要保证最小双边合理间隙值为0.132mm,最大双边合理间隙值为0.24mm。表6-1部分标准公差值(GB/T1800.3-1998)基本尺寸/mm 标准公差等级IT1IT2IT3IT4IT5IT6IT7IT8IT9IT10IT11IT12IT13IT14大于至ummm-30.81.2234610142540600.114253611.52.
47、545812183048750.120.180.361011.52.546915223658900.150.220.3610181.2235811182743701100.180.270.4318301.52.546913213352841300.210.330.5230501.52.54711162539621001600.250.390.625080235813193046741201900.30.460.74801202.5461015223554871402200.350.540.871201803.55812182540631001602500.40.6311802504.57101
48、4202946721151852900.460.721.15注释:包容表面取“+”,被包容表面取“-”孔中心距取“”表6-2 简单形状(方形、圆形)冲裁时凸、凹模制造偏差 (mm)公称尺寸凸模偏差凸凹模偏差凹公称尺寸凸模偏差凸凹模偏差凹1818303080801201201800.0200.0200.0200.0250.0300.0200.0250.0300.0350.0401802602603603605005000.0300.0350.0400.0500.0450.0500.0600.070表6-3 磨损系数 材料厚度工件公差1122440.160.200.240.300.170.350.
49、210.410.250.490.310.590.360.420.500.600.160.200.240.300.160.200.240.30磨损系数非圆形x值圆形x值10.750.50.750.5第七章 模具工作零件的结构设计7.1 冲裁凹模设计7.1.1 冲裁凹模结构的选择在模具内,凹模板属于刀口中的一个,所发挥出的作用也十分关键,通常一定要确保其平面度以及表面的粗糙度,对其四周还要求倒角处理,防止工人在搬运的时候出现挂伤,对于凹模采用的销钉孔同样有一定公差要求,详细的大小参照在CAD图纸中的标注,对于凹模板所采取的热处理手段为真空淬火,接着再回火处理,这样能够提升其硬度,确保冲裁次数。还有
50、就是凹模板直接决定了工件外形一部分的尺寸大小,所以通常对于内形孔的加工借助于线切割来实现,对于凹模板的台阶,有时还会借助于数控加工中心完成。7.1.2 冲裁凹模精度与材料的确定根据凹模作为工作零件,其精度要求较高,外形长宽精度不是很重要,只需要板材厂家加工的尺寸大于图示尺寸就可,高度尺寸有较高要求,一般高度需要经过磨床的精磨加工,尺寸精度可达到0.01mm,内型腔一般由快走丝或者加工中心加工,其加工精度可达到0.01mm,高度方向表面粗糙度为Ra0.8um,上下平面的平行度为0.01,材料选SKD-11,最终需要通过热处理得到对应的硬料,其硬度在58-62HRC左右就可。7.1.3 冲裁凹模外
51、形尺寸的确定凹模模在外形上通常有两种形式,一种是圆形,一种是矩形。其外形尺寸必须让凹模在强度、刚度以及耐磨性上可以达到使用的需求。因此其外形尺寸的确定,通常是借助于被冲裁见外形上的最大尺寸以及厚度完成计算确定,相应的计算公式为: 凹模厚度 H=Kb1(15mm) (7.1) 凹模边壁厚 c=(1.52)H(30-40) (7.2) 凹模板边长 L=b2+2c (7.3) 凹模板边宽 B=b3+2c ( 7.4)式中:b1-冲裁件的横向最大外形尺寸,在连续模中可近似为凹模板最长孔的长度;b2-在连续模中近似为凹模板两个横向最远距离冲裁或弯曲孔的横向距离;b3-在连续模中近似为凹模板两个纵向最远距
52、离冲裁或弯曲孔的纵向距离;K-系数,考虑板料厚度的影响,查表7-1。表7-1 系数K值材料料宽s/mm材料厚度t/mm0.51.02.03.03.0500.30.350.420.50.6501000.20.220.280.350.421002000.150.180.200.240.302000.10.120.150.180.22根据cad图纸凹模板上测量数据并且结合查表7-1得: K=0.4凹模厚度:H= Kb1=0.4187.2mm为了提高凹模板强度性能和减小凹模板由于过薄使得热处理后变形过大,并且结合工厂实习经验,需将凹模厚度调整为25mm根据公式7.2可计算凹模边壁厚: C=(1.52)
53、H =1.525225 =37.550mm根据凹模厚度、边壁厚和排样图可确定凹模板的长、宽的尺寸,再结合压力中心位置与模架的选取微调壁厚,但是由于是连续模为大批量生产,在合理范围内尽量选取较大壁厚。根据公式7.3可计算凹模长:L=b2+2c =18+248.5=115mm根据公式7.4可计算凹模宽: L=b3+2c =9.4+250 =110mm 即:LBH=115mm110mm25mm7.2 冲裁凸模的设计对于凸模,常见的制造结构形式是直通式以及台阶式,也就是T冲以及A冲两种形式。如今的模具中的所有部件逐步成为系列化以及标准化的产品,两种形式都能够十分方便的从现有市场中采购,并且加工都是采用
54、线切割加工实现。图7.2为本次设计采用的凸模结构。图7.2 凸模示意图凸模的高度我们可以直接通过CAD测量获得;L=40mm该模具要求有较高的寿命和较高的耐磨性,并能承受冲裁时的冲击力,并且还需要考虑到材料成本及加工成本,所以异形凸模的材料应选Cr12MoV,热处理5558HRC,圆形凸模材料应选SKD-11,热处理5862HRC。7.3 卸料装置的设计在本课题中,因为最后的工件选用原料厚度不大,因此不用提供太高的卸料力,参照本课题中针对冲压模具设计的真实状况,在将多种相关联因素进行考虑后,对于卸料板采取的为弹性卸料模式。对于本课题设计的模具使用过程中真实条件下采取的冲压成型工艺,将多种相关联
55、因素进行考虑后,最后制定了相应的出件模式,通过这种模式能够有效确保产品品质,并且提升冲压成型的效率。条料的顶料主要是为了条料能继续往前送进,把吸在凹模板上的条料通过顶料装置:槽式浮顶销、内六角凹模紧定螺钉、弹簧往上顶,使得料带脱离凹模板且略高于凹模工作表面。卸料板尺寸外形和凹模板一样,厚度取0.6-0.8凹模板厚度就可。在冲裁模卸料与出件装置中,常用的元件是弹簧和橡胶,结合本次连续模结构,若选用弹簧,则板上需要加工更多的孔,并且弹簧的成本高于橡胶,弹簧的力相对来说比橡胶小;因此,该模具采用的弹性元件为橡胶。橡胶允许承受的负载较大,安装调整较方便灵活,而且成本低,是中小型冲模中弹性卸料、顶件及压
56、边装置常用的弹性元件。以下为橡胶的选取计算过程:本次设计的连续模的工作行程为6mm,模具的卸料力为2.7KN,通过查文献2,表9-43即下表7-2选取橡胶垫块压缩量为30%,单位压力为1.52MPa,外直径为30mm,内直径为12mm,底面面积约为600,自由高度为20mm的带孔橡胶垫。单个橡胶垫的弹力F=600x1.520.9KN,一共选取4个。表7-2 橡胶垫压缩量和单位压力橡胶垫压缩量(%)单位压力p/MPa橡胶垫压缩量(%)单位压力p/MPa100.26251.06150.50301.52200.70352.107.4凸模固定板的设计凸模固定板顾名思义我们可以看出他是用来固定各种凸模的,保证凸模有足够的强度,使凸模与落料凹模、上模座、垫板更好的定位。凸模与固定板上空的配合按H7/m6。如图7.4所示。图7.4 凸模固定方式示意图卸料板尺寸外形和凹模板一样,厚度取0.6-0.8凹模板厚度就可。本次我们取15mm7.5垫板的设计垫板发挥的功能在于
- 温馨提示:
1: 本站所有资源如无特殊说明,都需要本地电脑安装OFFICE2007和PDF阅读器。图纸软件为CAD,CAXA,PROE,UG,SolidWorks等.压缩文件请下载最新的WinRAR软件解压。
2: 本站的文档不包含任何第三方提供的附件图纸等,如果需要附件,请联系上传者。文件的所有权益归上传用户所有。
3.本站RAR压缩包中若带图纸,网页内容里面会有图纸预览,若没有图纸预览就没有图纸。
4. 未经权益所有人同意不得将文件中的内容挪作商业或盈利用途。
5. 装配图网仅提供信息存储空间,仅对用户上传内容的表现方式做保护处理,对用户上传分享的文档内容本身不做任何修改或编辑,并不能对任何下载内容负责。
6. 下载文件中如有侵权或不适当内容,请与我们联系,我们立即纠正。
7. 本站不保证下载资源的准确性、安全性和完整性, 同时也不承担用户因使用这些下载资源对自己和他人造成任何形式的伤害或损失。