电动车动力总成在机械-电磁激励下的振动分析
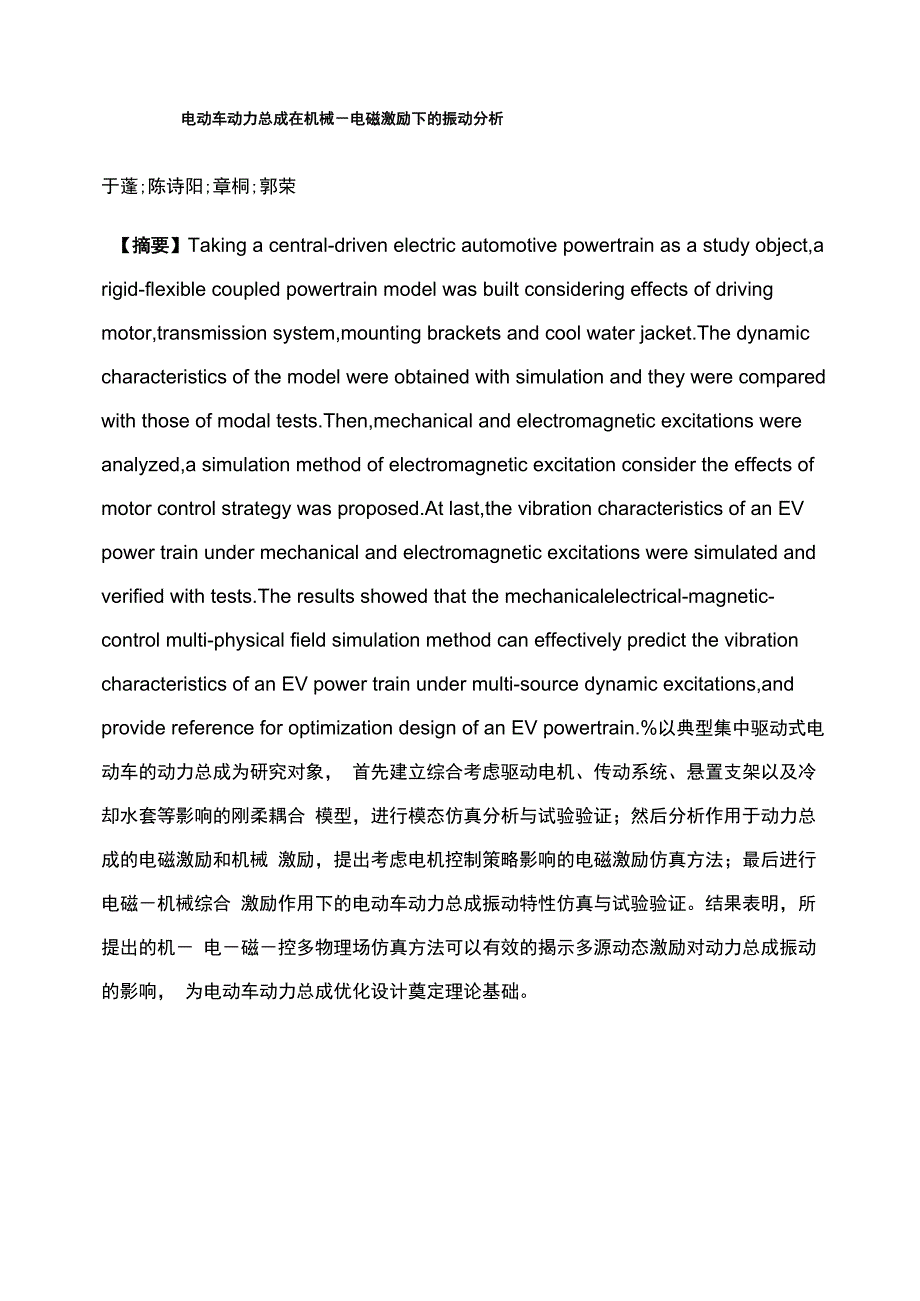


《电动车动力总成在机械-电磁激励下的振动分析》由会员分享,可在线阅读,更多相关《电动车动力总成在机械-电磁激励下的振动分析(12页珍藏版)》请在装配图网上搜索。
1、电动车动力总成在机械电磁激励下的振动分析于蓬;陈诗阳;章桐;郭荣【摘要】Taking a central-driven electric automotive powertrain as a study object,a rigid-flexible coupled powertrain model was built considering effects of driving motor,transmission system,mounting brackets and cool water jacket.The dynamic characteristics of the model w
2、ere obtained with simulation and they were compared with those of modal tests.Then,mechanical and electromagnetic excitations were analyzed,a simulation method of electromagnetic excitation consider the effects of motor control strategy was proposed.At last,the vibration characteristics of an EV pow
3、er train under mechanical and electromagnetic excitations were simulated and verified with tests.The results showed that the mechanicalelectrical-magnetic-control multi-physical field simulation method can effectively predict the vibration characteristics of an EV power train under multi-source dyna
4、mic excitations,and provide reference for optimization design of an EV powertrain.%以典型集中驱动式电动车的动力总成为研究对象, 首先建立综合考虑驱动电机、传动系统、悬置支架以及冷却水套等影响的刚柔耦合 模型,进行模态仿真分析与试验验证;然后分析作用于动力总成的电磁激励和机械 激励,提出考虑电机控制策略影响的电磁激励仿真方法;最后进行电磁机械综合 激励作用下的电动车动力总成振动特性仿真与试验验证。结果表明,所提出的机 电磁控多物理场仿真方法可以有效的揭示多源动态激励对动力总成振动的影响, 为电动车动力总成优化设计
5、奠定理论基础。期刊名称】振动与冲击年(卷),期】2016(035)013【总页数】8页(P99-105,139) 【关键词】 电动车;动力总成;振动特性;机械激励;电磁激励【作 者】 于蓬;陈诗阳;章桐;郭荣【作者单位】 同济大学新能源汽车工程中心;同济大学 汽车学院;同济大学新能源 汽车工程中心; 同济大学 汽车学院;同济大学 新能源汽车工程中心; 同济大学 汽车 学院;同济大学 中德学院,上海 201804;同济大学新能源汽车工程中心; 同济大学 汽车学院【正文语种】 中 文【中图分类】 U469.72+2随着电动汽车产业的发展,其整车振动、噪声与乘坐舒适性越来越受到电动车使用 者和研究者
6、的关注。相比于传统内燃机汽车,纯电动汽车的振动与噪声水平在总体 上都略低,但在某些工况和频段,其振动与噪声特性往往引发驾乘者不舒适的主观 感受1。电动车动力总成系统包括电机及齿轮减/差速器系统,其特有的内部综合 激励使电动车振动噪声产生新特点,永磁同步电机定转子间产生的电磁激励以及减/ 差速器由于齿轮传递误差、啮合刚度等因素导致的机械激励是电动车动力总成的重 要内部激励1。针对电机和传动系各类激励对振动噪声的影响,国内外学者已进行 了一定的研究。魏静2研究了齿轮箱系统在内、外部激励综合作用下的振动响应。唐政等3基于场路耦合研究了永磁同步电动机的瞬态特性。Mori等4分析了电 机径向电磁力对固有
7、频率和振动特性的影响。Pellerey等5分析了电流谐波对电 机壳体振动的影响。Kim等6-7使用一种弱磁固耦合方法,对某内置式永磁电机 的电磁振动进行了研究。Neves等8将多物理场电磁仿真用于不同类型的电机振 动研究中。以往研究的不足有:动力总成建模方面,虽然建立了总成整体的有限元模型, 但是对于壳体冷却水套、悬置支架柔性以及内部轴系支撑作用等因素,考虑不够全 面,获得的模态密度有限1,9;机械激励获取方面,使用齿轮动力学简化公式 模拟综合误差激励,数值模拟精度较低,振动响应结果较单一1;电磁力获取 方面,不考虑电机控制因素的影响,无法得到符合实际的径向和切向电磁力波,尤 其是其高频谐波往
8、往被忽略,造成振动响应结果偏差1,5,8:只进行综合激励 下壳体动态响应分析,对于机械-电磁分别独立作用下的响应分析不够,对各类激 励在动力总成中所占的比重缺少系统的对比4-5,8,对后续从被动角度优化齿轮 系统和从主动角度控制电流谐波的工程指导意义及效果预估不够明确。在以往研究的基础上,考虑转子-齿轮系统、悬置支架柔性、壳体及内部结构等因 素,建立较为准确的电动车动力总成刚柔耦合模型;充分考虑结构和控制方面的因 素,获取详细的机械激励和电磁激励;进行动力总成在机械-电磁激励下的振动响 应仿真及试验验证,分析电磁激励和机械激励对总成壳体振动影响的比重,总体把 握电动车动力总成振动的激励特性和响
9、应特性,为从主被动控制角度进行动力总成 的减振降噪控制提供技术支持。1.1 电动车动力总成建模 所研究的某款集中驱动式电动车的动力总成主要包括两部分:电机和减差速器壳体 结构以及动力总成内部传动系结构。动力总成内部传动系统包括电机、固定传动比 的二级减速器以及差速器。在Hypermsh软件中建立电机和减差速器壳体三维有 限元模型,在Romax软件中建立刚性齿轮传动系模型;然后在Romax软件中利 用节点耦合技术将建立的柔性壳体模型和刚性传动性模型进行装配,得到电动车动 力总成的刚柔耦合模型,如图1所示。具体的动力总成结构以及基于Romax软件和有限元软件进行刚柔耦合联合建模的 方法参见文献1,
10、10。本文模型的改进之处在于,与文献1中的模型相比,考虑了 电机定子外部冷却水套及三个悬置支架柔性的影响,能获得较高的模态密度;与文 献10中的模型相比,在减/差速器刚柔耦合模型的基础上,进一步考虑了转子-齿 轮系统的影响,建立了整个动力总成的刚柔耦合模型,便于整体把握。1.2 模态仿真及试验结果 对动力总成进行固有特性分析是研究其振动噪声特性的基础,一方面通过与试验对 比可以验证仿真模型的准确性;另一方面也有助于后续更全面地分析振动响应结果 对上述建立的动力总成刚柔耦合模型进行模态特性求解,设置求解频率范围0 5 000 Hz ,最终得到耦合模型在该频率范围内的模态阶数和频率,如表1所示。同
11、 时,模态试验测得的电动车电机与减速器05 000 Hz的模态参数也列入表中, 以便参考9。从表1中可以看到,动力总成耦合模型在05 000 Hz范围内共有15阶模态, 各阶模态频率与模态试验结果的误差基本保持在10%以内,验证了仿真模型的准 确性以及后续在动力总成振动响应研究中的可用性。对于模态试验中的1、2阶固 有频率,仿真模型并未体现出该固有特性,该固有频率的产生可能是由悬吊绳索的 影响所导致,仿真中未考虑悬吊绳索的影响。同时对比文献 9中的仿真结果可知, 综合考虑水套影响、支架柔性及转子-齿轮系统内部支撑的壳体模态结果,与忽略 这些因素的动力总成壳体模态结果相比,模态密度更大,有助于获
12、取更丰富的动力 学响应。2.1 机械激励 动力总成内部机械激励是指齿轮在啮合过程中产生的动态激励,主要包括啮合刚度 激励、传递误差激励以及啮合冲击激励1,10。Romax仿真方法可以全面的考虑 到以上因素,首先对动力总成运行条件下的内部机械激励进行获取。以车速40 km/h这一常用工况为例,计算该工况下的齿轮系传递误差以及动力总成的振动结 果,获取壳体表面各关键点的振动响应。以减速器二级齿轮轴外端轴承处的振动加 速度响应为例,振动频域结果如图2所示。从图2中可以看到,该轴承中心处的振动加速度值分别在606.6 Hz、1 010.1 Hz、1 868.7 Hz和3 181.8 Hz取得极值,在频
13、率1 868.7 Hz处出现峰值,振动加速 度达到了 0.886 m/s2。类似的,提取耦合模型8个轴承中心处的加速度振动响应 结果,作为后续壳体振动研究中的内部机械激励输入。以往研究使用简化公式计算 机械激励,只能考虑齿轮刚度、啮合误差等与齿轮系统相关的因素,对于其它影响 因素的考虑则不够全面。使用专业的Romax软件获取机械激励,与文献1 中使 用简化的齿轮动力学公式模拟激励相比,更能体现壳体柔性、悬置支撑、水套等若 干因素的影响,使结果更加符合实际。2.2 电磁激励 电机定子电流的交变产生气隙旋转磁场,该磁场与转子永磁体磁场相互作用,产生 驱动转矩供车辆运行。与此同时,气隙磁场产生作用于
14、定子铁芯内表面的电磁力波, 造成定子壳体在电磁激励下的结构振动,并向动力总成外部辐射电磁噪声。作用于 定子的电磁力主要包括径向和切向电磁力波。对于两个方向电磁力波的准确模拟, 是获得合理的壳体动态振动响应的关键。而电磁力波的产生与电机定子电流的供电 方式紧密相关,不同的控制策略将产生不同的谐波电流及电磁力波。本文的电磁力 获取将充分考虑电机控制策略的影响。首先在电磁仿真软件中建立电机2D电磁仿真模型,2D仿真是电动车驱动电机电 磁仿真的常用方法,其精度满足工程要求4-8(3D电磁仿真较多考虑端部效应, 较为适用于轴向尺寸较短的轮毂电机仿真或者气隙较大的高速电机仿真);其次, 使用MATLAB/
15、Simulink搭建控制电机模型,所研电动车的电机控制策略为最大 转矩电流比控制,该控制策略在文献11中已有较为详细的阐述,不再赘述。最后, 基于电磁场仿真软件和控制电机模型,进行场路耦合联合仿真。给出基于控制策略、 逆变器电路和电机有限元本体的联合仿真模型,如图3所示。求解在最大转矩电 流比控制条件下,永磁电机的电磁场分布和定子受到的电磁力。该仿真方法充分考 虑了电机控制策略对电磁力波的影响,能够获得更加丰富的动力学现象,尤其是高 频动态特性。选择三相输入电流为2 A,电机转速为2 800 r/min(对应车速40 km/h的工况, 对应转子基频f=46.7 Hz),得到永磁电机的电磁场气隙
16、磁密分布,经气隙磁密与 电磁力关系的转换公式计算5,最终得到电机壳体各点处切向和切向电磁力,以 电机内部齿槽上某点为例,其径向、切向电磁力波的频域结果如图4所示。仿真 中选定的电机的极对数p=4,所以电机的电磁力峰值频率应该以转子基频的2npf 倍为主。从图5看出,定子齿槽测点所受的电磁力的频率分量主要为有400Hz(8f)、1 200 Hz(24f)、4 000 Hz(88f)、4 600 Hz(96f)、5 000 Hz(104f)等,其峰值频率都对应于由磁极引起的谐波频率2npf(n = 123,4.)。600 Hz和4 800Hz这两个频率处的峰值是由转子磁极和定子齿槽共同作用所引起。
17、而各个特征频率下的峰值分布则受到控制电流谐波成分的影响,电机控制因素和结构因素对电磁 力影响的总结参见文献11。将图4结果与文献1,5中的电磁力进行对比发现,文献1,5中忽略电机控制策略 的影响,只能得到较为理想的电磁力仿真结果,无法获得更为符合实际的电磁力仿 真结果,尤其是在3 000-5 000 Hz的频率范围内,忽略控制电路的影响,将无 法体现电机由于控制策略的存在造成的定子电流谐波成分,进而无法得到较为贴合 实际的动力总成壳体振动响应,切向电磁力波的结果也是类似。获取电机内部所有 齿槽上的径向和切向电磁力,作为后续振动研究中的电磁激励输入。3.1 综合激励的施加Romax 是专业的齿轮
18、动力学仿真设计软件,但对于电动车动力总成电磁激励的施 加及响应分析方面,功能不够完善,后续使用后处理功能强大的商用化软件Ansys对动力总成壳体的振动响应进行分析,即利用Romax仿真获取机械激励, 利用电磁联合仿真获取电磁激励,再共同施加于Ansys有限元模型,进行动态响 应分析。动力总成有限元模型如图5(a)所示。为确保Ansys中的有限元模型模态仿真结果与之前模态结果的一致性,首先添加 梁单元和轴承孔的刚性连接,用于模拟Romax软件中的齿轮系和轴承,调整梁单 元截面、单元材料及属性,最终确定的内部梁单元支撑结构,如图5(b)所示;然 后,将前述获取的动力总成内部机械-电磁激励加载到壳体
19、单元上,机械激励加载 到各轴承孔刚性连接的中心点位置,电磁激励则加载到电机壳体内部齿槽内表面上, 电磁激励及其施加位置如图 6 所示。3.2 关键点响应及激励占比分析 对动力总成模型进行动响应仿真及频谱分析,得到动力总成壳体各处的振动响应结 果,参照电动车动力总成的动响应研究1,提取电机、减速器、差速器上各对应 点的振动响应结果进行分析,仿真结果如图 7 所示。图中不仅给出了机械-电磁激 励下的动态响应结果,还给出了机械激励和电磁激励共同作用下的结果,便于更加 全面的把握动力总成的振动特性。分析图 7 中各曲线可知:(1) 动力总成壳体表面上的电机仿真点、减速器仿真点以及差速器壳体表面仿真点
20、的振动响应,均受到机械激励和电磁激励的综合影响。电机定子虽然不与减速器直 接相连,但仍受到明显的机械系统振动激励的影响;减/差速器虽然不直接受到定 转子间电磁力的作用,但是其振动响应结果中也存在明显的电磁激励振动的成分。 表明动力总成一体化建模及仿真方法的优越性,若将电机和减/差速器分开建模则 无法得到文中类似的结果。(2) 机械激励单独作用下的动力总成振动响应和综合激励共同作用下的总成振动响 应较为吻合,说明在05 000 Hz的频段内,机械激励占据主导因素,而电磁激 励为次要因素。(3) 机械激励作用下和综合激励作用下的特征频率主要分布在2 500 Hz、3 800Hz以及4 500 Hz
21、附近,对应表1的模态信息可知,主要引发了动力总成第5、6、 10、14、15阶次的共振;引发这些共振的原因是转子-齿轮系统啮合频率的基频f 的倍频,这些频率有 z1 倍(1 354 Hz)、2z1 倍(2 708 Hz)、3z1 倍(4 062 Hz)、 z1 z3 / z2 倍(490 Hz)、2z1z3/z2 倍(980 Hz),z1、z2、z3 分别为电机转子输出 轴齿轮齿数、中间轴输入端齿轮齿数和输出端齿轮齿数。(4) 电磁激励作用下的特征频率主要分布在2 000 Hz、2 400 Hz、4 800 Hz 附近 结合图4和表1分析可知,2 000 Hz以下的径向、切向电磁激励幅值虽然较
22、大, 但是动力总成在该频段内的频率分布较稀疏,未能引发较大的壳体共振。2 000 Hz、2 400 Hz处的电磁激励虽然较小,但由于共振也出现了较明显的响应峰值, 主要引发了总成第2、4阶次的共振。而4 800 Hz在处,由于同时具有较大的电 磁激励峰值和共振的条件,也在电机和减速器表面引发了较为明显的电磁振动。综上所述,使用Romax软件获得机械激励、使用电磁仿真软件与电机控制策略相 结合的仿真方法获取电磁激励,与以往研究相比能体现更丰富的动力学现象。图7 结果与文献1中的对应测点的仿真结果相比,峰值频率点更多,与理论分析结果 更加吻合,体现了所提供的改进仿真方法的正确性。进一步分析系统振动
23、响应的主 要波峰处电磁与机械激励的贡献率,各个仿真点机械激励影响比值和电磁激励影响 比值如表24所示。机械和电磁激励作用占比计算公式为: 式中,fk为1/3倍频程中心频率,n为中心频率所在频段采样点数,i为中心频率 所在频段采样点编号,E为频率带上的能量,j代表机械激励,d代表电磁激励。 可以进一步得到如下结论:机械激励和电磁激励是引起电动车动力总成壳体的振动 两个主要内部激励,其中机械激励在整个频率段内比重相对较大,尤其是在04 000 Hz频段,机械激励占据主导地位;在4 000-5 000 Hz频段,电磁激励对壳 体振动的影响增大,尤其在电机壳体部位占据主导地位,使得电动车动力总成在高
24、频段的动力学现象更加复杂。另外,由于电动车动力总成的集成式一体化结构,电 机的电磁激励对差速器的振动也有一定影响,如差速器表面2 000 Hz左右的峰值 几乎全部由电磁激励引发。为了验证前述仿真结果的正确性,进行电动车整车转鼓试验。相关设备包括:纯电 动车样车、三向加速度传感器以及记录、分析、处理振动信号设备:LMS Testlab、 CANCASE/CANnape、LeCroy HDO4034 等。试验过程参照国家标准GB/T14365-93机动车辆噪声测量方法布置振动加速度传感器,主要测试工况 有:稳速工况-在10 km/h 80 km/h稳速巡航条件下,每间隔10 km/h进行 测量;转
25、鼓拖动工况-转鼓带动车轮速度从10 km/h 80 km/h巡航,每间隔10 km/h测量一次,用于辅助分析。对应仿真工况,以40 km/h的驱动和反拖工 况处理结果为例进行分析。加速度测点对应前述三个仿真测点,如图8所示。4.1 电机驱动工况 驱动试验工况对应机械-电磁综合激励下振动仿真工况。通过对比试验和仿真结果, 可以在模态试验的基础上,进一步验证模型的正确性。获取三个测点的振动加速度 时域结果,并进行快速傅里叶变换,得到频域处理结果如图9所示。将图9试验结果对比图7中的仿真结果可知,电机测点2 500 Hz和3 800 Hz处的由机械激励引发的峰值以及500 Hz、1 000 Hz、1
26、 500 Hz附近的由电磁激励引发的峰值都在试验中被反映了出来;但 在试验中第一峰值不是体现在3 800 Hz左右,而是出现在2 500 Hz左右,这是 因为在实车动力总成系统中,由于装配误差和磨损等因素,造成转子轴相比仿真时 较大的静、动偏心,从而引发的驱动小齿轮齿数的2倍频(2z1)的较大振动。(2) 减速器测点的试验及仿真结果吻合得较好。2 500 Hz处的峰值未出现类似于 电机测点高于仿真值的原因是,减速器测点在布置时,选择在了一级啮合齿轮中心 对应的测点处,较大程度的排除了输入轴静、动偏心的影响。(3) 差速器测点的试验及仿真结果在1 000 Hz以上频段吻合得较好,在01 000
27、Hz内试验获得的振动响应峰值明显多于仿真结果。这是因为差速器被包裹在动力 总成壳体中,试验测点无法直接布置在差速器壳体上,而是选取的临近差速器壳体 仿真点的动力总成壳体上,这样将受到半轴结构等的影响。进一步甄别可知,试验 中500 Hz左右的峰值是由于驱动半轴第一阶弯曲频率导致。总体来看,试验结果和仿真结果中各个测点加速度的主要峰值点和峰值频率的趋势, 具有较强的一致性,说明所提供的综合激励添加以及建模、仿真方法,可以较好的 预测动力总成的振动特性,为进一步的从主被动控制角度优化齿轮传动系统或者电 机控制策略提供有效仿真平台。4.2 测功机拖动工况 不失一般性,在进行驱动工况试验之后,为便于参
28、考分析,进行了相同转速下的转 鼓反拖试验。获取了相关测点的振动响应结果,如图 10 所示。需要首先明确的是, 该试验结果并不能完全对应单纯机械激励下的仿真结果。原因有:轮毂反拖试 验中,车辆挂空挡,虽然排除了驱动电机定转子间较大的电磁激励的影响,仅在齿 轮激励下获取振动响应结果,但是该工况仅为试验室工况,不完全对应车辆的实际 使用工况;试验中很难将机械激励和电磁激励完全剥离,反拖工况中,电机定 子线圈被动切割转子磁场磁感线,也产生少量的电磁转矩和电磁阻尼,但是其值远 小于驱动工况,对传动系统转矩、转速的抑制效果有限,可能导致反拖工况下,振 动幅值大于驱动工况;驱动工况下,电机驱动车轮,效果是减
29、速度增扭矩,而 反拖工况下,车轮驱动电机,效果是增速度减扭矩,转矩转速条件发生了较大变化。 综上,将反拖工况结果与单纯机械激励下的结果进行对比并不是必要的步骤,但是 仍然可以通过正驱和反拖试验对比,进一步把握动力总成的机械振动特性。 对比图10和图9可知,反拖工况下4 800 Hz处的峰值消失,这与反拖工况下,电机电磁啸叫噪声 (Whine)消失的主观感受一致。该峰值消失的原因,一方面是电机转子轴不作为激 励输入轴,其对应的高阶次倍频(3z1倍基频)能量大大减少,引发振动的作用减小, 另一方面是电磁激励减小,径向、切向电磁力波中的4 800 Hz附近的高频谐波含 量消失,无法引发总成壳体在该频
30、率附近的共振。(2)振动峰值主要集中在 490 Hz、980 Hz、1 500 Hz、2 000 Hz、2 500 Hz 附 近,这些频率均由齿轮啮合频率引发,是转子轴基频(46.7 Hz)的nz1z3/z2(n = 123,4,5.)倍,也就是二级齿轮啮合频率(490 Hz)的 nz3倍频。电机测点最大峰值出现在490 Hz,是因为动力从二级啮合齿轮传递到电机转 子轴,引发类似于空载齿轮非线性振动(Rattle)的现象所致。该转轴在输入工况下 受到重载荷及电磁阻尼的作用,而在反向拖动工况,仅受到转子惯量的影响,负载 及阻尼大大减小,对振动的衰减作用减小。(4) 减速器测点2 500 Hz处的
31、振动源于中间轴振动引发总成第5阶次的共振,与 驱动工况类似。差速器测点处01 000 Hz的较大峰值是由于半轴的影响,在测 功机驱动车轮的条件下,半轴成为动力源输入轴,具有较大的振动能量,对差速器 附近测点振动的影响加大。另外,部分频率点的振动幅值高于驱动工况,符合试验前的预期,这与电磁阻尼力 减小,进而抑制振动的作用减小,以及齿轮负载转矩减小而转速波动加大这一机械 激励特性的改变有关。这些变化能够在齿间侧隙数值不改变的情况下,造成更大的 轮齿啮合非线性振动的幅值。(1) 综合考虑转子-齿轮系统内部支撑、定子冷却水套、壳体及悬置支架柔性的刚柔 耦合建模方法,以及通过Romax详细获取机械激励和
32、考虑控制策略获取电磁激励 的仿真方法,能够较为准确地反映电动车动力总成的振动响应特性。(2) 机械激励和电磁激励是引起电动车动力总成壳体结构振动的两个主要激励源, 引发电动车动力总成的齿轮啸叫伴随电机啸叫现象。机械激励在整个频率段内占据 主导地位;在2 000 Hz左右及4 000 Hz 5 000 Hz频段,电磁激励的作用也较 为可观。电机驱动工况下,动力总成壳体共振主要由一级齿轮啮合频率1 354 Hz的2、 3倍频以及4 800 Hz附近的高频大幅值电磁力波激励引发;测功机反拖工况下复 杂的振动响应,主要是因为齿轮副在承载转矩小、转速波动大以及齿间侧隙的影响 下,产生的相对变大的啮合非线
33、性振动引发。(4) 反拖工况可用于整体把握,是否能直接用于对比机械激励单独作用下的仿真结 果,有待进一步探讨。后续将设定符合拖动工况运行状态的仿真工况,进行相应的 仿真分析。所做研究有助于整体把握电动车动力总成的振动特性,为进一步的从被动角度优化 齿轮传动系统和总成壳体系统及从主动控制角度改进电机控制策略奠定基础。E-mail:【相关文献】1 于蓬,陈霏霏,章桐,等集中驱动式电动车动力总成系统振动特性分析几振动与冲击,2015, 34(1): 44-48.YU Peng,CHEN Fei-fei,ZHANG Tong,et al. Vibration characteristics analy
34、sis of a central-driven electric vehicle powertrainJ. Journal of Vibration and Shock ,2 0 1 5, 34(1): 44-48.2 魏静,孙清超,孙伟,等大型风电齿轮箱系统耦合动态特性研究J振动与冲击,2012,31(8):16-23.WEI Jing,SUN Qing-chao,SUN Wei,et al. Dynamical coupling characteristics of a large wind turbine gearbox transmission systemJ.Journal of V
35、ibration and Shock,2012, 31(8):16-23.3 唐政,黄大贵.基于场路耦合时步有限元的永磁同步电动机瞬态特性研究J.微电机,2008, 41(11):11-14.TANG Zheng, HUANG Da-gui.Study on transient characteristic of permanent magnet synchronous motor based on field-circuit coupled time-stepping finite element methodJ.Micromotors,2008, 41(11):11-14.4 Mori D
36、, Ishikawa T. Force and vibration analysis of induction motors J. IEEE Transactions on Magnetics,2005,41(5): 1948-1951.5 Pellerey P, Lanfranchi V, Friedrich G. Coupled numerical simulation between electromagnetic and structural modelsJ. IEEE Transactions on Magnetics, 2012,48(2):983- 986.6 Park S, K
37、im S, Kim W.A numerical model for predicting vibration and acoustic noise of IPMSMC/IEEE Vehicle Power and Propulsion Conference.Seoul,2012:1054-1058.7 Kim D Y, Nam J K,Jang G H.Reduction of magnetically induced vibration of aspoke- type IPM motor using magnet mechanical coupled analysis and optimiz
38、ation J.I EEE Transactions on Magnetics , 2013,49(9): 5097-5105.8 Dupont J, Aydoun R, Bouvet P.Simulation of the noise radiated by an automotive electric motor: influence of the Motor DefectsJ. SAE Int. J. Alt. Power, 2014,3(2):310-320.9 方源,于蓬,章桐电动车动力总成模态试验与仿真分析几机械传动,2013,37(4):110-113. FANG Yuan ,
39、YU Peng ,ZHANG Tong,et al.Test and simulation analysis of modal parameter of an electric automotive powertrainJ. Journal of Mechanical Transmission , 2013,37(4):110-113.10 于蓬,章桐,冷毅,等电动车减/差速器振动特性分析及改进几振动与冲击,2015, 34(7): 85-92.YU Peng, ZHANG Tong, LENG Yi,et al. Vibration characteristics analysis and
40、improvement of differential/reducer of electric vehicleJ. Journal of Vibration and Shock,2015, 34(7): 85-92.11 于蓬,章桐,孙玲,等集中驱动式纯电动车动力传动系统扭转振动研究J振动与冲 击,2015,34(10):121-127.YU Peng,ZHANG Tong , SUN Ling , et al. Powertrain torsional vibration study of central- driven pure EVJ. Journal of Vibration and Shock,2015, 34(10): 121-127.
- 温馨提示:
1: 本站所有资源如无特殊说明,都需要本地电脑安装OFFICE2007和PDF阅读器。图纸软件为CAD,CAXA,PROE,UG,SolidWorks等.压缩文件请下载最新的WinRAR软件解压。
2: 本站的文档不包含任何第三方提供的附件图纸等,如果需要附件,请联系上传者。文件的所有权益归上传用户所有。
3.本站RAR压缩包中若带图纸,网页内容里面会有图纸预览,若没有图纸预览就没有图纸。
4. 未经权益所有人同意不得将文件中的内容挪作商业或盈利用途。
5. 装配图网仅提供信息存储空间,仅对用户上传内容的表现方式做保护处理,对用户上传分享的文档内容本身不做任何修改或编辑,并不能对任何下载内容负责。
6. 下载文件中如有侵权或不适当内容,请与我们联系,我们立即纠正。
7. 本站不保证下载资源的准确性、安全性和完整性, 同时也不承担用户因使用这些下载资源对自己和他人造成任何形式的伤害或损失。
最新文档
- 一元回归及相关分析课件
- 第六章北方地区第四节-祖国的首都——北京(课堂ppt)课件
- 第十三课《规划每一天》ppt课件
- 第十三课从蒸汽机到互联网ppt课件
- 第八章-真核基因表达调控ppt课件
- 第10章-中枢神经系统感染性疾病ppt课件
- 第十一课-公正处理民事关系ppt课件
- 第十三课《人的本质与利己利他》-一、正确处理利己和利他的关系ppt课件
- 第十四章-消息标题ppt课件
- 第23章第1节生物的生存依赖一定的环境ppt课件
- 第十八章电功率第1节电能电功ppt课件
- 第十二章-公共关系评估ppt课件
- 第十二章-词的初创及晚唐五代词ppt课件
- 一元二次方程解法——配方法课件
- 第十四章-流变学基础ppt课件