车床精度的概述
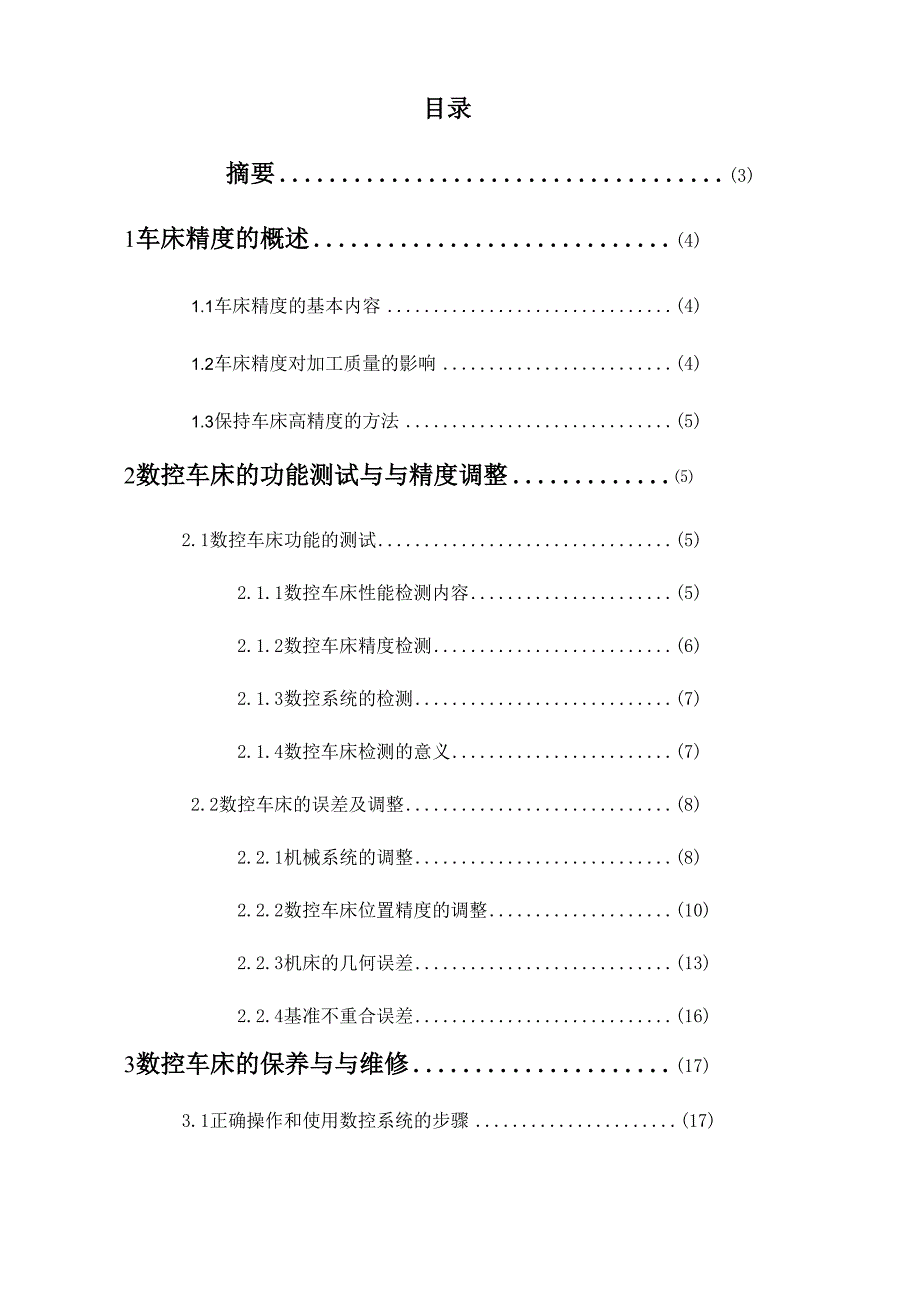


《车床精度的概述》由会员分享,可在线阅读,更多相关《车床精度的概述(31页珍藏版)》请在装配图网上搜索。
1、目录摘要(3)1车床精度的概述(4)1.1车床精度的基本内容(4)1.2车床精度对加工质量的影响(4)1.3保持车床高精度的方法(5)2数控车床的功能测试与与精度调整2.1数控车床功能的测试(5)2.1.1数控车床性能检测内容(5)2.1.2数控车床精度检测(6)2.1.3数控系统的检测(7)2.1.4数控车床检测的意义(7)2.2数控车床的误差及调整(8)2.2.1机械系统的调整(8)2.2.2数控车床位置精度的调整(10)2.2.3机床的几何误差(13)2.2.4基准不重合误差(16)3数控车床的保养与与维修(17)3.1正确操作和使用数控系统的步骤(17)3.2维护、设备管理(22)3.
2、3数控设备使用中应注意的问题(24)3.4数控机床的保养(24)3.5液压.气压系统的维护(26)3.6机床精度的维护(26)结术语(29)致谢(30)参考文献(31)先进的制造业装备技术水平的高低,直接影响一个国家在世界制造业的地 位。我们的国产车床及数控车床大多属于中低档产品,即使早年进口的数控机床 也因为年代久远、技术落后而面临淘汰,机床精度达不到加工高档产品的要求。 如何对我国现有的车床及数控车床保证加工质量、挖掘加工潜力是机械加工中迫 在眉睫的课题。车床作为应用广泛的机械加工设备,能否保证加工质量,在很大程度上取决 于日常的保养及规范操作及使用。为了保证车床安全平稳的运行,本文就车床
3、的 保养及精度的保证通过加工所出现的问题提出一些方法及维护建议。关键词:数控车床;维护;保养;维修1.车床精度的概述11、车床精度的基本内容车床精度包括几何精度、传动精度、定位精度以及工作精度等。不同类型的车床对这些方面的要求是不一样的。车床的几何精度,是指车床 在不工作的情况下,对车床工作精度有直接影响的零部件本身及其相互位置的几 何精度。属于这类精度的有:车床溜板移动的直线性及其与它表面间相互的不平行度; 车床主轴的径向跳动和轴向窜动,及其中心线与溜板移动方向的不平行度;主轴 锥孔中心线对车床导轨的不等距离等等。1. 2、车床精度对加工质量的影响在车床上加工工件时,影响加工质量的因素很多,
4、如车床本身的精度、工件 装夹方法、车道的几何参数、切削用量等。其中车床的精度是影响工件加工质量的关键因素。卧式车床精度对加工质量的影响见表1-1.2一序号工件产生的缺陷与车床有关的因素1车削工件时圆度超差1主轴前后轴承间隙过大2主轴轴颈的圆度超差2车圆柱形工件时产生锥度1主轴轴线对床鞍移动的平行度超差2床身导轨面严重磨损3两顶尖装夹工件时是由于尾座轴线与主轴轴 线不重合4地脚螺栓松动、车床水平变动3精车后工件端面平面度超差,圆跳 动超差1中滑板移动对主轴轴线的垂直度超差2主轴轴向窜动量超差4车削外圆时,工件素线的直线度超 差1两顶尖装夹工件时,床头和尾座两顶尖等高度 超差2床鞍移动的直线度超差
5、3利用小滑板车削时,小滑板移动对主轴轴线的 平行度超差5钻、扩、铰孔时,工件孔径扩大或 孔变为喇叭形1尾座套筒锥孔轴线对床鞍移动的平行度超差2尾座套筒轴线对床鞍移动的平行度超差3前后顶尖的等咼度超差6车削螺纹时螺距精度超差1丝杠的轴向窜动量超差2从主轴至丝杠间的传动链传动误差过大3开合螺母磨损造成啮合不良或间隙过大7车外圆时表面上有混乱的波纹1主轴滚动轴承滚道磨损,间隙过大2株洲的轴向窜动量超差3床鞍及中、小滑板滑动表面间隙过大8精车外圆时表面上轴向出现有规律 的波纹1溜板箱纵向进给小齿轮与齿条啮合不良2光杠弯曲,或光、丝杠的二孔轴线不同轴,并 与车床导轨不平行3溜板箱内某一传动齿轮(或蜗轮)
6、损坏4主轴箱、进给箱中的轴弯曲或齿轮损坏9精车外圆时圆周表面上出现有规律 的波纹1主轴的传动齿轮的齿形不良,齿部损坏或啮合 不良2电动机旋转不平衡而引起振动3带轮等旋转零件振幅过大而引起振动4主轴轴承间隙过大或过小表 11.21. 3、保持车床高精度的方法精度保持是指在正常使用条件下,机床能够较长时间保持其精度特性的能 力,主要取决于设计制造的各环节,而且和日常使用及维护有着密不可分的关 系。在日常使用过程中应规范操作,避免引起车床各部位间隙增大及磨损。经 常对机床进行润滑,尽量不在机床上加工铸铁件、锻件。加工时,吃刀量不要 太大。车床在加工偏心件时,尽量做到使工件保持平衡状态,减少对车床主轴
7、 的损害。经常调整机床拖板的间隙,使机床保持最佳状态。实际生产的普通车床上,多少都能看到撞车的痕迹。撞车会降低主轴的精 度,同时会发生安全方面的事故,应避免此类事故的发生。车床的精度不准主 要还是主轴,日常使用要注意加机油给予车床足够的润滑并及时清理切削,特 别是中滑板内部的丝杆。2数控车床的功能测试与精度调整2.1、数控车床功能的测试2.1.1、数控车床性能检测内容根据GB/T 17421机床检验通则,规定检验标准和性能评价部分:1、在无负荷或精加工条件下的几何精度;2、数控轴线的定位精度和重复定位精度的确定;3、热效应的评定;4、数控机床的圆检验;5、噪声辐射的评定;6、对角线位移检验。检
8、测部位分为:1、主轴系统(在不同转速下,手动方式连续5次正、反转的启动停止检验主轴动作的灵活性和可靠性)2、进给系统(在不同进给速度下,手动方式主轴正、反转的启 动、点动和停止动作的平稳可靠性)3、自动换刀系统(再到酷曼在条件下,通过手动方式、自动方 式检测刀具交换动作的灵活、稳定性)4、数控装置(检查各指示灯、操作面板的各功能及动作的可靠 性。数控装置于伺服驱动单元的连接电缆的可靠性)5、电气装置(在车床试运转时前后进行绝缘测试测定各单元的 绝缘性、可靠性)6、气、液装置(检测各项系统地密封性,油、气路的可靠性)7、润滑装置(检测润滑油路的可靠性,定期检测各润滑点油量 的均匀性)8、安全装置
9、(各种安全护罩的可靠性,坐标行程限位的保护功 能的可靠性)9、附属装置(各附属装置的工作情况的可靠性。10、机床噪声(试运行噪声不得超过80dB)2.1.2、数控车床精度检测精度检测主要分为几何精度检测,定位精度检测,切削精度检测 几何精度检测内容:(1)工作台的平面度。(2)各坐标方向移动时工作台 的平行度。(3) X、Y坐标方向移动时工作台面的平行度。(4)X坐标方向移动时工作台面T型槽侧面的平行度。(5) 主轴的轴向窜动。(6)主轴孔的径向跳动。(7)主轴箱沿 Z坐标方向移动时主轴轴心线的平行度。(8)主轴回转轴线 对工作台面的垂直度。(9)主轴箱在Z坐标方向移动的直线 度。定位精度检测
10、内容:(1)各直线运动轴的定位精度和重复定位精度;(2)直 线运动各轴的反向误差;(3)直线运动各轴机械原点的复归 精度;(4)回转运动的定位精度和重复数控车床定位精度;(5)回转运动的反向误差;(6)回转轴原点的复归精度。 切削精度检测内容:车削棒料试件测试切削精度。棒料试件要求包含多种开头,如:圆柱面、锥面、球面等。2.1.3、数控系统的检测数控系统的检测是对于其指令与实际加工情况是否吻合的一项重要检测内 容。数控系统的检验主要是由厂家调试时使用的考机程序来进行,由此程序来 体现出系统性能。数控系统功能决定着车床各性能指标,影响着机床的运行。214、数控车床检测的意义数控机床加工的零件质量
11、在很大程度上取决于机床自身的性能,但机床本身 的各种问题都可能导致加工零件的质量不合格。一般都是在零件加工后进行质 量检查,但发现问题,想对由零件加工质量造成的废品进行修复已为时过晚, 而且会导致长时间的停机,使得制造成本大大增加。领翔的解决办法是对机床 定期进行检测,使其保持应有的精度。影响加工中心位置精度的有关因素是:1、CNC装置采用算法的精度,2、 伺服系统检测装置的分辨率,3、伺服电机的不灵敏区,4、机械传动元件的间 隙和弹性变形,5、滚珠丝杠螺距误差的变化,6、滚珠丝杠支承系统的净、动 柔度,7、导轨副的摩擦力8、温度的变化等。在上述因素中1,2, 3项是基本 不变的,而4,5,6
12、,7,8项是变化的。目前,加工中心采用的数控系统均有误差补偿功能,在有限的范围内可以 对伺服进给系统的间隙和螺距的误差进行一定的补偿来提高加工中心的位置精 度。因此,对于一台刚出厂的加工中心而言,出厂前制造厂对其位置精度已经 用双频激光干涉仪进行了必要的检测与补偿,使其达到精度要求。然而,对于 一台使用了多年的加工中心由于磨损的客观存在,机械传动元件的间隙、导轨 副的间隙必然加大,滚珠丝杠螺距误差的补偿值不可避免的也已经发生了变化。 毋庸讳言,所有这些变化导致加工中心原有的位置精度已经不在产品刚出厂时 的状态或者说已经丧失,使得加工中心的加工精度大打折扣。这一点必须引起 加工中心用户的高度重视
13、。2.2、数控车床的调整2.2.1机械系统的调整机械系统的要达到的要求:1、高静、动刚度2、良好的抗振性3、高灵敏度4、热变形小5、高精度保持性和高可靠性调整内容:主轴部件的结构与调整、进给运动部件的调整、自动换刀装置 的调整、位置检测装置的调整、床身导轨的调整。回转运动部件:分度工作台:按最小角度的整数倍分度回转工作台;回转进给运动,实现任意角度分度及控制多齿盘分度工作台的调整加工中心回转工通过作台的调整主轴跳动或圆度不合格可通过主轴卡头重新装配或车卡头来实现精度调整。 滚珠丝杠螺母副的调整:重复定位精度可通过调整丝杠间距获得精度,下面介绍了一种调整方法。 垫片调整法(如图)垫片调隙是调整垫
14、片厚度使左右两螺母产生轴向位移,即可消除间隙和产 生的预紧力。这种方法简单,刚性好,但调整不便,滚道有磨损时不能随 时消除间隙和进行预紧。垫片 I放大图 22.1滚珠丝杠螺母副的预紧预紧力计算公式:Fv 1/3Fmaxmax进给传动系统部件的调整数控机床进给传动系统的布置形式:水平布置和垂直布置水平布置和普通车床布置形式相同,大多采用滚珠丝杠代替滑动丝杠,其形式有:一端装推力轴承、两端装推力轴承、一端推力轴承,另一端深沟球轴承、两端推力轴承及深沟球轴承。数控车床与普通车床进给系统结构布置的不同之处;1)数控机床进给传动链首端件是伺服电动机2)垂直布置的进给传动系统结构中,设置有制动装置3)齿轮
15、副采用了消除齿轮啮合间隙结构自动换刀装置的调整自动换刀装置的形式;刀库式和机械手式自动换刀装置刀库类型有:转塔式,圆盘式,链式,格子盒式。机械手类型有单臂式和回转 式单臂双手。根据自动换刀装置的类型做相应的调整。刀塔精度根据后方电机和刀塔装配位 置调整。床身导轨的调整床身需要稳定的机床基础,否则精度调整无法进行。在机床安装时要做好机床 地基,并经过一段时间的保养使其稳定。导轨需要保持润滑,防止磨损锈蚀。调整床身的水平度和机床主要几何精度, 主要运动部件与主机的相对位置。2.2. 2、数控车床位置精度的调整目前数控机床位置精度的检验通常采用国际标准IS0230-2或国家 标准GB10931-89
16、等。同一台机床,由于采用的标准不同,所得到的位置精度 也不相同,因此在选择数控机床的精度指标时,也要注意它所采用的标准。 数控机床的位置标准通常指各数控轴的反向偏差和定位精度。对于这二者的 测定和补偿是提高加工精度的必要途径。一、反向偏差在数控机床上,由于各坐标轴进给传动链上驱动部件(如伺服电动 机、伺服液压马达和步进电动机等)的反向死区、各机械运动传动副的反向 间隙等误差的存在,造成各坐标轴在由正向运动转为反向运动时形成反向偏 差,通常也称反向间隙或失动量。对于采用半闭环伺服系统的数控机床,反 向偏差的存在就会影响到机床的定位精度和重复定位精度,从而影响产品的 加工精度。如在G01切削运动时
17、,反向偏差会影响插补运动的精度,若偏差过 大就会造成“圆不够圆,方不够方”的情形;而在00快速定位运动中,反向 偏差影响机床的定位精度,使得钻孔、镗孔等孔加工时各孔间的位置精度降 低。同时,随着设备投入运行时间的增长,反向偏差还会随因磨损造成运动 副间隙的逐渐增大而增加,因此需要定期对机床各坐标轴的反向偏差进行测 定和补偿。反向偏差的测定反向偏差的测定方法:在所测量坐标轴的行程内,预先向正向或反 向移动一个距离并以此停止位置为基准,再在同一方向给予一定移动指令值, 使之移动一段距离,然后再往相反方向移动相同的距离,测量停止位置与基 准位置之差。在靠近行程的中点及两端的三个位置分别进行多次测定(
18、一般 为七次),求出各个位置上的平均值,以所得平均值中的最大值为反向偏差 测量值。在测量时一定要先移动一段距离,否则不能得到正确的反向偏差值。测量直线运动轴的反向偏差时,测量工具通常采有千分表或百分表,若 条件允许,可使用双频激光干涉仪进行测量。当采用千分表或百分表进行测 量时,需要注意的是表座和表杆不要伸出过高过长,因为测量时由于悬臂较 长,表座易受力移动,造成计数不准,补偿值也就不真实了。若采用编程法 实现测量,则能使测量过程变得更便捷更精确。例如,在三坐标立式机床上测量X轴的反向偏差,可先将表压住主轴的 圆柱表面,然后运行下程序来测量:N10 G91 G01 X50 F1000;工作台右
19、移N20 X-50;工作台左移并消除传动间隙N30 G04 X5;暂停以便观察N40 Z50;Z轴抬高让开N50 X-50; 工作台左移N60 X50; 工作台右移复位N70 Z-50;Z轴复位N80 G04 X5;暂停以便观察N90 M99.需要注意的是,在工作台不同的运行速度下所测出的结果会有所不同。 一般情况下,低速的测出值要比高速的大,特别是在机床轴负荷和运动阻力 较大时。低速运动时工作台运动速度较低,不易发生过冲超程(相对“反向 间隙”),因此测出值较大;在高速时,由于工作台速度较高,容易发生过 冲超程,测得值偏小。反向偏差的补偿国产数控机床,定位精度有不少0.02mm,但没有补偿功
20、能。对这类 机床,在某些场合下,可用编程法实现单向定位,清除反向间隙,在机械部 分不变的情况下,只要低速单向定位到达插补起始点,然后再开始插补加工。 插补进给中遇反向时,给反向间隙值再正式插补,即可提高插补加工的精度, 基本上可以保证零件的公差要求。对于其他类别的数控机床,通常数控装置内存中设有若干个地址, 专供存储各轴的反向间隙值。当机床的某个轴被指令改变运动方向时,数控 装置会自动读取该轴的反向间隙值,对坐标位移指令值进行补偿、修正,使 机床准确地定位在指令位置上,消除或减小反向偏差对机床精度的不利影响。一般数控系统只有单一的反向间隙补偿值可供使用,为了兼顾高、低速 的运动精度,除了要在机
21、械上做得更好以外,只能将在快速运动时测得的反 向偏差值作为补偿值输入,因此难以做到平衡、兼顾快速定位精度和切削时 的插补精度。对于FANUCOi、FANUC18i等数控系统,有用于快速运动(G00)和低 速切削进给运动(G01)的两种反向间隙补偿可供选用。根据进给方式的不同, 数控系统自动选择使用不同的补偿值,完成较高精度的加工。将G01切削进给运动测得的反向间隙值A输入参数NO11851(G01的 测试速度可根据常用的切削进给速度及机床特性来决定),将GO0测得的反向 间隙值B输入参数NO11852。需要注意的是,若要数控系统执行分别指定的反 向间隙补偿,应将参数号码1800的第四位(RBK
22、)设定为1;若RBK设定为0, 则不执行分别指定的反向间隙补偿。G02、G03、JOG与G01使用相同的补偿值。二、定位精度数控机床的定位精度是指所测量的机床运动部件在数控系统控制下 运动所能达到的位置精度,是数控机床有别于普通机床的一项重要精度,它 与机床的几何精度共同对机床切削精度产生重要的影响,尤其对孔隙加工中 的孔距误差具有决定性的影响。一台数控机床可以从它所能达到的定位精度 判出它的加工精度,所以对数控机床的定位精度进行检测和补偿是保证加工 质量的必要途径。定位精度的测定目前多采用双频激光干涉仪对机床检测和处理分析,利用激光干涉 测量原理,以激光实时波长为测量基准,所以提高了测试精度
23、及增强了适用 范围。检测方法如下:安装双频激光干涉仪;在需要测量的机床坐标轴方向上安装光学测量装置;调整激光头,使测量轴线与机床移动轴线共线或平行,即将光路预调准 直;待激光预热后输入测量参数;按规定的测量程序运动机床进行测量;数据处理及结果输出。定位精度的补偿若测得数控机床的定位误差超出误差允许范围,则必须对机床进行 误差补偿。常用方法是计算出螺距误差补偿表,手动输入机床CNC系统,从而 消除定位误差,由于数控机床三轴或四轴补偿点可能有几百上千点,所以手 动补偿需要花费较多时间,并且容易出错。现在通过RS232接口将计算机与机床CNC控制器联接起来,用VB编写 的自动校准软件控制激光干涉仪与
24、数控机床同步工作,实现对数控机床定位 精度的自动检测及自动螺距误差补偿,其补偿方法如下:备份CNC控制系统中的已有补偿参数;由计算机产生进行逐点定位精度测量的机床CNC程序,并传送给CNC系统; 自动测量各点的定位误差;根据指定的补偿点产生一组新的补偿参数,并传送给CNC系统,螺距自动 补偿完成;重复c.进行精度验证。2.2.3、机床的几何误差加工中刀具相对于工件的成形运动一般都是通过机床完成的,因此,工件的 加工精度在很大程度上取决于机床的精度。机床制造误差对工件加工精度影响较 大的有:主轴回转误差、导轨误差和传动链误差。机床的磨损将使机床工作精度 下降。1)主轴回转误差,机床主轴是装夹工件
25、或刀具的基准,并将运动和动力传 给工件或刀具,主轴回转误差将直接影响被加工工件的精度。主轴回转误差是指主轴各瞬间的实际回转轴线相对其平均回转轴线的变动 量。它可分解为径向圆跳动、轴向窜动和角度摆动三种基本形式,如下图。a)径向圆跳动b)端面圆跳动c)倾角摆动主轴回转误差基本形式产生主轴径向回转误差的主要原因有:主轴几段轴颈的同轴度误差、轴承本 身的各种误差、轴承之间的同轴度误差、主轴绕度等。但它们对主轴径向回转精 度的影响大小随加工方式的不同而不同。产生轴向窜动的主要原因是主轴轴肩端面和轴承承载端面对主轴回转轴线 有垂直度误差。不同的加工方法,主轴回转误差所引起的的加工误差也不同。在 车床上加
26、工外圆和内孔时,主轴径向回转误差可以引起工件的圆度和圆柱度误 差,但对加工工件端面则无直接影响。主轴轴向回转误差对加工外圆和内孔的影响不大,但对所加工端面的垂直度及平面度则有较大的影响。在车螺纹时,主轴 向回转误差可使被加工螺纹的导程产生周期性误差。适当提高主轴及箱体的制造精度,选用高精度的轴承,提高主轴部件的装配 精度,对高速主轴部件进行平衡,对滚动轴承进行预紧等,均可提高机床主轴的 回转精度。2)导轨误差:导轨是机床上确定各机床部件相对位置关系的基准,也是机 床运动的基准。除了导轨本身的制造误差外,导轨的不均匀磨损和安装质量,也 使造成导轨误差的重要因素。导轨磨损是机床精度下降的主要原因之
27、一。3)传动链误差:传动链误差是指传动链始末两端传动元件间相对运动的误 差。一般用传动链末端元件的转角误差来衡量。传动误差是由传动链中各组成环 节的制造和装配误差,以及使用过程中的磨损所引起。以车螺纹为例,说明传动 链精度对工件加工精度的影响,如图所示:工件导程误差可表示为:由丝杠副传动误图 2-2.3a由传动链总传动比 误差引起的误差4)刀具的几何误差:刀具误差对加工精度的影响随刀具种类的不同而不同。 任何刀具在切削过程中,都不可避免要产生磨损,并由此引起工件尺寸和形状地 改变。正确地选用刀具材料和选用新型耐磨的刀具材料,合理地选用刀具几何参 数和切削用量,正确地采用冷却液等,均能最大限度地
28、减少刀具的尺寸磨损。 必要时还可采用补偿装置对刀具尺寸磨损进行自动补偿。一般刀具的尺寸磨损对加工精度的影响:一般刀具如:车刀、立铣刀等,主要靠调整刀具位置来保证加工尺寸,其制造精度不会影响加工尺寸精度。但刀具的磨损将对工件的加工精度 产生影响如下图。刀具磨损误差图223b2.2.4、基准不重合误差在零件图上用来确定某一表面尺寸、位置所依据的基准称为设计基准。在工 序图上用来确定本工序被加工表面加工后的尺寸、位置所依据的基准称为工序基 准。一般情况下,工序基准应与设计基准重合。在机床上对工件进行加工时,须 定位基准与设计基准不重合时所产生的基准不重合误差,只有在采用调整法加工 时才会产生,在试切
29、法加工中不会产生。如下图所示,工序尺寸B的基准是D面, 定位基准是F面,工序基准与定位基准不重合。工序基准与定位基准之间的联系 尺寸为LA L,槽的的位置相对定位基准一定,由于工序基准相对定位基准存 在误差AL,使得工序基准在一定范围内变动,从而造成这批工件工序尺寸B 存在不重合的加工误差。 B = 2A L。如图所示,工序基准为F面,定位基准为 E面,基准不重合。尺寸C一定时,由于定位基准E面的误差,加工误差为定位 误差 B二SmaxSmin=6 s(1) 定位误差只产生在调法加工一批工件的条件下,采用试切法加工,不存 在定位误差。(2) 定位误差产生的原因是工件的制造误差和定位元件的制造误
30、差,即两者 的配合间隙和工序基准相对定位基准的误差。(3) 定位误差由基准位移误差和基准不重合组成。定位基准与工序基准重合 时厶B = 0 ,定位基准无变动时 Y = 0。定位误差 D=A YA B。3.数控机床的保养与维修数控机床的维修概念,不能单纯局限于数控系统发生故障时,如何排除故障 和及时修复,使数控系统尽早投入使用,还应包括正确使用和日常保养等。3.1正确操作和使用数控系统的步骤数控系统通电前的检查(1) 检查CNC装置内的各个印刷线路板是否紧固,各个插头有无松动。(2) 认真检查CNC装置与外界之间的全部连接电缆是否按随机提供的连接手 册的规定,正确而可靠地连接。(3) 交流输入电
31、源的连接是否符合CNC装置规定的要求。(4) 确认CNC装置内的各种硬件设定是否符合CNC装置的要求。只有经过上述检查,CNC装置才能投入通电运行。数控系统通电后的检査(1) 首先要检查数控装置中各个风扇是否正常运转。(2) 确认各个印刷线路或模块上的直流电源是否正常,是否在允许的波动范 围之内。(3) 进一步确认CNC装置的各种参数。(4) 当数控装置与机床联机通电时,应在接通电源的同时,作为按压紧急停 止按钮的准备,以备出现紧急情况时随时切断电源。(5) 用手动以低速给移动各个轴,观察机床移动方向的显示是否正确。(6) 进行几次返回机床基准点的动作,用来检查数控机床是否有返回基准点 功能,
32、以及每次返回基准点的位置是否完全一致。(7) CNC装置的功能测试。CNC系统的日常维护(1) 制订CNC系统的日常维护的规章制度。(2) 应尽量少开数控柜和强电柜的门。(3) 定时清理数控装置的散热通风系统。(4) CNC系统的输入/输出装置的定期维护。(5) 定期检查和更换直流电机电刷。(6) 经常监视CNC装置用的电网电压。(7) 存储器用电池的定期更换。(8) CNC系统长期不用时的维护。(9) 备用印刷线路板的维护。对于已购置的备用印刷线路板应定期装到CNC 装置上通电运行一段时间,以防损坏。做好维修前期的准备工作:1) 技术准备:维修人员应在平时充分了解系统的性能。2) 工具准备:
33、作为最终用户,维修工具只需准备一些常规的仪器设备,如交 流电压表,直流电压表,可能用指针式的也可以是数字式的,测量误差在土 2%范 围内即可。万用表也是一种常用的仪表。3) 备件准备:一旦由于CNC系统的部件或元器件损坏,使系统发生故障。为能及时排除故障,用户应准备一些常用的备件。故障处置一旦CNC系统发生故障,系统操作人员应采取急停措施,停止系统运行,保 护好现场。(1)故障的表现1)系统发生故障的工作方式工作方式有:Tape (纸带方式)、MDI (手动数据输入方式)、MEMORY (存储 器方式)、EDIT (编辑)、HANDLE (手轮)、JOG (点动)方式。2)MDI/DPL (手
34、动数据输入/显示)。3)系统状态显示有时系统发生故障时却没有报警,此时需要通过诊断画面观 察系统所处的状态。4)定位误差超差情况。5)在CRT上的报警及报警号。6)刀具轨迹出现误差时的速度。(2)故障的频繁程度1)故障发生的时间及频率。2)加工同类工件时,发生故障的概率。3)故障发生的方式,判别是否与进给速度、换刀方式或是与螺纹切削有关。4)出现故障的程序段。(3)故障的重复性1)将引起故障的程序段重复执行多次进行观察,来考察故障的重复性。2)将该程序段的编程值与系统内的实际数值进行比较,确认两者是否有差 异。3)本系统以前是否发生过同样故障?(4)外界状况1)环境温度。2)周围的振动源。3)
35、系统的安装位置检查,出故障时是否受到阳光的直射等。4)切削液、润滑油是否飞溅到了系统柜、系统柜里是否进水,受到水的浸渍(如暖气漏水)等。5)输入电压调查,输入电源是否有波动、电压值等。6)工厂内是否有使用大电流的装置。7)近处是否存在干扰源。8)附近是否正在修理或调试机床、安装了新机床等。9)重复出现的故障是否与外界因素有关?(5)有关操作情况1)经过什么操作之后才发生的故障?2)机床的操作方式对吗?3)程序内是否包含有增量指令?(6)机床情况1)机床调整状况。2)机床在运输过程中是否发生振动?3)所用刀具的刀尖是否正常?4)换刀时是否设置了偏移量?5)间隙补偿给的是否恰当?6)机械另件是否随
36、温度变化而变形?7)工件测量是否正确?(7)运转情况1)在运转过程中是否改变过或调整过运转方式?2)机床侧是否处于报警状态?是否已作好运转准备?3)机床操作面板上的售开关是否设定为“ 0”?4)机床是否处于锁住状态?5)系统是否处于急停状态?6)系统的保险丝是否烧断?7)机床操作面板上的方式选择开关设定是否正确?(8)机床和系统之间接线情况 电缆是否完整无损? 交流电源线和系统内部电线是否分开安装? 电源线和信号线是否分开走线? 信号屏蔽线接地是否正确? 继电器、电磁铁以及电动机等电磁部件是否装有噪声抑制器?(9)CNC装置的外观检查1)机柜。检查破损情况和是否是在打开柜门的状态下操作。2 )
37、机柜内部。风扇电机工作是否正常?控制部分污染程序。3)纸带阅读机。纸带阅读机是否有污物?4 )电源单元。保险丝是否正?5 )电缆。电缆连接器插头是否完全插入、拧紧?6)印刷线路板。印刷线路板数量有无缺损?7)MDI/C7RT 单元。(10)有关穿孔纸带的检査1)纸带阅读机天关是否正常?2)有关纸带操作的设定是否正确?3)纸带是否折、皱和存有污物?4)纸带的连接处正常否?5)纸带上的孔有无破损?6)这条纸带是否用过?7)使用的是黑色纸带还是其它颜色的纸带?故障检査方法(1)直观法这是一种最基本的方法。维修人员通过对故障发生时的各种光、声、味等异 常现象的观察以及认真察看系统的每一处,往往可将故障
38、范围缩小到一个模块或 一块印刷线路板。这要求维修人员具有丰富的实际经验,要有多学科的较宽的知 识和综合判断的能力。(2)自诊断功能法现代的数控系统虽然尚未达到智能化很高的程度,但已经具备了较强的自诊 断功能。能随时监视数控系统的硬件和软件的工作状况。一旦发现异常,立即在C RT上报警信息或用发光二极管批示出故障的大致起因。利用自诊断功能,也能显 示出系统与主机之间接口信号的状态,从而判断出故障发生在机械部分还是数控 系统部分,并批示出故障的大致部位。这个方法是当前维修时最有效的一种方法。(3)功能程序测试法所谓功能程序测试法就是将数控系统的常用功能和特殊功能,如直线定位、 圆弧插补、螺纹切削、
39、固定循环、用户宏程序等用手工编程或自动编程方法,编 制成一个功能程序测试纸带,通过纸带阅读机送入数控系统中,然后启动数控系 统使之进行运行,藉以检查机床执行这些功能的准确性和可靠性,进而判断出故 障发生的可能起因。本方法对于长期闲置的数控机床第一次开机时的检查以及机 床加工造成废品但又无报警的情况下,一时难以确定是编程错误或是操作错误, 还是机床故障时的判断是一较好的方法。(4)交换法这是一种简单易行的方法,也是现场判断时最常用的方法之一。所谓交换法 就是在分析出故障大致起因的情况下,维修人员可以利用备用的印刷线路板、模 板,集成电路芯片或元器件替换有疑点的部分,从而把故障范围缩小到印刷线路
40、板或芯片一级。它实际上也是在验证分析的正确性。在备板交换之前,应仔细检查备板是否完好,并应检查备板的状态应与原板 状态完全一致。这包括检查板上的选择开关,短路棒的设定位置以及电位器的位 置。在置换CNC装置的存储器板时,往往还需要对系统作存储器的初始化操作(如 日本FANUC公司的FS6系统用的磁泡存储器就需要进行这项工作),重新设定 各种数控数据,否则系统仍将不能正常地工作。又如更换FANUC公司的7系统的 存储器板之后,需重新输入参数,并对存储器区进行分配操作。缺少了后一步, 一旦零件程序输入,将产生60号报警(存储器容量不够)。有的CNC系统在更换 了主板之后,带需进行一些特定的操作。如
41、FNUC3.2维护、设备管理转移法所谓转移法就是将CNC系统中具有相同功能的二块印刷线路板、模块、集成 电路芯片或元器件互相交换,观察故障现象是否随之转移。藉此,可迅速确定系 统的故障部位。这个方法实际上就是交换法的一种。因此,有关注意事项同交换 法所述。参数检査法众所周知,数控参数能直接影响数控机床的功能。参数 通常是存放在磁泡 存储器或存放在需由电池保持的CMOS RAM中,一旦电池不足或由于外界的某种 干扰等因素,会使个别参数丢失或变化,发生混乱,使机床无法正常工作。此时, 通过核对、修正参数,就能将故障排除。当机床长期闲置工作时无缘无故地出现 不正常现象或有故障而无报警时,就应根据故障
42、特征,检查和校对有关参数。另外,经过长期运行的数控机床,由于其机械传动部件磨损,电气无件性能 变化等原因,也需对其有关参数进行调整。有些机床的故障往往就是由于未及时 修改某些不适应的参数所致。当然这些故障都是属于故障的范畴.测量比较法CNC系统生产厂在设计印刷线路板时,为了调整、维修的便利,在印刷线路 板上设计了多个检测用端子。用户也可利用这些端子比较测量正常的印刷线路板 和有故障的印刷线路板之间的差异。可以检测这些测量端子的电压或波形,分析 故障的起因及故障的所在位置。甚至,有时还可对正常的印刷线路人为地制造“故障”,如断开连线或短路,拨去组件等,以判断真实故障的起因。为此,维 修人员应在平
43、时积累印刷线路板上关键部位或易出故障部位在正常时的正确波 形和电压值。因为CNC系统生产厂往往不提供有关这方面的资料。敲击法当系统出现的故障表现为若有若无时,往往可用敲击法检查出故障的部位所 在。这是由于CNC系统是由多块印刷线路板组成,每块板上又有许多焊点,板间 或模块间又通过插接件及电缆相连。因此,任何虚焊或接触不良,都可能引起故 障。当用绝缘物轻轻敲打有虚焊及接触不良的疑点处,故障肯定会重复再现。局部升温CNC系统经过长期运行后元器件均要老化,性能会变坏。当它们尚未完全损 坏时,出现的故障变得时有时无。这时可用热吹风机或电烙铁等来局部升温被怀 疑的元器件,加速其老化,以便彻底暴露故障部件
44、。当然,采用此法时,一定要 注意元器件的温度参数等,不要将原来是好的器件烤坏。10.原理分析法根据CNC系统的组成原理,可从逻辑上分析各点的逻辑电平和特征参数(如 电压值或波形),然后用万用表、逻辑笔、示波器或逻辑分析仪进行测量、分析 和比较,从而对故障定位。运用这种方法,要求维修人员必须对整个系统或每个 电路的原理有清楚的、较深的了解。除了以上常用的故障检查测试方法外,还有拔板法,电压拉偏法,开环检测 法以及在上章中曾提出的诊断方法等多种。这些检查方法各有特点,按照不同的 故障现象,可以同时选择几种方法灵活应用,对故障进行综合分析,才能逐步缩 小故障范围,较快地排除故障。3.3数控设备使用中
45、应注意的问题数控设备的使用环境为提高数控设备的使用寿命,一般要求要避免阳光的直接照射和其他热辐 射,要避免太潮湿、粉尘过多或有腐蚀气体的场所。精密数控设备要远离振动大 的设备,如冲床、锻压设备等。良好的电源保证为了避免电源波动幅度大(大于10%)和可能的瞬间干扰信号等影响,数 控设备一般采用专线供电(如从低压配电室分一路单独供数控机床使用)或增设 稳压装置等,都可减少供电质量的影响和电气干扰。制定有效操作规程在数控机床的使用与管理方面,应制定一系列切合实际、行之有效的操作规 程。例如润滑、保养、合理使用及规范的交接班制度等,是数控设备使用及管理 的主要内容。制定和遵守操作规程是保证数控机床安全
46、运行的重要措施之一。实 践证明,众多故障都可由遵守操作规程而减少。数控设备不宜长期封存购买数控机床以后要充分利用,尤其是投入使用的第一年,使其容易出故障 的薄弱环节尽早暴露,得以在保修期内得以排除。加工中,尽量减少数控机床主 轴的启闭,以降低对离合器、齿轮等器件的磨损。没有加工任务时,数控机床也 要定期通电,最好是每周通电12次,每次空运行1小时左右,以利用机床本 身的发热量来降低机内的湿度,使电子元件不致受潮,同时也能及时发现有无电 池电量不足报警,以防止系统设定参数的丢失。34数控机床的保养数控机床种类多,各类数控机床因其功能,结构及系统的不同,各具不同的 特性。其维护保养的内容和规则也各
47、有其特色,具体应根据其机床种类、型号及 实际使用情况,并参照机床使用说明书要求,制订和建立必要的定期、定级保养 制度。下面是一些常见、通用的日常维护保养要点。 严格遵守操作规程和日常维护制度数控设备操作人员要严格遵守操作规程和日常维护制度,操作人员的技术业 务素质的优劣是影响故障发生频率的重要因素。当机床发生故障时,操作者要注 意保留现场,并向维修人员如实说明出现故障前后的情况,以利于分析、诊断出 故障的原因,及时排除。(2) 防止灰尘污物进入数控装置内部在机加工车间的空气中一般都会有油雾、灰尘甚至金属粉末,一旦它们落在 数控系统内的电路板或电子器件上,容易引起元器件间绝缘电阻下降,甚至导致
48、元器件及电路板损坏。有的用户在夏天为了使数控系统能超负荷长期工作,采取 打开数控柜的门来散热,这是一种极不可取的方法,其最终将导致数控系统的加 速损坏,应该尽量减少打开数控柜和强电柜门。(3) 防止系统过热应该检查数控柜上的各个冷却风扇工作是否正常。每半年或每季度检查一次 风道过滤器是否有堵塞现象,若过滤网上灰尘积聚过多,不及时清理,会引起数 控柜内温度过高。(4) 数控系统的输入/输出装置的定期维护80年代以前生产的数控机床,大多带有光电式纸带阅读机,如果读带部分 被污染,将导致读入信息出错。为此,必须按规定对光电阅读机进行维护。(5) 直流电动机电刷的定期检查和更换直流电动机电刷的过度磨损
49、,会影响电动机的性能,甚至造成电动机损坏。 为此,应对电动机电刷进行定期检查和更换。数控车床、数控铣床、加工中心等, 应每年检查一次。(6) 定期检査和更换存储用电池一般数控系统内对CMOS RAM存储器件设有可充电电池维护电路,以保证系 统不通电期间能保持其存储器的内容。在一般情况下,即使尚未失效,也应每年 更换一次,以确保系统正常工作。电池的更换应在数控系统供电状态下进行,以 防更换时RAM内信息丢失。备用电路板的维护备用的印制电路板长期不用时,应定期装到数控系统中通电运行一段时间,以 防损坏。主传动链的维护定期调整主轴驱动带的松紧程度,防止因带打滑造成的丢转现象;检查主轴 润滑的恒温油箱
50、、调节温度范围,及时补充油量,并清洗过滤器;主轴中刀具夹 紧装置长时间使用后,会产生间隙,影响刀具的夹紧,需及时调整液压缸活塞的 位移量。(2)滚珠丝杠螺纹副的维护定期检查、调整丝杠螺纹副的轴向间隙,保证反向传动精度和轴向刚度;定 期检查丝杠与床身的连接是否有松动;丝杠防护装置有损坏要及时更换,以防灰 尘或切屑进入。(3)刀库及换刀机械手严禁把超重、超长的刀具装入刀库,以避免机械手换刀时掉刀或刀具与工件、 夹具发生碰撞;经常检查刀库的回零位置是否正确,检查机床主轴回换刀点位置 是否到位,并及时调整;开机时,应使刀库和机械手空运行,检查各部分工作是 否正常,特别是各行程开关和电磁阀能否正常动作;
51、检查刀具在机械手上锁紧是 否可靠,发现不正常应及时处理。3.5液压、气压系统维护定期对各润滑、液压、气压系统的过滤器或分滤网进行清洗或更换;定期对 液压系统进行油质化验检查、添加和更换液压油;定期对气压系统分水滤气器放 水。3.6机床精度的维护定期进行机床水平和机械精度检查并校正。机械精度的校正方法有软硬两 种。其软方法主要是通过系统参数补偿,如丝杠反向间隙补偿、各坐标定位精度 定点补偿、机床回参考点位置校正等;硬方法一般要在机床大修时进行,如进行导轨修刮、滚珠丝杠螺母副预紧调整反向间隙等。以下是某加工中心日常保养维护(表1),可供制订有关保养制度时参考3位梅香耍求内容)1毎天导轨润滑油檢杳釉
52、量 及时添仙润滑 油润滑油泵是否能定时启 动打油及停止2毎无主釉润滑恒温油繼工ft杲古止常r油量是好充 足温度范園是否合适每夫机床液压垂统油箱憋麹汲异常噪声 工作油面咼度杲否合适土 /.;边期不是否止常管路及 各接乱有无泄漏4厨天压縮空气气源压力气动控制系统压力是否在 正常范围之内5.毎天气源自鹽器自动空气干 燥器及时洁理分水皺遽蚩的 水分保证自动空气干燥器 工作正常$毎天.气液转换器和増压油面油屋不够时要及时补充足.7毎无X. Y: Z 轴导轨面涪際切凰和污物检杳导轨 面有无划饬损坏,润滑抽是 否充足8 .毎天CNC输悶输出单元如光电阅读机的涪洁机械润滑是否良好9毎天各防护装置导轨“盛味防护
53、罩等是否安 全毎效10毎天恕通斑裟置答电气柜中冷却凤扇是否 工作正常趣遽网有无 堵塞;及时溶除过滤器11毎周各电气拒过虑翩诸除粘附的尘土12不定 朋水藕陡时檢查澈面肓度即时添 水人必要时要更 换*潘诜油藉 ?Kffi J和过13不定 期厦油池泾的脈進积存在废油池中 的展油以免溢出14不定 期排鞭经养理切屑-检杳有无卡注等现象15半年检杳主轴呃动皮带按枇底说明书要求调整菠带的袪紧程度16半年蘇表気滚轮OlSffi明书要求调整松8紧程度结术语目前机械制造业发展迅猛,在机械加工方面已取得了一些成果。随着我国 机械制造业的发展和各种各样零件的需求与日俱增,机械加工精度必然要求更 精。然而在实际生产中,
54、部分厂家的维护工作不到位,并导致部分普通车床规定 的精度要求却无法加工出要求精度的工件,数控车床也有此例。普车与数车的精 度保证还是在于日常使用及维护中体现。通过实践证明,提高机械加工精度要从 加工设备及加工方法入手,首先要保证设备的精度,对影响车床精度因素的深入 分析,并找出原因,提出了相应的措施,使机械加工技术进一步完善,并对机械 加工技术起到一定的指导作用。研究我国现有车床的精度与潜力的发掘是目前我 国市场变化和需求所要求的,有很大的意义。致谢不知不觉就要毕业了,再回首,还记得老师们的谆谆教导,还记得他们在讲 台上传授知识的姿态,感慨颇深!大三是一个向社会转型的时期,在院系领导以 及各位老师的认真教导下,我明白了许多,学到了很多东西,这对我很有帮助。在此,谨向各位领导和老师们表示万分诚恳的感激!他们教导我要有敢想, 敢做的良好学习心态,不要怕失败,不要畏缩不前,要不怕吃苦,认真仔细对待 问题。老师的教导不仅使我顺利完成论文,还教会我很多道理。再次向各位老师 的认真教导表示感谢!同时也感谢各位同学曾给予的帮助!参考文献1王侃夫,数控机床故障诊断及维护M北京:机械工业出版社,20032熊军,数控机床维修与调整M北京:人民邮电出版社,20073杨治平,机械精度设计与检测技术基础M北京:机械工业出版社,20044王公安,车工工艺学M北京:中国劳动社会保障出版社,2005
- 温馨提示:
1: 本站所有资源如无特殊说明,都需要本地电脑安装OFFICE2007和PDF阅读器。图纸软件为CAD,CAXA,PROE,UG,SolidWorks等.压缩文件请下载最新的WinRAR软件解压。
2: 本站的文档不包含任何第三方提供的附件图纸等,如果需要附件,请联系上传者。文件的所有权益归上传用户所有。
3.本站RAR压缩包中若带图纸,网页内容里面会有图纸预览,若没有图纸预览就没有图纸。
4. 未经权益所有人同意不得将文件中的内容挪作商业或盈利用途。
5. 装配图网仅提供信息存储空间,仅对用户上传内容的表现方式做保护处理,对用户上传分享的文档内容本身不做任何修改或编辑,并不能对任何下载内容负责。
6. 下载文件中如有侵权或不适当内容,请与我们联系,我们立即纠正。
7. 本站不保证下载资源的准确性、安全性和完整性, 同时也不承担用户因使用这些下载资源对自己和他人造成任何形式的伤害或损失。