线切割加工模具的工艺要点分析
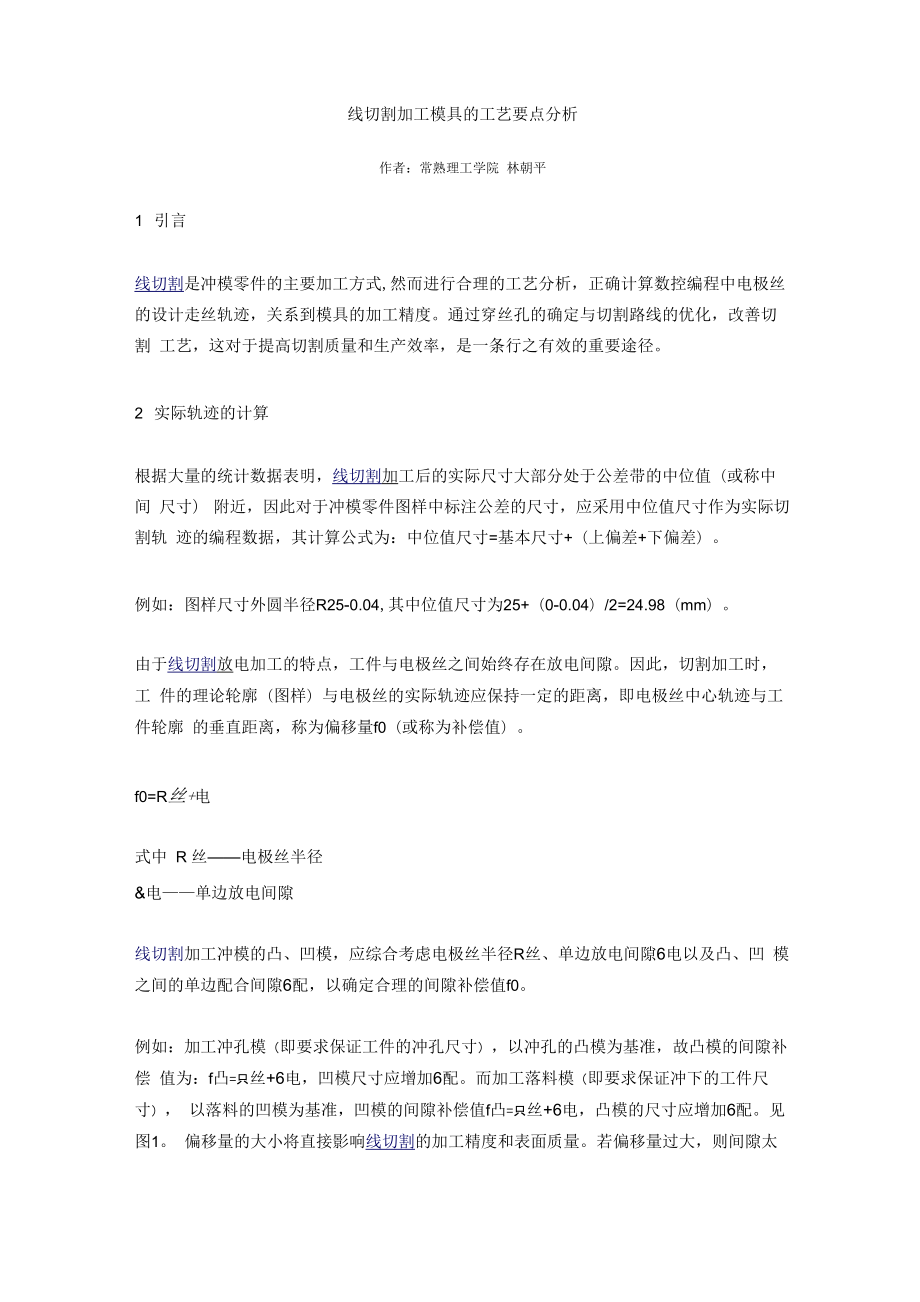


《线切割加工模具的工艺要点分析》由会员分享,可在线阅读,更多相关《线切割加工模具的工艺要点分析(5页珍藏版)》请在装配图网上搜索。
1、线切割加工模具的工艺要点分析作者:常熟理工学院 林朝平1 引言线切割是冲模零件的主要加工方式,然而进行合理的工艺分析,正确计算数控编程中电极丝 的设计走丝轨迹,关系到模具的加工精度。通过穿丝孔的确定与切割路线的优化,改善切割 工艺,这对于提高切割质量和生产效率,是一条行之有效的重要途径。2 实际轨迹的计算根据大量的统计数据表明,线切割加工后的实际尺寸大部分处于公差带的中位值(或称中间 尺寸) 附近,因此对于冲模零件图样中标注公差的尺寸,应采用中位值尺寸作为实际切割轨 迹的编程数据,其计算公式为:中位值尺寸=基本尺寸+(上偏差+下偏差)。例如:图样尺寸外圆半径R25-0.04,其中位值尺寸为25
2、+(0-0.04)/2=24.98(mm)。由于线切割放电加工的特点,工件与电极丝之间始终存在放电间隙。因此,切割加工时,工 件的理论轮廓(图样)与电极丝的实际轨迹应保持一定的距离,即电极丝中心轨迹与工件轮廓 的垂直距离,称为偏移量f0(或称为补偿值)。f0=R丝+电式中 R 丝电极丝半径&电单边放电间隙线切割加工冲模的凸、凹模,应综合考虑电极丝半径R丝、单边放电间隙6电以及凸、凹 模之间的单边配合间隙6配,以确定合理的间隙补偿值f0。例如:加工冲孔模(即要求保证工件的冲孔尺寸),以冲孔的凸模为基准,故凸模的间隙补偿 值为:f凸=只丝+6电,凹模尺寸应增加6配。而加工落料模(即要求保证冲下的工
3、件尺寸), 以落料的凹模为基准,凹模的间隙补偿值f凸=只丝+6电,凸模的尺寸应增加6配。见图1。 偏移量的大小将直接影响线切割的加工精度和表面质量。若偏移量过大,则间隙太大,放电 不稳定,影响尺寸精度;偏移量过小,则间隙太小,会影响修切余量。修切加工时的电参数将依次减弱,非电参数也应作相应调整,以提高加工质量。电梅丝中心轨进(a)b)图 1 凸模与凹模的间隙补偿值(a)凸模(b)凹模根据实践经验,线切割加工冲裁模具的配合间隙应比国际上所流行的大间隙冲模(手册 推荐值)应小些。因为凸、凹模线切割加工中,工件表面会形成一层组织脆松的熔化层,电 参数越大,表面粗糙度越差,熔化层较厚。且随着模具冲裁次
4、数的增加,这层脆松的表层会 逐渐磨损,使模具的配合间隙逐渐增大,满足 大 间隙的要求。3 穿丝孔的确定穿丝孔的位置对于加工精度及切割速度关系甚大。通常,穿丝孔的位置最好选在已知轨迹尺 寸的交点处或便于计算的坐标点上,以简化编程中有关坐标尺寸的计算,减少误差。当切割 带有封闭型孔的凹模工件时,穿丝孔应设在型孔的中心,这样既可准确地加工穿丝孔,又较 方便地控制坐标轨迹的计算,但无用的切入行程较长。对于大的型孔切割,穿丝孔可设在靠 近加工轨迹的边角处,以缩短无用行程。在切割凸模外形时,应将穿丝孔选在型面外,最好 设在靠近切割起始点处。切割窄槽时,穿丝孔应设在图形的最宽处,不允许穿丝孔与切割轨 迹发生
5、相交现象。此外,在同一块坯件上切割出两个以上工件时,应设置各自独立的穿丝孔, 不可仅设一个穿丝孔一次切割出所有工件。切割大型凸模时,有条件者可沿加工轨迹设置数 个穿丝孔,以便切割中发生断丝时能够就近重新穿丝,继续切割。穿丝孔的直径大小应适宜,一般为02mm08mm。若孔径过小,既增加钻孔难度又不方 便穿丝;若孔径太大,则会增加钳工工作量。如果要求切割的型孔数较多,孔径太小,排布 较为密集,应采用较小的穿丝孔(00.3mm00.5mm),以避免各穿丝孔相互打通或发生干涉现象。4 切割路线的优化切割路线的合理与否将关系到工件变形的大小。 因此,优化切割路线有利于提高切割质量和缩短加工时间。切割路线
6、的安排应有利于工件在 加工过程中始终与装夹支撑架保持在同一坐标系内,避免应力变形的影响,并遵循以下原则。(1) 一般情况下,最好将切割起始点安排在靠近夹持端,将工件与其夹持部分分离的切割段 安排在切割路线的末端,将暂停点设在靠近坯件夹持端部位。(2) 切割路线的起始点应选择在工件表面较为平坦、对工作性能影响较小的部位。对于精度 要求较高的工件,最好将切割起始点取在坯件上预制的穿丝孔中,不可从坯件外部直接切入, 以免引起工件切开处发生变形。(3) 为减小工件变形,切割路线与坯件外形应保持一定的距离,一般不小于5mm。线切割加工中对于一些具体工艺要求,应重点关注切割路线的优化。(1) 二次(或多次
7、)切割法对于一些形状复杂、壁厚或截面变化大的凹模型腔零件,为减小变形, 保证加工精度,宜采用二次切割法。通常,精度要求高的部位留2mm3mm余量先进行粗 切割,待工件释放较多变形后,再进行精切割至要求尺寸。若为了进一步提高切割精度,在 精切割之前,留 0.20mm0.30mm 余量进行半精切割,即为 3 次切割法,第 1 次为粗切割, 第2次为半精切割,第3次为精切割。这是提高模具线切割加工精度的有效方法。(2) 尖角切割法当要求工件切割成尖角(或称 清角)时,可采用方法一,在原路线上增加一 小段超切路程,如图2所示的A0-A1段,使电极丝切割的最大滞后点达到程序A0点,然 后再前进到附加点A
8、1,并返回至A0点,接着再执行原程序,便可切割出尖角。也可采用 图 3 所示的方法二的切割路线,在尖角处增加一段过切的小正方形或小三角形路线作为附 加程序,这样便可保证切割出棱边清晰的尖角。图 2 尖角切割方法(3) 拐角的割法线切割放电加工过程中,由于放电的反作用力造成电极丝的实际位置比机床 X、Y 坐标轴移动位置滞后,从而造成拐角精度较差。电极丝的滞后移动则会造成工件的外圆弧加工过亏,而内圆弧加工不足,致使工件拐角处精 度下降。为此,对于工件精度要求高的拐角处,应自动调慢X、Y轴的驱动速度,使电极丝 的实际移动速度与X、Y轴同步。也就是,加工精度要求越高,拐角处的驱动速度应越慢。(4) 小
9、圆角切割法若发现图样要求的内圆角半径小于切割时的偏移量,将会造成圆角处根切现象。为此,应明确图样轮廓中最小圆角必须大于最后一遍修切的偏移量,否则应选择直径 更细的电极丝。在主切割加工及初修切割加工中,可根据各遍加工时不同的偏移量,设置不 同的内圆角半径,即对于同段轮廓编制不同的内圆角半径子程序,子程序中的内圆角半径应 大于此遍切割的偏移量,这样就可切割出很小的圆角,并获取较好的圆角切割质量。5 切割前工件的准备 为了减少切割过程中模具的变形及提高加工质量,切割前凸凹模零件应满足以下要求:(1) 工件上、下两平面的平行度误差应小于 0.05mm。(2) 工件应加工一对正交立面,作为定位、校验与测
10、量基准。(3) 模具切割应采用封闭式切割,以降低切割温度,减小变形。(4) 切割工件的四周边料留量应为模具厚度的1/4为宜,一般边缘留量不小于5mm。(5) 为减小模具变形,并正确选择加工方法和严格执行热处理规范,对于精度要求高的模具 最好进行两次回火处理。(6) 工件淬火前应将所有销孔、螺钉孔加工成形。(7) 模具热处理后,穿丝孔内应去除氧化皮与杂质,防止导电性能降低而引起断丝故障。(8) 线切割前,工件表面应去除氧化皮和锈迹,并进行消磁处理。6 结语编程完成后、正式切割加工之前,应对编制的程序进行检查与验证,确定其正确性线切割 机床的数控系统均提供程序验证的方法,常用的方法有:画图检验法主要用于验证程序中是 否存在错误语法及是否符合图样加工轮廓;空行程检验法可检验程序的实际加工情况,检查 加工中是否存在碰撞或干涉现象,以及机床行程是否满足加工要求等;动态模拟加工检验法 通过模拟动态加工实况,对程序及加工轨迹路线进行全面验证。通常,可按编制的程序全部 运行一遍,观察图形是否回零 。对于一些尺寸精度要求高、凸、凹模配合间隙小的冲模, 可先用薄板料试切割,检查有关尺寸精度与配合间隙,如发现不符要求处,应及时修正程序, 直至验证合格后,方可正式切割加工。正式切割结束后,不可急于拆下工件,应检查起始与 终结坐标点是否一致,如发现有问题,应及时采取补救措施。(end)
- 温馨提示:
1: 本站所有资源如无特殊说明,都需要本地电脑安装OFFICE2007和PDF阅读器。图纸软件为CAD,CAXA,PROE,UG,SolidWorks等.压缩文件请下载最新的WinRAR软件解压。
2: 本站的文档不包含任何第三方提供的附件图纸等,如果需要附件,请联系上传者。文件的所有权益归上传用户所有。
3.本站RAR压缩包中若带图纸,网页内容里面会有图纸预览,若没有图纸预览就没有图纸。
4. 未经权益所有人同意不得将文件中的内容挪作商业或盈利用途。
5. 装配图网仅提供信息存储空间,仅对用户上传内容的表现方式做保护处理,对用户上传分享的文档内容本身不做任何修改或编辑,并不能对任何下载内容负责。
6. 下载文件中如有侵权或不适当内容,请与我们联系,我们立即纠正。
7. 本站不保证下载资源的准确性、安全性和完整性, 同时也不承担用户因使用这些下载资源对自己和他人造成任何形式的伤害或损失。
最新文档
- 幼儿园绘本故事当我睡不着的时候课件
- 人教版小学五年级品德与社会上册《五十六个民族五十六朵花》ppt课件
- 人教版小学一年级音乐下册红眼睛绿眼睛ppt课件
- 人教版小学数学四年级上册《数学广角》ppt课件
- 幼儿园优质课件小猫的生日
- 幼儿园科学活动区创设与材料投放课件
- 人教版小学四年级音乐小螺号ppt课件
- 幼儿园科学教育的方法和途径课件
- 开盘前广告策略案课件
- 人教版小学一年级品德与生活《校园铃声》ppt课件
- 人教版小学五年级音乐吹起羌笛跳锅庄ppt课件
- 人教版小学四年级英语下册unit3_weather第三课ppt课件
- 人教版小学一年级上册数学第二单元上下前后ppt课件
- 人教版小学五年级美术第17课电脑动画ppt课件
- 幼儿园优质课件-幼儿园中班“我们都是好朋友”课件