锥齿轮测量与修正技术.ppt
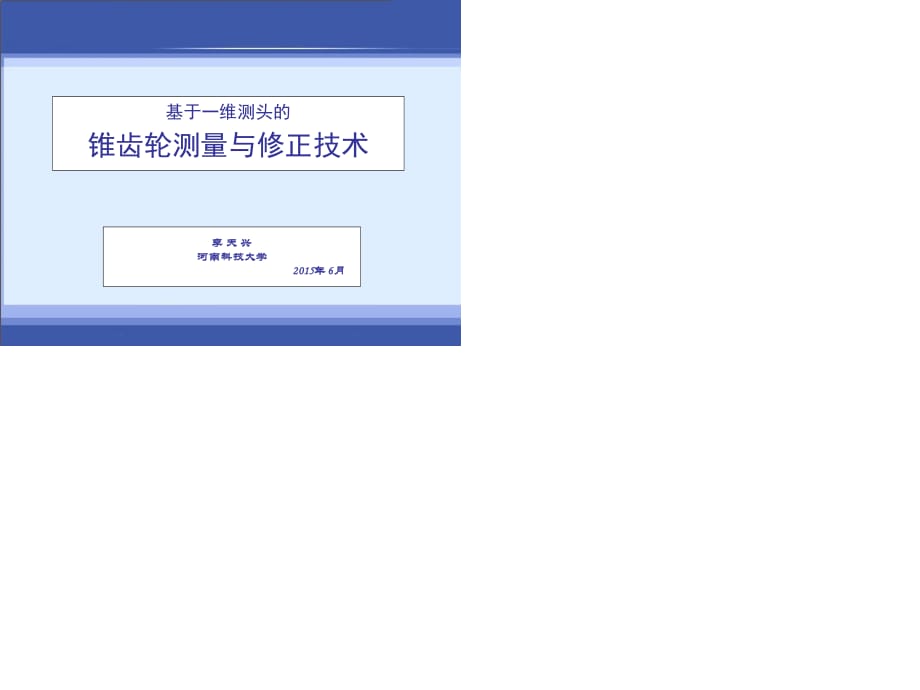


《锥齿轮测量与修正技术.ppt》由会员分享,可在线阅读,更多相关《锥齿轮测量与修正技术.ppt(102页珍藏版)》请在装配图网上搜索。
1、基于一维测头的 锥齿轮测量与修正技术 李 天 兴 河南科技大学 2015年 6月 一. 锥齿轮齿面测量与修正的必要性 二. 锥齿轮精度标准简介 三. 锥齿轮误差检测设备概述 四. 锥齿轮齿面展成与测量模型 五. 锥齿轮齿面及齿距误差测量与评定 六. 基于齿面误差的机床运动修正与反馈 七. 锥齿轮测量与修正软件系统及应用 八. 直齿锥齿轮齿面测量简介 报告内容 一 .锥齿轮测量与修正的必要性 重叠系数大、传动平稳、冲击和噪音小、承载能力高、寿命长 应用越来越广泛 。 锥齿轮通过轮齿曲面相互啮合传递主被动齿轮之间的运动和动力,因此轮 齿的 分度准确度 及实际齿面与设计齿面之间的 几何形状误差 对锥
2、齿轮传动性 能有重要影响。 一 .锥齿轮测量与修正的必要性 高速、高可靠性、重载、低噪声、低成本是趋势。 齿面精度和啮合质量 是保证机械产品的效率、噪声、传动精度和使用 寿命等综合性能的关键。 齿面几何拓扑结构极为复杂 与之相应的误差理论和测量技术 远远落后于圆柱齿轮。 1. 齿面质量控制的重要性 传统的锥齿轮质量控制手段主要是衡量齿面接触区 (接触痕迹 )和运动 平稳性,需要依靠技术人员及工人的丰富经验, 质量控制极其繁琐而 困难 。 两种传统修正方式: 2. 传统的齿面啮合质量控制( 齿面、齿距及侧隙等 ) 小轮控制数据 :由技术人员根据接触区性质改变某些数据重新计 算,给出新的调整卡。
3、比例修正 :根据现场齿面接触区的配对情况改变机床的调整参数。 小轮控制数据的修正方法对齿面接触区的修正很有效,但需要技术人 员重新计算切齿调整数据,在现场使用很不方便。 一 .锥齿轮测量与修正的必要性 往往得不到理想的接触区,或者为了得到理想的接触区,需要多次试 切和多次机床调整 ,费时费力,多次试切中机床调整又要依赖工人的调 整经验。因此加工高品质的螺旋锥齿轮较难实现。 检验结果只能用于保证接触区的位置,对齿轮副实际廓线偏离理论廓线 的修正、误差来源的分析和啮合质量的提高 没有指导意义 ,对齿面二阶 和三阶接触特性的修正具有很大的 盲目性 。 主要针对 齿面接触精度 , 齿面几何精度问题被忽
4、略 ,难以实现高质量锥 齿轮的加工。 齿面几何精度控制在现在的生产中已有应用,但效果不理想,主要是由 于齿面加工与数字化检测及修正等关键环节不能很好的融合。 3. 传统的齿面质量控制存在的问题 一 .锥齿轮测量与修正的必要性 锥齿轮齿面几何及其精度在很大程度上决定了齿面的接触精度及齿轮副 的啮合传动质量。 实际加工齿面与理论设计齿面趋于一致以确保实际啮合传动性能最优。 齿面质量的数字化控制是关键技术难题。锥齿轮数字化闭环制造技术是 重要技术手段。可以有效地控制齿面质量,提高加工效率,缩短开发周期。 美国、日本及德国等发达国家,闭环制造已经替代传统制造模式,齿面 测量及数字化制造技术已经在生产中
5、广泛应用。 锥齿轮数字化闭环制造技术 就是基于齿轮测量中心,规划出遍布全齿面 的网格,测量真实齿面网格点处的齿面坐标,根据测量结果,识别齿面误 差来源并计算切齿修正量,从而使切齿机床调整参数修正后加工出的真实 齿面同理论齿面之间的误差最小。 4. 齿面质量控制的趋势 一 .锥齿轮测量与修正的必要性 5. 锥齿轮测量与修正的作用 测量实际齿面与设计或“理论”齿面之间的误差值,判断是否符合 设计要求; 分析误差产生的原因、寻求修正误差的措施; 未知机床调整参数的实际齿面的反求与复制(利用齿面误差的数字 化修正技术,反求实际齿面参数,复制实际齿面几何); 配对齿轮副的传动性能预测(包括理论设计齿面的
6、预测、实际测量 齿面的预测、修正齿面的预测等)。 一 .锥齿轮测量与修正的必要性 二 . 锥齿轮精度标准简介 1. 锥齿轮精度标准: GB/T 11365-1989,适用于齿面中点法向模数 mn1mm的各类锥齿轮。 GB/T 10225-1988,适用于齿面中点法向模数 mn 1mm的各类锥齿轮。 ANSI/AGMA 2009-B01(2001.10),总的来说适用于齿面中点法向模数 mn0.2mm、 齿数 5、测量直径 5mm的各类锥齿轮,但对每一误差项目 均规定了适用范围。 ISO 17485:2006(E),适用于齿面中点法向模数 mn1mm和 mn 1mm的 各类锥齿轮。 DIN 39
7、65-1986,适用于齿面中点法向模数 mn1mm的各类锥齿轮。 AGMA 2009-B01与 ISO 17485:2006(E)反映了齿轮检测新技术,如坐标测 量方法,使用准确方便。 GB/T 规定的测量项目的公差值列为表格,为一范围值。未反映关于齿形误 差的 CMM测量新技术应用。 二 . 锥齿轮精度标准简介 2. GB/T 11365-1989共计规定了 23个测量项目 : 齿轮副轴间距偏差 齿厚偏差 齿圈轴向位移 齿形相对误差 齿轮副侧隙变动量 齿距偏差 齿轮副侧隙 齿圈跳动 接触斑点 K个齿距累积误差 齿轮副齿频周期误差 齿距累积误差 齿轮副周期误差 周期误差 齿轮副一齿轴交角综合误
8、差 一齿轴交角综合误差 齿轮副轴交角综合误差 轴交角综合误差 齿轮副一齿切向综合误差 一齿切向综合误差 齿轮副切向综合误差 切向综合误差 ()iiFF ()iiff ()iiFF ()iiff ()zk zkff ()ppFF ()pk pkFF ()rrFF ()pt ptff ()ccff ()s ss si sE E E T 、 、 ()ic icFF ()ic icff ()i c i cFF ()i c i cff ()zkc zkcff ()zzc zzcff ()vj vjFF ()AM AMff ()aaff 齿轮副轴交角偏差 ()EE 二 . 锥齿轮精度标准简介 3. GB/
9、T 11365-1989 规定了 12个精度等级 , 1级最高, 12级最低;限于当时的 加工水平, 1 3级未规定具体公差数值,公差表只给出 412级的公差值。 4. GB/T 11365-1989公差组及检验组 : 分 三个公差组 。第 公差组:主要影响 运动精度;第 公差组:主要影响工作平稳性;第 公差组:主要影响接触 质量。 二 . 锥齿轮精度标准简介 二 . 锥齿轮精度标准简介 5. GB/T 11365 89规定的 误差项目较多 ,一些项目的 定义不准确 ,如:齿轮 副一齿轴交角综合误差(分锥顶点重合),一些项目 不便于测量 ,如:齿 形相对误差。公差值较 DIN 3965和 AN
10、SI/AGMA 2009-B01大。 6. 相对地, AGMA 2009-B01规定的公差比其他标准 规定的公差小。例如:当 锥齿轮参数为 ,其齿距极限偏 差公差分别为: Z = 3 9 m = 1 1 . 1 3 1 B = 6 2 = 3 4 2 2 7 9 7 、 、 、 、 精度等级 AGMA 2009-B01 GB/T 11365 DIN 3965 6级 12.16 16 16 7级 17.2 22 22 三 .锥齿轮误差检测设备概述 1. 锥齿轮检测项目 单项误差测量 ,如齿形、齿距、齿厚、径向跳动等误差,使用仪 器如齿轮测量中心 啮合传动误差测量 ,如切向综合误差、侧隙变动量、接
11、触斑点等, 使用仪器如 Gleason 600HTT、 Oerlikon T60等类型的滚动检查 机、单啮仪、双啮仪等 整体误差测量 2. 齿轮测量中心 可实现锥齿轮单项误差测量,如齿形、齿距、齿厚、径向跳动等。 三 .锥齿轮误差检测设备概述 三 .锥齿轮误差检测设备概述 3. 锥齿轮滚动检查机 可实现锥齿轮啮合传动误差测量,如切向综合误差、接触斑点等。 三 .锥齿轮误差检测设备概述 四 .锥齿轮数控加工与测量模型 1. 传统锥齿轮铣齿机加工原理 传统机械铣齿机床是按齿轮啮合原理设计的。能够上下摆动的摇 台机构模拟一个假想的齿轮(假想产形轮),圆盘铣刀被偏心安 装在摇台上,其切削面形成假想产形
12、轮与齿轮相啮合的一个轮齿 的齿面。当被加工齿轮与假想产形轮以一定的滚切比绕各自轴线 旋转时,刀盘就会在轮坯上切出一个齿槽。齿轮的切削过程就像 一对准双曲面齿轮的啮合过程一样,刀盘切削面与被加工齿轮的 齿面是一对完全共轭的齿面。 基本机床调整参数(共 13项): 刀盘直径、刀盘齿形角、径向刀位、角向刀位、总刀倾角、基本 刀转角、轮坯安装角、水平轮位、垂直轮位、床位、滚切比、二 阶变性系数、三阶变性系数 摇 台 偏 心 结 构 刀 转 机 构 刀 倾 机 构 工 件 旋 转 轴 水 平 轮 位 垂 直 轮 位 圆 盘 铣 刀 床 位 轮 坯 安 装 角 假 想 产 形 轮 圆 盘 铣 刀 被 加
13、工 齿 轮 四 .锥齿轮数控加工与测量模型 结构复杂 传动链长而复杂 加工调整复杂 加工周期较长 四 .锥齿轮数控加工与测量模型 2. 数控展成原理 数控铣齿机床取消了摇台、刀倾以及偏心结构, 用三个直线运动轴 X、 Y、 Z和三个旋转运动轴 A、 B、 C来实现齿面展成所需的全部运动。 加工时,将展成齿面所需的运动转化为各数控轴 运动或联动,代替了传统机械铣齿机中复杂的传 动链,灵活控制被加工齿轮与铣刀盘在空间中的 位置和运动,通过复合空间运动来完成实际展成 运动形成加工齿面。 注:刀倾法加工时, 刀盘轴线的倾角被补偿到 B 轴。 四 .锥齿轮数控加工与测量模型 伺服电机直接驱动 水平 X和
14、垂直 Y替代摇台及偏心机构 机构的精简 使机床的静态 和动态刚度得到了提高, 数 字系统对各轴的精确控制 使 加工出的齿轮的齿形精度和 齿面质量均得到了改善,并 增加了可优化的空间,使 齿 面的接触性能及质量更易于 控制。 四 .锥齿轮数控加工与测量模型 四 .锥齿轮数控加工与测量模型 c o s c o s c o s s in s in () tt t t t t tn ( si n ) c os ( si n ) si n ( , ) c os 1 t t F t t t F t t Ft Ft rs rs rs s 四 .锥齿轮数控加工与测量模型 ( , , , ) ( ) ( ) (
15、 , ) ( , ) ( , ) w F t c w w f w fd d m m c c c a a b b t t F t w t w c t F t r s r s rs M M M M M M M M ( , , ) ( ) () ( ) ( ) ( , ) w c w w f w fd d m m c c c a a b b t t w t c w t tt t nn n L L L L L L L L () 0cwmmnv ( , ; ) ( , ; ) w w t c j w w t c j rr nn 理论设计齿面数学表达: 传统机械铣齿机床的齿面展成模型 四 .锥齿轮数控加工
16、与测量模型 四 .锥齿轮数控加工与测量模型 完全等效转换原理 : ( ) ( ) ( ) ( )( ) ( ) CG w t w t CG t w w t w wO O O O LL 12 11 23 33 13 * 24 34 14 * 34 24 * 24 34 14 ( ) ( ) a t a n ( ) ( ) a t a n ( ) ( ) a si n ( ) ( si n c os ) si n ( ) c os ( ) si n c os ( ) ( si n c os ) c os ( ) si n c t c c w c c m c c w w m m c w w c w
17、w m m T a a A a a Ba X a a XA a Y a a Z a a XA a 四 .锥齿轮数控加工与测量模型 变性法加工齿轮时 , 0ti sj 23 * * * ( ) 2 ( ) ( ) ( ) ( ) c os( ) ( ) c os( ) ( ) si n( ) ( ) si n( ) c t c c w a c c c mm c r c a m c r c m a m b Tq A R C D B X S q XA X Y S q E Z XA X X 四 .锥齿轮数控加工与测量模型 3. 齿面测量原理 在齿轮测量过程中,中心计算机根据被测齿轮齿面的 理论数据控制
18、 X、 Y、 Z轴和 C轴运动 , 同时齿轮不断转 动使每个被测点法线方向的 Y轴分量接近于 0。与一般 锥齿轮的齿面检测相比,由于螺旋锥齿轮齿面曲率很 大,因此需要控制 B轴旋转一定角度,保证一维测头 始终沿着被测点的法线方向与齿面靠近、接触。在测 头沿齿轮齿面运动的过程中,计算机不断采集各坐标 轴的实际位置,并存储起来,这些数据记录了被测齿 轮实际加工齿面的数据;对测头半径补偿得到实际齿 面,应用坐标变换方法及曲面匹配处理后使实际齿面 与理论设计齿面处于最佳匹配位置,筛选、分析并计 算测量网格处实际齿面与理论设计齿面之间的法向距 离,从而得到齿面被测点处的法向偏差。 cZ cO cYcX
19、wO wX wY wZ L XZ CB 四 .锥齿轮数控加工与测量模型 四 .锥齿轮数控加工与测量模型 机床结构发生了很大变化。 加工原理不变 :获得一定的运动关系以实现刀盘 与齿坯之间的相对位姿。 四 .锥齿轮数控加工与测量模型 齿面接触精度修正 齿面几何精度修正 四 .锥齿轮数控加工与测量模型 数字化修正的思路 : 1、国产数控铣齿机床 功能结构完善、多自由度; 齿面接触区的 修正和控制更灵活 2、国产齿轮测量中心 测量重复性及精度 工艺技术、驱动软件研发及其数据补偿处理技术 易于联网 3、基于齿面 偏差信息修正机床运动。 以齿面几何精度控制为目标,基于齿面偏差检测信息,建立机床调整 参数
20、、实际加工齿面及理论设计齿面三者之间的映射关系,获取机床调 整参数的实际误差,从而达到修正齿面精度的目的。 避免齿面接触精度检验及试切的繁琐过程,有效提高齿面精度和加工 效率。 四 .锥齿轮数控加工与测量模型 五 .锥齿轮齿面及齿距误差测量与评定 1. 检测方式及规划 2. 齿面误差的产生与分类 3. 测量区域规划 4. 数据处理中的四个面 5. 理论齿面及数字化处理 6. 齿面误差的精确补偿计算原理 7. 齿轮定位和齿面定位(测量参考点) 8. 测量过程的增维与降维处理 9. 一维测头的实际接触位置补偿 10. 实际齿面重构及分析 11. 测量齿面的最佳匹配 12. 影响齿面真实误差获取的几
21、个方面 13. 齿距误差测量 五 .锥齿轮齿面及齿距误差测量与评定 齿面检测方式及规划 五 .锥齿轮齿面及齿距误差测量与评定 五 .锥齿轮齿面及齿距误差测量与评定 齿面偏差的来源 齿面质量及精度主要取决于 铣齿机床系统误差 及 机床调整误差 等 传统切齿计算的近似性; 机床调整参数误差; 刀具参数误差; 切削力和热变形; 刀具磨损; 热处理变形。 五 .锥齿轮齿面及齿距误差测量与评定 切齿计算误差 机床运动误差 热变形等 通过机床运动参数和刀盘参数来予以转化或替代。 五 .锥齿轮齿面及齿距误差测量与评定 齿长偏差 齿高偏差 对角偏差 齿面偏差的分布趋势 五 .锥齿轮齿面及齿距误差测量与评定 3
22、. 测量区域规划( 美国齿轮制造商协会标准( AGMA STANDARD) ) 齿面误差测量是建立在齿面上一组严格定义的网格点,测量点的数目和 位置的选择至关重要,其对测量效率和精度影响很大。 总体要求:测量点的数目必须足够到能够提供轮齿的精确信息,同时不降 低测量效率;测量区域足够大以保证测量的准确性和真实性。 测量点太多,其误差会导致拟合齿面局部区域曲率变化很大,对齿面数字 化处理不利,并且测量效率也不高,计算量按级数增大;测量点太少影响 整个齿面拟合精度以及求解机床调整参数修正值的准确度。 测量点的区域要足够大但不能太接近齿顶、齿根过渡曲面,或者大小端面 以保证测量的准确性和真实性 五
23、.锥齿轮齿面及齿距误差测量与评定 3. 测量区域规划( 美国齿轮制造商协会标准( AGMA STANDARD) ) 五 .锥齿轮齿面及齿距误差测量与评定 4.数据处理中的四个面 H *H eH e*H 理论设计齿面 实际加工齿面 理论设计齿面的等距面(测球理论运动轨迹面) 实际加工齿面的等距面(测球实际运动坐标) 齿面误差定义:实 际加工齿面偏离理 论设计齿面的法向 距离 。 五 .锥齿轮齿面及齿距误差测量与评定 5. 理论齿面及数字化处理(测球理论轨迹) 齿面误差是定义在齿面的法线方向上,因此需要计算每一个被测点的坐标值(三 维)及法线的方向余弦。 * 2 2 * ( , ; ) ( , ;
24、 ) ( , ; ) i t c j i t c j i t c j xx y z y SUMT法求解 五 .锥齿轮齿面及齿距误差测量与评定 ( , ; ) ( , ; ) w w t c j w w t c j HH nn 工件坐标系 中: wS 测量 坐标系 中: cS , , ; , t c j c w t c t c j c w t c j ( ; ) ( ) ( ; ) ( ; ) M M w w HH nn 测量中心进行接触式测量时,一般采用球 形测头。通过齿轮测量中心读出的数据为 测头中心的位置坐标,而不是测头球形表 面和工件接触点的位置坐标,其间的差值 与测头半径的大小和测量位
25、置有关。 为了便于测量和得到正确的测量结果,在 测量前和测量后都应对被测点进行测头半 径补偿处理。 齿面测量的依据 测量坐标系下测头的理论运动轨迹面 测头半径补偿处理: e , , ,t c j t c j t c j( ; ) ( ; ) ( ; ) H H n 五 .锥齿轮齿面及齿距误差测量与评定 6.齿面误差的精确补偿计算原理 模型 1: 对理论齿面 上一点 P0,过其法矢 ,找到与 P0对应的实际齿面 上的点 P*,计算这两点之间偏差即为齿面加工时在点 P0所形成的齿面误差 H n *H *() H H n 五 .锥齿轮齿面及齿距误差测量与评定 6.齿面误差的精确补偿计算原理 模型 2
26、: 以实际齿面点 P*为初始基准点,沿实际齿面法矢方向 ,找到理 论齿面 上与实际齿面点 P*对应的点 P1,对应点之间距离即为齿面误差 H *n * * *() H H n 五 .锥齿轮齿面及齿距误差测量与评定 6.齿面误差的精确补偿计算原理 模型 1与模型 2差异的数学描述: * * * * * * ( ) ( ) ( ) ( ) ( ) ( 1 ) ( ) ( 1 c os ) n H H H H n n H H n n HH *() H H n * * *() H H n * 2 *1( ) ( )2 n H H 仅与 和 相关 决定于 *( , )nn 决定于实际齿面精度 若齿面精度
27、较高,两误差模型差异将 十分微小,可忽略不计。 在加工误差较大的齿面时,差异则不 容忽视。 五 .锥齿轮齿面及齿距误差测量与评定 6.齿面误差的精确补偿计算原理 齿面误差计算模型的选择: 方法 2由实际齿面点寻找理论齿面上对应 点时,理论齿面已经解析表达,不存在对理 论齿面拟合问题,消除了拟合误差; 方法 1由理论齿面点寻找实际齿面上对应 点时,需要对检测数据进行曲面拟合,这样 必然带入拟合误差,有可能掩盖真实加工误 差,不利于齿面精度评价和机床参数反调。 在齿面测量过程中,采样点的个数远远大于理论齿面测量点的个数,若采用 非均匀有理 B样条对实际齿面测量点进行拟合,必有较好保凸性,不会造成实
28、 际加工信息损失,有利于确保评定精度; 齿面数控展成中的误差补偿都是以理论齿面为基础。 无论是从误差评定的准确程度,还是数控展成的便捷程度,选用方法 1来分析 与计算齿面误差将更加准确方便。 五 .锥齿轮齿面及齿距误差测量与评定 实际齿面偏差的精确补偿计算 *() H H n * ,tw( ; ) H H nj * * *e ,( u v ) H H n测头实际运动轨迹面 : * * *ee () H H H H n n *ee , , , , ( )t w j t w j t w j( u v ) ( ; ) ( ; ) ( ; ) H H n n n *ee( , , ) , , ( c
29、o s 1 )t w j t w j t w j( u v ) ( ; ) ( ; ) ( ; ) H H n *ee( , , ) , ,t w j t w j t w j( u v ) ( ; ) ( ; ) ( ; ) H H n 2( c o s 1 ) / 2= 测量中的一项 重要误差源 采用小直径测头 是减小测量误差的重要手段。 五 .锥齿轮齿面及齿距误差测量与评定 *ee, , , ,t w j t w j t w j( ; ) ( ; ) ( ; ) ( u v ) H n H *e, ( , ) , ,t w j t w j t w j( ; ) ( ; ) ( ; ) (
30、u v ) H n H *e, ( , , ) ,i ti wi j i i ti wi j ti wi j( ; ) = ( u v ) - ( ; ) ( ; ) - H H n 齿面偏差精确计算的方程表达式 齿面偏差与机床运动参数映射关系 : 五 .锥齿轮齿面及齿距误差测量与评定 *e, ( , ) , ,t w j t w j t w j( ; ) ( ; ) ( ; ) ( u v ) H n H 齿面偏差计算 :以 、 、 为设计变量的非线性方程组 设计变量: 已知项:测头半径 机床运动参数 测头运动实际轨迹面 理论设计齿面 单位法矢 求解方法:非线性方程组 优化迭代求解 u v
31、u v j *e ( , )uvH ,t w j( ; ) H ,t w j( ; ) n 五 .锥齿轮齿面及齿距误差测量与评定 机床运动参数修正 :寻求最佳机床参数 使得齿面偏差 趋于最小 设计变量: 已知项:测头半径 齿面偏差 实际加工齿面 求解方法:非线性方程组 优化求解 *e ( , )uvH *e, ( , ) , ,t w j t w j t w j( ; ) ( ; ) ( ; ) ( u v ) H n H j t j w 五 .锥齿轮齿面及齿距误差测量与评定 7.1齿轮定位(工件和测量两坐标系空间位置的吻合) 工件坐标系和测量坐标系的空间位置吻合是实现齿面 偏差准确测量的前提
32、,加工与测量的定位基准重合是 关键。 齿轮测量中心的坐标系原点是回转工作台中心,被测 齿轮在测量中心上一般采用回转工作台和顶尖分别进 行加工基准端面和基准轴线定位;而理论设计齿面所 在的工件坐标系原点是设计交叉点,切齿定位基准是 内孔(或轴线)和端面。齿面检测要尽量保证测量基 准和加工基准的一致以减小安装定位误差对测量结果 的影响。 j c w j j c w j ( , ; ) M ( , ; ) ( , ; ) M ( , ; ) 0 0 HH nn 五 .锥齿轮齿面及齿距误差测量与评定 7.1齿轮定位(工件和测量两坐标系空间位置的吻合) 五 .锥齿轮齿面及齿距误差测量与评定 7.1齿轮定
33、位(工件和测量两坐标系空间位置的吻合) 五 .锥齿轮齿面及齿距误差测量与评定 7.2齿面定位(测量参考点) 齿轮定位后,齿轮沿轴线的回转自由度依旧没有消除( 角),即在测量 坐标系 Sc中被测齿面和理论齿面的相对定位问题,也就是找准测量参考点 M确定实际加工齿面相对于理论设计齿面在测量坐标系中的相对位置。 单齿定位 测量参考点 既是齿面数字化的 基准点,也是测头定位的初始点。 一般选取实际齿面网格的中间点 作为测量参考点,假设理论齿面 和实际齿面在该点重合,偏差为 零。这样可以有效地测出其它点 的相对误差,测量结果也真实反 映齿面误差。 五 .锥齿轮齿面及齿距误差测量与评定 8.一维测头的增维
34、与降维处理 一维测头 只能感应一个方向的信号,必须考虑测头的敏 感方向和齿面测点法线方向的一致问题。 测头敏感方向和齿面点法线方向的不一致是使用一维测 头检测螺旋锥齿轮齿面偏差所面临的首要问题 增维与降维 处理,在同一个二维平面内弥补由于方向不 一致而引起的测量误差。 五 .锥齿轮齿面及齿距误差测量与评定 ( 1 , 2 , , 45 ) T( 0) ( 0) ( 0) ( 0) c i i i T( 0) ( 0) ( 0) ( 0) c x i y i z i = x y z i n n n r n= 测头半径补偿后的齿面坐标和单位法线 : 一维测头的初始敏感方向 : 00 T( 0 )
35、( 0 ) p r o b e p xnn= 0 0 0a ta n ( )( 0) ( 0)yxnn 0 0 0 0 0 0 0 0 0 0 0 0 0 0 0 c os si n 0 c os si n si n c os 0 0 0 0 1 ( 1) ( 0) ( 0) ( 0) x x x y ( 1) ( 1) ( 0) c y y ( 1) ( 0) ( 0) z z z n n n n nn n n n n 齿面测量参考点的法矢方向转至平面 XcOcZc内 : 此时,齿面法线由 空间的三维转换为平面的二维 五 .锥齿轮齿面及齿距误差测量与评定 参考点法线 方向与测头敏感方向的夹角
36、 : 00a t a n ( )( 1 ) ( 1 )zxnn c os 0 si n c os 0 1 0 0 0 si n 0 c os 0 si n ( 0) ( 0) px px ( 1) probe ( 0) px nn n n= 此时,测头敏感方向由一维 转换为平面的二维 ,和齿面法 线方向保持一致。 五 .锥齿轮齿面及齿距误差测量与评定 一点一转动 五 .锥齿轮齿面及齿距误差测量与评定 9.一维测头的实际接触位置补偿 严格来讲,测量后得到的齿面偏差不是被测点法线上的偏差,而是实际 接触点在测头敏感方向上的偏差。因为除参考点外,测头敏感方向和被测 点的法线方向仍存在部分夹角误差,导
37、致了测头和实际齿面的接触点位置 发生改变;尤其使用一维测头进行齿面测量,测头与齿面的实际接触位置 是影响测量准确与否的重要因素。 五 .锥齿轮齿面及齿距误差测量与评定 9.一维测头的实际接触位置补偿 在微观域内可认为接触位置周围是小平 面,存在以下的几何关系: 1( 1 ) c o s 要接触到理论点,必须对测头与齿面的实际接触位置作补偿, Z方向 必需有一定量的补偿。 至于对测头球体上接触点的位置不影响电感信号的输出,对测量结果 也不产生影响。 五 .锥齿轮齿面及齿距误差测量与评定 10.实际加工齿面的重构及分析 螺旋锥齿轮实际齿面重构就是利用 NURBS 方法来建立实际齿面的数学模型, 即
38、实际齿面的反求,其实质就是用一个具有准确数学表达式 NURBS曲面最大 限度地表示螺旋锥齿轮的真实齿面。 型 值 点 参 数 化 初 始 化 参 数 固 定 一 个 参 数 得 到 一 条 等 参 数 的 控 制 点 ,ijD 控 制 点 即 为 所 求 得 到 另 一 条 等 参 数 控 制 点 D 存 放 在 数 组 D 中 固 定 另 外 一 个 参 数 ,ijD 五 .锥齿轮齿面及齿距误差测量与评定 从理论上来说 , 实际齿面和理论齿面的关联性可以通过选取测量参考点来 实现 。 但是在实际测量过程中 , 由于被测齿轮在测量机上的安装高度误差 、 安装轴线偏移及测量机整体误差等的存在 ,
39、 实际齿面与理论齿面还必须进行 最佳贴合匹配 , 这也是评价测量数据优劣的前提和关键 。 11.实际测量齿面的最佳匹配 五 .锥齿轮齿面及齿距误差测量与评定 11.实际测量齿面的最佳匹配 Y Z nl s l s ( a ) 初 始 位 置 ( b ) 放 大 情 形 ( c ) 最 佳 匹 配 位 置 l 1s 以测量齿面偏差的平方和最小化为 目标函数 以各坐标轴的移动和转动为 设计变量 以各轴的自由度对两齿面相对位置的综合影响为 约束条件 曲面匹配使实际曲面相对于理论齿面达到较好位置,以消除基 准不重合误差。 五 .锥齿轮齿面及齿距误差测量与评定 12.影响齿面真实误差获取的几个方面(测量
40、误差影响总结) 1、测头直径 2、测头敏感方向与齿面法线方向夹角 3、误差计算模型的选取 4、 5、测球与齿面接触位置补偿处理 2( c o s 1 ) / 2= 五 .锥齿轮齿面及齿距误差测量与评定 13.齿距误差测量 1 , m a x , m i n ; 1 , m a x( ( ) , ( ) ) ; 1 , m a x( ) m i n( ) ; 0 , pt i i i pt pt i pt i p i i f i n f abs f abs f i n F i n 齿距累积总偏差: 单个齿距偏差: 相邻齿距偏差: 六 .基于齿面误差的机床运动修正与反馈 1. 齿面的数字化修正原理
41、与方法 2. 齿面误差影响规律分析 3. 齿面的数字化修正模型 4. 齿面误差类型的自动识别 5. 数控机床运动的修正过程与策略 6. 机床运动参数自动反馈 1.齿面误差修正原理 1)比例修正原理 一般按切齿计算数据切出一对锥齿轮,在滚动检验机上检查接触区。其接触区 的修正工作,通常都是在小轮上进行的,这是因为小轮齿数少,切齿时间少的 关系。个别情况,也有修正大轮的。 修正顺序:螺旋角修正 压力角修正 齿面节线曲率修正 齿形曲率修正 对角修正 齿面的修正是一个反复的过程。 每一次修正都对应机床的调整和试切一次。 六 .基于齿面误差的机床运动修正与反馈 1.齿面误差修正原理 1)比例修正原理 齿
42、长误差一般体现为螺旋角误差和齿面节线曲率偏差。 改变刀位修正螺旋角误差, 改变刀盘直径及刀位来实现修正齿面节线曲率偏差;对于存在刀倾刀转机构的 机床,必须同时改变床位。 六 .基于齿面误差的机床运动修正与反馈 1.齿面误差修正原理 1)比例修正原理 齿高方向偏差一般体现为压力角误差和齿形曲率偏差。 改变刀位、水平轮位和床位来修正压力角误差;对于存在刀倾刀转机构的机床, 可以改变刀倾角、刀转角、刀位、刀盘半径和床位来修正压力角误差;过大的 压力角误差时需要改变滚切比予以修正; 齿形曲率偏差的存在可以改变垂直轮位、刀位和滚切比来修正。 六 .基于齿面误差的机床运动修正与反馈 1.齿面误差修正原理
43、1)比例修正原理 齿面对角偏差一般体现为对角接触。 改变滚切传动比和水平轮位、床位、刀位或者三阶变性系数等可达到设计要求。 六 .基于齿面误差的机床运动修正与反馈 1.齿面误差修正原理 2)数字化修正原理 六 .基于齿面误差的机床运动修正与反馈 数字化修正思路 : 齿面几何完全受控于机床调整参数,齿面偏差完全受 控于机床调整参数误差,理论设计齿面和实际加工齿面 分别对应着理论机床调整参数和实际机床调整参数。 采用 逆向求解 方法,通过机床调整参数的反调修正来 实现齿面偏差的最小化。 1.齿面误差修正原理 2)数字化修正原理 六 .基于齿面误差的机床运动修正与反馈 数字化反调修正原理 改变理论机
44、床调整参数使理论设计齿面逐步向实际加 工齿面靠拢并贴合,齿面偏差达到最小。 反调修正的目的: 求解实际机床调整参数及修正量。 1.齿面误差修正原理 2)数字化修正原理 六 .基于齿面误差的机床运动修正与反馈 数字化反调修正策略 “修正齿面 1” ; “修正齿面 2” ; “修正齿面 n” 最大机床调整参数修正量 实际机床调整参数 =最大机床调整参数修正量 +理论最佳机床调整参数 参数 刀盘半径 齿形角 安装角 偏差 趋势 小 端 大 端齿 顶 凸 面 凹 面 小 端 大 端齿 顶 凸 面 凹 面 小 端 大 端齿 顶 凸 面 凹 面 影响 分析 齿长偏差,轻微齿高偏 差,影响齿面节线曲率 齿高
45、偏差 对角偏差 参数 径向刀位 水平轮位 垂直轮位 偏差 趋势 小 端 大 端齿 顶 凹 面 凸 面 小 端 大 端齿 顶 凸 面 凹 面 小 端 大 端齿 顶 凸 面 凹 面 影响 分析 主要齿长偏差,轻微齿 高偏差 主要齿高偏差,轻微齿 长偏差 对角偏差,影响齿高 曲 率 参数 床位 滚切比 偏差 趋势 小 端 大 端齿 顶 凸 面 凹 面 小 端 大 端齿 顶 凸 面 凹 面 影响 分析 齿长偏差,轻微齿高偏 差 主要齿高偏差,次之齿 长偏差 右 旋 大 轮 齿 面 偏 差 影 响 分 析 齿 面 偏 差 的 影 响 分 析 六 .基于齿面误差的机床运动修正与反馈 齿 面 偏 差 的 影
46、 响 分 析 左 旋 小 轮 齿 面 偏 差 影 响 分 析 参数 刀盘半径 齿形角 安装角 偏差 趋势 小 端 大 端齿 顶 凸 面 凹 面 小 端 大 端齿 顶 凹 面 凸 面 小 端 大 端齿 顶 凹 面 凸 面 影响 分析 齿长偏差,轻微齿高偏 差,影响齿面节线曲率 齿高偏差 对角偏差 参数 径向刀位 水平轮位 垂直轮位 偏差 趋势 小 端 大 端齿 顶 凹 面 凸 面 小 端 大 端齿 顶 凹 面 凸 面 小 端 大 端齿 顶 凹 面 凸 面 影响 分析 主要齿长偏差,轻微齿 高偏差 主要齿高偏差,轻微齿 长偏差 对角偏差,影响齿高 曲 率 六 .基于齿面误差的机床运动修正与反馈 齿
47、 面 偏 差 的 影 响 分 析 参数 床位 滚切比 刀倾角 偏差 趋势 小 端 大 端齿 顶 凹 面 凸 面 小 端 大 端齿 顶 凹 面 凸 面 小 端 大 端齿 顶 凹 面 凸 面 影响 分析 轻微对角偏差 主要齿高偏差,轻微齿 长偏差 主要齿高偏差,轻微 齿 长偏差 参数 刀转角 二阶变性系数 三阶变性系数 偏差 趋势 小 端 大 端齿 顶 凹 面 凸 面 小 端 大 端齿 顶 凹 面 凸 面 小 端 大 端齿 顶 凹 面 凸 面 影响 分析 对角偏差,影响较小 对角偏差,影响齿高曲 率 对角偏差,影响齿面 节 线曲率和齿高曲率 左 旋 小 轮 齿 面 偏 差 影 响 分 析 六 .基
48、于齿面误差的机床运动修正与反馈 齿 面 偏 差 的 影 响 分 析 X、 Y轴 影响铣刀盘中心的瞬时位置; Z轴 影响切齿深度; A轴 影响工件齿轮转角(滚切比); B轴 影响轮坯安装角。 将各数控轴运动误差转换为传统机械铣齿机床的机床调 整参数误差来分析机床运动误差对齿面几何结构的影响。 影响螺旋锥齿轮齿面偏差的主要因素: 六 .基于齿面误差的机床运动修正与反馈 齿 面 偏 差 的 影 响 分 析 展成法 各数控轴的运动轨迹: c o s( ) ( ) c o s( ) sin( ) ( ) sin( ) r a m rm a m b w mm X S q X A X Y S q E Z X
49、 A X X A B ( ) c o s ( ) ( ) c o s ( )r r a mX X S S q q X A X ( ) s in ( )r r mY Y S S q q E ()a ta n ( ) c os( ) m am Y Y Eqq X X X A X () ()sin a ta n ( ) c o s( ) m rr m am Y Y ESS Y Y E X X X A X 六 .基于齿面误差的机床运动修正与反馈 齿 面 偏 差 的 影 响 分 析 X Y的齿面偏差影响 的齿面偏差影响 Z对齿面偏差的影响与床位相同; A对齿面偏差的影响与滚切比相同; B对齿面偏差的影响
50、与轮坯安装角相同。 六 .基于齿面误差的机床运动修正与反馈 六 .基于齿面误差的机床运动修正与反馈 3.齿面偏差的数字化修正模型 45 2 ( ) ( ) 1 45 2 * ( ) ( ) e 1 m i n m i n ( , , ) , kk ti w i j ti w i j i kk i i ti w i j ti w i j i f ( , ; ) ( , ( u v ) - ( ; ) ( ; ) - H H n ( * ) ( * )j j j 最佳机床运动参数: 4.齿面误差类型的自动识别 齿面误差修正时,首先要对误差类型进行识别,再根据不同的 误差类型和切齿方法,来修正相应的
51、机床运动参数。 在齿面的 45个测量节点中选 取比较有代表性的四个点 (例如大端、小端、齿顶和 齿根的四个边界点),根据 其误差值大小及正负,运用 数学逻辑算法归纳出齿面偏 差的总体趋势;还可选取八 个测量点,来进一步判断齿 面的曲率偏差, 六 .基于齿面误差的机床运动修正与反馈 六 .基于齿面误差的机床运动修正与反馈 六 .基于齿面误差的机床运动修正与反馈 机 床 运 动 的 数 字 化 修 正 过 程 与 策 略 齿面的修正是一个反复的过程 先修正齿 长 偏差和齿高偏差 每一次修正均对应一次机床调整和试切。 六 .基于齿面误差的机床运动修正与反馈 机 床 运 动 的 数 字 化 修 正 过
52、 程 与 策 略 传 统 机 械 铣 齿 机 床 的 数 字 化 修 正 六 .基于齿面误差的机床运动修正与反馈 机 床 运 动 的 数 字 化 修 正 过 程 与 策 略 现 代 数 控 铣 齿 机 床 的 数 字 化 修 正 六 .基于齿面误差的机床运动修正与反馈 机 床 运 动 的 数 字 化 修 正 过 程 与 策 略 通 用 数 控 加 工 机 床 的 数 字 化 修 正 六 .基于齿面误差的机床运动修正与反馈 机 床 运 动 参 数 的 自 动 反 馈 七 .锥齿轮测量与修正软件系统及应用 齿轮测量中心是一种先进的齿轮测量仪器,应 用该测量仪器可自动、高效、精密地测量和修正锥 齿轮
53、的齿面误差。应用实践表明,该测量系统操作 使用简单方便,可有效减小齿面误差,改善齿面精 度,为高质量锥齿轮制造提供了先进的测量技术手 段。 七 .锥齿轮测量与修正软件系统及应用 软件系统的主要功能: 标准球、测头中心位置自动校正; 盘类齿轮内孔中心及定位端面的辅助校正; 适用于各类加工方法和机床的齿面理论模型建立、测量点几何参数与机 床运动参数计算; 自动划分齿面测量网格,规划测量路径,测量、计算并图形显示测量网 格点法向齿形误差; 手动、自动测量齿距误差,根据 GB/T 11365-1989、 GB/T 10225-1988、 AGMA 2009-B01、 ISO 17485:2006(E)
54、及企业自定义标准自动进行精度等 级评定; 根据齿面误差值自动计算机床运动参数修正量,并自动输出机床运动参 数修正卡。 七 .锥齿轮测量与修正软件系统及应用 七 .锥齿轮测量与修正软件系统及应用 七 .锥齿轮测量与修正软件系统及应用 七 .锥齿轮测量与修正软件系统及应用 七 .锥齿轮测量与修正软件系统及应用 七 .锥齿轮测量与修正软件系统及应用 七 .锥齿轮测量与修正软件系统及应用 七 .锥齿轮测量与修正软件系统及应用 由中心计算机、国产 JD45+型齿轮测量中心及国产 YK2260T型数控螺旋 锥齿轮铣齿机组成的数字化闭环制造生产线 八 . 直齿锥齿轮测量 八 . 直齿锥齿轮测量 2 0 1* c os ( t a n( ) ) 2 c os 1* si n(ta n( ) ) 2 c os kk kk mn z r mn z 00 12 00 1 0 0 0 0 c os( ) si n( ) 0 0 si n( ) c os( ) 0 0 0 0 1 kk kk M 01 c os si n 0 / c os si n c os 0 0 0 0 1 0 0 0 0 1 R M 0 1 1 2 2r M M r 数学模型更简单,近似渐开线或球面渐开线,齿面几何与加工机床无关; 沿齿长方向是直线,所以测量路径与弧齿有所区别,但是测量效率更高。 谢谢大家!
- 温馨提示:
1: 本站所有资源如无特殊说明,都需要本地电脑安装OFFICE2007和PDF阅读器。图纸软件为CAD,CAXA,PROE,UG,SolidWorks等.压缩文件请下载最新的WinRAR软件解压。
2: 本站的文档不包含任何第三方提供的附件图纸等,如果需要附件,请联系上传者。文件的所有权益归上传用户所有。
3.本站RAR压缩包中若带图纸,网页内容里面会有图纸预览,若没有图纸预览就没有图纸。
4. 未经权益所有人同意不得将文件中的内容挪作商业或盈利用途。
5. 装配图网仅提供信息存储空间,仅对用户上传内容的表现方式做保护处理,对用户上传分享的文档内容本身不做任何修改或编辑,并不能对任何下载内容负责。
6. 下载文件中如有侵权或不适当内容,请与我们联系,我们立即纠正。
7. 本站不保证下载资源的准确性、安全性和完整性, 同时也不承担用户因使用这些下载资源对自己和他人造成任何形式的伤害或损失。