无取向硅钢冲裁回弹影响因素分析
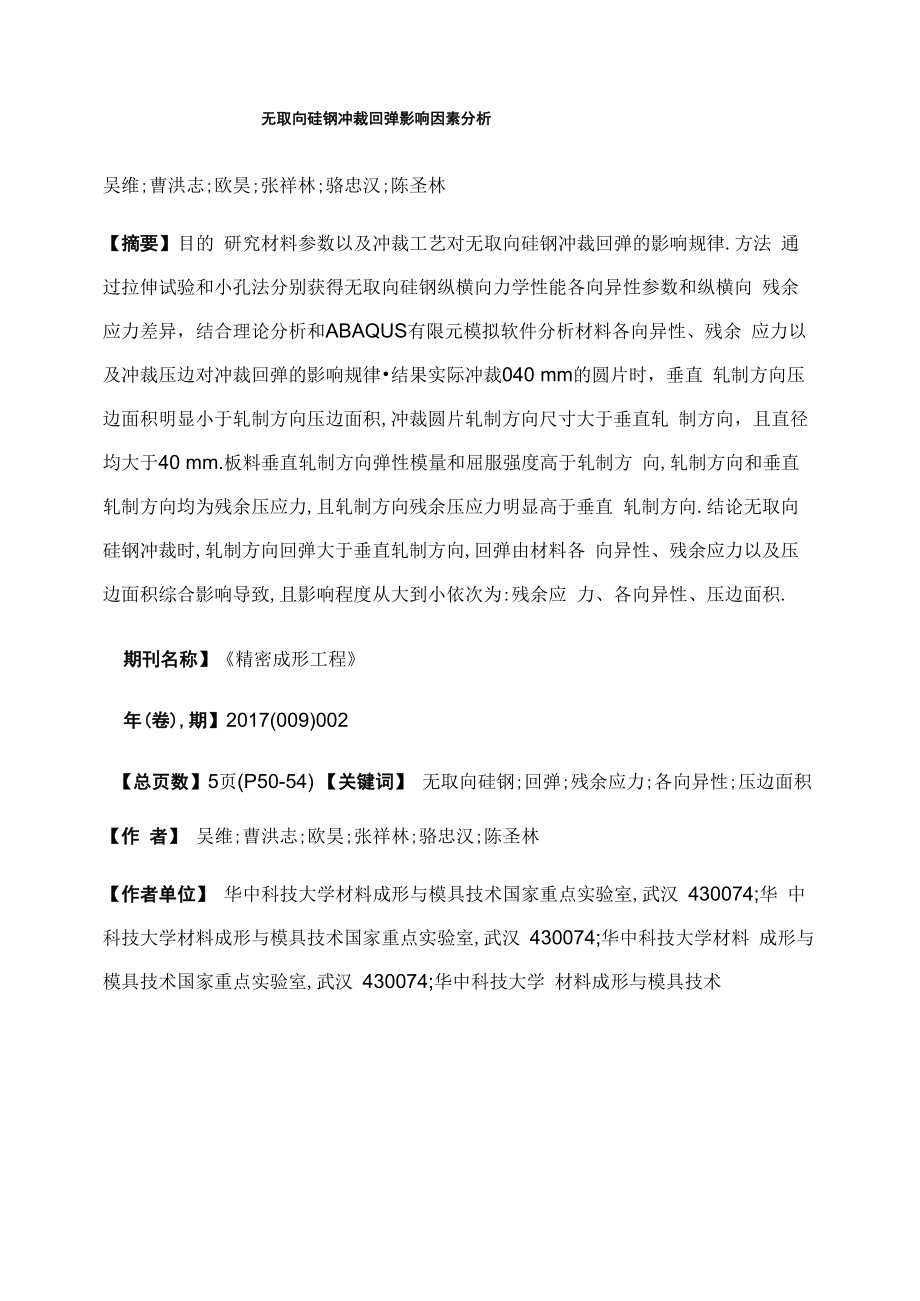


《无取向硅钢冲裁回弹影响因素分析》由会员分享,可在线阅读,更多相关《无取向硅钢冲裁回弹影响因素分析(9页珍藏版)》请在装配图网上搜索。
1、无取向硅钢冲裁回弹影响因素分析吴维;曹洪志;欧昊;张祥林;骆忠汉;陈圣林【摘要】目的 研究材料参数以及冲裁工艺对无取向硅钢冲裁回弹的影响规律.方法 通过拉伸试验和小孔法分别获得无取向硅钢纵横向力学性能各向异性参数和纵横向 残余应力差异,结合理论分析和ABAQUS有限元模拟软件分析材料各向异性、残余 应力以及冲裁压边对冲裁回弹的影响规律结果实际冲裁040 mm的圆片时,垂直 轧制方向压边面积明显小于轧制方向压边面积,冲裁圆片轧制方向尺寸大于垂直轧 制方向,且直径均大于40 mm.板料垂直轧制方向弹性模量和屈服强度高于轧制方 向,轧制方向和垂直轧制方向均为残余压应力,且轧制方向残余压应力明显高于垂
2、直 轧制方向.结论无取向硅钢冲裁时,轧制方向回弹大于垂直轧制方向,回弹由材料各 向异性、残余应力以及压边面积综合影响导致,且影响程度从大到小依次为:残余应 力、各向异性、压边面积.期刊名称】精密成形工程年(卷),期】2017(009)002【总页数】5页(P50-54) 【关键词】 无取向硅钢;回弹;残余应力;各向异性;压边面积【作 者】 吴维;曹洪志;欧昊;张祥林;骆忠汉;陈圣林【作者单位】 华中科技大学材料成形与模具技术国家重点实验室,武汉 430074;华 中科技大学材料成形与模具技术国家重点实验室,武汉 430074;华中科技大学材料 成形与模具技术国家重点实验室,武汉 430074;
3、华中科技大学 材料成形与模具技术国家重点实验室,武汉 430074;武汉钢铁(集团)公司 国家硅钢工程技术研究中心,武汉 430080;武汉钢铁(集团)公司 国家硅钢工程技术研究中心,武汉 430080【正文语种】中文【中图分类】TG306无取向硅钢作为一种重要的硅铁软磁材料,具有较低的铁损和较高的磁感特性,广 泛应用于电力、电子和军事工业等行业,是电机和压缩机铁芯的主要生产材12。 在电机、压缩机生产过程中,一定尺寸和形状的定转子铁芯通常是在级进模上冲裁 和叠压而成。冲裁过程见图1,在冲裁过程中,凸凹模间存在间隙,当凸模向下运 动时挤压板料,板料在凸凹模间隙处产生弯矩,且在凹模内部分会有一定
4、的弯拱, 冲裁结束后落料件的尺寸会大于凹模的尺寸,即回弹现象3。无取向硅钢由于冲 裁间隙很小,板料纵横向力学性能差异大,定转子冲裁落料件不同位置回弹量不同, 从而导致定转子间气隙不均匀,电机在运转时会出现噪声大、振动剧烈、耗电大等 缺陷。企业生产中一般要求定转子的实际冲裁尺寸与设计值误差在0.02 mm以内, 这就要求模具设计者在设计模具时要充分考虑无取向硅钢冲裁时不同部位的回弹, 从而对模具的尺寸进行适当的圆度补偿。目前对回弹的分析大多集中在弯曲回弹以及高强钢的冲压回弹方面46,对无取 向硅钢的研究则大部分集中在轧制和退火过程中的织构变化78以及冲剪加工对 磁性能的影响910,对于无取向硅钢
5、冲裁回弹则研究较少,但是无取向硅钢的 冲裁回弹却是一个不可忽视的问题,对于材料各向异性、残余应力分布以及压边面 积等因素对无取向硅钢冲裁回弹的影响一直缺乏系统研究,而模具企业在设计模具 时由于没有科学指导数据,经常通过多次试模来确定最终的模具尺寸,文中以武汉 钢铁集团公司生产的50WW470为材料,自主设计一套高精度冲压模具,分析冲 裁过程中的回弹现象,同时系统分析材料各向异性、残余应力分布以及压边面积对 冲裁回弹的影响。实验的材料为武汉钢铁集团生产的无取向硅钢,牌号为50WW470,厚度为0.5 mm。该牌号硅钢主要成分为质量分数大于97.4%的Fe,2%的Si,0.25%的Mn, 0.25
6、%的Al,不超过0.02%的P,不超过0.005%的S,不超过0.007%的C,其 密度为7.7 g/cm3,伸长率为37%,拉伸强度为450 MPa,硬度为HV155。为 简化实验模型,便于分析冲裁回弹的影响因素,实验设计一套高精度冲裁模具,冲 裁直径为040 mm的圆片,模具设计图和冲裁模具实物图分别见图2和图3。冲 裁模在型号Y41K-25的单柱校正压力机上冲裁,采用浮动式模架,来保证冲裁模 具的精度。冲裁板料剪切成300 mmx46 mm条料,沿轧制方向送料(长度方 向)。冲裁间隙根据冲裁企业和模具企业调研结果选取为双面间隙8%料厚。落料 圆片直径用微米千分尺测量,精度为1 pm,为避
7、免单次测量误差,通过多次测量 取平均值作为实际测试结果。2.1 回弹现象冲裁实验结果显示,冲裁落料圆片轧制方向的平均直径为40.022 mm,垂直轧制 方向的平均直径为40.008 mm,即冲裁后轧制方向和垂直轧制方向直径均大于 40 mm ,且轧制方向回弹比垂直轧制方向大14 pm。即冲裁回弹客观存在,且轧 制方向的回弹明显大于垂直轧制方向。造成回弹不一致的因素有很多,有研究表明, 冲裁间隙对回弹有较大影响,当冲裁间隙减小时,板料在凸凹模的间隙挤压变形更 加严重,板料的回弹也就更大1112。实验是在单一间隙下冲裁,轧制方向和 垂直轧制方向的冲裁间隙均为8%的料厚,因此造成轧制方向和垂直轧制方
8、向回弹 不一致的原因则可能是2个方向模具结构的差异或者是无取向硅钢材料本身在轧 制方向和垂直轧制方向的性能差异。2.2 压边面积差异 由于该冲裁模为圆形落料,模具结构(凸模、凹模以及卸料板等)在轧制方向和垂 直轧制方向均保持一致,该模具结构并不是导致2个方向回弹不一致的因素,但 是冲裁的无取向硅钢板料在轧制方向和垂直轧制方向上的尺寸分布却并不均匀,冲 裁板料为300 mmx46 mm条料,其排样见图4。由图4可知,实际冲裁时垂直 车b制方向上压边长度始终为3 mm,而条料是前后延伸的,实际冲裁时前一次冲 裁留下的废料和板料待冲裁的部分均为轧制方向的压边长度,因而在轧制方向上的 压边长度实际上远
9、大于3 mm。压边面积是影响冲裁回弹的一个重要因素13,在 相同的压边力下,压边面积越大,冲裁时材料向凸凹模间隙的流动越困难,流入间 隙的金属越少,冲裁后材料的回弹也会越小,因此单从压边面积方面考虑,轧制方 向压边多,该方向回弹小,冲裁后轧制方向的尺寸应该比垂直轧制方向小,但实际 情况是轧制方向的尺寸比垂直方向大,说明轧制方向上的回弹还受其他因素的影响, 且影响程度大于压边面积的影响。2.3 材料各向异性为探究材料力学性能参数在板料轧制方向和垂直轧制方向上有无明显的各向异性, 从原始无取向硅钢板料上分别沿着轧制方向和垂直轧制方向上制作拉伸标准样,进 行单向拉伸试验获得材料的力学性能参数。轧制方
10、向上,屈服强度为345.38 MPa, 抗拉强度为476.88 MPa,伸长率为27.98%,弹性模量为183.5 GPa ;垂直轧制 方向上,屈服强度为360.85 MPa,抗拉强度为495.36 MPa,伸长率为31.16% , 弹性模量为202.0 GPa,对比2个方向的力学性能参数可以发现,轧制方向上的 屈服强度、抗拉强度以及弹性模量均小于垂直轧制方向。冲裁回弹大小与屈服强度 和弹性模量均相关,当材料弹性模量相同或相近时,屈服强度越大,冲裁后材料回 弹越大;而当材料的屈服强度相同或者相近时,弹性模量越大,冲裁后材料回弹越 小14。虽然实验结果显示,轧制方向的屈服强度和弹性模量均比垂直轧
11、制方向小, 但是轧制方向屈服强度相对垂直轧制方向小4.3%,而弹性模量相对垂直轧制方向 小9.2% , 2个方向上弹性模量的差异更加明显,对回弹的影响也会更大。轧制方 向弹性模量小,冲裁后的回弹更大,这与冲裁结果相一致,认为无取向硅钢2个 方向上的弹性模量是影响冲裁回弹的一个重要因素。2.4 残余应力分布 在考虑材料性能的差异时,残余应力作为一个重要的性能指标也应被考虑。由于所 试验的无取向硅钢板料的厚度为0.5 mm,综合比较几种常用的残余应力测量手段(X衍射残余应力测试法、纳米压痕测试法、小孔法),采用小孔法测量轧制方向 和垂直轧制方向上的残余应力。测试时使用BE120-2CA-K型应变花
12、,分别测量钻 孔后0(轧制方向), 45, 90(垂直轧制方向)的应变,然后根据残余应力计算 公式分别计算0和90方向上的残余应力15 , 3次测量结果显示,轧制方向上残 余应力分别为-127.67,-178.74,-212.24 MPa;垂直轧制方向上残余应力分别为 -78.00, -86.30, -136.61 MPa。对比轧制方向和垂直轧制方向上的残余应力分布,可以发现,该材料在2个方向 上的残余应力均为残余压应力,且轧制方向上的残余压应力明显大于垂直轧制方向, 数值大小近似为垂直轧制方向的2倍。冲裁时材料内部平衡被打破,残余应力得 到释放。由于初始应力为残余压应力,压应力释放后材料趋于
13、向外回复16,而轧 制方向上的残余压应力更大,材料冲裁后在该方向上的回复就更大,从而导致轧制 方向回弹比垂直轧制方向大。即残余应力在轧制方向和垂直轧制方向上的不均匀分 布也是材料冲裁后回弹不一致的重要原因。由于冲裁回弹的影响因素有多种,包括上面分析过的压边面积、材料的各向异性以 及残余应力,但是无法通过传统的实验手段对这些因素进行逐一剥离验证。在模拟 的前处理阶段,有限元数值模拟可以将这些因素分别定义与输入,通过改变这些参 数多次模拟计算,从而分析出单个因素的影响以及不同因素之间的影响程度大小, 从而到达传统实验无法完成的部分,同时与传统实验的结果进行相互验证17 18。为探究压边面积、材料各
14、向异性以及残余应力分布对冲裁回弹的影响程度大小,何 种因素占主导地位,采用ABAQUS有限元模拟软件,分别输入3种因素对冲裁过 程进行模拟。冲裁过程采用Dynamic, Explicit模块,将拉伸试验获得的材料拉伸 过程中的名义应力与名义应变换算成对应的真实塑性应力与真实塑性应变,作为材 料的塑性参数输入。弹性模量的各向异性通过在弹性参数中选择Engineering Constants进行定义,厚度方向弹性模量与垂直轧制方向一样。残余应力通过在 预应力场中得初始应力状态中设置纵横向不同的应力值。为提高模拟的精度,在板 料冲裁区域采用网格局部细化,模拟的模型图以及无取向硅钢板料的网格模型见图
15、5和图6。 为探究3种因素对回弹的影响,设置4组参数进行模拟计算,板料的尺寸始终固 定为60 mmx46 mm(轧制方向压边多,垂直轧制方向压边少),板料网格和边 界条件始终固定不变。第1组参数设置为材料各向同性,轧制方向和垂直轧制方 向弹性模量均为183.5 GPa ,验证压边面积对回弹的影响;第2组参数设置为材 料各向异性,轧制方向弹性模量为183.5 GPa,垂直轧制方向弹性模量为202.0 GPa,验证压边面积和弹性模量对回弹的影响;第3组参数设置残余应力,材料设 置为各向同性,弹性模量均为183.5 GPa,但是轧制方向残余应力设置为-100 MPa,垂直轧制方向残余应力设置为-50
16、 MPa,验证压边面积和残余应力对回弹 的影响;第4组参数设置为材料各向异性和残余应力,轧制方向弹性模量为183.5 GPa,垂直轧制方向弹性模量为202.0 GPa,轧制方向残余应力设置为-100 MPa , 垂直轧制方向残余应力设置为-50 MPa ,验证压边面积、弹性模量和残余应力3 种综合对回弹的影响。将模拟得到的轧制方向的尺寸减去垂直轧制方向的尺寸作为回弹的差异。上述4 种参数模拟得到的回弹差分别为-7.6, 5.1, 9.2, 13.6 pm。可以发现,当无取向硅 钢板料设置成各向同性,只有压边面积影响时(第1组) ,冲裁后轧制方向的尺 寸比垂直轧制方向小7.6 pm,说明压边面积
17、小的方向回弹量大;对施加各向异性 时(第2组),冲裁后轧制方向的尺寸比垂直轧制方向大5.1 pm,则弹性模量越 大的方向回弹越小,而且弹性模量的影响程度大于压边面积的影响,冲裁后弹性模 量造成的回弹大于压边面积造成的回弹,从而导致最终的回弹尺寸是轧制方向尺寸 大;对材料只施加残余应力时(第3组) ,冲裁后轧制方向的尺寸比垂直轧制方 向大9.2 pm ,差值比第2组的结果更大,认为残余应力对回弹的影响比弹性模量 的影响更大,残余压应力越大,冲裁后的回弹越大;对材料同时施加各向异性和残 余应力时(第4组),冲裁后轧制方向的尺寸比垂直轧制方向大13.6 pm, 2个 方向的回弹差异更大。更加验证之前
18、3种因素对回弹影响的分析,而且其数值大 小与冲裁实验时的回弹差值相近,也从另一个方面说明了模拟的准确性,同时,将 4组数据综合来看可以发现,3种因素之间的影响并非是简单的代数加减(如果是 代数相加,第 4 组的回弹差应该是第 2 组数据加上第 3 组数据再减去第 1 组数据, 其差值应该为2 1.9 pm ) ,因此认为这3种因素在实际的冲裁过程中是相互影响 的,并非相互独立的影响因素。1)无取向硅钢冲裁时,回弹现象明显,冲裁后落料件尺寸大于凹模设计尺寸,且 轧制方向回弹大于垂直轧制方向。2)压边面积、材料各向异性以及残余应力均对冲裁回弹有较大影响。压边面积越 大,冲裁后回弹越小;材料屈服强度
19、相近时,弹性模量越小,冲裁后回弹越大;残 余压应力越大,冲裁后回弹越大。3)压边面积、材料各向异性以及残余应力三者对回弹的影响程度从大到小依次为 残余应力,弹性模量,压边面积,且三者之间相互影响,并不是简单的代数叠加。相关文献】1 CULLITY B D, GRAHAM C D. Introduction to Magnet-ic MaterialsM. John Wiley & Sons, 2008.2 汪水泽,李长生,王廷溥,等薄板坯连铸连轧生产无取向硅钢技术的发展及前景J钢铁研究学 报, 2008, 20(9): 14. WANG Shui-ze, LI Chang-sheng, WNA
20、G Ting-pu, et al. Development and Future of Non-Oriented Silicon Steel Manufactured by Thin Slab Casting and Rolling TechnologyJ. Journal of Iron and Steel Research, 2008, 20(9): 14.3 罗云华,王磊.高强钢板冲压回弹影响因素研究J.锻压技术,2009, 34(1): 2326. LUO Yun- hua, WANG Lei. Research on Influencing Factors of Springback
21、 during Sheet Metal Stamping of High Strength SteelJ. Forging & Stamping Technology, 2009, 34(1): 2326.4 张松殷晨波,张在梅.铝合金汽车覆盖件冲压成形回弹的仿真研究J.机械设计与制造,2011(2): 109111. ZHANG Song, YIN Chen-bo, ZHANG Zai-mei. Research on Springback Numerical Simulation of Sheet Metal Forming of Aluminum Alloy Automobile Pan
22、elJ. Machinery Design & Manufacture, 2011(2): 109111.5 胡志超,李延平,常勇,等基于数值模拟的板料冲压成形回弹补偿方法J.锻压技术,2012, 37(2): 163166. HU Zhi-chao, LI Yan-ping, CHANG Yong, et al. Compensation Algorithm for Springback in Sheet Metal Forming Based on Numerical SimulationJ. Forging & Stamping Technology, 2012, 37(2): 1631
23、66.6 CHAN W M, CHEW H I, LEE H P, et al. Finite Element Analysis of Spring-back of V- bending Sheet Metal Forming ProcessesJ. Journal of Materials Processing Technology, 2004, 148(1): 1524.7 SANJARI M, HE Y, HILINSKI E J, et al. Development of the 113 Texture during the Annealing of a Skew Cold Roll
24、ed Non-oriented Electrical SteelJ. Scripta Materialia, 2016, 124: 179183.8 PAOLINELLI S C, CUNHA M A, COTA A B. Effect of Hot Band Grain Size on the Texture Evolution of 2% Si Non-Oriented Steel During Final AnnealingJ. IEEE Transactions on Magnetics, 2015, 51(6): 14.9 SALEEM A, ALATAWNEH N, CHROMIK
25、 R R, et al. Effect of Shear Cutting on Microstructure and Magnetic Properties of Non-Oriented Electrical SteelJ. IEEE Transactions on Magnetics, 2016, 52(5): 14.10 LEWIS N, ANDERSON P, HALL J, et al. Power Loss Models in Punched Non-Oriented Electrical Steel RingsJ. IEEE Transactions on Magnetics,
26、2016, 52(5): 14.11 郑辉.论冲裁间隙J.现代制造技术与装备,2009(4): 4749. ZHENG Hui. The Discussion of Punching ClearanceJ. Modern Manufacturing Technology and Equipment, 2009(4): 4749.12 白云.冲裁工艺中模具间隙的研究J.金属加工:热加工,2015(9): 2728. BAI Yun. The Study of Mould Clearance in Punching ProcessJ. MW Metal Forming, 2015(9): 2728
27、.13 CHEN P, KOC M. Simulation of Springback Variation in Forming of Advaneed HighStrength SteelsJ. Journal of Materials Processing Technology, 2007, 190(1): 189 198.14 张如华.冲压工艺与模具设计M.北京:清华大学出版社,2006. ZHANG Ru-hua. Stamping Process and Die DesignM. Beijing: Tsinghua University Press, 2006.15 RENDLER
28、N J, VIGNESS I. Hole-drilling Strain-gage Method of Measuring Residual StressesJ. Experimental Mechanics, 1966, 6(12): 577 586 .16 曹洪志,郝林坡,吴维,等.模具间隙对无取向硅钢冲片质量的影响研究几锻压技术,2016, 41(3): 9498. CAO Hong-zhi, HAO Lin-po, WU Wei, et al. Research on Influence of Die Clearance on the Quality of Non-oriented E
29、lectrical Steel PartsJ. Forging & Stamping Technology, 2016, 41(3): 9498.17 FRIES T P, BELYTSCHKO T. The Extended/ Generalized Finite Element Method: an Overview of the Method and Its ApplicationsJ. International Journal for Numerical Methods in Engineering, 2010, 84(3): 253304.18 LEE M G, KIM S J, WAGONER R H, et al. Constitutive Modeling for Anisotropic/Asymmetric Hardening Behavior of Magnesium Alloy Sheets: Application to Sheet SpringbackJ. International Journal of Plasticity, 2009, 25(1): 70104.
- 温馨提示:
1: 本站所有资源如无特殊说明,都需要本地电脑安装OFFICE2007和PDF阅读器。图纸软件为CAD,CAXA,PROE,UG,SolidWorks等.压缩文件请下载最新的WinRAR软件解压。
2: 本站的文档不包含任何第三方提供的附件图纸等,如果需要附件,请联系上传者。文件的所有权益归上传用户所有。
3.本站RAR压缩包中若带图纸,网页内容里面会有图纸预览,若没有图纸预览就没有图纸。
4. 未经权益所有人同意不得将文件中的内容挪作商业或盈利用途。
5. 装配图网仅提供信息存储空间,仅对用户上传内容的表现方式做保护处理,对用户上传分享的文档内容本身不做任何修改或编辑,并不能对任何下载内容负责。
6. 下载文件中如有侵权或不适当内容,请与我们联系,我们立即纠正。
7. 本站不保证下载资源的准确性、安全性和完整性, 同时也不承担用户因使用这些下载资源对自己和他人造成任何形式的伤害或损失。
最新文档
- 三基培训ppt课件--抗生素的分类及临床应用
- 三年级科学上册3.2《果实累累的季节》-ppt课件大象版
- 《离子键》ppt教学讲解课件
- 三年级科学上册4.2《动物怎样过冬》-ppt课件大象版
- 中考“转换”专题徽标类资料课件
- 人力资源管理师(二级第三章师级培训开发)课件
- 《利用相似三角形测高》教学ppt课件
- 两条直线的交点坐标及两点间的距离公式课件
- 人力资源管理师(四级)第三版-第六章-劳动关系管理课件
- 严格按照定额计价即施工图预算法课件
- 《良性前列腺增生》PPT课件
- 《廉颇蔺相如列传》复习ppt课件上课
- 人教版九年级物理上册ppt课件第十五章电流和电路
- 严谨务实准确高效课件
- 《廉颇蔺相如列传》公开课优质课ppt课件