车辆安全与RAMS思考
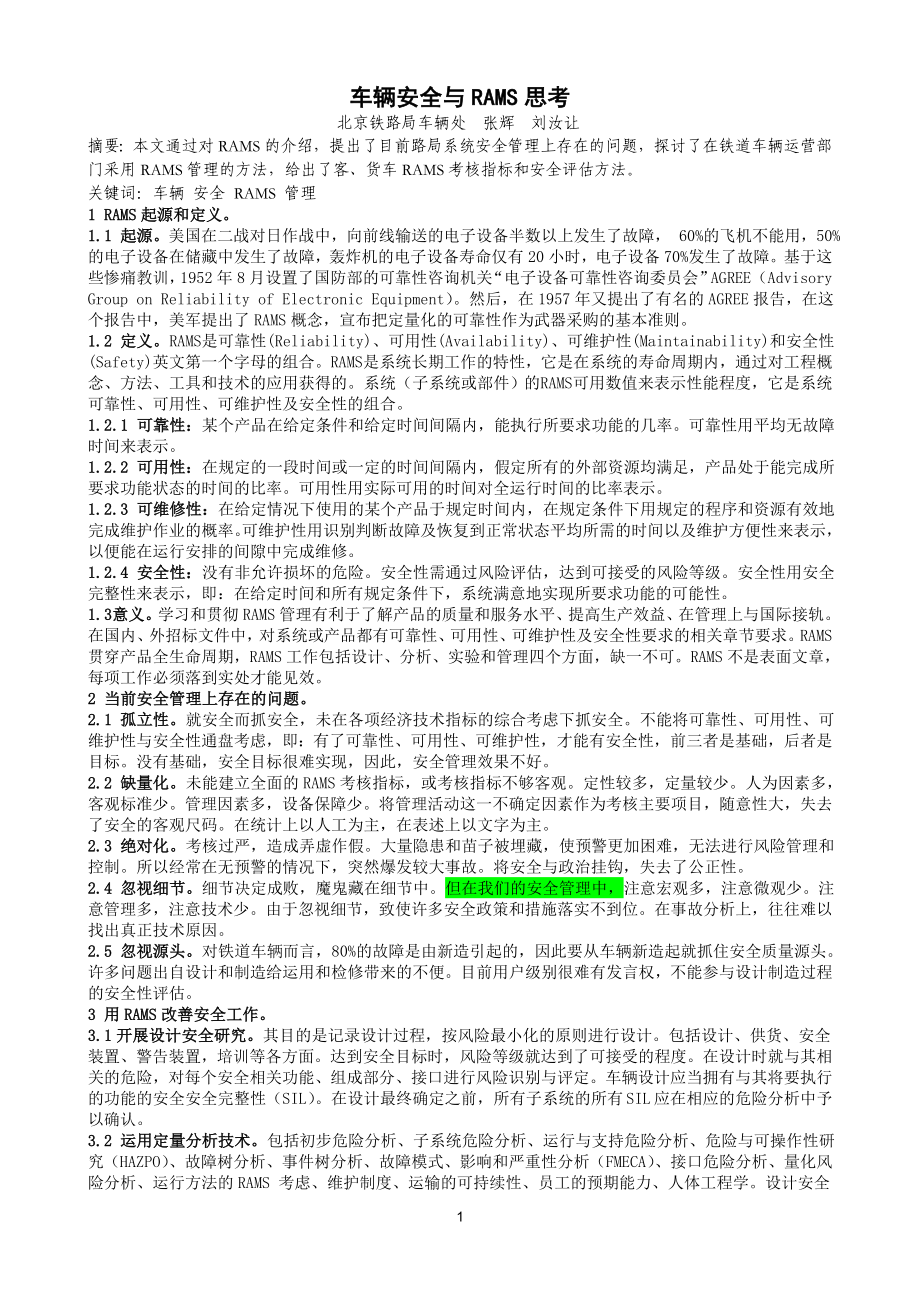


《车辆安全与RAMS思考》由会员分享,可在线阅读,更多相关《车辆安全与RAMS思考(7页珍藏版)》请在装配图网上搜索。
1、车辆安全与RAMS思考 北京铁路局车辆处 张辉 刘汝让摘要:本文通过对RAMS的介绍,提出了目前路局系统安全管理上存在的问题,探讨了在铁道车辆运营部门采用RAMS管理的方法,给出了客、货车RAMS考核指标和安全评估方法。关键词:车辆 安全 RAMS 管理 1 RAMS起源和定义。1.1 起源。美国在二战对日作战中,向前线输送的电子设备半数以上发生了故障, 60%的飞机不能用,50%的电子设备在储藏中发生了故障,轰炸机的电子设备寿命仅有20小时,电子设备70%发生了故障。基于这些惨痛教训,1952年8月设置了国防部的可靠性咨询机关“电子设备可靠性咨询委员会”AGREE(Advisory Grou
2、p on Reliability of Electronic Equipment)。然后,在1957年又提出了有名的AGREE报告,在这个报告中,美军提出了RAMS概念,宣布把定量化的可靠性作为武器采购的基本准则。1.2 定义。RAMS是可靠性(Reliability)、可用性(Availability)、可维护性(Maintainability)和安全性(Safety)英文第一个字母的组合。RAMS是系统长期工作的特性,它是在系统的寿命周期内,通过对工程概念、方法、工具和技术的应用获得的。系统(子系统或部件)的RAMS可用数值来表示性能程度,它是系统可靠性、可用性、可维护性及安全性的组合。1
3、.2.1 可靠性:某个产品在给定条件和给定时间间隔内,能执行所要求功能的几率。可靠性用平均无故障时间来表示。1.2.2 可用性:在规定的一段时间或一定的时间间隔内,假定所有的外部资源均满足,产品处于能完成所要求功能状态的时间的比率。可用性用实际可用的时间对全运行时间的比率表示。1.2.3 可维修性:在给定情况下使用的某个产品于规定时间内,在规定条件下用规定的程序和资源有效地完成维护作业的概率。可维护性用识别判断故障及恢复到正常状态平均所需的时间以及维护方便性来表示,以便能在运行安排的间隙中完成维修。1.2.4 安全性:没有非允许损坏的危险。安全性需通过风险评估,达到可接受的风险等级。安全性用安
4、全完整性来表示,即:在给定时间和所有规定条件下,系统满意地实现所要求功能的可能性。1.3 意义。学习和贯彻RAMS管理有利于了解产品的质量和服务水平、提高生产效益、在管理上与国际接轨。在国内、外招标文件中,对系统或产品都有可靠性、可用性、可维护性及安全性要求的相关章节要求。RAMS贯穿产品全生命周期,RAMS工作包括设计、分析、实验和管理四个方面,缺一不可。RAMS不是表面文章,每项工作必须落到实处才能见效。2 当前安全管理上存在的问题。2.1 孤立性。就安全而抓安全,未在各项经济技术指标的综合考虑下抓安全。不能将可靠性、可用性、可维护性与安全性通盘考虑,即:有了可靠性、可用性、可维护性,才能
5、有安全性,前三者是基础,后者是目标。没有基础,安全目标很难实现,因此,安全管理效果不好。2.2 缺量化。未能建立全面的RAMS考核指标,或考核指标不够客观。定性较多,定量较少。人为因素多,客观标准少。管理因素多,设备保障少。将管理活动这一不确定因素作为考核主要项目,随意性大,失去了安全的客观尺码。在统计上以人工为主,在表述上以文字为主。2.3 绝对化。考核过严,造成弄虚作假。大量隐患和苗子被埋藏,使预警更加困难,无法进行风险管理和控制。所以经常在无预警的情况下,突然爆发较大事故。将安全与政治挂钩,失去了公正性。2.4 忽视细节。细节决定成败,魔鬼藏在细节中。但在我们的安全管理中,注意宏观多,注
6、意微观少。注意管理多,注意技术少。由于忽视细节,致使许多安全政策和措施落实不到位。在事故分析上,往往难以找出真正技术原因。2.5 忽视源头。对铁道车辆而言,80%的故障是由新造引起的,因此要从车辆新造起就抓住安全质量源头。许多问题出自设计和制造给运用和检修带来的不便。目前用户级别很难有发言权,不能参与设计制造过程的安全性评估。3 用RAMS改善安全工作。3.1开展设计安全研究。其目的是记录设计过程,按风险最小化的原则进行设计。包括设计、供货、安全装置、警告装置,培训等各方面。达到安全目标时,风险等级就达到了可接受的程度。在设计时就与其相关的危险,对每个安全相关功能、组成部分、接口进行风险识别与
7、评定。车辆设计应当拥有与其将要执行的功能的安全安全完整性(SIL)。在设计最终确定之前,所有子系统的所有 SIL 应在相应的危险分析中予以确认。3.2 运用定量分析技术。包括初步危险分析、子系统危险分析、运行与支持危险分析、危险与可操作性研究(HAZPO)、故障树分析、事件树分析、故障模式、影响和严重性分析(FMECA)、接口危险分析、量化风险分析、运行方法的RAMS 考虑、维护制度、运输的可持续性、员工的预期能力、人体工程学。设计安全研究应当特别参考来自维护的正常、降级运行模式、紧急情况、有效性或自然灾害,建议缓解的措施。3.3 抓源头质量。每个车型主导厂和配套厂应对其设计制造厂的子系统的
8、RAMS 参数都要进行分析,必须根据用户的RAMS计划进行所有的响应分析,从理论预测角度说明该型车及其子系统都能够达到要求。如果任一承包商/分包商未能达到其指定的目标,应改变设计,重新计算系统的运用性能。应在基本设计阶段和详细设计阶段均向用户提交一份 RAMS分析与预测报告。制造商RAMS 分析和预测报告的结果应与用户的运行维护计划完全一致。为此,路局系统应主导车辆制造的RAMS计划编制。3.3.1 开展可靠性预测。应进行可靠性性能的估计,并将其与系统和子系统的指定目标进行比较。在设计阶段早期识别潜在缺陷,并采取纠正措施,修改设计,以改善识别潜在缺陷。在制造前,在已说明所有潜在缺陷并且满足指定
9、要求后,更新可靠性预测,还应进行可靠性持续性的推测。可靠性是一项重要的质量指标,只是定性描述不行,必须使之数量化,这样才能进行精确的描述和比较。可靠性的定量表示有其自己的特点,由于使用场合的不同,要根据车辆运用特征量来制定。3.3.2 开展可用性预测。系统级别的可用性目标一般应为 99.93 %。应识别可能导致服务故障的系统故障,并预测每年此类事件的频率。制造商应使用故障平均时间(MTBF)到维修平均时间(MTTR)进行系统和子系统可用性计算,使用以下公式:MTBFMTBF 可用性 = -MTTR+MTBF采用以更换插件作为故障的统计方法是直观易行的,可以在相当程度上反映产品的质量,由此得到的
10、实际平均无故障时间AMTBF可以作为衡量危害出现频度的依据。3.3.3 开展可维护性预测。以深度要求的专业判断为基础,进行可维护性性能估计,并将结果与指定目标相比较,以在设计阶段早期识别潜在缺陷,采取纠正措施改善潜在缺陷。完善的维护计划应包括预防性维护活动的程度和频率,保证满足平均修复时间( MTTR)得到满足。为提供高级别的系统可用性并将 MTTR 降至最低,所有子系统应根据 LRU (现场可更换单元)概念进行设计,以确保下线维修中的故障子装置快速替换。4制定RAMS指标。当前我国并未能制定出铁道车辆的RAMS指标。笔者建议按如下思路制定车辆设计、制造、运用、检修一体化考核指标。4.1 客车
11、。4.1.1 可用性。序号项目指标备注1运行前的各项始发试验时间少于15分钟2列车准备的过程时间少于1小时如预冷或预热3将列车拖出或自行退出主干线的时间少于15分钟列车重大故障的情况下,在救援抵达时4在发现故障后,处理故障并重新投入运行的时间少于5分钟列车出现较小故障的情况下(并没有造成商业服务的中断)5从车辆的一侧或两侧将水、沙子、挡风玻璃液、气体等充注(整备)少于10分钟能通过充注指示器观察6从车辆的一侧或两侧排放和冲洗厕所少于10分钟能通过状态指示器观察7集便器容量大于等于2天8救援联挂装有自动车钩,可实现救援时自动机械和电气连挂。连接地点不受约束。需与救援车辆可进行通讯连接。9故障诊断
12、有一套维护、诊断、检测、记录辅助软件系统,以便于执行自动测试, 记录配置、状态数据、运行操作和设备故障。要求故障代码系统完善。10可测试性易于通过通用或专用设备检测故障。11平均修复时间(MTTR)对于95%的车辆故障而言,处理不得超过1小时。诊断错误或未发现故障不得超过10%。12模块化通过基本单元的并置或者组合来完成,易于判断故障和配件的更换和组装。最大程度地使用模块化设计.13可及性维护人员能够触及和接近故障处所。14可互换性通过一个相似的备件来更换替代车辆的某个元件、配件或者设备单元。无严格限制。15可替换能力“可替换”具有拆分和装配配件和基本元件的能力特点。不同设计阶段的产品具有通用
13、替换性。16可安装和拆除能力在一个元件或一个部件的装配之间,能够拆除和安装相关各元件。17外皮可清洗能力可使用一台固定的清洗机来进行外部清洗,无障碍物。可贯穿通过洗车机18检测和调整磨损极限易于从车辆的外部获得磨损和调整数值。 通过驾驶室中的辅助维护软件系统来自动记录检测信息。19当地卫生安全措施确保符合当地卫生和安全的法律和法规。20人体工程学使维护人员在各种条件下执行其维护任务所使用的设备也应该符合人体工程学。4.1.2 可维修性。1年走行公里60万公里2润滑要求允许尽可能简单地进行润滑。3防污染防止和保护机械关节(阻尼器等)进沙子和受到污染。可简单地检查气动回路。防止电子部件堵塞和受到污
14、染。4易于检查不必拆卸,可通过非破坏性试验(着色、渗透、超声波、磁力试验等)可以检查部件的安全性。可使用传统工具抽出零部件。5现场可更换单元允许单独拆卸和重新组装的每个LRU,可以很容易地触及每个重型部件或者LRU。可采用滑动或者伸缩导轨。使用叉车可以直接进行安装和拆卸。(LRU:大型互换配件更换)6转向架能够对转向架的关键部件进行调整、测量和更换(闸盘、闸瓦、踏面等)。(带着轮轴和可能的转向系统)。应允许在车间停车线上移动转向架。使用拖车可以移动、牵引转向架,包括转弯.可从地沟进行直接的外观检查,不用专用工具的调节。7轮轴允许高压水清洗,不会造成任何的轴箱损坏。可使用不落轮镟。可使用固定式超
15、声波探伤仪,踏面诊断以及车轮裂纹检测。8所有的维修活动持续时间少于4小时包括清理9低级修程走行公里大于或等于5000公里10外接电源可实现从外部的电气箱向车辆供电或者蓄电池充电11简易维修不会拆卸相邻的部件,就可进行简单的修理维修(排放、过滤器更换、调整等)。12部件清洗可进行列车内部简单的每日保洁: 座椅、地板、面板、门、窗等。易于维护装饰罩、机柜、侧板、车内底板、天花板、窗户、照明灯具、视听设备及外部设备箱。13使用安全性发生故障的部件不会造成列车内的乘客伤害以及跌落伤人。14电气和电子设备类LRU不同种类 LRU 的数量应保持最低。充分利用 LRU 的可互换性。LRU 应能防止误插入或连
16、接。优先考虑使用“插入”的连接方法。且每个 LRU 的最大重量不得超过 15 kg。15寿命及中期寿命。寿命30年。寿命中期15年时允许翻新改造。16大修修时4天车身结构无重大改变17车窗要求不超过4天。允许从车辆的内部,更换所有的车厢侧窗。18仓储配件能够在一般条件下进行仓储、包装和运输。19耐脏性其可见表面不易于变脏。外形无凸凹,没有可能积聚污物的空间.并且具有相应合适的耐磨、耐撕、抗冲击、耐切割以及抗光晒的能力。20抗破坏能力所使用的布置和材料应该尽可能地防止诸如涂鸦、切割、拆除、破碎等破坏行为。易于清洗污渍(油漆喷涂、涂鸦、粘贴胶)。21耐腐蚀承受频繁使用不同的维护材料(酸性或者碱性清
17、洗液、油基溶剂)及清洗刷的机械动作.其表面外观的颜色没有改变并且没有显著的磨损。22废弃组件报废,在没有进行任何接口修改的情况下,设备的设计应该易于替换备件,功能不变。机械修改、电气修改或者软件修改.废弃件无污染。4.1.3寿命周期成本(LCC)系数。寿命周期成本为:客车整个寿命期间的各级维修成本之和。如果每组客车每年平均各级维修成本之和为600万元,寿命为30年,则该型车的寿命周期成本为:600*30=18000万元。寿命周期成本系数为:寿命周期成本/该组客车新造价格。如果该车组新造价格为9000万元,则寿命周期成本系数为18000/9000=2。国际上客车寿命周期成本系数一般为2,如果我国
18、客车配件国产化率较低,或维修频率较高,造成该值过高,就要引起注意。4.2 货车。4.2.1 RAMS指标。序号性能项目定义单位指标备注1可靠性机破率=Nf/t%每年故障数2临修率%每年平均摘车数3平均故障间隔时间MTBF=t/Nf小时/次累计工作时间与故障次数之比4不良反应次以外局电报为准5厂、段修故障率%借助于HMIS6网络抽查排名质量故障辆数、质量故障辆次、质量故障件数数部电统计7大修周期时间年2或走行公里8辅修车占全部货车比例小于1的数09货车日临修率%0.30%10使用寿命年5-30年11运用车保有量量12 日车公里(km/d)48013可用性货车检修率检修货车数/保有数%0.2614
19、平均休车时间某种修程修竣车辆总检修时间/该修程修竣的车辆数日厂修10天,段修3天。车辆检修全周转时间15段修循环系数1年/段修周期小于1的数0.716辅修循环系数1年/辅修周期小于1的数017车辆利用率现有运用车总数/现有车总数18可用度现有运用车总数/现有车总数19可维修性可达性20互换性21防误装22维修安全性23易检测24贵重部件可修复25维修难度小26货车段修台位利用系数日段修车数/台位数大于1的数1.427货车站修台位利用系数日辅修+临修数修车数/台位数大于1的数1.828人体工程学要求29平均修复时间MTTR=t/n30最大修复时间MTTRMAX=t/n31维修费用万元/辆万元32
20、段修劳动生产率全年段修数/段修人员辆/人年2433寿命周期成本整个寿命期间的各级维修成本之和/新造价格大于1的数2.434安全性特别重大事故sh=Nsh/t小于1的数部安全通报35MTBF=t/Nsh天部安全通报36重大事故sh=Nsh/t小于1的数部安全通报37MTBF=t/Nsh天部安全通报38较大事故sh=Nsh/t小于1的数部安全通报39MTBF=t/Nsh天部安全通报40一般事故sh=Nsh/t小于1的数部安全通报41MTBF=t/Nsh天部安全通报4.2.2 指标的相互关系。 保有量:管内所有车辆总数,是反映运用车规模的核心指标。运量与保有量有国际上有一个适当比例,如果保有量高于运
21、量过多,说明车辆可用性低。 日车公里:反映了车辆运用的强度,一般以年计算:日车公里365天=万公里,普通车按10万公里/年计算,大秦铁路按20万公里/年计算。日车公里与检修周期相匹配,如运用强度低,而检修周期短,说明车辆可用性不好。段修循环系数:1年/段修周期。如段修周期1.5年,则段修循环系数=1/1.5=0.67。管内发生段修数与段修能力应基本平衡。段修周期与车辆寿命周期成本密切相关,最重要的是处理好安全性与寿命周期成本的关系,应按国际标准控制。货车段修台位利用系数:以每日一个台位应修一辆车计算,货车段修台位利用系数=实际修车数/台位能力数。表明了车辆修理的难度,直接影响可维修性。保有量段
22、修循环系数=段修台位货车段修台位利用系数,因此,对每个局来说,管内发生段修数与段修能力应基本平衡。辅修循环系数:与段修循环系数相似,但如取消辅修,则该数为零。货车日临修率:每日发生临修占保有量的比率,货车日临修率=临修数/报有量。表明了货车的可靠性。临修数=临修率保有量=段修台位货车段修台位利用系数,即:管内发生临修数与临修能力应基本平衡。段修劳动生产率:考核段修生产效率的指标,段修劳动生产率=年换算段修数/从事段修人员数。寿命周期成本:同客车。 5. 开展安全完整性评估。5.1安全完整性等级(SIL)。SIL是Safety Integrity Level的缩写,译为安全完整性等级。SIL是在
23、1998年颁布的IEC61508功能安全标准中首次提出的,它是功能安全等级的一种划分,将SIL划分为4级,即SIL1,SIL2,SIL3和SIL4。安全相关系统的SIL应该达到哪一级别,是由风险分析得来的,即通过分析风险后果严重程度、风险暴露时间和频率、不能避开风险的概率及不期望事件发生概率这四个因素综合得出。级别越高要求其危险失效概率越低。SIL整体安全性等级 PFD按要求的故障概率 PFH每小时的危险故障概率110-210-1 10-610-5210-310-2 10-710-6310-410-310-810-7410-510-410-910-8SIL概念使得车辆段的运用能够根据预期损害来
24、划分其设备的要求。另外,SIL概念为产品制造商提供了一个描述产品故障性能的方法。SIL概念就是评定故障及其后果,评估结果是根据概率计算得出的。实际运用中最高安全目标应等于或低于这些数值。安全完整性等级的确定需要进行安全系统风险分析,它是进行系统 研发的目标和基础,是评估系统能否保证安全的依据。车辆运用应具有以下安全记录:每 108 人次公里死亡人数每 108 小时死亡人数0,0425.2 风险评估5.2.1 危险发生频率以下类别可用于对危险发生频率进行分类类别每年危险发生频率说明频繁性F 102可能频繁发生。将继续发生危险。可能性101 F 102将发生数次。危险可能经常发生。偶然性10-2
25、F 101在系统寿命周期内可能发生数次危险。渺小的10-4 F 10-2在系统寿命周期的某个时间可能发生。但是在系统寿命周期内发生危险的概率较低。不大可能10-6 F 10-4不大可能发生,但仍有概率。可以假定危险可能意外发生。难以置信P 10-6极其不可能发生。可以假定危险不会发生。5.2.2 危险严重性以下类别应当用于对危险发生的严重性进行分类:纳入考虑范围的后果是为人员、系统和环境后果。严重性等级人员或环境后果系统后果灾难性的一个或多个伤亡事故和/或主要的环境毁坏列车运行的丧失严重的单次伤亡和/或严重伤害和/或重大环境毁坏。主系统丧失边缘性的较轻的伤害和/或重大的环境威胁。严重的系统损坏
26、无关紧要的可能的较轻的伤害较轻的系统损坏5.2.3 风险评估方法用如下所示矩阵进行评估,后果的严重性与发生频率组合在一起以进一步处理风险。此矩阵给出了危险发生频率与严重性的可能组合,它同样给出了风险可接受性的各种区域。严重性无关紧要的边缘性的严重的灾难性的频率频繁性R3R4R4R4可能性R2R3R4R4偶然性R2R3R3R4渺小的R1R2R3R3不大可能R1R1R2R2难以置信R1R1R1R1其中:风险指数R1,指可忽略的风险评估,是无需同意就可以接受的。风险指数R2,指可容忍的风险评估,是须有足够的控制和安全管理部门的同意后才可接受的。风险指数R3,指不希望的风险评估,是只有在风险抑减不可行,且取得安全管理部门的同意后才可接受的。风险指数R4,指不可容忍的风险评估,是应予以排除的。注:本文作者简介张辉:北京铁路局车辆处,工程师,副处长,1977年10月出生,男,内蒙古赤峰刘汝让:北京铁路局车辆处,教授级高工,副科长,1960年6月出生,北京市(电话:13501362272) 2013年4月26日 于北京7
- 温馨提示:
1: 本站所有资源如无特殊说明,都需要本地电脑安装OFFICE2007和PDF阅读器。图纸软件为CAD,CAXA,PROE,UG,SolidWorks等.压缩文件请下载最新的WinRAR软件解压。
2: 本站的文档不包含任何第三方提供的附件图纸等,如果需要附件,请联系上传者。文件的所有权益归上传用户所有。
3.本站RAR压缩包中若带图纸,网页内容里面会有图纸预览,若没有图纸预览就没有图纸。
4. 未经权益所有人同意不得将文件中的内容挪作商业或盈利用途。
5. 装配图网仅提供信息存储空间,仅对用户上传内容的表现方式做保护处理,对用户上传分享的文档内容本身不做任何修改或编辑,并不能对任何下载内容负责。
6. 下载文件中如有侵权或不适当内容,请与我们联系,我们立即纠正。
7. 本站不保证下载资源的准确性、安全性和完整性, 同时也不承担用户因使用这些下载资源对自己和他人造成任何形式的伤害或损失。