离合器设计的计算过程
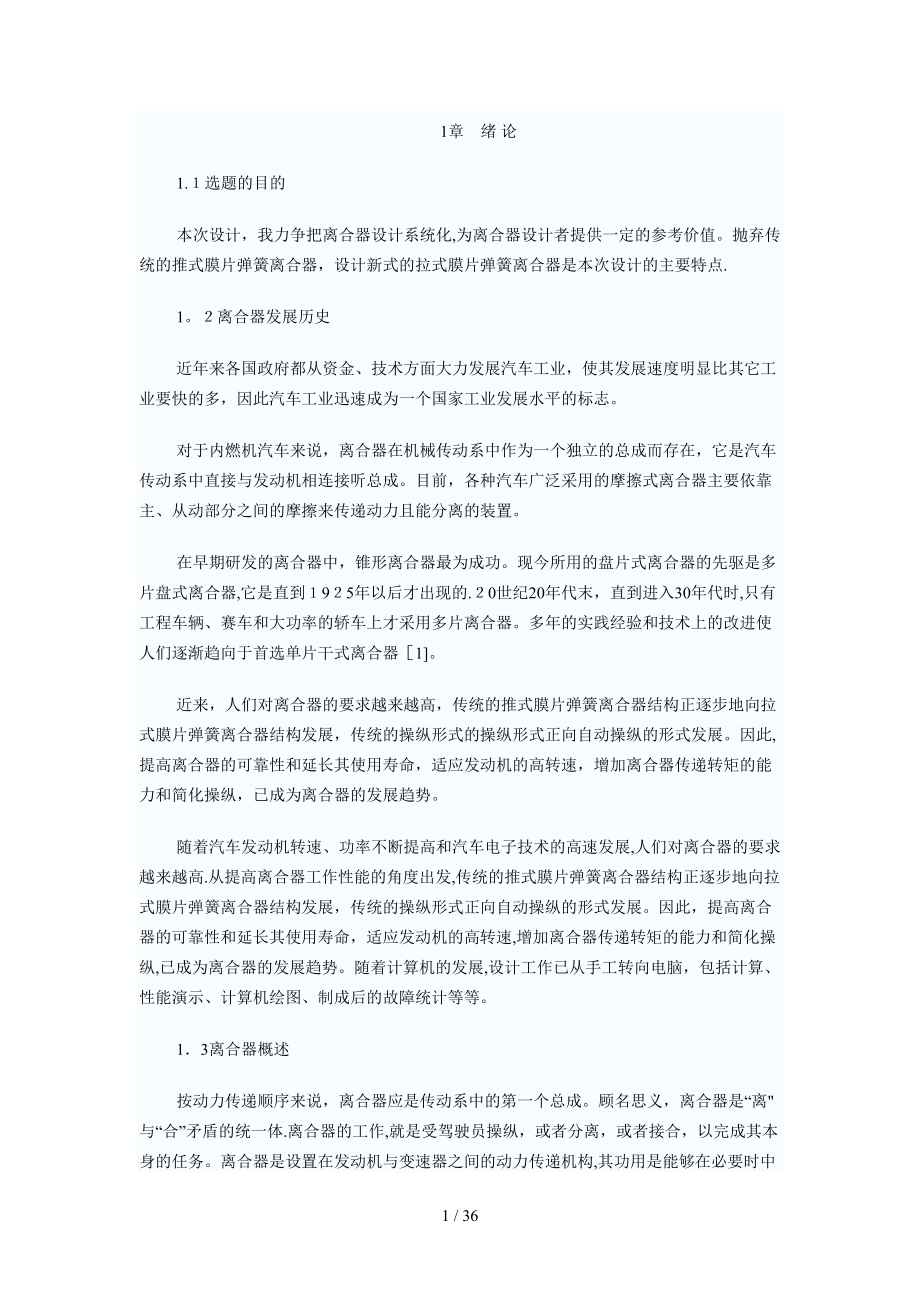


《离合器设计的计算过程》由会员分享,可在线阅读,更多相关《离合器设计的计算过程(36页珍藏版)》请在装配图网上搜索。
1、1章绪论1.选题的目的本次设计,我力争把离合器设计系统化,为离合器设计者提供一定的参考价值。抛弃传统的推式膜片弹簧离合器,设计新式的拉式膜片弹簧离合器是本次设计的主要特点.1。离合器发展历史近年来各国政府都从资金、技术方面大力发展汽车工业,使其发展速度明显比其它工业要快的多,因此汽车工业迅速成为一个国家工业发展水平的标志。对于内燃机汽车来说,离合器在机械传动系中作为一个独立的总成而存在,它是汽车传动系中直接与发动机相连接听总成。目前,各种汽车广泛采用的摩擦式离合器主要依靠主、从动部分之间的摩擦来传递动力且能分离的装置。在早期研发的离合器中,锥形离合器最为成功。现今所用的盘片式离合器的先驱是多片
2、盘式离合器,它是直到95年以后才出现的.0世纪20年代末,直到进入30年代时,只有工程车辆、赛车和大功率的轿车上才采用多片离合器。多年的实践经验和技术上的改进使人们逐渐趋向于首选单片干式离合器1。近来,人们对离合器的要求越来越高,传统的推式膜片弹簧离合器结构正逐步地向拉式膜片弹簧离合器结构发展,传统的操纵形式的操纵形式正向自动操纵的形式发展。因此,提高离合器的可靠性和延长其使用寿命,适应发动机的高转速,增加离合器传递转矩的能力和简化操纵,已成为离合器的发展趋势。随着汽车发动机转速、功率不断提高和汽车电子技术的高速发展,人们对离合器的要求越来越高.从提高离合器工作性能的角度出发,传统的推式膜片弹
3、簧离合器结构正逐步地向拉式膜片弹簧离合器结构发展,传统的操纵形式正向自动操纵的形式发展。因此,提高离合器的可靠性和延长其使用寿命,适应发动机的高转速,增加离合器传递转矩的能力和简化操纵,已成为离合器的发展趋势。随着计算机的发展,设计工作已从手工转向电脑,包括计算、性能演示、计算机绘图、制成后的故障统计等等。13离合器概述按动力传递顺序来说,离合器应是传动系中的第一个总成。顾名思义,离合器是“离与“合”矛盾的统一体.离合器的工作,就是受驾驶员操纵,或者分离,或者接合,以完成其本身的任务。离合器是设置在发动机与变速器之间的动力传递机构,其功用是能够在必要时中断动力的传递,保证汽车平稳地起步;保证传
4、动系换档时工作平稳;限制传动系所能承受的最大扭矩,防止传动系过载。为使离合器起到以上几个作用,目前汽车上广泛采用弹簧压紧的摩擦式离合器,摩擦离合器所能传递的最大扭矩取决于摩擦面间的工作压紧力和摩擦片的尺寸以及摩擦面的表面状况等。即主要取决于离合器基本参数和主要尺寸。膜片弹簧离合器在技术上比较先进,经济性合理,同时其性能良好,使用可靠性高寿命长,结构简单、紧凑,操作轻便,在保证可靠地传递发动机最大扭矩的前提下,有以下优点2: ()结合时平顺、柔和,使汽车起步时不震动、冲击;(2)离合器分离彻底;(3)从动部分惯量小,以减轻换档时齿轮副的冲击;(4)散热性能好;()高速回转时只有可靠强度;(6)避
5、免汽车传动系共振,具有吸收震动、冲击和减小噪声能力;()操纵轻便;(8)工作性能(最大摩擦力矩和后备系数保持稳定);(9)使用寿命长。1。31离合器的功用离合器可使发动机与传动系逐渐接合,保证汽车平稳起步.如前所述,现代车用活塞式发动机不能带负荷启动,它必须先在空负荷下启动,然后再逐渐加载.发动机启动后,得以稳定运转的最低转速约为0050r/min,而汽车则只能由静止开始起步,一个运转着的发动机,要带一个静止的传动系,是不能突然刚性接合的。因为如果是突然的刚性连接,就必然造成不是汽车猛烈攒动,就是发动机熄火。所以离合器可使发动机与传动系逐渐地柔和地接合在一网 起,使发动机加给传动系的扭矩逐渐变
6、大,至足以克服行驶阻力时,汽车便由静止开始缓慢地平稳起步了. 虽然利用变速器的空档,也可以实现发动机与传动系的分离.但变速器在空档位置时,变速器内的主动齿轮和发动机还是连接的,要转动发动机,就必须和变速器内的主动齿轮一起拖转,而变速器内的齿轮浸在黏度较大的齿轮油中,拖转它的阻力是很大的。尤其在寒冷季节,如没有离合器来分离发动机和传动系,发动机起动是很困难的。所以离合器的第二个功用,就是暂时分开发动机和传动系的联系,以便于发动机起动.汽车行驶中变速器要经常变换档位,即变速器内的齿轮副要经常脱开啮合和进入啮合.如在脱档时,由于原来啮合的齿面压力的存在,可能使脱档困难,但如用离合器暂时分离传动系,即
7、能便利脱档.同时在挂档时,依靠驾驶员掌握,使待啮合的齿轮副圆周速度达到同步是较为困难的,待啮合齿轮副圆周速度的差异将会造成挂档冲击甚至挂不上档,此时又需要离合器暂时分开传动系,以便使与离合器主动齿轮联结的质量减小,这样即可以减少挂挡冲击以便利换档.离合器所能传递的最大扭矩是有一定限制的,在汽车紧急制动时,传动系受到很大的惯性负荷,此时由于离合器自动打滑,可避免传动系零件超载损坏,起保护作用。3。现代汽车离合器应满足的要求根据离合器的功用,它应满足下列主要要求:(1)能在任何行驶情况下,可靠地传递发动机的最大扭矩。为此,离合器的摩擦力矩()应大于发动机最大扭矩();(2)接合平顺、柔和。即要求离
8、合器所传递的扭矩能缓和地增加,以免汽车起步冲撞或抖动;(3)分离迅速、彻底.换档时若离合器分离不彻底,则飞轮上的力矩继续有一部份传入变速器,会使换档困难,引起齿轮的冲击响声;()从动盘的转动惯量小.离合器分离时,和变速器主动齿轮相连接的质量就只有离合器的从动盘。减小从动盘的转动惯量,换档时的冲击即降低;(5)具有吸收振动、噪声和冲击的能力;(6)散热良好,以免摩擦零件因温度过高而烧裂或因摩擦系数下降而打滑;(7)操纵轻便,以减少驾驶员的疲劳。尤其是对城市行驶的轿车和公共汽车,非常重要;(8)摩擦式离合器,摩擦衬面要耐高温、耐磨损,衬面磨损在一定范围内,要能通过调整,使离合器正常工作。1。3 离
9、合器工作原理如图1.1所示,摩擦离合器一般是有主动部分、从动部分组成、压紧机构和操纵机构四部分组成。离合器在接合状态时,发动机扭矩自曲轴传出,通过飞轮2和压盘借摩擦作用传给从动盘3,在通过从动轴传给变速器。当驾驶员踩下踏板时,通过拉杆,分离叉、分离套筒和分离轴承8,将分离杠杆的内端推向右方,由于分离杠杆的中间是以离合器盖5上的支柱为支点,而外端与压盘连接,所以能克服压紧弹簧的力量拉动压盘向左,这样,从动盘3两面的压力消失,因而摩擦力消失,发动机的扭矩就不再传入变速器,离合器处于分离状态。当放开踏板,回位弹簧克服各拉杆接头和支承中的摩擦力,使踏板返回原位。此时压紧弹簧就推动压盘向右,仍将从动盘压
10、紧在飞轮上,这样发动机的扭矩又传入变速器。轴承 2飞轮3从动盘 4-压盘 5离合器盖螺栓 6-离合器盖 -膜片弹簧 8分离轴承 9轴图。1 离合器总成1。3.4拉式膜片弹簧离合器的优点与推式相比,拉式膜片弹簧离合器具有许多优点:取消了中间支承各零件,并不用支承环或只用一个支承环,使其结构更简单、紧凑,零件数目更少,质量更少;拉式膜片弹簧是中部与压盘相压在同样压盘尺寸的条件下可采用直径较大的膜片弹簧,提高了压紧力与传递转矩的能力,且并不增大踏板力,在传递相同的转矩时,可采用尺寸较小的结构;在接合或分离状态下,离合器盖的变形量小,刚度大,分离效率更高;拉式的杠杆比大于推式的杠杆比,且中间支承减少了
11、摩擦损失,传动效率较高,踏板操纵更轻便,拉式的踏板力比推式的一般可减少约;无论在接合状态或分离状态,拉式结构的膜片弹簧大端与离合器盖支承始终保持接触,在支承环磨损后不会形成间隙而增大踏板自由行程,不会产生冲击和哭声;使用寿命更长。 1.设计的预期成果本次设计,我将取得如下成果:1、设计说明书:(1)离合器各零件的结构;(2)离合器主要参数的选择与优化;()膜片弹簧的计算与优化;(4)扭转减振器的设计;(5)离合器操纵机构的设计计算.2、图纸有:扭转减振器、摩擦片、膜片弹簧、从动盘、轴、压盘、离合器总成。第2章 离合器的结构设计为了达到计划书所给的数据要求,设计时应根据车型的类别、使用要求、制造
12、条件,以及“系列化、通用化、标准化”的要求等,合理选择离合器结构。. 离合器结构选择与论证21。1摩擦片的选择单片离合器因为结构简单,尺寸紧凑,散热良好,维修调整方便,从动部分转动惯量小,在使用时能保证分离彻底接合平顺,所以被广泛使用于轿车和中、小型货车,因此该设计选择单片离合器。摩擦片数为2.2。1.压紧弹簧布置形式的选择离合器压紧装置可分为周布弹簧式、中央弹簧式、斜置弹簧式、膜片弹簧式等.其中膜片弹簧的主要特点是用一个膜片弹簧代替螺旋弹簧和分离杠杆。膜片弹簧与其他几类相比又有以下几个优点9:(1)由于膜片弹簧有理想的非线性特征,弹簧压力在摩擦片磨损范围内能保证大致不变,从而使离合器在使用中
13、能保持其传递转矩的能力不变.当离合器分离时,弹簧压力不像圆柱弹簧那样升高,而是降低,从而降低踏板力;()膜片弹簧兼起压紧弹簧和分离杠杆的作用,使结构简单紧凑,轴向尺寸小,零件数目少,质量小;()高速旋转时,压紧力降低很少,性能较稳定;而圆柱弹簧压紧力明显下降;()由于膜片弹簧大断面环形与压盘接触,故其压力分布均匀,摩擦片磨损均匀,可提高使用寿命;()易于实现良好的通风散热,使用寿命长;(6)平衡性好;(7)有利于大批量生产,降低制造成本。但膜片弹簧的制造工艺较复杂,对材料质量和尺寸精度要求高,其非线性特性在生产中不易控制,开口处容易产生裂纹,端部容易磨损.近年来,由于材料性能的提高,制造工艺和
14、设计方法的逐步完善,膜片弹簧的制造已日趋成熟.因此,我选用膜片弹簧式离合器。1。3压盘的驱动方式在膜片弹簧离合器中,扭矩从离合器盖传递到压盘的方法有三种9: ()凸台窗孔式:它是将压盘的背面凸起部分嵌入在离合器盖上的窗孔内,通过二者的配合,将扭矩从离合器盖传到压盘上,此方式结构简单,应用较多;缺点:压盘上凸台在传动过程中存在滑动摩擦,因而接触部分容易产生分离不彻底。(2)径向传动驱动式:这种方式使用弹簧刚制的径向片将离合器盖和压盘连接在一起,此传动的方式较上一种在结构上稍显复杂一些,但它没有相对滑动部分,因而不存在磨损,同时踏板力也需要的小一些,操纵方便;另外,工作时压盘和离合器盖径向相对位置
15、不发生变化,因此离合器盖等旋转物件不会失去平衡而产生异常振动和噪声。() 径向传动片驱动方式:它用弹簧钢制的传动片将压盘与离合器盖连接在一起,除传动片的布置方向是沿压盘的弦向布置外,其他的结构特征都与径向传动驱动方式相同.经比较,我选择径向传动驱动方式.2.1.分离杠杆、分离轴承分离杠杆的作用由膜片弹簧承担,其作用是通过分离轴承克服离合器弹簧的推力并推动压盘移动,从而使压盘与从动盘和从动盘与飞轮相互分离,截断动力的传递,分离杠杆要具有足够的强度和刚度,以承受反复作用在其上面的弯曲应力,分离轴承的作用是通过分离叉的作用使分离轴承沿变速器前端盖导向套作轴向移动,推动旋转中的膜片弹簧中部分离前端,使
16、离合器起到分离作用。分离本次设计选用的是油封轴承,它可以将润滑脂密封在轴承壳内,使用中不需要增加润滑,相比供油式轴承则需增加。 21.5离合器的散热通风试验表明,摩擦片的磨损是随压盘温度的升高而增大的,当压盘工作表面超过10200C时摩擦片磨损剧烈增加,正常使用条件的离合器盘,工作表面的瞬时温度一般在10C以下。在特别频繁的使用下,压盘表面的瞬时温度有可能达到000C,过高的温度能使压盘受压变形产生裂纹和碎裂。为使摩擦表面温度不致过高,除要求压盘有足够大的质量以保证足够的热容量外,还要求散热通风好。改善离合器散热通风结构的措施有:在压盘上设散热筋,或鼓风筋;在离合器中间压盘内铸通风槽;将离合器
17、盖和压杆制成特殊的叶轮形状,用以鼓风;在离合器外壳内装导流罩。膜片弹簧式离合器本身构造能良好实现通风散热效果,故不需作另外设置。 2。1。 从动盘总成从动盘总成由摩擦片,从动片,减震器和从动盘穀等组成。它虽然对离合器工作性能影响很大的构件,但是其工作寿命薄弱,因此在结构和材料上的选择是设计的重点。从动盘总成应满足如下设计要求:()转动惯量要小,以减小变速器换档时轮齿简单冲击;()应具有轴向弹性,使离合器接合平顺,便于起步,而且使摩擦面压力均匀,减小磨损。(3)应装扭转减振器,以避免传动系共振,并缓和冲击。1、摩擦片要求摩擦系数稳定、工作温度、单位压力的变化对其影响要小,有足够的机械强度和耐磨性
18、;热稳定性好,磨合性好,密度小;有利于结合平顺,长期停放离合器摩擦片不会粘着现象的.综上所述,选择石棉基材料。石棉基摩擦材料是由石棉或石棉织物、粘结剂(树脂或硅胶)和特种添加剂热压制成,其摩擦系数为.250.3,密度小,价格便宜,多年来在汽车离合器上使用效果良好.同时,摩擦片从动钢片用铆钉连接,连接可靠,更换摩擦片方便,而且适宜在从动钢片上装波形弹簧片以获得轴向弹性.2、从动盘的轴向弹性从动盘的轴向弹性可改善离合器性能,使离合器接合柔和,摩擦面接触均匀,磨损较小。为使从动盘有轴向弹性,单独制造扇形波状弹簧与从动钢片铆接。波状弹簧可用比钢片轻薄的材料制造,轴向弹性较好,转动惯量小,适宜高速旋转,
19、且弹簧对置分布,弹性好.因此设计中选用此类弹簧。、扭转减震器扭转减震器几乎是现代汽车离合器从动盘上必备的部件,主要由弹性元件和阻尼元件组成。弹性元件可降低传动系的首端扭转刚度,从而降低传动系扭转系统的某阶固有频率,改变系统的固有振型,使之尽可能避免由发动机转矩主谐量激励引起的共振。但是,这种共振往往难以避免.汽车行驶在不平的道路上行驶阻力也会时刻变化.当由于路面不平引起的激力频率与传动系的某阶自振频率重合时,也会发生共振现象。阻尼元件则可有效的耗散此时的振动能量,因而扭转减震器可有效地降低传动系共振载荷与噪声。扭转减震器的弹性特性,又线性和非线性两种。弹性元件采用圆柱螺旋弹簧的减震器,其弹性特
20、点为线性。阻尼元件采用摩擦片通过碟形弹簧建立阻尼默片的正应力,其阻尼力矩比较稳定。因此发动机的扭矩实际上是通过一些弹性元件传递到传动系的。 摩擦式扭转减震器工作原理:离合器工作时,扭矩从摩擦片传给从动钢片再传给从动盘毂,此时弹簧被压缩,从动钢片相对从动盘毂前移(从动毂边缘上的缺口控制着钢片与毂的最大位移).2。2离合器结构设计的要点在进行离合器的具体设计时,首先应保证传递发动机最大扭矩为前提,然后满足下列条件:()如前所述,扇形波状弹簧对置分布铆接在从动钢片上,并在从动盘上设置扭转减震器保证离合器接合柔和,摩擦片制成一定锥度(从动盘锥形量约为05m)使其大端面向飞轮,这样从动盘毂在从动轴(即变
21、速器第一轴)花键上易于滑动,有利于离合器彻底分离。()离合器主动部分与从动部分的连接和支撑形式,离合器的主动部分包括飞轮,离合器盖与他们一起转动并能轴向移动的压盘,压盘通过钢片与离合器盖相连,离合器从动部分有从动盘,从动轴,从动轴装在飞轮与压盘之间,可在从动轴花键上滑动,设计时把离合器从动轴的前轴承安装在发动机曲轴的中心孔内。(3)离合器从动轴的轴向定位及轴承润滑,离合器从动轴在安装后应保持轴向定位,在拆卸时便于离合器中抽出来。因此,设计时使从动轴前轴承外圆与飞轮为过渡配合,而前轴承内圈与从动轴为间隙配合,离合器的从动轴轴向定位是靠从动轴后轴承来保证的。离合器分离轴承靠注入黄油润滑的,而从动轴
22、前轴承靠油杯定期注入润滑。 为防止润滑油流到摩擦衬面,造成离合器打滑,除在轴承处安有自紧油封外,还在飞轮上开泄油孔。(4)离合器运动零件的限位,离合器处于接合时为使压盘与摩擦片很好接合,应使分离弹簧与分离轴承之间保持一定间隙,这是分离轴承回位弹簧加以保证.分离时,应对踏板的最大行程加以限制。.3离合器主要零件的设计2。3。 从动盘扇形波状弹簧两两对置铆接与从动钢片上,两侧在铆接摩擦片,铆钉都采用铝制埋头铆钉,摩擦衬面在铆接后腰磨削加工,使其工作表面的不平度误差小于0.2,从动盘本体采用4号钢冲压加工得到,为防止其弯曲变形而引起分离不彻底,一般在从动盘本体上设径向切口。2.3。2 摩擦片摩擦片在
23、性能上要满足如下要求:(1)摩擦系数稳定,工作温度,滑磨速度,单位压力的变化对其影响;()具有足够的机械强度和耐磨性,热稳定性好;(3)有利于接合平顺;.长期停放离合器摩擦面会发生粘着现象.(4)摩擦片选用材料为石棉基摩擦材料,它是由石棉或石棉织物、粘结剂和特种添加剂热压而成,其摩擦系数为.2-0.3.石棉基摩擦材料密度小,工作温度小于18,价格便宜,使用效果良好,在汽车离合器中广泛使用。2.。3膜片弹簧膜片弹簧使用优质高精质钢。其碟簧部分的尺寸精度要求高,碟簧材料为6iMnA。为了提高膜片弹簧的承载能力,要对膜片弹簧进行调质处理,得具有高抗疲劳能力的回火索氏体.要防止膜片内缘离开,同时对膜片
24、弹簧进行强压处理(将弹簧压平并保持12-14小时),使其高压力区产生塑性变形以产生残余反向应力,对膜片弹簧的凹表面进行喷丸处理,喷丸是0.8的白口铁小丸, 可提高弹簧的疲劳寿命。同时,为提高分离指的耐磨性,对其进行局部高频淬火式镀铬。采用乳白镀铬,若膜片弹簧许用应力可取为15010N/mm2。压盘压盘的材料选用T20-4铸造制成。它要有一定的质量和刚度,以保证足够的热容量和防止温度升高而产生的弯曲变形。压盘应与飞轮保持良好的对中,并进行静平衡。压盘的摩擦工作面需平整光滑,其端面粗糙不低于0。压盘壳用M1m螺栓将其一端固定在飞轮端面上,另一端固定在压盘端面上。2.3。5离合器盖离合器盖的膜片弹簧
25、支撑处须具有较大的刚度和较高的尺寸精度,压盘高度(丛承压点到摩擦面的距离)公差要小,支撑环和支撑铆钉的安装尺寸精度要高,耐磨性好,膜片弹簧的支撑形式采用铆钉作支承时,如果分离轴承与曲轴中心线不同心,可引起铆钉的过度磨损。提高铆钉硬度的套筒和支承与曲轴中心线不同心,亦可引起铆钉的过度。提高铆钉硬度的套筒和支承圈是提高耐磨性的结构措施,采用10钢材材料、H4050。 24 本章小结本章系统介绍了膜片弹簧离合器的结构,并讲述了离合器各零件的结构和材料,以及各部分的连接关系,为下章离合器的计算打下基础。第3章 离合器的设计计算及说明3.1 离合器设计所需数据表3。 离合器原始数据汽车的驱动形式2汽车的
26、质量180kg发动机位置前置发动机最大功率4.3W发动机最大转速30r/min发动机最大扭矩15Nm离合器形式机械、干式、单片、膜片弹簧(压式)操纵形式液压人力操纵踏板行程050m0=6.9 g=5。913 ig2=2.5i31。 ig4=1.00汽车最大时速0kmh3.2 摩擦片主要参数的选择采用单片摩擦离合器是利用摩擦来传递发动机扭矩的,为保证可靠度,离合器静摩擦力矩应大于发动机最大扭矩摩擦片的静压力:(3.1) 式中: 离合器后备系数() (1)后备系数是离合器的重要参数,反映离合器传递发动机最大扭矩的可靠程度,选择时,应从以下几个方面考虑:a. 摩擦片在使用中有一定磨损后,离合器还能确
27、保传递发动机最大扭矩; 防止离合器本身滑磨程度过大;c. 要求能够防止传动系过载。通常轿车和轻型货车=1.5。结合设计实际情况,故选择=。5.则有可有表.查得1。5。表. 离合器后备系数的取值范围车型后备系数乘用车及最大总质量小于t的商用车201。5最大总质量为614t的商用车1.502。5挂车。804.摩擦片的外径可有式: (.3) 求得为直径系数,取值见表3.3 取 得=2141。表. 直径系数的取值范围车型直径系数乘用车14。6最大总质量为1.8。0t的商用车60185(单片离合器)。15.(双片离合器)最大总质量大于。0的商用车2。240摩擦片的尺寸已系列化和标准化,标准如下表(部分)
28、:表离合器摩擦片尺寸系列和参数外径m6018002252580305内径dmm115050556517519厚度/mm3。23.5。53。5335。53.506870。690。7000660。620.589583。585 0。675670。57。7030。76209608020.800单面面积m1613160102402466546选取D=00mm d75m 厚度为3。5mm 摩擦片的摩擦因数f取决于摩擦片所用的材料及基工作温度、单位压力和滑磨速度等因素。可由表35查得:f=0。25摩擦面数为离合器从动盘数的两倍,决定于离合器所需传递转矩的大小及其结构尺寸。本题目设计单片离合器,因此=2。离合
29、器间隙t是指离合器处于正常接合状态、分离套筒被回位弹簧拉到后极限位置时,为保证摩擦片正常磨损过程中离合器仍能完全接合,在分离轴承和分离杠杆内端之间留有的间隙.该间隙t一般为4mm。取=m.表3。5摩擦材料的摩擦因数的取值范围摩擦材料摩擦因数f石棉基材料模压0.10。25编织0。25。3粉末冶金材料铜基0.250.35铁基0。350。50金属陶瓷材料1。01.50离合器的静摩擦力矩为: (34)与式(1)联立得:() 代入数据得:单位压力4MPa。表3。6 摩擦片单位压力的取值范围摩擦片材料单位压力/Pa石棉基材料模压0。150.编织.25035粉末冶金材料模压0。350.50编织金属陶瓷材料0
30、.70。50查表得摩擦片采用石棉基材料模压可以满足要求。3。 摩擦片基本参数的优化(1)摩擦片外径D(mm)的选取应使最大圆周速度不超过6570/s,即9.6m/sm (3。)式中,。为摩擦片最大圆周速度(m);。为发动机最高转速(/min)。()摩擦片的内、外径比应在.5070范围内,即(3)为了保证离合器可靠地传递发动机的转矩,并防止传动系过载,不同车型的值应在一定范围内,最大范围为24。0。而=1.5满足要求。(4)为了保证扭转减振器的安装,摩擦片内径d必须大于减振器振器弹簧位置直径约5mm,即故取=06d/2=5.875=15+50=163.75mm ()为反映离合器传递的转矩并保护过
31、载的能力,单位摩擦面积传递的转矩应小于其许用值,即 (。7)式中,为单位摩擦面积传递的转矩(N。m/mm2),可按表。6选取。35经检查,合格。表37 单位摩擦面积传递转矩的许用值离合器规格0203035。40(6)为降低离合器滑磨时的热负荷,防止摩擦片损伤,对于不同车型,单位压力的最大范围为0。0。50MPa,即()为了减少汽车起步过程中离合器的滑磨,防止摩擦片表面温度过高而发生烧伤,离合器每一次接合的单位摩擦面积滑磨功应小于其许用值,即。 (38)式中,。为单位摩擦面积滑磨(Jmm2);为其许用值(/mm),对于乘用车:=0。40J/2,对于最大总质量小于0的商用车:033mm2,对于最大
32、总质量大于60t商用车:025J/mm:W为汽车起步时离合器接合一次所产生的总滑磨功(J),可根据下式计算 (39)式中,为汽车总质量(K); 为轮胎滚动半径(m);为汽车起步时所用变速器挡位的传动比;为主减速器传动比;为发动机转速/in,计算时乘用车取0r/mi,商用车取500r/mi。其中: m 代入式(3)得W=443,代入式(。8)得,合格.(8)离合器接合的温升式中,t为压盘温升,不超过80C;c为压盘的比热容,c481.4J/(g);为传到压盘的热量所占的比例,对单片离合器压盘;=0.5,为压盘的质量。15Kg代入,t5.42C,合格。4膜片弹簧主要参数的选择1.比较H/h的选择此
33、值对膜片弹簧的弹性特性影响极大,分析式(3.10)中载荷与变形1之间的函数关系可知,当Hh时,F有一极大值和极小值;当H/h时,极小值在横坐标上,见图3.1。1-2 -4 5图31 膜片弹簧的弹性特性曲线为保证离合器压紧力变化不大和操纵方便,汽车离合器用膜片弹簧的H/通常在1.2范围内选取.常用的膜片弹簧板厚为24m,本设计Hh ,h=3mm ,则5m 。 R/r选择通过分析表明,R/r越小,应力越高,弹簧越硬,弹性曲线受直径误差影响越大。汽车离合器膜片弹簧根据结构布置和压紧力的要求,r常在。21. 的范围内取值。本设计中取R/=1.2,摩擦片的平均半径=12。5mm, 取R=10m则r=1m
34、m。 。圆锥底角汽车膜片弹簧在自由状态时,圆锥底角一般在91范围内,本设计中 得在15之间,合格。分离指数常取为8,大尺寸膜片弹簧有取24的,对于小尺寸膜片弹簧,也有取12的,本设计所取分离指数为18。4切槽宽度mm,m,取mm,应满足的要求.11210=102mm。所以取105. 压盘加载点半径和支承环加载点半径的确定应略大于且尽量接近,应略小于R且尽量接近R。本设计取38m,1mm.膜片弹簧应用优质高精度钢板制成,其碟簧部分的尺寸精度要高。国内常用的碟簧材料的为6izMnA,当量应力可取为1001700N/m2。6 公差与精度离合器盖的膜片弹簧支承处,要具有大的刚度和高的尺寸精度,压力盘高
35、度(从承压点到摩擦面的距离)公差要小,支承环和支承铆钉安装尺寸精度要高,耐磨性要好.3。5 膜片弹簧的优化设计()为了满足离合器使用性能的要求,弹簧的H/h与初始锥角应在一定范围内,即(2)弹簧各部分有关尺寸的比值应符合一定的范围,即()为了使摩擦片上的压紧力分布比较均匀,推式膜片弹簧的压盘加载点半径(或拉式膜片弹簧的压盘加载点半径)应位于摩擦片的平均半径与外半径之间,即推式: 拉式:(4)根据弹簧结构布置要求,与R,与之差应在一定范围内选取,即(5)膜片弹簧的分离指起分离杠杆的作用,因此杠杆比应在一定范围内选取,即推式: 拉式: 由(4)和(5)得m,mm.膜片弹簧的载荷与变形关系碟形弹簧的
36、形状如以锥型垫片,见图.2,它具有独特的弹性特征,广泛应用于机械制造业中.膜片弹簧是具有特殊结构的碟形弹簧,在碟簧的小端伸出许多由径向槽隔开的挂状部分-分离指.膜片弹簧的弹性特性与尺寸如其碟簧部分的碟形弹簧完全相同(当加载点相同时).因此,碟形弹簧有关设计公式对膜片弹簧也适用。通过支承环和压盘加在膜片弹簧上的沿圆周分布的载荷,假象集中在支承点处,用1表示,加载点间的相对变形(轴向)为1,则压紧力F与变形1之间的关系式为: (3。1)式中: E-弹性模量,对于钢,泊松比,对于钢,=03-膜片弹簧在自由状态时,其碟簧部分的内锥高度-弹簧钢板厚度-弹簧自由状态时碟簧部分的大端半径r弹簧自由状态时碟簧
37、部分的小端半径R1压盘加载点半径r1支承环加载点半径图3。2膜片弹簧的尺寸简图表3.8 膜片弹簧弹性特性所用到的系数RrR1r1Hh40123853代入(310)得(3。11)对(3。11)式求一次导数,可解出11的凹凸点,求二次导数可得拐点.凹点:m时,N凸点:m时,N拐点:m时,N、当离合器分离时,膜片弹簧加载点发生变化。设分离轴承对膜片弹簧指所加的载荷为F2,对应此载荷作用点的变形为。由 0。 (3.) (3。13)列出表3:表3. 膜片弹簧工作点的数据。4456.07.921246170069160150472509260181膜片弹簧工作点位置的选择.从膜片弹簧的弹性特性曲线图分析出
38、,该曲线的拐点H对应着膜片弹簧压平位置,而。新离合器在接合状态时,膜片弹簧工作点B一般取在凸点和拐点之间,且靠近或在点处,一般,以保证摩擦片在最大磨损限度范围内压紧力从F到1A变化不大。当分离时,膜片弹簧工作点从B变到C ,为最大限度地减小踏板力,C点应尽量靠近N点。为了保证摩擦片磨损后仍能可靠的传递传矩,并考虑摩擦因数的下降,摩擦片磨损后弹簧工作压紧力应大于或等于新摩擦片时的压紧力,见图3。3。.膜片弹簧的应力计算假定膜片弹簧在承载过程中其子午断面刚性地绕此断面上的某中性点转动(图3.4)。断面在O点沿圆周方向的切向应变为零,故该点的切向应力为零,O点以外的点均存在切向应变和切向应力.现选定
39、坐标于子午断面,使坐标原点位于中性点O。令X轴平行于子午断面的上下边,其方向如上图所示,则断面上任意点的切向应力为: (。14)图3.3膜片弹簧工作点位置式中 -碟簧部分子午断面的转角(从自由状态算起)碟簧部分子有状态时的圆锥底角e 碟簧部分子午断面内中性点的半径e=(Rr)/In(R/r)(3。15)为了分析断面中断向应力的分布规律,将(3.4)式写成Y与X轴的关系式:马棚网y=(3。16) 图3。 切向应力在子午断面的分布由上式可知,当膜片弹簧变形位置一定时,一定的切向应力t在XY坐标系里呈线性分布。因为的值很小,我们可以将看成,由上式可写成Y=X。此式表明,对于一定的零应力分布在中性点O
40、而与轴承角的直线上。从式(3.16)可以看出当X=时无论取任何值,都有Y=-e。显然,零应力直线为点与O点的连线,在零应力直线内侧为压应力区,外侧位拉应力区,等应力直线离应力直线越远,其应力越高。由此可知,碟簧部分内缘点B处切向压应力最大,A处切向拉应力最大,分析表明,B点的切向应力最大,计算膜片弹簧的应力只需校核B处应力就可以了,将B点的坐标X=(er)和h/2 代入(3.1)式有: (3.17)令可以求出切向压应力达极大值的转角由于: =12。8mm所以: 0.415,102.5N/m2B点作为分离指根部的一点,在分离轴承推力F2作用下还受有弯曲应力: (3.18)式中 n分离指数目 n=
41、18br-单个分离指的根部宽=16。5因此:338.42Nmm2由于rB是与切向压应力B垂直的拉应力,所以根据最大剪应力强度理论,点的当量应力为:421082。5=744.3N/m2500170N/mm2膜片弹簧的设计应力一般都稍高于材料的局限,为提高膜片弹簧的承载能力,一般要经过以下工艺:先对其进行调质处理,得到具有较高抗疲劳能力的回火索氏体,对膜片弹簧进行强压处理(将弹簧压平并保持1214h),使其高应力区产生塑性变形以产生残余反向应力,对膜片弹簧的凹表面进行喷丸处理,提高弹簧疲劳寿命,对分离指进行局部高频淬火或镀铝,以提高其耐磨性.故膜片弹簧和当量应力不超出允许应力范围,所以用设数据合适
42、。.8 扭转减振器设计减震器极转矩 取=43Nm 摩擦转矩 1.5Nm预紧转矩 取=20Nm极限转角 取为4 扭转角刚度=559Nmrad 详细见图。5。9 减振弹簧的设计1减振弹簧的安装位置=(0。0。7)d2,结合d+50mm,得取62mm,则0。71.满足要求。2全部减振弹簧总的工作负荷6.9N3单个减振弹簧的工作负荷P115N式中Z为减振弹簧的个数,按表3.选择:取Z=6表31 减振弹簧个数的选取摩擦片的外径D/mm2252502502532535050Z6681010马棚网图3 扭转减振器4减振弹簧尺寸(1)选择材料,计算许用应力根据机械原理与设计(机械工业出版社)采用65Mn弹簧钢
43、丝, 设弹簧丝直径d4m,=120Ma,810MP。(2)选择旋绕比,计算曲度系数根据下表选择旋绕比表3。11 旋绕比的荐用范围/m确定旋绕比6,曲度系数K(4-)/(4C4)0。61/C=.5(3)弹簧丝直径、外径、中径的计算7mm,与原来的d接近,合格。中径mm;外径=mm()弹簧的工作应力计算=179p弹簧刚度 一般K=245N/mm这里取35/mm(5)弹簧工作圈数的计算弹簧的切变模量对于碳钢G=8000-900MPa,取8000Mpa则弹簧的工作圈数=5.3总圈数为=i+(1.52。5)取n=7()弹簧工作负荷下的变形/m3mm(7)弹簧附加变形量单片离合器 mm取2mm()弹簧的自
44、由高度663m(9)弹簧最大负荷时的间隙m取1mm(0)弹簧的工作高度33。mm(11)弹簧的最大负荷125 为离合器彻底分离时的弹簧的最大负荷,一般规定 经验算符合要求.3。10 操纵机构汽车离合器操纵机构是驾驶员用来控制离合器分离又使之柔和接合的一套机构。它始于离合器踏板,终止于离合器壳内的分离轴承.由于离合器使用频繁,因此离合器操纵机构首先要求操作轻便。轻便性包括两个方面,一是加在离合器踏板上的力不应过大,另一方面是应有踏板形成的校正机构。离合器操纵机构按分离时所需的能源不同可分为机械式、液压式、弹簧助力式、气压助力机械式、气压助力液压式等等.离合器操纵机构应满足的要求是3:(1)踏板力
45、要小,轿车一般在50N范围内,货车不大于15000N;(2)踏板行程对轿车一般在m范围内,对货车最大不超过18mm;()踏板行程应能调整,以保证摩擦片磨损后分离轴承的自由行程可复原;()应有对踏板行程进行限位的装置,以防止操纵机构因受力过大而损坏;(5)应具有足够的刚度;(6)传动效率要高;()发动机振动及车架和驾驶室的变形不会影响其正常工作。机械式操纵机构有杠系传动和绳索系两种传动形式,杠传动结构简单,工作可靠,但是机械效率低,质量大,车架和驾驶室的形变可影响其正常工作,远距离操纵杆系,布置困难,而绳索传动可消除上述缺点,但寿命短,机构效率不高。本次设计的普通轮型离合器操纵机构,采用液压式操
46、纵机构。液压操纵机构有如下优点:(1)液压式操纵,机构传动效率高,质量小,布置方便;便于采用吊挂踏板,从而容易密封,不会因驾驶室和车架的变形及发动机的振动而产生运动干涉;(2)可使离合器接合柔和,可以降低因猛踩踏板而在传动系产生的动载荷,正由于液压式操纵有以上的优点,故应用日益广泛,离合器液压操纵机构由主缸、工作缸、管路系统等部分组成。mm,m,mm,mm,mm,mm。10.1 离合器踏板行程计算踏板行程由自由行程和工作行程组成:(3。9)式中,为分离轴承的自由行程,一般为mm,取mm;反映到踏板上的自由行程一般为mm;、分别为主缸和工作缸的直径;Z为摩擦片面数;为离合器分离时对偶摩擦面间的间
47、隙,单片:m,取;、为杠杆尺寸。得:mm,m,合格。图3. 液压操纵机构示意图3.10。踏板力的计算踏板力为 (3。20)式中,为离合器分离时,压紧弹簧对压盘的总压力;为操纵机构总传动比,;为机械效率,液压式:,机械式:;为克服回位弹簧1、的拉力所需的踏板力,在初步设计时,可忽略之.N,,%;则N合格。分离离合器所作的功为式中,为离合器拉接合状态下压紧弹簧的总压紧力,,则合格.3。11从动轴的计算1选材40r调质钢可用于载荷较2.确定轴的直径式中,A为由材料与受载情况决定的系数,见表。11:表3。12轴常用几种材料的及A值轴的材料Q25A,20Q275,35(C18Nii)454C,Sin38
48、iMnMo,3Cr125235254536A149126131122610311297取,n 为轴的转速,n=380r/in,则m,取mm。12 从动盘毂从动盘毂是离合器中承受载荷最大的零件,它几乎承受由发动机传来的全部转矩。它一般采用齿侧对中的矩形花键安装在变速器的第一轴上,花键的尺寸可根据摩擦片的外径与发动机的最大转矩由表.12选取:一般取1.014倍的花键轴直径。从动盘毂一般采用碳钢,并经调质处理,表面和心部硬度一般2632HRC。为提高花键内孔表面硬度和耐磨性,可采用镀铬工艺;对减振弹簧窗口及与从动片配合处,应进行高频处理。取花键齿数=1,40mm,2mm,t5 mm,l0 mm,1.
49、5 Ma.验证:挤压应力的计算公式为:式中,为花键的齿侧面压力,它由下式确定:从动盘毂轴向长度不宜过小,以免在花键轴上滑动时产生偏斜而使分离不彻底, ,分别为花键的内外径;Z为从动盘毂的数目;取Z=1h为花键齿工作高度;得P194,。46MPa105Pa,合格.表3.13花健的的选取摩擦片的外径/m/N花健尺寸挤压应力/Pa齿数n外径/m内径m齿厚mm有效齿长mm160491312098106102621320162000232511.1225170301132519610358351.2280271035244012.00304100325010.3340325411。43501040325
50、013。0。13分离轴承的寿命计算分离轴承的参数表.14 分离轴承参数表型号rn014C4。2KN13380r/min则由下式:得:h3。14 本章小结本章讲述了离合器的计算,包括摩擦片主要参数的选择与优化、膜片弹簧主要参数的选择与优化、通过膜片弹簧载荷与变形的关系计算离合器的压紧力与膜片弹簧的应力、扭转减振器与减振弹簧的计算、操纵机构与输出轴的计算、选取从动盘毂,最后计算分离轴承的寿命。本章所用原始数据为CA1040货车的数据。结论通过以上对膜片弹簧离合器及液压操纵机构的工作原理的阐述及各构件的计算说明,可以看出离合器操纵机构的设计要从选材,尺寸约束,传递发动机扭矩,驾驶员操作等各方面的综合
51、考虑。计算方面:离合器的主要参数,P0,D,d,结果按照基本公式运算得出并通过约束条件,检验合格。操纵机构自由行程符合规格,总行程131mm10m符合标准条件,在此前提下同时也保证了机件具有足够的刚度,在有外部压力的情况下不会轻易变形。设计所得尺寸既符合工作机理的需求又满足安装的要求。选材方面:摩擦片选用石棉基材料,保证其有足够的强度和耐磨性、热稳定性、磨合性,不会发生粘着现象.扭转减振器中的扭转弹簧选用Si2MnA,其中所含硅成分提高了机件的弹性,所含錳,加强了耐高温性;设计后的离合器顺利通过温升校核,目的是防止摩擦元件过快地磨损和温度过高。综上所述,本次设计遵从了:(1)分离彻底;(2)接
52、合柔和;(3)操纵轻便,工作特征稳定;(4)从动部分转动惯量小的设计要点,数据全部通过约网 束条件检验,原件所使用的材料基本上符合耐磨,耐压和耐高温的要求,而且离合器尺寸合适,适宜安装,能最高效率传递发动机扭矩,完全符合计划书及国家标准。但是,我的设计中仍存在大量的错误和缺点,如加工精度问题等等。 对于我在设计中出现的错误,希望广大读者和专家批评指正。参考文献1徐石安,江发潮。汽车离合器。清华大学出版社0 陈家瑞.汽车构造M。 机械工业出版社00. 3 王望予.汽车设计 机械工业出版社。2006. 中国机械工程学会,中国机械设计大典编委会.中国机械设计大典M.江西科学技术出版社.202. 余仁
53、义,梁涛.汽车离合器操纵机构的设计J。专用汽车.200 董丽霞,张平简明汽车技术词典M。人民交通出版社。2003。 7张金柱,韩玉敏,石美玉汽车工程专业英语M化学工业出版社。20。8 廖清林.汽车离合器膜片弹簧的稳健优化设计J。重庆工学院学报202。 9王志明,胡树根,王兆军。汽车离合器盖成形工艺和模具设计。实用技术.205(12)。罗颂荣,胡浩,刘文清.汽车拉式膜片弹簧片的优化设计J常德师范学院学报.201(3)11 王洋,高翔,陈祥,朱茂桃膜片弹簧设计的概率优化研究J.江苏理工大学学报。01(1).2 王三民,诸文俊.机械原理与设计M。机械工业出版社。2 1张铁山,高翔,夏长高,朱茂桃汽车
54、离合器传动片设计研究J江苏理工学报.01(11) 14 严正峰,盛学斌5膜片弹簧离合器校核设计J. 设计.计算研究。2004(5)。 王宝玺汽车拖拉机制造工艺学 M.机械工业出版社.20516 A。 C. Ra.Trns.O the Pemace Knmai Chins。 CSME J 1N 2,1998。17 夏华,胡亚民,黎勇等.汽车离合器盖成形工艺和模具设计J。 锻压技术.05,2.8D。 GChetwyndand P。 H Phiusox,An ivetiton of refenecriria uedunes mesreent,.hyE:Sciinstrum。J1980,13():50
55、 - 538 致谢毕业设计的顺利完成除了自己付出的汗水外,还有指导老师的辛勤教诲。在这里我要特别感谢赵强老师,谢谢他们在百忙之中对我的指正和教导,也因此使我在设计后的学习与人生的道路上向着更高更深层次地方向前进!赵强老师知识渊博、平易近人经常利用休息时间为我指导。我在画图方面基础很差,赵老师仔细审阅我的AD图纸,指出一系列的问题,使我的图纸得到完善,再次向赵老师表示衷心的感谢。齐晓杰老师和苏清源老师为我指出许多关于CD错误。在此,向齐老师和苏老师表示感谢。方彬、李绍辉、许雨涛等同学以及同组的刘飞同学也给我许多帮助,在这里,一并感谢。实验室免费开放,为我的毕业设计提供实物和模型.在此,向实验室老师表示感谢。文中如有不足,请您指教!36 / 36
- 温馨提示:
1: 本站所有资源如无特殊说明,都需要本地电脑安装OFFICE2007和PDF阅读器。图纸软件为CAD,CAXA,PROE,UG,SolidWorks等.压缩文件请下载最新的WinRAR软件解压。
2: 本站的文档不包含任何第三方提供的附件图纸等,如果需要附件,请联系上传者。文件的所有权益归上传用户所有。
3.本站RAR压缩包中若带图纸,网页内容里面会有图纸预览,若没有图纸预览就没有图纸。
4. 未经权益所有人同意不得将文件中的内容挪作商业或盈利用途。
5. 装配图网仅提供信息存储空间,仅对用户上传内容的表现方式做保护处理,对用户上传分享的文档内容本身不做任何修改或编辑,并不能对任何下载内容负责。
6. 下载文件中如有侵权或不适当内容,请与我们联系,我们立即纠正。
7. 本站不保证下载资源的准确性、安全性和完整性, 同时也不承担用户因使用这些下载资源对自己和他人造成任何形式的伤害或损失。