【行业标准】UL 6140 Outline of Investigation for Wind Turbine Generating Systems
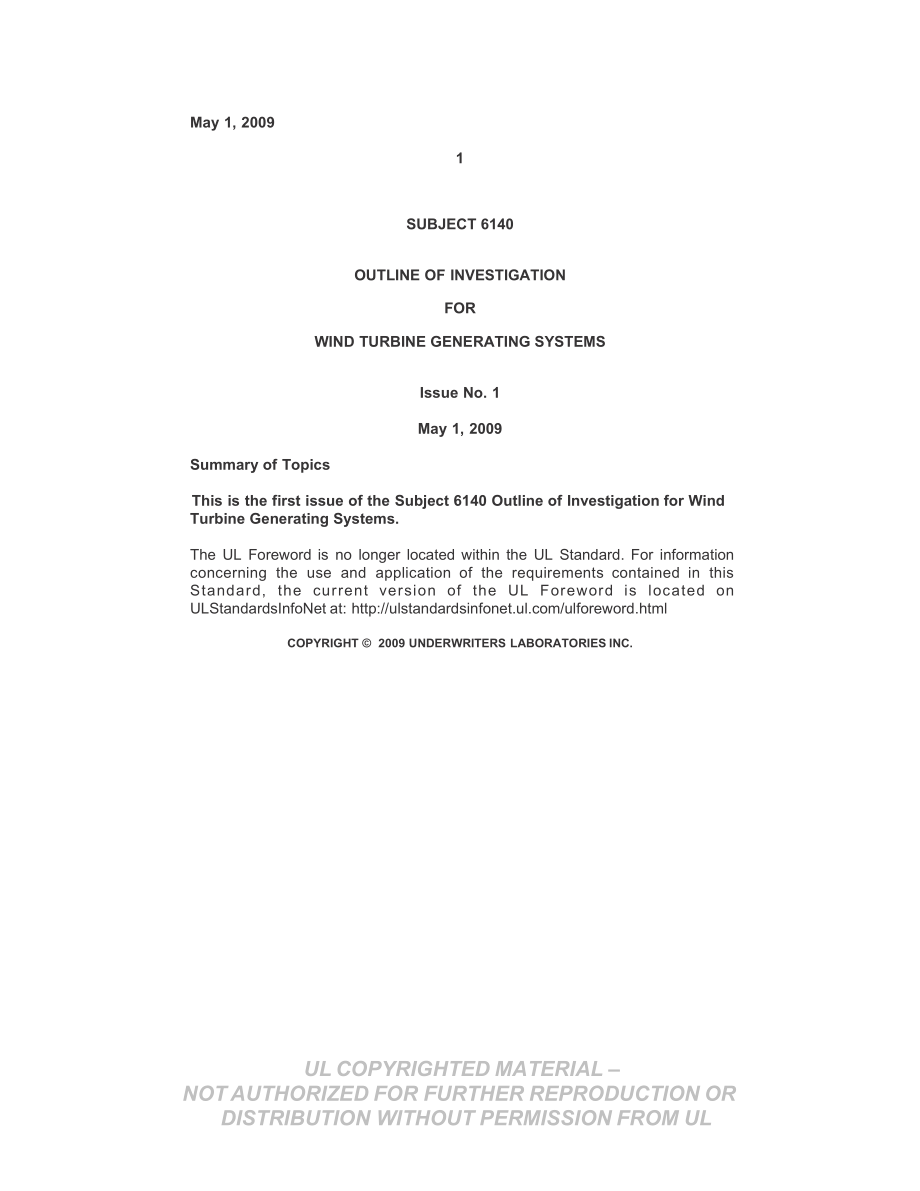


《【行业标准】UL 6140 Outline of Investigation for Wind Turbine Generating Systems》由会员分享,可在线阅读,更多相关《【行业标准】UL 6140 Outline of Investigation for Wind Turbine Generating Systems(21页珍藏版)》请在装配图网上搜索。
1、May 1, 20091SUBJECT 6140OUTLINE OF INVESTIGATION FORWIND TURBINE GENERATING SYSTEMSIssue No. 1May 1, 2009Summary of TopicsThis is the first issue of the Subject 6140 Outline of Investigation for WindTurbine Generating Systems.The UL Foreword is no longer located within the UL Standard. For informati
2、on concerning the use and application of the requirements contained in this Standard, the current version of the UL Foreword is located on ULStandardsInfoNet at: COPYRIGHT 2009 UNDERWRITERS LABORATORIES INC.UL COPYRIGHTED MATERIAL NOT AUTHORIZED FOR FURTHER REPRODUCTION OR DISTRIBUTION WITHOUT PERMI
3、SSION FROM UL2SUBJECT 6140MAY 1, 2009No Text on This PageMAY 1, 2009SUBJECT 61403CONTENTSINTRODUCTION1 Scope . .42 General . .42.1 Components . .42.2 Units of Measurement . .52.3 Undated References . .53 Special Components and Subassemblies of WTGS . .53.1 Wiring . .53.2 Cable drip loop . .63.3 Bus
4、bars . .63.4 Switchgear . .83.5 Transformers . .83.6 Hub . .93.7 Converter/Inverter . .93.8 Lightning protection systems . .93.9 Slip rings . .93.10 Gearboxes . .103.11 Hoists and winches . .103.12 Fire alarms . .113.13 Emergency stop . .11CONSTRUCTIONWTGS AND SUBASSEMBLY4 General . .125 Disconnecti
5、on Device . .126 Spacings . .137 Energy Storage Units . .147.1 General. .147.2 Battery mounting . .148 Working Space . .159 Safety Related Controls System (SRCS) . .169.1 General . .169.2 Protection functions . .169.3 Abnormal conditions for safety related controls system . .17APPENDIX AStandards fo
6、r Components. A14SUBJECT 6140MAY 1, 2009INTRODUCTION1 Scope1.1 This Outline of Investigation covers Wind Turbine Generating Systems (WTGS) and electrical subassemblies. These units are intended for use in stand-alone (not grid-connected) or utility interactive applications. Utility-interactive WTGS
7、are operated in parallel with an electric power system (EPS) to supply power to common loads.1.2 The WTGS power, control and protection systems are evaluated only to the extent that they function within the manufacturers specified limits and response times. These control and protection functions are
8、 evaluated with respect to risk of electric shock and fire. It is intended that the electrical subassemblies that address power transfer control and protection functions evaluated per this document are to be coordinated with the mechanical and structural evaluation of the WTGS in accordance with the
9、 IEC 61400 series documents or Germanischer Lloyd WindEnergie GMBH: Guideline for the Certification of Wind Turbines documents.1.3 This Outline of Investigation does not cover:a) WTGS intended for off-shore installation.b) Mechanical or structural integrity of the WTGS or subassemblies.c) Coordinati
10、on of electrical and mechanical systems to maintain the WTGS within its safe mechanical and structural limits.d) Mechanical loading of ladders, scaffolding, personnel tie offs, or other personnel load bearing functional parts.1.4 The products, systems, and subassemblies covered by these requirements
11、 are intended to be installed in accordance with the National Electrical Code, ANSI/NFPA 70.2 General2.1 Components2.1.1 Except as indicated in 2.1.2, a component of a product covered by this Outline shall comply with the requirements for that component. See Appendix A for a list of standards coveri
12、ng components used in the products covered by this Outline. See also Section 3, Special Components and Subassemblies of WTGS.2.1.2 A component is not required to comply with a specific requirement that:a) Involves a feature or characteristic not required in the application of the component in the pr
13、oduct covered by this Outline, orb) Is superseded by a requirement in this Outline.MAY 1, 2009SUBJECT 614052.1.3 A component shall be used in accordance with its rating established for the intended conditions of use.2.1.4 Specific components are incomplete in construction features or restricted in p
14、erformance capabilities. Such components are intended for use only under limited conditions, such as certain temperatures not exceeding specified limits, and shall be used only under those specific conditions.2.1.5 Components and subassemblies of the overall WTGS shall be evaluated and found suitabl
15、e for operation over the normal range of electrical and environmental conditions as specified by the WTGS manufacturer.2.2 Units of Measurement2.2.1 Values stated without parentheses are the requirement. Values in parentheses are explanatory or approximate information.2.3 Undated References2.3.1 Any
16、 undated reference to a code or standard appearing in the requirements of this Outline ofInvestigation shall be interpreted as referring to the latest edition of that code or standard.3 Special Components and Subassemblies of WTGS3.1 Wiring3.1.1 Internal wiring shall comply with the Standard for Ind
17、ustrial Control Equipment, UL 508, in addition to the requirements in this section.3.1.2 Wiring that is subject to movement, flexing, or twisting during operation of the wind turbine shall be investigated for suitability in the conditions of use and rated life or cycle time.3.1.3 All wiring within a
18、 WTGS that is large enough for service personnel to enter the structure shall be rated for tray cable usage. The following meet the intent of the requirement:a) Multiconductor cable complying with the Outline of Investigation for Flexible Motor SupplyCable and Wind Turbine Tray Cable, Subject 2277,
19、and marked for Wind Turbine usage.b) Power-limited circuit cabling complying with the Standard for Power-Limited Circuit Cables, UL 13, suitable for Tray Cable usage (Types CMG, CM, CL2, CL3, PLTC, CMR, CL2R, CL3R, CMP, CL2P, CL3P).c) Optical fiber circuits complying with the Standard for Optical Fi
20、ber Cable, UL 1651.d) Power cabling complying with the Standard for Thermoplastic-Insulated Wires and Cables, UL 83, or the Standard for Thermoset-Insulated Wires and Cables, UL 44, and additionally marked for Cable Tray usage (“CT”, “For Cable Tray Use”, “For CT Use”, or “For Use in Cable Trays”) o
21、r marked FT4.Exception: Wiring within a component need only meet the requirements for the component.Note: For Canada, an FT4 rating is required per the Canadian Electrical Code.6SUBJECT 6140MAY 1, 20093.1.4 Wiring within a rotating hub shall be additionally protected from mechanical damage. Such pro
22、tection may be provided by enclosures or conduit complying with the Standard for Metallic Outlet Boxes, UL 514A, and/or the Standard for Conduit, Tubing, and Cable Fittings, UL 514B, mechanical shielding, or the equivalent.3.1.5 Wiring subjected to exposure to water or oil during normal or abnormal
23、conditions such as a gasket or seal leak shall be suitably rated for the condition.3.1.6 Wiring subjected to UV exposure shall be rated for exposure to sunlight.3.2 Cable drip loop3.2.1 If operation of the wind turbine may result in twisting of flexible cables, such as the connecting cables between
24、rotating parts (nacelle) and parts of the fixed structure (tower or foundation), the operational conditions of use shall not cause damage to the conductors or their insulation. The evaluation shall address service life, electrical and environmental operating conditions of the subassembly.3.2.2 Contr
25、ols that prevent damage to conductors or their insulation including rotational limits shall be considered part of the Safety Related Controls System evaluation of this document. The Control shall be designed such that resetting to the neutral position is possible. See Section 9, Safety Related Contr
26、ols System (SRCS).3.3 Bus bars3.3.1 Sections of bus shall be suitably attached to the tower or to components of the tower intended to support the bus. The compliance of the attachment method shall be determined by subjecting a representative bus to Impact, Static Load, and Flexing tests.3.3.2 Bus sh
27、all be guarded or insulated to prevent unintentional contact in accordance with the following:a) Bus shall be metal enclosed at each work platform for a minimum of 8 feet above each platform.b) In areas other than work platforms, bus operating at 2500 V or more shall be metal enclosed.c) In areas ot
28、her than work platforms, bus operating at less than 2500 V shall be metal enclosed, enclosed in a non-metallic enclosure complying with the Standard for Polymeric Materials Use in Electrical Equipment Evaluations, UL 746C, or the conductors shall be protected by insulation and jacket that would be r
29、equired of comparable tray cables specified by the Outline for Flexible Motor Supply Cable and Wind Turbine Tray Cable, Subject 2277, the Standard for Electrical Power and Control Tray Cables with Optional Optical-Fiber Members, UL1277, and the Standard for Thermoplastic-Insulated Wires and Cables,
30、UL 83.3.3.3 Where cables are connected to bus assemblies, suitable wiring terminals shall be provided. Where the anticipated movement of the tower assembly causes movement of the cable or bus assembly, strain relief shall be provided to prevent movement of the connection.MAY 1, 2009SUBJECT 614073.3.
31、4 Performance requirements shall be based on the Standard for Busways, UL 857, for bus rated 600V or less and on the Standard for Metal Enclosed Bus, IEEE C37.23, for bus rated more than 600 V. Performance testing shall include electrical and mechanical tests. See 3.3.5 and 3.3.6.3.3.5 The following
32、 electrical tests shall be conducted:a) Continuous Current (Heating),b) Dielectric Withstand (Applied Potential) for all voltage ratings, c) Impulse Withstand for bus rated more than 2.2kV,d) Short Circuit Withstand for bus assemblies rated up to 600V, ande) Momentary and Short-Time tests for bus as
33、semblies rated greater than 600V.3.3.6 The mechanical tests specified in (a), (b), and (c) shall be conducted. The parameters for vibration and flexing tests are to be determined based on the amount of flexing transmitted to the bus assembly through movement of the wind turbine and tower under antic
34、ipated extreme conditions determined based upon the WTGS calculations in Wind turbines Part 1: Design requirements, IEC 61400-1.a) Impact Tests Ambient and cold impacts shall be conducted on the enclosure, housing or insulator as specified in the Standard for Busways, UL 857, or the Standard for Met
35、al Enclosed Bus, IEEE C37.23, the Standard for Polymeric Materials Use in Electrical Equipment Evaluations, UL 746C, or the Standard for Thermoplastic-Insulated Wires and Cables, UL 83,as applicable.b) Static Load Test The bus bar and the lower structural support shall be subjected to a force of 4 t
36、imes the normal load of the fully assembled longest bus bar in the system. This test force shall include any additional weight of connection cables. Bus bar sidewall supports, guides and associated bracketry are to be subjected to a force of 4 times the maximum normal operating force encountered dur
37、ing tower movement. As a result of the loading test, there shall not be permanent deformation, breakage, dislocation, cracking or other damage to the system or mounting structure.c) Flexing Test The bus bar shall be subjected to a flexing test to simulate expecteddeflection and forces on bus bars an
38、d support structure over the wind turbine expected life in its intended installation location. The site class as designated by Section 6 of Wind turbines Part1: Design requirements, IEC 61400-1 shall be used to define and quantify this expected mechanical operating environment over time. The test ex
39、cursion movements required for this test shall be 1.5 times the calculated movement of the bus bar system. Prior to the test, the bus bar assembly is to be subjected to loading on the top of the bus bar section to simulate the loading of the upper sections of bus bar, insulator and cables. Forces ar
40、e to be cyclicallyapplied to the bus bar to represent movement of the actual tower. As a result of the loadingtest, there shall not be permanent deformation, breakage, dislocation, cracking or other damage to the system or mounting structure.Exception: Mechanical means to mitigate bus bar stress and
41、 force may preclude the need to perform a mechanical flexing test.8SUBJECT 6140MAY 1, 20093.3.7 The dielectric tests shall be performed following each of the above tests. Following the above tests, the bus bar insulators shall prevent accessibility to electrically live parts as determined by applica
42、tion of the accessibility probe.3.3.8 The leakage current test shall be performed following the above tests for polymeric enclosed bus bars.3.4 Switchgear3.4.1 Switchgear installed within the tower assembly shall comply with the appropriate ANSI standard for the type of switchgear installed.3.4.2 Sw
43、itchgear installed within the tower assembly is considered to be installed in an indoor location, but may be subjected to dripping water. Enclosures for switchgear shall not have openings on the top surface, unless such openings are protected by a drip hood which prevents entrance of falling water.3
44、.4.3 The service conditions within the tower assembly shall be considered with respect to the normal service conditions for the type of switchgear installed within the tower. Where the anticipated service conditions within the tower are more severe than the normal service conditions for the switchge
45、ar, these conditions shall be mitigated, or additional investigation of the switchgear may be required.Note: As an example, the normal service conditions for Metal-Clad Switchgear are defined in ANSI/IEEE C37.20.2 to include an ambient air temperature of 30 to 40 C, and an altitude of 1000 m or less
46、. If the anticipated temperature within the tower assembly is less than 30 C, supplemental heating may be required.3.5 Transformers3.5.1 Power transformers rated 600 V ac or less shall comply with the requirements in the Standard for Specialty Transformers, UL 506, the Standard for Dry-Type General
47、Purpose and Power Transformers, UL 1561, the Standard for Low Voltage Transformers Part 1: General Requirements, UL 5085-1, the Standard for Low Voltage Transformers Part 2: General Purpose Transformers, UL 5085-2, or the Standard for Low Voltage Transformers Part 3: Class 2 and Class 3 Transformers
48、, UL 5085-3.3.5.2 Power transformers rated greater than 600 Vac shall comply with the requirements in the Standard for Transformers, Distribution, Dry-Type Over 600 Volts, UL 1562.3.5.3 Overcurrent protection for power transformers shall comply with Article 240 Part IX, OvercurrentProtection Over 60
49、0 V, Nominal of the National Electrical Code, ANSI/NFPA 70.3.5.4 Instrument transformers shall comply with ANSI/IEEE C57.13,Standard Requirements for Instrument Transformers, and ANSI/IEEE C57.13.2, IEEE Standard Conformance Test Procedures for Instrument Transformers”.MAY 1, 2009SUBJECT 614093.6 Hu
50、b3.6.1 Assemblies and components in the rotating hub shall be suitable for the expected rotating motion of the assembly.3.6.2 Electrical cabinets in the hub shall have doors secured by latches requiring a tool for removal to prevent damage to electrical components by loose material in the hub. The e
51、nclosures shall comply with the applicable enclosure requirements of the Standard for Industrial Control Equipment, UL 508, or the Standard for Power Conversion Equipment, UL 508C.3.7 Converter/Inverter3.7.1 The Converter/Inverter assembly of a WTGS shall comply with the Outline of Investigation for
52、 WindTurbine Converters and Interconnection Systems Equipment, Subject 6141.3.8 Lightning protection systems3.8.1 Lightning Protection Systems on a WTGS shall comply with NFPA 780, Standard for Installation ofLightning Protection Systems, Including Annex N Wind Turbine Generator Systems.3.8.2 Compon
53、ents of the Lightning Protection System shall comply with the Standard for LightingProtection Components, UL 96.3.9 Slip rings3.9.1 General3.9.1.1 Slip rings used for transmission of power, control, and signal circuits to the hub shall be evaluated to the requirements of the Standard for Industrial
54、Control Equipment, UL 508.3.9.1.2 The UL 508 Temperature Test shall be conducted with the unit rotating as intended in its end-use installation.3.9.1.3 The slip ring circuits and ground paths shall withstand fault current ratings in accordance with UL508, or ratings equal to or greater than the over
55、current protection provided in the end-use installation.10SUBJECT 6140MAY 1, 20093.9.2 Slip ring overload3.9.2.1 The slip ring is to be mounted and enclosed to represent its end application and the unit is to be tested with a load current and time duration as indicated in 3.9.2.2. The unit shall be
56、tested at rated voltage15 percent. The slip ring shall not show evidence of ignition, sealant leakage, cracking, breakage, or similar physical damage.3.9.2.2 For a slip ring with integral overcurrent protection, the overload current is to be 135 percent of the overcurrent protective device rating. F
57、or a slip ring without integral overcurrent protection, the overload current is to be 135 percent of the current rating of the maximum size branch circuit to which the slip ring can be properly connected. The overload test current is to be applied for 1 hour for test currents up to 81A and 2 hours for test currents greater than 81 A. If agreeable to those concerned, multiple circuits (above and below 81 amps) may be tested for 2 hours. The integral overcurrent protect
- 温馨提示:
1: 本站所有资源如无特殊说明,都需要本地电脑安装OFFICE2007和PDF阅读器。图纸软件为CAD,CAXA,PROE,UG,SolidWorks等.压缩文件请下载最新的WinRAR软件解压。
2: 本站的文档不包含任何第三方提供的附件图纸等,如果需要附件,请联系上传者。文件的所有权益归上传用户所有。
3.本站RAR压缩包中若带图纸,网页内容里面会有图纸预览,若没有图纸预览就没有图纸。
4. 未经权益所有人同意不得将文件中的内容挪作商业或盈利用途。
5. 装配图网仅提供信息存储空间,仅对用户上传内容的表现方式做保护处理,对用户上传分享的文档内容本身不做任何修改或编辑,并不能对任何下载内容负责。
6. 下载文件中如有侵权或不适当内容,请与我们联系,我们立即纠正。
7. 本站不保证下载资源的准确性、安全性和完整性, 同时也不承担用户因使用这些下载资源对自己和他人造成任何形式的伤害或损失。
最新文档
- 城市总体规划的作用——以深圳为例(蕾奥讲座)ppt课件
- 服饰图案设计色彩ppt课件
- 戴斯大酒店导视信息规划设计ppt课件
- 城市绿地系统规划概论ppt课件
- 城市地下综合管廊明挖法深基坑开挖支护施工技术ppt课件
- 厂内交通安全知识培训PPT课件
- 成考专科数学PPT课件
- 八年级地理上册总复习(人教)ppt课件
- 包丰自驾游方案ppt课件
- 标准化工地建设及样板引路(图文并茂)ppt课件
- 把观察到的事物写清楚——我的植物朋友(全国一等奖)ppt课件
- 安全防护·标志·标识标准化图册ppt课件
- 大港油田129事故安全经验分享ppt课件
- 大数据、智慧城市与智慧交通(下)ppt课件
- 大数据时代思维变革3更好ppt课件