凯迪电力MW生物质机组锅炉机组说明书
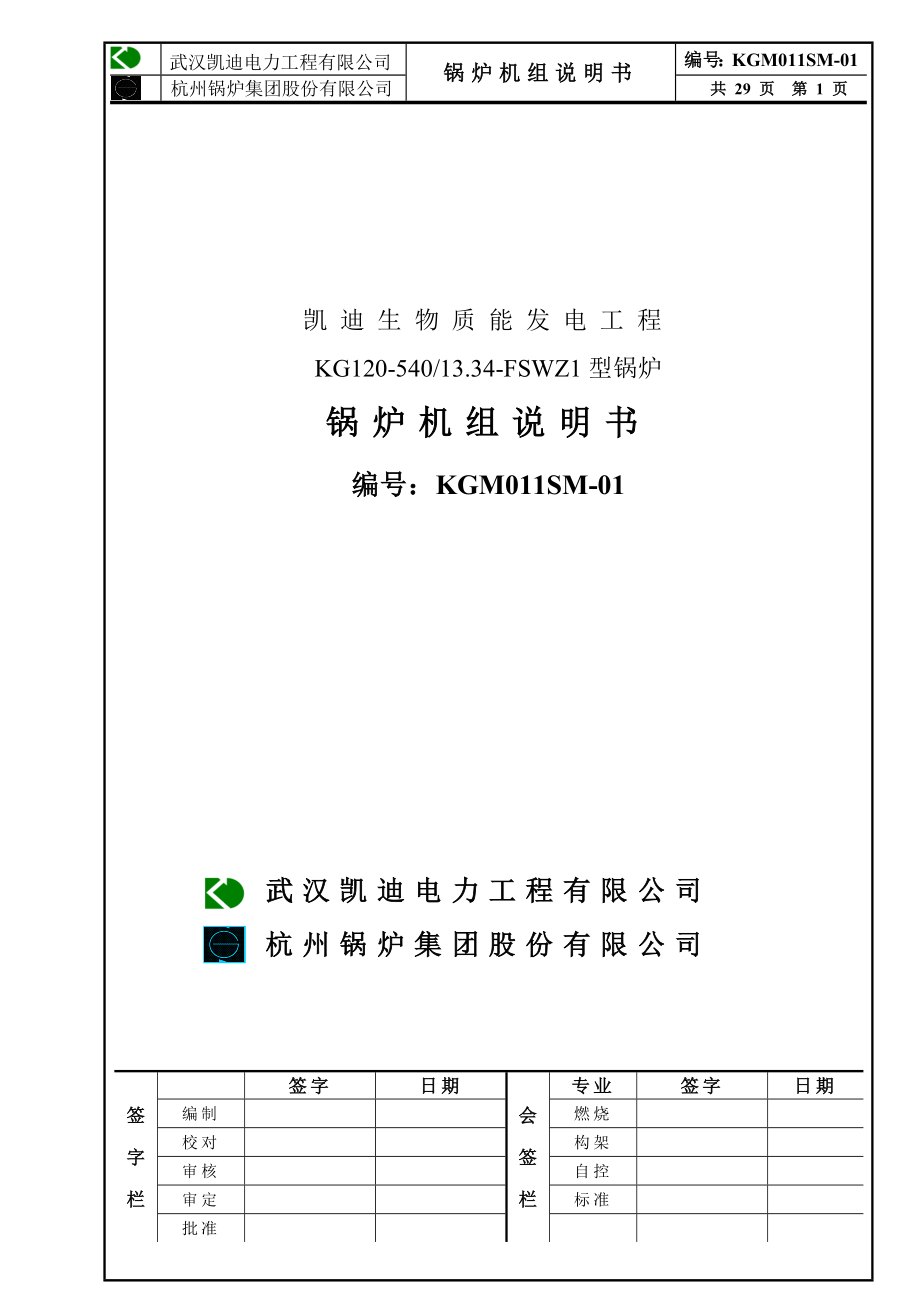


《凯迪电力MW生物质机组锅炉机组说明书》由会员分享,可在线阅读,更多相关《凯迪电力MW生物质机组锅炉机组说明书(29页珍藏版)》请在装配图网上搜索。
1、武汉凯迪电力工程有限公司锅炉机组说明书编号:KGM011SM-01杭州锅炉集团股份有限公司共 29 页 第 29 页 凯迪生物质能发电工程KG120-540/13.34-FSWZ1型锅炉锅炉机组说明书编号:KGM011SM-01武汉凯迪电力工程有限公司杭州锅炉集团股份有限公司签字栏签字日期会签栏专业签字日期编制燃烧校对构架审核自控审定标准批准目 录第1章循环流化床锅炉技术31-1常规流化床锅炉技术31-2生物质循环流化床锅炉技术4第2章锅炉主要设计参数及整体布置62-1锅炉设计主要基础数据62-2锅炉主要计算数据72-3锅炉整体布置9第3章锅炉主要部件结构163-1锅筒163-2锅筒内部设备1
2、73-3燃烧室及水冷壁183-4下降管193-5汽水引出管193-6水冷布风板193-7过热器系统及汽温调节203-8省煤器213-9空气预热器223-10物料循环系统223-11冷渣器233-12刚性梁233-13膨胀中心233-14锅炉范围内管道233-15吹灰系统243-16锅炉构架243-17启动燃烧器263-18炉前油管路系统263-19耐火耐磨材料263-20炉墙27第4章附图284-1锅炉主视图284-2锅炉俯视图29第1章 循环流化床锅炉技术1-1 常规流化床锅炉技术循环流化床(CFB)是上世纪七十年代末发展起来的高效率、低污染和良好综合利用的燃烧技术,由于它在燃料适应性和变负
3、荷能力以及污染物排放上具有的独特优势,使其得到迅速发展。循环流化床锅炉采用流态化的燃烧方式,这是一种介于煤粉炉悬浮燃烧和链条炉固定燃烧之间的燃烧方式,即通常所讲的半悬浮燃烧方式。所谓的流态化是指固体颗粒在空气的作用下处于流动状态,从而具有许多流体性质的状态。在循环流化床锅炉炉内存在着大量的床料(物料),这些床料在锅炉一次风、二次风的作用下处于流化状态,并实现炉膛内的内循环和炉膛外的外循环,从而实现物料在炉内不断的往复循环燃烧。与其它锅炉相比,循环流化床锅炉增加了物料循环回路部分即分离器、回料阀;另外还增加了底渣冷却装置冷渣器。分离器的作用在于实现气固两相分离,将烟气中夹带的绝大多数固体颗粒分离
4、下来;回料阀的作用一是将分离器分离下来的固体颗粒返送回炉膛,实现锅炉燃料及石灰石的往复循环燃烧和反应;二是通过循环物料在回料阀进料管内形成一定的料位,实现料封,防止炉内的正压烟气反窜进入负压的分离器内造成烟气短路,破坏分离器内的正常气固两相流动及炉内正常的燃烧和传热。冷渣器的作用是将炉内排出的高温底渣冷却到150以下,从而有利于底渣的输送和处理。一般循环流化床锅炉处在850-950的工作温度下,在此温度下石灰石可充分发生焙烧反应,使碳酸钙分解为氧化钙,氧化钙与煤燃烧产生的二氧化硫进行盐化反应,生成硫酸钙,以固体形式排出达到脱硫的目的。循环流化床锅炉可实现炉内高效廉价脱硫,一般脱硫率均在90%以
5、上。同时,由于较低的炉内燃烧温度,使循环流化床锅炉中生成的NOX主要来自于燃料中的N转化成的NOX;而热力NOX即空气中的N转化成的NOX生成量很小;同时循环流化床锅炉采用分级送风的方式即一次风从布风板下送入,二次风分多层从炉膛下部密相区送入,也可以有效地抑制NOX的生成。因此循环流化床锅炉中的污染物排放很低。在锅炉运行时,炉内的床料主要由燃料中的灰、未反应的石灰石、石灰石脱硫反应产物等构成,这些床料在从布风板下送入的一次风和从布风板上送入二次风的作用下处于流化状态,部分颗粒被烟气夹带在炉膛内向上运动。在炉膛的不同高度一部分固体颗粒将沿着炉膛边壁下落,形成物料的内循环;其余固体颗粒被烟气夹带进
6、入分离器,进行气固两相分离,绝大多数颗粒被分离下来,通过回料阀返送回炉膛,形成物料的外循环。所以循环流化床锅炉具有很高的燃烧效率。在循环流化床锅炉中,一般根据物料浓度的不同将炉膛分为密相区、过渡区和稀相区三部分,密相区中固体颗粒浓度较大,具有很大的热容量,给煤进入密相区后,可以顺利实现着火,因此循环流化床锅炉可以燃用无烟煤、矸石等劣质燃料,还具有很大的锅炉负荷调节范围;与密相区相比,稀相区的物料浓度较小,稀相区是燃料的燃烧、燃尽段,同时完成炉内气固两相介质与炉内受热面的换热,以保证锅炉的出力及炉内温度的控制。循环流化床锅炉的不同部位处于不同的气固两相流动形式,炉内处于快速床的工作状态,具有颗粒
7、间存在强烈扰动和返混等性质;回料阀进料管内处于负压差移动填充床状态,返料管内处于鼓泡床流动状态;尾部烟道处于气力输送状态。1-2 生物质循环流化床锅炉技术随着社会对能源需求的日益增长,而作为主要能源来源的化石燃料却迅速地减少。因此,寻找一种可再生的替代能源,成为社会普遍关注的焦点。而生物质是唯一的既可再生又可直接储存与运输,且可实现CO2零排放的能源,因此,燃用生物质发电的锅炉将被广泛的应用。本工程锅炉燃用树枝、稻壳、秸秆等林业及农作物生物质燃料,采用循环流化床燃烧方式。由于生物质燃料含硫量较低,并且自脱硫能力较强,考虑到飞灰综合利用等因素。同常规循环流化床锅炉相比,生物循环流化床锅炉不设置石
8、灰石添加系统。生物质燃料同常规燃料(煤)相比较,其燃烧特性有较大区别,主要表现以下几个方面: 生物质燃料在不同的季节燃料成分有所差别,燃料量也随季节的不同而改变,这就要求锅炉有较好的适应性以适应燃料的变化。 生物质燃料挥发份高、含氧量高、灰量偏少、燃料及灰密度低。具有容易着火(300左右)、燃烬率低、CO排放量较大的特点,燃烧特性总体劣于煤。同时,又存在流化不稳定、循环物料量不足、易于积灰和堵灰等问题。 稻壳灰中的SiO2含量高,存在着床料易于结团,尾部对流受热面磨损严重的问题。 秸秆灰中Na、K、CL离子含量高,容易出现高低温腐蚀。 树根和稻草等生物质燃料存在难破碎的特点,燃料制备系统较为复
9、杂。综合上述因素,生物质循环流化锅炉设计中采取了相应措施以保证锅炉的安全、稳定、经济运行。 通过采用合理的炉膛出口温度、采用高效旋风分离器、分级燃烧、合理布置二次风风口高度,采用4通道布置,增加烟气流程,选取较大过量空气系数等措施,以保证碳粒的燃烧条件和在炉内的停留时间,提高锅炉燃烧效率、减少CO排放。 炉膛采用超大的截面积,适应生物质燃料水分变化带来烟气量变化的情况;保证各粒度燃料的正常流化,加大下炉膛深度方向的收缩比,减少布风板的面积;选取合理的流化速度,保证炉膛温度场的均匀性:采用分级燃烧、合理布置二次风风口高度,选取较大过量空气系数等措施,以保证碳粒的燃烧条件和在炉内的停留时间,提高锅
10、炉燃烧效率、减少CO排放。 设置床料补充系统、选用含Fe2O3较多的流化床锅炉底渣作为启动床料和补充床料、采用较高的风帽阻力,以避免床料结团和分层流化、保证流化均匀。 在炉内布置优质耐腐蚀的高温屏式过热器,降低炉膛出口烟温,合理控制高温过热器入口烟温、减少汽温偏差,以减轻过热器高温腐蚀。 高低温过热器采用大节距、顺列布置、布置高效吹灰器等手段,以减轻磨损、防止沾污、堵灰和积灰。 采用热管式空气预热器,提高空气预热器冷端壁温,克服低温腐蚀。综上所述,充分考虑生物质燃料特性,采取有效措施的情况下,本工程燃用生物质的循环流化床锅炉具有下列特点: 锅炉有较好的适应性、可以适应燃料的变化。 燃烧效率高。
11、 合理的燃烧温度,分级送风方式、可以降低燃烧过程中NOX生成量,无需对烟气处理也能满足排放要求。 能够充分利用灰中的CaO,减少了SO2的排放。 燃烧温度低于灰熔点温度,能够避免结焦。 采用低倍率循环流化床燃烧方式,合理设计关键部件,提高锅炉的可用率,使其能够长期稳定运行。 锅炉在不低于30MCR负荷时,不加辅助燃料可以稳定燃烧,在10040MCR范围内可正常运行。 生物质燃料在低温燃烧后,燃料灰活性好,一些微量元素含量高。可作为水泥添加剂、农作物肥料等,有着很好的市场前景,利于灰渣的综合利用。第2章 锅炉主要设计参数及整体布置2-1 锅炉设计主要基础数据2-1.1 燃料成份本工程燃料采用生物
12、质能,生物质能又称“绿色能源”,包括树木、茅草、农作物秸秆、稻壳、秸秆压块等。本工程燃用燃料分三种情况:以林业资源为主的燃料情况;以农作物资源为主的燃料情况,适当考虑林业资源;以农作物资源为主的燃料情况,不考虑林业资源。为保证锅炉具有良好的燃料适用性,锅炉按以农作物资源为主要的燃料情况,适当考虑林业资源拟合后的平均成份进行设计。锅炉考核试验时,按相关国家标准进行折算。锅炉运行时,根据实际的燃料情况进行运行调整。设计燃料和校核燃料成分见下表。种类项目名称符号单位设计燃料校核燃料1校核燃料2工业分析挥发份Vdaf%81.3785.677.1灰分Aar%7.303.4089.52水分Mar%28.6
13、940.819.83元素分析收到基碳Car%30.2327.8732.80收到基氢Har%4.293.694.88收到基氧Oar%28.823.3632.51收到基氮Nar%0.640.840.44收到基硫Sar%0.0520.0480.056合计tot%100100100低位发热值QMJ/kg10.6929.5411.82Kcal/kg255422802823.42-1.2 点火用油参数油种:0 轻柴油(GB2522000)序号项目数值1运动粘度(20下)3.08.0 mm2/s2灰份不大于0.01%3水份不大于痕迹4机械杂质无5凝固点不高于06闭口闪点不低于557硫含量不大于0.2%810
14、蒸发物残炭不大于0.3%9低位热值Qnet.ar41868KJ/Kg2-1.3 给水品质给水质量标准:GB/T12145-2008火力发电机组及蒸汽动力设备水汽质量标准。锅炉连续排污率(B-MCR):1%。2-1.4 启动床料和补充床料启动床料和补充床料采用循环流化床锅炉底渣筛分而成,启动颗粒粒度:最大允许粒径 dmax5000m;d501600m补充床料颗粒度为:最大允许粒径dmax=3000m,d50=1200m;要求控制床料中的钠、钾含量,以免引起床料结团。其中:Na2O1.02.0%;K2O2.03.0%2-2 锅炉主要计算数据下列计算数据如果与热力计算汇总表不符,以锅炉热力计算汇总表
15、为准2-2.1 锅炉汽水参数序号项目符号单位BMCR设计燃料1额定蒸发量Dt/h120.462给水量Dgst/h116.63过热器减温水量Dpst/h7.494主蒸汽压力PMpa(g)13.345主蒸汽温度t5406给水温度tgs240.57给水压力PgsMpa(g)15.108锅筒压力PgtMpa(g)14.752-2.2 锅炉主要参数汇总序号项目符号单位BMCR1锅炉排污率pw%32减温水温度Tjw240.53减温水压力PjwMpa15.14一级减温水量D1jwt/h05一级调温幅度T1jw06二级减温水量D2jwt/h4.797二级调温幅度T2jw26.38三级减温水量D3jwt/h2.
16、79三级调温幅度T2jw19.0210环境温度thj2011冷空气温度tlk3012一次风温度tfw123613二次风温度tfw223614炉膛床温tlt82215炉膛出口温度tlck85416排烟温度tpy15117炉膛出口过量空气系数-1.318飞灰份额afh%8019锅炉保证效率%90.092-2.3 汽水运行参数项目工质温度 ()工质压力 (Mpa)工质流量质量流速入口出口温升入口出口压降t/hkg/m2.sm/s省煤器240.5321.280.6615.09614.810.28116.6610.10.8锅筒341.614.75水冷壁341.614.75包墙过热器341.6366.4
17、24.83 14.75 14.58 0.221 112.97 一级过热器SH1366.4 406.3 39.9 14.58 14.288 0.292 112.97 616.6 9.5 一级减温器406.3 406.3 0.0 14.288 14.285 0.003 0二级过热器SH2406.4 451.3 44.90 14.285 14.108 0.177 112.97 554.9 10.2 二级减温器451.3 425.0 -26.3 14.108 14.105 0.002 4.79三级过热器SH3425523.7 98.7 14.105 13.805 0.300 117.76 810.6
18、17.2 三级减温器523.7 504.7 -19.0 13.805 13.803 0.002 2.700 四级过热器SH4504.7 540.0 35.3 13.803 13.340.463 120 754.7 18.3 2-2.4 烟气运行参数项目BMCR烟气温度 ()烟气速度入口出口温降m/s炉膛8543.70屏式(三级)过热器8548543.70分离器854854-屏式(二级)过热器8547121428.96 转向室712696.515.5-高温(四级)过热器696.562076.58.02 低温过热器6204991217.17 省煤器499275224空气预热器2751511242-
19、2.5 燃烧侧流量(过量空气系数=1.3)项目单位燃料1总烟气量Nm3/h147688烟气密度/Nm31.2636 总的湿空气量Nm3/h113233总的干空气量Nm3/h111456空气密度/Nm31.285燃料消耗量/h30210 计算燃料消耗量/h29904 飞灰量/h1991 底渣量/h498 总灰量/h2489 补充床料量/h10002-2.6 锅炉风量分配项目单位BRCM数值比率风量分配一次风量Nm3/h50955 45.%二次风量Nm3/h45584 40.26%播料风量Nm3/h8153 7.2%密封风风量Nm3/h5662 5.%高压流化风风风量Nm3/h28802.54%通
20、过布风板风量Nm3/h50955 一次风上二次风风量Nm3/h17094 二次风中二次风风量Nm3/h17094 二次风下二次风风量Nm3/h11396 二次风点火风风量Nm3/h24900启动用风混合风风量Nm3/h211000启动用风2-3 锅炉整体布置2-3.1 锅炉整体布置概述本工程采用高温超高压参数、单锅筒、自然循环、单段蒸发系统、集中下降管、平衡通风循环流化床锅炉,露天布置。锅炉主要由炉膛、高温绝热分离器和自平衡“U”形水冷回料阀及尾部3个部分组成。炉膛蒸发受热面采用膜式水冷壁、尾部第1、第2烟道采用汽冷包墙。炉膛下部布置水冷布风板,布风板上安装钟罩式风帽,具有布风均匀、防堵塞、防
21、结焦和便于维修等优点。炉膛上部稀相区布置高温屏式三级过热器(SH3)。锅炉采用2台高温绝热分离器,布置在炉膛与尾部对流烟道之间,外壳由钢板制造,内衬绝热材料及耐磨耐火材料,分离器上部为蜗壳形,下部为锥形。防磨绝热材料采用拉钩、抓钉、支架固定。每台高温绝热分离器回料腿下布置一个非机械型回料阀,回料为自平衡式,流化密封风由高压风机单独供给。回料立管及回料阀采用膜式壁结构,内衬45mm耐磨耐火材料。耐磨材料通过销钉固定在膜式壁上。炉膛、旋风分离器和回料阀三部分构成了循环流化床锅炉的核心部分物料热循环回路,燃料在炉膛内与循环物料混合并燃烧,产生热烟气,形成气固两相流。气固两相流在炉膛内向上流动。在这一
22、过程中大颗粒循环物料在不同高度向下回落,形成循环流化床锅炉的内循环。其余循环物料随热烟气经炉膛出口进入分离器,进行气固分离,分离下来的固体颗粒经过回料阀返回到炉膛,形成锅炉的外循环。被净化过的烟气则经分离器出口烟道进入尾部烟道并依次流经布置在尾部第1烟道中的低温屏式过热器、布置在尾部第2烟道的高温过热器、低温过热器、布置尾部第3烟道的省煤器和热管式空气预热器。过热蒸汽温度由布置在过热器之间的三级喷水减温器调节,减温喷水来自于锅炉给水。尾部第1、2烟道采用汽冷包墙,膜式壁结构,尾部第3烟道采用护板结构。炉膛与尾部第1、2烟道包墙均采用水平绕带式刚性梁来防止内外压差作用造成的变形。锅炉设有膨胀中心
23、,各部分烟气、物料的连接烟道之间设置性能优异的膨胀节,解决由热位移引起的密封问题,各受热面穿墙部位均采用成熟的密封技术设计,确保锅炉的密闭性。锅炉采用焊接钢构架。锅炉采用支吊结合的固定方式。炉膛、尾部第一烟道、尾部第二烟道、过热器系统、省煤器系统和回料阀采用悬吊结构。分离器、回料阀立管和热管空气预热器采用支撑结构。2-3.2 锅炉整体布置的主要特点2-3.2.1 采用按烟气流程四通道布置方式锅炉从前到后依次是炉膛、分离器及回料阀、尾部第一烟道、尾部第二烟道和第三烟道。炉膛和旋风分离器相连接,分离器下布置回料阀并通过回料斜管和炉膛下部相连接。炉膛、分离器和回料阀组成了锅炉的物料循环系统。炉膛内布
24、置高温屏式过热器(SH3)。尾部第一烟道内布置低温屏式过热器(SH2)。尾部第二烟道内布置高温过热器(SH4)、低温过热器(SH1)。尾部第三烟道内布置省煤器和热管空气预热器。2-3.2.2 可靠的防磨措施循环流化床锅炉中,由于大量高温循环粒子不断流经燃烧室、分离器和回料阀,所以存在着严重的磨损问题,为使锅炉长期安全可靠运行,在以下表面采取了可靠的防磨措施: 高温绝热分离器及料腿内表面 回料阀内表面 高温绝热分离器和对流烟道之间的连接烟道内表面 下部炉膛内表面和布风板上表面 燃烧室出口烟道及出口烟道周围 炉膛开孔及穿墙处 炉内屏式过热器的迎烟气面弯头 屏式过热器的迎烟气面2-3.2.3 尾部高
25、低温过热器采用大节距、顺列的布置方式高、低温过热器采用大节距、顺列布置,有利于减轻受热面的积灰和磨损。2-3.2.4 水冷布风板和钟罩式风帽锅炉采用水冷布风板,使布风板得到可靠的冷却。布风板管间鳍片上布置有钟罩式风帽,每个风帽由较小直径的内管和较大直径的外罩组成。这种风帽具有流化均匀、防堵塞、耐磨损、安装、维修方便的优点。由于启动点火时,水冷风室内温度较高,所以,在水冷风室内表面敷设有耐火材料。2-3.2.5 屏式受热面在炉膛上部布置了过热器屏式受热面(SH3),可以降低分离器入口烟气温度,避免分离器内部温度过高,从而避免结渣。 在尾部第1烟道内布置了过热器屏式受热面(SH2)。一方面,可以降
26、低高温过热器入口烟气温度,避免因高温过热器壁温过高,从而避免局部高温腐蚀。另一方面,有凝渣作用,可以减轻其后对流受热面的积灰和堵灰。2-3.2.6 三向膨胀节本锅炉采用支吊结合的固定方式,为解决炉膛与高温绝热分离器、回料阀、冷渣器之间以及高温绝热分离器与回料阀、尾部对流烟道之间的相对三向膨胀,在以上各处装有既能耐高温、又能抗磨损的三向膨胀节。安装时,应按图纸要求施工,保证金属件、耐磨耐火材料相对尺寸。2-3.2.7 高温绝热分离器采用蜗壳式高温分离器,中心筒采用特殊结构,有利于气固分离,分离效率高、运行可靠。2-3.2.8 双H型鳍片省煤器采用双H型鳍片省煤器,顺列布置。一方面可以有效的减轻省
27、煤器磨损;另一方面又可以减轻省煤器的积灰和堵灰。2-3.2.9 热管式空气预热器采用无机传热介质热管式空气预热器,提高空气预热器冷端壁温,防止空气预热器的低温腐蚀。同时,又可以选用较低的排烟温度,提高锅炉效率,并适应布袋除尘器要求。2-3.2.10 全疏水结构除低温屏式过热器受热面(SH2)外、其余受热面采用全疏水结构,锅炉停炉后可全部疏水,有利于锅炉的停炉保护。2-3.2.11 膨胀中心锅炉设置有膨胀中心,可进行膨胀量计算,作为膨胀补偿、间隙予留和管系应力分析的依据,并便于与设计院所设计的各管道的受力情况相配合,也为锅炉本体的刚性梁,密封结构和吊杆的设计提供了依据。2-3.2.12 燃烧室正
28、压运行锅炉采用平衡通风方式,压力平衡点位于炉膛出口,所以运行时燃烧室处于正压工况,为了防止烟气泄漏,确保燃烧室的密封性,所有门、孔以及管束穿墙处都设有密封盒或焊接密封。2-3.2.13 水冷滚筒式冷渣器冷渣器采用水冷滚筒式冷渣器。可以把渣冷却到150以下,然后排至除渣系统。具有运行方便,安全可靠的特点。冷却水为工业水。2-3.2.14 床下启动燃烧器炉膛下部水冷风室侧墙一次风道上布置2只床下启动燃烧器,用于锅炉的启动和低负荷稳燃。具有启动速度快、热利用率高、节约启动用油的优点。2-3.3 锅炉主要系统及流程2-3.3.1 锅炉汽水流程锅炉给水经过水冷回料阀到省煤器入口集箱和水平布置的省煤器,进
29、入省煤器的出口集箱,最后由省煤器引出管接至锅筒。在启动阶段,省煤器再循环系统可以将炉水从锅筒直接引至水冷回料阀进口集箱,从而保护水冷回料阀和省煤器。锅炉采用自然循环,锅筒内的锅水由集中下降管分配到炉膛水冷壁和和延伸墙水冷壁,经炉膛水冷壁和和延伸墙水冷壁加热后成为汽水混合物,随后经水冷壁上集箱和和延伸墙水冷壁上集箱、汽水引出管引入锅筒进行汽水分离。被分离出来的锅水进入锅筒水空间,进行再循环。分离出来的饱和蒸汽由锅筒顶部的饱和蒸汽连接管分别引至第1烟道的前墙、中间墙,汇集到前墙下集箱和中间墙下集箱,再分别经过烟道的侧墙、后墙流入低温过热器入口集箱,然后依次经过低温过热器(SH1)、备用喷水减温器、
30、低温屏式过热器(SH2)、二级喷水减温器、高温屏式过热器(SH3)、三级喷水减温器、高温过热器(SH4),最后将合格的过热蒸汽引向汽轮机。2-3.3.2 锅炉烟风系统锅炉设有一次风系统、二次风系统、高压流化风系统和烟气系统。锅炉采用平衡通风,零压点设置在炉膛出口处,通过引风机挡板的开度进行调节。 一次风系统:一次风系统用风由一次风机提供。经过一次风机出口的冷风分冷热2路,一路经过空气预热器加热后,成为热风,然后又分为锅炉一次风和锅炉启动用风。另一路不经过空气预热器,作为锅炉的播料风和给料密封风。锅炉一次风流经水冷风室和布风板上风帽进入炉膛底部,实现炉膛的物料流化、辅助燃料着火和助燃。锅炉点火期
31、间,此路风关闭,由启动用风代替。锅炉的启动用风又分为点火风和混合风。点火风用于启动燃烧器油点火,混合风用于控制油燃烧后的烟气温度。锅炉正常运行时,此路风关闭。不经过空气预热器的冷风经过增压风机增压后,接到炉前给料装置的特定部位,使燃料能够顺利的进入炉膛,同时防止炉膛内烟气返窜,保护给料系统。 二次风系统二次风系统用风由二次风机提供。二次风经过空气预热器后,分别进入上、中、下二次风箱及其支管,然后进入到炉膛过渡区和稀相区,用于燃料的助燃。运行中可以通过调节一、二次风风量的配比来控制炉膛温度。 高压流化风系统高压流化风机提供的高压流化风经回料阀底部风室,分别进入到回料阀的下料区和返料区,实现回料阀
32、中物料的流化和回料阀的自密封。 烟气系统燃料在炉膛内燃烧后产生的烟气和没有被分离器分离的飞灰先后流经尾部的对流受热面,然后经过除尘系统、引风机,进入烟囱,排向大气。2-3.3.3 物料循环过程 锅炉冷态启动时,在炉膛内加装启动物料后,首先启动床下燃烧器,燃烧产生的高温烟气,通过水冷式布风板送入炉膛,启动物料被流化和加热。床温上升到约450并维持稳定后,燃料开始分别由炉前给料口送入炉膛下部的密相区内。锅炉启动完成后,关闭启动燃烧器。燃烧空气分为一、二次风,分别由炉底和布风板上部送入。一次风经床底水冷风室,作为一次燃烧用风和炉内物料的流化介质送入燃烧室,二次风在前后墙沿炉高方向上分3层布置,以保证
33、提供给燃料颗粒足够的燃烧用空气并参与燃烧调整;同时,分级布置的二次风在炉内能够营造出局部的还原性气氛,降低氮氧化物NOX 的生成。燃烧产生的烟气携带大量床料经炉顶转向,通过位于后墙水冷壁上部的两个烟气出口,分别进入两台绝热式蜗壳分离器进行气固分离。分离后含少量飞灰的烟气由分离器中心筒引出,进入尾部烟道,对布置在其中低温屏式过热器(SH2)、高温过热器(SH4)、低温过热器(SH1)、省煤器及空气预热器放热,到锅炉尾部出口时,烟温已降至151左右。被分离器捕集下来的灰,通过分离器下部的立管和返料器送返炉膛实现循环燃烧。炉膛底部设有两个排渣口,通过排渣量大小的控制,使床层压降维持在合理范围以内,以
34、保证锅炉良好的运行状态。2-3.3.4 燃料的供给及排渣系统锅炉给料系统采用前墙集中布置,炉前布置有六个给料口。一定粒度的燃料经给料机进入布置在前墙的六台给料装置,然后被送入炉膛燃烧。燃料燃烧后的灰渣分别以底渣和飞灰的形式排出,底渣从炉膛底部排出,飞灰从尾部排出。燃料的种类、粒度、成灰特性等会影响底渣和飞灰所占的份额。就本设计燃料和要求粒度而言,按底渣占总灰量的20%及飞灰占总灰量的80%进行设计。锅炉的排渣采用水冷滚筒冷渣器。为保证长期停炉的过程中,将床料完全排出,返料器下还设有排灰口,现场可根据实际情况,将其纳入底渣系统。2-3.3.5 膨胀、密封、吊挂系统根据锅炉支、吊结构布置方式,整台
35、锅炉在深度方向上共设置了五个膨胀中心:炉膛中心线、两个旋风分离器中心线、包墙中心线和第3烟道中心。锅炉的炉膛水冷壁、汽冷包墙、省煤器及护板全部悬吊在顶板上,由上向下膨胀;炉膛通过刚性梁的限位装置使其以炉膛几何中心线为零点向前后、左右膨胀;汽冷包墙也通过刚性梁的限位装置使其以包墙中心线为零点向前后、左右膨胀。旋风分离器筒体、空气预热器均以自己的支承面为基准向上、下膨胀, 前后、左右为对称膨胀。考虑到锅炉的密封和运行的可靠性,各单独的膨胀体系通过金属或非金属膨胀节连接。所有穿墙管束在穿墙处封焊或密封固定,或通过膨胀节形成柔性密封,以适应热膨胀和变负荷的要求。2-3.3.6 吹灰系统为了保持受热面的
36、清洁,本锅炉采用激波吹灰系统。2-3.4 锅炉整体布置基本尺寸锅炉深度(前后外支柱中心距离)29300mm锅炉宽度(两侧外支柱中心线距离)13200mm锅炉顶板标高41100mm锅炉运转层标高8000mm锅筒中心线标高36550mm省煤器进口集箱标高23215mm过热器出口集汽集箱标高20000mm2-3.5 锅炉水容积名称单位锅筒水冷系统过热器系统省煤器系统总计水压时 M320 50298107 正常运行时 M38 500866 2-3.6 锅炉受压元件的规格材料汇总表序号名称 规 格材料1锅筒17809013MnNiMoR2炉膛前、后水冷壁上集箱2734520G3炉膛前、后水冷壁下集箱27
37、34520G4炉膛侧水冷壁上集箱2193220G5炉膛侧水冷壁下集箱2193220G6炉膛出口烟道集箱2192820G7水冷壁延伸墙入口集箱2192820G8水冷壁延伸墙出口集箱2192820G9炉膛出口烟道立管1591620G10炉膛水冷壁管子606.520G11延伸墙水冷管子606.520G12布风板水冷壁管子601015CrMoG13水冷壁下水分配管5086020G14炉膛集中下降管4573520G15延伸墙下水分配管3775220G16延伸墙集中下降管3253020G17延伸墙汽水引出管1591620G18水冷壁汽水引出管1591620G19前包墙上集箱273x4020G20前包墙中间
38、集箱219x3220G21中隔墙上集箱273x4020G22包墙下集箱273x4020G23中隔墙下集箱219x3220G24左侧包墙下集箱219x3220G25右侧包墙下集箱219x3220G26侧包墙上集箱219x3220G27低过进口集箱273x4020G28低过出口集箱273x2012Cr1MoVG29屏过进口集箱273x2612Cr1MoVG30屏过出口集箱273x2612Cr1MoVG31高过进口集箱273x2612Cr1MoVG32高过出口集箱273x4012Cr1MoVG33集汽集箱273x4012Cr1MoVG34二级减温器集箱273x2612Cr1MoVG35一级减温器集箱
39、273x2612Cr1MoVG36前、中、后包墙管38x720G37侧包墙管38x720G38前、后顶管38x720G39高温过热器蛇形管(上组)42x712Cr1MoVG40高温过热器蛇形管(下组)42x6TP-347H41前/侧/中包墙管38x720G42低温过热器蛇形管(上一组)42x620G43低温过热器蛇形管(下二组)42x615CrMoG44屏过管 42x8TP-347H45集汽集箱引入管133x1612Cr1MoVG46饱和蒸汽引出管 108x1020G47省煤器蛇形管42x520G48省煤器入口集箱219x2520G49省煤器出口集箱219x2520G50省煤器中间集箱219x
40、2520G51省煤器散管60x1020G52省煤器引出管133x1320G53省煤器引出管集箱159x1620G54省煤器集箱至锅筒的连接管76x7.520G第3章 锅炉主要部件结构3-1 锅筒3-1.1 结构锅筒采用13MnNiMoR材料制成,内径为1780mm,壁厚90mm,筒身直段全长8200mm,两端采用半球形封头。锅筒筒身顶部装焊有饱和蒸汽引出管座、弹簧安全阀管座、压力表管座;与水平呈45夹角处装焊有给水引入套管接头;筒身水平部位及与水平呈-15夹角处装焊有汽水混合物引入管座;筒身底座部装焊有大直径下降管管座;此外,筒身还装焊有水位表连排、加药、紧急放水、再循环等管座,封头上装有人孔
41、。锅筒上下表面还焊有三对预焊板,工地安装时,将用来监测锅筒运行时上、下壁温的热电偶焊于其上。锅筒被吊挂在锅炉顶板上。在安装现场,锅筒内、外壁禁止施焊。3-1.2 水位锅筒正常水位在锅筒中心线以下150mm处,最高水位和最低水位离正常水位各50mm。真实水位的测定与控制对锅炉的运行是非常重要的。由于水位计中贮存的水处在锅炉外部较冷的大气中,其密度大于锅筒中水的密度,锅筒中的真实水位高于水位计中的指示的水位,因此,安装时要准确标定水位表中正常水位的位置。3-2 锅筒内部设备本锅炉汽水分离采用单段蒸发系统,锅筒内部装有旋风分离器、梯形波形板分离器、顶部百叶窗分离器等设备。它们的作用在于消除汽水混合物
42、的动能保持水位平衡,进行汽水分离和保证蒸汽上升速度均匀,保证蒸汽中的含盐量在标准以下。3-2.1 旋风分离器锅筒内部沿筒身全长两侧布置共有16只直径为315mm的旋风分离器,在锅炉MCR工况下,每只分离器的平均蒸汽负荷为7.5t/h。旋风分离器能消除高速进入锅筒的汽水混合物的动能以保持水位平衡和进行汽水混合物的粗分离,分离出的蒸汽沿分离器中部向上流动而分离出的水沿筒内壁向下流动,平稳地流入锅筒的水空间。3-2.2 梯形波形板分离器每只旋风分离器上部装有一只梯形波形板分离器,以均匀旋风筒中蒸汽上升速度,在离心力的作用下将蒸汽携带的水分进一步分离出来。3-2.3 顶部均汽孔板分离器在锅筒上部靠近饱
43、和蒸汽引出管沿锅筒筒身方向布置20个均汽孔板,其作用是进一步分离蒸汽中的水分,且均汽孔板能使通过的蒸汽均匀速度,有利于水的重力分离,同时也能阻挡一些水滴,起到一定的分离作用。3-2.4 排污管连续排污管布置在锅筒水空间的上部,以排出含盐浓度最大的锅水,维持锅水的含盐量在允许的范围内。3-2.5 加药管利用加药管沿全长向锅筒水空间加入磷酸盐,维持锅水碱度在PH=9.09.5范围内,降低硅酸盐的分配系数,降低蒸汽的溶解性携带。3-2.6 紧急放水管当锅炉给水与蒸发量不相吻合而造成水位增高超过最高允许水位时,应通过紧急放水管放水至正常水位,防止满水造成事故。3-2.7 定期排污管定期排污管装在集中下
44、降管下部的分配集箱底部,由于在锅水中加入磷酸盐,将产生一些不溶于水的悬浮物质,随流入下降管的水流至分配集箱底部并沉积在底部,悬浮物质可通过定期排污管排出,保持锅水的清洁。定期排污的时间可根据锅水品质决定。3-3 燃烧室及水冷壁3-3.1 结构燃烧室断面呈矩形,宽度深度=89304690mm,炉膛高度27000mm。燃烧室各面墙全部采用膜式水冷壁,由光管和扁钢焊制而成。底部为水冷布风板和水冷风室;除布风板水冷壁的节距为160mm以外,其余水冷壁的节距均为80mm,水冷壁管子采用606.5,材料为20G的管子。在燃烧室四周布置有延伸墙水冷壁管屏,共有52片,前后墙各20片,两侧墙各6片,每片屏由4
45、根管子组成,屏与屏的节距前后墙为480mm、侧墙为240mm。水冷壁延伸墙管子采用606.5,材料为20G,节距72mm。屏的两端为光管,中间为膜式壁。燃烧室下部为密相区,采用向外让弯管结构,用于减轻水冷壁磨损。水冷风室由两侧水冷壁、水冷布风板和前后膜式壁组成,布风板的截面积小于上部燃烧室的截面积,使水冷布风板处具有合理的风速。燃烧室壁面开有循环物料返回口、锅炉给料口、二次风口、测温、测压孔、至旋风筒的烟气出口和人孔。除至旋风筒的烟气出口及部分测孔外,其它门、孔都集中在下部水冷壁上,由于燃烧室在正压下运行,所有门、孔应具良好密封。3-3.2 循环回路本锅炉采用循环流化床燃烧方式,在MCR负荷下
46、燃烧室出口烟气温度为854左右,而炉膛密相区燃烧温度约为822。由于沿炉膛宽度和深度的热负荷均匀,所以不需要像煤粉炉那样划分多个水循环回路,而是炉膛水冷壁设计为三个循环回路(相对于锅筒),延伸墙水冷壁设计为两个循环回路,也能保证水循环安全可靠。两侧水冷壁各有独立的下集箱和上集箱,水经集中下降管和分配管进入下集箱,然后经侧水冷壁至上集箱,再由汽水引出管将汽水混合物引至锅筒。前、后水冷壁公用上下集箱,水经集中下降管和分配管进入下集箱,然后分两路经前后水冷壁至上集箱,再由汽水引出管将汽水混合物引至锅筒。延伸墙水冷壁设有独立的下集箱和上集箱,水经集中下降管和分配管进入下集箱,然后经水冷壁至上集箱,再由
47、汽水引出管将汽水混合物引至锅筒。3-3.3 水冷壁固定水冷壁及其附着在水冷壁上的零部件及耐磨耐火材料的全部重量都通过刚性吊杆装置悬吊在顶板上,前墙有8根吊杆,后墙有8根,两侧墙各有5根吊杆,安装时应调整螺母,使每根吊杆均匀承载。为了减轻水冷壁振动以及防止燃烧室因爆燃等原因而损坏水冷壁,在水冷壁外侧四周,沿燃烧室高度方向装有多层刚性梁,设有导向限位装置。3-4 下降管3-4.1 结构本锅炉下降管采用集中与分散相结合的方式,由锅筒下部引出4根下降管,其中2根32530mm延伸墙集中下降管位于锅筒两端,2根45735mm炉膛集中下降管位于锅筒两侧靠近中间位置。2根32530mm延伸墙集中下降管,用1
48、2根15916mm分散下降管,与延伸墙水冷壁下集箱连接。2根45735mm炉膛集中下降管, 用24根15916mm分散下降管,与炉膛水冷壁下集箱连接。3-4.2 下降管固定下降管重量主要由锅筒,水冷壁和锅炉钢结构分担,四根集中下降管上各有2只耳板、2只吊架、水冷壁下部分散下降管上有4只吊架装置,支吊在前水冷壁下集箱上,延伸墙分散下降管有2只吊架装置支吊在刚性平台上。集中下降管上设有两层导向装置。3-5 汽水引出管3-5.1 结构炉膛水冷壁上集箱至锅筒汽水引出管两侧墙各有4根、前后墙上集箱有16根,共计24根。延伸墙水冷壁上集箱至锅筒汽水引出管两侧各有2根、前后墙上集箱有6根,共计12根。汽水引
49、出管均为15916mm管子。3-5.2 汽水引出管固定部分较长的汽水引出管用钢性吊杆,吊挂在锅炉顶板上。3-6 水冷布风板水冷布风板位于炉膛底部,由水平的膜式管屏和风帽组成。布风板的管子直径6010mm,节距160mm,材料为15CrMoG。耐热铸钢制成的钟罩式风帽按一定规律安装在水冷管屏鳍片上。2个排渣口布置在布风板上,布风板上所敷的耐火材料表面由前后向中间倾斜。3-7 过热器系统及汽温调节过热器系统由包墙过热器、低温过热器(SH1)、低温屏式过热器(SH2)、高温屏式过热器(SH3)和高温过热器(SH4)组成,低温过热器(SH1) 与低温屏式过热器(SH2)、低温屏式过热器(SH2)与高温
50、屏式过热器(SH3)、高温屏式过热器(SH3)与高温过热器(SH4)之间管道上,分别布置有一、二、三级喷水减温器。3-7.1 过热蒸汽流程饱和蒸汽自锅筒顶部由6根连接管引入第1烟道前包墙上集箱,分两路分别进入前包墙管连接管和顶包墙管,再分别进入前包墙和中间包墙,经过前包墙的蒸汽由前包墙下集箱进入两侧下集箱,经侧包墙至侧包墙上集箱;而经过中间包墙的蒸汽由中间包墙下集箱通过连接管进入后包墙下集箱,经第2烟道的后包墙,和侧包墙上集箱一起汇入低温过热器(SH1)入口集箱,蒸汽在低温过热器中下行,进入低温过热器(SH1)出口集箱,再自集箱两端引出,经连接管流经级喷水减温器后,引向低温屏式过热器入口集箱(
51、SH2),蒸汽在屏中被加热后进入低温屏式过热器出口集箱,再自集箱两端引出,经连接管流经级喷水减温器减温后,进入到高温屏式过热器(SH3)入口集箱,蒸汽在高温过热器中先上行进入中间集箱,而后进入高温屏式过热器(SH3)出口集箱,再自集箱两端引出,经连接管流经喷水减温器减温后,进入到高温过热器(SH4)入口集箱,蒸汽在高温过热器中下行,进入高温过热器出口集箱,然后用6根连接管引入到锅炉集汽集箱。集汽集箱右端与主汽管道相连接。3-7.2 包墙过热器3-7.2.1 结构尾部第1和第2烟道为汽冷包墙,由膜式壁构成。2个烟道公用1个中间隔墙。烟道断面呈矩形,烟道宽度为7300mm,第1烟道深度为2300m
52、m,第2烟道深度为2800mm。包墙各面墙全部采用膜式壁,由光管和扁钢焊制而成。前、中、后墙、两侧包墙节距均为100mm,前顶墙节距为90mm,包墙管子均为386,材料为20G,扁钢材料为15CrMo。尾部第1烟道包墙过热器顶部全部布置浇注耐磨耐火材料,两侧墙和前墙从顶部以下9.6m区域布置耐磨耐火浇注料;后墙出口烟道处布置耐磨耐火浇注料。烟道下部设计落灰斗,用于清除底部积灰。3-7.2.2 包墙的固定同炉膛水冷壁一样,包墙过热器及其附着在包墙上的零部件及耐磨耐火材料的全部重量都通过刚性吊杆装置悬吊在构架或顶板上。沿包墙高度方向装有多层刚性梁,并设有导向限位装置。3-7.3 低温过热器(SH1
53、)低温过热器布置在尾部第2烟道上部,逆流顺列水平布置,共有3个管组,蛇形管横向节距为200mm,横向排数36排,管子直径426mm,上一组采用20G材料,下两组采用15CrMoG。3-7.4 低温屏式过热器(SH2)低温屏式过热器布置在尾部第1烟道中,垂直布置,共16片屏,屏间节距450mm。低温屏式过热热器上部烟气入口处浇注耐磨耐火材料,以防止磨损。每片屏有管子5根,采用w形布置方式,管间节距55mm,管子直径426mm,材料为12Cr1MoVG,管屏为膜式壁。3-7.5 高温屏式过热器(SH3)高温屏式过热器共八片,其中分下降段4片和上升段4片,布置在炉膛上部靠近炉膛前墙。高温屏式过热器为
54、膜式结构,由428的TP347H管子与扁钢焊接而成。在屏式过热器下部水平段、倾斜段及一部分垂直段设置有耐磨材料,以防止炉内灰粒子对屏过受热面的磨损、冲蚀。屏式过热器下部穿墙处通过密封罩壳固定在前墙水冷壁上,整个屏式过热器除随前水冷壁向下膨胀外,还有部分向上膨胀,通过弹簧吊架悬吊在大板梁之上。3-7.6 高温过热器(SH4)高温过热器布置在尾部第2烟道下部,逆流顺列水平布置,共有2个管组,蛇形管横向节距为200mm,横向排数36排,冷段管子直径427mm,热段管子直径426,冷段材料为12Cr1MoVG、热段材料为TP347H。 3-7.7 汽温调节在锅炉定压运行时,保证在70%B-ECR至B-
55、MCR负荷内过热蒸汽温度能达到额定值,在滑压运行时,保证在50%B-ECR至B-MCR负荷内过热蒸汽温度能达到额定值,允许偏差5。蒸汽温度的调节采用三级喷水减温器,布置在连接管道上。喷水水源为锅炉给水,减温器采用笛形管式。三级喷水减温器中,第一级作为备用喷水用,第二、三级作为汽温调节用。3-7.8 固定装置 低温过热器、高温过热器蛇形管通过固定装置固定在尾部烟道的中间隔墙及后墙上,随包墙吊到构架顶板上。低温及高温屏式过热器管道吊挂在锅炉钢梁上。3-8 省煤器本锅炉采用双H型鳍片式省煤器,布置在尾部烟道内,逆流、水平、顺列布置,省煤器分成2个管组。管子规格425mm,材料20G,蛇形管为单绕,横
56、向节距为100mm,横向排数为66排。锅炉给水先经过水冷返料器,再由省煤器的入口集箱两端引入,经省煤器受热面逆流而上,依次进入出口集箱,经过2根13313mm的引出管再到省煤器引出管集箱,最后通过8根767.5mm连接管引至锅筒。 省煤器每个管组通过吊板吊挂在中间集箱上,中间集箱再由20根6010mm的引出管吊起,并通过吊杆吊挂在锅炉钢构架上。3-9 空气预热器锅炉一次风、二次风均经过空气预热器。根据生物燃料特性,采用无机传热介质热管式空气预热器,以保证锅炉BMCR管子壁温大于110,避免低温腐蚀。空气预热器卧式、逆流、顺列布置、支撑在锅炉钢构架上。空气预热器整体采购。3-10 物料循环系统物
57、料循环系统由旋风分离器、返料装置、分离器出口烟道组成。锅炉炉膛后方布置有两个旋风分离器,由进口烟道将炉膛的后墙烟气出口与旋风分离器连接,并形成了气密的烟气通道,使烟气进入两个旋风分离器进行离心分离,将气固两相流中的大部分固体粒子分离下来,通过立管进入返料装置,继而送回燃烧室,分离后的较清洁的烟气经中心筒,流入出口烟道,最后进入尾部烟道对流受热面。旋风分离器由进口烟道、筒体、锥体和中心筒组成。除中心筒外,所有组件均由=10mm碳钢钢板卷制而成,内敷保温、耐火防磨材料。旋风筒为蜗壳形,中心筒为锥型,由=12mm,1Cr20Ni14Si2钢板卷制而成。每个旋风分离器的重量通过焊在旋风筒外壳上的4个支座,支撑在钢梁上,并垫有聚四氟乙烯聚合板可沿径向自由膨胀。旋风分离器与燃烧室之间,装有耐高温的膨胀节,以补偿其胀差。每个高温绝热分离器下端装有一只返料装置,用以回路密封并将分离器分离下来的固体物料,返回燃烧室,继续参与循环与燃烧。在返料装置的底部装有布风板和风箱,来自高压风机的风通过风箱和布风板上的风帽来流化、输送物料。本
- 温馨提示:
1: 本站所有资源如无特殊说明,都需要本地电脑安装OFFICE2007和PDF阅读器。图纸软件为CAD,CAXA,PROE,UG,SolidWorks等.压缩文件请下载最新的WinRAR软件解压。
2: 本站的文档不包含任何第三方提供的附件图纸等,如果需要附件,请联系上传者。文件的所有权益归上传用户所有。
3.本站RAR压缩包中若带图纸,网页内容里面会有图纸预览,若没有图纸预览就没有图纸。
4. 未经权益所有人同意不得将文件中的内容挪作商业或盈利用途。
5. 装配图网仅提供信息存储空间,仅对用户上传内容的表现方式做保护处理,对用户上传分享的文档内容本身不做任何修改或编辑,并不能对任何下载内容负责。
6. 下载文件中如有侵权或不适当内容,请与我们联系,我们立即纠正。
7. 本站不保证下载资源的准确性、安全性和完整性, 同时也不承担用户因使用这些下载资源对自己和他人造成任何形式的伤害或损失。