机械工艺自考题
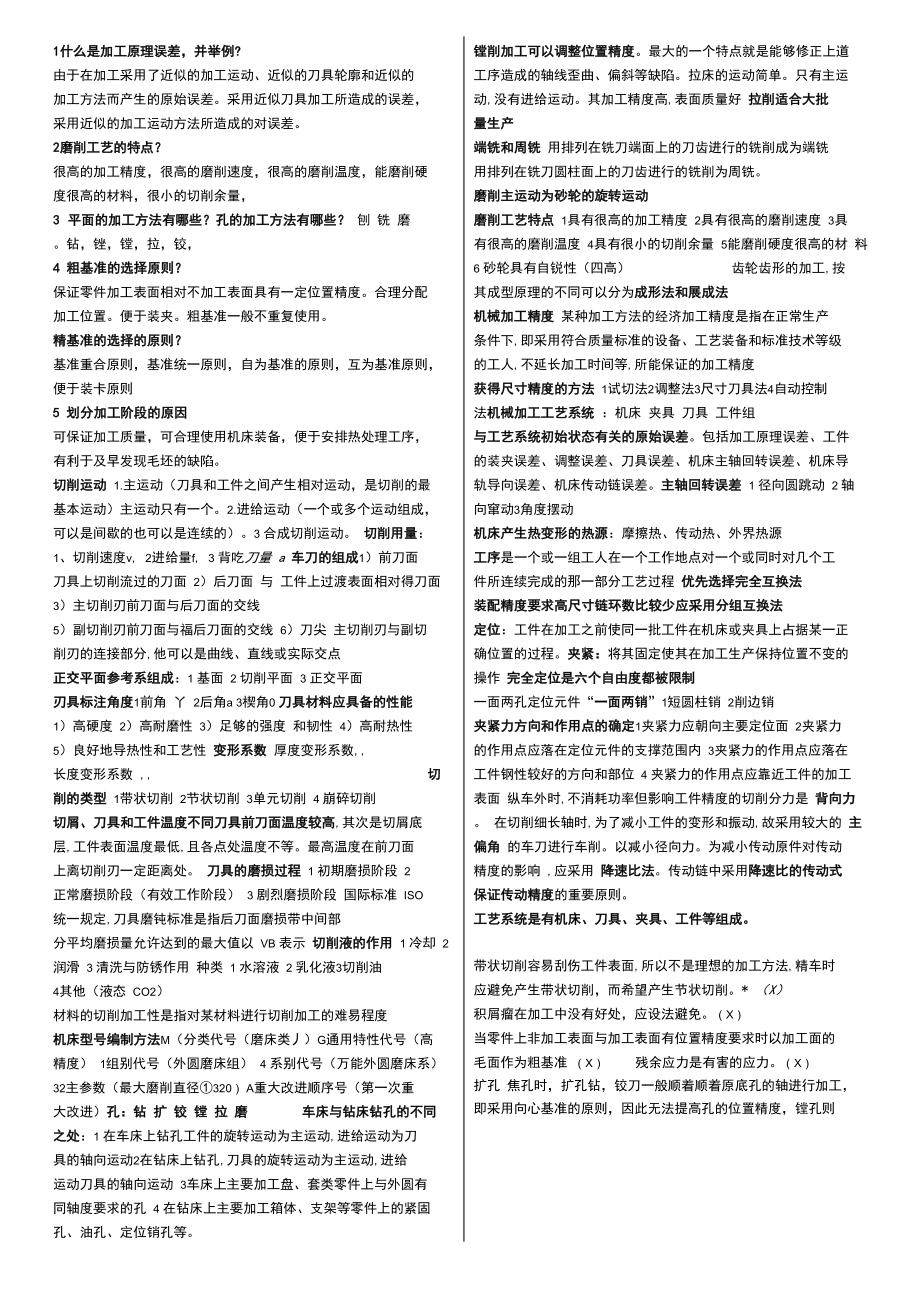

《机械工艺自考题》由会员分享,可在线阅读,更多相关《机械工艺自考题(2页珍藏版)》请在装配图网上搜索。
1、1什么是加工原理误差,并举例? 由于在加工采用了近似的加工运动、近似的刀具轮廓和近似的 加工方法而产生的原始误差。采用近似刀具加工所造成的误差, 采用近似的加工运动方法所造成的对误差。2磨削工艺的特点? 很高的加工精度,很高的磨削速度,很高的磨削温度,能磨削硬 度很高的材料,很小的切削余量,3 平面的加工方法有哪些?孔的加工方法有哪些? 刨 铣 磨 。钻,锉,镗,拉,铰,4 粗基准的选择原则? 保证零件加工表面相对不加工表面具有一定位置精度。合理分配 加工位置。便于装夹。粗基准一般不重复使用。精基准的选择的原则? 基准重合原则,基准统一原则,自为基准的原则,互为基准原则, 便于装卡原则5 划分
2、加工阶段的原因 可保证加工质量,可合理使用机床装备,便于安排热处理工序, 有利于及早发现毛坯的缺陷。切削运动 1.主运动(刀具和工件之间产生相对运动,是切削的最 基本运动)主运动只有一个。2.进给运动(一个或多个运动组成, 可以是间歇的也可以是连续的)。3 合成切削运动。 切削用量: 1、切削速度v, 2进给量f, 3 背吃刀量 a 车刀的组成1)前刀面 刀具上切削流过的刀面 2)后刀面 与 工件上过渡表面相对得刀面 3)主切削刃前刀面与后刀面的交线 5)副切削刃前刀面与福后刀面的交线 6)刀尖 主切削刃与副切 削刃的连接部分,他可以是曲线、直线或实际交点 正交平面参考系组成:1 基面 2 切
3、削平面 3 正交平面 刃具标注角度1前角 丫 2后角a 3楔角0 刀具材料应具备的性能 1)高硬度 2)高耐磨性 3)足够的强度 和韧性 4)高耐热性 5)良好地导热性和工艺性 变形系数 厚度变形系数, 长度变形系数 ,切削的类型 1带状切削 2节状切削 3单元切削 4 崩碎切削 切屑、刀具和工件温度不同刀具前刀面温度较高,其次是切屑底 层,工件表面温度最低,且各点处温度不等。最高温度在前刀面 上离切削刃一定距离处。 刀具的磨损过程 1 初期磨损阶段 2 正常磨损阶段(有效工作阶段) 3 剧烈磨损阶段 国际标准 ISO 统一规定,刀具磨钝标准是指后刀面磨损带中间部 分平均磨损量允许达到的最大值
4、以 VB 表示 切削液的作用 1 冷却 2 润滑 3 清洗与防锈作用 种类 1 水溶液 2 乳化液3切削油 4其他(液态 CO2) 材料的切削加工性是指对某材料进行切削加工的难易程度 机床型号编制方法M(分类代号(磨床类丿)G通用特性代号(高 精度) 1组别代号(外圆磨床组) 4 系别代号(万能外圆磨床系) 32主参数(最大磨削直径320) A重大改进顺序号(第一次重 大改进)孔:钻 扩 铰 镗 拉 磨车床与钻床钻孔的不同之处:1 在车床上钻孔工件的旋转运动为主运动,进给运动为刀 具的轴向运动2在钻床上钻孔,刀具的旋转运动为主运动,进给 运动刀具的轴向运动 3车床上主要加工盘、套类零件上与外圆
5、有 同轴度要求的孔 4 在钻床上主要加工箱体、支架等零件上的紧固 孔、油孔、定位销孔等。 镗削加工可以调整位置精度。最大的一个特点就是能够修正上道 工序造成的轴线歪曲、偏斜等缺陷。拉床的运动简单。只有主运 动,没有进给运动。其加工精度高,表面质量好 拉削适合大批 量生产端铣和周铣 用排列在铣刀端面上的刀齿进行的铣削成为端铣 用排列在铣刀圆柱面上的刀齿进行的铣削为周铣。 磨削主运动为砂轮的旋转运动磨削工艺特点 1具有很高的加工精度 2具有很高的磨削速度 3具 有很高的磨削温度 4具有很小的切削余量 5能磨削硬度很高的材 料 6 砂轮具有自锐性(四高)齿轮齿形的加工,按其成型原理的不同可以分为成形
6、法和展成法机械加工精度 某种加工方法的经济加工精度是指在正常生产 条件下,即采用符合质量标准的设备、工艺装备和标准技术等级 的工人,不延长加工时间等,所能保证的加工精度 获得尺寸精度的方法 1试切法2调整法3尺寸刀具法4自动控制 法机械加工工艺系统 :机床 夹具 刀具 工件组 与工艺系统初始状态有关的原始误差。包括加工原理误差、工件 的装夹误差、调整误差、刀具误差、机床主轴回转误差、机床导 轨导向误差、机床传动链误差。主轴回转误差 1 径向圆跳动 2 轴 向窜动3角度摆动 机床产生热变形的热源:摩擦热、传动热、外界热源 工序是一个或一组工人在一个工作地点对一个或同时对几个工 件所连续完成的那一
7、部分工艺过程 优先选择完全互换法 装配精度要求高尺寸链环数比较少应采用分组互换法 定位:工件在加工之前使同一批工件在机床或夹具上占据某一正 确位置的过程。夹紧:将其固定使其在加工生产保持位置不变的 操作 完全定位是六个自由度都被限制 一面两孔定位元件“一面两销”1短圆柱销 2削边销 夹紧力方向和作用点的确定1夹紧力应朝向主要定位面 2夹紧力 的作用点应落在定位元件的支撑范围内 3夹紧力的作用点应落在 工件钢性较好的方向和部位 4 夹紧力的作用点应靠近工件的加工 表面 纵车外时,不消耗功率但影响工件精度的切削分力是 背向力 。 在切削细长轴时,为了减小工件的变形和振动,故采用较大的 主 偏角 的
8、车刀进行车削。以减小径向力。为减小传动原件对传动 精度的影响 ,应采用 降速比法。传动链中采用降速比的传动式 保证传动精度的重要原则。工艺系统是有机床、刀具、夹具、工件等组成。带状切削容易刮伤工件表面,所以不是理想的加工方法,精车时 应避免产生带状切削,而希望产生节状切削。* (X) 积屑瘤在加工中没有好处,应设法避免。(X) 当零件上非加工表面与加工表面有位置精度要求时以加工面的 毛面作为粗基准 (X)残余应力是有害的应力。(X)扩孔 焦孔时,扩孔钻,铰刀一般顺着顺着原底孔的轴进行加工, 即采用向心基准的原则,因此无法提高孔的位置精度,镗孔则表面层的加工硬化使零件的表面层硬度提高,从而表面层
9、处的弹性和塑性变形减小,磨削减少,使零件的耐磨性提高oV 工序是组成工艺过程的基本单元。V 单件小批量生产宜选用工序集中原则。V 从集中发展方向看,今后更趋于工序集中V 判断带状切削容易刮伤工件表面,所以不是理想的加工方法,精车时 应避免产生带状切削,而希望产生节状切削。* (X) 积屑瘤在加工中没有好处,应设法避免。(X) 当零件上非加工表面与加工表面有位置精度要求时以加工面的 毛面作为粗基准 (X)残余应力是有害的应力。(X)扩孔 焦孔时,扩孔钻,铰刀一般顺着顺着原底孔的轴进行加工, 即采用向心基准的原则,因此无法提高孔的位置精度,镗孔则 使机床产生热变形的热源主要是摩擦热、传动热和外界热
10、源传入 的热量。V表面层的加工硬化使零件的表面层硬度提高,从而表面层处的弹 性和塑性变形减小,磨削减少,使零件的耐磨性提高。V 工序是组成工艺过程的基本单元。V 单件小批量生产宜选用工序集中原则。V 从集中发展方向看,今后更趋于工序集中V 纵车外圆是,不消耗功率但影响工件精度的切削分力是 背向 力。 在切削细长轴时,为了减小工件的变形和振动,故采用较大的 主偏角 的车刀进行车削。以减小径向力。为减小传动原件对传 动精度的影响 ,应采用 降速法。传动链中采用 降速比 的传动式保证传动精度的重要原则。 工艺系统是有机床、刀具、夹具、工件等组成。简答题 1什么是加工原理误差,并举例?由于在加工采用了
11、近似的加工运动、近似的刀具轮廓和近似的 加工方法而产生的原始误差。采用近似刀具加工所造成的误差, 采用近似的加工运动方法所造成的对误差。2磨削工艺的特点? 很高的加工精度,很高的磨削速度,很高的磨削温度,能磨削硬 度很高的材料,很小的切削余量,3 平面的加工方法有哪些?孔的加工方法有哪些? 刨 铣 磨 。钻,锉,镗,拉,铰, 4粗基准的选择原则?保证零件加工表面相对不加工表面具有一定位置精度。合理分配 加工位置。便于装夹。粗基准一般不重复使用。精基准的选择的原则? 基准重合原则,基准统一原则,自为基准的原则,互为基准原则, 便于装卡原则5 划分加工阶段的原因 可保证加工质量,可合理使用机床装备,便于安排热处理工序, 有利于及早发现毛坯的缺陷。
- 温馨提示:
1: 本站所有资源如无特殊说明,都需要本地电脑安装OFFICE2007和PDF阅读器。图纸软件为CAD,CAXA,PROE,UG,SolidWorks等.压缩文件请下载最新的WinRAR软件解压。
2: 本站的文档不包含任何第三方提供的附件图纸等,如果需要附件,请联系上传者。文件的所有权益归上传用户所有。
3.本站RAR压缩包中若带图纸,网页内容里面会有图纸预览,若没有图纸预览就没有图纸。
4. 未经权益所有人同意不得将文件中的内容挪作商业或盈利用途。
5. 装配图网仅提供信息存储空间,仅对用户上传内容的表现方式做保护处理,对用户上传分享的文档内容本身不做任何修改或编辑,并不能对任何下载内容负责。
6. 下载文件中如有侵权或不适当内容,请与我们联系,我们立即纠正。
7. 本站不保证下载资源的准确性、安全性和完整性, 同时也不承担用户因使用这些下载资源对自己和他人造成任何形式的伤害或损失。