毕业设计论文铣削组合机床及其工作台设计
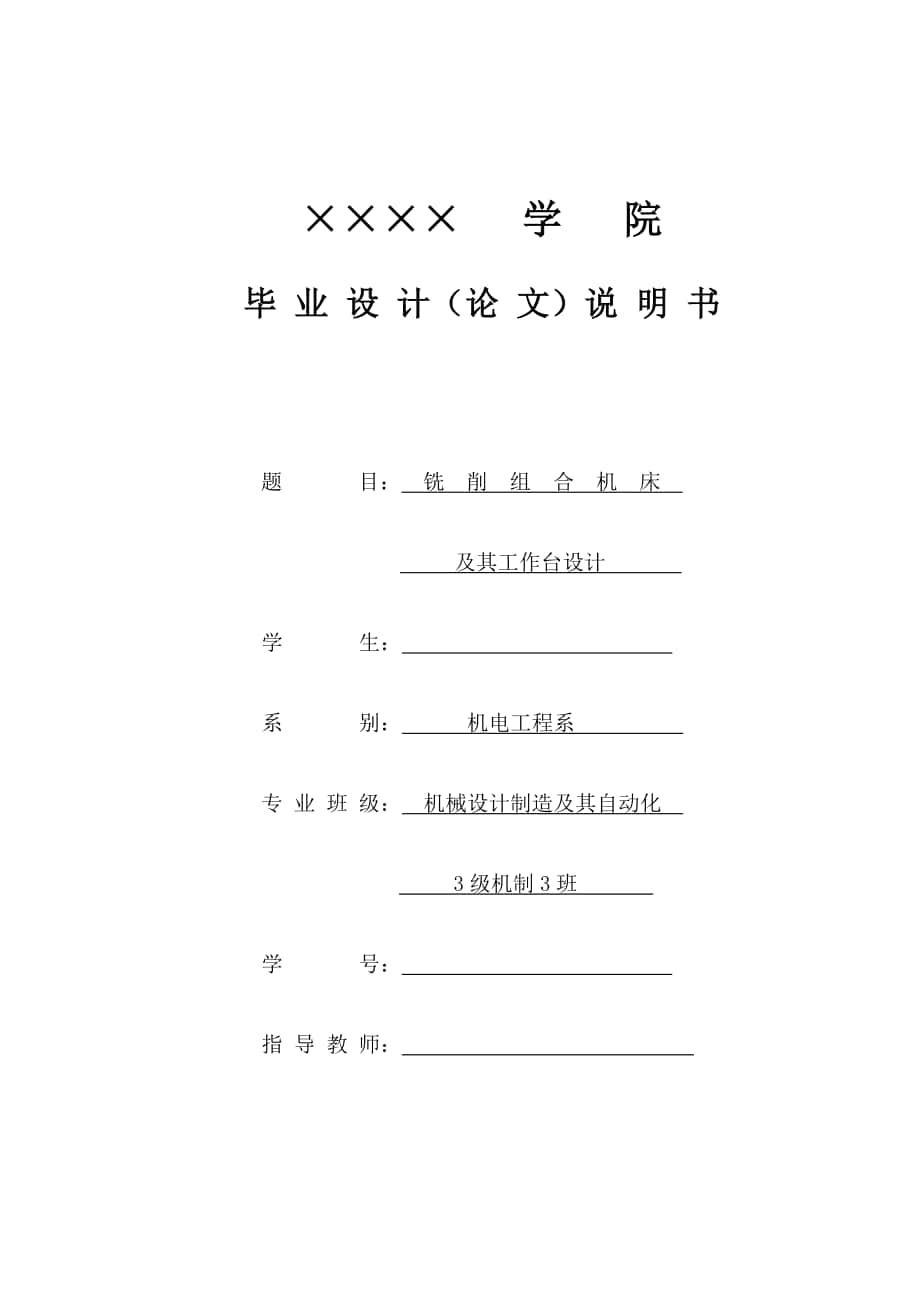


《毕业设计论文铣削组合机床及其工作台设计》由会员分享,可在线阅读,更多相关《毕业设计论文铣削组合机床及其工作台设计(42页珍藏版)》请在装配图网上搜索。
1、 学 院毕 业 设 计(论 文)说 明 书题 目: 铣 削 组 合 机 床 及其工作台设计 学 生: 系 别: 机电工程系 专 业 班 级: 机械设计制造及其自动化 3级机制3班 学 号: 指 导 教 师: 学 院毕业设计(论文)任务书设计题目: 铣削组合机床及其工作台设计 系: 机 电 专业: 机 制 班级: 033 学号: 学生: 指导教师: 专业负责人: 接 受 任 务 时 间 教 研 室 主 任 (签名)系 主 任 (签名)1毕业设计(论文)的主要内容及基本要求1绘制铣削组合机床总图1张2设计铣削组合机床工作台并绘制工作台装配图1张3绘制铣削组合机床工作台零件图2张4编写设计说明书1份
2、 2指定查阅的主要参考文献1机械设计手册2组合机床设计 沈阳工业大学等编 上海科学技术出版社 1985.93金属切削机床设计 编写组编 上海科学技术出版社 1986.43设计的原始参数1减荷阀体零件图1张2铣刀盘直径75-110,YG64进度安排设计(论文)各阶段名称起止日期1查阅和搜集设计资料,撰写开题报告3.5-3.112进行铣削组合机床总体设计并绘制草图3.12-4.13设计铣削组合机床工作台并绘制装配图、零件图4.2-4.224绘制铣削组合机床总图4.23-4.295编写设计说明书4.3-5.66检查、修改5.7-6.3摘 要组合机床是根据具体情况的需要,对机床进行合理的设计,使其满足
3、加工要求。它具有自动化程度较高,加工质量稳定,工序高度集中等特点。目前,组合机床的研制正向高效、高精度、高自动化和柔性化方向发展。本次设计是完成对铣削组合机床及其工作台的设计,使其满足对减荷阀体的前后两端面的切削加工。首先针对所要加工的零件,对机床进行总体方案设计,确定机床的总体布局。然后对工作台进行设计。在设计工作台时,根据工作台移动速度,确定丝杠转速,并确定进给变速箱传动方案,最后设计工作台结构。关键词:组合机床,工作台,丝杠,进给变速箱ABSTRACTCombination machine is based on the specific needs of the machine for
4、 a reasonable design to meet the processing requirements. It has a fairly high degree of automation, processing, stable quality, highly centralized process characteristics. Currently, the portfolio machine being developed efficient, high-precision, high automation and flexible direction.This design
5、is completed right combination milling machine and its stage design, make it responsive to the valve body by the Security Council ends before and after the cutting. First in response to the processing of parts for machine tools for the overall program design, overall layout of the machine. Then the
6、design stage. In the design stage, according to the speed mobile workstations, set screw speed, and to determine the feed Gearbox Drive program final design stage structure. Keywords: Combination machine, workstations, screw, feed Gearbox 目 录中文摘要英文摘要前言1第1章 组合机床概述21.1 组合机床及其特点21.2 组合机床的工艺范围及加工精度21.3
7、组合机床的发展趋向3第2章 机床总体设计42.1 影响组合机床方案制订的主要因素42.2机床总体方案设计的依据42.2.1 工件42.2.2 刀具52.3工艺分析52.3.1工艺方法的确定52.3.2机床运动的确定62.4确定切削用量72.4.1确定工件余量72.4.2选择切削用量72.5机床主要技术参数的确定72.5.1主轴转速的确定72.5.2主运动驱动电动机功率的确定82.5.3进给驱动电动机功率的确定9第3章 工作台设计(进给传动设计)103.1铣刀切削力的分解103.2工作台的设计113.2.1工作台T形槽的选用113.2.2导轨的设计113.3滑动丝杠螺母机构143.3.1移动部件
8、重力计算153.3.2导轨所受力的分解与计算153.3.3进给牵引力的计算153.3.4传动丝杠直径设计163.3.5传动丝杠结构设计173.3.6传动丝杠的支承183.3.7传动丝杠螺母的结构193.4支承件的设计203.4.1支承件的功用及基本要求203.4.2支承件的结构分析213.5进给传动设计223.5.1确定丝杠转速233.5.2传动变速箱设计233.6标准件的选择27总结30参考文献31致谢32前 言金属切削机床(简称机床)是用刀具或磨具对金属工件进行切削加工的机器。在一般机械制造厂中,机床约占机器设备总台数的5070%。现代化工业生产的特征主要表现在高生产率和先进的技术经济指标
9、两方面,而这些则首先取决于机械制造工业提高的装备的技术水平。机床工业是机器制造业的重要部门,担负着为农业、工业、科学技术和国防现代化提供技术装备的任务,在整个国民经济中占有重要地位。一个国家机床工业的技术水平、机床的拥有量和现代化程度,是衡量这个国家工业生产能力和技术水平的重要标志之一。从事机床设计的人员,应妥善处理既要赶超国际水平,又要符合我国国情;既要技术上先进,又要经济效果好;既要好造,又要好用、好修。要努力实践,大胆创新,更多地设计和制造出生产率高、静、动态性能好、结构简单、成本低、使用方便、节省能源、造型美观的具有我国风格的机床。设计机床的步骤归纳起来大体上可以分为调查研究、拟定方案
10、、结构设计、零件图设计和试制鉴定五个阶段。1调查研究 调查研究的内容包括调查使用单位、制造单位,查阅、收集国内相关文献、技术资料等。2拟定总体方案 拟定方案的内容包括:设计本机床理由或必要性;机床用途和使用范围,国内外同类机床的比较,本机床的技术性能、轮廓尺寸和估计重量;所采用的工艺方案,总体布局,主要结构,控制方案;机床的优缺点和经济分析。3结构设计与计算 主要是根据拟定的方案,绘制机床各部件装配图,同时画出机床传动系统图、液压系统图和电器系统图,并进行必要的计算。4零件图设计与编写技术文件 绘制全部专用件的工作图和通用件的补充加工图,并进行必要的计算。装配图和零件图应经工艺审查和标准化审查
11、,有时还须再按已设计完的零件重新绘制部件装配图和机床外观图,最后编写技术文件。5试制鉴定 工作图设计完成后,如果是通用机床,须先试制一台样机,进行试验鉴定;如果是专用机床,由于它的生产数量一般很少,有时仅制造一台,因此没有单独的样机试制阶段。由于本人能力所限,设计尚有许多不足之处,恳请各位老师给予指导。第一章 组合机床概述1.1 组合机床及其特点组合机床是由大量的通用部件和少量专用部件组成的工序集中的高效率专用机床。它能够对一种(或几种)零件进行多刀、多轴、多面、多工位加工。在组合机床上可以完成钻孔、扩孔、铰孔、镗孔、攻丝、车削、铣削、磨削等工序,生产效率高,加工质量稳定。组合机床与通用机床、
12、其他专用机床比较,具有以下特点:(1)组合机床上的通用部件和标准零件约占全部机床零、部件总量的70%80%,因此设计和制造的周期短,投资少,经济效果好。(2)由于组合机床采用多刀加工,并且自动化程度高,因而比通用机床生产效率高,产品质量稳定,劳动强度低。(3)组合机床的通用部件是经过周密设计和长期生产实践考验的,又有专门工厂成批制造,因此性能稳定、工作可靠,使用和维修方便。(4)在组合机床上加工零件时,由于采用专用夹具、刀具和导向装置等,加工质量靠工艺装备保证,对操作工人的技术水平要求不高。(5)当被加工产品改变时,若采用的是组合机床,其大多数通用部件可以重复利用,不必另行设计和制造,节约了投
13、资,有利于企业产品的更新换代。(6)组合机床易于组成组合机床自动线,以适应大规模的生产需要。组合机床常用的通用部件有:床身(侧底座)、底座(包括中间底座和立柱底座)、立柱、动力箱、动力滑台、各种工艺切削头等。对于一些按顺序加工的多工位组合机床,还具有移动工作台或回转工作台。组合机床的通用部件,绝大多数已有国家标准,并按标准所规定的名义尺寸、主参数、互换尺寸等定型,各种通用部件之间有配套关系。这样,用户可根据被加工零件的尺寸、形状和技术要求等,选用通用部件,组成不同型式的组合机床,以满足生产的需要。1.2 组合机床的工艺范围及加工精度组合机床可完成的工艺有铣平面、刮平面、车端面、钻孔、扩孔、镗孔
14、、铰孔、攻丝、倒角、锪窝、钻深孔、切槽等。随着综合自动化技术的发展,组合机床可完成的工艺范围也在不断扩大,除了上述工艺外,还可完成车外圆、车锥面、车弧面、切削内外螺纹、滚压孔、拉削内外圆柱面和平面、磨削、抛光、珩磨,甚至还可进行冲压、焊接、热处理、装配、自动测量和检查等。组合机床中平面加工的加工精度简述如下:在组合机床及其自动线上常用铣削、刮削、车削(端面)和拉削等方法加工平面。铣削平面时,一般采用铣削头、滑台和滑座等通用部件,根据被加工工件的工艺要求组成单面、双面以及立式、回转台式等多种型式的组合铣床。当加工大型的箱体类工件时,一般采用铣削头固定、工件安装在工作台上移动的布局型式。这样的机床
15、结构简单,刚性较好,加工精度较高。在加工中小型工件时,通常将铣削头组成鼓轮式组合机床或立式连续回转台式组合机床,这类机床生产效率高,加工精度较低。在组合机床上加工平面的平直度可以达到在1000毫米长度内偏差0.020.05毫米,表面粗糙度3.2微米。对定位基面的平行度可以保证在0.05毫米以内,到定位基面的距离(一般在500毫米以内)尺寸公差可以保证在0.05毫米以内。1.3 组合机床的发展趋向一、提高通用部件的水平二、发展适应中、小批生产的组合机床三、采用新刀具四、开发自动检测技术五、扩大工艺范围第二章 机床总体设计2.1 影响组合机床方案制订的主要因素1、 被加工零件的加工精度和加工工序被
16、加工零件需要在组合机床上完成的加工工序及应保证的加工精度,是制定机床方案的主要依据。例如精度为H7的孔加工工序,不仅工步数多(通常48个),而且对于不同尺寸的孔径,也须采取不同的工艺方法(镗或铰)。当孔与孔之间有较高位置精度要求(如0.05毫米)时,安排工艺应考虑在一个安装工位上对所有孔同时进行最终精加工。如果同一轴线上有几个孔同轴度要求较高时(0.05毫米),其最后精加工应从一面进行。2、 被加工零件特点这主要指零件的材料、硬度、加工部位的结构形状、工件刚性、定位基准面的特点等。它们对机床工艺方案制定有着重要的影响。同样精度的孔,因材料、硬度的不同,其工艺方案也不同,如钢件一般比铸铁的加工工
17、步数多。加工薄壁易振的工件,安排工序时,必须考虑防止共振。加工箱体零件多层壁同轴线等直径孔,通常在一根镗杆上安装多个镗刀头进行镗削。3、 零件的生产批量零件的生产批量是决定采用单工位、多工位或自动线,还是按中小批生产的特点设计组合机床的重要因素。有时从工件外形及轮廓尺寸看,本来可以采取单工位固定式夹具的机床配置型式,但由生产批量较大,就不得不采取多工位的机床配置方案,以使装卸工件时间与机动时间重合。4、 机床的使用条件(1) 车间布置情况(2) 工艺间的联系(3) 使用厂的技术能力和自然条件2.2 机床总体方案设计的依据2.2.1 工件工件是机床总体方案设计的重要依据,设计者必须明确工件的特点
18、和加工要求。本次毕业设计要求设计一台组合机床,用于加工VF-6/7型空压机减荷体(如图21)的两侧面,工件材料为HT200硬度为190210HB。加工部位的加工要求如下:(1)被加工表面的粗糙度均为R10;(2)被加工表面的相互位置精度为:图21 减荷阀体简图平面1与2之间的距离为225mm;平面12与95中心线的垂直度要求为0.03mm。2.2.2刀具硬质合金端铣刀,牌号为YG6,铣刀盘直径为75110,刀具齿数Z=4。2.3 工艺分析2.3.1 工艺方法的确定机床的工艺方法是多种多样的,按工种可分为车、铣、刨、钻、镗、磨、研磨、电加工、振动加工、激光加工等;每一种还可再分,如车加工有车外圆
19、、车端面、车槽、车球面等之分;按加工精度各表面粗糙度可分为粗加工、半精加工、光整加工等;按工序集中程度可分为单刀、多刀、单工件、多工件、单工位、多工位等;按作业形式可分平行作业、顺序作业、平行-顺序作业等。工艺方法对机床的结构和性能的影响很大,工艺方法的改变常导致机床的运动、传动、布局、结构、性能以及经济效果等方面的一系列变化。加工平面的方法有很多,比如说车削,铣削,刨削。对于VF-6/7型空压机减荷阀体,用车床进行车削加工时,由于减荷阀体外形复杂,且为壳类零件,不宜装夹在车床主轴上进行加工,装夹稳定性也不高;用刨床进行刨削加工时,机床需要两个运动,机床和刀具结构简单,装夹在工件台上快速,稳固
20、,但生产率低,加工精度也达不到设计要求;用端铣刀进行铣削加工时,生产率不仅提高了,也能满足设计所要求的加工精度,且装夹快速,方便。与普通机床相比,组合机床具有生产率高,加工精度稳定,研制周期短,便于设计、制造和使用维护、成本低、自动化程度高、劳动强度低,配置灵活等特点,因此,用组合机床进行加工更合理。根据减荷阀体的加工要求,采用一台组合铣床进行加工,如图22所示: 图22 加工减荷阀体的工艺方法方案1.机座 2.动力滑台 3.工件 4.端铣刀 5.电动机 6.变速箱 7.主轴箱减荷阀体安装在工作台上,铣削动力头带动铣刀作旋转主运动,工作台作纵向进给运动,完成对工件的切削加工。此方案的优点是各部
21、件均是针对减荷阀体设计的,因此,结构紧凑,刚性好,生产率高,加工质量稳定。2.3.2 机床运动的确定确定机床运动,指确定机床运动的数目,运动类型以及运动的执行件。本次毕业设计的组合机床的工艺方法是,用一把端铣刀直接进行加工。相应的表面成形运动为:单主轴的回转运动,工作台纵向进给运动;辅助运动为:主轴轴向调整运动。2.4 确定切削用量2.4.1 确定工件余量VF-6/7型空压机减荷阀体,零件材料为HT200,硬度190210HB,生产类型大批量,铸造毛坯。查机械制造工艺设计简明手册表2.22.5,取加工余量为2.5mm(此为双边加工)。2.4.2 选择切削用量由于被加工的铣削宽度为175mm,需
22、进行二次走刀,故一次走刀为90mm(宽度),二次走刀为175-90=85mm,即:=90mm。根据组合机床设计简明手册第132133页,选择铣削切削用量。铣削用量的选择与要求的加工表面粗糙度值及其生产率有关系。当铣削表面粗糙度数值要求较低时,铣削速度应选高一些,每一齿走刀量应小一些。若生产率要求不高,可以取很小的每齿走刀量,一次铣削45mm的余量达到R=1.6m的表面粗糙度,这时每齿的进给量一般为0.020.03mm。根据本次设计所加工的零件要求,其表面粗糙度数值较高,加工材料为铸铁,查表6-16得:0.20.4mm/z,5080mm, 取mm/z。2.5 机床主要技术参数的确定机床主要技术参
23、数包括主参数和基本参数,基本参数又包括尺寸参数,运动参数,动力参数。2.5.1 主轴转速的确定2.5.1.1 主轴最高,最低转速按照典型工序的切削速度和刀具(或工件)直径、计算主轴最高转速、最低转速。计算公式如下: , 式中:、主轴最高、最低转速(r/min)、最高、最低切削速度(m/min)、最大、最小计算直径(mm)根据机械制造工艺金属切削机床设计指导第6970页,可查出以下数据: 查表2.2-3 取最大,最小切削速度:m/min, 取m/min20m/min, 取m/min铣床的、可取使用的刀具最大、最小直径即:mm, mm则主轴最高、最低转速为r/min 取标准数列值:r/minr/m
24、in取标准数列值:r/min2.5.1.2 主轴转速的合理排列最高、最低转速确定后,还需确定中间转速,选择公比,转速级数Z,则转速数列为:r/min, , , 查标准数列,取公比(12)转速范围: 转速级数: 取由于本次设计的要求,主轴转速级数只需设计四级就能满足要求,取。即:,, , (r/min)2.5.2主运动驱动电动机功率的确定由前面已知,本次设计的组合机床的最高转速为=315r/min,则这时的切削速度为: =108.8m/min200m/min由此可见,切削速度满足要求。计算铣削工件时的切削力 式中:铣削宽度,=90mm铣削深度,由于是一次铣削就能达到设计尺寸,则铣削深度为工件加工
25、余量,即=2.5mm每齿进给量,=0.2mm/r转速级速,=4铣刀直径,取=110mm则铣削力的大小为:N根据机械制造工艺金属机床设计指导第72页,可得切削功率公式为:KW估算电动机功率式中:主转动系统的机械效率,回转运动的机床=0.70.85。选择电动机:Y112-4 =4 KW =1440 r/min =43 kg2.5.3 进给驱动电动机功率的确定进给驱动电动机功率取决于进给的有效功率和传动件的机械效率,即: 式中:进给驱动电动机功率(KW) 进给抗力(N) 进给速度(m/min)进给传动系统的总机械效率(一般取0.150.2)粗略计算时,可根据进给传动与主传动所需功率之比值来估算进给驱
26、动电机功率。对于铣床: KW选择电动机: Y90S-4 =1.1 KW =1440 r/min =22 kg第三章 工作台设计(进给传动设计)3.1 铣刀切削力的分解查机械制造工艺设计手册第8485页,可得各类铣刀切削力的分解及其比例关系:图31 铣削切削力的分解端铣不对称顺铣FH=(0.150.30)FZFV=(0.901.00)FZFO=(0.500.55)FZ由前一章计算可知,FZ=1213.1N则 FH=0.30FZ=0.301213.1=364NFV=1.00FZ=1213.1NFO=0.55FZ=0.551213.1=667N3.2 工作台的设计根据本次设计的目的和要求,所设计的组
27、合机床的工作台为单独驱动的工作台,工作台下面为导轨面,直接与床身导轨相接触,起到定位和承受重力的作用。工作台材料:HT200。3.2.1 工作台T形槽的选用查简明机械设计手册表3.15得:图32 T形槽尺寸选基本尺寸A=18mm,则其余尺寸为:Bmax=32,Bmin=30,Cmax=14,Cmin=12,Hmax=36,Hmin=30,E=1.6,F=1,G=1.6图33 T形槽间距尺寸查表3.16得,T形槽间距尺寸:P=803.2.2 导轨的设计导轨主要用来支承和引导运动部件,沿着一定的轨迹运动。机床上两相对运动部件的配合面组成一对导轨副,其中,不动的配合面称为固定导轨,运动的配合面称为运
28、动导轨。在运动部件(工作台)与固定不动的部件(床身)之间只许有一个自由度。为此,导轨副必须限制运动部件的其它五个自由度。导轨按运动轨迹可分为直线运动导轨和圆周运动导轨。3.2.2.1 直线滑动导轨的截面形状直线滑动导轨一般由若干个平面组成,从制造、装配和检验来说,平面的数量应尽可能少,常用的有矩形、三角形、燕尾形及圆形截面。截面形状如图34:图34 直线滑动导轨的截面形状矩形导轨(图34a):该导轨制造简便,刚度和承载能力大,水平方向和垂直方向上的位移互不影响,因此安装、调整都比较方便。矩形导轨中起导向作用的导轨面磨损后不能自动补偿间隙,所以需要有间隙调整装置。三角形导轨(图34b):该导轨在
29、水平布置时,在垂直载荷作用下,导轨磨损后能自动补偿,不会产生间隙,因此导向性好。此外,当两导轨面上受力不对称、相差较大时,为使导轨面上压力分布均匀,可采用不对称导轨。三角形导轨的顶角一般取90度;重型机床上承受载荷较大,为增大承载面积,可取110120度,但导向精度变差;在精密机床上,采用小于90度的顶角以提高导向精度。燕尾形导轨(图34c):该导轨磨损后不能自动补偿间隙,需用镶条调整。两燕尾面起压板面作用,可承受倾覆力矩,用一根镶条就可调整水平、垂直方向的间隙。导轨制造、检验和修理较复杂,摩擦阻力大。当承受垂直作用力时,它以支承平面为主要工作面,它的刚度与矩形导轨相近;当承受倾覆力矩时,斜面
30、为主要工作面,则刚度较低。一般用于要求高度小的多层移动部件。燕尾形导轨可以看成是三角形导轨的变型,两个导轨面间的夹角为55度。圆柱形导轨(图34d):该导轨制造简单,内孔可珩磨,外圆经过磨削可达到精密配合,但磨损后调整间隙困难。为防止转动,可在圆柱表面上开键槽或加工出平面,但不能承受大的扭矩,主要用于受轴向载荷的场合,如拉床、珩磨机及机械手等。3.2.2.2直线运动导轨的组合就相对运动部件而言,如果导轨面窄,便不能限制绕X轴方向转动,所以在机床上一般都采用两条导轨来承受载荷和导向。在重型机床上,根据机床受载情况,可用三至四条导轨。导轨有下述的组合型式(如图35):图35 导轨的组合型式双三角形
31、组合(图35a):这种导轨同时起支承、导向作用。磨损后相对位置不变,能自行补偿垂直方向及水平方向的磨损。导向精度高,但要求四个表面的刮削或磨削后同时接触,工艺性较差,床身与运动部件热变形不一样时,难保证四个面同时接触。这种导轨用于龙门刨床与高精度车床。双矩形组合(图35b):这种导轨主要承受与主支承面相垂直的作用力,承载能力大,但导向性差。双矩形组合导轨制造、调整简单,闭合导轨有压板面,用压板调整间隙,导向面用镶条调整间隙,用于普通精度机床,如升降台铣床、龙门铣床。三角形平导轨组合(图35c):这种导轨通常用于磨床、精密镗床和龙门刨床上。由于磨削力主要是向下的压力,精镗切削力很小,工作台实际上
32、没有抬起的可能性。三角形矩形组合(图35d):这各导轨兼有导向性好、制造方便和刚度高的优点,应用最广泛。三角形导轨作主要导向面,具有双三角形的优点,但比双三角形制造方便,导向性比双矩形好。矩形导轨作主要承载面,承载能力较大。三角形导轨磨损后不能调整,对位置精度有影响。平平三角形组合:在龙门铣床机床工作台宽度大于3000毫米、龙门刨床工作台宽度大于5000毫米时,为了不使工作台中间挠度过大,可用三根导轨的组合。三角形导轨主要起导向作用,平导轨主要起承载作用,不需用镶条调整间隙。工作台用双齿条传动,使偏转力矩较小。根据本次设计的要求,并通过对直线运动导轨的组合进行比较,选择三角形矩形导轨更为合理。
33、工作台形状及其尺寸见工作台零件图。3.2.2.3.估算工作台的质量估算工作台体积V工=7432080026208003800(18183012)30308002422660025042280=18944000416000164160036000013104001176000=148720002查简明机械设计手册表115得,铸铁HT200的密度=7000/m3,则工作台的质量m1=V工=70001487200010-9104。3.3 滑动丝杠螺母机构滑动丝杠螺母是指螺纹的表面直接接触的丝杠螺母机构。滑动丝杠螺母机构的特点:(1)降速比大 丝杠导程小,当丝杠转速较高时,螺母的移动速度仍较低,因此,
34、在传动链中其他传动副降速比不大的情况下就能获得低速运动,换句话说,可以缩短传动链,有利于提高传动精度。因此,这种机构适用于中、低速进给传动。(2)运动平稳和传动精度高 适用于精密位移传动,如果与螺距校正装置和消除间隙机构配合应用,则可用于精密位移,位移精度可达0.001毫米。一般在精密丝杠车床和螺纹磨床等内联系传动中广泛应用。(3)轴向牵引力大 由于降速比大,在传递扭矩较小的情况下,可获得较大的轴向牵引力。(4)自锁性能好 一般情况下,螺旋角小于摩擦角,有自锁性能。因此,适用于垂直移动部件的传动(如铣床工作台或横梁升降),可防止部件因自重而下滑。(5)传动效率低 螺旋面之间属于滑动摩擦,摩擦损
35、失较大,其机械效率一般为0.20.4。与滚动摩擦相比,其磨损较快。(6)刚度低 丝杠为细长轴,依靠两端支承,不能像齿条那样固定在床身或工作台上,因此刚度较低。3.3.1 移动部件重力计算由上节计算可知:工作台重量为m1=104kg由减荷阀体零件图可知:减荷阀体重量为13.5kg估算传动丝杠螺母部分的重量为m2=6.5kg则移动部件的重量为m=1046.513.5=124kg即移动部件的重力G=mg=12410=1240N3.3.2 导轨所受力的分解与计算导轨所受的力可分解成以下三个力:导轨的纵向(长度方向)分力;垂直于导轨的分力;导轨的横向分力。根据减荷阀体和铣刀盘之间作用力与反作用力的关系,
36、且减荷阀体是固定在工作台上进行加工的,则减荷阀体所受的力也是工作台(导轨)所受到的力,即导轨所受分力的大小为:3.3.3.进给牵引力的计算根据机械制造装备设计表13,可得进给牵引力的公式:式中:进给牵引力(N);考虑倾覆力矩影响的系数;三角形和矩形导轨K=1.11.5;燕尾形导轨K=1.4;当量摩擦系数;在正常润滑条件下,铸铁三角形导轨副=0.170.18;铸件矩形导轨副=0.120.13;铸铁燕尾形导轨副=0.2;铸铁(或淬火)与氟塑料组成的导轨副=0.030.05。导轨的纵向(长度方向)分力(N);垂直于导轨面的分力(N);导轨的横向分力(N);移动部件的重力(N)。代入前两节所计算得到的
37、数据,得3.3.4.传动丝杠直径设计丝杠工作时,主要承受扭矩、拉力或压力。丝杠螺母传动主要失效形式是磨损,因此应通过耐磨性计算来决定丝杠的直径。根据金属切削机床设计第102页,计算方法如下:每一圈螺纹的工作面积为式中:螺纹中径;螺纹的工作高度。螺母全长上的螺纹圈数为式中:螺距;导程;螺纹头数。螺纹全长上的工作面积为如果最大牵引力为(牛),则平均单位面积压力为(帕)式中的、的单位均为毫米。对于标准梯形螺纹,代入上式可得:许用单位压力值见表31。 表31 许用单位压力 (帕)应 用 范 围丝 杠螺 母 材 料不淬硬钢铸铁不淬硬钢青铜淬硬钢青铜精密传动丝杠一般传动丝杠根据本次设计的要求,丝杠螺母材料
38、选用不淬硬钢青铜,应用范围为一般传动丝杠,则许用单位压力(帕)。螺母全长的设计:由工作台结构可知,螺母的长度为120mm。根据许用单位压力公式,可推导出传动丝杠直径按耐磨性设计公式: mm取中径mm。查简明机械设计手册表67至表69,可计算出梯形螺纹的基本参数:螺距mm,公称直径mm,外螺纹小径mm,内螺纹大径mm,内螺纹小径mm。3.3.5 传动丝杠结构设计参考自贡山川空压机厂使用的组合铣床,设计传动丝杠结构如图36:图36 传动丝杠结构图3.3.6 传动丝杠的支承滑动丝杠的径向支承一般采用滑动轴承,由于丝杠转速低、载荷小,轴承的材料常用耐磨铸铁和青铜;而在中等精度,高速重载的情况下采用滚动
39、轴承。滑动丝杠的轴向支承一般采用推力滚动轴承;在精度要求较高的精密机床中采用推力滑动轴承;目前在数控机床中,常采用接触角为60的向心推力球轴承,既能承受较大的轴向力,又可减少轴承数量。由于本次设计的组合铣床精度要求较高,所以滑动丝杠的支承采用滚动轴承。丝杠支承的布置,一般采用两端支承,对于要求不高的短丝杠(如普通车床上的刀架丝杠),常采用一端支承,而利用螺母起第二个支承作用。丝杠的一对推力轴承应尽可能地布置在丝杠的同一端,而丝杠的另一端只有径向支承,并在结构上能让丝杠自由伸缩,以免受热伸长而顶弯。此外,推力轴承的布置,应尽量使丝杠在大部分工作时间内受接力。对于大型机床和精密机床的水平丝杠,为了
40、防止丝杠自重引起的挠曲,应在中间加辅助支承。在本次设计中,丝杠的支承采用一端固定,一端游动支承的方式。固定端采用一对角接触球轴承进行固定,另一端采用一对深沟球轴承游动支承。丝杠的支承方式如图37:图37 传动丝杠的支承方式3.3.7 传动丝杠螺母的结构螺母结构形式很多,机床上常用的有单螺母、双螺母、半螺母和开合螺母等。(1)单螺母 在普通车床小滑板的丝杠螺母机构中,常采用浮动安装方式,螺母的圆柱头装入移动部件孔内,螺母能沿垂直方向浮动,并在垂直方向自动地对正丝杠中心线,但刚度较低。另一种方式是将单螺母直接固定在移动部件上,刚度较高,但装配调整麻烦。这种结构适用于要求不高或不太重要的进给传动中。
41、(2)双螺母 主要用来消除丝杠和螺母之间的间隙,以保证机床正常工作和加工质量。(3)半螺母 半螺母结构的优点是结构简单,装配方便,丝杠与螺母的间隙可借垫片调整。缺点是丝杠受单方向径向力,引起弯曲变形。与全螺母相比较,接触刚度低,所以,半螺母只适用于受力较小的地方。(4)开合螺母 主要用于普通车床溜板箱中,接通和断开车螺纹传动链。通过分析和比较,选用单螺母更为合适。为了提高螺母的使用寿命,使用一铜螺母嵌入螺母底座内,并用一锁紧螺钉将其周向固定。螺母底座的结构如图38:图38 丝杠螺母底座铜螺母结构如图39:图39 铜螺母3.4支承件的设计机床中的支承件主要是指床身、立柱、横梁、摇臂、底座、刀架、
42、工作台、箱体和升降台等尺寸在的零件,也称是大件,它是机床的基础构件。3.4.1 支承件的功用及基本要求机床的各种支承件有的互相固定连接,有的在导轨上运动。支承件起着支承机床部件的作用,并承受重力、切削力、惯性力、摩擦力等的作用;支承件内部空间常作为变速箱、液压油箱,或安置电气箱、冷却和润滑装置及电动机;正确设计支承件结构及其布局对保证各部件之间的相对位置精度和运动部件的运动精度具有重要意义。对支承件的基本要求是:1.足够的静刚度 在机床额定载荷作用下,变形量不得超出规定值,以保证刀具和工件在加工过程中相对位移不超过加工允许误差。支承件静刚度包括三个方面。(1)自身刚度 支承件抵抗自身变形的能力
43、,称为自身刚度。支承件的自身刚度主要为弯曲刚度和扭转刚度。自身刚度主要取决于支承件材料、构造、形状、尺寸及隔板的布置等。(2)局部刚度 支承件抵抗局部变形的能力,称为局部刚度。局部变形主要发生在支承件上载荷较集中的局部结构处。局部刚度主要取决于受载部位的构造、尺寸以及肋条的设置。(3)接触刚度 支承件的结合面在外载荷作用下抵抗接触变形的能力,称为接触刚度。2.良好的动态特性 在规定的切削条件下工作时,使受迫振动的振幅不超过允许值,不产生自激振动等,保证切削的稳定性。要求有较大动刚度和阻尼。3.较小的热变形和内应力 在机床工作过程中的摩擦热、切削热等热量会引起支承件的热变形和热应力;支承件在铸造
44、、焊接、粗加工过程中会形成内应力,在使用中内应力重新分布并逐渐消失,导致支承件变形。4.较高的刚度/质量比 在满足刚度的前提下,应尽量减小支承件的质量。支承件的质量往往占机床总质量的80%以上,所以它在很大程度上反映了支承件设计的合理性。5.支承件的设计应便于制造、装配、维修、排屑及吊运等。3.4.2 支承件的结构分析支承件结构及布局是否合理将直接影响机床的加工质量和生产率,因此,应该正确地选用。合理的结构通常是根据使用要求和受力情况,参考同类型机床,初步确定其形状和尺寸。在支承件设计时主要考虑如何提高刚度、减少热变形、合理选用材料及热处理方式、有较好的结构工艺性。提高支承件自身刚度和局部刚度
45、1.正确选择截面的形状和尺寸 支承件主要是承受弯矩、扭矩以及弯扭复合载荷,所以自身刚度主要是考虑弯曲刚度和扭转刚度。截面积相同时空心截面刚度大于实心截面刚度,封闭的截面刚度大于不封闭的截面刚度,方形截面的抗弯刚度比圆形的大,而抗扭刚度较低。因此,设计支承件时总是采用空心截面、适当加大轮廓尺寸并在工艺允许的前提下减小壁厚;在可能的条件下,尽量把支承件的截面设计成封闭的框形,如数控车床要有高的刚度,以适应粗加工要求,故床身为四面封闭结构,其导轨倾斜以利于排屑;在支承件以承受弯矩为主时,则应采用方形截面或矩形截面;矩形截面在其高度方向的抗弯刚度比方形截面高,但抗扭刚度则较低,支承件以承受一个方向的弯
46、矩为主时,常取矩形截面,并以其高度方向作为受弯方向;当支承件以承受扭矩为主时,应采用圆形(空心)截面;如果所承受的弯矩和扭矩都相当大,则常取近似方形截面。2.合理布置隔板和加强肋 在两壁之间起连接作用的内壁称为隔板。隔板的功用在于把作用于支承件局部地区的载荷传递给其它壁板,从而使整个支承件能比较均匀地承受载荷。因此,当支承件不能采用全封闭截面时,应布置隔板和加强肋来提高支承件的刚度。隔板布置有横向、纵向和斜向等基本形式。横向隔板主要可提高抗扭刚度;纵向隔板主要可提高抗弯刚度;斜向隔板则兼有提高抗弯和抗扭的效果。为了便于排屑,床身一般由前壁、后壁隔板组成。普通机床的隔板的基本形式如图310:图3
47、10 机床隔板图310a在床身前后壁间用T形隔板联接,主要提高水平面抗弯刚度,对提高垂直面抗弯刚度和抗扭刚度作用不显著,多用在刚度要求不高的床身上,但这种床身结构简单,铸造工艺性好。图310b的 形隔板具有一定的宽度和高度,在垂直面上和水平面上的抗弯刚度都比上一种好,铸造工艺性也不差,在很多大中型机床上都可看到。图310c的斜向隔板在床身的前后壁间呈W形布置,能较大地提高水平面的抗弯抗扭刚度。在中心距超过1500毫米的长床身,收效最为显著。在机床中心距为7501000毫米时,斜向隔板的刚度与 形隔板的差不多,而铸造则较困难,故斜向隔板只在长床身中才推荐采用。相邻两斜板间的夹角一般为60100。
48、通过比较,床身隔板的形式选用第二种。3.5进给传动设计进给传动系统一般是由动力源、变速机构、换向机构、分配机构、安全机构、快速运动传动链、变回转运动为直线运动的转换机构、执行件等部分组成。进给传动的特点:1.进给传动速度低、受力小、消耗功率少 一般机床的进给量都比较小,最小进给量可达0.01毫米/转,甚至几微米/转。为了实现这样低的速度,须解决降速问题。常采用降速很大的传动机构,如丝杠螺母、蜗杆蜗轮、行星机构等,以便缩短进给传动链。进给传动受力比较小,因此各传动件的尺寸比较小,箱体内结构较紧凑。2.进给传动中对传动链换接的要求比较多多数机床进给运动的数目比较多。进给运动一般需要换向。执行进给运
49、动的部件,往往还需作快速运动和调整运动等。因此,进给传动中传动链换接要求比较多。3.进给传动的载荷特点为恒扭矩工作进给传动的载荷特点与主传动不同,当粗加工进给量较大时,一般采用较小的切削深度;当切削深度较大时,多采用较小的进给量,所以,在各种不同进给量的情况下,产生的切削力大致相同,即都有可能达到最大进给力,因此,最后输出轴最大扭矩基本不变,这就是进给传动的恒扭矩工作特点。3.5.1确定丝杠转速加工减荷阀体的两侧面时,我们可选用主轴转速为180r/min进行加工。铣刀每齿进给量mm,则铣刀进给量mm。由于在铣削加工中,进给运动是由工作台来完成的,则工作台的移动速度就是铣刀的进给速度。即工作台的
50、移动速度为:mm/min则丝杠此时的转速应为r/min取标准数列数值:r/min根据金属切削机床设计表24,取公比根据本次设计的要求:转速级数Z=3查标准数列,取传动丝杠转速分别为r/min,r/min,r/min3.5.2传动变速箱设计由于最大传动比,且转速级数Z=3,故采用一对蜗杆蜗轮传动,进行大传动比的降速,再采用一对三联滑移齿轮进行三级变速。参照铣床进给传动系统,按照本次设计要求,确定该进给传动系统的传动方案如图311:图311 组合铣床进给传动方案假设 即 轴与轴之间为蜗杆传动,查机械设计课程设计手册表18,蜗杆传动传动比,取。轴为电动机轴,则r/minr/min则轴到轴之间的三联滑
51、移齿轮的传动比分别为:3.5.2.1 确定蜗杆蜗轮参数蜗杆头数蜗轮齿数查机械设计表13.4得:齿形角,模数蜗杆分度圆直径mm根据机械设计表13.5,得:蜗杆直径系数蜗轮分度圆直径mm蜗轮齿宽mm取齿宽mm中心距(未变位蜗杆蜗轮传动)mm3.5.2.2 齿轮传动参数的确定查机械设计表12.3,取标准模数由于进给传动变速箱采用的是三联滑移齿轮传动,则三对传动齿轮之和应相等。根据传动比要求,确定滑移齿轮的齿数:,则分度圆直径为mmmmmmmmmmmm查机械设计表12.13,选齿面为硬齿面,由于传动齿轮为直齿圆柱齿轮,则可取齿宽系数由于齿宽系数是齿宽和小齿轮分度圆直径的比值,则按小齿轮来设计齿宽,即三
52、对传动齿轮的齿宽为:mmmmmm为便于装配和调整,分别取齿宽:mm,mm,mm则进给传动示意图如图312:图312 进给传动示意图3.6 标准件的选择1.深沟球轴承的选择查机械设计课程设计手册表61,深沟球轴承结构如图313:图313 深沟球轴承在本次设计中,只有一种规格的深沟球轴承,则选轴承代号为6205,即其基本尺寸为:d=25,D=52,B=152、角接触球轴承查机械设计课程设计手册表66,角接触球轴承结构如图314:图314 角接触球轴承本次设计中,共有两种不同规格的角接触球轴承,则选轴承代号为7026C和7208C,即其基本尺寸分别为:d1=30,D1=62,B=16d2=40,D2
53、=80,B=183.圆锥滚子轴承查机械设计课程设计手册表67,圆锥滚子轴承结构如图315:图315 圆锥滚子轴承本次设计中,共有两种规格的圆锥滚子轴承,则选轴承代号为30206和30210,即其基本尺寸分别为:d1=30,D1=62,T1=17.25,B1=16,C1=14d2=40,D2=80,T2=21.75,B2=20,C2=174.圆螺母查机械设计课程设计手册表56,圆螺母结构如图316:图316 圆螺母在本次设计中,共有三种不同规格的圆螺母,其螺纹公称直径分别为M24、M30、M36,查表得其基本尺寸为:5.螺钉锁紧挡圈查机械设计课程设计手册表52,螺钉锁紧挡圈结构见图317:图31
54、7 螺钉锁紧挡圈在本次设计中,只有一个螺钉锁紧挡圈,其公称直径,则其基本尺寸为:,螺钉(GB71-85):6.联轴器参照机械设计第408页,按照本次设计的结构和要求,联轴器选择牙嵌联轴器。牙嵌联轴器由两个端面都有凸牙和凹槽的半联轴器组成。每个凸牙都嵌在对应的半联轴器中的凹槽内,当两轴作轴向位移时,凸牙可在凹槽内滑移,从而构成一动联接。为便于两轴对中,在左方的半联轴器中装有定中环,并有螺钉固定,右端的轴则伸入该环内。关于牙嵌联轴器的计算和尺寸可参考牙嵌离合器。牙嵌联轴器的结构及尺寸如图318:图318 牙嵌联轴器的结构尺寸结 论在过去的三个月里,我们从接受毕业设计课题开始,到查阅相关文献,再对组
55、合机床进行设计,最后编写技术文件。在这期间,我们查阅了相关的设计手册和技术标准,并在指导老师的细心指导下,我们从一张仅有的零件图到写完整个设计说明书和画出所有规定的设计图,每一个环节都是从无到有,使我们真正的了解了设计的基本过程,锻炼了我们运用所学知识和查阅相关文献的能力。此次毕业设计涉及到的知识面很广,涉及到了材料力学、机械工程材料、机械制造技术基础、机械制造装备设计、公差配合与技术测量、机械设计、金属材料及热处理等课程的相关知识,同时还联系到了生产实习中的一些经验,应用到的知识广、全面。通过此次毕业设计的顺利完成,使我进行了一次对本专业知识的一个综合运用练习,这是我们在校期间的最后一次设计
56、,这不仅能反映出我们在学习上的知识度,更是为我们以后的社会实践积累了一定的宝贵经验。参 考 文 献1 王绍俊机械制造工艺设计手册M北京:机械工业出版社,1985.112 李洪机械制造工艺金属切削机床设计指导M辽宁:东北工学院出版社,1989.33 谢家瀛组合机床设计简明手册M北京:机械工业出版社,1994.24 李庆余,张佳机械制造装备设计M北京:机械工业出版社,2003.85 黄鹤汀机械制造装备M北京:机械工业出版社,2004.76 邱宣怀机械设计(第四版)M北京:高等教育出版社,1997.77 吴宗泽,罗圣国机械设计课程设计手册(第二版)M北京:高等教育出版社,1999.68 金属切削机床设计编写组金属切削机床设计(上、下册) M上海:上海科学技术出版社,1980.29 金属切削机床设计编写组金属切削机床设计(修订本) M上海:上海科学技术出版社,1985.510 徐灏机械设计手册M北京:机械工业出版社,1991.911 陈泽民公差配合与技术测量M北京:机械工业出版社,1984.1112 王焕庭,李茅华,徐善国机械工程材料M辽宁:大连理工大学出版社,1988.813 赵忠,丁仁亮,周而康金属材料及热处理M北京:机械工业出版社,1999.1014 沈阳工业大学组合机床设计M上海:上海科技出版社,1985.
- 温馨提示:
1: 本站所有资源如无特殊说明,都需要本地电脑安装OFFICE2007和PDF阅读器。图纸软件为CAD,CAXA,PROE,UG,SolidWorks等.压缩文件请下载最新的WinRAR软件解压。
2: 本站的文档不包含任何第三方提供的附件图纸等,如果需要附件,请联系上传者。文件的所有权益归上传用户所有。
3.本站RAR压缩包中若带图纸,网页内容里面会有图纸预览,若没有图纸预览就没有图纸。
4. 未经权益所有人同意不得将文件中的内容挪作商业或盈利用途。
5. 装配图网仅提供信息存储空间,仅对用户上传内容的表现方式做保护处理,对用户上传分享的文档内容本身不做任何修改或编辑,并不能对任何下载内容负责。
6. 下载文件中如有侵权或不适当内容,请与我们联系,我们立即纠正。
7. 本站不保证下载资源的准确性、安全性和完整性, 同时也不承担用户因使用这些下载资源对自己和他人造成任何形式的伤害或损失。