PLC控制步进电机系统
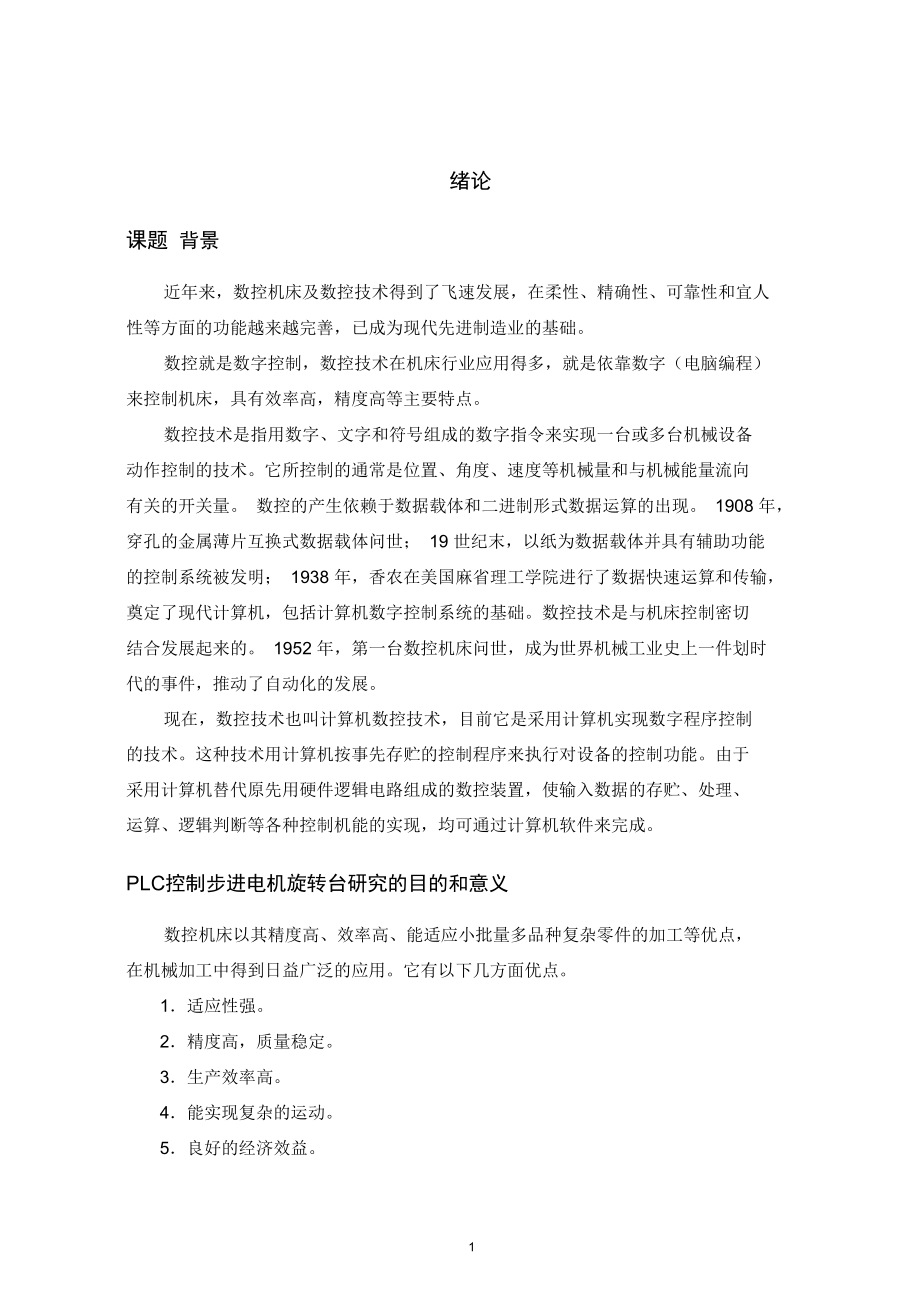


《PLC控制步进电机系统》由会员分享,可在线阅读,更多相关《PLC控制步进电机系统(41页珍藏版)》请在装配图网上搜索。
1、绪论课题 背景近年来,数控机床及数控技术得到了飞速发展,在柔性、精确性、可靠性和宜人 性等方面的功能越来越完善,已成为现代先进制造业的基础。数控就是数字控制,数控技术在机床行业应用得多,就是依靠数字(电脑编程) 来控制机床,具有效率高,精度高等主要特点。数控技术是指用数字、文字和符号组成的数字指令来实现一台或多台机械设备 动作控制的技术。它所控制的通常是位置、角度、速度等机械量和与机械能量流向 有关的开关量。 数控的产生依赖于数据载体和二进制形式数据运算的出现。 1908 年, 穿孔的金属薄片互换式数据载体问世; 19 世纪末,以纸为数据载体并具有辅助功能 的控制系统被发明; 1938 年,香
2、农在美国麻省理工学院进行了数据快速运算和传输, 奠定了现代计算机,包括计算机数字控制系统的基础。数控技术是与机床控制密切 结合发展起来的。 1952 年,第一台数控机床问世,成为世界机械工业史上一件划时 代的事件,推动了自动化的发展。现在,数控技术也叫计算机数控技术,目前它是采用计算机实现数字程序控制 的技术。这种技术用计算机按事先存贮的控制程序来执行对设备的控制功能。由于 采用计算机替代原先用硬件逻辑电路组成的数控装置,使输入数据的存贮、处理、 运算、逻辑判断等各种控制机能的实现,均可通过计算机软件来完成。PLC控制步进电机旋转台研究的目的和意义数控机床以其精度高、效率高、能适应小批量多品种
3、复杂零件的加工等优点, 在机械加工中得到日益广泛的应用。它有以下几方面优点。1适应性强。2精度高,质量稳定。3生产效率高。4能实现复杂的运动。5良好的经济效益。6有利于生产管理的现代化。数控机床由程序编制及程序载体、输入装置、数控装置( CNC、伺服驱动及位 置检测、辅助控制装置、机床本体等几部分组成。数控机床发展的概况从 1952 年至今,数控机床按照控制机的发展,已经历了五代。1959 年,由于在计算机行业中研制出晶体管元件,因而在数控系统中广泛采用 晶体管和印刷电路板,从而跨入了第二代。1965 年,出现小规模集成电路,由于它体积小、功耗低,使数控系统的可靠性 得以进一步提高。数控系统发
4、展到第三代。以上三代系统,都是采用专用控制计算 机的硬接线数控系统,我们称之为硬线系统,统称为普通数控系统(NC、。随着计算技术的发展,小型计算机的价格急剧下降,激烈地冲击着市场。数控 系统的生产厂家认识到,采用小型计算机来取代专用控制计算机,经济上是合算的, 许多功能可以依靠编制专用程序存在计算机的存储器中,构成所谓控制软件而加以 实现,提高了系统的可靠性和功能特色。这种数控系统,称为第四代系统,即计算 机数控系统( CNC、。但是,计算机技术的发展是日新月异的, 就在 1970 年前后,美国英特尔( Intel 、 公司开发和使用了四位微处理器,微处理芯片渗透到各个行业,数控技术也不例外。
5、 我们把以微处理机技术为特征的数控系统称为第五代系统( MNC、。我国数控机床发展的概况1958年,清华大学和北京第一机床厂合作研制出我国第一台数控铣床,由于我 国基础理论研究滞后,相关工业基础薄弱,特别是电子技术落后,数控系统没有突 破,虽然我国起步不晚,但发展不快, 60-70 年代,由于文革等因素,我国与发达国 家差距开始拉大。 70 年代国家组织数控机床攻关,取得一定成效,相继推出一些数 控机床品种,但从整体来看,我国数控机床产业尚处于起步阶段。80年代前期,我国引进了日本数控系统,通过消化吸收,提高了数控系统的可 靠性。同时开始自行研制、开发并小批量生产数控机床,数控机床品种和质量有
6、了 突破性进展,我国数控机床进入实用阶段。国家从科技攻关和技术改造两方面对数控机床产业进行了重点扶植,并加快了 国产数控系统的开发。普及型数控系统开发成功,为数控机床商品化和规模化生产 奠定了基础。一些数控机床主机厂组建床身、箱体、主轴、轴套等成组单元,厂内 组织专业化生产,生产水平进一步提高。 CADCAPPCA开始应用,开发能力、工艺 水平和产品质量进一步提高,奠定产业化基础,“十五”数控机床进入了快速发展 期。我国从 1958 年试制成功第一台数控铣床, 经历了漫长的发展历程。 从“六五” (1980-1985)开始数控机床产业化,通过二十多年的发展,初步建立了国产数控机 床产业化体系。
7、进入新世纪以来,科学技术发展迅速,随着新技术革命向纵深发展, 特别是电子技术和信息技术的快速发展,一批新技术的应用与当代各学科技术的融 合,数控机床的发展进入了新阶段,我国数控机床面临关键技术突破和产业升级的 战略机遇。未来的发展方向目前,世界先进制造技术不断兴起,超高速切削、超精密加工等技术的应用, 柔性制造系统的迅速发展和计算机集成系统的不断成熟,对数控加工技术提出了更 高的要求。当今数控机床正在朝着以下几个方向发展:1高速度、高精度化。速度和精度是数控机床的两个重要指标,它直接关系到 加工效率和产品质量。目前,数控系统采用位数、频率更高的处理器,以提高系统 的基本运算速度。同时,采用超大
8、规模的集成电路和多微处理器结构,以提高系统 的数据处理能力,即提高插补运算的速度和精度,并采用直线电动机直接驱动机床 工作台的直线伺服进给方式,其高速度和动态响应特性相当优越。采用前馈控制技 术,使追踪滞后误差大大减小,从而改善拐角切削的加工精度。为适应超高速加工的要求,数控机床采用主轴电动机与机床主轴合二为一的结 构形式,实现了变频电动机与机床主轴一体化,主轴电机的轴承采用磁浮轴承、液 体动静压轴承或陶瓷滚动轴承等形式。目前,陶瓷刀具和金刚石涂层刀具已开始得 到应用。2多功能化。配有自动换刀机构 (刀库容量可达 100 把以上)的各类加工中心, 能在同一台机床上同时实现铣削、镗削、钻削、车削
9、、铰孔、扩孔、攻螺纹等多种 工序加工,现代数控机床还采用了多主轴、多面体切削,即同时对一个零件的不同 部位进行不同方式的切削加工。数控系统由于采用了多CPU吉构和分级中断控制方式,即可在一台机床上同时进行零件加工和程序编制,实现所谓的“前台加工,后 台编辑”。为了适应柔性制造系统和计算机集成系统的要求,数控系统具有远距离 串行接口,甚至可以联网,实现数控机床之间的数据通信,也可以直接对多台数控 机床进行控制。3智能化。现代数控机床将引进自适应控制技术,根据切削条件的变化,自动 调节工作参数,使加工过程中能保持最佳工作状态,从而得到较高的加工精度和较 小的表面粗糙度,同时也能提高刀具的使用寿命和
10、设备的生产效率。具有自诊断、 自修复功能,在整个工作状态中,系统随时对 CNC系统本身以及与其相连的各种设 备进行自诊断、检查。一旦出现故障时,立即采用停机等措施,并进行故障报警, 提示发生故障的部位、原因等。还可以自动使故障模块脱机,而接通备用模块,以 确保无人化工作环境的要求。为实现更高的故障诊断要求,其发展趋势是采用人工 智能专家诊断系统。4数控编程自动化。随着计算机应用技术的发展,目前CADZ CAh图形交互式自动编程已得到较多的应用,是数控技术发展的新趋势。它是利用CAD绘制的零件加工图样,再经计算机内的刀具轨迹数据进行计算和后置处理,从而自动生成NC零件加工程序,以实现CAD与 C
11、AMI勺集成。随着CIMS技术的发展,当前又出现了 CAD Z CAPZ CAh集成的全自动编程方式,它与 CADZ CAM系统编程的最大区别是其编程 所需的加工工艺参数不必由人工参与,直接从系统内的CAPP数据库获得。5可靠性最大化。数控机床的可靠性一直是用户最关心的主要指标。数控系统 将采用更高集成度的电路芯片,利用大规模或超大规模的专用及混合式集成电路, 以减少元器件的数量,来提高可靠性。通过硬件功能软件化,以适应各种控制功能 的要求,同时采用硬件吉构机床本体的模块化、标准化和通用化及系列化,使得既 提高硬件生产批量,又便于组织生产和质量把关。还通过自动运行启动诊断、在线 诊断、离线诊断
12、等多种诊断程序,实现对系统内硬件、软件和各种外部设备进行故 障诊断和报警。利用报警提示,及时排除故障; 利用容错技术,对重要部件采用 余”设计,以实现故障自恢复;利用各种测试、监控技术,当生产超程、刀损、干 扰、断电等各种意外时,自动进行相应的保护。6控制系统小型化。数控系统小型化便于将机、电装置结合为一体。目前主要 采用超大规模集成元件、多层印刷电路板,采用三维安装方法,使电子元器件得以 高密度安装,较大规模缩小系统的占有空间。而利用新型的彩色液晶薄型显示器替 代传统的阴极射线管,将使数控操作系统进一步小型化。这样可以方便地将它安装 在机床设备上,更便于对数控机床的操作使用。411 可编程控
13、制器简介可编程控制器是 60 年代末在美国首先出现,当时叫可编程逻辑控制器 PLC ( Programmable Logic Controller ),目的是用来取代继电器,以执行逻辑判断、 计时、计数等顺序控制功能。PLC的基本设计思想是把计算机功能完善、灵活、通用 等优点和继电器控制系统的简单易懂、操作方便、价格便宜等优点结合起来,控制 器的硬件是标准的、通用的。根据实际应用对象,将控制内容编成软件写入控制器 的用户程序存储器内。控制器和被控对象连接方便。随着半导体技术,尤其是微处理器和微型计算机技术的发展,到 70 年代中期以 后,PLC已广泛地使用微处理器作为中央处理器, 输入输出模块
14、和外围电路也都采用 了中、大规模甚至超大规模的集成电路,这时的 PLC已不再是逻辑判断功能,还同 时具有数据处理、 PID 调节和数据通信功能。可编程控制器是一种数字运算操作的电子系统, 专为在工业环境下应用而设计。 它采用了可编程序的存储器,用来在其内部存储执行逻辑运算,顺序控制、定时、 计算和算术运算等操作的指令,并通过数字式和模拟式的输入输出,控制各种类型 的机械或生产过程。PLC是微机技术与传统的继电接触控制技术相结合的产物,它克服了继电接触控制系统中机械触点的接线复杂、可靠性低、功耗高、通用性和灵活 性差的缺点,充分利用微处理器的优点。可编程控制器对用户来说,是一种无触点设备,改变程
15、序即可改变生产工艺, 因此可在初步设计阶段选用可编程控制器,在实施阶段再确定工艺过程。另一方面, 从制造生产可编程控制器的厂商角度看,在制造阶段不需要根据用户的订货要求专 门设计控制器,适合批量生产。由于这些特点,可编程控制器问世以后很快受到工 业控制界的欢迎,并得到迅速的发展。目前,可编程控制器已成为工厂自动化的强 有力工具,得到了广泛的应用。1.1 PLC 的结构及各部分的作用可编程控制器的结构多种多样,但其组成的一般原理基本相同,都是以微处理 器为核心的结构。通常由中央处理单元(CPU、存储器(RAM RO)输入输出单元 ( I/O )、电源和编程器等几个部分组成。1.1.1 中央处理单
16、元( CPU)CPU乍为整个PLC的核心,起着总指挥的作用。CPU一般由控制电路、运算器和 寄存器组成。这些电路通常都被封装在一个集成电路的芯片上。 CPU!过地址总线、 数据总线、控制总线与存储单元、输入输出接口电路连接。 CPU勺功能有以下一些: 从存储器中读取指令,执行指令,取下一条指令,处理中断。1.1.2 存储器( RAM、 ROM)存储器主要用于存放系统程序、 用户程序及工作数据。 存放系统软件的存储器称 为系统程序存储器 ; 存放应用软件的存储器称为用户程序存储器; 存放工作数据的存 储器称为数据存储器。常用的存储器有 RAM EPRO和EEPRQMRAh是一种可进行读 写操作的
17、随机存储器存放用户程序,生成用户数据区,存放在RAM中的用户程序可方便地修改。RAM存储器是一种高密度、低功耗、价格便宜的半导体存储器,可用锂 电池做备用电源。掉电时,可有效地保持存储的信息。EPROMIEEPRO都是只读存储器。用这些类型存储器固化系统管理程序和应用程序。1.1.3 输入输出单元( I/O 单元)I/O 单元实际上是PLC与被控对象间传递输入输出信号的接口部件。I/O单元有 良好的电隔离和滤波作用。接到 PLC输入接口的输入器件是各种开关、按钮、传感 器等。PLC的各输出控制器件往往是电磁阀、接触器、继电器,而继电器有交流和直 流型,高电压型和低电压型,电压型和电流型。1.1
18、.4 电源PLC 电源单元包括系统的电源及备用电池, 电源单元的作用是把外部电源转换成 内部工作电压。PLC内有一个稳压电源用于对 PLC的CPU单元和I/O单元供电。1.1.5 编程器编程器是PLC的最重要外围设备。利用编程器将用户程序送入PLC的存储器, 还可以用编程器检查程序,修改程序,监视 PLC 的工作状态。除此以外,在个人计 算机上添加适当的硬件接口和软件包,即可用个人计算机对 PLC 编程。利用微机作 为编程器,可以直接编制并显示梯形图。1.2 PLC 的工作原理PLC采用循环扫描的工作方式,在PLC中用户程序按先后顺序存放,CPL从第一 条指令开始执行程序,直到遇到结束符后又返
19、回第一条,如此周而复始不断循环。PLC的扫描过程分为内部处理、通信操作、程序输入处理、程序执行、程序输出几个 阶段。全过程扫描一次所需的时间称为扫描周期。当PLC处于停状态时,只进行内部处理和通信操作服务等内容。在 PLC处于运行状态时,从内部处理、通信操作、 程序输入、程序执行、程序输出,一直循环扫描工作。1.2.1 输入处理输入处理也叫输入采样。在此阶段,顺序读入所有输入端子的通端状态,并将 读入的信息存入内存中所对应的映象寄存器。在此输入映象寄存器被刷新。接着进 入程序执行阶段。在程序执行时,输入映象寄存器与外界隔离,即使输入信号发生 变化,其映象寄存器的内容也不会发生变化,只有在下一个
20、扫描周期的输入处理阶 段才能被读入信息。1.2.2 程序执行根据PLC梯形图程序扫描原则,按先左后右先上后下的步序,逐句扫描,执行 程序。遇到程序跳转指令,根据跳转条件是否满足来决定程序的跳转地址。从用户 程序涉及到输入输出状态时,PLC从输入映象寄存器中读出上一阶段采入的对应输入 端子状态,从输出映象寄存器读出对应映象寄存器,根据用户程序进行逻辑运算, 存入有关器件寄存器中。对每个器件来说,器件映象寄存器中所寄存的内容,会随 着程序执行过程而变化。1.2.3 输出处理程序执行完毕后,将输出映象寄存器,即器件映象寄存器中的Y 寄存器的状态,在输出处理阶段转存到输出锁存器,通过隔离电路,驱动功率
21、放大电路,使输出端 子向外界输出控制信号,驱动外部负载。1.3 PLC 编程语言1.3.1 梯形图编程语言梯形图沿袭了继电器控制电路的形式,它是在电器控制系统中常用的继电器、 接触器逻辑控制基础上简化了符号演变来的,形象、直观、实用。梯形图的设计应注意以下三点:4.1.1 梯形图按从左到右、从上到下的顺序排列。每一逻辑行起始于左母线,然后 是触点的串、并联接,最后是线圈与右母线相联。4.1.2 梯形图中每个梯级流过的不是物理电流,而是“概念电流” ,从左流向右, 其两端没有电源。这个“概念电流”只是形象地描述用户程序执行中应满足线圈接 通的条件。4.1.3 输入继电器用于接收外部输入信号, 而
22、不能由PLC内部其它继电器的触点来 驱动。因此,梯形图中只出现输入继电器的触点,而不出现其线圈。输出继电器输 出程序执行结果给外部输出设备,当梯形图中的输出继电器线圈得电时,就有信号 输出,但不是直接驱动输出设备,而要通过输出接口的继电器、晶体管或晶闸管才 能实现。输出继电器的触点可供内部编程使用。(1) 语句表编程语言指令语句表示一种与计算机汇编语言相类似的助记符编程方式,但比汇编语言 易懂易学。一条指令语句是由步序、指令语和作用器件编号三部分组成。(2) 控制系统流程图编程图控制系统流程图是一种较新的编程方法。它是用像控制系统流程图一样的功能 图表达一个控制过程,目前国际电工协会 (IEC
23、) 正在实施发展这种新式的编程标准。1.4 小结本章介绍了可编程控制器的组成、工作原理及 PLC的编程语言。根据以上介绍, 可以看出PLC的特点:编程方法简单易学;功能强,性能价格比高;硬件配套齐全, 用户使用方便,适应性强;可靠性高,抗干扰能力强;系统的设计、安装、调试工 作量少;维修工作量小,维修方便;体积小,能耗低。因此,PLC的应用领域十分广泛,主要应用于开关量逻辑控制、运动控制、闭环 过程控制、数据处理及通信联网等。2 伺服系统及步进电机简介伺服系统主要研究内容是机械运动过程中涉及的力学、机械学、动力驱动、伺 服参数检测和控制等方面的理论和技术问题。伺服系统对自动化、自动控制、电气
24、工程、机电一体化等专业既是一项基础技术,又是一项专业技术,因为它不仅分析 各种基本的变换电路,而且结合生产实际,解决各种复杂定位控制问题,如机器人 控制、数控机床等,它是运动控制系统及现代电力电子技术相结合的交叉学科,是 力学、机械、电工、电子、计算机、信息和自动化等学科和技术领域的综合,这些 技术出现的新进展都使它向前迈进一步,其技术进步是日新月异的。2.1 伺服系统的作用及组成在自动控制系统中,使输出量能够以一定准确度跟随输入量的变化而变化的系 统称为随动系统,亦称伺服系统。数控机床的伺服系统是指以机床移动部件的位置 和速度作为控制量的自动控制系统。数控机床进给伺服系统的作用在于接受来自数
25、控装置的指令信号,驱动机床移 动部件跟随指令脉冲运动,并保证动作的快速和准确,这就要求是高质量的速度和 位置伺服。数控机床的精度和速度等技术指标往往主要取决于伺服系统。数控机床伺服系统的一般结构如图 2-1 所示。它是一个双闭环系统,内环是速 度环,外环是位置环。速度环中用作速度反馈的检测装置为测速发电机、脉冲编码 器等。速度控制单元是一个独立的单元部件,它由速度调节器、电流调节器、及功 率驱动放大器等个部分组成。位置环是由 CNC 装置中的位置控制模块、速度控制单 元、位置检测及反馈控制等各部分组成,位置控制主要是对机床运动坐标轴进行控 制。轴控制是要求最高的位置控制,不仅单个轴的运动速度和
26、位置精度的控制有严 格要求,而且在多轴联动时,还要求各移动轴有很多的动态配合,才能保证加工效 率、加工精度和表面粗糙度指令图2-1伺服系统结构图2.2伺服系统的分类伺服系统按调节理论分类可分为开环伺服系统、闭环伺服系统、半闭环伺服系 统;按使用的驱动元件分类可分为步进伺服系统、直流伺服系统、交流伺服系统。 在这里我们重点介绍开环伺服系统和步进伺服系统。2.2.1开环伺服系统这是一种比较原始的伺服系统。这类数控系统将零件的程序处理后,输出数据 指令给伺服系统,驱动机床运动,没有来自位置传感器的反馈信号。最典型的系统 就是采用步进电机的伺服系统,如图 2-2所示。工作台图2-2开环伺服系统它一般由
27、环形分配器、步进电机功率放大器、步进电动机、配速齿轮和丝杠螺 母传动副等组成。数控系统每发出一个指令脉冲,经驱动电路功率放大后,驱动步 进电动机旋转一个固定角度(即步距脚),再经传动机构带动工作台移动。这类系统 信息流是是单向的,即进给脉冲发出去后,实际移动值不再反馈回来,所以称为开 环控制。2.2.2步进伺服系统如上图2-1所示,步进式伺服系统亦称为开环位置伺服系统,其驱动元件为步 进电动机。功率步进电动机盛行于 20世纪70年代,且控制系统的结构最简单,控 制最容易,维修最方便,控制为全数字化(即数字化的输入指令脉冲对应着数字化 的位置输出),这完全符合数字化控制技术的要求,数控系统与步进
28、电动机的驱动控 制电路结为一体。随着计算机技术的发展,除功率驱动电路之外,其他硬件电路均可由软件实现, 从而简化了系统结构,降低了成本,提高了系统的可靠性。但步进电动机的耗能太 大,速度也不高,当其在脉冲当量 S为1卩m时,最高移动速度仅有2mm/min且功 率越大移动速度越低,所以主要用于速度与精度要求不高的经济型数控机床及旧设 备改造中2.3 步进电机工作原理步进电机是一种将电子数字脉冲信号转变为机械运动的电磁增量运动器件。典 型的电机绕组固定在定子上,而转子则由硬磁或软磁材料组成。当控制系统将一个 电脉冲信号经功率装置加到定子绕组中,电机便会沿一定的方向旋转一步。脉冲的 频率决定电机的转
29、速。电机转动的角度与所输入的电脉冲个数成正比;因此,只要 简单地改变输入脉冲的数目,就能控制步进电机的转子运行角度,从而达到位置控 制的目的。步进电机有以下特点:(1)运行角度正比于输入脉冲,便于开环运行,花费少;(2)具有锁定转矩;(3)定位精度高,并且没有累积误差;(4)具有优良的起动、停止、反转响应;(5)无电刷和可靠性高;(6)可低速运行,直接驱动负载;(7)不适宜的控制会引起振动;(8)不宜运行于高速状态。4.2.1 步进电机的控制(2) 开环控制步进电机的最显著的优势是不需要位置反馈信号就能够进行精确的位置控制。 这种开环控制形式省去了昂贵的位置传感器件,只需对输入指令脉冲信号计数
30、,就 能知道电机的位置。图 2-3 所示的是一个步进电机开环控制的基本组成,它包括驱动电路、脉冲发 生器和能使电机绕组按特定相序励磁的脉冲分配器。图2-3步进电机的开环控制原理图(3) 闭环控制在开环控制系统中,电机响应走步指令后的实际运行情况,控制系统是无法预 测和监视的。在一些运行速度范围宽、负载大小变化频繁的场合,步进电机容易失 步,而使整个系统趋于失控。这时候,可以对步进电机进行位置闭环控制。控制系 统对电动机转子位置进行检测,并将信号反馈至控制单元,使得系统对步进电机发 出的走步命令,只有得到相应实际位置响应后,方告完成。因此,闭环控制的最基 本任务是防止步进电机失步。实际上是一种简
31、单的位置伺服系统。图2-4为闭环系统的原理图,整个系统是在开环系统的基础上增加了位置检测、 数据处理的闭环控制电路。图2-4步进电机的闭环控制原理图(3) 小结作为数控机床的重要功能部件,伺服系统的特性一直是影响系统加工性能的重 要指标。围绕伺服系统动态特性与静态特性的提高,近年来发展了多种伺服驱动技 术。可以预见随着超高速切削、超精密加工、网络制造等先进制造技术的发展,具 有网络接口的全数字伺服系统、直线电动机及高速电主轴等将成为数控机床行业的 关注的热点,并成为伺服系统的发展方向。3 PLC 控制步进电机方法的研究随着微电子技术和计算机技术的发展,可编程序控制器有了突飞猛进的发展, 其功能
32、已远远超出了逻辑控制、顺序控制的范围,它与计算机有效结合,可进行模 拟量控制,具有远程通信功能等。有人将其称为现代工业控制的三大支柱(即PLC,机器人,CAD/CA M之一。目前可编程序控制器(Programmable Con troller )简称 PLC已广泛应用于冶金、矿业、机械、轻工等领域,为工业自动化提供了有力的工具。3.1 PLC 的基本结构PLC采用了典型的计算机结构,主要包括CPU RAM ROMP输入/输出接口电路等。 如果把PLC看作一个系统,该系统由输入变量-PLC-输出变量组成,外部的各种开关 信号、模拟信号、传感器检测的信号均作为 PLC勺输入变量,它们经PLC外部端
33、子输 入到内部寄存器中,经PLC内部逻辑运算或其它各种运算、处理后送到输出端子,它 们是PLC的输出变量,由这些输出变量对外围设备进行各种控制。3.2 控制方法及研究3.2.1 FP1 的特殊功能简介脉冲输出FP1的输出端丫7可输出脉冲,脉冲频率可通过软件编程进行调节,其输出频率范 围为 360Hz 5kHz。高速计数器( HSC)FP1内部有高速计数器,可同时输入两路脉冲,最高计数频率为10kHz,计数范围 -8388608 +8388607。输入延时滤波FP1 的输入端采用输入延时滤波,可防止因开关机械抖动带来的不可靠性,其延 时时间可根据需要进行调节,调节范围为 1ms128ms。中断功
34、能FP1的中断有两种类型,一种是外部硬中断,一种是内部定时中断。322步进电机的速度控制FP1有一条SPD0旨令,该指令配合HS和丫7的脉冲输出功能可实现速度及位置控制。速度控制梯形图见图3-1,控制方式参数见图3-2,脉冲输出频率设定曲线见图3-3。F164SPDO图3-1速度控制梯形图图3-3脉冲输出频率设定曲线3.2.3控制系统的程序运行图3-4控制系统原理图图3-4是控制系统的原理接线图,图4中丫7输出的脉冲作为步进电机的时钟脉冲, 经驱动器产生节拍脉冲,控制步进电机运转。同时 丫7接至PLC勺输入接点X0,并经X0 送至PLC内部的HSC HS计数丫7的脉冲数,当达到预定值时发生中断
35、,使 丫7的脉冲频 率切换至下一参数,从而实现较准确的位置控制。实现这一控制的梯形图见图3-5。l)MV ru vKOU ArUM VK UF0MV+K70FlDMV K1000FOMV ,K0DF图3-5控制梯形图控制系统的运行程序:第一句是将 DT9044和DT9045青零,即为HSC进行计数做准 备;第二句第五句是建立参数表,参数存放在以 DT2(为首地址的数据寄存器区;最 后一句是启动SPD指令,执行到这句则从DT2(开始取出设定的参数并完成相应的控 制要求。由第一句可知第一个参数是K0,是PULS方式的特征值,由此规定了输出方式。 第二个参数是K70,对应脉冲频率为500Hz,于是丫
36、7发出频率为500HZ勺脉冲。第三个 参数是K1000,即按此频率发1000个脉冲后则切换到下一个频率。而下一个频率即最 后一个参数是K0,所以当执行到这一步时脉冲停止,于是电机停转。故当运行此程 序时即可使步进电机按照规定的速度、预定的转数驱动控制对象,使之达到预定位 置后自动停止。3.3小结利用可编程序控制器可以方便地实现对电机速度和位置的控制,方便可靠地进 行各种步进电机的操作,完成各种复杂的工作。它代表了先进的工业自动化革命, 加速了机电一体化的实现。4实验系统的介绍和调试4.1系统概述王要用途HJD-4型机电一体化教学实验系统主要用途为:可完成机电传动控制、可编程控制器原理与应用、机
37、床电气控制、机电一体化控制技术与系统等课程的实验教学;为机电类本科生、专科生的课程设计及毕业设计提供实践环节;为教师和相关科技人员从事机电产品开发提供实验平台;为企业培养机电一体化设备的维护管理人员。4.1.2系统组成HJD-4型机电一体化教学实验系统由个人计算机、 电控柜以及微加工中心等几个 部分组成,如图4-1所示。电控柜微加工中心图4-1系统组成个人计算机个人计算机是整个控制系统的上位机,完成两大功能:(1)通过232串行通讯线与HDJ-2型控制系统中的PLC串行通讯板连接,形成 两级控制系统,实现对PLC的监控及两级控制;通过SC-09编程电缆与PLC连接,实现PLC的编程、程序的输入
38、输出、监 控等。HDJ-2型控制系统控制核心为PLC,包括继电器接触器系统、PLC位置控制模 块(1PG和20GM、交流伺服控制系统、步进电动机控制系统、交流变频调速系统统、 控制面板和面板接线端子等,如图 4-2所示:20GM1PGPLC步进电 动机控 制系统面板接线端子(保险谅07诽厂小叮咂止华中蚪扭丈第您城 / 操作 面板断路器接触器交流 伺服 系统变频调速 系统继电器图4-2控制系统结构图电控柜通过接线端子与微加工中心连接,实现对微加工中心的控制4.2主要技术参数输入电压三相四线:380V, 50HZ4.2.2坐标轴参数坐标轴主要参数如表4-1所示表4-1 :坐标轴主要参数技术规格单
39、位参 数工作台尺寸(长X宽)mm160X 160行程X轴mm160丫轴mm160Z轴mm100C轴deg 180主轴转速范围r/mi n101400进给速度 (X、丫、Z)mm/min1 1000 (步进)12000 (伺 服)快移速度(X、丫、Z)mm/min1000 (步进)2000 (伺服)刀库刀具容量把8脉冲当量X轴mm0.02丫轴mm0.0016Z轴mm0.02刀库mdeg0.744.2.3计算机环境(1)硬件要求CPU In tel Celero n400 以上;内存:不小于64M显示器:800 X 600以上,颜色设置为256色以上;串行通讯口:两个。软件要求操作系统平台: Wi
40、n 98/Wi nMe/Win2000/Wi nXp应用软件:FXGPW、FXVPS-E Visual Basic 6.0、Flash5.0、MedWin等。4.2.4坐标系微加工中心由X、Y、Z、C四轴工作台和刀库机械手组成,其坐标系如下图所示图4-3 坐标系4.3控制系统的电源控制控制系统的主电路如图4-4所示。其主要操作如下:bb AP 阳回fHMMh(a)控制电路、风扇和照明灯电路TEmwwlN dd-arJ#44vU一耳吨陶(b)控制电源、PLC电源、步进电动机电源控制电路(c )交流伺服、交流变频和正反转电机控制电路FX2JN-80MT1iiiiI! 斑f 血1 血2 普3 TH
41、! KM ! D6 ! T3F ivs;Yii KA2 KAJ KA4 KAj KAj(; KA? LaKA?申堰岂学电療覇比矍电卒覃整黑打 牟會辱(d) PLC与各控制系统的连接(e)控制系统的控制图4-4 主电路图操作步骤将控制系统上的电源插头接到380V的电源上。合上电源总断路器Q(电源总开关位于操作台下部的右边),如图4-4所示, 控制电路电源接通,电柜风扇通电,操作电柜侧边的开关可控制照明灯点亮和熄灭;合上断路器QF1,用操作面板上的电源开关使 PLG 24V和5V控制电压接通 电源,使所有的短路器的输入端接通交流电源。如果要使步进电动机控制系统接通电源,在(3)的基础上,首先合上短
42、路器 QF2然后用PLC控制程序控制PLC的输出接点丫30为1,从而使KM2的线圈得电, 主触头导通,步进电动机控制系统接通电源(详细使用说明请参考“步进电动机升 降速及性能测试实验”实验说明)。图4-5电源总断路器的位置如果要使伺服电动机控制系统接通电源,在 (3 )的基础上,首先合上短路器QF3交流然伺服电动机控制系统的控制电压接通,然后用PLC控制程序控制PLC的输出接点丫31为1,从而使KM3的线圈得电,主触头导通,交流伺服电动机控制系 统主回路接通电源(详细使用说明请参考“交流伺服定位性能测试实验”实验说明);如果要使交流变频调速系统接通电源,在(3 )的基础上,首先合上短路器QF4
43、然后用PLC控制程序控制PLC的输出接点丫32为1,从而使KM4的线圈得电, 主触头导通,交直流调速系统接通电源(详细使用说明请参考“三相异步电动机变 频调速性能测试实验”实验说明)。如果要使正反转电动机实现正反转,在(3)的基础上,首先合上短路器QF5 然后用PLC控制程序控制PLC的输出接点丫33或丫34为1,从而使KM5或 KM6的线圈 得电,主触头导通,正反转电动机正转或反转(详细使用说明请参考“三相异步电 动机正反转控制实验”实验说明)。(8)如果要使油泵电动机接通电源,在(3)的基础上,首先合上断路器 QF7然 后用PLC控制程序控制PLC的输出接点丫35为1,从而使KM7的线圈得
44、电,主触头导 通,油泵电动机接通电源(详细使用说明请参考“液压系统的PLC控制实验”实验说明)04.4主要参数设定FX-20GM在系统中,FX-20GM可对X轴和Z轴步进电机驱动器实现单轴和联动控制,其主要参数设定如表4-2所示。表4-2 FX-20GM主要参数设定参数号X 轴Z轴字节数寄存器设定值寄存器设定值1D9202200D940220022D92044000D9404400023D92082000D9408200024D9210400D941040025D9216500D941650026D9218500D941850027D9226400D942640028D9228200D9428
45、20029D92340D94340210D92361D94362所有参数通过PLC指令DMO来设定。有关参数的意义与设定方法请参考附录“ FX-20GM的使用说明”和“ PLC定位模 块应用实验”实验说明。442交流伺服控制系统在系统中,PLC的脉冲输出端(丫0或丫1)以及脉冲方向输出端(除丫0 Y1以外 的其他输出端)为交流伺服控制系统的脉冲/方向信号,从而对丫轴进行定位控制, 其主要参数设定如表4-3所示。表4-3交流伺服控制系统主要参数设定参数号设定值Pr020Pr040Pr423Pr431微型加工中心的C轴为旋转工作台,它的传动机构为蜗轮蜗杆(蜗轮蜗杆的减 速比为1: 38,即蜗杆旋转
46、38转,蜗轮旋转1转)。本实验采用可调速脉冲输出指令“ DPLSR,通过PLC的丫1输出端产生脉冲给步 进电机驱动器SH-20402A驱动步进电机M按升降速方式运行。而步进电机则驱动蜗 轮蜗杆,再由蜗轮蜗杆带动 C轴旋转。(说明:本实验所用PLC为FX2N-128MT属于 晶体管输出型,其输出端 丫0 丫1均可产生高速脉冲,其频率为10KHZ以下。)SH-20402A* +24VDC-“U辆电机X0i正向COM&lPLC n ”一X2T2 O傅止X313 iX4COXliCOMU1 H2图4-6 PLC控制接线图当步进电机带动刀库旋转时,为避免C轴与Z轴发生碰撞而损坏,应在实验之前将Z轴移开!
47、可调速脉冲输出指令“ DPLSR可控制步进电机按升降速方式运行,其使用方法 如下:X10DPLSRS1S2S3D工作频率总脉冲数升降速时间Y0或Y1(HZ)( PLS)( ms)其中:S1的设定范围为:1020000HZ ;的设定范围为:110 2,147,483, 647PLS (因为 DPLSR为 32 位运算指令);的设定范围为:500ms以下;D 的规定:(1).只能为Y0或Y1 ;(2). 定为晶体管输出本实验步进电机45BYG250的步距角为1.8度;驱动器SH-20402A为细分驱动器,可实现1、2、4、8、16、32、64细分(其中: 1时为整步,2为半步)。本实验采用64细分
48、,驱动器向步进电机发 64个脉冲,步 进电机走一步。驱动器向步进电机每发送64*200个脉冲,步进电机旋转1圈。又因蜗轮蜗杆的 减速比为1 : 38 (蜗杆旋转38转,蜗轮旋转1转),因此,要使C轴旋转1圈,驱 动器须向步进电机发射64*200*38个脉冲。PLC控制步进电机旋转台梯形图XOOOX004I_北二(Y03OY030图4-7 PLC控制步进电机旋转台梯形图(a)PLC控制步进电机旋转台程序如图4-7所示,当常开触点X0变为常闭触点时, 线圈丫30通电,驱动器启动。当 X1的常开触点接通后,辅助继电器 M2通电,驱动 器向步进电机发送频率为500HZ的 12800个脉冲,线圈Y1和丫
49、2通电,旋转台正转。 当X2的常开触点接通后,辅助继电器 Ml M2通电,此时M1的常闭触点变为常开触 点,驱动器向步进电机发送脉冲,线圈 丫1通电而线圈丫2断电,旋转台反转。X004M1M2M1M8200Y001Y030iX00L1 jX003X002M2M2X002X001M1DPLSR K5000 K128000 K2000 Y001Y002C200 K0 END图4-8 PLC控制步进电机旋转台梯形图(b)图4-8所示的PLC控制步进电机旋转台梯形图是我在实验过程根据原有的实验 程序进行改编的,在原有的程序中加入一个计数器 C200,由特殊辅助继电器M8200进 行控制。当特殊辅助继电
50、器 M8200接收到的脉冲为“ 0”时,计数器C200进行加计 数;当M8200接收到的脉冲为“ 1”时,计数器C200进行减计数。当X1的常开触点 接通后,旋转台正转,M8200接收到的脉冲为“ 0”,C200加计数;当X2的常开触点 接通后,旋转台反转,M8200通电,接收到的脉冲为“ 1”,C200减计数。通过这样一个程序,我们能更直观的观察到旋转台所进行的运动,也可以更方便的看到驱动 器向步进电机发出的脉冲数,从而更快的计算出步进电机所旋转的圈数。总结这次毕业设计我做的是 PLC 控制步进电机旋转台的研究,要做好该设计,必须 对整个系统有一个全面的了解,因此我最开始是在实验室里对该系统
51、的各个模块进 行实验,弄清楚各部分的工作原理和特性。在实验中,并不是十分顺利,经常会出 现各种问题,例如线路,或者其他电路的分析,在实验中经常会出现各种问题,例 如电机不转或方向出现问题,有时是没有按预先启动,就要检查线路,通常我们都 会用到万用表,示波器等工具检查电压,极性等来查找问题的所在,随着问题的出 现,我们就在老师的帮助下解决并弄懂很多原理,很多都是实践中的经验,十分宝 贵,让我们平时学的一些书面的理论有了很好的实践和融会贯通,很多都通过实验 后都变的很直观,觉得每天都有新的收获,同时也锻炼了我们的动手能力。这次毕业设计不仅增强了我的专业方面的能力,在与小组成员的合作中,我们 也学会
52、了沟通和合作,学会共同解决问题,互帮互助。对于各自的个题也有更深的 理解。也锻炼了我们在问题和困难面前的耐心与毅力,不轻易放弃,一遍不行就试 第二遍,相信自己最终都能解决。当然要感谢刘老师在整个设计中对我们耐心详细 的讲解和辅导,及理论和技术等各方面的支持。使我们能更好的完成毕业设计。致谢实践是检验真理的唯一标准。通过本次毕业设计,使我们对平时所学的各科理 论知识有了更深更全面的理解,同时也提高了动手能力。因此要感谢学校提供的良 好的实验设备和学习环境以及校,系领导的关怀。特别要感谢导师刘政廉老师在整 个的毕业设计过程中对我们的耐心尽责的辅导,以及各方面的鼓励支持。最后要感 谢本组的所有成员的
53、共同努力和愉快合作!参考文献钱平主编.交直调速系统 .第一版. 北京:机械工业出版社 .2002.王季铁主编 . 微特电机应用技术手册 .第一版. 上海:上海科学技术出版社 .2003.郭庆鼎主编 . 现代永磁电动机交流伺服系统 . 第一版 . 北京:中国电力出版 社.2006.赵俊生主编 . 数控机床控制技术基础 .第一版. 北京:化工出版社 .2006. 廖常初主编.PLC编程及应用.第一版.北京:机械工业出版社.2006.郭庆鼎,王成元主编 . 交流伺服系统 . 第一版 . 北京:机械工业出版社 .1994.廖效果,刘又午 编著. 数控技术. 第一版. 武汉: 湖北科学技术出版社 .20
54、00.王爱玲,白恩远,赵学良编著 . 现代数控机床 .第三版. 现代数控机床 . 北京:国 防工业出版社 .2004.电力电子及电气传动实验台实验指导书 . 第一版 . 杭州求是科教设备有限公 司.2001.廖常初编著.FX系列PLC编程及应用.第一版.北京:机械工业出版社.2007.李恩光主编 . 机电伺服控制技术 . 上海.第一版. 东华大学出版社 .2003.李永东编著 .交流电机数字控制系统 . 第一版. 北京:机械工业出版社 .2003.钱平主编 . 伺服系统 . 第一版. 北京:机械工业出版社 .2005.吴祖育,秦鹏飞主编 . 数控机床 . 第一版. 上海:上海科学技术出版社 .
55、1989.王永章主编 . 机床的数字控制技术 . 第一版 . 哈尔滨:哈尔滨工业大学出版 社.1995.MITSUBISHI ELECTRICCORPORATION.FSXeries Programmable Controllers Programming Manual,2002MITSUBISHI ELECTRIC CORPORATION2.NFSXeries Programmable Controllers Programming Manual,1999I.Boldea and Sayed A.N.Linear electric actuators and generator.London
56、:Cambridge University Press,1997.Jack F.G and Zbigniew J.P.Linear synchronous motors:transportation and automation systems.NewYork:CRC Press,2000andGeorge W.Y.Industrial servo control systems:Fundamentals Applications.Second Edition.Wisconsin:Marcel Dekker,Inc.2003.Karl Heinz-John,Micheal Tiegelkamp.IEC1131-3:Programming Industrial Automation Systems,Springer-Verlag Benlin Heidelberg.2001
- 温馨提示:
1: 本站所有资源如无特殊说明,都需要本地电脑安装OFFICE2007和PDF阅读器。图纸软件为CAD,CAXA,PROE,UG,SolidWorks等.压缩文件请下载最新的WinRAR软件解压。
2: 本站的文档不包含任何第三方提供的附件图纸等,如果需要附件,请联系上传者。文件的所有权益归上传用户所有。
3.本站RAR压缩包中若带图纸,网页内容里面会有图纸预览,若没有图纸预览就没有图纸。
4. 未经权益所有人同意不得将文件中的内容挪作商业或盈利用途。
5. 装配图网仅提供信息存储空间,仅对用户上传内容的表现方式做保护处理,对用户上传分享的文档内容本身不做任何修改或编辑,并不能对任何下载内容负责。
6. 下载文件中如有侵权或不适当内容,请与我们联系,我们立即纠正。
7. 本站不保证下载资源的准确性、安全性和完整性, 同时也不承担用户因使用这些下载资源对自己和他人造成任何形式的伤害或损失。