压力容器现场组焊工艺标(校对版)
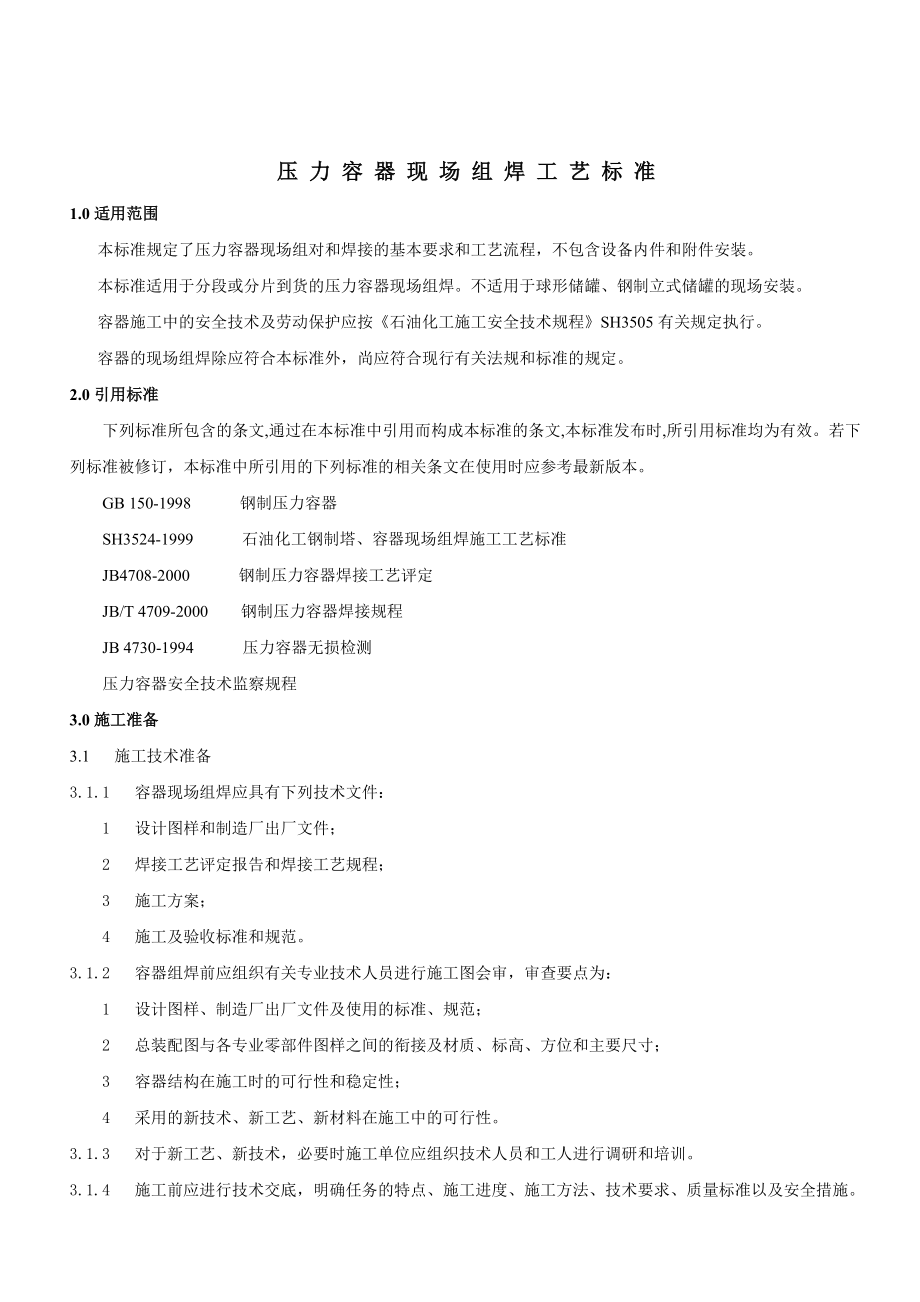


《压力容器现场组焊工艺标(校对版)》由会员分享,可在线阅读,更多相关《压力容器现场组焊工艺标(校对版)(22页珍藏版)》请在装配图网上搜索。
1、压 力 容 器 现 场 组 焊 工 艺 标 准1.0适用范围本标准规定了压力容器现场组对和焊接的基本要求和工艺流程,不包含设备内件和附件安装。本标准适用于分段或分片到货的压力容器现场组焊。不适用于球形储罐、钢制立式储罐的现场安装。容器施工中的安全技术及劳动保护应按石油化工施工安全技术规程SH3505有关规定执行。容器的现场组焊除应符合本标准外,尚应符合现行有关法规和标准的规定。2.0引用标准下列标准所包含的条文,通过在本标准中引用而构成本标准的条文,本标准发布时,所引用标准均为有效。若下列标准被修订,本标准中所引用的下列标准的相关条文在使用时应参考最新版本。GB 150-1998 钢制压力容器
2、SH3524-1999 石油化工钢制塔、容器现场组焊施工工艺标准JB4708-2000 钢制压力容器焊接工艺评定JB/T 4709-2000 钢制压力容器焊接规程JB 4730-1994 压力容器无损检测压力容器安全技术监察规程3.0施工准备3.1 施工技术准备3.1.1 容器现场组焊应具有下列技术文件:1 设计图样和制造厂出厂文件;2 焊接工艺评定报告和焊接工艺规程;3 施工方案;4 施工及验收标准和规范。3.1.2 容器组焊前应组织有关专业技术人员进行施工图会审,审查要点为:1 设计图样、制造厂出厂文件及使用的标准、规范;2 总装配图与各专业零部件图样之间的衔接及材质、标高、方位和主要尺寸
3、;3 容器结构在施工时的可行性和稳定性;4 采用的新技术、新工艺、新材料在施工中的可行性。3.1.3 对于新工艺、新技术,必要时施工单位应组织技术人员和工人进行调研和培训。3.1.4 施工前应进行技术交底,明确任务的特点、施工进度、施工方法、技术要求、质量标准以及安全措施。3.1.5 现场组对安装的压力容器在施工前,应按照国家质量技术监督局制订的压力容器安全技术检察规程向压力容器使用登记所在地的安全检察机构进行申报。申报的内容有:压力容器的名称、数量、制造单位、使用单位、安装单位及安装地点;申报资料包括:制造和安装单位资质,特殊施工人员岗位资质、质保手册和质保体系、施工方案等。 3.2 施工现
4、场准备3.2.1施工现场应按施工平面图进行布置,场地平整、道路畅通。组焊平台和施工机具应按规定位置就位。3.2.2施工机具应性能可靠;工卡具、样板应合格;计量器具应在鉴定周期内。3.2.3半成品、零部件及焊接应按施工方案要求运进施工现场。3.2.4现场的消防器材、安全设施应符合要求,并经安全监督部门验收通过。4 .0 设备到货验收4.1进入现场的容器半成品、零部件必须具有下列出厂技术文件: 1、装箱单; 2、压力容器产品安全质量监督检查证书; 3、 产品质量证明文件;其中,材料质量证明书上至少应列出以下项目:炉(罐)号、批号,实测的化学成分和机械性能(包括,b、s、5、k,对于奥氏体不锈钢可不
5、提供k值)及供货熔炼热处理状态;对于低温(-20)设备用材料还应提供夏比“V”形缺口试样的冲击值;产品合格证明书上至少应包括:规格、尺寸、焊接工艺、热处理工艺、修补记录、拆除卡具位置及排版图等项内容;现场设备的筒体或瓣片上的材料代号、组装(排板)编号、焊接人员代号等均应有醒目的标记、且应于排板图相一致。 4、其他技术文件。4.2各零部件几何尺寸的允许偏差应符合设计文件和标准SH3524-1999的要求。4.3容器半成品的坡口表面应符合下列要求: 1、坡口尺寸符合图样规定,表面应平滑; 2、熔渣、氧化皮应清除干净; 3、坡口表面不得有裂纹、分层、夹渣等缺陷。5.0 现场组装5.1 一般规定5.1
6、.1 现场组焊的容器应按本标准的要求验收合格后方可组装。5.1.2 容器的组装,应按设计图样、排版图和施工方案的要求进行。5.1.3 容器主要受压部分的焊接接头分为A、B、C、D四类 1、圆筒部分的纵向接头、球形接头与圆筒连接的环向接头、各类凸形封头中的所有拼焊接头以及嵌入式接管与壳体对接连接的接头,均属于A类焊接接头; 2、壳体部分的环向接头、锥形封头小端与接管连接的接头、长颈法兰与接管连接的接头,均属B类焊接接头,但已规定为A、C、D类的焊接接头除外; 3、平盖、管板与圆筒非对接连接的接头,法兰与壳体、接管非对接连接的接头,内封头与圆筒的搭接接头,均属于C类焊接接头; 4、接管、人孔、凸缘
7、及补强圈等与壳体连接的焊接接头,均属于D类焊接接头,但已规定为A、B类的焊接接头除外。5.1.4 容器现场组装宜采用如下程序:在钢平台上组焊上、下封头筒节组焊筒节和封头组焊筒节之间组焊裙座与下封头组焊分段壳体组焊在分段壳体内划出基准圆,进行内固定件划线、开孔组焊接管,组焊内固定件及外加固圈壳体组焊。5.1.5 复合钢板的筒节组装时,以复层为基准,防止错边超标。定位板与组对卡具应焊在基层,防止损伤复层,5.1.6 不锈钢和复合钢板复层表面在组装时不得采用碳钢制工具直接敲打。局部伤痕等影响耐腐蚀性能的缺陷,必须进行修磨,修磨后的厚度不应小于名义厚度减去钢板负偏差。5.1.7 在基础上组装必须在基础
8、验收合格后进行。基础验收按静设备安装的有关规定进行。5.2 封头、筒节的组装5.2.1分瓣封头应按下列程序组装:1 在钢平台上划出组装基准圆,将基准圆按照封头的分瓣数n等分,至少在距等分线两侧约100 mm.处各设置一块定位板;2 在组装基准圆内,设置封头组装胎具,以定位板和组装胎具为基准,用工卡具使瓣片紧靠定位板和胎具,并调整对口间隙和错边量。5.2.2 瓣片在钢平台上组队成封头后,应对每道焊口进行检查,检测结果应符合SH3524-1999的要求。5.2.3 封头焊接后的几何尺寸应符合下列要求:1 棱角E值不得大于名义厚度n的1/10加2 mm,且不大于5 mm;2 圆度e应符合本标准第5.
9、2.2条第4款的要求;3 封头几何尺寸偏差应符合SH3524-1999的规定。5.2.4 封头经检验合格后,按排版图定出0、90、180、270四条方位母线并作上标记,按开孔方位图组焊接管。5.2.5 筒节组对前,应根据每圈板片数n和封头端部实际周长在钢平台上划出筒体基准圆,在基准圆内侧每隔10001500 mm焊一块定位板。5.2.6 筒节组对时,应按照排版图将同一圈的板片按顺序逐块吊至基准圆外,使用工卡具进行组对。5.2.7 筒节组对完,应按要求检查:对口间隙、对口错边量、对口后纵缝棱角E、圆筒e、相邻两筒节外圆周长差以及筒体的长度允许偏差,允许偏差要求参照SH3524-1999。5.2.
10、8 对于直径较大、钢性较差的筒节和封头,应根据具体情况采取十字形和米字形临时加固措施,加固件应支撑在圆弧加强板上。5.3 壳体组焊5.3.1 壳体组装可根据施工现场情况采取立装法和卧装法施工。5.3.2 壳体立装可采用分段组装或利用基础由下至上逐段组装。其主要施工程序如下:1 分段组装首先确定分段位置,然后按排版图进行分段组装。分段宜参照下列原则进行:a 有利于现场施工作业,尽量减少高处作业;b 符合现场吊装能力;c 接口宜设在同一材质、同一厚度的直筒段,并避开接管;2 组对时,在上口内或外侧约每隔1000mm焊一块定位板,再将上面一圈筒节吊放上去,在对口处每隔1000mm放间隙片一块,间隙片
11、的厚度应以保证对口间隙为原则,同时上、下两圈筒节的四条方位母线必须对正,其偏差不得大于5mm;3 用调节丝杠调整间隙,用卡子,销子调整对口错边量,使其沿圆周均匀分布,防止局部超标,符合要求后,进行定位焊。5.3.3 壳体卧装主要施工顺序为:上段壳体中段壳体下段壳体底段壳体(含裙座)。其主要施工要领如下:1 在滚轮架或其他胎具上组对。胎具设置应尽量避免地基不均匀沉陷和壳体局部变形;摆放支座处的地基必须坚实,支座的数量应视分段的长度和重量经计算确定,其位置应避开壳体、人孔和接合管;2 用滚轮架时,两滚轮与壳体的中心夹角宜为6070;3 两段对口前,必须将两段的对口端的周长差,换算成直径差。在对口时
12、应将差值匀开,以免错边集中在局部而造成超标;4 各段壳体吊到滚轮架或胎具支座上时,四条方位母线应对正。对口时,应以各分段的对口基准圆为准,调整间隙及错变量。并用0.51 mm钢丝检查两筒体对口后的直线度,合格后进行定位焊。5 卧装时,各分段壳体上的人孔及接合管宜在壳体成型并检验合格后进行安装。5.3.4 壳体环缝组对后应满足下列要求:1 错边量应符合SH3524-1999的要求,当两板厚度不等时,对口错边量允许值应以较薄板厚为基准进行计算,测量时不应计入两板厚度差值;2 组对后形成的棱角E,用长度不小于300 mm的直尺检查,E值不得大于钢板厚度n的1/10加2 mm,且不大于3 mm;3 相
13、邻筒节的A类接头焊缝中心线间外圆弧长以及封头A类接头焊缝中心线与相邻筒节的A类接头焊缝中心线间外圆弧长应大于钢板厚度n的3倍,且不小于100mm;4 壳体分段组焊后,应按照排版图上的方位在各段内外壁校准相隔90的四条方位母线,并在壳体内壁距端部200500 mm处划出基准圆,作为整体组装及内构件组装的基准。5.3.5 分段壳体检验合格后,进行内构件的划线、组焊,合格后方可将各分段壳体组装成整体。6.0焊接工艺要求6.1焊接工艺评定要求施焊下列各类焊缝的焊接工艺必须按JB4708标准评定合格:a 受压元件焊缝;b 与受压元件相焊的焊缝;c 熔入永久焊缝内的定位焊缝;d 上述焊缝的返修焊缝。6.2
14、焊接工艺卡的编制要求a) 所有形式的焊缝焊接前必须编制焊接工艺卡;b) 焊接工艺卡的编制应依据焊接工艺评定要求进行;c) 焊接工艺卡由焊接责任工程师编制,项目技术负责人审核;d) 焊接工艺卡的编制内容参考附录表格。6.3焊工资格审查要求6.3.1施焊下列各类焊缝的焊工必须按锅炉压力容器焊工考试规则规定考试合格。a) 受压元件焊缝;b) 与受压元件相焊的焊缝;c) 熔入永久焊缝内的定位焊缝;d) 受压元件母材表面耐蚀焊缝。3.3.2焊工持证项目必须包含或与施焊项目一致。3.3.3必须对所有施焊焊工进行登记,编制合格焊工登记表。6.4焊接材料6.4.1焊接材料包括焊条、焊丝、钢带、焊剂、气体、电极
15、和衬垫等。6.4.2焊接材料选用原则:应根据母材的化学成分、力学性能、焊接性能,并结合压力容器的结构特点、使用条件及焊接方法综合考虑选用焊接材料,必要时通过试验确定。6.4.3焊缝金属的性能应高于或等于相应母材标准规定值的下限或满足图样规定的技术要求。对各类钢的焊缝金属要求如下:1相同钢号相焊的焊缝金属应保证力学性能,且其抗拉强度不应超过母材标准规定的上限值加30Mpa。耐热心型低合金钢的焊缝金属还应保证化学成分。2高合金钢的焊缝金属应保证力学性能和耐腐蚀性能。3不锈钢复合钢基层的焊缝金属应保证力学性能,且其抗拉强度不应超过母材标准规定的上限值加30Mpa;复层的焊缝金属应保证耐腐蚀性能,当有
16、力学性能要求时还应保证力学性能。4复层焊缝与基层焊缝以及复层焊缝与基层钢板的交界处宜采用过渡焊缝。5不同强度钢号的碳素钢、低合金钢之间的焊缝金属应保证力学性能,且其抗拉强度不应超过强度较高母材标准规定的上限值。6奥氏体高合金钢与碳素钢或低合金钢之间的焊缝金属应保证抗裂性能和力学性能。6.4.4焊接材料的选用,一般情况下要求与焊接工艺评定上所使用的材料一致,也可参考下表进行选用(常用)。钢号焊条电弧焊CO2气保焊氩弧焊焊 条焊丝钢号(标准号)焊丝钢号(标准号)型号(标准号)牌号示例Q235-BQ235-C20G,20g20R,20(锻)E4316(GB/T5117)J426H08MnSi(GB/
17、T14958)E4315(GB/T5117)J42716Mn,16MnRE5016(GB/T5117)J506H08Mn2SiA(GB/T14958)H10MnSi(GB/T14957)E5015(GB/T5117)J50712CrMo12CrMo GE5515-B1(GB/T5118)R207H08CrMoA(GB/T14957)15CrMo15CrMo G15CrMo RE5515-B2(GB/T5118)R307H13CrMoA(GB/T14957)12CrMoV12CrMoVGE5515-B2-V(GB/T5118)R317H08CrMoVA(GB/T14957)1Cr5MoE5MoV
18、-15(GB/T5118)R-5070Cr18Ni9E308-16(GB/T983)A102H0Cr21Ni10(YB/T5091)E308-15(GB/T983)A1070Cr18Ni10Ti1Cr18Ni9TiE347-16(GB/T983)A132H0Cr21Ni10Ti(YB/T5091)E347-15(GB/T983)A1370Cr17Ni12Mo2E316-16(GB/T983)A202H0Cr19Ni12Mo2(YB/T5091)E316-15(GB/T983)A2070Cr18Ni12Mo2TiE316L-16(GB/T983)A022H00Cr19Ni12Mo2(YB/T50
19、91)E318L-16(GB/T983)A2120Cr19Ni13Mo3E317L-16(GB/T983)H0Cr20Ni14Mo3(YB/T5091)00Cr19Ni10E308L-16(GB/T983)A002H00Cr21Ni10(YB/T5091)00Cr17Ni14Mo2E316L-16(GB/T983)A02200Cr19Ni13Mo3E317L-16(GB/T983)A2420Cr13E-410-16(GB/T983)G202E-410-15(GB/T983)G2076.5焊前准备6.5.1 焊条、焊剂按规定烘干、保温,常用焊材烘干温度及保持时间下表;焊丝需去除油、锈;保护气体应
20、保持干燥。常用焊材烘干温度及保持时间类别牌号温度,时间,h碳钢和低合金钢焊条J4221501J4263001J4273501J5021501J506,5073501J506RH,J507RH3504301J507MoW3501J5573501J556RH4001J606,J6073501J607RH3504301J7073501J707RH4002低温钢焊条W607,W7073501钼和铬钼耐热钢焊条R207,R3073501R307H4001R317,R407,R5073501铬镍不锈钢焊条A1021501A1072501A1321501A1372501A2021501A2072501A00
21、2,A022,A212,A2421501铬不锈钢焊条G2021501G2072501G3021501G3072003001熔炼焊剂HJ4312502HJ350,HJ2603004002HJ2503003502烧结焊剂SJ1013003502SJ1026.6 预热6.6.1 根据母材的化学成分、焊接性能、厚度、焊接接头的拘束程度、焊接方法和焊接环境等综合考虑是否预热,必要时通过试验(工艺评定)确定。常用钢号推荐的预热温度见下表。钢号厚度,mm预热温度,20G,20,20R,20g3050505010010010015016Mn,16MnR15MnVR,15MnNbR30501005015020M
22、nMo20MnMoD08MnNiCrMoVD任意厚度10007MnCrMoVR07MnNiCrMoVDR163060304080405010013MnNiMoNbR18MnMoNbR任意厚度15018020MnMoNb任意厚度20012CrMo,15 CrMo12CrMoG,15 CrMoR15 CrMoG1015012Cr1MoV12Cr1MoVG14Cr1MoR14Cr1Mo12Cr2Mo,12Cr2Mo112Cr2MoG,12Cr2Mo1R62001Cr5Mo任意厚度2506.6.2 不同钢号相焊时,预热温度按预热温度要求较高的钢号选取。6.6.3 采取局部预热时,应防止局部应力过大。预
23、热的范围为焊缝两侧各不小于焊件厚度的3倍,且不小于100mm。6.6.4 需要预热的焊件在整个焊接过程中应不低于预热温度。6.6.5 当用热加工法下料、开坡口、清根、开槽或施焊临时焊缝时,亦需考虑预热要求。6.7 组对定位6.7.1 组对时,坡口间隙、错边量、棱角度等应符合规定。6.7.2 尽量避免强力组装,定位焊缝间距应符合规定。6.7.3 焊接接头拘束度大时,推荐采用抗裂性能更好的焊条施焊。6.7.4 定位焊缝不得有裂纹,否则应清除重焊。如存在气孔、夹渣时亦应去除。6.7.5 熔入永久焊缝内的定位焊缝两端应便于接弧,否则应予修整。6.8 焊接6.8.1 焊前应按接头编制焊接工艺规程(推荐表
24、格见附录),焊工应按图样、工艺文件、技术标准施焊。6.8.2 焊接环境:焊接环境出现下列任一情况时,须采取有效防护措施,否则禁止施焊。 a) 风速:气体保护焊时大于2m/s,其他焊接方法大于10m/s; b) 相对湿度大于90%; c) 雨雪环境; d) 焊件温度低于-20。e)当焊件温度为0-20时,应在始焊处100mm范围内预热到15以上。6.8.3 应在引弧板或坡口内引弧,禁止在非焊接部位引弧。纵焊缝应在引出板上收弧,弧坑应填满。6.8.4 防止地线、电缆线、焊钳与焊件打弧。6.8.5 电弧擦伤处的弧坑需经修磨,使其均匀过渡到母材表面,修磨的深度应不大于该部位钢材厚度s的5%且不大于2m
25、m,否则应予补焊。6.8.6 对有冲击试验要求的焊件应当认真控制线能量,每条焊道的线能量都不高于评定合格数值。6.8.7 用焊条电弧焊或气焊焊接管子时,一般应采用多层焊,各焊层焊道的接头应尽量错开。6.8.8 受压元件角焊缝的根部应保证焊透。6.8.9 双面焊须清理焊根,显露出正面打底的焊缝金属。对于自动焊,若经试验确认能保证焊透,亦可不作清根处理。6.8.10 接弧处应保证焊透与熔合。6.8.11 施焊过程中应控制层间温度不超过规定的范围。当焊件预热时,应控制层间温度不得低于预热温度。6.8.12 每条焊缝应尽可能一次焊完。当中断焊接时,对冷裂纹敏感的焊件应及时采取后热、缓冷等措施。重新施焊
26、时,仍需按规定进行预热。6.8.13 采用锤击消除残余应力时,第一层焊缝和盖面层焊缝不宜锤击。6.8.14 引弧板、引出板、产品焊接试板不应锤击拆除。6.9后热6.9.1 对冷裂纹敏感性较大的低合金钢和拘束度较大的焊件应采取后热措施。6.9.2 后热应在焊后立即进行。6.9.3 后热温度一般为200350,保温时间与焊缝厚度有关,一般不低于0.5h。6.9.4 若焊后立即进行热处理则可不做后热。6.10 焊缝返修6.10.1 对需要焊接返修的缺陷应当分析产生原因,提出改进措施,按评定合格的焊接工艺,编制焊接返修工艺。6.10.2 焊缝同一部位返修次数不宜超过二次。6.10.3 返修前需将缺陷清
27、除干净,必要时可采用表面探伤检验确认。6.10.4 待补焊部位应开宽度均匀、表面平整、便于施焊的凹槽,且两端有一定坡度。6.10.5 如需预热,预热温度应较原焊缝适当提高。6.10.6 返修焊缝性能和质量要求应与原焊缝相同。6.11 焊接检验6.11.1 焊接检验主要方面1 焊前: a) 母材、焊接材料;b) 焊接设备、仪表、工艺装备;c) 焊接坡口、接头装配及清理;d) 焊工资格;e) 焊接工艺文件。2 施焊过程中: a) 焊接规范参数;b) 执行焊接工艺情况;c) 执行技术标准情况;d) 执行图样规定情况。7.0 焊后热处理7.1 根据母材的化学成分、焊接性能、厚度、焊接接头的拘束程度、容
28、器使用条件和有关标准综合确定是否需要进行焊后热处理。7.2 压力容器或受压元件焊后热处理厚度PWHT按如下规定选取。1 等厚度全焊透对接接头的焊后热处理厚度PWHT为其焊缝厚度,也即容器或其受压元件钢材厚度s。焊缝厚度是指焊缝横截面中,从焊缝正面到焊缝背面的距离(余高不计)。2 不等厚焊接接头的焊后热处理厚度PWHT:a对接接头取其较薄一侧母材厚度。b 焊接返修时,取其所填充的焊缝金属厚度。7.3 常用钢号的焊后热处理规范见下表。钢号焊后热处理温度(电弧焊)最短保温时间(h)10Q235-A,20Q235-B,20RQ235-C,20G20g6006401 当焊后热处理厚度PWHT50mm时为
29、PWHT/25h,但最短时间不低于1/4h当焊后热处理厚度PWHT50mm时为(2+1/4(PWHT-50)/25)h09MnD58062016MnR60064016Mn, 16MnD, 16MnDR15MnVR,15MnNbR54058020MnMo, 20MnMoD58062018MnMoNbR13MnNiMoNbR60064020MnMoNb07MnCrMoVR07MnNiCrMoVDR08MnNiCrMoVD55059009MnNiD,09MnNiDR15MnNiDR54058012CrMo12CrMoG6001 当焊后热处理厚度PWHT125mm时为PWHT/25h,但最短时间不低于
30、1/4h当焊后热处理厚度PWHT125mm时为(5+1/4(PWHT-125)/25)h15CrMo15CrMoG60015CrMoR12Cr1MoV12Cr1MoVG14Cr1MoR14Cr1Mo64012Cr2Mo12Cr2Mo112Cr2Mo1R12Cr2Mo1G6601Cr5Mo660当碳素钢、强度型低合金钢焊后热处理温度低于表6规定温度的下限值时,最短保温时间如下表规定。比规定温度范围下限值降低温度数值,降低温度后最短保温时间,252554801011020最短保温时间适用于焊后热处理厚度PWHT不大于25mm焊件,当焊后热处理厚度PWHT大于25mm时,厚度每增加25mm,最短保温
31、时间应增加15min。仅适用于碳素钢和16MnR钢。8.0压力试验和气密试验8.1 一般规定8.1.1 容器的压力试验和气密试验应按图样规定执行,容器的压力试验包括液压和气压试验。8.1.2 压力试验时试验介质应符合下列要求:1 试验液体可采用清洁淡水,需要时也可采用不会导致发生危险的其它液体。试验时液体的温度应低于其闪点或沸点;2 奥氏体不锈钢容器用水作介质试压时,水质的氯离子含量不得超过25mg/L;3 气压试验所用气体应为干燥洁净的空气、氮气或其它惰性气体。脱脂后的容器气压试验时,必须采用不含油气体。8.1.3 压力试验介质的温度控制如下: 1 碳钢、16MnR和正火15MnVR钢制容器
32、液压试验时液体的温度不得低于5;其余低合金钢制容器液压试验时液体的温度不得低于15,如果由于板厚等因素会造成材料无延性转变温度升高,则需相应提高试验液体温度;2 其它钢种制成的容器压力试验温度按图样要求;3 碳素钢和低合金钢制成的容器气压试验时,介质温度不得低于15,其它钢种制成的容器气压试验的介质温度应符合图样要求;8.1.4 容器压力试验前,必须对下列资料审查确认:1 容器质量证明书;2 容器附件及内件合格证书;3 设计修改及现场签证;4 容器组装及隐蔽记录;5 焊接记录(附合格焊工名单);6 无损检测报告;7 容器热处理记录。8.1.5 试压试验应有方案,并由本单位安全部门检查监督。8.
33、1.6 容器压力试验前应做好下列工作:1 检查容器外形、焊接接头及管件附件是否符合图样要求,连接螺栓垫片是否已全部紧固;2 检查容器内部,清除异物,封闭所有开孔。图样注明不耐钢的部件应予拆除或用盲板隔离;3 容器试压时,在容器最高处设放空点,在最低处设放排点;4 在容器最高处与最低处设置两块量程相同的压力表,并应避免安置在加压管路附近;5 压力表的精度为低压容器2.5 级,中压容器 1.5 级;6 试验压力读书以最高处压力表为准;7 气压试验前容器顶部应配置调试合格的安全阀。8.1.7 容器试压过程中,如发现缺陷应先卸压,经处理后再重新试压。8.1.8 压力试验过程中,不得对受压元件进行任何修
34、理,如果发现有异常响声、压力下降、油漆剥落应立即停止试验并卸压,查明原因。经处理后方可恢复压力试验。8.1.9 立式容器卧置进行水压试验时,试验压力应为立置的试验压力加设备高度的静压力。8.1.10 容器压力试验完毕,应先将容器最顶部放空阀门打开,然后从底部排放液体,以避免容器抽空变形。8.1.11 容器试压介质排完后,应将试压辅助部件全部拆除。8.1.12 压力试验完毕后,应填写“压力试验报告”,并由建设单位/监理单位、监检部门、施工单位等有关单位签字确认。8.2液压试验8.2.1 充水前试压系统、放空阀门及压力表,按规定安装完毕。8.2.2 充水时,先打开放空阀门,水从容器顶部溢出时,将放
35、空阀门关闭,检查各开孔及接头处有无渗漏。8.2.3 试验压力应缓慢上升,达到规定试验压力值,保持时间不少于30min。然后将压力将至设计压力。对所有的焊接接头和连接部位进行全面检查,符合下列情况,即认为合格: 1 无渗漏;2 无可见的变形;3 试验过程中无异常的响声;4 对抗拉强度下限值b大于540Mpa的材料,经表面无损检测抽查未发现裂纹。8.2.4 大型容器卧置水压试验时,充水前应对容器强度、局部稳定性进行核算。在充水过程中必须注意观察容器各支承点的变形情况。8.2.5 大型容器立置试压前要确定观测点,在充水过程中必须注意观察基础沉降情况。8.2.6 液压试验结束后,应将容器内液体排尽,必
36、要时用压缩空气将容器内部吹干。8.2.7 采用其它介质试压时按图样要求并参照上述方法进行。8.3气压试验8.3.1 气压试验方案或技术措施应经安全技术部门确认,由单位技术总负责人批准。8.3.2 气压试验时,试压区应设计警戒线,试验单位的安全部门应进行现场监督。8.3.3 气压试验时,应缓慢升压至规定试验压力的10%,且不超过0.05Mpa,保压5min ,然后对所有焊接接头和连接部位进行初次泄漏检查,如有泄漏,修补后重新试验。初次泄漏检查合格后,再继续缓慢升压至规定试验压力的50%,其后按每级为规定试验压力的10%的级差逐级升压至规定的试验压力,保压10min后将压力降至规定试验压力的87%
37、,并保持足够长的时间(不少于30min)后再次进行泄漏检查,无漏气、无可见的变形为合格。如有泄漏,修补后再按上述规定重新试验。卸压时应由放空阀缓慢降压,直至卸到常压。8.4气密试验8.4.1 容器需经液压试验合格后,方可进行气密试验。试验压力按图样规定。试验时压力应缓慢上升,达到规定试验压力后保持10min,然后降至设计压力,对所有的焊接接头和连接部位进行检查,不渗不漏为合格。8.4.2 作气压试验的压力容器,气压试验检查合格后如图样无规定可免做气密试验。9.0 施工记录a) 设备验收、清点记录b)现场设备组装记录c)现场设备预热及热处理记录d)实际施焊记录;e)焊缝外观及尺寸;f)后热、焊后
38、热处理;g)产品焊接试板、鉴证环;h)金相检验和断口检验(根据材质确定);i)无损检测报告;j)压力试验报告;k)致密性试验报告;l)压力容器应有地方监检部门的监检报告。12.0附录:(单 位 名 称)焊 接 工 艺 卡焊接工艺卡编号 产品编号 项 目 用 户 位 号 图 号 名 称 版次阶段说明修改标记及处数编制人及日期审核人及日期备注接 头 编 号 表焊接工艺规程接头编号示意图接头编号焊接工艺卡编号焊接工艺评定编号焊工持证项目无损检测要求注:如产品结构复杂,可另作一页不含表格的接头编号示意图。焊 接 材 料 汇 总 表焊接工艺规程母材焊条电弧焊SMAW埋弧焊SAW气体保护焊MIG/TIG焊条/规格烘干温度/时间焊丝/规格焊剂烘干温度/时间焊丝/规格保护气体纯度容 器 技 术 特 性部位设计压力,MPa设计温度,试验压力,MPa焊接接头系数容器类别备 注接 头 焊 接 工 艺 卡接头简图:焊接顺序焊接工艺卡编号图号接头名称接头编号焊接工艺评定报告编号焊工持证项目检 验序号本人锅检所第三方或用户母材厚度,mm焊缝金属厚度,mm焊接位置层-道焊接方法填充材料焊接电流电弧电压(V)焊接速度(cm/min)线能量(KJ/cm)施焊技术牌号直径极性电流(A)预热温度()层间温度()焊后热处理后热钨极直径脉冲频率脉宽比(%)气体成分气体流量正面背面
- 温馨提示:
1: 本站所有资源如无特殊说明,都需要本地电脑安装OFFICE2007和PDF阅读器。图纸软件为CAD,CAXA,PROE,UG,SolidWorks等.压缩文件请下载最新的WinRAR软件解压。
2: 本站的文档不包含任何第三方提供的附件图纸等,如果需要附件,请联系上传者。文件的所有权益归上传用户所有。
3.本站RAR压缩包中若带图纸,网页内容里面会有图纸预览,若没有图纸预览就没有图纸。
4. 未经权益所有人同意不得将文件中的内容挪作商业或盈利用途。
5. 装配图网仅提供信息存储空间,仅对用户上传内容的表现方式做保护处理,对用户上传分享的文档内容本身不做任何修改或编辑,并不能对任何下载内容负责。
6. 下载文件中如有侵权或不适当内容,请与我们联系,我们立即纠正。
7. 本站不保证下载资源的准确性、安全性和完整性, 同时也不承担用户因使用这些下载资源对自己和他人造成任何形式的伤害或损失。