机床数控技术课程设计参考资料
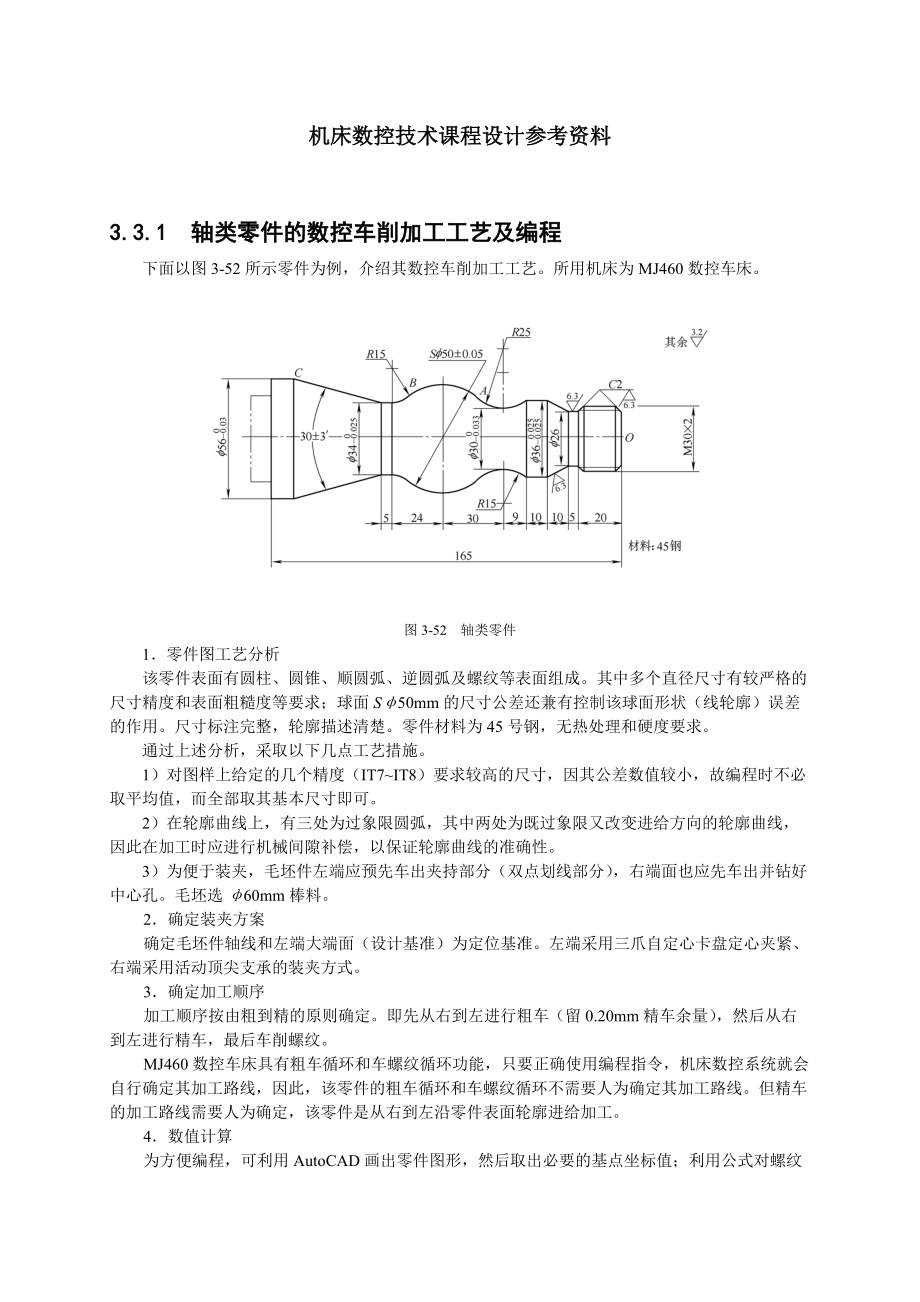


《机床数控技术课程设计参考资料》由会员分享,可在线阅读,更多相关《机床数控技术课程设计参考资料(11页珍藏版)》请在装配图网上搜索。
1、机床数控技术课程设计参考资料3.3.1 轴类零件的数控车削加工工艺及编程下面以图3-52所示零件为例,介绍其数控车削加工工艺。所用机床为MJ460数控车床。图3-52 轴类零件1零件图工艺分析该零件表面有圆柱、圆锥、顺圆弧、逆圆弧及螺纹等表面组成。其中多个直径尺寸有较严格的尺寸精度和表面粗糙度等要求;球面S50mm的尺寸公差还兼有控制该球面形状(线轮廓)误差的作用。尺寸标注完整,轮廓描述清楚。零件材料为45号钢,无热处理和硬度要求。通过上述分析,采取以下几点工艺措施。1)对图样上给定的几个精度(IT7IT8)要求较高的尺寸,因其公差数值较小,故编程时不必取平均值,而全部取其基本尺寸即可。2)在
2、轮廓曲线上,有三处为过象限圆弧,其中两处为既过象限又改变进给方向的轮廓曲线,因此在加工时应进行机械间隙补偿,以保证轮廓曲线的准确性。3)为便于装夹,毛坯件左端应预先车出夹持部分(双点划线部分),右端面也应先车出并钻好中心孔。毛坯选60mm棒料。2确定装夹方案确定毛坯件轴线和左端大端面(设计基准)为定位基准。左端采用三爪自定心卡盘定心夹紧、右端采用活动顶尖支承的装夹方式。3确定加工顺序加工顺序按由粗到精的原则确定。即先从右到左进行粗车(留0.20mm精车余量),然后从右到左进行精车,最后车削螺纹。MJ460数控车床具有粗车循环和车螺纹循环功能,只要正确使用编程指令,机床数控系统就会自行确定其加工
3、路线,因此,该零件的粗车循环和车螺纹循环不需要人为确定其加工路线。但精车的加工路线需要人为确定,该零件是从右到左沿零件表面轮廓进给加工。4数值计算为方便编程,可利用AutoCAD画出零件图形,然后取出必要的基点坐标值;利用公式对螺纹大经、小经进行计算。(1)基点计算 以图3-52上O点为工件坐标原点,则A、B、C三点坐标(mm)分别为: XA=40mm(直径量)、ZA=69 mm;XB=38.76 mm(直径量)、ZB=-99 mm;XC=56 mm(直径量)、ZC=154.09 mm。(2)螺纹大经、小经计算d大= d 0.2165p=300.21652=29.567 mm;d小= d大1.
4、299p=29.5671.2992=26.969mm。5选择刀具1)粗车、精车均选用35菱形涂层硬质合金外圆车刀,副偏角48,刀尖半径0.4mm,为防与工件轮廓发生干涉,必要时应用AutoCAD作图检验。2)车螺纹选用硬质合金60外螺纹车刀,取刀尖圆弧半径0.2mm。6选择切削用量(1)背吃刀量 粗车循环时,确定其背吃刀量ap=2mm;精车时,确定其背吃刀量ap=0.2mm。(2)主轴转速1)车直线和圆弧轮廓时的主轴转速:查表取粗车时的切削速度v=90m/min ,精车时的切削速度v=120m/min,根据坯件直径(精车时取平均直径),利用式n=1000v/d计算,并结合机床说明书选取:粗车时
5、,主轴转速n=500r/min;精车时,主轴转速n=1200r/min。2)车螺纹时的主轴转速:按公式np1200(n为主轴转速,p为螺距)。取主轴转速n=320r/min。(3)进给速度 粗车时,选取进给量f = 0.3 mm/r,精车时选取f = 0.05 mm / r。车螺纹的进给量等于螺纹导程,即f = 2mm/r。7数控加工工艺文件的制定1)按加工顺序将各工步的加工内容、所用刀具及其切削用量等填入表3-8数控加工工序卡片中。2)将选定的各工步所用刀具的型号、刀片型号、刀片牌号及刀尖圆弧半径等填入表3-9数控加工刀具卡片中。表3-8 数控加工工序卡片(工厂)数控加工工序卡产品名称或代号
6、零件名称材 料零件图号轴45工序号程序编号夹具名称夹具编号使用设备车 间三爪自定心卡盘MJ460工步号工 步 内 容加工面刀具号刀具规格主轴转速(rmin-1)进给量(mmr-1)背吃刀量(mm)备注1粗车轴外表面,留精车余量0.2mmT010135菱形5000.322精车轴外表面至尺寸T020235菱形12000.050.23车螺纹M302T0303603202见注编 制审 核批 准共 1 页第 1 页注:M30螺纹共分5次车削,但每次背吃刀量不同,查表3-7确定为(直径量):0.9、0.6、0.6、0.4、0.1(mm)。 表3-9 数控加工刀具卡片产品名称零件名称轴零件图号程序编号工 步
7、刀具号刀 具名 称刀 具型 号刀 片刀具位置补偿值刀尖半径(mm)刀尖位置备 注型 号牌 号X(mm)Z(mm)1T010135菱形可转位车刀000.432T020235菱形可转位车刀1.2030.7580.433T0303螺纹车刀2.3022.8190.28编 制审 核批 准共 1 页第 1 页例4-5 编写图3-52典型轴类零件的精加工程序,工件右段中心点O为工件坐标原点,2号刀为基准刀,该刀尖的起始位置为(280,130)。精加工程序如下:O3000; 程序名N010 G50 X280 Z130; 建立工件坐标系N020 M04 S1200 T0200; 启动主轴,换2号刀N030 G0
8、0 X26 Z3 M08; 快速接近工件,并打开冷却液N040 G42 G01 Z0 T0202 F0.05; 建立右刀补N050 X29.567 Z-2; 倒角N060 Z-18; 车螺纹外表面29.567N070 X26 Z-20; 倒角N080 W-5; 车26槽N090 U10 W-10; 车锥面N100 W-10; 车36外圆柱面N110 G02 U-6 W-9 R15; 车R15圆弧N120 G02 X40 Z-69 R25; 车R25圆弧N130 G03 X38.76 Z-99 R25; 车S50球面N140 G02 X34 W-9 R15; 车R15圆弧N150 G01 W-5
9、; 车34圆柱面N160 X56 Z-154.05; 车锥面N170 Z-165; 车56圆柱面N180 G40 G00 U10 T0200 M05 M09; 取消刀补并关闭冷却液N190 G28 U2 W2; 返回参考点N200 M04 S320 T0300; 主轴换速,换3号螺纹刀N210 G00 X40 Z3 T0303 M08; 刀具定位并建立位置补偿N220 G92 X28.667 Z-22 F2; 螺纹循环第一刀N230 X28.067; 螺纹循环第二刀N240 X27.467; 螺纹循环第三刀N250 X27.067; 螺纹循环第四刀N260 X26.969; 螺纹循环第五刀N2
10、70 G00 X45 T0300 M09; 取消刀具位置补偿并关冷却液N280 G28 U2 W2; 返回参考点N290 M30; 程序结束以上程序没有考虑粗加工,请同学们自己写出全部程序。3.3.3 盖板零件加工中心的加工工艺(属加工中心,不是数控铣床)盖板是机械加工中常见的零件,加工表面有平面和孔,通常需经过铣平面、钻孔、扩孔、镗孔、铰孔以及攻螺纹等工步才能完成。下面以图3-56所示盖板为例介绍其加工工艺。图3-56 盖板零件简图1分析图样,选择加工内容该盖板的材料为铸铁,故毛坯为铸件。由图3-56可知,盖板的四个侧面为不加工表面,全部加工表面都集中在A、B面上。最高精度为IT7级。从工序
11、集中和便于定位两个方面考虑,选择B面及位于B面上的全部孔在加工中心上加工,将A面作为主要定位基准,并在前道工序中先加工好。2选择加工中心由于B面及位于B面上的全部孔,只需单工位加工即可完成,故选择立式加工中心。加工表面不多,只有粗铣、精铣、粗镗、半精镗、精镗、钻、扩、锪 、铰及攻螺纹等工步,所需刀具不超过20把。选用国产TH5632型立式加工中心即可满足上述要求。该机床工作台工作面尺寸为1000mm320mm,x轴行程为750mm,y轴行程为400mm,z轴行程为470mm,主轴端面至工作台台面距离为180650mm,定位精度和重复定位精度分别为0.012mm和0.006mm,刀库容量为16把
12、,工件在一次装夹后可自动完成铣、钻、镗、铰及攻螺纹等工步的加工。3设计工艺(1)选择加工方法 B平面用铣削方法加工,因其表面粗糙度Ra6.3m,故采用粗铣精铣方案;60H7孔为已铸出毛坯孔,为达到IT7级精度和Ra0.8m的表面粗糙度,需经三次镗削,即采用粗镗半精镗精镗方案;对12H8孔,为防止钻偏和达到IT8级精度,按钻中心孔钻孔扩孔铰孔方案进行;16mm孔在12mm基础上锪至尺寸即可;M16螺纹孔采用先钻底孔后攻螺纹的加工方法,即按钻中心孔钻底孔倒角攻螺纹方案加工。(2)确定加工顺序 按照先面后孔、先粗后精的原则确定。具体加工顺序为粗、精铣B面;粗镗、半精镗、精镗60H7孔;钻各光孔和螺纹
13、孔的中心孔;钻、扩、锪、铰12 H8及16孔;M16螺孔钻底孔、倒角、和攻螺纹,详见表3-11。(3)确定装夹方案和选择夹具 该盖板零件形状简单,四个侧面较光整,加工面与不加工面之间的位置精度要求不高,故可选用通用台钳,以盖板底面A和两个侧面定位,用台钳钳口从侧面夹紧。(4)选择刀具 所需刀具有面铣刀、镗刀、中心钻、麻花钻、铰刀、立铣刀(锪16孔)及丝锥等,其规格根据加工尺寸选择。B面粗铣铣刀直径应选小一些,以减小切削力矩,但也不能太小,以免影响加工效率;B面精铣铣刀直径应选大一些,以减少接刀痕迹,但要考虑到刀库允许装刀直径(TH5632型加工中心的允许装刀直径:无相邻刀具为150mm,有相邻
14、刀具为80mm)也不能太大。刀柄柄部根据主轴锥孔和拉紧机构选择。(5)确定加工路线 B面的粗、精铣削加工加工路线根据铣刀直径确定,因所选铣刀直径为100mm ,故安排沿x方向两次进给(见图3-57)。所有孔加工进给路线均按最短路线确定,因为孔的位置精度要求不高,机床的定位精度完全能保证,图3-58 图3-62所示的即为各孔加工工步的加工路线。 图3-57 铣削B面加工路线图3-58 镗60H7孔加工路线图3-59 钻中心孔加工路线图3-60 钻、扩、铰12H8孔加工路线图3-61 锪16mm孔加工路线图3-62 钻螺纹底孔、攻螺纹加工路线(6)选择切削用量 查表确定切削速度和进给量,然后计算出
15、机床主轴转速和机床进给速度,详见表( 3-11)4数控加工工艺文件的制定(1)按加工顺序将各工步的加工内容、所用刀具及其切削用量等填入表3-11数控加工工序卡片中。(2)将选定的各工步所用刀具的名称、规格、刀辅具型号等填入表3-12数控加工刀具卡片中。表3-11 数控加工工序卡片(工厂)数控加工工序卡产品名称或代号零件名称材 料零件图号盖 板HT200工序号程序编号夹具名称夹具编号使用设备车 间台 钳TH5632工步号工 步 内 容加工面刀具号刀具规格(mm)主轴转速(rmin-1)进给速度(mmmin-1)背吃刀量(mm)备注1粗铣B平面留余量0.5mmT01100300703.52精铣B平
16、面至尺寸T13100350500.53粗镗60H7孔至58mmT0258400604半精镗60H7孔至59.95mmT0359.95450505精镗60H7孔至尺寸T0460H7500406钻412H8及4M16中心孔T0531000507钻412H8至10T0610600608扩412H8至11.85T0711.85300409锪416至尺寸T08161503010铰412H8至尺寸T0912H81004011钻4M16底孔至14T10144506012倒4M16底孔端角T11183004013攻4M16螺纹孔T12M16100200编 制审 核批 准共 1 页第 1 页表3-12 数控加工
17、刀具卡产品名称零件名称盖 板零件图号程序编号工 步刀具号刀 具名 称刀 柄型 号刀 具补偿量(mm)备 注直径(mm)长度(mm)1T01面铣刀1002T13面铣刀1003T02镗刀584T03镗刀59.955T04镗刀60H76T05中心钻37T06麻花钻108T07扩孔钻11.859T08阶梯铣刀1610T09铰刀12H811T10麻花钻1412T11麻花钻1813T12机用丝锥M16编 制审 核批 准共 1 页第 1 页数控线切割资料1、数控线切割机床的加工数控线切割机床,又称数控电火花线切割机床,其加工过程是利用一根移动着的金属丝(钼丝、钨丝或铜丝等)作工具电极,在金属丝与工件间通以脉
18、冲电流,使之产生脉冲放电而进行切割加工的。如图5-1所示,电极丝穿过工件上预先钻好的小孔(穿丝孔),经导轮由走丝机构带动进行轴向走丝运动。工件通过绝缘板安装在工作台上,由数控装置按加工程序指令控制沿X、Y两个坐标方向移动而合成所需的直线、圆弧等平面轨迹。在移动的同时,线电极和工件间不断地产生放电腐蚀现象,工作液通过喷嘴注入,将电蚀产物带走,最后在金属工件上留下细丝切割形成的细缝轨迹线,从而达到了使一部分金属与另一部分金属分离的加工要求。2走丝机构(1) 储丝筒组合件旋转时,其径向跳动小于0.01 mm;否则,可能引起钼丝抖动,出现断丝现象。将悬臂放置的走丝电机与轴承座连在一起,可增加其刚性,改
19、善受力情况,并且在结构工艺上容易保证与储丝筒的同轴度安装要求。(2) 为了保证储丝筒上整齐排绕钼丝,不出现叠丝现象,所以储丝筒组合件转动时,必须让储丝筒作相应的轴向位移,且轴向位移应平稳和轻便。在图5-2所示结构中,在储丝筒旋转的同时,通过二级齿轮减速传动带动丝杆转动,由于丝杆螺母副的作用而使得储丝筒所在的滑动走丝拖板相对于机床座体(丝架所在)产生轴向位移。如果二级齿轮传动中,每一级减速比为1 : 4,丝杆的螺距为2.75 mm,则当储丝筒转过一圈时,其轴向位移为1/162.75= 0.172 mm,就算用直径为( 0.15 mm的钼丝都不会产生叠丝。为了保证收丝方与放丝方不叠丝,可在丝架的上
20、面和下面各放一块硬质合金挡丝块,并特地偏开一定的距离(约1.5 mm)。(3) 储丝筒组合件由三相四极交流马达通过弹性联轴节直接带动,保证钼丝走速为810 m/s。采用弹性联轴节可以减缓因走丝换向带给储丝筒的冲击。 4) 为了循环使用钼丝,必须要让储丝筒能自动正反转换向。由于同时具有储丝筒拖板的轴向移动,所以可在合适位置上安装倒顺换向开关。这样,当储丝筒拖板往某一方向移动到压下换向开关时,机床电器线路将会使走丝电机自动反转,同时储丝筒开始反方向走丝,储丝筒拖板也相应地换向往回移动,直到碰到另一端的换向开关后再正转换向,如此反复,即达到循环走丝的目的。当然倒顺换向开关应做成可调节距离的形式,以适
21、应不同长度钼丝量的要求。倒顺换向开关的位置应调节到保证换向时,储丝筒上排丝的一方还有一定长度的钼丝;否则,会将丝冲断。3、快走丝线切割机床(1) 键盘输入。每次输入的程序最多可达380条,具有完备的检索、修改、删除、插入的功能。程序指令采用LED数码显示方式。 (2) 具有图形缩放功能,可放大一倍或缩小至一半。(3) 钼丝偏移功能。在工件切割前一次置入,内外偏移量最大为0.999 mm。 (4) 齿隙补偿功能。用于消除从步进电机到十字拖板间传动齿隙造成的误差,提高加工精度。x、y方向齿补量开机后一次置入,两个方向的补偿量均为00.015 mm,可任选。(5) 回退功能。系统具有从当前加工点按原
22、加工路线回退到本段程序起始处的功能。 (6) 通过加工程序输入,预置任意程序,加工结束后暂停,再按切割键(REG)即可继续加工(或重复加工)。(7) 坐标变换功能。坐标变换功能包括象限变换功能和对称加工功能。 4、工件的装夹 工件的装夹形式对加工精度有直接影响。线切割机床的夹具比较简单。一般是在通用夹具上采用压板螺钉固定工件。当然有时也会用到磁力夹具、旋转夹具或专用夹具。工件装夹的一般要求 (1) 工件的基准表面应清洁无毛刺,经热处理的工件,在穿丝孔内及扩孔的台阶处,要清除热处理残物及氧化皮。(2) 夹具应具有必要的精度,将其稳固地固定在工作台上,拧紧螺丝时用力要均匀。 (3) 工件装夹的位置
23、应有利于工件找正,并应与机床行程相适应,工作台移动时工件不得与丝架相碰。 (4) 对工件的夹紧力要均匀,不得使工件变形或翘起。 (5) 大批零件加工时,最好采用夹具,以提高生产效率。(6) 细小、精密、薄壁的工件应固定在不易变形的辅助夹具上。支撑装夹方法: (1) 悬臂支撑方式。通用性强,装夹方便。但由于工件单端压紧,另一端悬空,因此工件底部不易与工作台平行,所以易出现上仰或倾斜致使切割面与工件上下平面不垂直或达不到预定的精度。只用于要求不高或悬臂较小的情况。 (2) 两端支撑方式(如图5-8(a)所示)。其支撑稳定,平面定位精度高,工件底面与切割面垂直度好,但对于较小的零件不适用。 (3)
24、桥式支撑方式(如图5-8(b)所示)。采用两块支撑垫铁架在双端夹具体上。其特点是通用性强,装夹方便,大、中、小工件装夹都比较方便。 (4) 板式支撑方式(如图5-9(a)所示)。可根据经常加工工件的尺寸而定,可呈矩形或圆形孔,并可增加X、Y两方向的定位基准。装夹精度高,适于常规生产和批量生产。 (5) 复式支撑方式(如图5-9(b)所示)。在桥式夹具上,再装上专用夹具组合而成。装夹方便,特别适合于成批零件加工。可节省工件找正和调整电极丝相对位置等辅助工时,易保证工件加工的一致性。5、快走丝机床电极丝垂直度的校正 快走丝机床的电极丝上好并预紧后,先要进行垂直度的校正。如图5-11所示,先把刀刃角尺放在十字拖板工作台上的垫铁上,调节Y轴拖板,使刀刃角尺与钼丝靠近,观察刀刃角尺与钼丝之间的间隙,上下应均匀。若有误差,则在丝架固定面适当加垫片调整。然后把刀刃角尺旋转90o,调节X轴拖板,使刀刃角尺与钼丝靠近,观察刀刃角尺与钼丝之间的间隙,上下应均匀。若有误差,调整上下导轮组合件的位置,使间隙均匀。
- 温馨提示:
1: 本站所有资源如无特殊说明,都需要本地电脑安装OFFICE2007和PDF阅读器。图纸软件为CAD,CAXA,PROE,UG,SolidWorks等.压缩文件请下载最新的WinRAR软件解压。
2: 本站的文档不包含任何第三方提供的附件图纸等,如果需要附件,请联系上传者。文件的所有权益归上传用户所有。
3.本站RAR压缩包中若带图纸,网页内容里面会有图纸预览,若没有图纸预览就没有图纸。
4. 未经权益所有人同意不得将文件中的内容挪作商业或盈利用途。
5. 装配图网仅提供信息存储空间,仅对用户上传内容的表现方式做保护处理,对用户上传分享的文档内容本身不做任何修改或编辑,并不能对任何下载内容负责。
6. 下载文件中如有侵权或不适当内容,请与我们联系,我们立即纠正。
7. 本站不保证下载资源的准确性、安全性和完整性, 同时也不承担用户因使用这些下载资源对自己和他人造成任何形式的伤害或损失。