UG数控车加工编程(共92页)
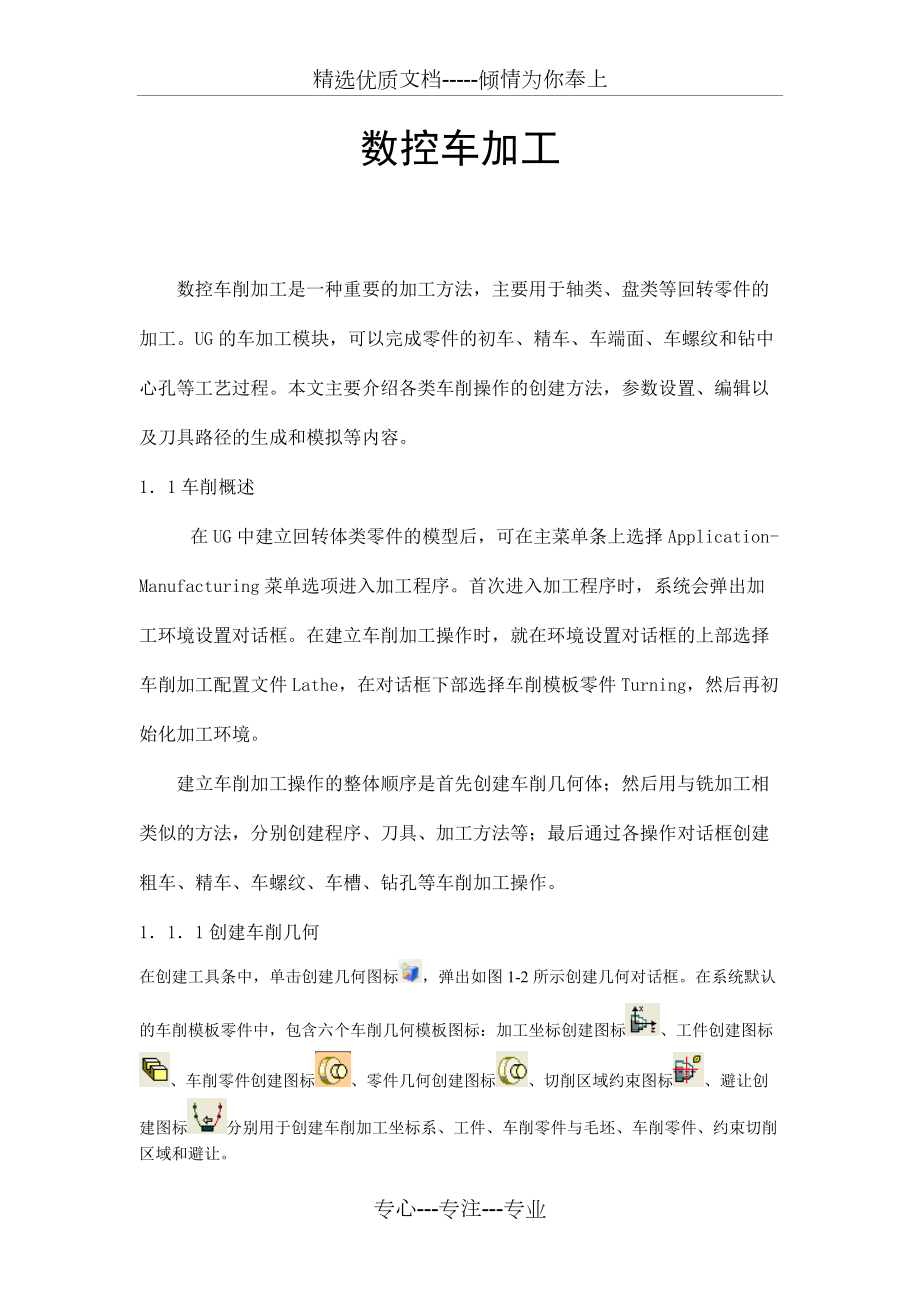


《UG数控车加工编程(共92页)》由会员分享,可在线阅读,更多相关《UG数控车加工编程(共92页)(93页珍藏版)》请在装配图网上搜索。
1、精选优质文档-倾情为你奉上数控车加工 数控车削加工是一种重要的加工方法,主要用于轴类、盘类等回转零件的加工。UG的车加工模块,可以完成零件的初车、精车、车端面、车螺纹和钻中心孔等工艺过程。本文主要介绍各类车削操作的创建方法,参数设置、编辑以及刀具路径的生成和模拟等内容。11车削概述在UG中建立回转体类零件的模型后,可在主菜单条上选择Application-Manufacturing菜单选项进入加工程序。首次进入加工程序时,系统会弹出加工环境设置对话框。在建立车削加工操作时,就在环境设置对话框的上部选择车削加工配置文件Lathe,在对话框下部选择车削模板零件Turning,然后再初始化加工环境。
2、建立车削加工操作的整体顺序是首先创建车削几何体;然后用与铣加工相类似的方法,分别创建程序、刀具、加工方法等;最后通过各操作对话框创建粗车、精车、车螺纹、车槽、钻孔等车削加工操作。111创建车削几何在创建工具条中,单击创建几何图标,弹出如图1-2所示创建几何对话框。在系统默认的车削模板零件中,包含六个车削几何模板图标:加工坐标创建图标、工件创建图标、车削零件创建图标、零件几何创建图标、切削区域约束图标、避让创建图标分别用于创建车削加工坐标系、工件、车削零件与毛坯、车削零件、约束切削区域和避让。图1-21创建车削坐标系图1-2对话框中的坐标系模板图标(MCS-SPINDLE),用于设置车削加工坐标
3、系。单击该图标后单击OK或Apply弹图1-3的坐标系设置对话框。设置加工坐标系时,使MCS坐标系和WCS坐标系在同一坐标原点,同时坐标轴方向一致,否则在生成刀具路径时因无法得到切削区域而出现错误显示。加工坐标系也可以操作导航工具中进行编辑。图132工件的创建方法创建工件时,先根据零件加工的需要,在子类区域中选择几何模板图标;再在Parent Group下拉列表框中选择父组的几何名称,继承父组的几何属性;然后,在Name文本框中输入在创建的车削几何名称;最后,单击OK或Apply。系统根据所选模板类型,弹出相应的对话框,供用户进行几何对象的定义。在各对话框中设置相关参数后,单击OK,则返回到图
4、1-2对话框,则在所选的父组下创建了指定名称的工件,并显示于操作导航工具几何视图中。在创建车削操作时可引用已创建的车削几何。(1)建立工件(WORKPIECE)在图1-2对话框中,单击工件设置图标(WORKPIECE),弹出如图1-4所示工件设置对话框,工件的建立包括选择零件、选择毛坯和选则检查体三项内容。Edit、Select和Display三个选项分别用于编辑、选择和显示零件几何、毛坯几何和检查几何。图14(2)建立零件(Part)在图1-4对话框中,单击零件设置图标(Part),弹出如图1-5所示设置零件边界对话框。单击图标后,单击Select,弹出图15建立零件几何对话框,零件几何与铣
5、加工基本相同,具体设置方法参见铣加工相关内容。图1-5 (3)建立毛坯(Block)在图14中单击(Block)图标后,单击Select弹出图16所示对话框,毛坯几何的设置方法与零件几何的设置方法基本相同,具体设置方法参见铣加工相关内容图163 车削工件的创建(TURNING_WORKPIECE)在图1-2对话框中,单击车削工件设置图标(TURNING_WORKPIECE),弹出如图1-7所示车削工件设置对话框,车削工件的建立包括选择零件、选择毛坯。通常零件继承父节点组(WORKPIECE)的特征,单击编辑边界选项(Edit),弹出图1-51对话框,可对存在的边界进行删除、添加和偏置蹬操作。毛
6、坯需要从新选择。图17对话框上部(Blank)选项下的Select用于选择毛坯。UG具有参数化毛坯边界设置和复杂轮廓毛坯边界设置两种功能,简单的棒料毛坯和管状毛坯可以采用参数化边界设置,而复杂轮廓毛坯则需在图形窗口中选取毛坯边界。参数化毛坯的设置步骤:首先,选择参数化毛坯的类型(棒料毛坯或管状毛坯),并输入有关的毛坯的长度和直径参数,然后,确定毛坯相对于工件的参考点以及毛坯的放置方向。如果已经对毛坯进行了边界设置,Disply选项将处于激活状态,并且Select选项会变成Reselect。单击Disply选项,可在图形窗口中显示已设置的毛坯边界;单击Reselect选项,可重新设置毛坯边界。在
7、图17中单击与Select弹出图18对话框。对话框中各选项说明如下。图18(Bar Stock):该图标用于设置棒料毛坯。选择该图标,可在对话框中输入毛坯长度和毛坯直径,并可指定毛坯和工件的相对位置。(Tube Stock):该图标用于设置管状毛坯。对于具有较大内径的零件一般采用管状毛坯,以减少内孔的加工时间。选择该图标,可在对话框中输入毛坯的长度、外径和内径等参数,并可指定毛坯和工件的相对位置。(From Cueve):该图标用于设置复杂轮廓毛坯的边界。单击该图标,并单击Select,弹出图1-9对话框,分别用毛坯面边界、曲线和点构造毛坯图19Mounting Poisition:该选项用于
8、设置毛坯相对于工件的位置参考点。单击Mounting Poisition下面的Select选项,可用弹出的点构造器设置参考点。如果选取的参考点不在工件轴线上时,系统会自动找到该点在轴线上的投射点,然后将棒料毛坯一端的圆心位置与该投射点对齐。Point Location:该选项用于确定毛坯相对于工件的放置方向。选取At Headstock选项,毛坯沿坐标轴的正向放置;选取Away From Headstock选项,则毛坯沿坐标轴的负向放置。设置毛坯各参数后,单击对话框中Disply选项,会在图形窗口中显示毛坯的边界轮廓,可以观察毛坯的尺寸大小和摆放位置是否正确。5切削区域约束图1-2中图标(Co
9、ntainment)用于约束切削区域,可以控制切削区域以及防止刀具碰到卡盘等辅具。切削区域约束也可以在后面切削操作对话框中进行设置,关于切削区域约束的设置,将在后面的切削参数设置中统一讲述。112车削加工刀具UG车削加工刀具包括:内外圆车刀、切槽车刀、螺纹车刀和成型车刀等,在选用选用加工刀具时,应考虑加工加工类型、加工表面形状和加工表面尺寸等因素。现以外圆车刀为例说明标准车刀的创建方法和参数设置。在操作导航器中点击刀具视图图标,将导航视图切换为刀具导航(Machine Tool)视图,点击创建刀具图标,并在出现的创建刀具对话框的Type一栏选择turing出现创建刀具菜单见图1图1在图1中选择
10、外圆车刀图标,在名称栏内输入要创建的刀具名称,并单击OK或Apply ,弹出如图2所示标准车刀参数设置对话框。各参数说明如下。图21刀片形状在图2车刀参数设置对话框中,上部各参数用于指定刀片形状和尺寸。(1)ISO Insert Shape该下拉列表框用于选择刀片的形状见图3当在该下拉列表框中选择某种形状的刀片时,刀片所对应的草图显示在对话框的顶部,同时在其下方的Nose Angle文本框中显示当前所选刀片的刀尖角。图3(2) Nose Angle该文本框用于显示或输入刀片的刀尖角,刀尖角是刀片主切削刃与副切削刃的夹角。(3)Nose该文本框用于输入刀尖圆角半径。(4)Orient Angle
11、该文本框用于输入方向角,确定刀杆相对于车床主轴轴线的位置。该角度为刀具的切削刃与加工表面之间的夹角。(5)Size该下拉列表框用于选择刀片尺寸。有三种尺寸确定方法:Cut Edge Length(刀片切边长度)、Inser. Circle(I.C.)(刀片内切圆直径)和I. C. ANSI(按ANSI标准的刀片内切圆直径)。选择哪种尺寸确定方法,应根据加工位置的形状来确定,可在其右方的文本框中输入相应的尺寸。(6)Thickness和Rwlief Angle这两个选项分别指定刀片的厚度和刀片的刃倾角。(7)Insert Position这个选项由加工时采用主轴的转向决定,在采用机床正转加工时在
12、下拉菜单中选择图标,机床主轴反转时选用图标。2定义轨迹点图1-000车刀参数设置对话框中的Tracking选项用于定义轨迹点,轨迹点是车刀上用于计算刀具路径的基准点。单击该选项,弹出如图4所示对话框,对话框中各选项说明如下。图4Radius ID:指定轨迹点刀尖半径ID号,从下拉列表选取,ID号见图5示意图。图5Tracking Piont P Number:指定轨迹点P代码,轨迹点P代码共有9种,环绕在选定的刀尖半径周围,从下拉列表选取,P代码示意图见图6。图6Radius ID、Tracking Piont P Number与车刀长度补偿值的寄存器号结合在一起指定了选取车刀上那一点作为轨迹
13、点,通常道具轨迹点定义在刀心或刀尖上,方头槽刀可以定义在左侧或右侧的刀心或刀尖上。图5与图6分别是R1_P3_0与R1_P9_0相结合形成的轨迹点,图5采用的是通常所说的刀尖编程,图6采用的是刀心编程。在图4所示的对话框窗口中XOFF:指定车刀轨迹点相对于车床的参考点在X方向(平行于主轴)的偏置距离。YOFF:指定车刀轨迹点相对于车床的参考点在Y方向(半径方向)的偏置距离。ADJUST Register:该选项指定存储车刀长度补偿值的寄存器号。CUTCOM Register:该选项指定存储车刀径向补偿值的寄存器号。Add/Modify/Delect: 轨迹点进行增加、编辑或删除操作。在图4所示
14、的对话框分别点击Radius ID与Tracking Piont P Number下拉列表,重新选择Radius ID与Tracking Piont P Number的代码,输入新的车刀长度补偿值的寄存器代码进行后,单击Add可以为车刀增加一个新的轨迹点。在图4所示的对话框窗口中点击相应的Radius ID与Tracking Piont P Number代码,使其高亮显示,如图4中R1_P8_3,重新选择Radius ID与Tracking Piont P Number的代码后,单击Modify对轨迹点进行编辑或直接点击Delect进行删除等操作。图5图6轨迹点的选择定义完成轨迹点后,在创建具
15、体加工操作菜单中,点击Machine选项,弹出Machine Control对话框,点击Define Tracking选项,弹Tracking Selection对话框见图7,点击轨迹点代码前面方框,就可激活该轨迹点。槽刀的轨迹点见图8,必须在Main Tracking Piont的下拉菜单选择一个主要轨迹点,另一点可选也可不选,但要注意选两点时与选一点生成的刀路轨迹不一样。 图7图8113创建车削操作创建车削操作的步骤为:先在车削环境中创建刀具、几何体、加工方法(具体创建方法请参见铣加工相关内容);然后在工具条中选择创建操作图标,或在主菜单中选择InsertOperation菜单项,或在操作
16、导航工具的弹出菜单中选择InsertOperation菜单项,系统弹出如图1-10所示的创建操作对话框,在该对话框中,依次选取模板图标、程序、几何体、刀具和加工方法;最后单击Apply,进入车削加工操作对话框,可设置各车削加工参数。图110在图1-10的子类型区域中,显示当前所选车削模板零件包含的操作模板。对于默认的车削模板零件Turning,它提供了多个建立车削操作的模板,各模板说明如表1-1所示。12粗车粗车是车削加工的经一道工序,用于切除毛坯的主要加工余量。在图1-10中选取粗车外圆操作模板图标,按前一节的方法选择相关对象后,单击Apply,弹出图1-1所示粗车外圆操作对话框。在该对话框
17、中,先指定粗车的走刀方式、选择切削区域、指定进刀退刀方式、并根据需要设置其他相关参数,然后,选择对话框底部的刀具路径生成图标生成刀具路径,最后单击OK,创建粗车外圆操作。图1-1121指定走刀方式在车削过程中,走刀方式控制刀具的加工轨迹。不同的走刀方式其加工特点不同,适应于不同类型的毛坯加工。如:直线走刀方式加工效率高,适应于加工余量较大的毛坯;轮廓走刀方式加工形状误差小,走刀空行程大,适应于加较小的复杂轮廓毛坯;径向进刀方式适应于加工与零件轴线垂直的轮廓面。在图1-1粗车外圆操作对话框中,有10种走刀方式,加工是应根据加工部位特点,加工精度要求选取适当的走刀方式。走刀方式介绍如下:(Line
18、ar Zig):单向直线走刀;(Linear Zig Zag):双向直线走刀;(Ramping Zig):单向斜线走刀;(Ramping Zig Zag):双向斜线走刀;(Contour Zig):沿轮廓单向走刀;(Contour Zig Zag):沿轮廓双向走刀;(Plunge Zig):单向车槽加工走刀方式;(Plunge Zig Zag):分层往返车槽加工走刀方式:(Plunge Alternate):中间开槽交替加工槽两边的加工方式;(Plunge Castling):槽刀交替移位切削,使刀具保持均匀磨损的走刀方式122设置切削区域图1-1中约束切削区域(Containment)选项,
19、是用修剪平面或修剪点来约束零件边界,限制切削区域。通过约束切削区域,可以指定边界上哪些部位为切削区域,哪些部位为非切削区域,从而可有选择地加工零件上的特定部位。单击该选项,弹出如图1-12所示几何约束对话框,对话框中各选项说明如下。图112(1)Trim Planes在图1-12对话框中,径向修剪平面(Trim Radial1,Trim Radial2)和轴向修剪平面(Trim Axial1,Trim Axial2)选项都是用平面限制零件的加工区域,可指定一个或两上修剪平面。修剪平面的设置步骤为:首先,打开图1-12中径向或轴向修剪平面选项Trim;然后输入径向或轴向坐标值,或者单击相应的Ra
20、dial或Axial选项弹出点构造器,在图形窗口中选定修剪平面的位置点。如图1-10所示,指定修剪平面后,系统根据修剪平面的位置,工件与毛坯边界以及刀具几何角度等参数自动计算出切削区域。图113修剪平面也可以与修剪点结合起来使用,当修剪平面所确定的切削区域与修剪点所确定的切削区域发生冲突时,系统自动将两者的公共区域视为切削区域。(2)Trim Point该选项通过设置修剪点来约束零件边界限制切削区域。与修剪平面相比,修剪点对切削区域的限制较少,具有更大的灵活性,它不仅可以设置修剪点,而且还可以设置角度限制切削区域。修剪点的设置步骤为:首先,打开图1-12修剪点选项;然后输入修剪点的坐标值,或者
21、单击Select选项,用弹出的点构造器指定修剪点位置。通常修剪点要求选在工件的边界上,如果所选的修剪点与工件边界有一定的偏差,系统自动将工件边界上离所选点距离最近的点视为修剪点。用修剪点限制切削区域,常用的方式是选择两个修剪点。选择两个修剪点后,系统自动将两点之间的工件边界、毛坯边界以及所设修剪角度之间围成的区域视为切削加工区域,而两点之外的区域则被忽略。如果只确定一个修剪点而没有设置其他的修剪平面,无论是选择第一个还是第二个修剪点选项,其实际修剪效果都和设定一个修剪平面的情形相同。图1-14所示的是设置两个修剪点约束零件边界以限制切削区域的情形,能很方便地控制切削起始点和终止点。图114(3
22、)Angles该选项用于设置修剪角度,对切削区域进行限制。修剪角度是在各修剪点处按矢量方向将工件边界和毛坯边界联系起来,确定切削区域。切削方向可以沿修剪角度朝修剪点方向,也可以是相反方向。通过设置修剪角度能很方便地对切削区域进行限制。修剪角度的设置步骤为:首先打开图1-12中Angle 1选项,为Trim Point 1设置修剪角度;或打开Angle 2 选项,为Trim Point 2设置修剪角度;然后,输入修剪角度值,或者单击Angle1或Angle 2 选项,用弹出的矢量构造器设置修剪角度。图1-15所示的是通过修剪点与修剪角度相结合,修剪角度设置为90度时对切削区域进行约束的情形。修剪
23、点常常需与修剪角度结合使用,才能很灵活地实现对切削区域的约束,在没有设置修剪角度时,系统自动将修剪点处切削运动的方向角设置为修剪角。图115(4)Check Geometry图1-12中该选项用于检查几何,是为了防止刀具沿设定的修剪角度切入工件或离开工件时与工件的某些表面发生碰撞。如图1-13所示,因没有打开检查几何选项,当刀具按照设定的修剪角度进行切削时,将出现与工件相碰现象。当刀具按修剪角切入工件或切出工件时,需打开检查几何选项。如图1-14所示,在打开检查几何选项之后,系统能使刀具在与工件相碰的位置自动地沿工件轮廓走刀,而不出现碰刀的现象。(5)Disply Containment该选项
24、用于在图形窗口中显示修剪平面或修剪点的位置。(6)Display Cut Regions该选项用于在图形窗口中显示切削区域,以观察所设置的修剪平面、修剪点以及修剪角度是否正确。(7)Select Cut Regions Manually该选项用于手工确定切削区域。选择该选项,会弹出点构造器,可以用光标单击所要加工的区域,如果系统发现多个区域时,系统会自动将离选择点最近的区域作为加工区域。选定一点后,系统会在该点显示SP(Selection Point) 标识。2Autodetection Control自动检测控制(Autodetection Control)选项,用于设置自动检测切削区域的相
25、关控制参数,如最小切削区域,起始点和终止点的偏置值以及起始点和终止点的角度等。单击图1-1中Autodetection Control选项,系统弹出图1-16所示自动控制对话框。可以该对话框中输入相关控制参数,以便系统检测切削区域。图116对话框中各参数说明如下。(1)Minimum Area该参数指定最小切削区域的大小,防止在很小的切削区域中产生不必要的刀具路径。当切削区域小于Minimum Area指定的参数值时,则不产生刀具路径。(2)Start Offset/End Offet该文本框用于设置切削起始点和终止点的偏移值。如果工件与毛坯边界不相交,系统将自动在工件和毛坯之间加直线段以确定
26、切削区域。在默认情况下,会在切削起始点和毛坯之间加一条与切削方向平行的直线,在切削终止点和毛坯之间加一条与切削方向垂直的直线。在Start Offset文本框中输入的数值,使起始点沿垂直于切削方向移动,在End Offset文本框中输入数值,使终止点沿切削方向移动。如果在Start Offet和End Offet文本框中输入正值时,则使切削区域扩大;输入负值时,则使切削区域缩小。(3)Start Angle /End Angle该文本框用于设置起始点角度和终止点角度。当角度为正值时,则扩大切削区域;当角度为负值时,则缩小切削区域。角度为以起始点或终止点与毛坯之间的连线绕逆时针旋转为正。123指
27、定走刀方向角在图1-1中,Level Angle选项用于设置走刀方向角。角度的测量是以工件轴线的正向为基准,逆时针方向为正。如图1-1所示,该选项右侧的红色箭头 能形象显示当前走刀方向角。设定切削加工的走刀方向角有两种方式:一是直接在 选项右侧的文本框中输入角度值;二是单击Level Angle选项,用弹出的矢量构造器指定方向角。124凹形区域加工方式图1-1中Reversal Mode下拉列表框(如图117)是用于选择凹形区域(如凹槽)的切削加工顺序。该下拉列表中各选项说明如下。图117(1)As Level该凹形区域加工方式是,使系统总是按最大的切削深度走刀到凹形区域,然后先中工靠近切削起
28、始点的凹形区域,再加邻近的凹形区域,如图1-19所示。图118(2)Inverse该凹形区域加工方式与As Level加工方式相反。系统总是按最大的切削深度走刀到凹形区域,然后加工其他的凹形区域,最后加工靠近切削起始点的凹形区域,如图1-19所示。图119(3)Closest该凹形区域加工方式是,先加工靠近刀具当前位置的凹形区域。如果采用Zig-Zag走刀方式,Closest加工方式就非常方便。因系统总是选择靠近当前刀具位置的凹槽先进行加工,这样可以减少刀具空行程时间,从而大大提高加工效率。(4)Cut Llater该凹形区域加工方式是,系统总是先加工靠近切削起始点的凹形区域,然后才加邻近的凹
29、槽。如果按一定深度进行加工,中间一次走刀的深度在邻近凹槽表面以内,会忽略邻近凹形区域,直至靠近切削起始点的凹形区域加工以后,才加工邻近凹形区域,如图1-21所示。与As Level选项不同,选择该选项,系统在切削邻近凹槽表面时会自动改变切削深度而不切入凹槽。当采用变切削深度如Variable Max选项进行加工时,系统会自动调整切削深度以免切入到邻近凹槽表面以内。图120(5)Omit该凹形区域加工方式是,除靠近切削起始点的凹形区域外,系统将忽略其他凹形区域的加工,如图1-22所示。图1211.2.5 切削深度 图18中的Cut Depth下拉列表框(如图122)用于设置每次走刀的切削深度,对
30、于不同的走刀方式,下拉列表框中的选项有所不同。例如,直线走刀方式包括:Constant、Variable Maximum、Variable Average、No.of Level、 Individual 等选项;沿轮廓走刀方式包括:Constant、No.of Passes、Individual三个选项。现对各种走刀方式下可能出现的切削深度选项进行说明。图122(1)Constant该选项设置切削深度为常量。在切削过程中,系统将按设定切削深度走刀,如果最后一次走刀的余量小于设定值,会将余下的部分一次切除。(2)Variable Maximum该选项通过设置最大值和最小值来确定切削深度的变化范围
31、。如果切削余量大于所设置的最大参数值时,系统将按所设置的最大切削深度进行切削,如果最后一次走刀的余理大于或等天最小切削深度,则将其一次切除。有两种情形系统会自动使用Variable Average模式进行切削:一种是当系统采用最大切削深度进行走刀时,其最后一镒走刀残留的切削深度小于最小切削深度;另一种是当零件的加工余量小于最大切削深度。(3)Variable Average该选项允许输入一个最大和最小切削深度来确定一个切削深度的变化范围,系统会在变化范围内自动确定一个切削深度并使走刀的次数最少。(4)No.of Level该选项用于输入直线走刀的次数,系统根据加工余量和指定的走刀次数确定切削深
32、度。(5)No.of Passes该选项用于设置走刀次数,系统根据加工余量和指定的走刀次数确定切削深度。该选项仅用于轮廓走刀方式。(6)Individual该选项用于设置每次走刀的切削深度,单击该选项,弹出如图1-23所示每次走刀切削深度设置对话框。在对话框中可以设置多个切削深度值以及切削深度值的走刀次数。如果前面的走刀切除了所有余量,系统将自动取消后面的走刀。如果所有的走刀已经完成而切削余还没有加工完,并且附加走刀(Nunber Additional Passes)设置为零时,系统会自动按最后一列的切削深度值进行加工,直到切除所有的加工余量为止。图123126光整表面在粗加工过程中,当采用直
33、线走刀方式时,常见的问题是每次走刀总会在工件表面留下一些刀痕,如图1-24所示。切削深度越大则表面留下的刀痕越深,从而使粗加工表面相当粗糙。光整粗加工表面的方法有两种:清理表面和沿轮廓车削。图1241清理表面清理表面是在每次走刀后,沿零件轮廓表面附加一个走刀运动,切除两次走刀之间的残余材料,从而降低表面粗糙度值,提高表面加工质量。在图1-1中,打开Cleanup 选项,在产生刀具路径时,系统会自动在每次走刀后沿工件轮廓表面附加一个走刀运动清理表面,去除表面刀痕。打开该选项后,其右侧的下拉列表框激活,可以选择不同的清理方式(见图125)。在不同的走刀方式下,下拉列表框中可选的清理方式有所不同。例
34、如,在沿轮廓走刀方式下只包括All和Down Only两个选项。现将常见的清理方式说明如下:图125All:清除所有表面的刀痕。Steep Only:仅清除陡峭面上的刀痕。All But Level:除陡峭面外,清除其他表面上的刀痕。Level Only:清除所有外圆表面上的刀痕。All But Level:除与轴线平行的表面之外,清除其他表面上的刀痕。Down Only:清除所有端面的刀痕。Per Reversal:在清除表面刀痕的过程中依次修光各凹槽表面。2沿轮廓车削这种光整表面的方法,是在多次走刀后,最后附加一个沿表面轮廓走刀,从而切除各次走刀的刀痕,达到光整表面的目的。在图1-1中的A
35、dditional Profiling选项,用于控制多次走刀后是否附加一个轮廓走刀。打开该选项,则在多次走刀后附加轮廓走刀;否则,不附加轮廓走刀。与Cleanup选项不同,Additional Profiling选项可以对所有表面或某指定表面进行光整加工,而Cleanup选项,在每次走刀之后,只在局部范围内修光前一次走刀留下的刀痕。3轮廓加工走刀方式多次走刀后,附加的轮廓走刀所加工的轮廓对象由轮廓走刀方式来决定。在图1-1对话框中选择Profiling选项,弹出图1-26所示对话框。应用对话框上部图标,可以指定轮廓走刀方式,从而确定进行轮廓切削时的加工对象类型和加工顺序。对话框下部选项,用于控
36、制轮廓走刀的相关参数。图126(1) 轮廓走刀方式走刀方式不仅决定切削过程中刀具的运动轨迹,而且将影响工件的加工质量。因此,根据具体的工件形状和加工质量要求选择合适的走刀方式。各走刀方式 说明如下: (Diameters Only):只加工圆柱面。 (Face Only):只加工端面。 (First Diameters Then Face):先加工外圆后加工端面。 (First Face Then Diameters):先加工端面后加工外圆。 (Towards Conner):从端面和外圆向角部加工。 (Away from Conner):从角部向端面和外圆加工。 (Down Only):只在
37、垂直于轴线方向加工。 (Finish All):加工所有表面。 (2)Spring Passes选项用于设置沿轮廓的附中走刀的走刀次数。当走刀次数设置为0时,实际轮廓走刀次数为1,当走刀次数设置为N时,实际走刀次数为N+1。(3)Fillets选项用于指定有关倒圆半径的处理方式。(4)Alternate当时行多次轮廓走刀时,打开该选项,则沿轮廓往返走刀。(5)Direction该选项用于设置轮廓车削的走刀方向。(6)关闭自动检测Override Autodetection选项用于关闭自动检测功能。如果加工余量为零,又希望加工完后在表面上再进行沿轮廓走刀,可以打开该选项来忽略系统的自动检测功能。
38、否则,当加工余量为零时,系统会自动停止走刀。(7)Local Return该选项用于中断切削过程插入机床控制等命令。127进刀与退刀方式在刀具接近工件的空行程中,刀具以快进速度移动,为防止碰刀和提高加工质量,在刀具靠近工件时,应设置附加的进刀运动和退刀运动,使刀具以较低的速度切入或离开工件。进刀和退刀方式(Engage and Retract)的设置决定刀具如何接近和离开工件。为提高工件的加工质量,选择适当的进刀和退刀方式是一个很重要的因素。UG车削加工根据切削类型的不同提从了多种不同的进刀退刀方式。在图1-1中,单击Engage/Retract1选项,弹出图书1-28所示进退刀设置对话框。在
39、该对话框中包括进刀和退刀设置两大类,每类中根据走刀方式(如水平切削、垂直进刀、轮廓切削等)的不同,所包含的进刀和退刀图标有所不同,图1-27中各选项用于设置进刀,单击图1-27中的Retract标签可弹出退刀设置对话框,退刀设置对话框中的各选项与图1-27中各进刀方式参数设置选项基本相同,现仅对进刀方式参数设置选项进行说明。图1271、走刀方式(1)Profiling该选项为沿工件表面轮廓走刀,常安排在粗车之后以提高粗车的加工质量见图128。单击该选项,可为表面轮廓走刀指定不同的进刀方式。如:自动圆弧(Auto Circular)、自动直线(Auto Linear)、矢量(Vector)、角度
40、距离(Angle Distance)、相对直线(Relative Linear)和进刀点(From Point)等进刀方式。图128注意:沿表面轮廓走刀的进刀方式参数设置,只有在图1-1中打开Additional Profiling选项,才能看到设置的进刀效果。(2)Level/Blank.该选项为直线走刀方式,直线走刀的方向平行于轴线,进刀的终止点在毛坯表面。如图1-29所示,该切削类型可选取的进刀方式包括:自动直线(Auto Linear)、矢量(Vector)、角度距离(Angle Distance)、进刀点(From Point)和双圆弧(2 Circlrs)。图129(3)Level
41、/Part该走刀方式为平行于轴线的直线走刀,进刀的终止点在工件的表面,如图1-30所示。该走刀方式可选取的进刀方式包括:自动直线(Auto Linear)、矢量(Vector)、角度距离(Angle Distance)、进刀点(From Point)和相切圆弧(2 Pt Tangent)。图1-30(4)Level/Safe该走刀方式为平行于轴线的直线走刀,在加工大部分余量后,为防止进刀时碰伤靠近切削区域的工件底面而采用安全进刀方式,如图1-31所示。该走刀方式可选取的进刀方式有自动直线(Auto Linear)、矢量(Vector)、角度距离(Angle Distance)和进刀点(From
42、 Point)。图1-31(5)Plunge该走刀方式为径向走刀,如图1-32所示。可选取的进刀方式有自动直线(Auto Linear)、矢量(Vector)、角度距离(Angle Distance)和进刀点(From Point)。图1-32(6)1st Plunge该走刀方式为首次径向进刀,如图1-33所示。可选取的进刀方式有自动直线(Auto Linear)、矢量(Vector)、角度距离(Angle Distance)和进刀点(From Point)。图1-332进刀方式(1)Auto Circular该进刀方式为自动圆弧进刀方式,可光滑切入工件而不产生刀痕,适于精加工或表面质量要求高
43、的曲面加工。其控制参数既可由系统自动设置,也可由用户输入圆弧的角度和半径。在图1-27中,当打开Use automatic values选项时,为自动圆弧进刀方式。如图1-34所示,系统自动生成的角度值为90度,半径值为刀尖圆弧半径的2倍。当关闭Use automatic values选项时,即为手动输入圆弧进刀参数。可在下面的半径和角度文本框中输入圆弧进刀的半径和角度见图1-35。该进刀方式只在粗加工的轮廓车兴旺方式和精加工中才会出现。 图1-34 图1-35(2)Auto Linear该进刀方式为自动直线进刀方式。采用该进刀方式,刀具根据工件或毛坯起始段和终止段的切削方向进刀,如图1-36
44、所示。.图1-36(3)Vector该进刀方式为矢量进刀方式。可通过输入X值和Y值,确定进刀位置和进刀方向,X、Y值是相对WCS坐标系而言的。单击该图标,可在Vector(X)和Vector(Y)文本框中输入矢量的X、Y分量,见图1-37。图1-37(4)Angle/Distance该进刀方式为角度和距离方式,通过输入距离值和角度值来确定时刀位置和进刀方向。其所使用的距离值和角度值都是相对于WCS 坐标系而言的。如图1-38所示,角度值是以进刀运动的起始点坐标轴正向为基准测量的,逆时针方向旋转为正。单击该图标,可在对话框中的Angle和Distance文本框输入参数。图1-38(5)Relat
45、ive Linear该进刀方式为相对直线方式,通过输入距离值和角度值,设置刀具的进刀方向和起始点。如图1-39所示,与Angle/Distance方式不同,Relative Linear方式的角度值是以起始段或终止段的切削方向为基准而测量的。单击该图标,可在下面的 Angle 和 Distance 文本框中输入参数。图1-39(6)To/From a Point该进刀方式是通过指定进刀起始点来控制进刀运动。如图1-40所示为通过确定进刀起始点来控制进刀运动的示意图。单击To/From a Point图标时,会弹出点构造器,引导用户选择点的位置。图1-40(7)Two Circles该进刀方式为
46、双圆弧方式,用两段相切圆弧控制进刀运动。它要求输入两段圆弧的半径值,只有切削类型为Level/Blank时才存在这种进刀方式。当单击该图标时, 可在1st Radius和2nd Radius文本框中输入相应半径。图1-41所示的是双圆弧进刀方式。图1-41(8)2 Point Tangent该进刀方式产生一个与工件表面相切的弧形进刀运动,如图1-42所示,此圆弧分别与直线切削运动轨迹和工件表面相切。只有切削类型为Level/Part时,才存在这种进刀方式。选择该进刀方式时,要求输入相对于粗车运动的角度值和圆弧半径值,可在Angle和Radius文本框中输入相应参数。图1-423延伸距离图1-2
47、7中Extend Distance选项,用于设置切削起始点(或终止点)沿坐标轴向的偏移值,只有在精车时或粗车时用轮廓类型才显示该选项。4进刀至修剪点图1-27中Direct engage to trim point选项,只在精加工时或者粗加工用轮廓走刀时才会出现。精车或附加轮廓车削的切削层很薄,为确保刀具能切入切削层并与工件的表面相切,可采用该选项使刀具进刀至修剪点。trim point可通过约束切削区域选项(Containment)设置。128切削参数图1-1中Cutting选项用于设置车削的相关控制参数。单击该选项,弹出图1-43所示切削参数对话框,对话框中的各选项说明如下。1公差Tole
48、rance选项用于设置粗车时的内公差(Intol)和外公差(Outtol)。图1-432刀具安全角刀具安全角(Cutter Clearance Angles)是指刀具切削刃与加工表面的夹角,主要是防止刀具在切削过程中与工件表面相碰。在指定刀具安全角时,可在对话框的First cutting Edge和Last cutting Edge文本框中,分别指定第一条切削刃和最后一条切削刃的安全角。3最小安全距离最小安全距离(Minimum Clearance)选项设置刀具距毛坯边界的最小安全距离,防止刀具在移到一个新的切削区域时与工件发生碰撞。在对话框的From Diameters和From Face
49、s 文本框中,可以分别指定距毛坯外表面和毛坯端面的最小安全距离。4切削运动限制图1-43中Cut Constraints选项用于控制切削运动。包括最小切削深度和最小切削长度两个选项,仅适应于直线走刀方式。如果切削深度和切削长度小于设定值,则忽略不加工。如图1-44所示,对于残留的余量,可通过打开Additional选项,附加一个轮廓走刀来切除。 图1-445轮廓面类型Contour Types选项用于定义轮廓面的类型。单击该选项,弹出图1-45所示轮廓类型设置对话框,在各选项中输入最大角度和最小角度值,确定轮廓面的角度变动范围。在加工过程中,系统能根据所设置的轮廓面角度变动范围自动判别工件各加
50、工面的类型。图1-45(1)Face该选项用于设置端面的角度变动范围,系统自动将位于该角度范围内的轮廓面视为端面类型。在端面Face选项中输入的最大角度为10度,最小角度为70度,当工件的某个面与坐标轴正向的夹角在这范围内变化时,系统自动将该面视为端面。(2)Diameter该选项用于设置圆柱面的角度变动范围,系统将位于该角度范围内的轮廓面视为圆柱面类型。在Diameter选项中输入最大角度为200度,最小角度为160度,工件的外圆表面与坐标轴正向的夹角在这范围内变化,系统自动将这睦面视为圆柱面。6切削控制图1-43的Cut Control用于对加工中的一些选项进行控制,其相关选项说明如下:(
51、1)Safe Distance该选项控制刀具切削起始点离工件表面的距离,在这段距离内刀具将以较低的切削速度切入工件,防止工件快速靠近工件时发生撞刀现象。(2)Undercut该选项用于加工带有特殊凹槽的工件。勾选Undercut选项,能使刀具切入特殊的凹槽之中,如图1-46左图所示:当关闭该选项时,切削情况如图1-46右图所示。图1-46(3)Relief Plunge该选项用于防止加工凹槽时划伤工件表面。加工稍大的凹槽时,如果切槽切具径向进刀然后进行水平切削,可能会因为切削力作用使刀具发生偏斜而划伤工件。勾选该选项,并输入偏离值,则在第一次垂直进刀之后,系统自动偏离工件表面一定距离,设置附加
52、的垂直进刀。这样,可以有效地防止划伤工件表面。该选项只有在直线走刀方式时(Zig和Zig-Zag)才有效,在轮廓车削或垂直于轴方向进刀的切槽加工中不会显示该选项。7粗车后延时停顿Dwell after Rough Cut选项用于设置停顿时间。在径向进刀切槽时,通过该选项可以在每次进刀后设置一个停顿进间。在轮廓加工时,该选项不起作用。停顿时间的单位可以是秒或主轴旋转的转数,默认值为0。129拐角加工方式在图1-1中,单击Conner选项,弹出图1-47所示拐角控制对话框。该对话框的上部和下部选项分别控制直角和钝角的加工方式,直角和钝角具有四种相同的加工方式,下面分别予以介绍。图1-471 Rol
53、l aroundType下拉列表中Roll around选项,刀具在遇到拐角时,会以拐角的尖点为圆心,以刀尖圆弧为半径,按圆弧方式加工。图1-48分别为加工直角和钝角时的走刀情况。1-48图2ClearType下拉列表中Clear选项,刀具在遇到拐角时,按拐角的轮廓直接改变切削方向。图1-49分别为直角和钝角的加工。图1-493RoundType下拉列表中Round选项,刀具将拐角按指定的圆弧半径进行倒圆,切掉尖角部分,产生一段圆弧刀具路径,如图1-50所示。图1-504BreakType下拉列表中Break选项,刀具将拐角按指定参数倒角,切掉尖角部分,产生一段直线刀具路径,如图1-51所示。
54、图1-511210设置加工余量在图1-1中,单击Stock选项,弹出如图1-52所示加工余量设置对话框。在该对话框中,可分别设置粗车余量(Rough Stock)、轮廓车削余量(Profile Stock)和毛坯余量(Blank Stock)。图152(1)Equidistant在该文本框中输入的余量值将应用于所有的加工表面。即所有表面都具有相同的加工余量。(2)Face在该文本框中输入的余量值将应用于所有的端面类型的加工表面。即所有端面都具有相同的加工余量。(3)Radial在该文本框中输入的余量值将应用于所有的圆柱类型的加工表面。即所有圆柱面都具有相同的加工余量。 1.2.1 切削速度与进
55、给量单击图1-1中Feed Rates选项,弹出图1-53所示的切削速度设置对话框。图1-531切削速度(Speeds)(1)Spindle Output Mode Spindle Output Mode的下拉列表用于指定切削速度的单位。有两种切削速度单位:RPM:每分种多少转。SMM/SFM:表面线速度每分钟多少米/每分钟多少英尺。如果切削速度单位指定为SMM,当加工不同直径的表面时,系统会自动调整主轴的转速,从而保证切削的线速度不变。(2)Surface Speed 、Maximum Speed当切削速度单位为SMM/SFM时,该两个文本框激活。可分别输入表面线速度和最大线速度。(3)Sp
56、indle Speed当切削速度单位为RPM时,可在该文本框中输入主轴转度。(4)Set Non-Cut Speed该选项用于调协所有非切削运动(如进刀、退刀、返回)的速度单位。(5)Set Cut Speed单击该选项,系统自动根据所选工件材料、刀具材料,以及加工要求等参数自动设置切削速度。2进给速度(Feeds)在图1-53对话框中,选择Feeds标签时,对话框切换为如图1-54所示形式,用于设置切削运动和非切削运动的进给速度。各参数设置说明如下:图1-54(1)Rapid该文本框用于设置空行程快速运动的速度,如:从From Point至Start point或从Return Point至
57、Gohome Point。(2)Approach该文本框用于设置刀具运动至进刀点速度。(3)Engage该文本框用于设置刀具运动至进刀点的速度,为防止碰伤刀具,进刀速度常设置为较小的值。(4)Cut该文本框用于设置切削运动的速度。(5)Retract该文本框用于设置退刀运动的速度。(6)Traveral该文本框用于设置跨越运动的速度。该速度可用于刀具从一个切削区域移动至另一个切削区域的跨越运动,也可用作刀具运动至最小安全平面时的速度。(7)Return该文本框用于设置刀具运动至返回点Return Point或Clearance Plane的速度。(8)Clear该文本框用于设置刀具从工件表面运
58、动至最小安全距离(Minimum Clearance)的速度。该选项仅用于粗加工径向进刀方式。(9)First Cut该文本框用于设置径向第一次走刀或粗加工第一次走刀的进给速度。(10)Step Over该文本框用于设置径向进刀加工凹槽时,刀具横向走刀的移动速度。3粗车相关的进给速度(Rough)在图1-53对话框中,选择Rough标签,对话框切换为如图1-54所示形式,用于设置粗车和表面清理的进给速度。各参数设置说明如下。图1-54(1)Rough Feed Rates该组合框用于设置与粗车相关的进给速度,各选项说明如下。Accelerate:粗车起始段的加速进给量。Length:粗车起始段
59、的加速距离。可输入距离值或刀具路径长度的百分比。如图1-59所示,在刀具切入工件的起始段设置有一定距离的加速区。Decelerate:粗车终止段的降速进给量。Length:粗车终止段的减速距离,可输入距离值或刀具路径长度的百分比。如图1-59所示,在刀具切出工件的终止段设置有一定距离的减速区。(2)Cleanup Feed RatesLinear:刀具走斜线(不平行轴线也不垂直轴线)时的进给速度。Face:加工端面的进给速度,端面按轮廓设置中指定的参数判断。Diameter:加工圆柱面的进给速度,圆柱面按轮廓设置中指定的参数判断。Circular cw:顺时针切削时的进给速度。Circular
60、 ccw:逆时针切削时的进给速度4轮廓加工进给速度 (Profile Feed Rates)在图1-54对话框中,选择Rough标签,对话框切换为如图1-55所示形式,图1-55该组合框用于设置轮廓走刀的进给速度,各选项与Cleanup Feed Rates的设置相同。1212避让单击图1-1中Avoidance选项,弹出图1-56所示避让设置对话框,应用该对话框可以设置切入和切出走刀路线。各参数设置说明如下。图1-561From Point该选项用于加工起始点,设置起始点时,打开对话框中的From Point选项,再单击Select,用弹出的点构造器或在图形区用鼠标点取来确定From Poi
61、nt的位置。2Motion to Start Point该选项用于设置从起始点运动到起刀点的方式和起始点位置。(1)Motion TypeMotion to Start Point的Motion Type下拉列表框中有5种可选的运动方式。(Direct):刀具从初始点走直线移动到起刀点。(Radial- Axial):刀具从初始点先作径向移动,再轴向移动到起刀点。(Axial- Radial):刀具从初始点先作径向移动,再径向移动到起刀点。(Clear Radial-Direct):刀具先从初始点直线移动到径向安全平面,然后径向移动至起刀点。(Clear Axial -Direct):刀具先从
62、初始点直线移动到轴向安全平面,然后沿轴向移动至起刀点。(2)Start Point该选项用于设置起刀点。在开始切削时,刀具将从起始点按指定方式运动到起刀点。起刀点有两种设置方法,指定点(Point)和用增量(Delta)。指定点(Point)设置起刀点时与From Point设置方发相同,是用用增量(Delta)设置起刀点时,在Start Point的下拉菜单中选择Delta再单击Select,用弹出的对话框来确定Start Point的位置。图157是用增量(Delta)设置起刀点到进给点的对话框,选取角度和距离(Angle and Distance)或增量矢量(Delta Vector)来确定起刀点位置,在图1-57所示对话框输入相应的值,就确定了起刀点。 图1-573Approach Path打开Approach Path选项并单击Select,弹出图1-58所示对话框,该对话框用于设置从起刀点到进给点的运动路径,各参数设置说明如下。图1-58List by:选择设定点时的坐标系,WCS为零件坐标系,MCS为加工坐标系。Motion to Approach Point:设置图1-56中AP1APn各点之间运动方式,与Motion to Start Point的设置方法相同。Select:单击Select弹出点
- 温馨提示:
1: 本站所有资源如无特殊说明,都需要本地电脑安装OFFICE2007和PDF阅读器。图纸软件为CAD,CAXA,PROE,UG,SolidWorks等.压缩文件请下载最新的WinRAR软件解压。
2: 本站的文档不包含任何第三方提供的附件图纸等,如果需要附件,请联系上传者。文件的所有权益归上传用户所有。
3.本站RAR压缩包中若带图纸,网页内容里面会有图纸预览,若没有图纸预览就没有图纸。
4. 未经权益所有人同意不得将文件中的内容挪作商业或盈利用途。
5. 装配图网仅提供信息存储空间,仅对用户上传内容的表现方式做保护处理,对用户上传分享的文档内容本身不做任何修改或编辑,并不能对任何下载内容负责。
6. 下载文件中如有侵权或不适当内容,请与我们联系,我们立即纠正。
7. 本站不保证下载资源的准确性、安全性和完整性, 同时也不承担用户因使用这些下载资源对自己和他人造成任何形式的伤害或损失。