设备维护与检修作业标准
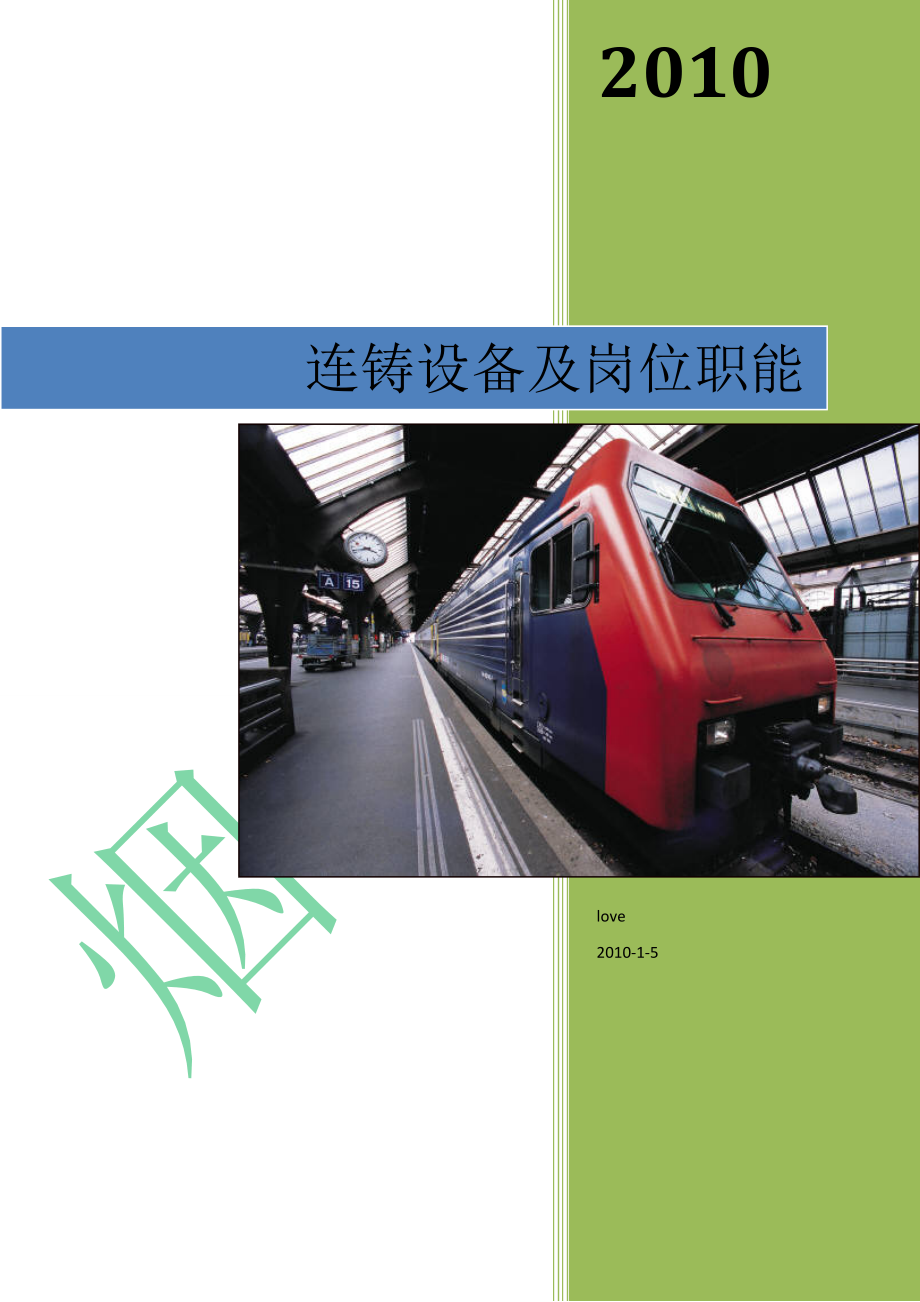


《设备维护与检修作业标准》由会员分享,可在线阅读,更多相关《设备维护与检修作业标准(19页珍藏版)》请在装配图网上搜索。
1、连铸设备及岗位职能2010love2010-1-5窗体底端 1.设备主要技术参数 1.1.设备主要技术参数: 连铸机型式 弧形小方坯连铸机 弧形半径 R=6000mm 流数 三机三流 流间距 1200mm 铸坯断面 120120mm 150150mm 110-160mm 铸坯定尺长度 3.7-12米 钢水罐支撑方式 钢包回转台 中间罐车台数 2台 中间罐型式、容量 电动缸自动控制塞棒开闭式,容量12t 结晶器结构形式 铜管水套组合式 铸坯导向装置 上段为活动段 下段为固定段 拉矫机拉速范围 0.6-6.0m/min 铸坯切断方式 火焰切割机 出坯方式 轨道,双层翻转冷床,翻缸机,移缸机和推钢机
2、 轨道速度 32m/min 移钢能力 3.2t 钢结构平台 上层平台面标高 +6.700m(轨道面标高+0.60m) 上层平台面长宽 2380013100mm 下层平台面标高 +4.05mm 连铸机长度(基准线至固定挡板面) 39680mm 1.2 主要设备技术性能 1.2.1钢包回转台 承载能力 280t(钢水重40t,钢包重40t) 回转半径 3500mm 旋转速度 正常1r/min,启、制动0.1r/min 旋转角度 180;故障时360 旋转用电机 YZR160MB-6 AC 8.5KW 930r/min 单轴伸 IM1001 380V H级绝缘 IP54 事故旋转速度 0.5rpm
3、事故旋转角度 180 事 故旋转油马达 斜轴式轴向柱塞马达A2F63W2P1 P=10-13MPa 471r/min N=5.2-6.8KW 放钢包时冲击系数 2 干油润滑系统: 1.2.1.1齿轮润滑系统 多点干油泵 ZB-2型 N=18KW 工作压力 31.5MPa 贮油容积 30L 给油量 3.2立方厘米/min DC24V 喷射嘴 GPZ-135型(JB/ZQ4538-86) 空气压力 0.45-0.6MPa 喷射直径 135mm 喷嘴与润滑表面距离 200mm 气动三联件 398.263 二位二通电磁阀 DF-10 DC24V 润滑介质 连铸机专用脂 空气工作压力 0.45-0.6M
4、Pa 1.2.1.2 轴承圈润滑系统 电动干油泵 DRB4-M120Z 换向阀 24EJF-M(JB/ZQ4584-86) 压差开关 YCK-M5 (JB/ZQ4585-86) 双线分配器 4SSP2-M1.5(JB/ZQ4583-86) 2SSP2-M1.5(JB/ZQ4583-86) 润滑介质 连铸机专用脂 1.2.2中间罐车 结构型式 框型结构的车架,单侧链轮驱动 载重量 15.5t 轨距 1700mm 轮架 3800mm 最大轮压 80KN 减速器 BWD2.2-3-29摆线针轮行星减速器 车轮直径 350mm 走行速度 9.52m/min 走行方向微调 手动操作 中间罐横向微调行程
5、30mm 车体运行距离 8000mm 供电方式 电缆卷筒 操作方式 固定操作箱 1.2.3中间罐烘烤站 结构型式 烧嘴可垂直旋转升降80 烧嘴型式 鼓风助燃的天然气火焰燃烧嘴 烘烤温度 -251100 烘烤时间 4560min 烧嘴数量 2个/台 天然气压 0.2MPa 空气压力 0.4MPa 风机型号(2机配置) GY8-12-1 NO.6 右旋 1.2.4 结晶器 结构型式 弧形铜管水套组合式 外弧半径 6000mm 断面尺寸 120120mm 150150mm 110-160mm 铜管长度 方坯750mm,圆坯 800mm 冷却水量 95立方米/小时 水压 0.6MPa-0.8Mpa 足
6、辊水 方坯角喷 120(44) 150(84); 圆坯110-160mm(63),160-180(83) 喷嘴型号 3/8PZ2265QZ1 1.2.5结晶器振动装置 结构型式 四连杆短臂振动 弧形半径 R6000mm 振动方式 正弦曲线 振幅 36mm(实际5) 频率 0300Hz(可调) 1.2.6二冷装置活动段 结构型式 弧形导架体气缸摆动 驱动用气缸 S型尾部悬挂式气缸 160750mm 气缸工作压力 0.4-0.6MPa 1.2.7.二冷装置固定1段 结构型式 带导向夹辊托辊固定式水冷弧形导向架 夹辊 160180mm 夹辊最大辊面间距 200mm 1.2.8二冷装置固定段 同固定段
7、 1.2.9拉矫机 1.2.9.1拉矫机 2连铸机铸坯断面mm120120mm 150150mm 110-160mm拉坯速度m/min0.3-5m/min开口度mm85-237拉矫辊直径宽350250mm个数5驱动辊两个上辊驱动减速器型号F1212.1(上海新中专利)总速比430.25液压缸型号UY-TF/MI(JB/ZQ4181-97)规格140/100320,140/100520工作压力010MPa1.2.9.2辅助拉矫机2连铸机铸坯断面mm120120mm 150150mm 110-160mm拉坯速度m/min0.3-5m/min开口度mm85-237拉矫辊直径宽350250mm个数5驱
8、动辊上辊单辊驱动减速器型号F1212.1(上海新中专利)总速比430.25液压缸型号UY-TF/MI( JB/ZQ4181-97)规格140/100320工作压力010MPa 1.2.10 蒸汽排出装置 2连铸机配风机 Y4-73N010D4 左 风量 44004立方米/min 1.2.11 引锭杆承放装置 结构型式 气缸驱动,四连杆摆动 摆动距离(升高距离) 80260mm 托架个数/流 8 每流驱动气缸数 2 气缸型号 2连铸机:S200250mm 空气压力 0.4-0.6MPa 1.2.12 引锭杆 结构型式 箱型对扣式半板簧引锭杆 总长 111000mm 节距 400mm 插入结晶器长
9、度 150mm 引锭杆断面 145143mm(150坯) 115113mm(120坯) 105(110坯) 115(120坯) 125(130坯) 135(140坯) 145(150坯) 155(160坯) 1.2.13轨道 1.2.13.1主要参数2机结构型式辊子双轴承支座,分组集中链条传动(辊径辊身长)输出辊道165180冷床区220200辊道运行速度32m/min冷床区32.17m/min减速机行星摆线针轮减速器BWD18-23-2.2 i=23冷床区辊道:XWD4-29-2.2 i=29链条16A-1(GB1243.1-83)1.2.13.2辊道分组(每流) 输出辊道分组编号辊道名称每
10、组辊子数辊子编号辊距mm备注切前辊道414820水冷切后辊道6812900输出辊道(一)61318900输出辊道(二)41922900输出辊道(三)523279002机冷床区辊道328309003031辊距1200431341200335371200 1.2.14 双层翻转冷床(2机) 铸坯定尺 2600mm-12000mm 铸坯截面 20120mm 150150mm 110-160mm 铸坯翻转角度 90 液压缸(2个) Y-HGI-E100380LEI-HL10T2 系统最大压力 14MPa1.2.15横向移钢机 横移铸坯重量 3200Kg 横移速度 23m/min 横移行程 6200mm
11、 减速器 ZS82.5-1-型 i=51.22 制动器 YWZ300/25型 配YT1-25 ZC/4电力液压推动器 额定推力 250N 额定行程 40mm 制动瓦退距 0.7mm 制动力矩 320Nm 1.2.16 推钢机和冷床 冷床尺寸 长12005mm 宽 11350mm 存放铸坯最大重量 42t 推钢机行程 1000mm 液压缸(2个) SDG-160/110-e型 行程650mm 系统最大压力 14MPa 1.2.17 中间包倾翻装置(2机) 倾翻速度 1.785rpm 倾翻方向 逆时针方向 倾翻角度 180 行星减速器 NGW123-11 i=56 输入1000r/min时允许输入
12、功率7.5kw 制动器 YT1-25电动液压推动器 1.2.18 拉矫机干油润滑站(2连铸机) 干油润滑泵(江苏启东润滑设备有限公司) 型号 HA1X 公称压力 40MPa 额定给油量 430ml/min 电机功率 1.5kw 贮油筒容积 60升 电动加油泵(江苏启东润滑设备有限公司) 型号 DJB-V70/860 公称压力 3.15MPa 额定给油量 70L/H 电机功率 0.37kw 贮油筒容积 200升 润滑介质 连铸机专用脂 1.2.19 二冷活动段,气动阀门站 分水滤气器 QSL-25 1MPa 空气减压阀 QTY-25 1MPa 压力表 Y-60ZT 0-1.6MPa 油雾器 QI
13、U-25 1MPa 电控电器滑阀 K25D2-15-L1 直流24v 消音器 XS-L15-L1 1.2.20二冷固定段气动阀门站 压力 0.20.6MPa 流量 0.130.15立方米/min 减压阀 QTY25 G1 1Mpa 节流阀 L41H-25 电控电气滑阀 k25D215L1 DC24 及以下项目 1.2.20.1快速调压阀1/2 AR400004 烟台未来气动组件设备有限公司 技术参数: 进口压力 0.71.0MPa 压力调节范围 0.050.6MPa 输入压力波动 0.2MPa时输入压力波动0.02MPa 压力变换时间 25秒 1.2.20.2旋塞阀X13W-10 G1/2 1
14、.2.20.3压力表Y-100ZT 01.6MPa 1.2.21火焰切割机 型号:FGR3 方圆坯火焰切割车 上海新中 切割钢种:普碳钢、优质钢、低合金钢 切割铸坯断面尺寸: 100100 120120 180180 220220 240240 100-200mm 铸坯最大拉速: 3.5m/min 切割速度:300450mm/min 能源介质:乙炔、天然气、液化石油气、丙烷、丙烯、焦炉煤气等。 1.2.22液面自动控制 液面检测方式:铯源型 液面控制方式:塞棒自动/手动 拉速自动 放射源:同位素铯137 (中核四零四公司) 塞棒启闭机构:嵌入式塞棒执行机构 数控电控缸: 行程 0140mm 数
15、控伺服电机精度:65535脉冲 控制定位精度:0.01mm 回应时间:500us 推力:500kg 最大动作速度:2000转/分钟或100mm/s 控制软件:多阶自适应前馈智慧控制软件 2. 设备维护作业标准 2.1设备的日常维护 2.1.1各设备传动装置: 2.1.1.1 定期检查各联轴器柱销是否齐全和完好。 2.1.1.2 每班检查制动器工作是否灵活可靠。定期检查制动轮有无损伤,闸皮磨损和销轴磨损是否在要求范围内。 2.1.1.3每班检查各减速机油位是否正常。 2.1.1.4每班检查各润滑系统运行是否正常,供油是否到位。 2.1.1.5每班检查各冷却水系统水置、水压、水温是否正常,压力表是
16、否完好 2.1.1.6每班检查各冷却水系统软管有无破裂泄漏,阀门有无损坏泄漏。 2.1.1.7 每班检查各气动系统压力是否正常,气动组件和管路阀门有无泄露。 2.1.1.8每班检查液压管管路有无泄漏。 2.1.1.9 定期检查并更换气动组件空气滤芯。 2.1.1.10定期检查拉矫机上下辊轴承情况。 2.1.1.11每班检查一次电机和减速机运转情况。 2.1.2 回转台 2.1.2.1定期对回转台钢结构的高强度螺栓的松弛、脱落,钢板的屈曲和裂纹,焊接部分的裂纹、腐蚀、锈蚀、镀层的剥离等进行保养和维修。 2.1.2.2定期检查地脚螺栓紧固有无松弛,螺纹部分有无异常。 2.1.2.3对回转台基础,当
17、钢包在回转臂的单侧放下时,应定期检查底座的底面与混凝土基础的顶面之间有无间隙产生,混凝土基础是否有裂纹。 2.1.2.4回转驱动装置减速机内的润滑油开始使用500小时后进行更换,以后每2500小时更换一次。 2.1.2.5开始工作100小时后,应检查螺栓的预紧力,以后每500小时检查一次。 2.1.2.6每半月检查一次回转支撑内部螺栓有无松动。 (1) 钢结构件高强度螺栓的预紧 A 预紧力矩: a 回转臂与回转支撑的连接螺栓M30,预紧力矩 1800Nm伸长量0.675mm。 b底座与回转支撑的连接螺栓M30,预紧力矩1800Nm,伸长量0.798mm。 B预紧说明: a螺栓预紧时,应在螺栓、
18、螺母的螺纹处及螺母的端面涂轻油。 b使用力矩扳手及千分表等工具以螺栓受到预紧力作用后所产生的伸长量为依据以控制预紧力。 c预紧高强度螺栓应在180方向对称、均一地连续进行,第一次预紧时,使螺栓伸长量达到计算伸长量的80%,第二次再使伸长量达到计算值。 (2) 地脚螺栓的预紧 A使用液压拉伸器给地脚螺栓加上400KN的负荷,这时螺栓与支撑面间产生间隙,再把螺母拧紧。 B在180方向对称均一地进行,第一次先把所有螺栓的预紧力加到计算值的 80%,第二次再加到计算值 (3) 回转支撑安装螺栓的预紧 A 应选用调质平垫,禁止使用弹簧垫圈。 B 螺栓的预紧方法同上所述。 2.1.3 中间罐车: 2.1.
19、3.1每班检查走行微调和横向微调机构动作是否灵活。 2.1.3.2每班检查罐车运行情况及链条松紧状况。 2.1.3.3定期检查4个车轮与辊道接触情况。 2.1.3.4每月对车轮及各座轴承加油一次。 2.1.4 中间罐烘烤站: 2.1.4.1每班检查电动推杆运行是否正常。 2.1.4.2每班检查空气压力和天然气压力是否正常。 2.1.4.3每班检查管路和阀门有无泄漏。 2.1.4.4及时疏通或更换被堵塞的天然气烧嘴。 2.1.5 结晶器振动装置: 2.1.5.1每班检查冷却水软管有无破损漏水。 2.1.5.2每班检查干油管路有无破损、烧损,接头处有无泄漏。 2.1.5.3定期检查各润滑点供油是否
20、到位。 2.1.5.4每班检查振动臂碟簧有无破损,失效和脱落。 2.1.5.5每当更换结晶器时检查台架板簧有无松动、烧损、严重变形。 2.1.5.6更换结晶器时,要采取措施防止杂物或尘土进入台架冷却水孔内。 2.1.5.7每班检查联轴器。 2.1.5.8定期打开减速器后盖观察蜗轮情况。 2.1.6 二冷段: 2.1.6.1定期检查紧固螺栓紧固情况。 2.1.6.2及时更换表面磨损或烧损严重的夹辊和托辊。 2.1.6.3每班检查上下夹辊转动情况,要保证其转动灵活。 2.1.6.4每次浇铸结束后检查并校正喷水管和喷嘴位置。 2.1.6.5定期检查R6000mm对弧,对弧间隙0.3mm 2.1.6.
21、6定期检查上辊架,不应有严重变形,紧固良好。 2.1.6.7每次检修完毕不装喷嘴,以最大水量冲洗喷淋水管。 2.1.7 拉矫机: 2.1.7.1浇铸拉坯时观察上下辊转动是否灵活、平稳,有无不转现象,并观察电流大小,以断定辊子轴承是否损坏。 2.1.7.2浇铸拉坯时观察上辊压下抬起动作是否正常,如有异常,应进一步检查处理。 2.1.7.3定期检查减速器齿轮磨损情况。 2.1.7.4坚查紧固2拉矫机传动辊部件与减速机间的紧固螺栓。 2.1.7.5每班检查各路冷却水是否畅通(拉完坯后用手触摸水管来判断)。 2.1.7.6每周检查减速机上下腔稀油润滑情况。 2.1.7.7每周集中加干油一次。 2.1.
22、7.8每周检查一次设备冷却水循环情况,如有堵塞,及时疏通,如有漏水严重处及时处理。 2.1.7.9每班检查气缸有无窜气。 2.1.8 引锭杆和引锭杆承放装置: 2.1.8.1每班检查头节、过渡节和尾节是否严重下挠影响正常送引锭杆和拉坯。 2.1.8.2每班检查节与节间连结销轴有无太松和窜出。 2.1.8.3每班检查引锭杆存放装置摆入辊道区后台架面是否高出辊面而影响正常送引锭杆和拉坯。 2.1.8.4链身上下不能粘有脏物和油污。 2.1.8.5定期检查存放装置轴承座地脚螺栓及同步轴联轴器夹紧螺栓的紧固情况。 2.1.9 辊道 2.1.9.1每班检查各辊道传动是否灵活,辊子轴承座地脚螺栓是否有松动
23、。 2.1.9.2及时更换磨损严重的辊子轴承。 2.1.9.3及时处理水冷辊泄漏点。 2.1.9.4每班检查减速机地脚螺栓有无松动,及时紧固。 2.1.9.5定期调整各链条的松紧程度。 2.1.10排蒸汽风机: 2.1.10.1每班检查风机运行是否平稳,风机和电机地脚螺栓有无松动。 2.1.10.2定期检查调节风门开闭是否灵活了。 2.1.10.3每班检查联轴器柱销有无被剪断,十分齐全。 2.1.11电动润滑泵和多点干油泵: 2.1.11.1注油筒盖应加锁,由专人负责加入润滑脂。 2.1.11.2加入的润滑脂须保证洁净,无杂物混入。 2.1.12 气源处理三联件的使用和维护: 2.1.12.1
24、过滤器装在进气方向最前段,油雾气装在最后,三联件须垂直安装,油杯、存水杯朝下。 2.1.12.2用专用扳手取下油雾器油杯加入HU-30汽轮机油到应有油位,不得超过最高油位。根据需要测量的大小调节油雾器给油量,一般转动1-2圈油路可全开,通过油窗观察滴油情况。 2.1.12.3QTY型减压阀的减压,可直接拧动其手轮来调到所需的工作压力。395系列空气 减压阀的减压,需先松开手轮上部的制动旋钮,然后拧动手轮来调节输出压力到所需的工作压力,再拧紧制动旋钮来锁进手轮。 2.1.12.4视过滤器内积水情况来定期来扳开下部的放水阀放水。 2.1.12.5要定期用专用扳手拆卸油杯和水杯进行清洗。 2.1.1
25、2.6定期清洗或更换过滤器中的滤芯。 2.1.12.7调压时压力上部去,应检查弹簧和大弹簧座是否断裂。 2.1.12.8平衡状态下减压阀溢流口漏气,应检查进气阀和溢流阀是否有尘埃,有尘埃则需取下清洗,还应检查膜片有无破损,如破损应及时更换。 2.1.12.9油雾器工作中如不出油,应检查进口流量是否减少,油针是否被堵塞,发现问题要及时处理。 2.2主要设备常见故障和处理方法 2.2.1中间罐车 2.2.1.1罐车行走不动 (1) 车轮轴承长期缺油而损坏,需更换轴承并保证其正常的润滑。 (2) 链传动啮合不正常,须进一步检查处理。 2.2.1.2横向微调装置损坏 长期受冲击载荷使轴承和轴承座损坏,
26、在吊放中间包到中间罐车上时应使中间罐对准后慢慢落下。 2.2.2中间罐烘烤器 2.2.2.1电动推杆传动装置故障造成烧嘴升降动作不正常,须拆检修理。 2.2.2.2烧嘴喷油孔被堵塞,须及时更换。 2.2.3结晶器振动装置 2.2.3.1结晶器与台架接合面漏水。 原因:(1) 安装时o形密封圈位置偏移或损坏。 (2) 密封圈实效。 (3) 结晶器外水套支撑面变形。 处理方法:(1) 安装时不要压扁密封圈。 (2) 及时检查更换密封圈。 (3) 更换外水套或修复变形的支撑面。 2.2.3.2支撑弹簧板下塞有结晶器溢钢生成的钢渣,应及时清理。 2.2.3.3支撑弹簧板被溢钢烧损、烧损严重的应及时更换
27、。 2.2.3.4支撑弹簧(弹簧板)端部断裂。 原因:疲劳破坏。 处理方法:及时更换。 2.2.3.5振动臂蝶簧失效、破损 原因:疲劳破坏。 处理方法:及时更换。 2.2.3.6 DN80冷却水金属软管破损漏水 处理方法:及时更换已漏水的软管。 2.2.3.7润滑脂供油钢管被漏钢损坏,及时安排更换,双线分配器故障造成供油不正常,更换后离线检修。 2.2.3.8因电器上原因使振动频率变化,须及时检查调整。 2.2.4 二冷段 2.2.4.1活动段摆动出现故障 原因:1) 轴承损坏而卡死。 2) 气动系统故障或是气缸漏气。 3) 活动段摆体上的钢渣积存太多。 4) 限位控制故障。 处理方法:1)
28、更换轴承。 2) 检查气动系统和气缸,针对问题进行相应的检修。 3) 及时清除摆体上的钢渣。 4) 检修限位装置。 2.2.4.2固定段的夹辊因漏钢塞卡而不能转动,操作工须在每次浇铸结束后清除掉漏钢,通过检修使夹辊转动灵活。 2.2.5拉矫机(2连铸机) 2.2.5.1水罩堵塞,冷却水不通,须及时更换。 2.2.5.2水冷旋转接头漏水,通常由于紧固螺栓松动或o型圈失效所致。 2.2.5.3减速机与辊轴座的连接螺栓常松动,须经常检查紧固。 2.2.5.4销轴(支撑上辊架)经常窜出,要及时检查。 2.2.6移钢机 2.2.6.1在某个拨爪被铸坯挡住的情况下操作移钢机移钢,使移钢机齿轮爬上齿条,车体
29、跳起落下,损坏设备。 2.2.6.2限位失灵,使移钢机的齿轮转出齿条,车体下落。 3 设备检修作业标准 3.1检修内容 3.1.1 检修油、气、水系统的泄漏点。 3.1.2 对所有加油点检查确认。 3.1.3 清除结晶器振动装置粘溅的冷钢残渣及更换断裂的弹簧板。 3.1.4 清除二冷段粘溅的冷钢,检修或更换辊子,使各辊转动灵活。 3.1.5 检查更换泄漏严重的气缸、液压钢。 3.1.6 检查更换传动不正常的拉矫机辊子。 3.1.7 更换堵塞的气缸塞和水冷板。 3.1.8 更换漏水严重的水冷旋转接头。 3.1.9检查调整三角皮带、辊道链条、钢丝绳的松紧度,更换磨损严重件。 3.1.10检查引锭杆
30、关节,清除冷钢杂物以及修理太松的关节。 3.1.11检查修理干油系统中油分配器的运行故障。 3.1.12检修稀油润滑站报警系统故障。 3.1.13拆检清洗各冷却水滤芯。 3.1.14检查更换气动三大件。 3.1.15更换损坏的轴承、辊子、销轴。 3.1.16更换各个部分地脚螺栓及联结螺栓。 3.1.17检查紧固各部分地脚螺栓及联结螺栓。 3.1.18解体清洗检查各传动减速机,更换损坏及磨损严重零部件。 3.1.19解体检查结晶器振动装置,更换磨损和损坏件。 3.1.20二冷段对弧。 3.1.21检查大包回转台紧固螺栓预紧力。 3.1.22更换变形严重的切前、切后辊道及其他辊子、轴承座。 3.1.23检查或更换联轴器。 3.1.24全面检查液压站各阀,更换磨损件。 3.1.25全面检修各气动阀门站。 3.1.26更换或调整冷床滑轨。 3.1.27清洗检查各干油、稀油泵,更换磨损件。 3.1.28翻钢机、移钢机和推钢机解体检修,更换磨损件。 3.1.29大包回转台平面轴承清洗、
- 温馨提示:
1: 本站所有资源如无特殊说明,都需要本地电脑安装OFFICE2007和PDF阅读器。图纸软件为CAD,CAXA,PROE,UG,SolidWorks等.压缩文件请下载最新的WinRAR软件解压。
2: 本站的文档不包含任何第三方提供的附件图纸等,如果需要附件,请联系上传者。文件的所有权益归上传用户所有。
3.本站RAR压缩包中若带图纸,网页内容里面会有图纸预览,若没有图纸预览就没有图纸。
4. 未经权益所有人同意不得将文件中的内容挪作商业或盈利用途。
5. 装配图网仅提供信息存储空间,仅对用户上传内容的表现方式做保护处理,对用户上传分享的文档内容本身不做任何修改或编辑,并不能对任何下载内容负责。
6. 下载文件中如有侵权或不适当内容,请与我们联系,我们立即纠正。
7. 本站不保证下载资源的准确性、安全性和完整性, 同时也不承担用户因使用这些下载资源对自己和他人造成任何形式的伤害或损失。