破译丰田生产体系的DNA
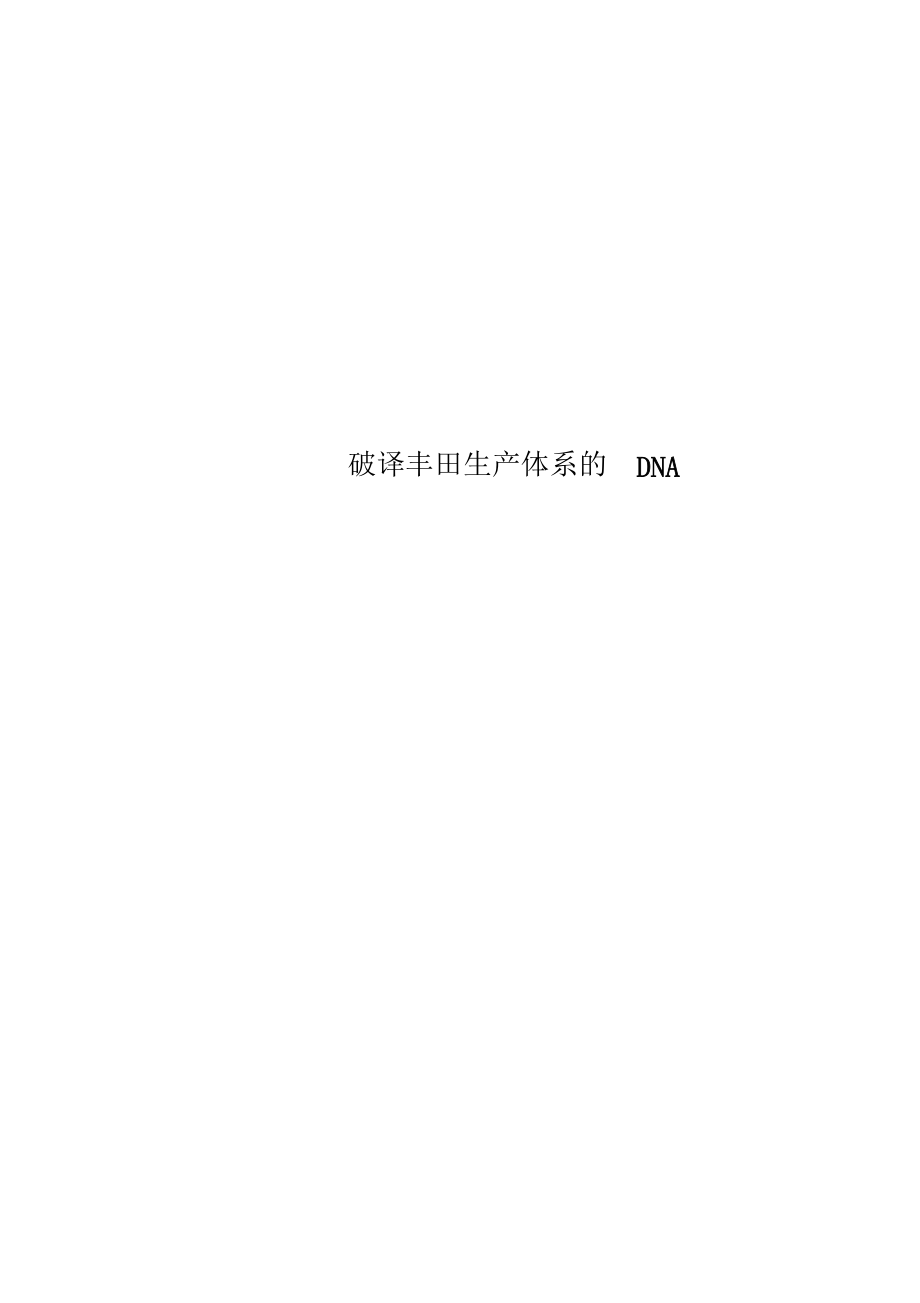


《破译丰田生产体系的DNA》由会员分享,可在线阅读,更多相关《破译丰田生产体系的DNA(34页珍藏版)》请在装配图网上搜索。
1、破译丰田生产体系的DNA破译丰田生产体系的 DNA 2008-06-28 16:34 分类:技术细节戦蒂文 斯比尔(Steven spear)肯特 鲍恩(H . Kent Bowen)长期以来,丰田生产方式或称丰田生产体系 (Toyota Production system , TPs)被誉为是丰 田公司卓越制造的奥秘所在。该体系一些独特的 实践方法如看板(kanban card)和质量管理小组” (quality circle) 广泛应用到其 他领域。事实上,在努力向全球最优秀的制造公 司看齐的过程中,通用汽车(GM)、福特汽车(F0rd)和克莱斯勒公司(Chrysler)各自独立地推 出了
2、一些重大举措,以便建立一套类似于丰田的 生产体系。不但汽车类企业纷纷效仿,在许多其 他领域,如航空航天、消费品、金属加工和工业 制品等等,企业也尝试采用这种生产方式。奇怪的是,虽然丰田毫无保留地公开了自 己的做法,但能够成功模仿它的制造商却寥寥无 几。丰田在日本和美国设有工厂,成千上万家企 业的无数经理人曾经去拜访取经,但却发现无法 复制丰田的绩效。许多人认为丰田的成功奥秘一定根植于它的日本文化背景之中。但事实并非如 此其他的日本企业,例如日产(Nissan)和本 田(HOnda),也难以望其项背;再者,丰田把它 的生产方式也成功移植到了全球各地,其中就包 括北美,1999年丰田公司在北美地区
3、的轿车、 小型客货车和轻型卡车的总产量超过了100万辆。那么,破解丰田生产体系的成功奥秘为什 么这样困难?我们认为,问题出在人们把参观工 厂时看到的具体工具和做法与生产体系本身混 为一谈了。这使得他们无法理解该体系中一个明 显的悖论一一丰田工厂中的各种活动、工作衔接 和生产流程都有严格的明文规定,但实际操作却 非常灵活、有很强的适应性。而且,这些活动和 流程也常常在人们的挑战和质疑之中被推向更 高一层的绩效水平,使得丰田公司能够持续创新 和改进。要洞悉丰田的成功之道,你必须首先破解 这个悖论一一你必须明白,正是一丝不苟的严格 规程给丰田带来了灵活性和创造力。这是我们对 丰田生产体系深入研究之后
4、得出的结论。在历时四年的广泛研究中,我们对丰田40余家工厂的内部运作方式进行了考察。这些工厂分布在美 国、欧洲和日本等地,有些是按照丰田方式运作 的,另外一些则不是;当中既有流程型生产企业 (process manufacturer),也有离散型生产企业 (discrete manufacturer);它们的产品包括预制 式房屋、汽车零配件和总装线、移动电话、打印 机、塑料注模制品(injection molded plastics) 和挤压铝型材等等。我们考察的对象不仅包括常 规的生产流程,还包括一些服务型职能,例如设 备维护、工人培训和管理、物流与材料搬运,以 及流程设计与再设计等等。我们
5、发现,对于外部人士来说,关键是要理 解:丰田生产方式造就了人人都是科学家的一个 组织。无论何时制订一项规程,丰田制订的都是 日后可以检验的一系列假设。换句话说,它采用 的是科学方法(scientific method)。在进行任何 改进之前,丰田都会采用一个解决问题的严格流 程:对事态现状进行详细评估,并且制订改进计 划实际上,该计划就是对拟定的变革进行实 验和验证。这种科学严谨性哪怕少一点点,丰田的变革就会像盲人赶路,成为一种随意莽撞的尝 试,并导致失误频频。这种科学方法显然在丰田已经根深蒂固,这 就是为什么在这家企业中,高度的规范化和结构 化并不像人们想像的那样会造成一个命令与控 制的环境
6、。事实上,在观察工人们工作并协助他 们设计生产流程时我们发现,该体系总是鼓励员 工和经理们积极参与实验一一这种实验被普遍 认为是学习型组织(Learn ing orga nizatio n)的 基石。把丰田与其他企业区别开莱的,也正是这 一点。四大规则蘊涵在丰田生产体系之中閒隐性知识(tacit knowledge)可限用四条基本规则来概 括.这些规则指导着每一产品和服勢所涉及的每一项作业、每一处衔援和每一条流程路 线的设计、实施和改进.这四条规则如下:规则一:所有工作的內容、袂序、时间和结果都必须明确规定规则二:每一种客户一供应商关系善恥须是直接的.发送要求和得封回应的方式必 须明确无误,非
7、“是即即W规则三:每一种产品和服务的流转路线書腕濒简单而直接.规则四:所有的改进都必须在老师的指导下、搜照科学的方法、在尽可能底的组织 层面上进行.这四条规则要求,企业的各种作业、衔接和凉程路线必狈能够进行自我检测,以自 动发出间题警示.正是由于不断地对1旬题做出响应,看说脩化的体系才得以保持柔性,丰田生产体系以及在背后支撑该体系的科学 方法,并不是强制推行的,甚至也不是有意为 之,而是经过50多年,慢慢地于实践中自然而 然形成的。因此,该体系的发展过程从未有过书 面记载,而丰田的工人们也常常说不清楚是怎么 回事。所以,外人一般很难洞悉其中的奥秘。在 本文中,我们试图揭开丰田生产方式的神秘面
8、纱,揭示该体系的内部运行机制。我们将详述四 条原则,其中三条是设计规则,说明丰田如何将 所有的作业流程变成一项项实验;另一条是改进 规则,讲述丰田怎样把科学方法传授给组织中各 个层级的工人。在我们看来,正是这些原则,而 非人们在参观工厂时所看到的具体做法和实用 工具,成了丰田生产方式的精髓。我们把这些原 则视为丰田生产体系的 DNA,原因也在于此。 下面,我们来仔细看一看这些原则。规则一:员工如何作业丰田的经理们认识到, 魔鬼存在于细节之中 (细节决定了成功与否),所以他们要确保所有作 业的内容、次序、时间安排和最终结果都有明确 规定。例如,在安装汽车座椅的时候,工人们总 是依照一定的次序来上
9、螺栓,而拧紧每个螺栓所 需的时间和转矩也都有明确规定。这种精确性不 仅体现在生产工人的重复性动作中,也反映在所 有员工的作业中,无论他们属于哪个职能部门, 或者处于哪个层级的职位,都必须严格遵循精确 的流程。丰田体系的第一条潜规则就是,必须对 每项作业活动详加说明。坦率地说,这条原则好 像很简单,似乎谁都能理解,谁都能轻松效仿。 但实际上,丰田之外的经理人和丰田的合作伙 伴,大多数都未能把该原则应用到工作的设计和 执行当中 尽管他们自认为是做到了。让我们来看看,在一个典型的美国汽车工 厂,装配工如何安装副驾驶位置上的座椅:他们 从纸板箱里取出4个螺栓,再拿一把扳手走到汽 车跟前,把螺栓拧紧,接
10、着在计算机里输入一个 代码,表示这项工作已经完成无误,然后等下一 辆汽车过来。通常,熟练工要给新手一定的培 训一一向新工人示范如何操作。当新手碰到任何 问题,例如未能拧紧某个螺栓或者忘记输入计算 机代码,就会有经验丰富的同事在一旁给予帮 助。这道工序听起来简单明了,那么问题出在哪 里呢?问题在于,这些规定实际上允许 甚至 假定一一工人们的操作方式有巨大差异。没有人 意识到,新手的作业方式与富有经验的老员工相 去甚远一一有些人习惯先拧上后面的两个螺 栓,然后再把前面的两个螺栓拧上,另一些人则 正相反;有些人喜欢先把四个螺栓都摆放好,然 后再一一拧紧;还有些人则可能放一个就拧紧一 个。所有这些差异
11、都会导致质量和生产率下降、 成本升高。更重要的是,这些 差异掩盖了工作方 式与结果之间的关联性,从而妨碍了组织的学习 和改进。在丰田的工厂里,对于某一项工作,操作工(不 论新老,也不论普通员工还是主管)都遵循着一 套严格规定的步骤。如果稍微偏离操作规程,问 题就会立即显露出来。下面,我们到位于美国肯 塔基州乔治敦市(Georgetown,Kentucky)的丰 田工厂看一看,了解那里的工人是如何安装佳美 (Camry)汽车的副驾驶座椅的。这道工序被分为 7项有序的任务,当车辆以固定的速度通过工作 区时,操作工必须在55秒钟内依次完成所有这 7项任务。如果工人发现自己先于第4项任务(安 装座椅前
12、部的两个螺栓)而完成了第6项任务(安 装座椅后部的两个螺栓),那么这道工序的完成就与最初的设计存在差异,这意味着出现了差 错。同样,第4项任务应该在第31秒前完成, 如果工人在第40秒钟时仍在执行这项任务,那 么也表明出现了差错。为了使问题更加容易被察 觉,工厂把工作区的地板按长度划成了10等分。如果工人在跨过第6个标记时(也就是进入 该工序已经有33秒钟),却尚未完成第4项任 务,那么这名工人和他的组长就知道,他已经落 后了。由于能够立即发现偏差,所以工人及主管 就能马上采取行动,纠正这个错误,然后再决定 如何修改流程规定,或者对该工人进行再培训, 以防止差错再次出现。(参见副栏丰田工人如何
13、 学习规则”其中简要介绍了工人们通过怎样的 方式来学习对工作的设计)即使是一些复杂的、不常见的活动,例如在 新工厂培训非熟练工人、推出一个新车型、更换 生产线,或者把设备从工厂的某个区域移至另一 个区域等等,也是按照这条原则来设计的。以丰 田的某个日本供应商为例,该公司为了应对某些 产品的需求变化,必须把设备从工厂的一个区域 搬迁至另一个区域,以建成一条新的生产线。这 个搬迁项目被分成14项独立的作业,每项作业又被进一步细分和设计为一系列任务,并指派专 人按照规定的次序执行每项任务。在搬每台设备 的时候,都将任务的实际执行方式与原始设计进 行对比,如有差异立刻就会发现。规则一要求工人们必须严格
14、按照规定的步骤 顺序完成工作,这样就迫使他们在行动中检验原 始的假设。完成这项作业会对工作设计中的两个 隐含假设进行检验:第一,完成这项作业的人有 正确执行任务的能力;第二,完成这项作业确实 会带来预期结果。还记得安装汽车座椅的工人吗? 如果他不能在规定的时间按照规定的方式把座 椅安装妥当,那么他显然至少把两个假设中的一 个给推翻了,说明这项作业需要重新设计,或者 这名工人需要重新培训。丰田工 人如何学习规则如果说丰田生产体系的规则是隐性的,那 么它们又是怎样传播的呢?丰田的管理者并不具 体告诉工人和主管们如何工作.而是采用一种教 与学的方法,让工人们通过解决问题来领悟这些规则。例如.在教第一
15、条规则时,主管会来到工 作现场,向正在工作的工人提出一系列问题:你是怎样做这项工作的?你怎样判断自己做的方式是正确的?你如何知道自己的工作成果没有瑕疵?如果遇到问题,你会怎样处理?这一持续发问的过程.使得员工对自己的具 体工作领悟得越来越深刻。在经历了多次类似的 提问之后,这名员工就逐渐学会了如何按照规则 一来设计各种作业。所有的规则都是通过苏格拉底式的反复提 问和解决问题来传授的。虽然这是一种非常有效 的教学方法,但是员工获得的知识却是隐性的。 所以.只有当管理者有能力并且愿意用这种提问 方式来督促工人在实践中学习时,丰田生产方式 才能够被成功地复制和移植。规则二:员工如何进行工作衔接第一条
16、规则阐述的是人们如何完成各自的 作业活动,而第二条规则解释了工人之间的工作 衔接。我们将规则二表述如下:每个衔接环节都 必须是规范化和直接的,必须毫不含糊地明确规 定涉及的人员、提供的产品和服务的形式和数 量、每个客户提出需求的方式,以及满足需求 的预计时间等等。通过该规则,每个工人与负责 为他提供特定货物或服务的员工之间,就建立起 一种客户一供应商关系。所以,在决定由何人、 于何时、把何物提供给谁这个问题上,不存在任 何灰色区域(gray zone)。当某个工人要求得到 零件时,谁应当来提供、要供应多少数量以及何 时交货等等,这些都是明白无误的。同样,如果 某人需要帮助,那么谁应该提供帮助、
17、从哪里开 始帮助,以及提供哪些服务等等,也都是明白无 误的。在这里,我们真正关心的问题是,丰田员工 之间的互动方式是否有别于其他企业。仍以汽车 座椅的安装工为例。当他需要一盒新的塑料螺帽 时,他就会把需求通知发送给材料保管员,后者 就是螺帽的指定供应者。通常,工人会通过看 板”来提出需求,这是一张薄薄的卡片,上面写明零件的代码、一盒零件的数量、零件供应者的 地点,以及需要这些零件的安装工(即 客户名 字。在丰田工厂中,诸如“看板”与“安 灯(andon)*。等其他装置在供给者与需求者之 间建立起直接联系。由于有了深思熟虑的设计和 不折不扣的执行,所以这些衔接工作进行得很顺 畅,犹如奥运会上最出
18、色的接力队在传递接力棒 一样。例如,对于任何一种零件来说,一盒零件 的数量以及在外流通的零件盒数量,都是由生产 系统的具体状况一一距离和切换时间 (changeover time) 等决定的。同样,每个小组的工人数量也取决于以下几个因素:可能出 现的问题是什么类型,小组成员需要何种程度的 帮助,以及组长的技能和能力如何等。*编者注:安灯装置是一种警示信号系统其他企业虽然也投入了巨大的资源来协调员 工,但是员工的工作衔接往往做不到这么直接和 明确无误。在大多数工厂里,一线生产工人对材 料的需求和其他求助通常要绕个弯儿,通过一个 中问人才能到达供应者那里。由于没有专人负责,所以任何一个主管都可以回
19、应任何一项请 求。这种方法的最大缺陷是:当一个问题变成所 有人的问题时,就不再是任何人的问题了。丰田 显然很清楚这一点。此外,丰田要求在规定的时间内对供货需求 做出响应,这进一步降低了产生差异的可能性。 如果涉及服务方面的需求,更是如此。当一名工 人碰到问题时,他就应当立即求助,而指定的帮 助者则应当立即做出回应,并且在那名工人的作 业周期内把问题解决。比方说,工人应该每55秒钟安装好一个副驾驶座椅,那么他的求助就必 须在55秒之内得到回复和解决。倘若这个问题 不可能在55秒之内得到解决,那么这一失败就 等于对供应者与客户之间求助关系的假设提出 了质疑:也许是求助信号含糊不清;也许是指定 的帮
20、助者收到的其他求助要求太多,忙得无法分 身,或者是他解决问题的能力不够。用这种方式 不断地对假设进行检验,就保持了整个体系的柔 性,使得系统的持续改善和建设性调整成为可皆企业巻腿23大规團进行理阱 毎个员工就合不扁罐开農实验 在其际損柞中竣諡个人的炸业 藩动*客户供应笑熹.潦H踣线和改进掘施毎方窗的设计所包含的各种锻设.下表列出了 设槍萤方戒.以及锻设祓推輛后所采取的咱应揩施規则假设1 工人列机制絵麻携歸規定逬行 作业如果按JW规定进行作业产品 或艇务就不会有冊維.2 罢户対产品和St务的需淑.症 祥娄卵收/上是朗确的供蛊考能第満足喜户的需求.出规的问薦应措施列断工人的鼻咒技壮朮章或韦野】舉的
21、 实际能力并邊行氓岂的坍训或取ift 修改设计活就-3 与淤用路线it立关験的毎个俱应将却是亞1!的,任何崇与適程路线慶立关联的 慎莊者邮垦不需雯的.果个工人戍崭果台机卅 算不提:JI的必不可少 某个未殺鶴左的彊应* 扯供丁中间猜筍或J务.4 討柞宣筍播馥番谨思腿线进冥隊结匸与發勒纯果存行的黑项受華能够陽低咸本疫差弄anv骑短前时何、小枇以及提豪安全悝算改邁度媳n协和覇定的.“定咒际需求的时洪应 看的实毎能力做岀判补 再遇训.蜡 改惮业活胡或番对暮户烘府曲戟 插新合理E时.判斷诵供厳舟为什么fit不必雾的并 斷设计満程路线.了解为什么區个未被指定的供应书瓯 而星实际中UK的一殊殊斷设计 激檯路
22、线了Hit件业的实际执行方或或者工 柞砌摂戒注軒賂垓的实時远作方衣 料斷变革指麗的实际效異新没计 这取变葦络搭这种要求工人立即求助的做法,明显与管理 者的直觉相违背管理者往往习惯于鼓励工 人在求助他人前依靠自身的努力解决问题。但那 样的话,问题就会被掩盖起来,不仅没有让众人 知情,也不会在整个公司范围内得到解决。假如 一开始就让工人们靠自己来解决问题,而后又由 他们任意决定问题严重到什么程度时才提出求 助,那么事情就会变得更糟糕。不但问题会堆积 如山,解决问题的时问也会大大推迟,至挪时, 关于问题的真正起因可能就无从查找了。规则三:生产线应如何构筑在丰田公司,构筑任何一条生产线,都必须 保证产
23、品或者服务能够沿着简单、确定的路线流 动,除非生产线需要重新设计,否则该路线不得 轻易更改。原则上, 在丰田的任何一条供应链 上,都不能有分岔或者回流等干扰正常流程的现 象这就是第三条规则。为了更好地理解该规则的具体含义,我们 再回到座椅安装这个例子。当他需要更多的塑料 螺帽时,就向负责为他供给螺帽的材料处理员申 领,该指定供应者又向工厂内部仓库的指定供应 者申领,后者则把需求直接发给螺帽厂家发货处 的指定人员。通过这种方式,所有参与产品生产 和交付的人员 从丰田的工厂到制模公司,甚 至到塑料粒子的制造商一一都被一条生产线联 系在一起。按照第三条规则设计生产线的时候,关键在 于货物和服务并不是
24、朝着任意一个有空暇的员 工或机器流去,而是流向某个指定的员工或者机 器。如果由于某种原因该员工或者机器不能及时 处理,丰田就会将其视为一个问题,这意味着生 产线需要重新设计。然而,每个产品都必须按照简单、既定的 路线流动这条规定,并不意味着每条路线只能由 一种产品专用。恰恰相反,丰田工厂里的每一条 生产线都适用于多种产品类型,通常比其他公司 生产线上适用的品种要多得多。第三条规则不仅适用于产品,也适用于服 务,如对求助的回应等。举例来说,如果座椅安 装工需要帮助,那么提供帮助的也必须是指定人 员。如果该人员不能提供必要的帮助,那么他又 会向自己的指定帮助者求助。在丰田的某些工厂 里,这样的援助
25、线路可能包括 3个、4个或者5 个环节,涉及人员从基层的车间工人一直到高层 的工厂经理。第三条规则不仅与关于生产线和共享资源 的常规思维相悖,甚至与大多数人想像中的丰田 生产方式也不同。照常理来说,当产品或者服务 沿生产线流动时,应当流向下一台空闲的机器或 者有空暇的员工来处理。同样,大多数人也认 为,谁有空闲就应该由谁来提供帮助,而不应局 限于某个指定人员。例如,我们对某汽车零件供 应企业进行研究时发现,大多数零件都可以在不 止一台压力机上进行冲压或者在不止一台焊台 上焊接。在采用丰田方式之前,该公司的做法是 把零件传送到下一台空闲的机器上或者下一名 有空暇的焊工那里。但自从在丰田公司的指导
26、下 采用了丰田方式之后,这家企业的每种零件的生 产流程就严格遵循一条流水线。第三条规则要求所有的线路必须得到明确 规定,从而保证线路的每次使用都相当于一次实 验。根据第三条规则所设计的线路包含着两个假 设:所有与该线路有关联的供应者都是必需的, 而任何未与该线路建立关联的供应者都不是必 需的。假如汽车零件供应企业的工人们希望转向 另一台机器或者焊台进行生产,或者转向非指定 的帮助者求助,那么他们就可以下结论:自己的 实际需求或实际能力与自己的初始预期并不相 符。此外,对于应该使用哪台压力机或者焊机, 也不应含糊不清。所以,这意味着工人们有必要 重新审查生产线的设计。就像规则一和规则二那 样,规
27、则三能够使丰田开展实验,同时又保持了 柔性和响应度。规则四:应如何持续改进发现问题只是第一步。要持续有效地变革, 人们必须知道如何变革以及谁应该负责变革。丰 田公司明确地指导员工如何进行改进,而不是指 望他们单凭个人经历获得教益。于是,就有了第 四条规则。具体而言,规则四规定:对生产作业、 工人或者机器之间的工作衔接以及流程路线所 做的任何改进,都必须按照科学的方法,在老师 的指导下,在尽可能低的组织架构层面施行。下 面,我们首先了解丰田员工是如何学习科学方法 的。如何学习不断改进爱信精机公司(Aisin Seiki)是丰田集团的下属企业,为汽车提供动力 传动系统(power train)等较
28、精密的产品。1986 年,该公司建造了一条弹簧垫的生产线,以消化 旗下某工厂过剩的生产能力。自那时开始,弹簧 垫的品种从200个增加到850个,日产量则从 160块增加到550块,生产率提高了一倍。以下 通过一个实例,来说明他们是如何做到的。在一次访问该工厂时,一组弹簧垫装配工正 在学习如何通过重新设计工作来改进解决问题的技能,我们对此进行了观察和研究。起初,工 人们只负责各自的标准化作业,并不负有解决问 题的职责。后来,公司给他们分派了一名组长, 后者培训他们如何更好地找出问题并设立和检 验各种假设。换句话说,组长教他们如何应用科 学方法,按照前三条规则设计整个小组的工作。 这种做法取得了很
29、好成效。例如,该小组重新设 计了在弹簧垫上安装边带的方法,从而把次品率 减少了 90%。(参见副栏 爱信弹簧垫厂的按需 生产”)盪fu弹赞张厂的按為d三严汲値橘机公司生产的弹H S參达8503天内即可送1ft上门 然而.姥信工厂刼只像持柏当于1倚天 需求幅的糜肓 为了做到这一点.爰佶对个人的作业活动,中间货物和 腓务在供構取方之洶的工作衔接.収及尊条生产线实擁了数以千计的 改进捎施下表列出了这昨变革带来的显着成效.198619882PZ年1996估97年品种20032S670750850曰均产160230360530550人均产811132026生产率播数TOO138175197208成品摩存
30、(天釵) 遮配线条数3022 521.S1.53152为了改进,员工们必须清楚地陈述假设中 存在的逻辑关系。我们来看看,这一过程到底包括哪些内容。Hajime Ohba先生是丰田供应商支 持中心(Toyota Supplier Support Center) 的总 经理,他正在对一家工厂进行考察,他的一名顾 问在这家工厂主持开展一项培训和改进项目(关 于丰田生产体系推广中心的职责,参见副栏丰田致力于培训“)该顾问的职责是帮助工人及其 主管把某条生产线的制造前置时间(1ead time) 缩短,而0hba先生此行的目的就是对该小组取 得的进展进行评估。在陈述时,小组成员首先描述了产品生产的 几个
31、步骤,然后讲述了机器在切换零件生产时所 发现的问题,并解释了针对每个问题所做的具体 改进。最后,他们总结说:原先,切换时间需要1 5分钟,我们计划把它缩短2/3,也就是5 分钟内完成切换,这样就可以把批量减少2/3。经过改造,我们最终在7. 5分钟内完成切换, 把时间缩短了一半。”陈述完毕之后,0hba先生询问工人们,为什 么未能实现当初设立的5分钟切换的目标。人们 听后颇感吃惊,因为他们毕竟已经把切换时间缩 短了一半,而0hba先生的询问表明,他显然认 为还有更大的改进余地。工人们解释说,这关系 到机器的复杂性、技术困难以及设备升级成本等 因素。针对这些回答,Ohba先生提出了更多的 问题,
32、每一个问题都促使顾问和工人们更认真地 回顾和质疑自己的基本假设:什么可以改变以及 什么不可以改变。这些假设指导并制约着他们解 决问题的方式,例如,是不是必须用四个螺栓 ? 或许只要两个螺栓就可以完成切换吧 ?切换中的 每个步骤都是必不可少的吗?是否其中的一些步 骤可以合并或去除?当询问工人们为何未能实现 最初设定的5分钟目标时,Ohba先生并不是暗 示这个小组失败了,而是试图使他们意识到,由 于对基本假设质疑得还不够深入,所以工人们没 有能够发掘所有的改进机会。Ohba先生坚持这样做还有另外一个理由他试图让工人们明白,他们的这次改进活动称不 上是一次真正的实验。由于工人们认为缩短切换 时间和减
33、少批量是一种优化生产,所以在这一前 提思想下他们设立了 5分钟的目标。他们认为, 通过采取自己计划好的具体改进措施,可以取得 一定的成果,所以就一厢情愿地设立了目标,而 不是根据假设进行合理的预测。所以,他们的改 进活动从一开始就没有设计成实验,没有为其确 立明晰、表述清楚、可验证的假设,比如: 只 要我们做出下述各项具体变革,我们就会得到这 个具体结果”。尽管工人们的确大幅缩短了切换 时间,但未能检验自己的这一做法所隐含的各种 假设。对于Ohba先生来说,至关重要的一点是 让这些工人及其主管认识到:如何变革以及做出 什么变革,两者同等重要。由谁来负责改进 一线工人对自己的作业 进行改进,而他
34、们的主管则担当着导师的角色, 为他们提供指导和帮助。假如在同一装配区内, 一位工人与指定供应者之间的衔接出了问题,那 么这两个人就在同一位主管的帮助下采取改进 措施。例如,上文提到的爱信精机的小组就是由 装配工人和主管组成的,主管同时担任工人的指 导老师。如果要进行更大规模的变革,那么丰田 要确保改进小组由直接受影响的员工和负责监 管该路线的主管组成。即使在工厂的最高层,也是这样的做法。 比如,在爱信的弹簧垫工厂我们发现,将生产线 从三条改回到两条(为了应对产品类型的增多, 生产线曾被增加到三条),是由厂长负责的。他 之所以被牵涉其中,不仅仅因为这是一次较大的 变革,而是因为他对总装配线负有监
35、控责任。通 过这种方式,丰田确保了组织各个层级的员工都 能够不断学习和持续改进。当然,我们也看到, 必要的时候丰田会请来外部专家,以保证学习过 程的质量。从长期来看,采用丰田生产方式的企业, 其组织结构将发生变化,以便对所遇问题的性质 和发生频率做出反应。然而,因为组织的变化通 常发生在较低的层面上,因此很难被局外人察 觉。这是因为,问题的性质决定了应当由谁来负 责解决问题,以及组织结构应当怎样设计。其结 果之一就是,不同的组织机构可以和谐地共存于 同一家工厂。我们来看看丰田汽车位于日本 Kamigo的 发动机制造厂。该工厂有两个制造部门,各有 3 个独立的生产车间。1998年夏天我们参观该工
36、 厂时发现,制造一部的生产人员向车间主管汇 报,而流程工程师则直接向部门领导汇报;然 而,制造二部的工程师却分散在3个车间里,与 生产工人一样受各自车间主管的领导。当然,这 两种组织结构从本质上说并没有哪个更胜一 筹。据受访者解释,这是因为制造一部所碰到的 问题要求工程师们必须相互学习、共享工程技术 资源;而制造二部遇到的问题则要求生产人员和 工程人员在一个车间内紧密协作。所以,组织结 构之间的差异,实际上反映了两个部门遇到了不 同的问题。丰 田致力于培训我们研究过的所有采用丰田方式进行管理的 企业,都信奉一个共同的理念 人是公司最重 要的资产为了打造企业竞争力,就必须对员工 进行投资.不断提
37、高他们的知识和技能。这就是 为什么在这些企业中,管理者不仅应当有能力做 所有下属的工作,而且应当指导手下的员工按照 科学方法去解决问题。这种领导模式既适用于基 层的 组长主管,也适用于企业的最高层领导。 这样,丰田的每位员工都参与人力资源的开发与 发展。实际上,在丰田有一条逐级培训的途径:从工厂经理开始由上至下地给每个层级的员工 传授知识,为每个人提供培训。为了强化学习和改进流程.丰田集团 (Toyota Group)的每家工厂和主要事业部都聘 用了一批丰田生产方式的专家顾问他们的主要 职责就是帮助高级经理们把组织推向理想的状 态。这些集学习者、领导者和教导者三个角色于 一身的顾问通过发现更微
38、妙和更复杂的问题并 指导人们如何科学地解决问题来使组织趋于完 美。许多顾问都在丰田运营管理咨询部 (Toyota s OperationsManagementConsulting Division , OMCD)接受过强化培 训。该咨询中心设在日本.是在大野耐一(丰田生产体系的设计师之一)的积极倡导下成立,目 的是在整个丰田集团及其供应商中间发展和传 播这一体系。丰田的许多高管.包括丰田汽车公 司仃oyota Motor)的新任总裁张富士夫 (Fuiio Cho) 都在OMCD锤炼过领导技能。在接受培 训期间(可能长达数年)这些经理人不再担负任 何一线要职,而是在丰田及其供应商进行的改进 和培
39、训活动中担任领导。以这种方式为丰田的工 厂和物流运作提供支持.OMCD就相当于一个 培训中心.为顾问们提供了解决难题并且教他人 解决难题的实践机会,从而使他们领导技能得到 提高。1992年.丰田在美国成立了丰田供应商支 持中心(Toyota Supplier Support Center) ,为 北美企业提供丰田生产体系的培训。该中心按照 OMCD的模式建成,已经为140多家公司举办 过研讨会,为80家企业提供过直接帮助。尽管 这些企业大部分是汽车配件供应商,但是属于丰 田的专有供应商却很少:接受培训的还包括来自 其他行业的企业、大学、政府机构和行业协会 等。事实上,本文的不少研究成果来源于其
40、中一 位作者的经历.他曾经在丰田供应商支持中心的 某一团队任职5个月,在一家为丰田和另外两家 汽车装配厂供应零配件的工厂推行丰田生产体 系。丰田的理想化体系通过向各个层级的员工反复灌输这种科学方 法,丰田公司确保员工在实施变革计划时,都能 明确地阐述所要检验的各种预期结果。此外,我 们还发现,在所有采用丰田方式的企业里,人们 都抱有一个共同的目标。他们知道,什么样的体 系才是理想的生产体系;正是这一共同愿景 (shared vision)激励着他们不断超越自己不仅仅停留于满足顾客的现有需求,而是不断地 持续改进。这种理想观念深深根植于每个人的心 中,我们认为这是理解丰田生产体系的关键。谈及理想
41、,丰田员工并不把它当成一个抽象 的哲学概念,而是在脑海里有一个具体定义,这 个定义在整个公司都是一致的。具体地说,丰田 的员工们认为,一个理想的人、理想的小组或者 理想的机器所创造的成果,都应该具备下述特 征:没有缺陷(也就是,功能和性能都达到顾客的 期望);可以一次满足一个需求(批量可为单件);按需供应客户所要款式;能够立即交付;在生产中不浪费任何物料、劳力、精力或 其他资源(例如与库存相关的成本);生产环境必须保证所有员工在身体上、精 神上和工作上三个方面的安全。我们发现,在采用丰田方式的工厂里,工人 们通过不断改进,把工厂的运营推向这一理想状 态。例如,在某机电企业,工人们发明了许多精
42、巧的检测错误的器具,用两个简单而明确的信 号 是和 否来表示产品是否完美无瑕,产 品无瑕疵才是理想化的生产体系。在另一家生产 模注零件的工厂里,工人们缩短了更换大型模具 的时间,从原本已经很短的5分钟缩短到现在的 3分钟。这就使得该厂每种零件的批量标准减少 了 40%,接近每批只生产一件的理想目标。在 朝理想努力的过程中,丰田可能暂时会把某个方 面看得比其他方面更重要。有时,这种做法看起 来似乎与大众眼中的丰田方式不相符合。比如, 我们曾经观察到,丰田有些工厂的库存或者生产 批量,高于或者超出了一般人所认为的即时生产(just in time)应保持的低水平(关于这一点,参 见副栏 丰田生产体
43、系中的临时对策”。大规模定制(mass customization)是一种能力,是以最高的效率和最低的成本,生产同一 产品的几乎无限多的变化品种。丰田眼里的理想 化状态,与这种流行的概念有许多共同之处。一 言以蔽之,丰田的理想工厂就是这样一个地方: 顾客把车开到装货处,提出对某项定制产品或者 服务的要求后,需求立即得到满足,并且以最低 的价格获得完美无瑕的产品或服务。只要丰田工 厂或者丰田员工的作业还达不到这种理想状 态,这一缺憾就会给丰田人带来压力,促使他们 不断创新和改进。丰田 生产体系中的临时对策对于看板和安灯等工具或做法,虽然外人 趋之若鹜,但丰田自己并不认为是丰田生产体系 的根本所在
44、,而只把它们视为对某些具体问题采 取的临时举措,等找到更好的解决办法或者当条 件改变时.它们就会被束之高阁。因此,它们被称为对策”(Countermeasure),而非解决方 案” (Solution).因为后者往往意味着问题的永久 性解决。多年来,丰田开发了一整套用做对策的 工具和做法,但是经过了持续改进许多对策已 经发生了变化.甚至被废弃不用。所以,某家企 业是否采用某种特定工具或者做法,并不能说明 该企业是否真正应用了丰田的设计规则和改进 规则。尤其在零库存(zero inventory)这一问题 上人们往往认为那是丰田生产体系的核心,但 我们却观察到丰田多次把增加材料库存作为一 项对策
45、。理想的生产体系可能不需要任何库存. 但是在实践中遇到以下情况时,库存还是有必要 的:故障时间或者生产量难以预知 由于出现 了意外的机械故障,员工或者机器无法立即响应 需求。所以,需要维持一定的安全库存(safetystock) 以使客户免受偶发事件的影响。负责确 保机器或者流程稳定性的人员负责管理安全库 存,并且他会努力降低故障的发生频率并缩短故 障时间从而减少安全库存量。切换时间过长机器从生产一种产品切换 到生产另一种产品时遇到的困难,可能使供应者 无法立即做出响应。所以,供应者一次生产的产 品数量会不止一件,而把多余的产品作为库存, 以便在日后立即响应客户需求。当然,供应者会 不断努力缩
46、短机器切换时间,尽可能地缩小批量 并减少存货。在这里,机器操作工和组长负责解 决问题并采取对策.他们承担着缩短切换时间和 缩小批量的责任。客户对产品种类与数量的需求变化莫测 在有些情况下,顾客的需求庞大且难以预测.所 以工厂难以迅速调整生产速度跟上变化.这时就 需要采取对策.在装运点及其附近设立缓冲库存 (buffer stock)。对产经理和销售经理来说,缓 冲库存相当于一个警示信号,提醒他们与客户接 触最直接的那个人必须帮助客户消除引起需求 动荡的潜在因素。在很多情况下,同一类产品存在于不同类 型的库存之中。尽管集中备库可以减少短期库存 需求但是丰田并没有把库存合并在一起。对于 一个以憎恨
47、浪费而闻名的管理体系来说,这似乎 听来有些荒谬。但是一旦我们认识到丰田管理者和工人们是在针对每个问题寻找相应的对策 时,这个悖论就可以解开了。规则对组织的影响假如说这些规则使得采用丰田方式的企业 变成了一个由多位科学家组成的、不断开展实验 的组织,那么为什么这些企业并没有陷入混乱 为什么一名工人在进行作业变革时,能够保证不 对生产线上的其他人产生负面影响?为什么丰田 在不断变革作业方式的同时,却仍然保证了生产 线的全速运转?换句话说,丰田如何做到在不断 改进的同时保持稳定?答案还是这些规则。这些规则使得员工能 够负责任地完成并改善本职工作,使得每个客户 与供应者之间的衔接规范化,并且把衔接和流
48、程 等问题的解决推到尽可能低的组织层面上。因 此,这些规则在组织中就创建了一个蜂窝状的模 块结构,而不是像传统的俄罗斯玩偶那样的层层 嵌套的结构。蜂窝状模块结构的最大好处就在 于,人们可以在某一局部做出设计变更,而不会 对其他部分产生不利影响。这就是丰田的管理者 能够高度授权,而不担心产生混乱的原因。应用 这些规则的其他企业也会发觉,自己能够进行有 效的变革,同时却不必担心产生混乱局面。当然,与采用丰田方式的企业相比,其他 企业的组织结构也具备类似优点。但是,我们在 研究中发现,但凡拥有全部这些特征的企业,没 有一家不是采用了丰田方式的。也许,只要像丰 田一样投入足够多的时间,最终你的企业也能建 立这样的组织结构。我们相信,假如一家企业能 够致力于掌握以上这四项原则,那么它就有可能 去成功复制丰田生产体系的 DNA,进而取得像 丰田那样的佳绩。
- 温馨提示:
1: 本站所有资源如无特殊说明,都需要本地电脑安装OFFICE2007和PDF阅读器。图纸软件为CAD,CAXA,PROE,UG,SolidWorks等.压缩文件请下载最新的WinRAR软件解压。
2: 本站的文档不包含任何第三方提供的附件图纸等,如果需要附件,请联系上传者。文件的所有权益归上传用户所有。
3.本站RAR压缩包中若带图纸,网页内容里面会有图纸预览,若没有图纸预览就没有图纸。
4. 未经权益所有人同意不得将文件中的内容挪作商业或盈利用途。
5. 装配图网仅提供信息存储空间,仅对用户上传内容的表现方式做保护处理,对用户上传分享的文档内容本身不做任何修改或编辑,并不能对任何下载内容负责。
6. 下载文件中如有侵权或不适当内容,请与我们联系,我们立即纠正。
7. 本站不保证下载资源的准确性、安全性和完整性, 同时也不承担用户因使用这些下载资源对自己和他人造成任何形式的伤害或损失。