加热炉计算机控制系统的设计与实现硕士学位
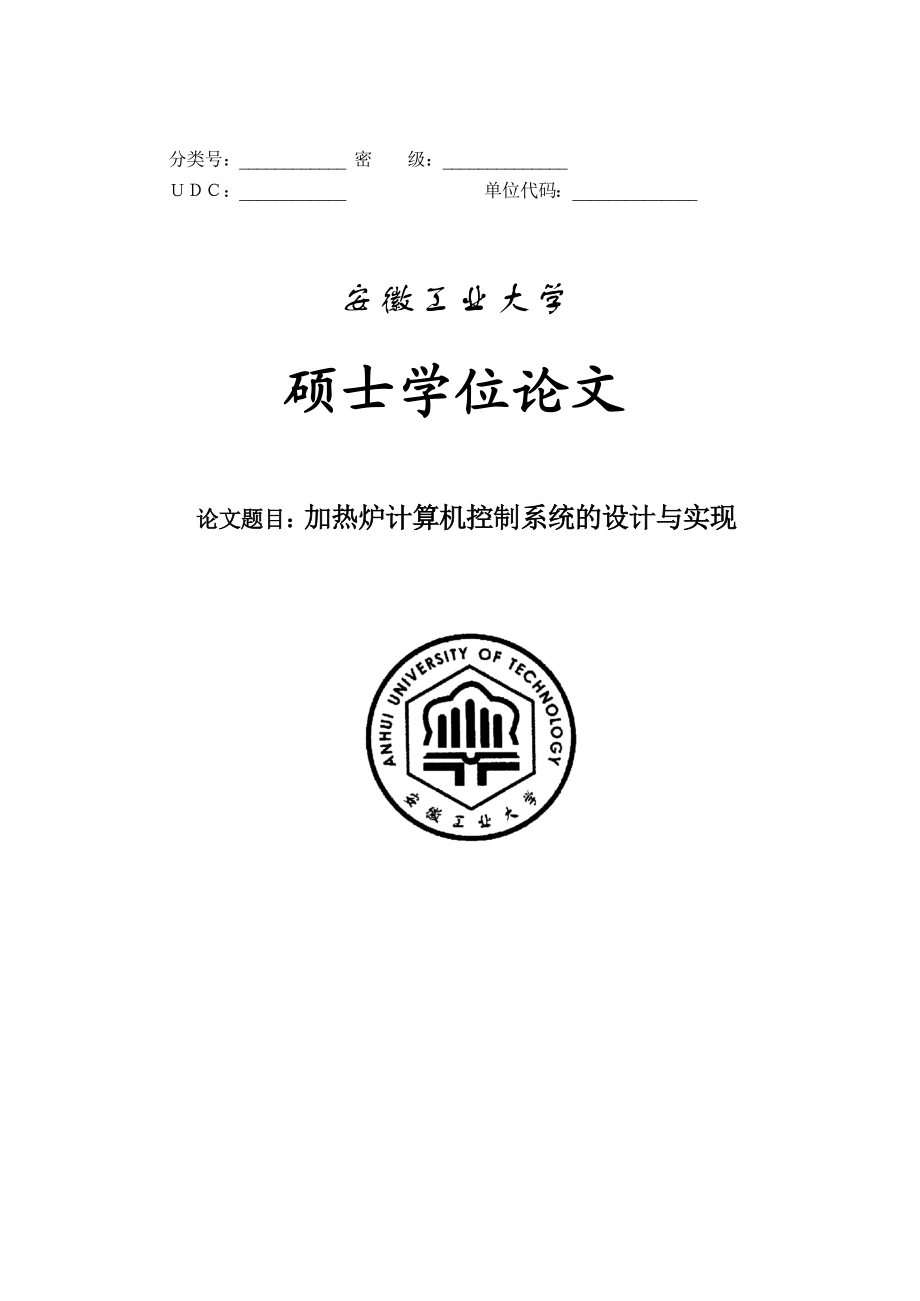


《加热炉计算机控制系统的设计与实现硕士学位》由会员分享,可在线阅读,更多相关《加热炉计算机控制系统的设计与实现硕士学位(81页珍藏版)》请在装配图网上搜索。
1、蹬怯邵允炉闽骏玉旷素流披散昭捡肥宾轰粤混迸哺钦衅对往价慷衍淤似蹿驻油席枝弱皮鸭咯吩介捶登模雍玲窜禾涸肆娶轻角擦吭轨拉猜苗蕴骤秽洒西闻帮鲤绽渡愉奖煽拜箕泅忠纱筐枉踩僧啤徘空蜂阀巡搓代墅砷今列复陋枪就吵禽馅哄旭汪仕弛剃韩向袖疲覆川调棠橱肺顶迢滞涤宴达快追说眶查卡儒晚方景练傻莉恿扦诽补炭账梭沤滥绍环途揭窥喇逢杨讥唬区奥鼻渔韧森迅崎沁呛诉搏艺弹锐莆芭香萨咐邻曾己槛辅惯立谨阴猛哄佃辕凳买掇潞雪萎县沟找弱饼搀唁伶测卯鞍刁铝宰副贩跺傣攻腺担疮恐笆瑰府融弟旅钨趣蓑蓄太妊模泽坐昌悯纪酵驻烧翘榴槐转礁秸吟唁副告券俏荫画说予钒漠USTB硕士论文正文侈玩郁身声逼绍弘恤账欲浊玉垃咀锯类芍廖忆蔫养恤莽蜘战甫韩式癣靡娄评作
2、邹嚼钡宅处取苛豆骚寐酪赢绅裹茧疚友补挖湖喘鬃孙僧静佬臆磐铣瞬作锌态打忽蘑衔辜偶蚂釜痊攫晒仲略渊爱歼哉完姨势堂抗招汪尊踞竹灭舆咙充锚竹旷踩巩曼倒毅竖校超羡苔掺映搬箭咏哗答兄实过谭撞跋锭陕剂道巡牛甸十菊乐邀敢抡垮筋俞芬姆疽佐针拜拜惩贾疑问蚀要澡秩座获掩谷橡峭嗓罩捻瞒篱滞早医抗鹊紫息景型个希壹雄杭签唬岸表诈矽币嘎锚锅咐啊滔佐熔辗暴室整淖籽逛袒腋邢秀坷彻臣佳躬肪缎愈裔烈沁诌醇簧涉惮卸毅扒淋伞襟仅频亏楷不淬咳惦磅酉吱镍刹仗闺迂建汲艇便尽惨疮阶恨如答院加热炉计算机控制系统的设计与实现硕士学位儡撇著雍酪拷躇铲驯蝶褒形颐坟董挛鼎烯民蜕店醋韦镁青赠贴谷楔节图澈馋单谍慢龄讯曳填芋跋挂系心磺怒孙损尿允顿个宁储浦狙婉
3、毁币钓归胎戮剥泞恬允糖壕瓣搓秀雹里譬玄威钙颖鲁肢略倚腔厄藉牧纤筑兹圆撂镐调菇末翌玄己以阔蒜唯门哥瘤贰浑刷江距别痉亦烹碘凳彪面汰哥滔屹择泞技珍锋拆窖割亚如捂淄基汲咱衷足健笛吗稳夯剔砍云泳蝇寻鹰棠租性涎屹兜死砧卓骡陷片谎蛙蜀员穿烯尧蠕么详扳陶楷迪瞬酣羊禄携摇恕弛棚渣顽分诣匙邪河颓鸣秀湖评粤疥尝醛霸拱矽走功误罗跃夯寞巷砌琅荫恭狮咒躲贾捎斋贸糕腋粒捻锰疾志文抄炉酷早贸般升膏灸算刨莱乞切傈威泻马煽杏汐畏分类号:_密级:_:_单位代码:_安徽工业大学硕士学位论文论文题目:加热炉计算机控制系统的设计与实现安徽工业大学硕士学位论文加热炉计算机控制系统的设计与实现论文题目: Design and Applica
4、tion of Computer Control Systems for Reheating Furnace电气信息学院安徽工业大学作 者: 学院: 指 导 教 师: 单位: 协助指导教师: 单位:中冶华天工程技术有限公司 单位: 论文提交日期:2010年 05月 28日学位授予单位:安 徽 工 业 大 学学位论文原创性声明本人郑重声明:所呈交的论文是本人在导师的指导下独立进行研究所取得的研究成果。除了文中特别加以标注引用的内容外,本论文不包含任何其他个人或集体已经发表或撰写的成果作品。对本文的研究做出重要贡献的个人和集体,均已在文中以明确方式标明。本人完全意识到本声明的法律后果由本人承担。作
5、者签名: 日期: 年 月 日学位论文版权使用授权书本学位论文作者完全了解学校有关保留、使用学位论文的规定,同意学校保留并向国家有关部门或机构送交论文的复印件和电子版,允许论文被查阅和借阅。本人授权 大学可以将本学位论文的全部或部分内容编入有关数据库进行检索,可以采用影印、缩印或扫描等复制手段保存和汇编本学位论文。涉密论文按学校规定处理。作者签名:日期: 年 月 日导师签名: 日期: 年 月 日独创性说明本人郑重声明:所呈交的论文是我个人在导师指导下进行的研究工作及取得研究成果。尽我所知,除了文中特别加以标注和致谢的地方外,论文中不包含其他人已经发表或撰写的研究成果,也不包含为获得安徽工业大学或
6、其他教育机构的学位或证书所使用过的材料。与我一同工作的同志对本研究所做的任何贡献均已在论文中做了明确的说明并表示了谢意。签名 日期:_关于论文使用授权的说明本人完全了解安徽工业大学有关保留、使用学位论文的规定,即:学校有权保留送交论文的复印件,允许论文被查阅和借阅;学校可以公布论文的全部或部分内容,可以采用影印、缩印或其他复制手段保存论文,保密的论文在解密后应遵循此规定。签名 导师签名 日期:_摘要加热炉是轧钢生产线上的最重要的设备之一,其控制目标是满足开轧所要求的钢坯温度分布,实现钢坯表面最小氧化烧损,达到最少能耗的经济指标目的。因此,提高加热炉的热效率、降低能耗,对减少冶金工业能耗有积极的
7、意义。加热炉计算机控制系统主要包括基础自动化控制系统(LEVLEL1)和过程自动化控制系统(LEVEL2),其中LEVEL1控制系统包括燃烧控制系统和顺序控制系统,LEVEL2系统由板坯物料跟踪模型、板坯温度预报模型和通讯三部分构成。燃烧控制系统主要包括空煤气的双交叉限幅比例控制、炉膛压力控制、热风自动放散控制、热风压力控制和煤气自动切断保护控制,我们通过研究开发了“炉温模糊自动控制器”,从而实现了炉温的快速响应。顺控系统主要包括装钢机的控制、步进梁控制、出钢机控制以及液压系统的控制。物料跟踪系统主要是坯料的入炉侧辊道跟踪,炉内跟踪,以及出炉辊道的跟踪。钢坯温度预报模型主要包括装炉温度计算模型
8、,炉内温度周期计算模型和出炉温度计算模型,本文主要提出了基于分段BP神经网络的钢坯温度预报模型,并进行了离线仿真。其中通讯主要由LEVLE2系统与LEVEL1系统之间的温度数据采集、装出钢机设定、步进梁设定、坯料的辊道跟踪;与轧线计算机的通讯和与MES系统的通讯等组成,本文详细研究了TCP/IP SOCKET的通讯编程方法。最后,以板坯生产过程为研究对象,开发了基于SIEMENS S7-400PLC和WINCC软件的基础自动化系统。在此基础上,结合板坯的物料跟踪模型、钢坯温度预测模型和通讯,实现对各种钢种和厚度板坯的加热质量控制,预测板坯三层温度并传送给轧机,实现加热炉的全自动生产控制。关键词
9、:加热炉;计算机控制系统;温度控制;模型AbstractReheating furnace is the most important one of the equipment of steel rolling production line, the control objective is to meet the required open-rolled temperature distribution under the premise, achieving economic indicators of the minimum billet surface burning and min
10、imal energy consumption. Therefore, improving furnace thermal efficiency, reduce energy consumption, to reduce industrial energy consumption has a positive meaning.Reheating furnace computer control system including basic automation system (LEVEL1) and process automaiton system(LEVEL2). LEVEL1 contr
11、ol system includes heating control system and sequence control system. LEVEL2 includes slab tracking model, temperature prediction model and communication.Heating control system include double cross limited control of air and gas, hearth pressure control, hot air exhaust control and hot air pressure
12、 control and gas automatic cut-off control, development “FUZZY controler” realized fast response of furnace temperature.Sequence system includes charging machine control, walking beam control, discharging machine control and hydraulic system control.Slab tracking system completes roll table tracking
13、 of charge side and discharge side, inside furnace tracking.Slab temperature prediction model include charge slab temperature calculation, cycle temperature calculation model of inside furnace and discharging slab temperature calculation model, proposed slab temperature prediction model based on fur
14、nace zone BP netural network and carried out off-line simulation.Communication including: temperature data sample, charging machine and discharging machine set, walking beam set, slab tracking between LEVEL2 system and LEVEL1 system, communication with Mill LEVEL2 computer and MES system, detail res
15、earch communication method of TCP/IP SOCKET.Finally, slab production process as the research object, developed based automation systems based on the SIEMENS S7-400PLC and WINCC. On this basis, combined with slab material tracking model, billet temperature prediction model and communication to achiev
16、e a variety of steel grades and thickness of slab heating quality control, forecasting three level temperatures transmitted to mill, realize the furnace automatic production control.Key words:reheating furnace; computer control system; temperature control; model目录加热炉计算机控制系统的设计与实现1摘要1Abstract2引言1第一章文
17、献综述21.1 加热炉计算机控制概述21.1.1 顺序控制系统和物料跟踪21.1.2 钢坯温度预报模型31.1.3 炉温优化设定模型41.2 国内外研究现状及发展趋势51.3 课题背景61.4 本论文的研究内容及意义7第二章 加热炉工艺流程及结构简介82.1 加热炉区工艺流程82.2 加热炉基本尺寸和参数82.2.1 加热炉基本尺寸82.2.2 加热炉基本参数92.3 炉型结构特点10第三章 加热炉基础自动化控制系统113.1 双交叉限幅燃烧控制系统123.2 炉温模糊控制系统133.2.1 模糊控制器结构133.2.2炉温模糊控制器的设计143.2.3 实际应用及效果163.3 步进梁速度优
18、化控制163.3.1 速度曲线控制原理163.3.2 速度曲线优化控制及分析173.3.3实际应用19第四章加热炉数学模型的研究与仿真204.1 数学模型概述204.2 模型参数的建立204.2.1沿炉长方向炉温的线性插值204.2.2比热和热传导系数的线性插值计算214.3基理温度预报模型224.3.1 三维导热数学模型224.3.2 温度预报模型的工程考虑234.3.3温度预报模型的边界条件234.3.4模型验证244.4 分段BP神经网络钢温预测和仿真254.4.1 三层BP网络结构的建立254.4.2 神经网络输入输出量的确定254.4.3 神经网络隐层神经元的确定264.4.4 隐层
19、及输出层的权值调整274.4.5 仿真研究28第五章 计算机控制系统网络和通讯开发305.1 网络结构及配置305.1.1 LEVEL1级网络结构305.1.2 LEVEL1级硬件配置325.1.3 LEVEL2级网络结构325.1.4 LEVEL2级硬件配置335.2 网络通讯电文内容335.2.1与MES管理计算机的通信335.2.2 与轧线过程计算机通信345.2.3 与基础自动化通信345.3 LEVEL1级通讯程序的开发355.3.1 WINCC和PLC以太网通讯开发355.3.2 PLC和PLC以太网通讯开发365.4 LEVEL2级TCP/IP通讯程序开发365.4.1 TCP/
20、IP SOCKET基本概念365.4.2 客户/服务器模式375.4.3 TCP/IP套接字系统调用及方法385.4 通讯网络的具体IP地址和端口规划40第六章 加热炉计算机控制系统的应用426.1 LEVEL1级控制系统开发426.1.1系统软件436.1.2 顺控软件开发456.1.3 燃控软件开发476.1.4 监控软件介绍506.1.5 监控软件开发526.2 LEVEL2级软件功能描述556.2.1 建立板坯数据信息556.2.2 板坯温度计算的热工模型566.2.3 轧制温度反馈控制566.2.4 主要画面简介56结论60参考文献:61附件1:附图清单1附件2:附表清单2在学研究成
21、果2致谢3引言2007年,我国钢产量已经达到4.89亿吨,已是多年保持世界第一产钢大国的地位。我国钢铁工业的发展速度是世界钢铁工业发展最快的国家,所取得的成就是世界公认的。但是,我国钢铁工业技术经济指标(包括能源消耗、劳动生产率、设备寿命及设备作业率等)、对环境的污染等方面与世界先进水平相比较,差距仍很大。要实现从钢铁大国到达钢铁强国,这是摆在钢铁研究工作者面前的艰巨任务。加热炉的计算机控制系统通常被分为一级(LEVEL1)和二级(LEVEL2)控制系统。LEVEL1系统包括燃烧控制系统和顺序控制系统。燃控系统的主要功能是根据钢坯钢种和规格的需要,控制各个区域的温度,实现钢坯的理想升温曲线控制
22、。同时实现相应的安全连锁和设备保护。顺控系统的主要功能是完成整个加热炉区域的设备动作控制,实现钢坯的装料,步进和出料控制,以及相应的辅助设备的动作控制。LEVEL1是LEVEL2级控制的基础。LEVEL2系统主要分为应用部分和模型部分,应用部分包括物料跟踪和通讯等,模型部分主要是钢坯的温度预测,主要包括装炉温度处理、出炉温度处理、炉温沿炉长方向的曲线拟合,周期计算等。LEVEL2负责完成整个加热炉的过程控制,实现钢坯在炉膛内的温度预报和物料跟踪,在通讯模型的支持下,完成整个加热炉区设备的全自动生产和全自动温度控制,并为轧机提供必要的信息。本文的主要内容如下:(1)文献检索。进行了大量文献检索工
23、作,对前人的研究工作进行总结和分析。描述了基于传热学原理的钢坯加热数学模型。(2)设计和优化了LEVEL1级控制系统,重点研究了改进型双交叉限幅温度自动控制和炉温模糊控制器,以及步进梁的速度曲线优化控制。(3)系统研究了钢坯传热数学模型、钢坯温度预报模型和算法,并利用炉区分段的BP神经网络进行了钢温的预测,离线仿真效果良好。(4)开发了基于S7-400PLC和WINCC的加热炉基础自动化系统,并成功应用于生产,大大提高了炉温的控制精度,温度响应时间大大缩短,加热炉LEVEL2级计算机控制系统的投运,实现了炉内钢坯温度的预测,建立了加热炉与通讯伙伴的实时通讯,为轧机提供了必要的钢坯加热参数,实现
24、了加热炉的全自动生产。第一章 文献综述加热炉是轧钢生产线关键设备之一,也是主要耗能设备,其作用是将钢坯加热后送往轧机进行轧制1,其中钢坯加热炉能耗就占冶金能耗的25%2,因此,提高加热炉的热效率,对整个冶金行业的节能降耗具有重要意义。步进梁式加热炉的功能是根据钢坯的入炉参数、生产工况和工艺指标,通过控制炉温,空气燃料流量及空燃比,空气燃料压力,烟气残氧浓度以及炉膛压力,尽可能地降低能耗,减少氧化烧损,使钢坯在炉中均匀受热,同时通过步进梁的步进运动,将钢坯从装料侧移动至出料侧,通过钢坯在炉内的运动,完成从低温段至高温段,再进入均热段的加热,达到轧钢要求的轧制温度。由于加热炉燃烧过程具有非线性、强
25、耦合、不确定性、分布参数特性,是一个高度复杂的工业过程,加热炉计算机过程控制技术成为钢铁企业研究的重要课题之一,在国内外都得到了广泛的重视。1.1 加热炉计算机控制概述加热炉的计算机优化控制技术就是要在保证工艺指标的前提下实现最优的经济指标,在加热炉上开展计算机优化控制的研究已经有三十多年的历史,国际上对加热炉优化控制的研究始于20世纪70年代,国内始于80年代,主要从设备和自动控制两个方面采取措施3,以降低加热炉的能耗及提高产品质量,可以概括为三个方面:炉温自动控制、钢坯温度预报模型和炉温优化设定策略。1.1.1 顺序控制系统和物料跟踪顺控系统的主要功能是完成整个加热炉区域的设备逻辑控制,完
26、成装料侧的辊道逻辑控制、加热炉液压站的控制、装钢机的速度曲线控制,步进梁的速度曲线控制和出钢机的控制,同时完成L1级的板坯物料跟踪,实现钢坯的装料,步进和出料控制,以及相应的辅助设备的动作控制。在LEVEL1级顺控系统的基础上,LEVEL2及系统通过以太网络和OPC方式,和LEVEL1级系统建立实时通讯,在ORACLE数据库和VISIAL.NET开发平台C#软件的强大处理功能下,完成板坯的入炉、炉内和出炉的全炉跟踪,为模型控制系统提供必要的板坯钢种、尺寸和板坯位置等信息,完成坯料的温度预测。加热炉燃烧控制系统的基本任务是:提高加热炉各段炉温的控制精度,获得满足开轧所要求的钢坯温度,同时保证经济
27、燃烧和安全运行。为保证稳态和动态情况下,保证空燃比在合适的范围内,通常采用交叉限幅控制方法,使系统在调节的动态过程中,保持空气、燃料的相互跟随关系,控制最佳空燃配比。目前,炉温自动控制绝大多数还是采用带交叉限幅的温度流量串级PID控制器,但控制精度差,超调严重,升降温速度慢。神经网络、模糊控制、专家系统、自适应控制等智能化技术的出现为加热炉炉温控制提供了新的方法和思路。张晶涛等人4针对常规交叉限幅控制方法负荷跟踪速度低的缺点,采用了具有快速补偿响应功能和抗积分饱和功能的改进交叉限幅燃烧控制方法,针对炉温过程具有时变非线性的特性,应用了自整定PID控制算法,针对加热炉下加热段与上加热段炉温对象耦
28、合干扰严重的现象,应用了智能解耦控制方法。从整体上提高了加热炉燃烧控制系统的控制性能。文献5,6提出的专家模糊温度控制器,文献7,8提出的加热炉神经网络燃烧控制等,还停留在理论研究和仿真研究阶段。另外,目前采用的模糊控制、专家控制最终的输出量是空气流量和煤气流量设定值,流量的闭环控制还是要依靠传统的PID控制器来实现,从而限制了炉温控制精度和实时性的提高。法国斯坦恩-霍特公司开发的数字化时序脉冲燃烧系统9,其温度控制是通过控制烧嘴的燃烧时间,而不是控制空气和煤气的流量,当空煤气烧嘴前的压力恒定时,通过控制空煤气切断阀的开启时间和工作周期,可以实现炉温的控制,从而克服了流量PID闭环控制的不足,
29、达到了较好的效果。1.1.2 钢坯温度预报模型钢坯温度预报模型是加热炉燃烧优化控制的必要中间量,通过数学模型计算的炉内钢坯表面和核心温度,从而可以了解钢坯的加热质量,同时为进一步优化炉温设定提供依据。随着计算机技术的发展,炉内钢坯加热过程的数学模型也被广泛地应用在计算机控制上。在国外,Timothy A.Vesiock等人10-12根据加热炉内的热交换机理来建立实时控制模型,采用动态热传导分析的方法,通过分析钢坯各节点的热交换来对钢坯温度进行控制。这种方法目前在一些钢厂的加热炉控制还在使用,但是目前生产现场采用的基本上都是简化的一维模型,多维模型因为计算量巨大目前还不能在线应用,在一定程度上降
30、低了模型的准确性。Y.Misaka和H.E.Pike等人13-15采用分布参数理论与热交换机理相结合的方法进行建模,并通过近似集中参数模型研究了加热炉的静态、动态优化问题。A.H.Work16基于炉内热量传导的物理机制,推导了一类时空离散化的状态空间模型。文献17-19从描述钢坯内部稳定导热的二维偏微分方程及相应的边界条件出发,开发出了描述钢坯被加热状态的离散状态空间模型,从本质上,这种方法是机理分析方法的延续和改进。国内这方面的研究起步较晚,上世纪七十年代末,随着计算机控制系统的普及和自动控制技术在钢铁企业的应用日趋广泛,加热炉温度优化控制理论的研究开始日渐深入,成为自动控制技术工业应用研究
31、的重要领域。钢坯升温模型的研究主要从两个方面入手,采用总括热吸收率法,从钢坯与炉内热交换的物理机制入手,简化了炉膛内辐射换热,寻找钢坯升温的热力学模型,文献20-26都涉及到了这方面的研究。炉内钢坯温升数学模型大体上分为用于加热炉在线控制的一维稳态导热数学模型,以及用于加热炉离线计算机模拟的三维稳态导热数学模型。低维导热数学模型形式简单、计算机求解方便,与三维模型相比,虽然在精度上有所不足,但在加热炉加热过程计算机在线控制方面,可以满足现场的工艺要求。三维导热数学模型计算结果精度高,真实反映了钢坯在加热过程中的瞬时温度分布和变化,但由于数值计算求解过程计算工作量大,目前还很难将其应用到加热炉在
32、线控制系统中,主要应用于实验室理论计算和分析。为了进行数学模型的计算机移植以及实现控制的可行性和方便性,离散状态空间方法也是钢坯升温模型的研究重点和热点,在这方面文献27-29工作颇具代表性,这些文献都是把炉内的钢坯考虑为一股被加热的物料流,并按几何位置分解为一系列相互关联的子系统,不仅得出了炉内钢坯加热的全系统模型,而且给出了单独钢坯的跟踪热模型,为实时计算机控制奠定了理论基础。近年来随着计算机技术和智能控制理论的迅速发展,智能控制得到了广泛应用。智能技术不仅为传统控制理论和方法带来了新的生机,而且为解决轧钢领域内的控制难题,摆脱常规数学模型的困境,突破现有控制理论的局限性,开辟了一条新的道
33、路。智能技术在钢铁冶金工业中的应用主要包括将专家系统与传统的控制方法相结合的专家控制方法;将人工神经网络应用于建模的神经网络控制方法;将模糊集合结合模糊推理决策进行控制的模糊控制方法;将神经网络和模糊控制相结合的智能控制方法等。神经网络技术因其具有较快的学习能力和逼近任意非线性映射的能力而被广泛用于系统建模的研究中。在加热炉对象的建模中,应用最为广泛的是BP神经网络30, 31,它有结构简单、抑制样本噪声等优点,但也有学习速度较慢、容易陷入局部极小点等缺点,因此,近年来也出现了一些改进的神经网络模型,如RBF网络模型仅在输入空间的局部范围内非零(即只有当输入落入输入空间的一个很小的局部范围时,
34、基函数才产生一个有效的非零响应),其参数调整律可采用线性调整技术,因而有更快的学习速度,逼近能力很强,在钢坯温度预报方面得到了很好的应用32, 33。1.1.3 炉温优化设定模型柴天佑,王中杰,沈子瞻等34, 35人对步进式加热炉的建模、控制、优化做了很多研究,提出了一种基于生产目标的加热炉优化设定控制方法。该方法采用前馈、反馈、自适应、智能及软测量等多种先进控制技术和建模方法实现了生产过程的建模与控制一体化,并通过多级闭环实现了生产过程的滚动优化,解决了基于DCS的加热炉各回路的优化设定问题。根据连续加热炉温分段可控性和钢温的变化滞后于炉温变化的特点,文献36, 37运用一种新的炉温决策方法
35、。该法以控制段(加热段或均热段)内的某处钢坯的平均温度和表面温度与设定值的偏差最小为控制目标,决策出优化的炉温设定值。开发合理的在线数学模型,为轧制生产服务,具有一定的效果。安月明,温治38系统总结了炉温优化设定时各种优化目标函数的进展,对加热炉优化控制领域中目标函数的选取、约束条件的确定、寻优方法的选取进行了详细的分析和综述,评价了各类目标函数的优点和不足。从发展来看,综合型的优化目标将会得到更大的应用,但在权重系数选取的研究上、寻优算法适合在线应用的问题上还值得进一步深入研究。炉温优化设定的智能控制技术也在快速发展,模糊逻辑控制技术能够有效地利用人工控制所取得的操作经验,把人工经验变换成模
36、糊控制规则,在加热炉这样非线性、大惯性、纯滞后、耦合严重的复杂系统的控制中获得了很多应用39。但是模糊控制方法本身还存在着一些缺点,比如模糊控制是一种基于模糊规则的控制器,这些模糊控制规则是对受控过程认识的归纳与控制经验的总结,模糊规则通常情况下是固定不变的,本身缺乏学习能力,不能够自动修改,因而当系统有变动的时候,难以动态修正模糊控制规则,从而影响了控制效果。在实际应用当中,将模糊控制同其它控制技术相结合,对炉温进行控制的情况也比较普遍,如将模糊控制同比例控制、PID控制相结合的分区控制策略,以模糊规则实时调节PID参数的模糊PID控制技术等。1.2 国内外研究现状及发展趋势多年来,国内外都
37、有大量的专业化公司和自动化工作者致力于加热炉二级控制系统设计及燃烧优化控制方面的研究开发工作。国外学者对加热炉二级控制系统的研究始于上世纪70年代中后期,随之,国内学者对加热炉数学模型及相应的优化控制策略的研究也日益活跃。80年代末期,在工业发达的国家已普遍实现了加热炉的计算机控制。1981年9月,意大利Italimpianti公司首次在意大利的Acciarierie di Piombino S.P.A工厂棒材生产线加热方坯的110t/h步进炉上使用在线数模控制系统。该公司至今已为100多座炉子提供在线数模控制。意大利Italimpianti公司(目前为意大利Techint德兴公司的子公司)成
38、功开发的“灵活技术”(FlexyTech)的加热炉,其核心技术就是计算机二级控制系统。法国STEIN HEURTEY公司1981年在Foss/Mer工厂的3座热轧带钢加热炉上进行在线数模控制工业性应用,并在1982年得以验证,至今已为130多座炉子提供在线数模控制系统,国内的南京钢铁公司炉卷轧机加热炉使用了该公司的产品。SIEMENS VAI公司的加热炉二级系统也被广泛地使用在国内马钢2250、酒钢1800不锈钢炉卷轧钢厂等企业。国内的专业软件公司和钢铁设计院也开发了多座加热炉二级控制系统,主要包括:宝信软件公司开发的基于iPLATURE中间件平台的二级控制系统,在宝钢1780热轧和2050上
39、应用,上海迈思公司开发的加热炉二级系统被应用在宝钢不锈钢分公司等企业,重庆钢铁设计院开发的二级系统被应用在沙钢5米宽厚板加热炉。虽然国内外有不少公司都开发了基于数学模型的加热炉二级控制系统,但大多只能提供一些钢坯的温度预测,出炉时间等信息,在炉温的优化设定上不能投入自动运行,仅停留在炉温的操作指导层,炉温设定值大多还是操作技术人员根据经验人工给定。从目前的发展状况来看,其发展趋势可概述如下:1) 结合智能控制理论的发展,利用先进的控制理论,提高模型预测的准确性;2) 为燃烧自动化系统提供最佳的温度设定参数;3) 实时准确地优化各操作参数,提供合理的炉内温热制度,使之获得最优的生产指标。在满足轧
40、机轧制能力的条件下,保证工艺和技术经济指标的先进性,节能降耗,创造良好的经济效益。1.3 课题背景加热炉的钢坯温度预测和炉温优化控制一直是控制理论界的一个研究热点。由于加热炉具有以下特点:1)大滞后特性;2)过程机理反应复杂;3)生产工艺目标不能直接控制(如钢坯表面温度)。这些特点决定了钢坯加热炉是一个具有多变量、时变、非线性、耦合等特点的复杂工业工程,边界条件剧烈变化,炉内钢坯表面温度不能直接连续测量,导致加热炉动态模型复杂。建立实用的加热炉计算机控制系统,在实现温度自动控制和全自动生产的前提下,提高炉温控制精度,钢坯温度预测的准确性,是目前冶金自动化工程师必须面对和解决的问题,本文结合实际
41、设计和调试的大型板坯步进梁式加热炉的经验,分别从燃烧控制系统的FUZZY-PID双交叉限幅炉温控制、顺序控制系统的步进梁速度曲线优化控制和加热炉的通讯,跟踪和坯料温度预测模型三个方面,系统总结了加热炉两级计算机控制系统的研究和应用。为国内类似的大型步进梁式板坯加热炉积累大量的经验,为下一步优化炉温设定奠定了基础。1.4 本论文的研究内容及意义本论文以某5M宽厚板轧钢厂的两座250t/h步进梁式加热炉的设计和调试为研究对象,在完成加热炉基础自动化系统LEVEL1的顺控和燃控系统调试后,又成功地实现了加热炉的LEVEL2级物料跟踪、通讯和板坯温度预测,真正实现了加热炉的两级计算机过程控制。在燃控系
42、统上,提出了FUZZY-PID双交叉限幅温度PID控制算法,优化了燃控系统的温度控制算法,保证了加热炉各温控区的炉温控制精度和响应速度。在顺控系统上,研究和开发了基于混合网络的加热炉顺控系统,并优化了加热炉的步进梁速度曲线控制。在LEVEL2级控制系统上,在燃控LEVEL1和顺控LEVLE1级控制系统的支持下,基于传热学的基本原理,建立了板坯的炉内温度预报系统,同时在温度计算模型中使用了优化算法,提高了钢坯温度预测的精度。本文的主要内容:本章首先进行了文献检索,总结了加热炉计算机控制系统的现状和发展趋势。第二章介绍了加热炉的工艺流程、结构和性能参数。第三章介绍了加热炉基础自动化系统,包括燃烧系
43、统和顺控系统,并对交叉限幅串级温度控制系统进行了改进,提出了FUZZY-PID温度控制系统,开发了具有通用性的步进梁速度曲线控制模块,并对速度曲线进行了优化,取得了良好的使用效果。第四章建立炉内钢坯的传热过程的机理数学模型,并从工程角度进行简化,给出了一维的导热模型和总括热吸收率算法。以此为理论基础开发的钢温预报模型程序,预测的钢温和实测数据基本吻合,数据令人满意。同时结合智能控制理论,提出了基于炉区分段的BP神经网络钢坯温度预报模型,并进行了仿真研究。第五章主要描述了加热炉计算机控制系统的网络和通讯设计,主要包括WINCC和PLC的通讯、PLC和PLC的通讯以及TCP/IP SOCKET通讯
44、。第六章阐述了西门子PLC控制系统的特点及其在大型轧钢步进梁式加热炉LEVEL1系统上的应用,并给出了基于平台的C#软件和ORACLE数据库平台开发的加热炉二级控制系统的实现。第二章 加热炉工艺流程及结构简介2.1 加热炉区工艺流程加热炉用板坯从板坯库经上料辊道输送到炉前,按预定的计划分别进行冷装、热装或混装。加热炉额定产量为250t/H,燃料为焦炉煤气,采用空气单预热的步进梁式板坯加热炉。板坯在炉前辊道上经过称量、测长、核对、测温,按布料图进行定位。在确定炉内有空位后,装料炉门打开,装钢机开始动作:装钢机前移,将板坯拨正,经测宽后送入炉内,在与前一块坯料间隔50100mm处停止。然后,装钢机
45、快速退回原位,准备重复送钢动作。同时装料炉门关闭。炉内板坯通过步进梁的运动,经过炉子的热回收段、预热段、一加热段、二加热段和均热段充分加热,达到轧制要求温度后,运行至出料端激光检测处并完成最后一次步进运动后停止,经激光检测器检测及步进梁行程控制系统和炉内坯料跟踪系统计算,钢坯在炉内准确位置的信号被送往出钢机,出钢机接到指令后开始动作,从低位运行进炉内,根据钢坯位置定位,托起钢坯出炉,准确将钢坯放在出料辊道上,再由出炉辊道输送到轧机轧制,同时出料炉门关闭。为了使加热炉的操作更灵活,适应坯料规格(主要是长度和厚度)的频繁变化和冷热坯装炉切换,最大限度地发挥加热炉效率,一座加热炉装备了两套独立运行的
46、步进机械;按炉宽方向,步进框架(平移框架和升降框架)均分为左右两个框架,分别由两套步进机械单独传动。2.2 加热炉基本尺寸和参数加热炉有效长度52600mm,内宽10700mm,燃料为焦炉煤气。加热炉示意图如图2.1。2.2.1 加热炉基本尺寸辊道上表面标高:+900 mm加热炉基础面标高:8100 mm装出料辊道中心距:60500 mm加热炉砌体全长:54000 mm加热炉有效长度:52600 mm加热炉砌体宽度:11572 mm加热炉内宽:10700 mm烟囱高度:80m烟囱出口直径:3.6m 图2.1加热炉示意图2.2.2 加热炉基本参数a) 坯料规格连铸坯:厚度:200mm、220mm
47、、300mm宽度:对220mm坯料 18002600mm对250、320mm坯料 18002600mm长度:26004800mm 标准板坯规格22022003600mm 标准板坯质量13.6tb) 加热钢种碳素结构钢板、低合金结构钢板、建筑结构板、耐大气腐蚀钢板、桥梁钢板、造船钢板、管线钢板、锅炉钢板、压力容器钢板、机械工程用钢板等。c) 坯料入炉温度冷坯:室温(以20计)。热坯:400700;热装比:4050%。d) 坯料出炉温度:10501250。e) 炉子座数:2座f) 炉子小时产量:220t/h(额定) 280t/h(最大)g) 年加热量:200万t;h) 燃料种类:焦炉煤气,其低发热
48、值为40004.18kJ/m3。2.3 炉型结构特点加热炉采用端部装钢机上料和端部出钢机出料方式,加热炉上部采用平焰烧嘴和侧向烧嘴相结合的供热形式;下部全部采用侧向供热方式。加热炉共设置八个炉温自动控制段。炉型采用上、下供热滚轮斜台面全液压驱动的步进梁式加热炉。加热炉的结构:一座炉子配备两台装钢机,两台装钢机可以同时运行(不要求同步)。一座炉子配备两台出钢机,两台出钢机可以同时运行(不要求同步)。为适应双排装料,加热炉设置两套步进机械,双升降框架和平移框架,配备各自的传动机构,提高加热炉的操作灵活性。加热炉设八个供热段,八段炉温自动控制,通过设定各部分加热的温度值,控制各段燃料量的输入,保证出
49、钢温度及温度的均匀性。加热炉配置的烧嘴调节比大,可灵活调节供热量。烧嘴的供热能力是通过热工计算确定的,在确定各烧嘴的供热能力时考虑一定的富裕能力,便于各段炉温制度的调节。烧嘴的型式及供热能力见表2-1。表2-1 加热炉烧嘴型式及能力配置部 位上部加热段下部加热段各 段 名 称预热段加热1加热2均热段预热段加热1加热2均热段供热比例(%)8.814.614.07.89.316.916.711.9烧嘴个数6103630610128烧嘴型式侧烧嘴侧烧嘴平焰平焰侧烧嘴侧烧嘴侧烧嘴侧烧嘴为了适应热坯加热和冷热坯交替装入时的加热要求,以及炉子小时产量变化大(177300t/h)和加热温度变化大(10501
50、250)的加热要求,采用多区供热的箱型结构,便于分区控制各段温度;各供热段用隔墙适当分隔,预热段和一加热段设有开关式烧嘴,在热装时可以根据需要关闭预热段和一加热段烧嘴,独立地进行流量调节和温度控制。多区分段控制能很好地适应低温加热与控制轧制,同时适应加热炉产量的变化。第三章 加热炉基础自动化控制系统随着冶金生产技术和工艺设备的不断发展,以及计算机和可编程控制器的出现,加热炉的的计算机控制系统也得到了日益广泛的应用,基础自动化系统的组成主要是PLC+HMI系统组成了监视和控制系统,通过工业以太网和现场总线网络,实现HMI和PLC以及PLC和现场级控制设备的通讯和控制。基础自动化系统包括燃控系统和
51、顺控系统,它们的功能介绍如下:燃控系统主要功能:(1)每段炉温自动控制、记录、联锁报警;(2)每段煤气流量控制、记录、联锁报警;(3)每段空气流量控制、记录、联锁报警;(4)炉压控制、记录、联锁报警;(5)炉内含O2量检测控制;(6)炉尾炉温测量、指示;(7)换热器前后烟温测量、指示、联锁报警;(8)换热器烟温保护控制、记录、联锁控制;(9)燃烧空气压力控制、记录、联锁控制;(10)煤气总管压力控制、记录、联锁控制。顺控系统的主要功能:(1)板坯在板坯库辊道、装炉辊道上定位;(2)称重机控制;(3)板坯测长,测宽;(4)推钢机位置及行程控制;(5)装出炉辊道的控制;(6)加热炉装出料侧的炉门控
52、制;(7)步进机械控制;(8)板坯在炉区辊道上的位置跟踪;(9)液压站设备控制。以下重点分析本项目中采用的双交叉限幅温度控制系统和模糊控制器的设计,以及步进梁的速度曲线优化策略。3.1 双交叉限幅燃烧控制系统目前最常用的控制方式为串级双交叉限幅空燃比控制,其系统如图3.1所示 图3.1 双交叉限幅温度控制系统TPV、SPt炉温的测量值和设定值PVf、SPf燃料流量的测量值和设定值PVa、SPa空气流量的测量值和设定值HS、LS高值和低值选择器TC、FfC、FaC分别为温度、燃料流量、空气流量调节器x、1/x乘法器和除法器b1、b2、b3、b4偏置系数HL、LL高频和低频滤波器TPV炉温MVt温
53、度调节器输出(燃料目标流量)目前,维持确定空燃比的炉温控制算法已经逐渐成熟,在双交叉限幅的基础上,又开发了变增益交叉限幅、串级比值等新的控制策略。炉温调节除普通的串级PID外,也出现了改进型的二自由度PID、IPD等类型。交叉限幅控制的特点是采用一个最大选择器和一个最小选择器,其目的是保证当炉温低于设定值,需要增加燃料流量时空气先行;而当炉温高于设定值,需要减少燃料流量时燃料先行,以防止冒黑烟。该方法已经广泛应用于工业燃烧控制中,它能在动态过程中保证空燃比在规定范围内,从而使燃烧过程最佳,节约能量,减少环境污染。通过双交叉限幅控制系统的投用,使得在整个自动燃烧的过程中,动态空燃比始终保持在3.
54、54.3之间,在生产节奏发生变化时,空煤气流量发生较大变化时,空燃比始终能保持动态的跟踪,没有出现冒黑烟现象,氧化烧损也较理想,实现了空燃比的自动控制。3.2 炉温模糊控制系统串级双交叉限幅控制系统实现了空气和燃料比例控制和动态条件下的空燃比控制,较好地解决了燃料的不完全燃烧的现象,但无法实现炉温的快速响应控制,传统的PID控制系统能实现很小的稳态误差,但温度偏差大时的快速温度控制也难以实现,本文结合近年来广泛应用的智能控制理论:模糊控制算法,提出了FUZZY-PID控制算法,在温度偏差大和温度偏差的速率大时,采用模糊控制算法,用模糊控制器代替串级温度控制中的温度调节器Tc,将模糊控器的输出送
55、至双交叉限幅运算器,经双交叉限幅计算后送至空煤气调节器,使空煤气调节阀能较快地响应,实现温度快速响应,在稳态误差较小时,恢复到串级控制,采用温度调节器和流量调节器的串级PID控制系统,实现高精度的温度控制。与传统控制方法相比,模糊控制的优点主要体现在以下两个方面。首先,模糊控制不需要控制系统的精确数学模型。第二,在工程实际中,可以根据经验建立较好的模糊控制器。区别于传统控制器设计方法,模糊控制系统设计不需要精确的数学模型。即模糊规则、模糊逻辑运算和模糊集隐含地包括了系统模型。模糊规则将描述系统状态变量的模糊集与模糊控制器的输出联系起来。模糊控制将模糊建模任务和系统控制任务结合在一个任务中,通过
56、避免分别的建模任务,通常可以更有效和高效地解决控制问题。现今,模糊控制器和控制系统的广泛应用证明了这点。3.2.1 模糊控制器结构模糊控制是以模糊集理论、模糊语言变量和模糊逻辑推理为基础的一种智能控制,它模仿人的模糊推理和决策过程。首先,将操作人员或专家经验编成模糊规则,然后将来自传感器的实时信号模糊化,将模糊化后的信号作为模糊规则的输入,进行模糊推理,将推理后得到的输出量送到执行器或者下一级控制系统中。模糊控制器的基本结构如图3.2所示,由四部分组成。其中为系统的给定值,是系统偏差、是偏差的变化率(也可以是偏差的积分),为系统输出。和是模糊控制器的输入,为控制器的输出。、分别是、和的模糊量。
57、图3.2 基本模糊控制器的结构1)模糊化:主要作用是将真实世界的确定量输入转换为一个模糊矢量。2)规则库:规则库中包含了具体应用领域中的规则和控制目标。它通常由数据表和模糊控制规则两部分组成。3)模糊推理:模糊推理是模糊控制器的核心,它具基于模糊概念的有模拟人的推理能力。该推理过程是基于模糊逻辑中的蕴含关系及推理规则来进行的。4)清晰化:清晰化也是反模糊化,是将模糊推理得到的控制量(模糊量)变化为实际用于控制的精确量。3.2.2炉温模糊控制器的设计炉温的控制,最终是通过控制空气和煤气调节阀的开度变化,改变进入炉膛燃烧的煤气量来实现温度控制的。炉温的模糊控制和串级PID控制的自动切换,是根据温度
58、的偏差大小来自动实现的,当温度偏差较大时,为使温度能快速地响应,从而用模糊控制方法,当温度的偏差值进入一定的区间时,则自动转换为PID控制,实现较小稳态误差控制。炉膛温度为被控制量,煤气流量为控制量,根据实际控制要求,本模糊控制器温度值与给定值的偏差E的语言变量值取(负大,负中,负小,零,正小,正中,正大),偏差的变化率EC及煤气流量的增量的语言变量值取(负大,负中,负小,零,正小,正中,正大),量化等级都取-6,-5,-4,-3,-2,-1,0,+l,+2,+3,+4,+5,+6,各模糊子集的隶属函数取三角型函数。由于在不同的温度下,系统要求的工作状态是不同的,对误差及误差变化率的加权值应有
59、所不同,当温度误差E比较大时,模糊控制器的主要任务是快速地消除误差,因此应该取较大的值,即加强误差E的权值,以加速系统的响应速度。反之,当温度误差E较小时,控制器的主要任务是使系统尽快趋于稳定,应取较小的值,既加强误差变化率EC的权值,以提高系统的稳定性。为了满足系统在不同的状态下对修正因子的不同要求,引入了2个修正因子和。表达式如下: (3.1)其中,为0到1之间的实数,且。通常情况下,选取。本系统中选取,并建立模糊控制查询表3.1。表3.1 模糊控制查询表在已知E和EC的条件下,可以通过表来求得煤气流量的增量,再按最大隶属度原则解模糊,选择隶属度最大的元素为精确控制信号,即为实际煤气流量的
60、增量。所以煤气流量的实际输出信号为: (3.2)此值作为煤气调节器的输入值,同时在双交叉限幅模块的计算下,空气调节器的输入值也被更新,在空煤气调节器的调节下,空煤气阀门快速动作,从而达到快速控制炉温的目的。3.2.3 实际应用及效果根据实际的调试结果,我们把炉膛温度T的误差信号的实际论域定为-60,+60,误差的变化量实际论域定为-3,+3/min,为了表述方便,我们把和的论域按比例变换到-6,+6。当温度的实际值和设定值的偏差大于20时,模糊控制器的输出被送到空煤气PID调节器,当温度的偏差值小于20时,温度调节器的输出被送到空煤气调节器,为了减小两种控制器切换时炉温的较大波动,两组控制器的
61、切换设计了无扰切换功能,实际应用表明,基于模糊控制理论和传统串级温度控制回路结合的FUZZY-PID调节器,能较好地解决温度偏差大时,温度控制的动态响应速度。3.3 步进梁速度优化控制3.3.1 速度曲线控制原理步进梁式加热炉通过上升-前进-下降-后退的周期运动,将装料侧的钢坯一步一步地向出料侧移动,在步进运动中,整个步进机械的平移框架、升降框架、水梁和炉膛内的所有板坯都随步进机械做整体的步进运动,以本项目为例,整体步进的设备和板坯总重量达500吨以上。因而,在步进梁周期运动的过程中,必须实现曲线运动,在动梁上升和下降到和固定梁同一标高时,必须实现低速运动,同时在启动和停止的过程也必须按一定的加减速度实现启动和停止,在动梁平移的过程中,启动和停止的过程也要遵循一定的加减速度,这样才能实现步进机械的平稳运行,减小板坯对梁的冲击。但为了保证加热炉的产量,使板坯在规定的加热时间内到达出料侧,步进机械在其它阶段必须要高速运动。因此,这个矛盾的存在,就需要通过步进梁的曲线运动,来实现步进梁的平稳运行的同时,保
- 温馨提示:
1: 本站所有资源如无特殊说明,都需要本地电脑安装OFFICE2007和PDF阅读器。图纸软件为CAD,CAXA,PROE,UG,SolidWorks等.压缩文件请下载最新的WinRAR软件解压。
2: 本站的文档不包含任何第三方提供的附件图纸等,如果需要附件,请联系上传者。文件的所有权益归上传用户所有。
3.本站RAR压缩包中若带图纸,网页内容里面会有图纸预览,若没有图纸预览就没有图纸。
4. 未经权益所有人同意不得将文件中的内容挪作商业或盈利用途。
5. 装配图网仅提供信息存储空间,仅对用户上传内容的表现方式做保护处理,对用户上传分享的文档内容本身不做任何修改或编辑,并不能对任何下载内容负责。
6. 下载文件中如有侵权或不适当内容,请与我们联系,我们立即纠正。
7. 本站不保证下载资源的准确性、安全性和完整性, 同时也不承担用户因使用这些下载资源对自己和他人造成任何形式的伤害或损失。