毕业设计(论文)窗户锁扣冲裁模设计
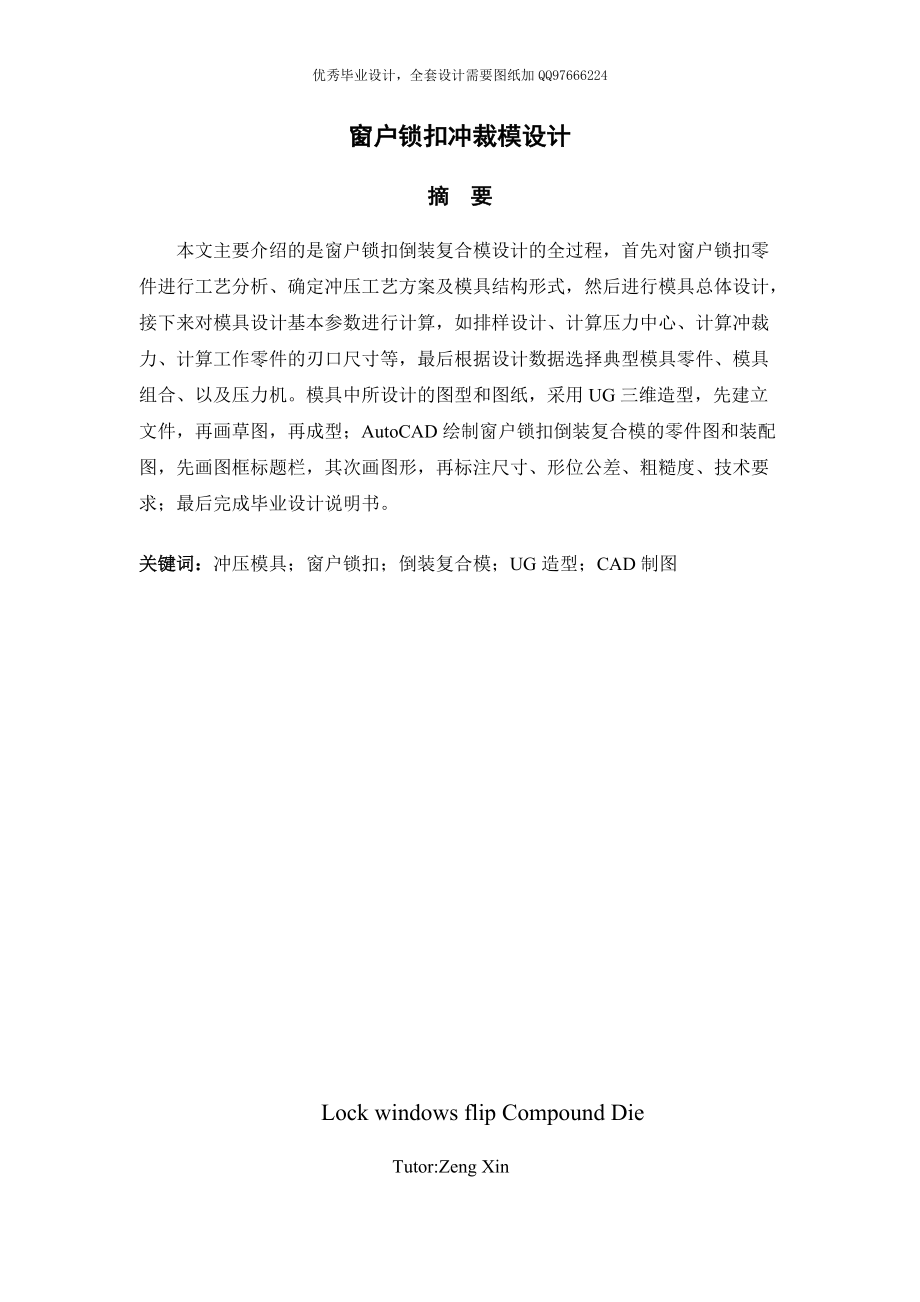


《毕业设计(论文)窗户锁扣冲裁模设计》由会员分享,可在线阅读,更多相关《毕业设计(论文)窗户锁扣冲裁模设计(60页珍藏版)》请在装配图网上搜索。
1、优秀毕业设计,全套设计需要图纸加QQ97666224窗户锁扣冲裁模设计摘 要本文主要介绍的是窗户锁扣倒装复合模设计的全过程,首先对窗户锁扣零件进行工艺分析、确定冲压工艺方案及模具结构形式,然后进行模具总体设计,接下来对模具设计基本参数进行计算,如排样设计、计算压力中心、计算冲裁力、计算工作零件的刃口尺寸等,最后根据设计数据选择典型模具零件、模具组合、以及压力机。模具中所设计的图型和图纸,采用UG三维造型,先建立文件,再画草图,再成型;AutoCAD绘制窗户锁扣倒装复合模的零件图和装配图,先画图框标题栏,其次画图形,再标注尺寸、形位公差、粗糙度、技术要求;最后完成毕业设计说明书。关键词:冲压模具
2、;窗户锁扣;倒装复合模;UG造型;CAD制图Lock windows flip Compound DieTutor:Zeng XinAuthor:Liu YuABSTRACTIn this paper, the window lock flip compound die design process, the first lock on the window components for process analysis to determine the stamping process and die structure the program, and then the mold desi
3、gn, mold design and the next is calculate the basic parameters, such as layout design, calculating center of pressure, calculated blanking force, the working parts of the edge size calculation, the final choice is based on design data, typical mold parts, mold mix, and the press.Mold in the design d
4、rawings, using UG, AutoCAD software to Lock windows compound die assembly flip chart and non-standard parts diagram, and finally completed graduate design specifications.Key words: stamping die; window lock; flip compound优秀毕业设计,全套设计需要图纸加QQ97666224目 录1 绪 论11.1冷冲压的发展史11.1.1概述11.1.2冷冲压的历经阶段11.2常用的冲压模具材
5、料22 冲裁件的结构工艺性分析53 确定工艺方案及模具的结构形式74 模具总体结构设计84.1模具类型的选择84.2定位方式的选择84.3卸料、出件方式的选择84.4标准模架和导向零件的选择85 模具设计工艺计算105.1计算毛坯尺寸105.2排样、计算条料宽度及步距的确定105.2.1搭边值的确定105.2.2条料宽度的确定115.2.3导料销的选用115.2.4排样方法125.2.5材料利用率136 冲裁力相关的计算166.1计算冲裁力的公式166.2总冲裁力、推料力、卸料力和总冲压力166.2.1总冲裁力166.2.2计算卸料力176.2.3计算推料力186.2.4计算总冲压力F187
6、模具压力中心与计算198 冲裁间隙219 刃口尺寸的计算239.1刃口尺寸计算的基本原则239.2刃口尺寸的计算方法249.3计算凸凹模刃口的尺寸249.3.1对落料的刃口尺寸进行计算269.3.2对冲孔的刃口尺寸进行计算279.4冲裁刃口高度2810 主要零部件的设计2910.1工作零件的结构设计2910.1.1凹模的设计2910.1.2凸凹模的设计3110.1.3圆形凸模的设计3110.1.4非圆凸模和复杂非圆凸模设计3210.2卸料部分的设计3210.2.1卸料板的设计3210.2.2卸料橡胶的设计3210.3定位零件的设计3410.4模架及其它零件的设计3510.4.1上下模座3510
7、.4.2模柄3610.4.3推件块和打杆的设计3610.4.4模具的闭合高度3711 模具总装图3812 压力机的选择3913 UG造型4013.1建立ao mo.prt文件4013.2绘制草图3813.3拉伸实体3913.4其它UG造型图40结 论46致 谢47参考文献48附 录4952优秀毕业设计,全套设计需要图纸加QQ976662241 绪 论1.1冷冲压的发展史1.1.1概述模具材料是模具加工业的基础。随着我国国民经济发展和人民生活水平的提高,人们对产品的审美观,价值观也不断提高,从而对各类模具产品,无论是内在质量还是外表美观等方面均要求日益精臻,困此势必对工模具材料在数量上、系列上和
8、质量上提出更高的要求。中国的模具材料从无到有,从小到大,从少到多,直到现在,无论是从钢种还是从规格、标准化、系列化等方面,都是伴随着模具制造发展而发展的。 1.1.2冷冲压的历经阶段(1)五十至七十年代(空白阶段)在这三十年中,由于我国推行计划经济的模式和产业结构上依照前苏联的生产方式,模具制造纯属依附于企业的一个配件加工车间。再则由于工业发展的缓慢和经济封闭,以及人民的生活水平处于很低的消费水平等诸多因素,抑制了模具制造的产业化、社会化和商品化。由此而带来了模具制造业对其所采用的材料要求不高甚至没有要求,供需关系处于有什么用什么的不合理的混乱状态。(2)八十年代(发展阶段)随着改革开放和国民
9、经济的增长,很大程度上推动了模具制造业的发展。模具制造业已走出企业禁锢的状态,十年中,我国的仿制国外新钢种的同时,还在高校、科研院所和各钢厂的配合下,自行研制开发了一批适合我国国情的模具新钢种。不仅改善了加工性能,而且还大大提高了模具的使用寿命。仿制D2钢代替Cr12MoV制造冲压模,用P20钢代替45号钢制造塑料模型芯、型腔,使模具的光洁度和寿命都有了较大的提高。用H13钢代替国外已淘汰的3CW8V制造锻模和压铸模。在冷作模具钢方面,自行开发了65Nb、O12A、CG-2、LM1-2、LD、GD、GM、DS钢等品种。其中65Nb、LD、GD及DS钢因具有良好的抗冲击性而更适合于作冷墩及原料冲
10、裁凸模。GM钢因有良好的耐磨性特别适合于作螺纹滚丝轮,与Cr12MoV相比,寿命可提高十多倍。除上述合金钢外,还开发了GT35及DT等牌号的钢结硬质合金和YG系列的钨钴类硬硬合金以满足高寿命的要求,制造高速冲床用的模具。在塑料模具钢方面,自行开发了易切削类的5NiCa、06Ni、SM1、SM2以及PMS、CPR、PCY等钢,都是一些具有良好加工、使用性能的优良钢种,并在使用上得到用户的认可。在热作模具钢方面Y4、Y10、HM-1、GR、ER8等新品种的开发和应用彻底改变了热作模具几十年来由3Cr2W8V一统天下的局面。(3)九十年代(竞争阶段)随着我国国民经济的发展和产品的更新换代,我国已成为
11、模具和模具材料的生产大国。据1997年统计,我国年耗模具材料13万吨,其中普钢4.5吨。这说明模具这个特殊的产品在近十年中从计划经济条件下的备件逐步发展成市场经济条件下的商品,并日益被模具制造商在其质量和品牌上得到重视。而作为一个工业日趋发展,产品交替更新节奏很快的国家,其对模具的发展也更进一步地被产品生产商重视。因此,一批过去已被研制成功的系列的能适应不同工况条件和产品制造要求的模具材料的开发、试制和生产成为各大特钢厂竞争相推出和竞争的市场热点。但是,模具材料由于其规格繁多,同规格单次需求量少,市场即时采购等特点,使得各大钢厂规模性生产装备无法适应。因此纷纷寻找合适的代理商以求得规模效应。可
12、是,众多的代理商虽然手中握有厚资,但是对于模具工况条件,材料特性以及相关热处理等问题的了解不够,都停留于普钢类方面的激列竞争。另外,国外的资深代理机构和各著名钢厂近几年来组织重兵力图挤入中国的模具材料市场。如:瑞典的NUDDEHOLM、ASSAB,以及德国的蒂森、萨斯特,日本的大同等公司都在上海乃至全国各地树起了优特钢的旗帜,但由于他们的价格过高,已逐渐显得无法展开规模销售,就连目前在国内较有名气的外资公司都在中国寻找价格低廉,品质优良的模具材料。1.2常用的冲压模具材料冲压模具的材料绝大部分以钢材为主,常用的冲压模具部件材料的种类有:碳素工具钢、低合金工具钢、高碳高铬工具钢、中碳合金钢、高速
13、钢、基体钢以及硬质合金、钢结硬质合金等。(1)碳素工具钢加工性能好,价格便宜。但淬透性和红硬性差,热处理变形大,承载能力较低。冲压模具中应用较多的碳素工具钢为T8A、T10A等。(2)低合金工具钢低合金工具钢是在碳素工具钢的基础上加入了适量的合金元素,减少了淬火变形和开裂倾向,提高了钢的淬透性,耐磨性亦较好。用于制造冲压模具的低合金钢有CrWMn、9Mn2V、7CrSiMnMoV(代号CH-1)、6CrNiSiMnMoV(代号GD)等。(3)高碳高铬工具钢具有较好的淬透性、淬硬性和耐磨性,热处理变形很小,为高耐磨微变形模具钢,承载能力仅次于高速钢。常用的高碳高铬工具钢有Cr12和Cr12MoV
14、、Cr12Mo1V1(代号D2)。(4)高碳中铬工具钢含铬量较低,共晶碳化物少,碳化物分布均匀,热处理变形小,具有良好的淬透性和尺寸稳定性。用于模具的高碳中铬工具钢有Cr4W2MoV、Cr6WV、Cr5MoV等。(5)高速钢高速钢具有模具钢中最高的的硬度、耐磨性和抗压强度,承载能力很高。模具中常用的有W18Cr4V(代号8-4-1)和含钨量较少的W6Mo5Cr4V2。(6)基体钢在高速钢的基本成分上添加少量的其它元素,适当增减含碳量,以改善钢的性能。这样的钢种统称基体钢。具有一定的耐磨性和硬度,而且抗疲劳强度和韧性均优于高速钢,为高强韧性冷作模具钢,材料成本却比高速钢低。模具中常用的基体钢有6
15、Cr4W3Mo2VNb(代号65Nb)、7Cr7Mo2V2Si(代号LD)、5Cr4Mo3SiMnVAL(代号012AL)等。(7)硬质合金和钢结硬质合金硬质合金的硬度和耐磨性高于其它任何种类的模具钢,但抗弯强度和韧性差。用作模具的硬质合金是钨钴类,对冲击性小而耐磨性要求高的模具,可选用含钴量较低的硬质合金。对冲击性大的模具,可选用含钴量较高的硬质合金。钢结硬质合金是以铁粉加入少量的合金元素粉末(如铬、钼、钨、钒等)做粘合剂,以碳化钛或碳化钨为硬质相,用粉末冶金方法烧结而成。2 冲裁件的结构工艺性分析图2-1 工件图(1)结构:零件大小适中,外形简单,对称;制件需要进行冲孔、落料二道基本工序。
16、(2)材料:08钢属于优质碳素结构钢、质量较好、含碳量波动小、性能较稳定,并可通过热处理进行强化;该钢属于低碳钢、强度低、塑性好、具有良好的冷冲压性能和焊接性能,宜于制作各种冷冲压件。(3)公差:零件图上所有尺寸均未标注公差,属自由尺寸,可按IT14级确定工件尺寸的公差。亦无其他特殊要求,利用普通冲裁既可达到零件图纸要求。经查公差表各尺寸公差为:、 、。(4)两个孔的位置公差为:、。(5)生产批量:大批量。表2-1 年产量与生产类型的关系生产类型同类零件的年产量(件)轻型零件(零件质量100kg)中型零件(零件质量1002000kg)重型零件(零件质量2000kg)单件生产100105成批生产
17、小批100500102005100中批5005000 200500 100300大批500050000 5005000 3001000大量生产5000050001000结论:由表2-1可得出零件是轻型零件,制件可以进行冲裁,制件要大批量生产,应重视模具材料和结构,保证模具的复杂程度和寿命。3 确定工艺方案及模具的结构形式根据制件的工艺分析,该工件包括冲孔、落料二个基本工序,按其先后顺序组合,可以有以下三种工艺方案:方案一:落料-冲孔,采用单工序模生产;方案二:冲孔-落料,采用级进模生产;方案三:冲孔-落料,采用复合模生产;方案一单工序模是在压力机一次行程中,只完成一道冲压工序的模具。优点:模具
18、结构简单,模具寿命长,制造周期短,投产快;缺点:工序分散,模具及操作人员多,劳动量大。方案二级进模(又称为连续模、跳步模)是指压力机在一次行程中,依次在模具几个不同的位置上同时完成多道冲压工序的冲模。优点:效率高、操作安全、模具寿命长,易于实现自动化;缺点:结构复杂、制造精度高、周期长、成本高,材料利用率较其它低。方案三复合模是只有一个工位,在压力机的一次行程中,在同一工位同时完成两道或两道以上冲压工序的模具。优点:结构紧凑,生产率高,冲裁件的内孔与外缘的相对位置精度高;缺点:结构复杂,制造精度要求高,成本高。通过对上述三种方案的的分析比较,由于该制件属于多异形孔,冲裁较困难,所以该制件的冲压
19、生产采用方案三为佳。4 模具总体结构设计4.1模具类型的选择由冲压工艺分析可知,该模具采用复合冲压模。复合模采用倒装式复合模,因其结构简单、又可以直接利用压力机的打杆装置进行推件、卸料可靠、便于操作、并为机械化出件提供了有利条件,所以模具类型为倒装式复合模。4.2定位方式的选择为保证冲裁出外形完整的合格零件,毛坯在模具中应该有正确的位置,正确位置是依靠定位零件来保证的。由于毛坯形式和模具结构不同,所以定位零件的种类很多,设计时应根据毛坯形式、模具结构、零件公差大小、生产效率等进行选择。因为该模具采用的是条料,控制条料的送进方向采用导料销。控制条料的送进步距采用固定挡料销。4.3卸料、出件方式的
20、选择弹压卸料板具有卸料和压料的双重作用,主要用在冲裁料厚在1.5以下的板料,由于有压料作用,冲裁件比较平整。弹压卸料板与弹性元件 (弹簧或橡皮)、卸料螺钉组成弹压卸料装置。卸料板与凸模之间单边间隙选择(0.10.2)t, 若弹压卸料板还需对凸模起导向作用时,二者的配合间隙应小于冲裁间隙。弹性元件的选择,应满足卸料力和冲模结构的要求。为使卸料可靠,卸料板应高出模具刃口工作面0.30.5,材料采用45钢,热处理淬火硬度4348HRC。因为工件料厚1,相对较薄,卸料力不大,由此可知卸料、出件方式的选择可采用弹性卸料装置卸料。4.4标准模架和导向零件的选择模架是整副模具的骨架,模具的全部零件都固定其上
21、,并承受冲压过程的全部载荷。上下模间的精确位置,由导柱、导套的导向实现。方案一:采用对角导柱模架。由于导柱安装在模具压力中心对称的对角线上,所以上模座在导柱上滑动平稳。常用于横向送料级进模或纵向送料的落料模、复合模。方案二:采用后侧导柱模架。由于前面和左、右不受限制,送料和操作比较方便。因为导柱安装在后侧,操作者可以看见条料在模具中的送进动作。但是不能使用浮动模柄。方案三:四导柱模架。具有导向平稳、导向准确可靠、刚性好等优点。常用于冲压件尺寸较大或精度要求较高的冲压零件及大量生产用的自动冲压模架。方案四:中间导柱模架。导柱安装在模具的对称线上,导向平稳、准确。只能一个方向送料。根据以上方案比较
22、并结合模具结构形式和送料方式,为提高模具寿命和工件质量,采用后侧导柱模架,操作者可以看见条料在模具中的送进动作。由于前面和左、右不受限制,送料和操作比较方便,并能满足工件成型的要求。即方案二最佳。5 模具设计工艺计算5.1计算毛坯尺寸根据图2-1得:工件的尺寸()。5.2排样、计算条料宽度及步距的确定5.2.1搭边值的确定排样时零件之间以及零件与条料侧边之间留下的工艺余料,称为搭边。搭边的作用是补偿定位误差,保持条料有一定的刚度,以保证零件质量和送料方便。搭边过大,浪费材料。搭边过小,冲裁时容易翘曲或被拉断,不仅会增大冲件毛刺,有时还会拉入凸、凹模间隙中损坏模具刃口,降低模具寿命或影响送料工作
23、。搭边值通常由经验确定,表5-1所列搭边值为普通冲裁时经验数据之一。表5-1 搭边a和a1数值材料厚度圆件及r2t的工件矩形工件边长L50矩形工件边长L50或r2t的工件工件间a1沿边a工件间a1沿边a工件间a1沿边a0.25 0.250.50.50.80.81.21.21.61.62.02.02.52.53.03.03.53.54.04.05.05.0121.81.21.00.81.01.21.51.82.22.53.0 0.6t2.01.51.21.01.21.51.82.22.52.83.5 0.7t2.21.81.51.21.51.82.02.22.52.53.5 0.7t2.52.0
24、1.81.51.82.02.22.52.83.24.0 0.8t2.82.21.81.51.82.02.22.52.83.24.0 0.8t3.02.52.01.82.02.22.52.83.23.54.5 0.9t根据制件厚度与制件的排样方法可以查表5-1得,搭边值工件间a1为1.5,沿边a为1.8。5.2.2条料宽度的确定条料宽度公式: (5-1)式中:-条料宽度方向冲裁件的最大尺寸,; -侧搭边值,;其中条料宽度偏差上偏差为0,下偏差为,见表5-2条料宽度偏差。表5-2 条料宽度偏差 条料宽度B/材料厚度0.50.5112200.050.080.1020300.080.100.15305
25、00.100.150.20查表5-2可得条料宽度偏差的下偏差()为。根据公式(5-1)得:5.2.3导料销的选用设计导料销时,应注意以下几点:(1)工件外形简单时,应以外形定位,外形复杂时以内孔定位。(2)定位要可靠,放置毛坯和取出工件要方便,确保操作安全。(3)若工件需要经过几道工序完成时,各套冲模应尽可能利用工件上同一位基准,避免累积误差。查模具设计手册该模具导料销的直径为。标记 热处理4348导料销距离公式: (5-2)式中:-导料销工作部位的半径(),得=6;根据公式(5-2)得:图5-2 导料销5.2.4排样方法排样合理与否不但影响材料的经济利用,还影响制件的质量、模具的寿命、制件的
26、生产率和模具的成本等技术、经济指标。根据材料经济利用程度,排样方法可以分为有废料、少废料和无废料排样三种,根据制件在条料上的布置形式,排样又可以分为直排、斜排、对排、混合排、多排等多重形式。采用少、无废料排样法,材料利用率高,不但有利于一次冲程获得多个制件,而且可以简化模具结构,降低冲裁力,但是,因条料本身的公差以及条料导向与定位所产生的误差的影响,所以模具冲裁件的公差等级较低。同时,因模具单面受力(单边切断时),不但会加剧模具的磨损,降低模具的寿命,而且也直接影响到冲裁件的断面质量。根据设计的零件的形状、厚度、材料等方面的全面考虑,排样方法采用有废料直排法。5.2.5材料利用率本设计中将冲裁
27、零件的面积分成上、下两部分:上部为梯形,下部为矩形。 查模具设计手册钢板毛坯规格为:送料步距为:材料利用率通常以一个步距内制件的实际面积与所用毛坯面积的百分率表示: (5-3)式中:-材料利用率();-冲裁件的数目(=1);-冲裁件的实际面积(=);-板料宽度(=41.6);-步距(=47.7)。根据公式(5-3)得:由此可之,值越大,材料的利用率就越高,废料越少。工艺废料的多少决定于搭边和余量的大小,也决定于排样的形式和冲压方式。因此,要提高材料利用率,就要合理排样,减少工艺废料。横裁时的条料数为:(条) 可冲72条每条的件数为: (件) 可冲15件板料可冲总件数为:(件)板料利用率:纵裁时
28、的条料数为:(条) 可冲18条每条的件数为: (件) 可冲62件板料可冲总件数为:(件)板料利用率:因纵裁的利用率高一点,所以该零件采用纵裁法。如图5-3所示: 图5-3 排样图6 冲裁力相关的计算6.1计算冲裁力的公式计算冲裁力是为了选择合适的压力机,设计模具和检验模具的强度,压力机的吨位必须大于所计算的冲裁力,以适宜冲裁的要求,普通平刃冲裁模,其冲裁力一般可以按下式计算: (6-1)式中:-材料抗剪强度;-冲裁周边总长();-材料厚度();系数是考虑到冲裁模刃口的磨损,凸模与凹模间隙之波动(数值的变化或分布不均),润滑情况,材料力学性能与厚度公差的变化等因数而设置的安全系数,一般取=1.3
29、。根据常用金属冲压材料的力学性能查出08钢抗剪强度为255333,取=300。6.2总冲裁力、推料力、卸料力和总冲压力由于冲裁模具采用弹压卸料装置和自然落料方式。总的冲裁力包括:(1)-总冲压力 (2)-总冲裁力(3)-卸料力(4)-推料力6.2.1总冲裁力 (6-2)式中:-落料时的冲裁力;-冲孔时的冲裁力;-落料周长();-冲孔周长()。计算其冲裁周边的长():落料周长为: 冲孔周长为: 根据公式(6-2)得: 表6-1 卸料力、推件力和顶件力系数料厚t/钢0.10.10.50.52.52.56.56.50.0650.0750.0450.0550.040.050.030.040.020.0
30、30.10.0630.0550.0450.0250.140.080.060.050.03铝、铝合金纯铜、黄铜0.0250.080.020.060.030.070.030.09注:对于表中的数据,厚的材料取小值,薄材料取大值。6.2.2计算卸料力 (6-3)查表6-1得: 根据公式(6-3)得:6.2.3计算推料力 (6-4)查表6-1得: n-根塞在凹模内的制件或度料数量()根据公式(6-4)得: 6.2.4计算总冲压力F (6-5) 根据总冲压力,初选压力机为:开式双柱可倾压力机J23-16(参数见附录4)。7 模具压力中心与计算模具压力中心是指冲压时诸冲压力合力的作用点位置。为了确保压力机
31、和模具正常工作,应使模具的压力中心与压力机滑块的中心相重合,否则,会使冲模和压力机滑块产生偏心载荷,使滑块和导轨之间产生过大的摩擦,模具导向零件加速磨损,降低模具和压力机的使用寿命。模具的压力中心,可按以下原则来确定:(1)对称零件的单个冲裁件,冲裁的压力中心为冲裁件的几何中心。(2)工件形状相同且分布对称时,冲裁的压力中心与零件的对称中心重合。(3)各分力对某坐标轴的力矩之代数和等于诸力的合力对该轴的力矩。求出合力作用点的坐标位置0,0(x=0,y=0),即为所求模具的压力中心。 (7-1) (7-2)零件属于多形孔冲裁、冲压模的压力中心可以用解析计算法求出冲模压力中心。下面用解析法确定与计
32、算模具的压力中心: 图7-1 压力中心图把刃口轮廓分为25段,并确定各段长度,具体数值列于下表7-1中。表7-1 落料件的压力中心计算数据线段长度()压力中心位置压力中心坐标xyL1=14.5L2=22.45L3=24.2L4=19L5=19L6=24.2L7=22.45L8=14.5L9=6.28L10=6.28L11=6.28L12=6.28L13=6.28L14=6L15=6.28L16=6L17=14L18=8L19=9.25L20=4.325L21=6.2L22=4.325L23=9.25L24=8L25=14C1=0.514.5=7.25C2=0.522.45=11.225C3=0
33、.524.2=12.1C4=0.519=9.5C5=0.519=9.5C6=0.524.2=12.1C7=0.522.45=11.225C8=0.514.5=7.25C9=0.56.28=3.14C10=0.56.28=3.145C11=0.56.28=3.14C12=0.56.28=3.14C13=0.56.28=3.14C14=0.56=3C15=0.56.28=13.14C16=0.56=3C17=0.514=7C18=0.58=4C19=0.59.25=4.625C20=0.54.325=2.1625C21=0.56.2=3.1C22=0.514.325=2.1625C23=0.59.
34、25=4.625C24=0.58=4C25=0.514=701134.146.246.234.1110373781318133034383634363834307.259.5199.5-9.5-19-9.5-7.251010-10-10020-27-149.3757.0250-7.025-9.375-14-7由于该零件是一个对称图形y轴可不计算落料凸模的压力中心坐标:根据公式(7-1)得: 故求得模具压力中心的坐标值,在模柄投影范围内,设计合理。8 冲裁间隙冲裁单面间隙是指凸模与凹模刃口横向尺寸差值的一半,间隙值的大小不但影响上、下裂纹的会合,而且影响变形应力的性质和大小。因此,设计模具时一定
35、要选择合理的间隙,以保证冲裁件的断面质量、尺寸精度满足产品的要求,所需冲裁力小、模具寿命高,但分别从质量,冲裁力、模具寿命等方面的要求确定的合理间隙并不是同一个数值,只是彼此接近。考虑制造中的偏差及使用中的磨损、生产中通常只选择一个适当的范围作为合理间隙,只要间隙在这个范围内,就可以冲出良好的制件,这个范围的最小值称为最小合理间隙,最大值称为最大合理间隙。考虑到模具在使用过程中的磨损使间隙增大,故设计与制造新模具时要采用最小合理间隙值。冲裁间隙的大小对冲裁件的断面质量有极其重要的影响,此外,冲裁间隙还影响模具寿命、卸料力、推件力、冲裁力和冲裁件的尺寸精度。冲裁过程中,凸模与被冲的孔之间,凹模与
36、落料件之间均有摩擦,间隙越小,模具作用的压应力越大,摩擦也越严重,而降低了模具的寿命。较大的间隙可使凸模侧面及材料间的摩擦减小,并延缓间隙由于受到制造和装配精度的限制,虽然提高了模具寿命,但出现间隙不均匀。因此,冲裁间隙是冲裁工艺与模具设计中的一个非常重要的工艺参数。根据间隙表8-1查得:材料08的最小双面间隙:最大双面间隙:表8-1 冲裁模初始用间隙2C()材料厚度08、10、35、09Mn、Q23516Mn40、5065Mn2Cmin2Cmax2Cmin2Cmax2Cmin2Cmax2Cmin2Cmax小于0.5极小间隙0.50.60.70.80.91.01.21.51.752.02.12
37、.52.753.03.54.04.55.56.06.58.00.0400.0480.0640.0720.0920.1000.1260.1320.2200.2460.2600.2600.4000.4600.5400.6100.7200.9401.0800.0600.0720.0920.1040.1260.1400.1800.2400.3200.3600.3800.5000.5600.6400.7400.8801.0001.2801.4400.0400.0480.0640.0720.0900.1000.1320.1700.2200.2600.2800.3800.4200.4800.5800.680
38、0.6800.7800.8400.9401.2000.0600.0720.0920.1040.1260.1400.1800.2400.3200.3800.4000.5400.6000.6600.7800.9200.9601.1001.2001.3001.6800.0400.0480.0640.0720.0900.1000.1320.1700.2200.2600.2800.3800.4200.4800.5800.6800.7800.9801.1400.0600.0720.0920.1040.1260.1400.1800.2400.3200.3800.4000.5400.6000.6600.780
39、0.9201.0401.3201.5000.0400.0480.0640.0640.0900.0900.0600.0720.0920.0920.1260.126注:冲裁皮革、石棉和纸板时,间隙取08钢的25%。9 刃口尺寸的计算9.1刃口尺寸计算的基本原则冲裁件的尺寸精度主要决定于模具刃口的尺寸精度,模具合理的间隙值是依靠模具刃口尺寸及制造精度来保证。正确确定模具刃口尺寸及其制造公差,是设计冲裁模的主要任务之一。从生产实践中可以发现:(1)由于凸、凹模之间存在间隙,使落下的料和冲出的孔都带有锥度,且落料件的大端尺寸等于凹模尺寸,冲孔件的小端尺寸等于凸模的尺寸。(2)在尺量与使用中,落料件是以大
40、端尺寸为基准,冲孔孔径是以小端尺寸为基准。(3)冲裁时,凸、凹模要与冲裁件或废料发生摩擦,凸模越磨愈小,凹模越磨愈大,结果使间隙越来越大。由此在决定模具刃口尺寸及其制造公差时需要考虑以下原则:(1)落料件尺寸由凹模尺寸决定,冲孔时的尺寸由凸模尺寸决定。故设计落料模时,以凹模为基准,间隙取在凹模上;设计冲孔模时,以凸模尺寸为基准,间隙取在凹模上。(2)考虑到冲裁中凸、凹模的磨损,设计落料凹模时,凹模基本尺寸应取尺寸公差范围的较小尺寸;设计冲孔模时,凹模基本尺寸应取工件孔尺寸公差范围的较大尺寸。这样在凸、凹模磨损到一定程度的情况下,人能冲出合格的制件。凸凹模间隙则取最小合理间隙值。(3)确定冲模刃
41、口制造公差时,应考虑制件的公差要求。如果对刃口精度要求过高(即制造公差过小),会使模具制造困难,增加成本,延长生产周期;如果对刃口要求过低(即制造公差过大)则生产出来的制件有可能不合格,会降低模具的寿命。若工件没有标注公差,则对于非圆形工件按国家“配合尺寸的公差数值”IT14级处理,冲模则可按IT11级制造;对于圆形工件可按IT7IT9级制造模具。冲压件的尺寸公差应按“入体原则”标注单项公差,落料件上偏差为零,下偏差为负;冲孔件上偏差为正,下偏差为零。9.2刃口尺寸的计算方法由于模具的加工方法不同,凸模与凹模刃口部分尺寸的计算公式与制造公差的标注也不同,刃口尺寸的计算方法可以分为两种情况。凸模
42、与凹模分开加工和凸模与凹模配合加工。对与该制件应该选用凸模与凹模配合加工方法。对于该工件的模具,为了保证冲裁凸、凹模间有一定的间隙值,必须采用配合加工。此方法是先做好其中一件(凸模或凹模)作为基准件,然后以此基准件的实际尺寸来配合加工另一件,使它们之间保留一定的间隙值,因此,只在基准件上标注尺寸制造公差,另一件只标注公称尺寸并注明配做所留的间隙值。这与就不再受间隙限制。根据经验,普通模具的制造公差一般可取(精密模具的制造公差可选(46)。这种方法不仅容易保证凸、凹模间隙值很小。而且还可以放大基准件的制造公差,使制造容易。在计算复杂形状的凸凹模工作部分的尺寸时,可以发现凸模和凹模磨损后,在一个凸
43、模或凹模上会同时存在三种不同磨损性质的尺寸,这时需要区别对待。(1)第一类:凸模或凹模磨损会增大的尺寸;(2)第二类:凸模或凹模磨损后会减小的尺寸;(3)第三类:凸模或凹模磨损后基本不变的尺寸。9.3计算凸凹模刃口的尺寸凸模与凹模配合加工的方法计算落料凸凹模的刃口尺寸。(1)凹模磨损后变大的尺寸,按一般落料凹模公式计算,即 (9-1)(2)凹模磨损后变小的尺寸,按一般冲孔凸模公式计算,因它在凹模上相当于冲孔凸模尺寸,即 (9-2)(3)凹模磨损后无变化的尺寸,其基本计算公式为: (9-3)为了方便使用,随工件尺寸的标注方法不同,将其分为三种情况:(1)工件尺寸为时 (9-4)(2)工件尺寸为时
44、 (9-5)(3)工件尺寸为时 (9-6)式中: 、-相应的凹模刃口尺寸;-工件的最大极限尺寸;-工件的最小极限尺寸;-工件的基本尺寸;-工件公差;-系数。为了避免冲裁件尺寸偏向极限尺寸(落料时偏向最小尺寸,冲孔时偏向最大尺寸),值在之间,与工件精度有关可查表9-1选取。-凹模制造偏差,通常取。表9-1 系数料厚t()非圆形圆形10.750.50.750.5工件公差/1122440.160.200.240.300.170.350.210.410.250.490.310.590.360.420.500.600.160.200.240.300.160.200.240.309.3.1对落料的刃口尺寸
45、进行计算如图9-1所示的窗户锁扣的落料零件图,计算其凸、凹模的刃口尺寸。考虑零件形状比较复杂,采用配作法加工凸、凹模。凹模磨损后其尺寸变化情况如下, 落料时应以凹模为基准件来配作凸模。图9-1 落料凹模座标图表9-2 凹模刃口磨损后尺寸计算代号工件尺寸公式刃口尺寸A25.7-00,5225.44+00.13BR2-00。252.99+00.075C20.4-00.5220.14+00.13D24.2-00。2523.94+00.13ER2-00。252.99+00.075F34-00.6233.79+00.155GR2-00。252.99+00.075H24.2-00。2523.94+00.1
46、3I20.4-00.5220.14+00.13JR2-00。252.99+00.075注:; 。查表得知: 9.3.2对冲孔的刃口尺寸进行计算图9-2 冲孔凸模座标图如图9-2为制件冲孔的零件图,计算凸、凹模刃口尺寸,按冲孔凸模尺寸公式进行计算。表9-3 凸模刃口磨损后尺寸计算代号工件尺寸公式刃口尺寸A12.56+00.43 12.755 -00.1075B12.56+00.4312.755 -00.1075C6.28+00.366.46 -00.09D6+00.306.225-00.075E6.28+00.366.46 -00.09F6+00.306.225-00.075G28+00.522
47、8.26-00.13H8+00.368.18 -00.09I9.25+00.369.43 -00.09J3.325+00.303.55-00.075K6.2+00.366.38 -00.09L3.325+00.303.55-00.075M9.25+00.369.43 -00.09N8+00.368.18 -00.09注:-冲孔凸模尺寸;-工件孔的最小尺寸;x-系数;-工件公差; ;。查表得知: 9.4冲裁刃口高度表9-4 刃口高度料厚0.50.5112244刃口高度h668810101214查表9-4得:刃口高度为=68,取=7。10 主要零部件的设计设计主要零部件时,首先要考虑主要零部件用什
48、么方法加工制造及总体装配方法。结合模具的特点,本模具适宜采用线切割加工凸模固定板、卸料板、凹模及外形凸模,内孔凸模。这种加工方法可以保证这些零件各个内孔的同轴度,使装配工作简化。下面就分别介绍各个零部件的设计方法。10.1工作零件的结构设计10.1.1凹模的设计凹模采用整体凹模,各种冲裁的凹模孔均采用线切割机床加工,安排凹模在模架上位置时,要依据计算压力中心的数据,将压力中心与模柄中心重合。模具的外形尺寸如下:(1)模具厚度的确定公式为: (10-1)式中:-系数值,考虑板料厚度的影响;-冲裁件的最大外形尺寸;表10-1 系数值Ks/材料厚度t/1133650501001002002000.3
49、00.400.200.300.150.200.100.150.350.500.220.350.180.220.120.180.450.600.300.450.220.300.150.22查表10-1得:查表10-2取(2)模具壁厚的确定公式为: (10-2) 凹模壁厚取:(3)凹模长度的确定公式为: (10-3) (4)凹模宽度的确定公式为: (10-4) 凹模的长度要考虑导料销发挥的作用,保证送料粗定位精度。查表10-2取标准=125(送料方向)。凹模轮廓尺寸为:;凹模材料选用Cr12,热处理6064。表10-2 矩形和圆形凹模的外形尺寸(GB2858-81)矩形凹模的宽度和长度BL矩形和圆
50、形凹模厚度H6350 636310、12、14、16、18、208063、8080、10063、10080、100100、1258012、14、16、18、20、22125100、125125、14080、14080、14、16、18、20、22、25140125、140140、160100、160125160140、200100、20012516、18、20、22、25、28160160、200140、200160、250125、250140、16、20、22、25、28、32200200、250160、250200、280160 、18、22、25、28、32、35250 250、2802
51、00、280250、315200、20、25、28、32、35、40315250、20、28、32、35、40、4510.1.2凸凹模的设计凸凹模的内、外缘之间的壁厚取决于冲裁件的尺寸,为保证凸凹模的强度,凸凹模应有一定的壁厚。凸凹模的尺寸是与凸模、凹模配作;凸凹模设计成台阶式凸凹模。为了固定凸凹模在凸凹模下部作有台阶:凸凹模的高度为: (10-5)式中: -卸料板的厚度,由标准得:;-橡胶的厚度,由计算得:;-凸凹模固定板的厚度,由标准得:;由此可得出: 10.1.3圆形凸模的设计将冲孔凸模设计成台阶式凸模,台阶式凸模工作部分和固定部分的形状做成不一样。凸模与凸模固定板的配合按H7/m6。凸
52、模的高度是凸模固定板的厚度、落料板的厚度的总和。外形凸模长度为: (10-6)式中:-凸模固定板厚度,由标准得:;-落料板厚度,由标准得:;-多出的凸模,由标准得:;根据公式(10-6)得: 标记 热处理5862。10.1.4非圆凸模和复杂非圆凸模设计因为是非圆凸摸和复杂非圆凸模,仍然选用台阶式凸模。与凸模固定板采用H7/m6配合。非圆凸模长度和复杂非圆凸模与圆形凸模长度相等为41。凸模材料应选Cr12,热处理5862。10.2卸料部分的设计10.2.1卸料板的设计本模具卸料板的边界尺寸与凹模的边界尺寸相同,卸料板的厚度按表10-3选择,卸料板厚度为12。卸料板与凸凹模的间隙以在凸凹模设计中确
53、定了为0.035。卸料板上设置了4个螺钉。卸料板采用45钢制造,热处理淬火硬度4548,卸料板标记:12510012。表10-3 固定卸料板厚度冲件厚度t卸料板宽度505080801251252002000.866810120.81.5681012141.5381012141610.2.2卸料橡胶的设计在冲裁模卸料于出件装置中,常用的元件是弹簧和橡胶,考虑本模具结构,该模具采用的弹性元件为橡胶。橡胶允许承受的负载较大,占据空间尺寸较小,安装调整方便灵活,而且成本低,是常用弹性元件。选择橡胶时应主要确定其自由高度预压缩量及截面积,其计算公式及步骤可由以下决定:(1)确定自由高度H自 (10-7)式中:-冲模的工作行程(mm),对冲裁模而言,;-预留的修模量,根据模具设计寿命一般取46;根据公式(10-7)得: (2)确定L预和H装 (10-8)式中:-橡胶的预压缩量;根据公式(10-8)得: =1.5()
- 温馨提示:
1: 本站所有资源如无特殊说明,都需要本地电脑安装OFFICE2007和PDF阅读器。图纸软件为CAD,CAXA,PROE,UG,SolidWorks等.压缩文件请下载最新的WinRAR软件解压。
2: 本站的文档不包含任何第三方提供的附件图纸等,如果需要附件,请联系上传者。文件的所有权益归上传用户所有。
3.本站RAR压缩包中若带图纸,网页内容里面会有图纸预览,若没有图纸预览就没有图纸。
4. 未经权益所有人同意不得将文件中的内容挪作商业或盈利用途。
5. 装配图网仅提供信息存储空间,仅对用户上传内容的表现方式做保护处理,对用户上传分享的文档内容本身不做任何修改或编辑,并不能对任何下载内容负责。
6. 下载文件中如有侵权或不适当内容,请与我们联系,我们立即纠正。
7. 本站不保证下载资源的准确性、安全性和完整性, 同时也不承担用户因使用这些下载资源对自己和他人造成任何形式的伤害或损失。