基于ARM的刀具磨损声谱监测系统设计
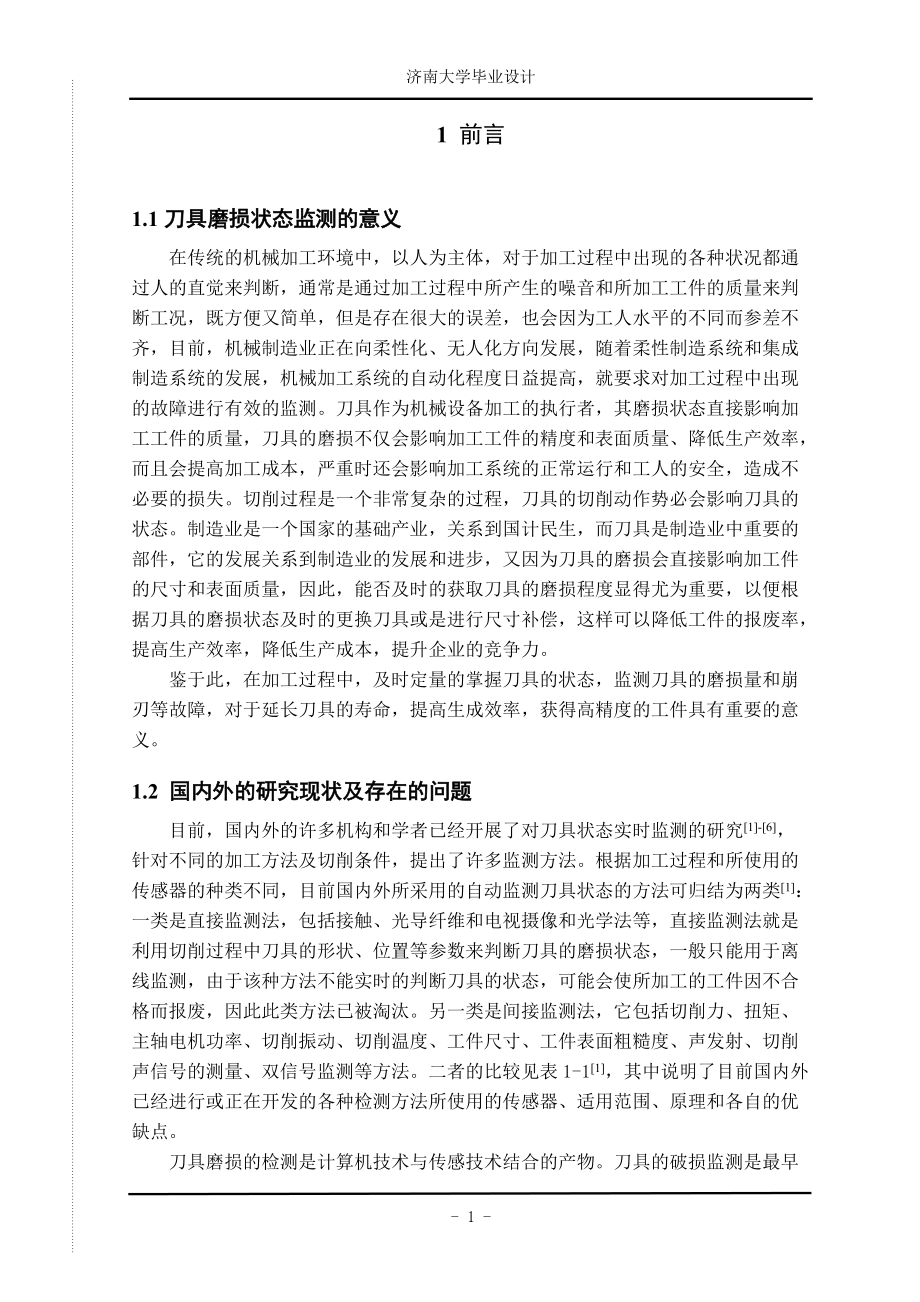


《基于ARM的刀具磨损声谱监测系统设计》由会员分享,可在线阅读,更多相关《基于ARM的刀具磨损声谱监测系统设计(20页珍藏版)》请在装配图网上搜索。
1、济南大学毕业设计1 前言1.1刀具磨损状态监测的意义在传统的机械加工环境中,以人为主体,对于加工过程中出现的各种状况都通过人的直觉来判断,通常是通过加工过程中所产生的噪音和所加工工件的质量来判断工况,既方便又简单,但是存在很大的误差,也会因为工人水平的不同而参差不齐,目前,机械制造业正在向柔性化、无人化方向发展,随着柔性制造系统和集成制造系统的发展,机械加工系统的自动化程度日益提高,就要求对加工过程中出现的故障进行有效的监测。刀具作为机械设备加工的执行者,其磨损状态直接影响加工工件的质量,刀具的磨损不仅会影响加工工件的精度和表面质量、降低生产效率,而且会提高加工成本,严重时还会影响加工系统的正
2、常运行和工人的安全,造成不必要的损失。切削过程是一个非常复杂的过程,刀具的切削动作势必会影响刀具的状态。制造业是一个国家的基础产业,关系到国计民生,而刀具是制造业中重要的部件,它的发展关系到制造业的发展和进步,又因为刀具的磨损会直接影响加工件的尺寸和表面质量,因此,能否及时的获取刀具的磨损程度显得尤为重要,以便根据刀具的磨损状态及时的更换刀具或是进行尺寸补偿,这样可以降低工件的报废率,提高生产效率,降低生产成本,提升企业的竞争力。鉴于此,在加工过程中,及时定量的掌握刀具的状态,监测刀具的磨损量和崩刃等故障,对于延长刀具的寿命,提高生成效率,获得高精度的工件具有重要的意义。1.2 国内外的研究现
3、状及存在的问题目前,国内外的许多机构和学者已经开展了对刀具状态实时监测的研究1-6,针对不同的加工方法及切削条件,提出了许多监测方法。根据加工过程和所使用的传感器的种类不同,目前国内外所采用的自动监测刀具状态的方法可归结为两类1:一类是直接监测法,包括接触、光导纤维和电视摄像和光学法等,直接监测法就是利用切削过程中刀具的形状、位置等参数来判断刀具的磨损状态,一般只能用于离线监测,由于该种方法不能实时的判断刀具的状态,可能会使所加工的工件因不合格而报废,因此此类方法已被淘汰。另一类是间接监测法,它包括切削力、扭矩、主轴电机功率、切削振动、切削温度、工件尺寸、工件表面粗糙度、声发射、切削声信号的测
4、量、双信号监测等方法。二者的比较见表1-11,其中说明了目前国内外已经进行或正在开发的各种检测方法所使用的传感器、适用范围、原理和各自的优缺点。刀具磨损的检测是计算机技术与传感技术结合的产物。刀具的破损监测是最早提出的研究方向,破损是刀具的主要失效形式之一,特别是由脆性材料制成的刀具(如硬质合金、陶瓷刀具等),由于刀具的破损监测技术已经比较成熟并已应用于生产,因此近些年来很多学者将研究的方向转向刀具磨损的在线监测上来。切削过程中,刀具的磨损在所难免,由于刀具的磨损是一个缓慢、渐进的过程,所以对刀具的磨损进行实时在线的监测的研究方法尚未成熟。表 1-1 常见的刀具监测方法监测方法传感器工作原理使
5、用范围及特点直接法光导纤维和电视摄像光纤、光学传感器、摄像机利用磨损面反射的光线或摄像机摄像,再经图象处理和识别在线、非实时监测多种刀具磨损及破损,可现直观图像。价格较高,正在进行实用化开发接触测头、靠模、磁间隙传感器检测切削刃位置用于车、钻、铣等,简便,但易受切屑及切削温度影响,不能实时检测,有一定的应用前景放射性技术放射性元素刀具里注入同位素,测切屑中的放射性用于各种切削加工,不受加工环境影响,但需要解决防护问题,实时性差。应用前景小间接法切削温度热电偶测工件、刀具间切削温度的突发增量用于车削,灵敏度较低,不能用于有冷却液的情况,应用前景小测表面粗糙度激光传感器红外传感器测加工表面粗糙度变
6、化量用于车、铣等,非实时检测,其应用受到一定局限振动加速度计、振动传感器 检测加工过程的振动信号及其变化用于车、铣、钻等,灵敏,实地检测,有应用前景,但需解决刀具的自激振动及环境噪声的干扰切削力 应变力传感器 压电力传感器 检测切削力、切削分力的比值及其变化率 用于车、铣、钻等,简便,实时检测,应用较广,有产品供应.但需改动机床部件 功率 互感器、分流器、功率传感器 主电机或进给电机功率及其变化率 用于车、铣、钻等,成本低,易使用,实时检测,可实现自适应加工,有商品供应,有应用前景声发射声发射传感器 检测加工过程中的声发射信号及其特征参量用于车、钻、攻丝、铣等,灵敏。实用,实时监侧,有较广应用
7、前景,有商品供应1.3 本课题的提出在刀具的切削过程中会产生大量的声音信号,切削声信号是其中的一种,声音信号的幅值和频率会随刀具的磨损状态而变化,有经验的工人可以根据切削过程中所产生的声音信号来判断刀具的磨损状态,由于工人的水平和工作状态不尽相同,因此该方法得不到推广,这也反映了利用声音信号进行刀具磨损监测是一种可行的方法。在利用切削声信号监测刀具磨损方面,许多学者也做了一些研究。厦门电视大学的张纪锁等2选取切削声的频带声压级(中心频率和幅值)作为判别刀具磨损状态的特征量,通过逐步回归计算,建立了刀具悬伸长度和频带声压级幅值与刀具磨损状态之间的判别方程,进一步通过实验表明,利用刀具磨损状态判别
8、方程可以很好的识别出刀具的磨损状态。上海交通大学的王敏等3利用铣削噪声信号作为监测刀具磨损状态的特征量,研究了铣削噪声信号与主轴转速、进给速率之间的关系,而且进一步得出在一定主轴转速和进给速率下,铣削噪声声压值随刀具磨损量的增大而增大,表明铣削噪声与刀具磨损量的相关性很好。天津大学的王太勇等4对切削过程中的声信号和振动信号采用多参数的功率谱分析技术进行了功率谱多参数分析,得出功率谱之和与刀具的磨损量有着密切的关系,而且谱散度分析可用于刀具正常磨损阶段磨损量值的估计。以上对于切削声信号的研究表明,切削声信号中包含大量与刀具磨损有关的信息,为本课题的提出提供了思路和参考价值,此外,与其他信号的提取
9、相比,切削声信号的提取方便而简单,只需在刀具旁安装一个驻极体麦克风就可以,与声发射传感器相比,驻极体麦克风有很高的性价比,其对声音信号的提取不会影响正常的加工过程,便于在工作现场推广。因此本文选用切削声信号作为监测刀具磨损状态的信号。由于切削声信号是一个复杂的信号,采用传统的时域分析和频域分析方法很难提取与刀具磨损有关的信息,因此,本文利用基于语音识别理论的倒谱分析所提取的特征量包含丰富信息的优点。采用线性预测倒谱系数(LPCC)作为切削声信号的特征参数进行刀具磨损状态的研究5,线性预测倒谱系数包含的信息量丰富,抗噪能力强,是目前声音信号处理中应用最为广泛、最有效的特征参数之一。 2 线性倒谱
10、预测的原理2.1 特征向量提取与选择的概念和任务特征向量提取6:由于受到电机转动、机床振动等噪声信号的影响,原始切削声信号中包含的特征数量可能会很大,从一组复杂的信号中提取一个简单的特征量进行信号分析的过程就叫做信号的特征向量提取。特征向量选择:从一组特征向量中挑选出一些最有效的特征向量,已达到能够准确分析刀具磨损状态的目的,这个过程叫做特征向量选择。 特征向量提取和特征向量选择的基本任务就是从许多特征向量中找出那些最能反映刀具磨损状态的特征向量。特征向量提取的正确与否直接关系到刀具磨损状态分析的结果,利用驻极体麦克风在加工现场采集到的切削声信号很难通过时域分析与频域分析的方法获得与刀具磨损相
11、关的特征参数,因此必须利用语音信号分析技术进行去噪处理后才可利用,才能得到最能反映刀具磨损状态的参数,因此,切削声信号的特征向量提取和选择是一个很重要的过程。本文引用切削声信号的线性预测倒谱系数LPCC(Linear Predictive Cepstrum Coefficient)作为监测刀具磨损状态的特征参数。2.2 切削声信号的预处理线性预测分析是在短时平稳这一现实的假设基础上进行的,即一段声音信号是各态历经的平稳随机过程,因此在提取切削声信号的LPCC(Linear Predictive Cepstrum Coefficient)之前,需要对切削声信号进行预处理,已得到短时的平稳信号。声
12、音信号的预处理7通常包括两方面的内容:样本分割和加窗分帧。2.2.1 样本分割由于刀具的切削工程是连续进行的,因此采集到的切削声信号的数据量是十分庞大的。为了便于对切削声信号进行分析,需要选取合适长度的信号,即样本分割。样本分割实际上是采用可以移动的一定长度的窗口截取切削声信号的过程,即使用一定窗宽的窗函数乘以切削声信号6,窗长的选择要根据实际情况综合考虑,但必须要保证所截取的样本包含完整的刀具磨损状态信息。选择1秒长度的声信号段作为声信号分析样本,保证了在一个分析样本里至少包含5个完整的刀具切削周期52.2.2 加窗分帧由于刀具的磨损是一个渐进的过程,因此切削声信号的特性是随时间不断变化的,
13、所以它是一个非稳态过程,但是在短时间范围内,其特性基本保持不变即相对平稳,所以可以认为短时间内的切削声信号是一个准稳态信号,鉴于这样的特性,对切削声信号的分析和处理必须建立在短时的基础上,即进行“短时分析”。将切削声信号分成一段一段的进行分析,每一段称为一帧,由于声音信号通常在10-30 ms内保持相对稳定8,因而帧长一般取10-30ms。为了得到短时的切削声信号,要对切削声信号进行加窗操作,即窗函数平滑的在切削声信号上滑动,将切削声信号进行分帧,也就是使用一定的窗函数乘以切削声信号。为了保证帧与帧之间的平滑过渡,保持其连续性,采用交叠分帧的方法,前后帧交叠的部分称为帧移,常用的窗函数有矩形窗
14、、汉明窗、三角窗等,本文采用矩形窗对切削声信号进行分帧,取帧长为20 ms,帧移为10 ms。图2-1给出了帧长与帧移的关系。图2-1帧长与帧移关系图加窗分帧后的切削声信号可以视为短时的平稳信号,因而可以利用对平稳声信号的分析方法进行分析。2.3 切削声信号LPCC的表征线性预测分析法是声音信号识别中的重要技术,线性预测分析的基本思想是12:一个声音信号的采样能够用过去若干个声音信号的采样的线性组合来逼近。通过使线性预测到的采样在最小均方误差意义上逼近实际声音信号的采样,可以求取一组唯一的预测系数。而这组预测系数就反映了声音信号的特征。根据声音信号线性预测的基本思想,声音信号的当前样本可以利用
15、前P个样本来预测,即 (1)式中,ak为线性预测系数(LPC),i=1,2,p;p为LPC的介数,实际的预测误差e(n)应为: (2)使e(n)的均方值达到最小时,可以求取唯一的一组ai,这个过程就是LPC的分析过程。利用公式(2)求得的LPC易受外界的干扰,一次必须进一步对线性预测系数进行倒谱处理6。线性预测倒谱参数(LPCC)是线性预测系数(LPC)在倒谱域中的表示。该特征是基于切削声信号是自回归信号的假设,利用线性预测分析获得倒谱系数。利用线性预测分析得到的LPCC继承了LPC描述声信号谱包络简洁有效的优点;同时,LPCC的求解过程实际上也是对声信号进行倒谱计算的过程7,通过倒谱处理和取
16、低阶系数(m取值10-16)5,可以去除大量卷积噪声,提高LPCC的抗干扰性能。线性预测倒谱系数的优点是比较彻底的去掉了切削声信号中大量与刀具磨损状态无关的噪声信息,而且计算量小,易于实现。往往只需要十几介就能很好的描述刀具磨损的状态9。切削声信号的的计算过程是:首先,对在加工现场采集到的切削声信号进行样本分割和加窗分帧;其次,计算每帧信号的自相关函数;再次,利用Durbin递推算法求取线性预测系数(LPC);最后,利用LPC得到切削声信号的LPCC。基于LPC分析的倒谱存在一种非常简单有效的递推求解方法,就是,如果已知线性预测系数,可利用下列递推公式求得相应的倒谱系数: (2)3 刀具磨损状
17、态监测硬件电路设计根据切削声信号的分析方法,进行基于切削声谱LPCC的刀具磨损监测系统设计,硬件部分选用广州友善之臂的ARM9内核的S3C2440的处理器作为系统的核心,通过扩展SDRAM、FLASH、RS232串口、LCD显示屏、音频芯片等来实现切削声信号的采集和处理,进而实现人机交互。3.1总体方案设计本课题采用切削声信号来检测刀具的磨损状态,因此要求硬件系统具有声音信号的采集、存储、分析和显示等功能,刀具磨损状态监测的硬件电路框图如图3-1所示:图3-1 刀具磨损监测系统硬件框图3.2 硬件电路设计3.2.1处理器的选择本课题选用Samsung S3C2440作为监测刀具磨损状态的处理器
18、,他完全可以满足监测系统对于处理器的要求,具有良好的可扩展性,使用方便,S3C2440处理器是广州友善之臂计算机科技有限公司开发的32位的嵌入式处理器。支持32位ARM指令和16位Thumb指令集,支持数据Cache和指令Cache,具有很高的指令和数据处理能力。S3C2440有以下组件:处理虚拟存储器管理的MMU,NAND FLASH的系统引导器,SDRAM控制器,触摸屏接口,USB接口,PLL时钟产生器等。集成在片上的功能包括:6内核1.25V供电,I/O口3.3V供电;外部存储器控制器(SDRAM和FLASH控制器和产生片选信号);8通道的10位ADC;3通道的UART和2通道SPI;S
19、D卡存储器控制接口;1个USB主机接口和1个USB设备接口;1通道的I2S总线和1通道的I2C总线;1个LCD控制器(支持STN和TFT带有触摸屏的液晶显示器);PLL时钟发生器;16kB的数据CACHE、指令CACHE和存储器管理单元(MMU);3.2.2音频信号采集的电路设计由于UDA1341TS芯片既可以实现模拟音频信号的采集(A/D),又可以实现数字音频信号的模拟输出(D/A),并且可以通过I2S总线与S3C2440直接相连,实现音频信号的数字化处理。因此,本系统选用UDA1341TS芯片实现切削声信号的采集。UDA1341TS内部集成了A/D、D/A、可编程增益放大器和数字自动增益控
20、制器等模块。由于I2S总线只能用于音频流的传输,因此,UDA1341TS需要另外使用L3总线进行控制命令的传送。L3总线包括L3MODE、L3CLOCK和L3DATA三条线,UDA1341TS的L3接口相当于一个混音器控制接口,可以用来控制输入/输出音频信号的的音量大小、低音等。UDA1341TS芯片的引脚如表3-1所示:本文采用UDA1341TS的ADC通道1作为切削声信号的输入接口,利用驻极体麦克风采集加工现场的切削声信号,使用IS总线实现UDA1341TS和S3C2440之间的音频信号传输。其硬件原理图如图3-2所示:表4-1 UDA1341TS芯片的引脚功能引脚号引脚名称网络标号功能描
21、述1VSAADC模拟地2VINL1MIC_INADC左边输入13VDDAADC模拟电压4VINR1VADCNMIC_INADC右边输入15VADCNADC负参考电压6VINL2ADC左边输入27VADCPADC正参考电压8VINR2ADC右边输入29OVERFL十进制滤波器溢出输出10VDDD数字电压11VSSD数字地12SYSCLKCDCLK系统时钟13L3MODEL3MODEL3总线模式输入14L3CLOCKL3CLOCKL3总线时钟输入15L3DATAL3DATAL总线数据输入/输出16BCKI2SSCLK位时钟输入17WSI2SLRCK字选择输入18DATA0I2SSDI数据输出19D
22、ATA1I2SSDO数据输入20TEST1测试控制121TEST2测试控制222AGCSTAT自动增益状态23QMUTE快速声音输入24VOUTRLINEOUT_RDAC右边输出25VDDA(DAC)DAC模拟电压26VOUTLLINEOUT_LDAC左边输出27VSSA(DAC)DAC模拟地28VrefADC和DAC参考电压图3-2 UDA1341TS芯片音频接口电路3.2.3存储器及其他硬件电路设计(1)Flash存储器Flash存储器是嵌入式系统中广泛使用的主流存储器,它的主要特点是按块进行擦除和写入,具有低功耗、高密度、小体积、掉电非易失性等优点。Flash芯片分为Nor-Flash和
23、Nand-Flash。Nor-Flash的地址线和数据线分开,可以直接与S3C2440的总线相连,读取速度快,但是存储容量小,而Nand-Flash需要使用I/O口与S3C2440相连,传输速度慢,由于Nor-Flash的擦除速度相比于Nand-Flash要慢得多,因此,写入速度也慢,另外,Nand-Flash内可能会有坏块,可靠性低。鉴于以上二者优缺点的比较,可知,Nor-Flash适用于代码存储,Nand-Flash适用于数据存储。本课题采用型号为AM29LV160DB-70EC的Nor-Flash,其为1M 16bit的存储器,采用型号为K9F1208U0B的Nand-Flash,其为6
24、4M8bit的存储器。二者与S3C2440连接见图3-3。图3-3 K9F1208U0B和AM29LV160DB-70EC与S3C2440的连接电路图(2)SDRAM同步动态存储器(Synchronous DRAM)具有容量大、存取速度快的特点,常常作为程序运行空间、数据的缓存,以提高系统的运行速度。S3C2440处理器内集成了SDRAM控制器,可以产生控制SDRAM的时钟信号,控制数据的读、写。另外,SDRAM需要刷新电路,才能使其内部的数据不丢失,S3C2440也可以控制SDRAM的刷新。本监测系统采用信号为HY57V561620T-H的SDRAM,其有4个bank,每个bank大小为4M
25、x16bit,由于S3C2440处理器的数据宽度是32位的,为了充分利用资源,在S3C2440的外围扩展两片SDRAM,其与S3C2440的连接见图3-4,其支持突发长度为1、2、4、8字节和全页形式的读取方式;刷新周期为64ms。图3-4 HY57V561620T-H与S3C2440连接电路图(3)RS232串口在刀具监测系统里,也扩展了RS-232串行接口。该串口主要功能是配合WINDOWS下的超级终端或者Linux下的minicom完成计算机与监测系统的通信,方便开发人员下载和调试程序。由于RS-232所规定的逻辑电平与S3c2410处理器所规定的逻辑电平不一致,因此,需要使用电平转换芯
26、片,将RS-232逻辑电平转换为S3c2410处理器的TTL电平。刀具监测系统使用MAX3232芯片进行逻辑电平转换。RS232接口电路如图3-5所示:图3-5 RS232接口电路(4)电源和复位电路由于外部供电电源提供的是12V的直流电,而该系统中很多芯片的工作电压是3.3V,因此,需要使用电压转换芯片将12V的直流电转换为3.3V的直流电,该系统使用信号为APL1117和LM2575S的电压转换芯片,其供电电路如图3-6所示。图3-6 S3C2440电源模块电路由于S3C2440处理器的内核工作电压为1.25V,因此需要采用型号为MAX8860EUA18的芯片来稳定内核电压。内核电压稳定电
27、路如图3-7所示:图3-7 内核电压稳定电路同时,使用芯片MAX708S产生复位信号。MAX708S可产生高、低复位电平信号,并支持手动复位。其复位电路如图3-8所示:图3-8 S3C2440复位电路(5)LCD接口电路在Samsung S3C2440已经集成了LCD控制器,可以支持STN和TFT带有触摸屏的液晶显示器,方便了用户的使用。经过应用程序处理的切削声信号通过I2C总线与LCD显示屏相连。该系统采用液晶显示器,以便随时了解刀具磨损状态的信息。LCD接口电路如图3-9所示:图3-9 LCD接口电路4刀具磨损状态监测系统的软件设计软件部分主要是在linux操作系统下编写程序代码,实现提取
28、切削声信号的特征参数LPCC的功能。4.1 总体方案设计刀具磨损监测系统软件系统流程图如图4-1所示音频驱动程序应用程序LCD驱动程序系统调用系统调用 图4-1 刀具磨损监测系统软件系统流程图4.2 应用程序通常,驱动程序主要完成具体的硬件操作,正如音频驱动程序里对UDA1341TS芯片的控制、读写等都是通过操作各种寄存器实现的;驱动程序提供的往往只是统一的操作接口,也就是所说的系统调用。要利用驱动程序所提供的这些统一接口实现信号分析、处理等都需要在应用程序中实现。在linux操作系统中,将每个物理设备看成一个设备文件。系统调用就会对该设备文件进行相应操作,执行驱动程序里被file_opera
29、tions结构体封装的对应部分以完成对物理设备的具体操作。应用程序主要通过以下步骤实现:首先,执行open()系统调用,打开DSP设备文件;其次,执行系统调用ioctl(),进行各种参数设置,再次,使用系统调用read()读取切削声信号。最后,使用编写的自相关函数和Durbin算法程序,得到声信号的LPC系数,并进行递推得到声信号的特征参数LPCC进行刀具磨损状态监测和显示。其程序流程图见图4-2所示:开始是否打开成功开成功是是否修改默认设置是调用ioctl进行设置否读取切削声信号是否读取成功是打开DSP设备文件对切削声信号进行分帧计算各帧的自相关系数利用Durbin算法求解LPC利用LPC递
30、推LPCC利用Durbin算法求解LPC提取相关分量分析刀具磨损状态是否停止是结束否图4-2 应用程序流程图5 结 论(1) 利用基于语音识别理论的倒谱分析所提取的特征量包含丰富信息的优点,采用线性预测倒谱系数(LPCC)作为切削声信号的特征参数进行刀具磨损状态的研究,对声信号进行加噪处理,进一步研究非平稳噪声的影响,得出切削声信号的LPCC能较准确的判断刀具的磨损状态,说明切削声信号的LPCC是监测刀具磨损状态最好的特征参数之一。(2) 刀具磨损监测系统的硬件部分和声信号特征参数提取已基本完成,但显示部分和声音信号处理的软件的代码有待进一步的开发。 (3) 加噪处理只是针对典型的噪声,需要进
31、一步分析其他噪声,或将噪声加得密一些,以消除偶然因素的影响。参 考 文 献1 雷继荣. 刀具监控技术的现状与发展J. 组合机床与自动化加工技术,1995(5):31-372 张纪锁, 吴建华, 郑炜. 用切削声信号识别刀具磨损J. 厦门大学学报(自然科学版),1995.34(1):52-573 谢政, 王敏, 范伟等. 基于铣削噪声的刀具状态监测研究J. 工具技术,2008.42(7):19-214 王太勇, 郭千里, 赵国立等. 刀具磨损声振特性的功率谱分析J. 天津大学学报,1995.28(4):582-5845 艾长胜, 董全成, 昃向博等. 基于切削声LPCC的刀具磨损监测J. 中国机
32、械工程,2008,20(17):2045-20486 鄢卉, 李仁发等. 语音信号倒谱特征提取建模与仿真J. 系统仿真学报, 2005,17(7):1774-17787 王炳锡, 屈丹, 彭煊等. 实用语音识别基础M. 北京: 国防工业出版社.20058 韩纪庆, 张磊, 郑铁然. 语音信号处理M. 北京: 清华大学出版社.20049 易克初, 田斌, 付强. 语音信号处理M. 北京: 国防工业出版社.200010 刘彬, 任玉艳, 冯冀宁. 数控车床刀具监测方法的研究J. 机械研究与应用,2003,16(2):44-4511 关山. 在线金属切削刀具磨损状态监测研究的回顾与展望II:信号特征
33、的提取J. 机床与液压, 2010,38(17):1001一388112 Litao Wang, Mostafa G. Mehrabi, and Elijah Kannatey-Asibu, Jr Engineering Research Center for Reconfigurable Machining Systems,Tool wear monitoring in reconfigurable machining systems through Wavelet analysis, University of Michigan, Ann Arbor, MI 48109-212513 Xi
34、aoli Li ,Wavelet packet transforms of acoustic emission signals for tool wear monitoring, Institute of Precision Engineering, Harbin Institute of Technology, Harbin, 150001, China Patri, K. Venuvinod14 ZHU HAI-YAN,Investigation of the Methods for Tool Wear On-line Monitoring During the Cutting Proce
35、ss, School ofRailway Tracks and Transportation,East China Jiaotong University, Nanchang, Jiangxi 330013, China15 H. H. Shahah.M.M.Ratnam,On-line monitoring of tool wear in turning operation in the presence of tool misalignment, Int J Adv Manuf Technol (2008) 38:718-72716 友善之臂科技. QQS3C2440V3用户手册M. 广州
36、: 广州友善之臂计算机科技有限公司致 谢毕业的日子日益临近,回想起四年的大学时光,感触颇深,无论是在学习还是在生活上,老师和同学都给了我很大的帮助,在此表示感谢。首先要感谢我的导师艾长胜教授,他严谨求实、认真负责的态度和渊博的知识使他的每一位学生都对他敬佩有加,艾老师不仅在学习上给予我们指导,而且教会了我们许多处事和做人的道理。在实验室学习的日子里机电实验室的其他老师也给了我很多指导和很大的帮助,在此向李国平老师、王娜老师、孙选老师、董全成老师,表示我深深地谢意,感谢他们给我的关心和指导。还要感谢实验室的孙艳杰师姐,以及王涛、徐成智、徐庆松等研究生师兄,及同学杜益刚、李井西等对我的设计给予了热
37、情帮助,在此向他们表达我的感激之情。附 录线性预测的倒谱系数计算子程序如下函数名:LPCC输入:(1)m 线性预测阶数 (2)float *a 线性预测系数 a1-am输出:(1)n 倒谱系数维数 (2)float *cepp 倒谱系数 cepp1-ceppn*Void LPCC(int m,int n,float *a,float *cepp) register int i,j; float sum=0.0, for(i=0;i=n;i+) ceppi=0; cepp1=a1; for(i=1;im;i+) Sum=0.0; for(i=1;j=i-1;j+) sum+=(1.0-(float)j/i)*aj*ceppi-j; ceppi=ai+sum; for(i=m+1;i=n;i+) Sum=0.0; for(j=1;j=m;j+) sum+=(1.0-(float)j/i)*aj*ceppi-j; ceppi=sum; - 20 -
- 温馨提示:
1: 本站所有资源如无特殊说明,都需要本地电脑安装OFFICE2007和PDF阅读器。图纸软件为CAD,CAXA,PROE,UG,SolidWorks等.压缩文件请下载最新的WinRAR软件解压。
2: 本站的文档不包含任何第三方提供的附件图纸等,如果需要附件,请联系上传者。文件的所有权益归上传用户所有。
3.本站RAR压缩包中若带图纸,网页内容里面会有图纸预览,若没有图纸预览就没有图纸。
4. 未经权益所有人同意不得将文件中的内容挪作商业或盈利用途。
5. 装配图网仅提供信息存储空间,仅对用户上传内容的表现方式做保护处理,对用户上传分享的文档内容本身不做任何修改或编辑,并不能对任何下载内容负责。
6. 下载文件中如有侵权或不适当内容,请与我们联系,我们立即纠正。
7. 本站不保证下载资源的准确性、安全性和完整性, 同时也不承担用户因使用这些下载资源对自己和他人造成任何形式的伤害或损失。