车辆工程毕业设计(论文)离合器压盘总成高速破坏试验台设计【】
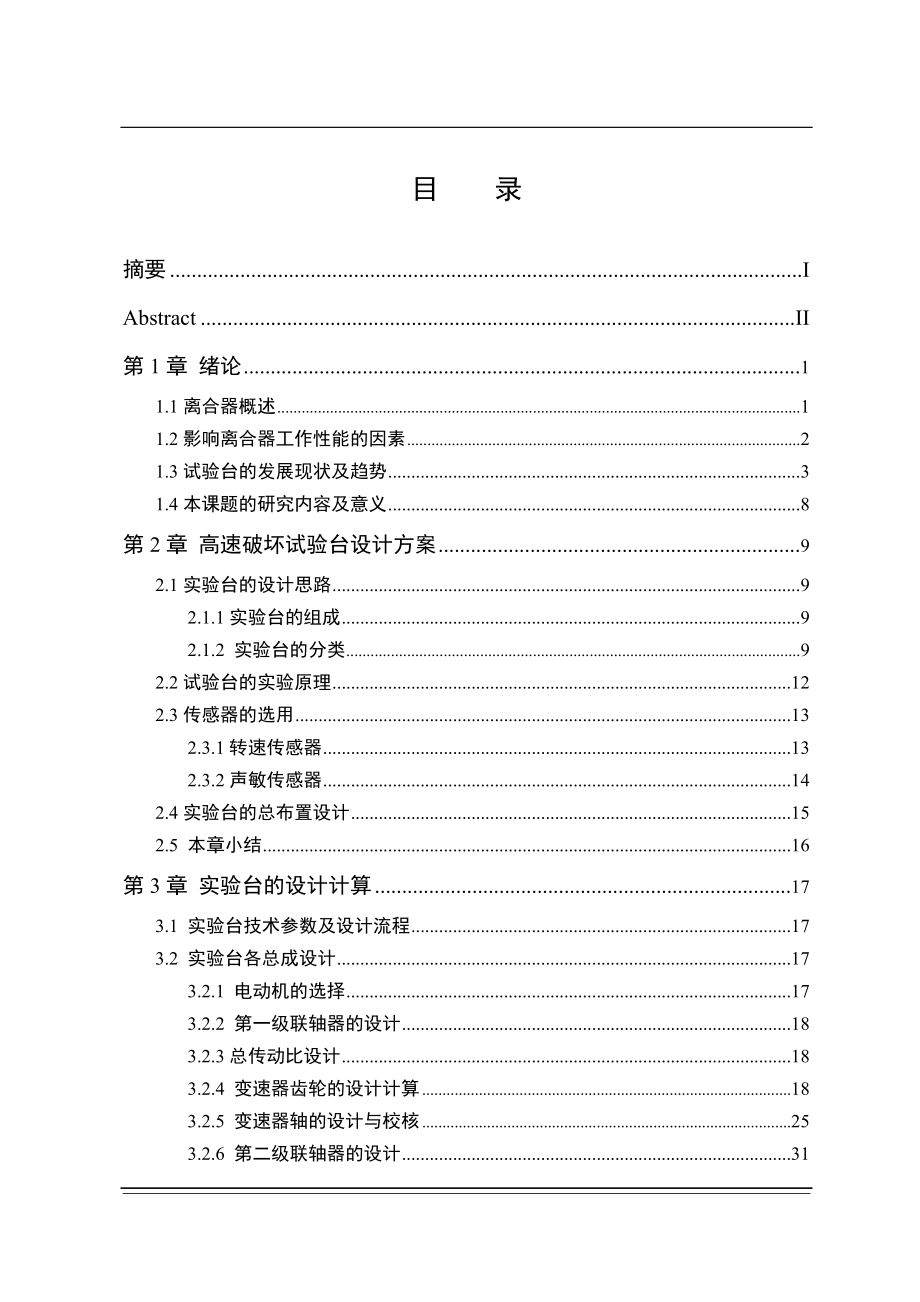


《车辆工程毕业设计(论文)离合器压盘总成高速破坏试验台设计【】》由会员分享,可在线阅读,更多相关《车辆工程毕业设计(论文)离合器压盘总成高速破坏试验台设计【】(44页珍藏版)》请在装配图网上搜索。
1、 目 录摘要IAbstractII第1章 绪论11.1离合器概述11.2影响离合器工作性能的因素21.3试验台的发展现状及趋势31.4本课题的研究内容及意义8第2章 高速破坏试验台设计方案92.1 实验台的设计思路92.1.1实验台的组成92.1.2 实验台的分类92.2试验台的实验原理122.3传感器的选用132.3.1转速传感器132.3.2声敏传感器142.4实验台的总布置设计152.5 本章小结16第3章 实验台的设计计算173.1 实验台技术参数及设计流程173.2 实验台各总成设计173.2.1 电动机的选择173.2.2 第一级联轴器的设计183.2.3 总传动比设计183.2.
2、4 变速器齿轮的设计计算183.2.5 变速器轴的设计与校核253.2.6 第二级联轴器的设计313.2.7 驱动轴的设计313.3 本章小结32结 论33参考文献34致谢35摘 要 随着现代汽车发动机转速的不断提高,对离合器也提出了新的要求,除了要求它在高速下仍能保证传递发动机的最大扭矩外,还要求其必须具有足够的旋转机械强度,以保证安全可靠的工作。离合器在工作过程中与变速器飞轮相连,其结构构成比较复杂,零件极易在高速旋转过程中在离心力的作用下,产生破坏,因此开发其具有破坏性的性能试验台,检验其承受高速运转的能力,避免其在使用过程中出现事故是十分必要的。设计过程中,针对整个试验台的性能要求对整
3、个试验台进行布置设计,包括电机的选择,传动比的分配,联轴器的选择等。另外,还对对变速器中的齿轮,轴,键进行设计计算以及强度等的校核计算,完成了离合器压盘总成高速破坏试验台的设计。为研制开发汽车零部件试验装置提供理论参考。全套图纸,加153893706关键词:离合器总成;传动机构;变速器;高速破坏性试验;试验台设计ABSTRACTWith he Hyundai Motor and continuous improvement in engine speed, the clutch also made new demands, in addition to the requirements des
4、pite its high-speed engines to ensure maximum torque transmission, but also require the rotation must have sufficient mechanical strength to ensure safety reliable work. In the course of clutch and transmission flywheel connected to the structure constitutes a complex, vulnerable parts in the high-s
5、peed rotation in the course of the effect of centrifugal force, resulting in damage, so the development of its devastating performance test rig, to test its high-speed operation under the the ability to avoid its use in case of accidents is very necessary.The design process, the test-bed for the ent
6、ire performance requirements of the test-bed for the entire layout, including the choice of motor, the transmission ratio of the distribution, the choice of coupling. In addition, in the right right reducer gears, shaft, key design and strength calculation of the check, the completion of the clutch
7、pressure plate and cover assembly of high-speed destruction of test-bed design. Research and development of automotive components for test equipment and provide a theoretical reference.Key words: Clutch Assembly; Transmission; Reducer; High-speed Destructive Test; Test-bed Design39第1章 绪 论1.1离合器概述离合器
8、是汽车传动系统中的一种重要的传动装置。它主要实现主动轴和从动轴之间运动和动力的传递和脱离。一般地说,离合器可以实现汽车的启动、停车、换挡、传动轴在运动中的同步、汽车启动和超载时的安全保护等功能,此外,还可以实现防止从动轴的逆转、控制传递扭矩的大小、满足接合时间等方面的要求。汽车主要使用摩擦离合器。摩擦离合器的传动原理是依靠本身的工作元件在接合时的摩擦作用来传递运动和扭矩。汽车离合器是一种常闭式可操纵离合器,其工作过程通常为工作脱开接合的循环过程。由于是常闭状态,所以使离合器通常处于承担负载的状态,只有在偶然或较短暂的时间条件下,才需要通过操纵装置加力使接合元件的主动部分和从动部分脱开,即操纵装
9、置对主动接合元件所施的力为脱开力,而离合器所需的重新接合的压紧力则是由弹簧力来实现。汽车离合器是最重要的结构,保证汽车平稳起步汽车由静止到行驶的过程,其速度由零逐渐增大。有了离合器,在汽车起步时离合器逐渐接合(与此同时,逐渐踩下加速踏板以增加发动机的输出转矩),这样,离合器所能传递的转矩也就逐渐增大,于是发动机的转矩便可有小变大地传给传动系,当牵引力足以克服汽车的行驶阻力时,汽车便由静止状态开始缓慢地加速,实现平稳起步。汽车在行驶过程中,为了适应行驶条件的变化,变速器需要经常换用不同的挡位工作,而普通齿轮式变速器换档时通过拨动换档机构来实现的,即在用挡位的一对齿轮副退出啮合,待用挡位的一对齿轮
10、副进入啮合,换档时,如果没有离合器将发动机与变速器之间的动力暂时切断,在用挡位齿轮副之间将因压力很大而难以脱开,待用挡位的齿轮副将因两者圆周速度不等而难以进入啮合,即使能进入啮合也会产生很大的冲击和噪声,损坏机件,装设了离合器后,换档前先使离合器分离,暂时切断传动系动力传递,然后再进行换档操作,以保证换档操作过程的顺利进行,并减轻或消除换档时的冲击。当汽车紧急制动时,车轮突然紧急降速。若发动机与传动系刚性连接,将迫使发动机也随着急剧降速,其所有运动件将产生很大的惯性力矩,这一力矩作用于传动系,会造成传动系过载而使机件损坏,有了离合器,当传动系承受载荷超过离合器所能传递的最大转矩时,离合器会自动
11、打滑以消除这一危险,从而起到过载保护的作用1。1.2 影响离合器工作性能的因素1. 原动机特性不同的原动机具有不同的工作特性,它是影响离合器工作储备能力的一个重要因素。例如,三相鼠笼电动机具有较硬的自然机械特性,而活塞式内燃机则具有较软的机械特性。软特性的原动机在加载后转速有较大的降低。离合器接合过程包括了原动机的降速过程,允许有较小的工作储备来工作,因为主、从动轴离合器是在较低的转差条件下接合,并在接合后共同以一较低的转速上升到预定的转速。离合器的接合是在原动机起启动后进行的,因此内燃机通常不能带负载起动,一般必须用离合器来实现与工作机的连接。2. 负载特性离合器需要传递的负载扭矩有两种:一
12、种是工作机的正常工作负载,另一种是工作机起动时包括离合器从动部分在内的所有从动质量的惯性负载。如果在起动时就有工作负载,则离合器需传递的扭矩就应包括在内。在起动时,所有从动件的惯量对离合器需传递扭矩的能力影响是很大的,特别是在高转差条件下,接合大的从动件惯量,惯性负载可以达到很大,有时甚至使工作负载显得微不足道。在接合过程中,如果要求接合时间过短,则可能导致离合器传递扭矩过大,而不得不加大离合器的容量和尺寸;如果接合容量仅仅根据工作负载来选择,则导致离合器严重打滑或接合时间过长2。在工作时,系统所产生的扭转振动可能出现很大的振动负载,使离合器或其他传动件产生破坏。振动的原因是系统受到周期性激振
13、力的作用。这种激振力可以是原动机(内燃机)产生的,也可以是工作的脉冲负载。如果系统的固有振动频率和激振频率相等,就会产生共振性振动负载。传动轴的转速达到轴系的临界转速时,将引起共振。设计时传动轴的正常工作转速应当远离临界转速才能使离合器所在的轴系避免共振。3. 离合器结构因素影响最大的是接合元件的接合特性。离合器的接合元件分为啮合与摩擦两大类,前者属于刚性接合,后者属于柔性接合。柔性接合的传动原理主要是依靠接合元件接触后的相互压紧,利用压紧后产生的摩擦力传递扭矩。此外允许在接合过程中有一定程度的打滑。虽然相对打滑在摩擦中会引起能量的损耗,使摩擦元件的温度迅速升高,甚至有可能使元件遭受很大磨损导
14、致损坏,但是只要严格控制使用条件,仍能达到预期的寿命。柔性接合的优点是能够使从动部分的转速较缓慢地上升,减小机械冲击,使机器的工作状态比较平稳;但是柔性接合的缺点是不能以恒定的传动比进行传动。4. 操纵方式不同的操纵方式也会影响离合器的工作性能,而且在某种程度上也决定了离合器的使用范围。5. 安装位置和精度各种离合器由于结构特点和工作性能不同,通常要求一定的安装位置和精度,否则就会影响离合器的正常工作和使用寿命。1.3试验台的发展现状及趋势机械制造业是现代工业的主体,是装备工业的支柱产业。在工业化中期,国民经济增长主要依赖制造业的高速增长,机械制造业对整个工业的发展起到基础和支撑作用。机械工业
15、是国家工业现代化的基础和经济实力的集中表现,也是实现军事现代化和保障国家安全的基础。因此,尽管当今世界上发达国家向以服务业为重心的后工业化社会和知识经济方向发展,但仍然高度重视机械工业的发展,其主导产业和战略产业地位依然牢固,美国、日本、德国拥有世界上最发达的机械工业,包括这三大国在内的许多发达国家都积极采取对策,重塑机械工业以迎接世界新一轮的产业结构调整和更加激烈的竞争3。当今世界机械工业的发展呈现全球化、集群化、信息化、服务化、产品高技术化的趋势。一是全球化战略已成为机械工业跨国公司抢占世界市场的首选战略,跨国公司为克服全球性生产能力过剩和产品生产成本不断上升的困难,加快了机械工业结构调整
16、的步伐,纷纷将重心转向国外,掀起了新的兼并浪潮,规模越来越大,规模化生产使得垄断性跨国公司的技术创新和市场主导作用日益增强,例如在电力设备领域,世界前三大公司控制了全球大型电力设备市场的70%;各大跨国公司在不断联合重组,扩张竞争实力的同时,纷纷收缩战线,剥离非主营业务,以精干主业,提高系统成套能力和个性化、多样化市场适应能力;作为规模化生产的前提和条件,生产高水平零部件和配套产品的"中场产业"快速发展,社会化生产服务体系不断完善,产业的国际化步伐不断加快。二是集群化趋势不断增强,同种产业或相关产业的制造企业在同一区域有机地集聚,通过不断创新而赢得竞争优势,具有特色的中小企
17、业发挥着重要作用。三是机械工业正向信息化方向迈进,新趋势主要表现为柔性制造系统、计算机集成制造系统的开发与推广应用,并向制造智能化方向发展,特别是网络技术的应用,进一步加速了机械工业全球化的进程,并正在改变机械工业的生产和流通方式。四是服务个性化,为适应市场需求的不确定性和个性化的用户要求,先进的制造企业不断吸收各种高新技术和现代管理技术等信息,并将其综合应用于产品设计、生产、管理、销售、使用、服务乃至回收的全过程,以实现优质、高效、低耗、清洁、灵敏及柔性化生产。五是产品高技术化,先进的机械工业是高新技术的重要组成部分,是促进相关产业技术升级和发展的重要依托,随着信息技术、工业自动化技术、数控
18、加工技术、机器人技术、先进的发电和输配电技术、电力电子技术、新型材料技术和新型生物、环保装备技术等当代高新技术成果的应用,使机械产品不断高技术化,其高新技术含量已成为市场竞争取胜的关键。在机械系统中,工作机一般都要靠原动机供给一定形式的能量才能工作。但是把原动机和工作机直接连接的情况很少,通常需要在二者之间加入传递动力或改变运动状态的传动方式。机械传动系统是应用最为普遍的传动装置及机器中的重要部件之一,随着科学的发展、技术的进步,机械传动系统的传动方式、方法、承载能力都有了迅速的发展,人们对产品性能和产品质量提出了更高更严格的要求。为了对机械传动系统的性能、寿命进行测试和分析,为产品设计与质量
19、评价提供可靠的科学依据,缩短产品的开发周期和提高产品质量,适应产品小批量、多品种的发展趋势。机械传动试验台是对常见的传动部件和装置如:链传动、带传动、减速器、变速箱等进行综合性能测试的试验设备。通过试验来检验传动装置设计的合理性,加工、制造、装配和调试的工艺性。对试验结果的深入分析将有助于了解和评定传动部件和装置的综合机械性能同时也为工程设计人员提供实践的参考资料和设计依据。随着机械工业向着高速比、大功率、低噪声等方向飞速发展,人们对于机器传动系统的性能提出了更高的要求,因此,本文对于传动试验台的深入研究将具有重要的实际应用意义。国外较早地开始了这方面的研究,如美国Gleason公司在五十年代
20、就设计出了用轮系作为加载系统的传动试验台的方案。比较著名的还有美国国家航空航天局(NASA)下属的Lewis研究中心、前苏联中央机械制造与设计研究院、美国通用动力公司、德国RENK公司、日本明电舍动力公司、日本丰田汽车公司、美国伊利诺斯大学机械工程系、法国Skoda公司等。从试验台方案的设计到最终的样品制造他们都进行了大量的研究工作,形成了系列化的设计模式。从十九世纪年至今,随着汽车的诞生与发展,欧美国家对汽车离合器的研究从简单到复杂、再到现在的智能化,他们对离合器的研究一直处于领先地位,特别是欧美国家对汽车离合器的研究从简单到复杂、再到现在的智能化,他们对离合器的研究一直处于领先地位,特别是
21、奥迪公司对离合器实验台的开发技术。使得他们对离合器的性能研究有了突飞猛进的发展,在九十年代他们就使用上了双离合器技术,正是有了实验台发展,才使得他们对离合器的开发得以进步,相应在研究离合器的性能时,也开发了许多型号的检测离合器各种性能的实验台,特别是离合器试验台模拟机是对真实的离合器性能试验台的微型化、模型化处理。如德国大众汽车集团开发的离合器,最为先进独特,它很少以外观“哗众取宠”,其内在表现只有那些亲身感受过的人才能领略。并且在2002年度,该公司把电子技术与离合器相结合起来,使离合器更加智能化,正是他们有先进的研发技术,同时也说明,欧美国家正是有了先进的检测技术,使得他们的产品更加先进,
22、安全可靠4。与国外相比,国内对于传动试验台的研究起步相对较晚。研究工作始于八十年代初期。国内较早从事这方面研究工作的主要单位有重庆大学、郑州机械研究所、长春汽车研究所、西安重型机械研究所、西安理工大学、合肥工业大学、四川工业学院、西安减速机厂、西安公路交通大学等单位。他们先后建立起了各种形式的传动试验台,这些试验台的建立从理论上和实践上都取得了很大的进步,积累了丰富的经验,代表着我国机械传动试验设备的发展水平。因此 ,对机械传动系统多功能试验台的研究具有特别重要的意义。现代的机械传动试验台正朝着电封闭功率流式的方向深入发展。采用电封闭功率流的试验台易于控制,易于设计制造,各组成部分之间逐渐模块
23、化、单元化,以便于使用和维护。在其组成上,原动机采用电动机,负载装置采用发电机。由于直流电动机具有易于控制、运行平稳和机械特性硬等优点,因此在电封闭试验台中处于主导地位,作为负载的发电机也多采用直流发电机,直流发电机发出的电能可以直接回馈给电动机,不需要逆变环节。这样就可以大大地简化试验台的组成,降低系统的复杂程度。在控制系统上,早期建立的试验台没有专门的控制系统,仅靠机构组合及传动零件间的啮合作用来实现特定的加载功能。随着加载技术的不断发展,逐渐开始采用继电器控制来完成简单的控制操作5。现代传动试验台已经广泛地应用电子技术和现代控制理论来实现试验过程的自动控制,如电动机的启动、转速调节、力矩
24、调节以及试验过程的自动监测、保护等功能。超速试验是利用高速旋转所产生的强大离心力在超出旋转构件实际转速1至几倍的工况下,对构件预加载荷,来验证旋转构件工作安全可靠性的一种试验方法。这种以实际构件经受应力考核来确定构件可靠性的试验方法称为超速试验技术是超应力技术的一个分支。超速试验必须在确保安全的专门试验设备 超速试验机中进行。高速旋转构件的理论计算十分必要。它是设计的基本前提。随着材料科学、断裂理论的发展以及计算机技术的综合应用,理论计算更趋近实际情况。但是复杂零件的局部结构可能存在应力集中,材料内部存在内应力或材料本身组织不均以及材料中可能存在三向应力,使理论计算与实际工况仍存在一定差异,甚
25、至较大差异。在这种情况下超速试验技术几乎成为确保高速大应力旋转构件工作可靠性的唯一手段。在发达国家,超速试验机在生产高速旋转机械的企业中已成为不可缺少的关键设备。1982年我国一机部部标JB26688O汽车离合器台架试验方法 的试验项目中把“高速破坏试验”列为汽车离合器6项台架试验之一,明确指出试验目的是“确定离合器压盘和从动盘在一定超速工况下的可靠性” 这一标准的实旋,将为我国汽车离合器的使用可靠性提高到一个新水平,也为超速试验技术在我国的推广应用开辟了广阔的前景。随着现代汽车发动机转速的不断提高,对离合器也提出了新的要求,除了要求它在高速下仍能保证传递发动机的最大扭矩外,还要求其必须具有足
26、够的旋转机械强度,以保证安全可靠的工作。离合器在工作过程中与变速器飞轮相连,其结构构成比较复杂,零件极易在高速旋转过程中在离心力的作用下,产生破坏,因此开发其具有破坏性的性能试验台,检验其承受高速运转的能力,避免其在使用过程中出现事故是十分必要的。1.国外超速技术的产生、发展和应用高速旋转机件由于失效而爆破的例子屡见不鲜。如导至飞机坠毁,压缩机叶轮飞裂,离合器、飞轮爆炸,离心机转子爆炸等,严重事故不仅造成重大经济损失,并对设备和生命安全造成很大威胁。严酷的事实迫使人们开始研究事故发生的原因并极力找出其解决办法 。美国是最早研究并推广超速技术的国家。1943年,美国G ·E公司首次利用
27、超速试验研究汽轮机轮盘的强度。经过数十年的发展与完善,目前已有美、英、日、法、意、瑞典、原苏联和原捷克等国家建立了各种超速装置。其中美国的TDI,Barbour Stock Will,日本的三菱、丸和电机,西德的Schench等公司已系列地生产各种超速试验设备。最大的可容纳试件重4 t,直径2.5 m,最大试验转速达25万rrain。1948年美国西屋公司建立了高温超速试验台以进行喷气发动机叶轮的热超速试验。1 947年,麻省理工学院在超速试验基础上对轮盘强度进行了研究。超速试验研究工作得到许多生产厂家的支持。1 974年起9年间,美国的Warren Brother Roads公司共售出大小超
28、速试验台60台套。其中汽车工业如Parkard,Studebaker各6台,Ford汽车公司4台,意大利Fiat汽车公司1台。在英国的航空公司中,仅R·R公司就拥有各种超速试验机12台。目前国外的航空和汽车工业中,各企业都拥有数台超速试验机。日本对超速试验技术的研究比美国晚10年。三菱重工横滨造船所于60年代中期制造了高温高速试验台,以后又生产了其他形式的超速装置数十台原苏联于1 970年在试验盘直径为500 mm 的BPa一500基础上,又建成盘径1500 mm,重达6 t的超速试验装置BP丑一1500,用于1.2 GW 汽轮机轮盘的超速试验。原捷克Skoda厂为发展200 Mw
29、汽轮机,于1969年建立了一个研究轮盘爆裂强度和确定材料断裂韧性的超速试验坑。目前,各国的离合器高速破坏性试验台的最高转速多在20000r/min左右。英国AP公司于60年代研制的一种离合器高速破坏性试验台设计原理如下:零件破坏时刻的判定,是借助于装在破坏舱顶部角落里的传声器实现的。当零件破坏时,传声器将此时的声响传至控制间的扬声器,操作者听见声音后,立即记录下当时的转速表读数,即为破坏转速。当然,对于零件破坏时的转速,现在已经能比较容易地实现自动记录了。在试验时,如果被试离合器压盘及盖总成中某个零件断裂、飞出,就会造成旋转件的不平衡。在如此高的转速下,即使是微小的不平衡,也会长生很大的离心力
30、,它作用于试验台本身和驱动装置的轴和轴承上,将有损于试验台。为了避免这种情况,在被试压盘及盖总成与驱动装置之间,增加一个相当于保险销的连接法兰。该法兰的轴颈断面系数设计的很小。一旦平衡遭到破坏,新的不平衡量所产生的弯矩,就会将连接法兰的轴颈折断,因而使整个被试总成与驱动装置脱开,从而使试验台得到保护。当然,该项试验所用的试验设备还有许多不同的结构形式,如有的应用直流电动机作为动力,经齿轮升速箱升速后,驱动被试件,这样可使试验的操纵控制较为简单,占地面积也可缩小。2.国内超速试验机的应用国内自60年代开始引进原苏联资料,但直到70年代才陆续在一些学校、研究单位建成这种设备。70年代中期又引进一些
31、超速试验台,但这些试验台体积庞大,结构复杂,价格昂贵,难以推广使用。80年代中期,我国开始独立设计汽车离合器的超速试验台。它们的体积较小,重量较轻,安装方便,价格低廉,安全可靠。试验参数如转速、加速度、恒速时间等均由微机控制,预先设定。试验后数据图表及报告可一次打印完成,自动化程度高。QHCSJ-I型超速试验机就是在这个基础上进一步完善起来的。我国超速试验技术的应用仍十分落后,目前国内生产的绝大部分旋转机械产品没有应用超速试验技术。而引进国外技术生产的压缩机,透平转子、离心机、离合器、燃汽轮机、飞轮和砂轮等产品都规定要进行超速试验。可以说,没有进行超速试验的高速旋转构件均潜伏着危险性。而一旦严
32、格地实行超速试验技术,已经发生的许多事故实际上都有可能避。随着现代汽车发动机转速的不断提高,对离合器了新的要求,除了要求它在高速下仍能保证传递发动机的最大扭矩外,还要求其必须具有足够的旋转机械强度,以保证安全可靠的工作。离合器在工作过程中与变速器飞轮相连,其结构构成比较复杂,零件极易在高速旋转过程中在离心力的作用下,产生破坏,因此开发其具有破坏性的性能试验台,检验其承受高速运转的能力,避免其在使用过程中出现事故是十分必要的。1.4本课题的研究内容离合器在工作过程中与变速器飞轮相连,其结构构成比较复杂,零件极易在高速旋转过程中在离心力的作用下,产生破坏,因此开发其具有破坏性的性能试验台,检验其承
33、受高速运转的能力,避免其在使用过程中出现事故是十分必要的。本设计主要内容如下:(1)离合器压盘总成高速破坏试验台的总体结构设计;(2)试验台各部件结构形式的确定及附件的选择;(3)传动机构的设计;第2章 高速破坏试验台设计方案2.1 试验台的设计思路2.1.1试验台的组成本试验装置为模块化结构,由三大模块组成,分别为: 动力源模块(电动机部分); 传动装置模块(减速器及其他传动部件组成传动系统); 离合器样品仓。将这三大模块用图表示,如图2.1所示。驱动装置离合器样品仓传动装置图2.1 离合器高速破坏试验台原理图从图2.1可以看出,整个试验台由驱动装置发出动力,通常用作驱动装置的有发动机、电动
34、机等;动力经过传动装置得到想要的转速;最后将转速传递到被试件,考验其耐高速性能。2.1.2 实验台的分类机械传动试验台从工作原理上可以分为开放功率流式试验台和封闭功率流式试验台。下面分别对它们的组成及特点作简要介绍。a)开放功率流式原动机传感器被试装置传感器负载装置测量装置控制台图 2.2 开放功率流式原理试验台的输入功率由原动机提供,经过被试装置传递至负载装置。负载装置采用纯粹的耗能部件,如磁粉制动器、电涡流测功机等,传递到负载装置的功率被负载装置完全消耗掉,同时给被试装置施加了载荷。由于整个试验台的功率流向未形成回路,故称其为开放功率流式6。开放式功率流式试验台的主要优点是:结构简单、制造
35、安装方便、加载稳定可靠、能够方便地进行不同功率和各种形式的被试装置的测试试验,但是,由于功率流开放使得动力消耗大,造成能量的巨大浪费,试验费用较高,这类试验大多用于中小功率、非长期运转的试验。b)封闭功率流式封闭功率流式试验台的组成原理如图2.3。原动机传感器被试装置传感器负载装置测量装置控制台能量回馈图 2.3 封闭功率流式原理通过机械或电气控制方法将试验台中的能量构成一封闭循环系统,以此实现试验能量的循环利用,可大大减小试验台的能量消耗,节省能源。采用这种原理设计的试验台被称为封闭功率流式试验台。根据构成封闭功率流方法的不同,它又可分为电封闭功率流式试验台和机械封闭功率流式试验台两大类型。
36、该种类型的试验台在结构上与开放功率流式相似,不同之处在于负载装置具有功率回收功能。从原动机发出的功率可以部分地反馈回原动机,既达到了加载的目的,又实现了节能。封闭功率流式试验台除了具有开放功率流式的优点外,还具有节能的优点,节能效果可达50%左右,因而它适用于较大功率的被试装置进行长期的运转试验。试验台的负载装置是用来对被试装置进行加载的,是试验台重要的组成部分。加载方式的不同对于试验台的性能有着重要的影响。常见的机械传动试验台的加载方式主要有机械加载、液压加载、电力加载。在传动试验台发展的初期阶段,大多采用机械加载方式。常见的机械式加载装置主要有摇摆齿轮箱、轮系、弹性扭力杆等。机械式加载具有
37、较大的力矩放大能力,适用于大功率和大扭矩的场合。其缺点是结构复杂,加载装置中的受力零件易被磨损而引起功率的损失,易产生振动和噪声,且在加载器的设计与制造时对于零件的材料和热处理有较高的要求,制造成本高。随着生产的不断发展,机械加载方式已逐渐被其它的加载方式所取代。液压加载方式是指采用液压泵、旋转液压伺服器等作为负载装置。液压加载可以实现较大的加载功率,利用液压加载控制系统可以在加载过程中改变载荷。液压加载的缺点就是加载过程中载荷是脉动性的,液压缸油路系统的泄漏也易造成加载不平稳,而且由于液体会被压缩,因而在小功率条件下的试验结果不准确。目前,试验台采用液压加载方式的单位有:西安重型机械研究所、
38、广西汽车拖拉机研究所、山东科技大学等单位7。电力加载的方式是指利用电涡流测功机、磁粉制动器、发电机等作为负载装置。电力加载具有运行平稳、易于控制、加载精度高等优点,特别是利用发电机作为加载装置,可以将机械能转化为电能并回馈给原动机,实现了能量的回收。目前电力加载的方式得到了广泛采用,国内采用电力加载方式的单位有:重庆大学、郑州机械研究所、吉林工业大学合肥业大学、西安理工大学、浙江大学等单位。另外,机械传动试验台的传动系的布置方案有垂直和平行两种。平行传动是指对于整个传动系来说,输入轴和输出轴是平行布置的。平行机械传动方案如图2.4所示。图2.4 平行轴式机械传动而垂直轴式机械传动指传动系统的输
39、入轴和输出轴是垂直布置的。下面图2.5和图2.6是垂直机械传动方案的简图。图2.5 垂直轴式机械传动2.2试验台的试验原理机械传动系统性能分析一般通过观察传动系统工作情况和分析机械性能参数曲线来得到。要观察系统传动是否平稳、有否噪声。要分析系统的传动比、效率在转速不变的情况下,随转矩变化的曲线,转速可在高速、中速范围内取几个恒定的值进行测量;传动比、效率在转矩不变的情况下,随转速变化的曲线,转矩可在大负荷、中负荷范围内取几个恒定的值进行测量。通过对某种机械传动装置和传动方案性能参数曲线的测试、来分析比较机械传动的性能特点12。试验台通过转电机输出基本的一些动力参数,这些参数也是整个传动系统的输
40、入参数。而传动系的输出端接入离合器样品中。这样就可以对所要试验的离合器样品输入要求的转速。试验台可替代传统的单一试验台进行有关类型机械传动的基本试验。如:V带传动试验、同步带传动试验、摆线针轮传动试验和进行多级组合传动系统布置优化试验。如:链齿轮及齿轮链组合试验;链蜗轮蜗杆及蜗轮蜗杆链组合试验;链摆线针轮及摆线针轮链组合试验等26组机械传动方案测试搭接试验。2.3整个试验台的总布置设计通过上面介绍的实验台的组成示意图,综合各种传动系统方案的方便性,本次设计选用下面的布置方案:动力从电机输出,然后经过联轴器,再经过传动系统中的增减速机构,增减速机构的输出端接一个联轴器,联轴器接离合器试验样品。对
41、于传动系统中的增减速机构,可以根据前面所列举的实验方案以及分析各种传动的优缺点来选择本次毕业设计所用的传动系统的结构。链传动虽然具有传动效率高,结构较为紧凑。但是,由于链传动一般用于高温,转速较低的情况,而且在两根平行轴间只能用于同向回转的传动,运转时不能保持恒定的瞬时传动比,磨损后易发生跳齿,效率较低,但是带传动结构简单,具有良好的挠性,具有过载打滑保护作用,可实现的中心距较大。对于减速器,齿轮传动效率高,结构紧凑,工作可靠,寿命长,传动比稳定等优点。而蜗轮传动比大,结构也紧凑,冲击载荷小,传动平稳,噪声低,具有自锁性。但是蜗杆传动由于摩擦与磨损严重,通常都用有色金属制造蜗轮。这样制造的成本
42、就很高。为了使结构简单,设计的实验台空间小。采用齿轮传动的减速器为本次设计的传动减速机构。综合以上分析,选择以下所示的图2.7做为本次设计的整个试验台的传动方案简图14。1电机;2皮带轮;3传动皮带;4被试件;5破坏舱图2.7 整个试验台的传动方案图2.4 本章小结本章确定了机械传动试验台的实验原理,分析了试验台的组成和分类,并根据离合器试验的要求,确定出离合器压盘及盖总成高速破坏试验台的传动方案和总体布置方案。 第3章 试验台的设计计算3.1试验台技术参数及设计流程1. 已知条件设计参数:传动系的输出转速为20000r/min工作条件:载荷冲击小2. 机械传动系统方案设计(见图3.1所示)电
43、机选择试验台机构设计变速机构传动装置参数计算与分析图3.1 试验台传动系统方案3.2 试验台结构设计3.2.1 电动机的选择根据本次毕业设计的要求,传动系的输出转速为20000r/min,参考车辆发动机的基本参数,而且本次设计所用的电机是用于做实验台用的,所以根据需要,选择Y系列(IP44)三相异步电机系列中的Y250M-2型号的电机,该电机的参数为:功率:p55kw转速:n3000r/min根据转速,功率和扭矩的关系,可以计算出电机的输出扭矩为: (3.1)式中:扭矩,单位为N.m; P 功率,单位为kw; 电机的转速由于从电机输出的功率至传动系统还要经过联轴器,转速器等机械传动机构。功率经
44、过这些机构时会有功率的损失。假设经过联轴器的效率假定为99,经过减速器中每一级传动的效率为97。则本次设计的综合试验台的减速器的输入扭矩为: (3.2)3.2.2 第一级联轴器的设计由于本次设计选的是Y250M-2型号的电机,根据电机的基本结构尺寸,得知电机输出轴的轴径为65mm,输出轴的伸出长度为142mm。联合联轴器的参数和结构尺寸,选择第一级联轴器的型号为GY8。3.2.3 总传动比的设计本次设计采用的传动系统中只有减速器用来增速,因此设计要求的离合器样品的转速即为减速器的输出转速。因此,整个减速器的输出转速为20000r/min。所以,整个减速器的总传动比为: (3.3)根据各种传动系
45、统的传动比的要求,可以选定第一级齿轮传动的传动比为2.6,选定第二级齿轮传动的传动比为2.6。3.2.4减速器齿轮的设计计算3.2.4.1第一级传动齿轮的设计计算输入功率P55kw,大齿轮转速3000r/min,小齿轮转速7800r/min齿数比u2.6工作寿命15年(设每年工作300天,每天工作8小时)1.选定齿轮类型、精度等级、材料及齿数1)按传动方案,选用直齿圆柱齿轮传动。2)通用减速器为一般工作机器,查表选用7级精度。3)材料选择。小齿轮均选择40Cr(调质)硬度280HBS,大齿轮材料为45钢(调质)硬度240HBS。两者相差40HBS。4)选小齿轮齿数19,大齿轮数u19×
46、;2.649.4,取50。2.按齿面接触强度设计由设计计算公式进行试算,即 (3.4)式中:小齿轮分度圆直径;载荷系数;小齿轮传递的转矩;齿宽系数;材料的弹性影响系数;接触疲劳强度极限。1.确定公式内各计算数值(1)试选载荷系数1.3;(2)计算小齿轮传递的转矩 (3.5)(3)支承相对齿轮作堆成分布,选取齿宽系数1;(4)大小齿轮均为锻钢材料,选取材料的弹性影响系数189.8MPa1/2;(5)按齿面硬度查得小齿轮的接触疲劳强度极限,大齿轮的接触疲劳强度极限;(6)计算应力循环次数 (3.6) (3.7)式中: 齿轮每转一圈时,同一齿面啮合次数; 工作寿命(7)查表得接触疲劳寿命系数;(8)
47、计算接触疲劳许用应力取失效概率为1%,安全系数S1,按许用应力公式得 (3.8) (3.9)2.计算(1)试算小齿轮分度圆直径,代入中较小值 (3.10)(3)计算齿宽b (3.11)(4)计算齿宽与齿高之比b/h模数 mm 取4mm (3.12) (3.13) (3.14)齿高 (3.15) (3.16)校核齿根弯曲疲劳强度(1)由表机械设计基础表5-6查的齿形系数和应力修正系数为:,。(2)小齿轮的弯曲疲劳极限;大齿轮的弯曲疲劳强度极限;(3)查表得弯曲疲劳寿命系数,;(4)计算弯曲疲劳许用应力取弯曲疲劳安全系数S1.4,得 (3.17) (3.18(5)计算圆周力 (3.19)(6)计算
48、轮齿齿根弯曲应力(3.20) (3.21)因此齿根弯曲强度足够。4.几何尺寸计算 图3.2 一级传动齿轮的结构示意图1)计算分度圆直径 (3.22) (3.23)2)计算中心距 (3.24)3)计算齿轮宽度 (3. 25)取 ,3.2.4.2第二级传动齿轮的设计计算第二级传动的输入功率,主动齿轮(大齿轮)转速7800r/min,齿数比u2.6假设工作寿命15年(设每年工作300天,每天工作8小时)1. 选定齿轮类型、精度等级、材料及齿数1)按传动方案,选用直齿圆柱齿轮传动。2)通用变速器为一般工作机器,查表选用7级精度。3)材料选择。小齿轮选择40Cr(调质)硬度280HBS,大齿轮材料为45
49、钢(调质)硬度240HBS。两者相差40HBS。4)选小齿轮齿数19,大齿轮数×u19×2.649.4,取50。因此,第二级齿轮传动的实际传动比为:2. 按齿面接触强度设计由设计计算公式进行试算, (3. 26) 式中: 小齿轮分度圆直径; 载荷系数; 小齿轮传递的转矩; 齿宽系数; 材料的弹性影响系数; 接触疲劳强度极限。1)确定公式内各计算数值(1)试选载荷系数;(2)计算小齿轮传递的转矩: (3. 27)(3)支承相对齿轮作对称分布,选取齿宽系数1;(4)大小齿轮均为锻钢材料,选取材料的弹性影响系数189.8MPa1/2标准齿轮=2.5;(5)按齿面硬度查得小齿轮的接
50、触疲劳强度极限,大齿轮的接触疲劳强度极限;(6)计算应力循环次数 (3. 28) (3. 29)式中:齿轮每转一圈时,同一齿面啮合次数; 工作寿命(7)查表得接触疲劳寿命系数;(8)计算接触疲劳许用应力取失效概率为1%,安全系数S1,按许用应力公式得 (3. 30) (3. 31)2)计算(1)试算小齿轮分度圆直径,代入中较小值 (3. 32) (3)计算齿宽b (3. 33)(4)计算齿宽与齿高之比b/h模数 取2.5mm (3. 34) (3.35) (3.36)齿高 (3. 37) (3. 38)校核齿根弯曲疲劳强度(1)由表机械设计基础表5-6查的齿形系数和应力修正系数为:,。(2)小
51、齿轮的弯曲疲劳极限;大齿轮的弯曲疲劳强度极限;(3)查表得弯曲疲劳寿命系数,;(4)计算弯曲疲劳许用应力取弯曲疲劳安全系数S1.4,得 (3.39) (3.40)(5)计算圆周力 (3.41)(6)计算轮齿齿根弯曲应力(3.42) (3.43)因此齿根弯曲强度足够。4. 几何尺寸计算 图3.3 第二级传动齿轮的结构示意图1) 计算分度圆直径 (3. 44) (3. 45)2) 计算中心距 (3. 46)3) 计算齿轮宽度 (3. 47)取 47.5mm,=47.5mm3.2.5变速器输入轴的设计与校核1)输入轴的设计初步确定轴的最小直径,选取轴的材料为45钢,调质处理。查得A0=112,于是得
52、: (3.48)根据选用的第一级联轴器的尺寸,设计与联轴器配合的轴段的直径为d1=65mm。如图3.4所示,根据轴向定位要求需要设计必要的轴肩,从左至右,各个轴段的直径分别为: 图3.4 输入轴的结构示意图2)输入轴受力分析与计算变速器输入轴的受力示意图如图3.5所示。图3.5 变速器输入轴受力示意图图中:FNH1和FNH2分别为轴承1和轴承2对轴的水平径向力; FNV1和FNV2分别为轴承1和轴承2对轴的垂直径向力; Ft为大齿轮受到的圆周力; Fr为大齿轮受到的径向力; T1为输入转矩 (3.49)(3.50)由式得:FNH1=1189.1N FNH2=560.9N同理由式可得:FNV1=
53、432.8N FNV2=204.1N变速器输入轴的载荷分析图如图3.6所示:图3.6 输入轴载荷分析图 (3.51) (3.52) (3.53)由图3.2可知所受弯矩最大处为安装齿轮的轴段的中心截面,所以对其进行强度校核,该段处轴径为77mm。3)强度校核按弯扭合成应力校核,弯扭合成强度条件为: (3.54)式中:为轴的计算应力,单位为Mpa 轴所受的弯矩,单位 W轴的抗弯截面系数,单位为mm 对称循环变应力时轴的许用弯曲应力查得=60Mpa代入公式(3.53),得: (3.55)由式(3.54)知该截面强度满足要求。2.输入轴上键的校核根据设计方案,选用参数为的平键。轴、键和轮毂的材料都是钢
54、,查得许用挤压应力,取其平均值。键的工作长度: (3.56)键和轮毂键槽的接触高度:所以有: (3.57)由式(3.55)知键的强度满足要求。3.中间轴的校核图3.7 中间轴的结构示意图1)中间轴的受力分析与计算变速器中间轴的受力示意图如图3.8所示图3.8 中间轴受力示意图图中:FNH1和FNH2分别为左端轴承1和右端轴承2对轴的水平径向力; FNV1和FNV2分别为左端轴承1和右端轴承2对轴的垂直径向力;Ft1为小齿轮受到的圆周力; Fr1为小齿轮受到的径向力;Ft2为大齿轮受到的圆周力; Fr2为大齿轮受到的径向力;由于齿轮间传动效率为97%,所以中间轴的输入转矩为: (3.58)所以有
55、: (3.59) (3.60) (3.61) (3.62)由式得:同理,由得:中间轴的载荷分析图如图3.9所示:BAMVMV2MV1Fr2Fr1FNV2FNV1MHMH2MH1FNH2Ft2Ft1FNH1图3.9 中间轴载荷分析计算得: (3.63) (3.64)因为,所以截面A为危险截面。对其进行强度校核,该处轴径为35mm。2)中间轴的强度校核截面A处受的扭矩为,根据公式(3.54)可得: (3.65)查得,所以强度符合要求。3.2.6 第二级联轴器的设计由于本第二级联轴器是与变速器输出轴联接的,而变速器的第二级输出轴的轴径为22mm,输出轴的伸出长度为52mm。联合联轴器的参数和结构尺寸
56、,选择第二级联轴器的型号为GYS2。3.2.7 驱动轴的设计初步确定轴的最小直径,选取轴的材料为45钢,调质处理。查得A0=112,于是得: (3.66)根据选用的第二级联轴器的尺寸,设计与联轴器配合的轴段的直径为d1=22mm。如图3-10所示,根据轴向定位要求需要设计必要的轴肩,从左至右,各个轴段的直径分别为:图3.10 驱动轴的结构示意图 3.3 本章小结 本章先对试验台的零部件进行了设计,对电机、联轴器的选择,传动比的分配,并对变速器中齿轮、轴、键的进行设计计算和强度校核,完成了试验台装配零件设计。第4章 传感器的选用4.1转速传感器起步辅助系统需要对汽车速度小于lkmh低速检测,并且
57、还需要检测车轮的旋转方向,而一般的ABS车用轮速传感器不能够满足上述要求,因此,需要选用一种既能测低速又判断转向的转速传感器代替原有转速传感器。本设计选用AD22157转速传感器,AD22157是AD公司生产的一种基于霍尔效应的传感器,它是一种混合信号磁场转换器,具有很大的测速范围(02500Hz)和较宽的操作温度范围(-40150°C)。它可在较大的车速范围内对汽车铁磁性目标轮进行转速与转动方向的测量。AD22157轮速传感器结构框图(图2.6):图2.6 AD22157的结构框图AD22157转速传感器的工作原理:AD22157转速传感器实际上是一个二线制电流调制传送器,它可根据磁场在空间的差模变化产生相应的电流脉冲。在其应用于转速传感器时,它所探测到的磁场是由一个放置于其后面的永久磁铁和位于传感器前端、目标轮上的铁制凹槽标记相互作用产生的。在这种条件下,传感器必须抵消恒定的磁场偏置,并放大差模调制磁场,从而准确判断目标轮的转动情况。AD22157转速传感器采用集成在硅衬底上的霍尔片结构来对磁场进行空间差模测量,从而抵消了偏置磁场的影响。此霍尔结构由直线排列的三组霍尔单元构成,可用于一些不窄于5mm的锯齿或凹槽输出对应的正交信号。每组霍尔单元都由4个独立的、直径为200 um
- 温馨提示:
1: 本站所有资源如无特殊说明,都需要本地电脑安装OFFICE2007和PDF阅读器。图纸软件为CAD,CAXA,PROE,UG,SolidWorks等.压缩文件请下载最新的WinRAR软件解压。
2: 本站的文档不包含任何第三方提供的附件图纸等,如果需要附件,请联系上传者。文件的所有权益归上传用户所有。
3.本站RAR压缩包中若带图纸,网页内容里面会有图纸预览,若没有图纸预览就没有图纸。
4. 未经权益所有人同意不得将文件中的内容挪作商业或盈利用途。
5. 装配图网仅提供信息存储空间,仅对用户上传内容的表现方式做保护处理,对用户上传分享的文档内容本身不做任何修改或编辑,并不能对任何下载内容负责。
6. 下载文件中如有侵权或不适当内容,请与我们联系,我们立即纠正。
7. 本站不保证下载资源的准确性、安全性和完整性, 同时也不承担用户因使用这些下载资源对自己和他人造成任何形式的伤害或损失。