半自动钻床设计和运动学分析设计论文(很全)
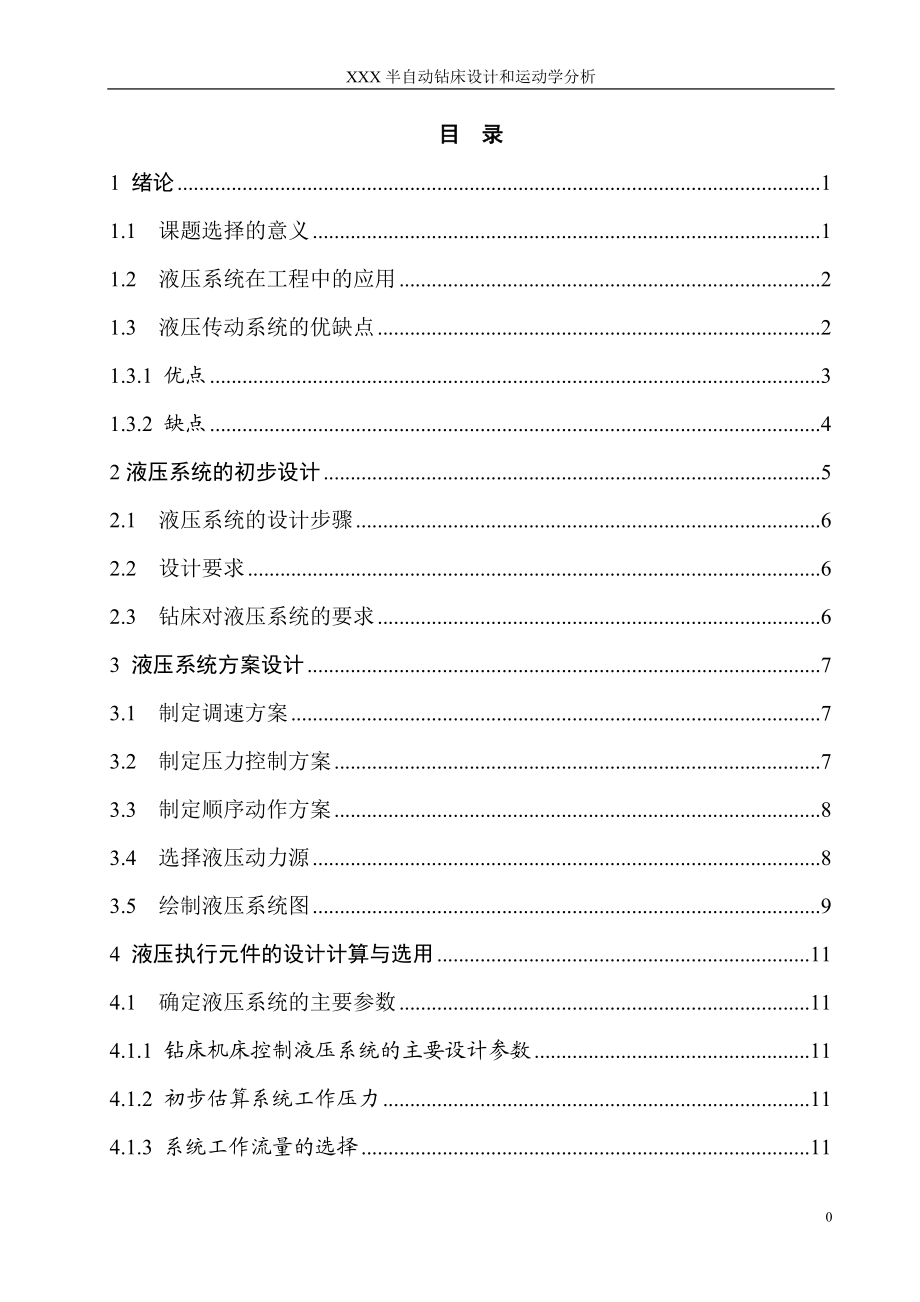


《半自动钻床设计和运动学分析设计论文(很全)》由会员分享,可在线阅读,更多相关《半自动钻床设计和运动学分析设计论文(很全)(66页珍藏版)》请在装配图网上搜索。
1、目 录1 绪论11.1 课题选择的意义11.2 液压系统在工程中的应用21.3 液压传动系统的优缺点21.3.1 优点31.3.2 缺点42液压系统的初步设计52.1 液压系统的设计步骤62.2 设计要求62.3 钻床对液压系统的要求63 液压系统方案设计73.1 制定调速方案73.2 制定压力控制方案73.3 制定顺序动作方案83.4 选择液压动力源83.5 绘制液压系统图94 液压执行元件的设计计算与选用114.1 确定液压系统的主要参数114.1.1 钻床机床控制液压系统的主要设计参数114.1.2 初步估算系统工作压力114.1.3 系统工作流量的选择114.2 管道尺寸的确定114.
2、3 各种阀类的选择124.3.1 换向阀的选取124.3.2 单向阀的选择124.3.3 减压阀的选择134.3.4 压力继电器的选择134.4 液压泵的选择134.5 液压泵驱动电机的选择144.6 液压马达的选取154.7 确定油箱的有效容积154.8 液压缸的载荷力计算155 系统性能验算175.1 沿程压力损失175.2 局部压力损失176 系统发热量的计算196.1 计算发热功率196.2 计算散热功率197 夹具设计217.1 概述217.2 夹紧机构设计227.2.1 定位方案227.2.2 夹紧机构237.2.3 导向装置237.2.4 夹具体238 运动学分析258.1 概述
3、258.2 夹具体运动学分析278.3 半自动化钻床整机工作运动学分析309 结论36参考文献37致谢38附录A139附录B147含有cad源图、中英文翻译等全套资料 如有需要 加我qq:1471368723摘要随着先进制造技术的发展和进步,半自动化加工已成为机加工过程中的一种主流技术。这一技术的运用提高了机加工过程中工作效率和加工精度。半自动化多工位钻床就是提高钻削加工精度和效率的一种很好的机加工工具。本文对半自动化多工位钻床进行了设计,采用了普通车床设计的步骤和方法,综合考虑半自动化机床的特点。从切削力入手确定主轴及电机,到整个机床的结构设计和机床的控制。最后到对机床初始化程序设计。本文所
4、做的工作:1.完成半自动化多工位钻床的资料收集与国、内外现状的调查比较,提出较为可行的方案;2.完成机床的机械结构设计计算与电气控制系统设计,初步完成控制系统的软硬件设计;提交论文及机械系统的装配与关键零部件的相应图纸及半自动化系统的硬件图,同时提交电子文档; 3.编写设计计算说明书。完成了一台经济型的半自动化机床的设计。关键词:半自动化技术、钻床、钻削、计算机控制、单片机AbstractWith the manufacturing development, numerical control manufacturing has become one of the major advanced
5、 technologies. efficiency and accuracy has been improved in application of the technology. Numerical control auto-drilling machine is a kind of the new machine tools that can improve the machining accuracy and efficiency. The paner has designed for Numerical control auto-drilling machine, using desi
6、gn method of the ordinary lathe, and considering the characteristic of the numerical control machine tools synthetically. cutting force has been calculated, the structural and the control system has been designed. Finally, the software routine has been explored.This paner has finished major works:1.
7、 Completed a investigation of internal and external of current situation for numerical control multistage-drilling machine, and compared it, put forward a feasible scheme;2. Completed the mechanical structural design an calculated and designed the electric control system, and finished the software a
8、nd hardware of the control system tentatively; Submit thesis and the assembly of mechanical system and hardware picture of key spare part and drawing of numerical control system, submit the electronic file at the same time;3. Write the specification of designing and calculating, has designed an econ
9、omy numerical control machine tool. Keywords: numerical control machining、drilling machine、drilling、computer control、single chip computer1 绪论1.1 课题选择的意义液压传动与其他类型的传动相比较具有许多突出的优点,液压传动技术在工程中,特别是在高效率的自动化和半自动化机械中,应用十分广泛。本文主要利用钻床液压系统设计来实现钻床的半自动化控制是工业中经常用到的一种控制方式,它采用液压完成传递能量的过程。因为液压传动控制方式的灵活性和便捷性,液压控制在工业上受
10、到广泛的重视。液压传动是研究以有压流体为能源介质,来实现各种机械和自动控制的学科。液压传动利用这种元件来组成所需要的各种控制回路,再由若干回路有机组合成为完成一定控制功能的传动系统来完成能量的传递、转换和控制。图1-1 液压传动能量传递过程Fig.1-1 hydraulic transmission energy transfer process从原理上来说,液压传动所基于的最基本的原理就是帕斯卡原理,就是说,液体各处的压强是一致的,这样,在平衡的系统中,比较小的活塞上面施加的压力比较小,而大的活塞上施加的压力也比较大,这样能够保持液体的静止。所以通过液体的传递,可以得到不同端上的不同的压力,
11、这样就可以达到一个变换的目的。我们所常见到的液压千斤顶就是利用了这个原理来达到力的传递2。 图1-2 液压传动基本原理 Fig.1-2 hydraulic transmission basic principle液压作为一个广泛应用的技术,在未来更是有广阔的前景。随着计算机的深入发展,液压控制系统可以和智能控制的技术、计算机控制的技术等技术结合起来,这样就能够更多的场合中发挥作用,也可以更加精巧的、更加灵活地完成预期的控制任务。1.2 液压系统在工程中的应用液压传动相对于机械传动来说,是一门新技术。自1795年制成第一台水压机起,液压技术就进入了工程领域,1906年开始应用于国防战备武器。第二
12、次世界大战期间,由于军事工业迫切需要反应快和精度高的自动控制系统,因而出现了液压伺服系统。20世纪60年代以后,由于原子能、空间技术、大型船舰及计算机技术的发展,不断地对液压技术提出新的要求,液压技术相应也得到了很大发展,渗透到国民经济的各个领域中。在工程机械、冶金、军工、农机、汽车、轻纺、船舶、石油、航空、和机床工业中,液压技术得到普遍应用。近年来液压技术已广泛应用于智能机器人、海洋开发、宇宙航行、地震预测及各种电液伺服系统,使液压技术的应用提高到一个崭新的高度。目前,液压技术正向高压、高速、大功率、高效率、低噪声和高度集成话等方向发展;同时,减小元件的重量和体积,提高元件寿命,研制新的传动
13、介质以及液压传动系统的计算机辅助设计、计算机仿真和优化设计、微机控制等工作,也日益取得显著成果。 解放前,我国经济落后,液压工业完全是空白。解放后,我国经济获得迅速发展,液压工业也和其它工业一样,发展很快。20世纪50年代就开始生产各种通用液压元件。当前,我国已生产出许多新型和自行设计的系列产品,如插装式锥阀、电液比例阀、电液伺服阀、电液脉冲马达以及其它新型液压元件等。但由于过去基础薄弱,所生产的液压元件,在品种与质量等方面和国外先进水平相比,还存在一定差距,我国液压技术也将获得进一步发展,它在各个工业技术的发展,可以预见,液压技术也将获得进一步发展,它在各个工业部门中的用应,也将会越来越广泛
14、。现代机械一般多是机械、电气、液压三者紧密联系,结合的一个综合体。液压传动与机械传动、电气传动并列为三大传统形式,液压传动系统的设计在现代机械的设计工作中占有重要的地位。1.3 液压传动系统的优缺点液压传动中所需要的元件主要有动力元件、执行元件、控制元件、辅助元件等。其中液压动力元件是为液压系统产生动力的部件,主要包括各种液压泵。液压泵依靠容积变化原理来工作,所以一般也称为容积液压泵。齿轮泵是最常见的一种液压泵,它通过两个啮合的齿轮的转动使得液体进行运动。其他的液压泵还有叶片泵、柱塞泵,在选择液压泵的时候主要需要注意的问题包括消耗的能量、效率、降低噪音。 除了上述的元件以外,液压控制系统还需要
15、液压辅助元件。这些元件包括管路和管接头、油箱、过滤器、蓄能器和密封装置。通过以上的各个器件,我们就能够建设出一个液压回路。所谓液压回路就是通过各种液压器件构成的相应的控制回路。根据不同的控制目标,我们能够设计不同的回路,比如压力控制回路、速度控制回路、多缸工作控制回路等。 液压传动的应用性是很强的,比如装卸堆码机液压系统,它作为一种仓储机械,在现代化的仓库里利用它实现纺织品包、油桶、木桶等货物的装卸机械化工作。也可以应用在万能外圆磨床液压系统等生产实践中。这些系统的特点是功率比较大,生产的效率比较高,平稳性比较好。1.3.1 优点1) 传动平稳 在液压传动装置中,由于油液的压缩量非常小,在通常
16、压力下可以认为不可压缩,依靠油液的连续流动进行传动。油液有吸振能力,在油路中还可以设置液压缓冲装置,故不像机械机构因加工和装配误差会引起振动扣撞击,使传动十分平稳,便于实现频繁的换向;因此它广泛地应用在要求传动平稳的机械上,例如磨床几乎全都采用了液压传动。 2) 质量轻体积小 液压传动与机械、电力等传动方式相比,在输出同样功率的条件下,体积和质量可以减少很多,因此惯性小、动作灵敏;这对液压仿形、液压自动控制和要求减轻质量的机器来说,是特别重要的。例如我国生产的1m3挖掘机在采用液压传动后,比采用机械传动时的质量减轻了1t。 3) 承载能力大 液压传动易于获得很大的力和转矩,因此广泛用于压制机、
17、隧道掘进机、万吨轮船操舵机和万吨水压机等。 4) 容易实现无级调速 在液压传动中,调节液体的流量就可实现无级凋速,并且调速范围很大,可达2000:1,很容易获得极低的速度。 5) 易于实现过载保护 液压系统中采取了很多安全保护措施,能够自动防止过载,避免发生事故。 6) 液压元件能够自动润滑 由于采用液压油作为工作介质,使液压传动装置能自动润滑,因此元件的使用寿命较长。 7) 容易实现复杂的动作 采用液压传动能获得各种复杂的机械动作,如仿形车床的液压仿形刀架、数控铣床的液压工作台,可加工出不规则形状的零件 8) 简化机构 采用液压传动可大大地简化机械结构,从而减少了机械零部件数目。 9) 便于
18、实现自动化 液压系统中,液体的压力、流量和方向是非常容易控制的,再加上电气装置的配合,很容易实现复杂的自动工作循环。目前,液压传动在组合机床和自动线上应用得很普遍。 10) 便于实现“三化” 液压元件易于实现系列比、标准化和通用化也易于设计和组织专业性大批量生产,从而可提高生产率、提高产品质量、降低成本3。1.3.2 缺点1) 液压元件制造精度要求高 由于元件的技术要求高和装配比较困难,使用维护比较严格。2) 实现定比传动困难 液压传动是以液压油为工作介质,在相对运动表面间不可避免的要有泄漏,同时油液也不是绝对不可压缩的。因此不宜应用在在传动比要求严格的场合,例如螺纹和齿轮加工机床的传动系统。
19、3) 油液受温度的影响 由于油的粘度随温度的改变而改变,故不宜在高温或低温的环境下工作。4) 不适宜远距离输送动力 由于采用油管传输压力油,压力损失较大,故不宜远距离输送动力。5) 油液中混入空气易影响工作性能 油液中混入空气后,容易引起爬行、振动和噪声,使系统的工作性能受到影响。6) 油液容易污染 油液污染后,会影响系统工作的可靠性。7) 发生故障不易检查和排除。2 液压系统的初步设计液压系统是机械伺服装置中的经典结构。即使在机电类元件获得长足进步的今天,液压系统仍以其高功率/重量比,响应快,低速特性好等特点而在不少系统当中扮演举足轻重的角色。在现代电子和控制技术推动下涌现出了一些原理新颖,
20、物美价廉的液压元器件,给这一传统的技术带来了新的生机。液压传动系统是液压机械的一个组成部分,液压传动系统的设计要同主机的总体设计同时进行。着手设计时,必须从实际情况出发,有机地结合各种传动形式,充分发挥液压传动的优点,力求设计出结构简单、工作可靠、成本低、效率高、操作简单、维修方便的液压传动系统。2.1 液压系统的设计步骤1) 明确设计方案;2) 确定液压执行元件的形式;3) 进行工况分析,确定系统的主要参数;4) 制定基本方案,拟定液压系统原理图;5) 选择液压元件;6) 液压系统的性能验算;7) 绘制工作图,编制技术文件4。2.2 设计要求设计要求是进行每项工程设计的依据,在制定基本方案并
21、进一步着手液压系统各部分设计之前,必须把设计要求以及与该设计内容有关的其他方面了解清楚。目前,大部分的钻床机床的卡盘,钻头等都是由液压来控制的。而他们的基本工作原理都是:通过液压系统回路,来实现控制卡盘的卡紧,松开及对不同的零件类型来实现正钻,反钻的控制。而它们的工作循环大都为:快进卡紧保压钻孔松开其中快进和卡紧并不是通过高低压的换向来控制,而是通过负载的增加来实现的,而保压过程是通过换向阀来实现的,而它是保证卡紧力在突然断电等事故发生时保护设备和人员安全的必要设备。2.3 钻床对液压系统的要求1) 卡盘卡紧,松开时动作要求平稳,在进行动做换向时不应有冲击;2) 当卡盘卡紧后,液压缸机构应具有
22、足够的保压能力,以防止因系统内泻而造成工件的脱落或当数控机床在加工零件是因为卡紧力不够而使工件轴向不垂直,加工零件尺寸出现偏差。3) 系统中要有减压装置,其作用为当卡盘接触工件时,系统压力忽然升高,为防止因压力过大而造成加上工件的事故发生,该系统在工作过程中因为恒压。4) 钻头工作时应没有冲击,爬行等不良现象。所以对系统的密封应有较高的标准。5) 为保证安全生产,避免忽然断电以及电机损坏等突发事件的发生,系统中应有连锁保压装置。3 液压系统方案设计3.1 制定调速方案液压执行元件确定之后,其运动方向和运动速度的控制是拟定液压回路的核心问题。方向控制用换向阀或逻辑控制单元来实现。对于一般中小流量
23、的液压系统,大多通过换向阀的有机组合实现所要求的动作。对高压大流量的液压系统,现多采用插装阀与先导控制阀的逻辑组合来实现。 速度控制通过改变液压执行元件输入或输出的流量或者利用密封空间的容积变化来实现。相应的调整方式有节流调速、容积调速以及二者的结合容积节流调速。节流调速一般采用定量泵供油,用流量控制阀改变输入或输出液压执行元件的流量来调节速度。此种调速方式结构简单,由于这种系统必须用闪流阀,故效率低,发热量大,多用于功率不大的场合。容积调速是靠改变液压泵或液压马达的排量来达到调速的目的。其优点是没有溢流损失和节流损失,效率较高。但为了散热和补充泄漏,需要有辅助泵。此种调速方式适用于功率大、运
24、动速度高的液压系统。容积节流调速一般是用变量泵供油,用流量控制阀调节输入或输出液压执行元件的流量,并使其供油量与需油量相适应。此种调速回路效率也较高,速度稳定性较好,但其结构比较复杂。节流调速又分别有进油节流、回油节流和旁路节流三种形式。进油节流起动冲击较小,回油节流常用于有负载荷的场合,旁路节流多用于高速。 调速回路一经确定,回路的循环形式也就随之确定了。 节流调速一般采用开式循环形式。在开式系统中,液压泵从油箱吸油,压力油流经系统释放能量后,再排回油箱。开式回路结构简单,散热性好,但油箱体积大,容易混入空气。 容积调速大多采用闭式循环形式。闭式系统中,液压泵的吸油口直接与执行元件的排油口相
25、通,形成一个封闭的循环回路。其结构紧凑,但散热条件差5。3.2 制定压力控制方案液压执行元件工作时,要求系统保持一定的工作压力或在一定压力范围内工作,也有的需要多级或无级调节压力,一般在节流调速系统中,通常由定量泵供油,用溢流阀调节所需压力,并保持恒定。在容积调速系统中,用变量泵供油,用安全阀起安全保护作用。 在有些液压系统中,有时需要流量不大的高压油,这时可考虑用增压回路得到高压,而不用单设高压泵。液压执行元件在工作循环中,某段时间不需要供油,而又不便停泵的情况下,需考虑选择卸荷回路。 在系统的某个局部,工作压力需低于主油源压力时,要考虑采用减压回路来获得所需的工作压力。3.3 制定顺序动作
26、方案主机各执行机构的顺序动作,根据设备类型不同,有的按固定程序运行,有的则是随机的或人为的。工程机械的操纵机构多为手动,一般用手动的多路换向阀控制。加工机械的各执行机构的顺序动作多采用行程控制,当工作部件移动到一定位置时,通过电气行程开关发出电信号给电磁铁推动电磁阀或直接压下行程阀来控制接续的动作。行程开关安装比较方便,而用行程阀需连接相应的油路,因此只适用于管路联接比较方便的场合。 另外还有时间控制、压力控制等。例如液压泵无载启动,经过一段时间,当泵正常运转后,延时继电器发出电信号使卸荷阀关闭,建立起正常的工作压力。压力控制多用在带有液压夹具的机床、挤压机压力机等场合。当某一执行元件完成预定
27、动作时,回路中的压力达到一定的数值,通过压力继电器发出电信号或打开顺序阀使压力油通过,来启动下一个动作。3.4 选择液压动力源液压系统的工作介质完全由液压源来提供,液压源的核心是液压泵。节流调速系统一般用定量泵供油,在无其他辅助油源的情况下,液压泵的供油量要大于系统的需油量,多余的油经溢流阀流回油箱,溢流阀同时起到控制并稳定油源压力的作用。容积调速系统多数是用变量泵供油,用安全阀限定系统的最高压力。 为节省能源提高效率,液压泵的供油量要尽量与系统所需流量相匹配。对在工作循环各阶段中系统所需油量相差较大的情况,一般采用多泵供油或变量泵供油。对长时间所需流量较小的情况,可增设蓄能器做辅助油源。油液
28、的净化装置是液压源中不可缺少的。一般泵的入口要装有粗过滤器,进入系统的油液根据被保护元件的要求,通过相应的精过滤器再次过滤。为防止系统中杂质流回油箱,可在回油路上设置磁性过滤器或其他型式的过滤器。根据液压设备所处环境及对温升的要求,还要考虑加热、冷却等措施6。3.5 绘制液压系统图根据上述分析,可以基本拟订本次所设计的数控机床液压控制系统的原理图及电磁铁动作表:表3-1 电磁铁动作Tab.3-1 electro-magnet movementYV1YV2YV3YV4缸进给+-缸返回-+马达正转+-马达反转-+图3-1 液压原理图Fig.3-1 hydraulic schematic diagr
29、am整机的液压系统图由拟定好的控制回路及液压源组合而成。各回路相互组合时要去掉重复多余的元件,力求系统结构简单。注意各元件间的联锁关系,避免误动作发生。要尽量减少能量损失环节。提高系统的工作效率7。 为便于液压系统的维护和监测,在系统中的主要路段要装设必要的检测元件(如压力表、温度计等)。 大型设备的关键部位,要附设备用件,以便意外事件发生时能迅速更换,保证主要连续工作。 各液压元件尽量采用国产标准件,在图中要按国家标准规定的液压元件职能符号的常态位置绘制。对于自行设计的非标准元件可用结构原理图绘制。 系统图中应注明各液压执行元件的名称和动作,注明各液压元件的序号以及各电磁铁的代号,并附有电磁
30、铁、行程阀及其他控制元件的动作表。 4 液压执行元件的设计计算与选用4.1 确定液压系统的主要参数液压系统的主要参数就是压力和流量,他们是设计液压系统,选择液压元件的主要依据。压力决定与外载荷。流量取决于液压执行元件的运动速度和结构尺寸。 4.1.1 钻床机床控制液压系统的主要设计参数系统工作压力:2.5-3Mpa系统流量 16.7L/Min马达工作压力 1.5Mpa马达转数范围 100-2000r/min液压油缸工作压力 1Mpa4.1.2 初步估算系统工作压力此钻床液压控制系统,压力最大时是在马达全速运转时,此时,油压是由泵提供的,其它工况时,载荷都没有此时大,所以系统的工作压力暂定为此时
31、的工作压力1.5Mpa.而液压系统的最大工作压力应按下式计算: = + (4-1)式中 系统最大工作压力液压缸或液压马达最大工作压力从液压泵到液压马达或液压缸之间总的管路损失,可按经验数据选取:管路简单,流速不大的取。也可选取高于0.5Mpa的压力。由本设计系统求得:该系统的最大工作压力取。4.1.3 系统工作流量的选择由于在工况中已经给出系统的最大流量所以在这里就不对系统的最大流量进行计算。用工况中给出的系统最大流量: 。4.2 管道尺寸的确定 (4-2)式中 系统流量V系统流速表4-1 流速推荐值Tab.4-1 speed of flow recommendation value管道推荐流
32、速(m/s)液压泵吸油管路0.51.5液压系统压油管路36液压系统回油管路1.52.6由上式及相关资料可求得下表:表4-2 各油管内外径实取值Tab.4-2 various drill tubings outer diameter solid value管路名称流量流速内径实取外径吸油管16.7L/min1m/s18.825mm20mm28mm压油管16.7L/min4m/s9.41mm10mm14mm回油管16.7L/min2m/s13.31mm14mm18mm4.3 各种阀类的选择根据本系统的设计技术要求,选择一个有电磁换向阀,叠加式双单向节流阀,叠加式压力计电器,叠加式减压阀组成液压回路
33、。实现卡盘的卡紧,松开和退回,钻头的正转反转等动作。阀的规格根据系统的工作压力和工作年限来通过样本的选取决定8。4.3.1 换向阀的选取一般来说,流量在190L/min以上的适宜用二通插装阀;190L/min以下时可采用滑阀式换向阀。70L/min以下时通常用电磁换向阀。控制阀的流量一般要选得比实际通过的流量大一些,必要时也可以有20以内的短时间过流量。根据以上要求,本系统选择的换向阀为电磁换向阀,具体的型号和尺寸由相关厂家的样本中查得。其中电磁换向阀的产品型号为:4WE6E6X/EG24NZ5L/B10。4.3.2 单向阀的选择应选择开启压力小的单向阀,开启压力较大的单向阀可作为背压阀使用。
34、所以,本系统选择叠加式双单向节流阀,具体型号和尺寸可由相关厂家样本中查得。其中叠加式双单向节流阀的型号为:Z2FS6-3-L4X/2Q。4.3.3 减压阀的选择减压阀根据不同的需要,可将液压系统区分成不同的压力油路,例如控制机构的控制油路或其他辅助油路,以使不同的执行机构产生不同的工作力;减压阀也可用作稳定油路工作压力的调节装置,使油路不受压力源压力变化及其他阀门工作时引起压力波动的影响。根据以上要求,本系统选择的减压阀为叠加式P口减压阀,具体型号和尺寸可由相关厂家样本中查得。本系统中的叠加式减压阀型号为:ZDR6DP3-30/2.5YM。4.3.4 压力继电器的选择压力继电器是利用液体压力信
35、号来启动或关闭电器触点的液压电器转换元件。它在油液压力达到其设定压力时,发出电信号,控制电器元件动作,实现泵的加载和卸荷。其设定值通常是比系统正常工作压力高出约0.5Mpa,所以本系统的压力继电器预先调定压力为3.5Mpa。根据以上要求,本系统选择的压力继电器为叠加式压力继电器,具体型号和尺寸可由相关厂家样本中查得9。叠加式压力继电器的型号为:HED40H10/5Z14/2。表4-3 系统中所用到的元件现总结Table.4-3 system uses the part presently summarizes序号名称数量规格1减压阀2ZDR6DP3-30/2.5YM2压力继电器1HED4OH1
36、0/5Z14/23双单向节流阀2Z2FS6-3-L4X/2Q4电磁换向阀24WE6E6X/EG24NZ5L/B105WU型网式过滤器1WU-401806空气滤清器1QUQ1-200.47液位计1YWZ-80T4.4 液压泵的选择1) 确定液压泵的最大工作压力: (4-3)式中 额定压力从液压泵出口到液压缸或液压马达入口之间总的管路损失。的准确计算要待元件选定并会出管路图时才能进行,初算时可按经验数据选取:管路简单,流速不大的,取2) 确定液压泵的流量: (4-4)式中 K泄露系数 一般取1.1-1.3;系统最大流量 发生在马达全速运转时:3) 选择泵的规格 根据以上求得的和值,按系统中拟定的液
37、压泵的形式,从产品样本或手册中选择相应的液压泵。为使液压泵有一定的压力储备,所以选择的泵的额定压力一般要比最大工作压力大。泵取YBX-16限压式变量泵,排量调节为,额定压力6.3Mpa,调节范围,转速,驱动功率为2.6Kw 效率。4.5 液压泵驱动电机的选择液压泵在额定压力和额定流量下工作时,其驱动电机的功率一般可直接从产品样本或技术手册中查得,但其数值在实际中往往偏大。因此,也可以根据具体工况用下述方法计算出来10。整个系统中所需功率最大的工况是发生在马达最大转速的情况下。 (4-5)式中 泵的最大工作压力泵的流量泵的总效率P=综上所述,由厂家样本中查出本系统所选择的电机型号为Y90L-4B
38、35 额定功率1.5kw 转速1440r/min4.6 液压马达的选取由系统所给定的马达排量为16.3ml/r,正常工作时转矩为,工作压力为1.5Mpa。选用YM-A19B,理论排量 19ml/r额定压力6.0Mpa,调速范围100-2000r/min,最高转矩 10-80Nm,机械效率大于11。马达的载荷转矩 (4-6)取马达的机械效率0.95,则理论转矩为 (4-7)4.7 确定油箱的有效容积按公式4-8初步确定油箱的有效容积 (4-8)式中 泵每分钟排出的容积;经验系数 取;取V=100L4.8 液压缸的载荷力计算液压缸尺寸(由系统给出)D=50mm,d=28mm 行程为35mm (4-
39、9)式中 d油缸内经;P油缸压力;进给时 返回时 (4-10)表4-3 液压油缸的载荷力 Tab.4-3 hydraulic ram loading force名称工况活塞上的载荷力卡紧油缸进给1.96KN返回1.35KN5 系统性能验算本系统比较简单,执行元件较少并且动作简单。管路损失很小,故主要验算各元件的压力损失对系统造成的影响12。5.1 沿程压力损失主要是压油管的压力损失,管长0.5m,内径0.01m,流量16.7L/min 选用L-HL 矿物油型液压油,正常运转时的运动粘度V=35.2,油液的密度。油在管中实际的流速为 (5-1) (5-2)油在管路中呈乱流流动状态,其沿程阻力系数
40、为: (5-3) (5-4)5.2 局部压力损失局部压力损失包括通过管路中折管和管接头等处的管路局部压力损失,以及通过控制阀的局部压力损失,其中管路局部压力损失相对来说小得多,故主要计算通过控制阀的局部压力损失。参看系统原理图可知从泵口到执行元件要经过减压阀,节流阀,换向阀各阀的性能如下表5-1所示:表5-1 各阀额定压力损失Tab.5-1 various valves rated pressure loss名称额定流量额定压力损失减压阀30L/min0.21Mpa节流阀80L/min0.315Mpa换向阀80L/min0.35Mpa所以通过各阀的局部压力损失之和为: (5-5)由以上计算结果
41、可求得此系统总的压力损失为:泵的出口压力距泵的额定压力有一定的压力裕度,所以泵的选取是合适的13。6 系统发热量的计算6.1 计算发热功率液压系统的功率损失全部转化为热量。按下式计算其发热功率: (6-1)式中 系统发热功率系统发出总功率系统有用功率对于本系统来说,是整个工作循环中泵的平均输入功率。 (6-2)式中 系统周期;泵的输入功率;第i台泵工作时间;Z泵的台数;泵的总效率;6.2 计算散热功率前面求得有效容积为0.1,按求各边之积: (6-3)图 6-1 油箱示意图Fig 6-1 tank Map选各边均为0.5m。式中 有效散热面积 (6-4)式中 散热功率;散热系数;取=;温差取;
42、油箱散热功率满足系统发热功率的需要14。7夹具设计7.1概述零件在工艺规格制定以后,就要按工艺规格顺序进行加工。加工中除了需要机床,刀具,量具之外,成批生产时还需要用机床夹具。它们是机床和工件之间的连接装置,是将工件进行定位、加紧;将刀具进行导向或对刀,以保证工件和刀具间的相对位置关系的附加装置,使工件相对于机床或刀具获得正确位置。机床夹具的好坏直接影响工件加工表面的位置精度,所以机床夹具设计是装配设计中一项重要的工作,是加工过程中最活跃的因素之一。一一般夹具的组成定位元件起定位作用,保证工件相对夹具的位置,可以用六点定位原理来分析其所受限制的自由度。加紧装置将工件加紧,以保证在加工时保持所限
43、制的自由度。导向元件和对刀装置用来保证刀具相对于夹具的位置。本设计为扩铰孔,需要夹具具有导向作用。连接元件是用来保证夹具和机床工作台之间的相对位置。对于钻床夹具,由于孔加工刀具加工时只是沿轴向进给就可完成,用导向元件就可以保证相对位置,因此在将夹具安装在工作台上时,用导向元件直接对刀具进行定位,不必再用连接元件定位了,所以一般钻床夹具没有连接元件。二夹紧机构的功能保证加工精度;提高生产率;扩大机床的使用范围;减轻工人的劳动强度,保证生产安全。加紧机构应满足的要求保证加工精度;夹具的总体方案应与年生产纲领相适应;安全,方便,减轻劳动强度;排屑顺畅;机床夹具应有良好的强度,刚度和结构工艺性。机构的
44、夹紧过程消除间隙阶段:从原动操作部分开始动作起,到各传动构件之间,以及夹紧元件与被夹紧部件之间完全消除间隙,开始接触为止;加力与变形阶段:夹紧元件被夹紧部位的压力从零开始逐渐增加,同时各传动轴构件也由于受力而发生弹性变形,直到夹紧元件对被夹紧部位的夹紧力达到预定值为止。7.2夹紧机构的设计设计机床的加紧机构前,应明确该部件的工作条件:作用于部件上切削力的大小,方向和作用点的坐标位置;部件的支承情况,即有关导轨以及部件与导轨接触处的各项几何尺寸;部件的重量以及重心的坐标位置。以上工作条件,本设计在机床总体设计与布局情况下已求得,现选择夹紧力作用点,夹紧力作用点选择的原则为:尽可能以最小夹紧力取得
45、防止机床部件滑移,颠覆和回转的最大效果;夹紧点布置在被夹紧零部件上刚度较大的部位,减少夹紧力引起的变形;尽量减少夹紧机构在夹紧、松开机床部件时的位移,保证定位精度。本设计夹紧点选在六个圆周孔的外边缘位置。此处离要加工孔的位置较近,可以用较小的夹紧力达到预期的夹紧效果,且此处刚度较大,受夹紧力所产生的变形较小。夹具的结构如下图:7.2.1定位方案工件以40圆柱结构及下端面为定位基准,采用平面和V型块组合定位方案,在定位平面及V型块与40的外圆柱面上定位,其中平面限制Z方向的移动自由度,V型块限制了X和Y方向上的平移和旋转4个自由度,共限制了5个自由度。定位误差的计算:由于定位基准与工序基准一致,
46、所以基准不重合误差b为0。由于V型块与定位平面存在垂直度误差,经计算最小偏差为0.03mm,最大为0.19mm。7.2.2夹紧机构根据生产纲领的要求,需要大批量生产,为了提高生产效率,故采用液动夹紧方案。具体原理是采用液压缸推动杠杆的一端,使杠杆的另一端压在工件的表面,可根据对液压回路的设计来调整压紧力的大小,其压紧的主要作用是防止工件在钻孔过程中,切削力的作用下产生转动和震动。图 7-1压杆Fig7-1 preaching gune 其夹紧力的计算根据杠杆原理:F1L1=F2L2,F2和F3是用力与反作用力的关系所以F3=F2, 则已知液压力,就可以求出压紧力。L1=76mm,L2=80mm
47、。活塞底面有效面积为256。设液压缸的入口压力为390625Pa。则液压力为100N,压紧力为95N。7.2.3导向装置采用可换钻套(JB/T 8045.2-1999)作为导向装置,孔径为15mm。钻套高度H=(12.5)d,这里取H=36mm,排削间隙h=(0.30.7)d,这里取h=10mm。6.4夹具与机床连接元件在夹具体上的两侧设计座耳,用T形螺栓固定。由于Z525型立式钻床工作台槽宽a=14H11,所以T形螺栓的直径d取12,夹具体两侧座耳槽宽取14。7.2.4夹具体由于被加工零件的孔有同轴度要求,所以定位平面与V型块在安装时垂直度在一点范围内范围内允差0.02mm。 图 7-2 夹
48、具装配体三维效果图 Fig7-2 the picture of the skin 图 7-3 V型块的三维效果图Fig7-3 V type of the three skin 8运动学分析8.1概述建立正确的运动学模型是半自动钻床运动学分析工作的基础。虚拟装配技术是利用计算机工具,而不需产品或者支持过程的物理实现,通过分析、预建模、可视化等进行或者辅助进行装配,根据产品设计的形状特征和精度特性,真实地模拟产品三维装配过程。Pro/E软件中的机构模块Mechanism,能够对设计进行模拟、仿真、校验,如运动仿真显示、运动干涉检验、运动轨迹、位移、速度和加速度计算等。本文利用Pro/E进行了半自动
49、钻床机构的虚拟装配和运动仿真,分析了装配中的干涉情况以及机构运动过程中的位移、速度和加速度情况,为半自动钻床的开发设计提供参考。一机构和运动学位置正反解机构的位置分析是求解机构的驱动输入和动平台之间的位置关系,这是机构运动分析的最基本的任务,也是机构速度、加速度、受力分析、误差分析、工作空间分析、动力学分析和机构综合等的基础。已知机构主动件的位置,求解机构的动平台的位置和姿态位置的分析称正解;若己知动平台的位置和姿态,求解机构驱动输入的位置称为机构位置的反解。同串联构分析相比,并联机构的位置反解容易,正解相当困难。关于正向运动学的解法主要分为两大类:数值法和解析法。由于并联机构结构复杂,位置正
50、解的难度较大,其中一种比较有效的方法是采用数值方法求解一组非线性方程,从而求的与输入对应的动平台的位置和姿态。数值法的优点是它可以应用于任何结构的并联机构,计算方法简单,但是该方法计算速度较慢,不能保证获得全部解,并且最终的结果与初值的选取有关。解析法是通过消元法消去机构约束方程中的未知数,从而获得输入输出方程中仅含一个未知数的多项式,这种方法的优点是可以求解机构中所有可能解并能区分不同连续工作空间中的解,但是推导过程相对复杂。二Pro/E中运动仿真的实现方法在Pro/E中,用户可以通过对机构添加运动副、驱动器使其运动起来,以实现机构的运动仿真。而机构又是由构件组合而成的,其中每个构件都是以一
51、定的方式至少与另一个构件相连接,这种连接不仅使2个构件直接接触,又使2个构件产生一定的相对运动。要使组件运动,在装配时就不能对其完全约束,而只能部分约束。即根据各组件之间的相对运动,通过“连接”设定限制组件的运动自由度。“连接”能够限制主体的自由度,仅保留所需的自由度,以产生机构所需的运动类型。 虚拟装配设计是在计算机上完成所设计零部件的装配模型,将不同的零件组装成一个装配体,并进行零件之间的静、动态干涉检查,发现零部件设计上的不合理结构部分,以改进设计。而通过机构仿真,可以在进行整体设计和零件设计后,对各种零件进行装配后模拟机构的运动,从而检查机构的运动是否达到设计的要求,可以检查机构运动中
52、各种运动构件之间是否发生干涉。同时,可直接分析各运动副与构件在某一时刻的位置、运动量以及各运动副之问的相互运动关系。随着计算机技术的发展,目前主流的CAD/CAM/CAE集成软件Pro/E、UG等都具备虚拟装配和运动仿真两大功能。半自动钻床由多个零件组成,零件之间是否满足装配要求和运动要求则可通过CAD/CAM/CAE集成软件来进行检验,从而达到优化零件设计的目的8.2夹具体运动学分析基于上述运动学分析理论,首先建立系统的模型。在此,主要以PRO/E三维实体软件为依托,以传统的系统设计手段为基础,分别建立模型有:压紧杠杆零件图、工件、夹具体底座(底座上带有梯形图块结构,其目的是与半自动化钻床的
53、集体底座的梯形槽相配合实现夹具体的槽配合并且移动实现刀具与工件相对位置的对准)、油缸外钢体、油缸内刚体、油缸连接耳环、用于与油缸和压紧杠杆的销钉链接副、V形块、定位板、连接螺栓。图8-2夹具及工件Fig8-2the gon of the skaded建立系统模型后,进入设备的模拟装配环境,在该环境下,将油缸的内外缸体采取圆柱链接方式进行连接,油缸外缸体和销孔材组销钉链接,压紧杠杆和销孔以及油缸内缸体分别采取销钉链接方式,将v形块玉工件设置为平面链接,将工件与定位板设定为平面链接,同时通过螺栓连接定位板和底座,此时,夹具体装配完毕。夹具体装配完毕,进入系统运动学分析与结构仿真分析环节:在装配完毕
54、的设备中分别添加动力装置于油缸内外缸体、设置质量属性(通过零件的几何尺寸计算机计算出其体积,通过定义不同零部件的密度或等效密度来计算整机质量)、重力加速度属性为10N/kg,将油缸的伸缩设置为弹簧、阻尼、质量块组成的系统,弹簧刚度、阻尼系数通过经验确定同时查机械设计手册校正。确定关键零部件的运动学性能,关键要素有夹具体夹紧杆与油缸连接处运动的位置、速度、加速度等。显示运动仿真分析的结果:显示方式有动画显示、数据表格显示、图像曲线显示,其中夹具体夹紧杆与油缸连接处运动位置曲线如图8-3所示图8-3夹具体夹紧杆与油缸连接处运动位置曲线Fig8-3 the picture of the line o
55、f the disability油缸连接处运动加速度变化曲线如图8-4所示图8-4加速度曲线Fig8-4the line of the asaed 油缸连接处运动速度变化曲线如图8-5所示图8-5速度曲线Fig8-5 victure line8.3半自动化钻床整机工作运动学分析在半自动化钻床整机工作运动学分析中,分别建立模型有:半自动钻床底座、夹具体底座、夹具体夹紧油缸、夹具压杆、定位座底盘、工件、定位V形块、螺栓、升降柱基座、升降柱密封圈、升降柱、升降柱定位手柄、摇臂、升降电机减速器、升降驱动电机、丝杠、滑槽、摇臂加强筋、刀具驱动电机、减速器2、刀具进给手轮、电控手柄、刀具卡盘、麻花钻、横向
56、控制手柄、液压系统箱等。建立系统模型后,进入设备的模拟装配环境,在该环境下,将夹具体子装配、半自动化钻床底座、升降柱机器相关配合零部件、电动机、首轮、刀具等装配于一体按照一定的规则,并且检查干涉理论,其装配后模型以下图形描述。初始装配位置图如8-6所示图8-6初始装配位置图Fig8-6 star line of the maded夹具体在滑槽内移动后装配位置图如8-7所示图8-7移动后装配位置Fig8-7the picture of the added type图8-8移动后装配位置Fig8-8 after linged of the type摇臂在升降柱上移动后位置关系如图x8-9所示:8-
57、9摇臂在升降柱上移动后位置关系Fig8-9the picture of the linde lind emedZ轴方向正向旋转调节图如图8-10所示图8-10Z轴方向正向旋转调节Fig8-10Z diturely of chargementZ轴方向负向旋转调节图如图8-11所示图8-11Z轴方向正向旋转调节Fig8-11Zdictum of the picture of niuded半自动化钻床刀具每个工作过程的推杆位置关系曲线如图8-12所示图8-12推杆位置曲线Fig8-12 nads lasd fdended通过分析曲线走势,首先上升,然后随着时间的推移上升到最高峰之后开始下降趋势,当时
58、间处于20s的时候曲线处于回归零的状态,分别表示凸轮传动进给系统的升程、回程、休止过程,从理论说明到实践经验分析确定该系统的运动学分析的模型建立、装配关系以及动力系统参数的添加趋于合理,属于可信系统 通过系统模型可行性的验证,下面分别提取进给机构连接点加速度变化曲线、刀具进给介个切削力变化曲线。进给机构连接点加速度曲线如图8-13所示图8-13进给机构连接点加速度曲线Fig8-13the jankded of the nubded刀具进给介个切削力变化曲线如图8-14所示8-14刀具进给介个切削力变化曲线Fig8-14the unseded of the picture9 结论本液压站是摇臂钻
- 温馨提示:
1: 本站所有资源如无特殊说明,都需要本地电脑安装OFFICE2007和PDF阅读器。图纸软件为CAD,CAXA,PROE,UG,SolidWorks等.压缩文件请下载最新的WinRAR软件解压。
2: 本站的文档不包含任何第三方提供的附件图纸等,如果需要附件,请联系上传者。文件的所有权益归上传用户所有。
3.本站RAR压缩包中若带图纸,网页内容里面会有图纸预览,若没有图纸预览就没有图纸。
4. 未经权益所有人同意不得将文件中的内容挪作商业或盈利用途。
5. 装配图网仅提供信息存储空间,仅对用户上传内容的表现方式做保护处理,对用户上传分享的文档内容本身不做任何修改或编辑,并不能对任何下载内容负责。
6. 下载文件中如有侵权或不适当内容,请与我们联系,我们立即纠正。
7. 本站不保证下载资源的准确性、安全性和完整性, 同时也不承担用户因使用这些下载资源对自己和他人造成任何形式的伤害或损失。