数控设计加工论文复杂数控加工零件加工工艺和程序设计
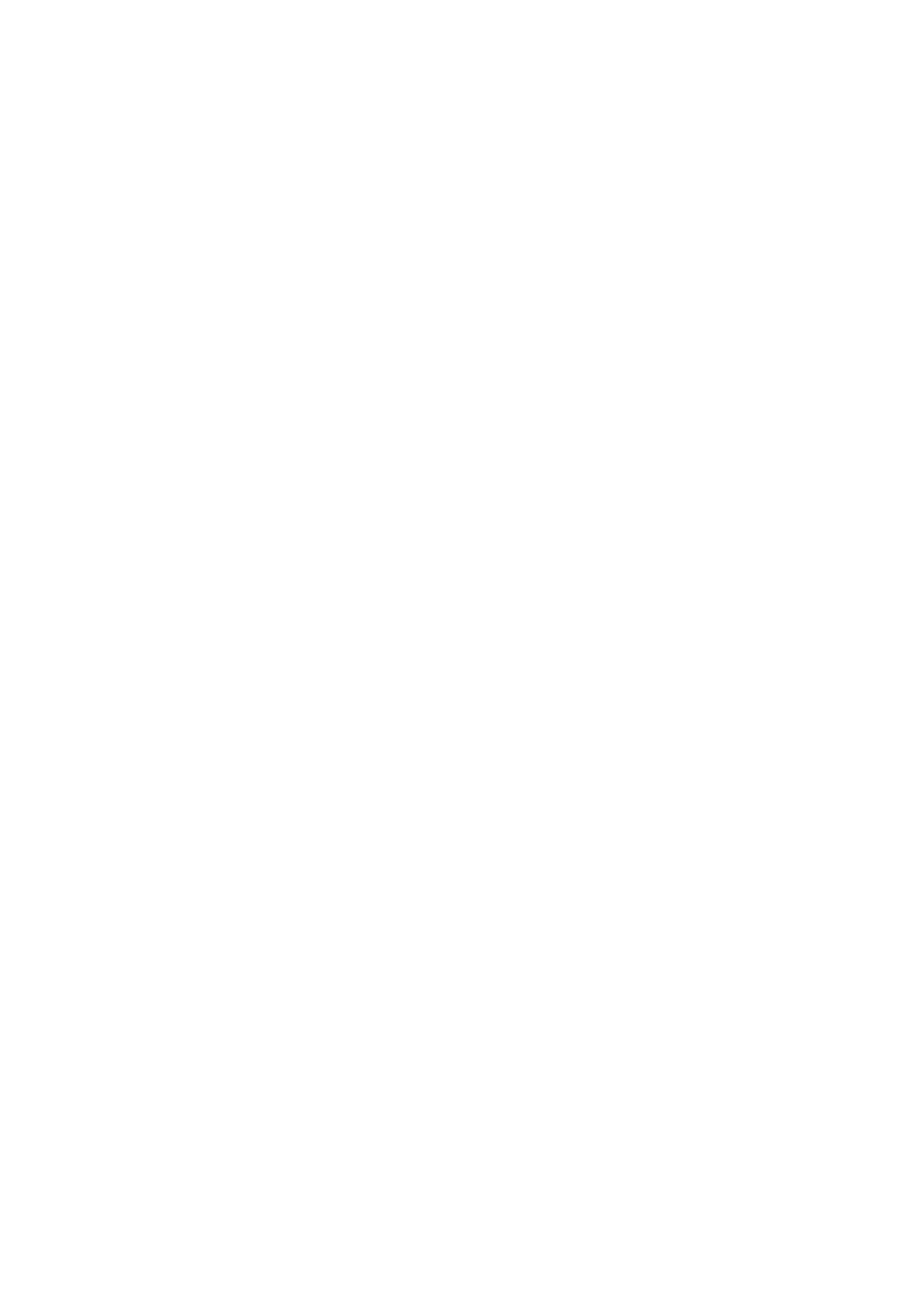


《数控设计加工论文复杂数控加工零件加工工艺和程序设计》由会员分享,可在线阅读,更多相关《数控设计加工论文复杂数控加工零件加工工艺和程序设计(47页珍藏版)》请在装配图网上搜索。
1、 一、课题名称课题名称: 复杂数控加工零件加工工艺和程序设计二、毕业论文(设计)主要内容毕业论文(设计)主要内容: 本毕业设计针对一个复杂数控加工零件进行加工工艺设计和程序设计,利用所学知识对该零件的图样进行分析,制定该产品零件的加工工艺方案,并针对该零件进行加工程序设计,完成该零件比较完整的设计方案。1 零件分析2. 零件造型3 选用加工设备4 零件加工工艺分析5 加工程序设计三、计划进度:第 8 周 查阅资料、确定设计方案; 第 911 周 确定工艺方案以及零件的加工路线; 第 12 周 完成毕业设计;第 13 周 答辩。四、毕业论文(设计)结束应提交的材料: 1、毕业设计论文; 2、零件
2、图;3、零件造型图4、UG 生成的加工程序指导教师 徐昆鹏 教研室主任 2010 年 10 月 18 日 年 月 日 论文真实性承诺及指导教师声明论文真实性承诺及指导教师声明学生论文真实性承诺学生论文真实性承诺本人郑重声明:所提交的作品是本人在指导教师的指导下,独立进行研究工作所取得的成果,内容真实可靠,不存在抄袭、造假等学术不端行为。除文中已经注明引用的内容外,本论文不含其他个人或集体已经发表或撰写过的研究成果。对本文的研究做出重要贡献的个人和集体,均已在文中以明确方式标明。如被发现论文中存在抄袭、造假等学术不端行为,本人愿承担本声明的法律责任和一切后果。毕业生签名: 日 期: 指导教师关于
3、学生论文真实性审核的声明指导教师关于学生论文真实性审核的声明本人郑重声明:已经对学生论文所涉及的内容进行严格审核,确定其内容均由学生在本人指导下取得,对他人论文及成果的引用已经明确注明,不存在抄袭等学术不端行为。指导教师签名: 日 期: 摘要本文简单的介绍了数控技术、数控的发展趋势、数控加工工艺、UG 在数控方面的应用(三维造型与数控自动加工)及手工编程。主要运用所学知识对零件图进行工艺分析、制定工艺路线、确定工艺方案,包括机床的选择、基准的选择、确定装夹方式、刀具的介绍与选择、切削用量及切削液的选择,深入了解了零件制造的全过程,加工完成后零件也达到了加工要求。并运用 UG 软件在数控加工方面
4、的功能进行三维造型和自动编程与加工,通过三维造型了解零件的工艺特点,通过加工模拟零件的加工过程,通过自动编程以最简单、最快捷的方式生成了 G 代码,并且达到了预期要求。关键词关键词:数控技术 加工工艺 UG 编程 AbstractThis article describes a simple numerical control technology, the development trend of CNC, CNC machining technology, UG in the application of CNC (CNC automatic three-dimensional model
5、ing and processing) and manual programming. The main use of the knowledge of the parts diagram for process analysis, development of process routes, determine the process plan, including the machines choice, the choice of benchmarks to determine the clamping method, the introduction and selection too
6、l, cutting parameters and the choice of cutting fluid, in-depth understanding of whole process of manufacturing of parts, the processing is complete part processing requirements are met. And using UG softwares capabilities in CNC machining three-dimensional modeling and automatic programming and pro
7、cessing, through the three-dimensional modeling to understand part of the process characteristics, through the processing of the processing of analog components, by automatically programming the easiest and fastest way to generate the G code, and met expectations. Key words: Numerical control techno
8、logy Processing technology UG Programming 目录目录第一章 绪论71.1 数控加工技术的发展趋势.71.1.1 继续向开放式、基于 PC 的第六代方向发展71.1.2 向高速化和高精度化发展71.1.3 向智能化方向发展71.2 UG 数控铣削编程的关键技术及应用 .81.2.1 数控编程模块81.2.2 刀具轨迹的生成81.2.3 刀具轴的导动方式101.2.4 刀具轨迹编辑的修改101.2.5 加工仿真101.2.6 后置处理101.2.7 切削参数库设置111.2.8 CAM 二次开发功能接口111.3 UNIGRAHPICSNX/CAM 数控编程
9、流程.12第二章 零件图纸的工艺分析132.1 零件图分析.132.1.1 读图和审图132.1.2 零件结构的工艺性142.2 毛坯、余量分析.152.2.1 毛坯的种类152.2.2 加工余量15第三章 加工准备及工艺路线的确定163.1 机床及工艺装备的选择.163.1.1 夹具的选择.173.1.2 刀具选择173.2 基准的选择.183.3 切削用量及切削液的选择.193.3.1 吃刀量193.3.2 进给速度20 3.3.3 切削速度213.3.4 切削液的选择223.4 确定工艺路线.233.5 确定进给路线.233.6 数控加工工序卡.24第四章 UG 加工和编程设计264.1
10、 加工并生成程序.264.1.1 工艺参数设定264.1.2 生成加工轨迹274.1.3 生成部分程序294.1.4 例举自动生成的程序304.2 手工编程.39参考文献42附录43致谢44 第一章 绪论数控技术是用数字信息对机床运动和工作过程进行控制的技术,它是集传统的机械制造技术、计算机技术、现代控制技术、传感检测技术、网络通信技术和光机电技术等于一体的现代制造业的基础技术,具有高精度、高效率、柔性自动化等特点,对制造业实现柔性自动化、集成化和智能化起着举足轻重的作用。数控装备则是以数控技术为代表的新技术对传统制造产业和新兴制造业的渗透而形成的机电一体化产品。数控技术是制造自动化的基础,是
11、现代制造装备的灵魂核心,是国家工业和国防工业现代化的重要手段,关系到国家战略地位,体现国家综合国力水平,其水平的高低和数控装备拥有量的多少是衡量一个国家工业现代化的重要标志。1.1 数控加工技术的发展趋势数控加工的发展趋势包括继续向开放式、基于 PC 的第六代方向发展、向高速化和高精度化发展、向智能化方向发展。1.1.11.1.1 继续向开放式、基于继续向开放式、基于 PCPC 的第六代方向发展的第六代方向发展基于 PC 所具有的开放性、低成本、高可靠性、软硬件资源丰富等特点,更多的数控系统生产厂家会走上这条道路。至少采用 PC 机作为它的前端机,来处理人机界面、编程、联网通信等问题,由原有的
12、系统承担数控的任务。PC 机所具有的友好的人机界面,将普及到所有的数控系统。远程通讯,远程诊断和维修将更加普遍。1.1.21.1.2 向高速化和高精度化发展向高速化和高精度化发展这是适应机床向高速和高精度方向发展的需要。1.1.31.1.3 向智能化方向发展向智能化方向发展随着人工智能在计算机领域的不断渗透和发展,数控系统的智能化程度将不断提高。(1)应用自适应控制技术数控系统能在运行过程中检测一些重要信息,并自动调整系统的有关参数,达到改进系统运行状态的目的。(2)引入专家系统指导加工将熟练工人和专家的经验,加工的一般规律和特殊规律存入系统中,以工艺参数数据库为支撑,建立具有人工智能的专家系
13、统。(3)引入故障诊断专家系统在设备故障诊断系统中借助多种数学原理和系统理论,形成了多种不同的诊断方法。(4)智能化数字伺服驱动装置可以通过自动识别负载,而自动调整参数,使驱动系统获得最佳的运行状态。 1.2 UG 数控铣削编程的关键技术及应用Unigrahics NX/CAM 有以下重要组成部分:三维建模、刀具轨迹设计、刀具轨迹编辑修改、加工仿真、后置处理、数控编程模板、切削参数库设计和二次开发功能接口等。1.2.11.2.1 数控编程模块数控编程模块使用数控编程模板有利于利用已有的经验和专家知识,达到企业内部资源共享的目的。系统提供了加工程式模板、刀具模板、加工对象模板和刀具轨迹模板。在模
14、板中不断注入数控编程员、加工工艺师和技术工人等的知识、经验和习惯,建立起规范的数控加工工艺过程,为强化企业生产管理、提高产品的加工效率和质量打下良好的工艺技术基础。CAM 系统创建用户自己的模板可以将预先的加工顺序、工艺参数和切削参数设置好。针对相似的零件加工 对象,应用模板可以大幅度提供数控编程的效率和质量,尤其是在模具行业对形似的成组零 件的加工。例如,在制造模具时将加工凸模和凹模时的最佳工艺过程定义为加工模板,在加 工新的产品对象时,只需调用模板文件,选择所需的几何体,并起动这个流程即可。用户通 过加工向导非常容易地从模板中获得专家级的制造过程指导。通过向导,预先定义的模板可以被激活,并
15、通过简单的交互快速生成数控加工刀具轨迹。Unigraphics NX 系统提供了基本的数控编程模板,以 Shops_diemould 模板集为例,其配置文件 Shops_diemold.dat 位于machresourceconfiguration 中,模板集文件 Shops_diemold.opt 则位于machresourcetemplate 目录下。用户可根据本企业的经验创建自己的程式、粗精加工、刀具、产品等类型的编程模板。利用模板之前,需要对不同产品类 的零件的不同加工方式的模板进行整理与收集。在创建模板时可按加工方式进行分类,对于 系列化或相似的加工工艺,如凸凹模具类零件的加工等,则
16、可以包含粗精加工方案、刀具及 工艺参数的选择等完整的加工流程模板。模板的定义可根据产品加工要求与几何特征划分, 也可根据产品加工要求与材料等多种方式进行划分。1.2.21.2.2 刀具轨迹的生成刀具轨迹的生成系统提供了钻孔循环、攻丝和镗孔等点位加工编程模块,具有多种轮廓加工、等高环切、行切以及岛屿加工平面铣削等编程功能。其提供的 35 坐标复杂曲面的固定轴与变轴加工编程功能,可以任意控制刀具轴的矢量方向,具有曲面轮廓、等高分层、参数线加工、曲面流线、陡斜面和曲面清根等多种刀具轨迹控制方式。(1)UG/Planar Milling(UG 平面铣削) UG 平面铣削模块功能,包括多次走刀轮廓铣、仿
17、形内腔铣、Z 字形走刀铣削,规定避开夹具和进行内部移动的安全余量,提供型腔分层切削功能、凹腔底面小岛加工功能,对边界和毛料几何形状的定义、显示未切削区域的边界,提供一些操作机床辅助运动的指令,如冷却、刀具补偿和夹紧等。 (2)UG/Core & CavityMilling(UG 型芯、型腔铣削) 利用 UG 型芯、型腔铣削可完成粗加工单个或多个型腔,可沿任意类似型芯的形状进行去除大余量的粗加工,对非常复杂的形状产生刀具运动轨迹,确定 走刀方式。通过容差型腔铣削可加工设计精度低、曲面之间有间隙和重叠的形状,而构成型腔的曲面可达数百个,发现型面异常时,它可以或自行更正,或在用户规定的公差范
18、围内加工出型腔来。 (3) UG/Fixed AxisMilling(UG 固定轴铣削) UG 固定轴铣削模块功,包括产生 3 轴联动加工刀具路径功能、加工区域选择功能,有多种驱动方法和走刀方式可供选择,如沿边界切削、放射状切削、螺旋切削及用户定义方式切削等。在沿边界驱动方式中,又可选择同心圆和放射状走刀等多种走刀方式,提供逆铣、顺铣控制以及螺旋进刀方式,自动识别前道工序未能切除的未加工区域和陡峭区域,以便用户进一步清理这些地方。 (4) UG/Flow Cut (UG 自动清根) 自动找出待加工零件上满足“双相切条件”的区域,一般情况下这些区域正好就是型腔中的根区和拐角。用户可直接选定加工刀
19、具,UG/Flow Cut 模块将自动计算对应于此刀具的“双相切条件”区域并将其作为驱动几何,自动生成一次或多次走刀的清根程序。当出现复杂的型芯或型腔加工时,该模块可减少精加工或半精加工的工作量。 (5) UG/Variable Axis Milling(UG 变轴铣削) 变轴铣削模块支持定轴和多轴铣削功能,可加工 UG 造型模块中生成的任意几何体,并保持主模型的相关性。该模块提供经多年工程使用验证的 35 轴铣削功能,提供刀轴控制、走刀方式选择和刀具路径生成功能。 (6) UG/Sequential Milling(UG 顺序铣) UG 顺序铣模块可实现如下功能:控制刀具路径生成过程中的每一
20、步骤的情况,支持 25 轴的铣削编程,和 UG 主模型完全相关,可以自动化的方式获得类似 APT 直接编程的绝对控制,允许用户交互式一段一段地生成刀具路径,并保持对过程中每一步的控制。它提供的循环功能使用户可以仅定义某个曲面上最内和最外的刀具路径,由该模块自动生成中间的步骤。该模块是 UG 数控加工模块中如自动清根等功能一样的特有模块,适合于高难度的数控程序编制。 (7) 高速铣削加工的支持 系统提供的等高分层加工应用于高速铣削场合,在转角处以圆角的形式过渡,避免 90急转(高速场合对导轨和电机容易损坏),同时采用螺旋进退刀,系统还提供环绕等多种方式支持高速加工刀具轨迹的生成策略。1.2.31
21、.2.3 刀具轴的导动方式刀具轴的导动方式空间曲面轴加工涉及的内容比较多,尤其是五轴加工时更明显。进行五轴加工时,涉及加工导动曲面、干涉面、轨迹限制区域、进退刀及刀轴矢量控制等关键技术。四轴五轴加工的关键技术之一是理解刀具轴的矢量(刀具轴的轴线矢量)在空间的变化。刀具轴的矢量变化是通过摆动工作台或主轴的摆动来实现的。对于矢量不发生变化的固定轴铣削场合,一般用三轴铣削即可加工出产品。五轴加工关键就是通过控制刀具轴矢量在空间位置的不断变化或使刀具轴的矢量与机床原始坐标系构成空间某个角度,利用铣刀的侧刃或底刃切削加工来完成。1.2.41.2.4 刀具轨迹编辑的修改刀具轨迹编辑的修改该模块可在图形方式
22、下观测刀具沿轨迹运动的情况并进行图形化修改,具有刀位文件复制、编辑和修改,定义刀具、机床和切削参数数据库等功能(如对刀具轨迹进行延伸、缩短或修改等) ,可按用户需求进行灵活的用户化修改和 剪裁等。1.2.51.2.5 加工仿真加工仿真切削仿真模块 UG/Vericut 是集成在 UG 软件中的第三方模块,它采用人机交互方式模拟、检验和显示 NC 加工程序,是一种方便的验证数控程序的方法。由于省去了试切样件的步骤,可节省机床调试时间,减少刀具磨损和机床清理工作。通过定义被切零件的毛坯形状,调用 NC 刀位文件数据,就可检验由 NC生成的刀具路径的正确性。UG/Vericut 可以显示出加工后并着
23、色的零件模型,用户可以容易地检查出不正确的加工情况。作为检验的另一部分,该模块还能计算出加工后零件的体积和毛坯的切除量,因此就容易确定原材料的损失。Vericut 提供了许多功能,其中有对毛坯尺寸、位置和方位的完全图形显示,可模拟 25 轴联动的铣削和钻削加工。1.2.61.2.6 后置处理后置处理后置处理最重要的是将 CAM 软件生成的刀位轨迹转化为适合数控系统加工的 NC 程序,通过读取刀位文件,根据机床运动结构及控制指令格式,进行坐标运动变换和指令格式转换。通用后置处理程序是在标准的刀位轨迹以及通用的CNC 系统的运动配置及控制指令的基础上进行处理。它包含机床坐标运动变换、非线性运动误差
24、校验、进给速度校验、数控程序格式变换及数控程序输出等方面的内容。只有采用正确的后置处理系统才能将刀位轨迹输出为相应数控系统的机床能正确进行加工的数控程序,因此,编制正确的后置处理系统模板是数控编程与加工的前提条件之一。后处理的主要内容包括三个方面的内容。 (1)数控系统控制指令的输出 主要包括机床种类及机床配置、机床的定位、插补、主轴、进给、暂停、冷却、刀具补偿、固定循环和程序头尾输出等方面的控制。 (2)格式转换 包括数据类型转换与圆整、字符串处理等,主要针对数控系统的输出格式,如单位、输出地址字符等方面的控制。 (3)算法处理 主要针对多坐标加工时的坐标变换、跨象限处理和进给速度控制等。
25、UG/Post Execute 和 UG/Post Builder 共组成了 UG 加工模块的后置处理。UG 的加工后置处理模块使用户可方便地建立自己的加工后置处理程序。该模块适用于目前世界上几乎所有主流 NC 机床和加工中心,多年的应用实践中已被证明适用于轴或更多轴的铣削加工,轴的车削加工和电火花线切割。UG/Nurbs Path Generator 样条轨迹生成器模块允许在 UG 软件中直接生成基于Nurbs 样条的刀具轨迹数据,使得生成的轨迹拥有更高的精度和光洁度,而加工程序量比标准格式减少 30%50%,实际加工时间则因为避免了机床控制器的等待时间而大幅度缩短。该模块是希望使用具有样条
26、插值功能的高速铣床(FANUC 或 SIEMENS)用户必备工具。利用 UG/Post Builder 进行后处理的新建、编辑和修改时,生成三个文件 :机床控制系统的功能和格式的定义文件*.def,用 Tcl 语言编写控制机床运动事件处理文件*.tcl 和利用 PostBuilder编辑器设置所有数据信息的参数文件*.pui。后置处理程序将 CAM 系统通过机床的 CNC 系统与机床数控加工紧密结合起来。 1.2.71.2.7 切削参数库设置切削参数库设置使用系统库可以得到机床、刀具及其材料、零件材料、切削工艺方法、主轴转速及进给速度的数据,定义标准化刀具库、加工工艺参数样板库,使粗加工、半精
27、加工、精加工等操作常用参数标准化,以减少使用培训时间并优化加工工艺,提供储存刀具及切削参数和标准刀具指令数据库。用户通过修改库中的数据,使其满足本企业的需要。 1.2.81.2.8 CAMCAM 二次开发功能接口二次开发功能接口使用系统提供了二次开发接口,用户可以 C 语言,利用 VisualC+为集成开发环境,开发专业的数控编程功能程序,以进一步提高编程的效率和简化操作。其提供的 C 语言头函数位于 UG OPEN 目录下,包括Uf_cam.h、Uf_camgeom.h、Uf_cam_planes.h 等头文件。下面位几个重要头文件的主要内容。 1)Uf_cam.h 主要定义系统加工的一些信
28、息,如枚举、结构体和系统起动入口设置,对用户应用程序完成初始化设置加载应用程序,访问系统机床、刀具、加工对象等数据库的方法函数。 (2)Uf_cam_planes.h 定义系统编程加工涉及的平面数据信息,如定义、编辑、访问平面的原点和法线,设置和访问平面的状态信息等内容的属性方法等。 (3)Uf_cambnd.h 用于定义设置、获取边界信息。 (4)Uf_camgeom.h 包含用于定义设置和获取 NC 加工的几何对象的属性和方法。 1.3 UnigrahpicsNX/CAM 数控编程流程Unigraphics NX/CAM 用于产品零件的数控加工,其流程一般如下。 首先是调用产品零件加载毛坯
29、,调用系统的模板或用户自定义的模板;然后分别创建加工的程式,定义工序加工的对象,设计刀具,定义加工的方式并生成该相应的加工程式;用户依据加工程式的内容,如加工对象的具体内容、刀具的导动方式、切削步距、主轴转速、进给量、切削角度、进退刀点、干涉面及安全平面等详细内容来确立刀具轨迹的生成方式;仿真加工后对刀具轨迹进行相应的编辑修改、拷贝等;待所有的刀具轨迹设计合格后,进行后处理生成相应数控系统的加工代码进行 DNC 传输与数控加工。Unigraphics NX/CAM 系统提供了多种加工对象的定义方式,刀具轴的导动方式和刀具轨迹的多样化设计。 第二章 零件图纸的工艺分析在数控铣削加工中,对零件图进
30、行工艺分析的主要内容包括零件结构工艺性分析、选择数控铣削的加工内容、零件毛坯的工艺性分析和加工方案分析。2.1 零件图分析2.1.12.1.1 读图和审图读图和审图如零件图图 2-1、及图 2-2 三维造型图所示零件: 图图 2-12-1 零件图零件图 图图 2-22-2 三维造型图三维造型图(1)该零件毛坯尺寸为 160 x120 x30,且不需要加工。(2)在零件上有多个加工特征,包括两个通孔、键槽、型腔、四个螺纹孔、曲面凸台,尺寸标注完整。(3)该零件表面粗糙度内轮廓及通孔 Ra1.6um 和其余 Ra3.2um,参数合理便于加工。(4)零件材料为 45 钢,切削加工性能较好,无热处理和
31、硬度要求。该复杂零件技术要求有:a.未注公差0.1mm;b.圆弧曲面误差不大于0.05mm;c.去除毛刺。加工要素有平面、曲线、腔槽、孔类和孔螺纹加工。主要加工项目有上下平面、主视图中对称腔槽60槽宽、槽深027. 0012mm、螺孔4-M10、孔、孔10H7、位置尺寸102.2870.017mm、022. 0010039. 0032位置尺寸1360.02mm、圆弧倒角R3、圆弧曲面R25、以及内轮廓的尺寸。2.1.22.1.2 零件结构的工艺性零件结构的工艺性零件的工艺性是指所设计的零件在满足使用要求的前提下制造的可行性和经济性。它包括零件各个制造过程中的工艺性,如零件的铸造、锻造、冲压、焊
32、接、热处理和切削加工工艺性能等。好的工艺性会使零件加工容易,节省工时,降低消耗;差的工艺性使零件加工困难,多耗工时,增大消耗。该复杂件的加工各工艺性能良好,耗工不大。该零件结构复杂,但就加工来说,还是易于加工的。在加工时要特别注意圆弧曲面的加工,4-M10 螺纹孔的加工以及内轮廓和岛屿的加工。 2.2 毛坯、余量分析2.2.12.2.1 毛坯的种类毛坯的种类常用毛坯的种类有铸件、锻件压制件、冲压件、焊接件、型材和板材等。 (1)铸件:适用于形状复杂的毛坯。薄壁零件不可用砂型铸造;尺寸大的铸件宜用砂型铸造;中、小型零件可用较先进的铸造方法。(2)锻件:适用于零件强度较高、形状较简单的零件。尺寸大
33、的零件因受设备限制,故一般用自由锻;中、小型零件可选用模锻;形状复杂的零件不宜用自由锻。(3)型材:热轧型材的尺寸较大,精度低,多用作一般零件的毛坯;冷轧型材尺寸较小,精度较高,多用于毛坯精度要求较高的中、小零件,适用于自动机床加工。(4)焊接件:对于大件来说,焊接件简单、方便,特别是单件、小批量的生产可大大缩短生产周期;但焊接后变形大,需经时效处理。(5)冷压件:适用于形状复杂的板料零件,多用于中、小尺寸零件的大批量加工。该零力选用 45 钢,45 钢属于中碳钢,这类钢调质处理后具有良好的综合力学性能,即既具有较高的强度、硬度,又具有较好的塑性、韧性,是优质碳素结构钢中应用最广泛的一类。该零
34、件结构复杂,但就加工来说,还是易于加工的。2.2.22.2.2 加工余量加工余量加工余量大小,直接影响零件的加工质量和生产率。加工余量过大,不仅增加机械加工劳动量,降低生产率,而且增加材料、工具和电力的消耗,增加成本。但若加工余量过小,又不能消除前工序的各种误差和表面缺陷,甚至产生废品。因此,必须合理地确定加工余量。其确定的方法有:经验估算法、查表修正法、分析计算法。首先根据工艺人员的经验来确定加工余量。为避免产生废品,所确定的加工余量一般偏大。要准确余量则需要根据有关手册,查得加工余量的数值,然后根据实际情况进行适当修正。该零件的加工余量如下:粗加工上下平面余量 0.1mm ,半精加工内轮廓
35、单边留 0.3mm 余量,半精加工外轮廓单边留 0.3mm 余量。 第三章 加工准备及工艺路线的确定在对零件进行加工前要对零件进行许多分析,如装夹方式、基准选择、确定坐标零点、刀具选择及机床选择等。3.1 机床及工艺装备的选择对于某个零件而言,并非全部加工工艺过程都适合在数控机床上完成,而往往只是其中的一部分适合于数控加工。这就需要对零件图样进行仔细的工艺分析,选择那些最适合、最需要进行数控加工的内容和工序。在选择时,应考虑各方面因素,充分发挥数控加工的优势。选择时应考虑以下因素: (1)通用机床无法加工的内容。 (2)通用机床难加工、质量也难以保证的内容应作为重点选择的内容。 (3)通用机床
36、效率低、工人劳动强度大的内容。从精度和效率两方面对数复杂零件的加工艺进行分析,加工精度必须达到图纸的要求,同时又能充分合理地发挥机床的功能,提高生产效率。根据以上条件可选择两轴半以上的数控铣床。本零件选用大连机床厂 XD-40A 型数控铣床,采用 FANUC0i-MB 系统。该铣床的功能参数如表 3-1 下。表表 3-13-1 XD-40AXD-40A 型数控铣床基本参数型数控铣床基本参数机床重4400Kg最大载重500kg800mm 长工作台400mm 宽X600mmY420mm坐标范围Z520mm轴承锥孔NO.40(7:24)最大钻孔直径22最大镗孔直径100主轴最高转速8000rmin主
37、轴功率7.5/11kwX、Y、Z 向切削进给速度0-10000 mmminX24 mminY24 mmin快速进给速度Z20 mmin工作电源380V3.1.13.1.1 夹具的选择夹具的选择机床夹具的种类很多,按使用的机床类型分为车床夹具、铣床夹具、钻床夹具、镗床夹具、加工中心夹具等。而按专门化程度划分来说,该零件使用的是立式数控铣床。零件又属于平面类零件,应使用通用夹具,通用夹具是已经标准化、无需调整或稍加调整就可以用来装夹不同工件的夹具。 所以这里我们使用的是精密平口钳。3.1.23.1.2 刀具选择刀具选择刀具的选择是在数控编程的人机交互状态下进行。应根据机床的加工能力、工件材料的性能
38、、加工工序、切削用量,以及其他相关因素正确选用刀具及刀柄。刀具选择总的原则是:安装调整方便,刚性好,耐用度和精度高。在满足加工要求的前提下,尽量选择较短的刀柄,以提高刀具加工时的刚性。选择合适的刀具和参数,对于金属切削加工,能起到事半功倍的效果。刀具材料选用硬质合金,钻头和铰刀选用高速钢。且切削速度比高速钢高410 倍,但其冲击韧性与抗拉强度远比高速钢差。而铣刀种类繁多,在使用时要根据加工部位、表面粗糙度、精度等来选用,根据图形的精度和加工部位来看,所选刀具卡见表 3-1。标准可转位面铣刀的直径为 16-630 mm。粗铣时,铣刀直径要小些,因为粗铣切削力大,选小直径铣刀可减小切削扭距。精铣时
39、,铣刀直径要选大些,尽量包容工件整个加工宽度,以提高加工精度和效率,并减小相邻两次进给之间的接刀痕迹。由于数控机床要求铣刀能快速自动装卸,而立铣刀刀柄部结构有很大不同。一般由专业厂家按照一定的规范制造成统一形式、尺寸的刀柄。直径大于40160mm 立铣刀可做成套式结构。立铣刀的有关尺寸参数,推荐用下述经验数据选取: 刀具半径R应小于零件内轮廓面的最小曲率半径,R一般取R=(0.80.9)R。 零件的加工高度H(1/41/6)R,以保证刀具有足够的刚度。 对于深槽,选取l=H+(510)mm(l为刀具切削部分长度)。加工肋时,刀具直径为D=(510)b(b为肋的厚度)。选择的刀具如下:80 盘铣
40、刀,用于外轮廓粗、精加工。10 立铣刀,用于外轮廓粗精加工。16 立铣刀,用于内轮廓粗精加工。A2 中心钻,用于 32mm、10H7、4-M10 的中心孔。20 钻头,用于预钻 32mm孔。32 精镗刀,精镗 32mm 通孔至尺寸要求。8.5 钻头,用于 4-M10 钻孔。9.6 钻头,用于 10H7 钻孔。10H7 铰刀,用于铰 10H7孔。R5 球头刀,用于圆弧面加工。M10 丝锥,用于螺纹加工。表表 3-13-1 复杂零件加工刀具清单复杂零件加工刀具清单序号名称规格数量备注1面铣刀150mm(R 型面铣刀)12立铣刀10mm 2 3球头铣刀R5mm14立铣刀16mm25中心钻A216钻头
41、20mm17钻头8.5mm、18钻头9.6mm19镗刀32mm110铰刀10H7mm111丝锥M10 的丝锥13.2 基准的选择(1)基准重合原则以设计基准为定位基准,避免基准不重合误差,调整法加工零件时,如果基准不重合将出现基准不重合误差。所谓调整法,是在预先调整好刀具与机床的相对位置,并在一批零件的加工过程中保持这种相对位置的加工方法。与之相对应的是试切法加工,即试切一测量一调整一再试切,循环反复直到零件达到尺寸要求为止。试切法适用于单件小批生产下的逐个零件加工。 (2)基准统一原则选用统一的定位基准来加工工件上的各个加工表面。以避免基准的转换带来的误差,利于保证各表面的位置精度,简化工艺
42、规程,夹具设计和制造缩短生产准备周期。典型的基准统一原则是轴类零件、盘类零件和箱体类零件。轴的精基准为轴两端的中心孔,齿轮是典型的盘类零件,常以中心孔及个端面为精加工基准,而箱体类常以一个平面及平面上的两个定位用工艺孔为精基准。(3)自为基准原则当某些精加工表面要求加工余量小而均匀时,可选择该加工表面本身作为定位基准,以搞高加工面本身的精度和表面质量。(4)互为基准原则能够提高重要表面间的相互位置精度,或使加工余量小而均匀。(5)装夹方便原则所选定位基准应能使工件定位稳定,夹紧可靠,操作方便,夹具结构简单。以上每项原则只能说明一个方面的问题,理想的情况是使基准既“重合” 又“统一”,同时又能使
43、定位稳定、可靠,操作方便,夹具结构简单。但实际运用中往往出现相互矛盾的情况,这就要求从技术和经济两方面进行综合分析,抓住主要矛盾,进行合理选择。还应该指出,工件上的定位精基准,一般应是工件上具有较高精度要求的重要工作表面,但有时为了使基准统一或定位可靠,操作方便,人为地制造一种基准面,这些表面在零件的工件中并不起作用,仅仅在加工中起定位作用,如顶尖孔、工艺搭子等。这类基准称为辅助基准。该零件设计基准在毛坯料右下角。根据上述原则,将工件坐标系的原点设定在毛坯上表面,岛屿对角线焦点位置。为使数控编程方便,将图纸转化为坐标。3.3 切削用量及切削液的选择 在一定切削条件下,合理选择切削用量是提高切削
44、效率、保证刀具耐用度和加工质量的主要手段。数控铣床的切削用量包括切削速度 Vc、进给速度 、背吃刀量和侧吃fvpa刀量。切削用量的选择方法是考虑刀具的耐用度,先选取背吃刀量或侧吃刀ca量,其次确定进给速度,最后确定切削速度。3.3.13.3.1 吃刀量吃刀量如图 3-1 所示,背吃刀量为平行于铣刀轴线测量的切削层尺寸,单位为pamm,端铣时为切削层深度,圆周铣削时为被加工表面的宽度。侧吃刀量papa为垂直于铣刀轴线测量的切削层尺寸,单位为 mm,端铣时为被加工表面宽caca度,圆周铣削时为切削层深度。端铣背吃刀量和圆周铣侧吃刀量的选取主要ca由加工余量和对表面质量要求决定。(1)工件表面粗糙度
45、要求为 Ra3.212.5m,分粗铣和半精铣两步铣削加工,粗铣后留半精铣余量 0.5 1.0mm。 图图 3-13-1 铣刀铣削用量铣刀铣削用量(2)工件表面粗糙度要求为 Ra0.83.2m,可分粗铣、半精铣、精铣三步铣削加工。半精铣时端铣背吃刀量或圆周铣削侧吃刀量取 1.52mm,精铣时圆周铣侧吃刀量取 0.30.5mm,端铣背吃刀量取 0.51mm。该工件的表面粗糙度为 Ra3.2,孔及型腔粗糙度为 Ra1.6,其余为 Ra3.2。应采用半精铣、精铣, 半精铣吃刀量 2mm,精铣吃刀量 1mm。3.3.23.3.2 进给速度进给速度进给速度指单位时间内工件与铣刀沿进给方向的相对位移,单位为
46、mm/min。它与铣刀转速 n、铣刀齿数 Z 及每齿进给量 (单位为 mm/z)有关。zf进給速度的计算公式: =Z n (3-fvzf1)式中: 每齿进给量的选用主要取决于工件材料和刀具材料的机械性能、zf工件表面粗糙度等因素。当工件材料的强度和硬度高,工件表面粗糙度的要求高,工件刚性差或刀具强度低,值取小值,每齿进给量的选用参考表见表 3-zf2。表表 3-23-2 铣刀每齿进给量铣刀每齿进给量参考表参考表zf每 齿 进 给 量 (mm/z)zf粗铣精铣工件材料高速钢铣刀硬质合金铣刀高速钢铣刀硬质合金铣刀钢0.100.150.100.25铸铁0.120.200.150.300.020.05
47、0.100.153.3.33.3.3 切削速度切削速度表表 3-43-4 铣削时的切削速度参考表铣削时的切削速度参考表切削速度 Vc (m/min)工件材料硬度(HBS)高速钢铣刀硬质合金刀具225184266150钢22532512365412032542562136751902136661501902609184590铸铁1603204.5102130 铣削的切削速度与刀具耐用度 T、每齿进给量、背吃刀量、侧吃刀zfpa 量以及铣刀齿数 Z 成反比,与铣刀直径 d 成正比。其原因是、Zeazfpaea增大时,使同时工作齿数增多,刀刃负荷和切削热增加,加快刀具磨损,因此刀具耐用度限制了切削速
48、度的提高。表 3-4 列出了铣削切削速度的参考值。cV而具体选用公式为=/1000 (3-2)cVnd 例举10、16 的立铣刀计算过程:10 的立铣刀选择的切削速度=100m/min,每齿进给量=0.2mm/z。根据公cVzf式(3-1)、(3-2)可得:主轴转速:n=1000/=1000 x100/3.14x10=3184r/mincVd进给速度:=Z n =0.2x2x3184=1273mm/min fvzf16 的立铣刀选择的切削速度=100m/min,每齿进给量=0.2mm/z。根据公cVzf式(3-1)、(3-2)可得:主轴转速:n=1000/=1000 x100/3.14x16=
49、1990r/mincVd进给速度:=Z n =0.2x2x1990=796mm/min fvzf 选用的参数如表 3-4。表表 3-43-4 切削用量切削用量切削用量切削用量工艺装备及编号工艺装备及编号工序工序工序内容工序内容吃刀量吃刀量主轴转速主轴转速进给速进给速度度刀具刀具量具量具夹夹具具粗25601201铣表面精198080150 的盘铣刀粗220008002外轮廓精13184127310 的立铣刀粗215006003内轮廓精1199079616 的立铣刀4钻中心孔287060A2 的中心钻 3.3.43.3.4 切削液的选择切削液的选择 切削液是为提高切削加工效率而使用的液体。它可有效
50、地减小摩擦,改善散热条件,从而降低切削力、切削温度和刀具磨损,提高生产率和加工表面质量。切削液具有冷却、润滑、清洗和防锈作用,常用的切削液有乳化液和切削油。切削该工件时使用的是硬质合金刀具,由于它的耐热性好,所以一般不使用切削液。若要使用,则必须大量注射,以免硬质合金刀具因冷热不均产生裂纹。3.4 确定工艺路线(1)工序的划分 在数控机床上加工零件与普通机加工相比,工序可以比较集中。根据数控加工的特点,数控加工工序的划分有几种方法。 加工该零件按粗、精加工划分工序,根据工件的加工精度要求、刚度和变形等因素,将零件的粗、精加工分开,先粗加工,后精加工。(2)工步的划分划分工步主要是从加工精度和效
51、率方面考虑。合理的工艺不仅要保证加工出符合图样要求的工件,同时应使机床的功能得到充分发挥。因此,在一个工序内往往需要采用不同的刀具和切削用量,对工件的不同表面进行加工。对于比较复杂的工序,为了便于分析和描述,常在工序内又细分工步。就本工件的5攻螺纹18060M10 的丝锥6铣曲面100030R5 的球头铣刀7钻 4 个通孔81315608.5 的钻头8预钻10 通孔81420609.6 的钻头9预钻32 通孔1515604020 的钻头10铣孔322150060016 的立铣刀11精镗孔320.155006032 的精镗刀12对孔进行精加工0.2501010H7 的铰刀 加工而言,划分时应注意
52、一下几点原则:同一加工表面按粗加工、半精加工、精加工依次完成,还是全部加工表面都先粗加工后精加工分开进行,主要要依据零件的精度要求考虑。对于既要加工平面又要加工孔的地方,可以采用“先面后孔“原则划分工步。先加工面可提高孔的加工精度,因为铣平面时切削力较大,工件易发生变形,而先铣平面后镗孔,则可使其变形有一段时间恢复,减少由于变形引起的对孔的精度的影响。反之,如先镗孔后铣面,则铣削平面时极易在孔口产生飞边、毛刺,进而破坏孔的精度。按所用刀具划分工步。某些机床工作台回转时间比换刀时间短,可采用刀具集中的方法划分工步,以减少换刀次数,缩短辅助时间,提高加工效率。在一次装夹中,尽可能完成所有能加工的表
53、面,有利于保证表面相互位置精度的要求。(3)加工顺序的安排加工顺序的安排应根据零件的结构和毛皮状况,结合定位和夹紧的需要一起考虑,重点应保证工件的刚性不被破坏,尽量减少变形。加工顺序的安排应遵循一些原则:基准先行。上道工序的加工能为后面的工序提供精基准和合适的夹紧表面。先面后孔,先简单后复杂。先粗后精,粗、精分开。减少安装次数。以相同定位、夹紧方式安装的工序,最好接连进行,以减少重复定位次数、换刀和夹紧次数。3.5 确定进给路线在数控加工中,刀具刀位点相对于工件运动的轨迹称为进给路线。进给路线不仅包括切削加工时的进给路线,还包括刀具到位、对刀、退刀和换刀等一系列过程的刀具运动路线。进给路线不仅
54、反映了几个内容,也说明了加工顺序。确定进给路线。主要是确定粗加工及空行程的进给路线,因为精加工的进给路线基本上是按零件的轮廓进行的。在确定时还要注意一些问题:(1)选择工件刚性破坏小的路线,以减少加工变形对加工精度的影响。(2)寻求最短的进给路线,以提高加工效率。(3)切入和切出的路线应考虑外延,以保证加工的表面质量。(4)完工时的最后一刀应一次走刀连续加工,以免产生刀痕等缺陷。此外,确定进给路线时,还要考虑工件的形状与刚度、加工余量大小、机床与刀具的刚度等情况,确定是一次进给还是多次进给来完成加工,确定刀具的切入与切出方向以及在铣削加工中试采用顺铣还是逆铣的铣削方式等。该零件的加工路线按照上
55、面的原则,首先我们要保证内外型面孔 10H7 位置精度。(1).铣平面:粗精铣下端面翻转工件粗精铣上平面。 (80 盘铣刀)(2).钻:钻通孔 10H7。 (9.6 钻头)(3).钻:预钻 20 的通孔。 (20 钻头)(4).钻:4-M10 的螺纹孔。 (8.5 钻头)(5).半精铣内轮廓:半精铣内轮廓至尺寸,单边留余量 0.3mm。 (16 立铣 刀)(6).精铣内轮廓:精铣内轮廓至尺寸。 (16 立铣刀)(7).铣孔:铣 16 的孔至尺寸 31.7mm。 (16 立铣刀)(8).镗孔:镗 32 的孔至尺寸要求。 (32 镗刀)(9).半精铣外轮廓:半精铣外轮廓至尺寸,单边留余量 0.3m
56、m。 (10 立铣刀)(10).精铣外轮廓:精铣外轮廓至尺寸。 (10 立铣刀)(11).铰孔:铰 10H7 的孔。 (10 铰刀)(12).攻螺纹:攻 4-M10 螺纹孔。 (M10 丝锥)(13).倒角:R3 的圆弧倒角。(14).铣曲面:加工曲面 R25 至尺寸。 (R5 球头铣刀)3.6 数控加工工序卡为了更好地指导编程和加工操作,把该零件的加工顺序、所用刀具和切削用量等参数编入下表 3-5 所示复杂零件数控加工工序卡中。表表 3-53-5 复杂零件加工生产加工工艺卡复杂零件加工生产加工工艺卡材料名称夹具名称使用设备45#钢机用平口钳数控铣床 XD-40A工序号工种工序内容刀具规格mm
57、备注1粗精铣下表面粗精铣零件下表面至Ra3.2150mm 面铣刀2粗精铣上表面粗精铣零件下表面至Ra3.2,保证:上下表面的平行度150mm 面铣刀3钻中心孔钻 10H7、32、4-M10的中心孔A2 中心钻3钻孔钻通孔 10H7。保证:10H7,102.2870.017mm。9.6 的麻花钻4钻孔钻通孔 20。保证:1360.02mm。20 的麻花钻5钻孔钻螺纹孔 4-M10。保证:960.1 , 760.18.5 的麻花钻6铣内轮廓保证:,046. 0080,Ra1.6um。054. 0010016 的立铣刀 7铣外轮廓保证:,80.05,30.92027. 001280.1,Ra1.6u
58、m10 的外铣刀8铣孔铣 32,保证:保证31.7mm 的尺寸精度16 的立铣刀9镗孔镗 32,保证:,1360.02mm。039. 003232 的镗刀10倒角倒 R3 圆角。10 的立铣刀11攻螺纹4-M10 孔螺纹的加工10 的丝锥12曲面圆弧曲面的加工。保证:Ra3.2umR5 的球头刀 第四章 UG 加工和编程设计UG 是一种功能强大的软件,在本零件的造型中我们用到的是 UG 的建模和加工模块。4.1 加工并生成程序 通过草图拉伸对毛坯进行设定,同时要确定毛坯中心在系统坐标系(绘图坐标系)中的坐标值。因为该例绘图原点在图形的底平面上,所以毛坯中心的坐标值设定值为(0,0,0) 。注意
59、对刀时,刀具找正毛坯中心后,要按该坐标值设定毛坯中心。然后进入 UG 加工模块,首先设定加工坐标系、工件加工的安全平面,对工件进行加工。4.1.14.1.1 工艺参数设定工艺参数设定首先我们定义刀具参数,根据列出的刀具清单。例如 12 立铣刀参数及图形如图 4-1、4-2 所示,其它刀具按照各自参数设定。图图 4-14-1 刀具显示刀具显示 图图 4-24-2 创建刀具创建刀具4.1.24.1.2 生成加工轨迹生成加工轨迹在加工中我们一般用到的加工方法有四种:mill planar(一般平面铣) 、mill contour(型腔铣) 、fixed contour(固定轴铣) 、drill(钻、
60、镗孔) 。在该零件的加工中,我们也用到上述四种加工方法。在这里我们例举件一薄壁a 的加工进行说明,薄壁 a 分为内型腔和外轮廓,其加工路线是粗加工、半精加工、精加工。内型腔加工粗加工时选择并输入图 4-3、图 4-4、图 4-5 的内容,选用一般平面铣,刀具选择 16 的。 图图 4-34-3 确定加工内容确定加工内容图图 4-44-4 进给和速度进给和速度 该零件所有加工轨迹完成后如图 4-5 所示,并要对其轨迹进行 3D 仿真加工,看看还有哪些地方未加工到。是否产生刀具干涉,轨迹是否需要编辑,最后确定后即完成加工轨迹生成。图图 4-54-5 刀轨刀轨4.1.34.1.3 生成部分程序生成部
61、分程序 所有加工轨迹完成后,要对其进行后置处理,生成加工程序。首先选择要输出程序的项,再点击“输出CLSF” ,设置好参数如图4-6自动即生成程序。图图 4-64-6 后处理后处理4.1.44.1.4 例举自动生成的程序例举自动生成的程序 本节只例举圆弧曲面的自动加工程序,其他程序见附录。如图 4-7 图图 4-74-7 圆弧曲面加工圆弧曲面加工自动生成程序如下:N0010 G40 G17 G90 G70N0020 G91 G28 Z0.0:0030 T00 M06N0040 G0 G90 X-.7855 Y-.9459 S800 M03N0050 G43 Z.1315 H00N0060 G1
62、 Z-.3664 F9.8 M08N0070 Y.8333N0080 Y.9519 Z-.3673N0090 X-.7801 Y.9909 Z-.367N0100 X-.7669 Y1.0281 Z-.3668N0110 X-.7465 Y1.0619 Z-.3666N0120 Y1.0536 Z-.3426N0130 Y1.0453 Z-.3278N0140 Y1.0287 Z-.3077N0150 Y1.0121 Z-.2942N0160 Y.9955 Z-.2848N0170 Y.9789 Z-.2785N0180 Y.9623 Z-.2749N0190 Y.9291 Z-.2736N0
63、200 Y-.9292N0210 Y-.9624 Z-.2749N0220 Y-.979 Z-.2786N0230 Y-.9956 Z-.2848N0240 Y-1.0121 Z-.2942N0250 Y-1.0287 Z-.3078N0260 Y-1.0453 Z-.3279N0270 Y-1.0536 Z-.3428N0280 Y-1.0619 Z-.3669N0290 X-.7283 Y-1.0829 Z-.3666N0300 X-.7072 Y-1.1011 Z-.3664N0310 Y-1.0925 Z-.3358N0320 Y-1.0839 Z-.3174N0330 Y-1.066
64、7 Z-.2922N0340 Y-1.0495 Z-.2745N0350 Y-1.0323 Z-.2614 N0360 Y-.9979 Z-.2442N0370 Y-.9634 Z-.2362N0380 Y-.8946 Z-.2351N0390 Y.8946N0400 Y.9634 Z-.2362N0410 Y.9978 Z-.2442N0420 Y1.0323 Z-.2614N0430 Y1.0495 Z-.2745N0440 Y1.0667 Z-.2922N0450 Y1.0839 Z-.3174N0460 Y1.0925 Z-.3357N0470 Y1.1011 Z-.3664N0480
65、 X-.6882 Y1.1136 Z-.3663N0490 X-.6679 Y1.1238N0500 Y1.115 Z-.3319N0510 Y1.1063 Z-.3117N0520 Y1.0887 Z-.2838N0530 Y1.0712 Z-.2633N0540 Y1.0536 Z-.2472N0550 Y1.0185 Z-.2245N0560 Y.9834 Z-.2117N0570 Y.9482 Z-.207N0580 Y-.9482N0590 Y-.9833 Z-.2117N0600 Y-1.0185 Z-.2245N0610 Y-1.0536 Z-.2472N0620 Y-1.071
66、1 Z-.2633N0630 Y-1.0887 Z-.2838N0640 Y-1.1063 Z-.3117N0650 Y-1.115 Z-.3319N0660 Y-1.1238 Z-.3663N0670 X-.6285 Y-1.1361N0680 Y-1.1272 Z-.3296N0690 Y-1.1183 Z-.3064N0700 Y-1.1006 Z-.2728N0710 Y-1.0828 Z-.2485N0720 Y-1.0651 Z-.2301N0730 Y-1.0473 Z-.2156N0740 Y-1.0296 Z-.2041N0750 Y-.9941 Z-.1888N0760 Y-.9586 Z-.1819N0770 Y-.9231 Z-.1813N0780 Y.7101N0790 Y.9231N0800 Y.9586 Z-.1819N0810 Y.9941 Z-.1888N0820 Y1.0296 Z-.2041N0830 Y1.0473 Z-.2156N0840 Y1.0651 Z-.2301N0850 Y1.0828 Z-.2485N0860 Y1.1006 Z-.2728
- 温馨提示:
1: 本站所有资源如无特殊说明,都需要本地电脑安装OFFICE2007和PDF阅读器。图纸软件为CAD,CAXA,PROE,UG,SolidWorks等.压缩文件请下载最新的WinRAR软件解压。
2: 本站的文档不包含任何第三方提供的附件图纸等,如果需要附件,请联系上传者。文件的所有权益归上传用户所有。
3.本站RAR压缩包中若带图纸,网页内容里面会有图纸预览,若没有图纸预览就没有图纸。
4. 未经权益所有人同意不得将文件中的内容挪作商业或盈利用途。
5. 装配图网仅提供信息存储空间,仅对用户上传内容的表现方式做保护处理,对用户上传分享的文档内容本身不做任何修改或编辑,并不能对任何下载内容负责。
6. 下载文件中如有侵权或不适当内容,请与我们联系,我们立即纠正。
7. 本站不保证下载资源的准确性、安全性和完整性, 同时也不承担用户因使用这些下载资源对自己和他人造成任何形式的伤害或损失。