4s店车间主任述职报告
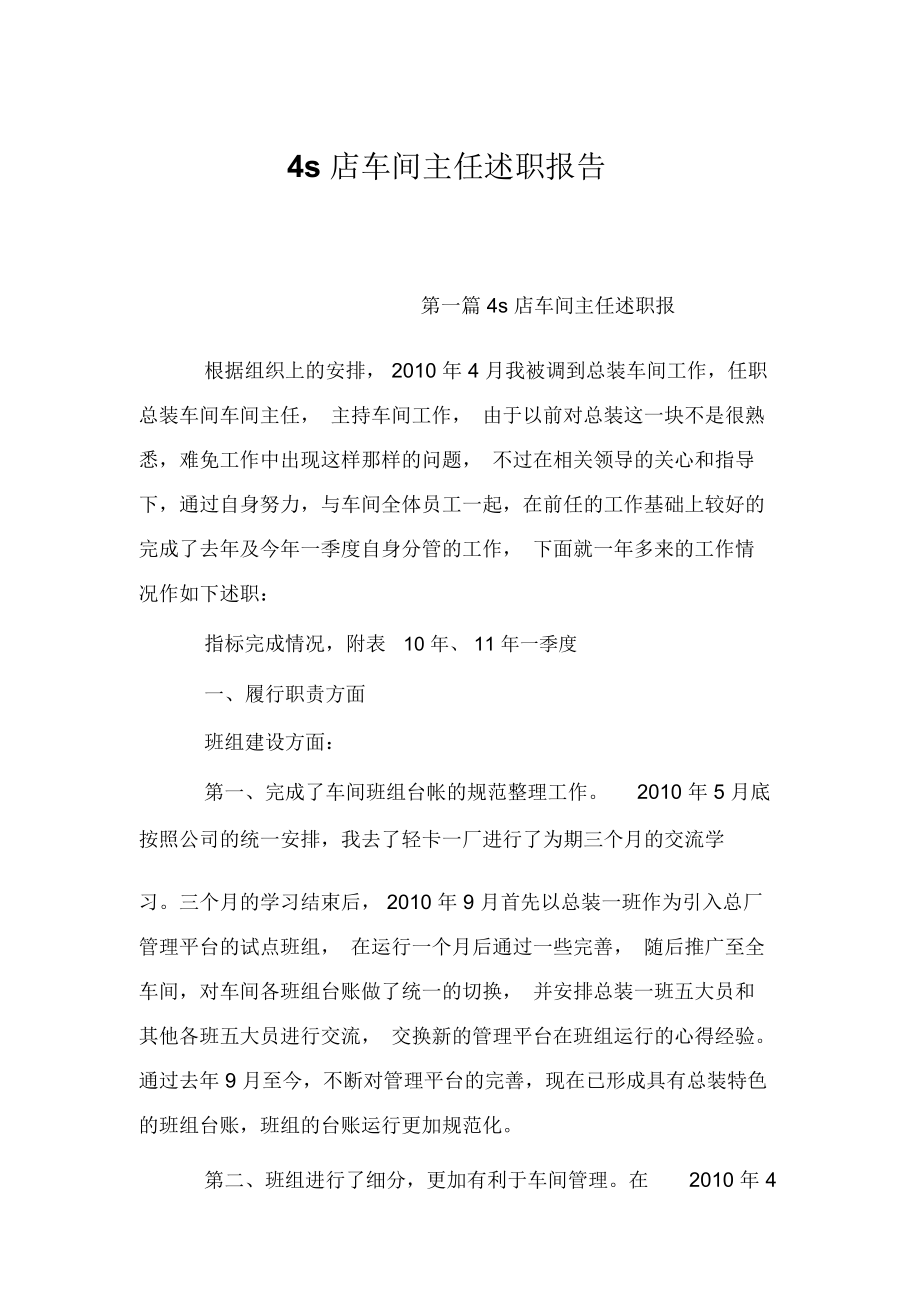


《4s店车间主任述职报告》由会员分享,可在线阅读,更多相关《4s店车间主任述职报告(10页珍藏版)》请在装配图网上搜索。
1、4s 店车间主任述职报告第一篇 4s 店车间主任述职报根据组织上的安排, 2010 年 4 月我被调到总装车间工作,任职总装车间车间主任, 主持车间工作, 由于以前对总装这一块不是很熟悉,难免工作中出现这样那样的问题, 不过在相关领导的关心和指导下,通过自身努力,与车间全体员工一起,在前任的工作基础上较好的完成了去年及今年一季度自身分管的工作, 下面就一年多来的工作情况作如下述职:指标完成情况,附表10 年、 11 年一季度一、履行职责方面班组建设方面:第一、完成了车间班组台帐的规范整理工作。2010 年 5 月底按照公司的统一安排,我去了轻卡一厂进行了为期三个月的交流学习。三个月的学习结束后
2、, 2010 年 9 月首先以总装一班作为引入总厂管理平台的试点班组, 在运行一个月后通过一些完善, 随后推广至全车间,对车间各班组台账做了统一的切换, 并安排总装一班五大员和其他各班五大员进行交流, 交换新的管理平台在班组运行的心得经验。通过去年 9 月至今,不断对管理平台的完善,现在已形成具有总装特色的班组台账,班组的台账运行更加规范化。第二、班组进行了细分,更加有利于车间管理。在2010 年 4月总装线只有两个班组,调试是一个班组, 6 月份刚成立的内饰当时也是一个班组, 后随着员工队伍的壮大, 原先的班组划分已经跟不上车间的发展了,于是我结合总厂学习的经验及时调整了车间班组划分,将大班
3、化为小班,保持每班人数在 20 人左右,并设立了内饰、总装、调试三个工段, 10 年 11 月上装划回总装后,又设立了上装工段。现车间有 13 个班组 4 个工段,车间各项工作业务内容划分清楚,使车间管理工作能更加有效的开展。第三、创建精益班组、安全合格班组及质量信得过班组。2010年带领全车间员工,并通过一起努力,创建精益班组 1 个,安全合格班组 13 个,质量信得过班组 2 个。车间每月对班组台账运行符合性进行一次检查, 车间留有检查记录。 通过检查及时发现班组管理存在问题,并跟踪班组整改,保证班组基础管理能有效开展。车间要求班组坚持每周开展一次安全隐患排查并留有记录, 同时车间每天有专
4、人检查现场的安全生产并检查班组隐患记录整改情况。车间各班组自 2010 年 4 月至今无一起轻重伤事故。车间在 2011 年年初组织各班组对车间质量目标分解, 指导班组按照目标进行各班组质量目标控制措施的制定,保证质量工作能落到实处。生产组织方面:第一、不折不扣完成生产任务。2010 年车间全年共生产工程自卸车 11088 台、好运 3160 台。车间根据计划安排的不同灵活调整车间的生产方式, 在高产期,由于调试产能不足, 当时就增开了夜班,保证了总装在高产时仍能按时按量完成了生产计划。在 2010 年 10 月份就开始了产能提升计划的策划, 通过工序优化重组、员工技能提升、工艺步骤的改造,现
5、在轻型系列工程车生产节拍已能达到4.5min/ 台,日产能达到 120 台,能充分应对 2011 年的生产高峰, 元月份 21 天的生产日,生产工程车和好运共计2016 台,三月份生产工程车和好运共计划台,二次更新了单月最高产量。驾驶室内饰生产从无到有,生产能力从 2010 年 8 月份每天五台,逐步提升到 2010 年三月底的每天 50 台,增加了产品的自制能力和控制能力。第二、大线物料配送方式整合。 总装车间原有的物料配送方式为材料员点料直接送上线, 大线物料比较混乱,缺料情况不清楚。 2010年 9 月我开始推行上线点料, 推行模式为线上每位员工点自己装配的物料,物料不准确和缺料由员工自
6、己上报班长,班长进行跟踪,保证了大线物料的顺畅。在推行一段时间后,对线上物料员进行了裁剪,将总装线原有的 4 名材料员精减为 2 名。安全现场方面:第一、车间油污重点整治。在刚接手车间工作时,发现车间几个存放油品及车辆下线区油污比较多。 通过了解明确了整改时间和相关整改措施,同时责任到岗位,车间现场油污得到根治。从2010 年4 月至今通过巩固措施,防止现场油污现象的回潮。还将油污治理列入车间现场检查的必查项。第二、车间工位器具适用性完善。 车间根据生产线特点对线上没有货架摆放的物料制作专用的货架摆放, 对线边不适宜货架进行整改和重新制作替换。 总装线和内饰线工位器具经过几轮增补, 现已无物料
7、落地现象。车间及时对新增工位器具定置、定容、定量,保持工位器具在现场摆放的有序性。第三、上装、调试现场的专项整治初显成效。上装在2010 年11 月刚划到总装时,占道作业和交叉作业比较严重,车间进行专项整治,现在现场占到作业已杜绝,交叉作业也大幅降低。调试工段物料摆放杂乱,根据这一情况车间制作了专用货架用于摆放物料, 现场维护主要采取动态维护,调试现场环境管理得到大幅改善。第四、车间建立安全巡视制度。 车间管理人员每天对现场进行一次现场检查, 车间安全员不定时巡查生产现场, 确保每天能安全生产。车间通过全体员工的一起努力,全年车间无一起轻重伤事故,并在 2010 年荣获了“省机械行业安全生产示
8、范车间”的称号。管理标准方面第一、牵头完善了车间班组管理的制度和管理台帐的内容的划分,使班组管理按达标的要求,有管理运行标准和操作运行平台。 11年元月份又结合每月的检查和改进项对班组管理制度进行新的一轮的完善。第二、牵头重新编制完成了车间级的管理制度和管理标准。使车间管理进一步向规范化的道路上迈进。11 年三月份对车间各类油品的月统计分析工作作了细化,并形成车间管理规定。第三、组织车间内饰、 调试两个工段的对作业标准符合性的再梳理和再细化,并在此基础上进行定产量的定岗定编工作。在11 年的三月份对生产大线和上装工段进行了定岗定编的梳理工作,已完成。三月份对前期出质量问题点情况较为严重的大线两
9、个点、二线和内饰各一个点, 进行了排查,已初步编制了增加控制能力质量控制点措施,对相关点的“三检制”逐步落实责任做到相关工序人人知、人人行。二、思想政治、廉政建设方面1 、思想政治方面: 2010 年,公司经常组织中干去集团学习党员先进事迹,公司内部开展各种会议精神的学习,通过该渠道,我也了解了国家的相关政策、 公司及厂的相关信息, 对自身工作的方向性有了很好的指引。在自身的业务学习上,今年主要通过领导干部的 “廉政教育”活动,树立了自身学习的榜样,制定了学习方案,对车间的相关制度、工艺原理和项目改造情况等进行了详细学习, 使自身业务能力逐步得到了提高。2 、廉政建设方面:自 10 年 4 月
10、到总装车间工作以来,我时刻提醒自己,工作上要经得起诱惑, 顶得住压力,干好自己的本职工作。同时做工作一定要就事论事,一视同仁,经得起同事、员工和领导的检验。另外在车间管理层建设方面, 车间内部在作出各种决定之前都要经过车间管理成员集体讨论通过,小到各种奖罚、评优创先,大到各种绩效奖励方案的制定等, 这充分体现了车间管理上民主管理、 团结协作的优良作风,同时对个人的廉政自律也提到了积极的作用。3. 在车间建立了管理人员与班组长的日对接管理示范会, 在每天下班后进行当日问题的沟通和明确责任,确定改进时间和运用方法,同时要求各班班长每天在晨会上要针对性的进行管理要求的再传递,以达到一级教育一级,一级
11、示范给一级看的目的。11 年又做了进一步改进,要问题发生责任人在第二天对接会上对前一天问题落实情况进行回复,以达到改进措施不落空的目的。三、存在的问题1 、车间在基础管理工作方面底子还很薄,因此执行中的符合性与标准化的要求差距还很大, 还存在应付检查的情况, 在达标控制方面还有待加强,真正的按标准干上还要做大量工作和努力 ;2 、车间在安全现场、质量控制、环境管理、成本管理、设备管理方面,管理理人员的实际运作水平不高, 专业管理知识学习有待提高 ;3 、工作中出现问题时积极主动性不够,存在等靠现象 ;四、今后努力方向1 、在 10 年工作基础上, 11 年要强化班组建设等基础工作,尤其是台帐运
12、行符合性和制度管理执行的掌握上要下狠功夫, 让工作执行标准常态化,减少应付随意的工作现象 ;( 具体执行在车间基础管理提升计划中 )2 、通过各种渠道了解和学习相关专业管理知识,解决自身管理瓶颈,同时作好传帮带,带领车间的相关管理人员学习和管理突破 ;( 具体执行在党员争先创优承诺措施中 )3 、在车间强调、强化工作的主体意识,积极主动介入自身工作,不等不靠, 按照工作职责及业绩合同要求主动开展自身工作,尤其今年是公司“十二五”战略的开端年,一定要打好开门仗,重点是安全、质量目标的实现和员工技能的培训( 装配工和调试工多能工的培训 ) ,其次是车间的MCU、TPM工作在每月的落实。 ( 具体执
13、行在车间每月重点计划中 )以上就是我 10 年度及 11 年第一季度的述职情况, 有不当之处,请批评指正。第二篇 4s 店车间主任述职报2010年已经过去,在这一年的时间里,我车间在厂里各级领导的正确指导下, 认真贯彻落实我厂2010 年安全生产目标, 按照“安全第一,预防为主,综合治理”的安全指导思想,全面建立并推行HSE管理体系。目前已全面完成了厂里的各项任务,先将2010 年工作述职如下。一.生产及产品质量管理方面1. 截止到年底,我车间一二期装置共加工三混18835.58 吨,全年回收率 93.5%,产品入库合格率百分之百。2. 二期工业萘装置利用检修期间共加工混合洗油1580 吨,其
14、中轻质洗油 948 吨,轻质洗油回收率60% 。3. 洗涤装置生产含酚的调节, 过去我们洗涤工段生产的中性酚钠的含酚比较低,游离碱高 ; 含酚不仅达不到产品质量指标,而且游离碱高还导致了碱的浪费。 今年在厂领导的指导下, 我制定了一系列提高含酚,降低游离碱的措施 ; 一、规定了稀碱与三混比例 0.35 :1,二、统一了稀碱浓度,提高稀碱浓度由原来的1012%提高到 12%14%,三、少加稀碱,少排酚盐; 加多少稀碱出多少酚盐; 四、不允许中钠产出后在进行返洗; 经过一段时间严格控制及调节中钠含酚提高至 20%以上,游离碱降至 1.5%以下,含酚不仅达到产品质量指标,而且还降低了碱的浪费,降低了
15、生产成本。4. 今年常遇到的洗涤连洗塔不分层的问题。 我们及时召集洗涤各班长及主操分析原因, 主要因是用碱钠配碱及碱钠带油所致, 因此我们及时制定实施措施。 从而解决了不分层的原因, 但是一期洗涤送酚盐管线还有待与 2011 年整改。具体措施:一、不允许用中钠或碱钠配碱 ; 二、不允许酚盐返洗 ; 三、不允许工业萘的酚盐送至洗涤碱钠槽; 必须送至原料槽 ; 四、严格控制二次保证已洗不能带酚盐, 从而减少工业萘返回的酚盐 ;5. 一期工业萘精塔塔压高, 从 8 月份开始一期工业萘塔压开始超压,压力一直居高不下 ; 这种情况在别的焦油厂从没出现过,我们也没有别的经验借鉴, 只能自己摸索。 因此在厂
16、领导的指导下我们及时分析原因,一方面我们制定塔压高时的控制措施 ; 另一方面并制定了整改检修方案,经过我们两次检修整改终于消除了塔压高这一安全隐患。6. 检修方面,全年一二期装置共组织全面检修 4 次,每次检修都按照 HSE管理体系要求做好检修计划、检修方案、危害因素辨识,并组织全员学习, 充分保证了检修的安全质量。 检修期间我们车间全体员工面对检修任务重, 发扬不怕苦不怕累的精神, 加班加点圆满完成了各项检修任务。 从而保障了全车间后续生产的顺利进行, 为全面完成 2010 年度生产目标打下了坚实的基础。二、安全方面1 、安全培训, 全面完成 2010 年员工培训任务。 2010 年,根据上
17、级的培训要求, 我们制定了详细的培训计划。 为了能够较全面的掌握专业知识和培养大家养成良好的学习习惯, 我们把业务培训工作日常化、制度化, 重点的学习了操作规程、各种产品的性质及各种应急预案等内容, 对提高大家安全意识、 工作能力起到了良好的促进作用。2 、根据厂里要求,我们在 2010 年初制定了车间安全、环保责任状,并分解细化到班组和个人。在2010 年一年的时间里,我们按照安全目标和工作要点的要求开展安全工作,全面完成了各项安全工作责任目标。3. 积极组织开展各种安全活动。每天的班前会各班组都必须组织学习安全知识 ; 车间安全综合素质的整体水平得到了提高。认真学习事故案例、编写事故预案、
18、进行事故演习及事故反思。另外,针对可能出现的不同应急事故,我们编写了各种应急事故预案,2010年我们车间组织了停水、停电、停煤气事故等演习,通过演习,员工应对处理突发事故的能力得到了锻炼和提高,在演习中也增强了团结协作的能力。三、 HSE体系建设与推进1 、组织全员参与对危害因素、环境因素进行辨识,并制定危害因素消减措施及管理方案 ;2 、进一步完善事故应急预案,提高预案有效性和可操作性;3 、完善并统一 HSE体系运行中的各种记录 ;4 、将 HSE体系运用到生产检修过程中去,每次开停工、检修都能按照 HSE要求执行 ;回顾 2010 年的工作,我们也清醒地认识到在工作中仍存在问题和不足,例如在隐患整改方面有时还不够及时、精细化管理尚需深入,有些新员工安全意识仍相对薄弱等,因此,在新的一年里,将会一如既往的发扬严、勤、细、实的工作作风,抓好安全生产,努力实现 2011 年的各项工作目标,为车间生产提供安全、稳定、环保的工作环境。
- 温馨提示:
1: 本站所有资源如无特殊说明,都需要本地电脑安装OFFICE2007和PDF阅读器。图纸软件为CAD,CAXA,PROE,UG,SolidWorks等.压缩文件请下载最新的WinRAR软件解压。
2: 本站的文档不包含任何第三方提供的附件图纸等,如果需要附件,请联系上传者。文件的所有权益归上传用户所有。
3.本站RAR压缩包中若带图纸,网页内容里面会有图纸预览,若没有图纸预览就没有图纸。
4. 未经权益所有人同意不得将文件中的内容挪作商业或盈利用途。
5. 装配图网仅提供信息存储空间,仅对用户上传内容的表现方式做保护处理,对用户上传分享的文档内容本身不做任何修改或编辑,并不能对任何下载内容负责。
6. 下载文件中如有侵权或不适当内容,请与我们联系,我们立即纠正。
7. 本站不保证下载资源的准确性、安全性和完整性, 同时也不承担用户因使用这些下载资源对自己和他人造成任何形式的伤害或损失。