装载机液压系统设计
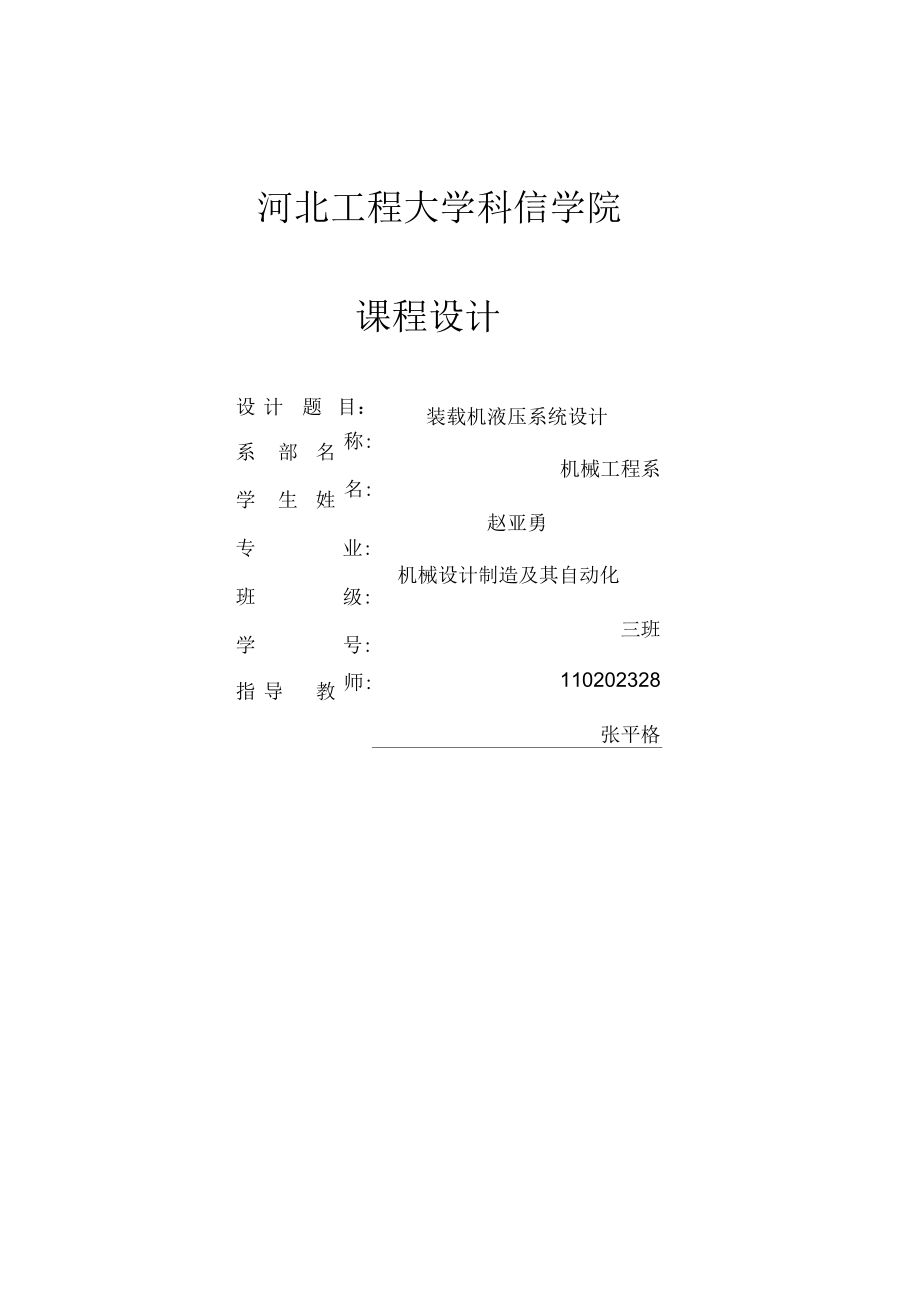


《装载机液压系统设计》由会员分享,可在线阅读,更多相关《装载机液压系统设计(39页珍藏版)》请在装配图网上搜索。
1、设计题目:系部名称:学生姓名:专业:班级:学号:指导教师:河北工程大学科信学院课程设计装载机液压系统设计机械工程系赵亚勇机械设计制造及其自动化三班110202328张平格填表时间:201501 月摘要装载机主要用来装卸散状物料,也能进行轻度的铲掘工作,并且具有良好的机动性能,广泛使用于工厂、矿山、建筑、水电上程、道路、码头、农田乃至家庭,是工程机械中保有 量较大的品种之一。装载总体方案设计是装载机设计的一个重要环节,它对装载机的设计质量、使用性能和装载机在市场上的竞争力有着决定性的影响。装载机性能的优劣和作业效率的发挥,不仅与相关总成及部件的工作性能有着密切关系,而且在很大程度上取决于各有关总
2、成及部件间的协调和参数匹配,取决于装载机的总体布置。装载机的工作装置和转向机构都采取液压传动,本文通过对工作装置及转向机构工作要求和载荷分析对液压系统进行设计。主要包括对执行元件,控制元件辅助元件的选择、设计。本文的设计,能够使读者对工程机械总体方案设计及液压系统设计进一步加深了解,同时能从中理会一些设计理念,为以后更好从事设计工作提供了帮助。关键词:装载机;液压传动;液压系统设计;绪论 11履带式装载机总体参数确定 21.1履带式液压装载机的组成 21. 2设计依据21 . 3传动方式31 . 4主要参数的确定31.5 行走装置的牵引力61.6 液压马达主要参数计算确定 61.7 缓冲张紧装
3、置设计要求与计算 71.8 四轮一带及其他部件选型 72液压系统的初步介绍 132.1液压系统的工作原理 132. 2液压系统的组成部分132.3技术要求 133液压系统的设计 153.1 制定液压系统方案 153.2 绘制液压系统原理图 173.3 确定液压系统的主要参数 183.4 液压元件的选择与专用件设计 223.5 液压系统的性能验算 253.6 液压系统冲击压力 294动臂液压缸的设计 304.1 液压缸的结构参数计算 304.2 液压缸的连接计算 314.3 活塞杆活塞杆强度及稳定性验算 32总结 354.4 献 36绪论装载机是一种常用的铲土运输机械,广泛应用于公路、铁路、建筑
4、、水电、 港口、矿山及国防工程中。具对加快工程建设速度,减轻劳动强度,提高工程质 量,降低工程成本等都发挥着重要的作用。因此,近年来,装载机在国内外均得 到了迅猛的发展,已成为工程机械的主导产品之一。一台装载机的设计是否成功,首先是从能否满足使用要求,好造、好用、好 修,具备较高的作业生产率和较低的使用成本来衡量的。这体现在设计工作中, 就是应当使装载机具有较完善的技术经济性能与指标以及先进的部件结构方案。常见的单斗装载机一般有以下特点来分类。(1)按行走装置不同分类:轮胎式和履带式。国产履带式装载机多是在推土机基础上形成及国内外使用和生产的绝大多数是轮胎式装载机,这两类装载机除行走装置不同外
5、,其它系统和构造大体相似。(2)按使用场合不同分类:露天用装载机和井下用装载机(铲运机) 。国内 外生产和使用的装载机绝大多数是露天轮式装载机。铲运机的结构相对来说是比 较简单的。(3)按传动形式不同分类:机械传动式,液力机械传动式,液压传动式和电传动式。机械传动式在国内仅用于 0.5m3以下的装载机,它一般直接采用汽车或 拖拉机的传动装置,即离合器和变速器。由于液力传动机械取消了机械传动中的离合器而换用液力变矩器, 取消了人 力换挡变速箱而换用了动力换档变速箱, 是发动机在不停车的情况下换挡,操作 轻便,工作可靠性高,因此液力机械传动式是轮式装载机的主要传动形式。液压传动使用柴油机带动液压泵
6、产生高压油,并通过控制系统和油管带动液 压马达使车轮传动。它能够简化传动系统,使整机质量减轻,但由于启动性差, 液压件价格昂贵,寿命也比较低,因此目前仅用于小型装载机上。电传动是由柴油机驱动交流发电机,以此来驱动装在车轮上的直流电动机, 然后通过轮边减速器带动车轮转动,这样可以实现无级调速。这种传动检查方便, 维修简单,工作可靠。缺点是电机设备质量大,费用高,目前只在大型装载机上 使用。(4)按装载方式不同分类:前卸式,后卸式,侧卸式和回转式。(5)按转向方式不同分类:整体式和较接式。履带式装载机总体参数的确定1.1. 履带式液压装载机的组成液压装载机机主要由发动机、液压系统、工作装置、行走装
7、置和电气控制等 部分组成。液压系统由液压泵、控制阀、液压缸、液压马达、管路、油箱等组成。 电气控制系统包括监控盘、发动机控制系统、泵控制系统、各类传感器、电磁阀 等,如图。图2 瓶带式装载机结构图1 行走机构2爱动扪3动智4争斗5转.油&动1T油缸 7驾城!T氏渴油箱1.2. 设计依据1.2.1. 履带式行走装置的主要特点(1)牵引力大(通常每条履带的牵引力达机重的35-40%),接地比小(一般为4-15N/cm2),转弯半径小,机动灵活;(2)采用液压传动,能实现无极调速;(3)每条履带各自有驱动的液压马达及减速装置。1.2.2. 设计参数(1)机重18t(2)总牵引力10KN(3)最大行走
8、速度2.2Km/h(4)驱动轮节圆直径323mm(5)减速器传动比4(6)动臂提升时间选8s(7)动臂不降时间选6s(8)铲斗前倾时间选3s装载机的外形尺寸,可以根据举升高度、卸载跑离、轮距、轴距、算出整机的长、宽、高。外形尺寸名称几何尺寸车长7080mm总宽度2940mm车局3370mm轴距2760mm轮距2200mm最小离地间隙300mm最大卸载高度3050mm1.3. 传动方式考虑到装载机一般在野外作业,工作载荷变化大,作业环境恶劣,技术保养 条件差;因此本设计采用了履带式行走装置。确定的行走装置的动力路线为:柴油机一液压泵一控制阀一液压马达一制动 器一减速器一驱动轮一履带1.4. 主要
9、参数确定1.4.1. 机体主要线性尺寸在本次设计中按照标注选定法、理论分析计算法等方法得出的参数值不可能都是完全切合的。通常在设计开始时一些参数还不能利用以上方法完全确定,因此在本设计中有的参数采用了经验公式法进行计算。(1)履带带长L1L1 = K a G1/ 3=1.25 (18 109) 1/ 3=3276mm式中:K a为尺寸系数(1.25 1.5),本设计取 Ka =1.25;考虑到整体布局,类比同型产品可在此基础上增大10%;故Li取为3604mm。(2)驱动轮与导向轮轴向中心距lili= K i G1/ 3 =1.1*(18*10 9)1/3=2880mm式中:Ki为尺寸系数(1
10、.0 1.2)。考虑到整体布局,类比同型产品可在此基础上增大10%;故11取为3281mm。(3)轨距BB= k b G1/ 3=0.8*(18*10 9)1/3=2100mm式中:K b为尺寸系数(0.75 0.85)。考虑到整体布局,类比同型产品可在此基础上增大10%;故B取为2400mm(4)履带高度HH= KTG1/ 3 =0.32*(18*10 9)1/3=840mm式中:Kt为尺寸系数(0.3 0.35)。为了整体的整体布局,考虑将其扩大17%左右,计算得H=980mm。(5)履带板宽b由经验数据得:b的值可在600 800mm问取值,根据标准手册查取b =600mm。(6)底盘总
11、宽CC =B +b =2400+600=3000mm(7)履带接地长度L接L 接=11 + 0.35D= 11 + 0.35( L1 - l1)=3394mm式中:D为驱动轮直径,约为L1 - 11o(8)后端支重轮到驱动轮间距C3C3 = K C1 lt=2.6 84=218mm式中:KC1为尺寸系数(2.4 2.6);1t为履带节距,根据标准查取1t =84mm。(9)前端支重轮到导向轮间距 C1C1 = K c 2 1t =3 84 =252mm式中:K c 2为尺寸系数(2.4 3)。(10)两端支重轮间距lolo = 11- C1 - C3=3281-252-218=2811mm(1
12、1)转台离地高hihi = Ko G1/ 3 =1048mm式中:K o为尺寸系数(0.37 0.42)。为了整体的整体布局,考虑将其扩大 3%左右,计算得h1=1080mm。(12)相邻两支重轮间距t1t1 =(1 2) lt =2*84=168mm机体主要线性尺寸如下表:机体主要线性尺寸项目履带长度L1轨距B轮距11履带总高H转台底部离地高h1悬架底离地高h2履带板宽b结果36042400328198010804956001.4.2. 驱动轮参数(1)主要参数的确定A、节距:驱动轮节距应与履带节距相等,lt 84 mm。B、齿数:增加驱动轮齿数Z,能使履带速度均匀性改善,摩擦损失减少,但会
13、 导致驱动轮直径增大,引起机重和整机高度的增加。驱动轮齿数一般为奇数,使 得啮合过程中每个齿都能和节销啮合。其齿数通常取23 27,本设计中取Z =23。C、驱动轮直径的确定:323mm。1.4.3. 功率及其他参数计算与确定(1)发动机功率N ,根据经验公式估算:N 17.7 92.7Q 17.2 92.7 0.7 82.09Kw式中:Q为斗容量 0.7m3。考虑到柴油机的功率必须充分满足主机工作过程的动力要求,取发动机功率为90千瓦,在设计允许范围内。(2)液压功率P,根据经验公式估算:P=(0.75 0.88) N=0.75 90=67.5Kw式中:N为发动机功率。(3)最大转弯力矩Mw
14、Mw Kw G4/3=0.3*0.6*18 4/3=8.49吨米式中:Kw为转弯系数(取0.3);为摩擦系数(不良路面取0.6)。(4)平均接地比压PcPc=K pc3 G =0.25*18 0.655 Kg/ cm2式中:Kpc为接地比系数(取为 0.21 0.28)1.5. 行走装置的牵引力牵引力是液压装载机行走装置设计计算的主要内容之一,但本设计确定总牵引力为10KN对行走装置来说实际上是在已定的功率条件下验算装载机的行走速 度、爬坡能力和转弯能力。1.6. 液压马达主要参数计算确定(1)液压马达输出转速non i v/兀 D =4 0.61/3.14 0.323 =2.4r / s(2
15、)液压马达的最大负载力矩MmMm= kFD?/ni=21N.M(3)马达理论排量qq= M m/(pm/m)式中:Pm -马达有效工作压力;m-马达机械效率,本次设计中采用柱塞式马达,其效率m取值为(09 0.95)。 马达有效工作压力Pm可由下式确定:pm= ph-p式中:ph-为回油背压,取值范围为 0.5 1MPa ;p j为压力损失,参考同类型7压挖掘经验数据取值3 4MPa ;pb-为液压泵的出口压力,15吨以上的中型机械普遍采用中高压压力:25MPapb 32MPa ,本次设计中取pb = 25MPa 。计算得:pm=25-4-1=20 MPa将已知数据代入式(3.55) : q=
16、705/ (20*0.9) =39.17ml/r所以每分钟排量q1计算如下:q1=q nm=39.17 1563.43 = 61.23_/min1.7.缓冲张紧装置设计要求与计算缓冲张紧装置设计要求应包括以下几个方面:(1)缓冲弹簧应有必要的预紧力,防止车辆正常行驶时因履带跳动而使张紧装 置后移。(2)缓冲弹簧应有必要的弹性行程,防止行走机构遇障而张紧零件过载。(3)张紧装置要有一定的调节行程,方便因履带过松时取下一块履带板后,张 紧装置仍然可以调节履带板的松紧度。(4)当张紧轮和缓冲弹簧之间装变杠杆比机构时,张紧轮上的附加载荷不能增 加过大。1.7.1 张紧弹簧的设计履带张紧装置缓冲弹簧的作
17、用是:保证适当的履带张紧力;当导向轮受到前 方的冲击载荷时,缓冲弹簧回缩以吸收振动防止履带和驱动轮损坏。因此在对张 紧装置缓冲弹簧进行设计时,必须考虑到两个重要问题是弹簧的预载和缓冲量。(1)履带的张紧度hh = (0.03 0.06) L =0.045 3281 =147.6mm式中:L为张紧轮与驱动 轮问。(2)静态张紧力TeTe = (0.25 0.30) G =0.3*18 =5.4t(3)缓冲装置的预紧力 Ph 1和最大弹性行程时的张力PH2张紧装置最小工作载荷F1为:F1 = Te =5.4t张紧装置最大工作载荷F2为:F2 = (0.6 0.9) G=0.6 18 =10.8t张
18、紧装置极限工作载荷F3为:F3 =(1.2 2) G =1.2 18=21.6t取最大行程时的张力Ph 2 =F2 =10.8t,取预紧力Ph i = F 1=5.4t1.8. 四轮一带及其他部件选型1.8.1 四轮一带选型履带与其所绕过的驱动轮、导向轮、支重轮及拖链轮组成“四轮一带”, 是 履带式行走装置的重要零部件,它直接关系到挖掘机的工作性能和行走性能。这 部分的重量相当大,约占整机的1/4 ,制造成本高,约占整机的1/4.因此,合 理设计“四轮一带”具有重要的意义。履带的选取履带将挖掘机的重力及工作和行走时的载荷传给地面。其形状和构造必须考 虑到机械的稳定性和适应于各种工况的工作, 行
19、走时,还要保证发出足够的牵引 力。履带的结构有整体式和组合式两种。(1)整体式履带整体式履带是在履带板上带啮合齿, 直接与驱动轮啮合,履带板本身成为支 重轮等轮子的滚动轨道。履带板用销轴连接,销子浮置于销孔中并有0.5 1.5mm 的空隙,这种履带一般在大型挖掘机上应用较多。这种履带的优点是制造方便, 拆装容易。缺点是泥沙等污物易进入销孔中,使零件磨损加快,影响使用寿命。(2)组合式履带组合式履带由轨链节、履带板、销子和衬套等组成(图 5.1 ) o轨链节和 履带板用螺栓连接。履带销子和衬套的配合为 0.15 0.45mm过盈紧配合,装配 时要在40t以上的压床上进行。为了装拆方便,可将其中的
20、一节制成较松的配合。组合式履带的优点是:销子和衬套的密封较好,泥沙等污物不容易进入,由 于销子和衬套的硬度要求较高,连接处较耐磨,因而使用寿命也较高;履带节距 小,绕转性好,不会因履带板损坏、衬套开裂或连接螺栓剪断而中止行走。止匕外, 组合式履带零部件通用化程度高,易损件容易购置,所以维修、更换方便,制造 成本低。缺点是连接螺栓易折断,拆装比较困难。本设计中采用组合式履带,根据用途确定结构型式为三筋式。根据标准选取 规格系列为LD84勺履带,其名义节距为84mm履带板宽600mm经计算选取履带 板节数为90节。选取结果:履带 LD84 600 90H带板履带旌右键教节左域轨节索南鞘/ */餐蕈
21、铺套 / /驱动轮设计发动机的动力通过驱动轮传给履带,因此对驱动轮的要求应是与履带啮合正 确传动平稳,并且当履带因销套磨损而伸长后仍能很好啮合。导向轮的选型导向轮用于引导履带正确绕转,可以防止跑偏或越轨。大部分液压装载机的 导向轮同时起到支重轮的作用,这样可增加履带对地面的接触面积,减小比压。导向轮采用油塞灌油润滑,材料通常用40、45号钢或35Mn$钢,热处理采用 表面淬火,淬硬层深度为4 6mm硬度硬达HRC50 55张紧轮轴可选用50Mr 40Cr等材料,表面淬火,淬硬层2mm硬度HRC55许用弯曲应力u =220300MPa10。为了使导向轮发挥作用和延长使用寿命,制造时规定轮缘工作表
22、面对配合孔 的跳动不得超过3mm安装时应正确对中。根据中华人民共和国机械工业部标准一履带式推土机引导轮JB3262- 83选取与84型履带相配的导向轮。经选择,导向轮体的型号为:84节距导向轮体550*160mmJB 3262 (2) 83。 其最大外圆直径为D1=606mm导向轮的中间挡肩环宽度为 bi=80mm高度为 28mm张紧轮轴的基本尺寸为 60mm支重轮选型支重轮将装载机的重量传给履带,并在履带上滚动,它还用来夹持履带,不 使履带横向滑脱,并在装载机转向时迫使履带在地面上滑移。 支重轮工作环境十 分恶劣,常在泥水、沙土中工作,承受强烈的冲击。因此,要求支重轮应保持良 好的润滑状态,
23、减少磨擦件的磨损,提高使用寿命,保证密封装置的密封效果。支重轮的布置原则:支重轮在导向轮和驱动轮之间的布置应有利于增大履带 接地长度,因此最前一个支重轮应尽量靠近导向轮, 最后一个支重轮应尽量靠近 驱动轮。为了不和它们的运动发生干涉,支重轮的位置应保证当导向轮在缓冲弹 簧到达最大变形时相互不发生干涉,后支重轮轮缘外径与驱动轮齿顶圆之间应该 保留一定的间隙,以保证当悬架弹簧最大变形时不发生干涉,此间隙一般不小于20mm各支重轮间距均布。从这些条件出发,本设计每条履带布置了8个支重轮。支重轮间距t i和履带节距一般应满足:lt ti 2 lt所以取支重轮间距ti :ti=1.9lt =1.9*84
24、 =159.6mm取 ti=160mm,满足要求。本设计采用直轴式支重轮,采用浮动油封,双金属套滑动轴承。支重轮体材 料一般为35Mn或50M加工后热处理采用滚动面火焰淬火或整体加热喷水淬火, 硬度 HRC48 57。根据标准选择支重轮的型号和规格系列为:支重轮 WZ84.296.95。其机构如图拖链轮选型拖链轮的作用是托住履带上方区域,减少上方履带的跳动和下垂量,并防止履带从侧向滑脱。拖链轮轴固定在台车架纵梁上,受力较小,构造简单,一般为 悬臂结构。本机每边布置了两个拖链轮。拖链轮的位置应有利于履带脱离驱动链轮的啮合,并平稳而顺利地滑过拖链 轮和保持履带的张紧状态。当采用两个拖链轮时,两拖链
25、轮之间的距离通常约取 0.4倍轮距,两轮分别到驱动轮和导向轮的距离大致相同。其轮缘上平面高度ht、 拖链轮外径Dt和驱动轮节圆直径Dk应满足关系式:ht +0.5 Dt 0.5 Dk(5.3)拖链轮的材料可以采用灰铸铁或ZG50Mn造。拖链轮表面淬火,淬层深度 不小于4mm硬度HRC 53。拖链轮轴采用50Mri冈,调质硬度为HB255285根据标准,选择拖链轮的型号和规格系列为:拖链轮 WT84.150.42GB-10679。1.8.2 悬架选型与制动器选型悬架选型在工程机械中,连接机体与行走机构的元件称为悬架。悬架型式有刚性悬架、 半刚性悬架和弹性悬架三种:(1)采用刚性悬架的机械,机体与
26、行走机构之间只有平衡梁,没有弹性元 件,机体与行走机构之间为刚性连接,机体重量和地面冲击经过刚性悬架互相传 递。刚性悬架的结构简单,适合行走速度低的车辆。(2)采用半刚性悬架的机械为机体后部与行走机构刚性连接,机体前部与 行走机构弹性连接,机体重量通过前部的弹性连接和后部的刚性连接传递给行走 机构,大部分履带式装载机采用半刚性悬架。(3)采用弹性悬架的机械,机体与行走机构之间完全借助于弹性元件连接, 机体重量全部通过弹性元件传递给行走机构。弹性悬架的减振、缓和路面冲击的能力强。由于履带式液压装载机的行走速度较低,通常低于10km/h。故本设计采用刚性悬架。制动器选型制动器用于工程机械行驶时降速
27、或停车, 用于下坡运行时控制车速,不使车 速越来越快,以及用于坡道停车或车场停车。工程机械运行和作业的安全性,取决于转向系和制动系的工作情况。良好的 转向系和制动系可以提高履带式装载机的运行速度和生产率。制动器的型式诸多,本设计采用摩擦式多片制动器。现在“四轮一带”及其 他部件选型设计结果列下表:四轮一带”及其他部件选型设计结果名称规格与类型履带 LD 8460090GB 10677驱动轮自行设计导384节距导向轮体550 160mmJB 3262 (2) 83WZ84.295.95GB-10679拖链轮WT84.150.42GB-10679悬架刚性悬架制动器摩擦式多片制动器2液压系统的初步介
28、绍2.1 液压系统的工作原理液压系统是由各种液压元件(包括液压泵、液压阀、执行元件及辅助元件等) 按一定需要合理组合而成。它的工作原理是:液压泵由电动机带动旋转后,从油 箱中吸油。油液经滤油器进入液压泵,当它从泵中输出进入压力管后,通过开停 阀、节流阀、换向阀进入液压缸一腔,推动活塞和上作台运动。这时,液压缸另 一腔的油经换向阀和回油管排回油箱。由此可知 :(1)液压传动是以液体作为上作介质来传递能量的;(2)液压传动用液体的压力能来传递动力,它与利用液体动能的液力传动是 不相同的;(3)液压传动中的上作介质在受控制、受调节的状态下进行上作的,因此液 压传动和液压控制常常难以截然分开。2.2
29、液压系统的组成部分液压传动主要山以下四部分组成:(1)能源装置一一把机械能转换成油液液压能的装置,最常见的形式就是压 泵它给液压系统提供压力油;(2)执行装置一一把油液的液压能转换成机械能的装置,它可以是作直线运 动的液压缸,也可以是作回转运动的液压马达;(3)控制调节装置一一对系统中油液压力、流量或方向进行控制或调节的装 置,例如溢流阀、节流阀、换向阀、开停阀等。这些元件的不同组合形成了不同 功能的液压系统;(4)辅助装置一一上述三部分以外的其它装置, 例如油箱、滤油器、油管等, 他们对保证系统正常上作也有重要作用。2.3 技术要求液压工作系统首先要满足使用要求,好造、好用、好修、具有较高的
30、作业生 产率和较低的使用成本来衡量的。由于液力机械传动系统具有质量小、 适应作业 要求的性能好、操作方便等优点。在设计中要在满足工作要求的条件下尽可能使 用标准件,以使成本更低更利于维修。选择适当的压力和流量进行参数设计。采 用管式联接,结构紧凑,体积小而且要以压力损失小,震动和噪音小为目的。步骤如下:设计新的液压系统,首先要仔细查明机器对液压系统究竟有哪些要求,要与用户或主机厂共同讨论,力求定量地掌握这些技术要求,作为设计的 出发点和依据。需要掌握的技术要求可能有:1 .机器的特性(1) 用途及工作目的。(2)功能、性能及负载特性 负载种类(恒定负载、变化负载及冲击负载)及 大小;运动方式(
31、直线运动、旋转运动、摆动)及运动量(位移、速度、加速度), 惯性力,摩擦力(静摩擦、动摩擦、粘性摩擦),动作特性、动作时间,精度(定 位精度、跟踪精度、同步精度)o(3)结构 机构、与被驱动部分的连接条件、安装上的限制条件等。(4) 驱动方式 原动机的种类(电动机、内燃机等)、容量(功率、转速、转矩)、 稳定性。(5)控制方式 操作方式(手动、自动)、信号处理方式(继电器、逻辑电路、 可编程控制器、微计算机)。(6)循环时间系统中各种执行器的动作顺序、动作时间的相互关系。2 .使用条件(1) 工作时间。(2) 设置场所(室内、室外)。(3) 设置环境 环境温度、湿度(高温、寒带、热带),粉尘种
32、类和浓度(防护、 净化等),腐蚀性气体(所用元件的结构、材质、表面处理、涂覆等),易爆气体(防 爆措施),机械振动(机械强度、耐振结构),噪声限制(降低噪声措施)。(4) 维护条件维护程度与周期,维护人员的技术水平;维护空间、作业性、 互换性。3 .适用标准、法规4 .安全性、可靠性(1)用户在安全性方面有无特殊要求。(2)明确保用期、保用条件。5 .经济性不能只考虑投资费用,还要考虑能源消耗、维护保养等运行费用液压系统设计3.1 制定液压系统方案3.1.1 油路循环方式的分析与选择油路的循环方式分为开式和闭式两种。开式回路散热较方便,但油箱占空间 较大;抗污染性较差,采用压力油箱和虑油器改善
33、;用平衡阀进行能耗限速,用 制动法进行能耗制动,引起油液发热;对泵的自吸性要求较高。闭式回路较复杂, 须用辅助泵换油冷却;抗污染性较好但油液过滤要求高;液压泵由电动机拖动时, 限速及制动过程中拖动电机能向电网输电,回收部分能量,在生限速及在生制动; 对主泵的自吸性无要求。通过对比,本系统采用开式回路。3.1.2 确定液压执行元件的形式液压执行元件大体分为液压缸或液压马达。前者实现直线运动,后者完成回 转运动。本机动作机构均为单纯的直线往复运动。各直线运动机构均为单活塞杆双作 用液压缸直接驱动。3.1.3 各机构液压回路的确定(1)转斗动作回路确定本机构动作主要通过换向阀的有机组合实现所要求的动
34、作要求,铲斗的前 倾与收起。要求工作可靠,操纵轻便,且要求能够自动限位。换向阀的右位、左 位、中位分别实现铲斗的收起、前倾和锁紧。转斗油缸的小油腔回路中应设有双作用安全阀。在动臂升降过程中,砖斗的连杆机构由于动作不协调而受到某种程度的干涉, 即在提升动臂时转斗液压缸的 活塞杆有被拉出的趋势,而在动臂下降时活塞杆又被强制顶回。此时换向阀中位, 油路不通。为了防止液压缸过载或真空,双作用液压缸能起到缓补油优作用。 当 产生真空时,可由单向阀从油缸中吸油。其原理图如下图3-1-1。图3-1-1转斗动作回路(2)动臂动作液压回路确定本机构要求通过换向阀的控制,实现动臂油缸的提升、中立、下降、浮动四 个
35、工作位置。换向阀处于中位时,动臂液压缸处于浮动状态,以便在坚硬的地面上铲取物 料或进行铲推作业。此时动臂随地面状态自由浮动,提高作业效能。动臂要求具 有较快的升降速度和良好的低速微调性能。液压缸的进油由双联泵供油,流量最大可达320L/min。动臂处于升和降状态时可控制换向阀阀口开度的大小实现节 流调速。图3-1-2动臂动作液压回路(3)转向液压回路的确定装载机作业周期短,动作要灵活,这一特点决定转向机构要求灵敏。 装载机 要求有稳定的转向速度,也就是要求进入转向液压缸的油液流量恒定, 转向液压 缸的油液主要来自转向泵,当发动机受其他负载影响转速下降时, 就会影响转速 的稳定性。这是需要加辅助
36、泵,通过流量转换阀补入转向泵所减少的流量, 以保 证转向油路的流量稳定。图3-1-3转向机构液压回路3.2 绘制液压系统原理图拟定液压系统图是整个液压系统设计中重要的一步,它从作用原理上和结构 组成上具体体现设计任务中提出的各项要求。拟定液压系统图包括两项内容:通 过分析对比选出合理的液压回路;把选出的液压回路组合成液压系统。由于有多种方案,本方案是在归纳、整理,增加一些必要的元件和辅助油路 后,并参考了国内外同类系统的成熟精练。根据以上分析,按以下几点要求:(1)尽可能归并作用相同或相近的液压元件,力求使系统结构简单,尽可能采用标准元件。(2)保证系统上作循环中每个动作都安全可靠、无相互干扰
37、。特别要注意系统中压力控制元件的调节压力之间的关系。(3)尽可能提高系统的效率,防止系统过热。(4)尽可能使系统经济合理,便于维修 为此,拟定了系统原理图如图3-2图3-2液压系统原理图3.3 确定液压系统的主要参数液压系统的主要参数是压力和流量, 他们是设计液压系统,选择液压元件的 主要依据。压力决定于外负载。流量取决于液压执行元件的运动速度和结构尺寸。图3-3表示一个以液压缸为执行元件的液压系统计算简图。图3-3液压系统计算简图3.3.1 液压缸载荷组成22作往复直线运动的液压缸上的总负载由工作负载、导轨摩擦负载、惯性负载、重力负载、密封阻力、背压阻力六部分组成。(1)工作载荷Fg常见的工
38、作载荷有作用于活塞杆轴线上的重力、切削力、及压力等,这些作用力的方向与与活塞运动方向相同为负,相反为正。(2)导轨摩擦负载Ff对于水平导轨F G FnG-运动部件所受的重力,N;Fn外载荷作用于导轨上的正压力,N;N 摩+S系数,对于铸铁导轨N =0.10.2 ,滚动导轨,N =0.0050.01(3)惯性载荷巳F 上二 g Vt式中 g重力加速度,m/s; g=9.81。A v速度变化量, m/s ;At启动或制动时间,s0 一般At =0.10.5s ,对于轻载低速运动部 件取小值,对于高速重载部件一般取大值。行走机械一般取 Av/ At =0.51.5s 以上三种载荷之和称为液压缸的外负
39、载Fw启动加速时Fw Fg Ff F稳态运动时FW Fg Ff减速制动时Fw Fg Ff F工作载荷Fg并非每阶段都存在,如该阶段没有工作,则 Fg=0o除外载荷Fn外,作用于活塞上的载荷F还包括液压缸密封处的摩擦阻力 Fm, 由于各种液压缸的密封材质和密封形式不同,密封阻力难以精确计算,一般估算 为 Fm 1 m F式中 “m-液压缸白机械效率,一般取0.900.95。由上式计算出动臂液压缸的总推力11000NJ,转向液压缸缸的推力为327MF为22340N,铲斗液压缸的总推力为3.3.2 初选系统工作压力压力的选择要根据载荷大小和设备类型而定。还要考虑执行元件的装配空问、经济条件及元件供应
40、情况等的限制。 在载荷一定的情况下,工作压力低势必 要执行元件的尺寸,对于某些设备来说,尺寸要受到限制,从材料消耗的经济性 角度也不经济;反之,压力选得太高,对泵、缸、阀等元件的材质、密封、制造 精度也要求很高,必然要提高设备成本。一般来说,对于固定尺寸不太受限制的 设备,压力可以选低一些,行走机械重载设备压力要选得高一些。具体参照表3-3-1 和表 3-3-2载荷104 N5工作压力MPa57表3-3-1按载荷选择工作压力门刨床拉床小型程机大中型挖掘机机械类型磨床组合机械床工作压力MPa0.8 2352881010 1820 32表3-3-2各种机械常用的系统工作压力上表初步确定工作装置液压
41、系统工作压力为 16MPa转向液压控制系统工作压力为 13MPa3.3.3 计算液压缸的主要结构尺寸Pi T液压缸的钢筒内径、活塞杆直径及有效面积是主要结构参数。计算方法是:先由最大负载和选取的设计压力及估取的,液压缸的的有关设计参数如图这里要确定的参数是液压缸的内径和活塞杆直径。PiAiF p2A2(3-1)式中pi进油腔压力,Pa;Ai进油腔有效面积,m2;F液压缸总负载,No F=Fm, “m为液压缸的机械效率,一般取”市0.900.95;P2回油腔压力(背压),Pa;A回油腔有效面积,m2;背压P2的值可根据系统的特点及调速性能要求初选一个参考值,待系统回 路确定后再作修正。为了能够利
42、用上式进行设计,必须先选定背压出及活塞杆直径d与液压内径D的比值,记为dD(3-2)其比值可按工作压力选取参照表 3-3-1 。系统类型油路结构背压/MPa简单的系统和一般轻载的节流调速0.2 0.5中、低压系统系统回油路带调速阀的调速回路0.5 0.8回油路带背压阀0.5 1.5采用带补油泵的闭式回路0.8 1.5中高压系统同上比中低压系统局50%100%高压系统如锻压机械等初算时可忽略/、及3-3-工作压力MPa7.0d/D0.5 0.550.62 0.700.7表3-3-4按工作压力选取d/D将公式(3-1)代入(3-2)可得液压缸的内径为单杆液压缸D= 4F(3-3)Pi P2 12各
43、个回路的背压值均选为00(1)确定转斗油缸的内径及活塞杆直径由上式(3-3)可求得D=125mm皎表3-3-4可选d/D=0.7此时,d=87.5mm圆整, d 取 88mm(2)确定动臂油缸的内径及活塞杆直径由式(3-3)可求动臂油缸内径D2=165mm动臂油缸有速比要求取速比为入=1.33,d JId(3-4)式中 入速比。求出d=82mm3)确定转向油缸的内径及活塞杆直径由式(3-3)求转向油缸内径为D3=100mm要求伸出缩回速度相,取d=0.71D, d=71mm3.3.4 计算液压缸所需流量液压缸工作时所需的流量Q Av(3-4)式中 A液压缸的有效作用面积,m2;V 活塞与缸体的
44、相对速度,m/s。1)转斗油缸流量Q确定转斗油缸缩回速度为 vi=0.17m/s,可得,Q=tt (D2-d2)v/4=63.1L/min 。2)动臂油缸流量Q确定动臂油缸的伸出速度为 V2=0.0325m/s, Q=tt D2v/ 4=41.67L/min。3)转向油缸流量Q确定转向油缸的伸出速度为 V3=0.012m/s, Q=tt D2v/4=5.7L/min 。3.3.5 计算液压执行元件的实际工作压力按照最后确定的液压缸的结构尺寸计算出液压缸的实际工作压力,最终计算出工作装置液压系统液压缸的最大实际工作压力为14.2 MPa,转向系统液压缸的实际工作压力为11 MPa3.4 液压元件
45、的选择与专用件设计3.4.1 液压泵的选择(1)确定液压泵的最大工作压力液压泵的最大工作压力与执行机构的性质有关,通常有两种情况:一种是最大工作压力在执行机构终了时出现(如压力机或夹紧油缸)第二种是最大工作压 力在执行机构运动中出现(如组合机床)。对于第一种情况,液压泵的最大工作 压力就是执行机构所需的最大压力。对于第二种情况,液压缸的最大工作压力应是执行机构所需的最大压力于进油路总压力损失之和,即Pp Pl p (3-5)式中P p液压缸的最大工作压力,Pa;P i执行元件所需的最大压力,Pa;2Ap从液压泵出口到液压缸或马达之间总的管路损失,Pa。2Ap的准确计算要待元件选定并绘出管路图时
46、才能进行,初算时可按经验数据选取: 管路简单流速不大的,取 2 Ap= (0.20.5) MPa管路复杂进口油调速阀的, 取 2 Ap= (0.5 1.5) MPa由上述计算可知,对于工作装置液压系统系统,液压缸的最高压力为 14.2MPa, A2pW0.8MPa对于转向液压系统,7压缸的最高压力为11 MPa,A 2 p取1MPa工作装置液压泵的工作压力为15MPa转向系统液压泵的工作压力为12MPa2)确定液压泵的流量多液压缸同是工作时,液压泵的输出流量 Q应为Qp K Qmax(3-6)式中 K系统泄漏系数,一般取 K=1.11.3;的2 Qmax同时动作的液压缸的最大总流量。对于工作过
47、程中节流调速 的系统,还应加上溢流阀的最小溢流量,一般取 0.5 X 10-4 m/s。对于工作装置液压系统系统,液压缸的最大流量发生在最高点处的卸荷,由前面计算可得同时动作的液压缸的最大流量为63.1L/min。K取 1.1 时,Qmin=70L/min。对于转向液压系统,转向油缸的流量 5.7 L/min 。K取 1.2 时,CU =7L/min 。3)选择如液压泵的规格根据以上求得的pp和Qmax值,按系统拟定的液压泵形式,从手册中选择相应 的液压泵。为使液压泵有一定的压力储备,所选泵的额定压力一般要比最大工作 压力大25%- 60%工作装置液压系统选用CB-G2040/2050型双联齿
48、轮泵。转向液压系统选用CB-G205CS齿轮泵。3.4.2 液压阀的选择控制元件的类型和安装方式,在拟定液压原理图时已经确定,这里要做的是 根据阀所需要的最大工作压力和流量来选择标准阀类的规格。 通常所选阀的额定 压力必须大于最大工作压力,流量必须大于通过阀的实际最大流量, 同时要注意 以下几点:1)溢流阀或卸荷阀的额定流量不得小于泵的最大流量。2)流量控制阀的额定流量除需大于调速范围内的最大流量外,阀的最小稳 定流量必须小于低速时要求的最小稳定流量,即qV min vmin A(37)式中qvmin阀的最小稳定流量,L/min ;Vmin 执行元件白最低速度,m/s;A液压缸工作腔的有效面积
49、,m。由此,选出液压阀型号如下(参照液压系统图):阀 7, 824 口-B10阀 10YF-L20C;阀 11YF-L32H;阀 12YF-L10 H;阀 1334SX -L20H。3.4.3 辅元件的选择(1)油管的选择计算油管类型的选择:油管类型主要根据使用场合和系统的最大工作压力来选择。一般选用原则是中高压系统;装配不便的中低压系统可用铜管,有相对运动部件 间的连接采用橡胶软管。内径计算:通过油管的流量和油管内允许的流速来确定油管内径。v管内允许流速,m/s,见表3-4-1 o油液流经的管道推荐流速m/s液压泵吸油管道0.51.5, 一般取1m/s以下液压系统压油管道36,压力高,管道短
50、粘度小取大值液压系统回油管道1.52.6表3-4-1允许流速推荐值经计算,有如下结果:双联泵并联后管道允许流速取4.5m/s ,经计算内径取0.027m。转向油缸吸油口管道速度取1.0m/s,经计算内径取0.04m。转向油缸排油口管道速度取4.5m/s,经计算内径取0.019m。工作装置液压系统压油管道速度取 3m/s,经计算内径为0.034m。工作装置液压系统回有管道速度取 2.5m/s,经计算内径为0.058m。2)油箱容量的计算初始设计时,先按经验公式(3-9)确定油箱的容量,待系统确定后再按散热的要求进行校核。经验公式为:VQv(3-9)式中 Q液压泵每分钟排出压力油的容积,m3;经验
51、系数,见表3-4-2系统类型行走机械低压系统中压系统锻压机械冶金机械a12245761210表3-4-2经验系数在确定油箱尺寸时,一方面要满足系统的供油要求,还要保证执行元件全 部排油时,油不能溢出油箱,以及系统中最大可能充满油时,油箱的油位不低于 最低限度。工作装置液压系统双联泵的流量为 2X0. 16 m3=0.32 m3经验系数a =1。此 时算出油箱的有效容积为0.32 m3。3.5 液压系统的性能验算液压系统初步设计时在某些估计参数情况下进行的,当各回路形式、液压 元件及连接管路等完全确定后,针对实际情况对所设计的系统进行各项性分析。 对一般液压传动系统来说主要是进一步确切地计算液压
52、回路各个段压力损失、容积损失及系统效率,压力冲击和发热升温等。根据分析计算发现的问题对某些不 合理的系统进行调整,或采取其它的必要措施3.5.1 液压系统压力损失压力损失包括管路的沿程损失 A Pi过路的局部压力损失 A P2和阀类元件的 局部损失A p3,总的压力损失为:PPiP2P3l v2PiP2(3-10)(3-11)(3-12)式中l 管道长度,mi l=5m d管道内径,m; v液流平均速度,m/s; P液压油密度,kg/m3。p =928 kg/m3;入一一沿程阻力系数; 己一一局部阻力系数。选用20号机械油,正常运转后油的运动黏度 v =2.7 X 10-5m2/s ,油的密度
53、p =928 kg/m3,计算得沿程压力损失 Ap1=0.04MPaP3Pn(3-13)式中 Q阀的额定流量,m7s ;Q 通过阀的实际流量,m3/s ;Apn阀的额定压力损失,Pa。局部压力损中,管路局部压力损失 Ap2相对控制阀的局部压力损失要小得 多,只计算通过阀的局部压力损失。根据选择,经计算,通过各阀的局部压力损失之和Ap3=1.5MPa对于泵到执行元件间的压力损失,如果计算出A P比选泵时估计的管路损失 大得多时,应该重新调整泵及及其他相关元件的规格尺寸参数。系统的调整压力PtP1P(3-14)式中Pt液压泵的工作压力或支路的调整压力,1.5MP3 因为额定压力还有一定的压力裕度所
54、以泵的选择是合适的。3.5.2液压系统的发热温升计算计算的目的是要使系统在正常温度下达到热平衡。正常温度一般指3065C,根据机器的不同,其上作温度也有所不同,机床 3050C,最高70 0 C, 上程、矿山机械5080 C,最高85 C。过热会产生下列危害:(1)油变质,形成胶状沉淀;(2)使密封件变质; (3)效率降低,严重时会影响到系统的正常工作。发热的原因一般为:(1)动力方面:电机本身的发热;(2)泵效率低:泵的功率损失造成;(3)执行元件:油马达、油缸的容积漏油与机械损失造成;(4)管道沿程压力损失,只占整个发热量的 0.030.05;(5)液压元件:阀本身压力损失,转化为热;(6
55、)油箱大小,是散热面不足;(7)冷却器热交换量不足;(8)环境介质的温度较高;(9)在液压系统中混入了空气。液压系统工作时,除执行元件驱动外载荷数出有效功率外, 其余功率损失全 部转化为热量,使油温升高。对于较复杂的系统,通常用下式计算液压系统的发热功率Rr Pr PC(3-15)式中Pr是液压系统的总输入功率,Pc是输出的有效功率。pr - z RQk(3-16)Tt i 1 pi1n2 - FwiSi(3-17)Tt i 1式中 Tt工作周期,s; z、n分别为液压泵、液压缸的数量;Pi、Q、“pi 分别为第i台泵的实际输出压力、流量、效率;ti第i台泵的工作时间,ti =8s ;Fw、S
56、i 液压缸外载荷及此载荷时的行程,N、s0已知 z=2, n=3,计算出 Phr=10.4kWA3.5.3 计算液压系统的散热功率液压系统的主要散热渠道是油箱表面,还有一小部分通过油管、液压缸等散发。一般仅计算油箱的散热,假定全部热量由油箱散发Rc KA T(3-18)式中 K-油箱的散热系数,见表3-5-1 ; A油箱的散热面积,m2;AT油温与环境温度之差,C。当系统达到热平衡时则有 Phc = Phr,油温不再升高,此时,最大温差T 员(3-18)KAKw/m通风条件很差89通风条件良好15 17用风扇冷却23循环水强制冷却110170表3-5-1油箱散热系数环境温度为T,则T=To+
57、A T,若计算出的油温超过该系统得最高允许油温 (工 程机械正常温度5080C;最高允许油温7090C),在无法增加油箱散热面积 时,就要装设冷却器。3.5.4 根据散热要求计算油箱容量式(3-18)是在初步确定油箱容积的情况下,验算散热面积是否满足要求。当 系统的发热量求出之后,可根据散热要求确定油箱容量。可得油箱的散热面积为A -P(3-19)TK1油箱的主要设计参数如图(3-5-2)图3-5-2油箱结构尺寸一般油面的高度为油箱高度h的0.8倍,与油直接接触的表面算全面散热, 与油不直接接触的表面半散热面,图示油箱的有效容积和散热面积分别为 V 0.8abh(3-20)A 1.8h a b
58、 1.5ab(3-21)由前面初步求得油箱有效容积 0.32 m3,按V=0.8abc求得油箱各边之积:3abc=0.32/0.8=0.4m。取 a 为 0.8m,取 b 为 1m取 h 为 0.5m。3.6液压系统冲击压力压力冲击是由于管道液流速度急剧改变而形成的。例如液压执行元件在高速 运动中突然停止,换向阀的迅速开启和关闭,都会产生高于静态值的冲击压力。 它不仅伴随产生振动和噪音,而且会因过高的冲击压力而使管路、液压元件遭到 破坏。3.6.1 压力冲击的原因(1)油流的动量引起:m 2p -V2(3-22)式中 m单位流体质量,kg;g流体的重力加速度;v液体的流速 m/s,(2)共振引
59、起:主要是油泵的压力脉动及其他外界振荡因素引起。共振的原因在于振源的频率 1与2相接近。解决办法可提高系统的固有频率,使其他 干扰频率不一致。(3)惯性力产生的动能引起:由动能产生的压力p=F/A这个压力增加较 大,往往需要考虑。(4)截面积增压效应。(5)体积弹性增压效应,包括管道的油液体积。3.6.2 消除或减少压力冲击的措施1)减少驱动能;2)吸收惯性能;3)用蓄能器或缓冲器。4动臂液压缸的设计4.1 液压缸的结构参数计算4.1.1 缸筒壁厚计算工程机械用标准液压缸外径系列见表4-1-1缸径mm (p 16MPa液压缸外径 mm缸径mm(p 16MPa液压缸外径 mm405011013350601251466376140168809516019490108180219100121200245表4-1-1工程机械用液压缸外径系列由上表可知,转斗液压缸的外径为 146mm转向液压缸外径121mm壁厚分别为:转斗液压缸 6 1=(146-125)/2=10.5;转向液压缸6 3=(121-100)/2=10.5 。转斗液压缸、转向液压缸的尺寸结构已经标准化,故不用对其结构参数的计算亦
- 温馨提示:
1: 本站所有资源如无特殊说明,都需要本地电脑安装OFFICE2007和PDF阅读器。图纸软件为CAD,CAXA,PROE,UG,SolidWorks等.压缩文件请下载最新的WinRAR软件解压。
2: 本站的文档不包含任何第三方提供的附件图纸等,如果需要附件,请联系上传者。文件的所有权益归上传用户所有。
3.本站RAR压缩包中若带图纸,网页内容里面会有图纸预览,若没有图纸预览就没有图纸。
4. 未经权益所有人同意不得将文件中的内容挪作商业或盈利用途。
5. 装配图网仅提供信息存储空间,仅对用户上传内容的表现方式做保护处理,对用户上传分享的文档内容本身不做任何修改或编辑,并不能对任何下载内容负责。
6. 下载文件中如有侵权或不适当内容,请与我们联系,我们立即纠正。
7. 本站不保证下载资源的准确性、安全性和完整性, 同时也不承担用户因使用这些下载资源对自己和他人造成任何形式的伤害或损失。