毕业设计(论文)汽车转向节机械加工工艺规程及工艺装备设计
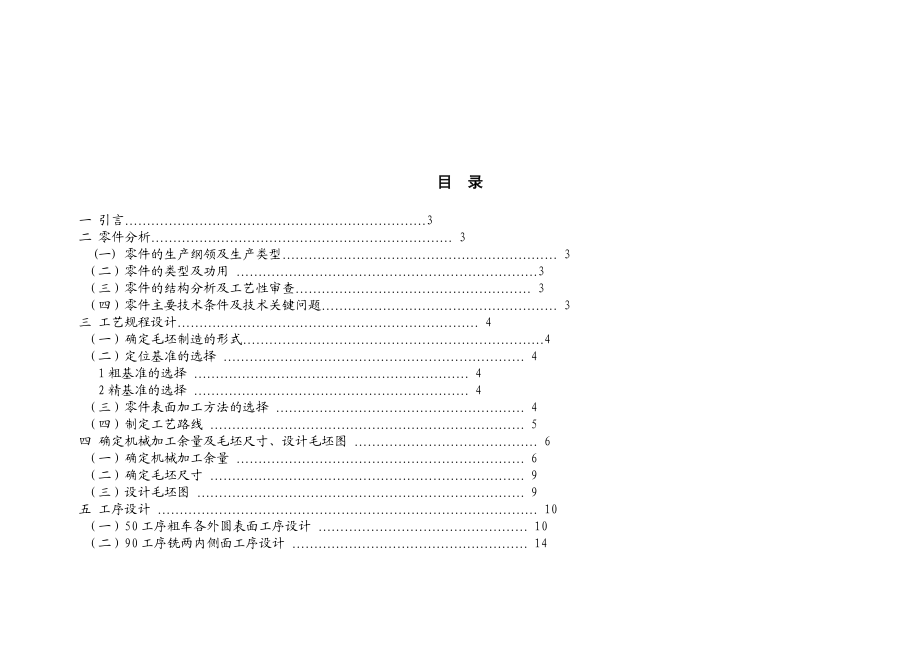


《毕业设计(论文)汽车转向节机械加工工艺规程及工艺装备设计》由会员分享,可在线阅读,更多相关《毕业设计(论文)汽车转向节机械加工工艺规程及工艺装备设计(53页珍藏版)》请在装配图网上搜索。
1、目 录一 引言3二 零件分析 3 (一) 零件的生产纲领及生产类型 3 (二)零件的类型及功用 3 (三)零件的结构分析及工艺性审查 3 (四)零件主要技术条件及技术关键问题 3三 工艺规程设计 4 (一)确定毛坯制造的形式4 (二)定位基准的选择 4 1粗基准的选择 4 2精基准的选择 4 (三)零件表面加工方法的选择 4 (四)制定工艺路线 5四 确定机械加工余量及毛坯尺寸、设计毛坯图 6 (一)确定机械加工余量 6 (二)确定毛坯尺寸 9 (三)设计毛坯图 9五 工序设计 10 (一)50工序粗车各外圆表面工序设计 10 (二)90工序铣两内侧面工序设计 14 (三)170工序拉主销孔工
2、序设计 15 (四)250工序磨外圆轴颈工序设计 15 (五)70工序半精车各外圆表面数控车削工序设计(方案二)16 六 专用夹具设计 18 (一)问题的提出18 (二)定位方案选择 18 1 定位基准的选择 18 (三)定位误差分析及计算 18 1刀具、钻具、衬套的选择 19 2对刀误差 19 3角度误差 20 4 分度误差 20 (四)夹紧方案选择 20 (五) 夹紧力计算 20 1 确定轴向切削力 20 2 确定夹紧力 20 (六)夹紧力方向与夹紧力作用点的选择 21七 专用刀具设计 21八 专用量具的设计 22九 结束语 23一十 参考文献33十一 致谢24附件一:英文资料译文附件二:
3、汽车转向节机械加工工艺规程附件三:汽车转向节零件图附件四:汽车转向节毛坯图附件五:钻主销孔夹具装配图及部分零件图附件六:1:8锥孔加工铰刀设计图附件七:工序170拉主销孔塞规设计图汽车转向节机械加工工艺规程及工艺装备设计作者 x x一、 引言毕业设计是我们大学期间的最后一个教学环节,是一个综合性的教学实践环节,是培养我们工程技术人员的主要教学环节之一,是对几年学习成效的综合性检验。通过这一环节培养我们综合运用所学知识解决问题的能力,提高我们开拓创新的能力。机械加工工艺设计和工装设计是机制专业学生的对口课题,同时又是一个有一定深度和难度的课题,是综合性和实践性较强的课题。本次毕业设计选择在大批大
4、量生产下,完成汽车转向节的机械加工工艺规程和工艺装备设计。详细讨论了汽车转向节从毛坯到成品的机械加工工艺过程,并制定了相应的机械加工工艺规程,并分析总结了叉杆类零件的特点,分析出本叉杆类零件的主要加工为外圆表面和孔的加工,针对该零件的主要技术要求,设计了钻孔用的回转钻模,以完成该零件主销孔的钻削加工,达到相应的技术要求,并满足了生产率的要求。同时,设计了该零件制造过程所需要的其他的工艺装备,包括刀具和量具等。二、零件分析(一)零件的生产纲领及生产类型 汽车转向节的生产纲领为10万台/年,生产类型为大批大量生产,所以在制定工艺路线时应充分考虑大批大量生产的特点,制定合适的工艺路线,选择合适的机床
5、、刀具、量具、检具,以便提高生产率,降低成本。(二)零件的类型及功用 汽车转向桥(即前桥)是利用转向节使前车轮可以偏转一定角度而使汽车转向的部件,同时也是汽车重要的前支承部件。转向节是汽车前桥上的一个关键零件。转向节叉形部分的主销孔用于插入主销,使转向节与前桥的前梁左右拳部连接为一体。转向节轴杆部分的两个外圆轴颈用于安装两个圆锥滚子轴承。两个圆锥滚子轴承的外圆则安装在前轮毂的轴承孔中,而前轮毂与前轮辐、前轮胎和前制动器是连接为一个整体的。由此可见,转向节是连接汽车前梁和前轮的一个必不可少的关键零件。因此,转向节的制造必须全面达到设计图样和各项技术条件的要求。(三)零件的结构分析及工艺性审查 汽
6、车转向节由尾柄、上下叉头及法兰盘组成。叉头与尾柄偏斜了一定的角度。该零件既有叉杆类零件的特点,又有轴类零件的特点,以外圆表面和内孔为主要加工表面,且有较高的尺寸公差和形位公差要求。 对零件图的结构工艺性审查得知锥孔的加工有一定难度,叉头部分的两内表面槽底做成R120的圆弧形其工艺性不如平面形槽底好。(四)零件主要技术条件及技术关键问题 汽车转向节的主要加工部分有:外圆表面的加工,孔的加工以及平面的加工,对这些加工部分的主要技术要求有:1、轴线X-X与轴线Y-Y应在同一平面内,公差0.22、锥孔轴线L-L垂直于X-X和Y-Y轴线所成的平面,公差0.15:1003、磨削前经磁力探伤,检验后退磁 本
7、零件的技术关键为:(1)叉形主销孔加工,有很高的同轴度要求。(2)轴杆上两主轴颈外圆加工,尺寸精度高、表面粗糙度值小、形位精度高。(3)下叉处锥孔加工。(4)尾柄上40mm的外圆表面与74mm的外圆表面相接处的过渡圆角R5应滚压,因为汽车转向节在工作过程中本连接处最易疲劳断裂,所以用滚压来提高疲劳强度。对于上述4处关键表面的加工,在制订工艺规程时必须充分重视、必须保证质量。三、 工艺规程设计(一)确定毛坯制造的形式毛坯材料为40Cr。零件外形较复杂。考虑到汽车在运行中要经常左右转向,零件在工作过程中则经常受交变载荷及冲击载荷 ,因此应选用锻件毛坯,使零件材料内部形成金属纤维组织,可提高承载能力
8、,保证零件工作可靠。由于零件年生产量10000件,已达大批大量的生产类型,而且零件的尺寸不大,故可采用模锻成形,这从提高生产率,保证加工精度上考虑,也是应该的。(二)定位基准的选择 基面选择是工艺规程设计中的重要工作之一,基面选择得正确与合理,可以使加工质量得以保证,生产率得以提高。否则,加工工艺过程中将问题百出,更有甚者,还会造成零件大批报废,使生产无法进行。1、粗基准的选择 本零件的尾柄部分是典型的轴类零件,故以外圆作为径向粗基准,以法兰盘端面作为轴向粗基准。2、 精基准的选择 零件精基准的选择主要考虑因素是提高定位精度,减少定位误差。对于转向节的加工,应按工种基本原则选择精基准,即基准重
9、合原则和基准统一原则。基准重合原则是将设计基准和工艺基准及测量基准相互重合。这样就可以避免由于基准不重合而产生的基准不重合误差。轴杆部分的设计基准是外圆轴线,而轴线是由轴两端的中心孔来体现的,故该零件选择两个中心孔作为第一组精基准。基准统一原则是加工过程中大多数工序采用相同的定位基准,这样也可减少定位误差。因此,两个轴颈外圆、法兰盘端面和一个10H7工艺孔作为第二组精基准。(三) 零件表面加工方法的选择 零件的主要加工表面为外圆表面、孔和平面。考虑到各个表面的技术要求,各种加工方法的经济加工精度范围,各加工表面的形状和尺寸大小,锻件材料(40Cr)的性质及可加工性和生产纲领与生产类型,选择各加
10、工表面的加工方法如下:1、25g6和40g6的外圆表面及轴颈74h10的端面:该外圆表面粗糙度为Ra1.6m,同时考虑到生产率的问题,选择粗车半精车磨削的加工方法。2、74h10外圆表面:该外圆表面粗糙度为Ra12.5m,采用粗车精车的加工方法。(1) 螺纹外圆表面:该外圆表面粗糙度为Ra25m,采用车削的加工方法。(2) 右杆部外圆锥面:该外圆表面粗糙度为Ra25m,采用车削的加工方法。(3) 尾柄端面:该表面粗糙度为Ra25m,故采用铣削的加工方法则可达到设计要求。(4) 主销孔30H9:其尺寸公差等级为IT9,表面粗糙度为Ra6.3m,圆度、圆柱度公差值为0.013,因尺寸公差、形位公差
11、和表面粗糙度均有较高要求,又因加工后要压入衬套,故采用钻、扩、拉的加工方法。(5) 孔4-10H11:其尺寸公差等级为IT11,表面粗糙度为Ra12.5m,位置度公差值为0.30,因尺寸公差、形位公差和表面粗糙度均有较高要求,故采用钻铰的加工方法。同时为了保证孔的位置度要求,以上工步必须在一次安装中完成。(6) 主销孔32H11:其尺寸公差等级为IT11,表面粗糙度为Ra12.5m,故采用钻、扩及倒角的加工方法。(7) 1:8锥孔28:其表面粗糙度为Ra3.2m,采用钻、扩、铰的加工方法。(8) 转向节的叉形内、外端面:其表面粗糙度为Ra12.5m,采用铣削的加工方法。(9) 键槽:其表面粗糙
12、度为Ra6.3m,因是大批大量生产,故采用拉键槽。(四)制定工艺路线 综合考虑各表面的加工方法,加工顺序及生产批量和经济性拟订汽车转向节的机械加工工艺过程如下:1、工艺方案一:表1 汽车转向节机械加工工艺过程简表序号工序内容定位基准设备10锻 坯20调 质30涂 漆40铣两端面、钻中心孔毛坯外圆及法兰盘端面铣端面、打中心孔机床50粗车右端杆部各外圆两端中心孔车床60钻、铰N面工艺孔两轴颈、法兰盘端面N钻床70半精车右端杆部各外圆两端中心孔车床80车右端面杆部外圆锥面车床90铣左端叉部两内侧面N端面、40h6外圆和10H7工艺孔铣床100铣上叉上平面铣床110铣下叉下平面铣床120铣下叉锥孔两端
13、面铣床130钻、铰N面4-13H11孔钻床140锪平N面4-28圆柱坑钻床150铰N面4-13H11孔钻床160钻、扩叉形主销孔及倒角钻床170拉主销孔32孔拉床180镗孔32H11N端面、40h6、10H7双面镗床190钻、铰下叉1:8锥孔钻床200钻、攻上叉两侧M10x1螺孔钻床210拉下叉锥孔键槽锥孔拉床220滚丝M22x1.522外圆滚丝机230铣M22x1.5处小平面轴颈、端面铣床240磨40g6外圆及74 端面两端中心孔外圆磨床250磨25g6外圆外圆磨床260滚压40g6外圆根部圆角滚压机270磁力探伤及退磁探伤机280钻杆部径向孔5轴颈外圆及端面钻床2905孔两端孔口倒角钻床3
14、00M22x1.5外螺纹套丝310去毛刺锐边320J最终检验2、 工艺方案二: 工序70即汽车转向节的右杆部的半精车过程,在数控车床上完成,以达到提高生产效率的目的,具体加工过程详见5.5,70工序半精车各外圆表面数控车削工序设计。四、 确定机械加工余量及毛坯尺寸,设计毛坯图(一)确定机械加工余量机械加工余量的确定由很多因素决定。在此主要考虑工序的经济性及各工序的加工方法。具体如表2表16所示:表2 轴颈40g6的机械加工余量工序工步名称双边余量mm工序的经济精度基本尺寸mm工序尺寸及公差值mm公差等级公差值mm磨0.5IT60.0164040半精车2.0IT80.03940.540.5粗车2
15、.5IT120.2542.542.5毛坯面IT161.64545表3 轴颈25g6的机械加工余量工序工步名称双边余量mm工序的经济精度基本尺寸mm工序尺寸及公差值mm公差等级公差值mm磨0.5IT60.0132525半精车3IT80.03325.525.5粗车16.5IT120.2128.528.5毛坯面IT161.64545表4 轴颈螺纹部分的机械加工余量工序工步名称双边余量mm工序的经济精度基本尺寸mm工序尺寸及公差值mm公差等级公差值mm精车3IT90.0522222粗车20IT120.212525毛坯面IT161.64545表5 74h10的机械加工余量工序工步名称双边余量mm工序的经
16、济精度基本尺寸mm工序尺寸及公差值mm公差等级公差值mm精车1IT100.127474粗车5IT120.37575毛坯面IT161.98080表6 74h10端面的机械加工余量工序工步名称双边余量mm工序的经济精度基本尺寸mm工序尺寸及公差值mm公差等级公差值mm磨0.5IT60.00855半精车1.5IT80.0185.55.5粗车3IT120.1577毛坯面IT160.91010表7 法兰盘端面的机械加工余量工序工步名称双边余量mm工序的经济精度基本尺寸mm工序尺寸及公差值mm公差等级公差值mm精车1.5IT80.02299粗车7.5IT120.1810.510.5毛坯面IT161.118
17、18表8 上叉外侧面的机械加工余量工序工步名称双边余量mm工序的经济精度基本尺寸mm工序尺寸及公差值mm公差等级公差值mm铣4IT120.254040毛坯面IT161.64444表9 下叉外侧面的机械加工余量工序工步名称双边余量mm工序的经济精度基本尺寸mm工序尺寸及公差值mm公差等级公差值mm铣4IT120.254040毛坯面IT161.64444表10 下、下叉两内侧面的机械加工余量工序工步名称双边余量mm工序的经济精度基本尺寸mm工序尺寸及公差值mm公差等级公差值mm铣8IT120.27676毛坯面IT161.68484表11 锥孔部分两端面的机械加工余量工序工步名称双边余量mm工序的经
18、济精度基本尺寸mm工序尺寸及公差值mm公差等级公差值mm铣4IT110.163636毛坯面IT161.64040表12 4-10H7的机械加工余量工序工步名称双边余量mm工序的经济精度基本尺寸mm工序尺寸及公差值mm公差等级公差值mm铰0.2IT110.111212钻11.8IT120.1811.811.8表13 主销孔30的机械加工余量工序工步名称双边余量mm工序的经济精度基本尺寸mm工序尺寸及公差值mm公差等级公差值mm拉2IT90.0523030扩3IT100.0842828钻25IT120.212525表14 主销孔32的机械加工余量工序工步名称双边余量mm工序的经济精度基本尺寸mm工
19、序尺寸及公差值mm公差等级公差值mm扩7IT110.163232钻25IT120.212525表15 螺孔M22x1的机械加工余量工序工步名称双边余量mm工序的经济精度基本尺寸mm工序尺寸及公差值mm公差等级公差值mm钻8.5IT120.158.58.5表16 1:8锥孔的机械加工余量工序工步名称双边余量mm工序的经济精度基本尺寸mm工序尺寸及公差值mm公差等级公差值mm铰0.2IT90.1229.929.9扩1.8IT100.08427.827.8钻26IT120.212626表17 销孔5的机械加工余量工序工步名称双边余量mm工序的经济精度基本尺寸mm工序尺寸及公差值mm公差等级公差值mm
20、钻5IT120.1255(二) 确定毛坯的尺寸 汽车转向节零件材料为40Cr,调质硬度为HRC3035,强度极限b=980Mpa,生产类型为大批大量生产,采用在锻模上合模模锻毛坯。因零件上所有孔径均较小,所以在毛坯中均不锻出。由参考文献8及表2.214得该锻件各对应面加工余量如下表所示:表18 各表面加工余量加工表面加工余量mm基本尺寸mm说明轴540双边余量节臂内、外端面440双边余量锥孔端面436双边余量(三)设计毛坯图根据上述所确定的加工总余量和毛坯尺寸来绘制毛坯图,毛坯轮廓用粗实线绘出,零件的实际尺寸用双点划线绘制,尺寸如表19所示。同时在图中标出毛坯尺寸、公差、技术要求、圆角半径和模
21、锻斜度等。具体见附件三。表19 各表面加工余量加工表面加工余量mm基本尺寸mm说明轴545双边余量节臂内、外端面444双边余量锥孔端面440双边余量五、 工序设计(一)50工序粗车各外圆表面工序设计1、加工设备与工艺装备加工设备:卧式车床CA6140 工艺装备:刀具:由参考文献7,根据表1.2 选择YT15硬质合金刀片,刀杆尺寸, , , ,刀具为偏头外圆车刀。 夹辅具:顶尖、拔盘 量具:游标卡尺 0.02 02002、 确定工序尺寸 见表2表73、 确定切削用量及计算基本时间(1) 车27mm外圆表面 计算切削用量: 切削深度 。确定进给量:由参考文献7 表1.4 当刀杆尺寸为,工件直径20
22、40mm,f=0.30.5mm/r,按CA6140,f=0.41mm/r。选择车刀磨钝标准及刀具使用寿命:由参考文献7 根据表1.9 车刀后刀面最大磨损量为1.0mm,车刀寿命 T=60min。确定切削速度:由参考文献7 根据表1.10,当使用YT15硬质合金车刀加工的钢料, 切削速度。 切削速度的修正系数:, , , , ,根据CA6140车床说明书,选择 实际切削速度vc为由参考文献7,根据表1.27 , , , 故选择,与查表结果相同,这时校验功率:, , , , , , , 故实际切削功率为,由此可见,所选切削用量可以采用。所以切削用量为: , , , 计算基本工时: 式中, , 根据
23、参考文献7表1.26,车削时的切入量及超切量为 。则,故式中:KTV切削速度的修正系数 VC实际切削速度(m/min) Tm切削时间(min) ap切削深度(mm) n机床主轴转速(r/min) f进给量(mm) L刀具或工作台行程长度(mm)(2) 车40mm外圆表面计算切削用量: 切削深度 。确定进给量:由参考文献7 表1.4 当刀杆尺寸为,工件直径2040mm,f=0.30.5mm/r,按CA6140,f=0.41mm/r。选择车刀磨钝标准及刀具使用寿命:由参考文献7 根据表1.9 车刀后刀面最大磨损量为1.0mm,车刀寿命 T=60min。确定切削速度:由参考文献7 根据表1.10,当
24、使用YT15硬质合金车刀加工的钢料, ,切削速度。 切削速度的修正系数:, , , , ,根据C6140车床说明书,选择 实际切削速度vc为由参考文献7,根据表1.27 , , , 故选择,与查表结果相同,这时校验功率:, , , , , , , 故实际切削功率为, 由此可见,所选切削用量可以采用。所选切削用量为:, , , 计算基本工时: 式中, , 根据参考文献7表1.26,车削时的切入量及超切量。则,故(3) 车24mm外圆表面 计算切削用量: 切削深度 。确定进给量:由参考文献7 表1.4 当刀杆尺寸为,工件直径2040mm,f=0.30.5mm/r,按CA6140,f=0.41mm/
25、r。选择车刀磨钝标准及刀具使用寿命:由参考文献7 根据表1.9 车刀后刀面最大磨损量为1.0mm,车刀寿命 T=60min。确定切削速度:由参考文献7 根据表1.10,当使用YT15硬质合金车刀加工的钢料, 切削速度。 切削速度的修正系数:, , , , ,根据CA6140车床说明书,选择 实际切削速度vc为由参考文献7,根据表1.27 , , , 故选择,与查表结果相同,这时校验功率:, , , , , , , 故实际切削功率为,由此可见,所选切削用量可以采用。所选切削用量:, , , 计算基本工时: 式中, , 根据表1.26,车削时的切入量及超切量。则,故(4) 车轴颈74mm端面 计算
26、切削用量: 切削深度 。确定进给量:由参考文献7 表1.4 当刀杆尺寸为,工件直径60100mm,f=0.61.0mm/r,按CA6140,f=0.7mm/r。选择车刀磨钝标准及刀具使用寿命:由参考文献7 根据表1.9 车刀后刀面最大磨损量为1.0mm,车刀寿命 T=60min。确定切削速度:由参考文献7 根据表1.10,当使用YT15硬质合金车刀加工的钢料, ,切削速度。 切削速度的修正系数:, , , , ,根据C6140车床说明书,选择 实际切削速度vc为由参考文献7,根据表1.27 , , , 故选择,与查表结果相同,这时校验功率:, , , , , , , 故实际切削功率为,由此可见
27、,所选切削用量可以采用。 所选切削用量为:, , , 计算基本工时: 式中, , 根据表1.26,车削时的切入量及超切量。则,故(5) 车法兰盘端面 计算切削用量: 切削深度 。确定进给量:由参考文献7 表1.4 当刀杆尺寸为,工件直径100600mm,f=0.81.4mm/r,按CA6140,f=1mm。选择车刀磨钝标准及刀具使用寿命:由参考文献7 根据表1.9 车刀后刀面最大磨损量为1.0mm,车刀寿命 T=60min。确定切削速度:由参考文献7 根据表1.10,当使用YT15硬质合金车刀加工的钢料, ,切削速度。 切削速度的修正系数:, , , , ,根据CA6140车床说明书,选择 实
28、际切削速度: 由参考文献7,根据表1.27 , , , 故选择,与查表结果相同,这时校验功率:, , , , , , , 故实际切削功率为,由此可见,所选切削用量可以采用。所选切削用量为:, , , 计算基本工时: 式中, , 根据表1.26,车削时的切入量 。则,故(二)90工序铣两内侧面工序设计1、选择加工设备与工艺装备 加工设备:卧式铣床X62 工艺装备:刀具:由参考文献7,根据表1.2 选择YT15硬质合金刀片,根据表3.1 故应根据铣削宽度 由于采用标准硬质合金端铣刀,由参考文献7,表3.13得 齿数Z=4。 夹辅具:铣夹具 量具:游标卡尺 0.02 02002、 确定工序尺寸 见表
29、8、表9、 表10。3、确定切削用量及计算基本时间(1) 计算切削用量: 切削深度 。(2) 确定每齿进给量:由参考文献7 表3.5 当使用YT15铣床,功率为7.5kw,由于采用对称铣,故取(3) 选择铣刀磨钝标准及刀具使用寿命: 根据表3.7 铣刀刀齿后刀面最大磨损量为1.0mm,由于铣刀直径 故刀具寿命 T=180min(4) 确定切削速度和进给量:切削速度可根据表3.27中的公式计算,也可直接查表。根据表3.13 当各修正系数:0.69,0.76故 =80.76m/min n=nt.kn=3910.690.76 =205.04r/min vf=vf.kvf=1880.690.76 =9
30、8.59m/min根据X62说明书,选择 ne=190r/min vfc=150m/min因此 实际切削速度和每齿进给量为=143.18m/min =0.1974 mm/z(5)校验机床功率 根据表 3.23 当 ,近似为,根据X62说明书,机床主轴允许的功率为,故 ,因此所选的切削用量可以采用。所选切削用量为: 143m/min 0.2mm/z 计算基本工时 式中 根据表3.26 则 所以 (三) 170工序拉主销孔工序设计1、 选择加工设备与工艺装备加工设备:卧式内拉床L6120工艺装备:刀具:圆孔拉刀30D80120 夹辅具:拉夹具 量具:光滑塞规2、确定工序尺寸见表123、 确定切削用
31、量及计算基本时间(1) 计算切削用量:切削深度 (2) 确定进给量 由参考文献17 表86 得f=0.02mm(3) 计算工时 其中, , , , (四) 250工序磨轴颈外圆25g6工序设计1、 选择加工设备与工艺装备 加工设备:外圆磨床M1432A 工艺装备:砂轮:1-50050203WA60L50V-35m/s 夹辅具:双顶尖、拔盘 量具:片形双头卡规2、确定工序尺寸 见表33、确定切削用量及计算基本时间(1) 计算切削用量:切削深度(2) 确定进给量:由参考文献17 表1225 可得(3) 计算工时:由参考文献17 得, 由参考文献7 表6.29,得k=1.5(五) 70工序半精车各外
32、圆表面数控车削工序设计(方案二)1、 加工设备:CK0630数控车床 工艺装备:刀具:刀片材料YT15,刀杆尺寸 2525mm,刀具为偏头外圆车刀,记为T1。T2为切槽刀,宽2mm,T3为螺纹车刀。 夹辅具:双顶尖、拔盘 量具:游标卡尺 0.02 0200根据CK0630数控车床的说明书,考虑到零件的材料及加工余量选 主轴转速: S=1000r/min 进给速度: F=50m/min2、零件加工尺寸如图所示: 3、 数控加工程序如下: N001 G90 N002 G54 X150 Z10 N003 M03 S1000 N004 M06 T1 N005 G00 X9.5 Z2 N006 G01
33、Z0 F50 N007 G01 X22 Z-1.5 N008 G01 Z-25 N009 G01 X25.484 N010 G01 Z-52 N011 G01 X40.481 Z-102 N012 G01 Z-141.5 N013 G01 X73.994 N014 G01 Z-147 N015 G01 X130 N016 G28 N017 G29 N018 M06 T2 N019 G00 X25 Z-25 N020 G01 X20 F50 N021 G01 X25 N022 G28 N023 G29 N024 M06 T3 N025 M03 S200 N026 G00 X22 Z2 N027
34、G91 N028 G33 D22 I19.8 X0.3 P1.5 L-23 Q0 NO29 G54 N030 G00 X25N031 G28N032 G29N033 M05N034 M02六、专用夹具设计 专用的机床夹具设计是机械制造工艺装备设计的一部分,夹具的优劣对零件加工精度、生产效率、制造成本、生产安全、劳动生产条件等都起着重要的作用。它用来确定工件与刀具的相对位置,将工件定位并夹紧。根据汽车转向节的技术要求,设计160工序钻、扩主销孔预孔28H10的钻床夹具。本夹具用于立式钻床,刀具为锥柄麻花钻和锥柄扩孔钻。(一)问题的提出 本夹具主要用来钻、扩主销孔30H9的预孔28H10,以达到零
35、件图上的有关技术要求。其中两孔有圆度、圆柱度和同轴度要求,还有距离尺寸要求和位置度要求。其中两孔的圆度和圆柱度要求由拉孔工序保证,其余要求由本工序的工艺及夹具保证。因此,本工序加工时,故本工序加工时,首先应考虑的是精度的问题,其次是如何提高生产率、降低劳动强度。(二)定位方案选择1、 定位基准的选择 如图1所示 为保证定位的精度,同时尽量减少与工件定位表面的接触面积,保证工件定位可靠,采用以工件尾柄在两套筒中定心,并以凸缘支承在其中一个套筒的端面上。工件又以法兰盘上的一个工艺孔为基准装在削边销上。两套筒限制四个不定度,端面限制一个不定度,削边销限制一个不定度,实现工件的完全定位。(三) 定位误
36、差分析及计算 如图1所示,工件采用套筒定位,故工件尾柄外圆轴线为第一定位基准,工件上的端面和法兰盘上的孔为第二和第三基准。工件上作为第一定位基准的外圆轴线,由于零件有角度倾斜,故有角度误差,钻头对工件有对刀误差以及钻模分度后还会存在分度误差。 削边销的尺寸及公差为10g6mm,对应销孔尺寸及公差为10H7mm。图1 工件定位示意图1、刀具、钻具、衬套的选择(1)直柄麻花钻25,1号扩孔钻28(2)钻套的选择 快换钻套,配用螺钉为M8,对应衬套, 扩套,配用螺钉为M8,对应衬套,2、对刀误差(1)TL夹: (2)(3)(4) (5)E 其中h=5mm,B=40mm E=0.08x(75/2+5+
37、40)/75=0.088mm 由零件图可得同轴度为0.5mm 3、角度误差 轴颈25mm与套筒的配合为H7/g6 轴颈40mm与套筒的配合为H7/g6 4、分度误差 L=1+2+e=0.136/2+0.08+0.018+0.003=0.169mm通过以上计算可以得出,该夹具满足工序要求,可以使用。(四)夹紧方案选择 本零件属于大批大量生产,所以在选择夹紧方案时除首先保证夹紧可靠外,还应考虑如何保证较高的生产率。因本零件形状较复杂,为了降低制造成本,使用通用机床,使工件装卸方便,所以选用手动螺旋夹紧。(五)夹紧力计算1、确定轴向切削力 由参考文献7,表2.7可得进给量f=0.39-0.47mm/
38、r,再由钻床Z535得f=0.32mm/r 由参考文献7,表2.32可得钻孔时轴向力、扭矩的计算公式:轴向力: 其中 , , , 扭矩: 其中 , , ,2、 确定夹紧力 工件受力图及压板受力图(如图2所示) 钻削时产生的扭矩由夹紧力和轴向力所产生的摩擦力矩来平衡。 静力矩方程: 由参考文献4,可取安全系数K=3实际夹紧力 由参考文献4,可知 其中 由参考文献3可确定星形轮处的螺栓为M16(a)工件受力 (b)压板受力图2 工件受力及压板受力示意图(六)夹紧力方向与夹紧力作用点的选择 按夹紧力方向应朝向对保证工件精度影响最大的定位面,应使工件变形最小,选择夹紧力方向水平,作用点选择在工件法兰盘
39、的中心,这样就保证了工件定位时已获得的正确位置。七、专用刀具设计 专用刀具设计是工艺装备设计的重要组成部分。在本次设计中选择190工序钻铰锥孔中所用的1:8锥度铰刀为设计内容。铰刀材料为高速钢W18Cr4V,硬度为HRC60-65。在立式钻床Z535进行加工由参考文献5中可得D=29.5mm,d=22.50.1mm。(一)铰刀的几何角度 1.铰刀切削部分呈锥形,其锥角2kr的大小主要影响被加工孔的质量和饺削时轴向力的大小。切削锥角:切削锥角的大小通常影响铰刀参加工作的长度和切屑厚薄以及各分力间的比值,对加工质量有较大影响,机用铰刀工作时,为提高切削效率,其导向和进给由机床保证在铰制刚件时kr=
40、1215。 2.前角和后角:由于铰刀切下的切屑很薄,切屑和前后刀面的的接触长度很短,前角的作用不显著,为制造方便,在精加工时,常取=0,而后角值应较大,但考虑到铰刀重磨后径向尺寸不至于变化过大,故一般取=610。刃磨后角时切削部分的刀齿必须磨尖而不留刃带,校准部分必须留有0.0050.3mm的刃带,以抛光和校准孔径,并便于制造和检验铰刀。 3. 轴向刃倾角:直槽硬质合金铰刀为便于制造,一般取=0,为避免切屑檫伤已加工表面也可取=-(35)(二) 锥柄的选择 铰刀锥柄选用莫氏2#锥度。(三)齿数:铰刀的加工余量小,容屑槽浅,所以齿数可以做得少,为了测量教导的直径,齿数一般选择偶数,根据孔径选择4
41、个齿。机用铰刀通常采用等距分布。故本铰刀采用等距分布的4齿锥柄饺刀。(四)中心孔的选择 中心孔选B2(GB14585)。其余尺寸和技术要求见附件六。八、专用量具的设计 量具设计是工艺装备设计的重要组成部分。在机械加工中经常用到专用量具,所以工艺人员需要经常根据实际设计专用量具。本次设计工序170拉削30孔后检验孔径的专用塞规。 30孔的上下偏差分别为:ES=0.045mm,EI=0mm。由参考文献12、16、21选通用IT7级精度,尺寸为30的量规的制造公差T=0.0024mm,Z=0.0034mm,则T/2=0.0012 画量规公差带图:计算量规的工作尺寸:塞规通端的基本尺寸:塞规通端的标注
42、尺寸:塞规止端的基本尺寸:塞规止端的标注尺寸:塞规材料选择40钢,对通端和止端表面进行氮化处理,工作面硬度HRC5865,其余表面硬度略低。塞规结构采用装配式结构,通端和止端用1:50锥轴与塞规手柄杆装配成一体。设计图样见附件六。九、结束语 历时两个多月,本次毕业设计顺利完成。在这次设计中我得到了以下几点体会:1、作为科技工作者和工程技术人员必须培养求真、务实和严谨的科学态度,必须培养理论联系实际、钻研创新与实事求是相结合的工作作风。2、必须培养独立工作与团队协作的能力与意识,使个人的能力在整个团队中充分发挥作用。3、 必须重视基础理论和基础知识的学习,只有在牢固的基础上才能有创新和发展。本着
43、力求能指导生产的指导思想,本次毕业设计基本达到了综合运用基本理论知识,解决实际生产问题的目的。但由于实践经验少、时间短等原因,本设计中存在许多不足和欠缺,望各位老师和同学指正,指出其中的不足和错误,提出改进建议。参 考 文 献1吴善元主编.现代制造技术J.扬州大学工学院,2004年10月14日2吴宗宪、罗圣国主编.机械设计课程设计M.北京:高等教育出版社,19993东北重型机械学院、洛阳工学院、第一汽车制造厂职工大学编.机床夹具设计手册(第二版)M.上海科学技术出版社,19984王启平主编.机床夹具设计(修订本)M.哈尔滨工业大学出版社,19965顾宗衔等编.机械制造工艺学(第二版)M.西安:
44、陕西科学技术出版社,19906邓文英主编.金属工艺学(上下册)M.高等教育出版社,19907艾兴、肖诗纲主编.切削用量简明手册M.机械工业出版社,19938李益民主编.机械制造工艺简明手册.机械工业出版社,19939赵家齐主编.机械制造工艺学课程设计指导书M.机械工业出版社,199410南京市机械研究所主编.金属切削机床夹具图册(第一版)M.机械工业出版社,198411王小华主编.机床夹具图册M.机械工业出版社,199212李硕根、吴骏等主编.互换性与技术测量(第二版)M.中国计量出版社,199113乐兑谦主编.金属切削刀具M.机械工业出版社,199314刘华明主编.金属切削刀具设计简明手册M
45、.机械工业出版社,199515大连理工大学工程教研室编.机械制图M.高等教育出版社,199316任嘉卉主编.公差与配合手册(第二版)M.机械工业出版社,200017成大先主编.机械设计手册(第三版)M.化学工业出版社,199318李华主编.机械制造技术M.机械工业出版社,199719国家自然科学基金委员会编.机械制造科学M.科学出版社,199520叶元烈主编.机械现代设计方法学M.中国计量出版社,200021李云主编.机械制造工艺及设备设计指导手册M.机械工业出版社,1997.822 孟少庆主编.机械加工工艺手册M.北京:机械工业出版社,1991.23李庆芬主编.机电工程专业英语M.哈尔滨工程
46、大学出版社,2001.624王丽娜主编.科技英语选读M.北京:北京外文出版,1999.925潘春旭主编.双面电弧焊接技术及其冶金学特征J. 四川:材料科学与工程研究新进展学术交流会论文集,2002年8月13-17日26潘春旭主编.AA4343/AA3003铝合金薄板钎焊接头的显微组织特征J.中国有色金属学报,2002年12月3日27陈浩、潘春旭、潘邻等主编.金属热处理J.中国有色金属学报,2002年5月,第27卷,第9期,pp.5-1028肖金生、刘杰、潘春旭等主编.陶瓷/金属梯度热障涂层的热冲击性能研究J.武汉理工大学学报, 2002年11月14日 28维普数据库.http:/202.202
47、.121.8/vip29陈家瑞主编.汽车构造(第四版M).北京:人民交通出版社,2002.2致 谢本次毕业设计是在李华英老师的悉心指导下完成的,如果没有李老师的指导和帮助,本论文不会顺利完成,她严谨的治学态度、丰富的实践经验和教学经验使我受益匪浅,在此致以衷心的感谢,还有就是要特别感谢周国玉老师和同组同学对我帮助和指导,她不但耐心的给我们解答设计中遇到的问题,还为我们提供了很多设计中需要的参考资料。在此表示衷心的感谢。 四年的大学生活,有过失败,有过成功,能够顺利的毕业,有赖于院系领导和老师的关怀、照顾以及同学的热心帮助,在此我表示衷心的感谢!湖北汽车工业学院机械工程系机 械 加 工 工 艺
48、过 程 卡第 页共 页零件名称轴承盖年产设计钢领10000材 料HT150毛坯种类盘类工序号工 序 名 称设 备 名 称设 备 型 号设备数量作业时间min工时定额min设备负荷率%备 注1粗车台阶面、62g6外圆柱表面以及左端面和退刀槽卧式车床C6127121.22粗镗31内孔表面、内台阶面以及50内孔表面卧式镗床T61614.63钻4个台阶孔立式钻床Z525116.84粗铣平面及圆弧面卧式铣床X6015精铣平面卧式铣床X6011.96半精镗31内孔表面、内台阶面以及50内孔表面卧式镗床T616122.17精铰4个台阶孔立式钻床Z525173.28半精车台阶面、62g6外圆柱表面以及倒角卧式
49、车床C61271209半精车左端面卧式车床C612715.410精磨62g6外圆柱表面万能磨床M12019.1班级T813-5学号组号姓名批 阅成绩日期机械加工工艺过程卡填写说明湖北汽车工业学院机械工程系机 械 加 工 工 艺 过 程 卡共(1)页第(2)页零件名称(3)年生产钢领(4)材料(5)毛坯种类(6)每坯件数(7)工序号工 序 名 称设 备 名 称设 备 型 号设备数量作业时间min工时定额min设备负荷率%备 注(8)(9)(10)(11)(12)(13)(14)(15)(16)班级组号成员批阅组成绩日期(1)过程卡和工序卡的总页数;(2)当前页页序;(3)按零件图填写;(4)按设
50、计任务书填写,包括了备品率和废品率;(5)按零件图填写;(6)填写“铸件”、“锻件”、“圆钢”、“板钢”等;(7)每毛坯可加工同一零件的数量;(8)工序号,可依自然数连续或不连续编号;(9)工序名称如“钻孔”、“粗铣面”、“攻螺纹”等;(10)填写设备名称如“立钻”;(11)填写设备型号如“Z5125A”;(12)填写该工序所需设备数量;(13)基本时间tm和辅助时间ta之和,也称为操作时间。基本时间取自工序卡。辅助时间按工序卡所表明的工序操作动作,查各动作的时间定额标准并累加得到(未见占基本时间百分比数据);(14)工时定额tt按公式tt=(tm+ta)1+(+)计算。其中布置工作地时间、休息和生理需要时间按它们占作业时间的百
- 温馨提示:
1: 本站所有资源如无特殊说明,都需要本地电脑安装OFFICE2007和PDF阅读器。图纸软件为CAD,CAXA,PROE,UG,SolidWorks等.压缩文件请下载最新的WinRAR软件解压。
2: 本站的文档不包含任何第三方提供的附件图纸等,如果需要附件,请联系上传者。文件的所有权益归上传用户所有。
3.本站RAR压缩包中若带图纸,网页内容里面会有图纸预览,若没有图纸预览就没有图纸。
4. 未经权益所有人同意不得将文件中的内容挪作商业或盈利用途。
5. 装配图网仅提供信息存储空间,仅对用户上传内容的表现方式做保护处理,对用户上传分享的文档内容本身不做任何修改或编辑,并不能对任何下载内容负责。
6. 下载文件中如有侵权或不适当内容,请与我们联系,我们立即纠正。
7. 本站不保证下载资源的准确性、安全性和完整性, 同时也不承担用户因使用这些下载资源对自己和他人造成任何形式的伤害或损失。
最新文档
- 2020【企业咨询】行业前景分析投资调研课件
- 2020、6《民法典》资深律师解读宣讲课件
- 2020《推广普通话主题班会》课件
- 1205史剑波《纪昌学射》教学ppt课件
- 1981-1990诺贝尔生理或医学奖课件
- 2020【CDMO】行业前景分析投资调研课件
- 2020-2021年A股投资策略报告课件
- 2020【自助售货机】行业前景分析投资调研课件
- 刘姥姥进大观园PPT部编版9上课件
- 2020-2021年创新说课大赛获奖作品:教师说课比赛:等差数列课件
- 婚姻家庭与继承法课件
- 2020-2021年85、95后宝妈人群洞察课件
- 青少年的同伴关系
- 2020-2021年创新说课大赛获奖作品:教师说课比赛:等差数列的前n项和课件
- 青少年用眼健康知识讲解