分离工程脱乙烷塔课程设计
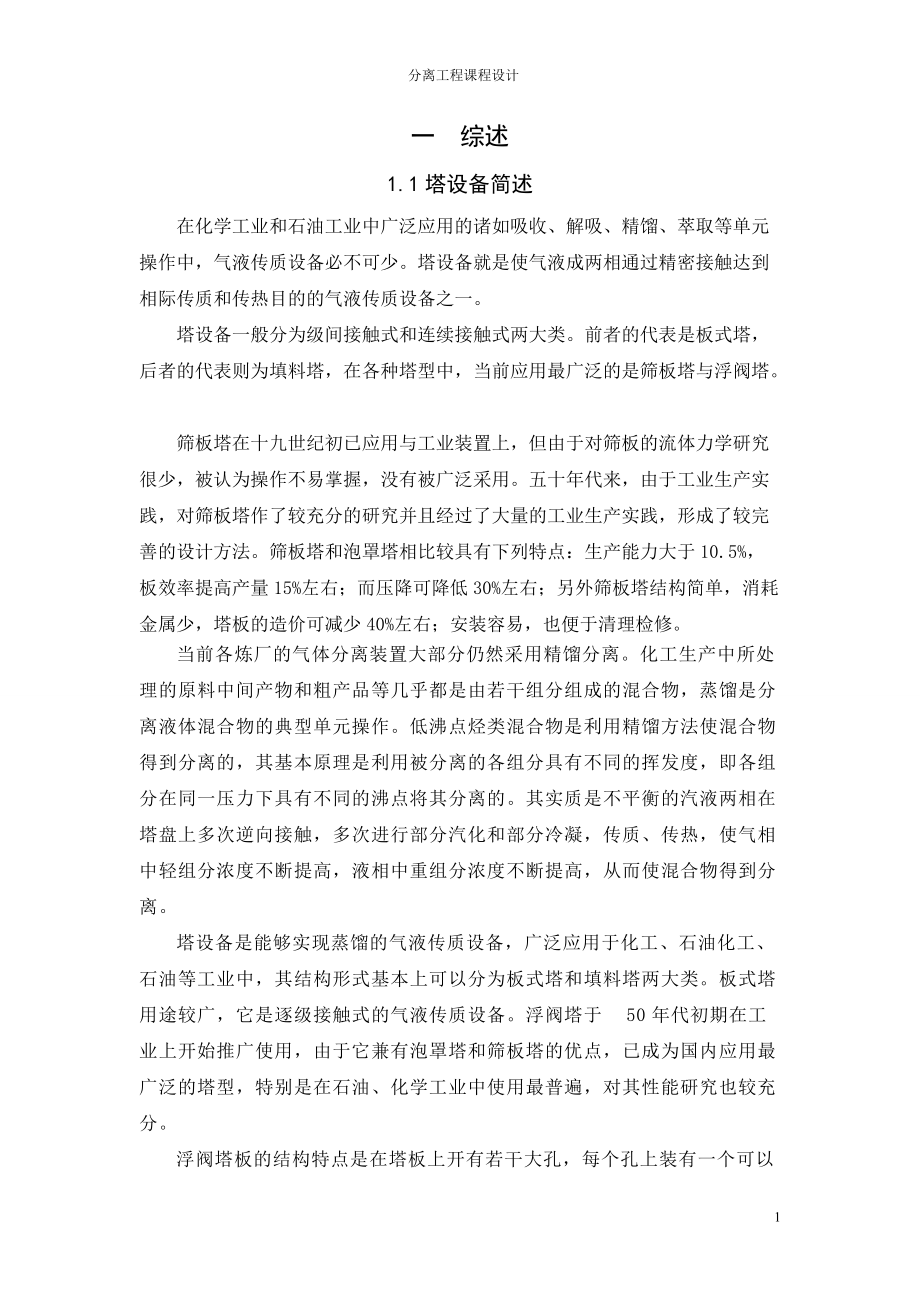


《分离工程脱乙烷塔课程设计》由会员分享,可在线阅读,更多相关《分离工程脱乙烷塔课程设计(35页珍藏版)》请在装配图网上搜索。
1、 分离工程课程设计一 综述1.1塔设备简述在化学工业和石油工业中广泛应用的诸如吸收、解吸、精馏、萃取等单元操作中,气液传质设备必不可少。塔设备就是使气液成两相通过精密接触达到相际传质和传热目的的气液传质设备之一。塔设备一般分为级间接触式和连续接触式两大类。前者的代表是板式塔,后者的代表则为填料塔,在各种塔型中,当前应用最广泛的是筛板塔与浮阀塔。筛板塔在十九世纪初已应用与工业装置上,但由于对筛板的流体力学研究很少,被认为操作不易掌握,没有被广泛采用。五十年代来,由于工业生产实践,对筛板塔作了较充分的研究并且经过了大量的工业生产实践,形成了较完善的设计方法。筛板塔和泡罩塔相比较具有下列特点:生产能
2、力大于10.5%,板效率提高产量15%左右;而压降可降低30%左右;另外筛板塔结构简单,消耗金属少,塔板的造价可减少40%左右;安装容易,也便于清理检修。当前各炼厂的气体分离装置大部分仍然采用精馏分离。化工生产中所处理的原料中间产物和粗产品等几乎都是由若干组分组成的混合物,蒸馏是分离液体混合物的典型单元操作。低沸点烃类混合物是利用精馏方法使混合物得到分离的,其基本原理是利用被分离的各组分具有不同的挥发度,即各组分在同一压力下具有不同的沸点将其分离的。其实质是不平衡的汽液两相在塔盘上多次逆向接触,多次进行部分汽化和部分冷凝,传质、传热,使气相中轻组分浓度不断提高,液相中重组分浓度不断提高,从而使
3、混合物得到分离。塔设备是能够实现蒸馏的气液传质设备,广泛应用于化工、石油化工、石油等工业中,其结构形式基本上可以分为板式塔和填料塔两大类。板式塔用途较广,它是逐级接触式的气液传质设备。浮阀塔于50年代初期在工业上开始推广使用,由于它兼有泡罩塔和筛板塔的优点,已成为国内应用最广泛的塔型,特别是在石油、化学工业中使用最普遍,对其性能研究也较充分。浮阀塔板的结构特点是在塔板上开有若干大孔,每个孔上装有一个可以上、下浮动的阀片,浮阀的型式很多,目前国内最常用型式的为F1型和V-4型。F1型浮阀的结构简单、制造方便、节省材料、性能良好,广泛用于化工及炼油生产中,现已列入部颁标准(JB1118-68)。操
4、作时,由阀孔上升的气流,经过阀片与塔板的间隙与塔板上横流的液体接触,浮阀开度随气体负荷而变,当气量很小时,气体仍能通过静止开度的缝隙而鼓泡。1.2我国化工工艺发展我国石油工业具有一定的水平,但还是一个发展中的国家,摆在我们石油工作者面前的任务是繁重的。炼油工业要对现有的炼油厂进行技术改造,继续坚持“自力更生,革新挖潜,全面提高,综合利用,大搞化工原料,赶超世界先进水平”的发展方针。要立足现有基础,搞好一、二次加工和系统工程的配套,扩大综合生产能力;要革新工艺,革新技术,革新设备,把老装置开出新水平;要发展加氢技术,发展新型催化剂和添加剂,全面提高产品质量,增加品种;要开展综合利用,大搞三次加工
5、,增产有机化工原料;要充分利用热能,大力降低消耗,各项经济技术指标要创出新水平;要治理“三废”,保护环境,为实现赶超世界先进水平而奋斗。二 设计方案的选择2.1工艺设计的原则工艺流程设计是工艺设计的核心,在整个设计中,设备选型、工艺计算、设备布置等工作都与工艺流程有直接关系。只有流程确定后,其他各项工作才能展开,工艺流程设计设计各个方面,而各个方面的变化又反过来影响 工艺流程设计,设置使流程发生较大的变化。因此,工艺流程设计是动手最早,而往往结束最晚。流程设计的主要任务包括两个方面:一是确定生产流程中各个生产过程的具体内容、顺序和组合方式;二是绘制工艺流程图,要求以图解的形式表示生产过程中,当
6、原料经过各个单元操作过程得到产品时,物料和能量发生的变化及其流向,以及采用了哪些化工过程和设备,再进一步通过图解形式表示出化工管道流程和计量控制流程。选型和工艺设计的原则如下:合理性 即设备必须满足工艺一般要求,设备与工艺流程、生产规模、工艺操作条件、工艺控制水平相适应,又能充分发挥设备的能力。先进性 要求设备的运转可靠性、自控水平、生产能力、转化率、收率、效率要尽可能的达到先进水平。安全性 要求安全可靠、操作稳定、弹性好、无事故隐患 。对工艺和建筑,地基、厂房等无苛刻要求;工人在操作时,劳动强度小,尽量避免高温高压操作,尽量不用有毒有害的设备附件附料。经济性 设备投资省,易于加工、维修、更新
7、,没有特殊的维护要求,运行费用减少。引进先进设备,亦应反复对比报价,考察设备性能,考虑是否易于被国内消化吸收和改进利用,避免盲目性。总之,在设备的设计及选型中,要综合考虑合理性、先进性、安全性、经济性的原则,审慎的研究,认真的设计。 2.2精馏操作对塔设备的要求精馏所进行的是气、液两相之间的传质,而作为气、液两相传质所用的塔设备,首先必须要能使气、液两相得到充分的接触,以达到较高的传质效率。但是,为了满足工业生产和需要,塔设备还得具备下列各种基本要求: () 气、液处理量大,即生产能力大时,仍不致发生大量的雾沫夹带、拦液或液泛等破坏操作的现象。 () 操作稳定,弹性大,即当塔设备的气、液负荷有
8、较大范围的变动时,仍能在较高的传质效率下进行稳定的操作并应保证长期连续操作所必须具有的可靠性。 () 流体流动的阻力小,即流体流经塔设备的压力降小,这将大大节省动力消耗,从而降低操作费用。对于减压精馏操作,过大的压力降还将使整个系统无法维持必要的真空度,最终破坏物系的操作。 () 结构简单,材料耗用量小,制造和安装容易。 () 耐腐蚀和不易堵塞,方便操作、调节和检修。() 塔内的滞留量要小。2.2.1板式塔类型: 气液传质设备主要分为板式塔和填料塔两大类。精馏操作既可采用板式塔,也可采用填料塔,板式塔为逐级接触型气液传质设备,其种类繁多,根据塔板上气液接触元件的不同,可分为泡罩塔、浮阀塔、筛板
9、塔、穿流多孔板塔、舌形塔、浮动舌形塔和浮动喷射塔等多种。板式塔在工业上最早使用的是泡罩塔(1813年)、筛板塔(1832年),其后,特别是在本世纪五十年代以后,随着石油、化学工业生产的迅速发展,相继出现了大批新型塔板,如S型板、浮阀塔板、多降液管筛板、舌形塔板、穿流式波纹塔板、浮动喷射塔板及角钢塔板等。目前从国内外实际使用情况看,主要的塔板类型为浮阀塔、筛板塔及泡罩塔,而前两者使用尤为广泛。2.2.2筛板塔:筛板塔也是传质过程常用的塔设备,它的主要优点有: () 结构比浮阀塔更简单,易于加工,造价约为泡罩塔的60,为浮阀塔的80左右。 () 处理能力大,比同塔径的泡罩塔可增加1015。 ()
10、塔板效率高,比泡罩塔高15左右。 () 压降较低,每板压力比泡罩塔约低30左右。 筛板塔的缺点是: () 塔板安装的水平度要求较高,否则气液接触不匀。 () 操作弹性较小(约23)。() 小孔筛板容易堵塞。2.2.3浮阀塔: 浮阀塔是在泡罩塔的基础上发展起来的,它主要的改进是取消了升气管和泡罩,在塔板开孔上设有浮动的浮阀,浮阀可根据气体流量上下浮动,自行调节,使气缝速度稳定在某一数值。这一改进使浮阀塔在操作弹性、塔板效率、压降、生产能力以及设备造价等方面比泡罩塔优越。但在处理粘稠度大的物料方面,又不及泡罩塔可靠。浮阀塔广泛用于精馏、吸收以及脱吸等传质过程中。塔径从200mm到6400mm,使用
11、效果均较好。国外浮阀塔径,大者可达10m,塔高可达80m,板数有的多达数百块。 浮阀塔之所以这样广泛地被采用,是因为它具有下列特点: () 处理能力大,比同塔径的泡罩塔可增加2040,而接近于筛板塔。 () 操作弹性大,一般约为59,比筛板、泡罩、舌形塔板的操作弹性要大得多。 () 塔板效率高,比泡罩塔高15左右。 () 压强小,在常压塔中每块板的压强降一般为400660N/m2。 () 液面梯度小。 () 使用周期长。粘度稍大以及有一般聚合现象的系统也能正常操作。() 结构简单,安装容易,制造费为泡罩塔板的6080,为筛板塔的120130据此本课程设计选取浮阀塔。2.3设计方案确定2.3.1
12、操作条件的确定:确定设计方案是指确定整个精馏装置的流程、各种设备的结构型式和某些操作指标。本设计的操作压力为235.5kpa。塔顶设置冷凝器,塔底设置再沸器。2.3.2进料状态:进料状态与塔板数、塔径、回流量及塔的热负荷都有密切的联系。在实际的生产中进料状态有多种,但一般都将料液预热到泡点或接近泡点才送入塔中,这主要是由于此时塔的操作比较容易控制,不致受季节气温的影响。此外,在泡点进料时,精馏段与提馏段的塔径相同,为设计和制造上提供了方便。本设计采用泡点进料。2.3.3加热方式: 蒸馏釜的加热方式通常采用间接蒸汽加热,设置再沸器。有时也可采用直接蒸汽加热。若塔底产物近于纯水,而且在浓度稀薄时溶
13、液的相对挥发度较大,便可采用直接蒸汽加热。直接蒸汽加热的优点是:可以利用压力较低的蒸汽加热;在釜内只须安装鼓泡管,不须安置庞大的传热面。这样,可节省一些操作费用和设备费用。然而,直接蒸汽加热,由于蒸汽的不断通入,对塔底溶液起了稀释作用,在塔底易挥发物损失量相同的情况下,塔底残液中易挥发组分的浓度应较低,因而塔板数稍有增加。本设计采用间接加热方式。下图是工艺装置原则流程图:三 脱烷烃精馏塔工艺计算3.1全塔物料平衡计算3.1.1 原始数据获取:表3-1 原料各组分数据汇总处理量项目200kmol/h组分i进料组成(摩尔分数)0.250.40.20.15分离要求 进料条件泡点进料,P=235.5k
14、p3.1.2 清晰分隔物料衡算:根据题意得:正戊烷为轻关键组分,正己烷为重关键组分。由清晰分割法计算: 表3-2 清晰分割物料衡算计算结果汇总组分i0.250.40.20.1550804030507640130043630700.38460.58460.0308000.05710.51430.42863.1.3 用泡点方程计算塔底温度:初设,由K-P-T图查得各组分的值,计算得,表明原假设温度偏高,按下表3-3计算结果可知汽相量最大的是正己烷,由公式得:由K-P-T图按P=235.5KP,查得t=107,再求得各组分相平衡常数值,计算结果如下表3-3:表3-3 泡点方程计算塔底温度结果组分i0
15、0.05710.51430.42861106.42.61.30.5800.14860.66860.24861.06581076.22.51.20.5400.14290.61720.23140.9915在所设的107条件下,符合要求。塔底温度为107。3.1.4 用露点方程计算塔顶温度:因为本塔采用全凝气,所以塔顶温度就是塔顶产品的露点温度。初设,由K-P-T图查得各组分的值,计算得,表明原假设温度偏低,按下表3-4计算结果可知液相量最大的是正戊烷,由公式得:由K-P-T图按P=235.5KP,查得t=57,再求得各组分相平衡常数值,计算结果如下表3-4:表3-4 露点方程计算塔顶温度结果组分i
16、0.38460.58460.03080562.20.780.290.110.17480.74950.106101.0304572.30.80.30.120.16720.73080.102601.0006在所设的57条件下,符合要求。塔顶温度为57。3.1.5 不清晰分割验证:求以重关键组分为对比组分的各组分的平均相对挥发度,用泡点方程计算列表如下:表3-5 各组分平均相对挥发度组分i2.30.80.30.127.6672.66710.46.22.51.20.545.1672.08310.456.2942.35710.4243代入汉斯特别克公式,得到: =分别将各组分的平均相对挥发度代入上式求得
17、,进一步求得,。列表如下:表3-6 ,计算结果组分i6.2942.35710.42436.9103196.510-45080403049.99287640.0195130.01237.210-343629.980569.98770.38450.58460.03080.00010.00010.05710.51440.4284 由上表数据可知: 符合要求。设塔底温度为107,列表计算如下:表3-7 组分i0.00010.05710.51440.42841.00001.22.51.20.540.000120.14290.61720.23140.99162塔底温度为107正确。设塔顶温度为57,列表计
18、算如下:表3-8组分i0.38450.58460.03080.00011.00002.30.80.30.120.16720.73080.10260.00081.0014塔顶温度为57正确。3.1.6 用泡点方程计算进料温度:设进料温度为,由K-P-T图查得各组分的值,计算得,表明原假设温度偏低,按下表3-9计算结果可知汽相量最大的是,由公式得:由K-P-T图按P=235.5KP,查得t=62,再求得各组分相平衡常数值,计算结果如下表3-9:表3-9 泡点方程计算进料温度结果组分i0.250.40.20.15601.80.820.310.130.450.3280.0620.01950.85956
19、22.20.880.340.140.550.3520.0680.0351.005在所设的62条件下,符合要求。进料温度为62.3.2用芬克斯方程计算最少理论塔板数 =5.99块3.3恩德伍德法求最小回流比塔顶、塔底的平均温度是:以为对比组分求各组分在P=235.5KP, 时的相对挥发度:表3-10 各组分相对挥发度82组分i0.250.40.20.153.81.50.60.266.32.510.43 因为是泡点进料,所以e=0 通过试差法计算求:表3-11 列表=1.220.30410.7813-0.9091-0.08160.095=1.20.30880.7692-10.0838-0.0058
20、=1.2 最小回流比3.4吉利兰法计算求理论板数操作回流比一般为最小回流比的倍。即:本塔取1.6倍,Y= = =0.5解得:S=12.98理论板数为12.98块。3.5计算理论进料位置=0.78S=n+m+1 =0.78解得:n=5.2 m=6.7精馏段理论塔板数:n=5.2块提留段实际塔板数:m=6.7块3.6计算实际板数和实际进料位置查表得各组分在时的黏度:3-12 各组分黏度组分i0.250.40.20.150.0950.1510.3060.2420.1817又=2.5 =0.5944 =59.44%实际塔板数:块精馏段实际塔板数:块提留段实际塔板数:=21-9=12块精馏塔工艺计算部分
21、计算结果列于下表:表3-13 精馏塔工艺计算结果项目符号数值单位进料流量200Kmol/h操作压力235.5KPa进料温度62塔顶温度107塔底温度57塔底产品流量130.0123Kmol/h塔顶产品流量69.9877Kmol/h最小回流比0.444实际回流比0.711最少理论板数5.99块全塔理论板数12.98块全塔总版效率59.44%全塔实际板数21块精馏段实际板数9块提馏段实际板数12块加料板位置第10块四 浮阀塔的设计计算4.1选取设计塔板4.1.1板型选取:根据化学工业出版社化工原理提供的液相流量参考表选取单流型塔板,单流型塔板是最常用的形式,结构简单,制作方便,且横贯全板的流道长,
22、有利于达到较高的塔板效率。4.1.2板间距的初选: 板间距NT的选定很重要,对完成一定生产任务,若采用较大的板间距,能允许较高的空塔气速,对塔板效率、操作弹性及安装检修有利;但板间距增大后,会增加塔身总高度,金属消耗量,塔基、支座等的负荷,从而导致全塔造价增加。反之,采用较小的板间距,只能允许较小的空塔气速,塔径就要增大,但塔高可降低;但是板间距过小,容易产生液泛现象,降低板效率。所以在选取板间距时,要根据各种不同情况予以考虑。如对易发泡的物系,板间距应取大一些,以保证塔的分离效果。板间距与塔径之间的关系,应根据实际情况,结合经济权衡,反复调整,已做出最佳选择。设计时通常根据塔径的大小,由塔板
23、间距的经验数值选取.初选板间距为0.45m.4.2汽、液体体积流量计算4.2.1 精馏段、提馏段的摩尔流量计算:精馏段气体摩尔流量: V=L+D=(R+1)D=(0.711+1)130.0123=224.45kmol/h=0.0624kmol/s提馏段气体摩尔流量:v=v=0.0624kmol/s精馏段液体摩尔流量:L=RD=130.01230.711=92.4kmol/h=0.0257kmol/s提馏段液体摩尔流量:L=L+F=92.44+200=292.44kmol/h=0.0812kmol/s4.2.2 精馏段、提馏段的体积流量计算:表4-1 气体体积流量计算表组分i58.12472.1
24、5186.178100.2050.38450.58460.03080.00010.00010.05710.51440.428422.348742.17952.65430.0167.19250.00584.1244.3342.927891.38360.16720.73080.10260.00080.000120.14290.61720.23140.00710.310453.189123.187486.69399.178352.7288.84190.080271.3684塔顶气体密度: 塔底气体密度:气体平均密度:塔顶气体体积流量:塔底气体积流量:全塔平均气体体积流量:表4-2 液体体积流量计算表
25、组分i0.00010.05710.51440.428458.12472.15186.178100.2050.00584.1244.3342.927891.38360.00060.04510.48510.46960.5790.8150.6590.6840.00010.05530.73610.68651.478322.347842.17952.65430.019.718352.7288.84190.080271.36840.13620.73880.12390.00110.23520.96050.1880.00161.3313塔底液体密度:塔顶液体密度:液体平均密度:塔底液体体积流量:塔顶液体体积流
26、量:全塔平均液体体积流量:4.3液体表面张力计算查表得各个组分的表面张力:表4-3 各组分表面张力组分i(57)3.1246.3998.02816.26(107)4.0797.75210.1812.510.00010.05710.51440.42840.16720.73080.10260.00080.00040.44265.23665.359311.03890.52234.67640.82370.0136.0354液体平均表面张力:4.4塔径的计算4.4.1 求上限空塔气速:取板间距(参考化工原理,浮阀塔板间距参考数值),由史密斯关联图查得:则上限空塔气速:4.4.2 计算空塔气速:适宜的空塔
27、气速是乘以安全系数,安全系数取(0.60.8)之间,本设计取安全系数为0.7,4.4.3 选取塔径和实际空塔气速:,根据浮阀塔直径系列标准圆整取塔径为1.4m。实际空塔流速: 4.5计算塔截面积塔截面积:4.6计算塔的有效高度塔的有效高度:4.7塔板的设计4.7.1 确定塔板溢流形式:根据有关文献介绍选取单溢流塔板操作。4.7.2 确定降液管的结构形式:根据有关资料降液管的结构形式采用弓形降液管。4.7.3 降液管的底隙高度:对于单溢流取堰长:取液体通过降液管底隙时的流速降液管的底隙高度:。取值根据经验一般可取0.070.25之间。确定的原则是保证流体流经此处时的阻力不太大,同时要有良好的液封
28、。4.7.4 求降液管的宽度及截面:,查化工原理图得: 4.7.5 求液体在降液管内的停留时间 能够满足要求。4.7.6 塔板四区尺寸的确定:边缘区宽度WC取0.05m。破沫区宽度WS取0.06m。溢流区宽度Wd=0.196m。鼓泡区面积Aa: =1.5854.7.7 初算浮阀个数:浮阀塔的操作性能以板上所有浮阀处于刚刚全开时的情况为最好,此时塔板的压强降及板上液体的泄露都比较小,且操作弹性较大,根据工业生产装置的数据对F1型重浮阀而言,当板上所有浮阀刚刚全开时,F0动能因数常在912之间。本设计取F0=10,因为,设为气体通过阀孔时的速度,F0为气体通过阀孔时的动能因数,为气体密度,则。d0
29、为浮阀孔直径取d0=0.039m,则,4.7.8 核算阀孔动能因数及孔速:因为阀孔动能因数变化不大仍在912范围之内,所以选取合理。4.7.9计算塔板开孔率:开孔率= 在(5%15%)内,符合要求。4.8塔板的水力学计算塔板的流体力学验算,目的在于核算上述各项工艺尺寸已经确定的塔板,在设计任务规定的气液负荷下能否正常操作。其内容包括对塔板压强、液泛、雾沫夹带、泄漏等项的验算。4.8.1气体通过浮阀塔板的压强降:1、干板阻力hC:临界孔速: 故用下式计算:2、板上充气液层阻hR:因为分离的混合物为碳氢化合物的混合物,故取板上充气程度因数0=0.45,取板上液层高度hL=0.06m。则3、液体表面
30、张力造成的阻力hP:浮阀塔的h值通常很小,计算时可以忽略,所以气体通过浮阀板的压降为hP=hC+hR=0.0356+0.027=0.0626m液柱,单板压降PP=hPLg=0.0626713.89.81=438.35KPa4.8.2液泛:该塔板不设进口堰,故液体通过降液管的压降:降液管降液管中当量清液层高度为:实际降液管中液体和泡沫的总高度大于0.13216这个值,为了防止液泛,应保证降液管中泡沫液体的总高度不超过上层塔板的出口堰,所以在设计中令,是参数考虑到降液管内液体充气及操作安全两种因素的校正系数。一般物系取=0.5,取出口堰高度hW=0.05m,HT=0.45m符合要求不会淹塔。4.8
31、.3雾沫夹带:式中:VS、VL分别为气、液负荷m3/s;、分别为塔内气、液密度kg/m3;ZL为板上液体流经长度m,对单溢流塔板ZL=D-2WS=1.4-20.196=1.008m;Ab为板上液体流经面积m2,对单溢流塔板Ab=AT-2Af=1.5386-20.123=1.2926m2;CF为泛点负荷系数,可根据气相密度及板距HT查得,CF=0.128,泛点率= = =45.84%80%或泛点率= =44.2%80%对于D0.9m的大塔,泛点率都应小于80%,实际求得的泛点率均小于80%,符合要求,所以雾沫夹带量能满足eV0.1kg(液)/kg(气)。4.9塔板负荷性能图4.9.1泄漏线以F0
32、=5作为规定气体取小负荷的标准,则根据(VS)min在纵坐标轴上定出一点作水平线,即为泄漏线。4.9.2液相负荷上限线:以=5秒作为液体在降液管中停留时间下限值,即(LS)max=AfHT/5=0.1230.45/5=0.0111m3/s。根据(LS)max在横坐标轴上定出一点C并作垂线,即为液相负荷上限线。4.9.3液相负荷下限线:对于平堰,一般取堰上液层高度h0W=0.006m作为液相负荷下限条件,低于此限时便不能保证板上液流的均匀分布,降低气液接触效果,根据公式:,一般how取作为下限条件。根据在横坐标轴取定一点B作垂线,即为液相负荷下限线。4.9.4液泛线:根据可导出VS与VS的关系式
33、,即。式中:则:表4-40.0010.0050.0080.010.0110.13080.12400.11820.11370.1114根据表的数据,再绘制出液泛线。4.9.5雾沫夹带上限线:雾沫夹带上限线表现了雾沫夹带量eV=0.1kg(液)/kg(汽)时的LSVS的关系。按泛点率=80%时找出LS与VS的关系,即泛点率= =80%绘图即雾沫夹带上限线。根据以上五条线绘出塔板负荷性能图:图4-1 塔板负荷性能曲线图4.9.6技术分析:(1)由塔板负荷性能图可以看出,在规定的气液负荷下的操作点在适宜操作区内的适宜位置,这说明本设计比较合理。(2) 因操作上限受雾沫夹带线控制,因此,若处理量提高较大
34、时,适当将雾沫夹带线上移,即提高板间距或加大开孔区面积。 表4-5 浮阀塔板设计计算结果及符号一览表项目符号单位数据及说明备注塔径m1.4板间距m0.45塔板形式重浮阀,单溢流降液管溢流堰高m0.05溢流堰长m0.98板上液层高度m0.13216降液管底隙高度m0.0303降液管宽度m0.196降液管截面积0.123鼓泡区面积1.585塔截面积1.5386浮阀个数个163阀孔直径m0.0309阀孔气速m/s4.0412空塔气速m/s0.51阀孔动能因数9.9647开孔率12.6%液体在降液管停留时间s9.9泛点率45.84%液相负荷上限0.0111液相负荷下限0.00084五接管尺寸计算5.1
35、进料管尺寸计算:表5-1 进料液体密度计算组分i0.250.40.20.1558.12472.15186.178100.20557981565968414.53128.860417.235615.030875.65780.19210.38150.22780.19870.33180.46810.34570.29051.4361进料管密度:取,经圆整取114mm.5.2塔顶蒸汽管尺寸计算:塔顶 5.3釜液出口管尺寸计算: ,取5.4塔高的计算:nF进料板数HF进料板间距nP人孔数HB塔底空间高度(6到8层设一人孔)HP人孔板间距HD塔顶空间高度H1封头高度H2裙座高度取, ,0.71.5,六 热量
36、衡算6.1塔顶冷凝器热量衡算冷凝器体系选取如下图:图6-1 冷凝器下表为基准焓值为57时饱和液相焓值,列汇总表如下:表6-1 塔顶冷凝器热量衡算计算表组分i58.12472.15186.178100.2050.38450.58460.03080.000118.6724.2329.5034.2641.725102278.30.34331517.89336.2塔底再沸器热量衡算下表为基准焓值为107时饱和液相焓值,列汇总表如下:表6-2 塔底再沸器热量衡算计算表组分i58.12472.15186.178100.2050.000120.14290.61720.231413.6520.4225.573
37、0.890.0952210.53791360.0443716.262286.9374七 课程设计总结对于设计过程我们通过查阅各种文献得到数据、公式,最后汇总。通过给出的任务进行计算,使我们的自学能力,汇总能力都得到了提高。对于最后部分塔附属高度的计算还不甚了解,很不熟练,有待提高。通过本次课程设计不仅增强了自己的自学能力,更促进了对分离工程知识的进一步了解,同时通过同学之间,同学和老师之间的相互交流使我的设计更加完善。 在良好的互动环境下我们大家都很努力认真,不仅是为了取得成绩,更是为了能在知识上,在能力上都有所提高。特别使对一些参考文献的使用,和对图表的查询都有了实质性的操作,动手能力也有了
38、显著提高,使我们大家都很高兴。虽然我们做设计的时间较以前的学哥学姐时间短,但我们相信我们的收获不比他们少。当然我知道自己的设计也许还存在这样或那样的不足,但我知道这是我努力的结果。我感谢能有这次让我努力并增长知识的机会,缺点和不足一定回尽力改正。这次课程设计确实是我自己第一次完整的来完成一件装置设计,真正让我体会到了设计好并非易事。书本的知识所有人都会学,但怎样把它用活,却是需要通过不断的实际经验积累获得的一种能力,需要自己有足够的耐心和毅力,还要有不耻下问虚心向他人请教的精神,学会独立思考的同时又要重视团队集体的智慧和力量。 通过本次课程设计,使我对从精馏塔设计方案到精馏塔设计的基本过程的设
39、计方法、步骤、思路有一定的了解与认识。它相当于实际精馏塔设计工作的模拟。在课程设计过程中,基本能按照规定的程序进行,先针对精馏塔的特点,收集、调查有关资料,然后进入草案阶段,其间与指导教师进行几次方案的讨论、修改、再讨论,逐步了解设计填料塔的基本顺序,最后定案。设计方案确定后,又在老师指导下进行扩充详细设计,并计算物料守衡、传质系数、填料层高度、塔高等,最后进行塔附件设计。此次课程设计基本能按照设计任务书、指导书、技术条件的要求进行。同学之间相互联系,讨论,整体设计基本满足使用要求,但是在设计指导过程中也发现一些问题。理论的数据计算不难,困难就在于实际选材,附件选择等实际问题。这些方面都应在以
40、后的学习中得以加强与改进。 八 体会以上是本次课程设计的指导过程中的心得与体会以及对课程设计完成情况的总结,希望在以后的学习当中能扬长避短,以取得更好的学习效果。 本次课程设计经过两周的时间得以完成,主要包括目录、绪论、设计方案、吸收塔的工艺计算等内容,主要通过上网搜集资料,查找统计文献,数据的整合计算,文字的筛选以及上机调试等部分组成,在此基础上形成了该课程设计的基础框架,最后由本人加以总结整合,提出了相关设计方案,具体内容在课程设计各章节均有所体现。本次课程设计让我取得了很多收获。 首先,通过课程设计资料的搜索以及对数据的计算中,让我对分离工程有了更加清晰、深刻的认识,课程设计本身的完成过
41、程,其实也是自己对分离工程轮廓的理解,对内容的把握的过程,这样可以更加丰富的了解分离工程的全貌,对自己的专业知识学习也更加深刻,不再流于表面。 其次,通过本次课程设计提高了我的逻辑思维能力以及对材料的整合和筛选能力,这对于我今后的研究和学习有很大的帮助,通过了整个课程设计方案的描述,让我更加全面的拓宽自己的思考能力。 再次,课程设计让我更加重视实践,重视对实际工作的关注,有利于提高我理论联系实际的能力。通过这次学习,我知道了如何去自觉学习,如何去体验实践的成果,如何在实践中后享受胜利的喜悦。 最后,对于我来说,独自完成课程设计是相当困难的,它的完成与老师和同学的合作是密不可分的,在共同的努力中
42、我感受到了团队的合作力量,团队的温暖,工作的同时也增进了我们的友谊,我想我们每个人都会为我们共同努力的汗水所骄傲和自豪。 但是,课程设计的完成并不代表我自身学习的终止,在完成过程中我发现自己有很多缺点不足。如:课程设计中的Auto CAD作用部分对自己来讲十分困难,另外,大量的内容也暴露出自己知识面窄,对实践活动的能力不强等诸多问题,我想困难和挑战才是激发自己前进的动力,自己也将会在今后的学习和生活中劈荆斩浪,挑战自我。 化工原理课程设计的完成对我来说有深刻的意义,我衷心感谢李翔老师的指导以及与我合作共同学习的同学,是你们带给我收获,带给我快乐!参考资料和文献1.化工原理(上、下册)谭天恩 窦
43、梅 周明华 编著。化学工业出版社(第三版) 2009年4月第21次印刷2.分离工程.张顺泽 刘丽华 徐辉 李翔 马江涛编著。河南城建学院3.化学单元操作基础. 化学工业出版社4.化学工程手册.北京:化学业出版社,19915.化工原理课程设计.天津:天津科学技术出版社,19946.化工设备设计.北京:清华大学出版社,19967.精细化工装备.李春燕 陆辟疆主编。化学工业出版社8.化工基本过程与设备.化学工业出版社9.化工物性算图手册.刘光启 马连湘 刑志有。化学工业出版社10.化工原理课程设计.柴诚敬 刘国维 李阿娜编。天津科学技术出版社11.化工工艺设计手册.化学工业出版社12.化工设备的选择与工艺设计.刘道德编著。中南工业大学出版社13.传质过程及设备.14.化工原理课程设计指导.任晓光主编。化学工业出版社35
- 温馨提示:
1: 本站所有资源如无特殊说明,都需要本地电脑安装OFFICE2007和PDF阅读器。图纸软件为CAD,CAXA,PROE,UG,SolidWorks等.压缩文件请下载最新的WinRAR软件解压。
2: 本站的文档不包含任何第三方提供的附件图纸等,如果需要附件,请联系上传者。文件的所有权益归上传用户所有。
3.本站RAR压缩包中若带图纸,网页内容里面会有图纸预览,若没有图纸预览就没有图纸。
4. 未经权益所有人同意不得将文件中的内容挪作商业或盈利用途。
5. 装配图网仅提供信息存储空间,仅对用户上传内容的表现方式做保护处理,对用户上传分享的文档内容本身不做任何修改或编辑,并不能对任何下载内容负责。
6. 下载文件中如有侵权或不适当内容,请与我们联系,我们立即纠正。
7. 本站不保证下载资源的准确性、安全性和完整性, 同时也不承担用户因使用这些下载资源对自己和他人造成任何形式的伤害或损失。
最新文档
- 沪教牛津英语六年级上册Module3单元全套ppt课件
- 沪科版《声音的产生与传播》ppt课件
- 店铺数据分析课件
- 美国研究文献资源指南.课件
- 绿色夏天清新汇报课件
- 美食咖啡下午茶餐饮课件
- 微生物学实验-1-口腔微生物的染色观察与显微镜油镜的使用;细菌的革兰氏染色教学课件
- 沪教版(上海)七年级数学第二学期ppt课件152(2)直角坐标平面内点的运动
- 店铺报告模本教学课件
- 民兵组织建设课件
- 沪教版(上海)七年级数学第二学期ppt课件152(1)直角坐标平面内点的运动
- 沪教版牛津英语小学二年级上学期期末复习句型课件
- 沪教版地理七年级上册42黄河课件
- 沪教版五年级数学下册《正方体、长方体的表面积2》ppt课件
- 微生物学基础知识培训课件