毕业设计发动机罩内板冲压模设计
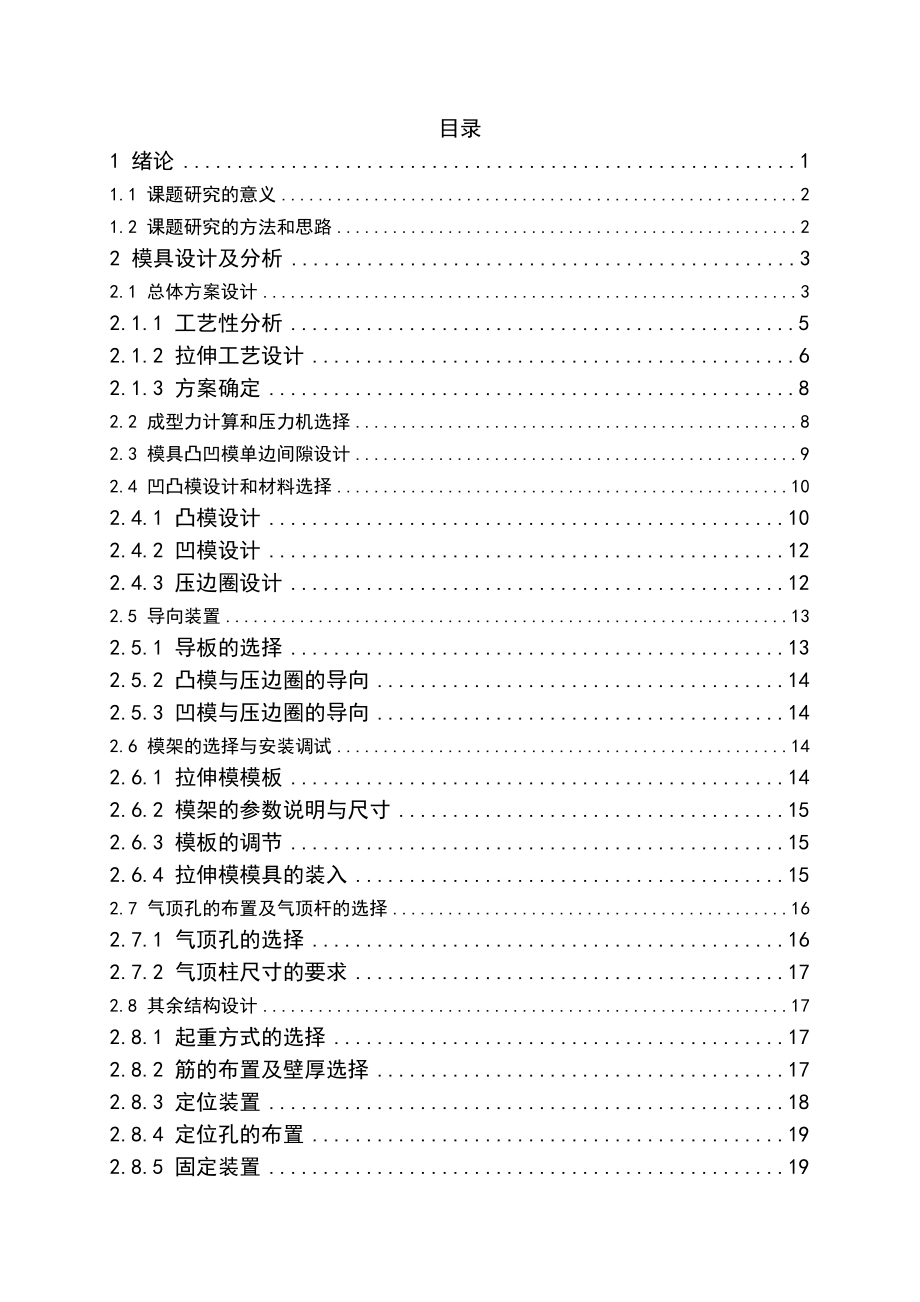


《毕业设计发动机罩内板冲压模设计》由会员分享,可在线阅读,更多相关《毕业设计发动机罩内板冲压模设计(34页珍藏版)》请在装配图网上搜索。
1、目录1 绪论11.1 课题研究的意义21.2 课题研究的方法和思路22 模具设计及分析32.1 总体方案设计32.1.1 工艺性分析52.1.2 拉伸工艺设计62.1.3 方案确定82.2 成型力计算和压力机选择82.3 模具凸凹模单边间隙设计92.4 凹凸模设计和材料选择102.4.1 凸模设计102.4.2 凹模设计122.4.3 压边圈设计122.5 导向装置132.5.1 导板的选择132.5.2 凸模与压边圈的导向142.5.3 凹模与压边圈的导向142.6 模架的选择与安装调试142.6.1 拉伸模模板142.6.2 模架的参数说明与尺寸152.6.3 模板的调节152.6.4 拉
2、伸模模具的装入152.7 气顶孔的布置及气顶杆的选择162.7.1 气顶孔的选择162.7.2 气顶柱尺寸的要求172.8 其余结构设计172.8.1 起重方式的选择172.8.2 筋的布置及壁厚选择172.8.3 定位装置182.8.4 定位孔的布置192.8.5 固定装置192.8.6 限位装置192.8.7 调压垫的布置202.8.8 挡料板的布置213 典型零件的制造工艺设计223.1 工艺路线的拟定223.2.1 凸模加工工艺223.2.2 凹模加工工艺234 模具的装配及调试244.1 模具的装配244.2 模具的调试245 总结与展望265.1 结论265.2 展望26谢 辞27
3、参考文献28附录1 覆盖件尺寸控制及专用检具制造29附录2 CAE拉伸分析30 桂林电子科技大学毕业设计(论文) 第 32 页 共 34 页1 绪论随着经济的快速发展,模具制造业在工业中的地位越来越重要,尤其是冲压模具技术方面更为重要。目前冲压技术广泛应用于金属制品个行业中,如汽车,仪表,家用电器等工业中。轿车车身制造的关键在于轿车车身覆盖件拉伸模具的设计和制造。与一般冲压件相比, 车身覆盖件具有材料薄、形状复杂、结构尺寸大和表面质量高的特点。此外, 车身覆盖件还要求有一定的刚度,能够适当承载以及防止汽车行驶时的振动破坏,并要求具有一定的尺寸精度, 以满足整车装配要求。车身覆盖件大多数是由复杂
4、的空间曲面形状组成, 坯料成形时各部分的变形状态非常复杂, 差别很大, 各处的应力也很不均匀。坯料在整个冲压过程中的变形路径是一个典型的拉伸、胀形变形过程。拉伸是车身覆盖件成形的关键工序, 绝大部分的车身覆盖件形状在这一工序中成形, 拉伸工艺的合理性是决定车身覆盖件产品质量成败的关键。发动机罩内板是典型的车身B类覆盖件, 本文针对发动机罩内板零件, 利用UG软件对内板拉伸模具型面进行曲面设计,研究车身覆盖件拉伸模具型面造型设计的一些原则和方法利用板料成形分析有限元软件Autoform对所设计的CAD 模型进行拉伸成形过程的仿真分析, 预测可能出现的质量问题, 分析其产生原因, 由仿真分析结果对
5、拉伸模具型面进行优化设计。本设计包括对冲压件工艺性分析,模具工艺方案的确定,合理的设计步骤,受力计算及其校核,压力机的型号选定等,使模具操作更加安全、快捷、方便,并且更容易达到冲压件的公差等级要求等。实现了冲压模具用材节省、结构合理、精度高、操作方便等优点。由于现代社会科技进步之故,各种产业都面临着莫大的挑战,譬如说汽车行业,更是应该调整步伐以适应时代的潮流。对于像汽车覆盖件、车灯的反射镜等自由曲面造型,其苛刻的设计条件困扰众多的使用电脑绘图软件的设计者,主要的原因包括曲面造型太过复杂、表面光整度要求严格、制件精度要求高等方面.因此很多造型设计师使用手绘图或者手工捏塑来设计原型,但无法回归电脑
6、资料来保存,且后续模具制作过程亦变得更加困难。因此在这种背景下,三维工程的出现变得呼之欲出、顺理成章,为众多的造型设计者开辟了一条捷径,使曲面造型有一个质的飞跃。另外本文作者所从事的工作部门是柳州福臻车体有限公司,针对该工作性质是从事汽车覆盖件造型研发,因此选择了这样一个毕业设计的课题,这对于本文作者来说是个全新的挑战,大学从未接触类似的零件,而在这短短的半个学期的时间里要完成这么复杂的课题,这个的确是一件艰巨的任务,幸好在老师的引导及鼓励下确定的信念,经历了种种挫折终于完成了此次毕业设计的课题。1.1 课题研究的意义目前,国外汽车公司为了降低模具开发、制造成本,缩短生产周期,将除轿车覆盖件之
7、外的部分轿车冲压件的模具都交由专业模具公司设计和制造,这些公司都有很强的开发能力,并在某些零件的模具制造方面拥有独到的优势。但作为整车厂,考虑到新车型开发过程中的保密,对诸如翼子板、行李箱盖、车门、侧围、车顶、发动机罩等敏感零部件的模具,则都由自己的模具制造部门来设计和制造。传统的模具设计尤其是对于像汽车覆盖件之类的曲面造型是一个反复而困难的研制过程,旷日持久而又投资巨大。随着工业化的日益发展,产品更新换代周期越来越短,产品间的竞争越来越激烈,因此必须缩短开发新的产品周期,并降低开发成本,从而达到产品实体模型数据资料的目的。从而为设计与制造实体模具做铺垫。1.2 课题研究的方法和思路本课题中将
8、采用三维扫描仪获取点数据,从而得到理想的点云资料,然后使用UG软件将得到的点生成相应的曲线,通过软件中的曲线功能对曲线进行分析处理,最后将得到的符合设计要求的曲线导入UG软件,通过软件中的面处理功能得到符合设计要求的三维模型。参照已经建好的模型,对模具的各个零件进行分析设计。2 模具设计及分析2.1 总体方案设计拉伸模是保证制成合格覆盖件最主要的装备。其作用是将平板状毛料经过拉伸工序使之成型为立体空间工件。拉伸模有双动和单动两种型式。双动拉伸模的凸模和压料圈在上,凹模在下,它使用双动压力机,凸模安装在内滑块上,压料圈安装在外滑块上,成型时外滑块首先下行,压料圈将毛料紧紧压在凹模面上,然后内滑块
9、下行,凸模将毛料引伸到凹模腔内,毛料在凸模、凹模和压料圈的作用下进行大塑性变形,如图2-1所示。单动拉伸模的凸模和压料圈在下,凹模在上,它使用单动压力机,凸模直接装在下工作台上,压料圈则使用压力机下面的顶出缸,通过顶杆获得所需的压料力,如图2-2所示。单动型式拉伸模只有在顶出压力能够满足压料需要的情况下方可采用。此次设计所选的就是后面一种即单动型式拉伸模。1-压边圈 2-凸模 3-凹模 4-导板 图2-1 单动拉伸模1-压边圈 2-凸模 3-凹模 4-导板 5-凸模垫板图2-2 双动拉伸模表2-3 拉伸膜各部位壁厚尺寸符合ABCDEFG尺寸(mm)45404060404015在设计的过程中,首
10、先要明确拉伸模模具的组成。(1)凸模、凹模 (2)压边圈 (3)导向装置(4)调压装置 (5)气顶装置(6)模具起吊装置拉伸模的导向分为内导向和外导向。外导向是指压料圈和凹模之间的导向,内导向是指压料圈和凸模之间的导向。而常用的导向零件有导板、导跟、和导柱三种。由于导向装置是置于压边圈内侧,所以此次设计将采用内导向的导向板导向。导向板类型如图2-4所示。图2-4 导向类型2.1.1 工艺性分析工艺设计是在模具设计制造之前的技术准备工作,其主要内容有以下几项:(1)根据生产纲领确定工艺方案;(2)根据覆盖件结构形状,分析成型可能性和确定工序数及模具品种;(3)根据装配要求确定覆盖件的验收标准;(
11、4)根据工厂条件决定模具使用的压床;(5)根据制造要求确定协调方法;(6)提出模具设计技术条件,其中包括结构要求、材料要求等。工艺设计内容是贯彻执行生产纲领的具体要求和体现,是生产纲领和模具设计制造之间的桥梁和纽带。工艺设计要求方案正确、内容可靠、符合实际和实施容易,不允许有任何大的漏洞。其责任分量很重,往往是成败的关键。该设计零件产量要求为:月产量为3000件(轿车),其属于中批量生产。其生产特点是比较稳定地长期生产,生产中形状改变时有发生。模具选择除要求拉伸模采用冲模外,其他工序如果影响质量和劳动量大也要相应选用冲模,模具寿命要求在5万件到30万件。如2-4图所示工件为发动机罩内板拉伸初成
12、型件,材料为DC04钢,单边数量一个,材料厚度为t=0.7mm。拉伸模常用灰口铸铁制造,表面火焰淬火处理。本模具结构采用导板导向,手工取件,固定或气动定位毛料,壁厚中等,设计中得适当考虑其合理性。图2-5 制件图2.1.2 拉伸工艺设计 拉伸工艺设计是汽车覆盖件模具设计过程中非常关键的一步,它决定拉伸工序的成败和质量。拉伸工艺设计包括以下几个步骤: 确定拉伸方向、翻边展开、设计工艺补充部分、设计压料面、布置。(1) 拉伸方向确定 确定拉伸方向是首先要遇到的问题,它不但决定能否拉伸出满意的拉伸件, 而且影响到工艺补充部分的多少和压料面的形状。有些形状复杂的拉伸件往往会由于拉伸方向确定不当,而拉伸
13、不出满意的效果,只好改变拉伸方向, 这样就需要修改拉伸模。有些拉伸模是很难或者无法修改的,需要重新设计和制造拉伸模,同时还必须相应地修改前后工序的模具,所以拉伸方向的确定必须慎重。拉伸方向的确定应遵循以下几条原则:保证凸模能进入凹模;凸模开始拉伸时与拉伸毛坯的接触面积要大;压料面应尽量保证毛坯平放,拉伸深度应均匀。图2-6(a)中凸模两侧的拉入角心可能做到基本一致,使两侧进料的阻力保持平衡。凸模表面同时接触毛料和点要多而分散,并且可能分布均匀,防止成型过程中毛料窜动,如图2-6(b)所示。当凸模和毛料为点接触时,应适当增加接触面积,如图2-6(c)所示,以防止应力集中造成局部破裂。图2-6 冲
14、压方向的选择(2)设计压料面和布置拉伸筋 压料面是工艺补充的一部分, 指凹模圆角半径以外的那一部分。压料有两种形式, 一种是压料面就是覆盖件本身的凸缘面, 这种压料面的形状是既定的。另一种是压料面由工艺补充部分补充成, 对这种压料面的要求是,压边圈将拉伸毛坯压紧在凹模上,压料面不应产生皱纹和裂痕, 以保证凸模对拉伸毛坯的拉伸,否则在拉伸过程中会形成波纹和皱纹。确定压料面形状应满足如下要求:有利于降低拉伸深度。1-凸模 2-凹模 3-压料面图2-7 拉伸模的压料面压料面应保证凸模对毛料有一定程度的拉伸效应。图2-8 压料面展开长度比凸模表面展开长度短覆盖件成型时,在压料面上敷设拉伸筋,改变阻力,
15、调整进料速度使之均匀化和防止起褶皱具有明显的效果。其主要作用是:增大进料阻力,使整个拉伸件进料速度达到平衡状态。加大拉伸成型的内应力数值,提高覆盖件的刚性。加大径向拉伸力,减少切向压应力。(3) 工艺补充部分设计 为了实现拉伸, 将覆盖件上的翻边展开, 窗口补满, 再加上工艺补充部分构成一个拉伸件。有些覆盖件上没有翻边, 就直接加上工艺补充部分。窗口补满部分也是工艺补充部分, 工艺补充部分是拉伸件不可缺少的部分, 拉伸以后要将工艺补充部分修掉, 所以工艺补充部分也是工艺上必要的材料消耗。因此,在能够拉伸出满意的拉伸件的条件下, 尽可能减少工艺补充部分, 工艺补充部分的多少也是衡量覆盖件设计和冲
16、压工艺先进与否的一个标志。工艺补充形式如图2-9所示。图2-9 工艺补充部分的几种情况2.1.3 方案确定在给定的条件下,判断出为中批生产,所以选择单动拉伸模成型,单动拉伸模成型:单动拉伸模的凸模和压边圈在下,凹模在上,它使用单动压力机,凸模直接装在下工作台上,压边圈则使用压力机下面的顶出缸,通过顶杆获得所需的压边力。该设计的拉伸件需要的坯料尺寸为梯形料(最大宽度1740mm,最小宽度1640mm,高1455mm),材料为汽车覆盖件常用材料冷轧钢DC04,厚度0.7mm。零件尺寸公差无特殊要求,按ITl4级选取。2.2 成型力计算和压力机选择压力机分为单动压力机和双动压力机。形状简单、深度浅的
17、覆盖件一般采用单动压力机来成型;形状复杂、深度深的覆盖件必须采用双动压力机成型,这是因为单动压力机的压料力是靠机床下面的油缸获得的,油缸的压力和行程都比双动压力机小得多,它不能提供较大压料力和大行程的复杂深拉伸件所需的成型力。其次,单动压力机所用拉伸模的压料圈比较薄,刚性相对弱,也不能适应复杂深拉伸件的成型。此模形状简单,深度浅的覆盖件应采用单动压力机。力的计算:公式:压力机公称压力:取式中,A为压边圈下毛坯的投影面积(由UG建模测算出来,为); P为单位压边力(Mpa),可查表2-10,取3Mpa。表2-10 在单动压床上拉伸时单位压边力的数值材料单位压边力P/Mpa铝0.8-1.2纯铜、硬
18、铝1.2-1.8黄铜1.5-2压轧钢2-2.220钢、08钢、镀锡钢板2.2-3软化状态的耐热钢2.8-3.5高合金钢、高锰钢、不锈钢3-4.5取式中,L为凸模周边长度(由UG建模测算出来,为);t 为坯料厚度(mm);为材料屈服强度,由企业标准中查出,DC04的冷轧钢的屈服强度为210Mpa;为拉伸系数,见表2-11,取0.8。表2-11 制件复杂程度难加工件普通加工件易加工件值0.90.80.7则所以为了保证压力选用压力机设备型号为A2000T,此机床的气顶杆最高行程为130mm,压力2000T。2.3 模具凸凹模单边间隙设计拉伸模单边间隙拉伸模单边间隙Z查表2-12可得,zt=0.7mm
19、 。表2-12聊厚t材料0.5t11.5t3DC04t(1+4%)t(1+3%)t(1+2%)t凸凹模具尺寸公差标注凸凹模具尺寸标注:由于汽车发动机罩内板自身无公差要求,所以按14级公差来设计,凸凹模的公差则需要选用高12级的公差等级。拉伸模的凹模圆角半径拉伸模的凹模圆角半径对拉深工作影响很大。若过小,则拉深力很大,从而影响模具的寿命;若过大,则不能充分发挥压边圈的防皱作用。根据毛坯的尺寸以及拉伸件的尺寸和材料厚度t决定,但由于汽车覆盖件的与普通拉伸模具设计的凸凹模不同,制件形状基本由凸模形状决定,凹模属于组合而成的模具,所以只能设计凸模的圆角半径,可取圆角范围为R2R6。2.4 凹凸模设计和
20、材料选择覆盖件冲压作业生产中适宜流水作业方式进行的所以对模具结构要适用于大量生产、高效率、长寿命等特点的要求。汽车发动机罩等覆盖件拉伸模的尺寸大而且形状复杂,凸模、和凹模和压料圈通常都采用铸件。其所用的材料应满足耐磨、不易拉毛(黏着)和易加工的要求,具有良好的淬透性,并能进行整体淬火。由于汽车产品类型更新换代时间比较快,多以生产的产品外形更换周期约为一年,所以汽车发动机罩等覆盖件的生产批量为大批量生产,适合用灰口铸铁HT300和铬钼合金铸铁GM241。凸凹模具尺寸标注:由于该零件自身无公差要求,所以按14级公差来设计。2.4.1 凸模设计简单的模具设计可以根据设计指导书去对模具进行尺寸设计和选
21、择,而该设计是比较复杂的零件对应的模具设计。而对于该零件,行业普遍使用三维扫描仪做逆向设计。先使用扫描仪得到点云数据,再用UG进行曲面造型。其设计成形思路如下:1、导入点云文件到Imageware软件中,处理跳动的点及多余的点。图2-13 零件点云2、用CATIA分析点云数据,构思实体模型的形状,根据所需形状由点云生成网格。图2-14 零件网格3、导入IGS文件到UG软件中,在UG软件中由曲线生成曲面。图2-15 零件图由于汽车发动机罩内板的体积较大,所以凸模具的体积也相对较大,且需要有一定的抗冲击变形和抗破坏能力(即满足强度刚度和稳定性要求)同时又要减轻自身的重量,减轻压力机的工作负载,在一
22、般工程中适合采用精密铸造来制作凸模,凸模采用如2-16图所示的结构:图2-16 凸模凸模进行时效处理后,再对工作表面进行铣削,然后进行火焰处理,提高表面硬度,同时又保证内部组织不发生改变,保持原有的韧性。2.4.2 凹模设计凹模结构也采用了铸造成型的,这样可以节省更多的成本去进行加工,如图2-17所示凹模的结构。图2-17 凹模2.4.3 压边圈设计结构也采用了铸造成型的,这样可以节省更多的成本去进行加工,如2-18图所示压边圈的结构。图2-18 压边圈2.5 导向装置2.5.1 导板的选择拉伸模的导向分为内导向和外导向。外导向是指压料圈和凹模之间的导向,即导板在压料圈之外;内导向是指压料圈和
23、凸模之间的导向。即导板在压料圈之内。而常用的导向零件有导向板、导向块、和背靠块三种。由于导向装置是置于压边圈内侧,所以此次设计将采用内导向的导向板导向,也称导板导向。导向板广泛用于中小型拉伸模,其长、宽尺寸依据模具大小和受力的方向等进行调整。装配导板时,导板是一个标准件,此标准件分为三层,中间层是导板,两边分别是滑配面和挡墙面。图2-19 导向板由于顶杆行程为130mm,所以选择了高度为150mm的导板。导板是安装在凸模与压边圈之间,安装时选用的是以下宽度的尺寸:(1)在凸模的两侧(窄面),安装12515010的导板;(2)在凸模的前后(宽面),安装12515010的导板。2.5.2 凸模与压
24、边圈的导向凸模和压边圈的导向是用48对导板导向,导板数量根据模具大小及具体结构选定。导板应放置在凸模外轮廓的直线或形状平滑的部位。导向面应在压料圈内轮廓与凸模外轮廓之间空隙的1/2处。拉伸开始时导向面的接触应根据公式t1+t10.2t,如图2-20所示,拉伸结束时,凸模导板不脱离压边圈导板。图2-20导板无论安装在凸模或压边圈处,其安装面应充分考虑到易于铸造保证尺寸,便于机械加工。在选定凸模导板结构的时候,铸件中的空隙大,机械加工面积最小,是合理的结构形式。2.5.3 凹模与压边圈的导向常用的压边圈和凹模之间的导向,是在压边圈和凹模上铸出凸台和凹槽,并在其上安装导板以起导向作用,导向间隙为0.
25、03mm。凸台和凹槽的放置位置根据需要决定。图2-21所示的凸台放在凹模上,其优点是工人操作时看得清楚且较安全,缺点是调整冲模时防碍打磨压料面和压料筋槽。图2-21所示的凸台放在压料圈上,此时打磨压边面和压料筋槽比较容易,放料和取件方便,多用于压边面形状复杂的情况。图2-21凸台和凹槽上安装导板有利于调整导向间隙,导向面可考虑一面装导板,另一面精加工,磨损时可在导板背后加垫调整,导板安装要考虑制孔的方便性。凹槽于导向面之间的距离A压边面长度加上2040mm;距离B决定于压边面的宽度,一般取压边面宽度的1/31/2。凹槽应对称分布。2.6 模架的选择与安装调试2.6.1 拉伸模模板 模板是结构标
26、准化的具体体现,那么模板中的每一个标准化结构都可以看作是一个模块。模板模块是指结构相对规则的上下模架部分,主要起定位和支撑等作用。考虑到模具要固定在机床上,专用型面模块的外形直接受型面的控制,所以将模架分成6个模块:上模板、下模板、上模体、下模体、机床和型面。模板的结构图如下图2-22所示。图2-22 模板结构图2.6.2 模架的参数说明与尺寸由于本次设计的是内导向的单动拉伸模具设计,所以在标准模架中调用了内导向的模架。其设计基本要求是:设计总体要满足零件拉伸工艺卡片的要求,达到闭合高度1000mm,再在此基础上对模架进行调整以满足零件成型要求,模具与模架的绝对坐标必须重合。其调整图如2-23
27、。拉伸模模架分为上、中、下三层模架,在模体装配之前还要对模板进行调节。图2-23 拉伸模模架2.6.3 模板的调节模板的尺寸有时候与模体尺寸在加工、检测上存在一定的误差,因此需要调节有如下要求:(1)导腿宽度应大于上模板宽度的1/3; (2)调节模板高度时,只有导腿有变化,其他部件没有变化;(3)无论调节哪个部件的变化,下模板与中模板之间的距离都是一定的;(4)调节完毕后,把上、中、下三层模架全部抽取,以便后续的编辑。2.6.4 拉伸模模具的装入上模模体与凹模本体合在一起作为凹模,下模模体与凸模本体连接在一起作为凸模。要求如下:(1)装入时,必须让模体几何中心保持在原点,因此,在调整模具位置时
28、, 只能移动模板,不能移动模体的中心线;(2)装入时,凸模体压边面应超出中模架10mm以上;(3)装入时,凹模体必须与上模架紧紧相贴,不得有空隙;(4)模体在模板当中尽量两边对称,使拉伸模体在模板的中央。2.7 气顶孔的布置及气顶杆的选择2.7.1 气顶孔的选择机床作为一个标准件分为上机床和下机床,凸模固定在下机床上,凹模固定在上机床上。机床上排列无数个小圆孔,之间的距离为150mm,圆孔里边有一定长度的气顶杆,每一个气顶杆顶出的力为7.7T。在冲压工艺卡给定压边圈的压边力为200T的基础上,选定标准件中10T的气顶杆,所以所需其顶杆个数N=200T/10T=20,为了保证强度和其顶杆的对称性
29、,选择了26个气顶杆。装入时,机床的几何中心先设置在原点,把下机床装在下模架的下方,上机床放在上模架的上方。图2-24 气顶孔分布最后,用UG中的抽取功能抽取所选择的孔,抽取的功能是能够对它进行后序的编辑与操作。用抽取的孔在下模架上开孔,前提是下模架是抽取的,孔直径为90mm,为的是让气顶柱穿过下模架,顶到压边圈上。为了更有力的顶住压边圈,在压边圈与气顶杆之间做个气顶柱,使气顶柱与压边圈合并为一个体。之后用20mm厚的垫片(标准件)装配到气顶住上。2.7.2 气顶柱尺寸的要求气顶柱直径一般取90mm。模架都已经安装在机床上,压边圈在机床的气顶杆的作用下先达到了最高行程300mm,且调试完毕保证
30、了闭合高度。为了达到冲压工艺卡中的压边圈最大行程为130mm。有以下公式:气顶柱底部(包含垫片)与下模架底部之间的距离 =气顶杆的最大行程压边圈最大行程=300mm130mm =170mm2.8 其余结构设计2.8.1 起重方式的选择模具采用吊耳起重棒形式,多工位和手动线采用整体铸出式起重棒,整体式起重棒布置在模具的左右两侧。此模架起重方式选择吊耳而不能选择起重棒。因为设计要求选用A2000T机床,用起重棒强度不够,容易引起断裂,使用时间难以达到厂家要求。故选用吊耳。起吊装置在模具加工、组装和安装、卸模、搬运等情况下使用,它是模具使用安全的重要部分。选用的吊耳是插销吊钩和铸嵌式吊钩。2.8.2
31、 筋的布置及壁厚选择拉伸模的凸模、凹模、压料圈都采用铸件毛坯。铸件既要尽量轻,又要有足够的强度和刚度。因此可将铸件的非重要部分挖空,并在影响强度和刚度的部位增加立筋。筋的厚度一般取40mm,在凸摸和下模架的中空底部、凹模和上模架的中空顶部都要立筋,筋的间距一般为300mm左右。筋的壁厚尽可能均匀,避免急聚变化的斜面。壁厚过薄,浇铸时熔融金属的流动变坏。壁厚和薄壁接合部位要设置过渡区。拉伸模的凸模、凹模、压料圈和凸模固定座及模架等都采用铸件毛坯。铸件既要尽量轻,又要有足够的强度和刚度。因此可将铸件的非重要部分挖空,并在影响强度和刚度的部位增加立筋。模具铸件壁厚与模具的尺寸、生产批量和受力情况有关
32、。合理选用铸件壁厚不仅可以节约材料,也有利于提高铸件质量。铸件的壁厚和结构参数没有同一的标准,各国各厂推荐的数据不尽相同,这里推荐在小批量和大批量生产时铸件各部分壁厚的参考数据分别见表2-25。表2-25 大批量生产时拉伸模铸件壁厚数据单位mm模具尺寸ABCDEFKMPQ150025005050405060206030010100020004040305050205030010800150030303040401030300104008003030303030103020010单位mm模具大小ABCDEFG中小型40503545354530403545303530大型7512060805065
33、4565506540503040压料面处的宽度安拉伸前毛配的压料宽度加大4080mm,约在130240mm范围内。本套模具壁厚即为40mm。2.8.3 定位装置凸模与下模架之间的定位凸模与下模架之间的定位,用三个键固定,即左右两侧和前后其中一侧,其尺寸为:长为80mm、宽为32mm、高为25mm,且有一面的倒角为3mm。在键的中央有一个沉头孔,其尺寸为:沉头深度为12mm,沉头直径为18mm,孔直径为11mm。安装键时有以下要求:(1)沉头孔朝上,倒角与沉头孔同面。(2)键的顶部与凸模上的槽留有5mm的间隙。(3)为了防止定位键作用的力对薄壁有影响,往往在键旁薄的地方加厚在布 置键槽时有如下要
34、求:(4) 在下模架上挖槽3mm,为了使凸模与下模架连接的更稳固,在凸模上截 取 10mm高,与下模架合并一起,即下模架上挖槽13mm;(5) 在凸模上挖槽17mm;(6)槽的一端最好设成半圆形,以便加工方便;(7)槽的长度要长于键长度15mm左右,以便给出它的活动量;2.11.2 上下模架与机床的定位上下模架与机床的定位,要用四个定位键,此键是交叉十字的通键,以便能够承受更大的力,即要在上下模架的筋上设置槽,其尺寸为:高20mm,宽32mm。2.8.4 定位孔的布置为了更准确的加工模具,需在各个模架上安装定位孔,其结构为两边是半圆结构,定位孔的圆心与某一个半圆的圆心一致,其尺寸为:两半圆的圆
35、心距为230mm,宽为250mm,定位孔直径为90mm,高为10mm定位孔的布置要求如下:(1)安装定位孔时,小孔的圆心必须与模体的中心线对齐; (2)每一个模架上安装3个定位孔即可,其中左右两侧两个,在Y轴的负方向(送料方向)上一个; (3)安装定位孔时,要与各模架的边缘相切,其中在上模架安装时,应与导腿边缘相切。2.8.5 固定装置 法兰台的制作凸模与下模架之间的固定,是由法兰台固定的,这里只制作大概的结构,后序的加工由车间的工作人员来进行研究,其结构尺寸为:台高为30mm,台上有个凸台,是为了安装螺栓用的,凸台高为10mm,凸台两边倒圆角半径为20mm。其安装要求为:(1)安装凸台的个数
36、最少为4个,而且要放置均匀;(2)必须是在凸模上安装,而且要与凸模合并为一体;(3)下模架上应要有10mm的法兰台,并与凸模上的法兰台对齐;(4)要消除法兰台对其他地方的干涉,留有15的空隙。压板槽的制作上下模架与机床的固定,是由压板槽中的螺栓固定的,压板槽分别布置在上下模架的顶部和底部,并与机床上的压板槽相对应,其安装数量要求为:1)当模具长L1500时,则安装数量为68个;2)当模具长L1500时,则安装数量为46个;3)其加工尺寸如下图2-26:其中高为10mm,用的是8个压板槽。图2-26 压板槽的剖面图2.8.6 限位装置合模限位块合模现为块又称条子整块,所有拉伸模必须装四块调整块,
37、装在压边圈四个角上,通过试验使压边圈周围保持均匀合模间隙,从而保证均匀压料力。调整块采用工具钢制造并淬火,保证承载能力7500N/cm2,设计时在图纸上注明:试压后把调整块磨薄0.75mm,用一片0.25mm厚垫片垫在下面。调整块要尽可能远离侧倒块。存放限位块存放限位块是拉伸模在不工作时,为了使弹性元件不是去弹力而必须设置的零件。其厚度要保证弹簧不受压缩而处于自由状态。压边圈限位螺钉单动拉伸模的压边圈套在凸模的上,在拉伸开始时,压边圈通过顶杆顶起使压边面超过凸模最高点,考虑顶杆顶起时有跳动的可能,因此压边圈应设置限位螺钉。其限位长度(螺钉的有效工作长度)应超出压边圈最大行程20mm。以上几种螺
38、钉都是标准件。选用的是压边圈限位螺钉。其安装要求如下:(1)限位螺钉应安装在下模架的四个角上,并通过压边圈; (2)限位螺钉的顶端不能超过中模板的上层板,并在顶端周围留有20mm左右的空隙,便于安装。2.8.7 调压垫的布置调压垫也叫墩死垫,在装配当中是一个标准件。在模具运行当中,来自机床的力给了凹模,当凹模与压边圈接触时,它们之间会存在很大的力,当压边圈与凸模接触时,这个力又给了凸模,由于模体的形状是不均匀的,难免会造成力的分布不均匀,致使会对压料件产生很大的影响,为了在模具运行过程当中的接触力达到平衡,在压边圈与凹模之间、凸模与压边圈之间的四周必须要安装调压垫。调压垫厚20mm,在它们之间
39、各有凸起的小圆台,因此调压垫就夹在小圆台之间。其结构图2-27如下图所示:图2-27 调压垫其安装要求为:(1)安装时,调压垫之间的距离不能大于300mm,且分布要均匀; (2)调压垫底部必须有筋,占60%即可,为了是底部能够承受更大的冲压力,防止模具损坏; (3)安装时,调压垫尽量靠近分模线,为了是最后改模具时更方便些。2.8.8 挡料板的布置在冲压板料的过程当中,难免会使板料发生移动,这样必须在压边圈的四周布置挡料板,挡料板现场配做。其安装要求为:(1)一般每侧安装2个挡料板,且尽量靠近四角,并安装要对称; (2)挡料板的挡料面与坯料线要有3mm水平距离的间隙;其它三侧离周围有10mm间隙
40、,挡料板底部应布置个安放台; (3)挡料面有曲面和直面,其中只能用直面来挡料,且在曲面与直面的相交处与压边面的垂直距离不能低于20mm。3 典型零件的制造工艺设计机械制造工艺包括生产过程和工艺过程。工艺过程指的是在生产过程中,直接改变生产对象的形状、尺寸、相对位置和性质(力学性能、物理性能、化学性能),使其成为成品(或者半成品)的过程。它是生产过程的主要组成部分。机械制造工艺过程又可分为:毛坯制造工艺过程、机械加工工艺过程、机械装配工艺过程等。根据本课题设计要求及特点,仅作机械加工工艺过程。结合设计出的冲压模具,可知,落料、拉伸用的凸凹模结构复杂,要求力学性能好,而自身的结构又决定了其壁厚很薄
41、,所以其工艺制定也成为该整个模具中各零件的最难点。机械加工工序是工艺规程的主要内容,其加工顺序的安排原则是:先基准后其他,先粗后精,先主后次,先面后孔,先外后里。3.1 工艺路线的拟定该零件需要加工的表面有:固定用上表面、法兰盘下表面、落料端面、最大圆柱面、工作内外圆柱面、内配合面、拉伸圆角面、螺纹孔及光孔。由其工作性质可知落料端面、工作内外圆柱面、拉伸圆角面、固定用上表面要求加工精度高,也是加工的主要表面。可安排四个加工阶段,即:去皮加工阶段、粗加工阶段、半精加工阶段、精加工阶段和光整加工阶段。在编制冲压工艺规程时,通常要根据冲压件的特点、生产批量、现有设备和生产能力等,拟订出几种可能的工艺
42、方案。在对各种工艺方案进行周密的综合分析和比较之后,在确定一种较先进、最经济合理的工艺方案。3.2.1 凸模加工工艺工艺路线如表3-1所示。表3-1 凸模加工工艺序号工序名称工序内容1铸造2热处理球化退火, 获得碳化物细小均匀、 呈球状颗粒分布的组织,以提高切削加工性,减轻淬火变形和开裂。3刻线在模具上对大体尺寸进行标注4刨刨上、下表面5磨削磨平面 厚度留余量0.2mm6铣削用大型龙门数控铣床对曲面加工,保证凸模的曲面表面粗糙度到达要求。7淬火火焰处理,保证凸模的曲面表面硬度到达要求。8铣削铣台阶9抛光使其表面粗糙度达到Ra=0.20.410去应力退火将抛光后的摆辗凹模和凸模置于170至200
43、摄氏度的油炉内保温8小时, 以消除残留应力。3.2.2 凹模加工工艺二次拉伸由凸模将材料拉入凹模,直接成形零件,凹模与凹模固定板采用过盈配合,加工工艺路线如表3-2。表3-2 凹模加工工艺序号工序名称工序内容1铸造2热处理球化退火, 获得碳化物细小均匀、 呈球状颗粒分布的组织,以提高切削加工性,减轻淬火变形和开裂。3刻线在模具上对大体尺寸进行标注4刨刨上、下表面5磨削磨平面厚度留余量0.2mm6铣削用大型龙门数控铣床对曲面加工,保证凸模的曲面表面粗糙度到达要求。7淬火火焰处理,保证凸模的曲面表面硬度到达要求。8铣削铣台阶9抛光使其表面粗糙度达到Ra=0.20.410去应力退火将抛光后的摆辗凹模
44、和凸模置于170至200摄氏度的油炉内保温8小时, 以消除残留应力。11焊接与凸模模体焊接4 模具的装配及调试模具的装配就是根据模具的结构特点和技术条件。以一定的装配顺序和方法,将符合图样技术要求的零件,经协调加工组装成满足使用要求的模具。在装配过程中,既要保证配合零件的配合精度,又要保证零件之间的位置精度,对于具有相对运动的零件,还必须保证它们之间的运动精度。因此,模具装配是最后实现冲模设计和冲压工艺意图的过程,是模具制造过程中的关键工序。模具装配的质量直接影响制件的冲压质量、模具的使用与维修和模具寿命。4.1 模具的装配为了便于对模,组装前应合理确定上、下模的装配顺序,以防出现不便调整的情
45、况。上、下模的装配顺序与模具的结构有关,装配顺序的选择关键。装配顺序的选择关键是要保证凸、凹模的相对位置精度,使其间隙均匀。通常是先装基准件,再装关联件,然后调整凸模、凹模间隙,最后装其他辅件。装配基准件是起到连接其他零部件的作用,并决定了这些零件之间的正确的相互位置。冲压模中常用凸、凹模及其组件或导向板、固定板作为基准件。本套模具的装配调试步骤:(1)装配前准备工作:把凸模压入到固定板中,并铆接;铆接之后把凸模末端的大平面磨平,保证按触面的平面度、表面粗糙度的要求;(2)装配凸模、固定板为一个组件;(3)装配凹模与下模座;(4)装配上模座;(5)装配卸料装置;(6)装配其他零件。4.2 模具
46、的调试在预想的工艺条件下进行模具设计,但是人们的认识往往是不完善的,因此必须在模具加工完成以后,进行试模试验,看成型的制件质量如何。发现以后,进行排除错误性的修模。模具按图样技术要求加工与装配后,必须在符合国际生产条件的环境中进行试冲压生产,通过试冲可以发现模具设计与制造的缺陷,找出产生原因,对模具进行适当的调整和修理后再进行试冲,直到模具能正常工作,才能特模具正式交付生产使用。图4-1 装配简图5 总结与展望5.1 结论车身覆盖件是一个品牌的标志和形象,代表着汽车的发展水平和一个企业的实力,成功的车型建立在良好的车身覆盖件基础上,车身覆盖件的成功决定了一个新车型的成功和销售前景。本文以本人实
47、习时参与设计的某款车型发动机罩内板为例,采用理论和实际相结合的方法详细介绍了设计冲压件时所应注意的条件、冲压件的设计方法和对冲压件进行成型性仿真的方法,最后,通过对该车型发动机罩内板的仿真结果分析,得出该冲压件成型性良好的结论。该零件有设计周期短、设计成本低的优点。主要工作有以下几点:(1)介绍了发动机罩内板的结构和车身与该零件件之间的关系;(2)对该零件的材料选择做了陈述,为后面将要进行的冲压件设计和成型性分析建立了材料基础;(3)分析了该零件设计时的设计条件,在三维软件UG平台下,提出了该零件的设计方法和思路,并对该零件设计完成后需要进行的校核进行了分析;(4)对前面设计完成的发动机罩内板
48、进行了成型性仿真分析,利用分析软件Autoform进行分析,并研究了分析结果,得出该发动机罩内板成型性良好的结论。5.2 展望因为能力和时间有限,在本文所作工作的基础上,本文认为可以进行的进一步的研究工作为:(1)复杂冲压件的设计。本文涉及的冲压件只是发动机罩内板的设计,对于较复杂的冲压件如车身外表面冲压件的设计,除了考虑本文提及的冲压件要求之外,更重要的是要达到A级曲面的要求,设计较为复杂,因此,研究车身冲压件需要研究轿车车身外表面的设计方法;(2)由于各种条件限制,本文没有考虑冲压件成型后的回弹,及出现较大回弹时应该采取的方法,进行回弹分析和控制是下一步要进行的工作;(3)影响冲压的工艺参
49、数有很多,如凹凸模圆角、模具间隙等,本文只在摩擦系数、模具间隙、压边力、拉延筋等工艺参数基础上对冲压件进行仿真,一些重要的工艺参数如凹凸模圆角并未考虑,后续工作将是研究其他工艺参数对冲压性能的影响。谢 辞经过一个学期的努力,终于完成了毕业设计的任务,在本次毕业设计期间,在此设计中尺寸的计算和结构的设计是工作量最大的,经过工艺分析后,必须采用两套模具才能完成对工件的制造,大大的增加了工作量。几个月来,在唐老师的耐心指导和热心的帮助下,我一步一步完成了设计任务的每一个步骤,并最终做出了令导师满意的成果。在此期间,导师给我的谆谆教诲和得力指导,我将永远铭记在心。唐老师不仅在理论设计的方面给了我帮助,
50、在实际问题方面也给了我莫大的帮助,为了让我尽快的理解课题唐老师给我带来了很多关于课题方面的资料,在设计第一副模具时由于没经验,老师指出了几个不足之处,并认真的教我修改。由于得到老师的帮助在设计的时候也减少了很多工作量,节省了不少时间。在整个毕业设计期间都耐心的为我解决困难,每个星期都对我进行两次辅导还经常主动联系我,询问毕业设计的情况。正是由于老师的孜孜不倦的指导和教育现在毕业设计才能顺利的完成,再次表示由衷的感谢。在毕业之际我还要感谢我们的院领导,是你们的给我创造了一个好的学习环境;感谢所有教过我的老师,从你们身上我学到了很多知识和做人的原则;同时还要感谢我们班的每一位同学,因为有了你们才使
51、我的大学生活充满快乐。参考文献1 刘鸿文材料力学(第三版)M北京:高等教育出版社,20012 赵经文,王铎文理论力学M北京:高等教育出版社,20013 孙玉芹,孟兆新机械精度设计基础M北京:科学出版社,20044 乐玉汉矫车车身设计M北京:高等教育出版社20005 张策机械原理与机械设计M北京:机械工业出版社,20046 谢龙汉,单岩CATIA V5零件设计M北京:清华大学出版社,20047 谢龙汉,单岩CATIA B5自由曲面造型M北京:清华大学出版社,20048 尤其风CATIA高级应用M北京:清华大学出版社,20069 徐政坤冲压模具及设备M北京:机械工业出版社,200710 李志刚模具
52、CAD/CAMM北京:机械工业出版社,200811 单岩,谢龙汉CATIAV5机械设计应用实例M北京:清华大学出版社,200412 李振平模具制造丁艺学M北京:机械T业出版社,200813 王孝培实用冲压技术手册M北京:机械T业出版社,200114 王树勋,苏树珊模具实用技术综合手册M广州:华南理T大学出版社,200315 于先逵现代制造技术手册M北京:国际工业出版社,200116 杜东福冷冲压上艺及模具设计M长沙:湖南科学技术出版社,199917 贺传军,范士均汽车模具行业CAE分析软件的应用拉延篇J现代零部件,2006,518 丁岩新一代的CATIA V5JCAD/CAM制造业信息,200
53、319 牟林,胡建华冲压模具与模具设计M北京:中国林业出版社,200620 模具实用技术丛书编委会冲模设计应用实例M北京:机械工业出版社,200321 张浩立,罗继相基于局部逆向工程的汽车覆盖件模具虚拟技术J锻压技术,2005,(2)22 王亚元模具逆向工程中的对象数字化技术J模具工业,2006,21(1)23 林忠钦车身冲压件冲压成型仿真口咽北京:机械工业出版社,200424 沈法计算机辅助产品造型设计表现技法M北京:人民邮电出版社,200225 张秉森,王珏计算机辅助设计教程M北京:清华人学出版社,200526 pKinuko Fujimoto et al. Fabrication of
54、dies in micro-scale for micro-sheet metal forming J. Journal of Materials Processing Technology, 2006, 177(1-3): 639-643.27 K. Manabe, H. Koyama, H. Nouka, M. Yang, K. Ito, Finite element analysis of micro cup drawing process using tool and blank models with surface roughness, in: Proceedings of the
55、 Eighth ICTP, Verona, Italy, 2005, CDROM.附录1 覆盖件尺寸控制及专用检具制造覆盖件的尺寸控制就是针对不同覆盖件产品质量特性、按不同的测量方法、对不同轿车覆盖件进行测量的过程。发动机罩内板尺寸控制方法有以下几种:(1)轿车覆盖件原材料质量特性验证。轿车覆盖件产品在成型过程中一般都要经过多次拉伸,这样对影响拉伸件的尺寸会产生影响,这些覆盖件产品尺寸是否符合规定,标准样架是根据轿车四门两盖等覆盖压件成形和拉伸的特殊项目就必须进行验证。原材料符合性验证就是对所使用原材料进行外形、尺寸、机械性能、化学成份等项目的验证,这些验证都是按照检验指导书的规定项目、方法、
56、频次和材料标准判定准则要求进行。(2)轿车覆盖件产品尺寸验证。轿车四门两盖等产品的覆盖件冲压尺寸一般是用标准样架来进行抽样检验,以确定件产品的外形尺寸和装配要求设计制造的,为确保轿车四门两盖等覆盖件产品冲压尺寸,对这些标准样架的测量点要定期检定,每天还要用标准样件对测量点进行校正,有关人员对标准样架尺寸的检测结果、样架测量点的检定结果和样架测量点的校正结果,按规定进行记录和分析尺寸稳定性。(3)轿车覆盖件产品装配位置尺寸验证。轿车四门两盖、左、右侧围和车身冲压件装配位置尺寸验证,一般是采用柔性检具和悬臂三座标测量仪来检测,并由三坐标测试室来定期控制这些检测仪器的稳定性和分析这些检测数据。这些覆盖件产品外形复杂,制造和使用标准样架难度较大,因此汽车企业一般都采用柔性检具来检测这些零件尺寸。发动机罩内板专用检具制造(1) 使用环氧树脂制作毛胚;(2) 对制作好的毛胚进行数控加工,降刻5mm(由于拉伸件会产生回弹);(3) 使用线切割制作板卡(板卡材料可以为铝板、铁板,使用板卡可以对拉伸件的局部进行尺寸测量)。附录2 CAE拉伸分析绝对原创!索UG图请Q70980464632
- 温馨提示:
1: 本站所有资源如无特殊说明,都需要本地电脑安装OFFICE2007和PDF阅读器。图纸软件为CAD,CAXA,PROE,UG,SolidWorks等.压缩文件请下载最新的WinRAR软件解压。
2: 本站的文档不包含任何第三方提供的附件图纸等,如果需要附件,请联系上传者。文件的所有权益归上传用户所有。
3.本站RAR压缩包中若带图纸,网页内容里面会有图纸预览,若没有图纸预览就没有图纸。
4. 未经权益所有人同意不得将文件中的内容挪作商业或盈利用途。
5. 装配图网仅提供信息存储空间,仅对用户上传内容的表现方式做保护处理,对用户上传分享的文档内容本身不做任何修改或编辑,并不能对任何下载内容负责。
6. 下载文件中如有侵权或不适当内容,请与我们联系,我们立即纠正。
7. 本站不保证下载资源的准确性、安全性和完整性, 同时也不承担用户因使用这些下载资源对自己和他人造成任何形式的伤害或损失。