敞车翻转焊胎总装胎体部分毕业设计说明书
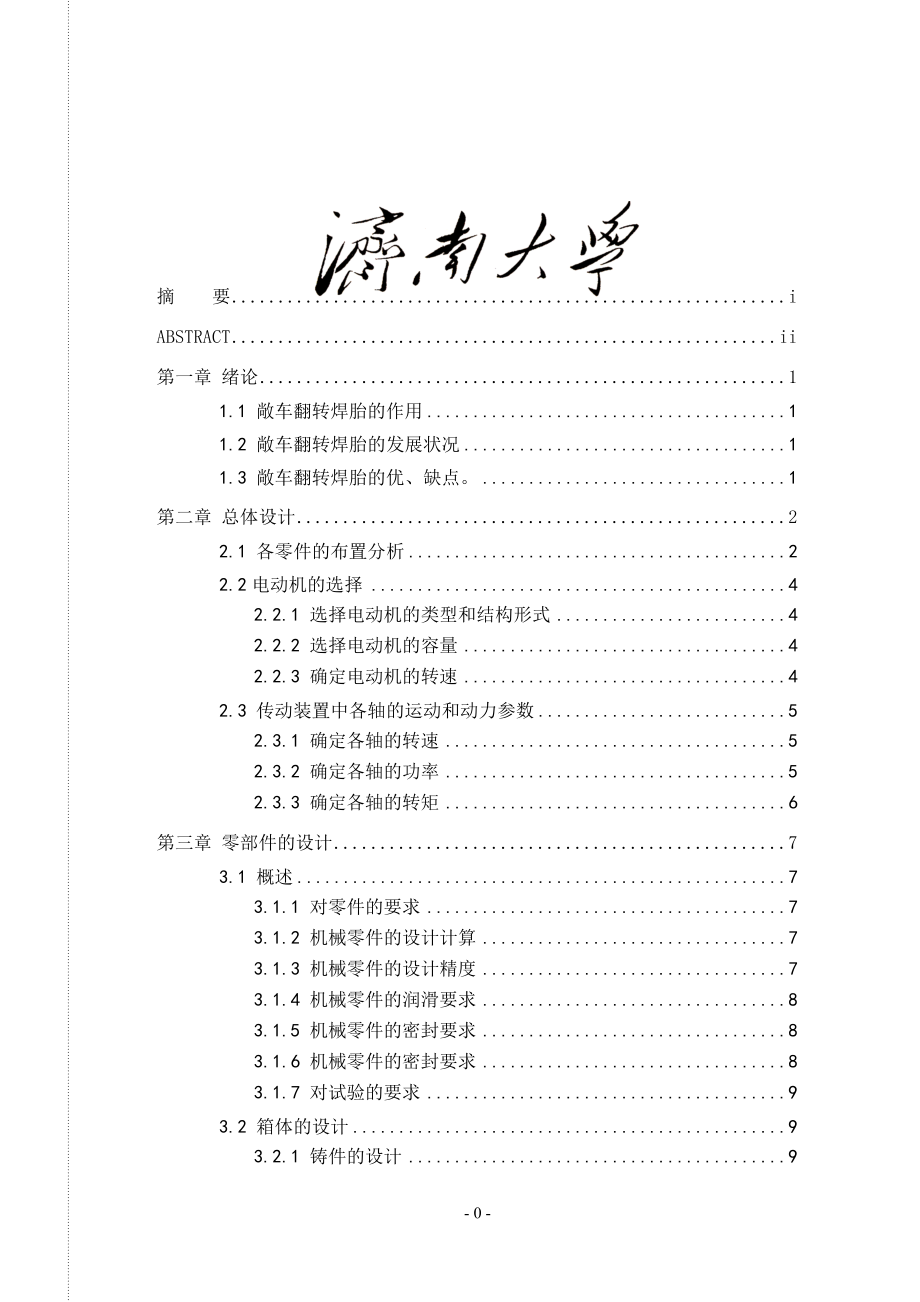


《敞车翻转焊胎总装胎体部分毕业设计说明书》由会员分享,可在线阅读,更多相关《敞车翻转焊胎总装胎体部分毕业设计说明书(35页珍藏版)》请在装配图网上搜索。
1、目 录摘 要iABSTRACTii第一章 绪论11.1 敞车翻转焊胎的作用11.2 敞车翻转焊胎的发展状况11.3 敞车翻转焊胎的优、缺点。1第二章 总体设计22.1 各零件的布置分析22.2电动机的选择42.2.1 选择电动机的类型和结构形式42.2.2 选择电动机的容量42.2.3 确定电动机的转速42.3 传动装置中各轴的运动和动力参数52.3.1 确定各轴的转速52.3.2 确定各轴的功率52.3.3 确定各轴的转矩6第三章 零部件的设计73.1 概述73.1.1 对零件的要求73.1.2 机械零件的设计计算73.1.3 机械零件的设计精度73.1.4 机械零件的润滑要求83.1.5
2、机械零件的密封要求83.1.6 机械零件的密封要求83.1.7 对试验的要求93.2 箱体的设计93.2.1 铸件的设计93.2.2 铸件的联接123.3 蜗轮蜗杆的传动设计133.3.1 选择蜗杆的传动类型133.3.2 选择材料143.3.3 按齿面接触疲劳强度进行设计143.3.4 蜗轮与蜗杆的主要参数与几何尺寸153.3.5 校核齿根弯曲疲劳强度153.3.6 蜗轮、蜗杆的几何尺寸163.4 蜗轮轴的强度校核163.4.1 求蜗轮轴的功率P2、转速n2、转矩T2163.4.2 初步确定轴的最小直径173.4.3 轴的结构设计173.4.4 轴的强度计算183.4.5 安全系数的校核计算
3、22第四章 胎体的设计与焊接工艺254.1 胎体的设计254.2 焊接工艺26致 谢28参考文献29- 2 -摘 要敞车翻转焊胎的工作原理是:敞车翻转焊胎包括动力装置、传动装置和工作装置、支撑装置和辅助装置组成。其工作原理是敞车翻转焊胎锁紧后将底架放在胎体上夹紧,然后进行焊接。底板上部焊接完成后通过减速装置将电机的高速运转变成2r/min左右的翻转,以减少冲击,由翻转装置带动底架翻转至所需要的焊接角度,焊接完成后车体调回原始位置,移出胎体。实施方案及主要研究手段是:本设计主要是为了实现机车底架的翻转焊接问题。机车的底盘是一个庞大的物体,而且有许多焊点,要使这个庞大的物体可以方便的焊接,需要有一
4、个辅助机构来帮助实现。机车翻转焊胎是专门用来辅助焊接的设备,将待焊的机体固定在翻转焊胎上,通过控制电机的启动和停止来控制焊胎,使其翻转到合适的位置以便于焊接。主要研究手段是通过查阅资料和到工厂参观实习。选题的创新之处是:适用于不需要精确定位的场合,且是大型的焊接材板。操作简单,成本低,不需要培训工人,可以立即投入使用。利用涡轮蜗杆传动的自锁性来实现胎体的定位。此设备不仅可用于敞车底板的焊接还能用于汽车底板的焊接。预期研究成果或结论是:通过传动部分使电机的高速运转变成2r/min左右的慢慢翻转,以减少冲击,最终使其停在所需要的位置。为实现胎体的定位本设计出了利用电机的启、停控制外,还利用涡轮蜗杆
5、传动的自锁性来实现。另外为实现夹紧的目的,设计中还用到了梯形螺纹的传动和传到特性。关键词:敞车;自锁;翻转;焊胎ABSTRACTThe flatcar turns over welds embryos principle of work is: The flatcar turns over welds the embryo including the power unit, the transmission device and the work installment, the blocking and the auxiliary unit composition. After its pr
6、inciple of work is the flatcar turns over welds the embryo locking, places the chassis on the carcass of tire to clamp, then carries on the welding. On after the ledger wall welds completes, through the decelerating device electrical machinerys high-speed operation turns about 2r/min the turn over,
7、reduces the impact, drives the ledger wall by the turnover device to turn over to the welding angle which needs, after the welding completes, the chassis recalls the initial position, emigrates the carcass of tire.Implementation of programmes and major research tools are: the design is to achieve th
8、e overturned locomotive chassis welding problems. The locomotive chassis is a huge objects, and many solder joints, to make this huge object can be a convenient welding, the need for a supporting institutions to help achieve. Locomotive overturned welding child is devoted to supporting the welding e
9、quipment, welding will be fixed in the body welding fetal overturned, by controlling the motor start and stop to control the welding child to flip to the right position in order to weld . Through the main means of access to information and training to visit the factory. Topics of innovation is: do n
10、ot apply to the precise positioning of the occasion, and a large plate of welding materials. Simple, low cost and do not need to train workers, you can immediately put into use. Use of the turbine worm drive to achieve self-locking of the carcass positioning. This equipment can be used not only gond
11、ola car chassis can also be used to weld the welding automobile chassis. Expected results or conclusions are: part of the electrical transmission through the high-speed operation into 2 r / min around slowly reversed to reduce the impact to the final stop in the required location. To achieve the pos
12、itioning of the carcass to design the use of motor Kai, stopping control, the turbines also use the worm transmission and to achieve self-locking. In addition achieve clamping for the purpose, also used in the design of a trapezoidal thread of the transmission and spread.KEYWORDS: Locomotive;Self-Lo
13、cking;Turns Over;Welding Carcass of Tire- 30 -济南大学毕业论文第一章 绪论第一章 绪论1.1 敞车翻转焊胎的作用本设计主要是为了实现敞车底架的焊接问题。由于敞车重约7吨,长12米,宽3米,而且有许多焊点,根据这些要求,我们需要设计一种辅助设备来实现庞大的敞车底架焊接问题,敞车翻转焊胎能够实现敞车底盘的焊接。机车车辆厂要对敞车底板各部位进行焊接操作,焊接方位、角度各有不同。为便于工作和保证焊接质量要求;设计了焊接敞车的专用设备敞车翻转焊胎。该设备主要是为了解决大型车辆底板的焊接问题的,这种设备主要用于定位不严格的场合,如果要想用于精确定位的场合,还须
14、利用电气传动等技术。1.2 敞车翻转焊胎的发展状况国外的自动翻转焊接技术发展比较快而我国70年代新产品较多,而进入80-90年代一直到现在几乎没有新产品问世但提出了一些新设想。无论国内还是国外总的发展趋势是朝着大体积、大吨位的方向发展但发展水平不太高。目前国内的现代化水平不高,离制动化和智能化控制还有一定的距离,有相当的企业还是用传统的机械控制。尽管科学技术迅速发展但是国内仍有相当部分的企业采用传统生产方式对他们来说立刻实现自动化和智能化无论从技术和财力上来说还不大现实。为了解决这种不足专门设计这样一台敞车翻转焊胎用于生产是在现实不过了。当然,随着科学技术的发展,对劳动强度的降低,生产的自动化
15、和智能化是企业发展的必然趋势。不过现在设计一台这样是比较实用的。1.3 敞车翻转焊胎的优、缺点。该设备的优点:降低了工人的劳动强度,操作简单,安全适用,成本低,可立即投入使用,通过改装可以焊接不同尺寸的底板。 该设备的缺点:自动化水平低,定位精度低。 济南大学毕业论文第二章 总体设计第二章 总体设计为实现预定的工作要求,该设备有动力装置、传动装置、工作装置、支撑装置和辅助装置五部分组成。动力装置是一个设备的动力源泉,合理的选择关系到设备的正常运转和经济节约的问题。在这里选用交流电动机。传动装置在动力装置与工作机之间。传动装置一般包括传动件(齿轮传动、蜗杆涡轮传动、带传动、链传动)和支撑件(轴、
16、轴承、机体)两部分。它的重量和成本在机器中占很大的比重,其性能和质量对机器的影响也很大,因此合理的设计方案很重要。2.1 各零件的布置分析布置传动顺序时,一般考虑一下特点:(1)动的承载能力较小,且有弹性,比较柔软,传动相同转矩时的结构尺寸较其它传动形式大,带传动的优点是传动平稳,噪音很小和能缓冲减震,结构简单,对制造精度要求低,特别适用于中心距大的传动;过载时打滑,具安全保护作用,因此宜布置在高速级(转速较时,传动相同功率转矩较小)。(2)链传动的特点是链传动与齿轮传动同属于啮合传动,但其链条是由金属构成的挠性件,这与带传动相似。与齿轮传动相比,具有以下优点和缺点:优点是与带传动相比没有弹性
17、滑动,传动效率较高;传动比准确,可靠。同样的载荷下张紧力比带传动的小,传动中心距较大,能够适应恶劣的环境,可以在温度,多油,潮湿的环境工作,其工作寿命比正常的工作环境里会缩短;缺点是瞬时传动比和在都不均匀,不适合高速传动;不适于急速反向传动;工作时有噪声;重量比较重;制造价格高。 因此,链传动不均匀,有冲击,不适于高速级,应布置在低速级。(3)蜗杆传动可实现较大的传动比,尺寸紧凑,传动平稳,但效率较低,适用于中小功率、间歇运动的场合。当与齿轮传动同时同用,对采用铝铁青铜或铸铁作为涡轮材料的蜗杆传动,由于允许齿面有较高的相对滑动的速度,可将蜗杆传动布置在高速级,以利于形成润滑油膜,可以提高承载能
18、力和传动效率。 (4)圆锥齿轮加工较困难,特别是大直径、大模数的圆锥齿轮,只有在改变轴的布置方向时采用,并尽量放在高速级和限制传动比,以减小圆锥齿轮的直径和模数。 (5)斜齿轮传动的平稳性较直齿轮传动性好,常用在高速级或要求传动平稳的场合。 (6)开式齿轮的工作环境更差,润滑条件不好,磨损较严重,寿命较短,应布置在低速级1。(7)一般将改变运动形式的机构(如螺旋传动、连杆传动、凸轮传动)布置在传动系统的最后一级,并且常为工作机的执行机构。本设计选用带传动较好,可以减少冲击。传动结构如图所示1.电动机 2.联轴器 3.带轮传动 4.夹紧装置 5.轴承 6.涡轮蜗杆装置 7.齿轮装置 8.胎体装置
19、图2-1 敞车翻转焊胎的传动结构图 工作部分是一个设备正常运转的主体,其重要性不言而愈。支撑部分也很重要,也是一套设备是否合理的标志,是设备正常运行的保证。2.2电动机的选择2.2.1 选择电动机的类型和结构形式交流电动机有异步电动机和同步电动机两类。异步电动机结构简单、工作可靠、价格低廉、维护方便,使用于不易燃、不易爆、无腐蚀性气体和无特殊要求的机械上。故本次设计中选用交流异步电动机。2.2.2 选择电动机的容量电动机的容量主要根据电动机运行时的发热条件决定。电动机的发热与其运行状态有关。电动机的运行状态有三类,即长期连续运行、短期运行和重复短期运行。本设计条件是短期重复运行2。电动机所需工
20、作功率按式 kw (21)其中: kw (22) F工作机的工作阻力; v工作机的线速度; T工作机的阻力距; n工作机的转速; 传动副的工作效率; (23)带传动的效率 1=0.95;蜗杆传动效率 2=0.72;滚动轴承的效率 3=0.980.980.980.98;齿轮传动效率 4 =0.96;Fv=7367Nms;所以 =0.950.720.960.980.980.980.98=0.53; =13.9(kw)2.2.3 确定电动机的转速翻转焊胎转速n=2 r/min;V带传动比i1= 24;圆柱齿轮传动比i2= 37;蜗杆传动比i3= 1070;总传动比i = 601120;故电动机可选转
21、速范围为: (24)=(601120)2=1202240(r/min)可选转速有750、1000、1500r/min。考虑到容量和转速,有由关手册查处三种电机的型号,综合比较选Y200-8L型。其性能如下表所示:表2-1 电动机的性能参数型 号额 定功 率满 载 时起 动电 流额 定电 流堵 转转 矩额 定转 矩最 大转 矩额 定转 矩转 速r/min电 流(380)A效 率 %功 率因 数Y200L-8157509.4840.776.01.822.3 传动装置中各轴的运动和动力参数2.3.1 确定各轴的转速蜗杆转速: n1=n/i1=730/2 =365(r/min) 涡轮轴的转速: n2=
22、n1/i2 =365/41 =8.9(r/min) 大齿轮轴的转速: n3=n2/i3 =8.9/4.5 =2(r/min)2.3.2 确定各轴的功率 输入蜗杆的功率: P1=Pd =150.880.95=12.54 (kw) 输入蜗轮轴的功率: P2=P1 =12.540.420.98 =5.16(kw)大齿轮轴的功率: P3=P2 =5.160.960.98 =4.86(kw)胎体转动功率: P4=P3 =4.860.980.98=4.66(kw)2.3.3 确定各轴的转矩 (2-5)其中: nw电动机满载转速; Pd电动机功率;故 Td=955015/730 =196(Nm)蜗杆转矩:
23、T1=Td i1 =19620.880.95 =327.7(Nm)涡轮轴的转矩: T2=T1 i2 =327.7410.420.98 =5530.13(Nm)大齿轮的转矩: T3=T2 i3 =5530.134.50.960.98 =23412.36(Nm)胎体轴的转矩: T4=T3 i4 =23412.360.980.98=22485.23(Nm) 济南大学毕业论文第三章 零部件的设计第三章 零部件的设计敞车翻转焊胎的各零部件设计是至关重要的,为了保证各零部件能够顺利安装必须注意其功能要求、工艺性要求、工艺性要求。3.1 概述3.1.1 对零件的要求a 功能要求 主要有强度、刚度、精度、寿命
24、、耐热性、平稳性等,有时还需满足质量体积、噪声、防蛀、环保要求。 b 工艺性要求 有利于毛胚的制取,机加工、热处理、装配、修理等工艺环节的实施,能实现装配、修理、更换的互换性。 c工艺性要求 要使综合经济效益高,合理的选择材料力求材料费用低;良好的结构工艺性,使标准化在一定的范围内,使设计尽量简化。 d 能够保证操作者操作方便、安全;使设计的产品外观美丽3。3.1.2 机械零件的设计计算机械零件的主要尺寸常需要根据强度、刚度、耐磨性等要求经过计算确定。由于零件的工作条件,复杂程度重要性不同的方法,甚至经验公式的计算。对于重要的零件应采用比较精确的计算方法。但在各种计算中,要对复杂的现象进行合理
25、的假设与简化,虽然这样的计算不够准确,但精确度还是比较高的。3.1.3 机械零件的设计精度机械零件功能要求的实现,相当程度上依赖于组成该产品的各零件的几何精度。因此,零件的几何精度设计是实现产品功能的基础。 在满足功能要求的前提下,精度的设计还必须充分考虑经济性要求。如果选择低精度的尽量选用低精度的,以便于提高产品性能价格比。但是,在评价精度设计的经济性时,还必须考虑到产品的无故障工作时间,随着科学技术的发展和生产力的提高人们可以在不断降低生产成本的条件下提高产品的精度。在零件装配前,应尽量按图纸检验零件的配合尺寸,合格零件才能装配。所有的零件要用煤油或汽油清洗,机体内不许有任何杂物存在,机体
26、内壁应涂上防侵蚀的涂料4。3.1.4 机械零件的润滑要求润滑剂对传动性能有很大的影响,起着减少摩擦、降低磨损和散热冷却的作用,同时也有助于减震、防锈及冲洗杂物,所以在技术要求上要求中应标明传动件及轴承所用的润滑剂牌号,用量、补充及更换时间。 选择润滑剂时,应考虑传动的类型、载荷的性质及运动速度。一般对重载、高速、频繁启动、反复运转等情况,由于形成油膜条件差,温度高,所以应选用粘度高、油性好和积压性好的润滑油。例如蜗杆减速器,低速重载齿轮传动就属于这种情况。对轻载、间歇工作的传动件可取粘度较轻的润滑剂5。 当传动件与齿轮采用同一润滑剂时(两者对润滑剂要求不同),应优先满足传动件并适当兼顾轴承的要
27、求。 对多级传动,由于高速级和低速级对润滑剂粘度要求不同,选用时可取其平均值。一般齿轮减速器常用40号、50号、70号等机械油润滑剂润滑。对中、重型减速器,可选汽缸油、28号轧钢机油、齿轮油(HL20、HL30)及工业齿轮油、极压齿轮油等润滑。对蜗杆减速器可用机械油、汽缸油、齿轮油及复合型润滑油润滑。传动件和轴承所用润滑剂的具体选择方法可参照手册。机体内装油量计算如前所述。换油时间取决于油中杂质多少氧化与被污染的程度,一般为半年左右。当采用润滑脂润滑时候,轴承空隙内润滑脂的填入量与速度有关,若轴承转速是n1500 r/min,润滑脂填入最多不超过轴承间隙的2/3;若轴承转速n1500r/min
28、,则不得超过轴承间隙容积的1/31/2。润滑脂用量过多会使阻力增加,温升提高影响润滑效果6。3.1.5 机械零件的密封要求在试运转中,所有联结面及轴身密封都不允许漏油。剖分面允许涂以封胶或水玻璃,不允许使用任何垫片。轴身处密封应涂以润滑脂。3.1.6 机械零件的密封要求在安装调整滚动轴承时,必须保证一定的轴向游隙。应在技术要求中提出游隙大小。因为游隙大小将影响轴承的正常工作。游隙过大会使滚动体受载不均、轴隙窜动;游隙过小则会妨碍轴隙因发热而伸长,增加轴承阻力,严重时会将轴承卡死。当轴承支点跨度大、运转温升高时,应取较大的游隙。当安装固定的轴承结构中采用不可调间隙的轴承(如向心球轴承)时,可在端
29、盖与轴承外圈面留有适当的轴向间隙(=0.250.4mm),以容许轴承的热伸长,间隙的大小可用垫片调整。其调整方法时,先用端盖将轴承顶紧到轴能够勉强转动,这时基本消除了轴承的间隙,而端盖的间隙,在用厚度为+的调整片至于端盖与轴承的轴向间隙之间,拧紧螺栓,即可得到需要的间隙。垫片可用一组厚度不同的软钢薄片所组成,其厚度为1.22mm。 对可调间隙的轴承(如角接触轴承和圆锥滚子轴承),由于其内外圈是分离的或是可以相互窜动,所以应仔细调整其间隙位置,最后锁紧螺母即可。端盖与轴承之间的垫片不起调节作用,只起密封作用7。 在安装齿轮或涡轮后必须保证需要的侧隙及齿面接触斑点,所以技术要求必须提出这方面的具体
30、要求,共安装后使用。侧隙和接触点是由传动精度确定,可用手册查出。 传动侧隙的检查是可以用塞尺或铅片尺塞进相互啮合的两齿间,然后测量塞尺的厚度或铅片变形后的厚度。 接触斑点的检查是在主动轮齿面上涂色,当主动轮齿传动23周后,观察从动轮的着色情况,由此判断接触区的位置及接触面积大小。 当传动侧隙及接触斑点不符合精度要求的时候,可对齿面进行刮研、跑合或调整传动件的啮合位置。对于圆锥齿轮减速器,可通过垫片调整圆锥齿轮位置。使两圆锥齿顶重合。对于蜗杆减速器,可通过垫片调整涡轮轴承垫片(一端加垫片,一端减垫片)使蜗杆轴心线通过蜗杆中间平面。对多级传动,当各级的侧隙合斑点要求不同时,应在技术要求中写明。3.
31、1.7 对试验的要求做空载试验正反各转一小时,要求运转平稳、噪声小、连接固定处不松动。负载实验时,油池温升不得超过35摄氏度,轴承温升不得超过40摄氏度。3.2 箱体的设计3.2.1 铸件的设计进行铸件设计时,不仅要保证其工作性能和机械性能要求,还必须考虑铸造工艺和合金铸造性能对铸件结构的要求,并使铸件的具体结构与这些要求相适应。铸件的结构是否合理,即其结构的工艺性是否良好,对铸件的质量、生产率及其成本有很大影响。当产品是大批量生产时,铸件的结构应便于采用机器造型;当产品是单件、小批量生产时则应使所设计的铸件尽可能的在现有的条件下生产出来。若某些铸件需要采用金属铸造时、压力铸造或熔模铸造等特种
32、铸造方法时,还必须考虑这些方法对铸件结构的特殊要求。铸件结构应尽可能使制模、造型、制芯、合箱和清理等过程简化,避免不必要的人力、物力的耗费,防止废品,并为实现机械化生产创造条件。因此,进行铸件设计时,必须考虑下列问题:a 铸件的外形应便于取出模型 铸件的外形在能满足使用要求的前提下,多可在一定范围内变动,因此,在设计铸件外形时,应从简化铸件工艺出发,使其便于取模,尽量避免操作费事的三箱造型、挖沙造型、活块造型及不必要的外部型芯。b 避免外部侧凹 铸件在起模方向若有侧凹,必须增加分型面的数量,这不仅使造型费工,而且增加了错箱的可能性,使铸件的尺寸误差增大。c 分型面尽量平直 平直的分型面可避免操
33、作费时的挖沙造型或假箱造型,同时,铸件的毛边少,便于清理,因此,在尽力避免弯曲的分型面。箱体设计应考虑一下几个问题:a 箱体要有足够的刚度 箱体刚度不够,会在加工和工作中过程产生不允许的变形,引起轴承座孔中心线歪斜,在传动中产生偏差,影响减速器正常工作。因此,在设计中,首先应保证轴承座的刚度。此时,使轴承座有足够的厚度,并在轴承座附近加撑肋。当轴承是剖分式,还要保证它的连接刚度。箱体加肋肋有外肋和内肋两种结构形式。内肋刚度大,外表光滑美观,虽然内肋阻碍润滑油流动,工艺也比较复杂。但目前采用内肋结构逐渐增多。当轴承伸到机体内部时,则常用内肋。为了提高轴承座的连接刚度,座孔两侧的联结螺栓距离应尽量
34、靠近,因此轴承座附近应做成凸台,其高度要保证安装时有足够定额扳手空间。为了保证箱体的刚度,箱体盖和箱体座的联结凸缘的宽度B应超过机体的内壁。b 因考虑便于箱体内零件的润滑、密封及散热 对于大多数减速器的箱体来说,由于其传动件的圆周速度V12m/s,故常采用浸油润滑(当V12m/s时应采用喷油润滑)。因此箱体内需要有足够的润滑油,用以润滑和散热。同时,为了避免油搅动沉渣泛起,池顶到油池底面的距离H不应小于3050mm。由此,即可决定箱体的座高度。传动件的浸油深度为h。对于下置式蜗杆减速器,浸油深度不应超过滚动轴承的最低滚动体中心,以免影响密封和增加搅油的损失。浸油深度决定后,即可定出所需油量。并
35、按传递功率的大小进行演算,以保证散热。对于单级传动来说,传递1kw需增加油量0.350.7 cm3;对于多级传动,按级数成比例增加,如不满足,应适当的增加机座的高度,以保证足够的容池溶积。 当轴承利用机体内的油润滑时,可在剖分面联结凸圆上做出输油沟槽,使飞溅的润滑油沿箱体盖经油槽通过端盖的缺口流入轴承。采用不同的加工油槽方式。对于采用润滑的多级传动,当低级传动齿轮浸油深度超过1/3分度圆半径时,往往会使搅油损失过大,这时可减少低速级大齿轮的浸油深度,而高速级齿轮则利用溅油装置润滑。对于下置蜗杆减速器的箱体,当油面高度受到轴承最低滚动体高度的限制时,蜗杆常接触不到油面,这时可在蜗杆减速器上装减油
36、盘,以使油溅到传动件上而进行润滑。当传动件(如蜗轮)转速较低时,若轴承需要利用机体内的油进行润滑,则可在靠近传动件处安置刮油板,其端油面靠近传动件端面,运转时将油从轮上被刮下,并引入轴承中。为了保证机盖和机座联结处密封,联结凸缘应有足够的宽度,联结表面应精刨,其表面粗糙度应不大于6.3m。密封要求的表面要经过刮研。为了提高密封性,在机座凸缘上面常铣出回油沟,使渗入凸缘联结缝隙面上的油重新回到机体内部。对于蜗杆减速器,由于发热过大,应进行热平衡计算。机体大小要考虑散热面积的需要,若经平衡计算不符要求,可适当的增加机体尺寸或增设散热片和风扇。散热片的方向应与空气流动方向一致。发热严重时还应在油池内
37、设置蛇形冷却水管,或改用循环系统,以降低油温。c 箱体结构要有良好的工艺性 箱体结构工艺性好坏,对提高精度和装配质量、提高劳动生产率以便于检修维护等方面,会有直接影响,故应特别注意。 在设计铸件机体时,应考虑到铸造工艺特点,力求形状简单、壁厚均匀、过渡平缓、金属不要局部积聚。考虑到液态金属流动的畅通性,逐渐壁厚不可太薄,沙形铸造圆角可取r5mm。为了避免因冷却不均匀而造成的内应力裂纹和缩孔,机体各部分壁厚应均匀。当由较厚的部分过渡到较薄的部分时,应采用平缓的过渡结构。设计箱体时,应采用机体外形简单,拔模方便。为了便于拔模,铸件沿拔模方向有1:101:20的拔模斜度。对于铸造机体,还应尽量减少沿
38、拔模凸起结构,否则在模型上就要设置活块,以减少拔模困难。当机体表面有几个凸起部分时,应尽量将其连成一片,以简化取模过程。箱体上还应尽量能避免出现裂缝,否则砂型强度不够,在取模和烧铸时易形成废品。设计结构形状时,应尽量减少机械加工面积,以提高劳动生产率,并减少刀具磨损。为了保证加工精度并缩短加工工时,应尽量减少在加工时工件和刀具的调整次数。例如同一方向的加工平面,应尽量一次调整加工成功。所以,各轴承座端面都应在同一平面上。箱体的仍可一部分加工面与非加工面必须严格分开。例如,箱体盖的轴承座端面需要加工,因而,应当突出,与螺栓头部或螺母接触的支撑面,应尽量进行机械加工8。3.2.2 铸件的联接设计铸
39、件壁的联接或转角时,也应尽力避免金属的积聚和内应力的产生。a 铸件的结构圆角 铸件壁间的转角处一般应具有结构圆角,这是由于:直角联接处形成金属积聚,而内侧散热条件差,故较容易产生缩孔和缩松;在载荷作用下,直角处的内侧产生应力集中,使内侧实际承受的应力较平均应力大大增加;在一些合金的结晶过程中,将形成垂直与铸件表面的柱壮晶,若采用直角联接,则因结晶方向性,在转角的分角面上,形成了整齐的分界面,在此则因结晶的方向性,在转角的分角线上,形成整齐的分界面,在此分界面上集中了许多杂质,使转角处成为铸件的薄弱环节。上述诸因素均使铸件转角处的机械性能下降,较易产生裂纹。当铸件采用圆角结构时,可以克服上述之不
40、足,提高了转角处的机械性能。此外,铸造外圆角还美化铸件的外形,避免划伤人体,铸造内圆角还可以防止金属液流将型腔尖角冲毁。总前所述,圆角是铸件结构的基本特征,不容忽视。铸造内圆角的大小与铸件的壁厚相适应,通常应使转角处内接圆直径小于相邻壁厚的1.5倍,过大则增大了缩孔的倾向。b 避免锐角接触 为了减少应力集中现象和热节现象,应避免铸件壁间的锐角联接。c 壁厚和壁间的联接要逐步过渡 铸件各部分的壁厚往往难以做到均匀一致,甚至存在很大的差别。为了减少应力集中现象,应采用逐步过渡的方法,防止壁厚的突变。d 防裂筋的应用 为了防止热裂,可在铸件易裂处增设防裂筋,为防裂筋能起到应有的效果,筋的方向必须与机
41、械应力一致,而且筋的厚度应为联接厚度的1/41/3。由于防裂筋很薄,故在冷却过程中迅速凝固而具有较高的强度,从而增大壁间的联接力。防裂筋常用铸钢、铸铝等易热裂合金。 必须指出的是,由于各类铸造合金的铸造性不同,因而 他们的结构也各有特点。普通灰口铸铁因其缩孔、缩松、热裂倾向小,所以对铸件的壁厚的均匀性、壁间的过渡、轮辐形式等要求均不象铸钢那样严格,但其壁厚对机械性能的敏感性大,故以剥壁结构最为适宜。另一方面,也要防止极薄的截面,以防止出现硬脆的白口组织。灰口铸铁的牌号愈高,因铸造性能随之变差,故对铸件结构的要求也愈高,但孕育铸铁可设计成较厚铸件9。综上所述箱体采用的材料是HT200,由于是蜗轮
42、蜗杆减速器查机械设计手册知:箱座的臂厚 =0.04a+38;由于 a=400mm,=0.04400+3=19(mm),所以满足条件 =20mm;由于蜗杆在上所以箱盖的壁厚 1=20mm;箱盖的凸缘厚度 b1=1.5=1.520=30(mm);箱座的凸缘厚度 b=1.5=1.520=30(mm);箱座底凸缘厚度 b2=2.520=50(mm) ;地脚螺钉的直径 df=0.036a+12=26.4(mm);地脚螺钉的数目 n4;轴承旁联接螺栓的直径 d1=0.75df=0.7526.4=12(mm);盖与座联接螺栓的直径 d2=(0.50.6)d1=(0.50.6)12=(67.2)mm;箱盖、箱
43、座肋厚 m1=0.851=0.8520=17(mm);蜗轮处圆与箱壁距离 116mm;蜗轮轮毂端面与内壁距离 10mm;3.3 蜗轮蜗杆的传动设计蜗杆传动用于交错轴间传递运动及动力,通常交错角为90,主要优点:传动比大,工作稳定、噪声低、结构紧凑、可以自锁;缺点:效率低10。已知:输入功P=12.54kw,蜗杆的转速n=365r/min,传动比i2=41,Lh=12000h。3.3.1 选择蜗杆的传动类型由于渐开线蜗杆(ZI)比较容易加工所以被选用。3.3.2 选择材料由于传动传递的功率不大,速度不高等故蜗杆用35CrMo;因希望效率高些,故蜗杆螺旋齿面要求淬火;硬度为45-50HRC。涡轮用
44、铸锡磷青铜(ZcuSn10PI);金属模铸造。仅齿圈用青铜制造,而轮芯用灰铸铁HT200制造11。3.3.3 按齿面接触疲劳强度进行设计根据闭式蜗杆传动的设计准则,再校核齿根弯曲疲劳强度。传动中心距 (3-1)1)确定作用在蜗轮上的转矩T2按Z1=1,估取效率=0.7,则=(Nmm)2)确定载荷系数K因工作载荷较稳定,故取载荷分布不均系数K=1;由表11-5选取使用系数KA=1.15;由于转速不高,冲击不大,可取动载系数KV=1.05;则K=KAKKV=1.1511.051.21 3)确定弹性影响系数ZE 因选用的是铸锡磷青铜涡轮和钢蜗杆相配,故ZE=160Mpa1/2。 4)确定接触系数Z先
45、假设蜗杆分度圆直径d1和传动中心距a的比值d1/a=0.3,从图11-8中可查得Z=3.0。5)确定许用接触应力H根据涡轮材料为铸锡磷青铜ZcuSn10PI,金属模铸造,蜗杆螺旋齿面硬度45HRC,可从表11-7中查的涡轮的基本许用应力H=270Mpa应力循环次数 寿命系数 则 H= KHNH=1.057270=285(Mpa)6)计算中心距 (mm)取中心距a=400mm,因i=41,故从表中取模数m=16mm,蜗杆分度圆直径d1=140mm,这时d1/a =0.35,从图11-8中可查得接触系数Z=2.9,因为ZZ 所以上计算的结果可用。3.3.4 蜗轮与蜗杆的主要参数与几何尺寸1)蜗杆轴
46、向齿距 pa=m=3.1416=50.24(mm)直径系数 q= d1/m=8.75齿根圆直径 df1=d1-2hf1=d1-2(ha+c)m=140-2(1+0.2)16=101.6(mm)分度圆导程角 蜗杆轴向齿厚 (mm)涡轮变形系数 2)涡轮涡轮齿数Z2=41;变位系数x2=0.125;验算传动比,这时传动比误差为,是允许的。涡轮分度圆直径 d2=mz2=1641=656(mm)涡轮喉圆直径 da2=d2+2ha2=(656+2161.125)=692(mm)涡轮齿根圆直径 df2=d2-2ha2=656-2161.075 =621.6(mm)顶圆直径 de2da2+2m=692+32
47、=724(mm)所以取 de2=712mm涡轮咽喉母圆半径 (mm)3.3.5 校核齿根弯曲疲劳强度 (3-2) 当量齿数 根据x2=0.125,zv2=41.84,从图11-9中可查得齿形系数YFa2=2.35螺旋角系数 许用弯曲应力F=FKFN从机械手册表11-8中查得由ZcuSn10PI制造的蜗杆的基本许用弯曲应力应该是F=56Mpa。寿命系数 KFN=0.86 F=560.86=48(MPa) (MPa) 弯曲强度是满足的12。3.3.6 蜗轮、蜗杆的几何尺寸 x2=0.125;=20;a=400mm;z1=1;z2=41;d1=140mm;d2=656mm; da1=d1+2ha1=
48、d1+2ham=140+216=172(mm); df1=d1-2hf1=d1-2(ha+C)m=140-21.216=101.6(mm); b1(8+0.06Z2)m=(80+0.0640)16=167.36(mm);取b1=170mm; da2=d2+2ha2=d2+2m(h*a+x2)=656+216(1+0.125)=692(mm); b20.75da1=0.75172=129(mm);(mm); Sa=m/2=25.12mm;Sn= Sacos=25.12cos6.25=24.96(mm); St=(0.5+22tan)m=(0.5+20.125tan20)=26.59(mm); l
49、=(1.21.8)d=1.44125=180(mm)3.4 蜗轮轴的强度校核3.4.1 求蜗轮轴的功率P2、转速n2、转矩T2取蜗轮的传动效率=0.42,则 P2=12.540.420.98=5.16(kw);n2=n1/i2=356/41=8.9(r/min); =(Nmm)求作用在蜗轮上的力,已知蜗轮分度圆的直径为d2=1641=656(mm)(N) (N)(N)3.4.2 初步确定轴的最小直径按公式 (3-2) 查表知A0=120所以 (mm)选轴的最小直径为110mm。选轴的材料为45号钢,经调质处理3.4.3 轴的结构设计(1)确定轴上的零件布置方案和固定方式 将蜗轮布置在轴的中部,
50、对称于两端轴承,蜗轮用轴肩和轴套作为轴向固定,用平键或过盈配合()轴向固定;左端轴承用轴肩和过渡配合固定的内套圈;右端轴承用轴套和过渡配合()固定在内套圈。轴的轴向定位是由轴承端盖单向固定轴承的外套来实现的。轴外伸段的齿轮用轴肩作轴向固定,用平键作周向固定13。(2)初步选择滚动轴承 因轴承同时受有径向力和轴向力的作用,故选用单列圆锥滚子轴承根据左端轴颈的直径120 mm,由轴承的产品目录中初步选取O基本游隙组,标准精度级的单列圆锥滚子轴承7124,其中尺寸为dDT=120mm180mm38.4mm。(3)确定轴各段直径 根据轴外伸段直径d=110mm,为了避免轴承端盖与外部所安齿轮的干涉取安
51、装齿轮轴的左侧的轴径的直径为115mm,根据工艺和强度,需要把轴承做成阶梯型。通过轴承端盖轴段直径为120mm(符合滚动轴承内径系列标准),根据轴设计的相关经验需要将轴肩左侧的轴段直径设计为130mm,安装蜗轮轴段直径为125 mm。取轴肩直径为135mm。确定蜗轮的轮毂长度为180mm,根据轴承内套圈宽度为38.4mm,取左端的轴径长度为38.4mm,根据箱体内壁与蜗轮轮毂之间的距离间隙的大小,取轴肩宽为17mm。该轴的尺寸如图3-1所示:3.4.4 轴的强度计算(1)绘制轴的受力简图 对单列圆锥滚子轴承7124型,查得作用力与轴线的交点距轴承端盖距离为a=38mm。根据轴的结构尺寸及支反力
52、点的确定,作出轴的受力图,如图3-2所示,轴承的跨度l=38.4+34.6+17+180+90-38-38=284(mm),轴上的作用力大小前已计算过14。 图3-1 蜗轮轴的尺寸 图3-2 蜗轮轴的受力、弯矩及扭矩图水平面内支反力图9-10(b)(N)铅垂面内支反力图9-10(d) (N)(式中d2为蜗轮的分度圆直径)(2)作弯矩图蜗轮作用力集中在齿宽中心。水平弯矩图MH见图9-10(c)在截面B左、右边 (Nmm)垂直面弯曲图MV见图9-10(e)在截面B左边(Nmm)在截面B的右边(Nmm)合成弯矩图从图9-10(c)可看出,B截面为危险截面,其合成弯矩为在截面B的左边=1413548.
53、586(Nmm)在B截面的右边(Nmm)合成图见图(f)。(3)作转矩图此轴输出转矩T=5.537106Nmm,向外传出,如图9-10(g)所示。轴频繁启、停,单向运转,可认为扭矩应力为脉动循环变化,故取=0.6,则 T=0.65.537106=3.3222106(Nmm)(4)求最大当量弯矩如图9-10(h)所示: =3610419.98(Nmm)(5)强度校核(Mpa)前以选定轴的材料为45号钢,调质处理,由表查知H=60Mpa。因此ca-1,故安全15。3.4.5 安全系数的校核计算(1)判断危险截面由图可知:轴段支点C右侧的截面只受扭矩作用,虽然键槽、轴肩及过渡配合所引起的应力集中均将
54、削弱轴的疲劳强度,但由于轴的最小直径是按扭转强度较为宽裕地确定的,所以轴段、支点C的右侧的载面无需要校核。从应力集中对轴的疲劳强度的影响看,轴和轴承过盈配合引起的应力集中最严重;从受载的情况来看,截面B左侧上当量弯矩MBca1最大。轴段上各截面的应力集中相近,但截面B左侧不受扭矩的作用,同时轴径较大,故不必进行强度校核,截面B上虽然弯矩最大,但应力集中不大,而且这里轴的直径较大,故载面B也不必校核。轴段和显然更不必校核。键槽的应力集中系数比过盈配合的小,因而该轴只需校核轴段和轴段连接处的截面mm两侧即可。(2)截面mm左侧1)计算弯曲截面系数抗弯截面系数为 W=0.1d3=0.11253=19
55、5312.5(mm3)抗扭截面系数 WT=0.2d3=0.21253=390625(mm3)截面mm左侧的弯矩为(Nmm)截面mm的转矩T为T=5.537106Nmm截面上的弯曲应力 (MPa)截面上的扭转切应力(MPa)2)计算综合系数轴的材料为45号钢,调质处理,由表9-1查得b=640MPa, -1=275 MPa, -1=155 MPa。a.应力系数。从图2-6、图2-7查取应力集中系数、及材料的敏性系数q、q。由式(2-4)得应力系数k=1+q(-1)=1+0.68(1.92-1)=1.63k=1+ q(-1)=1+0.76(1.65-1)=1.49b.由图2-8查取尺寸影响系数得=0.68,=0.83c.轴段按磨削加工,由图2-9查得表面质量系数为=0.92d.由式(2-5)得综合系数为 3)计算安全性系数材料特性系数、,对碳钢,=0.10.2,对合金钢=0.20.3;=0.5,取=0.15,=0.075。轴向力较小,它所引起的应力可不计,对于机器大多数轴来说r=c,所以有式(9-5)、(9-6),得轴在截
- 温馨提示:
1: 本站所有资源如无特殊说明,都需要本地电脑安装OFFICE2007和PDF阅读器。图纸软件为CAD,CAXA,PROE,UG,SolidWorks等.压缩文件请下载最新的WinRAR软件解压。
2: 本站的文档不包含任何第三方提供的附件图纸等,如果需要附件,请联系上传者。文件的所有权益归上传用户所有。
3.本站RAR压缩包中若带图纸,网页内容里面会有图纸预览,若没有图纸预览就没有图纸。
4. 未经权益所有人同意不得将文件中的内容挪作商业或盈利用途。
5. 装配图网仅提供信息存储空间,仅对用户上传内容的表现方式做保护处理,对用户上传分享的文档内容本身不做任何修改或编辑,并不能对任何下载内容负责。
6. 下载文件中如有侵权或不适当内容,请与我们联系,我们立即纠正。
7. 本站不保证下载资源的准确性、安全性和完整性, 同时也不承担用户因使用这些下载资源对自己和他人造成任何形式的伤害或损失。
最新文档
- 部编人教版语文三年级下册第八单元 方帽子店 ppt课件
- 微生物灭菌问题培训课件
- 廊坊房地产市场整合课件
- 廖小菲XXXX财务报告—利润表-课件
- 廊坊售后11月目标完成报告课件
- 部编人教版四年级语文上册《口语交际 我们与环境》优质ppt课件
- 延伸存取列表课件
- 部编人教版语文三年级下册第六单元 习作:身边那些有特点的人 ppt课件
- 廉颇蔺相如列传重点语句翻译上课-课件
- 廉颇蔺相如列传课件
- 廉颇蔺相如列传公开课优质课-课件
- 微生物活菌计数方法教学课件
- 部编人教版三年级数学下册第4课时 简单的路线图课件
- 廉洁行医秉公奉廉医疗卫生行业廉洁自律培训模板课件
- 部编人教版六年级道德与法制上册第8课《我们受特殊保护》 ppt课件完整版